Axiometrix Solutions imc BUSDAQflex User manual

imcTest & Measurement GmbH • Voltastr.5 • 13355Berlin • Germany
© 2023 imcTest & Measurement GmbH
imc BUSDAQflex
Getting Started
Edition 7 - 2023-08-24

imc BUSDAQflex - Getting Started, Edition 7 - 2023-08-24© 2023 imcTest & Measurement GmbH
Page 2
Disclaimer of liability
The contents of this documentation have been carefully checked for consistency with the hardware and
software systems described. Nevertheless, it is impossible to completely rule out inconsistencies, so that
we decline to offer any guarantee of total conformity.
We reserve the right to make technical modifications of the systems.
Copyright
© 2023 imcTest & Measurement GmbH, Germany
This documentation is the intellectual property of imcTest & Measurement GmbH. imcTest &
Measurement GmbH reserves all rights to this documentation. The applicable provisions are stipulated in
the "imc Software License Agreement".
The software described in this document may only be used in accordance with the provisions of the "imc
Software License Agreement".
Open Source Software Licenses
Some components of imc products use software which is licensed under the GNU General Public License
(GPL). Details are available in the About dialog.
A list of the open source software licenses for the imc measurement devices is located on the
imcSTUDIO/imcWAVE/imcSTUDIO Monitor installation medium in the folder "Products\imc
DEVICES\OSS" or "Products\imc DEVICEcore\OSS" or "Products\imc STUDIO\OSS". If you wish to receive a
copy of the GPL sources used, please contact our Hotline.

imc BUSDAQflex - Getting Started, Edition 7 - 2023-08-24© 2023 imcTest & Measurement GmbH
Page 3
Notes regarding this document
This document is an excerpt from the manual of the device / the module.
This document provides important notes on using the device / the module. Safe working is conditional on
compliance with all safety measures and instructions provided. The manual is to be used as a kind of
reference book. You can skip the description of the modules you do not have.
Additionally, all accident prevention and general safety regulations pertinent to the location at which the
device is used must be adhered to.
These instructions exclusively describe the device, not how to operate it by means of the software!
If you have any questions as to whether you can set up the device / module in the intended environment,
please contact the imc hotline. The measurement system has been designed, manufactured and unit-
tested with all due care and in accordance with the safety regulations before delivery and has left the
factory in perfect condition. In order to maintain this condition and to ensure safe operation, the user
must observe the notes and warnings contained in this chapter and in the specific sections applicable to
the concrete device. Never use the device outside the specification.
This will protect you and prevent damage to the device.
Special notes
Warning
Warnings contain information that must be
observed to protect the user from harm or to
prevent damage to property.
Note
Notes denote useful additional information on a
particular topic.
Reference
A reference in this document is a reference in
the text to another text passage.

imc BUSDAQflex - Getting Started, Edition 7 - 2023-08-24© 2023 imcTest & Measurement GmbH
Page 4
Table of contents
Table of contents
1 General introduction ........................................................................................ 6
1.1 imc Customer Support / Hotline ......................................................................................... 6
1.2 Legal notices ........................................................................................................................ 6
1.3 Explanation of symbols ....................................................................................................... 9
1.4 Last changes in content .................................................................................................... 10
2 Safety ............................................................................................................. 11
3 Assembly and connection ............................................................................... 14
3.1 After unpacking... .............................................................................................................. 14
3.2 Before commissioning ...................................................................................................... 14
3.3 Notes on connecting ......................................................................................................... 15
3.3.1 Precautions for operation ................................................................................................................... 15
3.3.2 Supply ................................................................................................................................................. 15
3.3.3 Grounding, shielding ........................................................................................................................... 19
3.3.4 Fuses (polarity-inversion protection) .................................................................................................. 20
3.3.5 Batteries .............................................................................................................................................. 20
4 Maintenance and servicing ............................................................................. 21
4.1 Maintenance and servicing ............................................................................................... 21
4.2 Cleaning ............................................................................................................................. 21
4.3 Storage .............................................................................................................................. 21
4.4 Transport ........................................................................................................................... 21
5 Start of operation Software / Firmware .......................................................... 22
5.1 Installation - Software ....................................................................................................... 22
5.1.1 System requirements .......................................................................................................................... 22
5.2 Connect the device ........................................................................................................... 22
5.3 Connecting via LAN in three steps .................................................................................... 23
5.4 Firmware update ............................................................................................................... 26
6 Introduction ................................................................................................... 29
6.1 imc BUSDAQflex device series .......................................................................................... 29
6.2 Topology and Mounting ................................................................................................... 30
6.3 CAN Termination ............................................................................................................... 32
6.4 Device variants and options ............................................................................................. 33
7 Pin configuration ............................................................................................ 34
7.1 DSUB-15 ............................................................................................................................ 34
7.2 Metal connector - Handling .............................................................................................. 35
7.3 LEMO.0B (6-pin) CTRL socket ............................................................................................ 36
7.4 DSUB-9 pin configuration ................................................................................................. 37
7.4.1 Display ................................................................................................................................................. 37
7.4.2 GPS ...................................................................................................................................................... 37
7.5 Pin configuration of the fieldbusses ................................................................................. 38
7.5.1 CAN-Bus, CAN FD (DSUB-9) ................................................................................................................. 38
7.5.2 LIN-Bus (DSUB-9) ................................................................................................................................. 38
7.5.3 FlexRay-Bus (DSUB-9) ......................................................................................................................... 38
7.5.4 XCPoE (RJ45) ....................................................................................................................................... 39

imc BUSDAQflex - Getting Started, Edition 7 - 2023-08-24© 2023 imcTest & Measurement GmbH
Page 5
Table of contents
7.5.5 ARINC-Bus (DSUB-15) .......................................................................................................................... 40
7.5.6 PROFIBUS (DSUB-9) ............................................................................................................................. 41
7.5.7 PROFINET (RJ45).................................................................................................................................. 41
7.5.8 MVB-Bus (DSUB-9) ............................................................................................................................. 41
Index ................................................................................................................. 44

imc BUSDAQflex - Getting Started, Edition 7 - 2023-08-24© 2023 imcTest & Measurement GmbH
Page 6
Chapter 1 General introduction
1 General introduction
1.1 imc Customer Support / Hotline
If you have problems or questions, please contact our Customer Support/Hotline:
imcTest & Measurement GmbH
Hotline
(Germany):
+49 30 467090-26
E-Mail:
hotline@imc-tm.de
Internet:
https://www.imc-tm.com
International partners
For our international partners see https://www.imc-tm.com/imc-worldwide/.
Tip for ensuring quick processing of your questions:
If you contact us you would help us, if you know the serial number of your devices and the version info
of the software. This documentation should also be on hand.
·
The device's serial number appears on the nameplate.
·
The program version designation is available in the About-Dialog.
1.2 Legal notices
Quality Management
imcTest & Measurement GmbH holds DIN-EN-ISO-9001
certification since May 1995. You can download the CE
Certification, current certificates and information about the imc
quality system on our website:
https://www.imc-tm.com/quality-assurance/.
imc Warranty
Subject to the general terms and conditions of imcTest & Measurement GmbH.

imc BUSDAQflex - Getting Started, Edition 7 - 2023-08-24© 2023 imcTest & Measurement GmbH
Page 7
Legal notices
Liability restrictions
All specifications and notes in this document are subject to applicable standards and regulations, and
reflect the state of the art well as accumulated years of knowledge and experience. The contents of this
document have been carefully checked for consistency with the hardware and the software systems
described. Nevertheless, it is impossible to completely rule out inconsistencies, so that we decline to
offer any guarantee of total conformity. We reserve the right to make technical modifications of the
systems.
The manufacturer declines any liability for damage arising from:
·
failure to comply with the provided documentation,
·
inappropriate use of the equipment.
Please note that all properties described refer to a closed measurement system and not to its individual
slices.
Guarantee
Each device is subjected to a 24-hour "burn-in" before leaving imc. This procedure is capable of detecting
almost all cases of early failure. This does not, however, guarantee that a component will not fail after
longer operation. Therefore, all imc devices are granted liability for a period of two years. The condition
for this guarantee is that no alterations or modifications have been made to the device by the customer.
Unauthorized intervention in the device renders the guarantee null and void.
Notes on radio interference suppression
imc BUSDAQflex devices satisfy the EMC requirements for an use in industrial settings.
Any additional products connected to the product must satisfy the EMC requirements as specified by the
responsible authority (within Europe1) in Germany the BNetzA - "Bundesnetzagentur" (formerly BMPT-
Vfg. No. 1046/84 or No. 243/91) or EC Guidelines 2014/30/EU. All products which satisfy these
requirements must be appropriately marked by the manufacturer or display the CE certification marking.
Products not satisfying these requirements may only be used with special approval of the regulating body
in the country where operated.
All lines connected to the imc BUSDAQflex devices should not be longer than 30m and they should be
shielded and the shielding must be grounded.
Note
The EMC tests were carried out using shielded and grounded input and output cables with the
exception of the power cord. Observe this condition when designing your setup to ensure high
interference immunity and low jamming.
1 If you are located outside Europe, please refer the appropriate EMC standards used in the country of operation.

imc BUSDAQflex - Getting Started, Edition 7 - 2023-08-24© 2023 imcTest & Measurement GmbH
Page 8
Chapter 1 General introduction
Cables and leads
In order to comply with the value limits applicable to Class B devices according to part 15 of the FCC
regulations, all signal leads connected to the imc BUSDAQflex devices must be shielded.
Unless otherwise indicated, no connection leads may be long leads (<30m) as defined by the standard
IEC 61326-1. LAN-cables (RJ 45) and CAN-Buscables (DSUB-9) are excepted from this rule.
Only cables with suitable properties for the task (e.g. isolation for protection against electric shock) may
be used.
ElektroG, RoHS 2, WEEE, CE
The imcTest & Measurement GmbH is registered with the authority as follows:
WEEE Reg. No. DE 43368136
valid from 24.11.2005
Reference
https://www.imc-tm.com/elekrog-rohs-weee/ and https://www.imc-tm.com/ce-conformity/
FCC-Notice
This product has been tested and found to comply with the limits for a Class B digital device, pursuant to
Part 15 of the FCC Rules. These limits are designed to provide reasonable protection against harmful
interference in a residential installation. This equipment generates, uses, and can radiate radio frequency
energy and, if not installed and used in accordance with the instructions, may cause harmful interference
to radio communications. However, there is no guarantee that interference will not occur in a particular
installation. If this equipment does cause harmful interference to radio or television reception, which can
be determined by turning the equipment on and off, the user is encouraged to try to correct the
interference by one or more of the following measures:
·
Reorient or relocate the receiving antenna.
·
Increase the separation between the equipment and the receiver.
·
Connect the equipment into an outlet on a circuit different from that to which the receiver is
connected.
·
Consult our imc Hotline or an experienced technician for help.
Modifications
The FCC requires the user to be notified that any changes or modifications made to this product that
are not expressly approved by imc may void the user's authority to operate this equipment.

imc BUSDAQflex - Getting Started, Edition 7 - 2023-08-24© 2023 imcTest & Measurement GmbH
Page 9
Explanation of symbols
1.3 Explanation of symbols
CE Conformity
see CE chapter 1.2
No household waste
Please do not dispose of the electrical/electronic device with household waste, but at the
appropriate collection points for electrical waste, see also chapter 1.2 .
Potential compensation
Connection for potential compensation
Grounding
Connection for grounding (general, without protective function)
Protective connection
Connection for the protective conductor or grounding with protective function
Attention! General danger zone!
This symbol indicates a dangerous situation;
Since there is insufficient space for indicating the rated quantity at the measuring inputs,
refer to this manual for the rated quantities of the measuring inputs before operation.
Attention! Injuries from hot surfaces!
Surfaces whose temperatures can exceed the limits under certain circumstances are
denoted by the symbol shown at left.
ESD-sensitive components (device/connector)
When handling unprotected circuit boards, take suitable measures to protect against ESD
(e.g. insert/remove ACC/CANFT-RESET).
Possibility of electric shock
The warning generally refers to high measurement voltages or signals at high potentials and
is located on devices suitable for such measurements. The device itself does not generate
dangerous voltages.
DC, Direct Current
Supply of the device via a DC voltage source (in the specified voltage range)
6
6

imc BUSDAQflex - Getting Started, Edition 7 - 2023-08-24© 2023 imcTest & Measurement GmbH
Page 10
Chapter 1 General introduction
RoHS of the PR China
The limits for hazardous substances in electrical/electronic equipment applicable in the PRC
are identical to those in the EU. The restrictions are complied with (see chapter 1.2 ). A
corresponding "China-RoHS" label is omitted for formal/economic reasons. Instead, the
number in the symbol indicates the number of years in which no hazardous substances are
released. (This is guaranteed by the absence of named substances).
Observe the documentation
Read the documentation before starting work and/or operating.
1.4 Last changes in content
Please help us to improve our documentation:
·
Which terms or descriptions are incomprehensible?
·
What additions and enhancements you suggest?
·
Where have material mistakes slipped in?
·
Which spelling, translation or typing errors have you found?
Responses and other feedback should be directed to the Hotline.
Amendments and bug-fix in Edition 7
Chapter
Amendment
GPS connection
Maximum current = 220 mA, i.e. the 5 V can be loaded with max. 220 mA
Amendments and bug-fix in Edition 6
Chapter
Amendment
Handling
In the last Edition 5 the content of this chapter was missing.
Amendments and bug-fix in Edition 5
General
Amendment
Symbols
Missing symbols added in chapter "Explanation of symbols".
Connecting via LAN
The dialog for configuring the IP address of the device also provides the IP address of
the PC. Thus, the first step was removed from the documentation, which presented
different possibilities in Windows to determine the IP address.
Technical Specs
We added a general introduction to this chapter.
6
35

imc BUSDAQflex - Getting Started, Edition 7 - 2023-08-24© 2023 imcTest & Measurement GmbH
Page 11
2 Safety
This section provides an overview of all important aspects of protection of the users for reliable and
trouble-free operation. Failure to comply with the instructions and protection notes provided here can
result in serious danger.
Responsibility of the operator
imc BUSDAQflex is for use in commercial applications. The user is therefore obligated to comply with
legal regulations for work safety.
Along with the work safety procedures described in this document, the user must also conform to
regulations for safety, accident prevention and environmental protection which apply to the work site. If
the product is not used in a manner specified by the manufacturer, the protection supported by the
product may be impaired.
The user must also ensure that any personnel assisting in the use of the imc BUSDAQflex have also read
and understood the content of this document.
Operating personnel
This document identifies the following qualifications for various fields of activity:
·
Users of measurement engineering: Fundamentals of measurement engineering. Basic knowledge of
electrical engineering is recommended. Familiarity with computers and the Microsoft Windows
operating system. Users must not open or structurally modify the measurement device.
·
Qualified personnel are able, due to training in the field and to possession of skills, experience and
familiarity with the relevant regulations, to perform work assigned while independently recognizing
any hazards.
Warning
·
Danger of injury due to inadequate qualifications!
·
Improper handling may lead to serious damage to personnel and property. When in doubt, consult
qualified personnel.
·
Work which may only be performed by trained imc personnel may not be performed by the user. Any
exceptions are subject to prior consultation with the manufacturer and are conditional on having
obtained corresponding training.

imc BUSDAQflex - Getting Started, Edition 7 - 2023-08-24© 2023 imcTest & Measurement GmbH
Page 12
Chapter 2 Safety
Special hazards
This segment states what residual dangers have been identified by the hazard analysis. Observe the
safety notes listed here and the warnings appearing in subsequent chapters of this manual in order to
reduce health risks and to avoid dangerous situations. Existing ventilation slits on the sides of the device
must be kept free to prevent heat accumulation inside the device. Please operate the device only in the
intended position of use if so specified.
Danger
Lethal danger from electric current!
·
Contact with conducting parts is associated with immediate lethal danger.
·
Damage to the insulation or to individual components can be lethally dangerous.
Therefore:
·
In case of damage to the insulation, immediately cut off the power supply and have
repair performed.
·
Work on the electrical equipment must be performed exclusively by expert
electricians.
·
During all work performed on the electrical equipment, it must be deactivated and
tested for static potential.
Injuries from hot surfaces!
·
Devices from imc are designed so that their surface temperatures do not exceed limits
stipulated in EN 61010-1 under normal conditions.
Therefore:
·
Surfaces whose temperature can exceed the limits under circumstances are denoted
by the symbol shown at left.
Industrial safety
We certify that imc BUSDAQflex in all product configuration options corresponding to this documentation
conforms to the directives in the accident prevention regulations in "Electric Installations and Industrial
Equipment" (DGUV Regulation 3)*. This confirmation applies exclusively to devices of the imc
BUSDAQflex series, but not to all other components included in the scope of delivery.
This certification has the sole purpose of releasing imc from the obligation to have the electrical
equipment tested prior to first use (§ 5 Sec. 1, 4 of DGUV Regulation3). This does not affect guarantee
and liability regulations of the civil code.
For repeat tests, a test voltage that is 1.5 times the specified working voltage should be used to test the
isolation for the highly isolated inputs (e.g. measurement inputs for high-voltage applications).
*
previously BGV A3.

imc BUSDAQflex - Getting Started, Edition 7 - 2023-08-24© 2023 imcTest & Measurement GmbH
Page 13
Observe notes and warnings
Devices from imc have been carefully designed, assembled and routinely tested in accordance with the
safety regulations specified in the included certificate of conformity and has left imc in perfect operating
condition. To maintain this condition and to ensure continued danger-free operation, the user should pay
particular attention to the remarks and warnings made in this chapter. In this way, you protect yourself
and prevent the device from being damaged.
Read this document before turning on the device for the first time carefully.
Warning
Before touching the device sockets and the lines connected to them, make sure static electricity is
diverted to ground. Damage arising from electrostatic discharge is not covered by the warranty.

imc BUSDAQflex - Getting Started, Edition 7 - 2023-08-24© 2023 imcTest & Measurement GmbH
Page 14
Chapter 3 Assembly and connection
3 Assembly and connection
3.1 After unpacking...
Check the delivered system immediately upon receiving it for completeness and for possible transport
damage. In case of damage visible from outside, proceed as follows:
·
Do not accept the delivery or only accept it with reservations
·
Note the extent of the damage on the packing documents or on the delivery service's packing list.
·
Begin the claims process.
Please check the device for mechanical damage and/ or loose parts after unpacking it. The supplier must
be notified immediately of any transportation damage! Do not operate a damaged device!
Check that the list of accessories is complete (product package):
·
AC/DC-power adaptor with appropriate LEMO plug
·
Grounding set consisting of: a spring washer S3 (stainless steel), a flat washer (A3.2 DIN 433 A2) and
a pan-head screw M3x8 (mounted on the rear panel).
·
1x Ethernet network cable with latch protection (uncrossed, 2 m)
·
1x protective cover for the remote control socket type 0B
·
Getting started with imc BUSDAQflex (one copy per delivery)
Note
File a claim about every fault as soon as it is detected. Claims for damages can only be honored
within the stated claims period.
3.2 Before commissioning
Condensation may form on the circuit boards when the device is moved from a cold environment to a
warm one. In these situations, always wait until the device warms up to room temperature and is
completely dry before turning it on. The acclimatization period should take about 2 hours. This is
especially recommended for devices without ET (extended environmental temperature range).
We recommend a warm-up phase of at least 30 min prior to measure.
Ambient temperature
The limits of the ambient temperature cannot be strictly specified because they depend on many factors
of the specific application and environment, such as air flow/convection, heat radiation balance in the
environment, contamination of the housing / contact with media, mounting structure, system
configuration, connected cables, operating mode, etc. This is taken into account by specifying the
operating temperature instead. Furthermore, it is not possible to predict any sharp limits for electronic
components. Basically, reliability decreases when operating under extreme conditions (forced ageing).
The operating temperature data represent the extreme limits at which the function of all components
can still be guaranteed.

imc BUSDAQflex - Getting Started, Edition 7 - 2023-08-24© 2023 imcTest & Measurement GmbH
Page 15
Notes on connecting
3.3 Notes on connecting
3.3.1 Precautions for operation
Certain basic rules for operating the system, aside from reasonable safety measures, must be observed
to prevent danger to the user, third parties, the device itself and the measurement object. These are the
use of the system in conformity to its design, and the refraining from altering the system, since possible
later users may not be properly informed and may ill-advisedly rely on the precision and safety promised
by the manufacturer.
Note
If you determine that the device cannot be operated in a non-dangerous manner, then the device is to
be immediately taken out of operation and protected from unintentional use. Taking this action is
justified under any of the following conditions:
I. the device is visibly damaged,
II. loose parts can be heard within the device,
III. the device does not work
IV. the device has been stored for a long period of time under unfavorable conditions (e.g. outdoors
or in high-humidity environments).
1. Observe the data in the chapter "Technical Specs", to prevent damage to the unit through
inappropriate signal connection.
2. If you are using a internal device drive, observe the notes in the imc software manual. Particular
care should be taken to comply with the storage device's max. ambient temperature limitation.
3. Change the removable flash storage with care.
3.3.2 Supply
The range of permitted supply voltages is 10 .. 50 V DC. The table-top power supply unit which is included
standard delivers 24VDC at a max. power consumption of 60W. The AC input voltage can be 110..240V
50/60Hz.
Note
Please note, that the operation temperature of the desktop supply is prepared for 0°C to 40°C, even
if your measurement devices is designed for extended temperature range!
Connecting a DC supply source such as a car battery is also fundamentally possible. Note when making
such a connection:
·
Grounding of the device must be provided. If the supply voltage source has a ground reference
(ground connected to the (–) terminal), then the device is automatically grounded via the (–)
terminal. The table-top power supply unit is configured in this manner.
·
The supply line must take the form of a low-resistance cable of sufficient cross-section. Any extra
(suppression) filters connected in the middle of the supply circuit should not contain any serial
inductance coils of more than 1 mH. Otherwise and extra parallel capacitor is needed.

imc BUSDAQflex - Getting Started, Edition 7 - 2023-08-24© 2023 imcTest & Measurement GmbH
Page 16
Chapter 3 Assembly and connection
3.3.2.1 Supply of directly connected imc CANSASflex modules
imc BUSDAQflex (BUSFX) is compatible with the imc CANSASflex series (CANFX), CAN-Bus based
measurement technique. All modules of the flex series (CANFX and BUSFX) can be joined together
mechanically and electrically by means of a latching ("click") mechanism , without the use of any tools
nor the need for any extra cables.
Note
The data sheet list the available power consumption for the supply of directly connected modules
(click-connection) and the max. current-limit of the module connector.
3.3.2.2 DC power supply at CAN-Nodes 1 and 2
If desired, the DC power supply can be made accessible at the CAN-nodes 1 and 2 (DSUB pin 1 and 5) .
This connection is directly wired through, bidirectional and with its PTC protected against overload with
max. 1 A current limit.
This option provides the possibility to use the DSUB-9 as an output and to power connected imc CANSAS
modules. If it is used as an input it is possible to supply the BUSDAQ via CAN-cable (e.g. OBD). In this case
there are no current reserves available to supply further connected CANSAS modules!
Note
In each case, using the CAN cable for supply purposes a cable with sufficient cross-section is required!
3.3.2.3 Notes on operation with power supply lead through the device
·
With this setup, the maximum current of 1 A must not be exceeded. The CANSAS modules' low
power consumption should not be underestimated, since low supply voltages can cause high power
values via high current. E.g. two CAN/UNI8 modules with a power consumption of approx. 30 W
(with connected sensors) already exceed the limit by having a current of 2 A at 15 V. Additional
factors are the voltage drop along long wires, and small wire cross-sections. In any case, it is
necessary to first calculate the power consumption and the current strengths to be expected.
·
By dint of its engineering, the CAN-bus is ideally suited to re-structuring systems. However, this can
easily lead to situations where the current demands and wire cross sections were correctly chosen
originally, but the specifications were later violated when the system was gradually supplemented
with new modules.
·
It is always possible to use only one supply source. If an external supply is applied to the CAN-bus
and the BUSDAQ's power supply unit is additionally connected, the BUSDAQ can be damaged
irreparably. Under no circumstances may the BUSDAQ's power supply unit be used as an
uninterrupted power supply for the connected CAN-Bus system.
·
The current limiter attempts to ensure that the measurement is correctly closed and that data loss
is thus avoided. Nevertheless, incorrect configuration may lead to data loss or damage of the
BUSDAQ unit. When in doubt, please contact our Customer Service department.
·
Using -SUPPLY does not replace the CAN_GND connection! CAN_GND should always be connected,
independent from this power supply. CAN_GND is necessary to keep a defined level for CAN_H and
CAN_L.
30
38

imc BUSDAQflex - Getting Started, Edition 7 - 2023-08-24© 2023 imcTest & Measurement GmbH
Page 17
Notes on connecting
Power via CAN
The following figures: A) and B) show connection possibilities, depending on the use of power via CAN. If
your device has the Power via CAN functionality, the DSUB connection on your device is labeled "Power
via CAN".
A) Power via CAN not used: no stubs, unlimited block size
B) Use of Power via CAN: max. size of stub blocks (Y-type stub), according CiA®

imc BUSDAQflex - Getting Started, Edition 7 - 2023-08-24© 2023 imcTest & Measurement GmbH
Page 18
Chapter 3 Assembly and connection
3.3.2.4 UPS and power fail function
Automatic conclusion of measurement and data saving upon power outage
imc BUSDAQflex comes with UPS-functionality to ensure the integrity of data in case of power outages.
When power outage occurs, this functionality prevents loss of data and is referred to as Power Fail. If the
power fails, the measurement stops automatically and the data are saved to the internal bulk memory
("μ-Disk": flash media or HDD) in sufficient time.
The parameter "Buffer-time constant" specifies the delay time which the device waits to actually initiate
automatic conclusion of measurement ("Auto-Shutdown") after a power outage has been detected. This
prevents a measurement from being stopped after only very short power outages. For all imc
BUSDAQflex device varieties, the buffer time constant is 1 second and can not be changed by means of
the device configuration (unlike in other imc device series).
After elapse of the buffer time constant, the running measurement is stopped and all open measurement
files are closed and saved to the device's Flash removable memory (CF-Card, "µ-Disk"). This can typically
take up to 10 more seconds.
The buffer capacity of the internal UPS Super-Caps is sufficient to securely buffer the device's power
supply (aggregate buffer time: 11 sec.). The condition for this is that the Super-Caps are fully charged.
Super-Caps have higher self-discharge rates than conventional rechargeable batteries and do not keep
their charge for long periods even when deactivated. For this reason, it is necessary for the device to
have been activated/running for a certain minimum duration (see table) in order to ensure the full
function of the "Auto-Data Saving in Power Outage". Accordingly, a sufficiently long time of
uninterrupted operation between successive Power-Fail events must be ensured, in order to recharge
the Super-Caps and to achieve the full buffer capacity.
Note
·
It must be ensured that the device is always deactivated in a controlled way by means of the switch.
Simply unplugging the power supply cable causes the buffering Power Fail function to become active,
which unnecessarily discharges the Super-Caps.
·
If the device is always only powered very briefly for the duration of very short measurements, correct
working of the Power Fail function can not be assured.

imc BUSDAQflex - Getting Started, Edition 7 - 2023-08-24© 2023 imcTest & Measurement GmbH
Page 19
Notes on connecting
3.3.2.5 Main switch
Switch ON
The device's main switch is a power-on button with a built-in "POWER"-LED which must be pressed down
for approx. 1sec. to achieve activation, indicated by the "POWER"-LED flashing. If the device boots
correctly, three short beep-tones are emitted.
Switch OFF
To switch the device off, press the power-on button again down for approx. 1sec, what will cause a
constant blinking of the "POWER"-LED. This causes the device to not be deactivated abruptly during a
running measurement. Instead, any files on the internal hard drive involved are closed before the device
switches off by itself. This process takes up to 10sec. Holding the power-on button down is not
necessary!
If no measurement is currently running, it takes only approx. 1 sec. for the device to be deactivated.
3.3.2.6 Remote On/Off
The imc BUSDAQflex can be activated and deactivated via the Control switch. When the pin Remote
On/Off is connected with –Supply via a push-button switch, the device can be activated/ deactivated as
with the blue LED-button. I.e., one short push of the button switches the device on or off after a brief
delay.
If these pins are connected via a closed two-way switch, the device remains on throughout. In such a
case, the device's blue push-button switch has no effect! In order to turn the device off, the switch must
be opened and then closed again, mimicking the behavior of a push-button switch. Please note:
Depending on the BUSFX variant, the behavior is different.
Reference
Please find here the pin configuration of the CTRL-socket .
3.3.3 Grounding, shielding
In order to comply with Part 15 of the FCC-regulations applicable to devices of Class B, the system must
be grounded. The same applies to the specified technical data.
3.3.3.1 Grounding
The grounding set supplied with the device can be used to ground your device. This grounding set
consists of: a spring washer S3 (stainless steel), a flat washer (A3.2 DIN 433 A2) and a pan-head screw
M3x8 (mounted on the rear panel).
When using the included table-top power adapter, this is ensured by the protection ground terminal: at
the LEMO terminal of the included table-top power adapter, both the power supply's negative contact,
and the shielding and connector pod are connected with the network cable's protection ground.
The DC power voltage applied to the device itself (LEMO-socket) is not isolated, i.e. it has contact with
the electrical system ground ("GND") or the frame ("CHASSIS")!
When drawing power from an isolated DC power supply (e.g. battery), be sure to provide grounding by
making a connection to the frame.
36

imc BUSDAQflex - Getting Started, Edition 7 - 2023-08-24© 2023 imcTest & Measurement GmbH
Page 20
Chapter 3 Assembly and connection
3.3.3.2 Shielding
As a matter of principle, the use of shielded and grounded cabling is required in order to comply with the
relevant EMC and interference suppression limits.
In many cases, the use of an affordable multi-wire single-layer shielded cable (even for multiple channels)
is adequate.
Note
·
Protect the CAN-H-L against common mode voltage using shielded cables.
·
Connect chassis with earth ground.
·
Use CAN-Ground.
·
Use shielded cables, connect shield to chassis.
·
To avoid compensation currents, always connect the shielding to one side (potential) only.
3.3.3.3 Potential difference with synchronized devices
When using multiple devices connected via the SYNC socket for synchronization purposes, ensure that all
devices are at the same voltage level.
Note
The yellow ring on the SYNC socket indicates that the socket is shielded from voltage differences.
3.3.4 Fuses (polarity-inversion protection)
The device supply input is equipped with maintenance-free polarity-inversion protection. No fuses or
surge protection is provided here. Particularly upon activation of the device, high current peaks are to be
expected. When using the device with a DC-voltage supply and custom-designed supply cable, be sure to
take this into account by providing adequate cable cross-section.
3.3.5 Batteries
For an uninterruptable power supply (UPS) Super-Caps are used to supply the imc BUSDAQflex device.
No special maintenance should be necessary. No fuses are included in the device.
Table of contents
Other Axiometrix Solutions Measuring Instrument manuals
Popular Measuring Instrument manuals by other brands
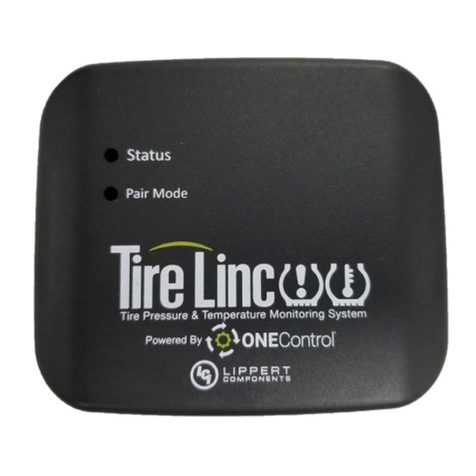
Lippert Components
Lippert Components Tire Linc 2020106863 Installation and owner's manual
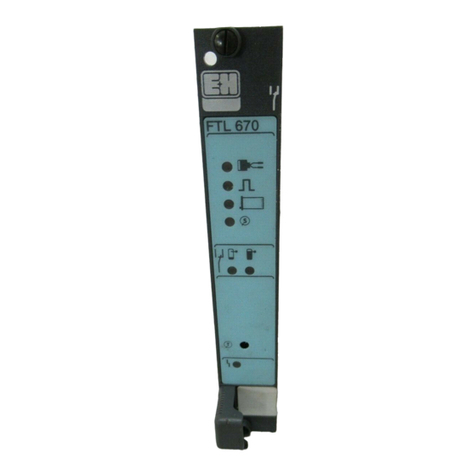
Endress+Hauser
Endress+Hauser Liquiphant S FDL60 Functional safety manual
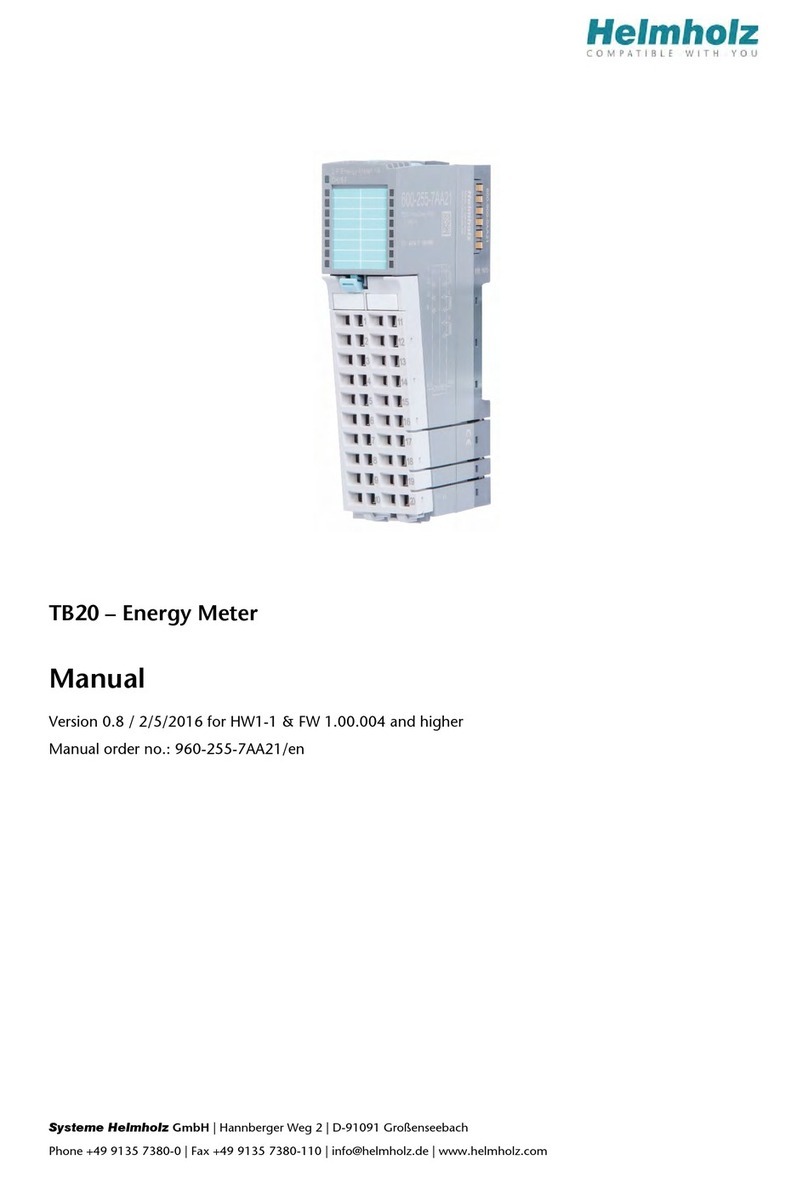
Helmholz
Helmholz TB20 manual

Halveon
Halveon T-Stream MU operating instructions
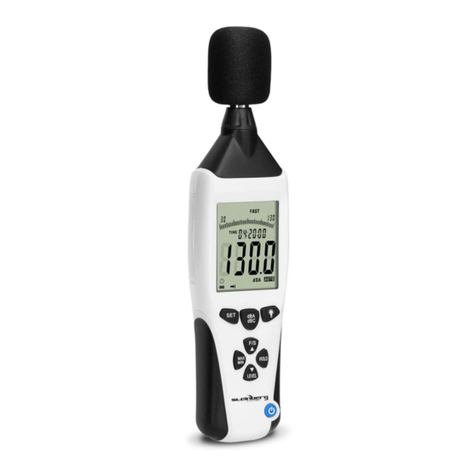
Steinberg
Steinberg SBS-SM-130C user manual

Megger
Megger MOM200A user manual