ALIND AN Series User manual

NUMERICAL SWITCHING RELAY
ANS 321 [AN SERIES]
User Manual
THE ALUMINIUM INDUSTRIES LIMITED
RELAYS DIVISION, TRIVANDRUM

SAFETY REQUIREMENTS ANS 321- I
INTRODUCTION ANS 321-II
HANDLING INSTALLATIONS &
CASE DIMENSIONS ANS 321-III
USER GUIDE ANS 321-IV
TECHNICAL DATA &
CHARACTERISTIC CURVES ANS 321-V
TROUBLE SHOOTING ANS 321-VI

ANS 321-I Page 1 of 8

SAFETY REQ. ANS 321-I Page 2 of 8
INTRODUCTION
HEALTH AND SAFETY
SYMBOLS AND EXTERNAL LABELS ON THE RELAY
INSTALLING, COMMISSIONING AND SERVICING
DECOMMISSIONING AND DISPOSAL
TECHNICAL SPECIFICATION FOR SAFETY

SAFETY REQ. ANS 321-I Page 3 of 8
INTRODUCTION
Before using this product, be sure to read this chapter carefully.
This chapter describes safety precautions when using the relay.
Before installing and using the equipment, read and understand this
chapter thoroughly.
It’s not a secret – electricity can be dangerous and when things go
wrong lives can be at stake!
Electrical engineers are Industrial safety doctors, so it’s our duty to
keep employees health and maintain a quality of life that we all deserve
by providing safe work practices to avoid electrical accidents.
How much electricity is dangerous?????
CURRENT
EFFECT
0.5 –3mA
Tingling sensations
3 –10mA
Muscle contractions
(painful)
10 –40mA
“can’t let go”
phenomena
40 –75mA
Respiratory paralysis
(possibly fatal)
75 –200mA
Ventricular fibrillation
(likely fatal)
200 –500mA
Heart clamps tight
>1.5A
Tissue and organs began
to burn
Fact: A 15 amp circuit breaker was designed to protect
equipment –not people!
The relay is developed with zero percentage of risk factor by its own
design. The current carrying paths and circuits are isolated from the
metal case and structure. Suitable clearance depending on the type
of insulation required for different classes are provided. The relay
confirms to Product safety requirement standard IEC 60255-27.

.
SAFETY REQ. ANS 321-I Page 4 of 8
HEALTH AND SAFETY
It deals with the handling of relay in proper way. An individual to be
considered as ‘qualified’ with regard to certain equipment in the
workplace, but ‘unqualified’ as to other equipment. “An employee,
who is undergoing on the job training and who, in the course of such
training, has demonstrated the ability to perform duties safely at his
or her level of training and who is under the direct supervision of a
qualified person also considered to be a qualified person for the
performance of those duties.”
The following requirements must be met, in the order given, before
circuits or equipments are re-energized, even temporarily.
People handling the equipment should be aware about the
relay safety handlet.
Ensure that the product is in the off condition before working
on the conducting or terminal side.
A qualified person must conduct tests and visual inspections,
as necessary, to verify that tools electrical jumpers, shorts,
grounds and other such devices have been removed, so that
the circuits and equipments can be safely re-energized.
Employees exposed to the hazards associated with re-
energizing the circuit or equipment must be warned to stay
clear of the circuits and equipment.
Each lock and tag must be removed by the employee who
applied it or someone else under that employee’s direct
supervision.
A visual determination that all employees are clear of the
circuits and equipments must be made.
For any queries related to relays, feel free to contact ALIND.

SAFETY REQ. ANS 321-I Page 5 of 8
SYMBOLS AND LABELS USED IN THE RELAY
1. FRONT SIDE
Caution: refer to equipment documentation Caution: risk of
electric shock
2. REAR SIDE
Protective Conductor (*Earth) terminal
Functional/Protective Conductor (*Earth) terminal.
CMOS Battery provided for the
RTC (Real Time Clock) purpose.
Confirm polarity of the battery
while replacing.

SAFETY REQ. ANS 321-I Page 6 of 8
WARNING
Current transformer circuit
Never allow the current transformer (CT)
secondary circuit connected to this equipment to
be opened while the primary system is live.
Opening the CT circuit will produce a dangerous
high voltage.
Exposed terminals
Do not touch the terminals of this equipment
while the power is on, as the high voltage
generated is dangerous
Residual voltage
Hazardous voltage can be present in the DC
circuit just after switching off the DC power
supply. It takes about 30 seconds for the
voltage to discharge.
CAUTION
Earth
Earth the earthing terminal of the equipment
securely.
Operation conditions
Use the equipment within the range of ambient
temperature, humidity and dust as detailed in the
specification and in an environment free of
abnormal vibration.
Ratings
Before applying AC voltage and current or DC
power supply to the equipment, check that they
conform to the equipment ratings.
Printed circuit board
Do not attach and remove the printed circuit
board while the DC power to the equipment is on,
as this may cause the equipment to malfunction.

SAFETY REQ. ANS 321-I Page 7 of 8
External circuit
When connecting the output contacts of the
equipment to an external circuit, carefully check
the supply voltage used and prevent the
connected circuit from overheating.
Connection cable
Carefully handle the connection cable without
applying excessive force.
Modification
Do not modify this equipment, as this may cause
the equipment to malfunction, and any such
cases, warranty may be affected.
DECOMMISIONING AND DISPOSAL
De-commissioning
The supply input (auxiliary) for the equipment
may include capacitors across the supply or to
earth. To avoid electric shock or energy hazards,
after completely isolating the supplies to the
equipment, the capacitors should be safely
discharged via the external terminals prior to de-
commissioning.
Disposal
When disposing of this equipment, do so in a safe
manner according to local regulations. It is
recommended that incineration and disposal to
water courses is avoided. Ensure the relay is in
de energized condition and take precautions to
avoid short circuits.

SAFETY REQ. ANS 321-I Page 8 of 8
TECHNICAL SPECIFICATIONS FOR SAFETY
1. Protective class
IEC 60255-27:2005 Class I (This equipment requires a
protective conductor (earth)
connection to ensure user safety.
2. Environment
IEC 60255-27:2005 Pollution degree 2 (Normally only
non-conductive pollution occurs
except occasionally a temporary
conductivity caused by condensation
is to be expected.)
3. Overvoltage Category
IEC 60255-27:2005 Category III (The auxiliary
energizing circuits of the equipment
are connected to a common battery,
common mode transient voltages of
a relatively high value may appear
on the supply leads, and differential
mode voltages may arise from
switching in other circuits connected
to the same battery source.
4. Contact data
Test voltage across open contact: 1 kV DC for 1 min

ANS 321-II Page 1 of 12

INTRODUCTION ANS 321-II Page 2 of 12
AN SERIES DESCRIPTION
BRIEF DESCRIPTION OF ANS 321
MAIN FUNCTIONS
GENERAL FUNCTIONS

INTRODUCTION ANS 321-II Page 3 of 12
AN SERIES (ALIND NUMERICAL SERIES)
Advanced Digital Fourier Transform based Numerical algorithm
design using 16-bit Digital Signal Controller (DSC).
Compact Construction covering several protection modules saving
panel space.
Man-Machine Communication through 20x4 character LCD display
and LEDs.
Self supervision of both hardware and software units.
Interface ability with SCADA is achieved through IEC 60870-5-103
communication protocol.
Facility for storing fault waveforms (Disturbance recorder) and
events with date and Time stamping. At a time a total of 5000
events and 200 latest fault waveforms (Disturbance recorder) will
be stored in the relay.
Graphical User Interface for Harmonic analysis, DC analysis and
di/dt analysis can be done on the uploaded fault waveforms with
facility for report generation.
Facility to access/modify the relay settings both online as well as
through menu in local PC through SCADA at RCC.
Relay Indication (LED) reset from RCC.
Suitable password protection.
IP 54 grade enclosure protection.
GPS time Synchronization Facility.

INTRODUCTION ANS 321-II Page 4 of 12
Settable CT and PT ratio.
CB close and open command initiation from relay through RCC.
ANS RELAYS
ANS series relays are designed for” ON LOAD SWITCHING” of
feeding power supply alternatively in the “NEUTRAL SECTION” which is
separated by the two sets of sections with TSS and SP, so that voltage
available within the neutral section is of same phase at any given time.
DESCRIPTION
The General arrangement of Automatic switching Neutral Section
for IR is shown below:

INTRODUCTION ANS 321-II Page 5 of 12
ANS 321 relay monitor current through three CT’s for detecting the
presence of traction load and changeover the supply of neutral section
by controlling connected Circuit Breakers .The changeover of supply in
Neutral Section are controlled by three Circuit Breakers.
ANS relay facilitate in automatic changeover at high speed so as to allow
the loco to pass the neutral section and it's also possible for the loco to
run the neutral section without reducing the speed or driver's intervention
in doing DJ off at phase break. The general arrangement of neutral section
is shown in above scheme.
Initial Conditions :
CB1 close condition
CB2 open condition
CB3 close condition
PT1 & PT2 healthy
In above scheme, Feed A and Feed B are of two separate phases.
The above diagram indicates 3 IOLs. CB1 bridges IOL1, CB2 bridges
IOL2 and CB3 bridges IOL3. Current Transformers CT1, CT2 & CT3 are
provided at bus bridging IOL1, IOL2 and IOL3 respectively. The relay
constantly monitors all CT currents and PT voltages as well as the status
of all CB’s. Depending on which CT reads first, the sequence of operation
is depicted below.

INTRODUCTION ANS 321-II Page 6 of 12
SEQUENCE OF OPERATIONS WHEN CT1 READS FIRST
CT1
CT2
CT3
CB1
CB2
CB3
1.
0
0
0
1
0
1
1
0
0
1
0
1→0
(After CB3 trips
relay)
1
0→1
(After
getting
CB3 trip
status+
CB2
close
delay)
0
Final Condition
1
1
0
2.
1
1
0
1→0(After
CB1 trip
delay)
1
0
0
1
0→1(After
getting CB1 trip
status + CB1
close delay)
Final Condition
0
1
1
3.
0
0
1
0
1
1
4.
0
0
0
0
1→0
(Forwad
under
current
delay +
CB2 trip
delay)
1
0→1(After
getting
CB2 trip
status +
CB1
delay)
0
1
Final Condition
1
0
1

INTRODUCTION ANS 321-II Page 7 of 12
If all PT’s were in healthy condition, CB1 and CB3 will be in close condition and
CB2 will be in tripped condition allowing the locomotive to enter the three IOLs in
both directions. Initially all CT’s reads zero current as no loco is present in any
IOL. When loco comes from feed A (forward direction) and approaching IOL1, CT1
starts reading. When CT1 reads above switching current setting, relay will trip CB3
(after CB3 trip delay). After analysing condition of CB3, relay will close CB2 (after
CB2 close delay). As loco continues its motion, CT2 starts reading on approaching
IOL2. When CT1& CT2 reads above the switching current setting, relay will trip
CB1 (after CB1 trip delay). After analysing condition of CB1, relay will close CB3
(after CB3 close delay) and the loco will be fed from feed B. When loco crosses the
IOL3, CT3 current falls below the under current setting, relay will trip CB2 (after
forward undercurrent delay + CB2 trip delay ) and closes CB1 (after CB1 close
delay) after analysing the condition of CB2 .

INTRODUCTION ANS 321-II Page 8 of 12
SEQUENCE OF OPERATIONS IF CT3 READS FIRST
CT1
CT2
CT3
CB1
CB2
CB3
1.
0
0
0
1
0
1
0
0
1
1→0
(After CB1
trips
relay)
0
1
0
0→1
(After
getting
CB1 trip
status+
CB2
close
delay)
1
Final Condition
0
1
1
2.
0
1
1
0
1
1→0(After CB3
trip relay)
0→1(After
getting
CB3 trip
status +
CB1 close
delay)
1
0
Final Condition
1
1
0
3.
1
0
0
1
1
0
4.
0
0
0
1
1→0
(Reverse
under
current
delay +
CB2 trip
delay)
0
1
0
0→1(After
getting CB2 trip
status + CB3
close delay
Final Condition
1
0
1

INTRODUCTION ANS 321-II Page 9 of 12
Initially all CT’s reads zero current as no loco is present in any IOL. When loco
comes from feed B (Reverse direction) and approaching IOL3, CT3 starts reading.
When CT3 current reads above switching current setting the relay will trip CB1
(after CB1 trip delay). After analysing the condition of CB1, the relay will close
CB2 (after CB2 close time delay). As loco continues its motion, CT2 starts reading
on approaching IOL2. When CT3 and CT2 reads above switching current setting,
the relay will trip CB3 (after CB3 trip delay). After analysing the condition of CB3,
relay will close CB1 (after CB1 close delay) and the loco will get feed from feed A.
When loco crosses the IOL1, CT1 current falls below the under current setting, the
relay trip CB2 (after reverse undercurrent delay + CB2 trip delay) and closes CB3
(after CB3 close delay) after analysing the condition of CB2.
RELAY BYPASS CONDITION
Necessary potential free auxiliary contacts is available for bypass the relay. Control
supply for operating breakers shall made available in bypass condition. A separate
contact are provided in the relay to enable getting indication at RCC, that the relay
is disabled. In addition, indication is also available in the front panel of the relay.

INTRODUCTION ANS 321-II Page 10 of 12
PT FAILURE
PT
CB
1
2
1
2
3
0
1
0
0
0
1
0
0
0
0
0
0
0
0
0
In case of any PT failure, all CB’s are tripped on the set delay (0-2000ms)
without considering any other factors.
In case of PT dead condition or DJ OFF condition, the loco pilot shall put down
the pantograph.
On restoring of the PT after failure, the ANS relay will restore the CBs status
as defined in the table given below.
FORWARD DIRECTION
STATE
ANS321
CONDITION
BEFORE PT fail
Remarks
ANS 321
CONDITION ON
RESTORING PT
Remarks
CB1
CB2
CB3
CB1
CB2
CB3
1
1
0
1
Initial condition
(no loco present
in ASNS).
1
0
1
Relay restores
to initial
condition after
restoring of PT.
2
1
1
0
Forward
sequence started
and loco crossed
IOL1.
0
1
1
Relay restores
to 0 1 1
condition of
forward
sequence and
allow loco to
complete the
sequence.
3
0
1
1
Loco Crossed
IOL2.
Other manuals for AN Series
3
This manual suits for next models
1
Table of contents
Other ALIND Relay manuals
Popular Relay manuals by other brands
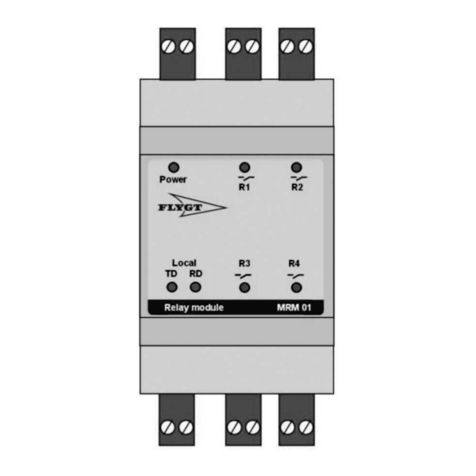
Xylem
Xylem FLYGT MRM 01 Installation, operation and maintenance manual

ABB
ABB SPAJ 111 C user manual
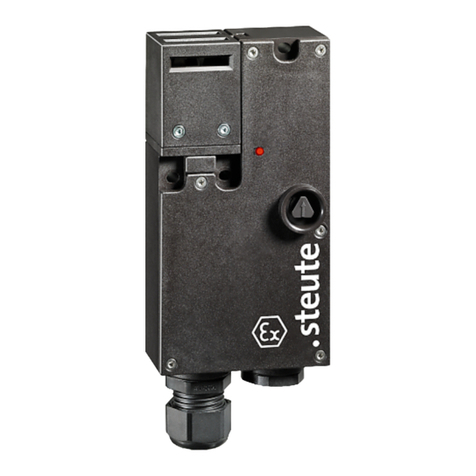
steute
steute Ex STM 295 3G/D Series Mounting and wiring instructions
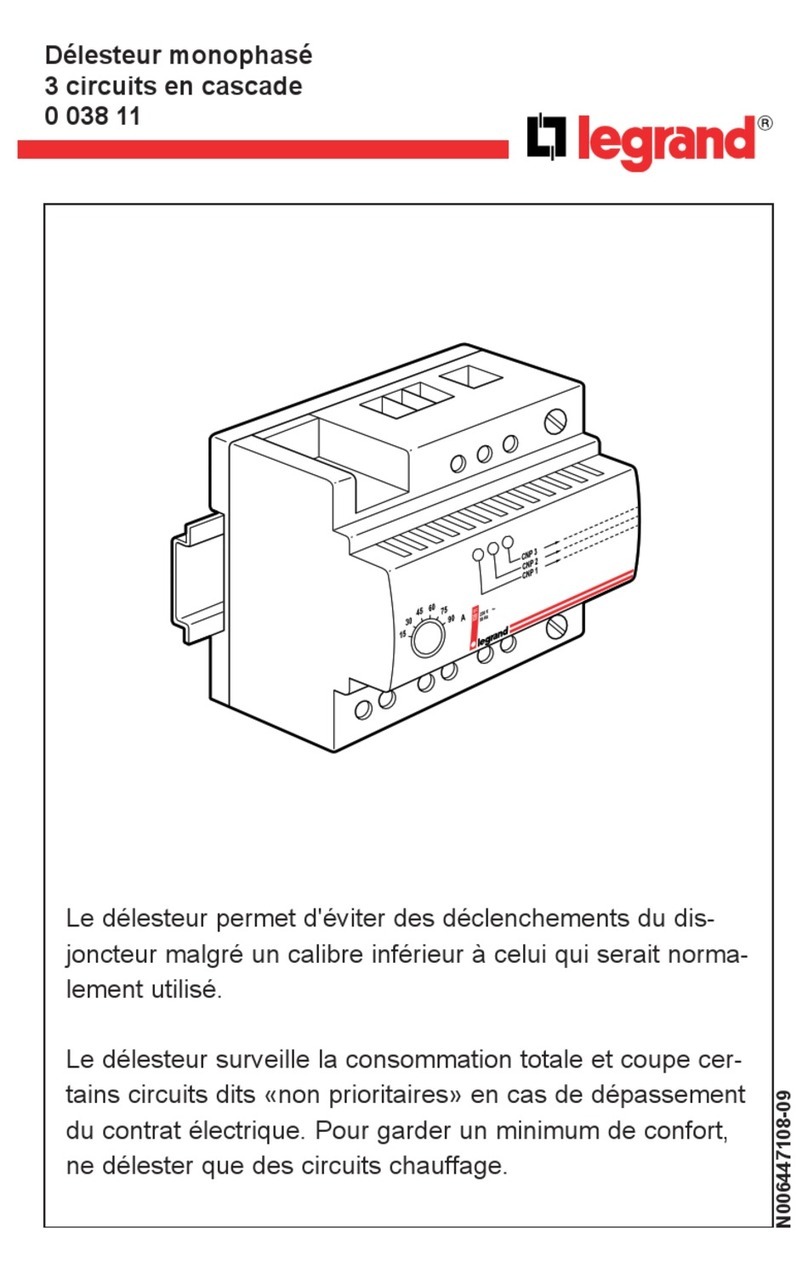
LEGRAND
LEGRAND 0 038 11 manual
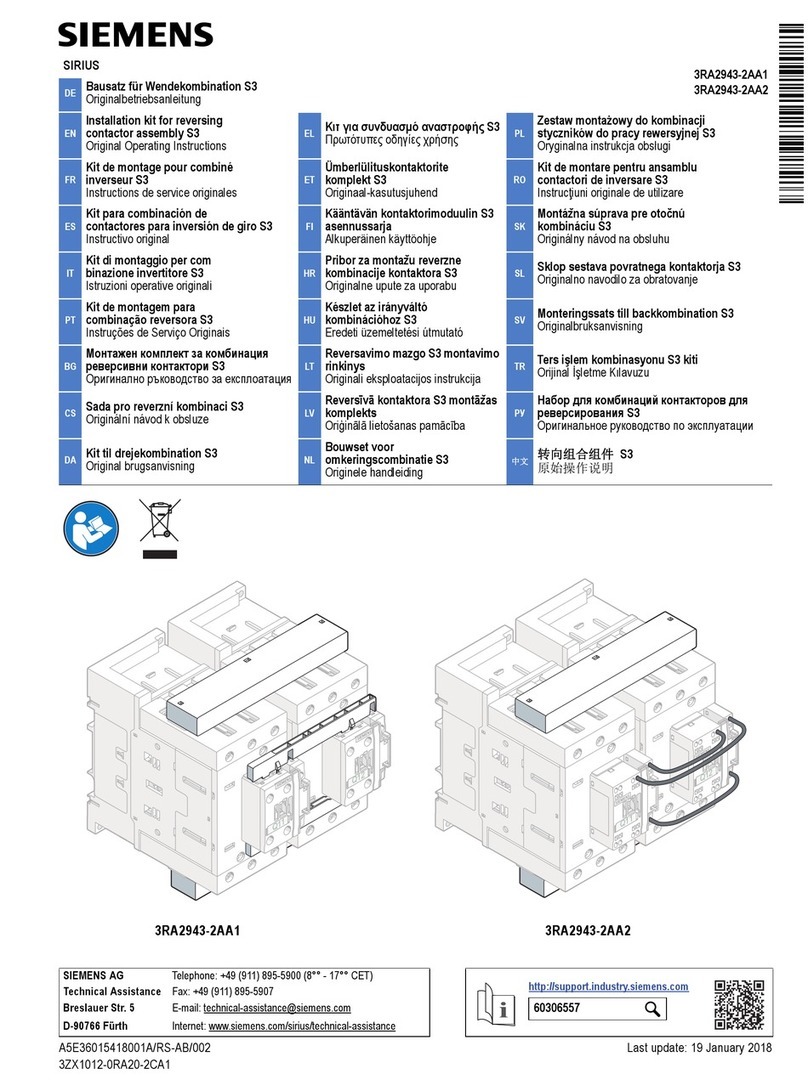
Siemens
Siemens SIRIUS 3RA2943-2AA1 Original operating instructions
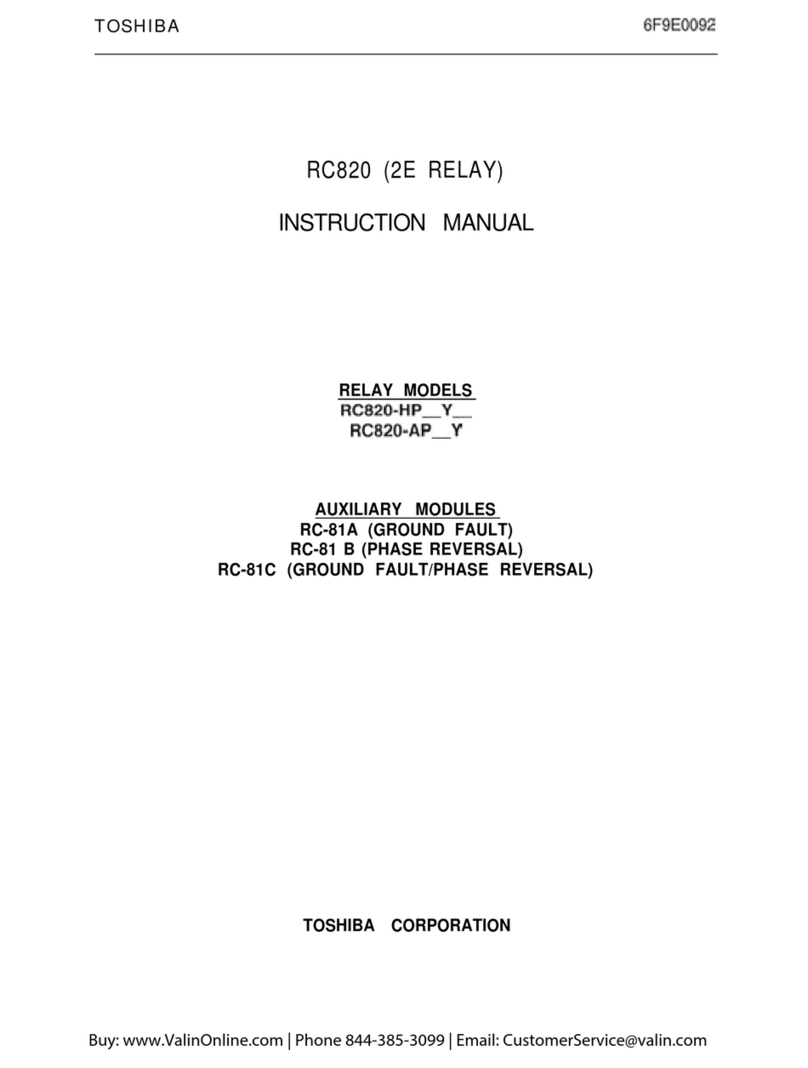
Toshiba
Toshiba RC820-HP-Y instruction manual