AMT 4562 User manual

ArA
INSTRUCTION
MANUAL
DRILL
PRESS
FOR
YOUR
OWN
SAFETY
READ
INSTRUCTION
MANUAL
BEFORE
OPERATING
DRILL
PRESS
RETAIN
THIS
MANUAL
FOR
FUTURE
REFERENCE
10415031
UL.
CSA

CONTENTS
Page
WARNING.
1
GENERAL
SAFETY
INSTRUCTIONS.1
SAFETY
INSTRUCTIONS
FOR
DRILL
PRESS.2
VOLTAGE
WARNING..
GROUNDING
INSTRUCTION.
3
ASSEMBLY.
.
ADJUSTMENT.
.
OPERATION.
.
ROUND-OUT
TOLERANCE.
.
LUBRICATION.
.
MAINTENANCE.
.
TROUBLESHOOTING.
g
ASSEMBLY
DIAGRAM....‘.
1
Q
PARTS
LIST.

WARNING
For
Your
Own
Safety
Read
Instruction
Manual
Before
Operating
Drill
Press
1.
Wear
eye
protection.
//
2.
Do
not
wear
gloves,
necktie,
or
loose
clothing.
3.
Clamp
workpiece
or
brace
against
column
to
prevent
rotation.
»
4.
Use
recommended
speed
for
drill
accessory,
and
workpiece
material.
-
GENERAL
SAFETY
INSTRUCTIONS
1.
KELP
GUARDS
IN
PLACE
and
in
working
order.
2.
REMOVE
ADJUSTING
KEYS
AND
WRENCHES.
From
habit
of
checking
to
see
that
keys
and
adjusting
wrenches
are
removed
from
tool
before
turning
it
on.
3.
KEEP
WORK
AREA
CLEAN.
Cluttered
areas
and
benches
invite
accidents.
4.
DON’T
USE
IN
DANGEROUS
ENVIRONMENT.
Don’t
use
power
tools
in
damp
or
wet
locations,
or
expose
them
to
rain.
Keep
work
area
well
lighted.
5.
KEEP
CHILDREN
AW
AY.
All
visitors
should
be
kept
a
safe
distance
from
work
area.
b.
MAKE
WORKSHOP
KID
PROOF
with
padlocks,
master
switches,
or
by
removing
starter
keys.
7.
DON’T
FORCE
TOOL.
It
will
do
the
job
better
and
safer
at
the
rate
for
which
it
was
designed.
8.
USE
RIGHT
TOOL.
Don't
force
too!
or
attachment
to
do
a
job
for
which
it
was
not
designed.
9.
WEAR
PROPER
APPAREL.
No
loose
clothing,
gloves,
neckties,
rings,
bracelets,
or
other
jewelry
to
get
caught
in
moving
parts.
Nonslip
lootwear
is
recommended.
Wear
protectective
hair
covering
to
contain
long
hair.
10.
ALWAYS
USE
SAFETY
GLASSES.
Also
use
face
or
dust
mask
if
cutting
operation
is
dusty.
Everyday
eyeglasses
only
have
impact
resistant
lenses,
they
are
NOT
safety
glasses.
11.
SECURE
WORK.
Use
calmps
or
a
vise
to
hold
work
when
practical.
It’s
safer
than
using
your
hand
and
it
frees
both
hands
to
operate
tools.
12.
DON’T
OVER
REACH.
Keep
proper
footing
and
balance
at
all
times.
13.
MAINTAIN
TOOLS
WITH
CARE.
Keep
tools
sharp
and
clean
for
best
and
safest
performance..
Follow
instructions
for
lubricating
and
changing
accessories.
14.
DISCONNECT
TOOLS
before
servicing;
when
changing
accessories
such
as
blades,
bits,
cutters,
etc.
15.
REDUCE
THE
RISK
OF
UNINTENTIONAL
STARTING.
Make
sure
switch
is
in
off
position
before
plugging
in.
16.
USE
RECOMMENDED
ACCESSORIES.
Consult
the
owner's
manual
for
recommended
accessories.
The
use
of
improper
accessories
may
cause
risk
of
injury
to
persons.
17.
NEVER
STAND
ON
TOOL.
Serious
injury
could
occur
it
the
tool
is
unintentionally
contacted.
18.
CHECK
DAMAGED
PARTS.
Before
further
use
of
the
tool,
a
guard
or
other
part
that
is
damaged
should
be
carefully
checked
to
determine
that
it
will
operate
properly
and
perform
its
intended
function-
check
for
alignment
of
moving
parts,
binding
of
moving
parts,
breakage
of
parts,
mountin,
and
any
other
conditions
that
may
affect
its
operation.
A
guard
or
other
part
that
is
damaged
should
be
properly
repaired
or
replaced.
19.
DIRECTION
OF
FEED.
Feed
wuik
into
a
blade
or
cutter
against
the
direction
of
rotation
of
the
blade
or
cutter
only.
20.
NEVER
LEAVE
TOOL
RUNNING
UNATTENDED.
TURN
POWER
OFF.
Don’t
leave
tool
until
it
comes
to
a
complete
stop.

SAFETY
INSTRUCTIONS
FOR
DRILL
PRESS
1.
Wear
eye
protection.
2.
Do
not
wear
gloves,
necktie,
or
loose
clothing.
*
3.
Clamp
workpiece
or
brace
against
column
to
prevent
rotation:
4.
Use
recommended
speed
for
drill
accessory,
and
workpiece
material.
5.
Be
sure
drill
bit
or
cutting
tool
is
securely
locked
in
the
chuck.
6.
Be
sure
chuck
key
is
removed
from
the
chuck
before
turning
on
power.
'
7.
Adjust
the
table
or
depth
stop
to
avoid
drilling
into
the
table.
Shut
off
the
power
remove
the
drill
hit
and
clean
the
table
before
leaving
the
machine.
8.
Do
not
operate
until
it
is
completely
assembled
and
installed
according
to
the
instructions.
9.
If
any
part
of
your
drill
press
has
malfunction
or
has
been
damaged
or
broken.do
not
operate
until
the
part
is
properly
repaired
or
replaced.
10.
Never
place
your
fingers
in
a
position
where
they
could
contact
the
drill
or
other
cutting
tool
if
the
workpiece
should
unexpectedly
shift.
11.
Never
use
your
hand
to
hold
on
the
object
while
drilling,
always
screw
the
object
tight
on
the
working
table
or
use
the
drill
vise
to
prevent
accident
injury.
12.
Never
perform
any
operation
by
moving
the
head
or
table
with
respect
to
one
another.
Do
not
pull
the
motor
switch
“I”
or
start
any
operation
before
checking
the
head
and
table
lock
handles
are
clamp¬
ed
tight
to
column,
and
head
and
table
support
collars
are
correctly
positioned.
13.
Before
pulling
the
motor
switch
“I”
be
positive
the
belt
guard
is
down
the
chuck
is
installed
propei-
ly.
14.
Lock
the
motor
switch
when
leaving
the
drill
press.
Do
not
perform
layout,
assembly
or
setup
w'ork
on
the
table
while
the
cutting
tool
is
rotating.
VOLTAGE
WARNING
1.
Before
connecting
the
tool
to
a
power
source
(receptacle,
outlet,
etc.J
Be
sure
the
voltage
supplied
is
the
same
as
the
rating
on
the
tool
itself.
2.
A
power
source
with
voltage
greater
than
that
specified
for
the
tool
can
result
in
serious
injury
to
the
user.
3.
If
you’re
unsure
of
the
voltage
rating
do
not
use
tool.
Using
a
power
source
with
voltage
less
or
more
than
the
motor
rating
will
harm
the
motor.
2

GROUNDING
INSTRUCTIONS
1
In
the
event
of
a
malfunction
or
breakdown,
grounding
provides
a
path
of
least
resistance
for
electric
current
to
reduce
the
risk
of
electric
shock.
This
too!
is
equipped
with
an
electric
cord
having
an
equipment-grounding
conductor
and
a
grounding
plug.
The
plug
must
be
plugged
into
a
matching
outlet
that
is
properly
installed
and
grounded
in
accordance
with
all
local
bodes
and
ordinances.
2.
Do
not
modify
the
plug
provided-
if
it
will
not
fit
the
outlet,
have
the
proper
outlet
installed
by
a
qualified
electrician.
*
3.
Improper
connection
of
the
equipment-grounding
conductor
can
result
in
a
risk
of
electric
shock.
The
conductor
with
insulation
having
an
outer
surface
that
is
green
with
or
without
yellow
stripes
is
the
equipment-grounding
conductor,
if
repair
or
replacement
of
the
electric
cord
or
plug
is
necessary,
do
not
connect
the
equipment-grounding
conductor
to
a
live
terminal.
4.
Check
with
a
qualified
electrician
or
serviceman
if
the
grounding
instructions
are
not
completely
understood,
or
if
in
doubt
as
to
whether
the
tool
is
properly
grounded.
5.
Use
only
3-wire
extension
cords
that
have
3-prong
grounding
plugs
and
3-pole
receptacles
that
accept
the
tool’s
plug.
6.
Repair
or
replace
damaged
or
worn
cord
immediately.
7
This
tool
is
intended
for
use
on
a
circuit
that
has
an
outlet,
grounding
plug
that
looks
like
the
one
illus¬
trated
in
Fig
1
A
temporary
adapter,
which
looks
like
the
adapter
illustrated
in
Sketches
B
and
C,
may
be
used
to
connect
this
plug
to
a
2-pole
receptacle
as
shown
in
Sketch
B
if
a
properly
grounded
outlet
is
not
available.
The
temporary
adapter
should
be
used
only
until
a
properly
grounded
outlet
can
be
installed
by
a
qualified
electrician.
The
green-colored
rigid
ear,
lug,
etc.
extending
from
the
adapter
must
be
connected
to
a
permanent
ground
such
as
a
properly
grounded
outlet
box.
The
adapter
is
not
alowed
for
use
in
Canada.
GROUNDING
METHODS
©
j£>
©
COVER
OF
GROUNDED
R
•—
OUTLET
BOX
(B)
AO
API
QL
GROUNDING
MEANS
Fig.
1
Grounding
methods
indicated
above
are
only
allowed
in
America
Continent.
For
other
counturies,
the
grounding
plug
and
outlet
box
may
differ
from
above.
Please
check
that
with
a
qualified
electrician.
3

UNPACKING
Carefully
unpack
the
drill
press
and
all
loose
items
from
the
carton.
Check
the
loose
parts
by
“Parts
List”
in
page
11.
ASSEMBLY
1.
BENCH
TYPE
DRILL
PRESS
ONLY
Assemble
column
(A)
Fig.
2,
to
base
(B)
using
four
screws
(three
of
which
are
shown
at
(C)
).
Loosen
set
screw
in
collar
(D)
and
remove
collar
(D)
and
raising
rack
(E).
2.
Place
raising
rack
(E)
in
position
inside
table
bracket
(F)
making
sure
gear
on
inside
of
table
bracket
is
engaged
with
teeth
of
raising
rack.
Then
Slide
table
bracket
(F),
with
raising
rack
(E)
onto
column
(A),
as
shown.
Engage
bottom
of
collar
(D)
with
top
of
rack
(E)
and
tighten
set
screw
(G)
in
collar.
3.
FLOOR
TYPE
DRILL
PRESS
ONLY
Assemble
column
(A)
to
the
base
(B)
using
the
four
screws
(C),
as
shown
in
Fig.
4.
Note:
Table
bracket
(F)
is
shipped
assembled
to
the
column,
as
shown
.
4

BENCH
AND
FLOOR
DRILL
PRESSES
4.
Assemble
table
(G)
to
table
bracket,
as
shown
in
Fig.
4,
and
lock
in
place
using
the
table
rotating
lock
screw
(H).
5.
Place
the
drill
press
head
on
column,
as
shown.
Line
up
head
with
base
and
tighten
two
head
locking
screw,
(I).
not
shown
(in
the
opposite
side
on
Fig.
5).
6.
Thread
the
three
feed
handles
(J)
Fig.
6,
into
the
three
threaded
holes
in
the
pinion
shaft.
7.
Assemble
table
raising
and
lowering
handle
(K)
Fig.
5
to
shaft
on
table
bracket
Line
up
flat
on
shaft
with
screw
(L)
and
tighten
it.
8.
Make
certain
the
bottom
taper
of
the
spindle
adapter(U),
and
the
tapered
hole
in
the
chuck
(R)
are
clean
and
push
the
chuck
up
onto
the
spindle
adapter
as
far
as
it
will
go.
See
Fig.
6
and
Fig.
7
or
Fig.
8,
Fig.
9
and
Fig.
10
for
whichever
inapplicable.
Note:
A.
Before
tapping
the
chuck
(R),
see
Fig.
7
&
10,
onto
spmdle
adapter,
open
the
chuck
jaws
as
wide
as
possible
by
turning
chuck
sleeve.
To
avoid
damage
to
the
chuck,
do
not
drive
the
chuck
directly
onto
the
spindle
adapter
with
a
metal
hammer.
Use
a
mallet
or
a
block
of
wood
is
recommended.
B.
When
push
spindle
adapter
(U)
Fig.
8
up
into
spindle
(T)
making
certain
the
tang
(V)
engages
and
locks
with
the
mating
slot
inside
spindle
(T).
Fig.
6
Fig.
8
Fig.
7
5
Fig.
9

ADJUSTMENTS
BEFORE
ADJUSTMENT,
DISCONNECT
THE
DRILL
PRESS
FROM
THE
POWER
SOURCE.
1.
For
the
purpose
of
automatically
returning
the
spindle
upward
after
a
hole
has
been
drilled,
a
spindle
return
spring
is
provided
in
the
spring
housing
(A)
Fig.
12.
This
spring
has
been
properly
adjusted
at
the
factory
and
should
not
be
disturbed
unless
absolutely
necessarily.
To
adjust
the
return
spring,
proceed
as
follows:
A.
Loosen
the
two
nuts
(B)
Fig.
12,
approximately
one-
quarter
inch.
IMPORTANT:
DO
NOT
REMOVE
NUT
(B)
FROM
SHAFT.
B.
While
FIRMLY
holding
spring
housing
(A)
Fig.
12,
pull
out
housing
and
rotate
it
until
the
roll
pin
(C)
is
engaged
with
the
next
notch
on
the
housing.
Turn
the
housing
counter-clockwise
to
increase
and
clock¬
wise
to
decrease
spring
tension.
Then
tighten
the
two
nuts
(B)
to
hold
the
housing
in
place.
IMPORTNAT:
NUTS
(B)
SHOULD
NOT
CONTACT
SPRING
HOUSING
(A)
WHEN
TIGHT.
2.
Where
a
number
of
holes
are
to
be
drilled
to
exactly
the
same
depth,
a
depth
stop
is
provided
in
the
pinion
shaft
housing
(A)
Fig.
13.
and
is
used
as
follwos:
A.
Loosen
lock
lever
(B)
Fig.
13,
and
rotate
housing
(A)
until
the
pointer
(C)
lines
up
with
the
depth
indicat¬
ed
on
the
inch
/metric
scale
(D)
you
want
the
spindle
to
lower.
Then
tighten
lock
lever
(B).
B.
The
spindle
will
then
low'er
to
the
exact
depth
as
indicated
on
the
scale
(D)
Fig.
13.
3.
To
adjust
table,
hold
the
table
with
one
hand
and
loosen
in
the
desired
position
and
retighten
the
lock
handle.
4.
Rotation
of
work
table:
Loosen
the
table
position.
To
obtain
more
distance
between
the
chuck
and
the
table,
the
work
table
can
be
rotated
180°
and
the
base
can
be
used
as
a
work
table.
This
will
per¬
mit
the
drilling
of
larger
objects.
5.
To
tilt
table,
loosen
the
pivot
bolt.
(A)
Fig.
14
Remove
the
small
locator
pin
(B).
To
do
this
"tighten”
the
nut
until
the
pin
easily
slips
out.
Tilt
the
table
to
the
desired
angle
up
to
45
and
retighten
bolt.
Reinsert
the
locator
pin
when
returning
the
table
to
zero
degree.
Fig.
14
6


6.
For
spindle
speeds,
please
refer
to
the
speed
diagram
inside
pulley
cover.
A
list
relates
how
to
choose
drill
bit
size
and
revolution
for
various
materials
is
available
for
your
reference
as
below.
Reference
List
of
Drill,
Revolution
and
Various
Materials
Material
Cast
Iron
Steel
Iron
Aluminum
Gun
Metal
Rotative
i
speed
R.P.M.
\
Drill
\
\
Dia.
(mm)
\\
es3
2550
1600
2230
9500
8000
0
4
1900
1200
1680
7200
6000
0
5
1530
955
1340
5700
4800
06
1270
800
1100
4800
4000
0
7
1090
680
960
4100
3400
0
8
960
600
840
3600
3000
.
0-9
850
530
740
3200
2650
0
I
O
765
480
670
2860
2400
0-11
700
435
610
2600
2170
0
I
2
640
400
560
2400
2000
0
13
590
370
515
2200
1840
0
14
545
340
480
2000
1700
0
1
6
480
300
420
1800
1500
0-18
425
265
370
1600
1300
0
20
380
240
335
1400
1200
022
350
220
305
1300
1100
025
305
190
270
1150
950
7.
To
change
spindle
speed,
loosen
the
slide
bar
bolt
(A),
See
Fig.
14.
Slide
the
motor
toward
the
front
of
the
drill
press
and
then
tighten
the
slide
bar
bolt.
This
will
loosen
the
belt
and
permit
relocating
the
belt
to
the
desired
pulley
for
the
required
spindle
speed.
After
selection
has
been
made,
loosen
the
slide
bar
bolt,
slide
the
motor
toward
the
rear
of
the
drill
press
and
tighten
the
slide
bar
bolt
again,
check
the
belt
for
proper
tension
and
make
any
final
adjustment.
Fig.
14
7

OPERATION
Use
scrap
material
for
practice
to
get
the
feel
of
the
machine
before
attempting
regular
work.
1.
Screw
tight
the
object
on
the
working
table
while
drilling,
so
as
to
prevent
injuries
and
to
have
a
precision
workmanship.
2.
You
can
place
the
size
of
drill
bit
you
desire
in
the
chuck.
3.
Plug
the
electric
socket
to
the
outlet
and
turn
the
switch
“ON’*
then
the
spindle
shaft
will
rotate
freely.
4.
When
drilling,
hold
on
the
feed
handle
Q),
See,
Fig.
5.
and
press
downward.
5.
Factors
which
determine
the
best
speed
to
use
in
any
drill
press
operation
are:
Kind
of
material
being
worked,
size
of
hole,
type
of
drill
or
other
cutter,
and
quality
of
cut
desired.
The
smaller
the
drill,
the
greater
the
required
RPM.
In
soft
materials,
the
speed
should
be'
higher
than
for
hard
metals.
See
“ADJUSTMENT”
section
item
6.
6.
Use
clamps
to
hold
the
work
when
drilling
in
metal.
The
work
should
never
be
held
in
the
bare
hand;
the
lips
of
the
drill
may
seize
the
work
at
any
time,especially
when
breaking
through
the
stock.
If
the
piece
is
whirled
out
of
the
operator’s
hand.he
may
be
injured.
In
any
case,the
drill
will
be
broken
when
the
work
strikes
the
column.
The
work
must
be
clamped
firmly
while
drilling;
any
tilting
twisting
or
shifting
results
not
only
in
a
rough
hole,
but
also
increases
drill
breakage.
For
flat
work,
lay
the
piece
on
a
wooden
base
and
clamp
it
firmly
down
against
the
table
to
prevent
it
from
turning.
If
the
piece
is
of
irregular
shape
and
cannot
be
laid
flat
on
the
table,
it
should
be
securely
blocked
and
clamped.
7.
Boring
in
Wood
Twist
drills,
although
intended
for
metal
drilling,may
also
be
used
for
boring
holes
in
wood.
However,
machine
spur
bits
are
generally
preferred
for
working
in
wood;
they
cut
a
square
bottom
hole
and
are
designed
for
removal
of
wood
chips.
Do
not
use
hand
bits
which
have
a
screw
tip;
at
drill
press
speeds
they
turn
into
the
wood
so
rapidly
as
to
lift
the
work
off
the
table
and
whirl
it.
For
throgli
boring,
line
up
the
table
so
that
the
bit
will
enter
the
center
hole
to
avoid
damage.
Scribe
a
vertical
line
on
the
front
of
the
column
and
a
matchmark
on
the
table
bracket,
so
that
the
table
can
be
clamped
in
center
position
at
any
height.
Feed
slowly
when
the
bit
is
about
to
cut
through
the
wood
to
prevent
splintering
the
bottom
face.
Use
a
scrap
piece
of
wood
for
a
base
block
under
the
work.
This
helps
to
teduce
splintering
and
protects
the
point
of
the
bit.
ROUND-OUT
TOLERANCE
l
ot
drilling
operations
requiring
dose
tolerances,
place
drill
blank
in
the
chuck
and
check
round
out
with
a
dial
indicator
if
the.
round-out
is
not
within
desired
tolerance,
tap
the
chuck
bottom
with
a
rubber
or
leather
mallet
until
you
get
the
desired
tolerance.
LUBRICATION
The
ball
bearings
in
the
quill
and
V-belt
pulley
are
grease-sealed
for
life.
Pull
quill
down
to
maximum
depth
and
oil
moderately
once
every
3
months.
Oil
slide
bars
lightly
every
2
months.
Grease
bracket
if
cranking
becomes
difficult.
MAINTENANCE
After
using
the
machine
you
have
to
clean
it
completely
and
lubricate
all
sliding
and
moving
parts.
8

TROUBLE
SHOOTING
Warning:
For
your
own
safety,
turn
switch
“Off'
and
always
remove
plug
from
power
source
outlet
before
trouble
shooting.
//
Trouble
Probable
Cause
Remedy
Noisy
operation
1.
Incorrect
belt
tension
1.
Adjust
tension.
2.
Dry
spindle.
2.
Lubricate
spindle.
See
"Lubrication"
section.
3.
Loose
spindle
pulley
or
motor
pulley.
3.
Tighten
set
screws
in
pulleys.
Bit
burns
or
smokes
1.
Incorrect
speed.
1.
Change
speed.
2.
Chips
not
coming
out
of
hole.
2.
Retract
bit
frequently
to
clear
chips
3.
Dull
bit.
3.
Sharpen
or
replace
bit.
4.
Feeding
too
slow.
4.
Feed
fast
enough
.
.
.
allow
drill
to
cut.
5.
Not
lubricated.
5.
Lubricate
bit.
6.
Bit
running
backwards.
6.
Check
motor
rotation.
Excessive
drill
1.
Bent
bit.
1.
Use
a
straight
bit.
runout
or
wobble
2.
Worn
spindle
bearings.
2.
Replace
bearings.
3.
Bit
not
properly
installed
in
chuck.
3.
Install
bit
properly.
4.
Chuck
not
properly
installed.
4.
Install
chuck
properly.
Drill
binds
in
workpiece
1.
Workpiece
pinching
bit
or
excessive
feed
pressure.
1
.
Support
or
clamp
workpiece.
2.
Improper
belt
tension.
2.
Adjust
tension.
Workpiece
torn
loose
from
hand
1.
Not
supported
or
clamped
properly.
1.
Support
or
clamp
workpiece
r
9

10
I


P
ART
S
LIST
(I*
1
ease
put
down
code
No.,
part
No.,
and
description
for
service)
Issued:
Sep.
12,
1990
Code
Part
Number
Description
Size
Q’ty
Code
Part
Number
Description
Size
02
A104001
A106002
Base
Column
Holder
1
1
52
53
10605202
2701QZD610
Seat
Set’Screw
Hex.
Nut
l/2”x20UNF,
T=10
1
1
2603BBLA66
Set
Screw
M10xl.5-12
54
10405402
Quill
Set
Screw
M8xl.25-22
04
A104004
Column
1
55
2701FZD108
Hex.
Nut
M8xl.25,
T=6
05
2601BBDA72
Hex.
Hd.
Screw
Ml
Ox
1.5-40
1
56
A104056
Quill
1
1
1
06
07
08
10600604
10600702
10600802
Bracket
Gear
Shaft
1
1
1
57
58
59
10305701
A104058*
2001ZZ6204
Rubber
Washer
Shaft
Ball
Bearing
6204ZZ
10600902
Worm
1
61
20015Z6201
Ball
Bearing
6201Z
1
10
10601002
Handle
1
62
2570BBN111
C-Ring
All
11
2601BZDA39
Hex.
Hd.
Screw
M6xl0-12
1
63
2570BBN117
C-Ring
A17
14
10601401
Pin
1/4”-30
1
65
10306522
Driving
Sleeve
15
2701QZD506
Hex.
Nut
l/4”x20UNC,
T=4.7
1
66
20015Z6203
Ball
Bearing
6203Z
16
17
18
10601601
10601702
2658MZDU36
Scale
Angle
Scale
Drive
Screw
0
2.3-5
1
1
4
67
69
70
10306701
10306901
A104070
Collar
Set
Nut
Spindle
Pulley
40
2
1
19
10601901
Column
Lock
Handle
Ml
2
1
72
2137103504
Chuck
(Optional;
20
21
22
23
24
10602001
A106021
A104022
A106023
2603BBLA39
Table
Lock
Handle
Table
Rack
Rack
Ring
Hex.
Soc.
Set
Screw
M10
M6xl.0-12
1
1
1
1
74
75
76
77
A104074
A2790
2615BZDD28
2501NZDN26
Motor
Motor
Wire
Hex.
Hd.
Screw
Flat
Washer
M8xl.25-25
5/16x7/8-5/64
1
1
4
4
25
10402506
Head
78
2701FZD108
Hex.
Nut
M8xl.25,
T=6
4
26
2603BBLA52
Hex.
Soc.
Set
Screw
M8xl.25-8
2
79
A104079
Motor
Pully
1
31
10403102
Spring
80
2571NNC204
Key
3/16”x3/16”-20
1
32
10403216
Slide
Bar
81
2603BBLA36
Hex.
Soc.
Set
Screw
M6xl0-6
2
33
10604201
Slide
Bar
Screw
M8xl.25-17
1
82
A2480
Strain
Relief
2
34
35
A104034
2501NZDN37
Motor
Base
Washer
1/2x1'/
4
-7/64
1
2
85
87
A2780
28503102
Cable
Switch
1
1
36
2601BZDA56
Hex.
Hd.
Screw
M8xl.
25-25
2
88
A103088
Switch
Cover
1
37
38
10303701
10403826
Handle
Body
Feed
Shaft
1
1
90A
92
10409005
2638BZDA39
Pulley
Cover
Cr.
Re.
Hd.
Screw
M6xl.0-12
1
4
39
2536MBE611
Spring
Pin
0
5-16
95
A104095
Center
Pulley
1
40
10404002
Scale
Set
Pin
96
20015Z6202
Ball
Bearing
6202Z
1
42
10604201
Slide
Bar
Screw
M8xl.25-17
98
10609802
Pulley
Shaft
1
43
44
A104043
A104044
Handle
Bar
Gripe
3
99
100
A2572ARM
2603BBLA52
V-Belt
Hex.
Soc.
Set
Screw
M8xl.25-8
1
1
45
10304501
Spindle
Depth
101
2501NNVN11
Plat
Washer
l/4”x3/4”-3/l
6
4
46
47
A104046
10604701
Scale
Spindle
Centering
Scale
1
1
119
149
2572ARM
2536MBE623
V-Belt
Spring
Pin
6-16
1
2
48
2658MZDU36
Drive
Screw
0
2.3-5
2
131
A2136BBD
Chuck
Key
(Optional)
1
49
50
10604902
10605002
10605115
Spring
Spring
Housing
Spring
Seat
Note:
1.
Parts
of
Code
Nos.
2
&
4,
37,
38
&
45,
43
&
44
are
served
as
one.
2.
Floor
Type
drill
press
is
the
same
as
Bench
Type,
except
code
Nos
of
2,
3.
4
Sc
22.
S.
Check
carefully
with.,the
loose
parts
are
counted
as
follows
(Nos
in
parenthesis
are
code
num-
bers)
(1)
Base
(1)
(2)
Column
Assembly
(For
floor
type,
Table
Bracket
is
shipped
assembled
to
the
column)
(3)
Hex.
Hd.
Screw
(5)
(4)
Table
(21)
(5)
Chuck
&
Key
(72,
131)
Optional
(6)
Lock
Handle
(19).
(7)
Raising
&
Lowering
Handle
(10)
(8)
Feed
Handles
(43
&
43)
(9)
Allen
Wrench
(700
&
701)
(10)
Instruction
Manual
11

Vjr+K
*wy
,ooi"‘
icAo<^|c
ka,L*uJ
3
circle
h»Lc.s.
a**
,064'
V
TIR.
+*»+**>
c^ocjc
fay
^
w
£>'
A-T
T*p
»*
Afa^
oroSS
HAT^N
,
T,/C
'
U5-«j
I/*
1
1
b
r
,
u
-
6/
1
*
<^^
l
c
,
4
»'«0'iA‘
+
''
4
-
^
®'*>
JO+
*°oy
Tl
.
r*
i
•
-
++_
-
0
bbSD-
»
4
«C
|$
Sa-f^
^
fN^ot)=-L
i
s.
4-5
k’S-
£)jk
c.
fi\JUjj
k
i
I
*

How
Table
is
attached
&
rotated
Concept
Drawing
by
Dale
C.
Maley
o
o
(/>
I/I
as
<v
°
?
■
3
*>
o
iH
T3
L?T
2
1-1
"O
JZ
OS
T3
>
ITS
>
nj
4->
1-
C
3
<V
Cl
o
O
o
‘M
"O
<u
fi
ID
J_)
^
o
Lf)
-Q
,H
S=
jz
ns
4->
I/)
>
o
5
o
4—>
o
c
-D
O
c
±i
<1>
i/i
4-1
O
-=
O-
o>_
A->
fU
«r
§
-Q
o
IS
c
a>
«
P
<5
cs
ft
as
as
c
o
cn-a
o
o
ITS
»-
_D
.
o
Ol
Ol
I
£
o
E
_C
3
^
%
o
oi
2
o
h-
4-1
u
I—
Si
-o
o
as
£
o
2
■
o
S
is
5
c
as
o
N
—
o
.2
f
ai
£
■
-
U
ro
as
-
D
o
_as
-sz
-Cl
Ol
2
■
-
B
g
£-2
S-g
-o'
2
ITS
o
2
O
V£>-
iH
—.
U
lo
rc
iH
_Q
a.
vo
"o
re
■
Sj^
-Q
a
~~~
as
in
JZ
as
ns
■
£
CL
ZJ
•
■
=
l-i
gll'l
'S-il
10
U
_£=
O
4~>
J->
<v


Table of contents
Other AMT Power Tools manuals
Popular Power Tools manuals by other brands
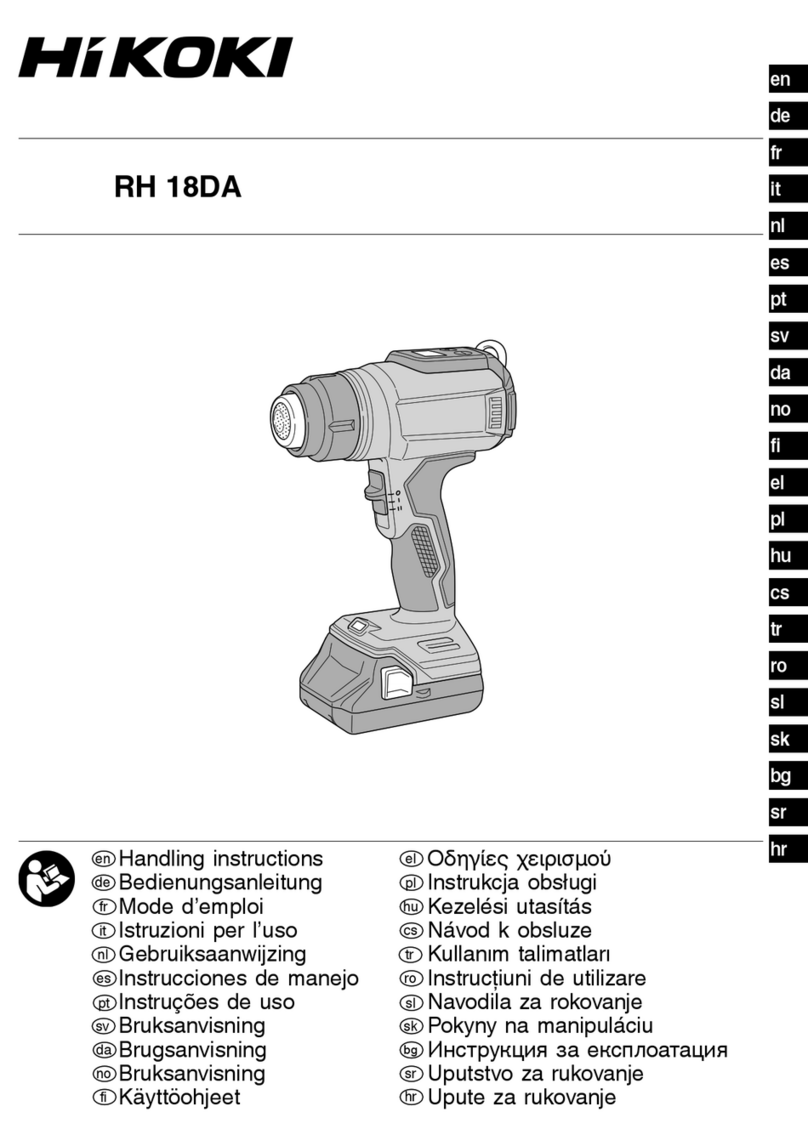
HIKOKI
HIKOKI RH18DAW2Z Handling instructions
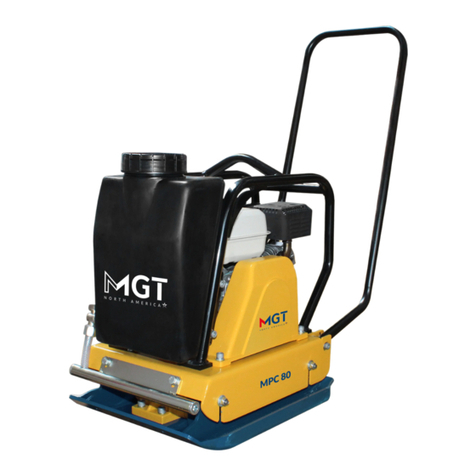
Discount Equipment
Discount Equipment MGT MPC 80 Technical manual

BIAX
BIAX FR 8-12PLUS Translation of the original operating manual

Weber mt
Weber mt CR 9-II Operating and maintenance manual
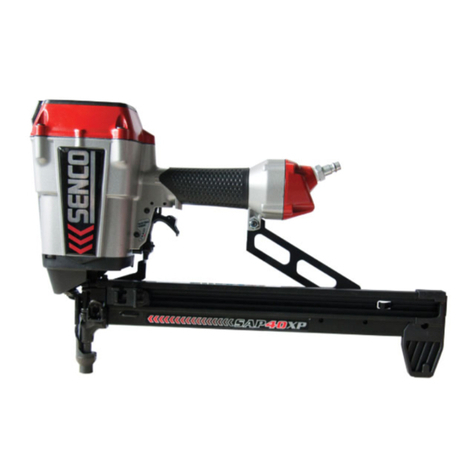
Senco
Senco SAP40XP operating instructions
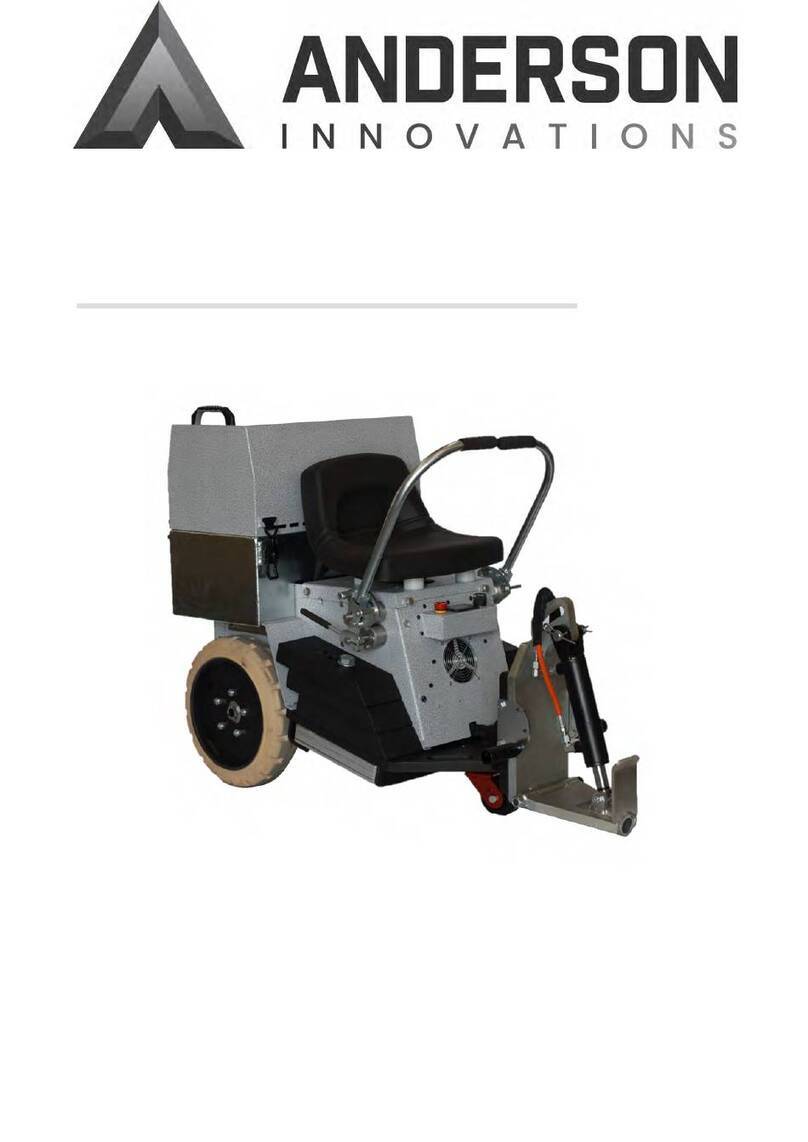
Anderson
Anderson ES 1300 user manual