Applied Motion Products STAC6-Q-H User manual
Other Applied Motion Products DC Drive manuals
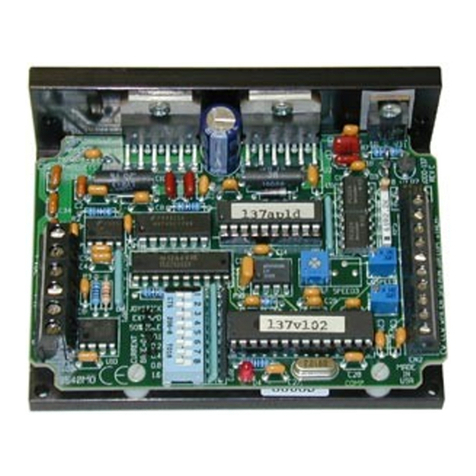
Applied Motion Products
Applied Motion Products 3540 MO User manual
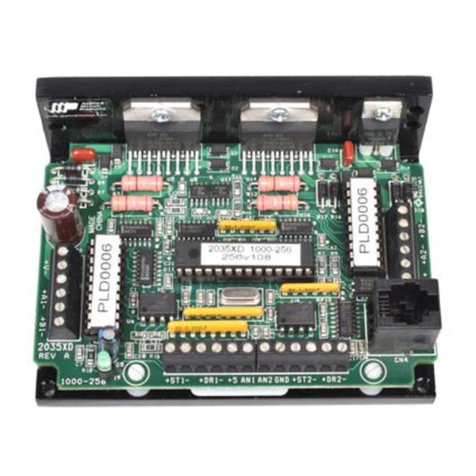
Applied Motion Products
Applied Motion Products 2035XD User manual
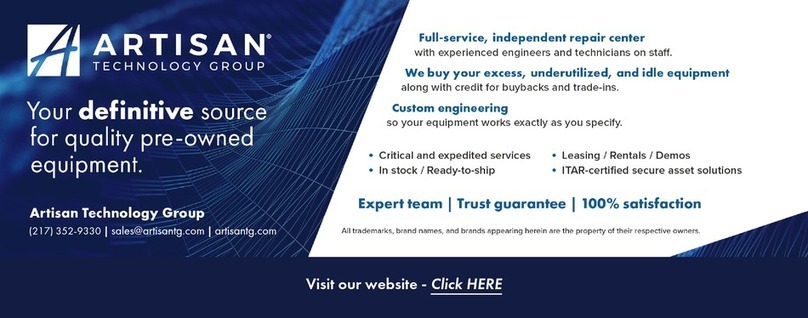
Applied Motion Products
Applied Motion Products PDO 3540 User manual
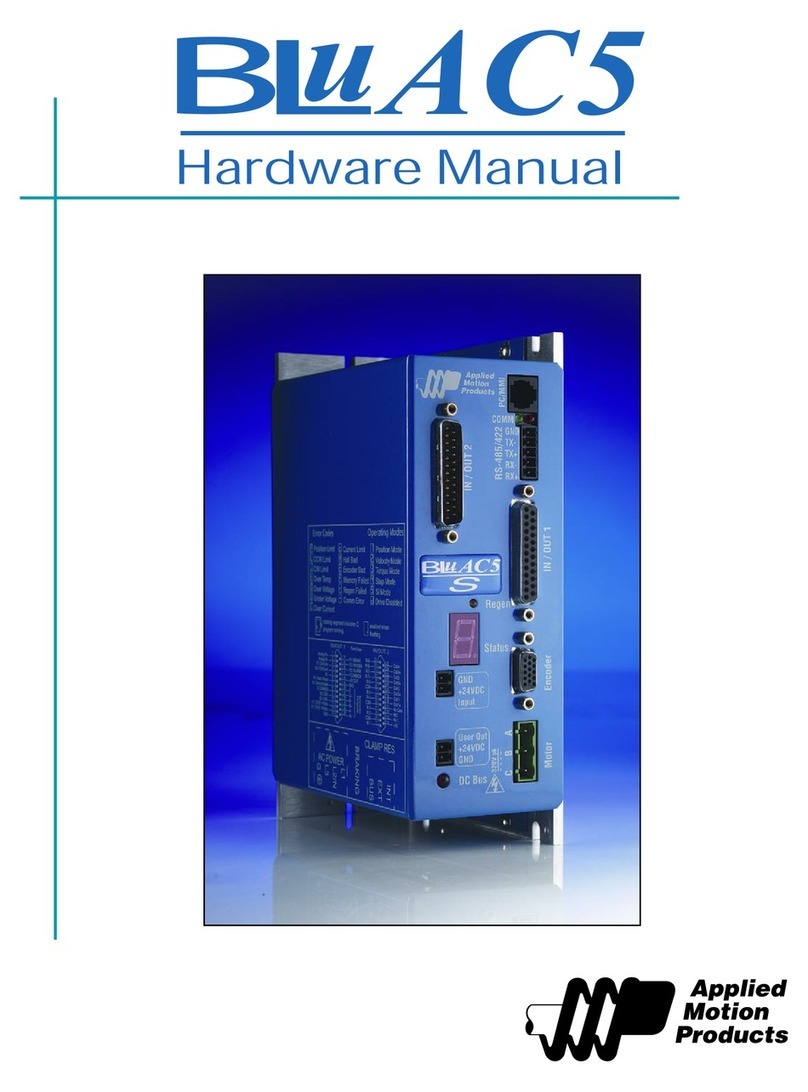
Applied Motion Products
Applied Motion Products BLuAC5 User manual
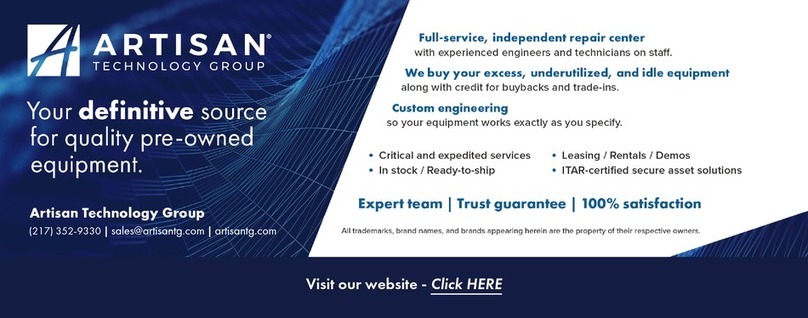
Applied Motion Products
Applied Motion Products PDO 2035 User manual
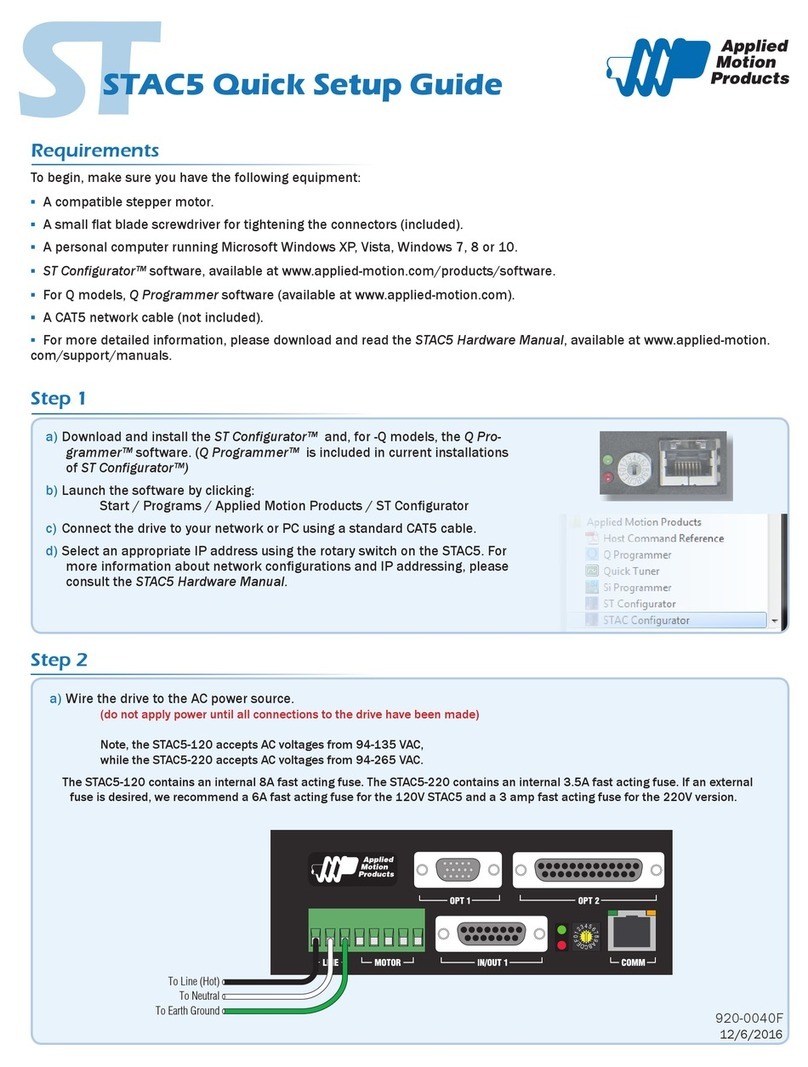
Applied Motion Products
Applied Motion Products STAC5 Series User manual

Applied Motion Products
Applied Motion Products STR2M User manual
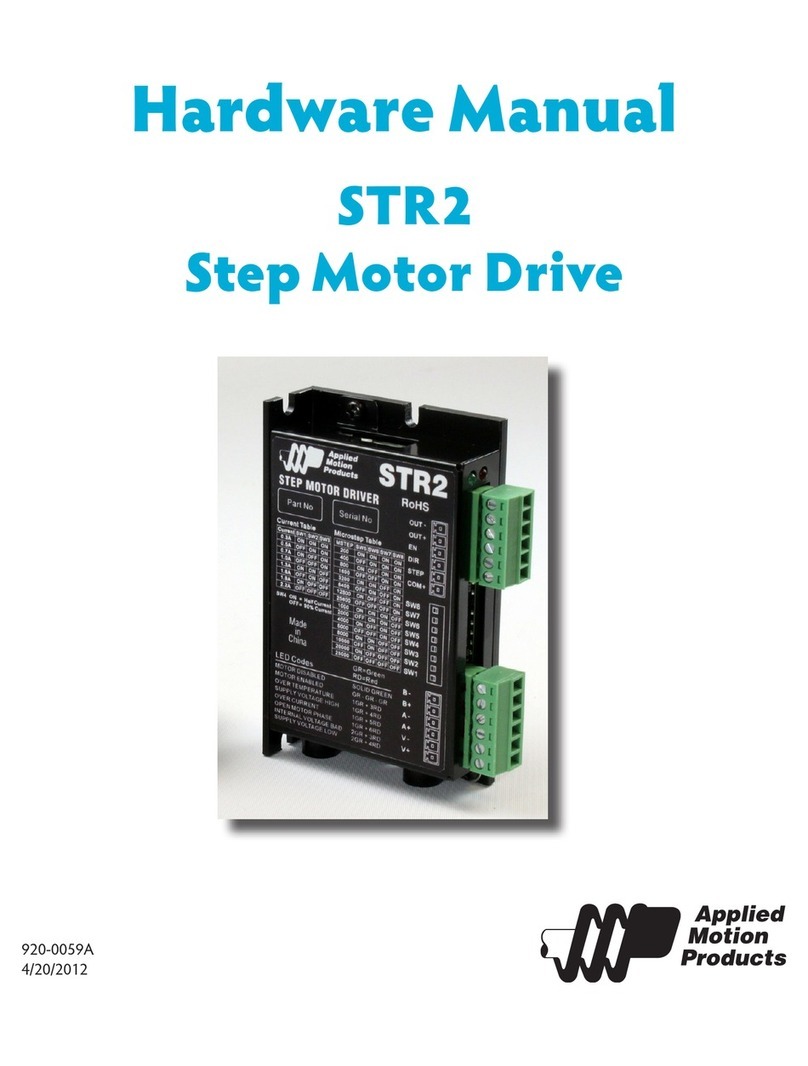
Applied Motion Products
Applied Motion Products STR2 User manual
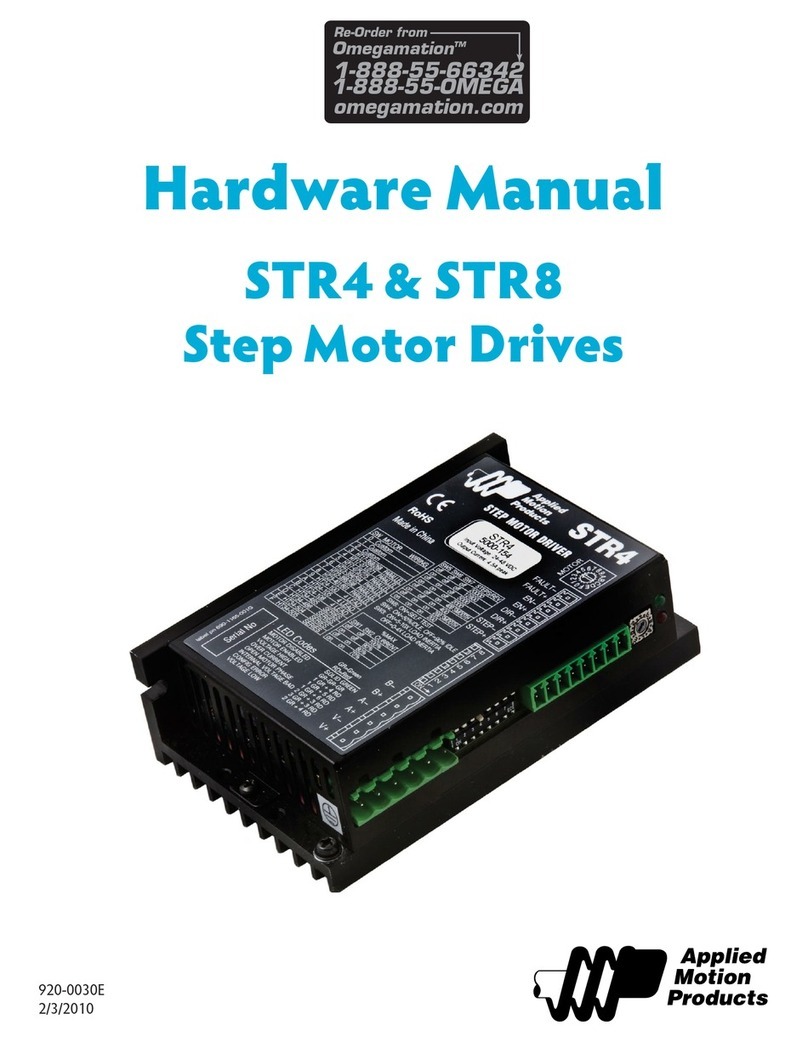
Applied Motion Products
Applied Motion Products STR4 User manual
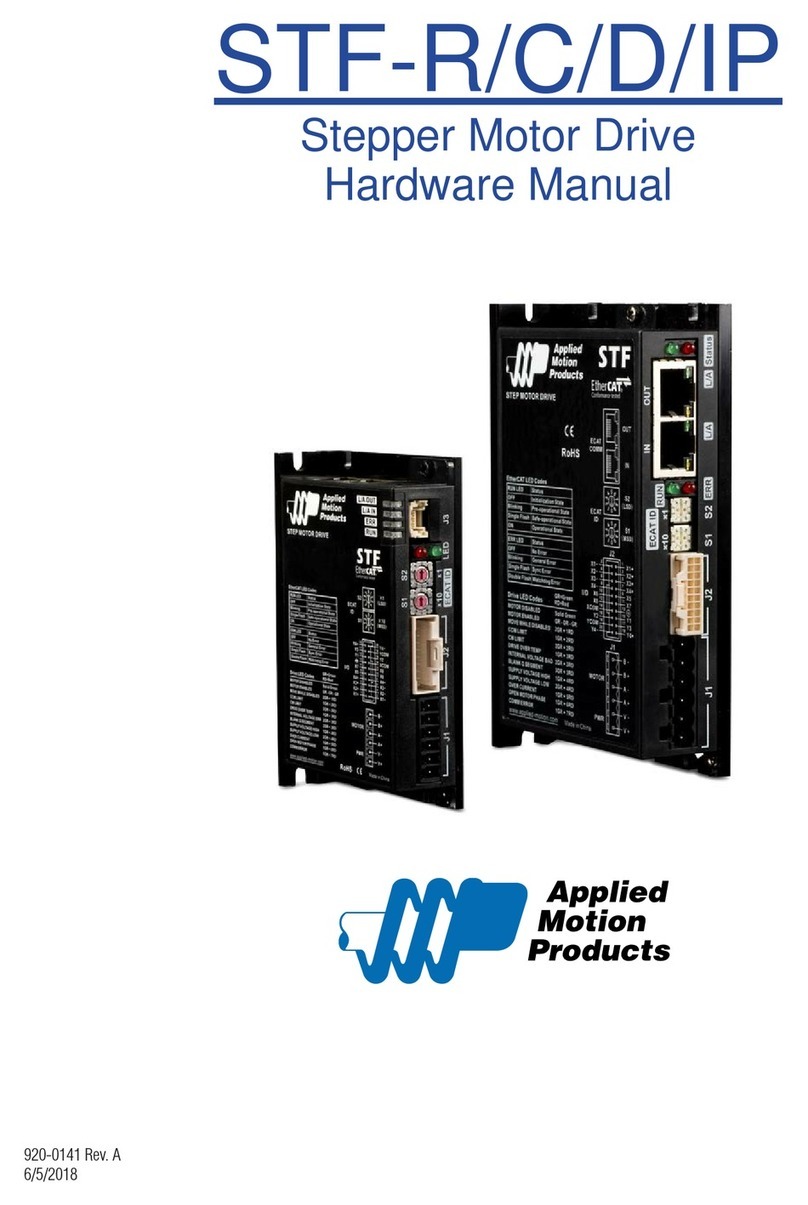
Applied Motion Products
Applied Motion Products STF-R Series User manual
Popular DC Drive manuals by other brands

SOMFY
SOMFY Sonesse 30 RS485 quick start guide

TPM
TPM STP-M112 user manual
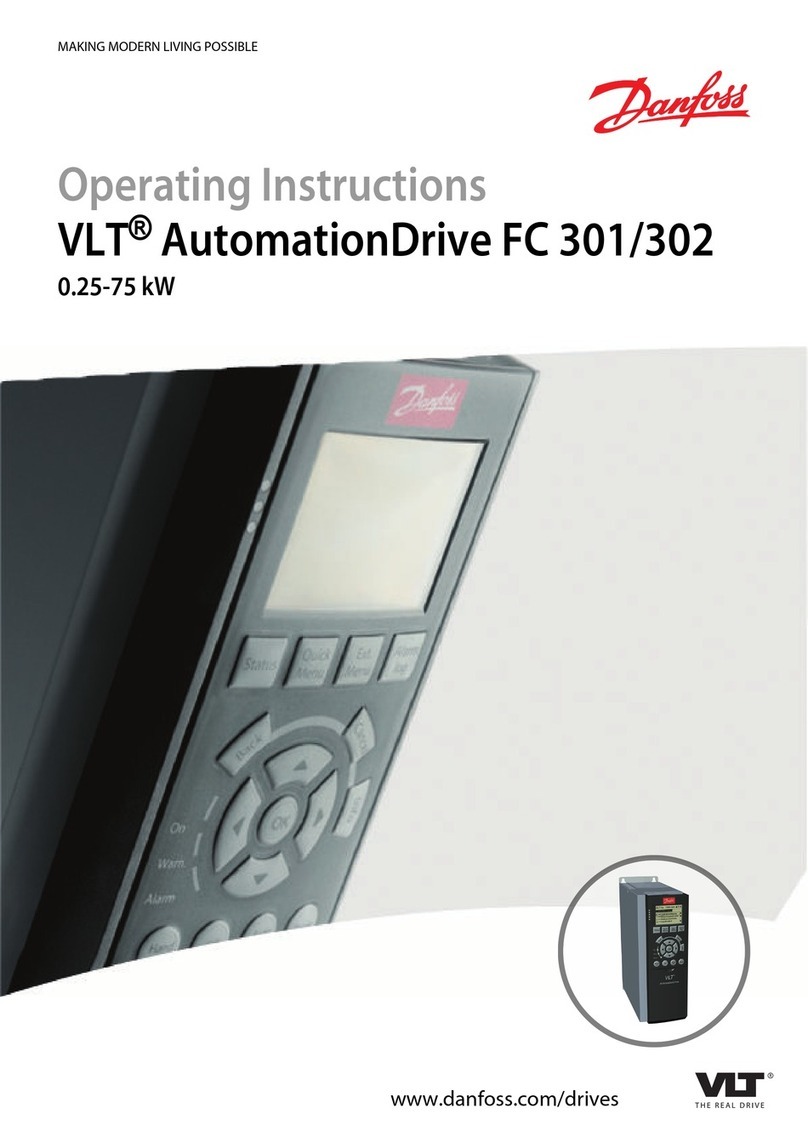
Danfoss
Danfoss VLT AutomationDrive FC 301 operating instructions

GFA
GFA ELEKTROMAT SI 40.15-40,00 installation instructions
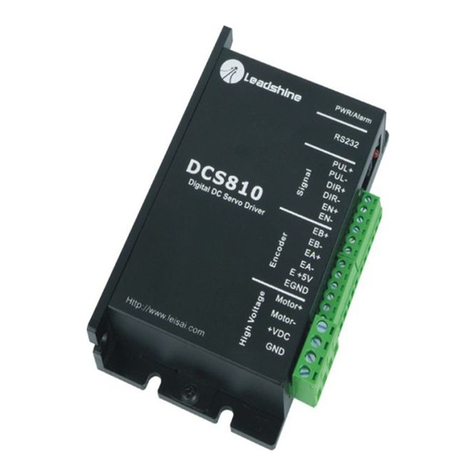
Leadshine Technology
Leadshine Technology DCS810V2 user manual

GFA
GFA ELEKTROMAT ST 80.24-50,00 installation instructions