AMOT C User manual

Doc No: OMMC00296 Revision: 2 – Sept 2020
Model C Valve
Thermostatic valve for
diverting and mixing
applications
Installation, Operation
and Maintenance Manual

Original instructions

3
Table of Contents
Doc No: OMMC00296 Revision: 2 – Sept 2020
Section 1
Table of Contents
Section 1 ....................................................................................... 3
Section 2 ....................................................................................... 5
2.1 Scope .................................................................................. 5
2.2 Safety ................................................................................. 5
2.3 Product support .................................................................... 5
Section 3 ....................................................................................... 7
3.1 Overview ............................................................................. 7
3.1.1 Manual override............................................................. 7
3.2 Features .............................................................................. 7
3.3 Valve Selection ..................................................................... 8
3.4 Identification of Model Number................................................ 9
Section 4 ......................................................................................13
4.1 Pressure Equipment Directive (PED)........................................13
4.2 Hazardous Areas ..................................................................14
4.2.1 Hazardous Area Directive (ATEX) ....................................14
4.2.2 Specific Conditions of Use ..............................................16
4.3 Machinery Directive ..............................................................16
Section 5 ......................................................................................17
5.1 Installing the valve ...............................................................17
5.1.1 Before starting installation .............................................17
5.1.2 Mounting the Valve in the Pipe........................................18
5.1.3 Start up ......................................................................18
Section 6 ......................................................................................19
6.1 Operation............................................................................19
6.1.1 Diverting applications ....................................................19
6.1.2 Mixing applications........................................................
19
6.1.3 2-way Water Saving Applications ....................................20
Section 7 ......................................................................................21
7.1 Dismantling the valve ...........................................................22
7.2 Reassembling the valve.........................................................24
7.3 User maintenance parts ........................................................26
Section 8 ......................................................................................27
8.1 System temperature too cold .................................................27
8.2 System temperature too hot ..................................................27
Section 9 ......................................................................................29
9.1 General valve specification ....................................................29
9.1.1 Materials .....................................................................29
9.1.2 Maximum working pressure............................................29
9.1.3 Maximum working temperature ......................................29
9.1.4 Valve handling..............................................................30
9.1.5 Storage .......................................................................30

4
Table of Contents
Revision: 2 – Sept 2020 OMMC00296

5
Introduction
Doc No: OMMC00296 Revision: 2 – Sept 2020
Section 2
Introduction
2.1 Scope
This manual details the installation, operation and maintenance of
the AMOT Model C Valve range.
2.2 Safety
Certain operations within this manual are potentially hazardous and
could cause injury to personnel or damage to equipment if the
instructions are not carried exactly as described. Where a significant,
potential hazard exists, the following text appears immediately
before steps in the procedure that present a particular hazard:
WARNING
A Warning identifies a hazard that could cause injury to personnel.
The text of the warning describes the hazard and details the
precautions that must be applied before the next step of the
procedure is carried out.
CAUTION
A Caution identifies a hazard that could cause damage to
equipment. The text of the caution describes the hazard and
details the precautions that must be applied before the next step
of the procedure is carried out.
Note
A Note contains supplementary information that may be useful to the
Operator before the next step of the procedure is carried out.
2.3 Product support
All necessary settings and, where appropriate, alterations inside the
equipment are described in this Operating Manual. If any difficulties
arise during start-up, you are asked not to carry out any
unauthorized actions on the unit. You could endanger your rights
under the equipment warranty.
For spares and service support, call the telephone number listed on
the back cover of this Manual.

6
Introduction
Revision: 2 – Sept 2020 OMMC00296

7
Description
Doc No: OMMC00296 Revision: 2 – Sept 2020
Section 3
Description
3.1 Overview
The Model C Valve is designed to provide fully automatic, 3-way fluid
temperature control for diverting or mixing applications. Typical
applications include engine water jackets, lubricating oil cooling
systems, and mixing and diverting of fluids in process control and
industrial applications.
The thermostatic element (also referred to as ‘element’) in a Model C
Valve is fully enclosed and factory set, providing tamper-proof
operation. For maintenance, or to achieve a different set
temperature, the element can be changed, although this does require
removal of the valve from the adjoining pipework. Elements are
available with set temperatures from 18 to 113°C (65 to 235°F).
Valves are available in five sizes, and a variety of materials to suit
different fluids.
3.1.1 Manual override
Model C Valves do not have manual override capability.
3.2 Features
Typical applications
•Lubricating oil temperature control
•Jacket water high temperature (HT)
•Secondary water low temperature (LT)
•Heat recovery
•Water saving applications.
•Boiler inlet temperature control
•Co-generation, cooling towers
•Temperature mixing or diverting
•Engine and compressor cooling system
Key benefits
•No external power source required – simple low cost
installation
•No user setting needed – ‘fit and forget’ solution
•Small number of parts – simple maintenance and low cost
ownership
•Robust design capable of high vibration and shock
applications
•Easy installation operates in nay mounting position
•Automatic self-sensing control with positive proportional
valve action

8
Description
Revision: 2 – Sept 2020 OMMC00296
3.3 Valve Selection
A wide range of valve sizes and materials of construction are available,
covering the applications in Section 3.2. An AMOT C Valve datasheet
containing information on selection of the appropriate valve type is
available, contact AMOT for a copy.
It is the responsibility of the end user to ensure suitability of the valve
with its intended use. The valve, element, and seal materials in particular
should be carefully selected to ensure compatibility with the process fluid
and the installation.
For further help in selecting the correct valve for the application, contact
AMOT (contact details available on the back cover of this manual).

9
Description
Doc No: OMMC00296 Revision: 2 – Sept 2020
3.4 Identification of Model Number
Example Code
1
CF
B
J
075
01
-0
0
-XXX
Code Description
Valve Size
Nominal Bore Size
Number of Elements
1/2
1/2 inch (DN15)
1
3/4
3/4 inch (DN20)
1
1
1 inch (DN25)
1
1 1/4
1 1/4 inch (DN32)
1 (2 for CCM valves)
1 1/2
1 1/2 inch (DN40)
1
Valve Model
Model
CM
Threaded valve
CCM
High flow valve (1 ¼” valve only, with 2 elements)
CL
Low flow rate
CF
Flanged connection (1 ½” valve only)
Valve Material
Valve Material
A
Aluminium (CM, ¾” and 1” only)
B
Bronze (CM and CL)
C
Cast Iron (CM, CCM, CF and CL)
S
Steel (1/2”, 3/4” and 1” CM & CL, 1 ½” CF only)
R
Stainless steel (1/2”, 3/4” and 1” CM & CL, 1 ½” CF only)
Port Connection
Port Connection
C
Flanged EN-1092, PN10, PN16
F
Flanged ANSI 125 lb
H
Flanged ANSI 300 lb (steel and stainless steel only)
J
Flanged 150 lb (steel and stainless steel only)
K
Flanged ANSI 600 lb (steel and stainless steel only)
M
Socket weld (1 ¼” and 1” steel & stainless steel CM valves)
T
Threaded NPT to USAS B2.1
U
Threaded BSP (PL) to BS 21
V
Threaded BSP (TR) Japanese (JIS)
W
Threaded to SAE J5 14H (straight thread, O-Ring seal)
R
Threaded BSP (PL), boss faced, DIN 3852 Form X (Bronze,
cast iron and ductile iron only)
Control Temperature (°F)
Control Temperature (°F)
***
See Element Temperatures, Table 2
Element Type
Element Type
**
See Element / Seal Types, Table 3
Leakhole sizes
Leakhole sizes inches
0
None
B
1/32" Dia
C
1/16" Dia
D
3/32" Dia
F
1/8" Dia
G
1/4" Dia
H
3/16" Dia
Leakhole Quantity*
No. of elements with Leakhole
0
None (Specified on CCM only)
1
One (Specified on CCM only)
2
Two (Specified on CCM only)
Customer Special Requirements
Customer Special Requirements
-AA
Standard Product
-***
Customer special code assigned
Table 1– Model Identification
*Note: Leakhole quantity character is not used for CM, CL, CF type valves, only
CCM
Other Flange connections are available. Contact AMOT for details.

10
Description
Revision: 2 – Sept 2020 OMMC00296
Code
Control
Temp
Rated Range
Max Temp
Continuous
Max Temp
Short Period
Crack Open
Full Open
°C
°F
°C
°F
°C
°F
°C
°F
°C
°F
065
18
65
15
59
25
77
47
116
55
131
075
24
75
20
68
29
85
60
140
68
154
085
30
85
24
75
34
93
63
145
71
160
095
35
95
30
86
40
104
73
163
81
178
100
38
100
33
91
42
108
61
143
70
158
110
43
110
38
100
47
117
82
180
90
194
120
49
120
43
110
55
131
86
187
94
201
130
54
130
49
120
60
140
95
203
105
221
140
60
140
54
130
65
150
95
203
105
221
150
65
150
60
140
71
160
100
212
110
230
160
71
160
65
150
76
170
100
212
110
230
170
76
170
72
163
82
180
100
212
110
230
175
80
175
76
170
85
185
105
221
115
239
180
82
180
79
175
88
190
110
230
120
248
185
85
185
82
180
91
196
112
230
120
248
190
87
190
85
185
93
200
110
230
120
248
200
93
200
90
194
100
212
110
230
120
248
215
101
215
96
205
107
225
115
239
125
257
225
107
225
101
214
114
237
120
248
130
266
235
113
235
107
225
133
253
124
255
134
273
Table 2 – Element Temperatures

11
Description
Doc No: OMMC00296 Revision: 2 – Sept 2020
Code
Element and Valve Seal Material
Valve model Element type
Element
construction
Seals
01
CM/CCM/CF
1125X
Standard element
Nitrile
(Buna N)
CL
10765X
06
CM/CCM/CF
1125X
Standard element
FKM (Viton)
CL
10765X
99
CM/CCM/CF
3362U
Standard element
Neoprene
CL
10765U
09
CM/CCM/CF
1125P
Nickel plated
Nitrile
(Buna N)
CL
10765P
02
CM/CCM/CF
1125P
Nickel plated
FKM (Viton)
CL
10765P
82
CM/CCM/CF
9778C
Nickel plated
Neoprene
CL
10765K
86
CM/CCM/CF
44844X
Salt water –
Stainless steel
FKM (Viton)
CL
Table 3 – Element/Seal Types
Other Elements and Seals are available. Contact AMOT for details.

12
Description
Revision: 2 – Sept 2020 OMMC00296

13
Use within the European Union (EU)
Doc No: OMMC00296 Revision: 2 – Sept 2020
Section 4
Use within the European Union (EU)
4.1 Pressure Equipment Directive (PED)
The Pressure Equipment Directive (PED) is applicable to the design,
manufacture and conformity of pressure equipment and assemblies
of pressure equipment with a maximum allowable pressure greater
than 0.5 bar.
In its design application of a thermostatic valve, this equipment is
defined as a Pressure Accessory under the terms of the EU Pressure
Equipment Directive (PED).
The Model C Valve, when suitable for use within the European
Community, carries a nameplate, an example of which is shown in
Figure 1. The nameplate contains the following information pertinent
to the Pressure Equipment Directive requirements:
Figure 1 – C Valve Nameplate
Model An alphanumeric text identifier stamped onto the
nameplate that fully describes the type of
equipment.
Serial No A unique serial number stamped on the nameplate
to allow traceability of manufacture.
Year The year in which the equipment was manufactured
is stamped here.
** BAR MAX The maximum pressure that the equipment is
permitted to see in service (refer to Section 9.1.2 for
value).

14
Use within the European Union (EU)
Revision: 2 – Sept 2020 OMMC00296
Name and address
Equipment complying with the Pressure Equipment
Directive must be marked with the name and
address of the manufacturer and where appropriate,
of his authorised representative established with the
European Community.
Suitable for liquids to Groups 1 & 2
When used with liquids defined as Groups 1 or 2, the
Model C Valve falls into the PED Sound Engineering
Practice (SEP) category. Units must not be CE
marked in the SEP category (although are CE
marked for compliance with the ATEX Directive (see
Section 4.2)).
Users who are uncertain as to the applicability of the Pressure
Equipment Directive should contact AMOT, particularly if using more
hazardous (Group 1) fluids.
4.2 Hazardous Areas
4.2.1 Hazardous Area Directive (ATEX)
The ATEX Directive is applicable to all equipment both electrical and
mechanical that is put into service in a designated hazardous area.
The Model C Valve, as mechanical equipment, has been assessed in
accordance with EN ISO 80079-36 and has been designated as Group
II equipment. Group II equipment is suitable for use in places where
a potentially explosive atmosphere may be present. Group II
equipment shall not be used underground in mines, or in the surface
installations of such mines that are susceptible to firedamp or
combustible dust.
The Model C Valve has been assessed for use in places designated as
containing hazardous gas; they shall not be used in places
designated as containing hazardous dust.
The Model C Valve, when suitable for use within the European
Community, carries a nameplate, an example of which is shown in
Figure 1. The nameplate contains the following information pertinent
to the ATEX Hazardous Area Directive requirements:
Model An alphanumeric text identifier stamped
onto the nameplate that fully describes the
type of equipment.
Serial No A unique serial number stamped on the
nameplate to allow traceability of
manufacture.

15
Use within the European Union (EU)
Doc No: OMMC00296 Revision: 2 – Sept 2020
Year The year in which the equipment was
manufactured is stamped here.
Ex Symbol The Distinctive Community Mark for
hazardous area application.
Equipment designation:
II Equipment Group (non-mining
applications).
2 Equipment Category (high protection
level).
G Hazardous Area Type (hazardous gas
environments).
h Protection of non-electrical equipment.
IIC Equipment Group Subdivision (for gas
group limitations).
T6…T3 Max surface temp (maximum surface
temperature depends on not on the
equipment itself but on the operating
conditions, and a single temperature
class cannot be marked by the
manufacturer).
Gb Equipment Protection Level (EPL)
(high protection level).
X Specific Conditions of Use apply,
including the Ambient Temperature
Range below, see Section 4.2.2.
CML 15ATEXT174 Confidential Technical File reference
(c/o Notified Body).
CE Marking All equipment used in a hazardous area
under the ATEX Directive must be CE
marked. Mechanical equipment in Group II
Category 2 is self-assessed, and a
confidential Technical File lodged with a
Notified Body (per Technical File ref.
above). Equipment that is CE marked must
comply with all relevant EU Directives. The
CE mark on the AMOT C Valve only
represents compliance to the ATEX
Directive and not to other EU Directives.
Name and address Equipment complying with the Hazardous
Area Directive must be marked with the
name and address of the manufacturer and
where appropriate, of his authorised
representative established with the
European Community.

16
Use within the European Union (EU)
Revision: 2 – Sept 2020 OMMC00296
For safe and trouble-free use within hazardous areas the instructions
within this Operating and Maintenance Manual must be strictly
adhered to.
The maximum temperature and internal pressure that this equipment
is permitted to work at is contained within Section 9.1.
The conditions for safe installation and commissioning of this
equipment are contained in 4.
The equipment must be maintained in accordance with Section 7,
and between maintenance periods it should be kept clean in
accordance with Section 4.2.2.
Users who are uncertain as to the applicability of the ATEX Directive
should contact AMOT for further advice.
4.2.2 Specific Conditions of Use
1. The equipment is designed for use in an extended ambient
temperature range of -20°C to +60°C.
2. The equipment contains no heat generating parts and assumes the
temperature of the fluid inside it, as denoted by the “T6…T3”
marking. The fluid temperature must remain within the limit
specified in Section 9.1.3.
3. Cleaning of equipment must only be completed using a damp cloth
or anti-static cloth.
4. Process fluids capable of generating ionising radiation (such as
radioactive substances) are not suitable for use with the equipment.
5. The equipment is not suitable for use with process fluids that could
cause exothermic reactions within the equipment or with the
equipment and its materials.
4.3 Machinery Directive
The Model C Valve supplied by AMOT is classified as a component.
The equipment falls outside the scope of the machinery directive.
Components are only intended to be incorporated into or assembled
with other machinery or equipment thereby forming Machinery.

17
Installation
Doc No: OMMC00296 Revision: 2 – Sept 2020
Section 5
Installation
WARNING
The valve is heavy; refer to 9.1.4. The appropriate manual
handling precautions must be applied to avoid personnel injury.
5.1 Installing the valve
5.1.1 Before starting installation
1. Upon receipt, the valve should be checked for damage
sustained in shipping. All AMOT valves have nameplates
attached, which are stamped with the valve model number
and serial number.
2. Understand the intended use of the valve as described in
Section 3.
3. Before installation, ensure that the valve is suitable for the
purpose, checking temperature, pressure and material
parameters, and any special approval requirements (refer to
Section 3.3). Check that the intended pipe fittings are
suitable for the application.
4. Check that the valve size has been selected in accordance
with the anticipated flow rate through the valve (refer to
Section 3.3). To maintain good temperature regulation the
pressure drop across the valve should be in the 0.14 to 0.5
bar (2 to 7 psi) range.
5. If the valve is to be fitted at a high point in the system, the
system should be vented to prevent trapped air around the
temperature elements.
6. For optimum temperature regulation the system should be
designed so that the element is in the mid-position under
nominal conditions. To achieve this, it may be necessary to
balance the fluid flow by inserting an orifice in the by-pass
circuit.
7. If appropriate, read and understand the legal requirements
of installing the valve within the European Union as
described in Section 4.

18
Installation
Revision: 2 – Sept 2020 OMMC00296
5.1.2 Mounting the Valve in the Pipe
The valve may be mounted in any orientation; but should be
adequately supported and not subjected to excessive bending and/or
stress. Ensure the pipe flange connections are correctly aligned to
avoid stressing the valve body.
For the main flanged ports, bolting and gaskets should comply with
the relevant standard.
All relevant local regulations must also be observed.
5.1.3 Start up
Upon installation and on start-up of the system, all parts of the
circuit should be closely monitored to ensure correct performance. A
system in which the valve has been properly selected for the
anticipated flows should operate very closely to the valve’s nominal
temperature rating.
Water cooling systems will usually operate at or slightly below the
nominal temperature. Lubricating oils and most other higher viscosity
fluids will operate at or slightly above the nominal temperature.
In any system where the indicated temperatures are more than
2.7°C (5°F) from the nominal temperature, then effort should made
to locate the cause.
Any system operating at an indicated 5.5°C (10°F) or more from the
nominal anticipated temperatures may well be malfunctioning and
the cause should be located and rectified immediately. See trouble-
shooting section for possible causes.

19
Operation
Doc No: OMMC00296 Revision: 2 – Sept 2020
Section 6
Operation
6.1 Operation
The Model C valve is completely automatic in operation and needs no
power supply.
Temperature control is achieved by the automatic movement of a
sliding valve, regulating the fluid flow between ports. Upon an
increase in fluid temperature, large forces are created by a highly
temperature sensitive expanding wax mixture in the element bulb, in
turn acting upon the sliding valve.
6.1.1 Diverting applications
(controls outlet temp from load source)
When valves are used for diverting service, the inlet port A
(temperature sensing port), with Port C being connected to the
cooler, and Port B connected to the cooler by-pass line.
6.1.2 Mixing applications
(controls inlet temp to load source)
When valves are used for mixing service, Port C is the cold fluid inlet
port from the cooler, Port B is the hot by-pass fluid inlet, and Port A
the common outlet. Port A is the temperature sensing port and will
mix the hot and cold fluids in the correct proportion so as to produce
the desired outlet temperature leaving Port A.

20
Operation
Revision: 2 – Sept 2020 OMMC00296
6.1.3 2-way Water Saving Applications
Valve as shown maintains minimum flow through cooler to conserve
water. Requires an internal leak hole to permit a small flow for
sensing.
Table of contents
Other AMOT Control Unit manuals
Popular Control Unit manuals by other brands
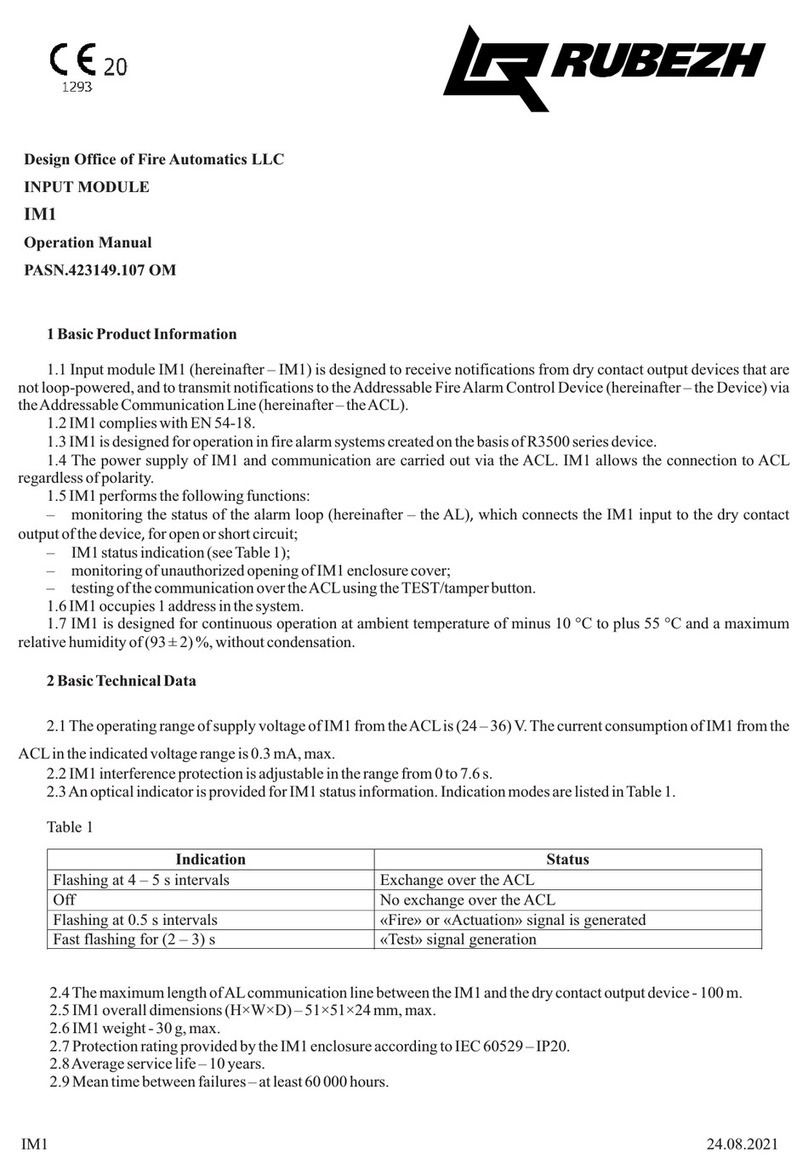
RUBEZH
RUBEZH IM1 Operation manual
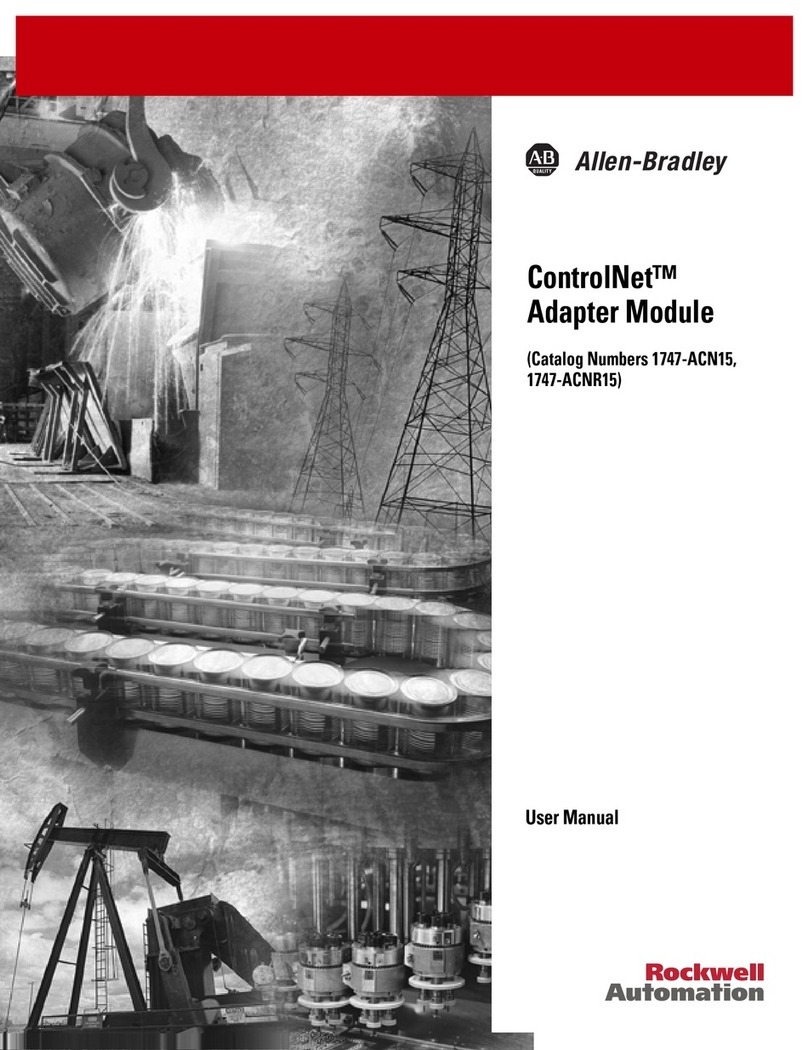
Allen-Bradley
Allen-Bradley ControlNet 1747-ACN15 user manual
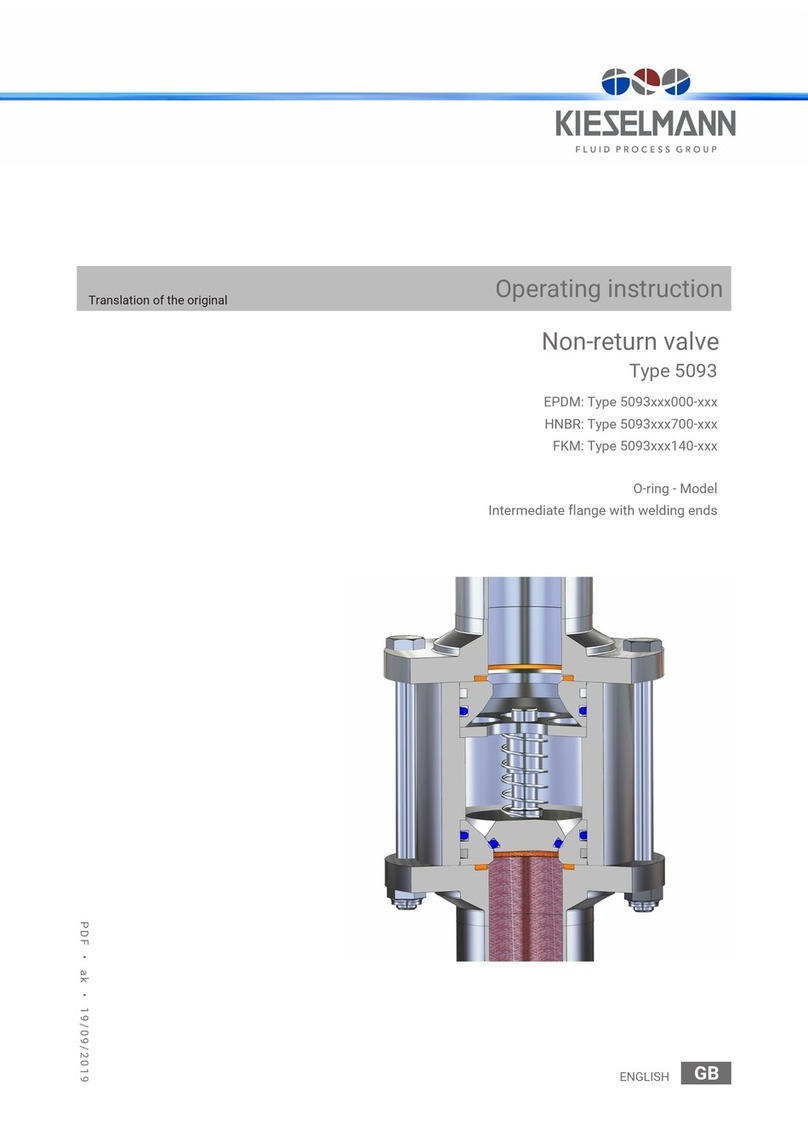
KIESELMANN
KIESELMANN 5093 Series Operating instruction
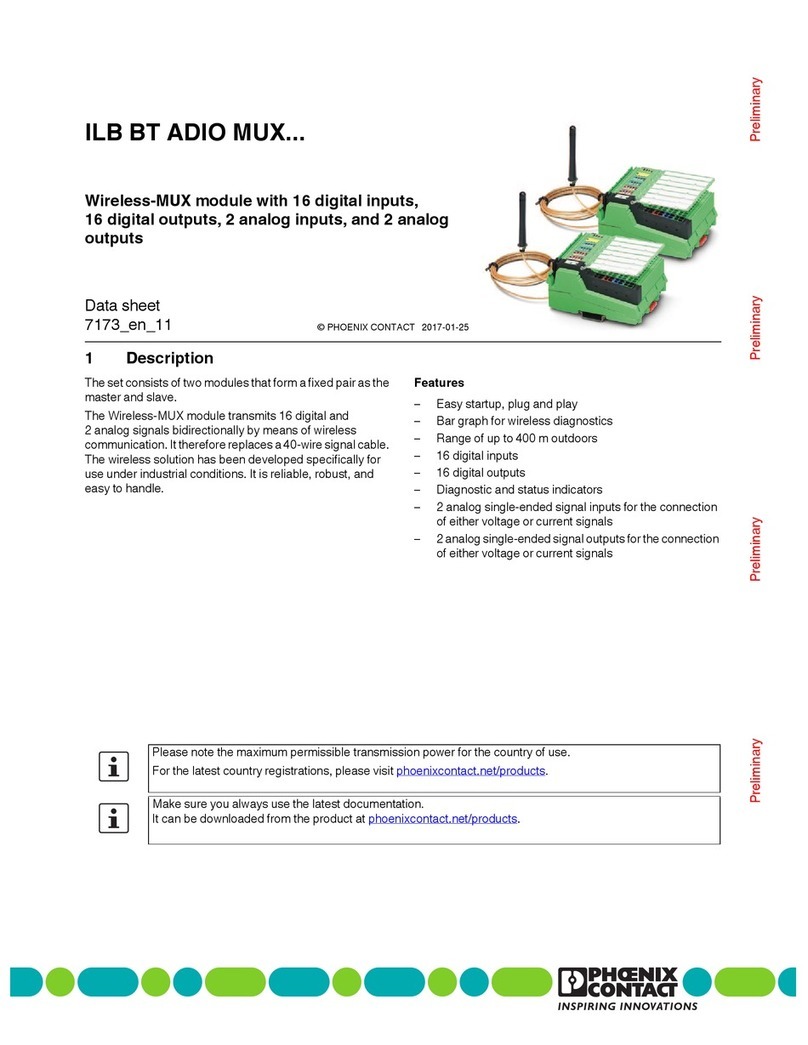
Phoenix Contact
Phoenix Contact ILB BT ADIO MUX-OMNI datasheet
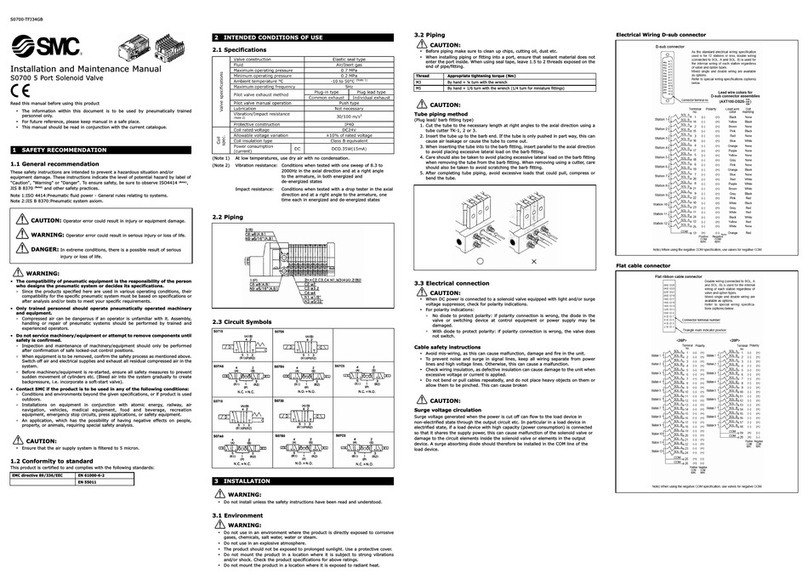
SMC Networks
SMC Networks S0700 Installation and maintenance manual
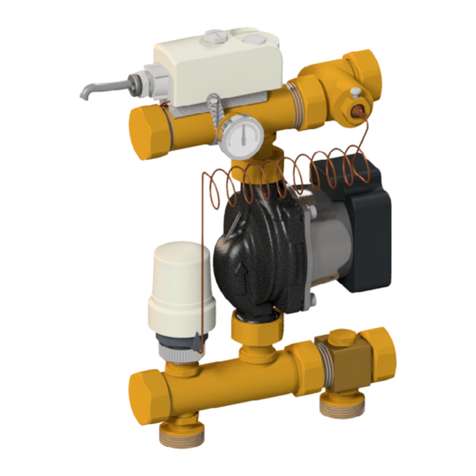
Watts
Watts FRG3015-F RV Installation and operating manual