Basler RDP-110C User manual

Publication
9318100995
Revision
—
Instructions
Date
Sep 2020
Copyright
2020
For terms of service relating to this product and software, see the Commercial Terms of Products and Services document available at www.basler.com/terms.
www.basler.com
+1 618.654.2341 (USA)
info@basler.com
Model
RDP-110C
Description
Remote Display Panel
CONTENTS
Introduction .................................................................................................................................................................1
Comprehensive Annunciation Capabilities .............................................................................................................1
Rugged and Flexible Construction..........................................................................................................................2
Simple Connections ................................................................................................................................................2
Style Number ..............................................................................................................................................................2
Specifications..............................................................................................................................................................2
Control Power .........................................................................................................................................................2
Power Dissipation ...................................................................................................................................................2
Communication .......................................................................................................................................................2
Audible Alarm..........................................................................................................................................................2
Temperature............................................................................................................................................................2
Weight .....................................................................................................................................................................3
Type Test Data........................................................................................................................................................3
Agency Certification ................................................................................................................................................3
Functional Description ................................................................................................................................................3
Inputs ......................................................................................................................................................................3
Microprocessor........................................................................................................................................................4
Firmware .................................................................................................................................................................4
Controls and Indicators...............................................................................................................................................4
Programmable Alarm and Pre-Alarm Indicator Configuration....................................................................................5
Installation...................................................................................................................................................................6
Mounting .................................................................................................................................................................6
Connections ............................................................................................................................................................9
Testing ..................................................................................................................................................................... 11
Test Equipment and Setup .................................................................................................................................. 11
Test Procedure..................................................................................................................................................... 11
INTRODUCTION
The RDP-110C Remote Display Panel provides remote annunciation of engine/generator status. When used with
Basler Digital Genset Controllers DGC-2020, DGC-2020ES, DGC-2020HD, DGC-500, or DGC-1000, the RDP-
110C provides compliance with NFPA 110 Level 1 and Level 2 requirements. The RDP-110C is suitable for use
with isolated generators or paralleled generating systems.
The RDP-110C serves as the successor to the RDP-110. The RDP-110C features identical functionality in a more
compact size, enabling its use in a broader range of applications. An optional adaptor plate enables convenient
replacement of an RDP-110 with an RDP-110C.
Comprehensive Annunciation Capabilities
The RDP-110C is equipped with the following LED indicators:
•RDP-110C control power applied
•Genset supplying load
•DGC not operating in Auto mode
•Six fixed-function alarms
•Two programmable alarms

Publication
9318100995
Revision
—
Instructions
Date
Sep 2020
Page
2 of 12
•Five fixed-function pre-alarms
•Two programmable pre-alarms
An audible alarm indicates the presence of alarms, pre-alarms, and when the DGC is taken out of Auto mode. An
Alarm Silence pushbutton resets the audible alarm.
Operation of the audible alarm and all visual indicators can be verified with the Lamp Test pushbutton.
Rugged and Flexible Construction
A rugged, compact metal case provides improved electromagnetic compatibility and make the RDP-110C
resistant to moisture, salt fog, dust, dirt, and chemical contaminants. Two available mounting configurations
provide the option of semi-flush mounting or surface (projection) mounting. Conduit knockouts on the case enable
the RDP-110C to be used as a “pass-through” or junction box for other site wiring.
Simple Connections
RDP-110C connections consist of control power wiring and wiring for communication between the DGC and RDP-
110C. Two-wire, RS-485 communication between the RDP-110C and DGC simplifies wiring and ensures
electrical noise immunity over long distances.
STYLE NUMBER
A style number defines the RDP-110C mounting configuration and Digital Genset Controller compatibility. The
style number appears on a label located on the right side of the case. Figure 1 illustrates the RDP-110C style
chart.
Figure 1. RDP-110C Style Chart
SPECIFICATIONS
Control Power
Range: 8 to 32 Vdc
Burden: 2 W maximum
Power Dissipation
Continuous: 3.5 W
Maximum: 5.3 W
Communication
The RDP-110C communicates through a serial, RS-485 port terminated with a 100 Ωresistor.
Audible Alarm
Frequency: 2.9 kHz, ±500 Hz
Sound level: 90 DB(A) at 24 in. (61 cm)
Temperature
Operating range: –40 to 70°C (–40 to 158°F)
Storage range: –40 to 85°C (–40 to 185°F)

Publication
9318100995
Revision
—
Instructions
Date
Sep 2020
Page
3 of 12
Weight
F1 style: 1.04 kg (2.3 lb.)
S1 style: 1.25 kg (2.75 lb.)
Type Test Data
Dielectric Strength
Withstood 500 Vdc for 1 minute between chassis ground and the circuit grouping of the control power and RS-485
terminals.
Radio Frequency Interference (RFI)
Tested using a 5-wattt handheld transceiver operating at random frequencies centered around 144 MHz and 440
MHz with the antenna located within 6 inches (15 centimeters) of the device in both the vertical and horizontal
planes.
Vibration
Withstood 2 G over a range of 10 to 500 Hz for three hours in each of the three mutually perpendicular planes, 15
sweeps at 12 minutes each, for a total of nine hours of vibration. No structural damage or degradation of
performance was observed.
Shock
Withstood three 15 G shocks in each direction in each of the three mutually perpendicular planes for a total of 18
shocks.
Agency Certification
UL recognized per Standard 508.
FUNCTIONAL DESCRIPTION
The RDP-110C uses microprocessor-based technology to provide remote annunciation of engine and generator
parameters. RDP-110C function blocks are illustrated in Figure 2 and described in the following paragraphs.
Figure 2. RDP-110C Function Blocks
Inputs
RDP-110C inputs consist of a control power input, a communication interface, and pushbuttons. Control power
and communication connections are made on the circuit board attached to the front panel.
Control Power
The dc control power input is applied to an internal switching power supply that provides filtered 5 Vdc operating
power for the RDP-110C circuitry.
The control power input accepts nominal battery voltage of 12 Vdc or 24 Vdc. The acceptable range of dc control
power is 8 to 32 Vdc.
Microprocessor
Power
Supply
RS-485
Interface
Lamp
Test
Alarm
Silence
LED Indicators Audible Alarm
12/24 Vdc From DGC
D2829-19

Publication
9318100995
Revision
—
Instructions
Date
Sep 2020
Page
4 of 12
Communication Interface
RDP-110C annunciation commands are received from the DGC over an RS-485 serial communication bus.
Received communication inputs are converted to signals suitable for use by the RDP-110C.
Pushbuttons
Two front panel pushbuttons accept local inputs: Lamp Test and Alarm Silence.
LED and horn operation can be verified by pressing the Lamp Test pushbutton.
An audible alarm is reset by pressing the Alarm Silence pushbutton. Once reset, the horn is reactivated only by
the occurrence of another separate pre-alarm or alarm condition.
Microprocessor
The microprocessor executes embedded firmware which interprets commands received from the DGC and
annunciates pre-alarm and alarm conditions by lighting the appropriate indicators and sounding the horn.
Firmware
Embedded firmware controls power-up initialization, annunciation element setup, and serial communication.
When control power is applied to the RDP-110C, the firmware initiates a power-up sequence, checks the onboard
memory, activates all annunciation functions, and begins monitoring for inputs from the DGC.
CONTROLS AND INDICATORS
RDP-110C controls and indicators consist of pushbuttons, LEDs, and an audible alarm (horn). These front panel
elements are illustrated in Figure 3 and described in Table 1. The lettered locators in Figure 3 correspond to the
lettered descriptions of Table 1.
Figure 3. Controls and Indicators

Publication
9318100995
Revision
—
Instructions
Date
Sep 2020
Page
5 of 12
Table 1. Control and Indicator Descriptions
Locator
Description
A
Green Display Panel On LED lights when control power is applied to the RDP-110C.
B
Green EPS Supplying Load LED lights when the genset is supplying more than 2% of rated
load.
C
The horn sounds when an alarm or pre-alarm exists or the connected DGC is not operating in
Auto mode. The horn is silenced by pressing the Alarm Silence pushbutton (locator E).
D
The amber Pre-Alarm LEDs light when the corresponding pre-alarm setting is exceeded.
Conditions annunciated by the pre-alarm LEDs include:
•High coolant temperature,
•Low coolant temperature,
•Low oil pressure,
•Low fuel level,
•Weak battery,
•Battery overvoltage, and
•Battery charger failure.
When the RDP-110C is used with a DGC-2020, the bottom two LEDs (Battery Overvoltage and
Battery Charger Failure) can be reprogrammed to indicate other pre-alarm conditions. See
Programmable Alarm and Pre-Alarm Configuration for information about configuring the two
programmable pre-alarm indicators.
E
RDP-110C controls consist of two pushbuttons.
•The Alarm Silence pushbutton silences the horn (locator C).
•The Lamp Test pushbutton can be used to verify operation of all RDP-110C LEDs and
the horn.
F
The red Alarm LEDs light when the corresponding alarm settings are exceeded. Conditions
annunciated by the alarm LEDs include:
•Low coolant level,
•High coolant temperature,
•Low oil pressure,
•Overcrank,
•Overspeed,
•Emergency stop activated,
•Fuel leak/sender failure, and
•Sender failure.
When the RDP-110C is used with a DGC-2020, DGC-2020ES, or DGC-2020HD, the bottom
two LEDs (Fuel Leak/Sender Failure and Sender Failure) can be reprogrammed to indicate
other alarm conditions. See Programmable Alarm and Pre-Alarm Configuration for information
about configuring the two programmable alarm indicators.
G
Red Switch Not in Auto LED lights when the DGC is not operating in Auto mode.
PROGRAMMABLE ALARM AND PRE-ALARM INDICATOR CONFIGURATION
When used with a DGC-2020, DGC-2020ES, or DGC-2020HD, the RDP-110C has the added capability of
programmable alarm and pre-alarm indicators. This ability applies only to the DGC-2020, DGC-2020ES, or DGC-
2020HD and is not available when the RDP-110C is paired with the DGC-500 or DGC-1000.
Up to two alarm LEDs and two pre-alarm LEDs may be reprogrammed to suit the needs of a particular
application. The two bottommost alarm LEDs are preconfigured in DGC logic to annunciate a fuel leak/sender
failure and sender failure. The two bottommost pre-alarm LEDs are preconfigured in DGC logic to annunciate
battery overvoltage and a battery charger failure. These LEDs are labeled as such with replaceable cards (Figure
4) that can be relabeled to match the function of each programmable indicator.

Publication
9318100995
Revision
—
Instructions
Date
Sep 2020
Page
6 of 12
Figure 4. Programmable Alarm and Pre-Alarm Label Cards
Information about configuring DGC logic to provide other alarm and pre-alarm annunciations is available in the
appropriate DGC instruction manual. To relabel the RDP-110C programmable alarm and pre-alarm LEDs,
perform the following steps.
1. Print the label text on readily-available address label sheets. The label cards accommodate adhesive-
backed labels measuring 0.25 by 1.5 inches. Brady®B33-45-423 or similar is suitable for this purpose.
2. Remove all control power from the RDP-110C.
3. Remove the four Phillips screws from the front panel and separate the front panel from the conduit box.
Disconnect the connector attached to the circuit board mounted to the front panel. When handling the
front panel, avoid touching the circuit board.
4. Lay the front panel face-down on a suitable work surface.
5. Grasp the tab of the label card to be changed and pull it free. The two label cards are located near the
two lower corners of the circuit board. When facing the back of the panel, the pre-alarm label card is on
the left and the alarm label card is on the right.
6. Apply the labels created in step 1 to the label cards. The rectangle outlines on each label card serve as
guides for attaching the labels.
7. After applying the new labels, insert each label card into the appropriate panel slot. Ensure that each
label card is oriented properly by viewing the custom labels through the label windows of the front panel.
8. Move the panel assembly adjacent to the conduit box and reconnect the cables to the two circuit board
connectors.
9. Secure the front panel to the conduit box with the four Phillips screws removed in step 3. Maximum
torque for these screws is 17 inch-pounds or 2 newton meters.
10. If desired, verify the function of the reprogrammed indicators before returning the RDP-110C to service.
INSTALLATION
A NEMA 1 enclosure makes the RDP-110C resistant to moisture and dust infiltration. Its metal construction
improves immunity to electromagnetic interference. Conduit knockouts on the case enable the RDP-110C to be
used as a “pass-through” or junction box for other site wiring. Two available mounting configurations provide the
option of semi-flush mounting or surface (projection) mounting.
If the RDP-110C will not be installed immediately, store it in the original shipping package in a moisture- and dust-
free environment.
Mounting
RDP-110C mounting dimensions are illustrated in Figure 5, Figure 6, and Figure 7. Dimensions ae shown in
inches with millimeters in parenthesis.
RDP-110 Replacement
An optional adaptor plate (P/N 9318100009) is available for replacement of an RDP-110 with an RDP-110C. The
replacement process is as follows.
1. Remove the RDP-110C front panel from its enclosure and attach it to the adaptor plate using the same
screws removed from the RDP-110C.
2. Remove the RDP-110 from its enclosure and secure the RDP-110C and adaptor plate assembly to the
RDP-110 enclosure using the screws removed from the RDP-110.

Publication
9318100995
Revision
—
Instructions
Date
Sep 2020
Page
7 of 12
Figure 5. Mounting Dimensions, Rear, F1 and S1 Styles

Publication
9318100995
Revision
—
Instructions
Date
Sep 2020
Page
8 of 12
Figure 6. Mounting Dimensions and Knockout Locations, Sides, F1 and S1 Styles

Publication
9318100995
Revision
—
Instructions
Date
Sep 2020
Page
9 of 12
Figure 7. Mounting Dimensions and Knockout Locations, Top and Bottom, F1 and S1 Styles
Connections
RDP-110C connections are made with a plug-in connector that mates with a header on the lower edge of the
RDP-110C circuit board. The circuit board connections, illustrated in Figure 8, are accessed by removing the front
panel from the conduit box.
Note
Ensure that the RDP-110C is hard-wired to earth ground with no
smaller than 16 AWG (1.5 mm2) copper wire attached to the conduit
box ground connection.
DC control power applied to the 12/24 (+) and DC COM (–) terminals
must be of the correct polarity. Incorrect dc control power polarity will
prevent the RDP-110C from functioning.

Publication
9318100995
Revision
—
Instructions
Date
Sep 2020
Page
10 of 12
Figure 8. Circuit Board Connections
Ground Connection
The RDP-110C grounding point consists of a 10-32 threaded hole located on the back of the enclosure. The
ground connection should be made with wire no smaller than 16 AWG (1.5 mm2).
Connector Wiring
Note the following guidelines when wiring the circuit board connector:
•Connections should be made with wire no smaller than 20 AWG (0.5 mm2)
•Maximum conductor size for each terminal is 12 AWG (4 mm2)
•Strip the insulation from each wire to reveal 0.28 inches (7 millimeters) of exposed conductor
•Apply no more than 4.4 in-lb (0.5 N•m) of torque to each terminal screw
RS-485 Communication Connections
Twisted-pair conductors are recommended for the communication wiring between the DGC and RDP-110C.
Overly long wiring runs may impair communication between the DGC and RDP-110C. Do not exceed an RS-485
conductor length of 4,000 feet (1,219 meters).
RS-485 Terminating Resistor
The RS-485 communication connection is internally terminated with a 100 Ω resistor. Connecting multiple display
panels may necessitate removal of this terminating resistor (R65). R65 is located on the back side of the circuit
board so the circuit board must be separated from the front panel in order to remove the surface-mount resistor.
Remove the five nuts from the front panel studs to free the circuit board and gain access to R65. Figure 9
illustrates the location of R65 on the back side of the circuit board.
Consult standard TIA/EIA-485 for guidance on the electrical requirements of multipoint communication systems.
Figure 9. RS-485 Terminating Resistor Location

Publication
9318100995
Revision
—
Instructions
Date
Sep 2020
Page
11 of 12
Typical Connections
Typical RDP-110C connections are shown in Figure 10.
Figure 10. Typical Connections
TESTING
A built-in test mode enables field testing of RDP-110C operation.
Test Equipment and Setup
Equipment needed for testing RDP-110C operation is listed below. Connections for the test are illustrated in
Figure 11.
•Power supply, 24 Vdc
•Fuse, 1 ampere
•Signal generator, 10 Hz, square wave, 5 volts peak-to-peak
Figure 11. RDP-110C Test Setup
Test Procedure
1. Connect the RDP-110C test setup as shown in Figure 11.
2. Apply 24 Vdc control power. The Display Panel On LED should light.
3. Press and hold the Lamp Test pushbutton. All LEDs should light and the horn should sound.
4. Release the Lamp Test pushbutton to reset the indicators and horn.
5. Apply the 10 Hz signal.
6. Press and release the Lamp Test pushbutton. Observe that the LEDs and horn annunciate in the
following sequence. This sequence will repeat until the Alarm Silence pushbutton is operated.

Publication
9318100995
Revision
—
Instructions
Date
Sep 2020
Page
12 of 12
a. Switch Not in Auto
b. Low Coolant Level Alarm
c. High Coolant Temperature Alarm
d. Low Oil Pressure Alarm
e. Overcrank Alarm
f. Overspeed Alarm
g. Emergency Stop Activated Alarm
h. Factory Selectable LED
i. Sender Failure Alarm
j. EPS Supplying Load
k. High Coolant Temperature Pre-Alarm
l. Low Coolant Temperature Pre-Alarm
m. Low Oil Pressure Pre-Alarm
n. Low Fuel Level Pre-Alarm
o. Battery Overvoltage Pre-Alarm
p. Weak Battery Pre-Alarm
q. Battery Charger Failure Pre-Alarm
r. Audible Alarm (Horn)
7. Press and release the Alarm Silence pushbutton to end the annunciation sequence.
8. Remove the 10 Hz signal and 24 Vdc control power.
Table of contents
Popular Industrial Monitor manuals by other brands
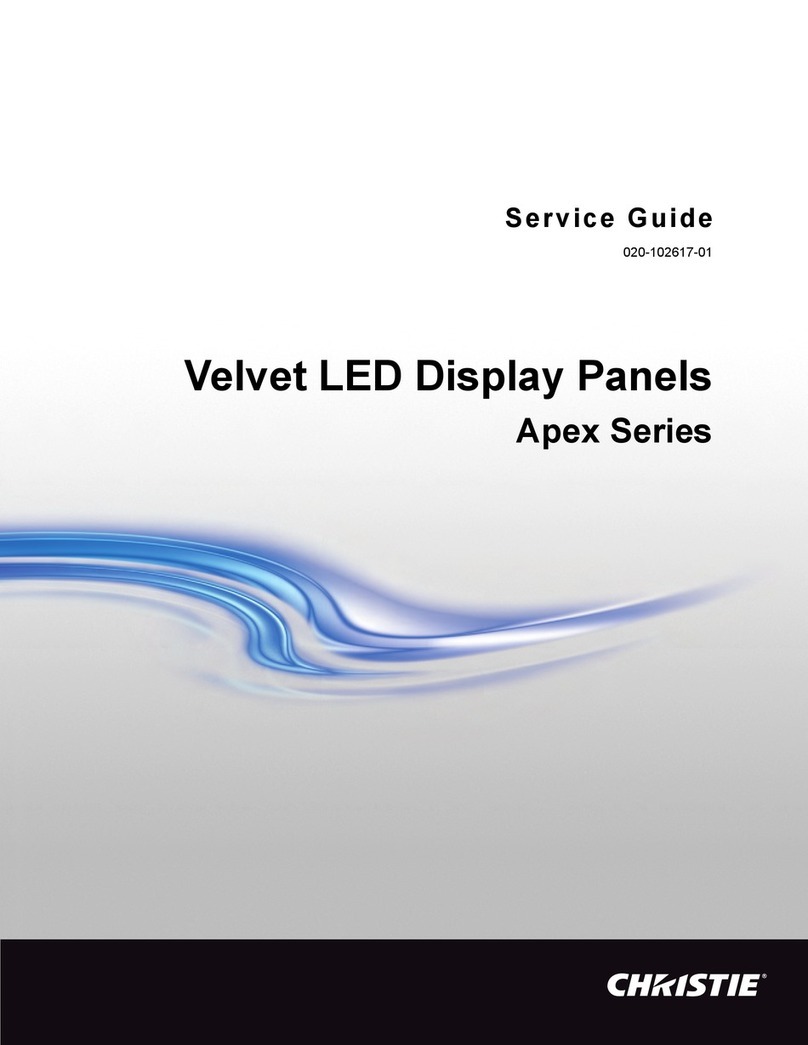
Christie
Christie Apex Series Service guide
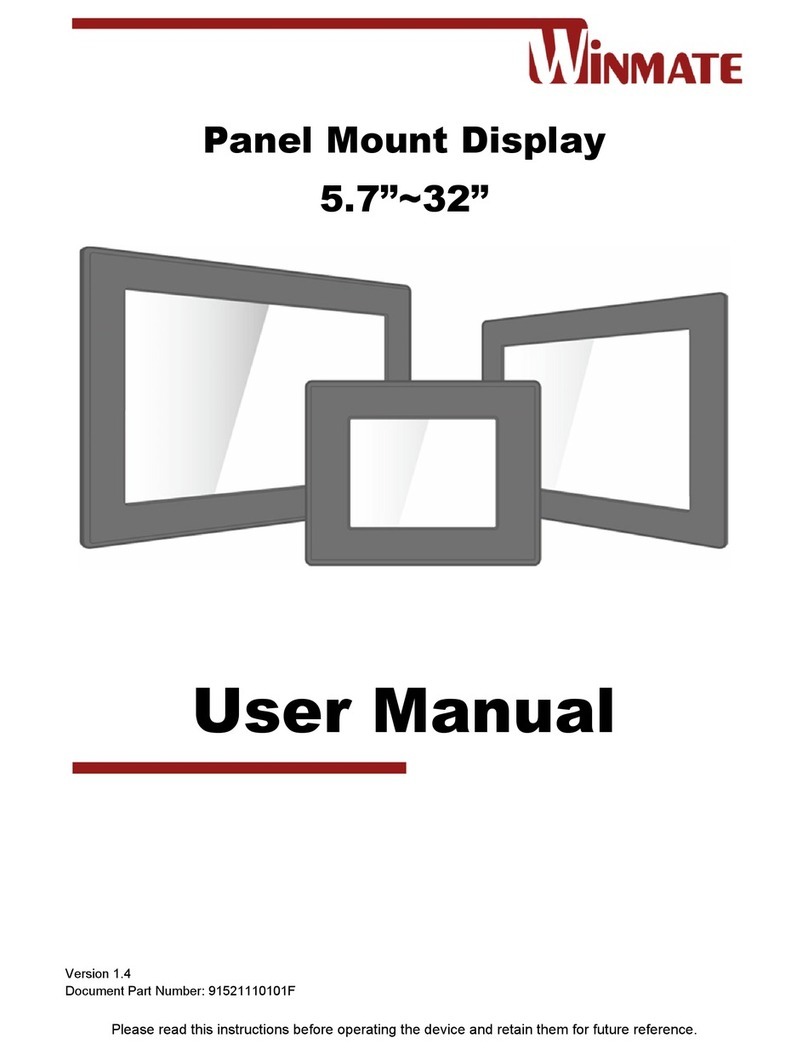
Winmate
Winmate R19L-PM Series user manual
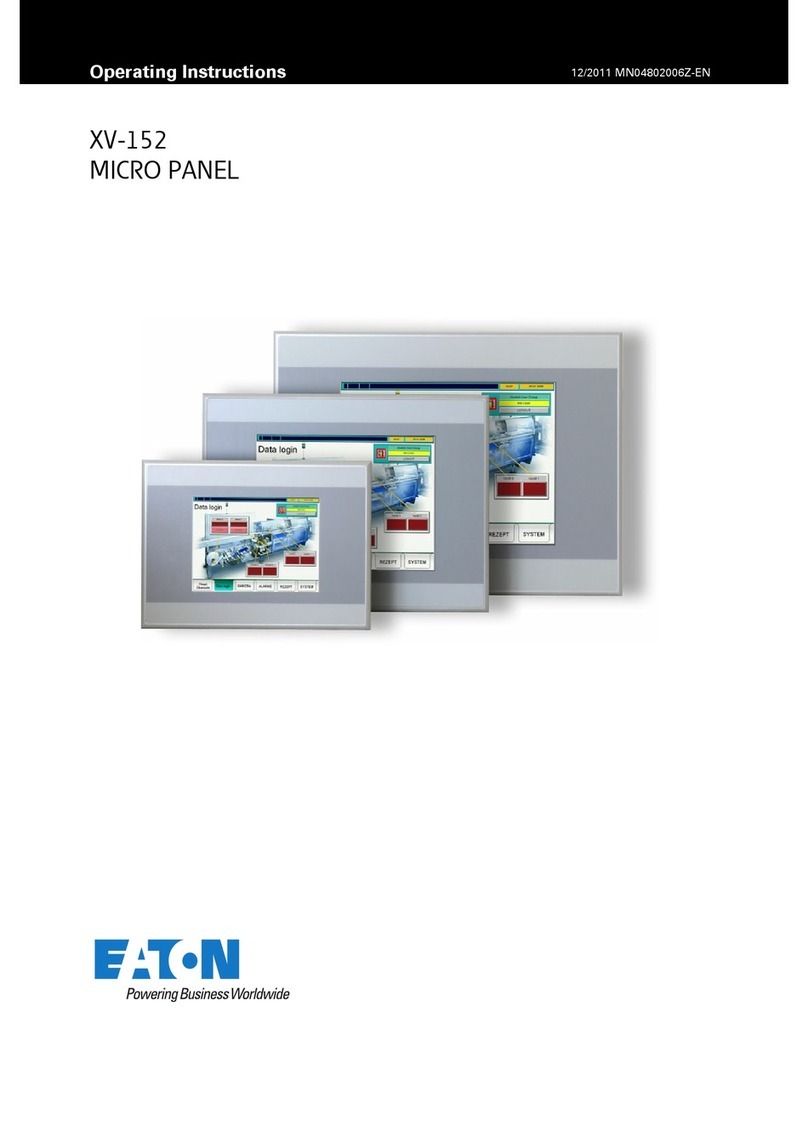
Eaton
Eaton XV-152 Series operating instructions
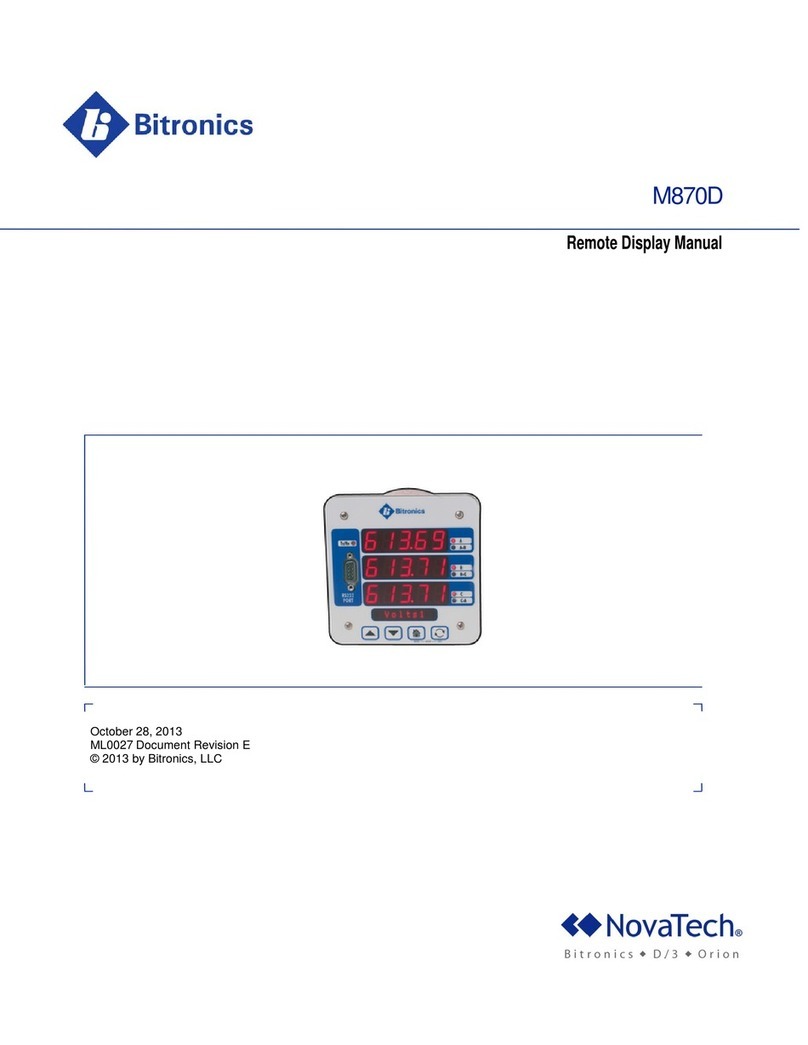
Bitronics
Bitronics M870D manual
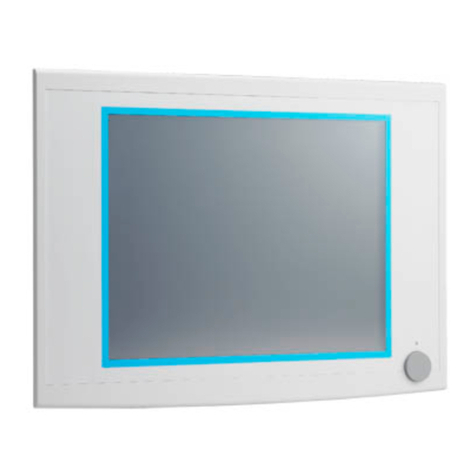
Advantech
Advantech FPM-5171G Series user manual
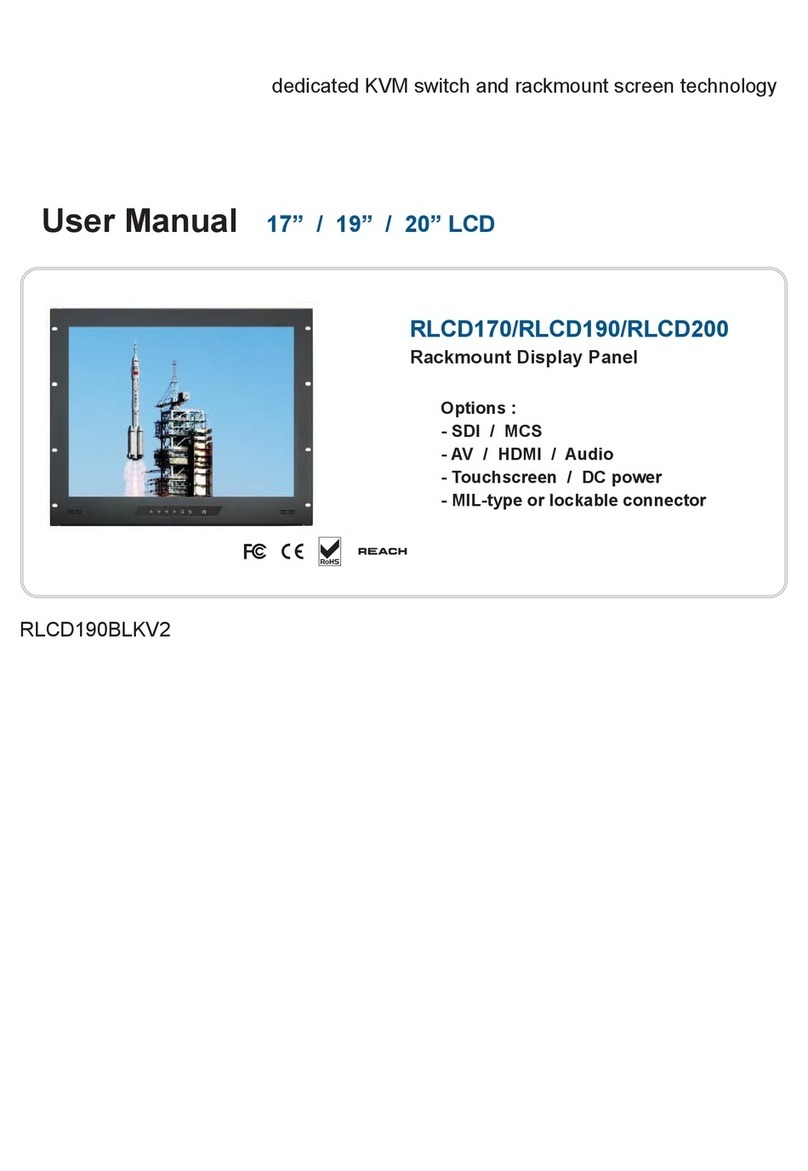
Industrial Automation and Enclosures Inc.
Industrial Automation and Enclosures Inc. RLCD170 user manual