Atrump A1-3T User manual

1
A Series
CNC BED MILL
OPERATION
MANUAL

2
TABLE CONTENT
Page
3
Introduction
CH
A
PTER
1
Safety Precautions
---
-
---------
--------------
4
1.1 Regulations
---
-
---------
--------------
5
1.2 Safety Warning
---
-
---------
--------------
7
1.3
Moving
Instructions
---
-
---------
--------------
8
CHAPTER 2
Machine Specification
---
-
---------
--------------
9
2.1 Machine Dimension
---
-
---------
--------------
9
2.2 Main Parts Of Machine
---
-
---------
--------------
13
2.3 Machine Travels
---
-
---------
--------------
14
CHAPTER 3
Installation
---
-
---------
--------------
18
3.1
Precaution
---
-
---------
--------------
18
3.2
Machine Unwrapped
---
-
---------
--------------
18
3.3
Workplace Environment Factors
---
-
---------
--------------
19
3.4 Machine Leveling
---
-
---------
--------------
23
3.5 Power Installation
---
-
---------
--------------
24
Chapter 4 Maintenance
---
-
---------
--------------
25
4.1 Maintenance Schedule
---
-
---------
--------------
25
4.2
Lubr
icator system
---
-
---------
--------------
27
Chapter 5 Trouble Shooting
---
-
---------
--------------
28
5.1 Introduction&Precaution
---
-
---------
--------------
28
5.2
Machine Diagnosis
---
-
---------
--------------
29
5.3
Survey of the problems
---
-
---------
--------------
30
5.4
Help & Support
---
-
---------
--------------
31
5.5
Other Problems
---
-
---------
--------------
32
Appendix
Mill Head Operation Instruction (for 3T/5T model)
---
-
---------
--------------
34

3
Introduction
1、Before installing and operating your machine please read the manual
in detail.
2、This manual will teach you the installation, operation and basic
maintenance of the machine. It teaches you how to operate this machine
safelyand correctly.
3、It’s very important to understandeach label and machine warning label in
this manual.
4、About the programming, please read the introduction of controller
programming.
5
、About the operation of CNC control panel, setting up parameter and function,
please read the introduction of controller operation.
6. Please don't discard this manual, if lost please contact us for a replacement.

4
CHAPTER 1
Safety Precautions
**THIS MACHINE MUST NOT BE SERVICED, REPAIRED OR MAINTAINED BY
UNQUALIFIEDAND UNTRAINED PERSONNEL. **
This machine is equipped with a number of safety devices to protect personnel and
equipmentfrom injury and damage. Operatorsshould not, however,rely solely
upon these safety devices but should operate the machine after fully
understandingthe following paragraphs.
Moreover, improper operation and maintenance of any CNC machine increases the
likelihoodof serious personalinjuryand greatly reduces theservice life of this
machine.Yourattention to this manual,in combinationwith commonsense and good
machining practice, can positively affect productivitybyreducing downtime and
promotingsafe operation of this machine unless they are explicitlystated in this
instructionmanual.
Additionalsafetyconsiderations may be required for your particularapplication.
Please refer to safety informationfor additional informationand reference
publications.

5
1.1 Regulation:
1. Only qualified personnel are permitted to maintain and operate this machine.
2. Do not operate or attempt to repair the machine until you have read and
understood all manuals that pertain to the machine, plus all warning and
instructionplates/decals mountedon the machine.
3. Be mentally alert on the job and keepsafety in mind. Never attempt to operate
or repair a machine if you are under medicationor alcohol influence.
4. Wear safetyshoes and eye protection within the work area. Safety shoes should
be oil-resistant and safety glasses with side shields are stronglyrecommended.
5. Remove watches, jewelry andother accessoriesto avoid getting them caught in
movingparts.
6. Maintaina clean and orderly workspace around machine.
7. Store tools and miscellaneousparts properly. Be sure there are on articles
aroundthe machine.
8. Do not use compressed airs to blow chips form the machine spindle or table,
controls,cabinets,or the floor around the machine. Use a brush or chip scraper to
remove chips. Donot remove chips by handor while thespindle is turning. Make
sure that the cutter has completelystopped before attempting to remove chips.
Dispose of chips frequently.
09. Never start the machine when the cutter is in contact with the workplace. Make
sure the direction of spindle rotation is correct to prevent cutter breakage.
10. Know where all the EMERGENCYSTOP push buttons are located. Keep all
machine doors closed while the machine is in operation,including those on the
console and the electrical cabinets.
11. In the event of power failure, turn off main circuit breaker immediately.

6
12. Do not start the machine unless all units contain the proper amount and type of
hydraulic oils, lubricant or acceptable equivalents.
13. Fuses replacement should have the proper current ratings.
14. Do not change parameters, volumes and other electrical setting unnecessarily. If
such changes are unavoidable,record the values prior to any adjustments for future
reference.
15. Do not soil, scratch or remove the caution plate. Should it become illegible to
reador missing,order anothercaution plate form the supplier.
16. Wheneveroperating a forklift truck, crane or similar equipment,special care
should be taken to prevent collisions and damage to surroundings.
17. Do not leave machine unattended, but stand away while it is running.
18. Turnoff the powersource before leavingforthe day.

7
1.2 SafetyWarning
Be sure your installation conforms to applicable electrical codes. Inspect all electrical
connections before installing, operating or servicing machine. Be sure power supply
voltage matches machine voltage.
Disconnect all power to the machine before installing or servicing machine. Disconnect
all power before opening electrical or control box. Service should be only performed
by a qualified engineer.

8
1.3 MovingInstructions
1. Make sure when moving the machine that you have a support block from the
working table to the mill head, because the spindle head may shake while moving.
2. When transporting the machine using a crane or forklift make sure you have a
trained/certified personnel operating the forklift/crane. Make sure to move the
machine slowly and keep it balanced to avoid damage to machine or collision.

9
CHAPTER 2
Machine Specification
2.1 MachineDimension

10

11

12

13
2.2 The Main PartsOf Machine
No.
Des
c
ripti
o
n
QTY
1
Mill Head
1
2
Co
l
u
mn
1
3
T
able
1
4
Sa
d
dle
1
5
Base
1
6
Sp
i
ndle
1
7
E
l
ectr
i
cal
Box
1

14
2.3 Machine Travel:

15

16

17

18
CHAPTER
3
Installation
3.1 Precaution
1. Only trained and qualified workers should operate forklift trucks,
cranes or similar equipment and apply slings.
2. Use only wires of dimensions specified in the manual. They must be
strong enough to support machine weight.
3. Before hoisting the machine, fixed each unit securely.
4. Maintain a clean and orderly surrounding around the machine.
5. “POWER ON” on the control panel can be pressed onlyafter the complete
installation.
6. Be sure electrical cables and wires are not damaged during
installation.
7. After installation, proper capacity should be checked before
connection the wire to the power source.
8. Removing the anti-rusty oil by rags with paraffin or fuel oil before
operating. Toluene compounds must not be used.
9. Never leave the control boxes open while the power is on.Adeadly high
voltage is present which can cause serious injury.
3. 2 Machine unwrapped:
1.Remove support blocks from the mill head, column (for counterweight), tool
changer and axes travel cover.
2.Inspect all piping is connected, including the tank's water pipes
3.Check all limit switches and stop blocks are not loose
4.Check whether the sheet metal door is installed properly.

19
3.3 Workplace Environment Factors
1. Avoid exposure to direct sunlight and/or near a heat source, etc.Room
temperature during operation should be 0 through 40℃
2. Avoid installing machines in a location where the humidity
fluctuates considerably and/or highly humid.
3. Avoid installing machines in a dusty, misty location.
4. Install machines where there is no vibration sources in surroundings areas.
5.Install machines in a flat and smooth surface and make sure the area is clean.
The minimum bearing pressure of the floor is 5000 ㎏/㎝²
6.The machine must be protected from electrical waves, such as electric
welders and an electric discharge machine (EDM).
7. Always ground machine independently. The ground resistance should be
100 ohms or less and the length of ground cable should be as short as
possible.
8. The noise level at the operator’s position should be under 85 dbA.
9. Make sure that the site is large enough to accommodate the machine, refer
to the machine's brochure for maximum floor space size chart. Machine floor
Space required for each model, please refer to following drawings.

20
This manual suits for next models
4
Table of contents
Other Atrump Power Tools manuals
Popular Power Tools manuals by other brands
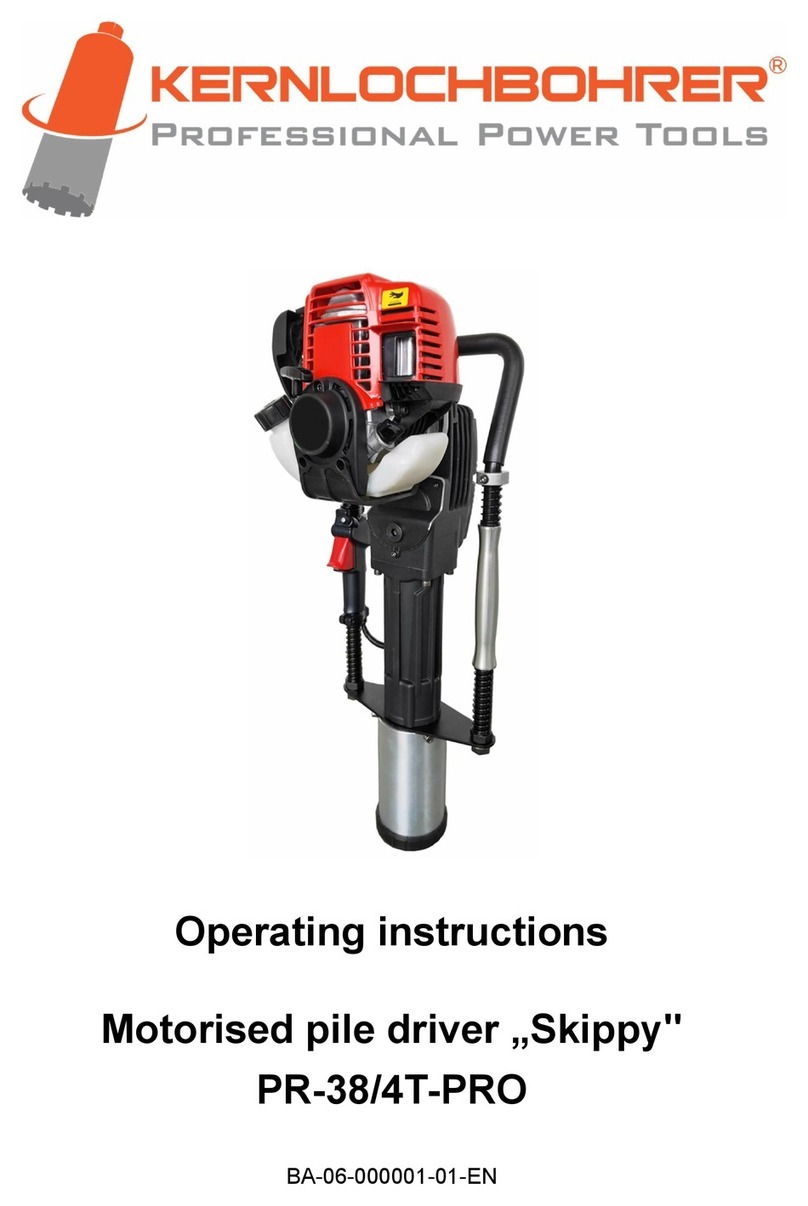
Kernlochbohrer
Kernlochbohrer Skippy operating instructions

YATO
YATO YT-82273 Original instructions
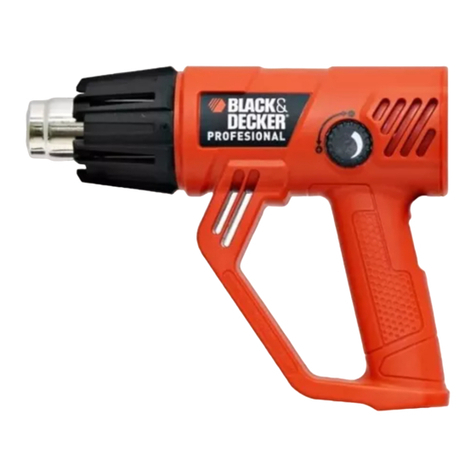
Black & Decker
Black & Decker HG2000 instruction manual

Westfalia
Westfalia 94 60 30 Original instructions
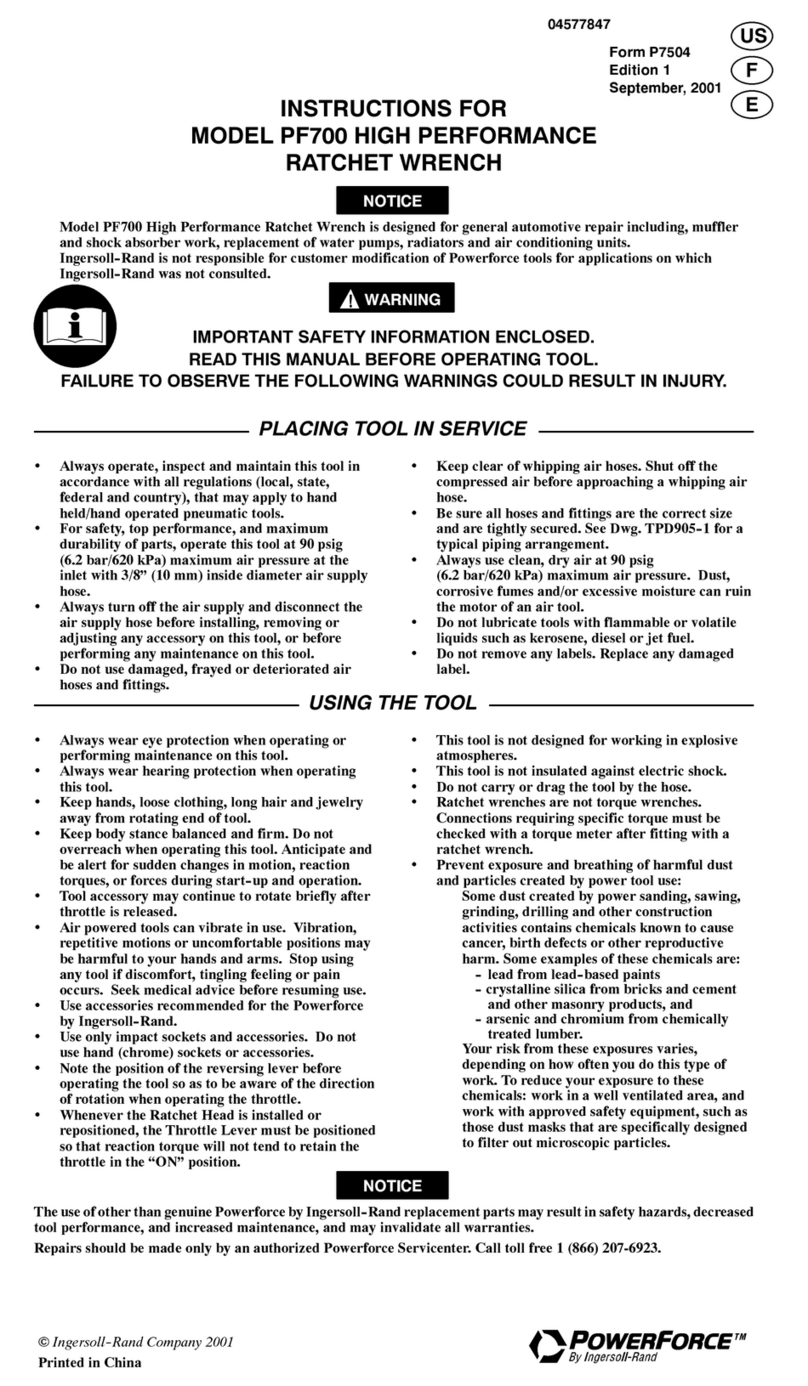
Ingersoll-Rand
Ingersoll-Rand PowerForce PF700 instructions
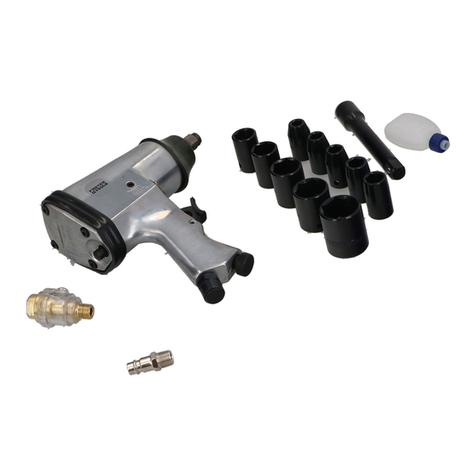
FASTER TOOLS
FASTER TOOLS 651 instruction manual