AMI 210BR User manual

08/31/2018 Made in the USA
AMI
Oxygen Analyzer Manual
Model 210BR
Costa Mesa, CA

AMI Analyzer Manual Contents i

AMI Analyzer Manual Contents ii
Contents
Preface 1
Thank you! 1
Caution 1
Address 1
Model 210BR Oxygen Analyzer 2
Introduction 2
Features: 2
Oxygen sensor: 4
Sensor Warranty: 4
Instrument Warranty: 4
Receiving the analyzer 4
Important: 5
Points to consider first! 5
Location: 6
Safety Considerations: 7
Installation Procedure 8
Analyzer Description 20
Basic description: 20
Drawings: 21
General Information 23
Basic knowledge about oxygen measurement 23
Analyzer operation 24
Sample tubing and components 24
Exhaust 24
Calibrating the analyzer 24
Using the analyzer 26
Output Range 26

AMI Analyzer Manual Contents iii
Security: 26
Communications 26
Advanced Features 27
Maintenance and troubleshooting 28
Maintenance: 28
Periodic Calibration: 28
Sensor Replacement: 28
Sensor replacement cautions: 29
Sensor replacement procedure: 29
Troubleshooting 30
Basics of oxygen troubleshooting 30
Accessories 34
Specifications and Disclaimer 37
Specifications: 37
Disclaimer 38

AMI Analyzer manual 210BR 1
Preface
Thank you!
We would like to thank you for purchasing the most advanced trace oxygen analyzer available. We have
gone to great lengths to make this analyzer as simple, and complete, as possible. It includes our patented
cell block, (patent numbers 5,728,289 and 6,675,629), and our patented sensor. It uses the most
sophisticated electronics with complete microprocessor control to provide many advanced features while
retaining the extreme ease of use for which this line of analyzers is famous. It is CSA approved to UL
standards for use in a wide variety of flammable gas applications in general purpose and Class 1 Division 1
Group BCD hazardous areas, such as natural gas, petrochemical refining and head space monitoring. With
the optional demister and liquid rejection probe accessory it provides a complete system for monitoring
trace oxygen in harsh environments with difficult, hot and wet samples.
Please verify that the analyzer was not damaged in transit. If so please contact the shipper as well as AMI.
Caution
Read and understand this manual fully before attempting to use the instrument. In particular understand
the hazards associated with using flammable or poisonous gases.
Address
Advanced Micro Instruments
225 Paularino Avenue
Costa Mesa, CA 92626
(714) 848-5533
www.AMIO2.com
Last Revised 08/31/2018

AMI Analyzer manual 210BR 2
Model 210BR Oxygen Analyzer
Introduction
The Advanced Micro Instruments Oxygen Analyzer Model 210BR provides the latest in high precision oxygen
measurement. It is specifically designed for use with flammable gases in hazardous areas, and includes a
number of features that make it particularly suitable for this application. It is approved by CSA to UL
standards for Class 1 Div. 1 Group BCD using flammable gas samples.
This manual covers software version 5.24.
Features:
Compact size
Unique patented cell block
4 Selectable output ranges
Auto-ranging display with user-selectable
output range
Three levels of security access settable via the
USB interface: no front panel settings
allowed, span only allowed and complete
access allowed.
Front panel sensor access
Optional air or span gas calibration, no zero
gases required
Virtually unaffected by hydrocarbons or other
oxidizable gases
Integrated sample system
Metering valve flow control
H2S resistant sensor up to 10ppm H2S
Optional 500ppm H2S resistant sensor
available
High accuracy and fast response
Large liquid crystal display
Bi-directional serial output with simple
protocol
Bi-directional Modbus™support over RS485
multi-drop loop
Backed by a two year warranty (excluding
sensor)
Choice of analog outputs: a current output of
4-20mA or a voltage output of 1-5V, both
isolated
Two fully adjustable alarm relay contact
closures 24VDC/110VAC @ 5A resistive
Programmable alarm delay
Front panel alarm and output hold off/bypass
with programmable delay
Programmable pulse drivers for latching-type
solenoid valves
Built-in data logging with real time clock
Logs oxygen, temperature, power supply
voltages
Optional low-power heater for stand-alone
operation in inclement weather
Approved for Class 1 Div. 1 Group BCD
Optional 117 VAC/12-24VDC operation
Automatic logging of low power, start up and
calibration events
USB connectivity

AMI Analyzer Manual Model 210BR Oxygen Analyzer 4
Oxygen sensor:
AMI manufactures its own electrochemical sensor. It measures the concentration of oxygen in a gas stream,
using an oxygen specific chemistry. It generates an output current in proportion to the amount of oxygen
present, and has zero output in the absence of oxygen, thus avoiding any requirement to zero the analyzer.
The cell is linear throughout its range. The span calibration may be performed using standard span gases or
ambient air. Unlike competitive sensors, the AMI sensor is made using a high capacity metallic body that
provides long life with about twice the active ingredients usually used.
Sensor Warranty:
The sensor is warranted to operate for a period determined by its class. If the sensor ceases to operate
correctly before this time has elapsed, contact AMI for a return authorization for evaluation. If there is any
evidence of defective material or workmanship the sensor will be replaced free of charge.
NOTE: Any evidence of abuse or physical damage, such as a torn membrane, will void the warranty.
Instrument Warranty:
Any failure of material or workmanship will be repaired free of charge for a period of two years from the
original purchase (shipping date) of the instrument. AMI will also pay for one way shipment (back to the
user).
This warranty does not cover the sensor, which is covered by its own warranty (see above).
Any indication of abuse or tampering will void the warranty.
Receiving the analyzer
When you receive the instrument, check the package for evidence of damage and if any is found, contact
the shipper.

AMI Analyzer Manual Important: 5
Important:
This section contains important information to do with safety and installation. Please don’t skip it!
Points to consider first!
Environment –what is the temperature range going to be where the analyzer will be installed? If the
temperature is going to go below freezing, you either need a heated version, a heated version in an extreme
weather enclosure, or to place it in a temperature controlled shelter. Also, make sure it won’t get too hot in
the summer –you may need to ventilate or even put it in an air conditioned building. Use a solar panel as a
sunshield if one is to be used. The standard (non-heated) temperature specification is 25ºF to 115°F; with a
heater it can go to -20ºF; in the optional extreme weather enclosure it can go to -40°F.
Sample conditions –if your sample is hot and wet, you will need to keep water from condensing in the
sample line or analyzer. The AMI demister brings hot and wet gases back to ambient temperature and
allows the condensation and entrained liquids to fall back into the pipeline (no draining is necessary, unlike a
coalescing filter which requires routine maintenance). The Liquid Rejection Probe stops occasional slugs of
water from contaminating the analyzer, and acts as a check valve, so that if a compressor goes down
drawing a vacuum on the line, air is not drawn back into the analyzer through its vent - it is available with a
built-in pressure regulator for high pressure lines (up to 1200psig).
Power supply –if you are going to run the unit off solar power, using a battery, you need to size both the
battery and the solar panel correctly. The analyzer draws about 30mA at 14.4 volts, but if you select the 4-
20mA output option this will go up to about 60mA. A heater draws up to 1.67A when the temperature is at
its coldest. We suggest that you use the solar panel as the sunshield for the analyzer by mounting it right
over the analyzer.
Electrical connections –make sure you use conduit seal-offs on the two conduit entrances located on the
bottom of the explosion proof housing, and we suggest you also use universal couplers so you can
disconnect the analyzer without cutting wires (if the unit has to be moved or removed for service).
Following best electrical practices, run the analog output connections separately from the power and alarm
connections. Modbus communications if used should be run with the analog output wiring, using twisted
pair wires for both circuits. Run the alarm wires in the same conduit as the power wires.
Solenoid valves –if the analyzer is going to be used to control gas flow (such as to shut in contaminated gas)
using solenoid valves, consider using latching type valves and the analyzer pulse feature so as to minimize
power consumption, particularly if you are using a battery as the power supply. Standard solenoid valves
require power to remain open (or closed), whereas latching valves require power only when changing their
position. This conserves a lot of power.

AMI Analyzer Manual Important: 6
Figure 1. Typical installation showing LRP and demister
Location:
Mount the analyzer on a wall or on a 2” pipe in a general purpose, Class 1 Division 1 Group B,C,D area or
Class 1 division 2 Group B,C,D area. When equipped with the optional heater, or the extreme weather
enclosure, it may be mounted outdoors, though it should be given a sun shield if in direct sunlight (consider
using the solar panel if one is used as the sunshield). Mount it at a suitable viewing level.

AMI Analyzer Manual Important: 7
Safety Considerations:
The unit MUST be installed according to the requirements in the National
Electrical Code, particularly those of article 500, the section that deals
with hazardous atmospheres.
For AC units, an external circuit breaker or switch MUST be provided to
allow disconnection of the AC power, in close proximity to the analyzer
and within easy reach of the operator!
The ground stud on the main panel MUST be made to a good earth, with a
resistance to ground of less than 1 Ohm USING AT LEAST 16AWG WIRE.
117VAC version is to be installed only in installation (overvoltage) category I or II.
ELECTRICAL SEAL-OFFS ARE REQUIRED ON ALL THE CONDULET ENTRIES, whether the area classification is
Division 1 or Division 2. We suggest that you use universal couplings between the analyzer and the seals so
that you can disconnect the analyzer if necessary without cutting wires.
The unit is designed for installation in either a general purpose or a Class 1 Div. 1 or Div. 2 Group B,C,D area,
but it is also designed so that a hazardous gas may be introduced into its main enclosure (the box on the
right hand side) as it is intrinsically safe. This gas may be any group B,C or D gas.
The unit consists of two enclosures mounted on a back panel. The smaller enclosure on the left is explosion-
proof and contains the electrical connections for the user, and also the power supply and safety
components for the other enclosure.
The larger enclosure on the right contains the controls, the analytical circuitry, the sample handling
components and the oxygen sensor. This circuitry is designed for intrinsic safety and approved as meeting
requirements for Class 1 Div. 1 Group B,C,D by CSA to UL standards.
There is a USB connection available from the explosion-proof section. This may be wired up permanently, or
may be used occasionally by removing the explosion-proof cap. If so, the area MUST be declassified first.
The sample vent should be brought to a safe place –don’t let it vent a flammable sample inside a
meter/analyzer building.

AMI Analyzer Manual Installation Procedure 8
Violation of the National Electrical Code installation requirements may
cause a fire or explosion, with potential for serious injury or loss of life.
Installation Procedure
Figure 2. The 210BR
1. Mount analyzer in a shelter if possible, at a convenient eye level, not too close to the right wall.
The basic analyzer is designed for operation between 25ºF and 115ºF. It is available with a heater, which
expands its temperature range to -20ºF, and an additional extreme weather enclosure which expands it to -
40ºF. The gas connections are made on the right side of the analyzer, while the electrical connections are at
the bottom of the explosion proof enclosure on the left side. Explosion proof seals must be used, so be sure

AMI Analyzer Manual Installation Procedure 9
to leave enough room under the analyzer for these, and for the conduit run. Leave enough space on the
right side of the analyzer for the gas connections.
The analyzer can be mounted on a wall, or on a two inch pipe.
If the analyzer is mounted outside, make sure it has some kind of sun shade. If it is DC powered with a solar
panel, use the panel to give the analyzer shade.
If the analyzer is mounted in a building with other equipment, make sure it won’t get too hot during the
summer. The sensor will become noisy and eventually fail in temperatures higher than 115ºF. You may need
to install ventilation or even air conditioning.
2. Connect the analyzer ground to an 8 ft. ground rod (or similar high quality ground) using at least
16AWG wire.
It is essential for safety that the analyzer has a good ground. Normally an 8ft rod pounded into the ground
will suffice, but in very dry or sandy areas something better may have to be done. Sometimes gas running in
pipelines can develop serious static charges on the lines, causing the pipeline to be at a high voltage
compared with the local ground. Be aware of this and make sure the pipeline is well grounded itself.
3. Confirm sample pressure is less than the analyzer specification (150psig). If it is higher, use a
suitable regulator such as the high pressure AMI Liquid Rejection Probe. Such a regulator must
have a stainless steel diaphragm.
The analyzer needs a minimum of about 1 PSIG, and a maximum of 150psig sample pressure. If the pressure
is too low, the gas flow will be low and the response time long, and if the flow is very low the effect of minor
leaks will become significant. If the pressure is too high the analyzer will be damaged, and you may get a
hazardous situation if the sample is flammable.
The response time will depend on the length of tubing, the diameter and the flow rate of gas through it.
You can roughly calculate it by assuming that the volume of tubing –the length multiplied by its internal
area –has to be completely replaced by the gas flowing before you get a representative reading. If the
sample pressure is high, the volume is effectively increased because more gas is packed into the tubing.
AMI can provide a version of the Liquid Rejection Probe with a built-in regulator that can handle pressures
up to 1500psig.
4. Deal with any potential condensation or liquid contamination issues.
If the sample may contain condensable liquids, they must be prevented from entering the analyzer. Natural
gas, for example, often contains water in vapor or liquid form, and other liquids such as oils, glycols or
methanol. Such liquids tend to collect in dips in the sample line, and come through the line as slugs,
particularly if the line is cleaned by “pigging” it (sending a cleaning device through it, preceded by a tidal
wave of sludge). Compressors heat the gas and also cause liquids to condense, particularly when the gas
cools off, so that even apparently dry gas going into a compressor may contain liquids when it comes out.
AMI can provide a “Demister” and Liquid Rejection Probe” that together work to prevent problems from hot
wet gases. The demister acts to coalesce droplets and cool the gas, while the Liquid Rejection Probe stops

AMI Analyzer Manual Installation Procedure 10
any liquids from getting to the analyzer. Any liquids fall back into the pipeline, thus minimizing maintenance
issues. Also, the Liquid Rejection Probe acts to prevent the problems that arise when the source of the gas
is shut off while the downstream compressor continues to run, thus pulling a vacuum on the line. Normally
this would cause air to be drawn into the line through the analyzer vent, but the Liquid Rejection Probe
contains a very sensitive check valve that prevents this.
5. Connect the sample line with ¼” stainless steel tubing.
Use stainless tubing only to connect the sample to the analyzer. Other materials are normally not robust
enough. Normally ¼” tubing is adequate unless the sample run is very long and the source pressure low –in
this case you may have to use wider tubing.
You should have some kind of blocking valve on the sample port. If you use a Demister, use at least a half
inch ball valve at its base.
6. Turn the Sample/Span/Off valve to the Off position.
The Sample/Span/Off valve is to the lower right of the grey faceplate above. This valve contains a metering
valve in its center. If you turn the Sample/Span/Off valve to the off position, it will stop either sample or
span gas from flowing into the analyzer –but the exhaust is still connected to the atmosphere so when you
have a sensor in the analyzer it is not sealed off by this valve. At this point in this procedure you shouldn’t
have the sensor in place yet. Don’t use the metering valve to shut off the flow (as it is a fine adjustment
valve)!
7. Pressurize the sample line to line pressure (1 –150psig).
The exact pressure doesn’t matter – we want enough so that you can easily see leaks in the following step.
8. Leak check every fitting and weld from the analyzer inlet to the sample tap.
Use a liquid soap solution such as “Snoop™” or similar. Don’t spray it on! You are looking for little bubbles
that appear after a while, indicating a leak. Even the tiniest leak will allow oxygen to enter the gas stream,
no matter what the pressure inside the line is. Check absolutely every possible source including welds, valve
packing, fittings both around the tube and the nut, and anything else that might leak.
9. Connect the vent line to outside, running slightly downhill all the way.
Particularly if the analyzer and gas is warmer than the environment, any water vapor in the gas will tend to
condense in the vent line. If the line runs uphill, or has a low point, water will collect and potentially freeze,
stopping the flow. If the sample gas is flammable, the vent must go to a safe area.
Also take precautions that insects don’t make nests in the exhaust line. You may need some sort of a grill
over it.
10. Adjust the sample flow to approximately 1 SCFH with the Flow control valve located in the middle
of the Sample/Span/Off valve.
The Flow Control Valve is the metering valve in the middle of the Sample/Span/Off valve. It is a sensitive
needle valve –so don’t try to use it to shut off the flow. Turn the main valve to the OFF position for this.

AMI Analyzer Manual Installation Procedure 11
The exact flow rate is not important –1 SCFH is half way up the flow meter, so is easy to see. You want the
flow between about 0.5 SCFH and 2 SCFH at the maximum. Lower flows will result in longer response times.
Higher flow rates will tend to increase the pressure on the sensor which will increase the oxygen reading.
11. Install electrical seal-offs, preferably with electrical couplers. Don’t fill them yet.
This is critically important! The electrical safety of the analyzer is based on its being installed properly. If
you don’t seal off the explosion-proof enclosure you have just made an igniter for the first time you get a
gas leak. Explosion-proof seal-offs are devices that allow you to put potting compound around the wires
going into and out of the enclosure so that burning gases can’t get past them. This compound also means
that you can’t remove the wires in the future, and if you don’t use the universal couplers we recommend
(and can supply) it will be very hard for you to remove the analyzer in the future. The couplers allow you to
remove the analyzer without having to completely rewire it when you replace it.
Figure 3. Electrical connections
12. Connect power, relay contacts, analog output and RS485 if desired. Run the power and alarms in
one conduit, and the analog output and RS485 in the other. Note that you MUST use rigid conduit

AMI Analyzer Manual Installation Procedure 12
for Class 1 Div 1 areas. You can use flexible conduit for Class 1 Div. 2 areas. See the NEC
handbook.
All the electrical connections are located in the left hand box –unscrew the cap with the red label. The
picture above shows the AC version (recognized by its black color). The DC version looks the same (except it
is white). The power is brought to the three position unpluggable terminal strip on the left (DC power looks
the same, but it’s marked differently). Make sure the wires are connected per the markings – Hot to H,
Neutral to N, Ground to the ground symbol. For DC units, connect the positive to the “+” symbol, the
negative to the “–“ symbol, and the ground as before. For DC units, the “–“ and the ground are connected
together, but run a separate ground wire to your main ground, and another wire from the –terminal to the
negative terminal on your power supply or battery.
The analog output –which may be either 1-5V or 4-20mA –is connected to the “+” and “-“ symbols. This
signal is isolated from ground. If the device to which you are connecting is also isolated from ground, make
sure you ground the “-“ connection at the analyzer. The terminal marked by the ground symbol may be
used for this purpose, in which case the output is no longer isolated. DO NOT GROUND BOTH ENDS! If you
do so, you will generate a ground loop which will seriously upset the readings. Normally you would use the
ground terminal for a shield. You can select which output is in use. The voltage output is lower power, but
more prone to interference. If you decide to change it, you will probably have to perform an output
calibration, described later in this manual.
The two terminals marked A and B are for the RS-485 ModBus connection. This is not isolated from ground.
There are two alarm contacts. These are two independent switches that either close, or open, their two
terminals. Think of them as being like a single pole light switch. You can determine whether they close
upon an alarm, or open, using the user interface program. They can switch up to 110V at 5A. Good practice
suggests adding snubbing diodes across any load they switch –although diodes are installed already on the
output circuit board. Be careful you don’t use them to short the power supply by attaching one end to your
hot and the other to ground. This can blow traces off the circuit board.
Each relay can be programmed to switch on or off, above or below set point, and with individual time
delays. They can also be set to operate latching valves, so that one contact opens the valve, and the other
closes it. Finally, they can themselves be set to reset automatically, or else to latch in position unless
someone presses the “Alarm hold off” button on the front panel. The User Interface Program must be used
to access all these options.
Run the power and alarm wires through one conduit, and the analog output and RS485 lines through the
other.
Make sure you are following the NEC (National Electrical Code) when you wire it up. In particular, if the
analyzer is in a class 1 Div. 1 area you have to use rigid conduit. You MUST always seal it off, in any case.
Also make sure you have a way of removing power from the analyzer nearby, per the code.
And don’t drill any holes in the enclosure! This will violate the safety approval, and may cause a fire or
explosion resulting in serious injury or loss of life.

AMI Analyzer Manual Installation Procedure 13

AMI Analyzer Manual Installation Procedure 14
13. Verify the analog output is correct and connect it.
Figure 4. Output selection switch positions
This unit is equipped with a selectable analog output. It may be either 1-5V or 4-20mA, selectable via a
switch on the output PCB (the board directly under the cover plate in the explosion proof housing). The
positioning of the switch is indicated on the PCB itself –put switch one position for 4-20mA, and put it the
other for 1-5V. The 4-20mA option will increase the current draw by up to 50mA, if the unit is powered
from DC. Note that if you change the position you will have to recalibrate the output using the AMI
software.
The output 4-20mA circuit is capable of driving a 600 Ohm load, while the voltage output needs at least a
10,000 Ohm load. Either will saturate at more than 125% of the nominal full scale range.
Using AMI software you can set the output to 4mA, 12mA and 20mA (or 1V, 3V and 5V), and adjust the
internal settings to calibrate these values so as to get the most accurate possible transfer of information to a
recording or computing device. If you leave a box checked so the output is at some value, like zero, the unit
will automatically return to its normal operation after ten minutes.

AMI Analyzer Manual Installation Procedure 15
14. Power up analyzer.
When you do so, the LCD should light up in the right side enclosure, and you may see some LEDs flicker
inside the explosion-proof enclosure. This is normal diagnostic information.
15. If you are not using the advanced features, set up the alarms and the output range from the front
panel of the analyzer.
The controls all work in the same way –first press the button you want to do something to, so that the LCD
shows whatever it might be that you have pressed. Then if you want to change it, press the up or down
arrows until the number shown reaches what you want. Then let go the button, and after a couple of
seconds the LCD will go back to reading oxygen and the change will be stored.
First choose the output range. This is the oxygen range that the analog output and alarms respond to. For
example, if you use a range of 10% full scale, 5V or 20mA corresponds to 10%, and 1V or 4mA correspond to
zero. Use a range that gives you enough resolution to see normal behavior, but allows you to have
reasonable alarm set points.
Set the range by pressing the OUTPUT RANGE button, and then scroll the number on the screen with the UP
and DOWN arrows until it says what you want.
When you have set the output range, set the alarms. The alarm set point is shown as a ppm (or percentage)
value, but it is internally stored as a percentage of the output range you just chose. If you change the range,
the alarm set points will change along with it.
Note that this range has nothing to do with the measurement range of the analyzer. The analyzer LCD
automatically scales its reading from 0.01% to 25%; it’s only the analog output that gets scaled by the range,
not the measurement.
If you want to set up other alarm features, such as whether the alarms latch or open or close on alarm, you
have to use the laptop user interface program.
If you press the UP button by itself, i.e. outside of changing something, the LCD will show the “Span factor”,
a number that indicates how much amplification the oxygen signal needs. As the sensor ages this number is
set higher by each successful calibration until it reaches 1000, at which point you should really have already
replaced the sensor.
If you press the DOWN button by itself, the LCD will show the temperature of the cell block in degrees
Fahrenheit.
16. Optional:
This section talks about using the laptop to make more advanced choices.

AMI Analyzer Manual Installation Procedure 16
Figure 5. User interface initial screen
a. Connect the laptop, run the User Interface and verify all alarm, output and security
settings.
Note that you must have power on the analyzer before the laptop can find the communication port! Plug in
a standard USB cable (such as the kind often used to connect a PC to a printer) to the port in the middle of
the explosion proof enclosure’s shield. Select the comm port at the top of the screen, and click Open
COMM. The program will figure out how to communicate to the analyzer, and fill in all the boxes once it
connects.
b. Set the analyzer clock time, and click on “Clear Data Log”.
The analyzer stores its readings for about two weeks for you to look at subsequently. It may have some
readings stored from the check-out process, and these might confuse you when you subsequently view
them. Also, we set it up on PST, and your time zone may be different. So set the time, and clear the data. In
due course, click on the Download Data button to see the stored data.
c. Verify the output calibration.
You should only need to do this if you have changed the output selection, or if your flow computer or similar
monitoring device has an uncalibrated input.
i. Connect the analog output terminals to an appropriate measuring device –preferably the
flow computer or similar monitoring device you are going to be using with this analyzer.

AMI Analyzer Manual Installation Procedure 17
You can simply use a multi meter connected to the output terminals. If so, make sure it is set correctly –
don’t use a voltmeter to measure current! Often people leave their meter in the current measurement
position and the next time they measure a voltage they blow the current fuse. If this has happened, the
meter won’t measure current until you replace it.
ii. Arrange that you can readily see the reading given by this device.
iii. On the AMI User Interface, check the “Zero” check box under SETUP in the ANALYZER
SETUP section.
iv. Observe the response of the monitoring device, and adjust the number in the box next to
the Zero label until the monitoring device shows what it considers to be zero (which
should correspond with either 1V or 4mA).
v. Check the box marked “Full Scale” in the SETUP section, and adjust the number in the box
next to it until the monitoring device shows full scale. This corresponds to 5V or 20mA.
vi. Check the “Mid Range” box and verify that the monitoring device shows mid scale.
vii. Uncheck any checked box (if you forget, the analyzer will revert to its ordinary operation in
ten minutes anyway).
17. Turn the Sample/Span/Off valve to OFF.
You don’t want to be flowing sample gas during the next step.
18. Unscrew the cell cap, and install the oxygen sensor.
Unscrew the cap first. Open the sensor bag, remove the sensor by holding the little handle and put it into
the cell compartment, gold side up, and with the little metal tag on the side facing you. When it is in place,
hold the sensor in place and pull out the tag. Do it in this order so that the sensor is always operating,
eating up oxygen that gets in through its membrane.
19. Optional: in the User Interface press the “NEW SENSOR” button, and record the sensor serial
number.
You might want to write it down. Note that you can read the serial number while the sensor is in place in its
cell block pocket –don’t leave the sensor out while you write it down.
20. Stabilize for 45 seconds, adjust span to 20.9%.
It will take the sensor about 20 seconds to come to a reasonably stable reading, but give it 45 seconds to be
sure. Don’t go over this time, even if the reading is still moving. The sensor is probably changing
temperature a bit which affects its reading until it has equilibrated with the analyzer. You aren’t concerned
with the utmost precision at this point, just a close-enough value.
21. IMMEDIATELY turn the Sample/Span/Off valve to SAMPLE.
Do this before you screw on the cell cap, because you will get rid of most of the air in the cell pocket
immediately, helping the sensor come down quickly.
22. If present, remove the USB cable.
23. Replace the Cell cap and tighten it down.
Table of contents
Other AMI Analytical Instrument manuals
Popular Analytical Instrument manuals by other brands
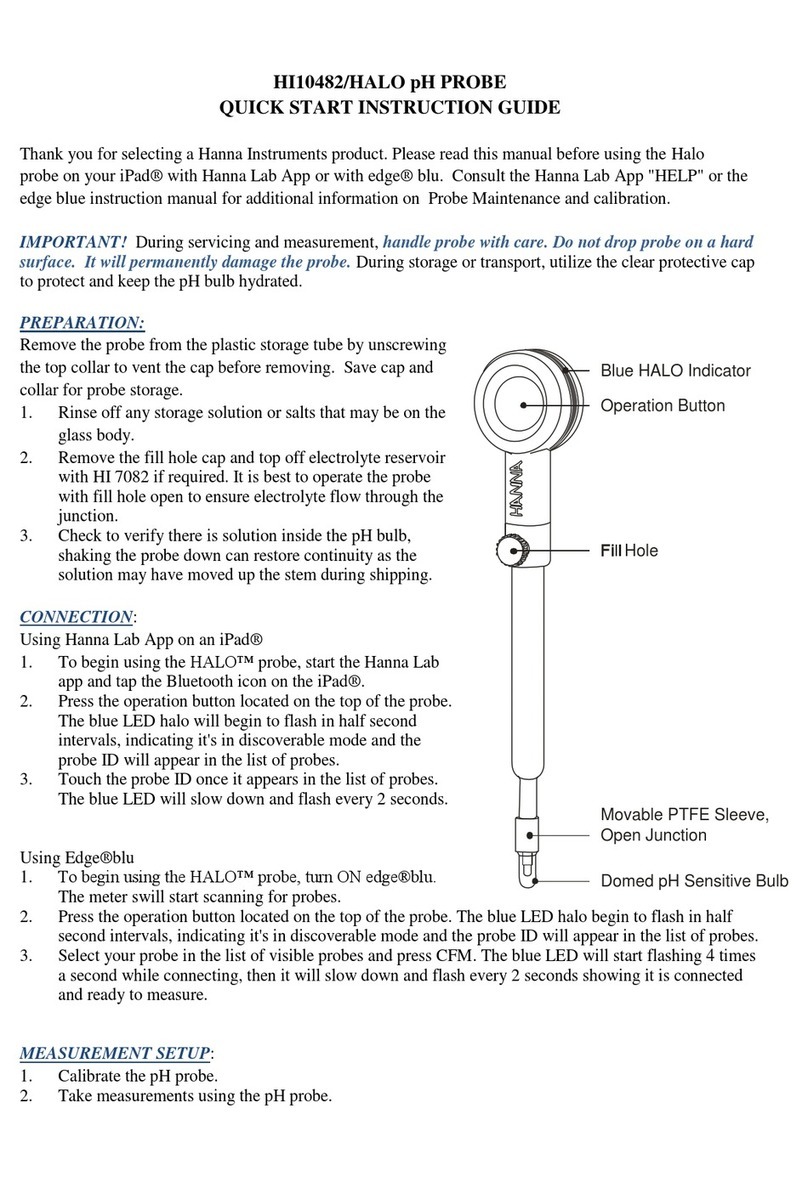
Hanna Instruments
Hanna Instruments HI10482/HALO QUICK START INSTRUCTION GUIDE
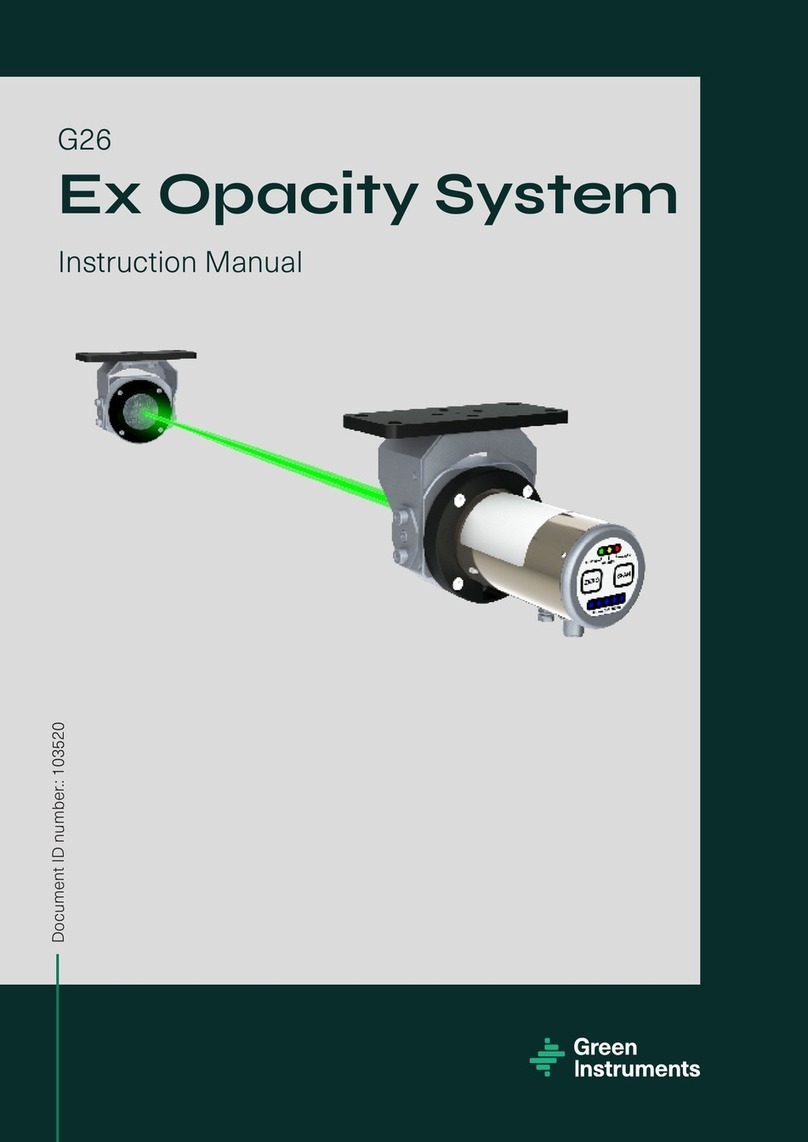
GREEN INSTRUMENTS
GREEN INSTRUMENTS G26 instruction manual

Philadelphia Scientific
Philadelphia Scientific iBOS Pro 6 Series installation manual
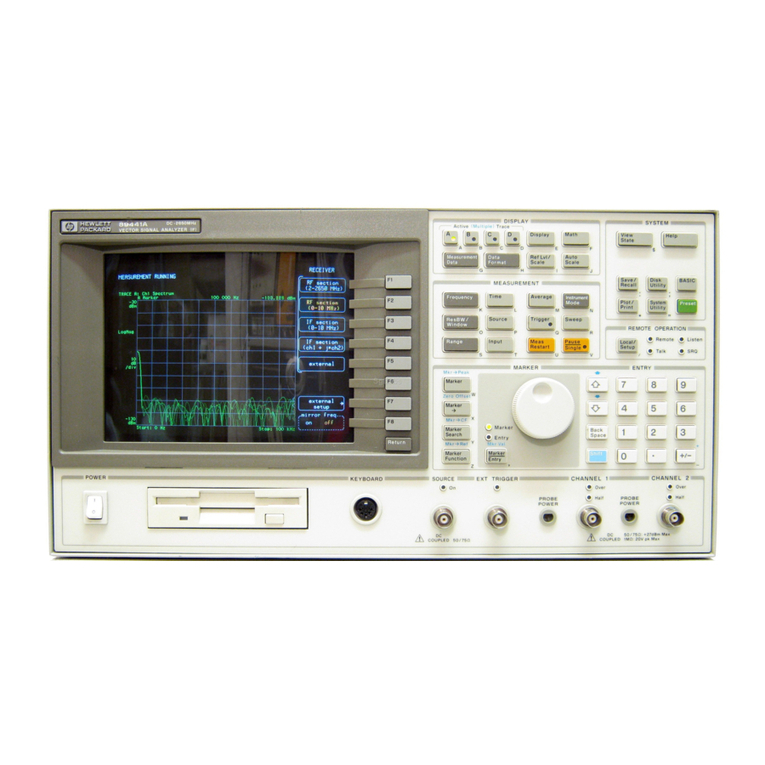
Agilent Technologies
Agilent Technologies 89410A Installation and Verification
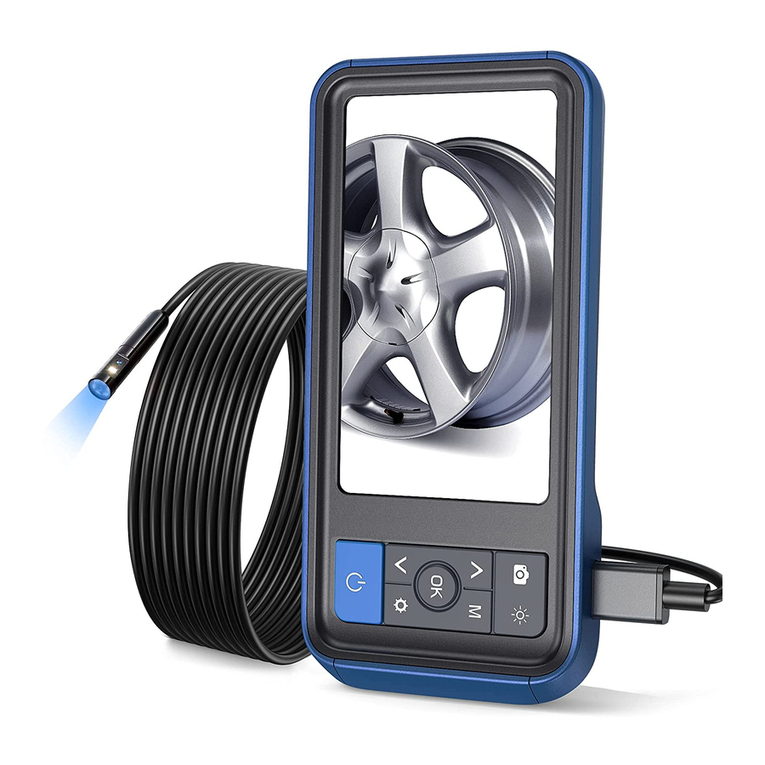
Teslong
Teslong MS450-NTC user manual
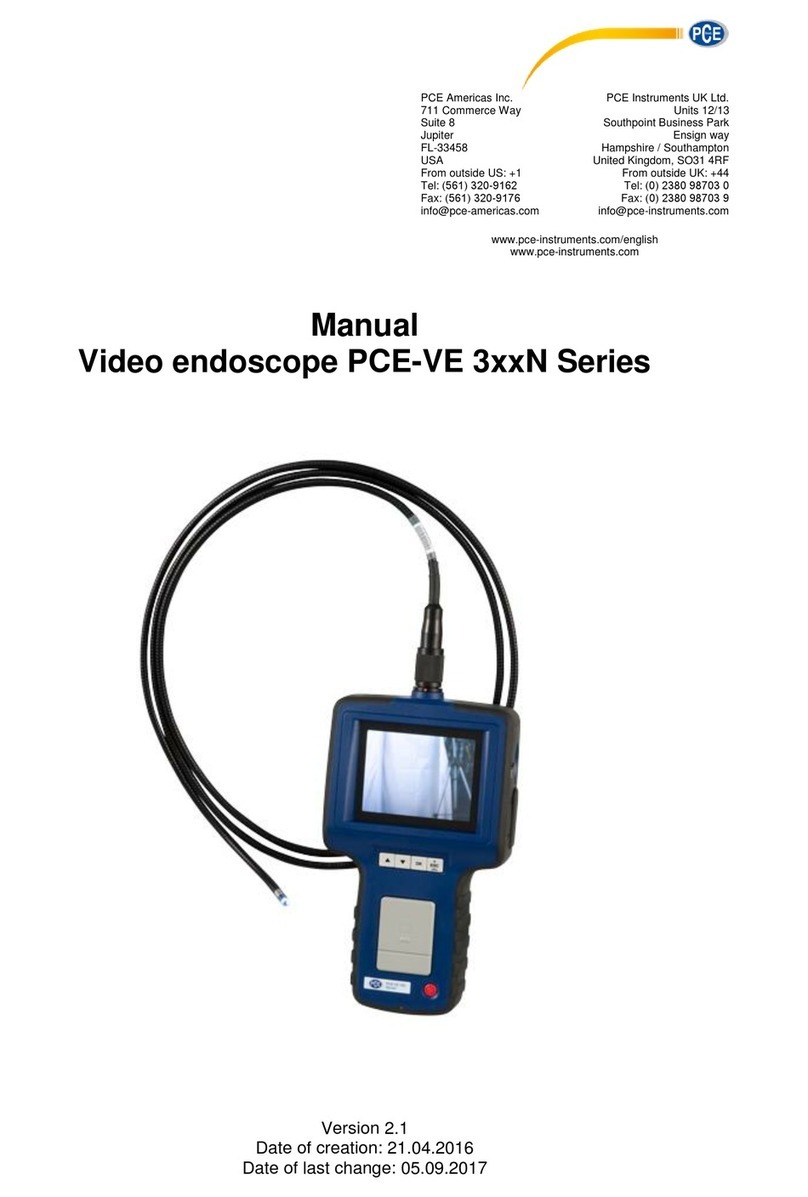
PCE Instruments
PCE Instruments PCE-IVE 320N manual