AST KODIAK M2 User manual


2
High Pressure
The Kodiak is capable of very high pressure. Extreme caution
must be used in its operation. Pressure increases as resistance
in the material line increases. Longer hose lengths will increase
pressure as will a kink in the line. The Kodiak will build pressure
to overcome the resistance and move the material through the
line. This machine is designed for high pressure. Lack of caution
for it’s high pressure capabilities may result in serious injury to the
operator or anyone close by.
Make sure the material line is free of restrictions and is not kinked be-
fore use. Valves are not standard equipment on the spray line, to in-
sure that a valve is not inadvertently closed while the pump is on.
Since there is no valve there will be some dripping from the gun after
the switch is turned off while the pressure is relieved from the material
line. You can continue to spray as the material begins to slow down or
point the gun into the hopper until the material stops flowing.
Extension Cord Use
The Kodiak is a powerful pump and requires a good power
source. It will draw from 5 to 15 amps depending on the type of
material being sprayed. The choice of extension cord is critical.
An improperly sized extension cord can cause the control box to
sense an under voltage condition and stop. This is a safety fea-
ture to protect the electric motor and control box. Use this chart to
select the right cord for your use:
Extension Cord Recommended
Wire Size Maximum Length
14 ga 25 feet
12 ga 50 feet
10 ga 75 feet
Note: These figures apply to the Kodiak in normal temperatures
under 100 degrees. Demanding conditions such as pumping a
thick knockdown mud in very high temperatures may require
shorter extension cords or larger wire size.
Electric Shock
This machine is designed to be operated in a dry environment.
Do not expose control box to rain, mist or streams of water.
Direct stream of water from a high pressure washer will overcome
the control box seal and cause a control box failure, creating a
hazard. To clean control box, wipe down with damp cloth only.
The Kodiak uses a lower voltage line to the gun to operate the on/
off switch. This is to reduce the hazard associated with shock.
This safety feature does not reduce the risk of an electrical spark
igniting flammable materials. Use caution at all times when oper-
ating the machine and do not expose the switch at the gun to
flammable materials.
Explosion
This machine operates on 110 VAC and is equipped with a three-
prong plug for grounding. Do not operate without the grounding
terminal on the plug. Use only properly grounded 110 VAC, 15
Amp outlets to reduce the risk of static sparking. Only use exten-
sion cords that accept a grounding wire. Static sparking can
cause explosion of flammable materials. Do not operate this ma-
chine in an enclosed area that contains flammable materials or
within 30 feet of any flammable or explosive materials.
Moving Parts
The pump uses a connecting rod in the pump body to turn the
rotor. This drive system is exposed to the top of the pump body
to allow the free flow of material. Keep all foreign objects, hands,
loose clothing or any other item from the pump cavity. Only put
material that you want to pump into the hopper or pump housing.
Foreign objects such as loose clothing can get caught in the drive
system and pull the object into the pump housing. Exercise
extreme caution around the pump.
On Site
Do not try to move the Kodiak once material has
been added to the hopper, the increased weight and higher cen-
ter of gravity could result in dangerous instability.
Damaged or Modified Equipment
Keep the machine in good repair.
CONTENTS
Warnings & Precautions ……….. 2
Technical Support ………………. 2
Getting Started ………………….. 3
Electronics Detail ……………….. 5
Parts List & Diagrams ……6 thru 9
Tools & Maintenance …………. 10
Troubleshooting …………………11
Terms & Warranty ………………12
TECHNICAL SUPPORT
Contact our factory by phone at 877-833-4342. Phone support hours are 8:00am-4:00pm PST, Mon. to Fri. Messages can be left after
hours with the message center. Please have your Kodiak serial number ready.
MY SERIAL NUMBER IS_______________________________________

GETTING STARTED
3
Rotor—Stator Assembly Instructions
Unwrap rotor and connecting
driveshaft.
Release locking cam ears on
the pump housing base.
Slide out the stator tube & pump
housing retainer assembly.
Thoroughly lubricate the inside of the
stator tube with liquid dish soap.
Apply a liberal amount of liquid dish
soap to the outside of the rotor.
Screw and push the rotor into the
stator tube, counter-clockwise.
Slide the rotor-stator assembly into the
pump housing base. If the assembly
does not go all the way back, check the
connecting drive shaft alignment.
The rotor should stick out approx. 2”
as shown above, making sure the
gasket in the brass retainer stays in
place.
The connecting drive shaft must
align with the square receiver on
the rigid coupling.
If the rotor is inserted far enough and the connecting drive shaft is
aligned, the assembly will connect back into it’s original position and
can be locked back in place. The Rotor-Stator Assembly is complete.
Reinstall the hopper.
If it will be more than a week between use, it is best to disassemble
these parts and reassemble when needed.
Uncrate the Kodiak and inspect all parts for any shipping damage.
Remove the rotor and connecting driveshaft from the hopper and follow the Rotor-Stator Assembly Instructions below:

1. NOTE BEFORE PROCEEDING: Never pump the Kodiak without
material running through the pump system - Do not run the pump
dry - this may result in pump failure. Progressive cavity
pumps like the Kodiak use the material being pumped as the
pump lubricant.
2. PROVIDE POWER by plugging the Kodiak into a dedicated
15 amp circuit. Shared circuits may deliver less than 15 amps
resulting in safety shutdown of the Kodiak pump. If using an
extension cord, you must meet the extension cord require-
ments shown on Page 2. If the power source is not adequate
or you do not have the correct gauge cord, the unit may stop
pumping and show a failure status light. You will need to cor-
rect this condition before proceeding with your spray job.
3. FILL HOPPER with a wetting solution to prime the material
hose. This is done by pumping a watered down slurry through
the hose like a soupy drywall mud. You can also use water
and dish detergent soap to wet the inside of the hose if that is
all that is available. If using soapy water, pour about a 1/4 cup
of Dawn liquid soap (or similar clear liquid dish soap) into
the hopper. Then fill the hopper 1/2 way up with water. If you
use dish soap, you will need to add your slurry soon after to
replace the soapy solution as it will tend to cause the rubber
stator tube to become squeaky clean and stick to the rotor.
4. PREPARE SPRAY GUN FOR USE. Insert a spray tip into the
end of the pole gun by removing the retaining nut at the gun
head, then replace the retaining nut to hold the spray tip in
place. The gun head and retaining nut are both aluminum for
light weight, so take care that there is no debris caught in the
threads - this may result in cross threading.
5. PREPARE the Kodiak controls and start pump. Initially, put all
controls to the OFF position.
• Put the push/pull switch at the gun to the OFF position ( pulled in).
• Put the toggle switch on the control box to OFF.
• Turn speed knob (located on the black control box) to 0.
• With all the controls set to OFF, move the speed setting to 50.
• Point the gun into the hopper so that when you turn on the pump,
you cycle/pump the material back into the hopper.
• Flip the control box toggle switch to ON.
• Activate pump body by pulling the push/pull switch out. You will
hear the electric motor turning the pump and the soapy water will
be pumped through the hose, back into the hopper.
M2 KODIAK SAFETY FEATURE: If the operator plugs the Kodi-
ak into a power source or flips the toggle switch to the ON posi-
tion when the push/pull switch is on, then the system goes to
sleep mode. This safety feature prevents the operator from acci-
dentally starting the pump. If this happens, then cycle the push/
pull switch to start the pump.
7. WETTING THE HOSE. Pump the slurry (from Step 4) into
the hopper for a minute or two, creating a lubricated slick
environment for the material to pass through the lines easily.
This helps to prevent a dry pack condition that can happen if
you pump thick material into a dry hose. The head of the
material sees only the dry inside of the hose and as it moves
along continues to dry out, causing a dry pack condition.
8. CLEAR THE HOSE of wetting solution. After wetting the
hose, you will pump almost all of the wet slurry out of the
hopper as you get ready pour the material in. When you are
running the water out of the Kodiak, do not drain the bottom
pump cavity out, making sure there is a little water left in the
pump before you add the material.
9. ADD TEXTURE MATERIAL. You are now ready to add the
material to spray. The first material coming out the tip will
be diluted with your wetting solution. Let that portion pass
until you see a steady flow of properly mixed spray material.
10. SYSTEM CLEAN UP FOR LONG TERM STORAGE. The
Kodiak is designed for easy clean-up. Using soapy water
and a scrub brush with a long handle to wipe the inside of
the hopper down and pump 5 gallons of soapy water
through the system into a container for disposal. After the
majority of the material is cleaned out and the less than a
few inches of water remain in the pump body you are free to
disassemble the pump by un-screwing the hopper and then
open the cam-loc levers on the lower hopper to access the
lower pump parts. Rinse the remaining parts and re-
assemble. We recommend you leave the rotor and stator
apart and stowed in the hopper for future use. Use liquid
dish soap, like Dawn to lubricate the pump on re-
assembly, as described in the Rotor-Stator Assembly proce-
dure on Page 3. The electronics are housed in a water re-
sistant case, however do not expose the control box to high
pressure water streams.
11. DO NOT RUN PUMP DRY.This pump operates by a chrome
plated steel rotor turning inside a rubber stator tube. These parts
are lubricated by the material that is being pumped. Without
material to wet the pump, it can overheat and stick, potentially
damaging the pump. If the pump is run dry or with water only, the
rotor may adhere to the stator making it difficult to turn. If
that happens refer to the trouble shooting section of this
manual. Replacement of the stator tube is simple and inex-
pensive.
12. BEFORE EACH USE. Before each use check to make sure
there are no blockages or kinks in the material line. Do not
run the pump if there are restrictions in the material line.
Damaging high pressure could build up due to line re-
strictions or kinks.
13. INITIAL START UP POWER. On initial startup the Kodiak
may benefit from being plugged directly into an outlet, with-
out an extension cord, until rotor turns freely. By doing this
you insure that sufficient power is available to the motor.
4

5
ELECTRONICS
TABLE 1 - CONTROL MODE AND STATUS LED INDICATION
CONTROL MODE STATUS LED INFORMATION
FLASH RATE COLOR
SEQUENCE
ILLUMINATION DURATION
SECONDS
RUN Slow Flash Green 1 Sec on - 1 Sec off
STOP Steady Yellow Constant
STAND-BY (SLEEP, see detail
on pg. 10)
Slow Flash Yellow 1 Sec on - 1 Sec. off
SHORT CIRCUIT Slow Flash Red 1 Sec on - 1 Sec. off
GROUND FAULT Quick Flash Red 1/4 Sec on - 1/4 Sec off
OVERLOAD Steady Red Constant
UNDERVOLTAGE Quick Flash Red-Yellow 1/4 Sec Red - 1/4 Sec Yellow
OVERVOLTAGE Slow Flash Red-Yellow 1 Sec Red - 1 Sec Yellow
RECOVERED UNDERVOLTAGE Quick Flash Red Yellow - off-
Green - off
.025 Sec Red - 0.25 Sec Yellow–0.5 Sec off—1
Sec Green—0.5 Sec off
RECOVERED OVERVOLTAGE Slow Flash Red-Yellow-off-Green-
off
1 Sec Red-1 Sec Yellow-0.5 Sec off-
1 Sec Green-0.5 Sec off
ROTABLE SPARE PROGRAM: The Kodiak electronic box is best serviced by factory technicians. We do not rec-
ommend that they be serviced in the field. Since the Kodiak is built to last, it pays to keep it operational. We offer a
unique and affordable spare control box program called ROTABLE SPARE PROGRAM. If you have a control box
that requires repair call our factory and ask to speak to our Service Department. The program is simple, you send
your box in and we send you a serviceable replacement (may be new or factory reconditioned) box for a substan-
tially reduced flat fee, no questions asked. That’s our way of keeping our customers going affordably. Overnight
shipping is available.

6
Fig. 3
Kodiak M2
Major Components
Ref PN Description Qty.
1 00511 Handle bar 1
2 00515 Collar, handle lock 2
3 00660 Electronic control box 1
4 00661 Motor power cable 1
5 00662 Main power cable 1
6 00663 Gun control cable 1
7 00624 Main chassis/frame 1
8 00643 Pump, gear motor (1 HP,5:1) 1
9 00523 Tire-wheel assy. 2
Ref PN Description Qty.
10 00646 Junction plate 1
11 00620 Pump housing base 1
12 00538 Lever, camloc 2
13 00650 Frame rail 2
14 00486 Stator tube 1
15 00621 Pump housing retainer 1
16 00623 Pump housing 1
17 00628 Flat seal, 6 inch 1
18 00622 Hopper 1
PARTS LISTS AND DIAGRAMS
Fig. 2
Kodiak M2
Control panel

7
FIG. 4
MOTOR OUT-DRIVE &
PUMP SEAL ASSEMBLY
REF P.N. DESCRIPTION QTY.
1 00688 Wing nut 4
2 00687 Washer, flat, 5/16 8
3 00682 Lock washer, 5/16 12
4 00695 Nut, 5/16 4
5 00690 Seal seat O-ring 1
6 00547 Seal seat 1
7 00693 Seal seat mate 1
8 00691 Drive band retainer 1
9 00692 Drive band seal 1
10 00694 Lower spring retainer 1
11 00549 Spring 1
12 00550 Spring retainer 1
13 00689 1
REF P.N. DESCRIPTION QTY.
14 00552 Square drive 1
15 00553 Connecting rod 1
16 00590 Mechanical seal assy. 1
17 00681 Bolt, 8 mm x 25 mm 4
18 00646 Junction plate 1
19 00647 Spacer plate 1
20 00643 Pump, gear motor
(1 hp, 5:1 Bison)
1
21 00629 Bracket, axle/motor 1
22 00632 Plate, motor mount 1
23 00686 Bolt, 8 mm x 16 mm 4
24 00542 Bolt, carriage 5/16 x 1 4
25 00624 Chassis, main 1

FIG. 5
PUMP HOUSING ASSEMBLY
REF P.N. DESCRIPTION QTY.
1 00646 Junction plate 1
2 00634 Gasket 1
3 00620 Base, pump housing 1
4 00621 Retainer, pump housing 1
5 00538 Lever, camloc 2
6 00627 Flat seal, 3 inch 2
7 00486 Stator tube 1
REF P.N. DESCRIPTION QTY.
8 00556 Rotor 1
9 00623 Pump housing 1
10 00628 Flat seal, 6 inch 1
11 00443 Camloc pin, 1-1/2 in 2
12 00539 Bolt, 5/16x1-1/4 4
13 00682 Lock washer, 5/16 4
8

9
Fig. 7
Handle Bar Assembly
REF P.N. DESCRIPTION QTY.
1 00650 Frame rail 2
2 00624 Main Chassis 1
3 00515 Collar, handle lock 2
4 00518 Stabilizer, handle 2
5 00511 Handle bar 1
6 00514 Screw, 1/4-20X3/8-collar 2
7 00516 Stop, handle 2
8 00517 Button, snap 4
9 00521 Screw, stabilizer 2
10 00685 Screw, 1/4-20x5/8, SHC 4
Fig. 6
Electric Pole Gun
REF P.N. DESCRIPTION
8 00340 Valve, air metering 1
9 00589 Switch, push pull 1
10 00134 Pipe, pole gun 1
11 00135 Bracket, elec. pole gun 1
12 3/4 close nipple (OPTIONAL) 1
13 00172 3/4 ball valve (OPTIONAL) 1
REF P.N. DESCRIPTION QTY.
1 00122 Nut, tip retainer 1
2 0012X Tip, pole gun 1
3 00133 Head, gun 1
4 125-4-4 Hose barb, 1/4 MNPT 1
5 OET 1518 Crimp, clamp 2
6 MP25300 Hose, air 1
7 128-4-4 Swivel hose barb, 1/4FNPT 1

Keep your machine in good working order. For general use and
maintenance, hand tools and a pipe wrench may be required.
WIRING CARE
Periodically check the wires for loose connections, cuts or fraying.
Replace power cord if ground prong is damaged.
MATERIAL HOSE CARE
Inspect hose lines for any weaknesses. These lines carry materi-
al at very high pressure, so it is important that they be in good
condition.
• The stator and rotor are wear parts. They will require re-
placement over time. The length of time between replace-
ment depends on the material pumped and frequency of use.
Any foreign material accidentally run through the pump may
lead to premature replacement.
• Grease the wheels every six months. There are grease zerts
on the wheel hub.
• Store the machine in a dry, protected area.
• Check the air in the tires periodically
• Do not let material harden in hopper or pump
MATERIAL COMPATABILITY
Not all liquids are suitable or approved for the Kodiak. Call the
factory if you have questions about materials other than drywall
spray mud.
CLEAN-UP
• Your clean up procedures will be different depending on the
product you are spraying and the time between jobs.
• Never use petroleum based cleaner on the Kodiak. It will de-
stroy the rubber pump parts.
• If you are spraying a standard drywall texture mud and there
is no more than a few days between use, you can leave a
mud in the hopper. Wipe down the machine and rinse off the
hose set. It will not hurt the pump or the hopper to leave tex-
ture in it. You may cover the hopper to keep texture from dry-
ing out.
• If you expect long delays between jobs, then it is best if you
do a more thorough clean-up (see Step 10 on Page 3).
• Flush soapy water solution through the hopper, pump and
hose set. Use liquid dish soap like Dawnor Joy. Remove
the stator tube and rotor and place them in the hopper for
future use and assembly. At this point, your Kodiak can be
stored safely for many months.
• If you are spraying a material that will harden and is not easily
removed after it sets, then a more thorough procedure will be
necessary after each use. Wipe down the machine and rinse
off the hose set. Use a liquid dish soap like Dawnor similar.
Remove the stator tube and rotor and place them in the hop-
per for future use and assembly. When reassembling, pour a
liberal amount of dish soap on the rotor and this will make the
reassembly easier.
• DO NOT SPRAY WATER ON THE CONTROL BOX. THE
CONTROL BOX IS WATER RESISTANT, NOT WATER
PROOF. WATER INSIDE THE BOX WILL CAUSE FAILURE
AND POSSIBLY A SAFETY HAZARD. SEE CONTOL BOX
TOOLS & MAINTENANCE
REF P.N. DESCRIPTION QTY.
1 00630 Axle 1
2 00525 Cotter pin 4
3 00633 Washer, 1” Flat 2
4 00522 Spacer, Plastic 4
5 00624 Main Chassis 1
6 00625 Left Collar 1
7 (not
show
n)
00626 Right Collar (not
shown)
1
8 00523 Tire wheel assy 2
9 00650 Frame rail 2
10 00685 Screw, 1/4-20x5/8,
SHC
8
Fig. 8
Axle & Collar Assembly
10

11
Problem Possible Cause Corrective Action
Pump delays before
starting
This is normal operation None
Pump will not start 1. Pump went to “sleep”* This hap-
pens if pump is plugged into power
source with gun switch in the “ON”
position
2. Worn electrical cord
3. Relay circuit failure in control box
1. Turn switch on and off at the gun
to restart the machine. (see Note
at bottom of this page for more
information)
2. Check cord and replace as needed.
3. Recommend factory repair of
components in control box.
Motor starts but will
not pump
Failure of drive mechanism Check to see if rotor is turning. Repair or
replace failed parts as needed.
Motor struggles but
can’t turn pump
Stator adhered to rotor, caused by
running pump dry or with water only.
New stator tubes are very tight, which
can make it difficult to turn the rotor.
This condition is similar to placing
rubber on clean glass without water.
It is very hard to move the rubber
against the glass until there is some
lubricant to allow the rubber to glide
freely.
Add slurry to pump and turn pump
on and off several times (1 second
cycles). If this does not work, put a pipe
wrench on stator tube and apply shock
load while turning on motor. If still not
freed, remove stator tube and free the
rotor. Reinstall with liquid dish soap as
lubricant.
Pump is slow and
getting worse
Rotor or stator is worn Rotor and stator are wear parts and must
be replaced from time to time.
Pump shows some
leakage
Mechanical seal is worn Mechanical seal is a wear part and will
need to be replaced occasionally. Service
depends on the nature of
the material being pumped and the ser-
vice duty.
TROUBLESHOOTING GUIDE
*SLEEP: Your Kodiak is equipped with a new safety feature to help prevent accidental pump
starts. This can happen when plugging the machine in to power while the switch at the gun and
the switch at the control box are in the ON position. If this happens the computer in the control
box recognizes this as an operator error and will go to “SLEEP”, this means it will not start the
pump. This condition is shown as Stand-by (see table 1 on page 4) in the status LED on the
control panel. To override this and start the pump, simply turn the switch at the gun OFF then
ON again and the pump will start. Cycling the switch off and on, in effect, wakes up the control
box and reactivates the pump.
CONTROL BOX REPAIR PROGRAM: If you have determined that you control box requires re-
pair take advantage of our affordable ROTABLE SPARE PROGRAM. See details on bottom of
page 5.

SPECIFICATIONS
Machine Weight, (excluding hose and gun) 138 lb.
Weight, 35’ hose and gun………………… 30 lb.
Shipping Weight …………………………. 196 lb.
Hopper Capacity………………………….. 16 gal.
Ratings:
1.0 hp 5:1 Gear Motor 110VAC 15 Amp
1.0 hp 15:1 Gear Motor 110VAC 15 Amp
1.5 hp 5:1 Gear Motor 220VAC 10 Amp
The information contained in this manual was, to the best of our
ability, accurate at the time of printing. .As a result of continuing
product development, the information and specifications contained
here are subject to change at any time without notice.
Kodiak M2 is manufactured in the USA
Copyright 2017 American Spray Technologies
US and foreign patents pending
Kodiak and Kodiak M2 are Trademarks of American Spray Technologies
1420 20th St. N.W. Suite A
Auburn, WA 98001
Toll free Tel 877-833-4342
Local 253-833-4342
STANDARD TERMS AND CONDITIONS OF SALE
Payment Terms: Prepaid unless approved for terms.
Service Charge: All amounts not paid within thirty (30) days of date of invoice will accrue a service charge in the amount of two (2) percent per month or the
highest rate allowed by applicable usury laws. The charge will be compounded each month in which the invoice or any part thereof remains unpaid.
Collection Costs: Purchaser agrees to pay all collection costs incurred by Seller in collecting unpaid amounts, including attorney fees, witness fees (expert or
otherwise) and all out-of-pocket costs.
Freight Policy: FOB shipping point. Title passes upon delivery to the carrier at the point of shipment. Shipments are not insured unless ordered by purchas-
er.
Delivery: Delivery dates given in advance of actual shipment are estimates and shall not be deemed to represent fixed or guaranteed delivery dates
Cancellation: Buyer may cancel an order at any time prior to shipment by mutual agreement of a reasonable cancellation charge to be paid to Seller. Orders
for equipment over $1,000.00 will incur a minimum of a 10% cancellation charge. Security deposits for orders may be withheld for a reasonable time to allow
for the resale of the inventory committed to the order. Such time will not normally exceed 6 months.
Returned Goods: Goods may not be returned without prior approval and a “Return Authorization Number” (RAN). Only new parts in new condition valued
under $1,000.00 may be returned. The return period is 30 days from original shipping date. A minimum restocking fee of 25% will apply. Items valued over
$1,000.00 including big rigs and theKodiak Sprayer are non-refundable. Custom and special order parts may not be returned.
Warranty and Limitation of Warranty: For a period of six months after retail purchase within the United States of America, Seller will, at its option, repair or
replace, free of charge, seller manufactured parts found to be defective in material or workmanship. Components not manufactured by the Seller are covered
under the original manufacturer warranty. Examples include, but are not limited to electric motors; gas powered engines, hydraulic parts, gear reduction boxes,
compressors, and batteries. Such components carry separate warranties. This warranty is limited to the original purchaser starting on the date of retail pur-
chase.
The provisions as set forth in this warranty provide the sole and exclusive remedy of Sellers obligations arising out of the sale of this equipment. Seller will not
be liable for incidental or consequential loss or damage. Seller’s sole liability under valid warranty claims shall be limited, at seller’s option, to repair or replace-
ment of defective parts or goods.
warranty on equipment that has been modified, neglected, abused or improperly operated or inadequately maintained. Seller will not be responsible
for expense in connection with repairs made by anyone other than a seller-authorized service station, unless prior written authorization has been obtained.
This limited warranty gives you specific legal rights, and you may also have other rights, which vary, from state to state. Certain disclaimers are not allowed in
some states and therefore they may not apply to you under all circumstances. It is the responsibility of the purchaser to deliver or ship the equipment covered
under this warranty to the factory. Freight costs will be paid by the purchaser.
Table of contents
Other AST Paint Sprayer manuals
Popular Paint Sprayer manuals by other brands
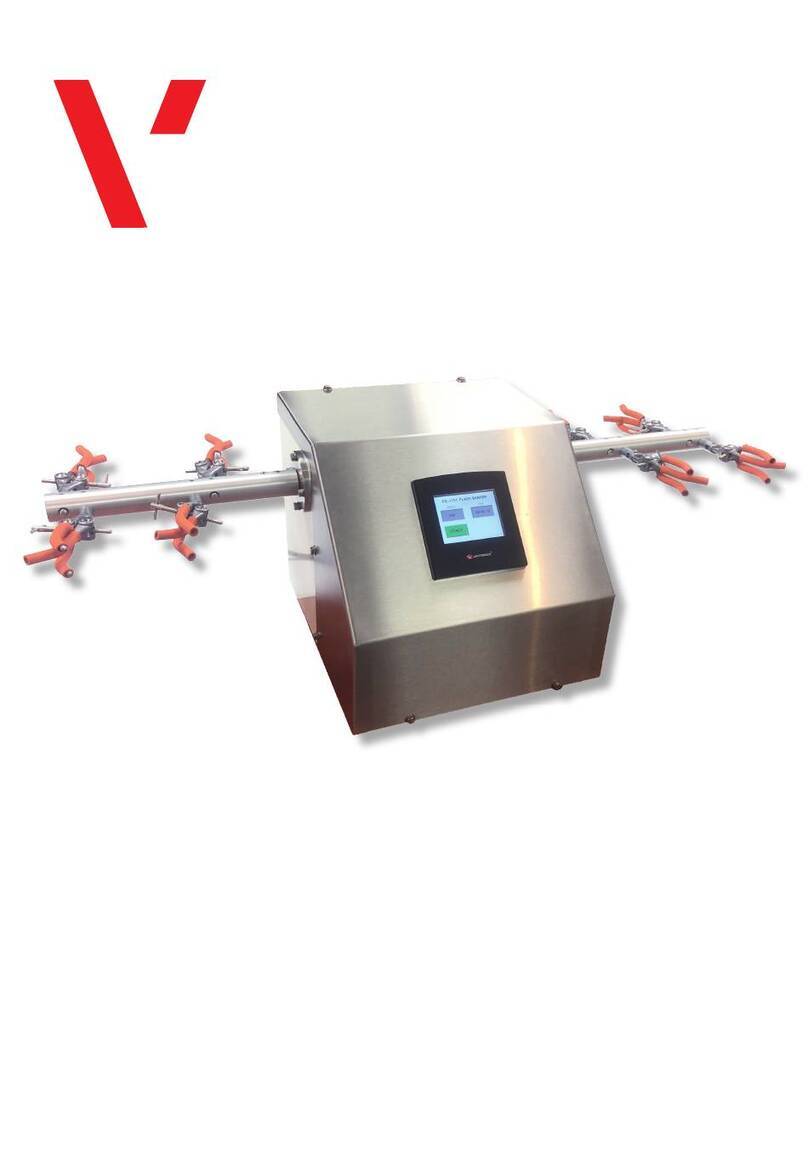
VOS
VOS 6313-FS1751 quick start guide
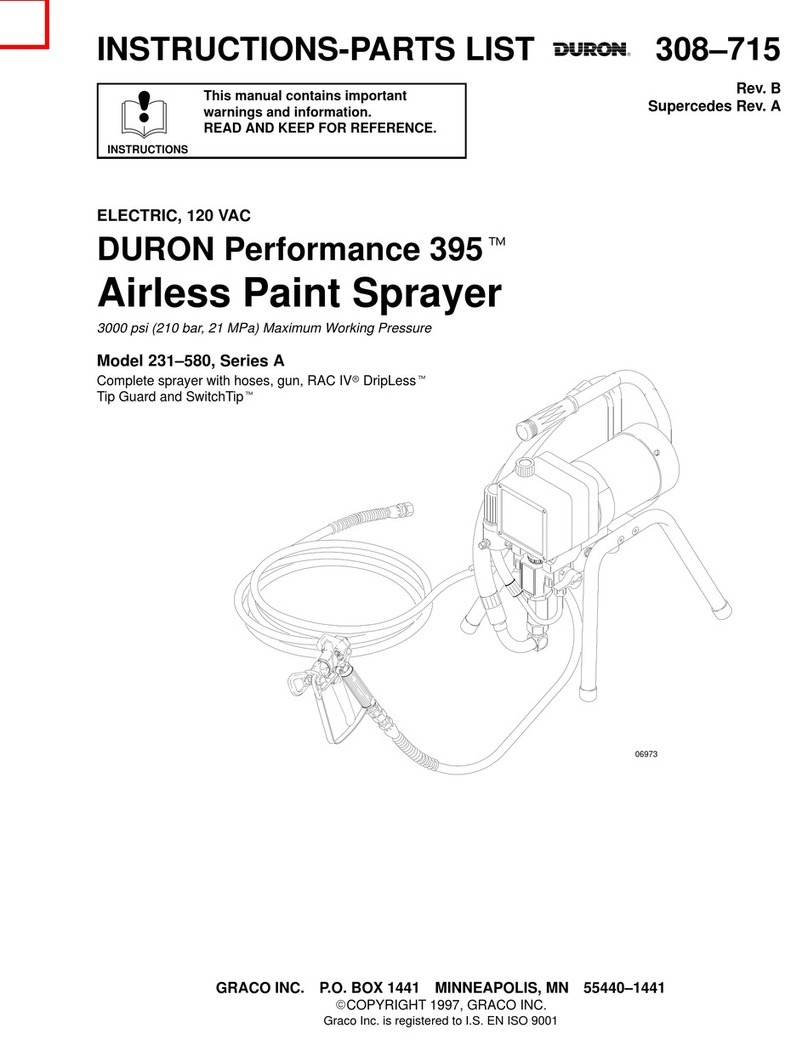
Graco
Graco DURON Performance 395 A Series Instructions-parts list
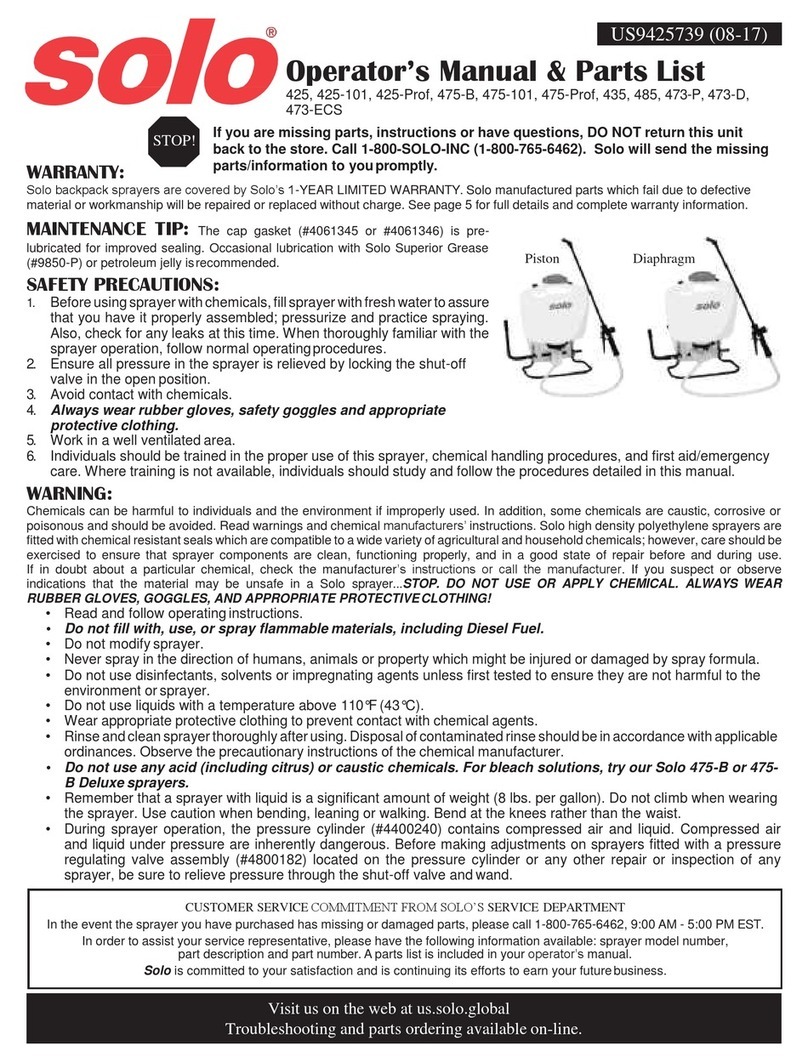
Solo
Solo 425-101 Operator's manual & parts list
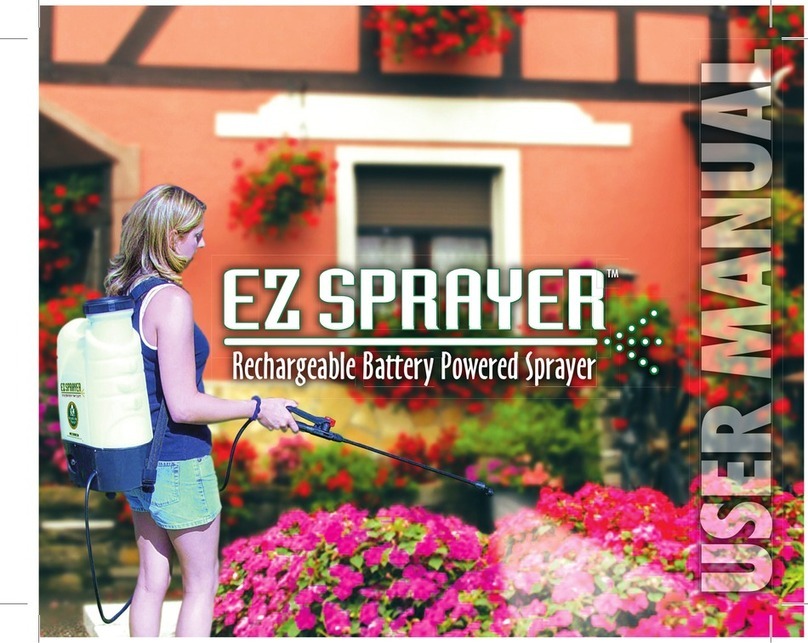
National Garden Wholesale
National Garden Wholesale EZ Sprayer user manual
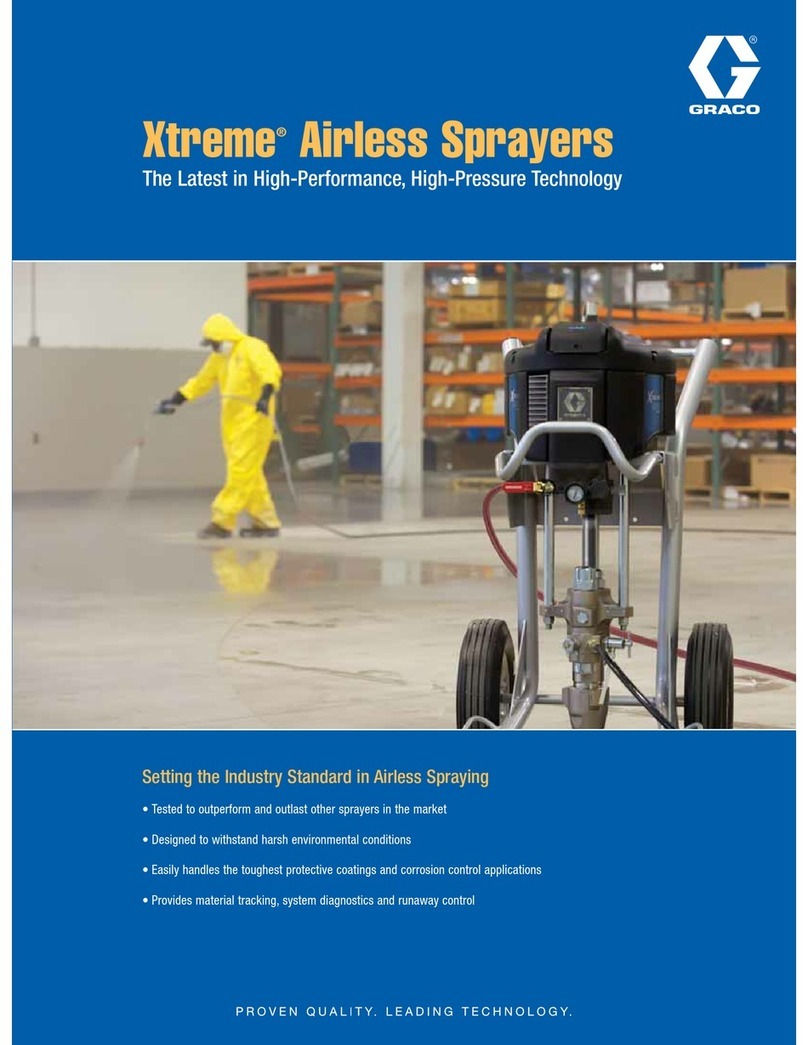
Graco
Graco Xtreme NXT Brochure & specs

Solo
Solo 425 Classic Operator's manual & parts list

Krautzberger
Krautzberger MA-1 operating instructions
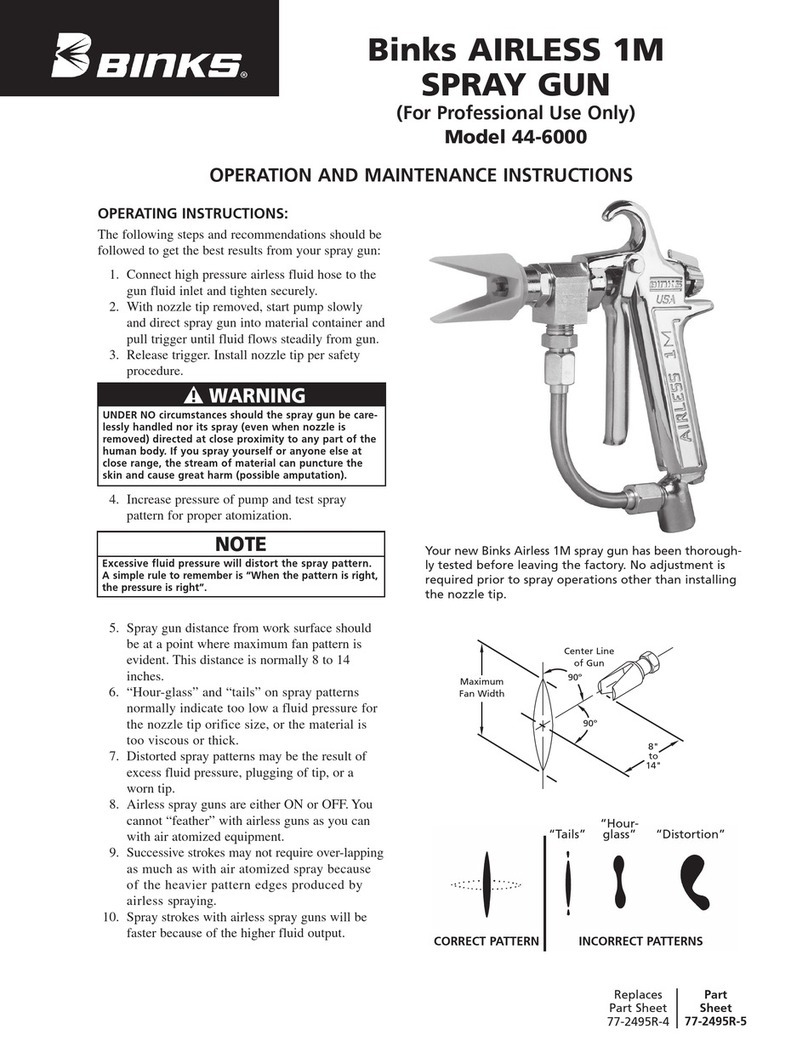
Binks
Binks 44-6000 Operation and maintenance instructions
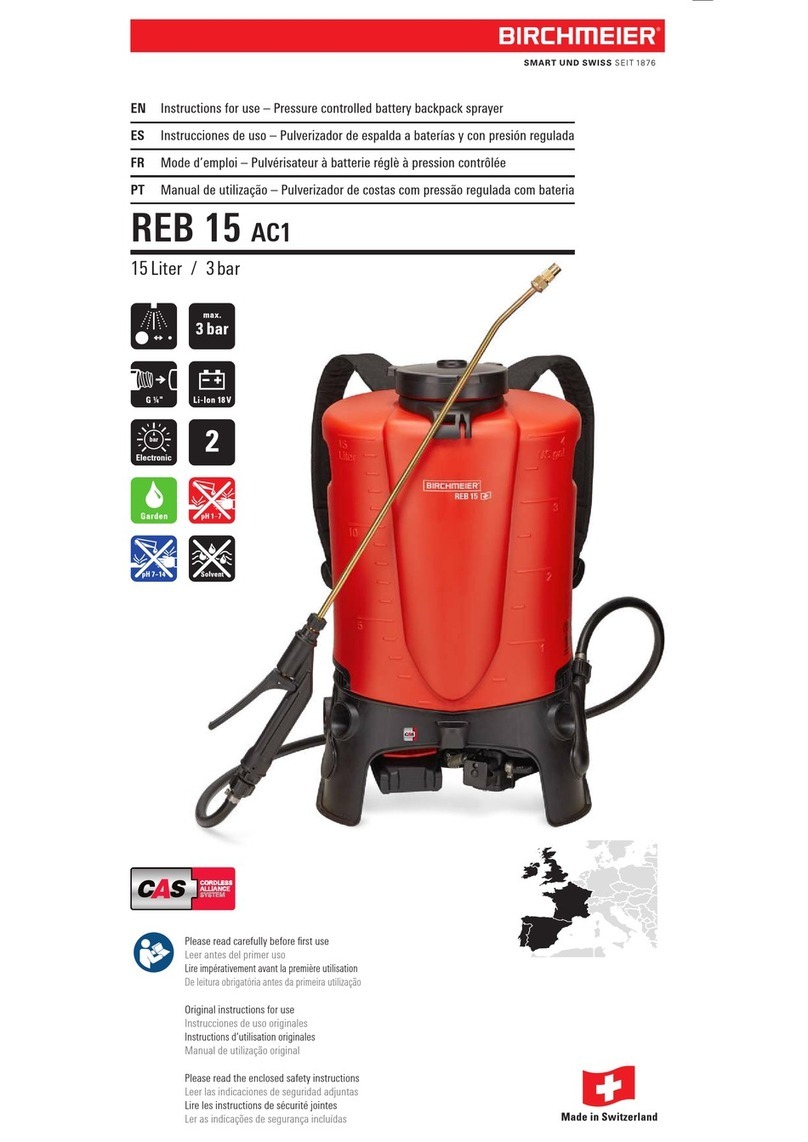
Birchmeier
Birchmeier REB 15 AC1 Instructions for use
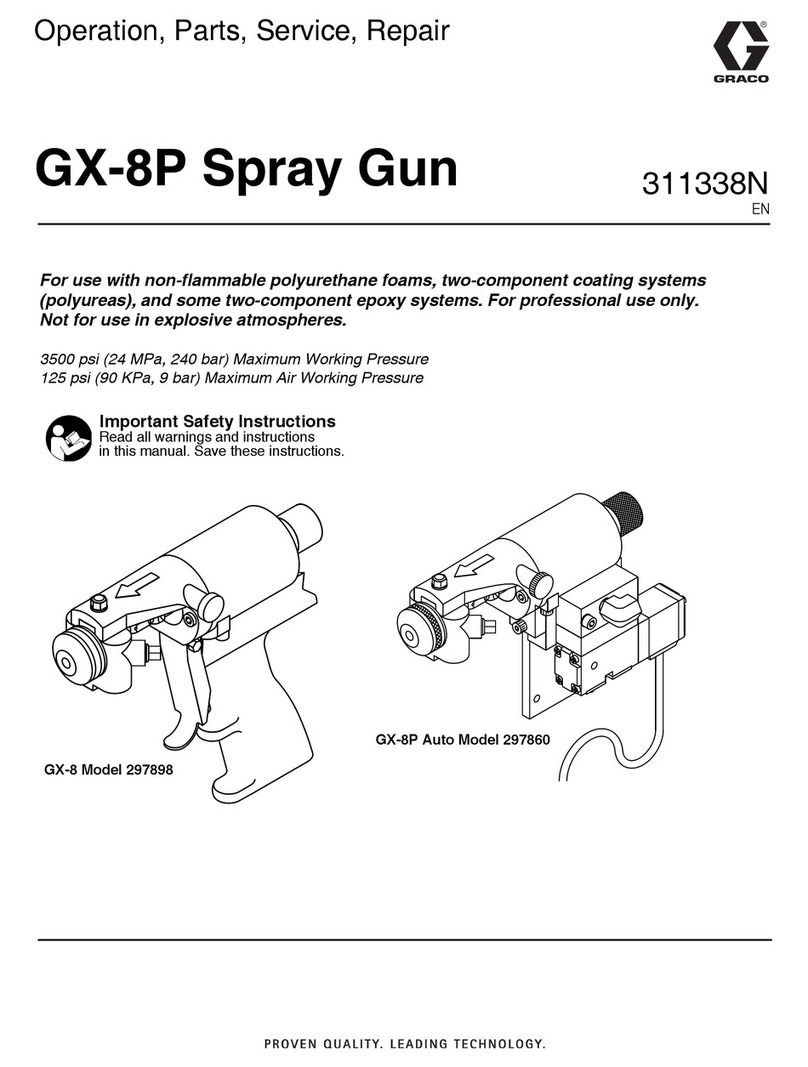
Graco
Graco GX-8 Operation, parts, service, repair

Sagola
Sagola PSAA 108 Instruction manual and spare parts list
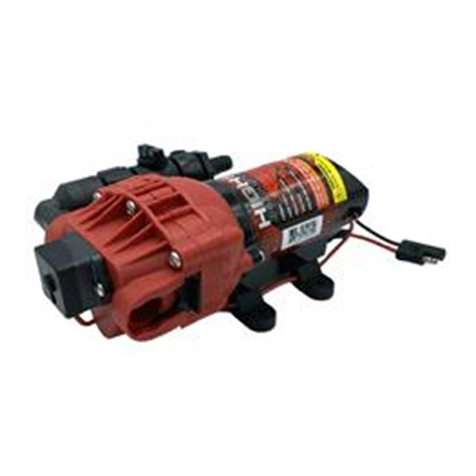
Fimco
Fimco SK-61-12V-TSC Assembly / operation instructions / parts