Altecnic Matrix Midi 135D Guide

Installation, Operation & Maintenance
Instructions
Please leave this instruction booklet with the end user as it contains important
guarantee, maintenance and safety information
Read this manual carefully before commencing installation.
This manual covers the following products:
Matrix Midi 135D
Pt. No. 121-1011
Matrix Midi 150D
Pt. No. 121-1012
Matrix Midi 235D
Pt. No. 121-1013
Matrix Midi 250D
Pt. No. 121-1014
2
CE compliant product
Matrix Midi

- 2 -
Cont ...
PRODUCT DESCRIPTION
Heating and cooling system pressurisation top up unit with integral water storage tank and electric
motor driven peripheral pump, automated control system consisting of pressure transducer and
water level sensors. The tank includes an AB air gap for category 5 fluid isolation (BS EN 1717).
APPLICATION
The Matrix Midi range is designed to provide initial system fill and intermittent water top up
to compensate for intermittent losses in system pressure in heating and cooling systems in
commercial or industrial applications. These could include slight leaks, air venting, etc. The units
are not designed to deal with sudden losses of system pressure due to major water losses over
extended periods. They are also not to be used for water boosting applications.
STORAGE
If this product is not to be installed immediately on receipt, ensure that it is stored in a dry, frost
and vibration free location in its original packaging.
CONTENTS Page
Checklist . . . . . . . . . . . . . . . . . . . . . . . . . . . . . . . . . . . . . . . . . . . . . . . . . . . . . . . . . . . . . . . . . . . . . . . 5
Important Facts - read before commencing installation ................................6
Location .......................................................................7
Key Features ...................................................................9
Installation .....................................................................10
Electrical Installation ............................................................14
Commissioning .................................................................18
Operation .....................................................................25
Maintenance ...................................................................27
Environment Protection ..........................................................28
Technical Specification ...........................................................29
Trouble Shooting ................................................................30
Product Log ....................................................................31
Guarantee .....................................................................34

- 3 -
Cont ...
WARNINGS:
zThis appliance must not be used for any other application
without the written consent of Altecnic Limited.
zThis appliance can be used by children aged from 8 years
and above and persons with reduced physical, sensory or
mental capabilities or lack of experience and knowledge if
they have been given supervision or instruction concerning
use of the appliance in a safe way and understand the
hazards involved. Children shall not play with the appliance.
Cleaning and user maintenance shall not be made by children
without supervision.
zChildren should be supervised to ensure that they do not
play with the appliance.
zThis product should not be used for the supply of water to
more than one heating/cooling system at a time.
zThe electrical installation must be carried out in accordance
with the current national electrical regulations.
zThe electrical installation must be installed by a qualified
person.
zThe motor is not accessible in normal operating mode. The
unit must only be operated with the front cover in place.
zThe electrical installation must be carried out in accordance
with the current national electrical regulations and installed
by a qualified person.
zIn the interests of electrical safety a 30 mA residual current
device (R.C.D. not supplied) should be installed in the supply
circuit. This may be part of a consumer unit or a separate
unit.
zThis appliance must be earthed via the supply cord.
Please read installation details carefully as they are intended to ensure this product provides
long, trouble free service. Failure to install the unit in accordance with the installation
instructions will lead to invalidation of the warranty.

- 4 -
Cont ...
CHECKLIST
Note:
Your product may vary slightly from the picture above.
Item Description Qty Item Description Qty
Matrix Midi 1 Fill valve flow restrictor 2
Front cover 1 Rubber hose sealing washer, to be
used with item C 2
Flexible hose, G ½ 15 mm
compression 2 Cable tie 2
M6 screw 1 Instruction book 1
Wall mounting plate 1
A
E
C
B
D
H
G
F
I
C
Fig. 1
IMPORTANT: With the appliance removed from its packaging
check for any damage prior to installation. If any damage is
found contact Altecnic Ltd within 24 hours of receipt.
AD
Front cover removed for clarity
B
E
Electrical rating
plate & serial
number
G
F
H

- 5 -
Cont ...
1 IMPORTANT FACTS: READ BEFORE COMMENCING PUMP INSTALLATION
A Water storage capacity.
1.11 The Matrix Midi has a usable water volume of approximately 8 litres; the length of time
the Matrix Midi takes to pressurise a system will be dependent on:-
The pressure differential between the cold fill and set pressures and also the refill rate of
the tank
1.12 Ensure the pumps are primed as described in the priming section before starting, to
avoid causing damage to the pump shaft seal. See Section 6.26 Hydraulic commissioning.
B Water temperature
This unit is designed to pump cold water only which should not exceed the following values:
1.13 The maximum allowable water temperature is 23 oC (see Section 10).
1.14 The minimum allowable water temperature is 4 oC.
C Pipework - General
1.15 Do not drill holes or put fastenings into the Matrix Midi tank, this will cause leakage.
1.16 Secure pipework: Ensure pipework to and from pump is independently supported &
clipped to prevent forces being transferred to inlet and outlet branches of the unit. Do
not secure pipework to the Matrix Midi, this will cause damage and possible leakage.
1.17 Flux: Solder joints must be completed and flux residues removed prior to Matrix Midi
installation (flux damage will void any warranty).
1.18 Pipework design: Care should be taken in the design of pipework runs to minimize the
risk of air locks e.g. use drawn bends rather than 90obends.
1.19 DO NOT introduce solder flux to flexible hose, tank, pump or any parts
manufactured from plastic.
1.20 DO NOT allow contact with oil or cellulose based paints, paint thinners or
strippers, acid based descalents or aggressive cleaning agents.
1.21 DO NOT bend the flexible hose beyond 90o. It must be installed as detailed,
DO NOT kink. See Installation Section 4.15.
D Plumbing Installation Regulations
1.22 The plumbing installation must comply with the current water and building regulations.
1.23 The plumbing installation must be installed by a qualified person.

- 6 -
Cont ...
2 LOCATION-GENERAL
2.11 Location: The preferred Matrix Midi location is either on a solid wall or on a
smooth level floor, both of sufficient strength to support the filled weight
of the Matrix Midi, close to the water source and a suitable overflow
position (see Section 9 - Technical Specification for filled weight). The Matrix
Midi must not be installed in a loft space. It must also be considered that
the noise and vibration from the Matrix Midi may be transmitted through the
structure it is sited on. Ensure the minimum clearance requirements are
followed to allow servicing of the unit
2.12 Access and minimum clearance requirements: For emergencies and
maintenance the Matrix Midi must be easily accessible and have the
minimum clearance around it as laid out in Fig. 2.
Additional access to the front of the unit will be required to operate the
keypad and view the display.
2.13 Protection: The Matrix Midi must be located in a dry, frost free area.
2.14 Ventilation: Ensure an adequate air flow to cool the Matrix Midi.
Separate the Matrix Midi from other appliances that generate heat.
Do not block the vent holes on the front cover or the air inlet at the rear.
2.15 Water retention: Site the Matrix Midi in a location where in the unlikely
event of a water leak, any spillage is contained or routed to avoid
electrics or areas sensitive to water damage. As part of the AB airgap (CAT
5 fluid isolation) the Matrix Midi has a weir type overflow on the right hand
side, water will be discharged from this area in the event of the failure of the
inlet valve or non-return valves.
2.16 Supply inlet pressure: The water supply inlet pressure must not exceed 7 bar.
2.17 Ambient temperature: The Matrix Midi must be sited in a location where the ambient
temperature does not drop below 4 °C or exceed 40 °C.
Fig. 2
300
500
300
150150
Dimensions in mm

- 7 -
Cont ...
2.18 Pipework: For optimum performance inlet and outlet pipework must be a minimum of
15 mm pipe.
2.19 Static outlet pressure: The static outlet head must be 3 metres below pump maximum
cold fill pressure (vertically above the appliance).
2.20 Noise: A flexible hose is supplied as standard which will minimise the transmission of
noise and vibration from the Matrix Midi pump to the pipework connected to the
appliance outlet. However, care must be taken when mounting the Matrix Midi that any
noise is not amplified through loose panels or pipework.
2.21 Flexible hose: Only use the Altecnic Ltd hoses supplied with the Matrix Midi.
2.22 Isolating valves: Separate system isolating valves (non-restrictive) must be fitted to allow
easy service of the Matrix Midi. Isolating valves must be mounted where specified to
allow the system isolation and removal of the Matrix Midi if needed. See Section 4.15 for
installation details.

- 8 -
Cont ...
3 KEY FEATURES
3.11 The Matrix Midi comprises of the following main components:-
1. Moulded tank – Main body of the Matrix Midi, comprising of an integrated water
tank with warning pipe and weir overflow and mounting the brass pump assembly,
manifold and controller.
2. Pump assembly – One or two brass peripheral pump units powered by induction
motors, with integrated non return valves and venting screw.
Mounted into the moulded tank with vibration isolating rubber mounts.
3. Outlet manifold – Brass manifold with pressure transducer used to monitor system
pressure and connection to the pump(s).
4. Programmable controller – Custom designed, user set controller, allowing system set
up and easy alarm connection.
5. Wall mounting plate – Robust stainless steel wall mounting plate allowing quick, easy
installation and removal if needed.
6. Moulded cover – Moulded acrylic capped ABS cover retained to the moulded tanks
with Dual LockTM fastening system for quick and easy access.
3.12 Principle of operation: The pressurisation unit consists of a break tank and one/two
peripheral pumps. The break tank is supplied with mains water from either the left or
right through a flexible hose connected to a float valve and includes an overflow and
weir to maintain an AB air gap in the tank. The unit is connected to the heating/chiller
system via another flexible hose which can exit the unit on either the left or right.
The pumps are connected to the tank via a rubber connector.
A pressure transducer monitors system pressure and if a reduction in system pressure is
detected, the controller runs the pumps until the system is re-pressurised to the
required pre-set level. If the unit only has a single pump connected it will run
continuously until this level is reached, if the unit is a twin pump model the pumps
run in duty standby mode (the controller will alternate which pump starts first
to even the wear on the pumps). The pumps are fitted with non-return valves to ensure
system pressure is maintained once pressurised.
1Fig. 3
2
3
4
5
6

- 9 -
Cont ...
4 INSTALLATION
4.11 Fill valve flow restrictor guidelines: The side entry fill valve must be fitted with the
correct filter and flow restrictor combination (dependant on the mains water pressure)
into the G ½ threaded tail as outlined below:
Coloured insert - To be used for water pressure between 1 and 4 bar
White insert - To be used for water pressure above 4 bar
4.12 Cold mains feed connection: The connection to the cold water mains inlet is made using
the 15 mm compression flexible hose supplied. Ensure the rubber sealing washer
supplied with the hose is installed when the hose is fitted. When tightening ensure the
fill valve within the tank is not rotated. If the valve is rotated it may not function correctly
with the risk of flooding. The hose is made water tight with a sealing washer on
assembly, nip tight to 4 to 5 Nm for water tight seal. (Do not overtighten). See Fig. 6.
Fig. 4
Fig. 5
Fig. 6

- 10 -
4.13 Wall plate fixing:
1. If installing the Matrix Midi on a wall ensure suitable fixings for the wall structure are
used and are suitable to support the unit when fully filled with water (see
Section 10 for filled weights). The holes in the wall plate are 6 mm in diameter, the
maximum permissible screw head height is 3 mm.
2. All holes in the wall mounting plate must have fixings used in them as per the image
below, do not leave out fastenings as this will compromise the integrity of the
wall plate.
3. Ensure you have sufficent room around the area you are mounting the Matrix Midi to
allow installation, servicing and operation. See section 2.12.
4. Ensure wall plate is fixed to a flat vertical wall and the top of the plate is horizontal.
5. Retain the Matrix Midi to the wall mounting plate using the single M6 retaining screw
at the top of the wall plate.
6. Fit the plastic cover by pressing as indicated below with the palm of the hand as until
the Dual LockTM is heard to ‘click’.
Fig. 7
Fig. 8
Fig. 9

- 11 -
Cont ...
4.14 Floor installation:
1. If installed on a floor ensure the Matrix Midi is located so it cannot be kicked or
knocked over.
2. Ensure the floor surface on which the Matrix Midi is located is flat and level.
3. If possible locate the unit against a wall for added stability.
4. If the Matrix Midi is located in an area that might be subjected to flooding, mount
the Matrix Midi on a raised plinth.
4.15 Pipework connections & guidelines:
1. Before connecting the Matrix Midi to the system ensure that system flushing has
been performed correctly and all foreign matter, including pipe scale, has been
removed.
Note: Foreign material from the system coming into contact with the expansion
vessel bladder could cause premature failure of the expansion vessel.
2. Isolating valves MUST be installed on the unit inlet and outlet, before connection to
the flexible hoses to allow the unit to be isolated if required. The isolation valve
on the outlet should be of a lockshield type. See Fig. 12.
3. A drain valve must be fitted on the outlet of the Matrix Midi before the isolation
valve. See Fig. 12.
4. The connection to the heating/chilling system is also made with the supplied flexible
hose and a 15 mm compression fitting. The hose is made water tight with a sealing
washer on assembly, nip tight to 4 to 5 Nm for water tight seal. (Do not overtighten).
5. The connection to the heating/chilling system can be made to the left or right hand
side by routing the flexible hose supplied as detailed below.
Fig. 11Fig. 10
Cable tie

- 12 -
6. The flexible hose and any wiring can be retained in the desired position using cable
ties and the two metal cable retention points on the top left and right of the Matrix
Midi tank. See Figs. 10 & 11.
7. The warning pipe should be connected to a suitable drain via a tundish enabling
visual warning of an overflow condition. The overflow fitting is designed to
use 19 to 23 mm diameter plastic waste pipe or connect to G ¾ threaded pipe.
Ensure there is a demountable joint in the pipe to allow the removal of the Matrix
Midi if needed.
8. Non-return valves, pressure reducing valves and RPZ valves MUST NOT be installed
between the Matrix Midi and the heating/cooling system. These devices will prevent
the pressure sensor from reading the system pressure and will lead to incorrect
operation of the unit.
9. The Matrix Midi should be connected to the system return header along with the
expansion vessels as specified in BS 7074. See Fig. 12.
4.16 Typical installation diagram:
4.17 Vessel sizing & location:
1. System expansion vessel sizing should comply with the BS 7074 Expansion Vessel
sizing calculation.
2. The pressurisation unit and expansion vessels should be connected to the system at
the same point, to provide a neutral pressure reading.
3. A lockshield valve and drain valve should be installed at the inlet of each expansion
vessel to allow for servicing.
Fig. 12
Fig. 13
Matrix Midi
Warning pipe
Drain
valve
Isolation
valves
Expansion
vessel
Return
header
Lockshield
valve
Drain valve

- 13 -
Cont ...
5 ELECTRICAL INSTALLATION / EARTHING
5.11 Regulations: The electrical installation must be carried out in accordance with
the current national electrical regulations and installed by a qualified person.
5.12 Safety: In the interests of electrical safety a 30 mA residual current device
(R.C.D. not supplied) should be installed in the supply circuit. This may be part
of a consumer unit or a separate unit.
5.13 Before starting work on the electrical supply ensure power supply is isolated.
5.14 DO NOT allow the supply cord to contact hot surfaces, including the motor
shell, pump body or pipework. The cord should be safely routed and secured
by cable clips.
5.15 Adjacent pipes: Adjacent suction and delivery pipes should be fitted with earthing
clamps in accordance with current regulations (Fig. 14).
5.16 Earthing: This appliance must be earthed via the supply cord.
5.17 Pipework: Copper or metallic pipework must have supplementary earth bonding where
the continuity has been broken by flexible hoses or plastic components.
5.18 Additional earthing: Certain installations may require additional earthing arrangements
such as equipotential bonding. Reference should be made to the relevant regulations
concerning this subject to ensure compliance.
5.19 Connections: The Matrix Midi must be connected to a dedicated fused spur via a
lockable isolator to avoid unauthorized disconnection.
5.20 The electrical connection must be made adjacent to (not behind) the Matrix Midi to
allow disconnection of the electrical supply should the pump module need to be
removed for service or maintenance.
Earth continuity
connection
Fig. 14
Flexible
hoses Metallic
pipework

- 14 -
5.21 Wiring of connection unit:
WARNING: This appliance must be earthed.
The wires in the mains lead (supply cord) are coloured in accordance with the following
code:
Green and Yellow: Earth
Blue: Neutral
Brown: Live
As the colours of the wires in the mains lead of this appliance may not correspond with
the coloured markings identifying the terminals in your connection unit proceed as
follows:
zThe wire which is coloured green and yellow must be connected to the terminal in
the connection unit which is marked with the letter E or by the earth symbol: or
coloured green or green and yellow.
zThe wire which is coloured blue must be connected to the terminal which is marked
with the letter N or coloured black.
zThe wire which is coloured brown must be connected to the terminal which is
marked with the letter L or coloured red.
5.22 Boiler interlock safety function:
The Matrix Midi is fitted with a volt free contact specifically assigned for boiler/chiller
shut down in the event that the Matrix Midi detects system pressure above the Hi alarm
pressure or below the Lo alarm pressure.
The boiler interlock contact will be open circuit below the Lo alarm pressure and above
the Hi alarm pressure.
When the system pressure is in its normal operating pressure range (above Lo alarm
pressure and below Hi alarm pressure settings) the contact is closed circuit
Always refer to the boiler/chiller manufacturer’s instructions for correct integration.

- 15 -
Cont ...
5.23 Alarm and boiler interlock connections:
Circuits connected to the relays are limited to 5 Amps, 230 V a.c. maximum.
The Installer MUST fit a 5 Amp fuse in the circuit to the alarm relay to
protect the Matrix Midi from damage.
For connection of output relays follow the steps and images below:
1) Remove the required green connector from the right hand side of the control board.
2) Strip 6-8 mm insulation from the end of the connection wire (Max 2.5 mm2CSA).
3) Insert wire into connector and screw down terminal screws to secure (0.6 Nm max.).
NC
NO
NO
NO
Boiler Interlock
Common Alarm
High pressure alarm
Low pressure alarm
Fig. 15
Fig. 16
Fig. 17
Fig. 18

- 16 -
Cont ...
5.26 Supply Cord Replacement:
The supply cord and internal wiring within the terminal box are routed and
secured to ensure compliance with the electrical standard EN 60335-1. It
is essential that prior to any disturbance of this internal wiring, all cable
routing and securing details are carefully noted to ensure re-assembly to
the same factory pattern is always maintained.
If the supply cord is to be changed or is damaged, it must be replaced with a special cord
assembly, please contact Altecnic Ltd for further details.
On disassembly note the cord retention and routing system. Re-assemble to the same
pattern.
For information on cable connection consult the wiring diagram (Section 8.12).
4) Re-insert connector into the correct location on the control board and route the
cable to the back of the Matrix Midi and secure with a cable tie to the retainer.
Model Fuse Size (AMPS)
All models 5
5.24 RS 485 Modbus – BMS Connection:
Not functioning on this revision of the product.
5.25 Fuses: The following fuse size should be used:
Fig. 19
Retainer
Cable tie

- 17 -
Cont ...
6 COMMISSIONING
6.11 Pre-commissioning checklist:
Before starting the commissioning process the following conditions must be met. If these
conditions are not adhered to, damage to the equipment, system and property may
result.
zEnsure the unit is sited in a frost free area, away from precipitation and water sprays/
jets.
zAll necessary pipe/electrical connections should have been made to a satisfactory
standard by a qualified person.
zThe temperature and pressure at the point of connection are within the operating
limits of the pressurisation unit.
zThe heating/cooling system is fitted with a safety valve and expansion vessel sized
appropriately.
6.12 In order for the pressurisation unit and heating/cooling system to function correctly the
following conditions must be met. If these conditions have not been met, the
commissioning process should not continue.
zEnsure the system connection has been made into the heating/chiller system return
header.
zEnsure Non-return valves, pressure reducing valves or RPZ valves are NOT installed
between the pressurisation unit and the heating/cooling system.
zThe expansion vessel is pre-charged to the correct pressure (equal to initial system
design pressure).
6.13 Prior to commissioning fill the heating/cooling system via a filling loop if possible. If this
is not possible, the pressurisation unit can be used to fill the system after commissioning
has taken place. Depending on the size of the system, this may take a considerable
amount of time. The system fill function of the unit will stop after 24 hours, if further
filling is required, reset this function.
zEnsure the heating/cooling system is filled and pressurised to the required cold fill
pressure, with the water at approximately ambient temperature.
zEnsure the system is dosed with a suitable corrosion inhibitor. Note the Matrix Midi
is not designed for dosing chemicals into the system, this must be done via other
means.
6.14 Expansion vessel setting:
zTo set or check the expansion vessel charge pressure the lock-shield valve between
the Matrix Midi and the vessel must be closed and the vessel drained using the drain
valve.
zA suitable gauge should be used to check the charge pressure.
zIf the charge pressure is too high it can be reduced by releasing air from the vessel
pre-charge valve or by using a pressure gauge with an integral air release valve.
zIf the charge pressure is too low a small increase can be provided using a car foot
pump otherwise an oil free compressor or nitrogen bottle is recommended.
zWhen the correct pressure is set the Schrader valve protective cap must be replaced.
zCheck the integrity of the pipe-work. Ensure the lock-shield valve between the
system and the expansion vessel is open and the drain valve is closed.

- 18 -
6.15 Controller overview
The Matrix Midi controller is designed to be intuitive to use and allows functions and
alarms to be set by the installer/user. It also allows faults to be monitored and logged to
enable easier system fault diagnosis.
The functions are set using the 4 buttons (A, B, C & D) on the front of the controller and
with the help of on screen prompts via the back lit LCD display. On the front of the
Matrix Midi a green ‘power on’ light will be displayed whilst the unit is powered. If an
alarm or error is raised the red ‘Error’ light will be displayed.
A number pressure set points can be set using the menus, these set points are detailed
below, 1 to 4 and in the description of the function.
Button A Scrolls up through menus or increases set values.
Button B Enters menus or selects values.
Button C Scrolls down through menus or reduces set values.
Button D Returns to previous menu
TIME
PRESSURE
HIGH ALARM SET VALUE (1)
LOW ALARM SET VALUE (4)
SYSTEM PRESSURE SET VALUE (2)
DIFFERENTIAL SET VALUE (3)
PUMP 'OFF'
PUMP 'ON'
SYSTEM FILL MODE NORMAL OPERATION
SYSTEM PRESSURE
Fig. 20
Fig. 21
A
B
C
D

- 19 -
Cont ...
6.16 Function list & explanation
The functions are contained within an initial display and 3 menus:-
Setting menu (pass code protected) see Section 6.18.
Advanced setting menu (pass code protected) see Section 6.19.
Test menu (pass code protected) see Section 6.20.
6.17 Initial display
On start up, and during operation, if the Matrix Midi has had no button inputs for
1 minute, a home screen (see Section 7.11) will be displayed with system pressure,
tank water level, any active alarm and any pump that is operating at the time.
By using buttons A & C to scroll up or down the following screens will be displayed:-
System pressure
Active errors
System fill status
Pump activity
Pump run time
Alarm reset
6.18 Setting menu
(Pass code protected, if set)
The following functions can be set and modified:-
System pressure (2)
see Fig. 20
Sets the required system pressure. Set in 0.1 bar increments up to
the maximum set value for the Matrix model. Matrix Midi 135D & Matrix
Midi 230D, 3.5 bar max., Matrix Midi 150D & Matrix Midi 250D, 4.1 bar
max.
Differential pressure (3)
see Fig. 20
Sets the pressure the Matrix Midi will turn on at as the system
pressure falls. Relative to the system pressure. Set in 0.05 bar
increments below the System pressure (2), cannot be set above 0.1 bar
below the System pressure (2).
Hi Alarm (1)
see Fig. 20
Sets high system pressure alarm. Set in 0.05 bar increments above
the System pressure (2). Cannot be set below System pressure + 0.5 bar.
Alarm auto resets when system pressure is reduced below alarm level.
Lo Alarm (4)
see Fig. 20
Sets low system pressure alarm. Set in 0.05 bar increments below
the System pressure (2) - Differential pressure (3) - 0.05 bar. Alarm auto
resets when system pressure is increased above alarm level
System fill
Turns on system fill option. System fill option will turn off once the
System pressure (2) has been reached or a period of 24 hours has passed
since it was set to ‘on’. Lo alarm and Max runtime functions are disabled
whilst System fill is turned on. Pumps will stop if the System pressure (2)
or Hi alarm pressure (1) is reached.
Start Activity High
Alarm triggered if the Matrix Midi starts more than the preset
limit in 24 Hours.
Set to minimum of 100 starts per 24 hrs. Set in increments of 100.

- 20 -
Cont ...
6.19 Advanced setting menu
(Pass code protected, if set)
The following functions can be set and modified:-
6.20 Test Menu
(Pass code protected, if set)
The following functions can be set and modified:-
Common alarm relay allocation
Can be set to operate if one of the following alarms activate:-
Low water
Pump fail
Pump run time
Pump activity high
Sensor error
Common relay operation Allows the relay to operate either as normally open or normally closed.
Run time limit
Sets the maximum time a pump can run before the pump run time alarm
is activated. Set in increments of
10 minutes up to 60 minutes maximum. Disabled when the System fill
option is turned on.
Passcode change Sets a 4 digit passcode, defaults to 0000 (off). Can be user set to limit
access to Setting, Advance setting and Test menus.
Pump run on delay
Sets the time the pump will continue to run after the system pressure
(2) is reached on rising pressure. Adjustable from 3 to 120 seconds, pre-
set to 10 seconds. Reducing this time will improve the accuracy of the
pressure setting on lower volume systems
Pump start delay
Sets the time delay in starting the pump after system pressure -
differential pressure (3) is reached on falling pressure. Adjustable from 3
to 120 seconds, pre-set to 3 seconds. Increasing this time will reduce un-
wanted Matrix Midi operation during rapid system pressure fluctuations
(circulator pump starts)
Pump test Forces pump 1 (LH) or 2 (RH) to run for 5-10 seconds to enable operation
of the pump to be confirmed.
System fill volume Monitors the volume of water pumped into the system since it was last
reset. Displayed in cubic metres (1m³ = 1000 litres). Can be user reset.
Fill rate Monitors the rate at which water is flowing into the system and is
displayed as a real time flow rate (l/min).
Power interrupt log
Monitors how long the electrical power has been applied to the Matrix
Midi. Resets when power is removed or during a power cut. No user
input.
Controller info Displays software revision and pump set up. No user input.
Alarm log Displays the last 4 alarm events. Can be user reset.
Pump run time log Displays how long each pump has run. Can be user reset
Pump activity log Displays which pump has run and how long it ran for. Can be user reset.
This manual suits for next models
7
Table of contents
Popular Control System manuals by other brands
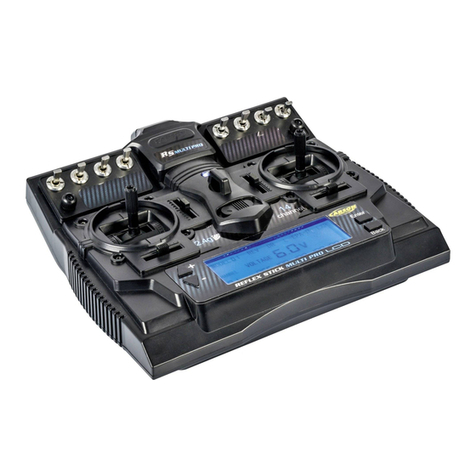
Carson
Carson Reflex Stick Multi Pro LCD 14 Channel instruction manual

Alltech
Alltech Manual Barrier quick start guide
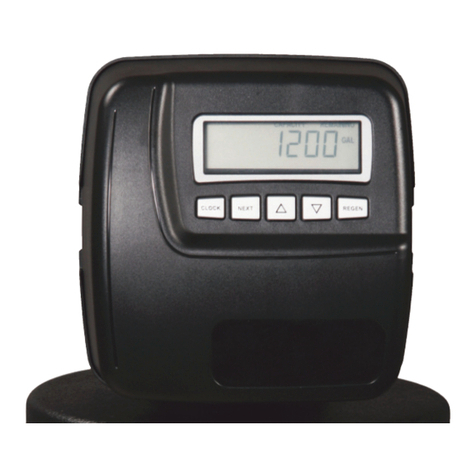
Charger
Charger WS1 Quick start manual
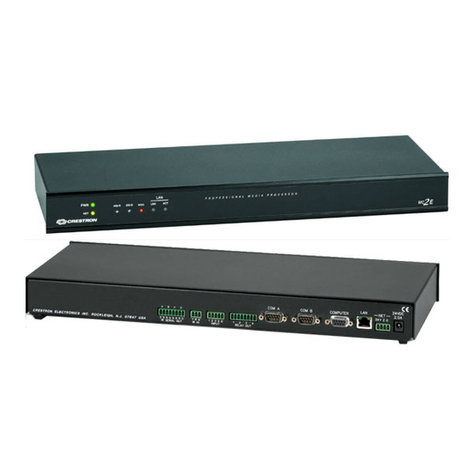
Crestron
Crestron MC2E Operation guide
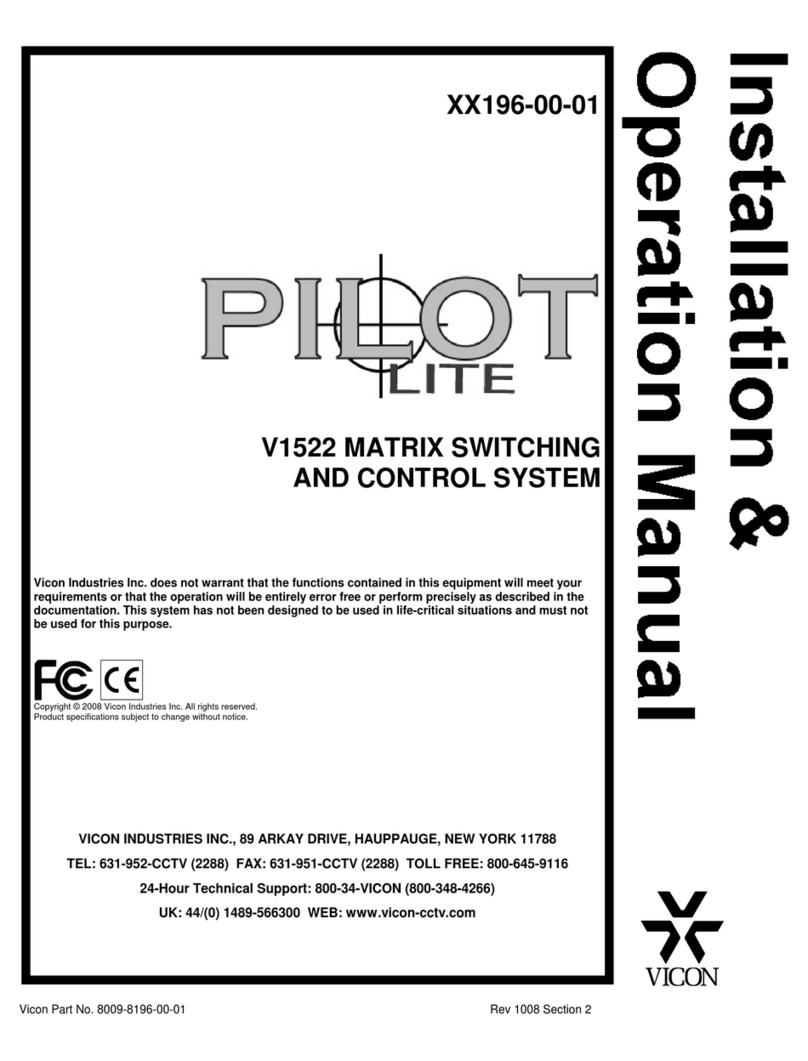
Vicon
Vicon Pilot Lite V1522 Installation and operation manual
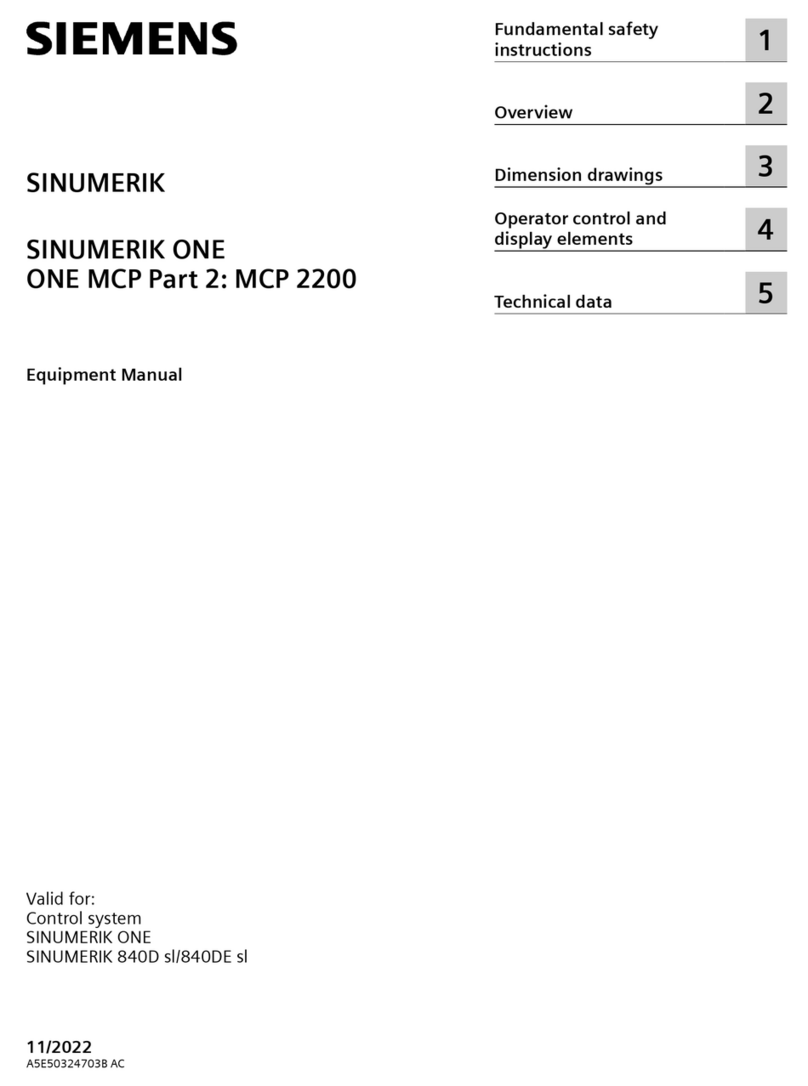
Siemens
Siemens SINUMERIK ONE MCP 2200 Equipment manual
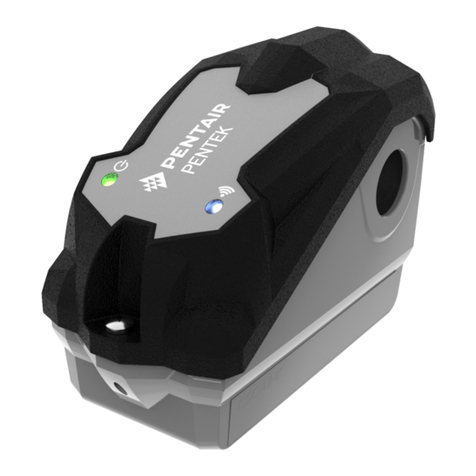
Pentair
Pentair PENTEK DEFENDER CSC-LINK Installation and operation manual

Mente Marine
Mente Marine ACS R/RP user manual
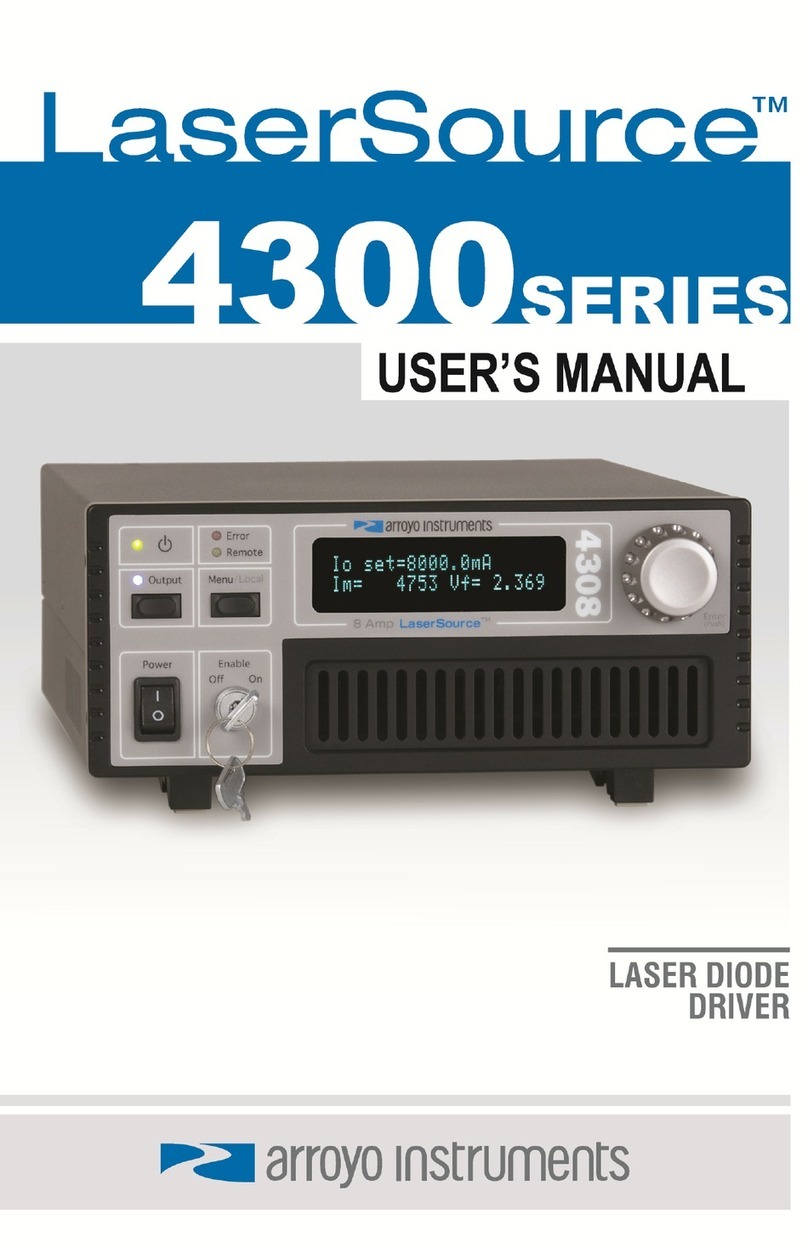
Arroyo Instruments
Arroyo Instruments LaserSource 4300 Series user manual
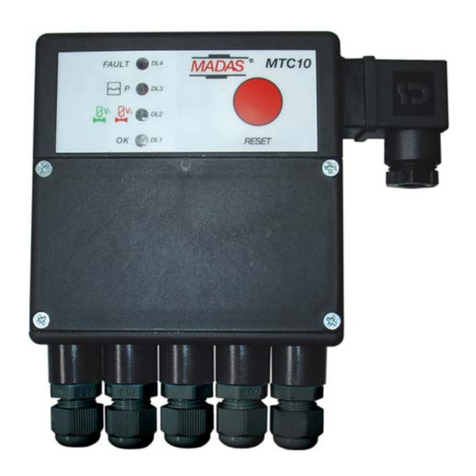
Madas
Madas MTC10 manual
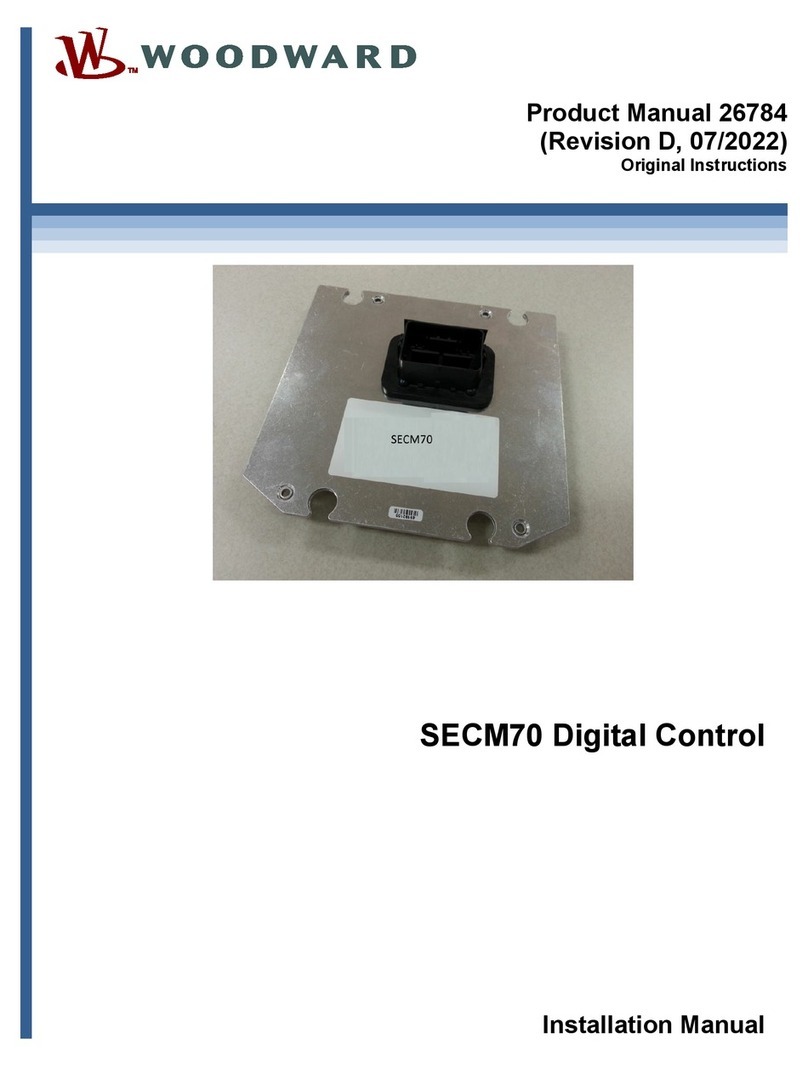
Woodward
Woodward SECM70 installation manual

YASKAWA
YASKAWA YASNAC i80 Maintenance manual