BAC RC Series Manual

OPERATION & MAINTENANCE MANUAL
RC Series

Construction Details

Construction Details
Figure 1. Typical cross section

Warnings
• WARNING: Do not perform any service on or near the fans, motors, and drives, or inside the unit
without rst ensuring that the fans and pumps are disconnected, locked out, and tagged out.
• WARNING: Check to ensure the controls for the fan motor are set to allow a maximum of six on-off
cycles per hour to prevent motor overload.
• WARNING: Openings and/or submerged obstructions may exist in the bottom of the cold water basin.
Use caution when walking inside this equipment.
• WARNING: The top horizontal surface of the unit is not intended to be used as a walking surface or
working platform. If access to the top of the unit is desired, the purchaser/end-user is cautioned to
use appropriate means complying with applicable safety standards of governmental authorities.
• WARNING: Drift eliminators on RC Series units are not designed to support the weight of a person or
to be used as a storage or work surface for any equipment or tools.
• WARNING: When the fan speed of the unit is to be changed from the factory set speed, including
changes achieved by the use of a variable fan speed device, steps must be taken to avoid operation
at or near the fan’s “critical speed” which could result in fan failure and possible personal injury
or damage. Contact your local BAC Representative regarding any such applications. Additionally,
inverter duty motors are required on installations that are to be controlled by VFDs.
• WARNING: The re-circulating water system may contain chemicals or biological contaminants,
including Legionella, which could be harmful if inhaled or ingested. Personnel exposed directly
to the discharge airstream and the associated drift mists, generated during operation of the water
distribution system and/or fans, or mists produced by high pressure water jets or compressed air
(if used to clean components of the re-circulating water system), must wear respiratory protection
equipment approved for such use by governmental occupational safety and health authorities.
• WARNING: The basin heater is not designed to prevent icing during unit operation.
General Maintenance Information
The services required to maintain a piece of evaporative cooling equipment are primarily a function of the
quality of the air and water in the locality of the installation:
• AIR: The most harmful atmospheric conditions are those with unusual quantities of industrial smoke,
chemical fumes, salt, or heavy dust. Such airborne impurities are carried into the equipment and
absorbed by the re-circulating water to form a corrosive solution.
• WATER: The most harmful conditions develop as water evaporates from the equipment, leaving behind the
dissolved solids originally contained in the make-up water. These dissolved solids may be either alkaline or
acidic and, as they are concentrated in the circulating water, can produce scaling or accelerated corrosion.
The extent of impurities in the air and water determines the frequency of most maintenance services and
also governs the extent of water treatment which can vary from a simple continuous bleed and biological
control to a sophisticated treatment system.

Cautions
• CAUTION: BAC units are typically installed immediately after shipment and many operate year round.
However, if the unit is to be stored for a prolonged period of time either before or after installation,
certain precautions should be observed. For instance, covering the unit with a clear plastic
tarpaulin during storage can trap heat inside the unit, potentially causing damage to the ll and
other components. If units must be covered during storage, an opaque, reective tarp should be
used. For normal seasonal shutdowns, refer to the applicable section in this manual.
• CAUTION: All electrical, mechanical, and rotating machinery are potential hazards, particularly for
those not familiar with their design, construction, and operation. Accordingly, use appropriate
lockout procedures. Adequate safeguards (including the use of protective enclosures where
necessary) should be taken with this equipment both to safeguard the public from injury and to
prevent damage to the equipment, its associated system, and the premises.
• CAUTION: When reversing the direction of fan rotation, allow the fan to come to a complete stop
before restarting the motor.
• CAUTION: Do not use oils containing detergents for bearing lubrication. Detergent oils will remove the
graphite in the bearing sleeve and cause bearing failure. Also, do not disturb bearing alignment by
tightening the bearing cap adjustment on a new unit, as it is torque adjusted at the factory.
• CAUTION: Do not use steam or high pressure water to clean PVC eliminators or materials other than steel.
• CAUTION: This equipment should never be operated without all fan screens, access panels, and access
doors in place. For the protection of authorised service and maintenance personnel, install a lockable
disconnect switch located within sight of the unit on each fan motor associated with the equipment.
• CAUTION: Mechanical and operational methods must be employed to protect these products
against damage and/or reduced effectiveness due to possible freeze-up. Contact your local BAC
Representative for recommended protection alternatives.
• CAUTION: Pressure greater than 69 kPa may cause damage to the distribution system.
• CAUTION: Never use chloride or chlorine based solvents such as bleach or muriatic (hydrochloric)
acid to clean stainless steel. It is important to rinse the surface with warm water and wipe with a
dry cloth after cleaning.
• CAUTION: All cooling equipment should be located as far away as possible from occupied areas,
open windows or air intakes to buildings.
• CAUTION: Installation and operation of cooling equipment may be subject to local regulations,
such as establishment of risk analysis. Ensure legislative and regulatory requirements are
consistently met.
Warranties
Please refer to the Limitation of Warranties in the submittal packet applicable to and in effect at the time
of the sale/purchase of these products. Described in this manual are the recommended services for start-
up, operation, and shutdown, and the approximate frequency of each.

Recommended Maintenance Service
WARNING: Do not perform any
service on or near the fans, motors
and drives, or inside the unit
without rst ensuring that the fans
and pumps are disconnected and
tagged out.
NOTES:
1. Recommended service intervals are the minimum for typical installations.
Different environmental conditions may dictate more frequent servicing.
2. When operating in ambient temperatures below freezing, the unit should be
inspected more frequently.
3. Tension on new belts must be readjusted after the rst 24 hours of
operation and quarterly, thereafter.
Table 1. Recommended Maintenance Services for RCC & RCF Units.
Inspect and clean as necessary: Start-Up Monthly Quarterly Annually Shutdown
Inspect general condition of the unit[2] and check unit
for unusual noise or vibration
Inspect cold water basin
Flush water distribution system/Inspect spray nozzles
Drain basin and piping
Inspect combined inlet shields
Check and adjust water level in basin(s)
Check operation of make-up valve
Inspect coil
Check and adjust bleed rate
Inspect tower nish
Mechanical equipment system: Start-Up Monthly Quarterly Annually Shutdown
Check belt condition
Adjust belt tension[3}
Lubricate fan shaft bearings
Lubricate motor base adjusting screw
Check drive alignment
Check motor voltage and current
Clean fan motor exterior
Check fan motor for proper rotation
Check general condition of the fan
Check and unplug fan drain holes (hollow blade fans)
Check fan for uniform pitch
Check fan for rotation without obstruction
Check and recoat steel shafts with RUST VETO®

1
WWW.BALTIMOREAIRCOIL.COM.AU
MAR210-2
Table of Contents
Construction Details
Warnings and Cautions
PART 1 Operation and Maintenance
3 Initial & Seasonal Start-Up
5 Extended Shutdown
6 Prolonged Outdoor Storage
PART 2 Detailed Component Maintenance Procedures
10 Cold Water Basin
11 Fan
12 Fan Drive System (Belt Direct Drive Units)
14 Fan Drive System (Direct Drive)
15 Fan Motors
16 Fan Shaft Bearings
17 Locking collars
17 Fan Shaft
18 Access Door
18 Louvres and Eliminators
19 Water Distribution and Heat Transfer Section
20 Water Level Control
PART 3 Corrosion Protection
23 Water Treatment
24 Corrosion and Scale Control
25 Biological Control
25 Gray Water and Reclaimed Water
26 Chemical Treatment Requirements
26 Passivation
27 Long Term Care of Stainless Steel
28 System Cleaning
PART 4 Bleed Rate
PART 5 Cold Weather Operation
33 Inspection and Maintenance
33 Fan Section Icing Protection
34 Basin Water and Internal Piping Freeze Protection
35 Coil Freeze Protection
PART 6 Factory Authorised Parts
37 The Perfect Fit
OPERATIONS & MAINTENANCE » RC SERIES

RC SERIES
Operation and Maintenance
INITIAL AND SEASONAL START -UP
EXTENDED SHUTDOWN
PROLONGED OUTDOOR STORAGE
1

3
WWW.BALTIMOREAIRCOIL.COM.AU
MAR210-2
RC SERIES
Operation and Maintenance
INITIAL AND SEASONAL START -UP
EXTENDED SHUTDOWN
PROLONGED OUTDOOR STORAGE
Operation and Maintenance
Initial & Seasonal Start-Up
General
Cleaning
Inspection
Initial & Seasonal Start-Up
General
• If the unit is mounted on vibration isolators or isolation rails (by
others), refer to the vibration isolation manufacturer’s guidelines
before loading/unloading weight from the unit.
• Verify fan and unit pump motors are disconnected, locked out, and
tagged out.
Cleaning
• Drain the cold water basin with the strainer in place.
• Remove all dirt and debris from the fan guard(s).
• Flush the water distribution system. Inspect and clean all spray nozzles.
• Clean all of the mechanical components, such as the fan and motor.
• Flush the cold water basin to remove any accumulated dirt and debris.
• Remove, clean, and replace the basin strainer.
Inspection
• Conduct external inspection of the equipment. Check for leaks,
corrosion, and any structural damage.
• Conduct internal inspection of the equipment. Check for anything
unusual such as structural or mechanical component damage.
• Inspect piping and connections.
• Thoroughly inspect the fan(s) for any mechanical or physical damage.
• At seasonal start-up or after prolonged shutdown, check the motor
insulation with an insulation tester prior to the motor start-up.
• For belt driven units, prior to seasonal start-up, check and adjust
the belt tension. At the initial start-up, the belt tension may not
require adjustment as the drive will be properly tensioned at the
factory prior to shipment.
WARNING: Do not perform any
service on or near the fans,
motors, and drives, or inside
the unit without rst ensuring
that the fans and pumps are
disconnected, locked out, and
tagged out.

4
WWW.BALTIMOREAIRCOIL.COM.AU
MAR210-2
CAUTION: Pressure greater than
69 kPa may cause damage to
the distribution system.
After 24 hours of operation
under thermal load, perform the
following services:
9Check the unit for any
unusual noise or vibrations.
9Check the operating water
level in the cold water basin.
9Adjust make-up valve if
necessary.
9Check the belt tension and
readjust if necessary.
9Inspect the spray nozzles
and heat transfer section.
Start-up
• Prior to seasonal start-up, lubricate the motor base adjusting
screw(s) and fan shaft bearings. At initial start-up, no bearing
lubrication is required since the bearings are factory lubricated prior
to the shipment.
• Apply RUST VETO® to steel shafts.
• Fill the cold water basin with fresh water up to the overow level via
the make-up valve.
–Water Treatment for New Installations: Initiate the biocide water
treatment program at this time.
–Water Treatment for Seasonal Start-up or after a Shutdown
period in excess of three days: Resume the biocide treatment
program or administer a shock treatment of appropriate biocides
prior to operating the cooling tower fans. This will eliminate
accumulated biological contaminants.
• Set the make-up valve oat so the water shuts off at the overow level.
• Start the unit pump and check for the proper rotation indicated by
the arrow on the pump cover.
• On installations where the unit pump was not furnished by BAC,
a globe valve should be installed in the pump discharge line and
the pump ow rate adjusted to the correct water ow and pressure
(2.25 psig at spray header connection).
• Check that the oat operated make-up valve is operating freely.
Closely monitor water level and adjust as necessary during the rst
24 hours of operation.
• Check the nozzle spray pattern as described in “Water Distribution
System and Heat Transfer System” on Page 19.
• Open the valve in the tower bleed line, and adjust the bleed by
closing or opening the valve.
• Verify fan tip clearance is between 3mm and 13mm.
• For initial start-up, bump the fan motor and note the direction of
rotation. Start the fan motor(s) and verify proper fan rotation without
obstruction. The fan(s) should rotate in the direction indicated by
the arrow on the fan cowl.
• Run the fan in manual mode for several minutes to check for any
unusual noise or vibrations.
• For a 2-speed motor, check to ensure the starter includes 15 second
time delay when switching from high speed to low speed.
• Check the operation of the optional vibration cutout switch.
• Once the cooling tower is operating, check the current and the
voltage of all three phases (legs) of the fan motor with a heat load
on the tower under warm ambient conditions. The current must not
exceed the nameplate ratings.

5
WWW.BALTIMOREAIRCOIL.COM.AU
MAR210-2
Extended Shutdown
Perform the following services whenever the unit is shutdown in
excess of three days:
• If the unit is mounted on vibration isolators or isolation rails (by
others), refer to the manufacturer’s guidelines before loading/
unloading weight from the unit.
• Disconnect, lock-out, and tag-out all fans and pumps.
• Close the shut-off valve in the make-up water line (supplied by
others), and drain the cold water basin and all exposed water
piping. Heat trace and insulate all exposed piping.
• Clean all the debris, such as leaves and dirt, from the interior and
exterior of the unit.
• Leave the cold water basin drain open so rain and melting snow will
drain from the unit.
• Clean the basin strainer and re-install.
• Cover the fan discharge to keep out dirt and debris.
• For belt driven units, lubricate the fan shaft bearings, motor base,
and motor base adjusting screw.
• Apply RUST VETO® to steel shafts.
• Inspect the protective nish on the unit. Clean and renish as required.
• Maintain the fan motor starting device in the “OFF” position to
ensure personal safety in the case of future inspection or service.
Operation and Maintenance
Initial & Seasonal Start-Up
Start-up
Extended Shutdown
WARNING: Rapid on-off cycling
can cause the fan motor to
overheat. It is recommended that
controls be set to allow a max of 6
on-off cycles per hour.

6
WWW.BALTIMOREAIRCOIL.COM.AU
MAR210-2
Prolonged Outdoor Storage
Storage Preparation
• Conduct the “Extended Shutdown” procedure on page 5 if the unit is
installed.
• Ensure the cold water basin is fully drained and the drain is open.
• For storage prior to installation, all components and accessories,
which sometimes ship inside the unit and are not a permanent xture
in the basin, should be removed and stored indoors.
• Remove the bottom drain plug to the spray pump(s). Put the plug(s)
in a marked plastic bag and attach to the spray pump(s) for future use.
• Remove and store fan belts (if supplied) at room temperature, keeping
matched belts together. Tag belts appropriately for future identication.
Precautions for RCF Closed Circuit Cooling Towers
- RCF Storage Prior to Installation - The unit’s coil connections
should remain capped for the duration of storage.
- RCF Installed and Piped but not Filled - This unit does not
require additional precautions.
- RCF Unit Installed and Operated - This unit should remain lled.
If the unit is stored in a freezing climate, the coil must be
protected from freezing. For protection against coil freeze-up,
use of an inhibited glycol solution is recommended. If protecting
the coils with glycol is not possible, the galvanized steel coils
should be drained completely and capped once as much water
and moisture is removed from the coil as possible.
Precautions for RCC Evaporative Condensers
- RCC Storage Prior to Installation - The coils are charged with
nitrogen at 100kPa at the factory.
- RCC Extended Shutdown Periods after Start-Up - The coils
should be charged with nitrogen at 100kPa in the eld and
capped by adding a threaded connection or a welded cap. Upon
start-up, the coil connections will require cutting and bevelling.
• Apply a weather-resistant lubricant or heavy grease such as Anti-Seize
(BAC Part # 160069) to all exposed threaded or anged connections
and the adjustable motor base threaded rod.
• Insert desiccant bags into the control panel (if supplied) to absorb
moisture. Seal the control panel for storage.
• Spray coat electrical component housings (if supplied) with a suitable
protective coating, such as Cosmoline® Weathershed, and individually
cover them with plastic, taking care to leave openings for free air
circulation.
• Inspect the protective nish on the unit. Clean and renish as required.
Refer to “Corrosion Protection” on page 24 for more details.

7
WWW.BALTIMOREAIRCOIL.COM.AU
MAR210-2
Motor Recommendations
BAC standard motors are designed for storage at ambient temperatures
of -20ºC to 40ºC. Prolonged periods of exposure above or below these
specied conditions could degrade components of the motor and cause
malfunction or premature failure.
• Motors should be removed and stored inside whenever possible.
When indoor storage is not possible the motors must be covered
with a tarpaulin. Do not use plastic or plastic lm. This cover should
extend below the motor and be secured; however, it should not
tightly wrap the motor. This will allow the captive air space to
breathe, minimizing formation of condensation.
• Care must also be taken to protect the motor from ooding or from
harmful chemical vapors.
• The storage area should be free from ambient vibration. Excessive
vibration can cause bearing damage. Motors that must be stored in
areas with high ambient vibration, such as from heavy construction
equipment or other sources, must have the shaft locked to prevent
any movement.
• Precautions should be taken to prevent rodents, snakes, birds, or
other small animals from nesting inside the motors. In areas where
they are prevalent, precautions must also be taken to prevent
insects from gaining access to the interior of the motor.
• If not stored indoors in a controlled environment, some form of
heating must be utilized to prevent condensation from accumulating
in the motor. This heating should maintain the winding temperature
at a minimum of 5ºC above the ambient temperature
of the room, keeping it from dropping below the dew point where
condensation could form inside the motor. If space heaters are
supplied, they should be energized. If none are available, single
phase or “trickle” heating may be utilized by energizing one phase
of the motor’s winding with a low voltage. Request the required
voltage and transformer capacity from your local BAC Representative.
A third option is to use an auxiliary heat source and keep the
winding warm by either convection or blowing warm air into the motor.
Operation and Maintenance
Prolonged Outdoor Storage
Storage Preparation
Motor Recommendations

8
WWW.BALTIMOREAIRCOIL.COM.AU
MAR210-2
Maintenance Requirements
• Rotate all fans and motor shafts monthly by hand. Hand-turning
will ensure that the shafts and bearings are free and will
redistribute grease within the bearings.
• Inspect the cold water basin monthly to ensure that the drain is
open and remove any leaves or debris that may have accumulated
in the cold water basin.
• Inspect the axial fan(s) annually to ensure the blades are tight and
there is no obvious corrosion between the hub and the fan blade
• Inspect the rust preventative coating on all motor external
machined surfaces including shaft extensions monthly. If necessary,
re-coat the surfaces with RUST VETO®.
Start-Up Preparation After Prolonged Storage
Keep in mind that start-up procedures after long periods of storage are
just as important as pre-shutdown procedures.
• The motor should be thoroughly inspected, cleaned, and restored to
its pre-storage condition.
• Inspect axial fans prior to start-up to ensure that the blades are
tight and that there is no obvious corrosion between the hub and
the fan blade. Do not energize the fans if there is obvious corrosion
of fan components. Loose fan blades could result in fan failure and
possible injury or damage.
• Reinstall all fan belts, motors, door gaskets, and drain plugs (as
applicable), and remove all protective coverings.
• For units stored prior to installation, conduct rigging procedures as
directed in the unit’s Rigging and Assembly Instructions, available
on www.BaltimoreAircoil.com.au or by contacting your local BAC Rep.
• Perform an insulation test of motor windings to ensure satisfactory
insulation resistance.
• Conduct full start-up procedure as stated in the “Start-Up
Procedure” on page 4. Be especially thorough for cleaning and
inspection prior to start-up.

2
RC SERIES
Detailed Component
Maintenance Procedures
COLD WATER BASIN
FAN
FAN DRIVE SYSTEM (BELT DRIVE UNITS)
FAN DRIVE SYSTEM (DIRECT DRIVE UNITS)
FAN MOTORS
FAN SHAFT BEARINGS
LOCKING COLLARS
FAN SHAFT
ACCESS DOOR
LOUVRES AND ELIMINATORS
WATER DISTRIBUTION AND HEAT TRANSFER SECTION
WATER LEVEL CONTROL

10
WWW.BALTIMOREAIRCOIL.COM.AU
MAR210-2
WARNING: Openings and/or
submerged obstructions may exist
in the bottom of the cold water
basin. Use caution when walking
inside this equipment.
WARNING: Do not use acid to
clean the strainers.
Cold Water Basin
As water circulating through the cooling tower is cooled, it collects in the
cold water basin and passes through the suction strainer into the system.
Water Levels
Model Number At Overow Level (mm) At Operating Level (mm)
All RC models (except RC*-1111) 443 343
RC*-1111 548 448
Table 1. Cold Water Basin Water Levels
• The values shown in Table 1 are relative to the base of the unit.
• The make-up valve controls the operating level, which is maintained
at the levels shown in Table 1.
• The operating water level in the cold water basin will vary with
system thermal load (evaporation rate), the bleed rate employed,
and the make-up water supply pressure.
• Check the operating water level monthly, and readjust the oat
when necessary to maintain the recommended operating level.
• Consult “Water Level Control” on Page 20 for information on how to
set and maintain basin operating level.
Inspection & Maintenance
• Inspect the cold water basin regularly. Remove trash or debris
accumulated in the basin or on the strainer.
• Quarterly or more often if necessary, drain, clean, and ush the
entire cold water basin with fresh water. This will remove the
sediment, which can collect in the basin during operation. If not
removed, sediment can become corrosive and cause deterioration of
the basin as well as be a potential area for biological growth.
• When ushing the basin, leave the strainer in place to prevent the
sediment from re-entering the system.
• Remove the strainer after the basin has been ushed.
• Clean and replace the strainer before relling the basin with
fresh water.
• Adjust the oat to maintain the design operating level. See Table 1.
Figure 2. Water Operating Level

11
WWW.BALTIMOREAIRCOIL.COM.AU
MAR210-2
Detailed Component
Maintenance Procedures
Cold Water Basin
Water Levels
Inspection & Maintenance
Fan
Inspection & Maintenance
WARNING: Do not perform any
service on or near the fans,
motors, and drives, or inside
the unit without rst ensuring
that the fans and pumps are
disconnected, locked out, and
tagged out.
WARNING: Check to ensure the
controls for the fan motor are set
to allow a maximum of six on-off
cycles per hour to prevent motor
overload.
Fan
Due to its size and speed, the fan has great potential for injury and
destruction if damaged. Inspect closely, and as required, replace
damaged or deteriorating members.
Inspection & Maintenance
• If the unit is already in operation, while the fan is running, check for
any unusual noise or vibration.
• With the fan off and the motor locked out and tagged out, check the
general condition of the fan:
–Inspect for any loose or missing bolts in the fan shaft bushing,
the fan hub, and the fan shaft bearing(s).
–Check the fan blades for looseness, rst by twisting the blade
by hand, and then by moving the blade tip up and down. There
should be no play or slippage.
–Inspect each blade for excessive scale build-up that could
cause vibration.
–Check each blade in the area of the shank for any signs of
cracking. If cracking is found, the fan motor should be locked
out immediately. Contact your local BAC Representative for
assistance.
• Tip Clearance: Check the clearance between the tip of the blade and
the fan cowl. The clearance should be between 3mm and 13mm.
• Blade Pitch: Check to ensure that the blades are all at the same
pitch. If uncertain, measure the pitch with an inclinometer. All
blades should be within 1/2° of each other.
• Rotation: Turn the fan by hand to ensure that it moves freely with
no rough spots, binding, or other malfunctions that could cause
vibration or fan motor overload. While rotating the fan, check the
blade tracking. All blades should track within a 13mm band at any
single point around the cowl.
• Direction of Rotation: On initial start-up, or if the fan motor has
been rewired, bump the fan motor and note the direction of
rotation. It should rotate in the direction indicated by the arrow on
the fan cowl.
• Operation: On initial start-up, run the fan in the manual position for
several minutes and check for any unusual noises or vibration.

12
WWW.BALTIMOREAIRCOIL.COM.AU
MAR210-2
Fan Drive System (Belt Drive Units)
Belt Drive Power Train
The drive train consists of SPB belts, a fan sheave and a motor sheave.
The high efciency belts provide the premium quality necessary for
evaporative cooling equipment.
Together these components provide a highly reliable system with
low maintenance requirements. The drive train should be inspected
periodically to check the belt tension, condition of the sheaves and
belt, and when necessary adjust the tension. The recommended service
intervals are specied elsewhere.
Inspection & Maintenance
The belt drive power train requires a periodic check of belt condition
and, when necessary, tension adjustment. The recommended service
intervals are as follows:
• Initial Start-Up:
–If the equipment was supplied in assembled major sections,
no servicing is required prior to initial startup since the drive
has been tensioned and aligned at the factory. If equipment
was supplied completely knocked down (CKD) then check drive
alignment & belt tensioning as per procedures outlined below.
• Seasonal Start-Up: Readjust the tension on the belt.
• Operation: After the rst 24 hours of operation, readjust the
belt tension on a new unit start-up or installation of a new belt.
Thereafter, check the belt condition monthly, and adjust tension as
necessary. Readjust tension at least once every three months.
Figure 3a. Belt Tension with a Straight Edge Figure 3b. Belt Tension with a Tape Measure
WARNING: No service work should
be performed on the drive train
without rst ensuring the fan
and pump motors have been
isolated, tagged and locked in
the off position.
6mm to 9mm 6mm to 9mm

13
WWW.BALTIMOREAIRCOIL.COM.AU
MAR210-2
Detailed Component
Maintenance Procedures
Fan Drive System
(Belt Drive Units)
Belt Drive Power Train
Inspection & Maintenance
• Belt tension check:
–Place a straight edge along the belt from sheave to sheave as
shown in Figure 3a, or use a tape measure as shown in Figure
3b to measure belt deection.
–Apply a moderate force by hand (approximately 2kg) evenly
across the width of the belt in the centre of the span between
the sheaves.
–There is adequate belt tension if the belt deects between 6mm
and 9mm as shown in Figures 3a and 3b.
–
• Belt tension adjustment (if required):
1. Loosen the motor pulley guard retaining nuts.
2. Loosen the lock nuts on the Motor Base Adjusting Screws.
3. Turn the Motor Base Adjusting Screws clockwise to tension the
belt, or counterclockwise to relieve belt tension. During adjustment
of belt tension the drives should be rotated several times by hand
to evenly distribute the tension throughout the belt.
4. When the belt is properly tensioned, retighten the locking nuts
on the Motor Base Adjusting Screws.
5. Tighten guard nuts.
Note: There should be no “chirp” or “squeal” when the fan motor is started.
NOTE: There should be no “chirp”
or “squeal” when the fan motor
is started.
Figure 4. Adjustable Motor Base (cover removed)
Motor Base
Locking Nuts
(both sides)
Adjusting
Screws

14
WWW.BALTIMOREAIRCOIL.COM.AU
MAR210-2
Figure 5. Drive Alignment
WARNING: Check to ensure the
controls for the fan motor are
set to allow a maximum of six
on-off cycles per hour to prevent
motor overload.
Alignment
• Check the drive alignment annually to ensure maximum belt life.
• Drive alignment check and adjustment:
–Place a straight edge across the driver and the driven sheaves as
shown in Figure 5.
–The straight edge should contact all four points as shown in
Figure 5 indicating that the drives are properly aligned.
–There should be no more than 1.5mm deviation from four points
of contact.
–In case of realignment, loosen the motor sheave and align it with
the fan sheave. Allow 6mm for draw-up as the bushing screw is
retightened.
Fan Drive System (Direct Drive Units)
Drive Train
The standard fan motor used
on direct driven units is a
TEAO (Totally Enclosed Air
Over) motor. The motor has
permanently lubricated ball
bearings and special moisture
protection on the bearings,
shaft, and windings. The only
servicing required during
operation is to clean the outside
surface of the motor at least
quarterly to ensure proper
motor cooling. After prolonged
shutdowns, the motor insulation
should be checked with a
“megger” insulation tester
before restarting the motor.
Figure 6. Belt Tensioning
Other manuals for RC Series
1
Table of contents
Other BAC Chiller manuals
Popular Chiller manuals by other brands
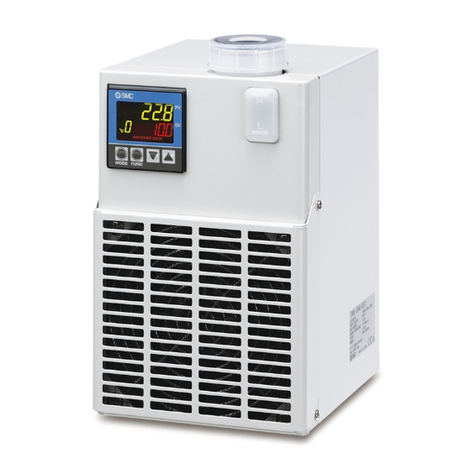
SMC Networks
SMC Networks Thermo-con INR-244-831 manual
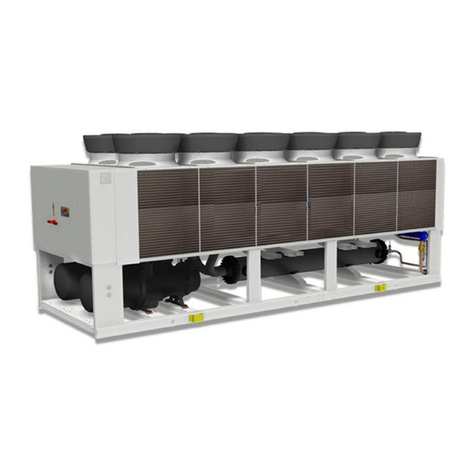
CLIVET
CLIVET WDAT-iL3 Series Installation and operating manual
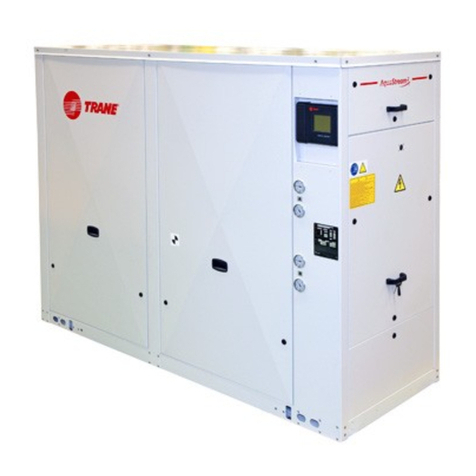
Trane
Trane AquaStream 2 CGWN Series Installation operation & maintenance
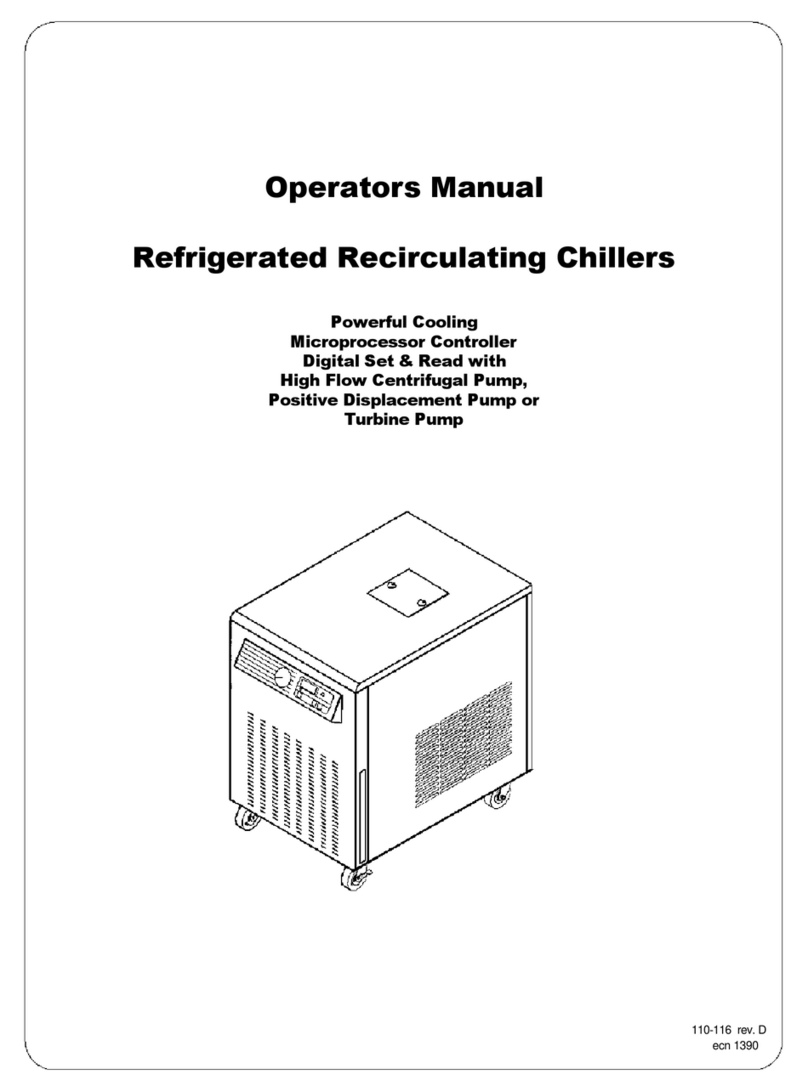
HP
HP Refrigerated Recirculating Chillers Operator's manual

Haier
Haier CA0065EANR Service manual
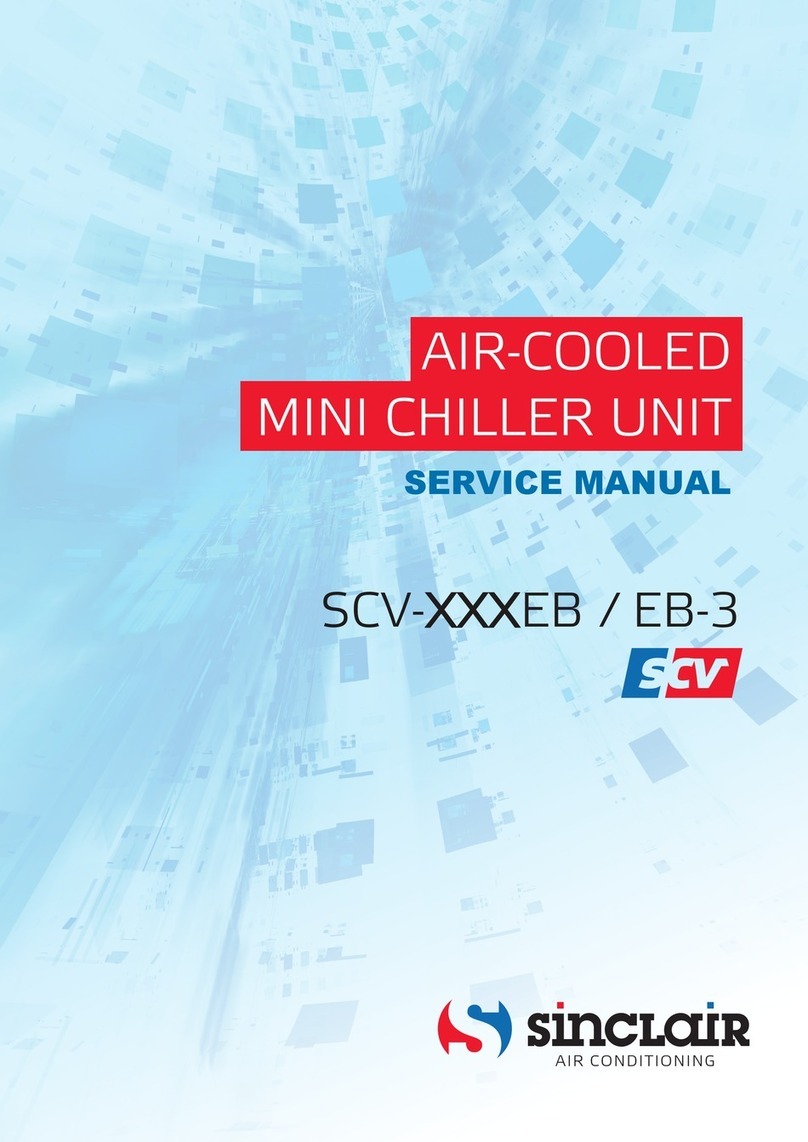
Sinclair
Sinclair SCV-EB Series Service manual

Thermal Care
Thermal Care TSE Operation, installation, and maintenance manual
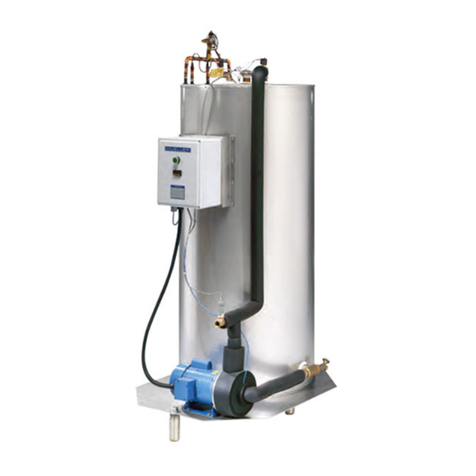
Mueller
Mueller PMC 40/50 Installation and operation manual
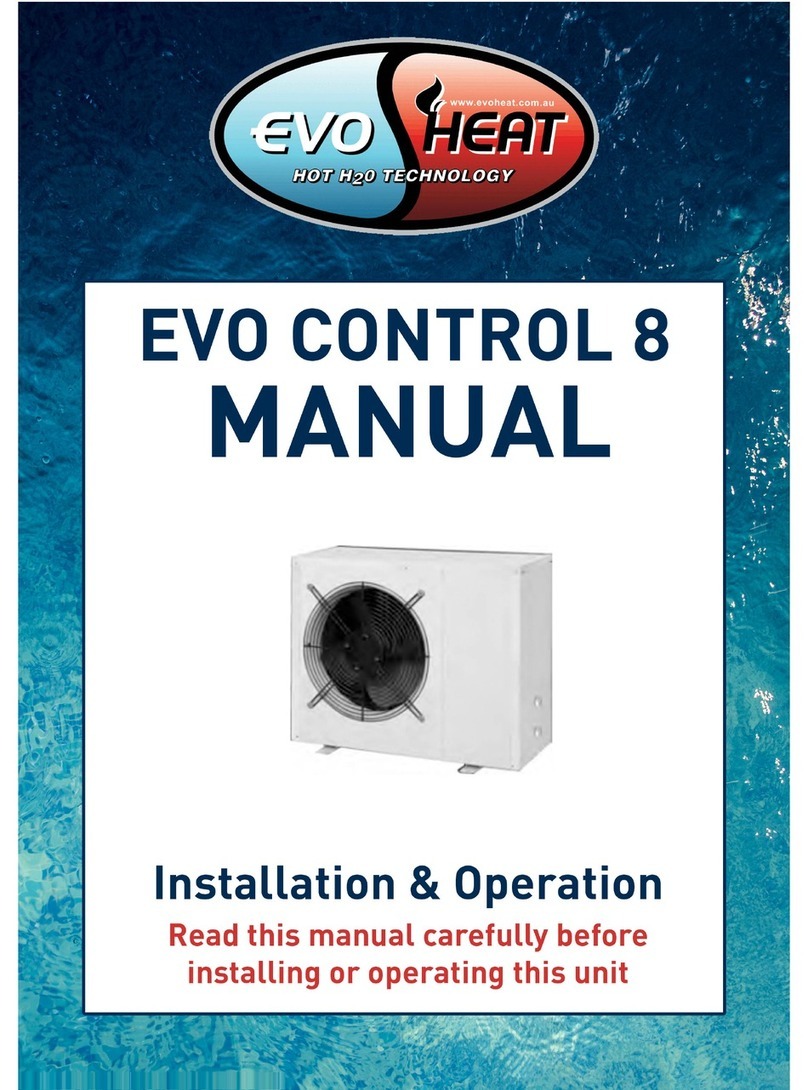
evoheat
evoheat Evo Control 8 Installation & operation
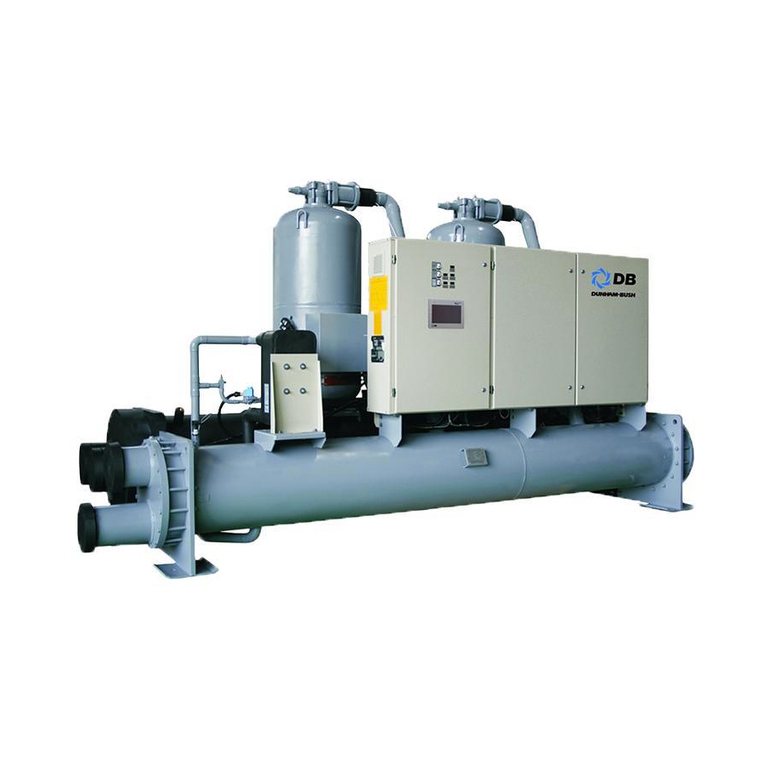
Dunham-Bush
Dunham-Bush WCFX-E Series manual
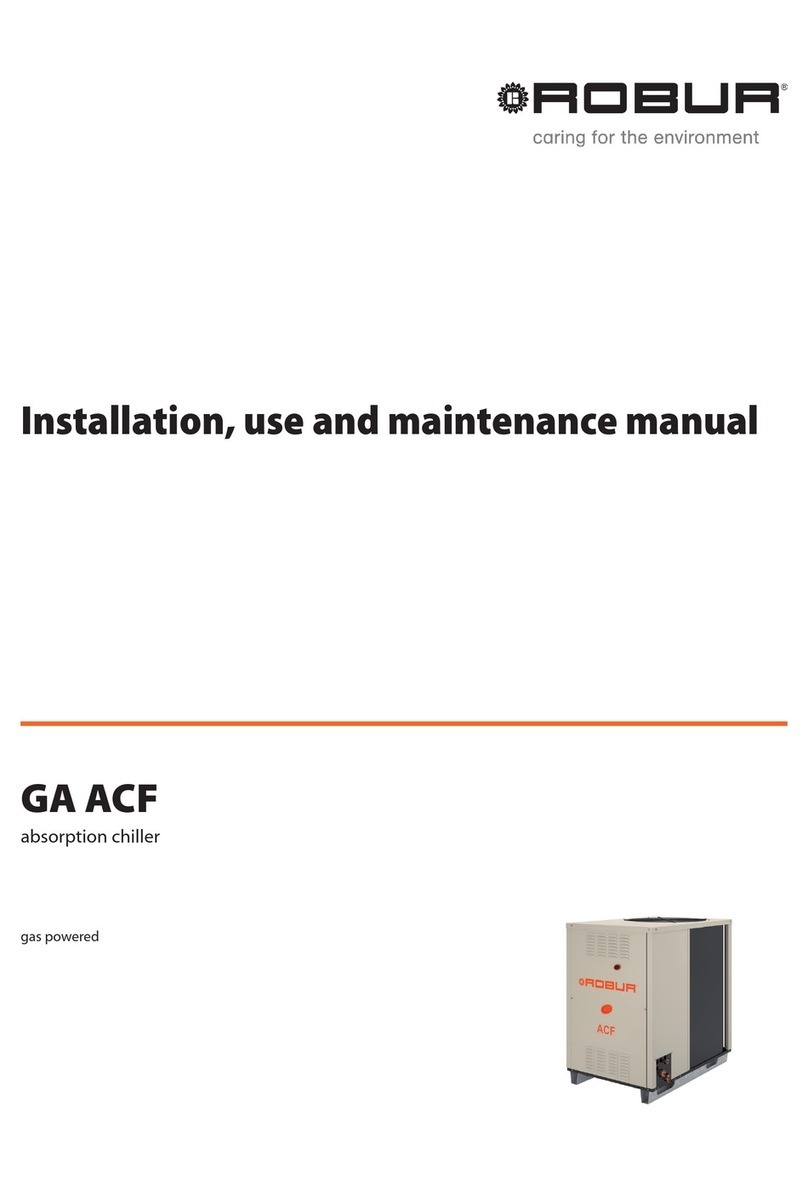
Robur
Robur GA ACF Installation, use and maintenance manual

Carrier
Carrier 30HR Series installation instructions