Badger Basket CD50 User manual

Service Manual
Self Expellling
Carbon Dioxide
Wheeled Fire Extinguishers
Models CD50, CD50-1
CD100, CD100-1

2
© Copyright 2012 Badger Fire Protection
Table of Contents
Contents . . . . . . . . . . . . . . . . . . . . . . . . . . . . . . Page 2
Introduction . . . . . . . . . . . . . . . . . . . . . . . . . . . . Page 3
General Information . . . . . . . . . . . . . . . . . . . . . . . . Page 3
Descriptions. . . . . . . . . . . . . . . . . . . . . . . . . . . . . Page 3
Equipment Shipping Receipt Information . . . . . . . . . . . . Page 4
Installation Procedures. . . . . . . . . . . . . . . . . . . . . . . Page 4
Operation Instructions . . . . . . . . . . . . . . . . . . . . . . . Page 5
After Use Instructions . . . . . . . . . . . . . . . . . . . . . . . Page 6
Monthly Inspection Procedures . . . . . . . . . . . . . . . . . . Page 6
Annual Maintenance and Service Examination Procedures . . . Page 7
Recharge Instructions . . . . . . . . . . . . . . . . . . . . . . . Page 9
Hydrostatic Test Requirements . . . . . . . . . . . . . . . . . . Page 12
Trouble Shooting Suggestions . . . . . . . . . . . . . . . . . . . Page 13
Exploded Parts Diagram . . . . . . . . . . . . . . . . . . . . . . Page 14
Part Numbers and Description. . . . . . . . . . . . . . . . . . . Page 15
Warning:
Failure to follow the instructions contained herein may result in property damage
and/or personal injury!
Important Notice
Any time an unusual extinguisher discrepancy is noticed or the specific corrective action or
procedure required to resolve this condition is not fully understood, personnel should stop
and seek proper qualified assistance prior to continuing.
For assistance, you may contact the nearest authorized Badger fire extinguisher distributor.
Your local distributor can be located in the phone book yellow pages, by contacting Badger Fire
Protection directly at (434) 964-3200 or by logging on to www.badgerfire.com.

3
© Copyright 2012 Badger Fire Protection
Introduction
This manual is designed as a guide for trained personnel having the appropriate equipment and
materials to properly perform the operation, after use, inspection, maintenance, service, recharge
and testing of Badger fire extinguishers.
The service instructions are written and intended for use only by properly trained and certified
service personnel already familiar with standard industry fire extinguisher safety procedures and
practices. Completion of the manufacturer’s factory fire extinguisher service certification school is
recommended.
Any modification, reproduction or distribution of this factory service manual or any part of its con-
tents is prohibited without written permission.
All fire extinguishers should be installed, inspected, maintained and tested in accordance with the
National Fire Protection Association Standard titled “Portable Extinguishers” (NFPA-10) and all the
requirements of the local authority having jurisdiction.
The instructions in the National Fire Protection Associations Standard for portable fire extinguishers
(NFPA-10), the Code of Federal Regulations and the Compressed Gas Association (CGA) pamphlets
are not generally repeated in the manual except where they may emphasize or clarify a point. Hy-
drostatic testing of fire extinguisher cylinders for example, is amply covered in NFPA-10 and CFR-49
part 180.209 which reference procedures in CGA pamphlets C-1, C-2 and C-6A.
NFPA Government Printing Office Compressed Gas Association
1 Batterymarch Park P.O. Box 371954 1235 Jefferson Davis HWY
Quincy, MA 02269 Pittsburgh, PA 15250-7954 Arlington, VA 22202
(617) 770-3000 (202) 512-1802 (703) 788-2700
www.nfpa.org www.bookstore.gpo.gov www.cganet.com
General Information
Badger CO2 wheeled extinguisher models are self-expelling hardware designs, which utilize DOT
specification agent cylinders. These models are charged with carbon dioxide as the extinguishing
agent. Carbon dioxide is a clean agent that discharges as a cold gas, heavier than air, which
displaces oxygen to extinguish fire.
At normal operating temperatures between indicated on the nameplate, these extinguishers are
engineered to effectively discharge the full contents of the carbon dioxide agent charge.
Never attempt to recharge a Badger carbon dioxide fire extinguisher with any other agent than
that specified on the original nameplate.
Descriptions
These hand portable fire extinguishers consist of the following basic parts:
1. Agent cylinder – High-pressure DOT specification cylinders contain the proper carbon dioxide
extinguishing agent charge.
2. Cylinder discharge valve assembly – consists of an operating hand wheel, pressure safety
relief and discharge outlet fitted with an anti-recoil device to permit the actuation and con-
trolled discharge of the extinguishing agent from the cylinder..

4
© Copyright 2012 Badger Fire Protection
3. Siphon tube assembly –provides a means for the liquid extinguishing agent to be drawn up
from the bottom of the agent cylinder to the discharge valve.
4. Ring pin and tamper seals – provide a means of visual assurance that the extinguisher has not
been activated, discharged or subjected to tampering.
5. Discharge hose assembly – High-pressure wire braided rubber hose provides a flexible means
of agent delivery from the cylinder valve to the nozzle assembly.
6. Nozzle and horn assembly – consists of a squeeze lever valve to provide on and off discharge
control of the extinguishing agent with a non-metal, stream shaping horn for optimum fire
fighting performance.
7. Carriage and wheel assembly – two 16 inch semi-pneumatic wheels and welded steel frame-
work for mounting components and providing mobility.
Equipment Shipping Receipt Information
IMPORTANT NOTICE: To accommodate various shipping needs and regulations, Badger
wheeled fire extinguisher models are often packaged and shipped from the factory with
certain operational components disconnected. It is important that personnel responsible
for receiving, delivering and placing this equipment into fire protection duty be aware
of this point.
NOTE: Badger recommends that only trained personnel who understand how to properly
remove the associated packaging and how to properly prepare the wheeled fire extin-
guisher for use and fire protection service attempt to do so.
1. Examine wheeled extinguisher assembly for any missing parts or signs of shipping damage.
(Properly document any missing items or damage observations and notify the carrier.)
2. Remove various forms of attached protective shipping wrappings, tape and attachments.
3. Properly disconnect and release unit from shipping pallet. (Unit may be bolted to pallet.)
4. Remove the protective safety-shipping cap from the top of carbon dioxide agent cylinder.
(This safety-shipping cap should be retained for re-use whenever re-shipment of the cylinder
is necessary per DOT CFR-49 regulations.)
5. Visually ensure the agent cylinder operating valve outlet is clear and unobstructed, then properly
connect the agent discharge hose assembly securely onto this port with a wrench.
NOTE: On Badger CD-100-1 models, both carbon dioxide agent cylinders will need to be
properly connected to the discharge hose manifold.
6. Ensure the discharge hose and nozzle assembly are properly stowed for operation.
Installation Procedures
NOTE: Badger recommends wheeled fire extinguishers be properly installed in accor-
dance with NFPA 10 guidelines.
1. Prior to placing wheeled fire extinguishers into service, a proper extinguisher inspection should
be performed in accordance with the inspection procedures described within this manual.

5
© Copyright 2012 Badger Fire Protection
2. Ensure the selected extinguisher installation location properly conforms to the environmental
operating limitations of the unit. Wheeled carbon dioxide fire extinguisher are approved for
ambient temperature exposures indicated on their nameplates.
3. The extinguisher should be standing vertically upon its stand, with the wheels off the ground.
4. Wheeled fire extinguishers should be properly placed and positioned so that they are accessible
for immediate use and/or able to be quickly mobilized in the event of a fire.
5. The nameplate operating instructions should face outward and the discharge hose/nozzle be
readily accessible.
Operation Instructions
1. Vertically stand and position the wheeled extinguisher upwind of the fire, at a minimum safe
distance of somewhere between 15 to 20 feet from the leading edge of the fire.
2. Remove the hose discharge nozzle assembly from the retainer and hold it securely with one hand.
3. While holding the discharge nozzle securely with one hand, pull and remove the ring pin from
the cylinder valve hand wheel breaking the visual tamper seal.
4. Fully rotate the cylinder valve hand wheel “counter clockwise” to the full open position.
5. Pull the discharge hose free from the extinguisher frame retainer and ensure there are no kinks,
which might hinder the flow of agent during fire fighting.6. Operators should approach the fire
from upwind, to within approximately 10-15 feet of the front edge of the fire.
6. Operators should approach the fire from upwind, to within approximately 10 to 15 feet of the
front edge of the fire.
WARNING:
Failure to start back at a sufficient distance from the front edge of the fire or to use
an adequate sweeping tempo of the agent discharge stream could cause splashing
and/or scattering of the burning material.
WARNING:
Sufficient concentrations of discharged carbon dioxide may reduce oxygen and
cause unconsciousness or even death. Avoid discharging carbon dioxide agent into
any occupied small or unventilated spaces.
7. Starting back from recommended distance, slowly squeeze the operating lever to initiate the
agent discharge.
Note: The carbon dioxide discharge will be very cold and may cause frostbite to unpro-
tected skin. Avoid touching or holding cold areas of the discharge horn during use.
8. Apply the extinguishing agent discharge at the base of the flames with a side-to-side sweeping
manner, being careful not to splash or scatter the fuel. Operators may advance closer as control
of the fire is gained however, they should avoid stepping into the fuel or fire area.
9. After the fire is extinguished, stand by and be prepared to address any re-flash, which may occur.
10. Once the fire is out and has cooled, the fuel should be properly removed and disposed of in
accordance with any local handling requirements.

6
© Copyright 2012 Badger Fire Protection
After Use Instructions
Note: Fire extinguishers should always be recharged immediately after any use.
1. After the fire is out and the hazard secured, the wheel extinguisher should be transported to a
location where the residual pressure left within the discharge hose can be blown clear.
2. Close agent cylinder valve, by turning hand wheel clockwise.
3. Then while securing and pointing the nozzle in a safe direction, squeeze the nozzle discharge
lever to clear hose and vent all remaining pressure.
4. Notify proper person that extinguisher was used, so that the extinguisher can be immediately
recharged or a replacement obtained.
Monthly Inspection Procedures
According to NFPA 10, inspection is a quick check that an extinguisher is available and will operate. It is
intended to give reasonable assurance that the extinguisher is fully charged and operable. This is done
by verifying that it is in its designated place, that it has not been actuated or subjected to tampering,
and that there is no obvious physical damage or condition to prevent its operation.
Inspections should be conducted whenever extinguishers are initially placed into service and there- af-
ter at approximately 30 day intervals. When circumstances require, more frequent intervals may be
necessary. Any time an inspection reveals a discrepancy, maintenance and service procedures should be
performed.
1. Ensure the extinguisher is properly located in plain view and its access is unobstructed.
2. Examine unit for any signs of corrosion, leakage or physical damage.
3. Ensure the nameplate is secure and legible and that “operating instructions” face outward.
4. Ensure ring pin and visual inspection tamper seal are in place and intact.
5. Ensure the carriage/frame clamps, bolts and hardware are in place and secure.
6. Tilt extinguisher about its wheeled axis or weigh the unit to determine its fullness. (When tilting the
unit, the sound of liquid agent movement within the cylinder may be heard. If any other sounds
are observed, refer to the maintenance and troubleshooting recommendations.)
Note: Badger recommends all Carbon Dioxide fire extinguishers be weighed at least semi-
annually to verify the proper agent weight per the nameplate instructions. Refer to the
maintenance procedures.
7. Squeeze the nozzle operating lever to ensure there is no pressure trapped within the hose assembly.
Visually examine the discharge nozzle, and/or hose assembly to ensure it is clear and unobstructed.
8. Ensure both wheels are not damaged and that they rotate freely.
9. Date and initial the inspection tag or record in accordance with NFPA 10 & local requirements.

7
© Copyright 2012 Badger Fire Protection
Annual Maintenance & Service Examination Procedures
Per NFPA 10, maintenance is a thorough examination of a fire extinguisher and is intended to
provide maximum assurance that it will operate effectively and safely. It includes a thorough
examination of all components and the repair or replacement of such items, if necessary.
Maintenance should be performed at intervals not to exceed one year apart or any time an
inspection discrepancy dictates.
Badger recommends that only authorized Badger distributors and certified personnel who have
been properly trained to recognize and correct discrepancies, as well as understand all the proper
industry safety procedures, conduct the maintenance or service of Badger fire extinguishers. Refer
to the trouble shooting section of this manual for additional information on specific equipment
observations or discrepancies. Only Badger factory replacement parts are recommended for
use in Badger extinguishers.
WARNING:
Prior to servicing or recharging an extinguisher, personnel should be thoroughly
familiar with the contents of this manual to recognize any equipment conditions or
discrepancies that might dictate or prohibit further equipment maintenance or repair.
WARNING:
To prevent injury or death, always ensure all pressure is properly relieved from an
extinguisher prior to attempting any service, repair or recharge.
1. Ensure extinguisher is installed in its proper location and that it is readily accessible. (Badger car-
bon dioxide extinguisher models are approved for temperatures indicated on the nameplate).
2. Externally examine unit and cylinder for any signs of damage, dents or corrosion that might
prohibit service or dictate the need for any special maintenance/repair procedures. Ensure cylindar
hydro date is within 5 year requirements.
3. Closely examine the extinguisher frame for any damage, corrosion, cracks or deformation.
When the extinguisher is tilted on its wheeled axis, service personnel should listen for any
sounds from within the cylinder that might indicate a broken siphon tube or foreign mate-
rial. (Refer to Trouble Shooting section)
4. Examine both wheels to ensure they are secure, not damaged and rotate freely. Lubricate
as necessary.
5. Unthread and remove the discharge hose assembly from the cylinder valve assembly. Fully extend
the hose assembly and closely examine the discharge nozzle valve, horn, hose and couplings for
any damage, abrasions, cracking, thread wear or conditions that might affect its proper function.
(ON Badger CD-100-1 MODELS) – The agent discharge hose assembly and hose manifold
assembly must both be disconnected and thoroughly examined.
6. Examine the discharge nozzle valve for any damage or corrosion and while pointing nozzle in a
safe direction slowly squeeze the lever to verify it operates properly. Ensure the nozzle discharge
horn is not damaged, cracked or obstructed and is correct for the model.
7. Blow (low pressure) dry air through the discharge hose assembly and nozzle to ensure it is not
plugged or obstructed and operates freely. (If hose is obstructed, properly secure hose assembly
and using the proper service kit adaptor, connect a regulated pressure source set no higher than
100 PSI to assist in clearing the hose and nozzle assembly.)

8
© Copyright 2012 Badger Fire Protection
8. Using a continuity tester, perform an agent hose continuity test between both of the metal
agent hose couplings to ensure the internal wire braid within the hose is intact, to dissipate
any potential static charge build up. Hoses passing this continuity test must be properly labeled
in accordance with NFPA-10 requirements.
9. Visually examine the cylinder valve discharge port(s) for any signs of thread wear, damage,
corrosion, obstructions or foreign material. Ensure the anti-recoil device is properly installed.
10. Examine the cylinder valve safety relief assembly to ensure it is intact and correct for the model.
Ensure the safety relief is not damaged, corroded or obstructed.
11. Install the proper CO2 cylinder “safety shipping cap” securely onto the valve for handling and
transportation. Loosen the frame retainer clamp and remove the cylinder from the extinguisher
frame.
12. Properly weigh the cylinder to ensure it correlates with the fully charged weight stamped on
the side of the cylinder valve.
13. The hydrostatic test date stamped into the shoulder of the extinguisher cylinder must be
checked. The maximum periodic interval for Badger carbon dioxide wheeled fire extinguishers is
5 years. (Refer to NFPA-10 and CFR-49 for specific cylinder hydrostatic re-test requirements and
procedures.)
14. Install safety shipping cap onto valve assembly for handling and transportation, then re-install
and properly secure the agent cylinder into the carriage/frame. Ensure the cylinder orientation
correctly faces the nameplate operating instructions outward.
15. Remove cylinder safety shipping cap then re-install and secure the discharge hose assembly
onto the cylinder discharge valve outlet port.(ON Badger CD-100-1 MODELS) – The agent hose
manifold assembly must both be reconnected to both cylinder valves and the agent hose assem-
bly properly connected to the manifold.
Note: Avoid the use of any teflon tape or similar materials which can compromise
continuity for dissipation of static build up.
16. Ensure the extinguisher nameplate is legible and secure. Check to ensure HMIS information is
present and legible.
17. Properly coil the agent hose assembly back onto the extinguisher hanger. Adjust the hose so
that it hangs clear of the floor/ground. Then secure discharge nozzle and horn back into the
retention clip/holder.
18. Being careful not to accidentally discharge the fire extinguisher, pull and remove the ring pin
from the cylinder operating valve hand wheel (breaking the visual inspection seal). Ensure the
ring pin pulls freely and is not bent, damaged or corroded. Re-install proper ring pin and install
a new visual inspection tamper seal through the pull pin loop and the hand wheel.
19. Wipe the extinguisher clean with a damp cloth to remove any surface dirt or contaminants that
may have accumulated.
20. Upon satisfactory completion of the maintenance examination, properly tag, label and record
the procedure in accordance with NFPA 10 and any local requirements.

9
© Copyright 2012 Badger Fire Protection
Recharge Instructions
According to NFPA 10, recharge is the replacement of extinguishing agent and expellant. All
rechargeable fire extinguishers shall be recharged after any use or as indicated by an inspection
or when performing maintenance. When performing extinguisher recharge, the recommendations
of the manufacturer shall be followed.
Because of potential performance or detrimental material compatibility problems which may occur
with the use of other agents, Badger recommends that only carbon dioxide extinguishing agent
meeting the following specification be utilized for recharge.
Carbon dioxide shall be of a commercial grade free of contaminants with a vapor
phase of 99.5% or greater and have a water content of less than 60 ppm by weight
at a –52 F (-46.6 C) dew point. The oil content of the carbon dioxide shall not exceed
10 ppm by weight.
WARNING:
Prior to recharging an extinguisher, personnel should be thoroughly familiar with
the contents of this manual to recognize any equipment conditions or discrepancies
that may prohibit the recharge or further service of the equipment.
WARNING:
To avoid personal injury or death, always ensure all pressure is properly relieved
from an extinguisher prior to attempting any service, repair or recharge.
WARNING:
Sufficient concentrations of discharged carbon dioxide may reduce oxygen and
cause unconsciousness or even death. Avoid discharging carbon dioxide agent into
any occupied small or unventilated spaces.
1. To ensure the extinguisher is empty, open the cylinder valve hand wheel.
2. While securing the discharge nozzle in a safe direction, slowly squeeze the discharge nozzle
lever to remove any remaining pressure.
3. Visually examine the complete wheeled fire extinguisher for any signs of damage, wear, corro-
sion, repair or other conditions that might prohibit the unit from being recharged. (Ensure the
bottom of the extinguisher is also examined.) When the extinguisher is tilted on its axis, service
personnel should listen for any sounds from within the cylinder that might indicate a broken
siphon tube or foreign material. (Refer to Trouble Shooting section.)
WARNING:
To avoid personal injury or death, should any audible pressure leakage be observed
during extinguisher disassembly, technicians should stop any further service action
and wait until all residual pressure is relieved.

10
© Copyright 2012 Badger Fire Protection
4. If internal cylinder examination is required, fully discharge and depressurize cylinder to per-
mit proper removal of valve assembly. Proper installation of siphon tubes require examination
of both threaded surfaces to ensure they are clean and undamaged. Prior to installation, a
light uniform bead of Permabond HM 118 should be carefully applied around the 2nd and 3rd
threads of the siphon tube, so that no sealant can enter the siphon tube. Screw siphon tube into
the valve assembly hand tight till it bottoms out and then tighten an additional ¼ turn with a
small pipe wrench. No exposed threads or gaps should be visible.
5. Closely examine the agent cylinder for any signs of damage, wear, dents, corrosion or repair.
6. The periodic re-hydrostatic test date of the extinguisher cylinder must be checked prior to
recharge. The maximum periodic interval for Badger carbon dioxide wheeled fire extinguishers is
5 years. (Refer to CFR-49 for specific cylinder hydrostatic test requirements and procedures.)
7. Ensure the extinguisher operating nameplate instructions are secure and legible. Check to
ensure HMIS information is present and legible.
8. Unthread and remove the agent hose assembly from the cylinder discharge valve assembly.
9. Visually examine the cylinder valve discharge port for any signs of thread wear, corrosion,
obstructions or accumulations of any foreign material. Ensure the anti-recoil device is properly
installed.
10. Examine the cylinder valve safety relief assembly to ensure it is not damaged, corroded or
obstructed.
Note: If replacement of safety relief is required, the extinguisher must first be emptied
and free of any pressure. A new Badger 3 part safety assembly (P/N-24643)) should be
installed washer first, then the disc (printed side outward) and then the nut. The new
safety assembly must be properly torqued between 30 to 35 foot-pounds.
11. Install the proper CO2 cylinder “safety shipping cap” securely onto the valve for handling and
transportation. Loosen the frame retainer clamp and remove the cylinder from the extinguisher
frame for filling.
12. Using a calibrated weight scale to determine the proper agent charge, the cylinder can be filled.
Install the proper carbon dioxide charge adapter into the cylinder valve outlet port. Slowly ro-
tate the extinguisher valve hand wheel operating lever and properly fill the cylinder to the
fully charged weight stamped on the cylinder valve.
NOTE: When filling extinguishers from a carbon dioxide supply utilizing a pump, the
specific instructions for using that equipment should be followed. Ensure the carbon
dioxide supply meets the extinguishing agent specifications identified earlier in this
manual for recharging Badger fire extinguishers.

11
© Copyright 2012 Badger Fire Protection
13. Upon reaching the proper fill weight, tightly close the cylinder valve hand wheel. Remove the
carbon dioxide charge adapter from the extinguisher valve assembly.
14. Properly install the pull pin back into the cylinder valve hand wheel. Then install a visual
inspection tamper seal through the ring pin pull loop and hand wheel.
15. Using a soapy solution or leak detecting fluid, properly perform a leak check of the cylinder valve
assembly and cylinder collar to ensure no pressure leakage is occurring. Upon successful completion
of the leak check, properly clean and dry all extinguisher surfaces.
16. Re-weigh the extinguisher cylinder to verify the total charged weight matches the filled weight
stamped on the cylinder valve and the tolerance limitations specified on the nameplate instructions.
17. Install safety shipping cap onto valve for handling and transportation, then re-install and properly
secure the agent cylinder into the carriage/frame. Ensure the cylinder orientation correctly faces the
nameplate operating instructions outward.
18. Fully extend the discharge hose assembly and closely examine the discharge nozzle, hose and cou-
plings for any damage, abrasions, cracking, wear or conditions that might affect its proper function.
Verify that the discharge nozzle is correct for the model.
19. Blow (low pressure) dry air through the hose /nozzle assembly to ensure it is not plugged or ob-
structed and that the nozzle operates freely. (If hose is obstructed, properly secure hose assembly
and using the proper service kit adaptor, connect a regulated pressure source set no higher than
100 PSI to assist with clearing hose assembly.)
20. Ensure the discharge hose assembly and nozzle are not plugged or obstructed and that the dis-
charge nozzle operates freely. Fully extend the hose assembly and closely examine the discharge
nozzle, hose and couplings for any damage, abrasions, cracking, wear or conditions that might af-
fect its proper function. Verify that the discharge nozzle is correct for the model.
21. Remove cylinder safety shipping cap then re-install and secure the discharge hose assembly onto the
cylinder operating valves outlet port.
(ON Badger CD-100-1 MODELS) – The agent hose manifold assembly must be re-connected to both
cylinder valves and the agent hose assembly properly connected to the manifold.
Note: Avoid the use of any teflon tape or similar materials which can compromise
continuity for dissipation of static build up.
22. Properly coil the agent hose assembly back onto the extinguisher hanger. Adjust the hose so that
it hangs clear of the floor/ground. Secure the hose nozzle back into the retention clip/holder.
23. Examine both wheels to ensure they are secure, not damaged and rotate freely. Lubricate as
necessary.
24. Ensure the extinguisher nameplate is legible and secure. Check to ensure HMIS information is
present and legible.
25. Wipe the extinguisher clean with a damp cloth to remove any surface dirt or contaminants that
may have accumulated.
26. Upon satisfactory completion of the recharge and maintenance examination, properly tag, label
and record the procedure in accordance with NFPA 10 and any local requirements.

12
© Copyright 2012 Badger Fire Protection
Hydrostatic Test Requirements
Hydrostatic testing is the integrity pressure testing method of a vessel utilizing a liquid compression me-
dium. Badger carbon dioxide extinguisher cylinders and hose assemblies require hydrostatic testing at
5 year periodic intervals or any time the integrity of the vessel is questioned from any visually observed
condition.
Visual cylinder examinations and hydrostatic testing should be performed in accordance with NFPA 10
and D.O.T. CFR-49 part 180.209 recommendations.
Evidence of conditions such as exposure to fire or heat, thread damage, thread wear, corrosion, cylinder
repairs or physical damage as detailed within NFPA 10, require the extinguisher cylinder to be removed
from service and at the owner’s direction, disposed of in the proper manner.
Hydrostatic testing should only be performed by those persons trained in the appropriate testing proce-
dures/safeguards and having the proper testing equipment, adapters, facilities, documents and infor-
mation.
Some Badger hydrostatic test recommendations:
• Carbon dioxide cylinder safety relief assemblies should be replaced every 5 years, when hydrostatic
testing the cylinder. A new Badger 3 part safety assembly (P/N-24643) should be installed washer first,
then the disc (printed side outward) and then the nut. The new safety assembly must have the proper
amount of torque between 30 to 35 foot-pounds. Never resue safety relief components and always
ensure the valve body seating surface is free of any damage or contamination prior to installation of
new assemblies.
• Extinguisher cylinders should be replaced any time the pressure vessel has been weakened due to cor-
rosion, cuts, dents, digs, etc. and be properly disposed in accordance with CGA pamphlet C-2.
• Only water be used as the hydro-test medium and that the vessel then be ushed clean, thoroughly
dried and visually re-examined after testing.
• The cylinder valve assembly should be removed prior to hydrostatic testing of the cylinder.
• The hydrostatic test marking methods should only utilize the proper type of record labels per
NFPA-10 and CFR-49 stamping requirements
• Never stamp or etch unauthorized markings onto the cylinder.
• Any time a re extinguisher is known to have contained agents, additives or mediums other than that
specified on the nameplate, it should be removed from service and at the owner’s direction, disposed
of in the proper manner.
• No repairs to the cylinder are permitted. If such cylinder repairs are observed, the extinguisher should
be removed from service and at the owner’s direction, disposed of in the proper manner.
• Badger recommends cylinder valve installations be properly torqued to 150 foot punds.
• Installation of new cylinder valve assemblies require the new fully charged cylinder weight be prop-
erly stamped on to the side of the new valve.
• Installation of siphon tubes into valve assembly should be in accordance with Badger product bulletin
P-224 instructions.
Hydrostatic Re-Test Data:
Component Description Periodic Test Interval Test Pressure
Agent cylinders 3A or 3AA 5 years per D.O.T. 3000 PSI
Agent hose assembly 5 years (same as agent cylinder) 1250 PSI
Agent manifold hose assembly 5 years (same as agent cylinder) 1250 PSI

13
© Copyright 2012 Badger Fire Protection
Trouble Shooting Suggestions
Problem Corrective Suggestion
Frame bent or damaged Repair or replace
Frame attachment bolts loose or missing Tighten and/or replace
Nozzle obstructed Clear, clean or replace
Discharge hose assembly obstructed Clear, clean or replace
Hose assembly worn, cracked or damaged. Replace
Discharge hose assembly fails continuity test Replace
Wheel missing or damaged Replace
Wheel does not rotate freely Clean and lubricate
Cylinder valve discharge port dirty or damaged Clean or de-pressurize and replace *
Safety relief damaged, corroded or obstructed De-pressurize & replace safety relief assembly **
Pull pin bent, corroded, missing or damaged Replace
Cylinder valve hand wheel bent or damaged De-pressurize and replace
Total charge weight of cylinder outside tolerance De-pressurize and recharge
Operating instructions missing or illegible Replace
Agent cylinder burned or repaired Replace
Agent cylinder damaged or corroded Inspect, hydrostatic re-test or dispose in
accordance with NFPA 10 and CFR-49
recommendations.
Siphon tube broken or disconnected De-pressurize & replace.
Refer to Product Bulletin P-224.
Leakage from safety relief area De-pressurize & replace safety relief **
Leakage from valve outlet or hand wheel area De-pressurize & replace valve *
Leakage from cylinder valve thread area De-pressurize, remove valve & examine sealing
surfaces. Replace valve if necessary*
* Badger recommends cylinder valve installations be torqued to 150 foot-pounds. Installation
of new cylinder valve assemblies require new charged cylinder weights be properly stamped
on to the new valve
** Badger recommends the safety relief assembly be installed washer first, then the disc (printed
side outward) and then nut. The new assembly must be properly torqued 30 to 35 foot-pounds.

14
© Copyright 2012 Badger Fire Protection
Extinguisher Parts Diagram
Badger Carbon Dioxide Wheeled Extinguishers:
CD50, CD50-1, CD100 and CD100-1

15
© Copyright 2012 Badger Fire Protection
Extinguisher Part Numbers
Badger Carbon Dioxide Wheeled Extinguishers:
CD50, CD50-1, CD100 and CD100-1
Item Part Numbers Description
1 22780 . . . . . . . . CD-50-1 Frame Assembly (Does not include wheels)
22782 . . . . . . . . CD-100-1 Frame Assembly (Does not include wheels)
2 22754 . . . . . . . . . -Wheel - 16” semi-pneumatic (2 required)
3 22770 . . . . . . . . . -Flat washer for axle (2 required)
4 22751 . . . . . . . . . -Cotter pin for axle (2 required)
5 22746 . . . . . . . . Cylinder assembly (charged with valve and cap)
6 22749 . . . . . . . . . -cylinder valve
7 22797 . . . . . . . . . . . ring pin
8 22777 . . . . . . . . . . . chain
9 22776 . . . . . . . . . . . chain drive pin
10 24643 . . . . . . . . . . . safety relief assembly (nut, disc and washer)
11 22776 . . . . . . . . . -siphon tube assembly
12 13735 . . . . . . . . . -replacement non-flammable gas label
13 22785 . . . . . . . . . -replacemtn UN-1013 label
14 22873 . . . . . . . . Replacement operating instruction CD-50-1 (w/o manifest)
22874 . . . . . . . . Replacement operating instruction CD-100-1 (w/o manifest)
15 13120 . . . . . . . . Visual inspection Seal (red field replacement)
16 22816 . . . . . . . . Manifold assembley (CD-100-1 model only)
17 22887 . . . . . . . . CD-50-1 Agant discharge hose assembly - 15 ft.
22885 . . . . . . . . CD-100-1 Agant discharge hose assembly - 40 ft.
18 22867 . . . . . . . . . . .Discharge nozzle assembly
19 05310 . . . . . . . . . - discharge valve assembly
20 22814 . . . . . . . . . - horn retaining nut
21 22811 . . . . . . . . . - discharge horn
22 22809 . . . . . . . . .- nozzle
23 22810 . . . . . . . . . - insulated handle
24 22812 . . . . . . . . . - pipe nipple

Badger Fire Protection
944 Glenwood Station Lane, Suite 303
Charlottesville, Virginia 22911
www.badgerfire.com
(Phone 1-800-964-3200)
Manual BP84A
P/N 24645 (Rev - 07/12)
Copyright © 2012
This manual suits for next models
3
Table of contents
Other Badger Basket Measuring Instrument manuals
Popular Measuring Instrument manuals by other brands

Martel
Martel BetaGauge PI User's reference manual
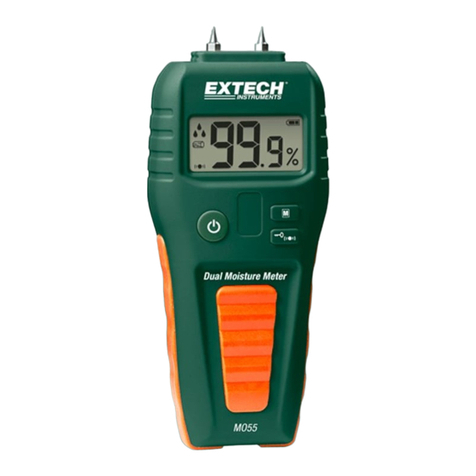
Extech Instruments
Extech Instruments MZ13604 user manual
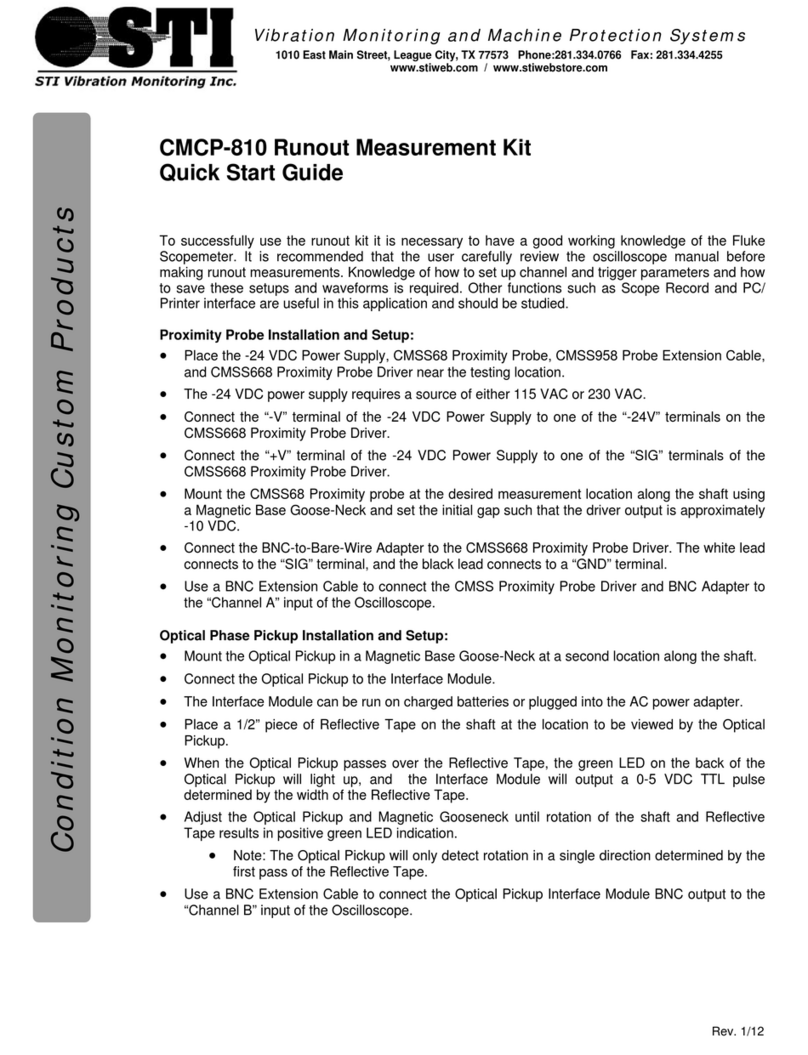
STI
STI CMCP810 Series quick start guide
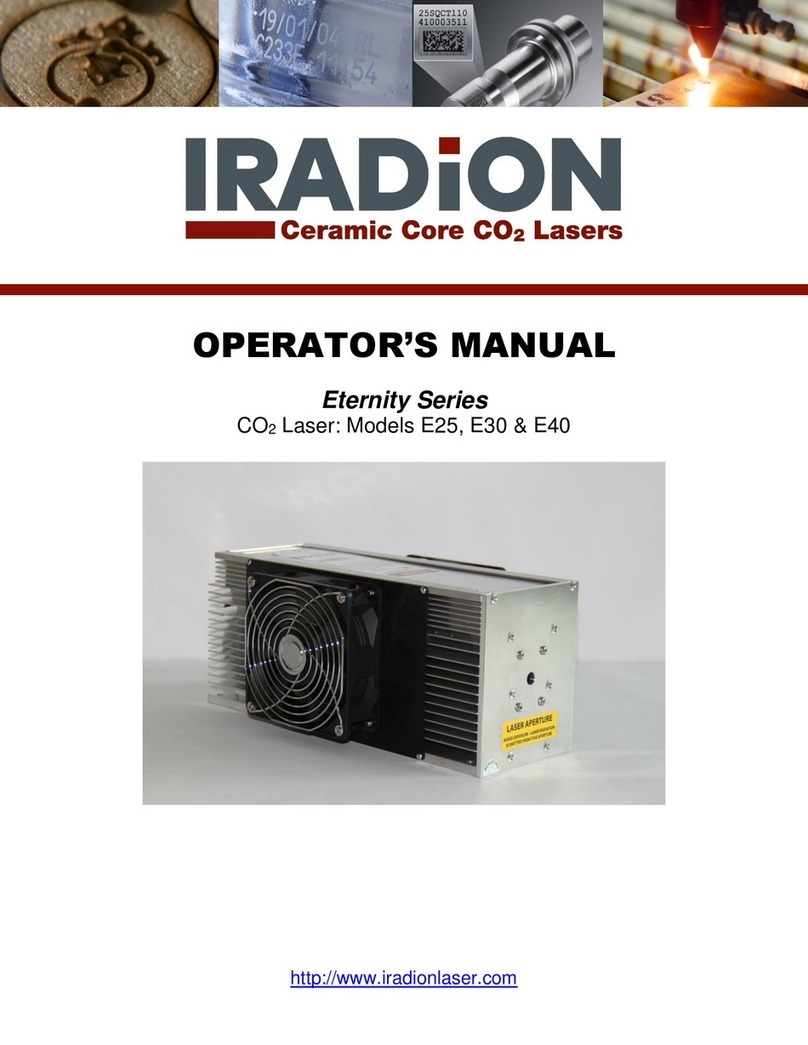
Iradion
Iradion Eternity Series Operator's manual
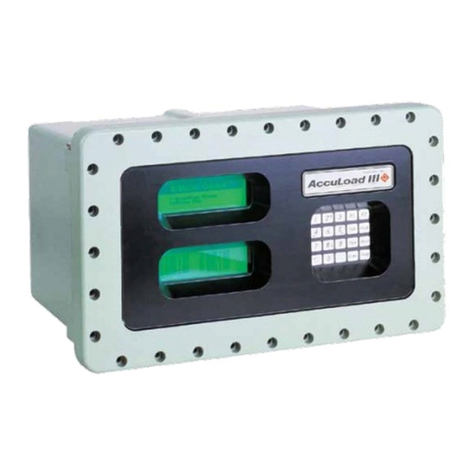
FMC Technologies
FMC Technologies Smith Meter AccuLoad III.net Applications manual

Endress+Hauser
Endress+Hauser Cerabar M PMC41 operating instructions