BABBITT LS7000 User manual

L
LS
S7
70
00
00
0
L
LE
EV
VE
EL
L
S
SW
WI
IT
TC
CH
H
O
OW
WN
NE
ER
RS
S
M
MA
AN
NU
UA
AL
L
♦
♦
I
IN
NS
ST
TA
AL
LL
LA
AT
TI
IO
ON
N
♦
♦
C
CA
AL
LI
IB
BR
RA
AT
TI
IO
ON
N
♦
♦
T
TR
RO
OU
UB
BL
LE
ES
SH
HO
OO
OT
TI
IN
NG
G
♦ W
WA
AR
RR
RA
AN
NT
TY
Y
BABBITT
INTERNATIONAL, INC.
P.O. Box 70094
Houston, TX 77270
(713) 467-4438

TABLE OF CONTENTS
Page
1. Description ------------------------------------------------------- 1
A. General Description ---------------------------------- 1
B. Specifications ------------------------------------------- 1
2. Theory of Operation ------------------------------------------- 2
3. Installation------------------------------------------------------------- 2
A. Inspection and Operation Check ------------------------- 2
B. Physical Installation ------------------------------------------- 2
C. Removing Electronics------------------------------------------- 3
D. Typical Applications and Wiring Diagrams ---------------- 3
1) LS7000 Terminal Layout ---------------------------------- 3
2) Ladder Diagrams ------------------------------------------- 5-6
4. Calibration ------------------------------------------------------------- 7
A. Setting the Time Delay ---------------------------------- 7
B. Fail Safe Selection ------------------------------------------- 7
C. Sensitivity Calibration ---------------------------------- 7
5. Maintenance and Troubleshooting ---------------------------------- 8
6. Warranty ------------------------------------------------------------- 9

LS7000 LEVEL SWITCH
1. DESCRIPTION
A. General Description
The LS7000 is a point level switch that detects the presence or absence of material in a bin, silo, tank or other
container. The basic unit is made up of a solid stainless steel probe attached to an explosion proof housing.
Inside the explosion proof housing are all calibration adjustments and sensing electronics. The unit is calibrated
in the absence of material and an internal relay changes state when material is detected.
B. Specifications
Electrical
Power: 115 VAC (±15%) 50/60 Hz. 2 watts, standard.
(12 VDC, 24 VDC or 230 VAC optional)
Output 2 Form C contacts, DPDT relay, 5 amp resistive
At 125, 250 VAC; 30 VDC
Fuse: On board, 250 mA @ 125 volts
Fail Safe: Selectable high or low level
Time Delay: Selectable: ON or OFF delay
Adjustable: 1/8 sec to 2 hrs.
RF Frequency: Approximately 1.3 MHz
Environmental
Hazardous Area: Class I, Group D, Class II, Group E, F, G
Temperature: Probe: -30° F to 400° F
Electronics: -40° F to 185° F
Pressure: Probe: 1500 psi @ 75° F. Higher ranges available
on request.
Construction: Probe: All wetted parts, 316 SS Teflon and Viton.
A Halar coating can be applied to the probe when
applicable.
Electronics: Housed in cast aluminum explosion
proof enclosure.
Specifications subject to change without notice.
C. Ordering Information
1
LS7000 – 115VAC – S – 10*
Model
Supply Voltage
“S” – 316 Stainless Steel Probe
“H” – Halar Coated Probe
Probe length in inches
*This describes an LS7000, powered by a 115 VAC,
with a 316 SS probe, 10” long. The probe length is
measured from the end of the nipple to the tip of the
probe.
1” NPT
1” NPT
½” DIA. 316 SS
6 1/8” 5 1/8”
INSULATOR
1 7/8”
4 ¾” 4”
MAX
10” Standard
Longer Lengths Available
FIGURE 7.1

2. THEORY OF OPERATION
The LS7000 employs a radio frequency (RF) balanced impedance bridge circuit to detect if the probe is in
contact with the material that is to be sensed.
When material is not in contact with the probe, the bridge is balanced by turning the adjustment pot to find the
threshold where the red led goes out.
When material is in contact with the probe, the bridge becomes unbalanced and the comparing circuit realizes
the change. This causes the relay to change state.
3. INSTALLATION
*CAUTION: ALL INSTALLATION AND WIRING MUST CONFORM TO NEC AND ALL OTHER
LOCAL ELECTRICAL CODES. TAKE SPECIAL CARE IN OBSERVING HAZARDOUS AREA
SAFETY PROCEDURES. WE ASSUME NO LIABILITY FOR IMPROPERLY INSTALLED OR
WIRED UNITS.
A. Inspection and Operation
After unpacking the LS7000, visually inspect the unit for any damages. Please advise the factory or your local
distributor of any damage. Before installing the unit, a simple operational check can be performed.
*THIS IS AN EXCELLENT TIME TO SET THE TIME DELAY IF IT IS TO BE USED IN YOUR
APPLICATION. (See calibration instructions, section 4, A)
On the bench, hook up the appropriate power to L1 and L2. The operating voltage of the LS7000 is marked on
the power supply board.
Hold the unit so that the probe is not touching any surface and press the test switch.
When the test switch is depressed, the red led should come on. This simulates product touching the probe. If a
timing mode has been selected it will operate as if installed.
NOTE: The timing mode can be adjusted when checking the unit but the sensitivity adjustment
MUST BE MADE AFTER the unit is installed where it will be used.
B. Physical Installation
1) The LS7000 is installed into the vessel wall using a 1” NPT connection.
This can be either a threaded coupling or a tapped entry such as a flange.
2) The teflon insulator should always extend at least 2” through the vessel wall.
3) Always check for physical room around the location you have chosen to allow for installation. Allow 3.25”
turning radius to screw the probe in and clearance above for the length of the probe.
4) CAUTION: Always take the necessary safety precautions when cutting or welding in the
coupling for the LS7000.
a) Tag and lock out the electrical power to the equipment that services the vessels.
b) Check liquid or dry powders that create a gas in the vessel for oxygen as well as the explosion factor.
(All dust will explode.)
c) Vessels that are cross vented have to be isolated.
5) Screw the LS7000 into the connection provided. In dry material application, no sealant on threads is
required. On liquid, teflon or a good pipe thread sealant may be used.
6) The LS7000 has a 1” NPT conduit entry. When wiring these units, conform to the National Electrical Code
and any other city or company codes.
7) Always install the electrical connection into the 1” NPT on the LS7000 so water will not follow the
connection routing into the threads of the 1” NPT hub. To guarantee that condensation and water will stay
outside the unit, install an EYSM unilet before each LS7000 and fill with explosion proof sealing cement.
8) When required, the LS7000 probe can be bent to meet your special application. Remember to allow 2” of
clearance between the probe and the vessel wall. If the probe is to be used in a pressure application, the
factory must bend the probe to your specifications.
9) Location of probes on high level installations is more critical on dry material than liquids. Note the
following:
2

a) For dry materials, mount the LS7000 in the top of the vessel whenever possible. (This allows you to
lengthen the probe if necessary.)
b) Avoid mounting the LS7000 near the product inlet, vent return lines, dust collectors and vessel
discharge openings on dry materials. Turbulence around these areas can cause erratic detection unless
the probe is long enough. On old installations it might be wise to fill the vessel first to determine the
length or location of the probe. CAUTION: Always take safety precautions before opening vessels for
such inspection. We recommend a 36” top mounted high level probe in storage silos and a 24” in
smaller vessels such as use bins.
c) On gravity filled vessels, take into consideration the angle of repose formed by the product.
d) On dry product that flows like water (starch), when using the LS7000 to stop the flow by means of a
butterfly valve or knifegate, make sure the probe is long enough to allow time to close these slow
moving valves.
e) In small vessels where a good location is hard to find, it may be necessary to put a baffle plate between
the probe and the product inlet to keep product off of the probe as it fills. (A short time delay could
also solve this problem.)
C. Removing the Electronics
1) To remove the sensing card, simply unplug it from the power supply card. When reinstalling, this card is
made so that it cannot be plugged in backwards.
2) To remove the power supply card you must:
a) Disconnect supply power at main power source.
b) Remove sensing card.
c) Disconnect wires from terminal strip.
d) Remove green grounding screw.
e) Unplug blue antenna lead.
f) Hold the top of the card guide and lift out.
To reinstall, reverse the above procedure.
D. Typical Applications and Wiring Diagrams
As follows:
LS7000 TERMINAL LAYOUT
•
*NOTE: EACH LS7000 POWER SUPPLY IS INTENDED FOR ONLY ONE SUPPLY VOLTAGE. THIS
VOLTAGE IS PRINTED ON THE POWER SUPPLY BOARD. FOR 115 VAC OR 230 VAC UNITS, HOOK UP THE
HOT LEAD TO L1 AND THE NEUTRAL TO L2, WITH APPROPRIATE GROUND. FOR 12 VDC OR 24 VDC
UNITS, HOOK THE POSITIVE VOLTAGE TO L1 AND THE COMMON OR GROUND TO L2.
FIGURE7.2
3
5 AMP RELAY CONTACTS
C2 NC2 NO2 NO1 NC1 C1 L2 L1 G
SUPPLYVOLTAGE*

4

TYPICAL WIRING APPLICATION
HIGHLEVELALARM
L1 115 VAC L2
L1 LS7000 L2 FAIL SAFE HIGH
SELECTED.
G
NC1 R HIGH LEVEL
ALARM LIGHT.
C1
FIGURE 7.4
NO1
TYPICAL WIRING APPLICATION
L1 115 VAC L2 AUTOMATIC FILLING OF TANK.
(WHEN LEVEL FALLS TO POINT “A”,
A PUMP COMES ON TO FILL TO
POINT “B”, THEN TURNS OFF.)
L1 LS7000 ”A” L2 FAIL SAFE LOW
SELECTED.
G
L1 LS7000 “B” L2 FAIL SAFE HIGH “B”
SELECTED.
G
LS7000 ALS7000 B
C1 NC1 C1 NO1 PUMP PUMP MOTOR
STARTER “A”
PUMP AUX. CONTACT PUMP
FIGURE 7.5

TYPICAL WIRING APPLICATION
L1 115 VAC L2 HIGH LEVEL ALARM USING
THE TIME DELAY TO IGNORE
SPLASHING OR WAVE ACTION.
(TIME ON, INSTANT OFF)
L1 LS7000 L2 FAIL SAFE HIGH
SELECTOR, ON,
G DELAY SET FOR
2 SECONDS
C1 NC1 R HIGH LEVEL
ALARM LIGHT. “A”
WHEN THE FLUID REACHES POINT “A”,
IT MUST REMAIN THERE FOR 2 SECONDS
BEFORE THE INDICATOR LAMP WILL
COME ON.
NOTE: PLEASE REVIEW FAIL SAFE
SELECTION INSTRUCTIONS,
SECTION IV B.
FIGURE 7.6
TYPICAL WIRING APPLICATION
L1 115 VAC L2
L1 LS7000 L2 FAIL SAFE HIGH
SELECTED, OFF
G DELAY SET FOR
ONE MINUTE.
C1 NC1 PUMP “A”
WHEN THE WATER LEVEL REACHES POINT “A”,
THE PUMP WILL TURN ON AND CONTINUE TO RUN
FOR 1 MINUTE AFTER THE WATER FALLS BELOW
THE PROBE. PUMP
NOTE: PLEASE REVIEW FAIL SAFE SELECTION
INSTRUCTIONS, SECTION IV B.
FIGURE 7.7

4. CALIBRATION
PLEASE READ THE ENTIRE CALIBRATION PROCEDURE BEFORE CALIBRATING THE LS7000.
If no time delay is required, turn the time adjustment pot completely CCW and set S1 down, S2 up. The
potentiometer has 18 turns and freewheels at the end of its travel without damage. You may hear “clicks” at the end
of travel.
A. Setting the Time Delay
1) Setting the timing mode, either on delay or off delay is done by positioning S3 and S4 as shown in the chart
below.
NOTE: S3 and S4 also select fail safe high level (FSH) or fail safe low level (FSL).
2) Select the timing range using S1 and S2 as shown on the chart below.
3) Adjust the time adjustment potentiometer clockwise to increase time or CW to decrease until the exact time
delay is arrived at. The test switch may be depressed to start the timing when checking timing sequence.
NOTE: For long timing ranges you can set the timer for a shorter range, then change the range
Switches (S1 and S2) to increase the time. For example, the desired time delay is 15
minutes. This is equal to 900 seconds. By setting S1 down and S2 up and adjusting the
timer to approximately 28 seconds, the ratio on this range is 1. To increase this range by
32, move S1 up and S2 up. 32x28 seconds equals approximately 15 minutes.
B. Fail Safe Selection
The fail safe feature provides a “false alarm” in case of power outage or major component failures. When
properly selected, the fail safe feature can protect equipment or alert you of a unit failure.
Fail Safe High (FSH) means that the relay is energized when NO PRODUCT is touching the probe. The green
led indicates relay status and is on when the relay is energized. When product comes into contact with the
probe, the relay is de-energized.
Fail Safe Low (FSL) means that the relay is energized when PRODUCT IS touching the probe.
NOTE: Due to the wide variety of applications and possible control or alarm functions, the proper
fail safe selection will depend on your circumstances. Please call your distributor or the factory if
you need assistance.
TIMING RANGE FAILSAFE TIMER MODE
S1 S2 TIME RATIO S3 S4
DN UP 1/8 sec - 35 sec 1 UP UP ON FSL
UP DN 1/2 sec - 140 sec 4 DN UP DELAY FSH
UP UP 4 sec - 18 min 32 DN DN OFF FSL
DN DN 32 sec - 2 hrs 260 UP DN DELAY FSH
C. Sensitivity Calibration
The LS7000 should be calibrated when no material is touching the probe and when the unit is installed where it
will be used.
1) Observe the red LED. If it is on, go to step 3.
2) If the red LED is off, turn the sensitivity adjustment potentiometer CW until it comes on.
3) Turn the sensitivity adjustment pot CCW until the red LED just goes out and continue to turn the pot CCW
at least ½ of a turn. This sets the unit to its maximum stable sensitivity. If in your application this is too
sensitive, you can turn the sensitivity adjustment pot further CCW. Always bring the product into contact
with the probe after calibration to assure proper performance.
NOTE: The green LED indicates relay status. The relay is energized when the green LED is on.
7

Every LS7000 has a diagram inside the screw cover to serve as a reminder to those who have calibrated the
unit before. This shows the calibration adjustments and indicators. This diagram is reproduced below.
SPECIAL CALIBRATION NOTES:
For some products, the LS7000 can be calibrated with product touching the probe. To do this, turn the
sensitivity adjust pot CW until the red LED just comes on and continue CW for 1/8 to ¼ of a turn. Always
check to see if the unit resets in the absence of product.
5. MAINTENANCE AND TROUBLESHOOTING
No routine maintenance is required other than keeping the interior of the unit clean and free of dirt, dust and other
contaminants.
The LS7000 consists of three main sub-assemblies. These are the enclosure with the antenna probe, the power
supply board and the sensing card. The following troubleshooting guide will assist in determining how to correct
most of the problems which may occur in the field. Review the Installation and Calibration procedures in sections 3
and 4.
PROBLEM POSSIBLE CAUSE SOLUTION
RED LED cannot be adjusted to
turn on.
Antenna lead not connected.
No power to unit.
Blown on-board fuse.
Bad sensing card.
Plug antenna lead into probe.
Check for correct power to unit.
Replace fuse.
Repair or replace card.
RED LED remains on at all times Antenna probe is shorted to case
or ground.
Bad sensing card.
Unplug banana plug and position
it so that the bare end is not
touching anything. Turn
calibration pot 20 turns CCW.
LED should go out. If it does,
repair, replace or clean antenna
probe. If LED does not go out,
replace electronics.
Repair or replace card.
Unit triggers when material
touches probe, but will not reset
when material recedes from probe
or unit and gives false alarm.
Improper mount of probe.
Improper calibration procedure.
Excessive material build-up on
probe.
Probe is mounted in flow of
material.
Contact factory or dist.
See section 4C.
Perform “dirty probe calibration”:
Recalibrate with built up material
on probe. See section 4C.
Revise mounting or use time
delay. See sec. 4A

Unit will not detect material.
Improper calibration.
Antenna lead not plugged into
probe.
Unit was calibrated with material
touching probe.
See calibration instructions,
section 4.
Plug antenna lead into probe.
Be sure material is not touching
probe and recalibrate.
Unit will not stay in calibration. Poor grounding of unit to vessel. Provide secure ground connection.
Relay operates properly, but no
signal at terminals.
Burned or broken lands on the
printed circuit board.
Bad relay contacts.
Turn off power. Remove module
from housing and inspect lands on
printed circuit for damage.
Replace if necessary.
Replace relay or return for repair.
PLEASE CONTACT THE FACTORY OR YOUR DISTRIBUTOR IF YOU HAVE ANY
QUESTIONS OR NEED ASSISTANCE.
6. WARRANTY
All components of the LS7000 are warranted to be free from defects in material and workmanship for a
period of two years from the date of purchase . This warranty applies to general purchaser and to
components installed, serviced and operated according to instructions.
Babbitt International, Inc. will repair or replace, at its option, FOB at its plant or any other location
designated, any part which proves to be defective in manufacture or workmanship.
All claims must be made in writing within the warranty period. No claims outside of the warranty period
will be honored.
Warranties are not applied to any components which have been damaged by improper installation, use,
exposure to unusual atmospheric conditions or components which have been misused, abused, damaged
by neglect or accident. This warranty shall not apply to any components which have been altered or
repaired without the prior written consent of Babbitt International, Inc.
Babbitt International, Inc. assumes no responsibility or liability for any labor or material back charges,
without written authorization. Any products returned must be with prior written authorization.
THE FOREGOING IS IN LIEU OF ALL OTHER WARRANTIES, EXPRESSED OR IMPLIED,
INCLUDING ANY WARRANTIES OF MERCHANTABILITY AND/OR FOR FITNESS FOR
PARTICULAR PURPOSE, AND BABBITT INTERNATIONAL, INC. ASSUMES NO OTHER
LIABILITIES EXPRESSED OR IMPLIED. BABBITT INTERNATIONAL, INC. SHALL NOT BE
LIABLE FOR NORMAL WEAR AND TEAR, NOR FOR DIRECT, INCIDENTIAL OR
CONSEQUENTIAL DAMAGES. IN NO EVENT SHALL BABBITT INTERNATIONAL
INCORPORATED’S LIABILITY EXCEED THE PRICE OF ITS PRODUCT AT THE TIME OF
PURCHASE.
9
Other manuals for LS7000
1
Table of contents
Other BABBITT Switch manuals
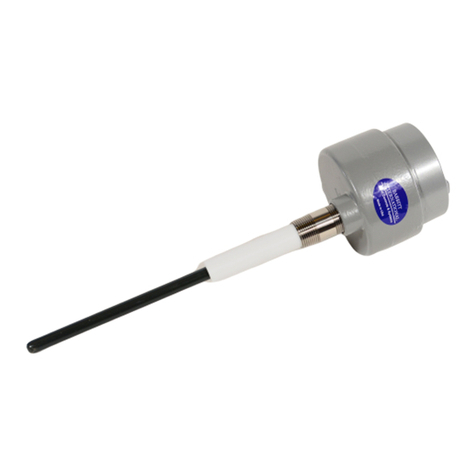
BABBITT
BABBITT LS7000/2 User manual
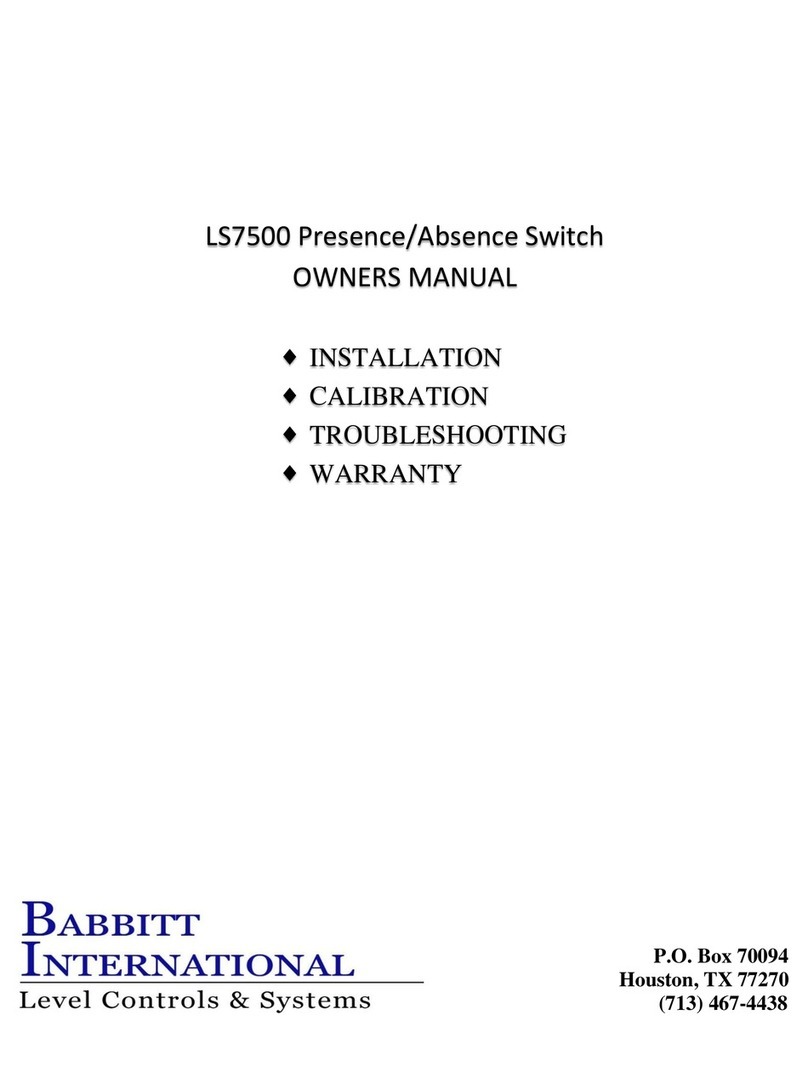
BABBITT
BABBITT LS7500 User manual
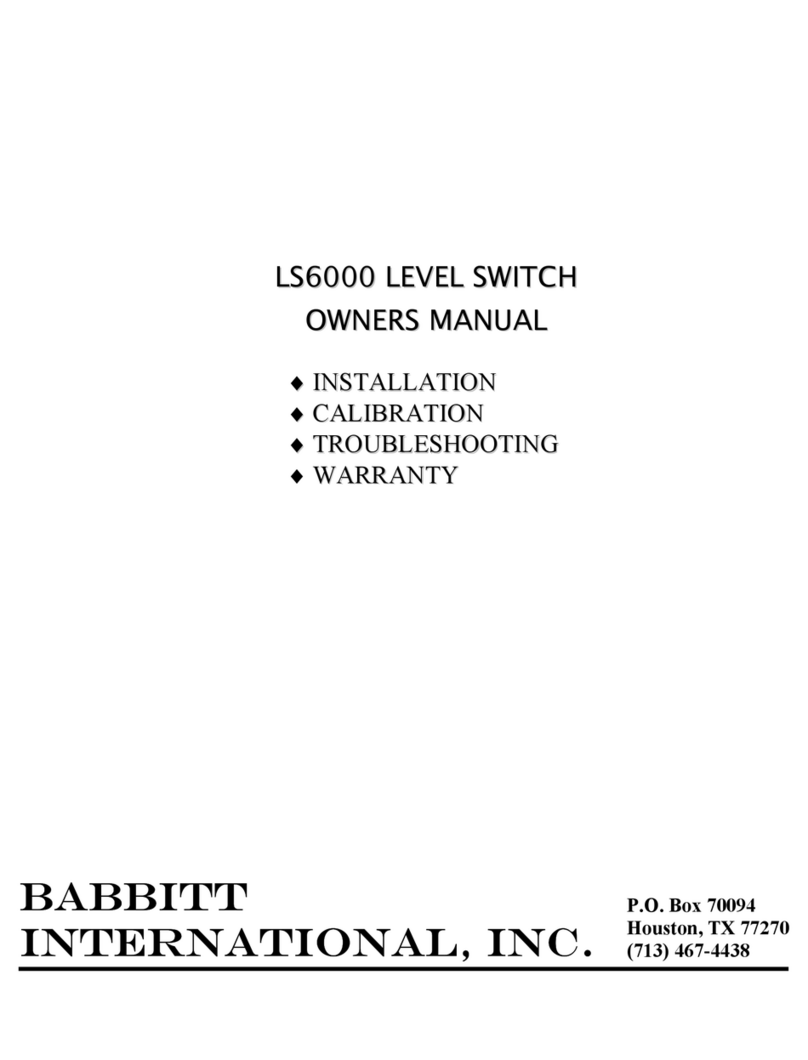
BABBITT
BABBITT LS6000 User manual
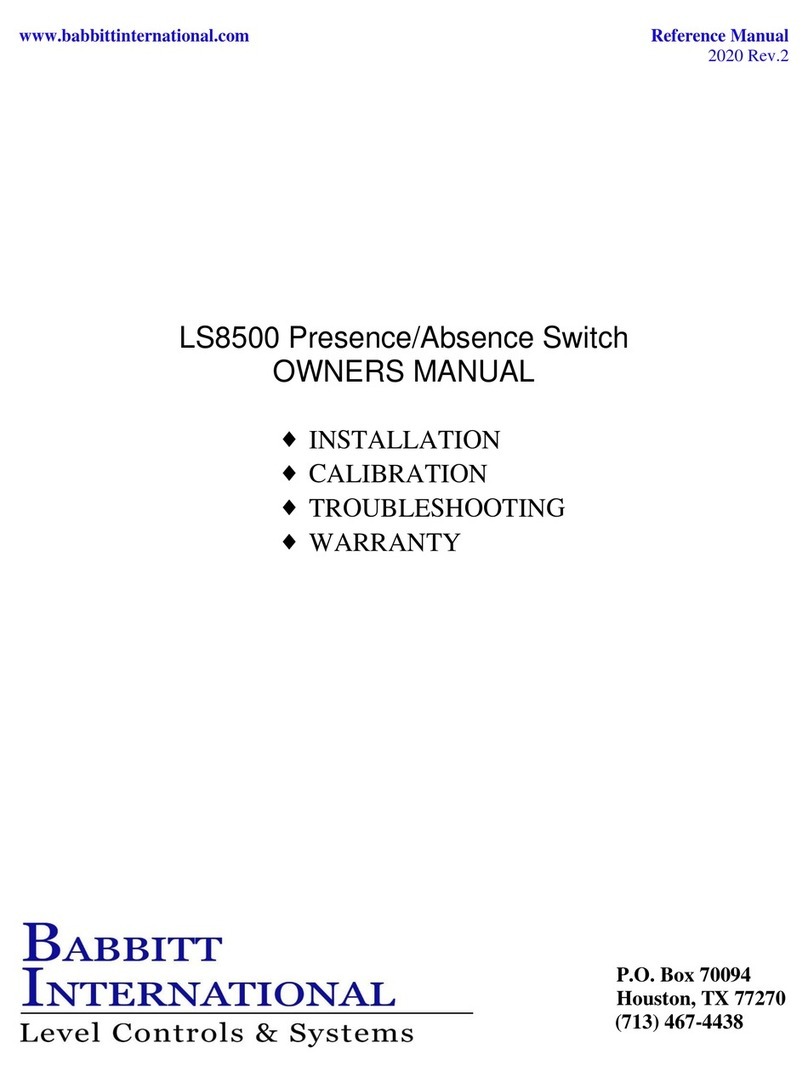
BABBITT
BABBITT LS8500 User manual
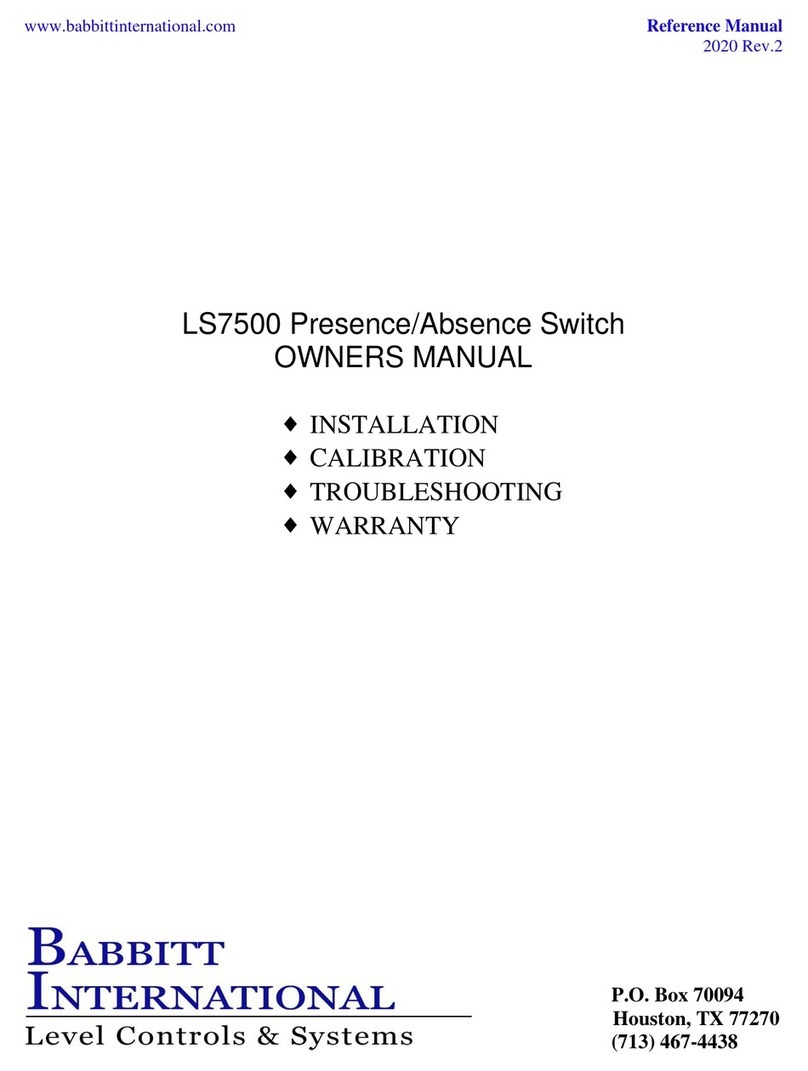
BABBITT
BABBITT LS7500 User manual

BABBITT
BABBITT LS8000/2 User manual
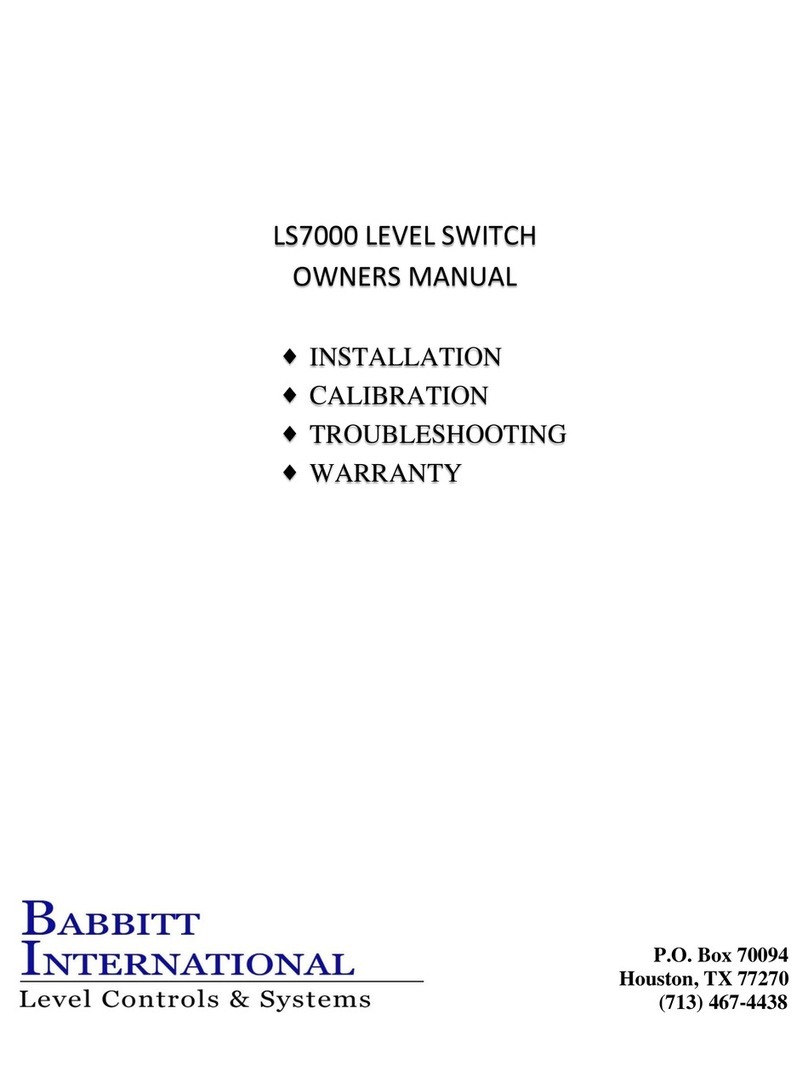
BABBITT
BABBITT LS7000 User manual

BABBITT
BABBITT LS8500 User manual
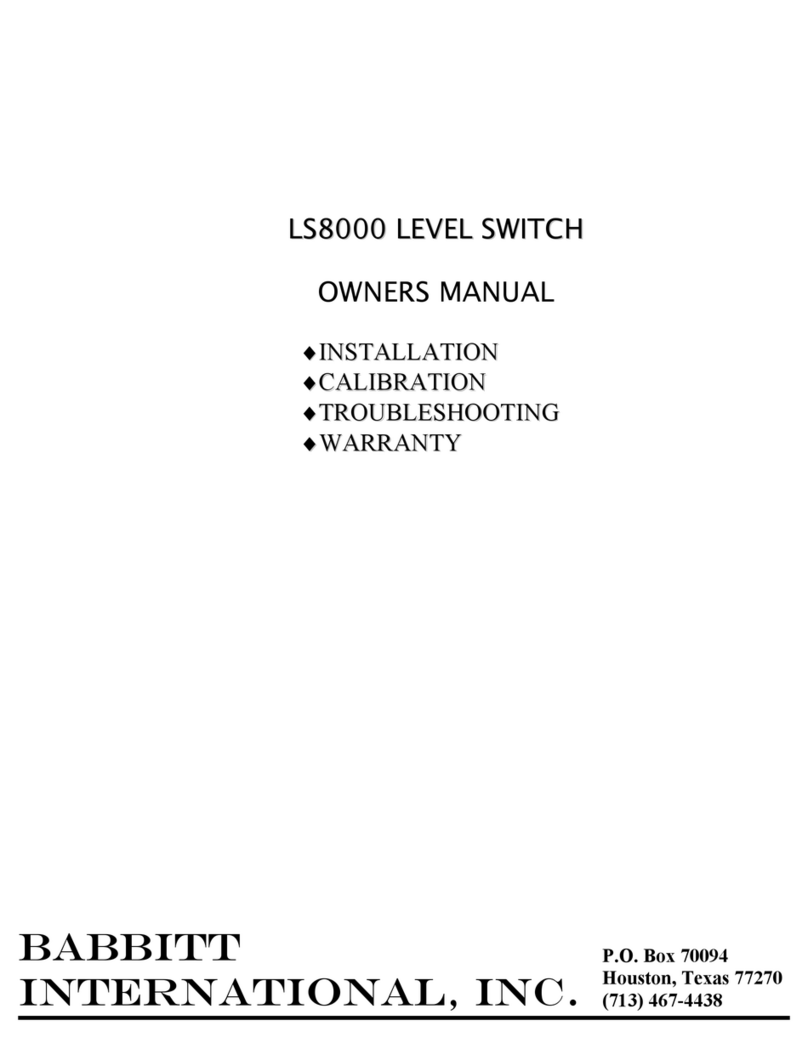
BABBITT
BABBITT LS8000 User manual
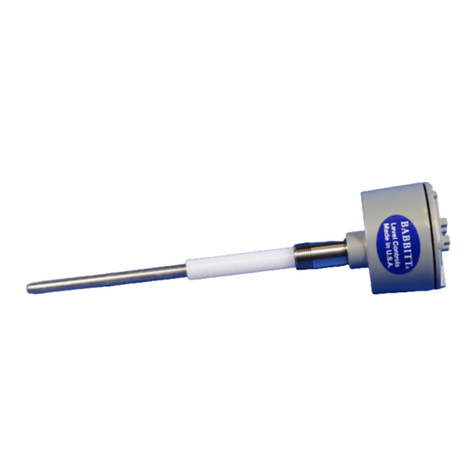
BABBITT
BABBITT LS2000 User manual
Popular Switch manuals by other brands
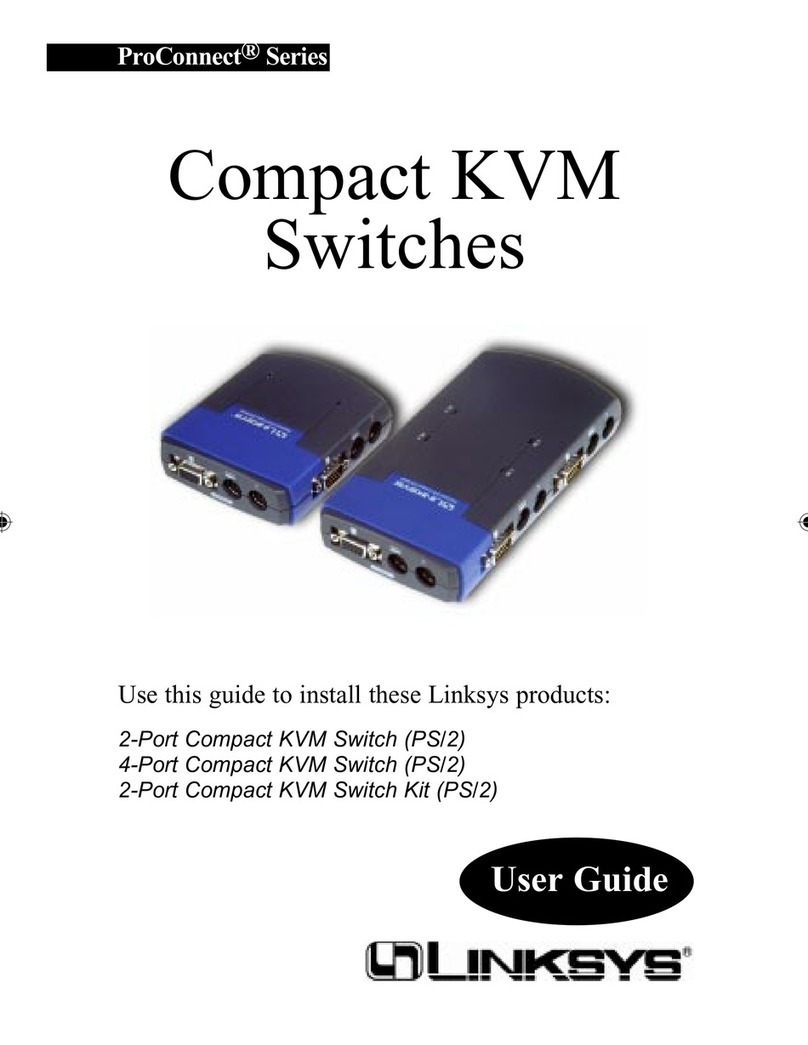
Linksys
Linksys ProConnect Series user guide

HP
HP JG640A Quickspecs

Chore-Time
Chore-Time 56310 Installation and operator's manual
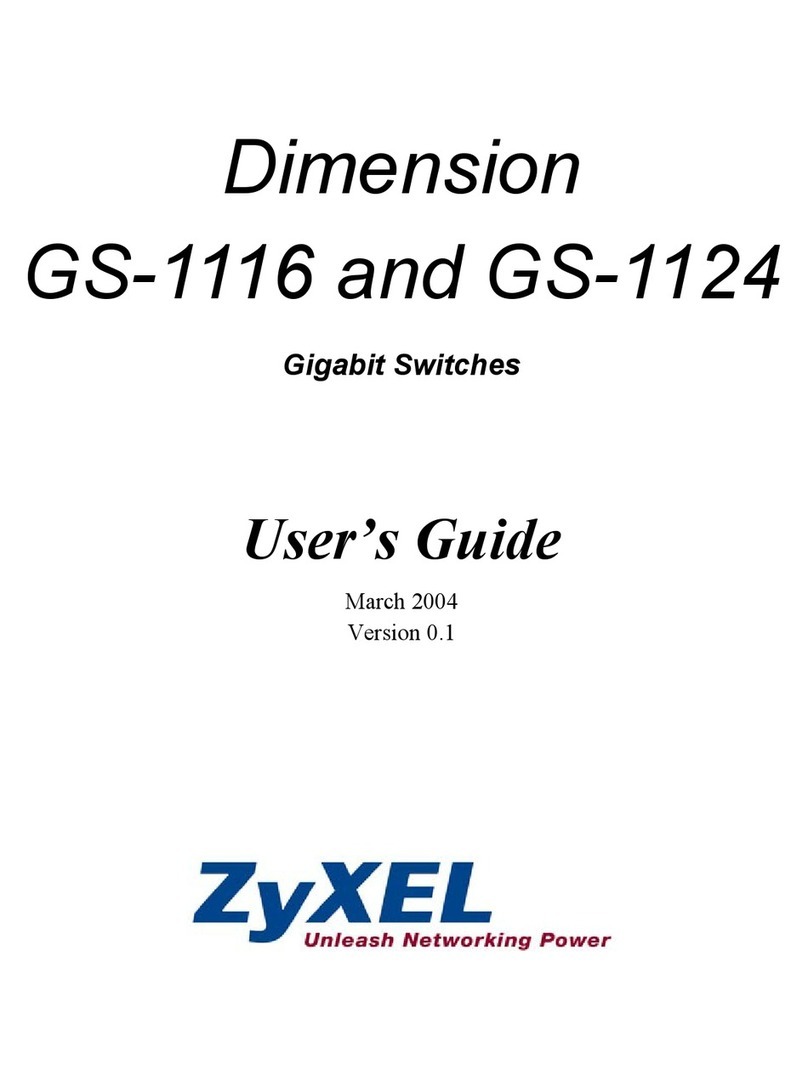
ZyXEL Communications
ZyXEL Communications Dimension GS-1116 user guide

Canyon
Canyon CN-D05P user guide
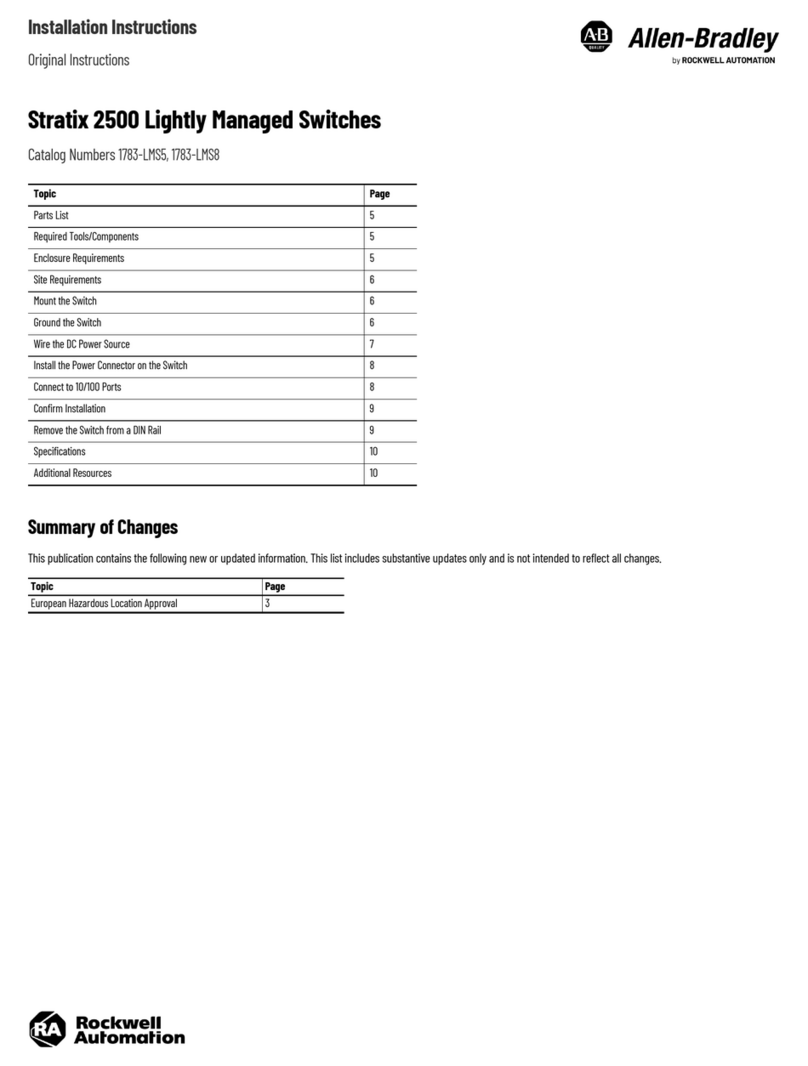
Rockwell Automation
Rockwell Automation Allen-Bradley Stratix 2500 installation instructions