AFLOWT MFT User manual

TECHNOLOGICAL MAGNETIC
FLOW METER
AFLOWT MFT
INSTALLATION MANUAL
ISO 9001:2015

2
CONTENTS Page
INTRODUCTION.....................................................................................................3
1. SAFETY INSTRUCTIONS...................................................................................4
2. PREPARATION FOR MOUNTING......................................................................4
3. MOUNTING……..................................................................................................5
3.1. General Requirements...........................................................................5
3.2. Mounting the flowmeter in the pipeline...................................................5
3.3. Mounting the secondary converter of the flowmeter remote version......9
3.4. Wiring the Flowmeter...........................................................................10
4. DISMOUNTING.................................................................................................11
5. PUTTING INTO OPERATION...........................................................................12
APPENDIX A. Mounting wafer type Flowmeters into the pipeline...............13
APPENDIX B. Mounting Flowmeters of flanged type into the pipeline........16
APPENDIX C. Mounting Secondary converter ...........................................19
APPENDIX D. Signal cables PFC-SC.........................................................21

3
The present manual covers procedures for on-site (at a metering
point) mounting and dismounting of "AFLOWT MFT" Technological
Magnetic Flowmeter. In the course of work, also refer to the
"Technological Magnetic Flowmeter "AFLOWT MFT". Operation
manual" document, Part I and Part II.
LIST OF ABBREVIATIONS
DN
BE
PFC
MFT
SC
- Nominal diameter
- Electronic block
- Flow sensor (Primary flow converter)
- Magnetic flowmeter
- Secondary converter
NOTE. Words in the text marked in bold, for example, FLOW
DATA, corresponds to the items displayed on the Flowmeter's screen.
CAUTION!
1.NEVER touch the electrodes in the flow sensor (PFC) inner channel.
2.When the flowmeter is energized, DO NOT perform electric welding in
the room where the flowmeter is placed in case the pipeline where the
flowsensor is installed is not filled with liquid, and on the pipeline where
the flow sensor is installed.
3.While welding, passing of weld current through the PFC body is
STRICTLY FORBIDDEN.
4.When welding is performed, DO NOT use the flowmeter with PFC
installed. Install the PFC dimension simulator provided in the delivery
package.
5.MFT mounted in the pipeline SHOULD NOT be rotated around the
pipeline axis.
6.When mounting and using MFT, DO NOT remove protection rings from
PFC. The protection rings are installed to protect projecting fluoroplastic
lining.
7.When relocating MFT, DO NOT hold it by the electronic block.

4
1. SAFETY INSTRUCTIONS
1.1. The flowmeter should be mounted (dismounted) by the qualified
technical staff:
- Certified for performing work of this type on the site where the flowmeter
is installed and authorized by the manufacturer
- Authorized to work with electrical installations up to 1000 V
- Familiar with the instructions for the flowmeter and the auxiliary
equipment used for mounting and dismounting.
1.2. When working with the flowmeter, the dangerous factors are as follows:
- AC voltage (RMS value up to 264 V, frequency 50/60 Hz)
- Pipeline pressure (up to 4.0 MPa depending on PFC design version)
- Temperature of medium (up to 150 °C depending on PFC design
version)
- Other installation site-specific factors.
1.3. In the course of mounting (dismounting), YOU MUST NOT:
- Connect to the flowmeter, switch over modes and replace electronic
components, if the flowmeter is powered up
- Remove the flowmeter from the pipeline until pressure in the pipeline
section worked on is fully released
- Use defective electronic devices and electric tools or use them without
proper grounding.
1.4. Prior to performing work, make sure that no dangerous AC/DC voltage
that may cause injury or death is applied to the pipeline section to be
worked on. Use an appropriate measuring device for this purpose.
2. PREPARATION FOR MOUNTING
2.1. The flowmeter should be transported packed in the manufacturer’s box.
2.2. After the flowmeter has been moved to the mounting location from a
cold environment into a warm one (with ambient temperature above
zero), it shall be left in the manufacturer’s box for at least 3 hours to
make sure that no moisture will condensate inside.
2.3. When unpacking the flowmeter, check that the delivery package
contains all items specified in the Passport.

5
3. MOUNTING
3.1. General Requirements
When mounting the flowmeter on site, a free pipeline section
should be provided. It is used to mount the flow sensor; straight pipe
runs of appropriate length upstream and downstream the flow sensor.
Overall dimensions and weight of the flowmeter are given in the
Operation Manual, Part I, Appendix A.
CAUTION! You MUST choose a mounting location with the
conditions meeting the requirements specified in the user manual.
3.2. Mounting the flowmeter in the pipeline
3.2.1. Mounting considerations:
- The flowmeter may be mounted into a pipeline installed horizontally,
vertically, or obliquely; special filters or dirt traps are not needed
- To prevent air collection at the mounting location, the flowmeter should
not be placed at the upper point of the pipeline or in the open-ended
pipeline; the best place to mount the flowmeter (if applicable) is the
lower or the uprising pipeline run (see Fig.1)
- Liquid pressure in the pipeline must not be of values that may facilitate
gas release
- The flowmeter should be mounted in the part of a pipeline where liquid
turbulence and pulsations are minimal.
Fig.1. Recommended MFT locations
- Straight pipe runs with nominal diameter (DN) equal to nominal
diameter of the flowmeter and length of no less than specified in table 1
should be provided upstream and downstream the flowmeter. These
runs must not include devices or components that may disturb flow
structure
- When the flowmeter is operated, PFC inner channel should be fully filled
with liquid

6
- When mounting the flowmeter into the horizontal or oblique pipeline,
position the axis of the Electronic Block (BE) in the vertical plane going
through the pipeline axis. Maximum deflection is ±30 °
- Intensity of external magnetic field (commercial frequency) should not
exceed 400 A/m.
Table 1. Lengths of straight runs for various MFT design versions
Unidirectional flow
Bidirectional flow
upstream MFT
downstream MFT
upstream MFT
downstream MFT
5DN
3DN
5DN
5DN
3.2.2. Assembly-welded structure made of the supplied fittings of appropriate
size and design must be used to mount flanged or wafer type
flowmeters into the pipeline.
3.2.3. The fitting assembly for the assembly-welded structure includes:
- Flat welded flanges modified (for flanged and wafer type PFC)
- PFC dimension simulator of appropriate size and design
- Gaskets
- Fasteners (for flanged and wafer type PFCs).
The simulator overall mounting dimensions and DN correspond to
the dimensions (with the highest possible tolerances) of the flowmeter’s
PFC to be mounted with this fitting assembly. The simulator is installed
instead of the flowmeter when performing mounting or welding or
dispatching MFT for regular calibration or repair.
In addition, the set may include straight pipe runs of appropriate
length (DNs equal to DN of the flowmeter) and concentric adaptors to
provide connection from pipeline's greater DN1(DN2) to DN of the
flowmeter. DN/DN1(DN2) ratio –at customer's option.
View of assembly-welded structures for mounting flanged
flowmeters into the pipeline, and reference linear dimensions are given
in Appendices A and B.
Delivery package is agreed with the customer. Design
documentation package for the fittings is available at customer's option.
3.2.4. Components of the assembly-welded structure are welded together and
then welded to the pipeline where the flow meter will be installed in
compliance with local rules and regulations in force. It is important to
provide alignment of the whole unit and flatness/parallel alignment of
the flanges between which the Flow Sensor is being installed.
3.2.5. The procedure for manufacturing the assembly-welded structure for the
flanged or wafer type flowmeters is as follows:
a) Weld the flanges to the straight pipe runs (pipeline) considering that the
straight pipe run (pipeline) axis should be perpendicular to the flange
plain adjacent to PFC (see Fig.2).
b) If necessary, weld the adaptors to the opposite ends of the runs (see
Fig.3).

7
Fig.2 Fig.3
CAUTION! Overlaps and undercuts inside the channel are
unacceptable. After completing the work, remove burrs and scales from
the inside.
c) Assemble the whole structure using bolts (studs) to fix components.
Please make sure that the simulator is installed instead of PFC to
provide alignment between two welded units, flatness/parallel alignment
of the flanges, and to avoid damages to the flowmeter in the course of
welding the structure to the pipeline. Before assembling, make sure that
mounting gaskets included in the set of fittings are installed.
3.2.6. Mounting fittings into the pipeline
3.2.6.1. Before mounting and where the set of fittings is to be installed, fix the
pipes that may tip out of their axes after cutting the pipeline to stationary
supports by clamps. Drain liquid from the pipeline, cut it and mount the
set of fittings considering the following conditions:
- Longer straight pipe run should be installed upstream
- M5 threaded holes on the cylindrical surface of the flanges used to
connect wires to BE case should be in a position allowing easy
connection of the wires.
3.2.6.2. After welding, the weld joints must be stress relieved by means of heat
treatment.
3.2.6.3. After completion of work, check weld joints and mating faces for
leakages according to the norms specified for pipelines of the
corresponding type. To do this, loosen the clamps fastening pipes to the
supports and put the pipeline into operation. Re-weld bad joints and
replace gaskets, if necessary.
Wash the system before the simulator is replaced by PFC.
The set of fittings should not be subjected to stresses and strains
from the pipeline (bending, compression, tension, twisting caused by
disbalance, misalignment or torque nonuniformity). To prevent this,
leave the supports of the inlet and outlet ducts and tighten the fastening
clamps.
3.2.6.4. Position the flowmeter so that the BE axis stand is arranged in vertical
plane with maximum deflection of ± 30 °. The arrow on PFC shall point
in the flow direction.
NOTE. For the flowmeter measuring bidirectional flow parameters,
the arrow shall match the forward (positive) or prevailing direction of the
flow.
Non-flanged flowmeters with protection rings are automatically centered
relative to companion flanges of the pipeline because the outer
diameter of the external rings matches the diameter of flange grooves.

8
When mounting the flowmeter, put new gaskets provided in the delivery
package into the companion flanges.
When mounting flanged type flowmeters into the pipeline, bolt
PFC/pipeline mating flanges from the side of the pipeline flanges.
Length of the bolts must provide the minimal distance of 3 mm from a
bolt end to the flowmeter’s assembly.
To move pipeline flanges apart when installing or removing the
flowmeter (Simulator), it is recommended to use special tool.
Alignment of the pipeline and PFC inner channel is provided when
the PFC flanges are aligned with the companion pipeline flanges.
When mounting the flowmeter into the pipeline, it is required to
install new rubberized asbestos fabric gaskets of appropriate thickness
or several gaskets of greater thickness.
When mounting flowmeters of corrosion-resistant type without the
protection rings into the pipeline, it is required to install new fluoroplastic
gaskets of appropriate thickness or several gaskets of greater
thickness.
CAUTION! Please make sure that the gaskets are aligned relative
to the PFC inner channel, i.e. a gasket must not even partly cover the
PFC inner channel. To provide alignment of gaskets, it is recommended
to fix the gaskets by adhesive.
The flowmeter is mounted into the pipeline when all construction,
welding and other works are finished.
3.2.6.5. When mounting PFC (Simulator) into the pipeline, tighten nuts in order
specified in Fig.4 by a torque indicating wrench with maximum torque
value that does not exceed the value specified in Table 2. Exceeding
of torque value may cause damage to PFC followed by leaking
liquid into the flowmeter.
To prevent disbalance and misalignment, it is recommended to
tighten nuts in several steps increasing torque step-by-step up to the
value specified in Table 2 while controlling alignment of the mating
flanges.
Table 2
DN, mm
10
15
20
25
32
40
50
65
80
100
150
200
300
Torque, N⋅m
15
15
15
20
25
35
35
40
50
60
80
100
150
Fig.4. Order of tightening flange nuts.

9
The flowmeter mounted in the pipeline SHOULD NOT be rotated
around the pipeline axis.
3.2.7. Mounting the flowmeter with threaded coupling
3.2.7.1. Select the flowmeter’s pipeline mounting location observing the rules
specified in Table 1. Cut the pipeline drained of liquid following the
instructions given in section 3.2.6.
3.2.7.2. Unscrew grooved nuts and dismount nipple joints which are the parts of
PFC.
3.2.7.3. Make sure that the simulator is installed into the assembly-welded
structure instead of PFC, this is necessary to provide alignment
between two welded units and to avoid damages to the flowmeter
during welding the structure to the pipeline.
Weld conical nozzles to the pipeline butt-to-butt in the same way as
to weld the adaptor pipes for the wafer type flowmeters, so that the
nozzle axis is perpendicular to the grooved nut plane. Welding works
shall be conducted in accordance with the requirements given in section
3.2.6.
CAUTION! When replacing the simulator by the flowmeter after
welding, it is recommended to use a compensator to ensure that the
threaded couplings are moved apart by the distance of no less than
10 mm. The compensator may be as follows:
- KRK manufactured by JSC "ArmaTreid"
-ARN/HYDRA by Danfoss
-Compensators from "WILLBRANDT" (authorized distributor is
"KREOLAIN" company), or similar.
The compensator shall be mounted into the pipeline following the
instructions outlined in the corresponding operational (maintenance)
documentation and considering the requirements given in Table 1.
3.2.7.4. Replace the simulator with the flowmeter. The whole structure is
assembled by firm tightening of grooved nuts. When assembling the
structure, it is required to install gaskets made of edible material and
supplied with the flowmeter, between the nozzles and grooved nuts.
3.3. Mounting the secondary converter of the flowmeter
remote version
3.3.1. The place of installation is selected from the condition of convenience of
work with the secondary Converter. Installation dimensions are
specified in the operating manual. When selecting the SC location, the
length of the flowmeter and SC communication cables must be taken
into account.
3.3.2. Do not install SC:
- In places where the ambient temperature can go beyond 5 to 50°C, and
the humidity can be above 80 %, at a temperature below 35°C
- Near heat sources such as hot pipes. Lighting SC is optional, its display
has its own backlight.
3.3.3. Using screws with a diameter of 5 mm bracket (Fig.C.1) installed on the
wall. Detachable coupling (Fig.C.3) one end is fixed to the rack of the
secondary Converter. The free end of the clutch is put on the bracket

10
protrusion as shown in Fig.C.4, after which the top plate is secured with
screws.
3.4. Wiring the Flowmeter
3.4.1. Power and communication cables are connected to the flowmeter after it
is installed into the pipeline.
Prior to connection, cut isolation from cable ends by 5 mm and after
that, connect them to the terminals on the switching module. Multicore
cables must be tinned.
3.4.2. For the flow meter in a combined version, the power and communication
cables are connected to the electronics block. Opening of back cover
BE to make by means of a key for oil filters "UNIOR" № 205. Skip the
power cable through one cable gland, interface cable –through the
other cable gland. Cables are connected to the connectors on the
switching module in accordance with the input and output diagrams
given in the operation manual. To ease wiring, the sticker designating
the switching module connection elements is put on the flowmeter's rear
cover.
3.4.3. The secondary converter flowmeter in the remote version comes with
mounted cables PFC-SC. Therefore, the connection of the free ends of
these cables is performed only to the PFC. For this opening of back
cover of the PFC communication block. Skip the cables through cable
glands. Cables are connected to the connectors on the switching
module (see Fig.D.1).
The maximum cable length is 10 meters. Connection of power and
communication cables to the electronics block is performed in the same
way as for the flow meter in a combined version (п.3.4.2).
3.4.4. As a 24 V power cable you must use twin core round conductor. The
power cable should be up to 150 m long for the core cross section of
1.5 mm2and up to 250 m for the core cross section of 2.5 mm2. For the
less core cross section, cable length is reduced proportionally.
Any twin/four core round cable up to 300 m long may be used as a
communication cable for the universal outputs. Twin core shielded
cable up to 1200 m long is used as a serial interface communication
cable.
A cable for the analogue output is selected considering load rating
of the output as well as the parameters of an input connected to receive
the analogue signal.
When several interfaces are used simultaneously, e.g. both
universal outputs of the flowmeter, analogue output (or an external
button), six core cable may be used.
Cable core cross section shall be within 0.2 mm2to 2.5 mm2 range.
3.4.5. The power and communication cables used must comply with the
operating conditions of the flow meter
CAUTION! To ensure the declared level of protection IP67, it is
necessary to execute following operations:
- The sealing ring of the case of the BE should be pure and intact at its
installation on the block case

11
- The cover BE should be reliably tightened
- Power and communication cables external diameter shall be from 5 to
8.8 mm
- The cable glands should be reliably tightened.
3.4.6. The power and communication cables are fixed on the wall wherever
possible. To avoid mechanical damages, it is recommended to place
them in a metal tube or sleeve. The signal (communication) and power
cables may be placed in one tube (sleeve).
DO NOT fix cables to the heated pipeline.
3.4.7. To provide electrical connection, it is necessary to connect the pipeline
sections cut in the wafer type MFT mounting location by wires (jumpers)
via a terminal located on the BE; wires should be of 4 mm2cross
section as a minimum (see Appendix A). If the pipeline has cathode
protection, cross section of the jumpers shall correspond to the value of
cathode protection current. Use the M5 threaded holes on cylindrical
surface of the flanges to connect the jumpers.
When mounting flanged type flowmeters, it is necessary to connect
the PFC flanges and the mating pipeline flanges by wires with cross
section of no less than 4 mm to ensure appropriate electrical connection
(see Appendix B).
When mounting flowmeters with the threaded coupling, connection
of the wires is not required as the electrical connection of the cut
pipeline parts is ensured by the flowmeter’s components.
3.4.8. The need for protective grounding is determined by power supply and
environment conditions under which the flow meter is operated.
To prevent failures of the flow meter, the grounding terminal must
not be connected to the lightning protection system.
As a grounding wire, you must use a mechanically protected
copper wire of 2.5 mm2cross-section as a minimum or a copper wire
without mechanical protection of 4 mm2cross section as a minimum.
The grounding conductor is connected to the fixing screw on the
electronic block.
CAUTION! If the pipeline is equipped with cathode protection,
do not ground the flowmeter.
3.4.9. After completing the wiring of the flow meter, install in place the back
cover of the electronics block, and for the flow meter in the remote
version –the cover of the switching block.
4. DISMOUNTING
4.1. The order of dismounting the flowmeter before dispatching for regular
calibration or repair is as follows:
- Turn off power, then disconnect network and signal cables from the
flowmeter
- Disconnect wires (connecting jumpers, if any) from the pipeline flanges
- Cut off liquid at the PFC location, make sure that pressure is released
and drain the liquid
- Remove PFC

12
- Immediately after PFC is dismounted from the pipeline, install the
clamping plates with the tightening stud (bolt) on PFC covered by
fluoroplastic with the protection rings removed
- Install the simulator in the pipeline instead of PFC.
4.2. On installing the simulator, check mating surfaces for leakage. Replace
gaskets, if necessary. In case that no leakages are found, put the
pipeline into operation.
4.3. Clear the PFC inner channel from sediment and liquid residues before
packing.
5. PUTTING INTO OPERATION
5.1. When putting the flowmeter into operation check the following:
- The flow is in the direction of the arrow located on the flowmeter's body
- Length of the inlet and outlet straight pipe runs corresponds to flow
direction
- The flowmeter and related equipment are connected in accordance with
the selected wiring diagram
- The outputs operate in the preset modes
- Power supply voltage corresponds to the specifications.
5.2. At first power-up or after a long break in operation, the flowmeter is
operational after:
- All hydraulic processes in the pipeline related to changes of flow rate
(draining, filling, flow adjustment etc.) are fully terminated
- PFC is washed by medium for 30 minutes
- The flowmeter is kept powered for 30 minutes.
5.3. To protect the device from unauthorized access during operation, the
cover of BE case may be sealed with hanging seals.
If a bypass is installed, it is necessary to seal its gates in closed
position.

13
APPENDIX A. Mounting wafer type Flowmeters into the
pipeline
13
23 124 5
L*
2L*L*
1
L*
3
L*
4
Flow direction
DN1
DN2
DN
1 –taper adaptor; 2 –adaptor pipe; 3 –mating flange; 4 –MFT (PFC
dimension simulator); 5 –wires (electrical jumpers) connecting the
flowmeter’s case and pipeline
Fig.A.1. Assembly-welded structure for mounting the wafer type flowmeters
DN10, DN15 into the pipeline
Table A.1. Dimensions of the assembly-welded structure for mounting the
wafer type flowmeters (mm)
DN
DN1/ DN2
L*
L1*
L2*
L3*
L4*
Notes
10
20
83
78
78
239
299
25
359
**
32
329
40
359
**
50
389
**
65
439
**
15
20
83
103
78
264
324
25
384
**
32
354
40
384
**
50
414
**
65
464
**
* - reference dimensions without processing tolerances
** - adaptor is made from two concentric adaptors

14
Flat weld flanges (for 2.5 MPa pressure) are used to mount the
MFT into the pipeline:
- For DN10, DN15 –flanges of design type B (with a fixing ridge)
- For DN20-DN150 –flanges of design type F (with a notch)
Modification of flanges is needed before welding which means
drilling a threaded hole M5 on the flange cylindrical surface to fix wires
(Fig.A.2).
DN, mm
D6, mm
h2, mm
db, mm
Workpiece
10
35 Н12
2,5±0,2
10
Flange 20-25-01-1-B St25
15
40 Н12
2,5±0,2
15
Flange 20-25-01-1-B St25
1 –revision to F;
2 –threaded hole М5
Fig.A.2. Modifications made for flanges for mounting MFT's of wafer type
When welding flanges shown in Fig.A.2 to the pipeline, adaptor
pipes shall be used (see Fig.A.3). The length of the adaptor pipes
should be no less than the length of the straight pipeline run (see
Table 1 of this manual).
After welding the flange to the adaptor pipe, process the surface
adjacent to the flowmeter as shown in Fig.A.4. The adaptors and
pipeline sections are welded butt-to-butt.

15
Fig.A.3. Adaptor pipes
Table A.3. Adaptor pipeline dimensions
DN, mm
d1, mm
d2, mm
d3, mm
c, mm
L, mm
L1, mm
10
11.6
26
17
0,5+0,5
75
40
15
15
26
21
100
65
Fig.A.4. Welding flanges to adaptor pipes

16
APPENDIX B. Mounting Flowmeters of flanged type into
the pipeline
132 5 234
L*
2
L*
3
L*
4
1
L* L *
1
4
75
6
Flow direction
DN1
DN2
DN
1 –taper adaptor; 2 –straight pipe run; 3 –rubberized asbestos fabric
gaskets; 4 –mating pipeline flange; 5 –PFC flange; 6 –MFT (PFC dimension
simulator) 7- wires connecting flowmeter’s flanges to the pipeline
Fig.B.1. Assembly-welded structure for mounting flanged flowmeters into
the pipeline
Table B.1. Dimensions of assembly-welded structure for flanged MFT,s (mm)
DN
DN1/
DN2
L*
L1*
L2*
L3*
L4*
Notes
with
protect.
rings
without
protect.
rings
with
protect.
rings
without
protect.
rings
with
protect.
rings
without
protect.
rings
1
2
3
4
5
6
7
8
9
10
11
20
25
150
142
124
84
362
354
422
414
32
422
414
40
422
414
50
452
444
65
592
584
**
80
602
594
**
25
32
200
192
149
99
452
444
512
504
40
512
504
50
542
534
65
682
674
**
80
692
684
**
100
702
684
**

17
Cont. of Table B.1
1
2
3
4
5
6
7
8
9
10
11
32
40
200
192
184
119
507
499
567
559
50
597
589
65
617
609
80
747
739
**
100
757
749
**
40
50
200
192
229
149
582
574
702
694
65
722
714
80
732
724
100
862
854
**
125
902
894
**
150
846
838
**
50
65
200
192
285
185
674
666
814
806
80
824
816
100
834
826
125
874
866
150
824
816
65
80
200
192
360
230
794
786
944
936
100
954
946
125
994
986
150
944
936
200
984
976
80
100
200
192
435
275
916
908
1074
1066
125
1114
1106
150
1174
1166
200
1104
1096
250
1354
1346
**
300
1324
1316
**
350
1614
1606
**
100
125
250
242
535
335
1124
1116
1324
1316
150
1384
1376
200
1314
1306
250
1404
1396
300
1404
1396
350
1824
1816
**
400
1824
1816
**
150
200
270
262
795
495
1564
1556
1844
1836
250
1924
1916
300
1844
1836
350
2004
1996
400
2004
1996
**
500
2604
2596
**
200
250
342
324
1050
650
2042
2028
2420
2406
300
2420
2406
350
2500
2486
400
2500
2486
500
3100
3086
**
300
350
503
485
1565
965
3033
3015
3491
3473
400
3491
3473
500
4091
4073
**

18
* - reference dimensions without processing tolerances
** - adaptor is made from two concentric adaptors
Flat welded (slip-on) flanges supplied with the set of fittings should
be modified as follows: a threaded M5 hole is drilled for fixing a wire on
the cylindrical surface of a flange.

19
APPENDIX C. Mounting Secondary converter
Fig.C1. Wall bracket.
Fig.C2. Top plate
Fig.C3. Detachable coupling

20
Fig.C4. The secondary converter is mounted on the bracket
Table of contents
Other AFLOWT Measuring Instrument manuals
Popular Measuring Instrument manuals by other brands
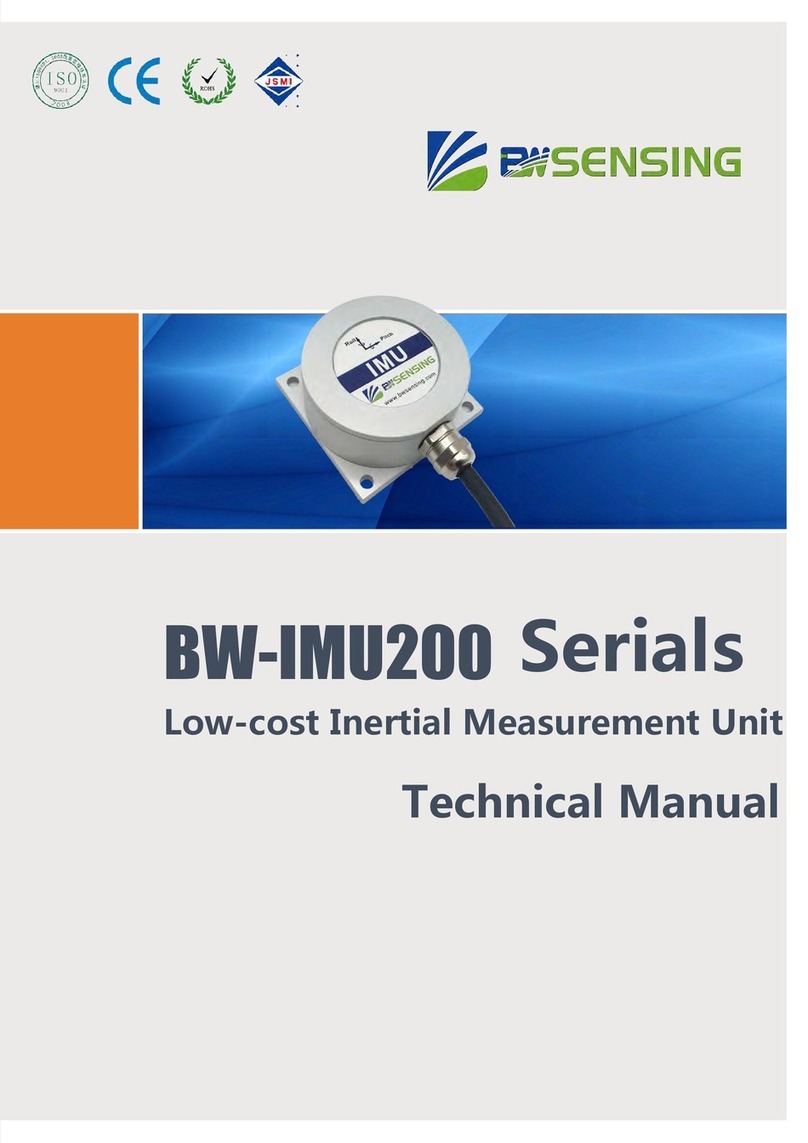
BW SENSING
BW SENSING BW-IMU200 Series Technical manual
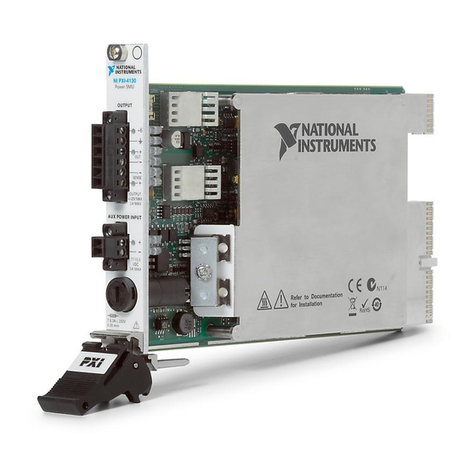
National Instruments
National Instruments PXI-4130 CALIBRATION PROCEDURE
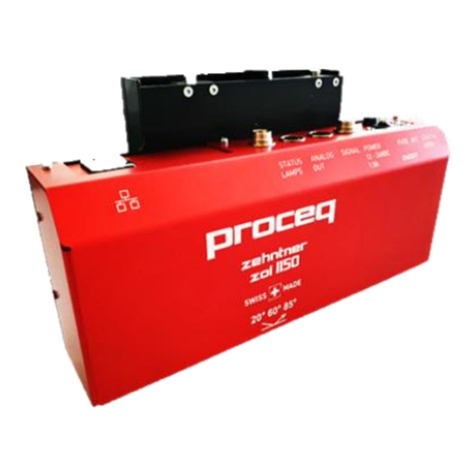
Proceq
Proceq ZOL1150 quick start guide
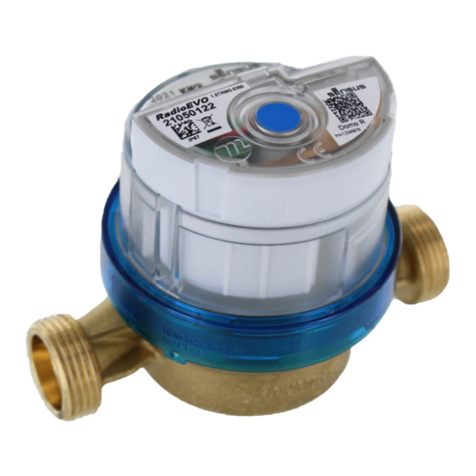
Xylem
Xylem sunsus Domo R Quick installation guide
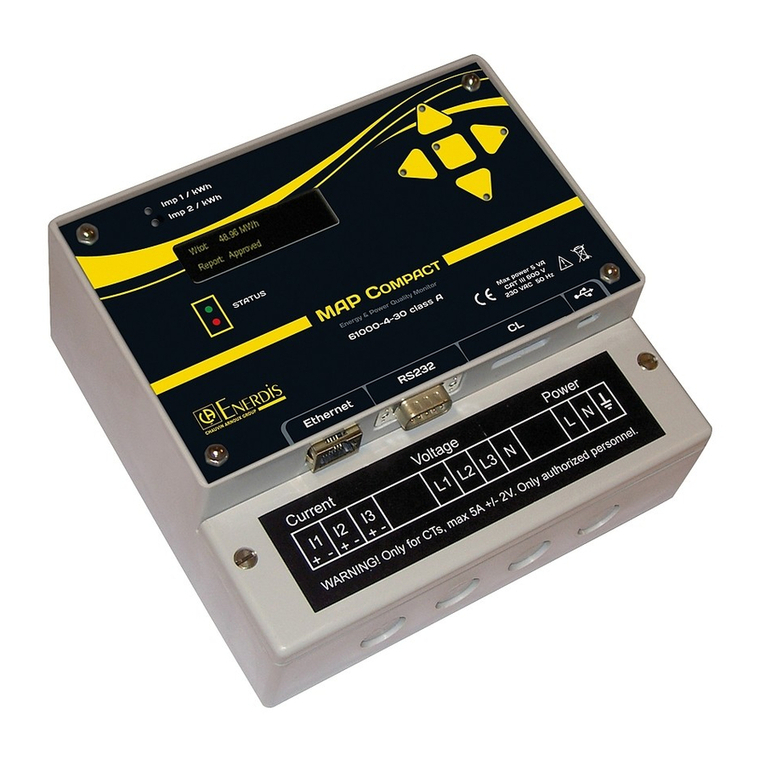
Chauvin Arnoux
Chauvin Arnoux MAP COMPACT Installation and operating manual
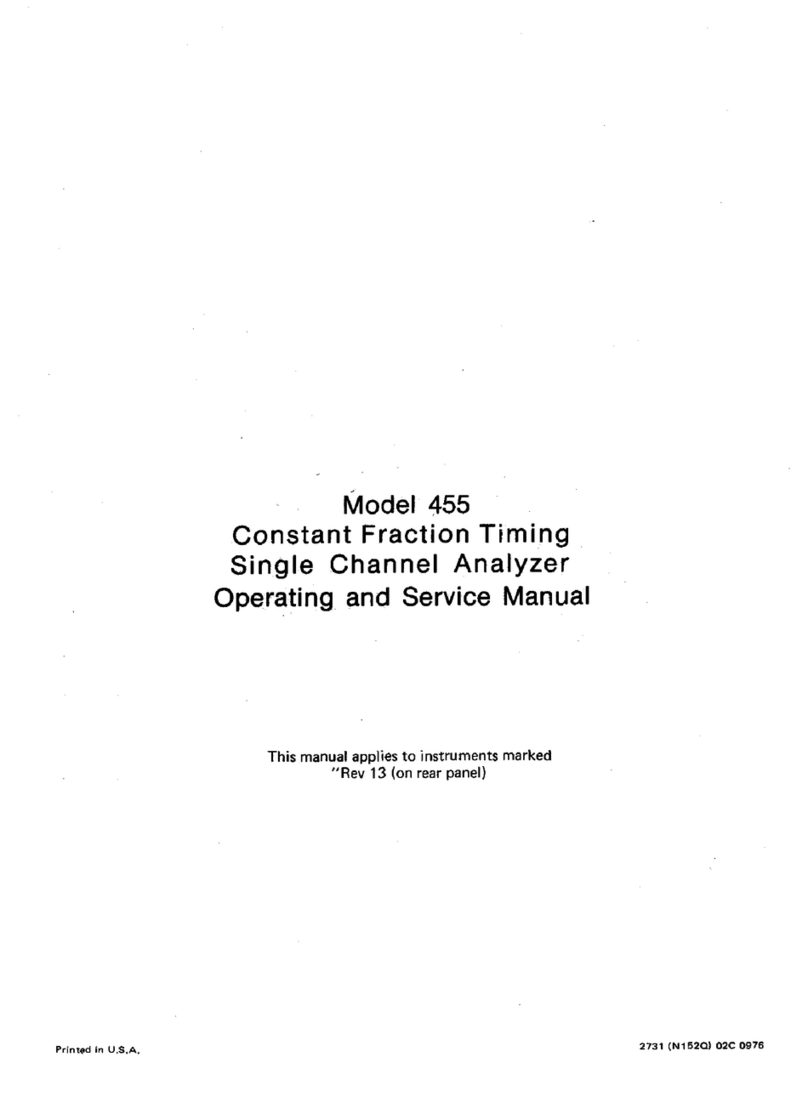
ORTEC
ORTEC 455 Service manual

ASCEL Electronic
ASCEL Electronic AE20204 Assembly and operation manual
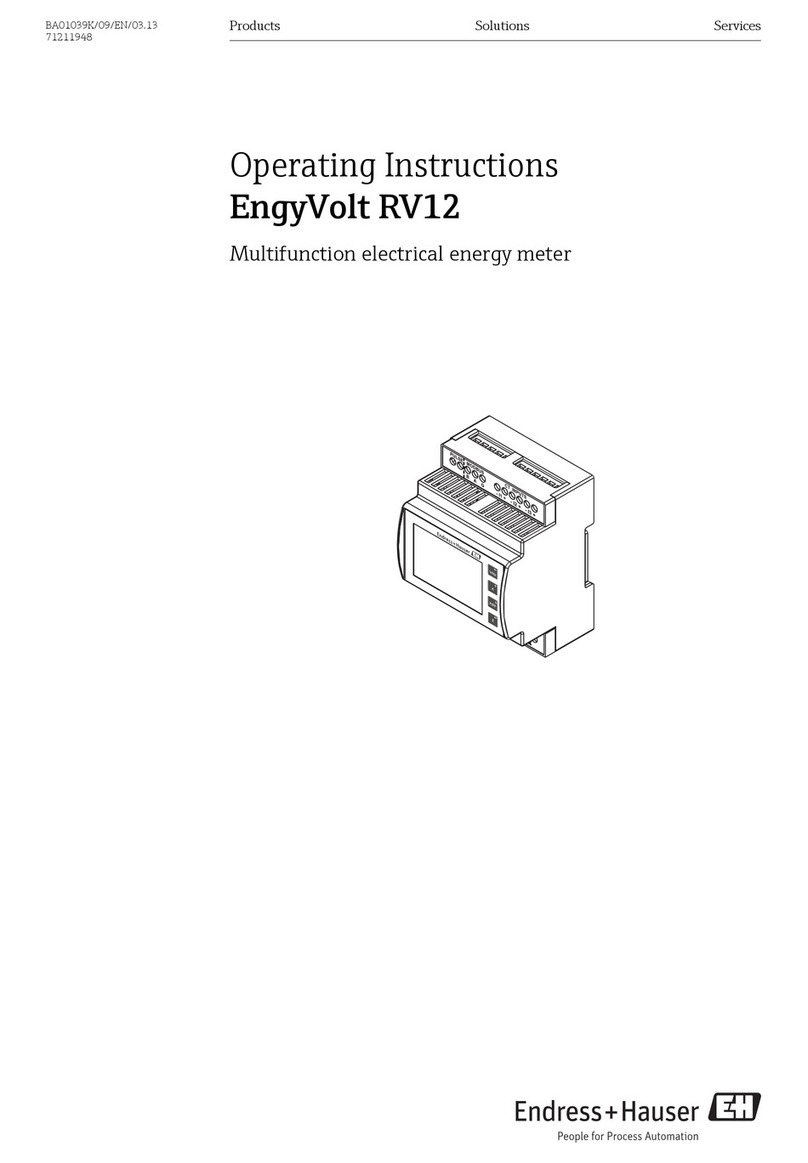
Endress+Hauser
Endress+Hauser EngyVolt RV12 operating instructions

Bosch
Bosch GAM 220 Professional Original instructions

Amprobe
Amprobe LM-200LED user manual
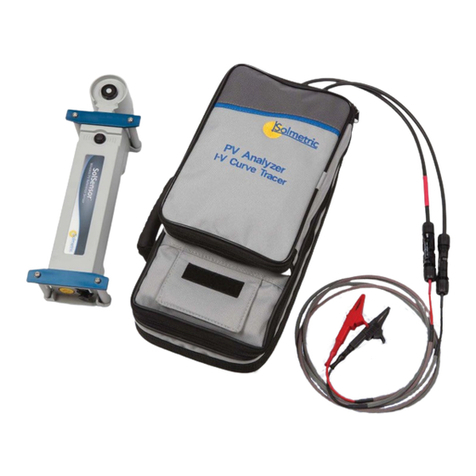
Solmetric
Solmetric PVA-1500T user guide
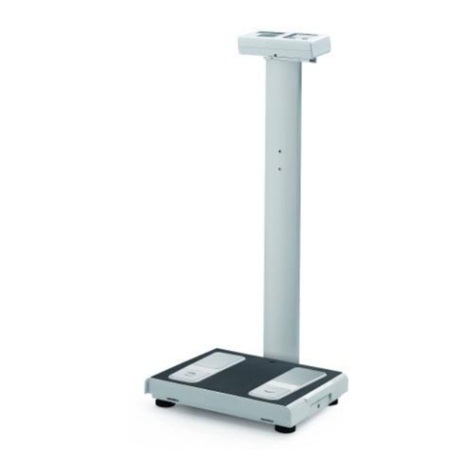
CHARDER MEDICAL
CHARDER MEDICAL MBF6000 user manual