Aliaxis FIP PVDF User manual

PIPES, FITTINGS
AND MANUAL VALVES
PVDF
The PVDF line consists of a comprehensive range of pipes,
fittings and manual valves for use in the construction of process
and service lines for conveying pressurised industrial fluids
in a temperature range from -40° C to 140° C.

PVDF
General characteristics
Reference standards
Approvals and quality marks
Main properties
Socket welding instructions
page 2
page 4
page 5
page 6
page 7
ISO-UNI pipe
Pressure pipe page 12
Fittings for socket welding
Fittings, metric series ISO-UNI
ISO-BSP adaptor fittings
page 20
page 34
VKD DN 10÷50
DUAL BLOCK® 2-way ball valve page 42
VKD DN 65÷100
DUAL BLOCK® 2-way ball valve page 56
VKR DN 10÷50
DUAL BLOCK® regulating ball valve page 70
SR DN 15÷50
Ball check valve page 82
FK DN 40÷400
Butterfly valve page 90
DK DN 15÷65
DIALOCK® 2-way diaphragm valve page 110
VM DN 80÷100
Diaphragm valve page 124
CM DN 12÷15
Compact diaphragm valve page 134
Key abbreviations page 141
PIPE, FITTINGS
AND MANUAL
VALVES
IN PVDF
CONTENTS

PVDF
PVDF (polyvinylidene
difluoride) is a
fluorinated and semi-
crystalline techno-
polymer containing
59% of its weight in
fluorine. This material
is obtained through
the polymerization
of vinylidene fluoride.
It boasts exceptional
mechanical,
physical and
chemical resistance,
guaranteeing
excellent thermal
stability up to 140° C.
The FIP PVDF line uses Solef® PVDF resins, manufactured by SOLVAY for
industrial applications, for the production of pipes, fittings and valves made
by extrusion and injection moulding. The entire line is made using Solef®
resins by SOLVAY S.A. classified according to ASTM D 3222 and complying
with the requirements of ISO 10931.
Thanks to its high purity and exceptional performance, PVDF is the best
alternative to metal materials, and is extensively used in industrial appli-
cations (chemical, oil, pharmaceutical, pulp and paper, electronic, etc.),
whether in process systems or otherwise.
Among the most important properties and advantages of Solef® PVDF, the
following are particularly worthy of note:
• Excellent chemical resistance:
the use of Solef® resin, a vinylidene fluoride polymer, ensures excellent
resistance to corrosion and abrasion when conveying highly aggressive
chemicals. PVDF is basically inert to most inorganic acids and bases, or-
ganic acids, aromatic and aliphatic hydrocarbons, alcohols and halogenat-
ed solvents. However, it is not recommended for use with fluorine, amines,
ketones and oleum (sulfuric acid with sulfur trioxide).
• Excellent thermal stability:
PVDF maintains its characteristics unchanged in a temperature range
between -40° C and +140° C. PVDF pipes are particularly suitable in all
applications requiring high operating temperatures, very low levels of fluid
contamination and high resistance to ageing due to atmospheric agents
and UV radiation. The material's excellent mechanical properties are re-
tained even at high temperatures.
• Fire resistance:
Solef® resins guarantee excellent fire resistance without the need for flame
retardants (Limit Oxygen Index, LOI = 44%). In case of combustion, smoke
emissions are moderated. Solef® PVDF resins are classified UL-94, class
V-O.
• Purity:
Solef® PVDF resin is an extremely pure polymer that does not contain
stabilizers, plasticizers, lubricants or flame retardants. As a result, it is the
ideal material for conveying ultra-pure water and chemicals, ensuring the
non-contamination of the conveyed fluid. As it is physiologically non-toxic,
it is suitable for conveying fluids and food products.
• High abrasion resistance:
according to the Taber Abrasion Test (in which the weight loss of a
material is measured after being exposed to an abrasive wheel for 1000
cycles), PVDF is the most resistant thermoplastic material (CS-10 Load 1kg
- Weight Loss / 1000 cycles = 5-10 mg.)
GENERAL CHARACTERISTICS
2

Density
Test method ISO 1183
Unit of measurement
g/cm3
Value Valves/fittings: 1.78 - Pipes: 1.78
Fluidity index (MFI 230° C, 5 kg)
Test method ISO 1133 ASTM D1238
Unit of measurement
g/(10 min) g/(10 min)
Value Valves/fittings: 6 - Pipes: 6 Valves/fittings: 24 - Pipes: 24
Modulus of elasticity
Test method ISO 527 ASTM D790
Unit of measurement
MPa = N/mm2MPa = N/mm2
Value
Valves/fittings: 2100 - Pipes: 2100 Valves/fittings: 2200 - Pipes: 2100
IZOD notched impact strength at 23°C
Test method ASTM D256
Unit of measurement
J/m
Value Valves/fittings: 55 - Pipes: 110
Ultimate elongation
Test method ISO 527-2 ASTM D 638
Unit of measurement
% %
Value Valves/fittings: 80 - Pipes: 80
Valves/fittings: 5-10 - Pipes: 20-50
Rockwell hardness
Test method ASTM D 785
Unit of measurement
R
Value Valves/fittings: 110 - Pipes: 110
Tensile strength
Test method ISO 527 ASTM D 638
Unit of measurement
MPa = N/mm2MPa = N/mm2
Value Valves/fittings: 50 - Pipes: 50
Valves/fittings: 53-57 - Pipes: 53-57
Heat distortion temperature HDT (0.46 N/mm2)
Test method ISO 75 ASTM D 648
Unit of measurement
°C °C
Value
Valves/fittings: 145 - Pipes: 145
Valves/fittings: 148 - Pipes: 147
Thermal conductivity at 23° C
Test method DIN 52612-1 ASTM C 177
Unit of measurement
W/(m °C) W/(m °C)
Value
Valves/fittings: 0.20 - Pipes: 0.20
Valves/fittings: 0.20 - Pipes: 0.20
Coecient of linear thermal expansion
Test method DIN 53752 ASTM D 696
Unit of measurement
m/(m °C) m/(m °C)
Value Valves/fittings: 12x10-5
Pipes: 12x10-5
Valves/fittings: 12x10-5
Pipes: 12x10-5
Limiting Oxygen Index
Test method ISO 4859-1 ASTM D 2863
Unit of measurement
% %
Value Valves/fittings: 44 - Pipes: 44 Valves/fittings: 44 - Pipes: 44
Surface electrical resistivity
Test method ASTM D257
Unit of measurement
ohm
Value Valves/fittings: >1014 - Pipes: >1014
Flammability
Test method UL94
Value V-0
3

REFERENCE
Production of the
PVDF Solef® lines is
carried out according
to the highest quality
standards and in
full compliance with
the environmental
restrictions set
by the applicable
laws in force and in
accordance with
ISO 14001.
All products are
made in accordance
with the quality
guarantee system in
compliance with ISO
9001.
• ANSI B16.5
Pipe flanges and stubs - NPS 1/2 to NPS 24 mm/inch.
• ASTM D3222
PVDF, material for extrusion moulding and coating.
• DIN 2501
Flanges, dimensions
• DIN 16962
PVDF fittings for socket and butt welding, dimensions.
• DIN 16963
Pipe joints and pipe components for pressurised fluids in HDPE.
• DVS 2202-1
Imperfections of PVDF welded joints, characteristics, descriptions and
evaluations.
• DVS 2207-15
Welding of components in PVDF.
• DVS 2208-1
Machinery and equipment for thermocouple welding.
• EN 558-1
Industrial valves - Overall dimensions of metal valves for use in flanged
pipe systems - Part 1: PN designated valves.
• EN 1092-1
Flanges and their joints - Circular flanges for pipes, valves and accessories
- Part 1: Steel flanges, PN designated.
• EN ISO 10931
Specifications for components (Pipes, Fittings and Valves) in PVDF for
industrial applications.
• ISO 5211
Part-turn actuator couplings.
• ISO 7005-1
Metal flanges; part 1: steel flanges.
STANDARDS
4

APPROVALS AND
• DVGW KTW, W270
Suitability of the SOLVAY PVDF Solef® resin for microbiological tests.
• FDA (Food and Drug Administration - USA)
Suitability of the SOLVAY PVDF Solef® resin for contact with food.
• NSF (National Sanitation Foundation USA)
Suitability of the SOLVAY PVDF Solef® resin for use in contact with drink-
ing water.
• DIBt
FIP PVDF Solef® valves have been tested and certified by DIBt (Deutsches
Institut für Bautechnik)
• GOST-R - EAC
PVDF Solef® valves and fittings are GOST-R and EAC certified in accord-
ance with Russian regulations on Safety, Hygiene and Quality
• TA-Luft
FIP PVDF Solef® valves have been tested and certified according to “TA-
Luft” by MPA Stuttgart in compliance with the Technical Instruction on Air
Quality Control TA-Luft/ VDI 2440
• UKR SEPRO
PVDF Solef® valves and fittings are certified in accordance with Ukraine
regulations on Safety, Hygiene and Quality
• WRAS (Water regulations advisory scheme - UK)
Suitability of the SOLVAY PVDF Solef® resin for use in contact with drink-
ing water.
QUALITY MARKS
5

MAIN
PROPERTIES
Properties of PVDF Benefits
Thermal resistance - Operating range: - 40 + 140° C (see
pressure/temperature regression
curves)
Low surface roughness - High flow coecients (extremely
smooth internal walls)
Chemical resistance - Exceptional chemical resistance
for conveying corrosive fluids
(generally inert to inorganic acids
and bases, aromatic and aliphatic
hydrocarbons, organic acids,
alcohols and halogenated solvents)
Abrasion resistance - Extremely low operating costs due
to its long service life
Fully recyclable and non-
toxic
- Physiologically safe
Easy jointing (hot socket,
butt and electrofusion
welding, flanging and
threading)
- Low installation costs
Excellent mechanical
properties
- PVDF responds to the need to
provide suitable mechanical
resistance meeting the design
requirements of industrial plants
6

SOCKET WELDING
INSTRUCTIONS
Fig. 1
Hot socket welding involves fusing the pipe in the fitting's socket. The joint is made
by simultaneously fusing the male and female surfaces by means of special manual
or automatic heating devices. These devices, in their simplest form, are composed of
a heating plate on which a series of heating bushes are mounted. The devices comes
with an appropriate heating system complete with an automatic temperature con-
troller. No additional materials are required for this type of welding. Socket welding
does not affect the chemical resistance of the PVDF, nor does it influence the inner
pressure resistance of the assembled pipes and fittings. The pipe to be welded must
be cut, chamfered and peeled if necessary. The external surface of the pipe and the
internal surface of the fitting must be carefully cleaned, and the external surfaces of
the pipe and fitting can be marked with a reference notch to eliminate the risk of in-
advertent rotation while the joint is setting. The next step is to insert the pipe in the
female bush and the fitting in the male bush and hold them in position for the neces-
sary heating time; when this time has elapsed, the parts must be quickly removed
from the bushes and then the pipe inserted into the fitting to the full previously de-
termined insertion length, ensuring the reference notches are correctly aligned. The
two elements must be supported for approximately 15 seconds after initial insertion
and then left to cool at ambient temperature without using forced air flows or water
immersion.
Procedure for hot socket welding
The method described below is applicable only when creating thermal socket welds
that call for the use of manual type welding equipment (fig. 1). The use of automatic
and semi-automatic appliances, which are particularly suitable for diameters greater
than 63 mm, calls for a specific working knowledge of the welding tool. In this case,
adhere strictly to the tool manufacturer's instructions
1) Select the female bushes and the male bushes of the required diameters, insert
them and secure them to the heating plate (fig. 2).
2) Carefully clean the contact surfaces (fig. 3). When choosing the type of liquid
detergent, use recommended products supplied by specialist producers: trichlo-
roethane, chlorothene, ethyl alcohol and isopropyl alcohol are all suitable.
3) Set the temperature of the heating tool. To form the joint correctly, the tempera-
ture should be set between 250° C and 270° C.
4) When the appliance has reached the preset temperature, check the temperature
of the heating plate using a fast acting thermoprobe.
5) Cut the pipe at right angles, chamfer it and if necessary peel it out (fig. 4-5). The
peeling diameter and length and the chamfer depth must correspond to the val-
ues shown in the table named “Pipe peeling and chamfer dimensions”. The cham-
fering process can be performed either after peeling or concurrently with this
operation, using special calibrated tools.
Fig. 2
Fig. 3 Fig. 4 Fig. 5
7

6) Mark the pipe with the insertion length L1 (fig. 6), referring to the values indicat-
ed in the table named “Pipe insertion length” and checking that any peeling has
been machined to the entire length shown in the table.
7) Mark a longitudinal reference line on the outside of the pipe and the fitting to
prevent the two parts from rotating while the joint is being made (fig. 7).
8) Clean the fitting and pipe from any traces of oil or dust on the weld surfaces (fig. 8).
9) After having checked that the surface temperature of the heating plate has sta-
bilized at the required value, insert the pipe into the female bush and the fitting
in the male bush (fig. 9). Holding the parts inserted in the two bushes (fitting
inserted to limit stop, pipe inserted up to the end of the peeling length), wait for
the minimum heating time shown in the table named “Heating, welding and cool-
ing times”.
10) When the minimum heating time has elapsed, quickly remove the elements
from the bushes and fit the pipe into the fitting for the entire insertion length L1
marked previously (fig. 10). Do not turn the pipe in the fitting; ensure the longitu-
dinal reference marks are perfectly aligned (fig. 11).
11) Hold the jointed elements for the welding time shown in the table named
“Heating, welding and cooling times” and then leave them to cool slowly at
ambient temperature without using forced air flows or water immersion.
12) When the internal and external surfaces have cooled sufficiently, pressurize the
plant for the joint hydraulic test.
Fig. 6
Fig. 7
Fig. 8
Fig. 9 Fig. 10 Fig. 11
8

External diameter
de (mm)
Peeling length
L (mm)
Chamfer
Sm (mm)
16 13 2
20 14 2
25 16 2
32 18 2
40 20 2
50 23 2
63 27 3
75 31 3
90 35 3
110 41 3
External diameter
de (mm)
Length of insertion into the fitting's socket
L1 (mm)
16 12
20 14
25 15
32 17
40 18
50 20
63 26
75 29
90 32
110 35
PIPE PEELING AND CHAMFER DIMENSIONS
PIPE INSERTION LENGTH
HEATING, WELDING AND COOLING TIMES
de
(mm)
PVDF pipes according to: DVS 2207 Part 15
Minimum
thickness* (mm)
Heating
time (sec)
Welding
time (s)
Cooling
time (min)
16 1.5 4 4 2
20 1.9 6 4 2
25 1.9 8 4 2
32 2.4 10 4 4
40 2.4 12 4 4
50 3 18 4 4
63 3 20 6 6
75 3 22 6 6
90 3 25 6 6
110 3 30 6 8
* For proper welding, we recommend using pipes with
wall thickness exceeding 2 mm, and precisely:
- for d up to 50 mm: pipe series PN 10 and PN 16
- for d from 63 to 110 mm: pipe series PN
16, PN 10 and PN 6.
9


ISO-UNI PIPE
PVDF
Pressure pipe

12
Technical specifications
Size range d 16 ÷ d 110 (mm)
Nominal pressure SDR 21 (PN16) with water at 20° C
SDR 33 (PN10) with water at 20° C
Temperature range -40 °C ÷ 140 °C
Coupling standards Welding: EN ISO 10931.
Can be coupled to pipes according to EN ISO 10931
Reference standards Construction criteria: EN ISO 10931
Test methods and requirements: EN ISO 10931
Installation criteria: DVS 2201-1, DVS 2207-15,
DVS 2208-1
Material PVDF
PIPE
Pressure pipes for
connection system
by butt or socket
welding.
PRESSURE PIPE
ISO-UNI

13
TECHNICAL DATA
REGRESSION CURVES
FOR PIPES IN PVDF
Regression coecients according to
ISO 10931 for MRS (minimum) = 25
N/mm2 (MPa)
The information in this leaflet is provided in good faith. No liability will be accepted concerning technical data that is not directly covered by
recognised international standards. FIP reserves the right to carry out any modification. Products must be installed and maintained by qualified
personnel.
PRESSURE VARIATION
ACCORDING TO
TEMPERATURE
For water and non-hazardous fluids
for which the material is classified
as CHEMICALLY RESISTANT (life
expectancy 25 years). In other
cases, a reduction of the nominal
pressure PN is required.
-40 -20 0 20 40 60 80 100 120 140 °C
16
14
12
10
8
6
4
2
0
Working pressure
Working temperature
bar
Hoop stress
Time to failure
bar 0.1 1 10 102103104105106h
20
25
30
40
50
15
10
0.5
1
1.5
2
2.5
3
3.5
4
5
6
7
8
9
20 °C
10 °C
30 °C
40 °C
50 °C
70 °C
80 °C
90 °C
95 °C
100 °C
140 °C
130 °C
120 °C
110 °C
60 °C
1
510 25 50 100
Years
PN 16
PN 10

14
PRESSURE PIPE
Pressure pipe in PVDF according to ISO 10931, translucent white, standard length 5m
DIMENSIONS
d DN s (mm) kg/m PN16 Code
SDR 21 - S10
16 10 1.9 0.137 PIPEF13016
20 15 1.9 0.21 PIPEF13020
25 20 1.9 0.269 PIPEF13025
32 25 2.4 0.435 PIPEF13032
40 32 2.4 0.553 PIPEF13040
50 40 3 0.825 PIPEF13050
63 50 3 1.09 PIPEF13063
75 65 3.6 1.55 PIPEF13075
90 80 4.3 2.22 PIPEF13090
110 100 5.3 3.33 PIPEF13110
d DN s (mm) kg/m PN10 Code
SDR 33 - S16
63 50 2.5 0.93 PIPEF33063
75 65 2.5 1.11 PIPEF33075
90 80 2.8 1.48 PIPEF33090
110 100 3.4 2.20 PIPEF33110

*for pipe support systems, refer to guidelines DVS 2210-1 (Planning and execution - above-ground pipe systems)
**resale product
d a b C h I Code
**3/8” 26 13 - 34 16 ZAKM038
**1/2” 33 14 - 39 20 ZAKM012
**3/4” 41 14 - 45 25 ZAKM034
**1” 49 15 - 52 32 ZAKM100
**1” 1/4 58 16 - 61 40 ZAKM114
**1” 1/2 68 17 - 67 50 ZAKM112
**2” 83 18 - 80 63 ZAKM200
**2” 1/2 96 19 - 96 75 ZAKM212
**3” 118 20 - 110 90 ZAKM300
**4” 140 25 60 135 140 ZAKM400
**6” 197 30 90 196 180 ZAKM600
ZAKM
Pipe clip for ASTM pipes in PP*
d a b C h I Code
**16 26 18 - 33 16 ZIKM016
**20 33 14 - 38 20 ZIKM020
**25 41 14 - 44 25 ZIKM025
**32 49 15 - 51 32 ZIKM032
**40 58 16 - 60 40 ZIKM040
**50 68 17 - 71 60 ZIKM050
**63 83 18 - 84 63 ZIKM063
**75 96 19 - 97 75 ZIKM075
**90 113 20 - 113 90 ZIKM090
**110 139 23 40 134 125 ZIKM110
**125 158 25 60 151 140 ZIKM125
**140 177 27 70 167 155 ZIKM140
**160 210 30 90 190 180 ZIKM160
**180 237 33 100 211 200 ZIKM180
ZIKM
Pipe clip for ISO-DIN pipes in PP*
*for pipe support systems, refer to guidelines DVS 2210-1 (Planning and execution - above-ground pipe systems)
**resale product
15

*for pipe support systems, refer to guidelines DVS 2210-1 (Planning and execution - above-ground pipe systems)
**resale product
d A B C D E Pack Master Code
**32 33 16 14 8 4 20 120 DSM032
**40 41 17 17 8 4 10 80 DSM040
**50 51 18 17 8 4 10 50 DSM050
**63 64 19 22.5 8 4 10 40 DSM063
**75 76 20 34.5 8 4 10 40 DSM075
DSM
Spacers in PP for ZIKM pipe clips*
16

Supporting PVDF pipes conveying liquids of density 1 g/cm3(water and other fluids of
equal intensity).
Supporting PVDF pipes conveying liquids of density other than 1 g/cm3.
If the liquid being conveyed has a density other than 1 g/cm3, the distance L must be
multiplied by the factors in the table.
INSTALLATION
The installation of thermoplastic pipe systems requires the use of support clips to pre-
vent flexing and the resulting mechanical stresses.
The distance between the clips depends on the pipe material, SDR, surface temperature
and the density of the conveyed fluid.
Before installing the clips, check the distances reported in the table below, as provided
for by guidelines DVS 2210-01 for water pipes.
Fluid density in g/cm3Support factor
1.25 0.96
1.50 0.92
1.75 0.88
2.00 0.84
< 0.01
1.48 for SDR33 / S16 / PN10
1.36 for SDR21 / S16 / PN16
1.31 for SDR17 / S8 / PN20
POSITIONING OF ZIKM AND ZAKM PIPE CLIPS
For dierent SDR values, multiply the data in the table by the following factors:
1.08 for SDR21 / S10 / PN16 size range d63 - d400
1.12 for SDR17 / S8 / PN20 entire size range
For pipes of SDR 33 / S 16 / PN 10 and SDR 21 / S 10 / PN 16:
For pipes of SDR 33 / S 16 / PN 10:
d
mm
distance L in mm at dierent wall temperatures
< 20° C 30° C 40° C 50° C 60° C 70° C 80° C 100° C 120° C 140° C
16 725 700 650 600 575 550 500 450 400 300
20 850 800 750 750 700 650 600 500 450 400
25 950 900 850 800 750 700 675 600 500 450
32 1100 1050 1000 950 900 850 800 700 600 500
40 1200 1150 1100 1050 1000 950 900 750 650 550
50 1400 1350 1300 1200 1150 1100 1000 900 750 600
d
mm
distance L in mm at dierent wall temperatures
< 20° C 30° C 40° C 50° C 60° C 70° C 80° C 100° C 120° C 140° C
63 1400 1350 1300 1250 1200 1150 1100 950 800 650
75 1500 1450 1400 1350 1300 1250 1200 1050 850 700
90 1600 1550 1500 1450 1400 1350 1300 1100 950 850
110 1800 1750 1700 1650 1550 1500 1450 1250 1100 950
125 1900 1850 1800 1700 1650 1600 1500 1350 1200 1000
140 2000 1950 1900 1800 1750 1700 1600 1450 1250 1050
160 2150 2100 2050 1950 1850 1800 1700 1550 1350 1150
180 2300 2200 2150 2050 1950 1900 1800 1600 1400 1200
200 2400 2350 2250 2150 2100 2000 1900 1700 1500 1300
225 2550 2500 2400 2300 2200 2100 2000 1800 1600 1400
250 2650 2600 2500 2400 2300 2200 2100 1900 1700 1500
280 2850 2750 2650 2550 2450 2350 2250 2000 1800 1600
315 3000 2950 2850 2750 2600 2500 2400 2150 1900 1650
355 3200 3100 3000 2850 2750 2650 2500 2250 2000 1750
400 3400 3300 3200 3050 2950 2800 2650 2400 2100 1800
17

18

FITTINGS
FOR SOCKET WELDING
Fittings, metric series ISO-UNI
PVDF
Table of contents
Other Aliaxis Control Unit manuals
Popular Control Unit manuals by other brands

MG
MG R30NCIT1 instruction manual

National Instruments
National Instruments FP-CTR-500 operating instructions
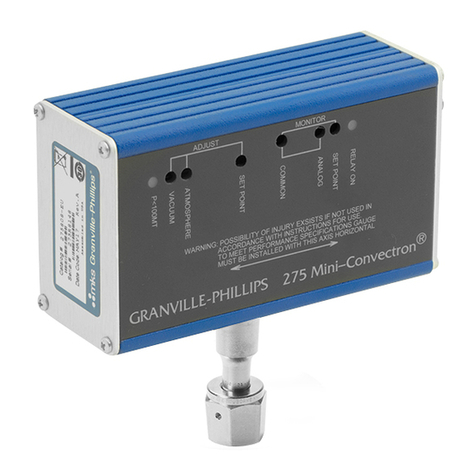
MKS
MKS Granville-Phillips Series 275 instruction manual
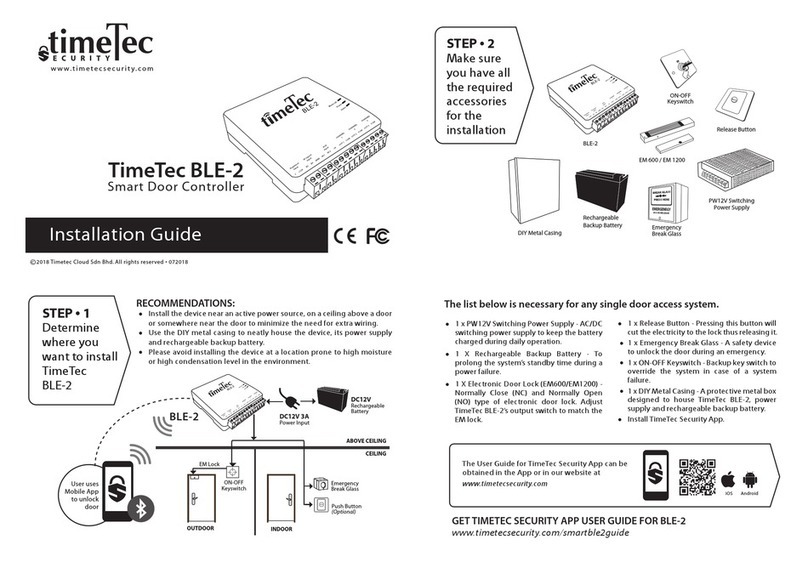
TimeTec Security
TimeTec Security TimeTec BLE-2 installation guide
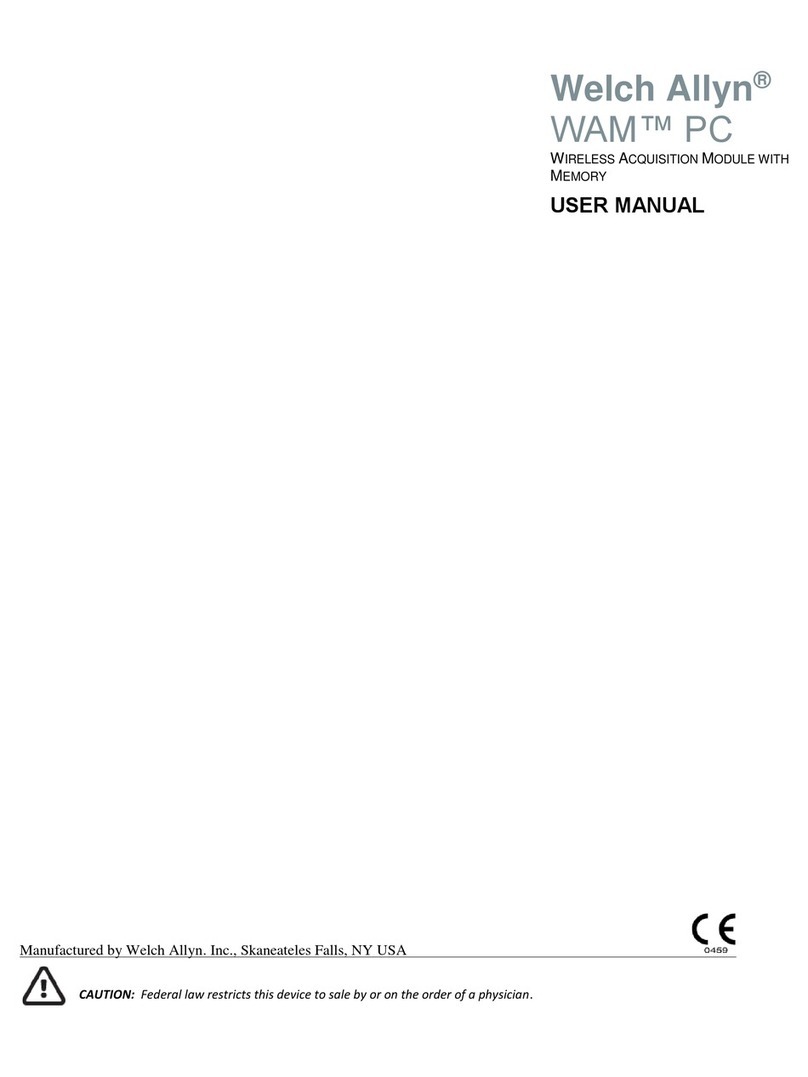
Welch Allyn
Welch Allyn WAM PC user manual

Panasonic
Panasonic SF-C21 instruction manual