STI CMCP810 Series User manual

To successfully use the runout kit it is necessary to have a good working knowledge of the Fluke
Scopemeter. It is recommended that the user carefully review the oscilloscope manual before
making runout measurements. Knowledge of how to set up channel and trigger parameters and how
to save these setups and waveforms is required. Other functions such as Scope Record and PC/
Printer interface are useful in this application and should be studied.
Proximity Probe Installation and Setup:
Place the -24 VDC Power Supply, CMSS68 Proximity Probe, CMSS958 Probe Extension Cable,
and CMSS668 Proximity Probe Driver near the testing location.
The -24 VDC power supply requires a source of either 115 VAC or 230 VAC.
Connect the “-V” terminal of the -24 VDC Power Supply to one of the “-24V” terminals on the
CMSS668 Proximity Probe Driver.
Connect the “+V” terminal of the -24 VDC Power Supply to one of the “SIG” terminals of the
CMSS668 Proximity Probe Driver.
Mount the CMSS68 Proximity probe at the desired measurement location along the shaft using
a Magnetic Base Goose-Neck and set the initial gap such that the driver output is approximately
-10 VDC.
Connect the BNC-to-Bare-Wire Adapter to the CMSS668 Proximity Probe Driver. The white lead
connects to the “SIG” terminal, and the black lead connects to a “GND” terminal.
Use a BNC Extension Cable to connect the CMSS Proximity Probe Driver and BNC Adapter to
the “Channel A” input of the Oscilloscope.
Optical Phase Pickup Installation and Setup:
Mount the Optical Pickup in a Magnetic Base Goose-Neck at a second location along the shaft.
Connect the Optical Pickup to the Interface Module.
The Interface Module can be run on charged batteries or plugged into the AC power adapter.
Place a 1/2” piece of Reflective Tape on the shaft at the location to be viewed by the Optical
Pickup.
When the Optical Pickup passes over the Reflective Tape, the green LED on the back of the
Optical Pickup will light up, and the Interface Module will output a 0-5 VDC TTL pulse
determined by the width of the Reflective Tape.
Adjust the Optical Pickup and Magnetic Gooseneck until rotation of the shaft and Reflective
Tape results in positive green LED indication.
Note: The Optical Pickup will only detect rotation in a single direction determined by the
first pass of the Reflective Tape.
Use a BNC Extension Cable to connect the Optical Pickup Interface Module BNC output to the
“Channel B” input of the Oscilloscope.
CMCP-810 Runout Measurement Kit
Quick Start Guide
Condition Monitoring Custom Products
Vibration Monitoring and Machine Protection Systems
1010 East Main Street, League City, TX 77573 Phone:281.334.0766 Fax: 281.334.4255
www.stiweb.com / www.stiwebstore.com
Rev. 1/12

Oscilloscope Setup and Operation:
Power on the -24 VDC Power Supply, Optical Pickup Interface Module, and the Oscilloscope.
Channel A Setup:
Press the “A” button to enter Channel A Setup.
Set the pop-up menu “INPUT A” to “ON” using the “F1” button.
Set the pop-up menu “COUPLING” to “DC” using the “F2” button.
Set the pop-up menu “PROBE A” to “Voltage and 1:1” using the “F3” button.
Press the “CLEAR MENU” button when finished.
Press the Channel A “RANGE” button to achieve a range of 200 or 500mV.
Channel B Setup:
Press the “B” button to enter Channel B Setup.
Set the pop-up menu “INPUT B” to “ON” using the “F1” button.
Set the pop-up menu “COUPLING” to “AC” using the “F2” button.
Set the pop-up menu “PROBE B” to “Voltage and 1:1” using the “F3” button.
Press the “CLEAR MENU” button when finished.
Press the Channel A “RANGE” button to achieve a range of 5V.
Time Setup:
Press the “TIME” button to achieve a range of 500ms to 2s depending on rotation
speed. You want to be able to capture an entire revolution in one screen.
Press the Channel A “MOVE” and Channel B “MOVE” buttons to establish a distance between
the two plots so that they do not overlap.
Runout Measurement:
Slowly rotate the shaft so that at least one revolution is captured on the screen.
Press the “SAVE PRINT” button to capture the screen.
Press the “SAVE” button on the pop-up menu using the “F1” key.
Use the Arrow Keys to highlight “SCREEN + SETUP” 1-10 and press the “SAVE” pop-up menu
button using the “F4” key.
To recall the saved screen press the “SAVE PRINT” key and select “RECALL” on the pop-up
menu using the “F2” key. Use the Arrow Keys to highlight the desired screen and press “F4”.
Consult the User’s Manual CD enclosed in the Oscilloscope’s “Quick Start” guide for printing
and data transfer.
To measure the shaft runout press the “CURSOR” button.
Use the “F1” key to select “=“ for parallel horizontal lines.
Use the “UP” and “DOWN” arrow keys to position the top cursor to the highest peak on the
Channel A plot.
Press the “F2” key to select the other cursor and use the “UP” and “DOWN” arrow keys to
position the other cursor to the lowest peak on the Channel A plot.
The runout voltage difference is visible on the top left of the screen. This correlates to the
200mV/mil output of the Proximity Probe System.
Condition Monitoring Custom Products
Vibration Monitoring and Machine Protection Systems
1010 East Main Street, League City, TX 77573 Phone:281.334.0766 Fax: 281.334.4255
www.stiweb.com / www.stiwebstore.com
Rev. 1/12

Correction of Common Oscilloscope User Errors:
In the event that the Oscilloscope is not functioning properly the easiest solution is to reset back
to Factory Default Settings and perform the Oscilloscope Setup from the beginning.
Press the “USER” button open the User Options Menu.
Use the Arrow Keys to highlight “Factory Default”.
Press “ENTER” using the “F4” key.
Note: This will erase all saved screens.
Repeat the Oscilloscope Setup on the previous page.
Surface Irregularities:
Surface irregularities or imperfections will appear on an oscilloscope as sharp voltage spikes
superimposed on the dynamic waveform.
Surface irregularities such as scratches, pitting, burrs, etc. will produce a runout condition as
observed by the eddy probe sensor.
In general, surface irregularities are created due to improper handling of the rotor during the
manufacturing or repair cycle. Care should be taken to protect the shaft surface to be used for
dynamic motion measurements. In essence, these surface areas should be given the same
protective measures used to protect a bearing journal surface. Crane lifts should be made with
cables attached to shaft areas away from the probe measurement surfaces. Support fixtures for
storage of rotors should not introduce surface scratches, dents, etc.
Occasionally, surface irregularities are introduced via a machine-cutting tool. If the tool is dull or the
feed is too rapid, some tool chatter may occur which can introduce small ripples in the shaft surface.
Electrical Runout:
Eddy probes will operate in the presence of magnetic field, as long as the field is uniform or
symmetrical and not localized to a particular location on the rotor. Electrical runout will be present if
a particular area of the shaft surface is highly magnetic, and the remaining surface is nonmagnetic,
or at a much lower value. This is due to the resultant change in sensitivity on the shaft surface to the
applied field from the eddy probe sensors.
Residual Stress Concentrations:
Observation of residual stress concentrations on an oscilloscope will yield a sinusoidal
waveform with high voltage, high frequency spikes superimposed on the waveform.
During manufacturing and repair of rotors, a variety of machining and surface treatment processes
can introduce small amounts of localized stress concentrations. Although these stress areas do not
adversely affect the mechanical properties of the rotor, they may give rise to an electrical runout
from the proximity transducers. Since one of the variables affecting voltage output from the
transducer is the resistivity of the observed shaft surface, any deviation of the resistance around the
circumference of the shaft (due to varying stress levels) will produce a voltage change.
Condition Monitoring Custom Products
Vibration Monitoring and Machine Protection Systems
1010 East Main Street, League City, TX 77573 Phone:281.334.0766 Fax: 281.334.4255
www.stiweb.com / www.stiwebstore.com
Rev. 1/12
Other manuals for CMCP810 Series
1
Table of contents
Other STI Measuring Instrument manuals
Popular Measuring Instrument manuals by other brands
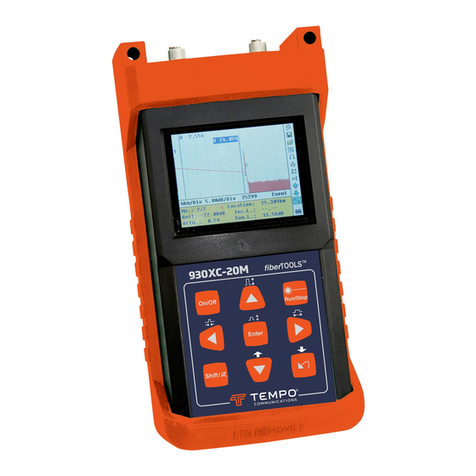
Tempo Communications
Tempo Communications 930XC-20C instruction manual
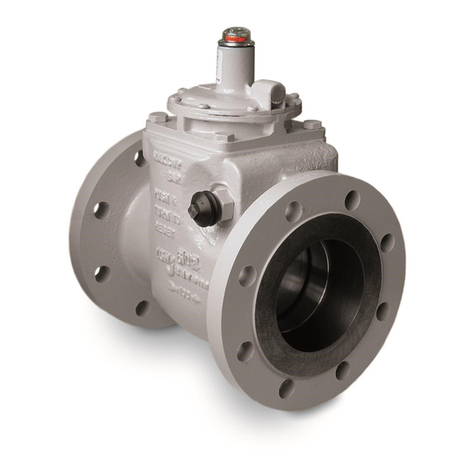
Elster
Elster S100 Commissioning instructions
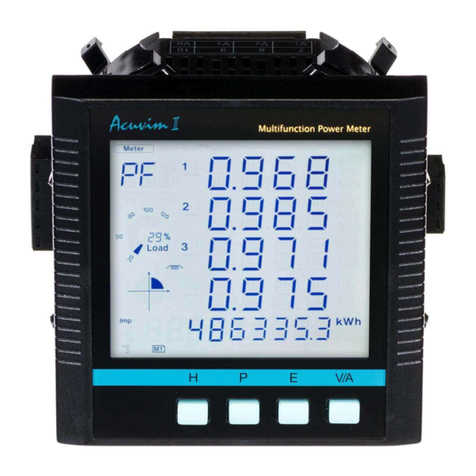
AccuEnergy
AccuEnergy Acuvim II series user manual
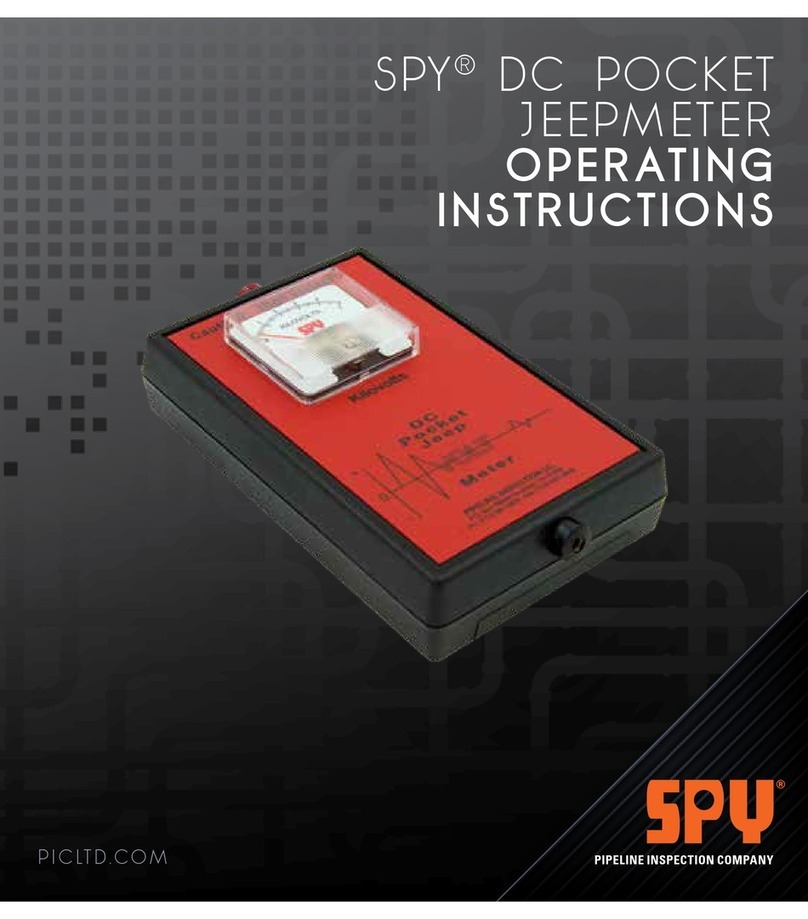
SPY
SPY DCPJM operating instructions
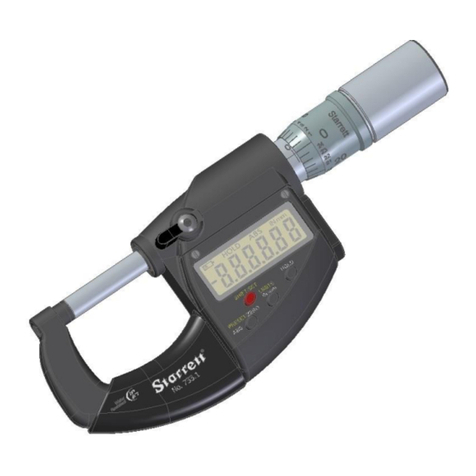
Starrett
Starrett 749.1 user manual
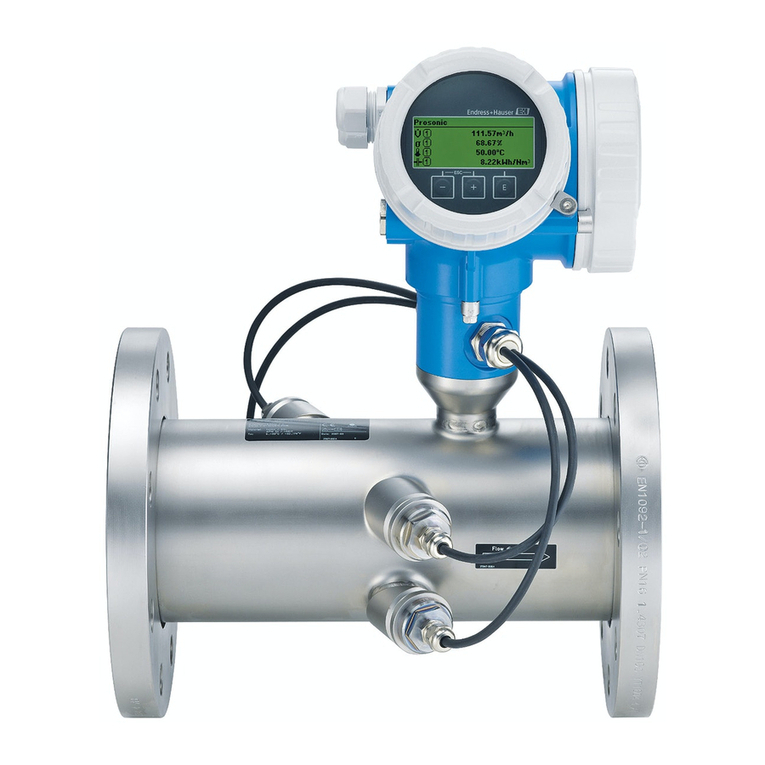
Endress+Hauser
Endress+Hauser Proline Prosonic Flow B 200 operating instructions
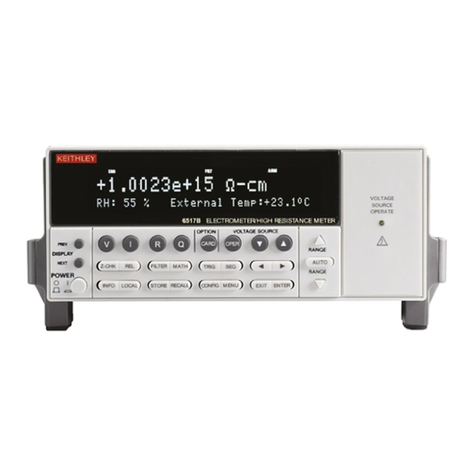
Keithley
Keithley 6517B Reference manual
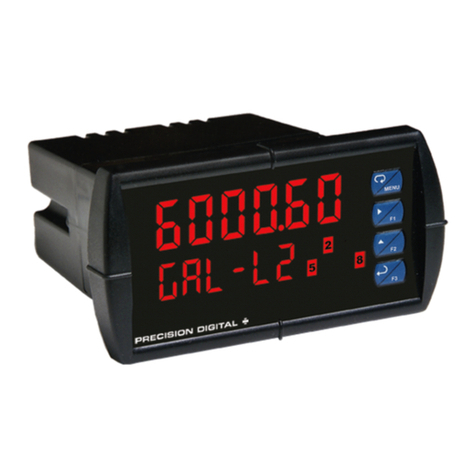
PRECISION DIGITAL
PRECISION DIGITAL PD6000-6R0 instruction manual
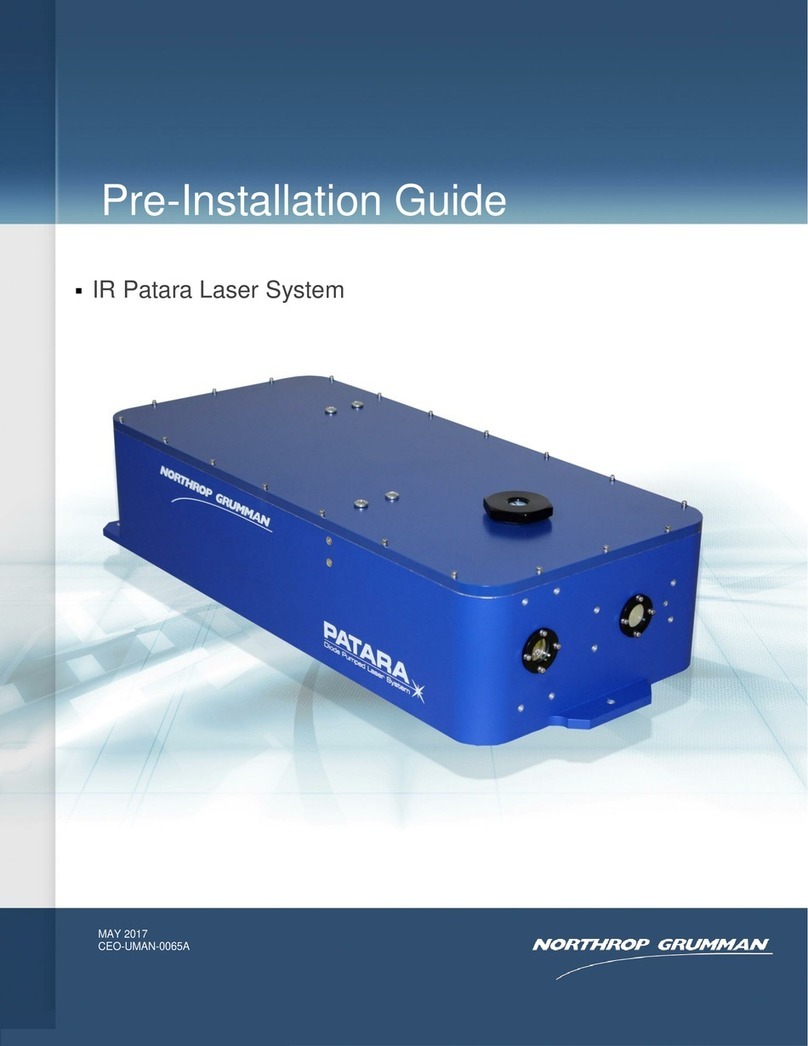
NORTHROP GRUMMAN
NORTHROP GRUMMAN IR Patara Laser System Pre-installation guide
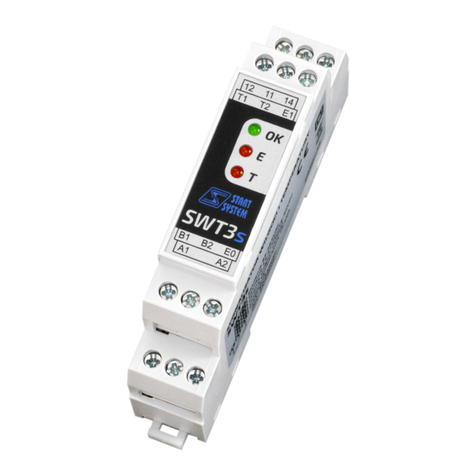
START SYSTEM
START SYSTEM SWT3s quick start guide

CEM
CEM CO-181 instruction sheet

NOVARENT
NOVARENT proceq quick start guide