Alicat Scientific EPCD Series User manual

Models EPCD · EPC

2
Thank you for purchasing your OEM pressure controllers.
Alicat Scientific
World Headquarters
M/s Halma India Pvt. Ltd.
C/O Avire India Pvt. Ltd.
Plot #A-147, Rd. #24
Wagale Ind. Estate, Thane
(West) 400604,
Maharashtra, India
+1 888-290-6060
info-cn@alicat.com
alicat.com.cn
2nd Floor, Block 63, No.
421, Hong Cao Rd,
Shanghai, PRC 200233
+86-21-60407398 ext.
801
europe@alicat.com
Geograaf 24
6921 EW Duiven
The Netherlands
+31 (0) 26 203.1651
This device comes with a NIST traceable calibration
certificate.
This device conforms to the European Union’s Restriction of
Use of Hazardous Substances in Electrical and Electronic
Equipment (RoHS) Directive 2011/65/EU.
This device complies with the requirements of the Low
Voltage Directive 2014/35/EU and the EMC Directive
2014/30/EU and carries the CE Marking accordingly.
This device complies with the requirements of the European
Union’s Waste Electrical & Electronic Equipment (WEEE)
Directive 2002/96/EC
Rev. 3 • 2020-08-24 • DOC-EPCMAN

4
Getting Started
Mounting
EPC and EPCD-Series controllers have mounting holes for convenient
mounting to flat panels. These controllers are position insensitive and can be
mounted in any orientation.
EPC
EPCD
Caution:
Minimize physical handling of the exposed circuit board of the EPC or
EPCD while installing. Hold the circuit board on its edges while installing, in order
to minimize contact with the exposed circuit board of the EPC or EPCD.

5
Plumbing
Process Ports
Your instrument is shipped with plastic plugs fitted in the port openings. To
lessen the chance of contaminating the flow stream do not remove these
plugs until you are ready to install the device.
Controllers with M5 (10-32) ports have O-ring face seals and require no sealant
or tape. Do not use tape with welded or O-ring fittings.
For non M5 (10-32) ports use thread sealing Teflon® tape to prevent leakage
around the port threads.
Do not wrap the first two threads. This will minimize the possibility of getting
tape into the flow stream and flow body.
!
Warning: Do not use pipe dopes or sealants on the process connections, as these
compounds can cause permanent damage to the controller should they get into the
flow stream.
When changing fittings, carefully clean any tape or debris from the port
connections.
Maximum Pressure
Both the valve and the sensor can be damaged from over-pressurization. The
valves on an EPC or EPCD are rated to 150 PSIG, unless custom-ordered. The
burst pressure of the pressure sensor is 3x the full scale, and permanent
damage will occur if this is exceeded.
Pressure Controller Operation
The response time of the system will depend on the size of the volume being
controlled, the operating conditions, and the PID tuning of the device. The
controllers are intended for use with clean, non-corrosive gases only.

6
EPC Single Valve Controller
Alicat Scientific EPC-Series Pressure Controllers incorporate a digital pressure
gauge with a single control valve and circuitry. The integrated control
algorithm measures the pressure, compares it with the setpoint, and adjusts
the valve accordingly at 1000 times per second.
The response time of the system will depend on the operating conditions and
the PID tuning of the device.
EPC-Series Pressure Controllers are normally intended to control the process
pressure downstream of the controller. In order for this to occur, a supply
pressure greater than the full scale pressure control range of the device
should be connected to the “IN” port.
EPC-Series Pressure Controllers can also be configured as back pressure
controllers, opening to release pressure upstream of the controller, and
closing to increase restriction and increase pressure upstream of the
controller. EPC Back Pressure controllers will have a “DS” in the part number.
EPCD Dual Valve Controller
Alicat Scientific EPCD-Series Closed Volume Pressure Controllers incorporate
a digital pressure gauge with dual control valves and circuitry. The integrated
PID loop measures the pressure, compares it with the setpoint, and adjusts
either the Inlet or Exhaust valve accordingly at 1000 times per second.
They are designed with a feed port, a process port, and an exhaust port. This
allows the controllers to raise and lower the pressure of a closed system
within the operating range of the controller without wasting gas under
constant pressure conditions.
Connect your EPCD into your process via the “OUT” port of the
unit. This is the “Process” port.
Connect a supply pressure greater than the full scale pressure
control range of the device to the “IN” port.
The “VENT” port can vent to atmosphere or be tied to a vacuum
source as the application demands.
✓
Note: The pressure at the vent port should be at atmospheric pressure or
below to allow the controller to be used over its full scale range.

7
Power and Signal Connections
Power and communications are supplied through the 6 pin Molex Micro-Fit
3.0 connector:
Pin
Function
1
Power in
2
0–5 Vdc
Optional: 1–5 Vdc or 0–10 Vdc output signal
3
Ground (common for power, digital
communications, and analog signals)
4
Serial RS-232TX output signal
Optional: RS-485 B
5
Serial RS-232RX input signal
Optional: RS-485 A
6
Analog setpoint input
Caution: Do not apply power to pins 2, 4, 5, or 6. Permanent damage can occur.
RS-232 or RS-485 Digital Signals
To use the RS-232 or RS-485 input signal, connect the RS-232 / RS-485 Output
Signal (Pin 4), the RS-232 / RS-485 Input Signal (Pin 5), and Ground (Pin 3) to
your computer serial port as shown below.
DB9 to MF6 Connection for RS-232 or RS-485 Signals
9-Pin Serial Connection
MF6 Connection
Pin
Function
Pin
Function
5
Ground
3
Ground
3
Transmit
5
Receive
2
Receive
4
Transmit

8
Analog Signals
Analog Output
Most devices include a primary analog output signal, which is linear over its
entire range. For ranges that start at 0 Vdc, a zero-pressure condition is
indicated at approximately 0.010 Vdc. Full scale pressure is indicated by the
top of the range: 5 Vdc for 0-5 Vdc, 10 Vdc for 0-10 Vdc, and so on.
Serial Communication
Establishing Serial Communication
After connecting your flow controller using a communications cable, you will
need to establish serial communications through a real or virtual COM port
on your computer or programmable logic computer (PLC).
•If you have connected your device to a serial port, note its COM port
number. This can be found in Windows® Device Manager.
•If you have a serial to USB adapter, plug it into your computer, ensure the
proper driver is installed, and note the COM port number.
The controller will be configured with the following settings:
•Baud: 19200 (default; others can be used if the computer, its software
and the controller are all set to the same rate)
•Data bits: 8
•Parity: none
•Stop bits: 1
•Flow control: none
Alicat devices use ASCII commands which are easily used in a serial terminal
or integrated into a PLC.
✓
Note: In what follows,
indicates an ASCII carriage return (decimal 13,
hexadecimal D). Serial commands are not case-sensitive.

9
Polling Mode
Controllers are shipped in polling mode with a unit ID of A, unless requested
otherwise. Each poll returns one line of data. To poll, simply enter its unit ID.
Poll the device: [unit ID]
Example: a(polls unit A)
You can change the unit ID of a polling device by typing:
Change the unit ID: [current unit ID]@=[desired unit ID]
Example: a@=b(changes unit A to unit B)
!
Warning: Care should be taken not to assign the same unit ID to more than one
device on a single COM port.
Streaming Mode
In streaming mode, your device continuously and automatically sends a line
of live data at regular intervals. Only one unit on a COM port may be in
streaming mode at a time.
✓
Note: RS-485 does not support streaming mode
To put your controller into streaming mode, type:
Begin streaming: [unit ID]@=@
Example: A@=@(Begins streaming unit A)
This is equivalent to changing the unit ID to “@”. To take the flow controller
out of streaming mode, assign it a unit ID by typing:
Stop streaming: @@=[desired unit ID]
Example: @@=a(stops and assigns unit ID of A)
When sending a command in streaming mode, the flow of data will not stop
while the user is typing. This may make the commands you type unreadable.
If the device does not receive a valid command, it will ignore it. If in doubt,
simply hit and start again.
The default streaming interval is 50 ms, but this can be increased by changing
Register 91 while the device is in polling mode:
Set streaming interval: [unit ID]w91=[time in milliseconds]
Example: aw91=500(streams data every 500 ms)

10
Taring
Taring pressure aligns the internal gauge pressure sensor with the current
barometric pressure, and must be done with the EPC/EPCD pressure sensor
open to atmosphere:
Tare gauge pressure: [unit ID]p
Example: ap
!
Warning:Do not send tare commands on absolute pressure EPC/EPCD
Collecting Pressure Data
Collect live data by typing the [unit ID]command or by setting your
controller to streaming. Each line of data for live measurements appears in
the format below, but Unit ID is not present in streaming mode.
The data frame on the screen represents the current measurements in the
device in the units shown on the display. By default, pressure controllers are
configured to output three columns of data.
A
+50.42
50.42
|
|
|
Unit ID
Pressure
Setpoint
Single spaces separate each parameter, and each value is displayed in the
chosen device engineering units. You can query the engineering units of the
serial data frame by typing:
Query live data info: [unit ID]??d*
Example: a??d*
(returns the data frame descriptions)
Additional columns, including status codes, may be present to the right of the
last column.

11
Commanding a New Setpoint
Before attempting to send setpoints to your flow controller serially, confirm
that its setpoint source is set to serial by checking register 20.
Read Register 20: [unit ID]r20
Example: ar20
For an EPC set to control forward pressure or an EPCD, if the value in register
20 is less than 16384, it’s already set up to receive setpoints serially. If not,
subtract 16384 to current value using the subtract command below.
For an EPC set to back pressure control, if the value in register 20 is less than
49152, it’s already set up to receive setpoints serially. If not, subtract 16384
to current value using the subtract command.
Subtract from Register 20: [unit ID]w20=~16384
Example: aw20=~16384
There are two ways to command a new setpoint over a serial connection, as
described below. In either of these methods, the data frame returns the new
setpoint value when it has been accepted as a valid setpoint.
Sending Setpoints as Floating Point Numbers
This is how to send the desired setpoint value as a floating point number in
the engineering units selected:
New setpoint: [unit ID]s[floating point number setpoint]
Example: as5.44(setpoint of +5.44 inH2OG)
When using a pressure controller with a negative pressure range or a
bidirectional range, negative sent points are sent by adding the minus sign.
New setpoint: [unit ID]s[floating point number setpoint]
Example: as-5.44(setpoint of -5.44 inH2OG)

12
Sending Setpoints as Integers
In this method, your controller’s full scale range (FS) is represented by a value
of 64000, and a zero setpoint is represented by 0. To calculate your intended
setpoint, use the following formula:
Integer value = 64000 × [desired setpoint] ⁄ [device FS]
Example 1: A desired setpoint of +5.44 inH2OG on a 10-inH2OG pressure
controller is calculated as 64000 × 5.44 ⁄ 10.00 = 32704. The command to
assign the setpoint based on this integer value is:
New setpoint: [unit ID][setpoint as integer where 64000 is FS]
Example: a32704(setpoint of 5.44 inH2OG)
Example 2: When using a bidirectional pressure controller, 0 represents -100%
of full scale, 32000 represents 0, and 64000 represents +100% of full scale.
Use the formula below to calculate the integer value.
Integer value = 64000 × [desired setpoint + FS] ⁄ [device FS]
A desired setpoint of +5.44 inH2OG on a 10-inH2OG pressure controller is
calculated as 64000 × [5.44 + 10]/10.00 = 9882. The command to assign the
setpoint based on this integer value is:
New setpoint: [unit ID][setpoint as integer where 64000 is FS]
Example: a9882(setpoint of 5.44 inH2OG)
Example 3: A setpoint of -5.44 inH2OG on the same bidirectional controller is
calculated as:
Integer value = 64000 x (-5.44 + 10)/10 = 29184

13
PID Tuning:
Your flow controller uses a closed-loop algorithm to determine how to
actuate its valve(s) in order to achieve the commanded setpoint. We have
tuned these settings for your specific operating conditions, but changes to
your process sometimes require on-site adjustments to maintain optimal
control performance. If you encounter issues with control stability,
oscillation, or speed of response, fine-tuning your closed loop control may
help.
Changing Gain Values
The only way to adjust The P, D, and I gains on an EPC or EPCD device is by
adjusting registers 21, 22, and 23, respectively.
For more information on reading and adjusting 16-Bit registers, as well as
definitions of the functionality of registers on the EPC or EPCD device please
download the Alicat Serial Primer at: Alicat.com/drivers
Tuning the PD/PDF control algorithm
The EPC controller’s default control algorithm (PD) employs pseudo-
derivative feedback (PDF) control, which uses two editable variables:
The larger the D gain, the slower the controller will correct errors
between the commanded setpoint and the measured process value.
This is equivalent to the P variable in common PDF controllers.
The larger the P gain, the faster the controller will correct for offsets
based on the size of the errors and the amount of time they have
occurred. This is equivalent to the I variable in common PDF
controllers.
✓
Note: The D and P variables in the PD/PDF control algorithm are more
typically referred to as P and I, respectively, in PDF

14
Tuning the PD²I control algorithm
The EPCD controller’s PD²I control algorithm is used to provide faster
response, and high-performance swapping of the operation of the inlet and
exhaust valve. This algorithm uses typical PI terms and adds a squared D term:
The larger the Pgain, the more aggressively the controller will correct
errors between the commanded setpoint and the measured value.
The larger the Igain, the faster the controller will correct for offsets
based on the size of the errors and the amount of time they have
occurred.
The larger the Dgain, the faster the controller will predict needed
future corrections based on the current rate of change in the system.
This often results in slowing the system down to minimize overshoot
and oscillations.
!
Warning: EPCDs are only intended for use with PD²I tuning and may
experience significant performance issues if switched to PD/PDF.
Troubleshooting valve performance with PID tuning
The following issues can often be resolved by adjusting the PID gain values
for your flow controller.
Fast oscillation around the setpoint
PD: Reduce the P gain in decrements of 10%
PD²I: Increase the P gain in increments of 10%, and then adjust the I
gain to fine-tune.
Overshot setpoint
PD: Reduce the P gain in decrements of 10%.
PD²I: If D is not 0, increase the P gain in increments of 10%.
Delayed or unattained setpoint
PD: Increase the P gain in increments of 10%, and then decrease the D
gain by small amounts to fine-tune.
PD²I: Increase the P gain in increments of 10%, and then increase the I
gain to fine-tune.
✓
Note: Valve tuning can be complex. Please give us a call, and we’ll be
happy to guide you through the process. Or, visit alicat.com/pid for more
detailed instructions

15
Quick Command Guide
✓
Note: Serial commands are not case-sensitive. For simplicity, we assume
that the unit ID of the flow controller when not streaming is ain the
listing that follows.
Change unit ID: a@=[desired unit ID]
Tare pressure: ap
Poll the live data frame: a
Begin streaming data: a@=@
Stop streaming data: @@=[desired unit ID]
Set streaming interval: aw91=[number of milliseconds]
New setpoint: as[setpoint as floating point #]
New setpoint: a[setpoint as integer where 64000 is full scale]
Hold valve(s) at
current position: ahp
Hold valve(s) closed: ahc
Exhaust (EPCD only): ae
Cancel valve hold: ac
Query live data info: a??d*
Manufacturer info: a??m*
Firmware version: a??m9
Write P Gain: aw21=[desired gain value]
Write D Gain: aw22=[desired gain value]
Write I Gain: aw23=[desired gain value]
Additional information can be found on our online Serial Primer document,
at: Alicat.com/drivers
If you have need of more advanced serial communication commands, please
contact support (page 2).

16
Maintenance
Cleaning
This device requires minimal maintenance. If necessary, the outside of the
device can be cleaned with a soft dry cloth. Avoid excess moisture or solvents.
The single most important thing that affects the life and accuracy of these
devices is the quality of the gas being measured. The instruments are
designed to measure clean, dry, non-corrosive gases.
Recalibration
The EPC device is an OEM product calibrated to NIST traceable standards at
the time of manufacture. As an OEM device there is not a factory
recommended periodic recalibration cycle. Recalibration can be requested at
the user’s discretion/requirement. A recalibration can be requested with your
serial number at alicat.com/service.
For repair, recalibration, or recycling of this product
contact us (page 2).
Technical Specifications and Dimensional Drawings
Please visit alicat.com/specs to find complete operating specifications and
dimensional drawings.
This manual suits for next models
1
Table of contents
Other Alicat Scientific Controllers manuals
Popular Controllers manuals by other brands
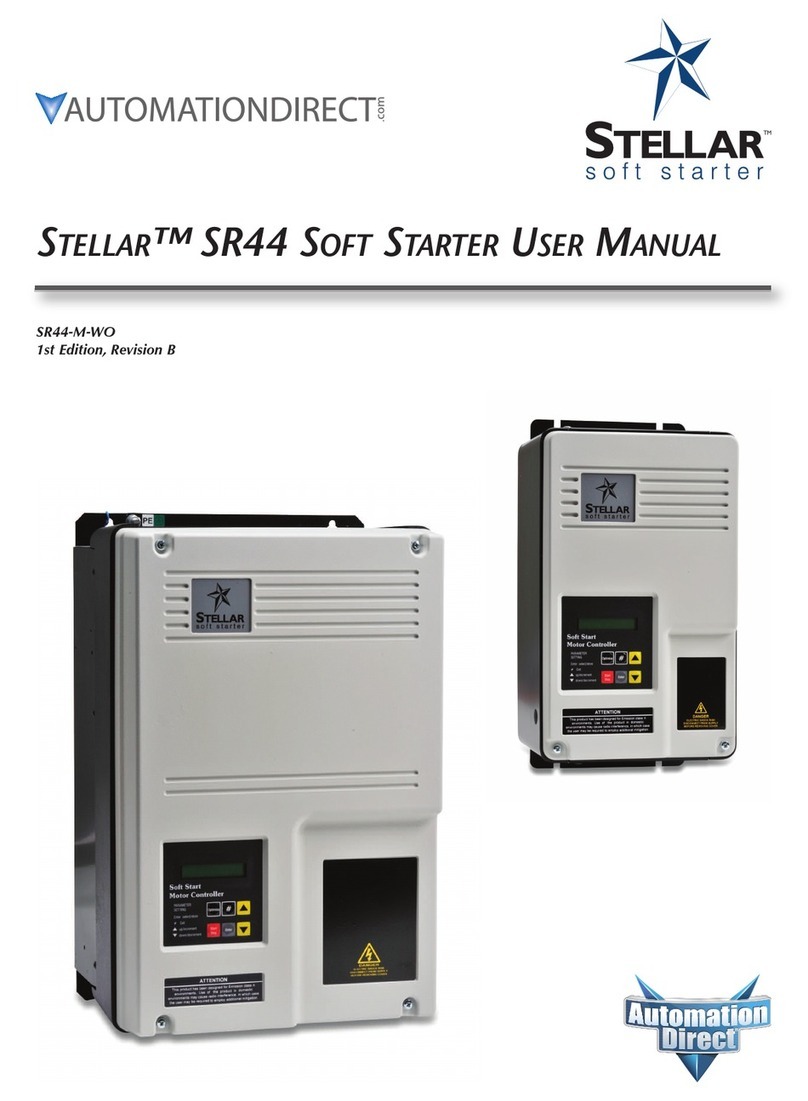
Automationdirect.com
Automationdirect.com Stellar SR44 user manual
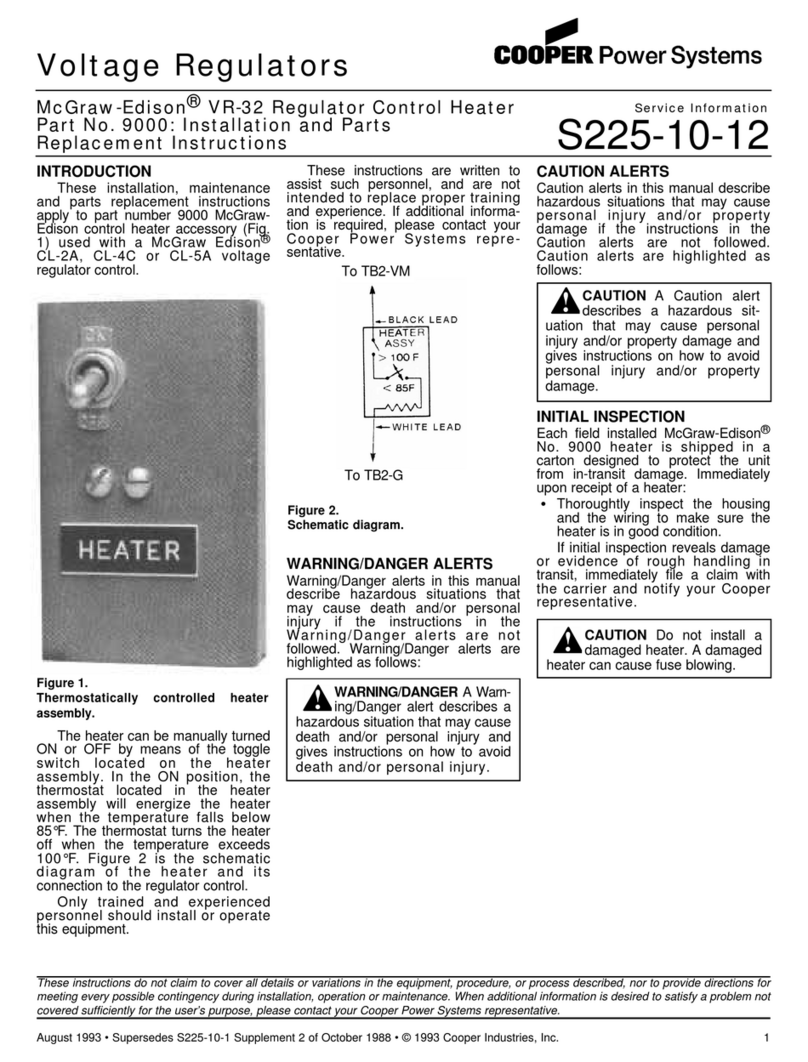
Cooper Power Systems
Cooper Power Systems mcGraw Edison 9000 Replacement instructions
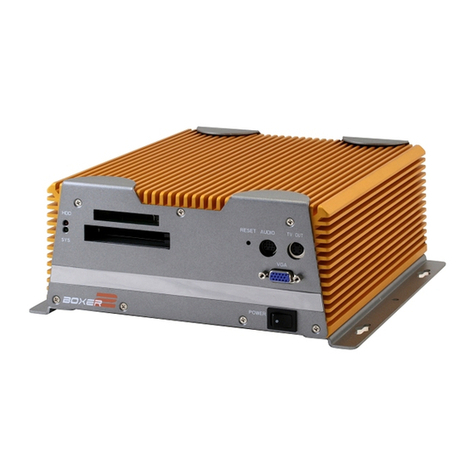
Aaeon
Aaeon AEC-6420 manual
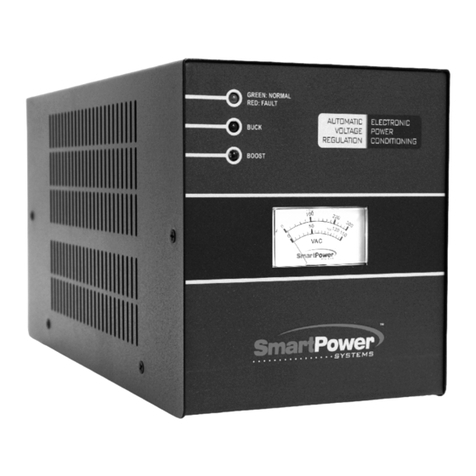
Power Quality
Power Quality SmartPower AVR Plus AVR10-120TBF user guide
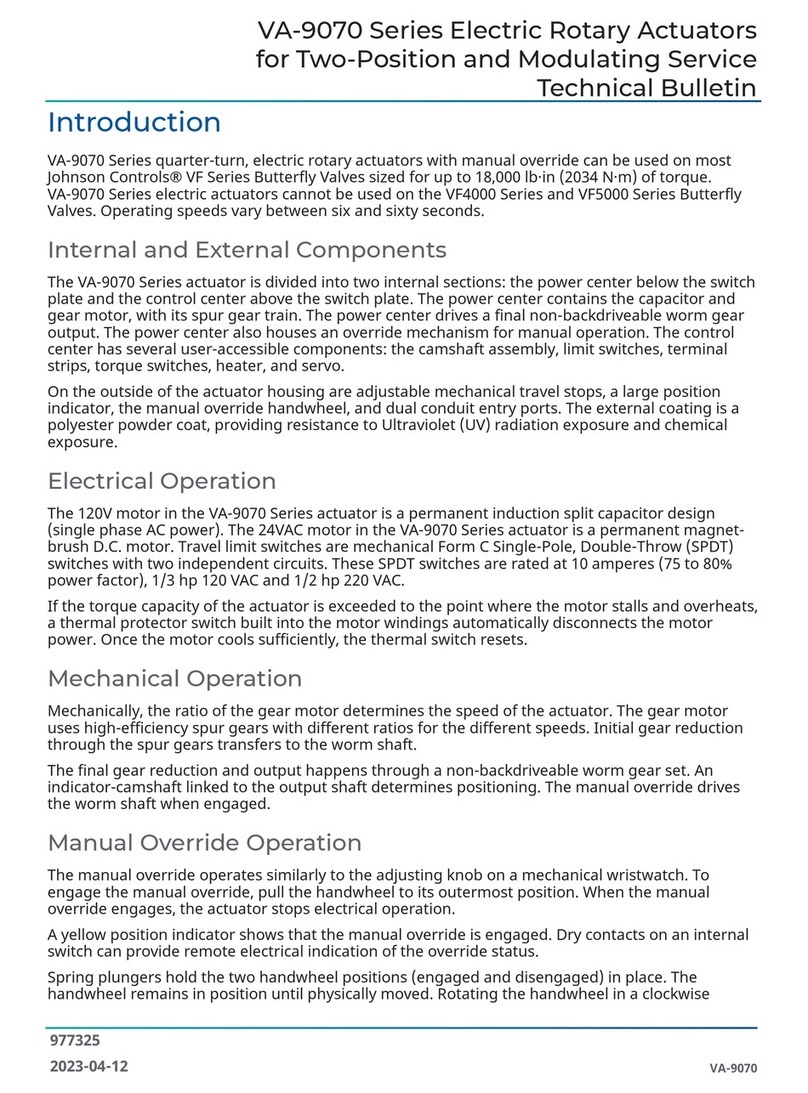
Johnson Controls
Johnson Controls VA-9070 Series Technical bulletin
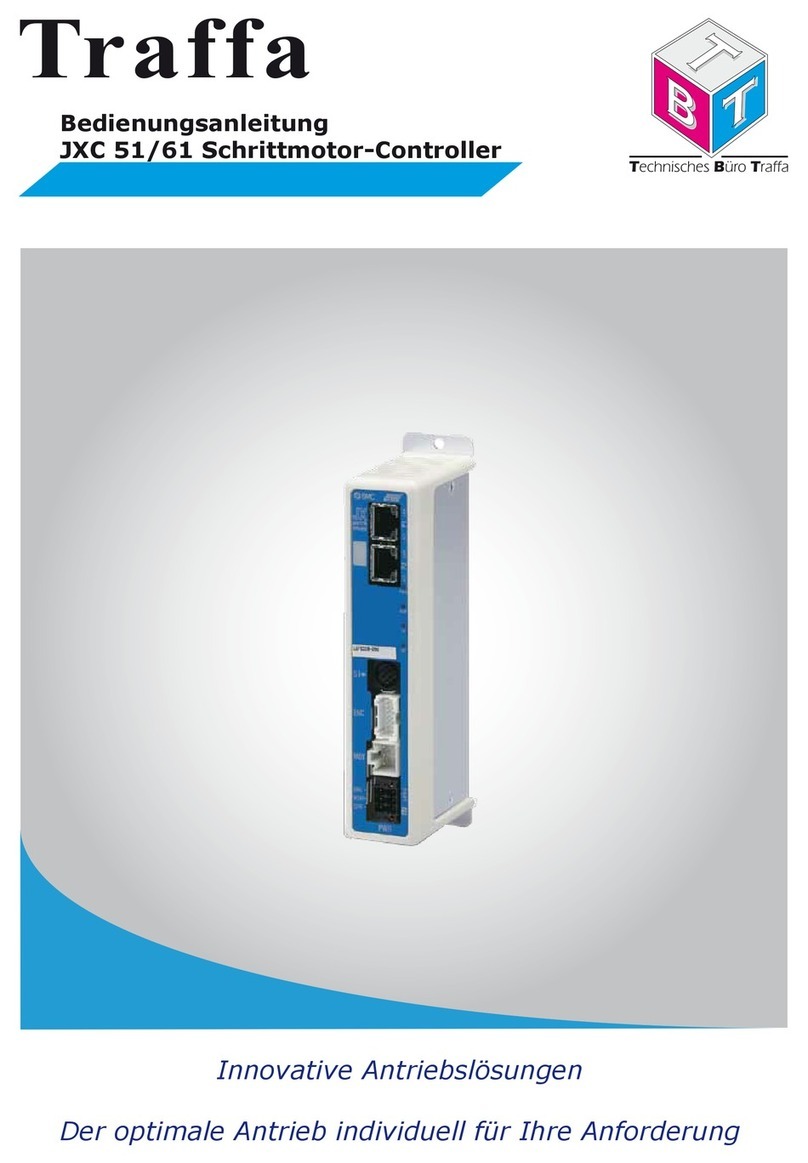
SMC Networks
SMC Networks JXC61 Operation manual