ALTHEN FDK-BT Series User manual

Germany | Switzerland | Austria
ALTHEN GmbH Sensors & Controls
Dieselstr. 2
65779 Kelkheim, Deutschland
Tel: + 49 (0)6195 - 70060
Netherlands | Belgium | Luxembourg
ALTHEN bv Sensors & Controls
Vlietweg 17a
2266 KA Leidschendam, The Netherlands
Tel: +31 (0)70 392 4421
France
ALTHEN Sensors & Controls
26, avenue de la Méditerranée
34110 Frontignan, France
Tél : 0033 (0)4 67 78 61 66
USA | Canada
ALTHEN Inc Sensors & Controls
2375 Woodacre Drive
Oceanside CA 92056, USA
Tel: +1 858-633-3572
Other Countries
For our international sales
partners please contact us
www.althensensors.com
Railway FDK-BT Series
Manual
FDK-BT Series
Certified according to ISO 9001:2008
04.2017 | version 20160122 Rev 1.2

1. Safety precautions and measurement conditions ....................................................................….…......3
2. Electromagnetic compatibility.........................................................................................................….…...3
3. General information........................................................................................................................….……..3
4. Basic data and performance characteristics ......................................................................................…..3
5. Example of item designation when ordering ..........................................................................................4
6. Complete set to be supplied.........................................................................................................….…......4
7. Design ........................................................................................................................................….…………..5
7.1. Electronic gauge.................................................................................................................…..…......5
7.2. Indication device (option) ..........................................................................................................…..5
8. Operation principle ........................................................................................................................…..….....7
9. Working with the gauge and working in autonomous regime ...........................................................7
9.1. Gauge turn-on .................................................................................................................….….........7
9.2. Single measurement......................................................................................................….…...........7
9.3. Measurement with averaging .............................................................................................…........8
9.4. Gauge turn-out ..................................................................................................................….….......8
10. Indication parameters setup...................................................................................................….…...........8
10.1. Bluetooth ON/OFF...........................................................................................................….….........8
10.2. Image rotation.................................................................................................................….…..........9
10.3. Image brightness set-up ................................................................................................…............10
10.4. Millimeters-Inches -Tapes display set-up ..................................................................................10
11. Service operation modes ....................................................................................................….……...........11
11.1. Calibration conditions ....................................................................................................….….........11
11.2. Get into operational modes ...........................................................................................….…........11
11.3. Calibration of the sensor zero ..........................................................................................….........11
11.4. Calibration of the device base .............................................................................................…......12
12. Working with the gauge and PDA ...........................................................................................….…........13
12.1. Operation principle ........................................................................................................….….........13
12.2. Gauge and PDA activation ................................................................................................….….....13
12.2.1. Gauge turn-on .........................................................................................................….…….........13
12.2.2. PDA turn-on...............................................................................................................….…….......13
12.3. On-line measurement ....................................................................................................….…........14
12.4. Measurements with database maintenance..............................................................................15
12.5. Browsing the database .....................................................................................................….….....17
12.6. Saving database on flash memory card .....................................................................................17
13. PDA program setting..................................................................................................................….…......18
13.1. Selection of measurement units ..................................................................................................18
13.2. Data and Time settings....................................................................................................…..….....18
13.3. Tolerances settings ........................................................................................................….…........19
13.4. Database selection ........................................................................................................….….........20
13.5. Selection and formation of measurement scheme..................................................................20
13.5.1 Selection or removal of the measurement scheme...............................................................20
13.5.2 Formation of a new measurement scheme ............................................................................21
13.5.3 Loading of a new measurement scheme ............................................................….…...........21
13.6. New electronic gauge connection ....................................................................................….......21
13.7. Selection and changing of language and terminology ...........................................................22
13.7.1 Preparation and installation of language support file ..........................................................22
13.8. PDA software version viewing.....................................................................................................22
13.9. Deactivation........................................................................................................................….…....23
14. Working with the gauge and PC...................................................................................................…......23
14.1. Program starting ....................................................................................................................…....23
14.2. IDK-PC connection ..............................................................................................................….…...23
14.3. Measurement....................................................................................................................….…......24
15. Database maintenance software ...........................................................................................….……....24
16. Charging of built-in accumulator battery ................................................................................….…....25
17. Warranty policy.......................................................................................................................….………....25
18. Annex 1. Procedure of installation of Bluetooth connection between IDK and PC.......................25
19. Annex2.Measurementdevicesforrailwaytransport .….…………….........................….….……......30
Contents
Page 2/29

1. Safety precautions and measurement conditions
· The metering accuracy depends greatly on the wheel surface quality. There-
fore it is necessary to carry out the check and presorting of the wheel surface
roughness and flaws before measuring the diameter.
· Prior to place the gauge onto the wheel there is a need to clean the wheel
parts that contact with gauge ball bearings, side supports and measuring tip,
of the mud.
· At arranging the gauge, do not allow hitting its supports on the wheel and any
measuring tip side hitting
· At arranging the gauge, do not apply strong forcing in the direction of the
measuring tip movement. It can result in the gauge sag, that will bring about
the uncertain metering result
· It is necessary to inspect the gauge supports periodically and to cleanse them
· To save the battery power the display extinguishes if there were no buttons
pressings for 60 seconds, at that only blinking dot is shown. Pressing any but-
ton just turns on the display and does not act in any other way in this case.
2. Electromagnetic compatibility
The gauge has been developed for use in industry and meets the requirements of the
following standards:
· EN 55022:2006 Information Technology Equipment. Radio disturbance
characteristics. Limits and methods of measurement.
· EN 61000-6-2:2005 Electromagnetic compatibility (EMC). Generic standards.
Immunity for industrial environments.
· EN 61326-1:2006 Electrical Equipment for Measurement, Control, and Laboratory
Use. EMC Requirements. General requirements.
3. General information
Electronic gauge is designed for measuring wheel rolling circle diameter (amount of
wear) of railway, metro and tram in the course of checkup, examination, repair and
formation of wheel sets. Measurements are made directly on rolling stock without
wheelset roll-out.
4. Basic data and performance characteristics
Name of parameter Value
Measurement range, mm 400…1400 or on request
Measurement error, mm ±0.2
Indication discreteness 0.1mm, 0.01mm * or 0.01 inch **
Position of measurement, S, mm On request
Distance between axes of ball bearings (base), mm
and measurement range, mm
122±0.5(400…750mm)or
200±0.5(400…950mm)or
250±0.5(600…1400mm)or
300±0.5(720…1400mm)
Display build-in, LED
Operating temperature, 0C -5…+55
Power supply – built-in rechargeable battery two AAA 1,2V
The number of measurements that can be taken before battery recharge is
not less than 1000
Weight, kg 0,5
Page 3/29

5. Example of item designation when ordering
FDK-S/B-MIN/MAX-X-BT
Symbol Description
S Position of measurement, mm
B Base, mm
MIN Bottom of measuring range, mm
MAX Up of measuring range, mm
X Positionofindication.A – Indicationisatthesideofsidesupports(figureA),B
– Indicationisatoppositeside(figureB)
BT Bluetooth presence*
* The gauge with Bluetooth can work in autonomous regime and together with FDRF303 PDA or PC, with
measurements saving in database.
Example: FDK-70/250-850/1260-A-BT. Position of measurement – 70 mm; base of the
gauge – 250 mm; bottom of measuring range – 850 mm; up of measuring range – 1260
mm; position of indication – A, BT – Bluetooth presence .
Fig. A Fig. B
6. Complete set to be supplied
Name Quantity Weight, kg
Wheel diameter measuring gauge FDK series 1 piece 0,5
Charger 1 piece 0,2
FDRF303 – PDA (option) 1 piece 0,4
Charging device 5V 3.0A for PDA (option)
Manual 1 piece
Case 1 piece
Database management system (CD)
Calibration tools (option) on request
Flat block FDRF510.11.000 (fig.4) -
Reference wheel block for calibrating FDRF510.11.850 (fig.5) -
Page 4/29

7. Design
7.1. Electronic gauge
The gages with bases of 200, 250 and 300 mm are shown on the Figure 1, the gage
with base of 122 mm – on Figure 1.1. Electronic gauge contains two ball supports to
place the gauge onto the roll surface, two side magnet supports to base the gauge to
the wheel edge and a measuring tip.
There are a digital numeric display and control buttons on the front panel of the
gauge.“Charge”connectorforchargingdeviceconnection and Bluetooth indication
LED are situated on the top panel of the gauge.
Figure 1
Figure 1.1
7.2. Indication device (option)
PDA is designed for control of the laser scanning module, data reception from the
scanning module, indication of measurement results, parameter input and data
storage.
Page 5 /29

Figure 2
Fig. 2 indicates:
(1) Turn-on button
(2) Charging indication, red/blue LED
(3) Connector to PC USB-port or charging device
(4) Flash memory card connector
(5) Stylus
(6) Bluetooth antenna
Overall dimensions of PDA are shown in figure 3.
Figure 3
Page 6/29

8. Operation principle
Themeasurementofthediameterisperformedaccordingtothe“threepoints”
technique, without the complete wheel coverage. The measurement method is based
on the diameter calculation by the known length of the segment chord (the distance
between the ball bearings centers), which is obtained at placing the gauge onto the
wheel.
The suggita of the segment is measured by means of the displacement converter.
Video presentation is available on request.
9. Working with the gauge and working in autonomous
regime
9.1. Gauge turn-on
Press Red buttontoturnonthepower.Thedisplayshows“ErrP”message if the
accumulator battery voltage became lower then the control level. In this case the short-
term work is possible after pressing any key.
9.2. Single measurement
To perform measurement, it is necessary to:
· turn the power on (press Red button). Thedisplayshows“- - - - -”;
· place the gauge onto the wheel;
· make sure the ball supports are tight against the roll surface and side sup-
ports are adjacent to the edge of the wheel;
· press Green button.
· in a 1 second the display will show the value of the wheel diameter.
For viewing the result of measurement with indication discreteness of 0.01mm (it
is accessible only in a mode of direct indication) it is necessary to press Blue button,
thus displayed result will be shifted to the left on one digit. Next pressing Blue button will
lead to return of indication to a starting position:
Page 7/29

9.3. Measurement with averaging
The program of the wheel diameter calculation contains an averaging algorithm that
allows eliminating the surface defects influence on the diameter measuring result.
All the results of metering, performed after the Red button pressing, are averaged.
The measurement is meant to be Green button pressing.
To carry out measurements it is necessary to
· turn the power on (press Red button).Thedisplayshows“- - - - -”;
· place the gauge onto the wheel
· make sure the ball supports are tight against the roll surface and side sup-
ports are adjacent to the edge of the wheel;
· press Green button;
· display shows the value of pressing counter “n x”,where x– quantity of av-
eraged values;
· in a 1 second display shows an average value over the set of metering (over
the quantity of Green button pressings)
· move the gauge to a new position and repeat the measuring.
(The total quantity of measurements averaged in this way can run up to 9999.)
· Press Red button to reset averaging result at switching to another wheel.
For viewing the result of measurement with indication discreteness 0.01mm (it is
accessible only in a mode of direct indication) it is necessary to press Blue button, thus
displayed result will be shifted to the left on one digit. Next pressing Blue button will
lead to return of indication to a starting position.
9.4. Gauge turn-out
The gauge turn-out occurs automatically. The display extinguishes if there were no
buttons pressings for 60 seconds, at that only blinking dot is shown. If there were no
button pressings for 4 more minutes, the gauge is turned out completely. You can
turn the gauge off by long pressing Red button (more then 3 sec.).
10. Indication parameters setup
10.1. Bluetooth ON/OFF
To switch Bluetooth ON it is necessary to:
· turn the power on
· press Blue button and keep it pressed for more than three seconds
· displaywillshow“bt On”
· to turn Bluetooth off press Green button.Displaywillshow“bt OF”
Page 8/29

· to save the changed parameters press Red button. The display shows
“SAUE”message,pressthe Green button to confirm saving and Red button
to cancel saving of the changed parameters
10.2. Image rotation
To rotate the image it is necessary to:
· turn the power on (press Red button);
· press Blue button and keep it pressed for more than three seconds;
· display will show "bt On" or "bt OF";
· press Blue buttonagain. Displaywillshow“Up”
· by the pressing of Green buttonturnovertheimage:themessage“Up”will
be turned over 1800;
· to save the changed parameters press Red button. The display shows
“SAUE”message,pressthe Green button to confirm saving and Red to can-
cel saving of the changed parameters;
Image rotation function allows observing the result in the way comfortable for the
operator regardless of the gauge placement direction.
Page 9/29

Notes:
- indication discreteness of 0.01mm is accessible only in a mode of direct indication;
- the separation point is indicated at the top side of the screen in the reverse indication
regime.
10.3. Image brightness set-up
To change the display brightness it is necessary to:
· turn the power on (press Red button).;
· press Blue button and keep it pressed for more than three seconds;
· display will show "bt On" or "bt OF";
· press Blue button again until “brt X”messageappearsonthedisplay;
· choose the necessary brightness value by Green button pressings;
· to save the changed parameters press Red buttonthedisplayshows“SAUE”
message, press the Green button to confirm saving and Red to cancel saving
of the changed parameters;
At brightness choosing one should take into account that increased brightness
enhances power consumption and decreases the period till battery recharge moment.
10.4. Millimeters-Inches -Tapes display set-up
To change the mode it is necessary to:
· turn the power on (press Red button).;
· press Blue button and keep it pressed for more than three seconds;
· display will show "bt On" or "bt OF";
· press Blue buttonagainuntiltheeither“SI”or“Inch” or“Tape” message
appearsonthedisplay.“SI” – measuringresultswillbeshowninmm,“Inch” –
measuring results will be shown in inches; “Tape” – measuring results will be
shown in tapes.
· choose the necessary value by Green button pressings;
Page 1 0/29

· to save the changed parameters press Red buttonthedisplayshows“SAUE”
message, press the Green button to confirm saving and Red to cancel saving
of the changed parameters
11. Service operation modes
This section contains the description of the modes for the check of device efficiency
and calibration. As erroneous actions in this mode can lead to invalid measurement
results, only specially trained personnel should perform such operations.
11.1. Calibration conditions
Calibration of the device is not necessary in the current work. It is necessary only
after producing, repairing and also after checking with negative result.
To perform calibration the following means are necessary:
· Calibration plate with the deviation from flatness less then ±0,5 um for 250
mm length (or Flat block FDRF510.11.000, figure 4);
· Johansson gauge;
· reference wheel of the known diameter (or Reference wheel block
FDRF510.11.850, figure 5)
11.2. Get into operational modes
· To get into the operational modes it is necessary to turn-off the device (press
Red button more then 3 seconds).
· Keeping Green button in pushed position turn-on the device (press Red but-
ton).
· Displayshows“CLbr.0”message(themodeofcalibrationofthesensor's"0").
· To get into this mode it is necessary to press Green button (see. p. 11.3).
· For transition to next mode it is necessary to press Blue button.
· Displayshows“CLbr.b”message(themodeof device base calibration).
· To get into this mode press Green button (see. p.11.4).
· To get out the mode of calibration press Red button.
11.3. Calibration of the sensor zero
· When zero calibration mode being enabled, the display shows the Johansson
gauge value used for calibrationinincrementsof0.5µm.
· If editing of the Johansson gauge value is not required, go to the next step. To
edit the Johansson gauge value, press the Blue button, and the digit to be ed-
ited starts blinking. Changing over between the digits is made by pressing the
Blue button while changing of values is made by pressing the Green button.
When editing is finished, press the Red button and confirm or cancel saving of
the parameter by pressing the Green button or Red button, respectively.
· Press the Green button, and the Johansson gauge value starts blinking,
which means that the device must be placed onto a flat plate and a Johans-
son gauge with nominal value of the previous step must be placed under the
measuring tip. The Johansson gauge must be tightly fitted to the flat plate and
supports and balls of the device must be firmly forced against the plate.
· Press the Green button, and the display shows current reading of the sensor
in its own coordinate system. By moving the device, assure that repeatability
of measurement results is obtained.
Page 1 1/29
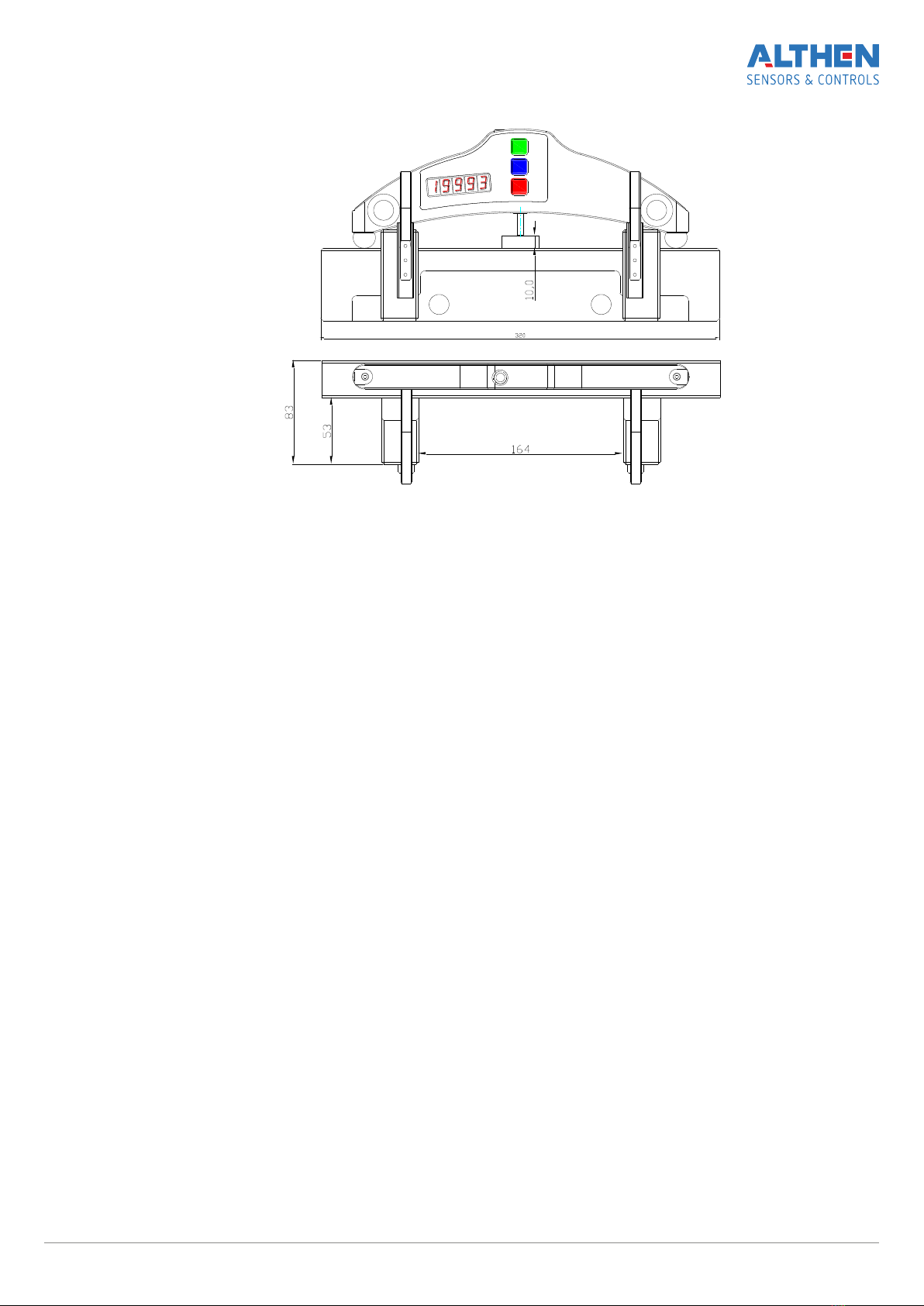
RF510.11.000
Figure 4
· If readings of the sensor are sufficiently stable, press the Blue button. Sensor
zero position is calculated in the device coordinate system, and prompt ap-
pears to save calibration results. Press the Green or Red button to confirm or
cancel saving of the results, respectively.
11.4. Calibration of the device base
· Device base calibration mode being enabled, the display shows the value of
reference diameter used for calibration.
· If editing of the diameter value is not required, go to the next step. To edit the
diameter value, press the Blue button, and the digit to be edited starts blink-
ing. Changing over between the digits is made by pressing the Blue button
while changing of values is made by pressing the Green button. When editing
is finished, press the Red button and confirm or cancel saving of the parameter by
pressing the Green button or Red button, respectively.
· Press the Green button, and the reference diameter value starts blinking,
which means that the device must be placed onto a gage with the diameter
value set at the previous step. The device supports must be firmly forced
against the reference block.
· Press the Green button, and the display shows current reading of the sensor
in the device coordinate system. By moving the device, assure that repeatability of
measurement results is obtained.
· If readings of the instrument are sufficiently stable, press the Blue button. Device
base value is calculated, and prompt appears to save calibration results.
Press the Green or Red button to confirm or cancel saving of the results,
respectively.
Page 1 2/29

Figure 5
NOTE: Video-help for calibration procedure is available on request.
12. Working with the gauge and PDA
12.1. Operation principle
Operator mounts the gauge onto the wheel to be measured. Having received a
command from PDA, the gauge performs the measurement of the wheel diameter.
Measurement result is displayed on PDA, can be saved in the PDA memory, and
transferred to the PC database. Simultaneously, additional parameters can be saved:
operator number, side identifier (left or right wheel), axis number, locomotive
(carriage) number, wheel pair number, etc.
12.2. Gauge and PDA activation
12.2.1. Gauge turn-on
Press Red buttontoturnonthepower.Thedisplayshows“ErrP”messageifthe
accumulator battery voltage became lower then the control level. In this case the short-
term work is possible after pressing any key.
12.2.2. PDA turn-on
Turn the PDA on by pressing the button (1), Fig. 2. Activation indication (2) will show a
green LED lit.
After the PDA is switched on, some time will pass until automatic wireless
communication is set between the gauge and the PDA, which is accompanied
by blinking of a blue LED (1) on the diameter gauge. The LED goes out when
the link is established.
The PDA screen will show the main program window containing: main menu;
indicators of PDA charging degree; indicator of Bluetooth connection showing serial
number of the gauge with which connection is established and the Measurement
button.
Page 1 3/29
RF510.11.XXXX

12.3. On-line measurement
To take measurements:
· turn-on the gauge, the display shows — “- - - - -”;
· turn-on PDA;
· press Measurement button on the screen of PDA; PDA is activated in
measurement regime and display shows:
· place the gauge onto the wheel;
· make sure the ball supports are tight against the roll surface and side sup-
ports are adjacent to the edge of the wheel;
· press Green button. (Note: hereinafter, the button, marked by green or red
color is a corresponding button on the gauge or PDA screen). In a 1 second
the displays of the gauge and PDA will show the value of the wheel diameter.
When the diameter goes beyond set limits its value is highlighted with red col-
or:
"Measurement"
button
Menu
PDA charging
Bluetooth
connection with
the gauge #02010
Page 1 4/29

Buttons:
- diameter measurement
- averaging reset
to continue the measurement with averaging:
· press Green button;
· displayshowsthevalueofpressingcounter“n x”,where x– quantity of
averaged values;
· in a 1 second display shows an average value over the set of metering (over
the quantity of Green button pressings)
· move the gauge to a new position and repeat the measuring. (The total quan-
tity of measurements averaged in this way can run up to 9999.)
· Press Red button to reset averaging result at switching to another wheel.
12.4. Measurements with database maintenance
A fully functional work with the gauge involves maintenance of the measurements
database.
To take measurements:
· select in the main menu Profilometer > Measurement, the window of
parameters input will appear
Page 1 5/29

· If necessary, fill in/edit the required fields
· to save parameters, press the Save button, and the program will offer the
selected measurement scheme (see par.13.5.):
Designations:
- order number of the car to be measured (number of cars in the
train);
- number of the car to be measured;
- editing of the input wheel parameters;
- a previous/subsequent wheel;
- a measured wheel;
- a wheel to be measured next time;
- a non-measured wheel;
- a measured wheel to be measured again
- measurement.
· Measure the wheel offered by the program (highlighted in green color), as it is
shown in par. 12.3.
After the measurement, the PDA will show the value of diameter. When a diameter falls
out of the specific tolerance, its value is indicated with red color.
Page 1 6/29

· when a satisfactory result is obtained, press Save on the display to save it
· the program will offer to pass to measurement of the next wheel in accordance
with selected scheme of measurement
12.5. Browsing the database
To browse the database:
· select Service > Profiles in the main window. View on the screen
· for data filtering select data, series and number of locomotive
Buttons:
– delete selected data
12.6. Saving database on flash memory card
One of the ways to transfer database from PDA to PC is to use flash memory card.
To save database on the card, proceed as follows:
· connect cable FDRF505.42 to the PDA universal connector
· insert flash card to the respective cable connector
· select Device > Save to USB flash in the main program window
Page 1 7/29

· if saving is successful, the screen will show Data saved on USB Flash
· remove flash card from the cable
13. PDA program setting
Prior to starting work with the gauge, PDA program setting must be performed.
13.1. Selection of measurement units
All parameters as well as measurement results can be presented in the metric
system (millimeters) or in the English system of units (inches). To set measurement
units, it is necessary to
· select IDK >Units of measuring>[mm/inch]
· select mm or inch option
13.2. Data and Time settings
To set data and time:
· select IDK > Data/Time in main window of the program. View on the
PDA screen:
Page 1 8/29

· write data and time
· press Save
13.3. Tolerances settings
The program automatically controls measured geometric parameters for going out
beyond the tolerances set. It is possible for the user to create groups of tolerances.
Control of parameters will be performed for a selected group. To set tolerances it
is necessary to:
· select Service > Tolerances in the main window. View on the screen:
· adjust tolerances in the selected group or add a new group of tolerances and
write corresponding values. All values are in micrometers.
Buttons:
- add new group of tolerances;
- delete selected group of tolerances;
- edit selected tolerance;
- exit.
Page 1 9/29

13.4. Database selection
If necessary, measurement results are saved in the PDA database. The program makes it
possible to simultaneously create and store several database files connected with a
concrete date of taking measurements. To select a database file,
· choose Service > DB files in the main window menu. The screen will show:
· To create a new database, press New DB. File with the name
wp_yy_mm_dd.ikp will be formed automatically, where yy_mm_dd is the
current date;
· to select the available database, activate the line with the file name and press
Select DB;
· to delete the selected file press Delete;
· to delete all files press Delete all;
· to save file in TXT form press Export;
· to exit from the window press Exit
13.5. Selection and formation of measurement scheme
Measurement scheme is meant as a sequence of making measurements/processing of
wheels in the rolling stock. The program automatically offers operator to perform
measurement on a concrete wheel in accordance with selected scheme of wheel
processing.
The program contains several preset schemes. Besides, the user can form his own
measurement scheme.
13.5.1 Selection or removal of the measurement scheme
To select a measurement scheme in the main window menu:
· select Service > Schemes. View on the screen:
Processing
scheme
Page 2 0 /29
This manual suits for next models
1
Table of contents
Other ALTHEN Measuring Instrument manuals