Athena S Series User manual

SERIES “S”
SOLID-STATE STAGING
CONTROLLERS
Instruction Manual
Note: Not all agency approvals apply to all models. See manual for detailed information.

Series S Solid-State Staging Controller Instruction Manual
Series S Solid-State Staging Controller Instruction Manual
Series “S” Agency Approvals
E57435 Industrial Control Equipment Component, Auxiliary Devices
UL-508
Models SCA, SUA
E66598 Component, Temperature Indicating and Regulating Equipment
UL-873
Models SCB, SCC, SUB, SUC
Athena Controls, Inc.
5145 Campus Drive
Plymouth Meeting, PA 19462
Phone: 610-828-2490
Fax: 610-828-7084
www.athenacontrols.com
You can reach our technical support team by phoning 1-800-782-6776 (from the United
States) or 610-828-2490 (from anywhere in the world). The e-mail address for tech
support is [email protected]
Athena® is a registered trademark of Athena Controls, Inc.
© 2004 Athena Controls, Inc. All rights reserved.

Series S Solid-State Staging Controller Instruction Manual
Series S Solid-State Staging Controller Instruction Manual
Two-Year Limited Warranty
THIS EQUIPMENT IS WARRANTED TO BE FREE FROM DEFECTS OF MATERIAL
AND WORKMANSHIP. IT IS SOLD SUBJECT TO OUR MUTUAL AGREEMENT THAT
THE LIABILITY OF ATHENA CONTROLS, INCORPORATED IS TO REPLACE OR
REPAIR THIS EQUIPMENT AT ITS FACTORY, PROVIDED THAT IT IS RETURNED
WITH TRANSPORTATION PREPAID WITHIN TWO (2) YEARS OF ITS PURCHASE.
THE PURCHASER AGREES THAT ATHENA CONTROLS, INCORPORATED ASSUMES
NO LIABILITY UNDER ANY CIRCUMSTANCES FOR CONSEQUENTIAL DAMAGES
RESULTING FROM ITS USE OR FROM IMPROPER HANDLING OR PACKAGING OF
SHIPMENTS RETURNED TO THE FACTORY.
COMPONENTS WHICH WEAR OR WHICH ARE DAMAGED BY MISUSE ARE NOT
WARRANTED. THESE INCLUDE CONTACT POINTS, FUSES, ELECTROMECHANICAL
RELAYS, AND TRIACS. UNITS WHICH HAVE BEEN MODIFIED BY A CUSTOMER IN
ANY WAY ARE NOT WARRANTED.
Other than those expressly stated herein, THERE ARE NO OTHER WARRANTIES
OF ANY KIND, EXPRESS OR IMPLIED, AND SPECIFICALLY EXCLUDED BUT NOT
BY WAY OF LIMITATION, ARE THE IMPLIED WARRANTIES OF FITNESS FOR A
PARTICULAR PURPOSE AND MERCHANTABILITY.
IT IS UNDERSTOOD AND AGREED THE SELLER’S LIABILITY WHETHER IN
CONTRACT, IN TORT, UNDER ANY WARRANTY, IN NEGLIGENCE OR OTHERWISE
SHALL NOT EXCEED THE RETURN OF THE AMOUNT OF THE PURCHASE PRICE
PAID BY THE PURCHASER AND UNDER NO CIRCUMSTANCES SHALL SELLER BE
LIABLE FOR SPECIAL, INDIRECT, INCIDENTAL OR CONSEQUENTIAL DAMAGES.
THE PRICE STATED FOR THE EQUIPMENT IS A CONSIDERATION IN LIMITING
SELLER’S LIABILITY. NO ACTION, REGARDLESS OF FORM, ARISING OUT OF THE
TRANSACTIONS OF THIS AGREEMENT MAY BE BROUGHT BY PURCHASER MORE
THAN ONE YEAR AFTER THE CAUSE OF ACTION HAS ACCRUED.
SELLER’S MAXIMUM LIABILITY SHALL NOT EXCEED AND BUYER’S REMEDY IS
LIMITED TO EITHER (i) REPAIR OR REPLACEMENT OF THE DEFECTIVE PART OR
PRODUCT, OR AT SELLER’S OPTION (ii) RETURN OF THE PRODUCT AND REFUND
OF THE PURCHASE PRICE, AND SUCH REMEDY SHALL BE BUYER’S ENTIRE AND
EXCLUSIVE REMEDY. THE SPECIFICATIONS PUT FORTH IN THIS MANUAL ARE
SUBJECT TO CHANGE WITHOUT NOTICE.

Series S Solid-State Staging Controller Instruction Manual Series S Solid-State Staging Controller Instruction Manual
1
Contents
Section 1 General Introduction
1.1 General Description…………………………...1
1.2 Typical Configurations...……………………....2
1.3 Specifications………...………………………...4
Section 2 Installation Instructions
2.1 Installation………………………...……….…...5
2.2 Module Explanation …………………….....….8
2.3 Operation………………………………..……...9
2.4 Adjustments…………………………..………...9
2.5 Time Proportioning Adjustment…..…………..10
2.7 Span Adjustment…………..…………………..11
2.8 System Adjustments………..…………………11
2.9 Fusing…………………………..………………11
Section 3 Options
3.1 Thermistor Input - “B” Option……...…………12
3.2 Thermistor Input - “C” Option………………...12
Section 4 Unit Repairs..................................................19

Series S Solid-State Staging Controller Instruction Manual Series S Solid-State Staging Controller Instruction Manual
1
Section 1 General Introduction
1.1 General Description
The Athena “S” Series Solid State Staging Controls
Provide pilot duty sequencing of multiple loads up to
18 stages.
SU - Up-Down Mode:
Adds stages in progression. Removes stages in
reverse order., the last stage ‘on’ being the first stage
‘off’ on load reductions. Blue Handle Cooling stages
provide automatic transfer to cooling. Starts with all
stages ‘off.’
Output capacity: 1 AMP per step (10 Amps inrush).
SC - Circular Mode:
Operates all heaters and contractors evenly. First
stage ‘on’ is first stage ‘off.’ Starts with all stages ‘off.’
Output capacity: 1 Amp per step (20 Amps inrush).

Series S Solid-State Staging Controller Instruction Manual
2
Series S Solid-State Staging Controller Instruction Manual
3
1.2 Typical Configurations
Circular - SC Type Controller
Ordering code example:
10 Heating Steps
Code: SCA - 10
Any number SC Heat Stages up to ten. End board
follows last used stage.
SC End Board
(Always follows
last used stage)
SC Heat Stages
Step Delay Board
Input Conditioner
BLACK
WHITE
WHITE
WHITE
WHITE
WHITE
WHITE
WHITE
WHITE
WHITE
WHITE
YELLOW
GREEN
9
8
7
6
5
10
4
3
2
1
9
8
7
6
5
10
4
3
2
1
(Timing)

Series S Solid-State Staging Controller Instruction Manual
2
Series S Solid-State Staging Controller Instruction Manual
3
1.2 Typical Configurations
Up-Down Operation – SU type Controller
Ordering code example:
6 Heating & 2 Cooling Steps
Code: SUA-06-02 or SUB-06-02
Any combination of heat and/or cool steps up to ten.
Cooling and heating modules may be intermixed if
reheat is desired. A heat module below a cool module
will provide automatic reheat.
Last position
not used on SU
SU Heat Stages
SU Cool Stages
Step Delay Board
Input Conditioner

Series S Solid-State Staging Controller Instruction Manual
4
Series S Solid-State Staging Controller Instruction Manual
5
1.3 Specifications
Input ‘A’: 4-20 mA dc. 60 mA max,
or 6 V dc, 9 V max. 135
ohms slidewire, 100-1000
ohms acceptable
Input ‘B’: Thermistor probe to match
range
Output: One amp per step max
(ten amps inrush)
Signal Isolation: 1500 volts from power
circuits and ground
Time Delay: Adjustable, from 2.5 to 12
seconds; automatic
slowdown near balance
Adjustments: Time Proportioning –
Adjustable from differential
to time proportioning
Span – Adjusts to input
range
Indication: L.E.D. logic status light on
each output stage.
Supply voltage: 120 V + 10%, - 15%,
50/60 Hz 4 VA plus total
contactor VA
Ambient Temperature: 30º to 130º F. (-1.1º to 54.4º C)
Dimensions: 13" L, 6" W, and 3" H
(34.3 cm L x 15.2 cm W x
8.9 cm H)

Series S Solid-State Staging Controller Instruction Manual
4
Series S Solid-State Staging Controller Instruction Manual
5
Section 2 Installation Instructions
2.1 Installation.
1. Carefully unpack instrument. Handle with care.
Inspect for shipping damage. Report and damage to
carrier immediately.
2. Pick a location for the controller where it will not be
subjected to excessive shock, vibration, dirt, moisture
or oil. The ambient temperature of the area should
be between 30º and 130ºF (-1.1º to 54.4º C).
3. Mount the controller
with four 8-32 x
” screws. The
controllers are not
position sensitive
and can be mounted
in any plane.
4. Consult the wiring
diagram on the next
page. Standard
units require
120 V 50/60 Hz.
5. Be certain that
power is off. Then
connect power wires
to .250 push-on
terminals marked X1
and X3. If used on
a grounded system,
the X2 terminal should be grounded.

Series S Solid-State Staging Controller Instruction Manual
6
Series S Solid-State Staging Controller Instruction Manual
7
Standard Wiring (up to 10 steps)
Standard Wiring (11 to 18 steps)
“A”
“A”
“B”
“C”

Series S Solid-State Staging Controller Instruction Manual
6
Series S Solid-State Staging Controller Instruction Manual
7
6. Contractors are connected to the .250 push-on
terminals marked on through ten. Connect one lead
from each contactor coil to the terminals starting from
number one up to a maximum of ten. Connect the
return wire from the contactors to X2, outside terminal.
Note: Power lines should be free of high power radio
frequency signals or other damaging voltage
spikes. If R.R. induction heating equipment or high
powered electric welders are nearby, filter all power
lines leading to the staging controller.
7. If a fuse blows, check wiring and/or contactors for
shorts or overcurrent.
8. Troubleshooting - Units with standard inputs (4-20
mA, or 135 ohms slidewire) can be quickly checked by
jumpering terminals D and E. All heating stages should
turn on, as indicated by the red L.E.D. on each stage.
Remove jumper from D and E and connect to C and D.
All heat stages should turn off and cool stages (if any)
should turn on., see red L.E.D. on cool stages. Remove
jumper from C and D.
9. Connect input signal to appropriate lettered terminals
– A through F. Standard Units: Terminals A & B – 4-20
mA source (Temperature Controller).
(A Input) Terminals C, D & E – 135 ohms slidewire
(Thermostat).
10. Turn Power on and check total system for proper
operation.
Warning: Since solid state devices do not turn off in
the same sense as relay contacts, a potential
shock hazard exists. For your protection, be
certain all line and control power has been
disconnected before working on the unit or
the auxiliary contactors.

Series S Solid-State Staging Controller Instruction Manual
8
Series S Solid-State Staging Controller Instruction Manual
9
2.2 Module Explanation.
The S Series Staging Controller consists of a main
frame and a large printed circuit board into which are
inserted a variety of input, timing and output stage
boards. For ease of identification and maintenance,
the individual boards are supplied with color coded
handles.
There are labels on each green and yellow handle
describing the exact input and time delay of the
signal conditioner and step delay modules. The label
supplies quick identification of the unit’s operating
modes. On the white, red, and blue stages, a logic
status light (light emitting diode – L.E.D.) can be seen
through the cover in the appropriate box as each
stage is energized.
The status light indicates the operation of the stage,
but is not an indication of the fuse nor the output triac
condition.
Note: Modules should never be placed in the unit
in arbitrary positions or while the controller is
energized.
BOARD # CODE DESIGNATION FUNCTION
785A072U01 Green Input Signal Conditioner 4-20 mA; 135 Slidewire (A)
785A073U08 Green Input Signal Conditioner Thermistor Temp. Control (B)
785A074U01 Yellow Step Delay Driver Adj Delay 2-5 to 12 Sec.
785A074U02 Yellow Step Delay Driver Adj Delay 2-7 to 50 Sec.
785A074U03 Yellow Step Delay Driver Adj Delay 2-14 to 100 Sec.
785A078U01 White Circular Mode Output Stge Heating SC Units
785A076U01 Black Circular End Board Completes Circular Loop
785A078U02 Red Up-Down, Heat SU Units
785A078U03 Blue Up-Down, Cool SU Units

Series S Solid-State Staging Controller Instruction Manual
8
Series S Solid-State Staging Controller Instruction Manual
9
2.3 Operation
The operation of a typical staging controller on a
heating process is as follows:
When power is applied, all steps at first will be off.
Then each step will turn on at the set time interval
until all steps are turned-on. When the process
reaches operating temperature (or as the process is
approaching setpoint depending on the proportional
band setting of the temperature controller), the
staging controller will cut back the number of steps
on, until the process requirements are satisfied.
After stabilization and if the time proportioning
adjustment is set at minimum, no steps will turn on
and off unless the process temperature changes
enough to require more or less steps if the time
proportioning adjustment is turned clockwise on an
‘Up-Down’ stepper, the last step ‘on’ will cycle on
and off to provide closer temperature control. On the
circular stepper, the next ‘off’ step will be turned on,
the first ‘on’ step will be turned off, and this action
will continue around as in a circle. The fastest rate
occurs with the adjustment full clockwise. Note:
The step interval is set by the timing module. Time
proportioning is only on the last step – and the fastest
rate is 5 seconds.
2.4 Adjustments
The following adjustments are found under the cover
plate on the yellow (step delay) module.
If a touch-up is desired, turn gently and wait at least
1 minute to observe results.

Series S Solid-State Staging Controller Instruction Manual
10
Series S Solid-State Staging Controller Instruction Manual
11
Timing Trim Pot
2.5 Time Proportioning (Cycling)
Adjustment – Right Side
This adjustment is used to provide vernier control of
power between steps by time proportioning a step of
power. Up-down steppers will proportion the last ‘on’
step, and the circular stepper will add the next ‘off’
step and subtract the last ‘on’ step at the required
percentage time. Turning the adjustment fully
clockwise will provide the fastest rate.
Minimum setting (ccw) provides an ‘on-off’ differential
on each stage (no time proportioning). Maximum
cycling will give high resolution control, but will also
cause maximum wear on contractors. Forced hot
air heating systems will generally require some
time proportioning for best control. Water heating
will usually not require any time proportioning for
excellent results, and the adjustment can be set to
zero (ccw).
2.6 Staging Interval Adjustment
This adjustment is used to set the time delay between
steps. Counterclockwise is the minimum delay of 2.5
seconds, adjustable fully clockwise to a maximum of
12 seconds on the standard yellow card.
i
n
c
i
n
c
i
n
c
Timing
SCAN
CALIBRATION
(CW = MORE ON)
STAGING INTERVAL
(CW = 12 seconds)
(CCW = 2.5 seconds)
TIME
PROPORTIONING
(CW = MORE PROPORTIONING)

Series S Solid-State Staging Controller Instruction Manual
10
Series S Solid-State Staging Controller Instruction Manual
11
2.7 Span Adjustment – Left Side
This adjustment scales the input signal to the number
of output steps on. On standard units, it is factory
present to turn all heat stages ‘on’ with 20 mA input
and all heat stages ‘off’ with less than 4 mA. If signal
levels are low or if span is miscalibrated, with full
input signal applied, very slowly turn the adjustment
clockwise until all heat stages come on. Also, if it
is desired to limit the number of steps on, apply
full input signal to the controller and turn the span
adjustment counterclockwise to turn off steps.
2.8 System Adjustments
Dynamic stability of the whole system should be
optimized using the proportional band adjustment on
the controller that drives the staging controller.
A narrow proportional band will produce tight control
with minimal droop on load changes. If there are
multiple time lags between heater and sensor,
or it thermal coupling is loose, the system will
continuously overshoot and undershoot (oscillate).
A better sensor location or wider proportional band
setting should stabilize the process.
2.9 Fusing
The controller is supplied with 1A small glass fuses.
Littelfuse type 3AG or Bussman type AGC. These
fuses protect the triacs in the output boards from
shorts in the contactor or in the contactor wiring. for
slow acting or larger contactors, the fuses should
be replaced with littelfuse type 3AG ‘Slo-Blo’ or
Bussman type MDL (1A). Small contactors up to

Series S Solid-State Staging Controller Instruction Manual
12
Series S Solid-State Staging Controller Instruction Manual
13
NEMA size 2 will operate with standard fuses. NEMA
3 and 4 contactors may require slow blow fuses,
depending on the manufacturer. NEMA 6, 7, and
8 are similar to the small contactors because they
have internal pilot contactors.
If a fuse blows, check the contactor and contactor
wiring for shorts before operating the controller. The
controller cannot cause the fuses to blow.
Section 3 Options
3.1 Thermistor Input – ‘B’ Option
When the ‘B’ put module is added to the staging
controller, the controller becomes a simple non-
indicating temperature controller. connect the
Thermistor probe to points A & B and connect the
setpoint pot to points C, D, and E. The leads can be
extended using conventional copper wire. Available
ranges are 50-180ºF (5006), 100-200ºF (5006), and
140- 250ºF (5008). The controller is failsafe to both
open and shorted probes.
To quickly check the controller, connect a test resistor
(1000 to 10,000 ohms) across points A & B to
simulate the probe. Turn the setpoint fully clockwise
(high temperature). All steps should come on. If all
steps do not turn on, slowly turn the span adjustment
on the yellow board clockwise until all steps turn on
(allow 1 minute per step).
Short terminals A & B and all heating stages will turn
off (cooling stages will turn on). Connect probe and
energize system.

Series S Solid-State Staging Controller Instruction Manual
12
Series S Solid-State Staging Controller Instruction Manual
13
For best control, the Thermistor should be placed
in the process so that it can detect any temperature
change with little thermal lag.
3.2 Thermistor Input – ‘C’ Option
Outdoor Reset: (Type C Input). Setpoint range is
60ºF-170ºF. Two Thermistor sensors; one process,
one outdoor reset, automatically change the
controlled temperature as the outdoor temperature
changes. This eliminates droop or offset error. The
ratio of effect the outdoor probe has over the indoor
(process) probe is adjustable from 10:1 to 1:2. The
setpoint and reset ratio adjustment potentiometers
are on the staging controller cover.
Refer to Table 1 for typical Initial Temperature settings
for a number of different types of heating systems.
TABLE 1 Typical heat-
ing medium
temperature at
design cond.
Typical
initial
setpoint
Reset Ratio
Design Temperature
-20˚ F 0˚ F 20˚ F
Hydronic
Direct
Standing
190˚ F 100˚ F 1:1 1:1.4 1:1.6
Convector/ Baseboard 200˚ F 120˚ F 1.1:1 1:1.1 1:1.6
Fan Coil
Heating Only
180˚ F 80˚ F 1:1.1 1:1.4 1:2
Heating/Cooling 140˚ F 80˚ F 1.5:1 1.2:1 1:1.2
Indirect
Floor Radiant
90 ˚ F 70˚ F 1.5:1 3.5:1 2.5:1
Ceiling Radiant 110˚ F 70˚ F 2.2:1 1.7:1 1.2:1
Forced Air 150˚ F 80˚ F 1.3:1 1:1 1:1.4
Make-Up Air 75˚ F 70˚ F 18:1 14:1 10:1

Series S Solid-State Staging Controller Instruction Manual
14
Series S Solid-State Staging Controller Instruction Manual
15
Reset Ratio
The reset ratio expresses the amount of change in
the heating medium control point caused by a change
in outdoor temperature. It is the ratio of outdoor
Change to heating medium control point change.
Notice that this is an inverse ratio: when outdoor
temperature goes down, the control point goes up.
Selecting The Reset Ratio
The reset ratio should be selected to provide a
complete range of heating medium temperatures
when the outdoor temperature goes from 70ºF to
the outdoor design temperature. Typical reset ratios
for a number of different types of heating systems
are given in TABLE 1. These figures are intended
to provide the installer with a starting point on
installations where the reset ratio is not specified.
Further adjustments may be necessary depending on
the requirements of a particular system.
Operation
The 5002 sensor measures the outdoor temperature.
A change to in and outdoor air temperature causes
a resistance change in the Thermistor element of
the sensor. This resistance change unbalances the
bridge circuit of the reset controller. The effect of the
unbalance is to offset the heating medium control
point. The amount of offset in the relation to outdoor
change is determined by the setting of the Reset
Ratio knob. The action of the controlled equipment
compensates for the bridge unbalance by supplying
more or less heat to the controlled space.

Series S Solid-State Staging Controller Instruction Manual
14
Series S Solid-State Staging Controller Instruction Manual
15
Unit Repairs
It is recommended that units requiring service be returned
to an authorized service center. Before a controller is
returned for service, please consult the service center
nearest you. In many cases, the problem can be cleared
up over the telephone. When the unit needs to be returned,
the service center will ask for a detailed explanation of
problems encountered and a P.O. to cover any charge. This
information should also be put in the box with the unit. This
should expedite return of the unit to you.
This document is based on information available at the time
of its publication. While efforts have been made to render
accuracy to its content,, the information contained herein
does not purport to cover all details or variations in the
hardware nor to provide for every possible contingency in
connection with the installation and maintenance. Features
may be described herein which are not present in all
hardware. Athena Controls Inc. assumes no obligation of
notice to holders of this document with respect to changes
subsequently made.
Proprietary information of Athena Controls, Inc. is furnished
for customer use only. No other use is authorized without
the written permission of Athena Controls, Inc.

For free technical assistance in the USA,
call toll free 1-800-782-6776 or
email [email protected]
Athena Controls, Inc • 5145 Campus Drive • Plymouth Meeting, PA 19462 USA
900M021U00-0304-150-JA
Table of contents
Other Athena Controllers manuals
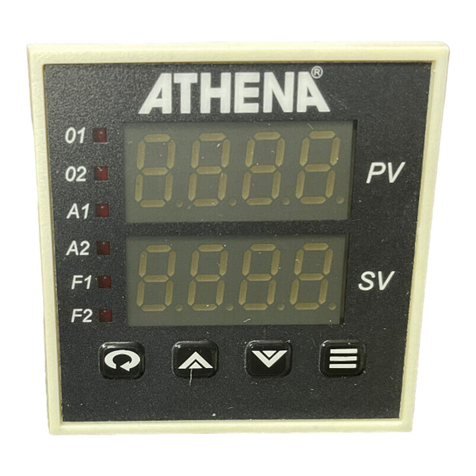
Athena
Athena SERIES 16 User manual
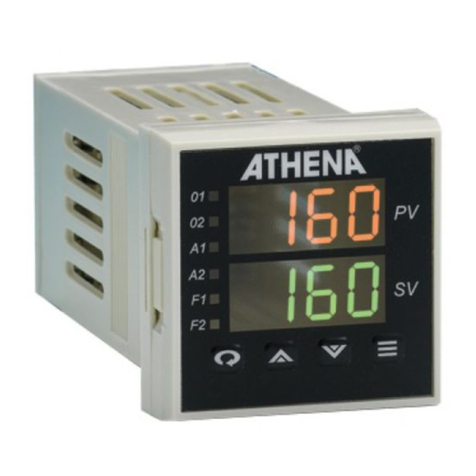
Athena
Athena SERIES 16 User manual
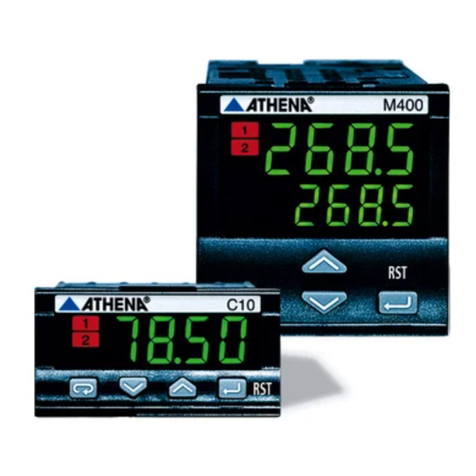
Athena
Athena C10 Series Use and care manual

Athena
Athena 18C Series User manual
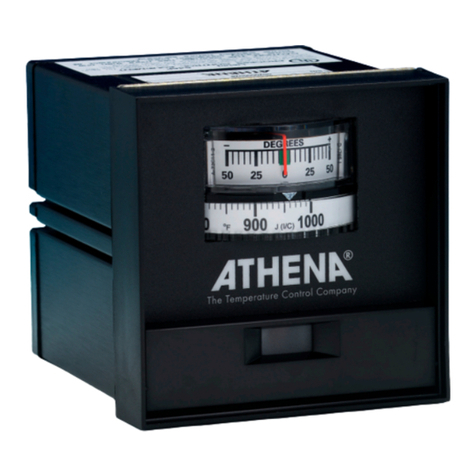
Athena
Athena 2000 Series User manual
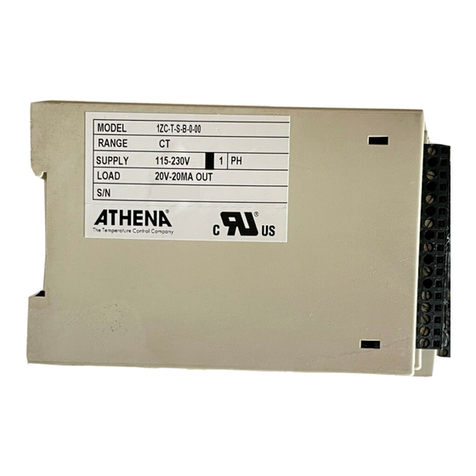
Athena
Athena 1ZC Series User manual
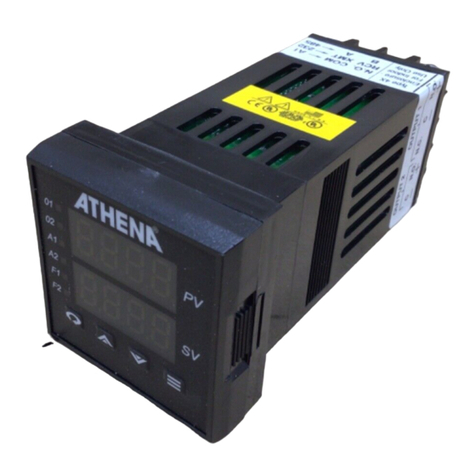
Athena
Athena 16C series User manual

Athena
Athena RMB/1 User manual
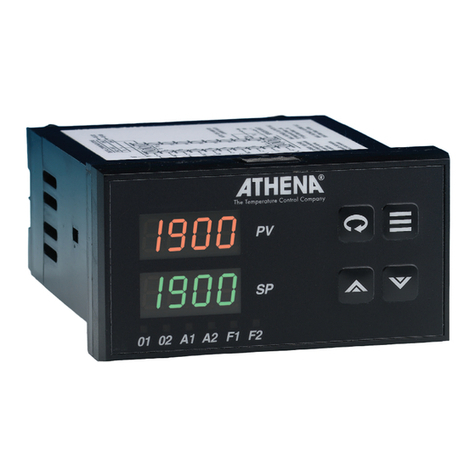
Athena
Athena 18C Series User manual