Anaheim Automation DPY50611 User manual

1
#L010196 September 2005
DPY50611DPY50611
DPY50611DPY50611
DPY50611
Programmable Driver PackProgrammable Driver Pack
Programmable Driver PackProgrammable Driver Pack
Programmable Driver Pack
User’s GuideUser’s Guide
User’s GuideUser’s Guide
User’s Guide
910 East Orangefair Lane, Anaheim, CA 92801
website: www.anaheimautomation.com
ANAHEIM AUTOMATION, INC.ANAHEIM AUTOMATION, INC.
ANAHEIM AUTOMATION, INC.ANAHEIM AUTOMATION, INC.
ANAHEIM AUTOMATION, INC.

2
#L010196 September 2005
Table of ContentsTable of Contents
Table of ContentsTable of Contents
Table of Contents
Section 1: IntroductionSection 1: Introduction
Section 1: IntroductionSection 1: Introduction
Section 1: Introduction....................................................................................................................................................................................................................................................
....................................................................................................................................................................................................................................................
.......................................................................................................................... 33
33
3
Description ............................................................................................................................................... 3
Electrical Specifications ........................................................................................................................... 4
Ordering Information ................................................................................................................................ 4
Dimensions/Switch Locations .................................................................................................................. 5
Wiring Diagrams....................................................................................................................................... 5
Terminal Descriptions - Driver ................................................................................................................. 6
Motor Ground........................................................................................................................................... 6
Terminal Descriptions - Controller ........................................................................................................... 7
Connector Descriptions - Controller......................................................................................................... 7
Slide Switch Descriptions - Controller...................................................................................................... 7
Section 2: Driver FunctionsSection 2: Driver Functions
Section 2: Driver FunctionsSection 2: Driver Functions
Section 2: Driver Functions ....................................................................................................................................................................................................................................
....................................................................................................................................................................................................................................
.................................................................................................................. 88
88
8
Motor Selection ........................................................................................................................................ 8
Step Motor Current Setting Guide............................................................................................................ 8
Microstep Selection - Driver SW1 Settings .............................................................................................. 9
Setting the Output Current ....................................................................................................................... 9
Reducing Output Current ....................................................................................................................... 10
Determining Output Current................................................................................................................... 10
Step Motor Configurations ..................................................................................................................... 10
Connecting the Step Motor .................................................................................................................... 12
Short-Circuit, Mis-Wire, and Over-Current Conditions........................................................................... 12
Section 3: Controller FunctionsSection 3: Controller Functions
Section 3: Controller FunctionsSection 3: Controller Functions
Section 3: Controller Functions ..................................................................................................................................................................................................................
..................................................................................................................................................................................................................
......................................................................................................... 1313
1313
13
Methods of Communication ................................................................................................................... 13
Baud Rate .............................................................................................................................................. 13
Axis Selection......................................................................................................................................... 13
Controller Status LED ............................................................................................................................ 13
Technical Support .................................................................................................................................. 13
Section 4: SMC60WIN SoftwareSection 4: SMC60WIN Software
Section 4: SMC60WIN SoftwareSection 4: SMC60WIN Software
Section 4: SMC60WIN Software....................................................................................................................................................................................................................
....................................................................................................................................................................................................................
.......................................................................................................... 1818
1818
18
File Menu ............................................................................................................................................... 19
Setup Menu............................................................................................................................................ 19
Setup - Axis Menu.................................................................................................................................. 19
Program Menu ....................................................................................................................................... 20
Program - Autostart Program Menu....................................................................................................... 20
Edit Menu............................................................................................................................................... 20
Help Menu.............................................................................................................................................. 21
“The Unit is Connected” / “The Unit is NOT Connected” ....................................................................... 21
Toolbar ................................................................................................................................................... 22
Tab Sheets............................................................................................................................................. 22
Add/Change/Insert Commands.............................................................................................................. 27
Calculator ............................................................................................................................................... 32
Section 5: Direct Talk ModeSection 5: Direct Talk Mode
Section 5: Direct Talk ModeSection 5: Direct Talk Mode
Section 5: Direct Talk Mode ................................................................................................................................................................................................................................
................................................................................................................................................................................................................................
................................................................................................................ 3333
3333
33
Section 6: TroubleshootingSection 6: Troubleshooting
Section 6: TroubleshootingSection 6: Troubleshooting
Section 6: Troubleshooting ................................................................................................................................................................................................................................
................................................................................................................................................................................................................................
................................................................................................................ 4343
4343
43
Error Codes............................................................................................................................................ 44
Section 7: Sample ProgramsSection 7: Sample Programs
Section 7: Sample ProgramsSection 7: Sample Programs
Section 7: Sample Programs ............................................................................................................................................................................................................................
............................................................................................................................................................................................................................
.............................................................................................................. 4545
4545
45
Appendix 1: ASCII Table for Direct Mode .............................................................................................. 50
Appendix 2: Firmware Revisions............................................................................................................ 50

3
#L010196 September 2005
Section 1: IntroductionSection 1: Introduction
Section 1: IntroductionSection 1: Introduction
Section 1: Introduction
The DPY50611 is a single-axis 5A bipolar microstep driver/controller containing 2 Kbytes of nonvolatile
stored programming space, quadrature encoder feedback, and a 125W power supply, all enclosed in a
package. It provides flexible, independent control of bipolar stepper motors with a current range from 0.5
to 5.0 amps/phase with microstepping resolutions from 200 steps per revolution to 12,800 steps per
revolution from a computer, or any machine controller with a serial port. It is also capable of standalone
operation, making it an embedded machine controller. The easy to use Windows software, SMC60WIN,
can be used to directly control motion and to program the DPY50611. The DPY50611 also has the ability
for real time functions.
The DPY50611 has 40 commands, which are easy-to-remember for direct movement of the stepper
motor and communicates via an USB data bus. A windows driver is provided to communicate with the
DPY50611 through a virtual comport from the PC. This driver will turn any USB port into a virtual comport,
thus enabling simple serial programs to send information to the DPY50611. To use the SMC60Win soft-
ware, the virtual comport driver must be installed. Special functions of the controller include 8 program-
mable open collector outputs and 6 TTL, CMOS and 24V compatible inputs, a quadrature encoder input
with the ability to autocorrect, an analog input to control either maximum speed or absolute position,
registration mark indexing during a slew command, an output that will trigger during an index command at
an absolute position, and a thumbwheel input for indexing a motor. The DPY50611 can be powered from
90-135 VAC, 50/60Hz,
DescriptionDescription
DescriptionDescription
Description
The driver in the DPY50611 (MBC05641) is a microstep motor driver that can drive motors rated from 0.5
to 5.0 amps/phase. It can handle 4, 6 and 8-lead motors in a bipolar fashion. The DPY50611’s driver
features motor current ON/OFF capabilities and a Reduced Current Enable to automatically reduces
motor current to 50% of the set value after the last step is made (20msec delay). With the DPY50611,
various step resolutions can be implemented by the onboard dip switch. These divisions range from 200
steps per revolution to 12,800 steps per revolution. Protection devices have been added to this driver for
short circuit and open circuit conditions. The driver has built-in features to indicate power on (Green LED),
Clocks being received (Yellow LED) and fault conditions (Red LED).
The controller in the DPY50611 (PCL601USB) provides independent programming of acceleration/
deceleration, base speed (start up speed), max speed (running speed), jog speed, and the number of
steps to be taken in both relative and absolute positioning modes. On absolute positioning moves, the
DPY50611 automatically determines the proper direction to go and the number of steps to take. The
relative positioning will move a number of steps in the direction that the user defines. The DPY50611 also
has specific functions such as
encoder feed back, autocorrection, index-on-the-fly and output-on-the-fly
.
An analog input can be used to set either the maximum speed or goto an absolute position based between
the upper and lower programmable limits. A seven decade thumbwheel switch can be read for relative
indexing. The DPY50611 also has a high level programming command set that includes: branching,
looping,conditionalstatements,timedelays,textstrings,and I/O which the user canuse in theprogramming
mode to fully control all machine functionality. A home input, a set of bidirectional hard and soft limit switch
inputs and bidirectional jog inputs are provided for each axis. These features are generally required in
most machine control designs. 6 testable TTL, CMOS and 24V compatible inputs and 8 programmable
open-collector outputs are provided per axis. The I/O may be used for monitoring and controlling machine
operation and/or interaxis coordination. The I/O are accessible independent of the busy state of the axis
controls. The DPY50611 has a built-in programmable reset circuit. Reset is automatic on power-up, or by
pressing the external reset button.

4
#L010196 September 2005
Electrical SpecificationsElectrical Specifications
Electrical SpecificationsElectrical Specifications
Electrical Specifications
Power Requirements:Power Requirements:
Power Requirements:Power Requirements:
Power Requirements:
90-135 VAC 50/60Hz
Operating Temperature:Operating Temperature:
Operating Temperature:Operating Temperature:
Operating Temperature:
0 to 60 degrees C
Pulse Output Range:Pulse Output Range:
Pulse Output Range:Pulse Output Range:
Pulse Output Range:
1 to 50,000 Hz
10uS negative going pulse width
Inputs (TTL-CMOS):Inputs (TTL-CMOS):
Inputs (TTL-CMOS):Inputs (TTL-CMOS):
Inputs (TTL-CMOS):
Logic “0”: 0 to 0.8VDC
Logic “1”: 3.5 to 24VDC
Analog input 1: 0 to 5VDC
Output Current Rating:Output Current Rating:
Output Current Rating:Output Current Rating:
Output Current Rating:
5.0 A/phase maximum running
3.5A/phase maximum standstill
Baud Rate:Baud Rate:
Baud Rate:Baud Rate:
Baud Rate:
38400 Baud, Fixed
Data Format:Data Format:
Data Format:Data Format:
Data Format:
Half-Duplex, 1 start bit, 8 data bits,
no parity, 1 stop bit
Outputs (8 programmable):Outputs (8 programmable):
Outputs (8 programmable):Outputs (8 programmable):
Outputs (8 programmable):
Open Drain Type
40V, 100mA
+5VDC Output, 50mA
Output1 active low time for output on the fly:Output1 active low time for output on the fly:
Output1 active low time for output on the fly:Output1 active low time for output on the fly:
Output1 active low time for output on the fly:
50uS
Note:Note:
Note:Note:
Note: For inductive loads, customers must connect
a clamping diode to protect from flyback voltage
spikes.
rebmuNtraP noitpircseD
11605YPD .ylppusrewopW521dnaevirdralopibpma5aserutaeF-kcaPevirD/rellortnoC
7SWT .rellortnocseires06CMSynahtiwelbitapmochctiwsleehwbmuhtnoitisopneveS
6-BA-BSUAA .rotcennocelamB-BSUenodnarotcennocelamA-BSUenohtiwelbacBSUtoof6
Ordering InformationOrdering Information
Ordering InformationOrdering Information
Ordering Information
Thetable below listsavariety of productsavailablefrom Anaheim Automation,Inc.These products include
those covered by this manual, along with supporting cables and devices. We are continually adding new
products to our line, so please consult Anaheim Automation, Inc. or its representatives for information on
the latest releases.
A CD, provided when you purchase the unit, contains this user’s manual, along with the SMC60WIN
software, windows virtual comport driver and DPY50611 program examples. The software allows you to
write and change programs that are to be stored in the DPY50611 for autostart use, and also upload the
program that is stored in the DPY50611 itself for editing and viewing. The software also allows you to save
the programs onto your computer hard drive, and easily retrieve them when needed.

5
#L010196 September 2005
Dimensions/Switch LocationsDimensions/Switch Locations
Dimensions/Switch LocationsDimensions/Switch Locations
Dimensions/Switch Locations
Wiring DiagramsWiring Diagrams
Wiring DiagramsWiring Diagrams
Wiring Diagrams

6
#L010196 September 2005
Terminal Descriptions - DriverTerminal Descriptions - Driver
Terminal Descriptions - DriverTerminal Descriptions - Driver
Terminal Descriptions - Driver
noitisoP stupnIrevirD-noitpircseD
1 CDV5+srellortnocotdetcennoCyllanretnI:)+(edonAtupnIkcolCpetS
2 tuptuokcolcsrellortnocotdetcennoCyllanretnI:)-(edohtaCtupnIkcolCpetS
3CDV5+srellortnocotdetcennoCyllanretnI:)+(edonAnoitceriD
4 tuptuonoitceridsrellortnocotdetcennoCyllanretnI:)-(edohtaCnoitceriD
5CDV5+srellortnocotdetcennoCyllanretnI:)+(edonAFFO/NO
6 tuptuoffo/nosrellortnocotdetcennoCyllanretnI:)-(edohtaCFFO/NO
noitisoP noitcennoCrotoM-noitpircseD
1rotoMpetSehtfo1esahP:AesahP
2rotoMpetSehtfo3esahP:AesahP
3rotoMpetSehtfo2esahP:BesahP
4rotoMpetSehtfo4esahP:BesahP
5dnuorGrotoM
Motor GroundMotor Ground
Motor GroundMotor Ground
Motor Ground
Meant to be used in conjunction with the motor cable ground wire. Make sure the connection is only on
one end of the motor cable ground wire. If no motor shield is available, and if the motor has no ground
wire, the motor ground pin can be left with no connection.

7
#L010196 September 2005
Slide Switch Descriptions - ControllerSlide Switch Descriptions - Controller
Slide Switch Descriptions - ControllerSlide Switch Descriptions - Controller
Slide Switch Descriptions - Controller
rebmuNhctiwS noitpircseD
2WS .6dna5stupniroleehwbmuhtehtrehtietcelesotdesusihctiwssihT
Connector Descriptions - ControllerConnector Descriptions - Controller
Connector Descriptions - ControllerConnector Descriptions - Controller
Connector Descriptions - Controller
rebmuNhctiwS noitpircseD
1J .SWTdelebalsidnaeludomleehwbmuhtehtrofsirotcennocsihT
Terminal Descriptions - ControllerTerminal Descriptions - Controller
Terminal Descriptions - ControllerTerminal Descriptions - Controller
Terminal Descriptions - Controller
noitisoP redocnE-noitpircseD
1redocnerofylppusCDV5+
2redocneroflennahcA
3redocneroflennahcB
4redocnerofnruterdnuorG
noitisoP stupnI-noitpircseD
1tupnigolanA-1tupnI
2tupniylfehtnoxednI-2tupnI
33tupnI
44tupnI
56/5NInoitisopni2WS-5tupnI
66/5NInoitisopni2WS-6tupnI
7dnuorG
noitisoP stuptuO-noitpircseD
1tuptuoylfehtnotuptuO-1tuptuO
22tuptuO
33tuptuO
44tuptuO
55tuptuO
66tuptuO
77tuptuO
8tuptuOrorrEseirteRredocnE-8tuptuO
noitisoP stupnIhctiwStimiL-noitpircseD
1timiLemoH
2+goJ
3-goJ
4goJtsaF
5+timiLdraH
6-timiLdraH
7+timiLtfoS
8-timiLtfoS
9dnuorG

8
#L010196 September 2005
Section 2: Driver FunctionsSection 2: Driver Functions
Section 2: Driver FunctionsSection 2: Driver Functions
Section 2: Driver Functions
Motor SelectionMotor Selection
Motor SelectionMotor Selection
Motor Selection
The DPY50611 incorporates a Bipolar Microstep Driver that is compatible with both Bipolar and Unipolar
Motor Configurations, (i.e. 8 and 4 lead motors, and 6 lead center tapped motors).
Step motors with low current ratings and high inductance will perform better at low speeds, providing
higher low-end torque. Motors with high current ratings and low inductance will perform better at higher
speeds, providing more high-end torque.
Since the DPY50611 is a constant current source, it is not necessary to use a motor that is rated at the
same voltage as the supply voltage. What is important is that the driver is set to the appropriate current
level based on the motor being used. Refer to the following chart for setting the current potentiometer
based on the current code in the part number of the motor. Examples of motor part numbers are shown
below. Anaheim Automation offers a comprehensive line of step motors in 14, 17, 23, 34 and 42 frame
sizes. Contact the factory to verify motor compatibility with the DPY50611.
Step Motor Current Setting GuideStep Motor Current Setting Guide
Step Motor Current Setting GuideStep Motor Current Setting Guide
Step Motor Current Setting Guide
Anaheim Automation offers motor cable, making hook-ups quick and easy!Anaheim Automation offers motor cable, making hook-ups quick and easy!
Anaheim Automation offers motor cable, making hook-ups quick and easy!Anaheim Automation offers motor cable, making hook-ups quick and easy!
Anaheim Automation offers motor cable, making hook-ups quick and easy!
Contact the factory or visit our website for more motor and cable offerings.Contact the factory or visit our website for more motor and cable offerings.
Contact the factory or visit our website for more motor and cable offerings.Contact the factory or visit our website for more motor and cable offerings.
Contact the factory or visit our website for more motor and cable offerings.
Table 5: Table selection for Anaheim Automation motor current settings.
elpmaxErotoMelpmaxErotoM elpmaxErotoM elpmaxErotoMelpmaxErotoM tnerruCrotoMtnerruCrotoM tnerruCrotoM tnerruCrotoMtnerruCrotoM edoCrebmuNedoCrebmuN edoCrebmuN edoCrebmuNedoCrebmuN ralopinUralopinU ralopinU ralopinUralopinU gnitaRgnitaR gnitaR gnitaRgnitaR kaePseireSkaePseireS kaePseireS kaePseireSkaePseireS gnitaRgnitaR gnitaR gnitaRgnitaR kaePlellaraPkaePlellaraP kaePlellaraP kaePlellaraPkaePlellaraP gnitaRgnitaR gnitaR gnitaRgnitaR
seireSseireS seireS seireSseireS tnerruCtnerruC tnerruC tnerruCtnerruC gnitteSgnitteS gnitteS gnitteSgnitteS
lellaraPlellaraP lellaraP lellaraPlellaraP tnerruCtnerruC tnerruC tnerruCtnerruC gnitteSgnitteS gnitteS gnitteSgnitteS
1D321D32 1D32 1D321D322020202020SS
S
SS 2020202020A0.1A0.1A0.2%22%04
3L323L32 3L32 3L323L3230303030308WL-D8WL-D 8WL-D 8WL-D8WL-D 3030303030A5.1A5.1A0.3%03%06
1N431N43 1N43 1N431N4340404040408WL-S8WL-S 8WL-S 8WL-S8WL-S 4040404040A0.2A0.2A0.4%04%08
04L3204L32 04L32 04L3204L3250505050508WL-D8WL-D 8WL-D 8WL-D8WL-D 5050505050A5.2A5.2A0.5%05%001
1A431A43 1A43 1A431A436060606060BB
B
BB 6060606060A0.3A0.3A0.6%06%001
2N432N43 2N43 2N432N4370707070708WL-S8WL-S 8WL-S 8WL-S8WL-S 7070707070A5.3A5.3A0.7%07%001
1K431K43 1K43 1K431K4380808080808WL-S8WL-S 8WL-S 8WL-S8WL-S 8080808080A0.4A0.4A0.8%08---
2N242N24 2N24 2N242N249090909090BC-SBC-S BC-S BC-SBC-S 9090909090A5.4A5.4A0.9%09---
3L323L32 3L32 3L323L3201010101018WL-S8WL-S 8WL-S 8WL-S8WL-S 0101010101A0.5A0.5A0.01%001---
3D433D43 3D43 3D433D431111111111DD
D
DD 1111111111A5.5A5.5A0.11%001---
1K241K24 1K24 1K241K242121212121BC-SBC-S BC-S BC-SBC-S 2121212121A0.6A0.6A0.21%001---

9
#L010196 September 2005
Microstep Selection - Driver SW1 SettingsMicrostep Selection - Driver SW1 Settings
Microstep Selection - Driver SW1 SettingsMicrostep Selection - Driver SW1 Settings
Microstep Selection - Driver SW1 Settings
Switches 2, 3 and 4, of the DIP switch select the number of microsteps per step. Table 6 shows the
standardresolution values alongwith the associatedpositions for theselect switches. Thestandard wave-
forms are sinusoidal.
Setting the Output CurrentSetting the Output Current
Setting the Output CurrentSetting the Output Current
Setting the Output Current
The output current on the DPY50611 is set by an onboard potentiometer. This potentiometer determines
the per phase peak output current of the driver. The relationship between the output current and the
potentiometer value is as follows:
Table 7: Potentiometer values with respect to the output current
Refer to Table 5 for specific motor current settings.Refer to Table 5 for specific motor current settings.
Refer to Table 5 for specific motor current settings.Refer to Table 5 for specific motor current settings.
Refer to Table 5 for specific motor current settings.
noituloseR veR/spetS 1tceleS 2tceleS 3tceleS 4tceleS tnerruCecudeRotuA
1002FFONONONOdelbasiD
2004FFONONOFFOdelbasiD
50001FFONOFFONOdelbasiD
80061FFONOFFOFFOdelbasiD
01 0002FFOFFONONOdelbasiD
61 0023FFOFFONOFFOdelbasiD
23 0046FFOFFOFFONOdelbasiD
46 00821FFOFFOFFOFFOdelbasiD
1002NONONONOdelbanE
2004NONONOFFOdelbanE
50001NONOFFONOdelbanE
80061NONOFFOFFOdelbanE
01 0002NOFFONONOdelbanE
61 0023NOFFONOFFOdelbanE
23 0046NOFFOFFONOdelbanE
46 00821NOFFOFFOFFOdelbanE
Table 6: Microstep selection on switch 1.
tnerruCkaePtnerruCkaeP tnerruCkaeP tnerruCkaePtnerruCkaeP gnitteSretemoitnetoPgnitteSretemoitnetoP gnitteSretemoitnetoP gnitteSretemoitnetoPgnitteSretemoitnetoP tnerruCkaePtnerruCkaeP tnerruCkaeP tnerruCkaePtnerruCkaeP gnitteSretemoitnetoPgnitteSretemoitnetoP gnitteSretemoitnetoP gnitteSretemoitnetoPgnitteSretemoitnetoP
A5.0%0 A0.3%06
A6.0%01 A5.3%07
A9.0%02 A0.4%08
A5.1%03 A5.4%09
A0.2%04 A0.5%001
A5.2%05 ----

10
#L010196 September 2005
When configuring the motor in a
series configurationseries configuration
series configurationseries configuration
series configuration
(connected from end to end with the center tap
floating) use the specified per Phase (or unipolar) current rating to determine the current setting potenti-
ometer value.
Reducing Output CurrentReducing Output Current
Reducing Output CurrentReducing Output Current
Reducing Output Current
Reducing the output current is accomplished by setting switch 1 of the DIP switch to the ON position and
occurs approximately 1 second after the last positive going edge of the step clock input. The amount of
current per phase in the reduction mode is approximately 50% of the set current. When the current
reduction circuit is activated, the current reduction resistor is paralleled with the current adjustment poten-
tiometer. This lowers the total resistance value, and thus lowers the per Phase output current.
Determining Output CurrentDetermining Output Current
Determining Output CurrentDetermining Output Current
Determining Output Current
The output current for the motor used when microstepping is determined differently from that of a full/half
step unipolar driver. In the DPY50611, a sine/cosine output function is used in rotating the motor. The
output current for a given motor is determined by the motors current rating and the wiring configuration of
the motor. There is a current adjustment potentiometer used to set the output current of the DPY50611.
This sets the peak output current of the sine/cosine waves. The specified motor current (which is the
unipolar value) is multiplied by a factor of 1.0, 1.4, or 2.0 depending on the motor configuration (series,
half-coil, or parallel).
Step Motor ConfigurationsStep Motor Configurations
Step Motor ConfigurationsStep Motor Configurations
Step Motor Configurations
Step motors can be configured as 4, 6, or 8 leads. Each configuration requires different currents. Refer to
the lead configurations and the procedures to determine their output current.
WARNING!WARNING!
WARNING!WARNING!
WARNING! Step motors will run hot even when configured correctly. Damage may occur to the motor if
a higher than specified current is used. Most specified motor currents are maximum values. Care
should be taken to not exceed these ratings.
6 Lead Motors6 Lead Motors
6 Lead Motors6 Lead Motors
6 Lead Motors
When configuring a 6 lead motor in a
half-coil configurationhalf-coil configuration
half-coil configurationhalf-coil configuration
half-coil configuration
(connected from one end of the coil to the
center tap), multiply the specified per Phase (or unipolar) current rating by 1.4 to determine the current
setting potentiometer value. This configuration will provide more torque at higher speeds when compared
to the series configuration.

11
#L010196 September 2005
4 Lead Motors4 Lead Motors
4 Lead Motors4 Lead Motors
4 Lead Motors
Multiply the specified
seriesseries
seriesseries
series
motor current by 1.4 to determine the current adjustment potentiometer
value. Four Lead Motors are usually rated with their appropriate series current, as opposed to the
Phase
Current
, which is the rating for 6 and 8 lead motors.
8 Lead Motors8 Lead Motors
8 Lead Motors8 Lead Motors
8 Lead Motors
Series Connection:Series Connection:
Series Connection:Series Connection:
Series Connection: When configuring the motor windings in series, use the per Phase (or unipolar)
current rating to determine the current setting potentiometer value.
Parallel Connection:Parallel Connection:
Parallel Connection:Parallel Connection:
Parallel Connection: When configuring the motor windings in parallel, multiply the per Phase (or unipo-
lar) current rating by 2.0 to determine the current setting potentiometer value.
NOTE:NOTE:
NOTE:NOTE:
NOTE: After the current has been determined, according to the motor connections above, use Table 3 to
choose the proper setting for the current setting potentiometer.

12
#L010196 September 2005
Connecting the Step MotorConnecting the Step Motor
Connecting the Step MotorConnecting the Step Motor
Connecting the Step Motor
Phase 1 and 3 of the Step Motor is connected between pins 1 and 2 on the motor connector (TB2). Phase
2 and 4 of the Step Motor is connected between pins 3 and 4 on the motor connector (TB2). The motors
case can be grounded to pin 5 on the motor connector (TB2). Refer to Figures 2, 3 & 4 for TYPICAL
APPLICATION HOOK-UP.
NOTENOTE
NOTENOTE
NOTE: The physical direction of the motor with respect to the direction input will depend on the connection
of the motor windings. To reverse the direction of the motor with respect to the direction input, switch the
wires on Phase 1 and Phase 3.
WARNING:WARNING:
WARNING:WARNING:
WARNING: Do not connect or disconnect motor wires while power is applied!
Short-Circuit, Mis-Wire, and Over-Current ConditionsShort-Circuit, Mis-Wire, and Over-Current Conditions
Short-Circuit, Mis-Wire, and Over-Current ConditionsShort-Circuit, Mis-Wire, and Over-Current Conditions
Short-Circuit, Mis-Wire, and Over-Current Conditions
If it is found that there is a condition that causes on over current in the driver phase transistors, the Red
LED will turn on solid and power will be shut off to the motor. To reset the drive turn power off, check
wiring, and turn power back on.

13
#L010196 September 2005
Section 3: Controller FunctionsSection 3: Controller Functions
Section 3: Controller FunctionsSection 3: Controller Functions
Section 3: Controller Functions
Methods of CommunicationMethods of Communication
Methods of CommunicationMethods of Communication
Methods of Communication
There are two methods for sending commands to the DPY50611. One is to directly talk to the DPY50611
by using Direct Talk Mode. This is usually used with a computer or PLC (Programmable Logic Controller),
where the computer or PLC gives the DPY50611 serial commands to off-load its processor. For example:
A PLC can utilize its outputs to toggle the DPY50611’s inputs and gain control of variable speeds, variable
programs, variable distances, etc. Simply using the DPY50611 as the intelligent pulse generator, a PLC
can remove some of the tasks that were not meant for ladder logic or any PLC processing time.
The second way to give commands to the DPY50611 is to use the software program SMC60WIN to either
manually control, or to write and send programs. This method is used when the DPY50611 is the main
controller. For example: A DPY50611 can replace simple motion control and replace I/O functional when
minimalquantities of I/Oarerequired to controlspecificmachinery. Simple motionprofilesthat can operate
with 6 or less inputs and 8 or less outputs can utilize a DPY50611 controller.
Baud RateBaud Rate
Baud RateBaud Rate
Baud Rate
A term used frequently in serial data communications, a “baud” is defined as the reciprocal of the shortest
pulse duration in a data word signal, including start, stop, and parity bits. This is often taken to mean the
same as “bits per second”, a term that expresses only the number of “data” bits per second. Very often,
the parity bit is included as an information or data bit. The DPY50611 accepts a baud rate of 38400 onlyThe DPY50611 accepts a baud rate of 38400 only
The DPY50611 accepts a baud rate of 38400 onlyThe DPY50611 accepts a baud rate of 38400 only
The DPY50611 accepts a baud rate of 38400 only.
Axis SelectionAxis Selection
Axis SelectionAxis Selection
Axis Selection
Each DPY50611 is addressed using a programmable register allowing the PC to address up to 99
DPY50611’s from one port. The Default axis is “0”. To change the axis, use the SMC60WIN software or
the “~” command. To verify or check the axis, use the SMC60WIN software or the “%” command. The axis
designation is nonvolatile and will remain the same until changed by the user.
Controller Status LEDController Status LED
Controller Status LEDController Status LED
Controller Status LED
When powered and operated properly, the status LED will be green. When an error occurs, the LED will
change to RED, and an error code will be generated in the error code register. To read and clear the error
with the software, click on the “Verify Parameters” button located in the “Motion Tab”. To read and clear
the error while in “Direct Mode”, use the error code “!” command. Once the error has been read and
cleared, the LED will return to green and the error code register will be cleared to 0. Refer to the table on
page 39 for a complete list of the error codes.
Technical SupportTechnical Support
Technical SupportTechnical Support
Technical Support
Everyone needs assistance on occasion. If you have problems using any of the equipment covered by
this manual, please read the manual to see if it will answer your questions. Be sure to look in the Trouble-
shooting Section located near the back of this manual. If you need assistance beyond what this manual
can provide, you may call the factory direct for application assistance. If possible, have this manual in
hand. It is often helpful to have the controller connected to a computer with the software installed.

14
#L010196 September 2005
Move Number of Steps:Move Number of Steps:
Move Number of Steps:Move Number of Steps:
Move Number of Steps: This command causes the motion to start in the direction last specified. This
command will move the motor the number of steps given. (Range: 1 to 8388607)
Move to Position:Move to Position:
Move to Position:Move to Position:
Move to Position: The move to position command specifies the next absolute position to go to. The
DPY50611 controller automatically sets the direction and number of steps needed to go to that position.
(Range: -8388607 to +8388607)
Slew:Slew:
Slew:Slew:
Slew: The slew command will accelerate the motor up to maximum speed and continue to run at that
speed until reaching a registration mark, hard limit switch, soft limit switch, receiving a “.” (stop hard) or
“,” (stop soft) command.
Set Position:Set Position:
Set Position:Set Position:
Set Position: The set position command sets the position register to a designated value. The number
will be the new absolute position of the motor. The default value is 0. (Range: -8388607 to +8388607)
Limit Switch Inputs:Limit Switch Inputs:
Limit Switch Inputs:Limit Switch Inputs:
Limit Switch Inputs: The limit switch inputs are internally pulled up by a resistor making them normally
+5 volts. To activate the input, the pin must be grounded to (0VDC). All limit switch inputs are internally
clamped to +5V, thus allowing voltages of upto +24VDC to be used.
Hard Limit Inputs:Hard Limit Inputs:
Hard Limit Inputs:Hard Limit Inputs:
Hard Limit Inputs: When a hard limit switch is encountered, the motion will stop immediately. The
position counter will also cease counting.
Hard limits are intended as an emergency stop for your
system. It should not be used to do any positioning type functions
. These limits are directional.
Soft Limit Inputs:Soft Limit Inputs:
Soft Limit Inputs:Soft Limit Inputs:
Soft Limit Inputs: These switches should be used exclusively for homing. Once positioned properly
with the appropriate parameters, it causes the motor to ramp down to the base speed before encoun-
tering the home limit switch. However, the soft limit switch will work for any type of motion command.
These limits are directional.
NOTE: Whenever a soft limit switch is activated, the motor will decelerate and run at base speed during
an indexing move, or stop during a slewing move. Be sure to come back past the soft limit switch to set
any origins, otherwise the motor will decelerate as it goes past the soft limit switch during normal
operation.
Home Limit Input:Home Limit Input:
Home Limit Input:Home Limit Input:
Home Limit Input: This switch is used to establish a position designated “home” or datum position
using the following: home to
soft and home limit
, or home to
home limit
. This limit is not directional.
Home to Soft, Home Limit (2 Switch Operation):Home to Soft, Home Limit (2 Switch Operation):
Home to Soft, Home Limit (2 Switch Operation):Home to Soft, Home Limit (2 Switch Operation):
Home to Soft, Home Limit (2 Switch Operation): This type of homing routine requires two grounding
type limit switches called home and soft. The first limit switch seen is the soft limit. This will decelerate
the motor down to base speed. The motor will then continue to run at base speed until it contacts the
home limit switch input causing the motor to stop. The home limit switch activates as a hard limit if a
soft limit is not sensed. The soft limit is directional, meaning that it will work in only one direction as
specified. The soft limit switch will work for any type of motion command. The home limit switch will
work only for the two home motion commands.
NOTE: There should be sufficient distance between the two limit switches, as to let the motor reach
base speed.
Home to Home Limit (1 Switch Operation)Home to Home Limit (1 Switch Operation)
Home to Home Limit (1 Switch Operation)Home to Home Limit (1 Switch Operation)
Home to Home Limit (1 Switch Operation): This type of homing differs in that only one limit switch is
needed. In this homing routine the motor moves toward the home limit switch. When the home limit
switch is contacted the motor will ramp down to base speed, reverse direction and continue at base
speed until the limit switch is released. This is a good way to compensate for any backlash in a sys-
tem. It is also useful for minimizing the number of limit switches needed for homing.
NOTE: The home switch needs to be low during the entire deceleration and reversing time.

15
#L010196 September 2005
Jog Inputs:Jog Inputs:
Jog Inputs:Jog Inputs:
Jog Inputs: The jog switch inputs are internally pulled up by a resistor making them normally +5 volts.
To activate the input, the pin must be grounded to (0VDC). All jog switch inputs are internally clamped
to +5V, thus allowing voltages of upto +24VDC to be used. Jog is a manual function. The user can
select the direction and speed (fast or slow) by grounding the appropriate combinations of inputs. To
jog a motor, it is necessary to ground the jog input for the direction desired. For fast jog, both the fast
input and jog input for the appropriate direction must be low at the same time. By grounding one of the
jog inputs, the user causes the motor to run at base speed. When the fast input is grounded, the motor
will then accelerate to the programmed jog speed. The position register will keep track of the number of
steps that are taken during jogging. Once a +jog or a -jog function has been performed, the direction
register will retain the last direction of movement; that is, a subsequent go command will be in the same
direction as the last jog command.
Inputs:Inputs:
Inputs:Inputs:
Inputs: All inputs (except input 1) are internally pulled up by a resistor making them normally +5 volts.
To activate the input, the pin must be grounded to (0VDC). All inputs are internally clamped to +5V,
thus allowing voltages of upto +24VDC to be used. Six inputs are provided per axis. The inputs are
TTL, CMOS and 24V compatible. The inputs may be used to initiate a machine cycle, for inter-axis
coordination (in stored program mode), for operator intervention, for sensing a machine condition such
as out of stock or wait for temperature to be reached, etc. A grounded input will read a “0” and an open
or high input will read as a “1”. Input 1 is a special input that is capable of reading an analog voltage
between 0 and +5VDC. Since this input does not have a pull-up resistor, biasing of this input is needed
if it is not used as an analog input. Inputs 5 and 6 are used together with the thumbwheel switch. To
use inputs 5 and 6, SW2 must be in the IN5/6 position. If SW2 is in the TWS position, then these two
inputs are not connected to the processor.
Analog Input:Analog Input:
Analog Input:Analog Input:
Analog Input: Input 1 can be configured to read an analog voltage to either set the absolute position of
the motor or to set the maximum speed of the motor.
To set the positionTo set the position
To set the positionTo set the position
To set the position, when told via the
goto analog position
command, the input will read a voltage
between 0 and +5VDC and based on the” upper and lower” limits of the function, a move will occur to a
calculated position between the two limits. The motor must finish the move before it can be told to read
the input again for the next position. For example, if the lower limit is set to 0 and the upper limit is set
to 5000 and the analog position is set at +2.0VDC, then the motor will move to position 2000. Changing
the lower limit to 1000 and the voltage to +3.2VDC, the motor will move to position 3560. See examples
below for calculations of the analog inputs. (Range of limits: 0 to 65535 and the lower limit < upper limit)
To set the max speedTo set the max speed
To set the max speedTo set the max speed
To set the max speed, when told via the
set analog speed
command the input will read a voltage
between 0 and +5VDC, and based on the “upper and lower” limits of the function, a max speed can be
obtained based on a calculated frequency between the two points. The speed however can not be
changed when the DPY50611 is busy (moving). See examples below for calculations of the analog
inputs. (Range of limits: 0 to 50000 and the lower limit < upper limit)
Analog calculations.Analog calculations.
Analog calculations.Analog calculations.
Analog calculations. Example1:Example1:
Example1:Example1:
Example1: Example2:Example2:
Example2:Example2:
Example2:
(Upper-Lower) * (Voltage/5) = X (5000 - 0) * (2 / 5) = 2000 (5000 - 1000) * (3.2 / 5) = 2560
Lower + X = Position or Frequency 0 + 2000 = 2000 1000 + 2560 = 3560
Outputs:Outputs:
Outputs:Outputs:
Outputs: Eight outputs are provided per axis. Outputs may be used to operate relays, coolant valves,
air cylinders, or, with the correct interfacing, any electronically controlled device. The outputs can drive
all types of common peripheral power loads, including lamps, relays, solenoids, LED’s, printer heads,
and heaters. For inductive loads, it will be necessary to connect a clamping diode (refer to specification
section) from the output to the power source in order to provide adequate fly-back protection. The
outputs are current sinking, open collector darlingtons. They are capable of sinking up to 100mA per
output with voltages up to 40VDC. Turning an output on will pull the output pin to ground and turning an
output off will make the output pin open. Output 1 has a special function
(output on the fly
) that will
enable it to be triggered at a certain absolute position during a move. Output 8 has a special function
that will trigger when the encoder retries function fails.

16
#L010196 September 2005
Output on the fly:Output on the fly:
Output on the fly:Output on the fly:
Output on the fly: This special function enables output 1 to turn on during a relative index or absolute
move. There are three critical portions of information needed to make this function work correctly. First,
output 1 will turn on (0VDC) for a preset delay of 50uS at a specific absolute position set by the
1st
output position
command. Second, the output can then repeat this after a preset amount of steps set by
the
number of steps between outputs
command, and third a predetermined amount of times to set the
output is required by the
number of outputs
command which determines the preset amount of times to
trigger the output. So if you start at position 0 and want to move to an absolute position of 10,000, you
can set output 1 to turn on at position 2000, and every 1000 steps after that 5 times. So at position
2000, 3000, 4000, 5000, and 6000 output 1 will turn on for 50uS. To only have the output turn on at one
position set both the “
number of steps between outputs
” and the “
number of outputs
” commands to 0.
This function must be enabled, and will only work during a relative index or absolute position move. The
output will trigger while going in either direction. If you do not want the output to trigger in the negative
direction, the function must be turned off before the index move is started.
Index on the Fly:Index on the Fly:
Index on the Fly:Index on the Fly:
Index on the Fly: This special function uses Input 2 when a motor is slewing to move a predetermined
amount of steps, set with the registration index command, before stopping. This function must be
enabled, and will only work during a slew move. The registration index must be set before movement
begins. (Range: 1 to 8388607)
End of Program:End of Program:
End of Program:End of Program:
End of Program: The end of program command, used within a stored program, stops execution of the
program. This command must be used at the end of all programs.
Wait:Wait:
Wait:Wait:
Wait: In stored program mode, the wait command pauses the program for the specified number of
milliseconds. (Range: 1 to 65535)
If/Then Statements:If/Then Statements:
If/Then Statements:If/Then Statements:
If/Then Statements: The if/then statements are conditional based on the values preset in the program.
The user can either test each individual input or all inputs at once. If the input or input register matches
the given value or values, then the program will execute the next line. If the input or input register does
not match the given value, the program will skip the next line and execute the following line. An open
input is read as a 1, and a grounded input is read as a 0.
Branching or Goto Statements:Branching or Goto Statements:
Branching or Goto Statements:Branching or Goto Statements:
Branching or Goto Statements: The goto instruction will have the program jump to the given label. If
no label is in the program, it will error when trying to send.
Return from Subroutine:Return from Subroutine:
Return from Subroutine:Return from Subroutine:
Return from Subroutine: This function can be placed anywhere in the program as long as a goto
statement has been already executed. The program will jump back to the last goto statement encoun-
tered and execute the next line in the program.
Inner and Outer Loop:Inner and Outer Loop:
Inner and Outer Loop:Inner and Outer Loop:
Inner and Outer Loop: The loop instructions allow the user to loop a program a variable number of
times. The program will loop to the designated label location of the program. However , the label must
always be at a lower line number than the loop instruction itself. You can only nest inner loops inside an
outer loop. You may not nest an inner loop inside an inner loop, or an outer loop inside an outer loop.
Multiple nested inner loops are allowed in one outer loop.
Finish Move:Finish Move:
Finish Move:Finish Move:
Finish Move: When writing a program, the finish move command is used directly after every motion
command. When using this command, the DPY50611 internally generates a busy signal and will wait
until the move is complete before executing any further commands. Unless the finish move command is
used, the DPY50611 will continue to execute the program. If it encounters a command that cannot be
used when the motor is moving, the DPY50611 will error and stop the program prematurely.
Repeat Last Move:Repeat Last Move:
Repeat Last Move:Repeat Last Move:
Repeat Last Move: This command will move the motor the number of steps given in the last indexing
move. This command will not work correctly if the encoder autocorrect function is enabled.

17
#L010196 September 2005
Encoder Commands:Encoder Commands:
Encoder Commands:Encoder Commands:
Encoder Commands: The DPY50611 controller is capable of using a quadrature incremental encoder
with A and B channels.
Encoder Auto Correct:Encoder Auto Correct:
Encoder Auto Correct:Encoder Auto Correct:
Encoder Auto Correct: This command will enable or disable the encoder feature of the DPY50611.
When enabled, the encoder function will compare the desired position with the actual encoder position.
If it is not in the correct position a correction move will be made.
Encoder DelayEncoder Delay
Encoder DelayEncoder Delay
Encoder Delay: This sets the wait time, which is a specified number of milliseconds after a relative
index or absolute move is finished, prior to reading the encoder. This is used to remove the ringing that
might be associated with the mechanics of the system. (Range: 0 to 65535)
Encoder Motor Ratio:Encoder Motor Ratio:
Encoder Motor Ratio:Encoder Motor Ratio:
Encoder Motor Ratio: This represents the ratio for the number of encoder pulses to one motor step.
This ratio must be a whole number. For example, given a 1000 line quadrature encoder and a 400 step/
revolution motor, the motor ratio is (1000 * 4) / 400 = 10 (Range: 1 to 255 and must be a whole num-
ber)
Encoder Retries:Encoder Retries:
Encoder Retries:Encoder Retries:
Encoder Retries: This is the number of times the DPY50611 will try to autocorrect the motor shaft
position before producing an error. When the error is produced, Output 8 is triggered. (Range: 0 to 255)
Encoder Window:Encoder Window:
Encoder Window:Encoder Window:
Encoder Window: This is the allowable error in encoder pulses (either plus or minus) from the desired
position that is allowed before the motor autocorrects. (Range: 0 to 255)
Thumbwheel Index:Thumbwheel Index:
Thumbwheel Index:Thumbwheel Index:
Thumbwheel Index: This special function allows a thumbwheel with up to 7 decades to be used with
the DPY50611 to set a relative index. To use the thumbwheel, SW2 must be in the TWS position or the
thumbwheel will be disabled.
Acceleration/Deceleration:Acceleration/Deceleration:
Acceleration/Deceleration:Acceleration/Deceleration:
Acceleration/Deceleration: The acceleration and deceleration are the same value. The acceleration is
entered directly as steps/sec2and controls the time that the motor will take to move from base speed to
max speed, and from max speed to base speed. The higher the value, the faster the motor will acceler-
ate. The same principal applies for the deceleration which is controlling the time it takes to go from the
max speed to base speed. (Range: 100 to 9,999,999)
Base Speed:Base Speed:
Base Speed:Base Speed:
Base Speed: The base speed is the speed at which motion starts and stops. It is entered directly as
the number of steps per second. This speed must always be less than the max speed and jog speed.
(Range: 1 to 5000)
Max Speed:Max Speed:
Max Speed:Max Speed:
Max Speed: The max speed is the top speed the user wants the motor to run. This speed must always
be greater than the base speed. It is entered directly as the number of steps per second.
(Range: 1 to 50000)
Jog Speed:Jog Speed:
Jog Speed:Jog Speed:
Jog Speed: The jog speed sets the fast jog rate. Jog (+/-) is used to run at base speed. The FJOG pin,
when grounded, will ramp the motor to the set jog speed. This speed must always be greater than the
base speed. It is entered directly as the number of steps per second. (Range: 1 to 50000)
Motor Current:Motor Current:
Motor Current:Motor Current:
Motor Current: This command will control the on/off output which is designed to connect to the on/off
input of Anaheim Automation’s step motor drivers. To energize and allow current to flow through the
coil of the motor, set the value to on. To de-energize and turn the current off to the motor, set the value
to off. This is a dedicated output and not controlled with the output register.
Verify:Verify:
Verify:Verify:
Verify: The verify command causes the DPY50611 controller to send data back to the PC or PLC. The
data is sent as an ASCII decimal string followed by a carriage return and a line feed. The verify com-
mands are shown in the table on page 34.

18
#L010196 September 2005
Section 4: SMC60WIN SoftwareSection 4: SMC60WIN Software
Section 4: SMC60WIN SoftwareSection 4: SMC60WIN Software
Section 4: SMC60WIN Software
The SMC60WIN software is a handy utility that supports Anaheim Automation’s line of DPY50611’s step
motor controllers. Connecting your PC to the DPY50611, via a serial cable, the SMC60WIN software can
easily perform the following tasks:
••
••
• Exercise and monitor the DPY50611 controller
••
••
• Write and edit stored programs for standalone operation
••
••
• Directly communicate with the DPY50611 controller
InstallationInstallation
InstallationInstallation
Installation
SoftwareSoftware
SoftwareSoftware
Software
••
••
• The SMC60WIN is supplied on a CD, containing the setup program of the SMC60WIN
software, Windows Virtual Comport Driver, DPY50611 manual and sample programs.
••
••
• SMC60WIN is compatible with all versions of Windows including Windows 2000 and
Windows XP.
Windows 95/98/NT/ME/2000/XP InstallationWindows 95/98/NT/ME/2000/XP Installation
Windows 95/98/NT/ME/2000/XP InstallationWindows 95/98/NT/ME/2000/XP Installation
Windows 95/98/NT/ME/2000/XP Installation
Option 1
1) Insert the CD into the drive
2) On the Windows Taskbar select StartStart
StartStart
Start | RR
RR
Runun
unun
un
3) Enter D:\setupD:\setup
D:\setupD:\setup
D:\setup and click OKOK
OKOK
OK - use the appropriate drive letter (i.e. DD
DD
D or EE
EE
E)
Option 2
1) Open Windows Explorer
2) Open CD Drive Folder (D: or E:)
3) Double click the Setup Icon
Getting StartedGetting Started
Getting StartedGetting Started
Getting Started
1) Apply power to the DPY50611 package. Follow the onscreen instructions to install the virtual
comport on the computer. The driver is located on the CD in the drivers folder.
2) Apply power to the DPY50611 controller.
3) Set the appropriate com port setting by selecting Setup | Com Port Settings from the menu bar.
(Ctrl+M is a shortcut)
4) Set the appropriate axis setting by selecting Setup | Axis from the menu bar.
(Ctrl+A is a shortcut)
5) Establish communications with the DPY50611 by clicking on the Connect Icon, or select
Setup | Connect from the menu bar. If the unit is connected properly, the program will notify you
when communications has been established. (Ctrl+C is a shortcut)
Changing the COM Port Number of the USB portChanging the COM Port Number of the USB port
Changing the COM Port Number of the USB portChanging the COM Port Number of the USB port
Changing the COM Port Number of the USB port
1) From
DeviceManageDeviceManage
DeviceManageDeviceManage
DeviceManage
r, select
“View devices by typ“View devices by typ
“View devices by typ“View devices by typ
“View devices by typ
e”, then
“Ports (COM & LPT“Ports (COM & LPT
“Ports (COM & LPT“Ports (COM & LPT
“Ports (COM & LPT
)”. Select
the USB serial port and click
PropertiePropertie
PropertiePropertie
Propertie
s. Select the
“Port Setting“Port Setting
“Port Setting“Port Setting
“Port Setting
s” tab, then click
Ad-Ad-
Ad-Ad-
Ad-
vancevance
vancevance
vance
d.
2) Choose the required COM port number from the list and click
OO
OO
O
K.

19
#L010196 September 2005
NmargorPwe.margorpwenagnitidetratS
OmargorPnep.ksidmorfmargorpgnitsixenanepO
SsAmargorPeva.ksidotmargorptnerrucehtevaS
P...tnir.margorptnerrucehttnirP
Exti.erawtfosNIW06CMSehttixE
FF
FF
File Menuile Menu
ile Menuile Menu
ile Menu
SS
SS
Setup Menuetup Menu
etup Menuetup Menu
etup Menu
Ctcenno.rellortnocehthtiwsnoitacinummochsilbatsE
Dtcennocsi.esuotsecivedrehtoroftropMOCehtesaeleR
moCP sgnitteStro.tropMOCtceleS
Asix.rellortnocehtfosixaderotsdnanoitcelessixateS
SS
SS
Setup -etup -
etup -etup -
etup - AA
AA
Axis Menuxis Menu
xis Menuxis Menu
xis Menu
SsixAtcele )99-1(.erawtfosNIW06CMSehtniretemaraptcelessixaehtsteS
DsixAenife )99-1(.rellortnocehtnisserddaelbammargorpehtsteS

20
#L010196 September 2005
SmargorPtrat .yromemrellortnocehtnimargorpehtfonoitucexeehttratS
St margorPpo .yromemrellortnocehtnimargorpehtfonoitucexeehtpotS
VmargorPwei.yromemrellortnocehtniderotsmargorpehtweiV
CyromeMmargorPrael.rellortnocehtniyromemmargorpehtraelC
AmargorPtratsotu.fforononoitcnuftratsotuaehtnruT
PP
PP
Program Menurogram Menu
rogram Menurogram Menu
rogram Menu
Delbasi .purewoptamargorpderotsafonoitucexeehtelbasidlliwmargorP
Eelban .puderewopsirellortnocnehwnoitucexetratslliwmargorP
PP
PP
Program -rogram -
rogram -rogram -
rogram - AA
AA
Autostart Program Menuutostart Program Menu
utostart Program Menuutostart Program Menu
utostart Program Menu
Add.magorpehtfodneehtotedocfoenilwenasddA
Cegnah.edocfoenildetcelesyltnerrucehtstidE
Itresn .edocfoenildetcelesyltnerrucehterofebedocfoenilwenatresnI
Detele.edocfoenildetcelesyltnerrucehtseteleD
EE
EE
Edit Menudit Menu
dit Menudit Menu
dit Menu
Table of contents
Popular Control Unit manuals by other brands
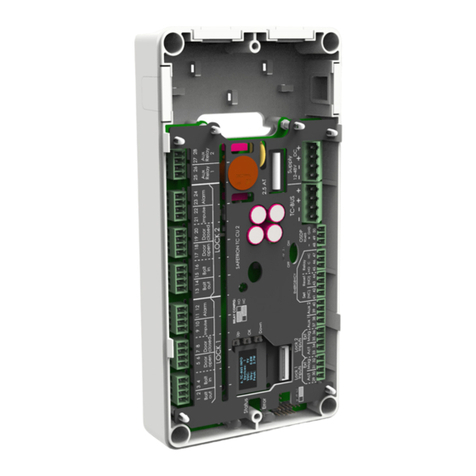
SAFE TRON
SAFE TRON CU2 instruction manual
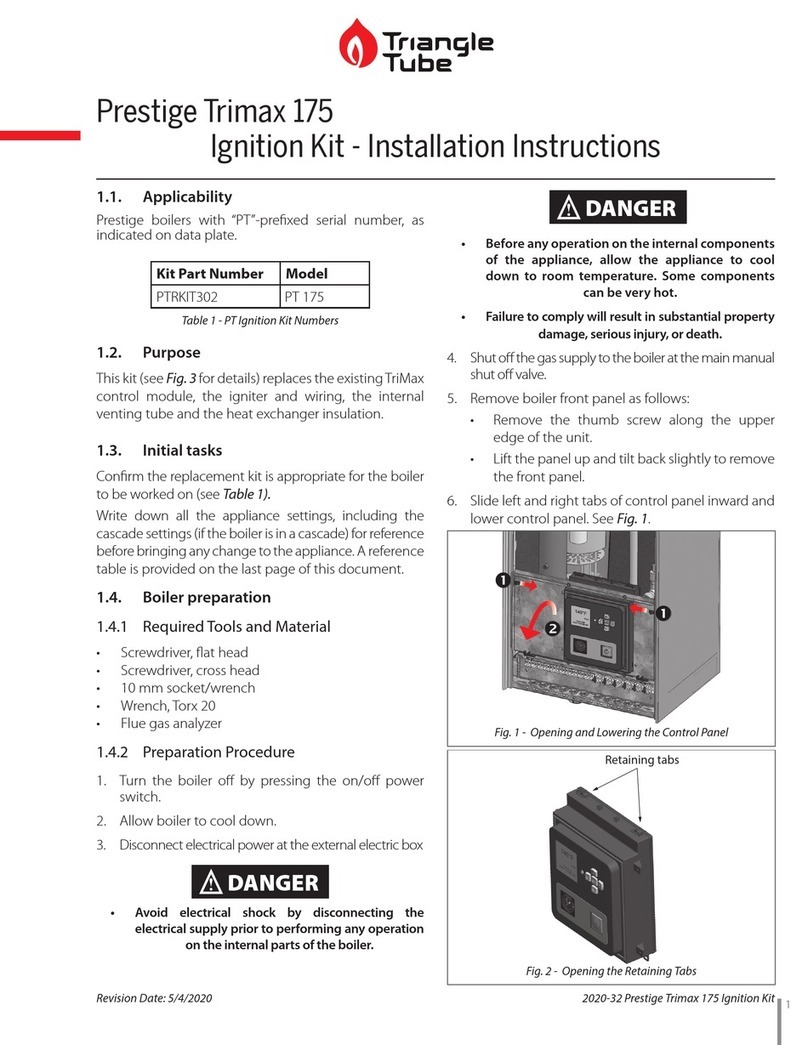
TriangleTube
TriangleTube Prestige Trimax 175 installation instructions

Definox
Definox DCX3 Installation guides
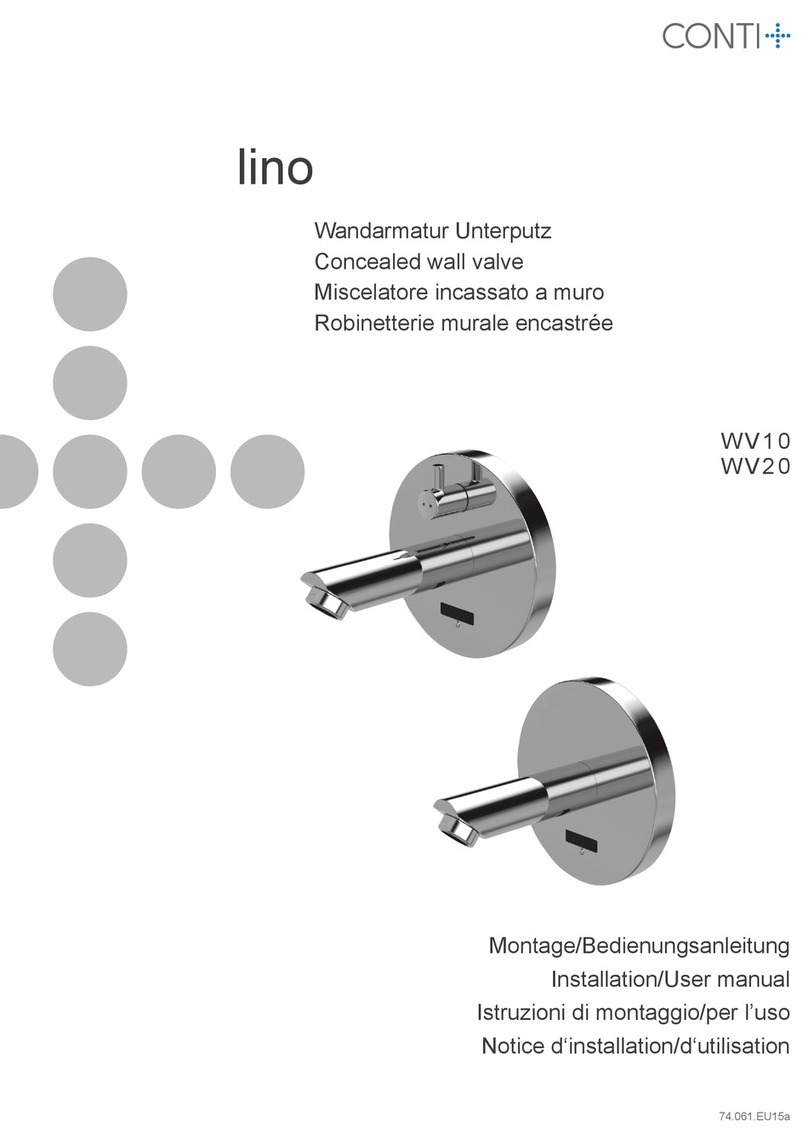
Conti+
Conti+ Lino WV10 Installation & user manual
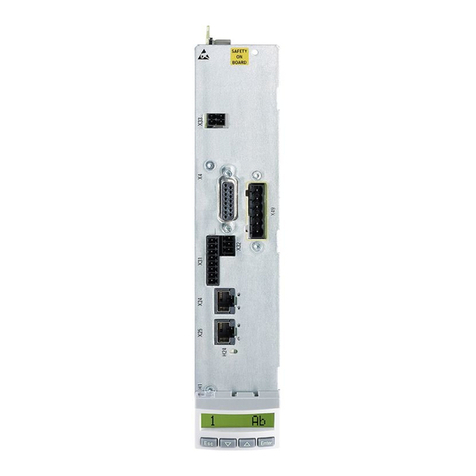
Bosch
Bosch Rexroth IndraDrive CSB02 Project planning manual
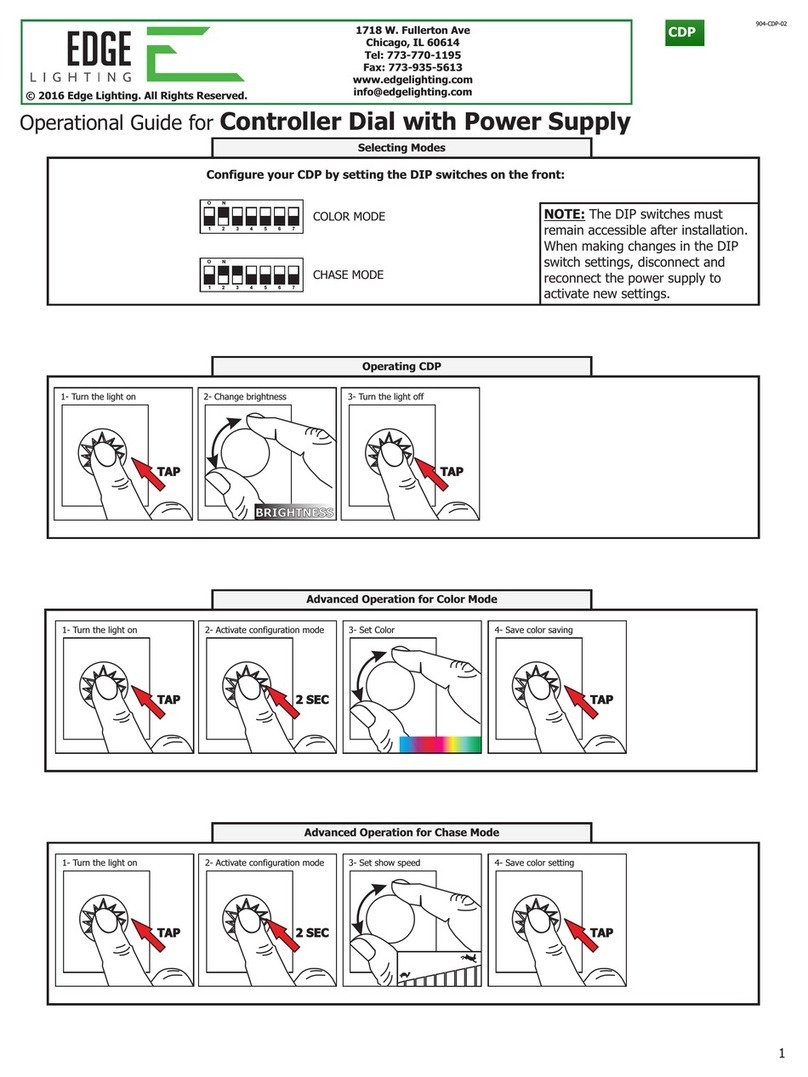
Edge Lighting
Edge Lighting Controller Dial with Power Supply Operational guide