AMOT 2230C User manual

Doc No: OMM223000015
Revision: 2 – May 06
2230C/4430B
Two-way Temperature Sensing
Valve
Installation, Operation and
Maintenance Manual


3
Contents
OMM223000015 Rev 2 – May 06
Introduction ......................................................................................................5
1.1 Scope of Manual .................................................................5
1.2 Safety Assessment..............................................................5
1.3 Procedure Safety ................................................................5
Description.........................................................................................................7
2.1 Overview...........................................................................7
2.2 Description of Operation ......................................................8
2.3 Valve Model Code ...............................................................9
2.4 Optional AMOT 4125 Vent Closure....................................... 10
Installation ......................................................................................................11
3.1 Install the Valve ............................................................... 11
Operation..........................................................................................................15
4.1 Introduction..................................................................... 15
Maintenance ....................................................................................................17
5.1 Introduction..................................................................... 17
5.2 Test the Setpoint .............................................................. 17
Technical Data ................................................................................................19

4
Contents
Rev 2 – May 06 OMM223000015

5
Introduction
OMM223000015 Rev 2 – May 06
Section 1
Introduction
Contents
Para Page
1.1 Scope of Manual......................................................................... 5
1.2 Safety Assessment ..................................................................... 5
1.3 Procedure Safety........................................................................ 5
1.1 Scope of Manual
This manual details the information to enable the user to install and maintain
the 2230C/4430B Temperature Sensing Valve and is divided into the following
sections:
Section 1 Introduction........................................ Page 5
Section 2 Description ......................................... Page 7
Section 3 Installation ......................................... Page 11
Section 4 Operation ........................................... Page 15
Section 5 Maintenance ....................................... Page 17
Section 6 Technical Data .................................... Page 19
1.2 Safety Assessment
This product has been assessed against the requirements of EU Directive
94/9/EC (ATEX) and has been shown to comply with the requirements for
mechanical equipment to Group IIG, Category 2. This classification would
permit the equipment to be used in Zone 1 and 2 hazardous areas. Such
compliance is indicated in the product labelling as:
II 2G X
The “X” marking is used in respect to the maximum surface temperature of the
valve which is wholly conditional on the temperature of the fluids passing
through it. The valve is specified to operate to a maximum temperature as
listed in the Technical Data, Section 6, page 19.
1.3 Procedure Safety
Certain operations within this manual are potentially hazardous and could
cause injury to personnel or equipment damage if the instructions are not
carried out exactly as described. Where a significant potential hazard exists,
the following text appears immediately before steps in the procedure that
present a particular hazard:

6
Introduction
Rev 2 – May 06 OMM223000015
WARNING
A Warning identifies a hazard that could cause injury to personnel.
The text of the warning describes the hazard and details of the
precautions that must be applied before the next step of the procedure
is carried out.
CAUTION
A Caution identifies a hazard that could cause damage to equipment.
The text of the caution describes the hazard and details of the
precautions that must be applied before the next step of the
procedure is carried out.
Note
A Note contains supplementary information that may be useful to the
Operator and may appear before or after a particular step in the procedure.

7
Description
OMM223000015 Rev 2 – May 06
Section 2
Description
Contents
Para Page
2.1 Overview................................................................................... 7
2.2 Description of Operation .............................................................. 8
2.3 Valve Model Code ....................................................................... 9
2.4 Optional AMOT 4125 Vent Closure .............................................. 10
2.1 Overview
The 2230C and 4430B Temperature Sensing Valves are normally closed, two-
way valves which are opened when the temperature of the process medium
increases above a preset setpoint.
The control pressure applied to the valve can be air, gas or lubricating oil and
is vented when the valve opens. This reduces the control pressure to an AMOT
Master Safety Control or other device to protect the engine when high
temperature is detected.
Fig 1 shows a typical installation using two Temperature Sensing Valves
connected in series. This ensures that the shutdown system is triggered in the
event of high temperature cooling water or gear case.
The orifice ensures that the pressure drop is transmitted to the shutdown
system device in large volume systems.
Fig 1 Typical installation

8
Description
Rev 2 – May 06 OMM223000015
2.2 Description of Operation
Refer to Fig 2.
Under normal conditions, the inlet pressure is prevented from reaching the
vent port by the valve seat assembly which is held closed by the spring.
If the temperature increases, the wax temperature element expands and
moves the pushrod against the spring pressure.
When the temperature rises above the setpoint, the valve seat is lifted by the
pushrod and the inlet pressure is connected to the vent port.
When the temperature falls, the valve seat assembly is closed again by spring
pressure.
The screw is used to adjust the setpoint (preset by AMOT).
Fig 2 AMOT 2230/4430 Temp Sensing Valve

9
Description
OMM223000015 Rev 2 – May 06
2.3 Valve Model Code
2230C
1 2 0 C N 120
C --
Construction
Brass 2230C
Stainless steel 4430B
Thread type and finish
Installation
thread
Port
thread
Element
finish
NPT NPT Standard 1
BSP(Tr) BSP(Tr) Standard 2
NPT NPT Plated 3
BSP(Tr) BSP(Tr) Plated 4
BSP(Pl) BSP(Tr) Standard 5
BSP(Pl) BSP(Tr) Plated 6
Seal material
Viton 2
Installed depth (Refer Fig 4, page 13)
Element
extension
3/4 in Well
Dim “M”
1 in Well
Dim “N”
34.9 (1 - 3/8)
(No extension) 25.4 (1) 0
55.6 (2 - 3/16) 42.9 (1 -11/16) 50.8 (2) 1
63.5 (2 -1/2) 49.2 (1 -15/16) 57.2 (2 -1/4) 2
76.2 (3) 61.9 (2 -7/16) 69.9 (2 -3/4) 3
88.9 (3 -1/2) 74.6 (2 -15/16) 82.6 (3 -1/4) 4
101.6 (4) 87.3 (3 -7/16) 95.3 (3 -3/4) 5
114.3 (4 -1/2) 100 (3 -15/16) 107.6 (4 -1/4) 6
127 (5) 112.7 (4 -7/16) 120.7 (4 -3/4) 7
Temperature range
Without well With well
19-35° C (65-95° F) 24-40° C (75-105°F) A/K
36-54° C (96-130° F) 41-60° C (106-140° F) B/M
55-71° C (131-160° F) 61-76° C (141-170° F) C/N
72-82° C (161-180° F) 78-88° C (171-190° F) D/P
83-100° C (181-212° F) 89-104° C (191-220° F) E/R
101-107° C (214-225° F) 108-113° C (225-235° F) F/S
108-118° C (226-245° F) 114-124°C (236-255° F) G/T
129°C (265° F) 132° C (270° F) H/W
119-124° C (246-255° F) 124-129° C (256-265° F) J/X
Thermal well codes
Calibrated in a well (well not fitted) V
Not fitted N
3/4 in NPT 1
1 in NPT 2
3/4 in BSP(Pl) 3
Temperature setting
Scale (Celsius /Fahrenheit)
Special requirements

10
Description
Rev 2 – May 06 OMM223000015
2.4 Optional AMOT 4125 Vent Closure
The optional AMOT 4125 Vent Closure can be screwed into the “VENT” port to
protect against the ingress of dirt, insects and corrosive atmospheres into the
Valve.
Fig 3 AMOT 4125 Vent Closure

11
Installation
OMM223000015 Rev 2 – May 06
Section 3
Installation
Contents
Para Page
3.1 Install the Valve ....................................................................... 11
3.1 Install the Valve
CAUTION
Some commercial fittings are not tapped deep enough and may
damage the temperature cup. It is recommended that a 22/32 in
diameter tap drill is run through the pipe fitting before installing the
Valve.
To prevent the pushrod being jammed by foreign objects and to keep
the ports clear, the control medium must be filtered before it enters
the Valve.
If the valve is located in a hazardous area and the mounting thread
does not provide good electrical contact between the valve and the
rest of the system, additional earth bonding will be required.
To ensure that the pressure drop is felt at the engine control device.
•An orifice must be fitted in the control medium input line. Suitable
orifices for a wide range of control media are available from
AMOT.
•Pipe lengths must be kept as short as possible to minimise the
control medium volume.
1Install the Valve into the pipe fitting or thermowell using a quality thread
sealant such as Loctite ™ Pipe Sealant to the pipe thread connections.
If required, two types of stainless steel well can be used. Refer to the
Technical Data, Section 6, page 19 for pressure limits.
#3802L – 3/4 in.
#2766L – 1 in.
Note
When a Valve is ordered in a thermowell, it is assembled by AMOT using
heat transfer compound (Part number 907L002) to minimise the lag time for
changing temperatures.

12
Installation
Rev 2 – May 06 OMM223000015
2Connect the control medium to the “IN” port using a quality thread
sealant such as Loctite ™ Pipe Sealant to the pipe thread connections -
8.62 bar (125 psi) maximum.
CAUTION
If the Valve is located in a hazardous area, the “VENT” port must be
connected by a pipe that vents outside the hazardous area.
3Connect the “VENT” port depending on the type of control medium.
#Air – no connection is required but it should be protected from
contamination by an AMOT 4125 Vent Closure (refer to Fig 3) or a
tubing elbow bent downwards.
#Oil – connect to the sump.
#Gas – connect to system vent.
If required, an AMOT 4054 Trip Indicator can be fitted (Refer to manual
OMM405400037).

13
Installation
OMM223000015 Rev 2 – May 06
Fig 4 Dimensions

14
Installation
Rev 2 – May 06 OMM223000015

15
Operation
OMM223000015 Rev 2 – May 06
Section 4
Operation
Contents
Para Page
4.1 Introduction ............................................................................ 15
4.1 Introduction
The 2230C/4430B Temperature Sensing Valve operates with no manual
intervention and resets automatically.
If the optional AMOT 4054C Trip Indicator is used, the red plunger must be
pushed in to reset it after the temperature has fallen below the setpoint.

16
Operation
Rev 2 – May 06 OMM223000015

17
Maintenance
OMM223000015 Rev 2 – May 06
Section 5
Maintenance
Contents
Para Page
5.1 Introduction ............................................................................ 17
5.2 Test the Setpoint...................................................................... 17
CAUTION
To satisfy the ATEX requirements, the external surface of the Valve
must be cleaned on a regular basis to prevent the accumulation of
potentially flammable dirt/spillages.
Where the control medium is flammable, the Valve must be inspected
at weekly intervals for leaks to minimise the risk of explosion.
5.1 Introduction
There are no user serviceable components in the 2230/4430 Temperature
sensing Valves.
The setpoint is preset by AMOT and it is recommended that the unit is
returned to AMOT if the setpoint requires adjustment. To test the setpoint,
refer to Section 5.2.
Maintenance of the 4054 Trip Indicator is described in OMM405400037.
5.2 Test the Setpoint
WARNING
To avoid injury, ensure that the process and control mediums are
cooled, drained and isolated before the Valve is removed from the
pipework.
1Ensure that the process and control mediums are cooled, drained and
isolated.
2Remove the Valve from the pipework.
3Fit a device to the “VENT” port to provide an indication when the Valve
trips.
4Fit a 4 bar (60 psi) pressure source to the “IN” port.
5Immerse the Valve temperature element into a container filled with well
agitated water or glycol (depending on the temperature) and a
thermometer to indicate the temperature.

18
Maintenance
Rev 2 – May 06 OMM223000015
CAUTION
To prevent damage, do not exceed the maximum temperature of the
Valve. Refer to the Technical Data, Section 6.
6Apply the inlet pressure of 4 bar (60 psi) and slowly heat the liquid in the
container until the Valve trips.
7Note the thermometer reading and ensure that it indicates the correct
setpoint.
Note
The Valve starts to bleed control pressure at 1 to 2° C (2 to 4° F) below the
setpoint.
8Allow the Valve to cool and ensure that it closes when the temperature
falls below the setpoint.
9If the “VENT” port leaks in the ‘cold’ condition or the setpoint requires
adjustment, return to AMOT at the address shown on the back cover of
this manual.

19
Technical Data
OMM223000015 Rev 2 – May 06
Section 6
Technical Data
Construction
2230 4430
Body and nut Brass 316 SS
Seals Viton Viton
Element Brass Brass
Extensions Brass 316 SS
Weight
Max net weight
(2230 and 4430) 0.57 kg (1 – 1/4 lb)
Max net weight
(Well) 0.45 kg (1 lb)
Pressure
Inlet pressure 8.62 bar (125 psi) maximum
Sensed pressure with well fitted:
2766L 690 bar (10000 psi) maximum
3802L 345 bar (5000 psi) maximum
Sensed pressure
Temp element 55.17 bar (800 psi) maximum
Temperature
Maximum allowable continuous temperature depends on the Model
Code:
Model Code Without well With well
A/K 48.9° C (120° F) 54.4° C (130° F)
B/M 68.3° C (155° F) 73.9° C (165° F)
C/N 85° C (185° F) 90.6° C (195° F)
D/P 101.7° C (215° F) 107.2° C (225° F)
E/R 110° C (230° F) 115.6° C (240° F)
F/S 118.3° C (245° F) 123.9° C (255° F)
G/T 123.9° C (255° F) 129.4° C (265° F)
H/W 135° C (275° F) 140.6° C (285° F)

Europe and Africa Americas
AMOT
Western Way
Bury St Edmunds
Suffolk, IP33 3SZ
England
Tel +44 (0) 1284 762222
Fax +44 (0) 1284 760256
AMOT Controls GmbH
Rondenbarg 25
22525 Hamburg
Germany
Tel +49 (0) 40 8537 1298
Fax +49 (0) 40 8537 1331
AMOT USA
8824 Fallbrook Dr
Houston
Texas 77064
USA
Tel +1 (281) 940 1800
Fax +1 (281) 668 8802
Asia and Australasia
AMOT Shanghai
Rm A8-671 Jiahua Business Center
808 Hongqiao Road
Shanghai 200030
China
Tel +86 (0) 21 6447 9708
Fax +86 (0) 21 6447 9718
AMOT Singapore
10 Eunos Road 8 #12-06
Singapore Post Centre
Singapore 408600
Tel +65 6293 4320
Fax +65 6293 3307
www.amot.com
Prepared by: TPI – Jan 2004
This manual suits for next models
1
Table of contents
Other AMOT Control Unit manuals
Popular Control Unit manuals by other brands

Connect Tech
Connect Tech CCG012 user guide
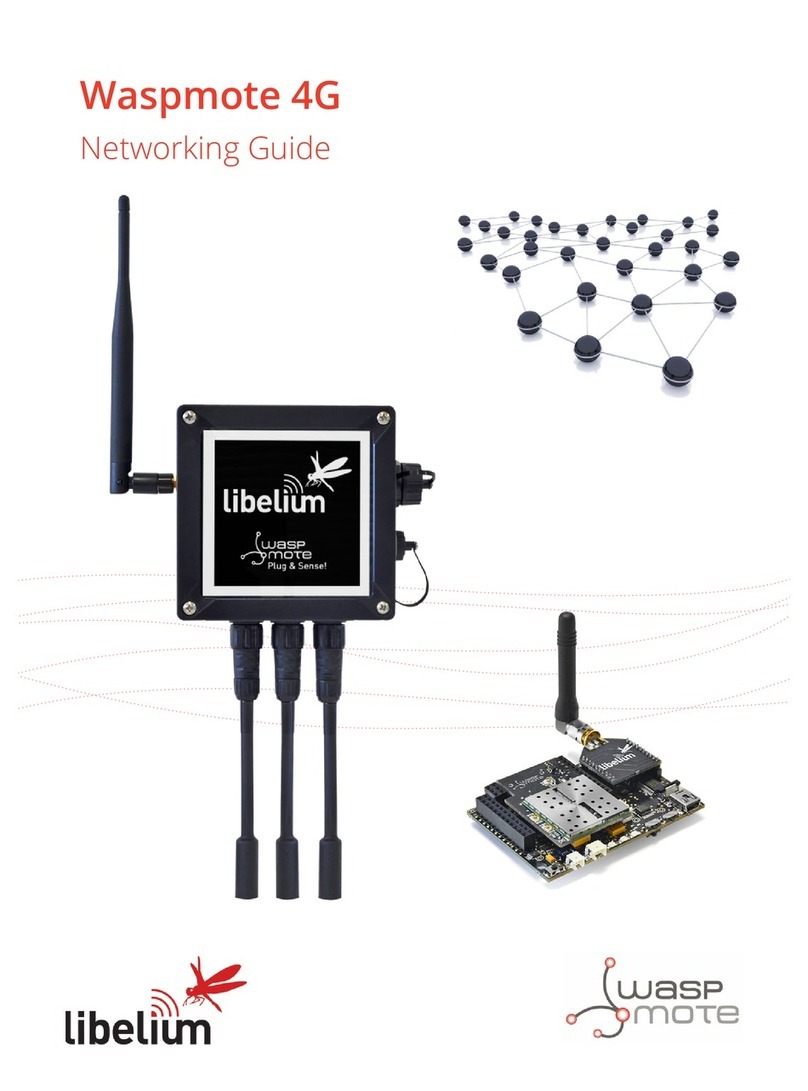
Libelium
Libelium SIM5215 Networking guide
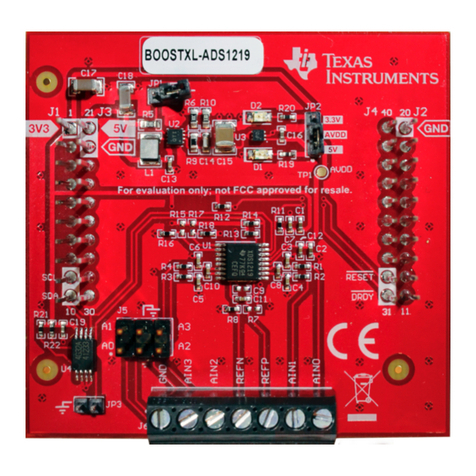
Texas Instruments
Texas Instruments BOOSTXL-ADS1219 BoosterPack user guide

HEX
HEX HS31 Maintenance instructions
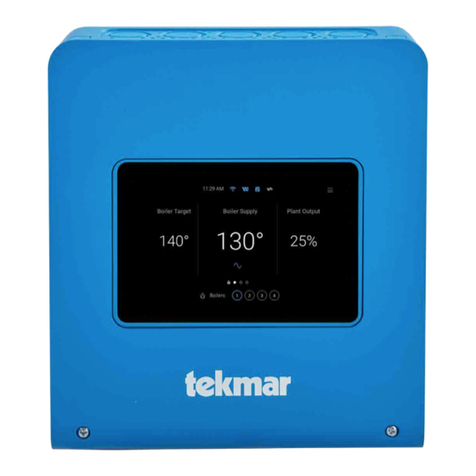
Watts
Watts tekmar Smart Boiler Control 294 Installation and operating manual

Grundfos
Grundfos LC 107 Installation and operating instructions