ATI Technologies RCE-710 User manual

Pinnacle Park • 1031 Goodworth Drive • Apex, NC 27539 • Tel: 919.772.0115 • Fax: 919.772.8259 • www.ati‑ia.com
S-1
RCE-710 Quick Start Guide Document #9640‑50‑1044‑02
RCE-710 Quick Start Guide
This document is intended to guide the user through setting up, wiring, and connecting an RCE-710
to a servo drive.
1. Initial Set-Up
Parts required: Refer to the RCE-710 manual
1. Mount the RCE-710. The RCE-710 can be side or rear mounted. Reference the RCE-710 manual for detailed
installation instructions, including appropriate interface plates.
2. Plug in the 4mm (5/32”) air tube into the compliance connector.
3. Optional: Plug the 1/4” tube into the cooling air manifold, reference Figure 1.1. The cooling air may be required
for more repetitive applications.
Figure 1.1—RCE-710 Overview
4. Connect the power and signal connections. Align the engraved dot on the cable with the circle on the RCE-710
and push to connect. Reference Figure 1.2.
Figure 1.2—Connecting Power and Signal Cables
Side Mounting Pattern
Rear Mounting Pattern
Cooling Air Connection
Compliance Air Connection
Orange Power Intercontec
915 ytec Connection
Green Signal Intercontec
615 ytec Connection
Align circle on cable
with circle on connector
Align circle on cable
with circle on connector

RCE-710 Quick Start Guide
Pinnacle Park • 1031 Goodworth Drive • Apex, NC 27539 • Tel: 919.772.0115 • Fax: 919.772.8259 • www.ati‑ia.com
S-2
Document #9640‑50‑1044‑02
Table 1.1—Orange Power Intercontec 915 ytec
Intercontec 915 pin out Pin Description
A U
B V
C W
GND Ground / Protected
Earth
5
N/C
6
7
8
9
Table 1.2—Green Signal Intercontec 615 ytec
Intercontec 615 pin out Pin Description
11Hall 1 (UV)
2 Hall 2 (VW)
3 Hall 3 (WU)
4 0V
5 (+) 5 – 24 VDC
6(-) Temp Sensor
7(+) Temp Sensor
8
N/C
9
10
11
12
Note:
1. Pin 1 is located directly underneath alignment circle on top of connector.
5. Route all cables and utilities down the robot arm ensuring ample bend radii.
NOTICE: Avoid tight loops or bends in cables. Use a motor cable that is short as possible without
impeding robot motion. Cutting and stripping the supplied cable may be required to achieve this.
6. Wire the power, signal and I/O connectors to the servo drive. Reference Section 2—Wiring Kollmorgen AKD2G
Drive for detailed wiring information.
7. Enable the motor and set the tool to the desired speed. See Step 4—Wire X21 for control and feedback signals.
within Section 2—Wiring Kollmorgen AKD2G Drive.
8. Test the robot program on a test part and observe the nish. Readjust tool parameters until desired nish is
achieved.

Pinnacle Park • 1031 Goodworth Drive • Apex, NC 27539 • Tel: 919.772.0115 • Fax: 919.772.8259 • www.ati‑ia.com
S-3
RCE-710 Quick Start Guide Document #9640‑50‑1044‑02
2. Wiring Kollmorgen AKD2G Drive
Parts required:
• 220V power source (120V accepted, but limits performance)
• 24 VDC power supply (minimum 3A recommended)
• 1.5A fuse
• E-Stop button (recommended)
• 16-20 AWG wire
• 22-24 AWG wire
• Cable for input power
• RJ45 Ethernet cable (X20) (optional)
• Drive connectors:
• Weidmuller BVF 7.62HP/04/180MF4 BCF/06R SN BK BX Female Terminal Block (X1)
• High Density Dsub 15-pin Male Connector (X23)
• 8-pin, pitch 7.62mm Pluggable Female Terminal Block (X3)
• 2-pin, pitch 5.08mm Pluggable Female Terminal Block (X10)
• 2 x 11 pins, pitch 3.5mm Pluggable Female Terminal Block (X21)
Figure 2.1—AKD2G Overview
X1:
Axis 1: Motor, Brake
Feedback 1
X20:
Service/HDMI
X21 I/O:
Feedback 4
X22 I/O:
Feedback 5
X23:
Feedback 3, EEO
PE:
Protective Earth
X3:
9-pin Power Supply
DC-Bus
Regen Resistor
SD Card Slot
X10:
24V Supply
Side View: Front View:

RCE-710 Quick Start Guide
Pinnacle Park • 1031 Goodworth Drive • Apex, NC 27539 • Tel: 919.772.0115 • Fax: 919.772.8259 • www.ati‑ia.com
S-4
Document #9640‑50‑1044‑02
1. Mount the AKD2G motor to the backplane of the controls cabinet and ensure adequate grounding.
2. Wire X1 with the Orange Intercontec 915 ytec from the RCE-710. Only pins 1, 2, 3 and 5 need to be wired.
Table 2.1—Orange Power Intercontec 915 ytec
Intercontec 915 Pin Out X1 Connector Pin Out Intercontec 915
(Orange Cable)
X1
Connector
A (U/L1) 1
B (V/L2) 3
C (W/L3) 2
Ground (PE) 5
3. Wire X3 for input power using a recommended 220V. The drive is programmed to accept both 220V and 120V,
though using 120V will limit performance.
Table 2.2—X3 Connector
X3 Connector Pin Out Power Cable X3
Connector
Ground 1
Line 2
Neutral 4
Jumper to 6 5
Jumper to 5 6
1
2
3
5
X1/X2
B-
F-
B+
F+
X3
1 2 3 4 5 6 7 8

Pinnacle Park • 1031 Goodworth Drive • Apex, NC 27539 • Tel: 919.772.0115 • Fax: 919.772.8259 • www.ati‑ia.com
S-5
RCE-710 Quick Start Guide Document #9640‑50‑1044‑02
4. Wire X21 for control and feedback signals:
a. Supply power to the motor. Wire the X21 digital signals as described in Table 2.3——X21 Connector.
b. Set RPM. Supply pin A1 with voltage between -10V and 10V. Supplying -10V corresponds to max speed
(15000 RPM) in the counter-clockwise direction, 0V is stopped, and 10V will result in the max speed (15000
RPM) in the clockwise direction. Reference Figure 2.2 for more detail.
NOTICE: Any voltage input on pin A1 between -.3V and .3V will result in no motion. This
deadband on the Set RPM input prevents unwanted motion due to signal oset or noise.
Table 2.3—X21 Connector
X21 Pin Out Pin Description Signal Type Voltage/Current
Limits
Digital Signals
B8 Axis Faulted 24V Digital
Output 30V/20mA
B7 Ready to Operate
A5 Enable/Disable Axis 24V Digital
Input
B4 Digital Signals
Ground Ground GND
RPM/Load Monitoring
B1 RPM Monitoring 10V Output 10V/1mA
B2 Analog Ground Ground GND
Set RPM
A1 Set RPM ±10V Input ±10V/1mA
B2 Analog Ground Ground GND
Safe Torque O
A11 STO-A-A1
Safe Digital
Input
ON: 17-30VDC, 5mA-
6mA
OFF: 0-5VDC, max
1mA
B11 STO-B-A1
Figure 2.2—RPM per Voltage Input
A1 B1
A11
B11
Voltage Input (V)
RPM
0510
-5
-10
0
-7500
-15000
7500
15000
-0.3 0.3
No Motion
Counter-clockwise Clockwise
-0.4V, 600 RPM 0.4V, 600 RPM

RCE-710 Quick Start Guide
Pinnacle Park • 1031 Goodworth Drive • Apex, NC 27539 • Tel: 919.772.0115 • Fax: 919.772.8259 • www.ati‑ia.com
S-6
Document #9640‑50‑1044‑02
5. Wire X23 with the green signal cable from the RCE-710 for hall sensor and thermal overload feedback.
Table 2.4—Green Signal Intercontec 615 ytec
Intercontec 615 Pin Out X23 Connector Pin Out Intercontec 615
(Green Cable)
X23
Connector
113
2 1
3 2
411
5 10
6 9
7 8
Note:
1. Pin 1 is located directly underneath alignment circle on top of connector.
6. Wire X10 connector for 24V I/O power.
Table 2.5—X10 Connector
X10 Connector Pin Out Power
Supply X10 Connector
+24VDC 1
Ground 2
7. Optional: Plug an ethernet cable in to X20 to control the drive through Kollmorgen’s WorkBench software. See
the Kollmorgen AKD2G manual for more information about connecting to and operating the servo drive through
WorkBench.
2
1
1
5
6
10
11
15

Pinnacle Park • 1031 Goodworth Drive • Apex, NC 27539 • Tel: 919.772.0115 • Fax: 919.772.8259 • www.ati‑ia.com
S-7
RCE-710 Quick Start Guide Document #9640‑50‑1044‑02
3. Motor Specications
Table 3.1—Motor Specications
Motor Name KBMS-10H02-C
Motor Type Rotary, Permanent Magnet
Continous Current 5.14 Arms
Peak Current 15.5 Arms
Coil Thermal Constant 7.176 mHz
Inductance (quad, I-I) 3.2 mH
Inductance (direct, I-I) 3.2 mH
Inductance Saturation 18000 Arms
Motor Poles 6
Motor Phase 0 deg
Inertia .249 kg*cm^2
Torque Constant .173 Nm/Arms
EMF Constant 10.46 Vrms/k-rpm
Motor Resistance (I-I) 1.77 Ohm
Maximum Voltage 240 Vrms
Maximum Speed117000 rpm
Notes:
1. AKD2G drive limits motor speed to 15000 RPM
2. For more information on the motor, refer to the Kollmorgen website.
Table of contents
Other ATI Technologies Tools manuals
Popular Tools manuals by other brands
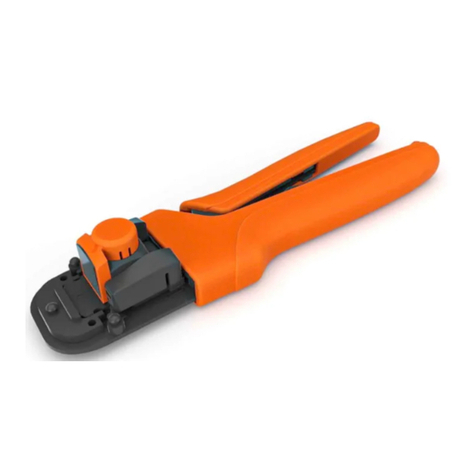
Samtec
Samtec CAT-HT-281-2430-11 instruction sheet
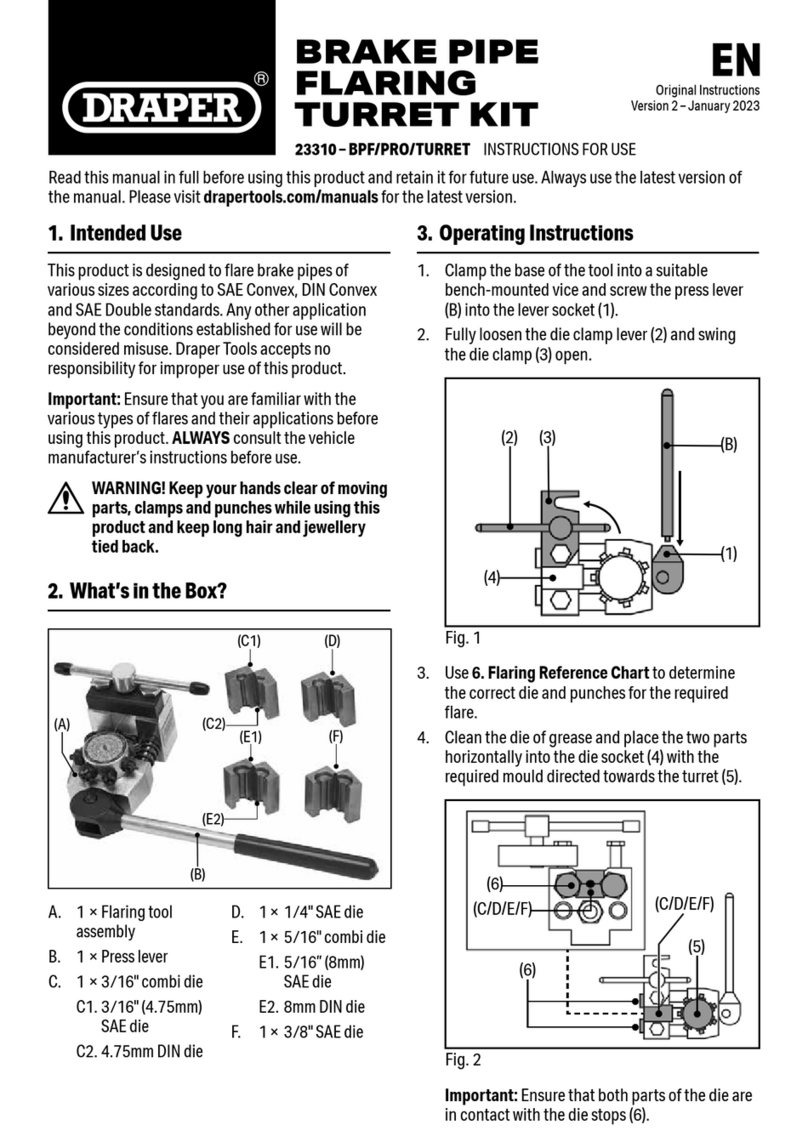
Draper
Draper 23310-BPF Original instructions
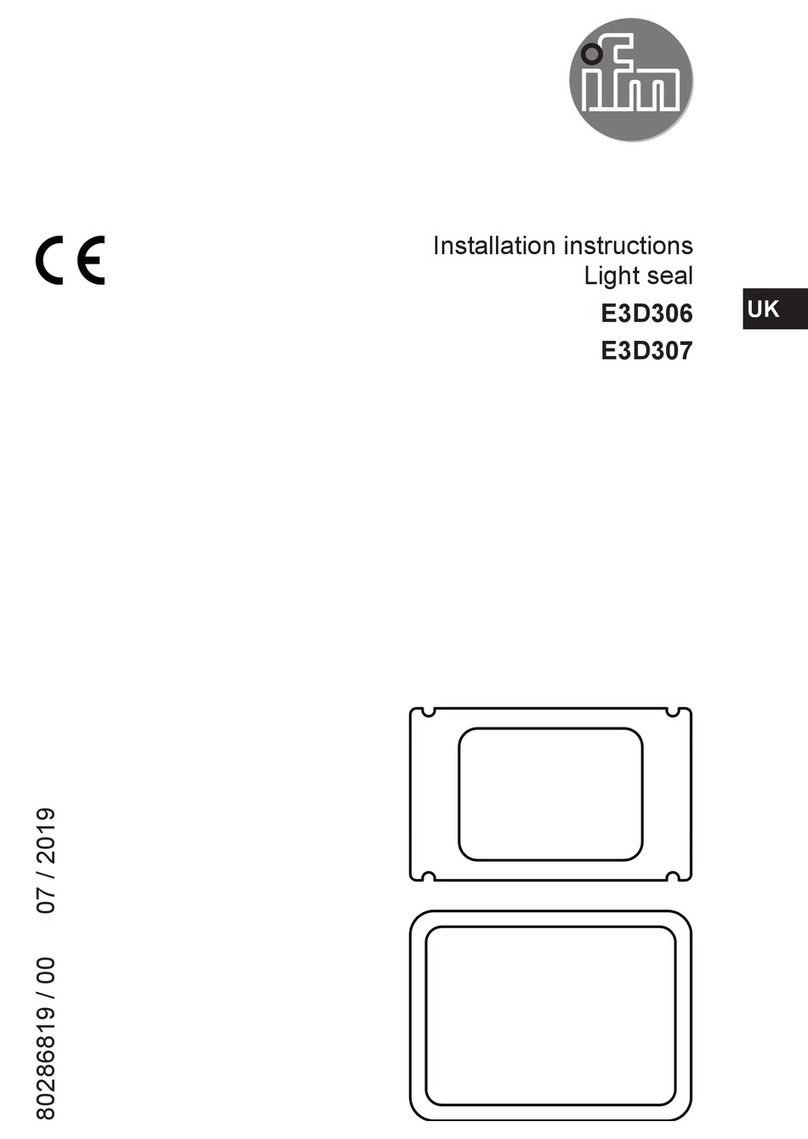
IFM
IFM E3D306 installation instructions

Chicago Pneumatic
Chicago Pneumatic B14A Operator's manual
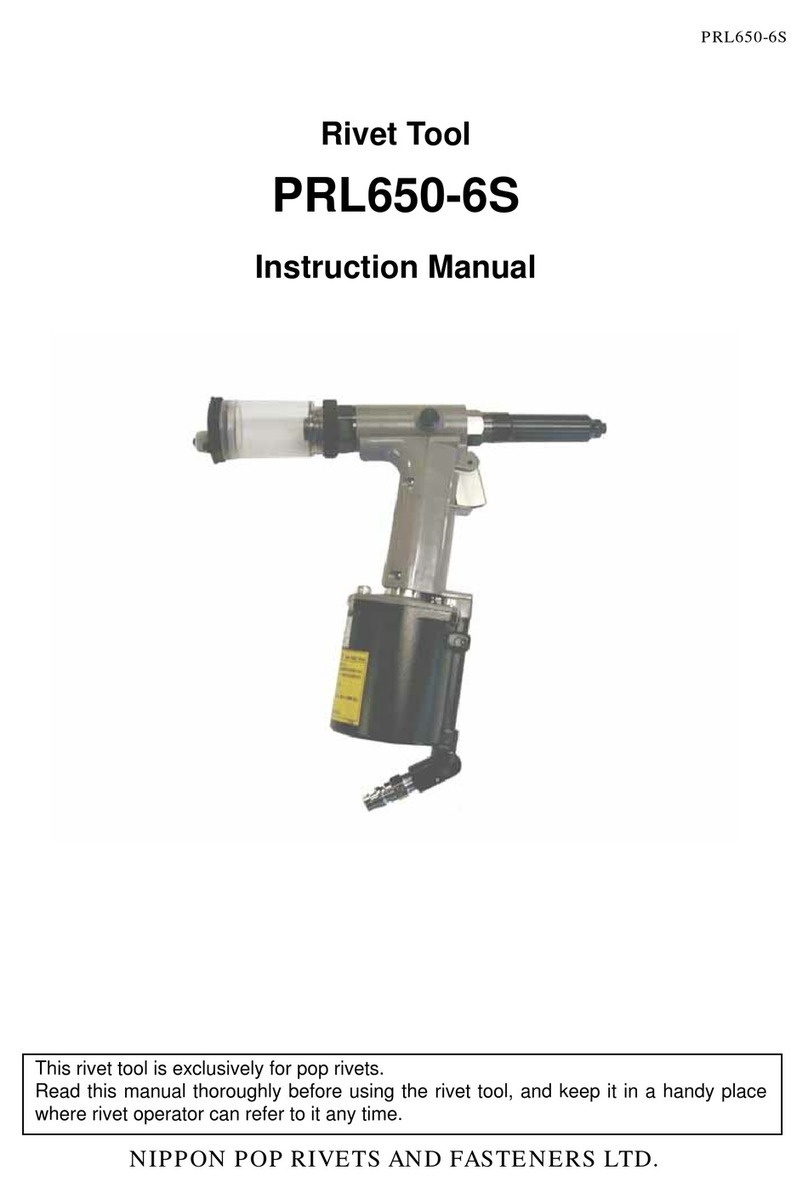
NIPPON POP RIVETS AND FASTENERS
NIPPON POP RIVETS AND FASTENERS PRL650-6S instruction manual
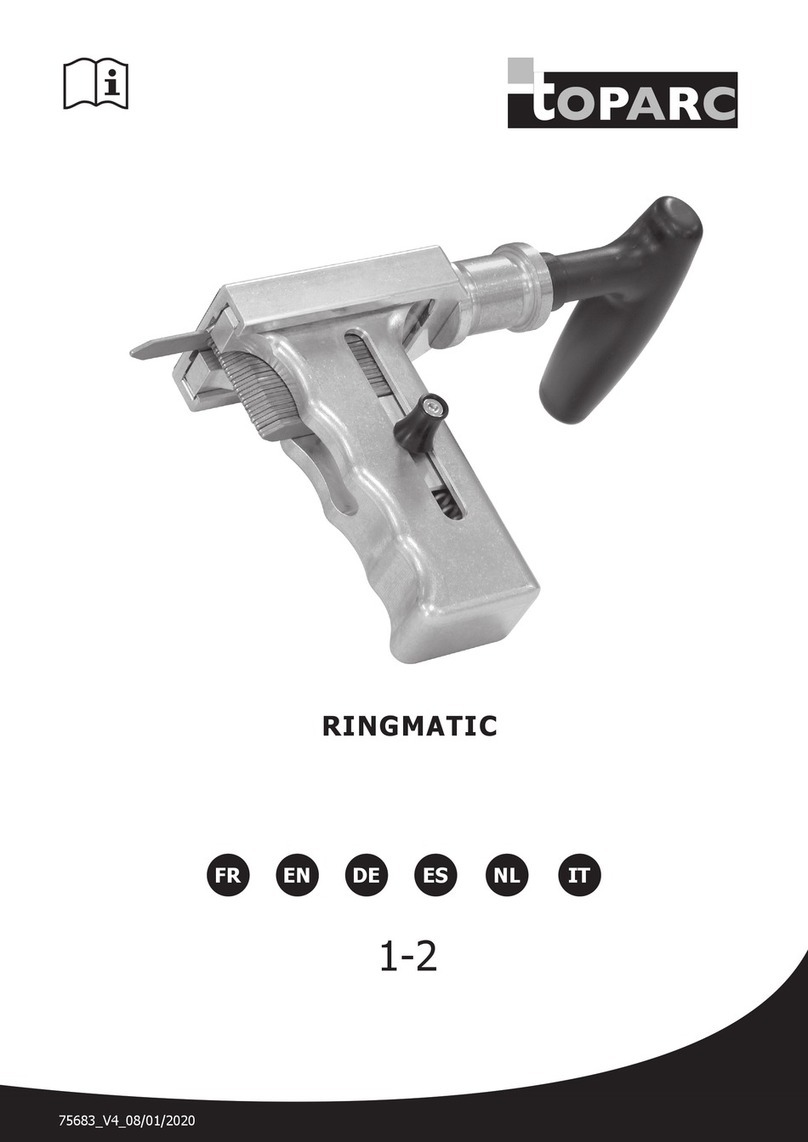
Toparc
Toparc RINGMATIC quick start guide