Autotrol Magnum Cv 942 Manual

Installation and Service Manual
Magnum Cv and Magnum IT Valves


Table of Contents
Section
1.0 Installation Profile Summary - - - - - - - - - - - - - - - - - - - - - - - - - - - 1
2.0 Introduction to the Magnum Cv and Magnum IT Series - - - - - - - - - - - - - - - 2
2.1 Assembling the Control to the Valve - - - - - - - - - - - - - - - - - - - - 3
2.2 General Specifications - - - - - - - - - - - - - - - - - - - - - - - - - - 7
2.3 Dimensional Specifications - - - - - - - - - - - - - - - - - - - - - - - - 8
3.0 General Installation Information - - - - - - - - - - - - - - - - - - - - - - - - - 10
3.1 Typical Installation Drawings - - - - - - - - - - - - - - - - - - - - - - - 12
4.0 Flow Diagrams - - - - - - - - - - - - - - - - - - - - - - - - - - - - - - - - 13
5.0 Control Settings - - - - - - - - - - - - - - - - - - - - - - - - - - - - - - - - 19
5.1 Manual Control - - - - - - - - - - - - - - - - - - - - - - - - - - - - - 19
5.2 Mechanical Control - - - - - - - - - - - - - - - - - - - - - - - - - - - 24
5.2.1 Common Settings - - - - - - - - - - - - - - - - - - - - - - - 24
5.2.2 Regenerating Iron Filter - - - - - - - - - - - - - - - - - - - - - 25
5.2.3 Backwashing Filter - - - - - - - - - - - - - - - - - - - - - - - 25
5.2.4 Salt Use Table - - - - - - - - - - - - - - - - - - - - - - - - - 26
5.2.5 Potassium Permanganate Use Table- - - - - - - - - - - - - - - 27
5.3 Impulse Controls - - - - - - - - - - - - - - - - - - - - - - - - - - - - 28
5.4 Electronic Controls- - - - - - - - - - - - - - - - - - - - - - - - - - - - 29
5.4.1 Connecting the 962 Control- - - - - - - - - - - - - - - - - - - 31
5.4.2 Connecting the 962M and the 962S Control - - - - - - - - - - - 32
5.4.3 Connecting the 962 Twin and Triple Parallel Control- - - - - - - - 33
6.0 Programming Tables for Electronic Controls - - - - - - - - - - - - - - - - - - - 34
6.1 Table I - Level I Values - - - - - - - - - - - - - - - - - - - - - - - - - - 34
6.2 Table IIA - Level II Program Values 962 Single Twin or Triple Parallel
Tank Softener or Dealkalizer - - - - - - - - - - - - - - - - - - - - - - - 35
6.3 Table IIB - Level II Program Values 962F
Single Tank Filter Mode Parameters - - - - - - - - - - - - - - - - - - - 36
6.4 Table IIC - Level II Program Values 962 Twin Tank Alternating
Softener - - - - - - - - - - - - - - - - - - - - - - - - - - - - - - - - 37
6.5 Table IID - Level II Program Values - Electronic Timeclock
Filter - - - - - - - - - - - - - - - - - - - - - - - - - - - - - - - - - 38
6.6 Table IIE - Level II Program Values - Electronic Timeclock
Softener - - - - - - - - - - - - - - - - - - - - - - - - - - - - - - - 39
6.7 Explanation of Parameter Values for the 962 Single and Parallel
Tank Controls - - - - - - - - - - - - - - - - - - - - - - - - - - - - - - - - 40
6.8 New Features in the 962 Family Controls - - - - - - - - - - - - - - - - - 42
6.9 Table III Historical Data - - - - - - - - - - - - - - - - - - - - - - - - - 43
6.10 Table IV Error Messages - - - - - - - - - - - - - - - - - - - - - - - - 44

7.0 Multi-Tank Systems - - - - - - - - - - - - - - - - - - - - - - - - - - - - - - 45
7.1 Twin Alternating - - - - - - - - - - - - - - - - - - - - - - - - - - - - - 45
7.1.1 Control Set-up - - - - - - - - - - - - - - - - - - - - - - - - - 46
7.1.2 Additional Checks - - - - - - - - - - - - - - - - - - - - - - - 47
7.2 Twin and Triple Parallel - - - - - - - - - - - - - - - - - - - - - - - - - 48
7.2.1 Control Set-up - - - - - - - - - - - - - - - - - - - - - - - - - 50
8.0 Start-Up Procedure - - - - - - - - - - - - - - - - - - - - - - - - - - - - - - 51
9.0 Service Instructions - - - - - - - - - - - - - - - - - - - - - - - - - - - - - - 52
9.1 Magnum Valve Cartridge Removal Procedure - - - - - - - - - - - - - - - 54
10.0 Performance Data - - - - - - - - - - - - - - - - - - - - - - - - - - - - - - 55
10.1 Injector Data- - - - - - - - - - - - - - - - - - - - - - - - - - - - - - 55
10.2 Refill Control Chart (P6 Values) - - - - - - - - - - - - - - - - - - - - - 57
10.3 Injector Chart (P7 Values) - - - - - - - - - - - - - - - - - - - - - - - - 58
10.4 Drain Line Flow Control Chart - - - - - - - - - - - - - - - - - - - - - - 59
10.5 Autotrol Drain Line Flow Controls (5 gpm - 40 gpm)- - - - - - - - - - - - 60
11.0 Wiring Diagrams - - - - - - - - - - - - - - - - - - - - - - - - - - - - - - - 61
11.1 962 Series Remote Start - - - - - - - - - - - - - - - - - - - - - - - - 61
11.2 952 Impulse - - - - - - - - - - - - - - - - - - - - - - - - - - - - - - 62
11.3 952 QC Impulse - - - - - - - - - - - - - - - - - - - - - - - - - - - - 62
11.4 962 Twin and Triple Parallel - - - - - - - - - - - - - - - - - - - - - - - 63
11.5 962 Twin Alternating - - - - - - - - - - - - - - - - - - - - - - - - - - 64
12.0 Assembly Drawings and Parts Lists - - - - - - - - - - - - - - - - - - - - - - 65
12.1 942Man and 942FMan Manual Controls - - - - - - - - - - - - - - - - - 65
12.2 942 and 942F Timeclock Controls - - - - - - - - - - - - - - - - - - - - 66
12.3 952,952F, and 952QC Impulse Controls - - - - - - - - - - - - - - - - - 67
12.4 962, 962F, 962TC, 962FTC, 962M, and 962S Electronic Controls - - - - - 69
12.5 Injector Assemblies - - - - - - - - - - - - - - - - - - - - - - - - - - 72
12.6 Refill Control Assemblies - - - - - - - - - - - - - - - - - - - - - - - - 73
12.7 2-inch Turbine Assembly - - - - - - - - - - - - - - - - - - - - - - - - 74
12.8 Installation Adapters - - - - - - - - - - - - - - - - - - - - - - - - - - 75
12.9 Valve Cartridges - - - - - - - - - - - - - - - - - - - - - - - - - - - - 77
12.10 Cam and Pilot Valve Assemblies - - - - - - - - - - - - - - - - - - - - 78
12.11 Kits and Assemblies - - - - - - - - - - - - - - - - - - - - - - - - - - 80
12.12 962 Optional Switch Kits Available - - - - - - - - - - - - - - - - - - - 81

1
1.0 Installation Profile Summary
Installation Date: ______________________________
Installation Location: ___________________________
Installer(s): ____________________________________
Phone Number:________________________________
Valve Number:_________________________________
Application Type: (Softener) (Filter) (Dealkalizer)
Water Source:
(Public Well) (Private Well)
(Surface Supply)
(Other)
Water Test Results:
Hardness:_______________ Iron:_______________
Other: ________________________________________
Misc:
Capacity: _______ Flow Rates:______ min. ____ max.
Tank Size: Diameter ________ Height: __________
Resin or Media Volume:_________________________
Resin or Media Type: ___________________________
Brine Tank Volume:_____________________________
Salt Setting per Regeneration: ___________________
Control Valve Configuration:
Valve Type:____________________________________
(Hard Water Bypass) (No Hard Water Bypass)
Refill Control:______________________________ gpm
Injector Control: ___________________________ gpm
Backwash Control: _________________________ gpm
Manual Control:
(Softener) (Filter)
Mechanical Timeclock:
(7 day) (12 day)
Salt Setting: __________________________________
Regeneration Frequency:
SM T W T F S
123456789101112
______________________________________________
______________________________________________
Impulse
(480) (Other) ___________________________________
Salt Setting:____________________________________
Electronic Demand Settings
P1 Time of Day _________________
P2 Time of Day Regen _________________
P3 Hardness of Water _________________
P4 Salt Amount _________________
P5 Capacity of Unit _________________
P6 Refill Control Value _________________
P7 Brine Draw Value _________________
P9 Backwash Time _________________
P10 Slow Rinse Time _________________
P11 Fast Rinse Time _________________
P12 Units of Measure _________________
P13 Clock Mode _________________
P14 Calendar Override _________________
P15 Reserve Type _________________
P16 Fixed Reserve Cap.
or Initial Ave. Value _________________
P17 Operation Type _________________
P18 Salt Change Lock Out _________________
P19 Flow Sensor Size _________________
P20 K-Factor or Pulse
Equivalent _________________
P21 Remote Regeneration
Switch Delay _________________
P22 Factory Use Only _________________
Twin Parallel Triple Parallel
Regeneration Type (P15): ___________
3 = Fixed Reserve with
Immediate Regeneration
Fixed Reserve (P16):____________% (0% only)
Twin Alternating
Regeneration Type (P15): ___________
0 = Immediate Regen
1 = Delayed Regen
Fixed Reserve (P16): _____________ %

2
2.0 Introduction to the Magnum Cv and Magnum IT Series
The Magnum CvTM and Magnum ITTM Series valves
offer a high degree of installation simplicity and
flexibility.
Figure 2.1 provides an overview of the major
components and connections of the 2-inch
(5.08-cm) Magnum IT valve.
The Magnum valve is available in either a
1-1/2-inch (3.81-cm) (Magnum CvTM) or a 2-inch
(5.08-cm) (Magnum IT™) configuration. Throughout
this manual, the 2-inch (5.08-cm) Magnum Cv is shown
in illustrations where the model type is irrelevant to
what is being demonstrated.
Figure 2.1
Magnum IT Series Valve
TM
InternalTurbine
Assembly

3
2.1 Assembling the Control to the
Magnum Valve
The control and the Magnum valve work together as an
integral system to ensure synchronization. Follow the
steps outlined below to install the control on the
Magnum valve.
Remove Cam Cover
Remove the cam cover by pressing in on the cover
release tabs (Figure 2.2). Note the cover locking tab
and the slot in the top plate. When you reassemble the
cover, the locking tab is placed in the slot first and the
cover lowered into position.
Figure 2.2
Align Camshaft
The camshaft is keyed and should only be engaged or
disengaged when in the position illustrated (Figure 2.3).
If the camshaft is not in the proper position, rotate the
cam assembly counterclockwise until the camshaft
arrow aligns with pillow block arrow.
Figure 2.3
Slide Camshaft
Slide the camshaft toward the back of the valve by
pressing on the release tab and pulling on the back end
of the camshaft (Figure 2.4). The front end of the
camshaft will be flush with the mounting plate.
Figure 2.4
Mount Control
Mount the control onto the valve by sliding the
mounting tabs over the mounting plate. Note that all
models of Magnum controls mount to the valve in the
same manner (Figure 2.5).
Figure 2.5
Engage Assembly
Engage the control by pressing on the release tab and
pushing the camshaft into the control (Figure 2.6). Do
not force the camshaft. If the camshaft does not slide
freely into the control, check the alignment of the
camshaft to ensure it is in the proper position
(Figure 2.3). The control indicator must be in the
REGENERATION COMPLETE position for the 942,
942Man, 952, and 962 when engaging the camshaft
into the control. The control indicator must be in the
BACKWASH COMPLETE position for the 942F,
942FMan 952F, and 962F when engaging the camshaft
Cover Release Tabs
Locking Tab and Slot
Camshaft Arrow Pillow Block Arrow
Release Tabs
Mounting Plate
Mounting Tabs

4
into the control. The control indicator must be in the
midpoint of the SERVICE position for the 962M and
962S when engaging the camshaft into the control.
Figure 2.6
Important:
When 942, 942Man, 952, or 962 controls are installed,
control dials must be in the REGENERATION
COMPLETE position.
When 942F, 942FMan, or 952F controls are installed,
control dials must be in the BACKWASH COMPLETE
position.
When 962M or 962S controls are installed, control dials
must be in the SERVICE position.
To disassemble the control from the valve, reverse the
assembling procedure.
Inlet, Outlet and Drain Connections
The inlet, outlet, and drain connections are designed to
accept an GE Osmonics supplied CPVC or brass
adapter (Figure 2.7). The adapters provide a convenient
union for the three connection ports on the valve. In
addition, they incorporate a positive O-ring face seal
for ease of installation and leak free operation. DO NOT
OVERTIGHTEN THE ADAPTERS. As a general
guideline, hand tightening the nut onto the valve will be
adequate. If additional tightening is required, never
exceed a quarter turn beyond the hand tight position.
The outlet of the 2-inch Magnum IT has an integrated
turbine. The turbine measures the flow of water through
the outlet. This information is used by the control to
determine the best time to recycle.
Figure 2.7
No Hardwater Bypass Feature
The Magnum control valve may be configured for “Hard
Water Bypass” or “No Hard Water Bypass”. With Hard
Water Bypass, unsoftened or unfiltered water is
allowed to bypass the Magnum control valve during
regeneration or backwash. With No Hard Water
Bypass, a valve cartridge ensures that no unsoftened
or unfiltered water bypasses the valve during
regeneration or backwash.
It is easy to observe which option is installed in the
valve. Note that the Hard Water Bypass End Cap has
much longer standoffs than the No Hard Water Bypass
cartridge. The No Hard Water Bypass assembly will
look identical to the other three valve cartridges on the
valve and will have a label identifying the cartridge
assembly (Figure 2.8).
Figure 2.8
Release Tab and
Camshaft
Normal Standoffs
No Hard Water Bypass
No Unfiltered Water Bypass
Extended Standoffs
With Hard Water Bypass
End Cap

5
Hydraulic Output Signal
An optional hydraulic output signal is available on the
valve. An optional cam lobe on pilot valve #6 is used on
the camshaft assembly to initiate the hydraulic output
signal during regeneration or backwash (Figure 2.9).
The hydraulic line pressure signal will be available
through the 1/4-inch connection on the back of the
valve marked “AUX”. (Remove the tube cap installed
for shipping.)
Optional cam lobes available are:
P/N 1000554 Provides a hydraulic signal from the
beginning of BACKWASH through the
start of REFILL.
P/N 1000553 Provides a hydraulic signal from the
beginning of BACKWASH through the
end of REFILL.
P/N 1001622 Used on Twin Alternating Systems
Only. Provides a hydraulic signal from
the beginning of BACKWASH through
and during STANDBY.
P/N 1041064 Breakaway cam. Can be programmed
to send a hydraulic signal at any time
during the REGENERATION or
BACKWASH cycle. Note: The camshaft
must be turning for the signal to change
states, i.e. switch from OFF to ON, or
from ON to OFF.
Figure 2.9
Figure 2.10
Magnum Tank Adapter
The tank adapter on the control valve is designed to be
compatible with a 4 inch-8UN (8 threads per inch) tank
opening. In addition, the adapter is designed to accept
a full 1-1/2-inch (3.81-cm) riser pipe with outside
diameter of 1.90 to 1.91 inches (48.26 to 48.51 mm)
(Figure 2.11). The riser pipe is sealed by an O-ring on
the inside of the tank adapter, Figure 2.11. It is
recommended that the riser pipe extend beyond the
top of the tank by 1/4 inch ± 3/8 inch (6 mm ± 9 mm).
Figure 2.11
Optional Switch Assembly
On single, twin parallel, and triple parallel tank
configurations, a single optional feedback switch kit is
available to provide an electrical signal during the
entire regeneration or backwash cycle (Figure 2.12).
The switch may be wired in the “Normally Open” or
“Normally Closed” position and is rated for 0.1 amp at
125 volts AC. An optional 5.0 amp switch at 1/10 HP
125/250 volts AC is available upon request.
Optional Cam
Lobe Position #6
“Hydraulic Output
For hydraulic output signal
install one of following cam
lobes:
1000553
1000554
1001622
1041064
Signal”
Auxiliary
Hydraulic
Output Port
Pilot Drain Port
“AUX”
.375" (9.52 mm)
0.8125"
(20.64 mm)
O-ring
Top of Tank
O-ring
Riser O-ring
Tank O-ring

6
Figure 2.12
On ALL Magnum tank configurations, optional multi-
switch kits are available to provide additional electrical
or switch closure signals during the regeneration or
backwash cycles. Coupled with the optional
breakaway cams, signals can be sent to external
system equipment at virtually any time while the
control/camshaft motor is running. Consult the
instruction sheet covering the multi-switch option for
additional application and programming information.
The instruction sheet is sent with the switch kit.
Normally Closed
Normally Open
Common

7
2.2 Magnum General Specifications
Operating and Environmental
Operating Pressure ............................................................................................... 25 to 125 psig (172 to 862 kPa)
100 psig (688kPa) maximum in Canada
Operating Water Temperature Range................................................................................. 34 to 100oF (1 to 36oC)
Ambient Temperature Range.............................................................................................. 34 to 120oF (1 to 50oC)
Cap Bolt Torque ...................................................................................................35-40 inch lbs. (3.95 to 4.51 Nm)
Connections
Inlet and Outlet................................................................................................................... 1-1/2 inch-Magnum Cv
2-inch-Magnum IT
Tank ....................................................................................................................................................... 4-inch-8UN
Brine ....................................................................................................................................................3/4-inch NPT
Pilot Drain and Auxiliary Hydraulic Out .................................................................................... 1/4-inch tube fitting
Riser Pipe Fitting .....................................................................................................................1-1/2-inch (3.81-cm)
Drain ........................................................................................................................................1-1/2-inch (3.81-cm)
Physical
Dimensions..................................................................................................... Refer to drawings on pages 8 and 9
Approximate Weight (Valve and Control).................................................................................... 23.3 lbs. (10.6 kg.)
Electrical*
Voltage - 962 Series Control .......................................................................... 12 VAC wall mount transformer only
Voltage - 942 Series Control ..................................................................120 VAC, 12 VAC wall mount transformer
Voltage - 952 Series Control ........................................................................................................24 VAC, 120 VAC
Power Draw........................................................................................................................................4.5 volt-amps
*See section on Electronic Controls for alternative electrical configurations.

8
2.3 Magnum Cv Dimensional Specifications
1 1/2-inch Inlet, Outlet and Drain
3.993 (10.14 cm)
6.493 (16.5 cm)
7.500 (19.05 cm)
22.796 (57.90 cm)
2.817 (7.15 cm)
4.018 (10.20 cm)
8.680 (22.04 cm)
9.000 (22.86 cm)
13.481 (34.24 cm)
19.500 (49.53 cm)
7.000 (17.78 cm)
14.000 (35.56 cm) 15.539 (39.47 cm)
1.113 (2.82 cm)
11.471 (29.13 cm)

9
Magnum IT Dimensional Specifications
2-Inch Inlet and Outlet, 1 1/2-Inch Drain
15.539
1.113
11.376
4.429
13.481
9.000
9.750
7.000 6.500
16.250
8.710
3.998
2.817
27.224
4.500 4.500
13.993
4.429

10
3.0 General Installation Information
Please review the following items thoroughly to ensure
an efficient and safe installation of the water treatment
system. Page 12 shows typical installation line
drawings for the Magnum valves.
Operating Conditions - A minimum dynamic
operating water pressure of 25 psig (172 kPa) is
required for the Magnum control valve to
operate properly. Water pressure is not to exceed
125 psig (862 kPa). In Canada, water pressure is not to
exceed 100 psig (688 kPa). Water temperature is not to
exceed 100oF (36oC). Do not subject the valve to
freezing conditions.
Space Requirements - Allow adequate space for the
water treatment system and associated piping. The
General Specifications section (pages 7-9) provides
the overall dimensions of the control valve as well as
the dimensional reference information for each of the
connection ports. A minimum of 4 1/2 inches (11.5 cm)
front and rear clearance is required for cartridge
assembly and removal.
Plumbing - Always follow good plumbing practices
and conform to local codes. Check existing pipes for
lime and/or iron buildup. Replace piping if heavy
buildup exists and initiate the proper treatment to
prevent additional occurrences. Locate the equipment
close to a drain that is capable of handling the
maximum drain flow rate during backwash.
Flexible Connectors - Some tanks expand and
contract over the acceptable range of operating water
pressures of the Magnum control valve. The use of
flexible connectors is recommended on polywound or
fiberglass tank installations of 24-inch (60.96-cm)
diameter and larger. Follow the tank manufacturer’s
instructions for more information.
Inlet and Outlet Piping - Inlet and outlet plumbing
should be adequately supported to avoid excessive
loads on the valve. Install a manual bypass system to
provide for occasions when the water conditioner must
be bypassed for servicing.
Drain LIne Piping - To prevent mineral loss during
backwash, and to ensure proper operation of the
Magnum Cv Series control valve, A DRAIN LINE
FLOW CONTROL must be plumbed into the drain line
prior to placing the valve in the service mode. Flow
controls from 5 to 40 gpm (18.92 to 151.4 Lpm) are
available from GE Osmonics and can be easily installed
in the drain line (Figure 3.1). Flow controls greater than
40 gpm (151.4 Lpm) must be plumbed externally.
Selection of the proper drain line flow control will
depend on the tank size and media used for the
installation. See Table 10.3.
The following general drain line piping guidelines
should be observed:
•1 inch (2.54 cm) or larger piping
•Should not exceed 20 feet (6.1 m)
•Should not be elevated higher than the control
valve
•No shut-off valves should be installed in drain line
•Minimal number of elbows and fittings should be
installed in drain line
•Piping must be self-supporting
•Install air gap to provide a siphon break
•Flow control should be installed as close to the
Magnum Cv Series control valve as possible if an
external flow control is used.
Figure 3.1
Brining System - The Magnum control valve utilizes
timed water refill to add water to the salt tank. A refill
tube with check ball is required in the brine tank that will
not restrict the refill or brine draw flow rate capabilities
of the valve. Although not required, a separate brine
valve (safety float) system is recommended for use with
Magnum installations. Select a “High-Flow” brine valve
that will not restrict the refill or brine draw flow rate
capabilities of the valve. The “Performance Data and
Charts” section (Section 10.0) of this manual contains
flow rate information for various size injectors and refill
controllers.
Pilot Drain - During regeneration, a small amount of
water (200 ml or 1 cup) is discharged from the 1/4-inch
(6.3-mm) tube fitting on the back of the valve marked
DRAIN (Figure 3.2). To prevent this water from being
discharged to the floor, plumb this connection to a non-
pressurized drain or to the brine tank. Do not plug or
apply back pressure to the pilot drain at any time.
Crimping the pilot drain line or installing the line to go
up, which causes backpressure, will prevent the
diaphragm cartridges from shifting properly through
the cycles of regeneration or backwash.
Drain Line Flow Control Disk

11
Figure 3.2
Electrical
1. Electrical requirements for the installation will
depend on the configuration of the control.
2. The standard North American Series 962 electronic
control is supplied with a 12 volt wall mount
transformer. Optional wall mount transformers are
available in the following configurations: Japanese
plug @ 100 volts/50 or 60 Hz, Australian/Argentine
plug @ 240 volts/50 Hz, British plug @ 240 volts/50
Hz, European/Italian plug @ 230 volts/50 Hz.
Optional transformers must be ordered separately
for all international 12 VAC configurations.
3. The standard North American Series 952 impulse
controls use 120 VAC or 24 VAC/50 or 60 Hz power.
Lubricants
It is very important that 100% silicone lubricant is the
only lubricant used for installing the Magnum control
valve. Any other lubricant may cause material
degradation and potential failure of the valve
components.
NOTE: Some silicone based lubricants contain
petroleum-based ingredients. If there is a question
about the lubrication that you are using contact the
manufacturer of that lubricant.
Auxiliary Hydraulic
Output Port - Plugged
Pilot Drain Port

12
3.1 Typical Installation Drawings
Figure 3.3 Magnum Cv and Magnum IT, Single Tank Softener Units with 962 Electronic Control
Inlet Valve
Drain
962 Control
1.5” Riser Tube
Hub & Lateral
Brine Tank
Brine Line
Turbine (standard
with 962 Control)
Outlet Valve
Manual Bypass Valve
Drain Line Flow Control
Note: Support Inlet and
Outlet Piping
Adequately.
(Required)
Magnum Cv
Magnum IT

13
4.0 Flow Diagrams
The Magnum control valve utilizes a series of pilot
valves to properly position the diaphragm valve
cartridges (Figure 4.1). The pilot valves are activated by
the camshaft (Figure 4.2). The flow diagrams that follow
represent the Service Cycle for a 5-cycle softener,
3-cycle filter, and 5-cycle twin alternating softener
configuration. Both the Hardwater Bypass and No
Hardwater Bypass service flow diagrams are
presented.
Figure 4.1 Pilot Valve Principle of Operation
Figure 4.2 Cam Assembly

14
B1B2
12
3
4
56
Pressure
Regulator
Pilot
Screen
Refill
Control
Brine
Tank
Untreated
Water
Treated
Water
Injector
Pilot
Valves
Inlet
Tank Top
Drain
1
Tank Bottom
Outlet
2
Backwash
Water
Regenerant
M
agnum
Aux. Pilot
Output Injector
Screen
Service Cycle
5 Cycle - Co-current - Hard Water Bypass - Softener
Resin Tank
4
3
Pilot Drain
Hard Water
Bypass
654321B2B1
Service
Backwash
Brine/Slow Rinse
Fast Rinse
Refill/Service
OPEN OPEN OPENCLSD CLSDCLSDCLSD
OPEN OPEN CLSDCLSDOPEN CLSD CLSD
OPEN OPEN
CLSDCLSD
OPENOPENOPEN CLSD CLSD
OPEN OPEN OPEN OPENCLSD
OPEN OPENCLSD OPEN OPENOPEN
CLSD
CLSD
CLSD
CLSD
CLSD CLSD

15
B1B2
12
3
4
56
Pressure
Regulator
Pilot
Screen
Refill
Control
Brine
Tank
Untreated
Water
Treated
Water
Injector
Pilot
Valves
Inlet
Tank Top
Drain
1
Tank Bottom
Outlet
2
Backwash
Water
Regenerant
M
agnum
Aux. Pilot
Output Injector
Screen
Service Cycle
5 Cycle - Co-current - No Hard Water Bypass - Softener
Resin Tank
4
3
Pilot Drain
No Hard
Water Bypass
654321B2B1
Service
Backwash
Brine/Slow Rinse
Fast Rinse
Refill/Service
OPEN OPEN OPENCLSD CLSDCLSDCLSD
OPEN OPEN CLSDCLSDOPEN CLSD CLSD
OPEN OPEN
CLSDCLSD
OPENOPENOPEN CLSD CLSD
OPEN OPEN OPEN OPENCLSD
OPEN OPENCLSD OPEN OPENOPEN
CLSD
CLSD
CLSD
CLSD
CLSD CLSD

16
B1B2
12
3
4
56
Pressure
Regulator
Pilot
Screen
Untreated
Water
Treated
Water
Plugged Injector
Pilot
Valves
Inlet
Tank Top
Drain
1
Tank Bottom
Outlet
2
Backwash
Water
Regenerant
M
agnum
Aux. Pilot
Output
Service Cyc
leService Cycle
3 Cycle - Unfiltered Water Bypass - Filter
Media Tank
4
3
Pilot Drain
Unfiltered
Water Bypass
654321B2B1
Service
Backwash
Fast Rinse
OPEN OPEN OPENCLSD CLSDCLSDCLSD
OPEN OPEN CLSDCLSDOPEN CLSD CLSD
CLSDCLSDOPEN OPEN OPEN OPENCLSD
CLSD
CLSD
CLSD
This manual suits for next models
8
Table of contents
Other Autotrol Control Unit manuals
Popular Control Unit manuals by other brands
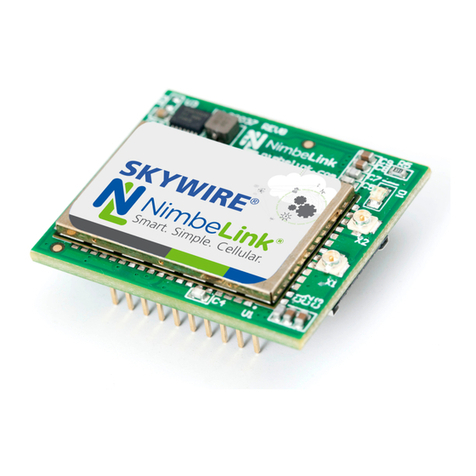
NimbeLink
NimbeLink Skywire NL-SW-LTE-GELS3 manual
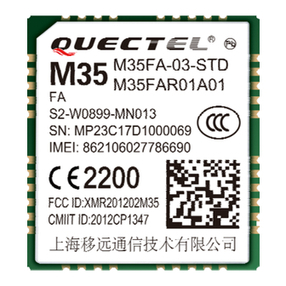
Quectel
Quectel M35 Command manual
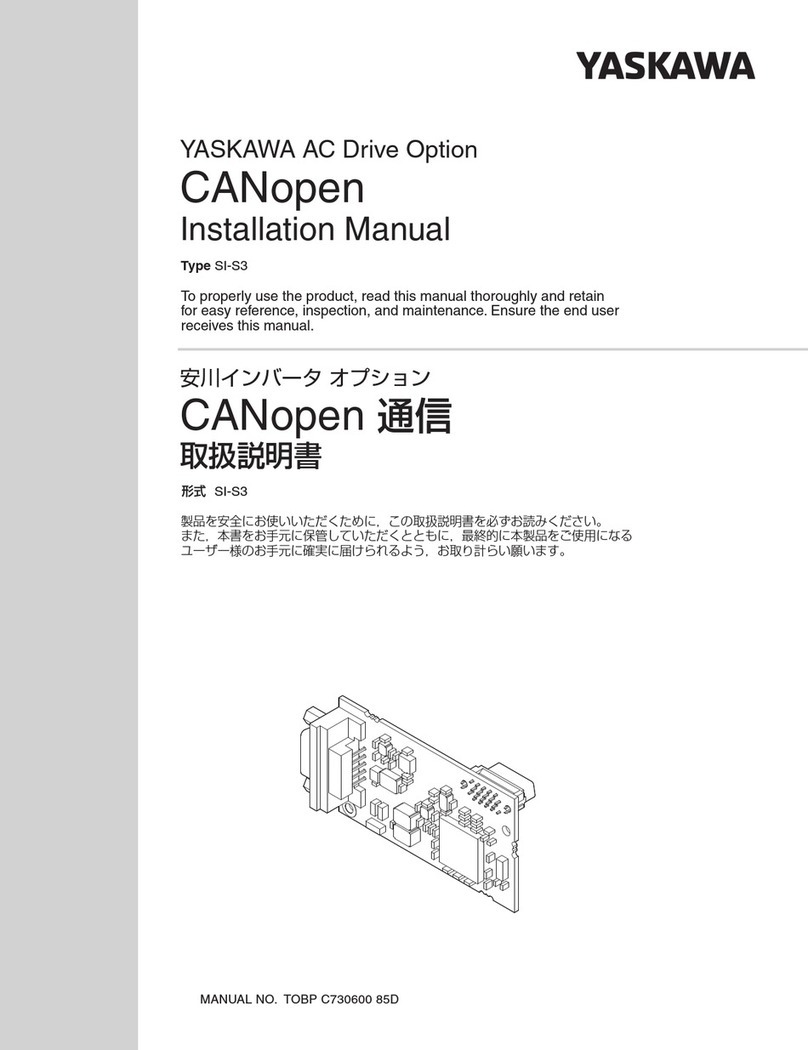
YASKAWA
YASKAWA CANopen SI-S3 installation manual
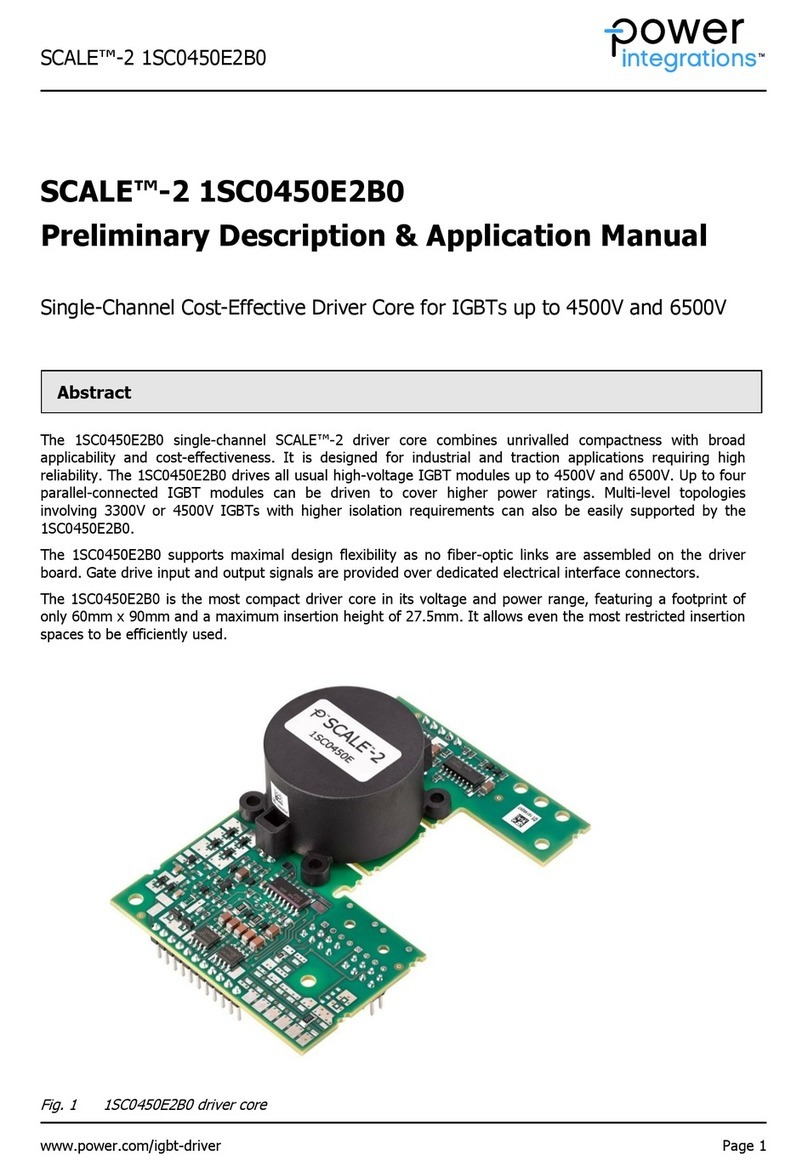
Power integrations
Power integrations Scale-2 1SC0450E2B0 Applications manual
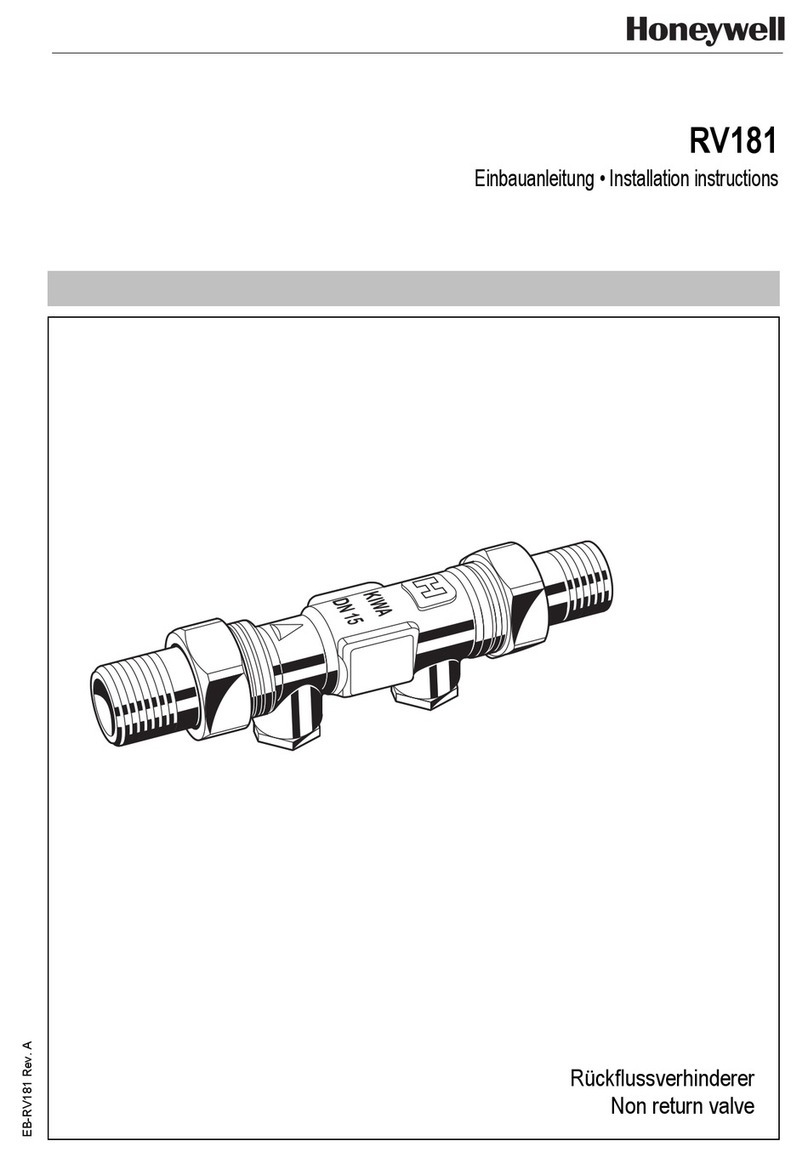
Honeywell
Honeywell RV181 Installation instruction
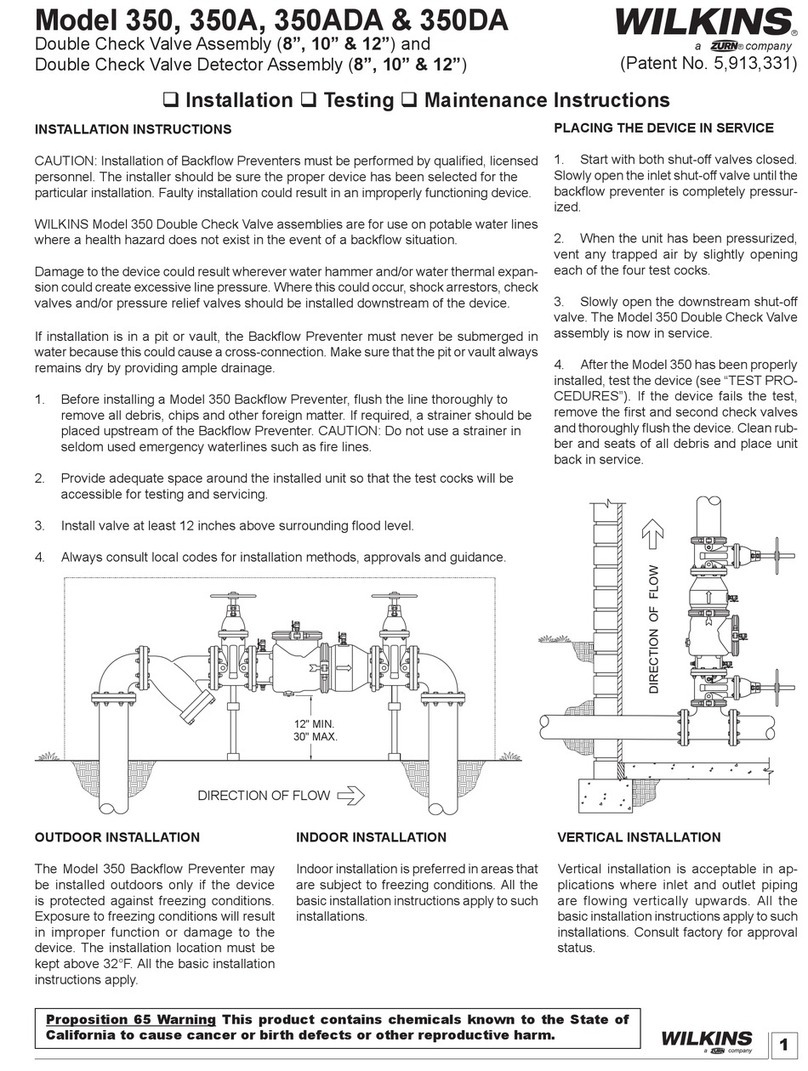
WILKINS
WILKINS 350 Installation and testing instructions
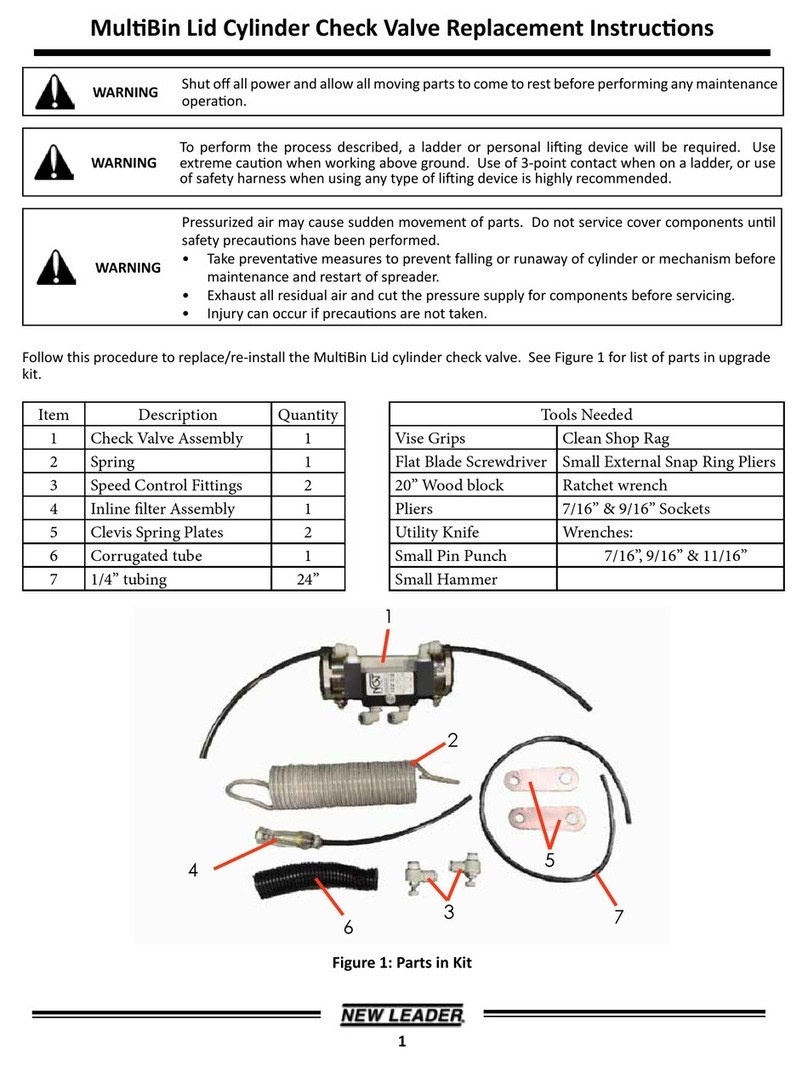
New Leader
New Leader MultiBin Replacement instructions
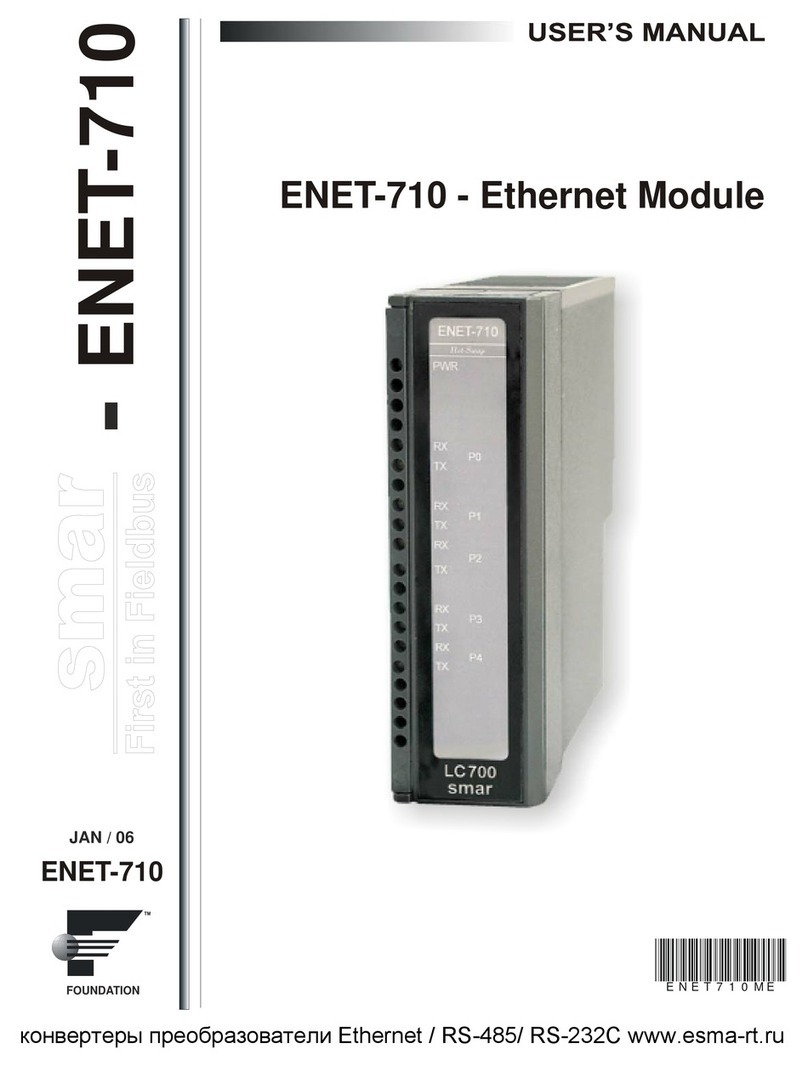
SMAR
SMAR ENET-710 user manual
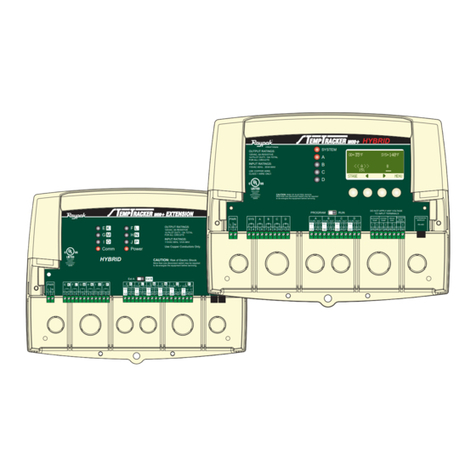
Rheem
Rheem Raypak TempTracker MOD+ HYBRID Installation and operation instruction
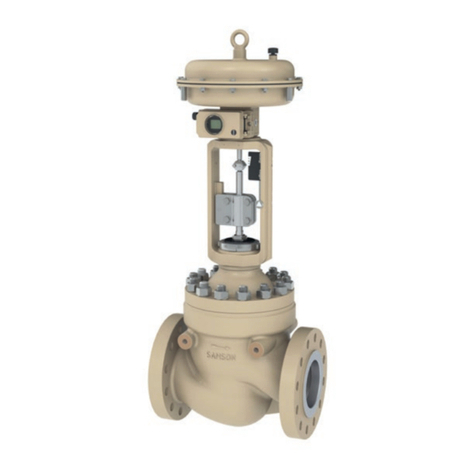
Samson
Samson 3251-E Mounting and operating instructions
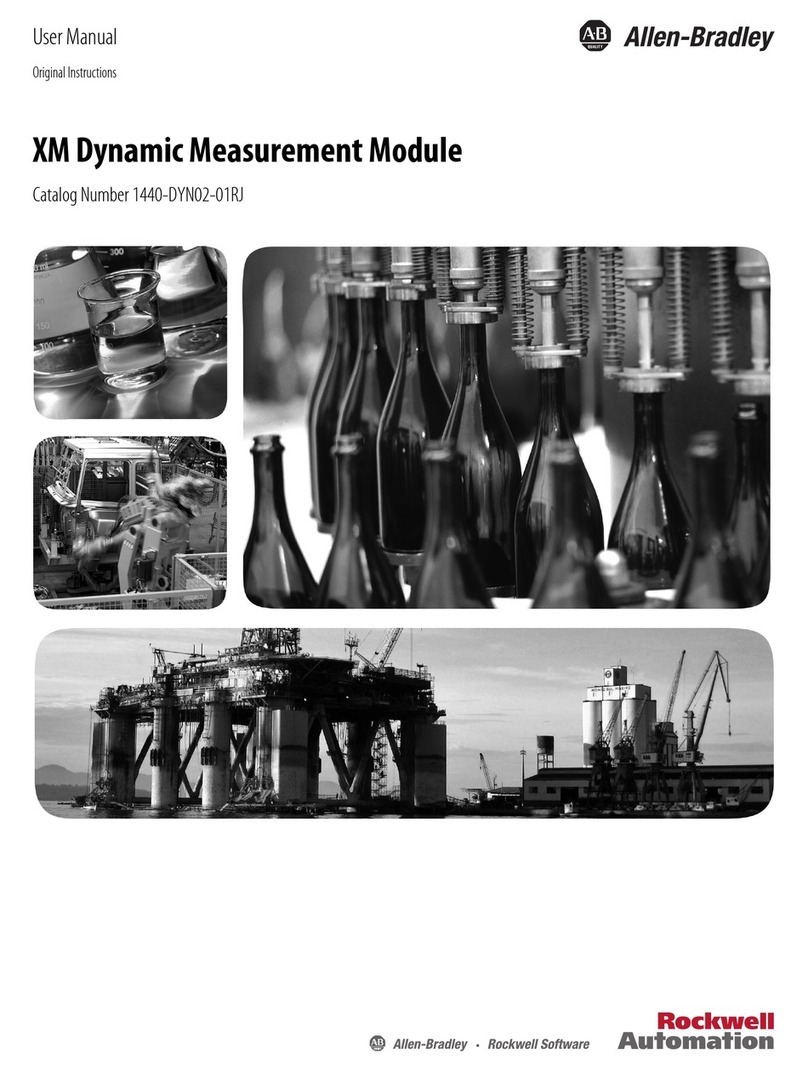
Allen-Bradley
Allen-Bradley 1440-DYN02-01RJ user manual

Espressif Systems
Espressif Systems ESP32-WROVER-E user manual