Badger Meter 340 MB Btu Series User manual

BadgerMeter, Inc.
Installation &
Operation Manual
Model 340MB Modbus EnergyTransmitter
PN 820035
12-07
PRELIMINARY

2
TABLE OF CONTENTS
Introduction.......................................2
Installation ........................................3
Programming the Transmitter .........................6
Diagnostic Utility ...................................8
Network Steup.....................................9
Factory Default Settings .............................9
Specifications ....................................10
INTRODUCTION
The Badger Meter Model 340MB Btu transmitter is an economi-
cal, compact device for sub-metering applications that utilizes the
Modbus communications protocol.
The Model 340MB calculates thermal energy using the signal
from a flow sensor installed in a hydronic heating or chilled water
system, and signals from two 10 kΩtemperature thermistors,
100ΩRTD’s, or 1000ΩRTD’s installed in the system’s inlet and
outlet points. The flow input may be provided by any Badger
Meter impeller sensor and many other pulse or sine wave signal
flow sensors.
The onboard microcontroller and digital circuitry make precise
measurements and produce accurate, drift-free outputs. The
Model 340MB is configured using Badger MeterWindows®based
programmingsoftware. Calibrationinformationforthe flowsensor,
units of measurement, and type of temperature sensor may be
preselected or entered in the field. Btu transmitter information is
available when connected to a PC or laptop computer.This infor-
mation includes flow rate, flow total, both T1 and T2 temperature
probe information, energy rate, and energy total.
TheModel340MBtransmitterfeaturestwoLED’sto verifyModbus
and flow sensor input activity.
The Modbus communications protocol allows the Model 340MB
transmitterto be assigned an address,and allow all measurement
parameters to be transmitted on a single 3-wire RS-485 bus.
The Model 340MB Btu transmitter operates on AC or DC power
supplies ranging from 12 to 24 volts.
The compact cast epoxy body measures 3.65”(93mm) x
2.95”(75mm) and can be easily mounted in panels, enclosures
or on DIN rails.
PRELIMINARY

3
INSTALLATION
Mechanical Installation
The Model 340MB transmitter may be surface mounted onto a
panel, attached to DIN rails using adapter clips or wall mounted
using optional enclosures.
Location
Although the Model 340MB device is encapsulated, all wiring
connections are made to exposed terminals. The unit should be
protected fromweatherandmoisture in accordance withelectrical
codes and standard trade practices.
In any mounting arrangement, the primary concerns are ease of
wiring and attachment of the programming cable. The unit gener-
ates very little heat so no consideration need be given to cooling
or ventilation.
Surface Mount Installation
The Model 340MB may be mounted to the surface of any panel
usingdouble-sidedadhesivetapeorbyattachingfastenersthrough
the holes in the mounting flanges of the unit.
DIN Rail Mounting
Optional clips snap onto the mounting flanges allowing the Model
340MB to be attached to DIN 15, 32, 35 mm DIN rail systems.
Wall Mounting
Optional metal and plastic enclosures are available for the Model
340MB.The enclosure is first attached to the wall using fasteners
through its mounting holes.
After wiring, the transmitter may be attached to the enclosure
with the terminal headers facing inwards using the slots in the
mounting flanges. As an alternate mounting arrangement, the
Model 340MB may be fastened to the box cover using double-
sided adhesive tape.
Temperature Sensor Installation
The location of the temperature sensors with respect to the flow
sensor is important to the accuracy of the energy calculation.The
temperaturesensor installed closesttotheflow sensorwillbe con-
sidered asTemperature SensorT1. Temperature sensors should
not be installed closer than a distance equal to 10 pipe diameters
upstream or 5 pipe diameters downstream from the flow sensor.
Irregular velocity profiles caused by improperly located valves, fit-
tings, and thermowells, etc.can lead to inaccurate flow indication
and therefore affect accuracy of the energy calculation. Figure 2: Model 340MB Metal Box Dimensions
Figure 3: Model 340MB Plastic Box Dimensions
Figure 1: Model 340MB Dimensions
1.60”
(40.6mm)
3.65”
(92.7mm)
2.95”
(74.9mm)
.88”
(22mm)
.60”
(15mm)
Model: 340MB
S/N 340MB-XXXXXX
Comm LED
Data
Industrial
RTU/ASCII
Sensor Input
Shield
Signal
Signal +
Power Out
-
REF
+
_
Modbus
Factory Port
NT PDPU
D.I.C.
Comm
Port
+
-
Power In
AC C /DC
AC L /DC
1
2
3
Temp 1
1
3
Temp 2
2
Input LED
.20”
(5mm)
PRELIMINARY

4
Figure 4:
Side View - Typical 300 Series Removable Connector Wiring
Figure 5: Sample Power Supply Wiring Diagram
Electrical Installation
All connections to the Model 340MB are made to screw terminals
on removable headers.
Power Supply Wiring
The Model 340MB requires 12-24 volts AC or DC to operate.
The power connections are made to the ORANGE header. The
connections are labeled beside the header. Observe the polarity
shown on the label.
If a Badger Meter plug in type power supply (Model A-1026 or
A-503) is used, connect the black/white striped wire to the termi-
nal marked positive (+) and the black wire to the terminal marked
negative (-).
Note:
Connect the earth ground lug of the Model 340MB to a solid
earth ground with a wire which is as short as possible.This
will help prevent electrical interference from affecting the
Model 340MB’s normal operation.
Sensor Wiring
All flow sensor types connect to the four terminal header labeled
Sensor Input.
Series 200
Connect the flow sensor red wire to Model 340MB Sensor Input
Signal(+)terminal,andconnecttheflowsensorblackwiretoModel
340MB Sensor Input Signal (-) terminal. The bare wire connects
to the Sensor Input Shield terminal.
SDI Series (standard pulse output option)
Connect SDI terminal number 3 to the Model 340MB transmitter
Sensor Input Signal (+) terminal, and SDI terminal number 2 to
the Model 340MB transmitter Sensor Input Signal (-) terminal.
Connect the shield terminal of the SDI sensor tot he Sensor Input
Shield terminal of the Model 340MB transmitter.
Other Sensors
The Sensor Input Power Out terminal on the 340MB transmitter
supplies nominal 12VDC excitation voltage for 3-wire sensors.
Connect the signal (+) and signal (-) terminals on the sensor to
corresponding terminals on the 340MB transmitter.
Note:
The green input LED flashes on and off as sensor pulses
are received.
Industrial
AC C /DC
Signal +
Signal
Sensor Input
Model: 340MB
S/N 340BN-XXXXXX
Power Out
Comm LED
Shield
-
+
1
2
3
Temp 1
1
3
Temp 2
2
Input LED
Data
AC L /DC
Power In
-
+
DC+
or
AC Load
Series 200
or
SDI Sensor
Shield
(if applicable)
Red Wire
or
Signal +
Earth
Ground
DC -
or
AC Common
AC or DC
Power Supply
Black Wire
or
Signal -
Figure 6: Sample Sensor Wiring Diagram
PRELIMINARY

5
Figure 9: SampleWiring Diagram to Modbus Network
Note 1: Biasing, circuitry, and resistors for PU, PD, and NT terminals are integral part of 340MB transmitter.
Note 2: For the final 340MB transmitter in a given Modbus network, NT, PU, and PD jumpers should be in “open”position. Otherwise,
NT, PU, and PD should be in the “closed” position.
Note 3: For the final 340MB transmitter in a given Modbus network, all three network terminals (+), (-), and REF should be connected
to the Modbus buss. Otherwise, connect only terminals (+), (-) to the Modbus buss.
Temperature Element Wiring
Thermistors
BadgerMeter thermistorsarenot polarity sensitive. Thethermistor
locatedclosesttothe flow sensor, termedtemperaturesensorT1,
should beconnected toterminals 2and 3on terminal blockTemp 1.
The thermistor located farthest from the flow sensor, termed tem-
perature sensorT2, should be connected to terminals 2 and 3 on
terminal blockTemp2. As shownin the thermistorwiring diagram,
it is strongly recommended to install a jumper between terminals
1 and 3 for both thermistors. This is considered good practice for
all unused inputs to limit electromagnetic interference.
ResistanceTemperature Detectors (RTD’s)
Badger Meter RTD’s are three-wire devices. Two of these wires
are the same color, and one of these two wires is used for lead
compensation. The lead compensation wire is attached to ter-
minal 1. The other common color lead is attached to terminal 3.
The single color lead is attached to terminal 2. The RTD located
closest to the flow sensor, termed temperature sensorT1, should
be connected to terminal blockTemp 1. The RTD located farthest
from the flow sensor, termed temperature sensor T2, should be
connected to terminal block Temp 2.
Connecting the Modbus Buss
As shown in the Modbus Sample Wiring Diagram, the position
of jumpers on each 340MB transmitter and wiring between each
340MBtransmitterand the Modbusnetworkaredifferent depend-
ing on where the transmitter is installed, i.e. its nodal position.
For all but the final 340MB transmitter in a Modbus network, the
three jumpers NT, PU, and PD should be in the open position,
and only the (+) and (-) network terminals should be connected
to the Modbus buss. For the final 340MB transmitter in a Modbus
network,thethree jumpersNT,PU, andPDshould be intheclosed
position, and all three network terminals (+), (-), and REF should
be connected to the Modbus buss.
Note: The Model 340MB transmitter default polling address
must be changed before it is introduced into an existing
network to avoid possible address conflicts. Please refer to
programming instructions in the next section. Figure 8: RTDWiring Diagram
+5 VDC
Ω
Ω
Ω
Ω
Ω
Ω
1
2
3
Temp 1
1
3
Temp 2
2
Node "n"
Supply
Return
Supply
Return
Temp 2
1
2
3
Temp 1
1
3
2
Node 1
Comm LED
REF
PU PDNT
_
+
47k
120
47k
Comm LED
REF
PU PDNT
_
+
+5 VDC
47k
120
47k
REF
-
+
Modbus
PU
Note 2Note 1
Note 2
Ω
10k Thermistors
Jumpers
Note 3
100
Ω
RTD’s or 1000
Ω
RTD’s
NT
PD
PU
NT
PD
RTU/ASCII
T2 T1 T2 T1
+5 VDC
Ω
Ω
Ω
Ω
Ω
Ω
1
2
3
Temp 1
1
3
Temp 2
2
Node "n"
Supply
Return
Supply
Return
Temp 2
1
2
3
Temp 1
1
3
2
Node 1
Comm LED
REF
PU PDNT
_
+
47k
120
47k
Comm LED
REF
PU PDNT
_
+
+5 VDC
47k
120
47k
REF
-
+
Modbus
PU
Note 2Note 1
Note 2
Ω
10k Thermistors
Jumpers
Note 3
100
Ω
RTD’s or 1000
Ω
RTD’s
NT
PD
PU
NT
PD
RTU/ASCII
T2 T1 T2 T1
+5 VDC
Ω
Ω
Ω
Ω
Ω
Ω
1
2
3
Temp 1
1
3
Temp 2
2
Node "n"
Supply
Return
Supply
Return
Temp 2
1
2
3
Temp 1
1
3
2
Node 1
Comm LED
REF
PU PDNT
_
+
47k
120
47k
Comm LED
REF
PU PDNT
_
+
+5 VDC
47k
120
47k
REF
-
+
Modbus
PU
Note 2Note 1
Note 2
Ω
10k Thermistors
Jumpers
Note 3
100
Ω
RTD’s or 1000
Ω
RTD’s
NT
PD
PU
NT
PD
RTU/ASCII
T2 T1 T2 T1
Figure 7:Thermistor Wiring Diagram
PRELIMINARY

6
Programming the Model 340MBTransmitter
Prior to introducing the Model 340MB onto a Modbus network, it
must be configured for the type of input signal, pipe size, desired
units of measure, filter coefficient, and temperature sensor. The
defaultnetworkaddressshouldbeassignedtoanunusedaddress
to avoid conflicts with other instruments on the Modbus network.
To change settings in the 340MB transmitter, Windows®based
Badger Meter software must be installed and new values entered
as outlined below:
1. Install the Badger Meter Combo PC Software.
2. Connect the PC to the Model 340MB transmitter using the
Badger Meter Model A301 communications cable. Plug the
Model RS232 connector on the Model A301 cable to the
Model 340MB socket labeled “D.I.C.Comm port”, taking care
to properly align the tab on the plug and socket to maintain
polarity. Plug the Model DB9 connector on the opposite end
of the Model A301 cable to an available PC communications
port. If a cable with a Model DB9 connector is not available, a
USB to DB9 adapter (e.g.IOGEAR GUC232A) can be used.
3. Connect the Model 340MB transmitter to a power supply.
4. Open the Badger Meter Combo PC Software.
5. From the main screen, select Configuration and open the Set
Comm Port screen to assign the correct communications port
for the Model A301 cable as shown in the dialog boxes below.
Press the OK button to return to the Main screen.
6. Select Device and 340 from the menu bar as shown below.
7. Open the Device Type pull-down menu and select Modbus
protocol as shown below.
8. Select Configuration from the menu bar and open the Param-
eters screen as shown below.
To go to the
calibration
settings screen
select
Parameters
from either
place shown
PRELIMINARY

7
9. ProgramtheModel340MBtransmitterusingthediagrambelow
as a reference.
Note #1:
Badger Meter sensors are pulse type sensors. The K and Off-
set information is printed in the owners manual shipped with
the product. This information is also available on our website.
Calibration constants for other sensors must be supplied by the
manufacturer.
Note #2
Typically the temperature measured byT1 will be greater than T2
in a heating application and less than T2 in a cooling application.
The selection of one of these choices will determine if energy
calculations are made for heating only (T1>T2), cooling only
(T1<T2), or both (absolute).
Note #3
The filter coefficient screen allows adjustment of the flow and
energy filters. Filter settings determine how the Series 340MB
responds to actual changes in flow and energy.A scale of 0 -10is
used with10 providing the greatest degree of smoothing.
Step 1
Select the flow
sensor type and
enter the K and
Offset values.
See Note 1.
Step 6
Select the desired
units for energy
rate and energy
total.
Step 7
Press Send to
transmit calibration
data to the
transmitter.
Step 8
Press Exit to close
the Parameters Screen
and return to the main screen.
If required, press to view
current programming
of the transmitter.
If required, press to
enter factory default
programming.
Note: This will
overwrite all settings.
Step 5
Select the filter
coefficients for
flow and energy.
See Note 3.
Step 4
Select the type of
temperature sensor.
Step 3
Select the method of
computing the temperature
differential. See Note 2.
Step 2
Select the desired unit
for the temperature sensor.
10. AftersettingModel340MBparameters,press Exit and return
to the Main screen.
11. SelectConfigureRS485PorttoopentheMS/TPSetupscreen
as shown below.
PRELIMINARY

8
12. To set the address for the 340MB transmitter, open the New
Address pull-down menu and select the correct polling ad-
dress which matches the polling address entered into the
master controller for this node of the Modbus network. Press
theAssignNew Address buttontotransmitpolling information
to the 340MB transmitter.
13. TosettheDelebaudrateforcommunicationfromtheModbus
buss to the Model 340MB transmitter, open the New Baud
Ratepull-downmenu and select the desired value. The most
commonbaudrateis9600. Pressthe AssignNewBaudRate
button to transmit the symbol rate to the Model 340MB trans-
mitter. Press the Close button to return to the Main screen.
Modbus Diagnostic Utility
The MS/TP ReadBack diagnostic utility is provided as a helpful
tool to verify connection between the Model 340MB transmitter
andModbusnetworkwhen installing a transmitteror while trouble-
shootingfaultycommunicationbetweenanindividualnodeandthe
master controller. To use this utility, the Model 340MB transmitter
must be connected to a PC or laptop and the Modbus network
as outlined below.
1. Connect the PC to the Model 340MB transmitter using
the Badger Meter Model A301 communications cable.
Plug the RS232 connector on the Model A301cable to
the 340MB socket labeled D.I.C. Comm Port, taking
care to properly align the tab on the plug and socket to
maintain polarity. Plug the DB9 connector on the op-
posite end of the Model A301 cable to an available PC
communications port. If a cable with a DB9 connector
is not available, a USB to DB9 adapter (e.g. IOGEAR
GUC232A) can be used.
2. If not already installed, connect the Model 340MB trans-
mitter to the Modbus network. Connect all three Model
340MBnetworkterminals(+),(-),andREFtotheModbus
bussif thetransmitteris the final nodeinagivennetwork.
Otherwise,connect only terminals (+) and(-)totheMod-
bus buss. Confirm the correct position of jumpers on the
Model 340MB transmitter. For the final transmitter in a
given Modbus network, NT, PU, and PD jumpers should
bein“open”position. Otherwise, NT,PU, and PD should
be in the “closed” position. Please refer to the Sample
Wiring Diagram to Modbus Network found on page 5.
3. Open the Badger Meter Combo PC Software.
4. Follow steps 5 through 7 found on page 6 to open the
Model 340MB Main screen.
5. From the Main screen, select MS/TP ReadBack.
PRELIMINARY

9
This will open the MS/TP Check screen as shown below.
PresstheRetrieveParametersbuttonwhichshoulddisplay340MB
transmitter object data as shown below.
The LED located next to the 340MB network port, labeled “Comm
LED”, will flash once to visually confirm communication between
the 340MB transmitter and Modbus master controller.
Use the scroll bar to view all object data.
If the 340MB transmitter fails to communicate with the Modbus
master controller, check that the correct polling address was
entered in step 12 found on page 8, the integrity of the network
port connection and, if necessary, settings in the Modbus master
controller.
Press the Close button to return to the Main Screen.
NETWORK SET-UP
The following Register Map is provided to assist in the program-
ming of the Modbus network.
MODEL 340MB REGISTER MAP
Register Name Address Data Type R/W
Inlet Temperature 0 IEEE754 Float Read Only
Outlet Temperature 2 IEEE754 Float Read Only
Input Frequency 4 IEEE754 Float Read Only
Total Volume 6 IEEE754 Float R/W
Total Energy 8 IEEE754 Float R/W
Flow Rate 10 IEEE754 Float Read Only
Energy Rate 12 IEEE754 Float Read Only
K Factor 14 IEEE754 Float R/W
Offset 16 IEEE754 Float R/W
Temperature Calculation Mode 18 IEEE754 Float R/W
Flow Filter Coefficient 20 IEEE754 Float R/W
Temperature Filter Coefficient 22 IEEE754 Float R/W
Specific Heat Capacity 24 IEEE754 Float R/W
Fluid Density 26 IEEE754 Float R/W
Temp In A Coefficient 28 IEEE754 Float R/W
Temp In B Coefficient 30 IEEE754 Float R/W
Temp In C Coefficient 32 IEEE754 Float R/W
Temp In Offset 34 IEEE754 Float R/W
Temp Out A Coefficient 36 IEEE754 Float R/W
Temp Out B Coefficient 38 IEEE754 Float R/W
Temp Out C Coefficient 40 IEEE754 Float R/W
Temp Out Offset 42 IEEE754 Float R/W
All variables above take two Modbus register locations.
(4 bytes). Note some registers are read only.
MODEL 340MB FACTORY DEFAULT SETTINGS
The table below is a list of factory default setting for all 340MB
variables. These settings can be changed by accessing the pa-
rameters sensor (page 7) or Configure MS/TP screen (page 8)
to best fit your application.As new valves are assigned, they can
be written in the blank provided next to each variable for future
reference.
Description Default Value Customer Value
Flow Sensor Type Pulse
1eulaV"K"
"Offset" Value 0mpgetaRwolF
Flow Total gallons
Temperature °F
Energy Calculation absolute
Temperature Sensor Type thermistor
Energy Rate kBTU/hr
Energy Total BTU
Flow Filter Coefficient 5
Energy Filter Coefficient 1
Factory Default Settings - Model 340MB
PRELIMINARY

10
Communication Port
RS-485 with termination, pull up and
pull down jumpers
OperatingTemperature
0° C to +70° C
32° F to +158° F
StorageTemperature
-40° C to +85° C
-40° F to +185° F
Weight
4.8 oz. with connector headers
installed
SENSOR CALIBRATION
Badger Meter
Use K and Offset provided in sensor
owner’s manual
Other Sensors
Check with factory
UNITS OF MEASURE
Flow measurement
Rate:
gpm, gph, l/sec, l/min, l/hr, ft3/sec,
ft3/min, ft3/hr, m3/sec, m3/min, m3/hr
Total:
gallons, liters, cubic feet, cubic
meters
Energy measurement
Rate
kBtu/min, kBtu/hr, kW, MW, hp, tons
Total
Btu, kBtu, MBtu, kWh, MWh, kJ, MJ
Temperature Units
Fahrenheit, Centigrade
PROGRAMMING
Requires PC or laptop running
Windows®2000, XP
Badger Meter Model 340BN
programming kit containing software
and Model A-301 programming cable is
required for programming and setup
SPECIFICATIONS
Power
Power supply options:
12-24 VAC rms Tolerance
12-24 VDC Tolerance
Current draw:
< 70mA @ 12 VDC
Flow Sensor Input
Pulse type sensors:
Signal amplitude:
2.5 VDC threshold
Signal limits:
Vin < 35V (DC or AC peak)
Frequency:
0-10kHz
Pull-up:
15 VDC @ 2 kΩSource Impedance
Sine wave sensors:
Signal amplitude:
30 mV p-p threshold
Signal limits:
Vin < 35V (DC or AC peak)
Frequency:
0-10kHz
Power out terminal
Excitation voltage 3 wire sensors:
15 VDC@500ΩSource Impedance
Temperature Sensor Input
2 required:
10 kΩthermistor, 2 wire, type II,
10 kΩ@ 25°C
100Ωplatinum RTD, DIN
calibration curve, conforms to
IEC-751 Standard
1000Ωplatinum RTD, DIN
calibration curve, conforms to
IEC-751 Standard
calibration range 0-150°C
Metal Enclosure Dimensions
Plastic Enclosure Dimensions
PRELIMINARY

11
(This page intentionally left blank.)
PRELIMINARY

Due to continuous research, product improvements and enhancements, Badger
Meter reserves the right to change product or system specifications without notice,
except to the extent an outstanding contractual obligation exists.
BadgerMeter, Inc.
6116 E. 15th Street, Tulsa, Oklahoma 74112
(918) 836-8411 / Fax: (918) 832-9962
www.badgermeter.com
Please see our website at www.dataindustrial.com
for specific contacts.
Copyright © Badger Meter, Inc. 2007.All rights reserved.
Data Industrial®is a registered trademark of Badger Meter, Inc.
Windows®is a registered trademark of Microsoft Corporation.
BACnet®is a registered trademark of American Society of Heating, Refrigerating and Air-Conditioning Engineers (ASHRAE).
PRELIMINARY
Table of contents
Other Badger Meter Transmitter manuals
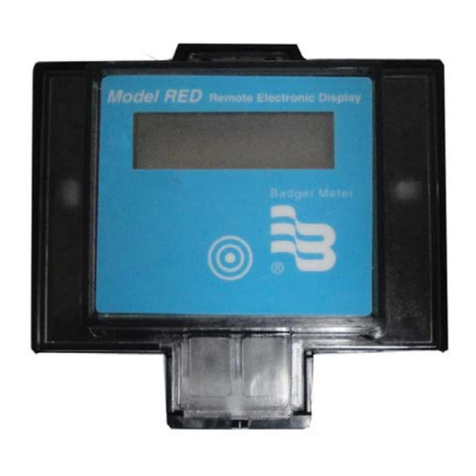
Badger Meter
Badger Meter Recordall RED Installation and user guide
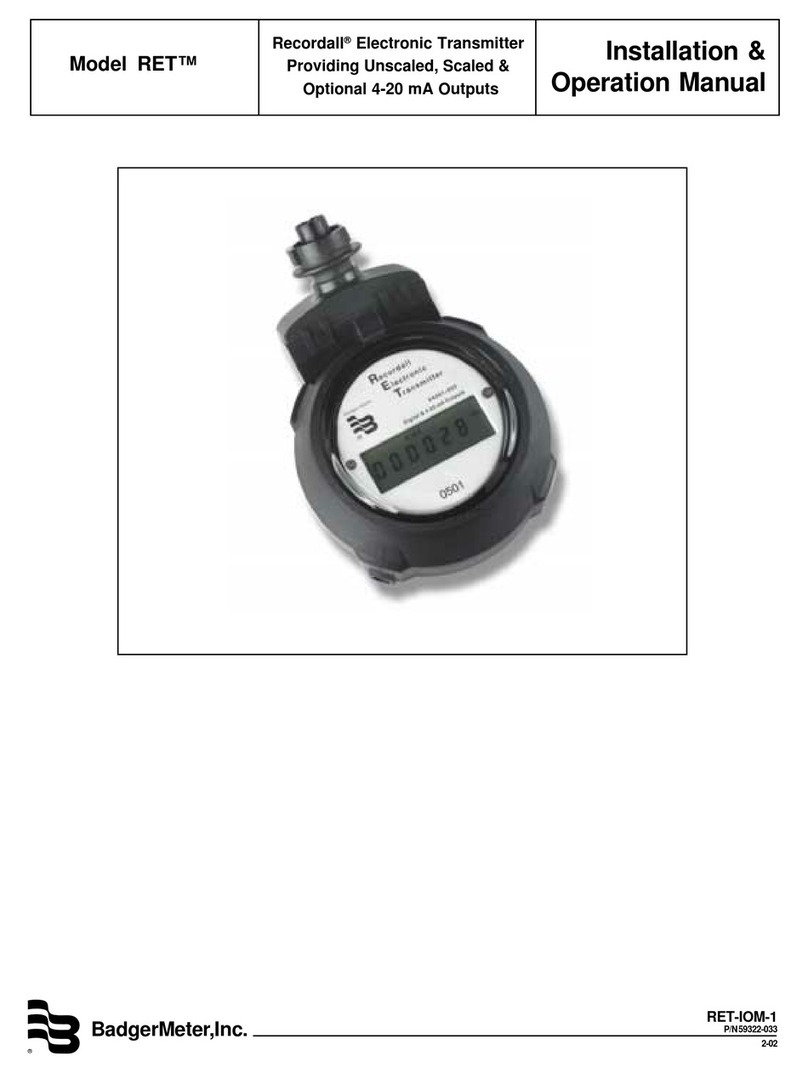
Badger Meter
Badger Meter Recordall RET User manual
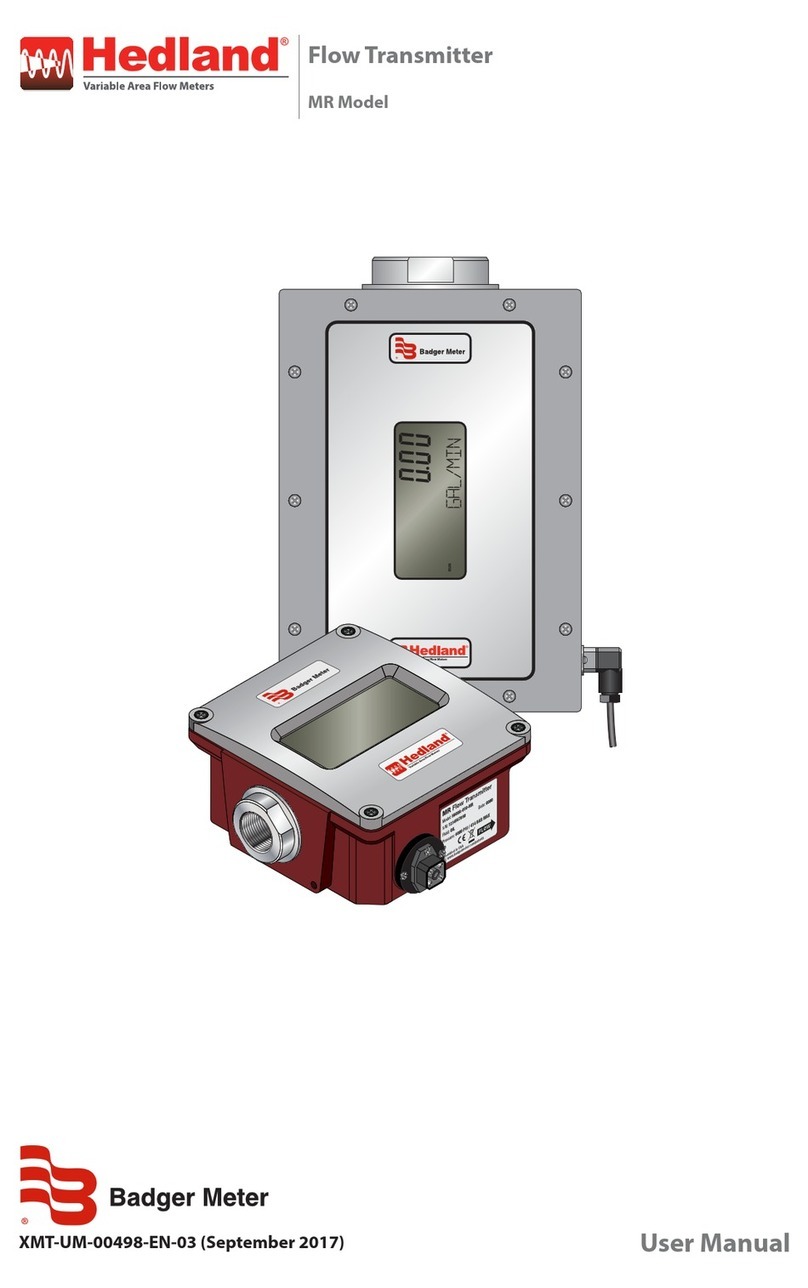
Badger Meter
Badger Meter Hedland MR User manual
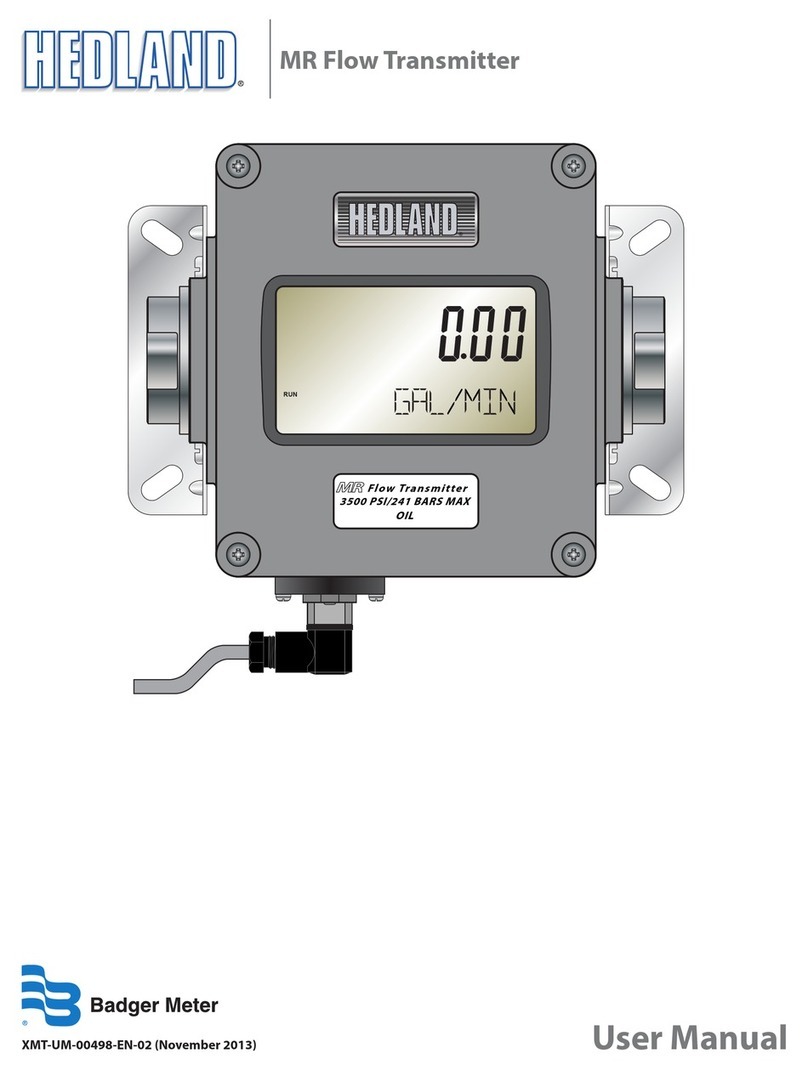
Badger Meter
Badger Meter HEDLAND MR Series User manual
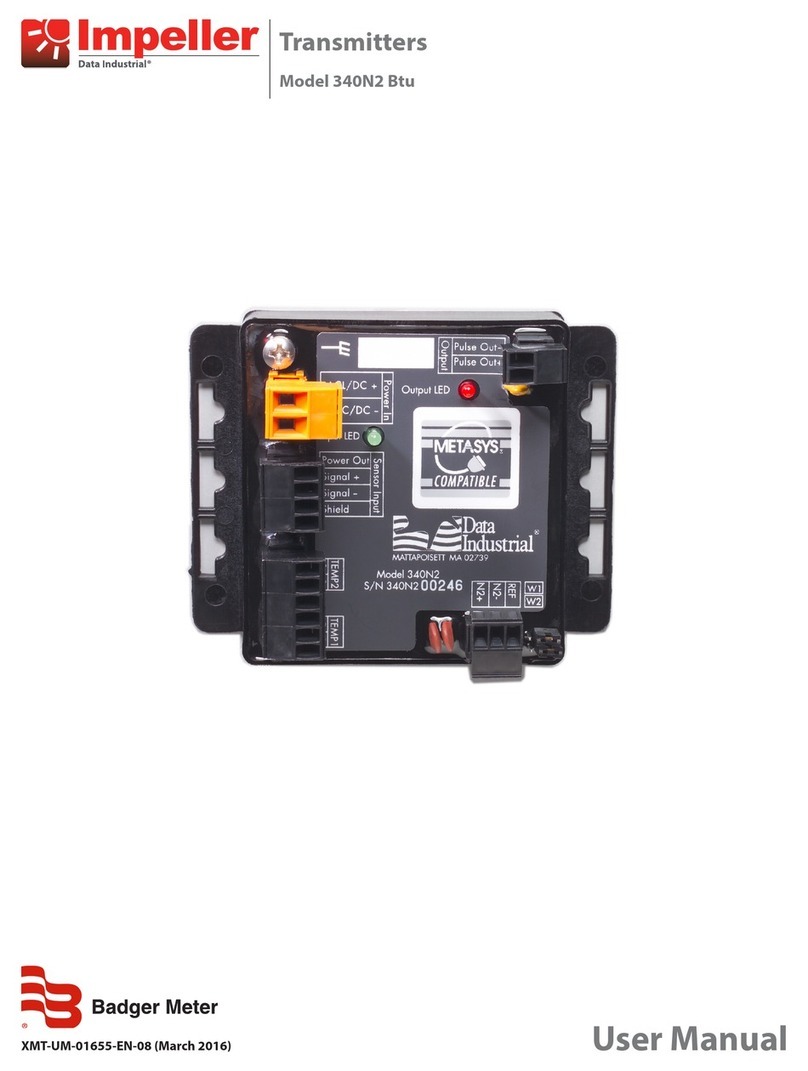
Badger Meter
Badger Meter 340N2 User manual
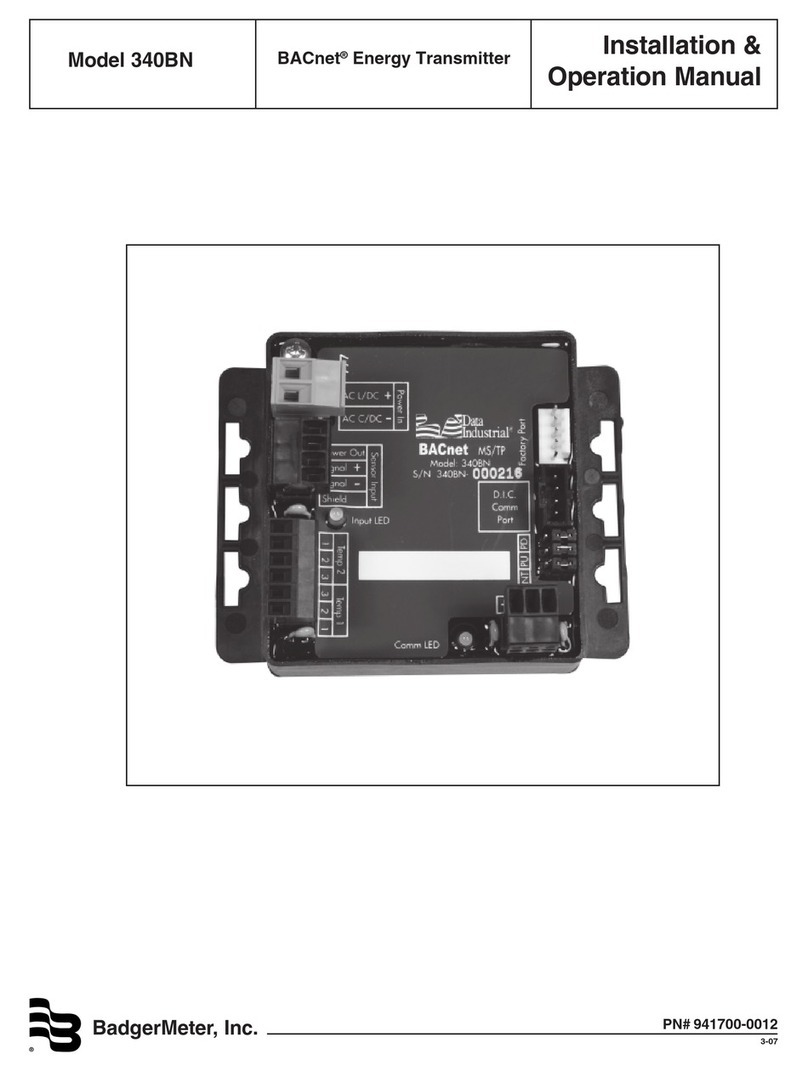
Badger Meter
Badger Meter 340BN User manual
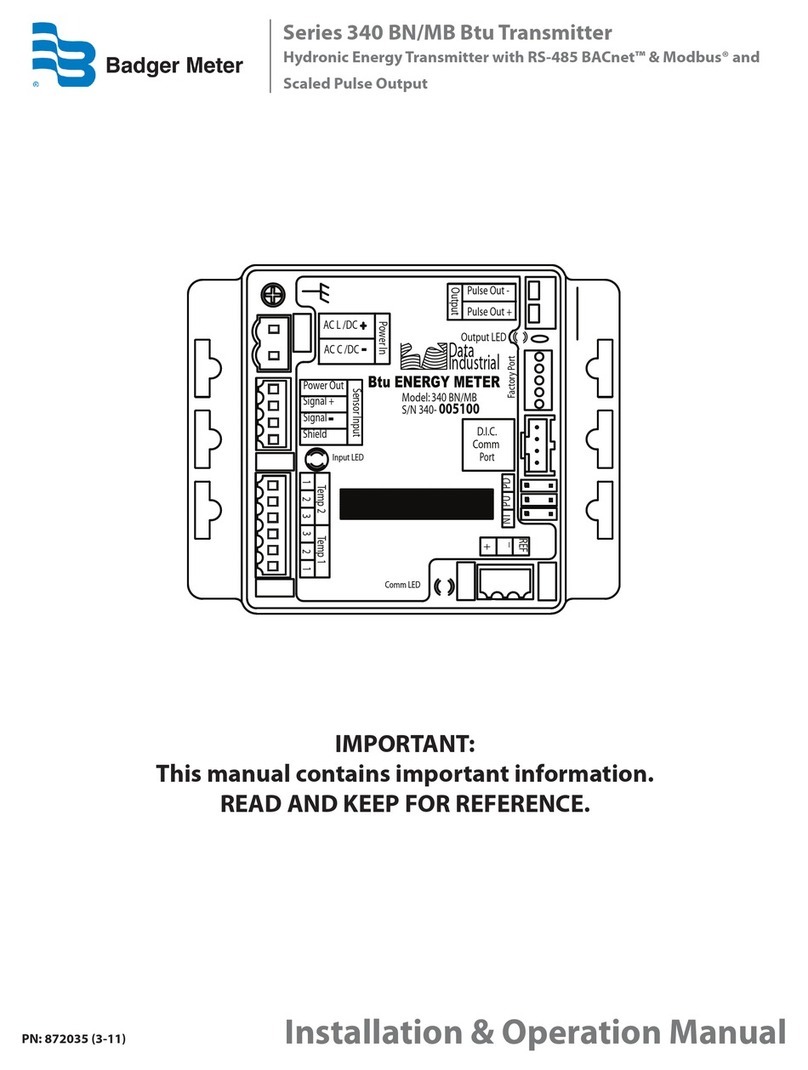
Badger Meter
Badger Meter 340BN User manual

Badger Meter
Badger Meter Data Industrial 340 BN/MB User manual
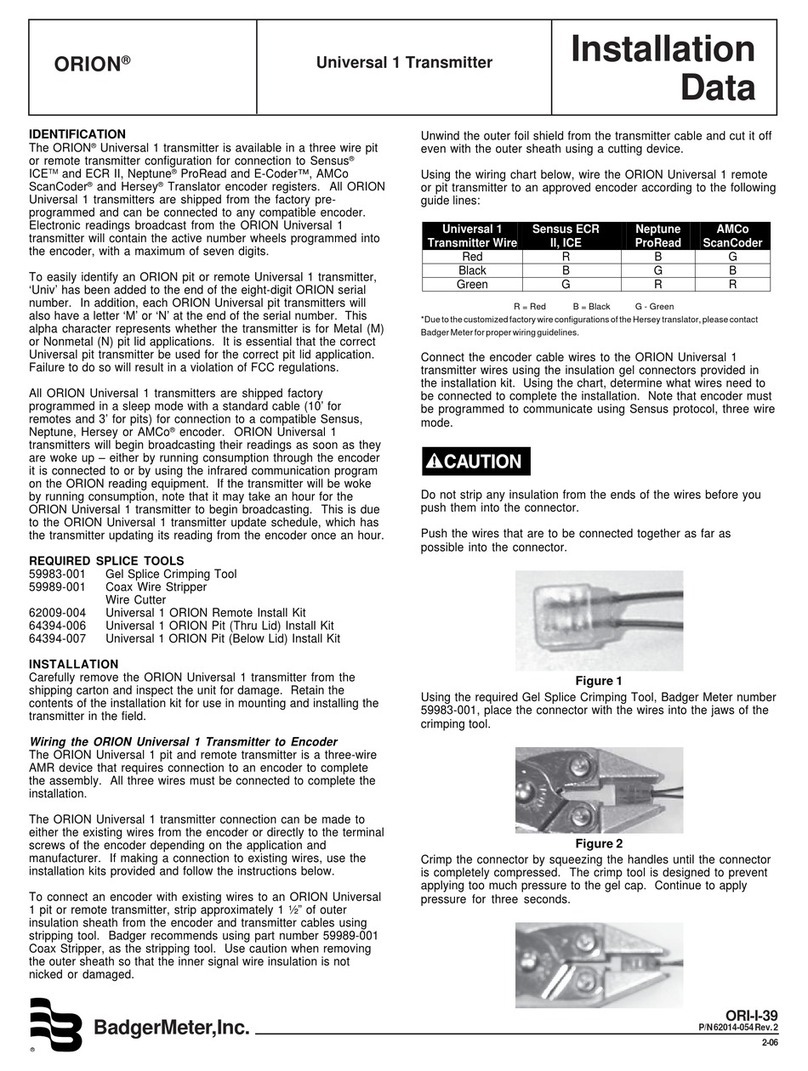
Badger Meter
Badger Meter Orion Universal 1 Transmitter Installation and user guide
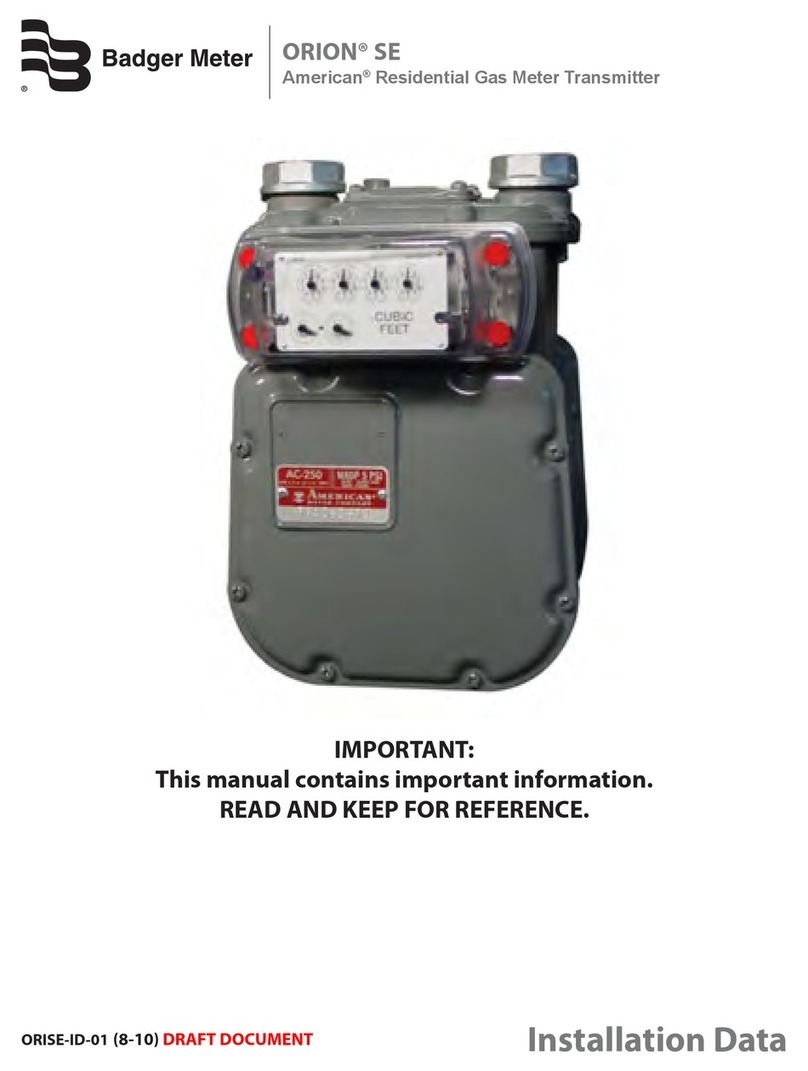
Badger Meter
Badger Meter ORION SE Installation and user guide