Basler BE1-40Q User manual

INSTRUCTION MANUAL
FOR
LOSS OF EXCITATION RELAY
BE1-40Q
Publication Number: 9 1715 00 990
Revision: K 02/01

BE1-40Q Introduction i
WARNING
To avoid personal injury or equipment damage, only qualified personnel
should perform the procedures presented in this manual.
INTRODUCTION
This Instruction Manual provides information concerning the operation and installation of BE1-40Q Loss of
Excitation Relays. To accomplish this, the following is provided.
!Specifications
!Functional characteristics
!Installation
!Operational Tests
!Mounting Information

ii BE1-40Q Introduction
CONFIDENTIAL INFORMATION
OF BASLER ELECTRIC COMPANY, HIGHLAND, IL. IT IS LOANED FOR CONFIDENTIAL USE, SUBJECT
TO RETURN ON REQUEST, AND WITH THE MUTUAL UNDERSTANDING THAT IT WILL NOT BE USED IN
ANY MANNER DETRIMENTAL TO THE INTEREST OF BASLER ELECTRIC COMPANY.
It is not the intention of this manual to cover all details and variations in
equipment, nor does this manual provide data for every possible contingency
regarding installation or operation. The availability and design of all features and
options are subject to modification without notice. Should further information be
required, contact Basler Electric Company, Highland, Illinois.
First Printing: January 1986
Printed in USA
© 1998, 2001 Basler Electric Co., Highland, IL 62249
February 2001
BASLER ELECTRIC
ROUTE 143, BOX 269
HIGHLAND, IL 62249 USA
http://www.basler.com, [email protected]
PHONE 618-654-2341 FAX 618-654-2351

BE1-40Q Introduction iii
CONTENTS
Section 1 GENERAL INFORMATION .......................................1-1
Application ....................................................1-1
General ...................................................1-1
Capability Curves ............................................1-1
Relay Operating Characteristics ................................1-1
Time Delay .................................................1-2
Model and Style Number Description ................................1-2
Style Number Identification Chart ...................................1-3
Specifications ..................................................1-4
Section 2 HUMAN-MACHINE INTERFACE ...................................2-1
Controls and Indicators ...........................................2-1
Section 3 FUNCTIONAL DESCRIPTION .....................................3-1
General .......................................................3-1
Functional Description ...........................................3-1
Voltage Sensing .............................................3-1
Phase Shift .................................................3-1
Current Sensing .............................................3-2
HI/LOW RANGE Switch .......................................3-2
TAP Switch ................................................3-3
Transducer .................................................3-3
Comparator ................................................3-3
Timing ....................................................3-3
Outputs ...................................................3-3
Targets ....................................................3-3
PUSH-TO-ENERGIZE Output Pushbutton .........................3-3
Power Supply ...............................................3-4
Power Supply Status Output ...................................3-4
Section 4 INSTALLATION ................................................4-1
General .......................................................4-1
Relay Operating Precautions ......................................4-1
Dielectric Test ..................................................4-1
Mounting ......................................................4-1
Connections ...................................................4-7
Section 5 SETTING AND TESTING ........................................5-1
Settings ......................................................5-1
Per Unit Conversion Example ..................................5-1
Operational Test Procedure .......................................5-2
Pickup Verification ...........................................5-2
Timing Verification ...........................................5-4
Relay Characteristics Verification ...............................5-4

iv BE1-40Q Introduction
CONTENTS- Continued
Section 6 MAINTENANCE ............................................... 6-1
General ...................................................... 6-1
In-House Repair ............................................... 6-1
Storage ...................................................... 6-1
Test Plug ..................................................... 6-1
Section 7 MANUAL CHANGE INFORMATION ............................... 7-1
Changes ..................................................... 7-1

BE1-40Q General Information 1-1
SECTION 1 • GENERAL INFORMATION
APPLICATION
General
Loss of excitation protection is applied on nearly all synchronous generators. Reduced or complete loss of
excitation can cause loss of synchronism, instability and, possibly, damage to the generator from
overheating. Many modern excitation systems include minimum-excitation limiters to prevent
underexcitation; however, loss of excitation protective relays are still applied as backup to these automatic
controls. BE1-40Q Loss of Excitation Relays provide this protection by monitoring the field excitation
(measuring the magnitude and direction of var flow) and tripping the generator before serious damage to
the generator can occur.
Synchronous generators in parallel are normally operated in the overexcited (lagging) region which allows
generation of reactive power (vars). Although the field excitation may be safely adjusted to cause the
generator to absorb vars (leading), this is usually avoided because stability is unreliable under this condition.
When field excitation is not sufficient to maintain the terminal voltage of an interconnected generator, the
system will attempt to supply reactive power to excite the generator. If the system cannot supply the
required vars, the weakened field may allow the rotor to slip poles during disturbances such as load changes
or faults, causing loss of synchronism.
When the system can supply the necessary vars, the generator will act as an induction generator, drawing
excitation from the system. The machine voltage will remain above the setting of undervoltage relays, but
the current induced by the rotor slip will flow in the damper (amortisseur) windings. The excessive heating
caused by the current flow reduces machine life exponentially.
Under either condition, BE1-40Q Relays will detect the increased vars at the generator terminals as a loss
of excitation and trips the generator to prevent loss of synchronism or excessive heating within the
generator.
Ca
p
abilit
y
Curves
Generator manufacturers supply capability curves that specify the operating limits of a particular machine
(similar to those shown in Figure 1-1). The curves are derived from the heating characteristics that occur
on the stator end iron, the stator winding, and the rotor winding. Plotted on the complex power plane, real
power P (kW) is on the horizontal axis and reactive power Q (var) is on the vertical axis.
An additional limit is often included on these curves, as shown in Figure 1-2. Here, the steady state stability
limit further defines the safe operating limit of the generator. If the stability limit is exceeded, an out-of-step
condition can occur due to loss of synchronism.
BE1-40Q O
p
eratin
g
Characteristics
BE1-40Q relay characteristics closely follow the generator capability curves. The response characteristic
is represented by a line eight degrees from horizontal, placed above the most restrictive limit of normal
operation. As shown in Figure 1-3, the attendant intercept of the line on the Q axis (at -0.4 per unit vars in
this example) is used to establish the pickup of the relay. A front panel rotary switch is used to set the TAP
setting. Refer to
Section 5, Setting And Testing
for specific information on determining the pickup setting.

1-2 BE1-40Q General Information
Figure 1-1. Typical Generator Capability Curve Figure 1-2. Normal Operation with Steady
State Stability Limit
Figure 1-3. An Example of BE1-40Q Relay Operating Characteristics
Time Dela
y
A time delay is included in BE1-40Q Relays to prevent misoperation for transient conditions such as power
swings due to synchronizing or external fault clearing. A definite time delay of 0.1 to 9.9 seconds can be
set on the front panel thumbwheels in increments of 0.1 second. Setting both thumbwheels to 0 causes an
instantaneous trip signal to be sent when the TAP setting is exceeded. Refer to Section 5 for specific setting
information.
MODEL AND STYLE NUMBER DESCRIPTION
BE1-40Q Loss of Excitation Relays electrical characteristics and operational features are defined by a
combination of letters and numbers that make up the style number. The model number, together with the
style number, describe the options included in a specific device, and appear on the front panel, drawout

BE1-40Q General Information 1-3
cradle, and inside the case assembly. Upon receipt of a relay, be sure to check the style number against
the requisition and the packing list to ensure that they agree.
Style number identification chart (Figure 1-4) defines the electrical characteristics and operational features
included in BE1-40Q relays. For example, if the style number were F3E E10 B1S2F, the device would have
the following:
(F) -60Hzsingle-phasecurrentsensing.
(3) -120Vac,4to200W.
(E) -Oneoutputrelaywithnormallyopencontacts.
(E1) -Definitetiming.
(0) -Operatingpowerderivedfrom48Vdc.
(B) -Onecurrentoperatedtarget.
(1) -Push-to-energizeoutput(pushbutton).
(S) -Powersupplystatusoutput.
(2) -Oneauxiliaryoutputrelaywithnormallyclosedcontacts.
(F) -Semi-flushmounting.
Figure 1-4. Style Number Identification Chart

1-4 BE1-40Q General Information
SPECIFICATIONS
Current Sensing Unit is designed to operate from the secondary of a standard current
transformer rated at 5 A, 50 and 60 Hz (based on configuration). Internal
current sensing transformers are rated at 10 A continuous, 15 A for 1
minute, and 200 A for 1 second.
Current Sensing Burden Maximum sensing burden is less than 0.1 ohm at pickup over the
frequency range of 45 to 65 Hz.
Voltage Sensing Three line-to-line voltage sensing inputs are available: 120, 208, and 240
Vac (nominal). Each have a burden that is less than 1 VA over the
frequency range of 45 to 65 Hz.
Pickup Range Refer to Table 1-1.
Table 1-1. Pickup Setting
SENSING
INPUT
TYPE
NOMINAL
VOLTS
SENSING
INPUT
RANGE PICKUP SETTING (in secondary vars)
F & W 120 3
TAP A B C D E F G H J K
HI 100 200 300 400 500 600 700 800 900 1000
LOW 25 50 75 100 125 150 175 200 225 250
F & W 208 & 240 6 & 9
HI 200 400 600 800 1000 1200 1400 1600 1800 2000
LOW 50 100 150 200 250 300 350 400 450 500
Pickup Accuracy ±2% of the front panel setting or ±0.1 var, whichever is greater for a power
factor angle of -90!.
Dropout Not less than 95% of actual pickup.
Time Delay Range Definite time delay is adjustable by two front panel thumbwheels over a
range of 01 to 99 (0.1 to 9.9 seconds) in increments of 0.1 seconds. A
setting of 00 enables instantaneous operation.
Timing Accuracy Shown in Figure 1-5. Note that each curve is slightly offset by a factor that
represents integration time. Repeatability is within ±5% or 25 milliseconds,
whichever is greater.
Power Supply Power for the internal circuitry may be derived from a variety of ac or dc
power sources, as shown in Table 1-2.
Output Circuits Output contacts are rated as follows:
Resistive:
120/240 Vac Make 30 A for 0.2 seconds, carry 7 A continuously, and break 7 A.
250 Vdc Make 30 A for 0.2 seconds, carry 7 A continuously, and break 0.3 A.
Inductive:
120/240 Vac, Make 30 A for 0.2 seconds, carry 7 A continuously, and break 0.3 A.
125/250 Vdc (L/R = 0.04).

BE1-40Q General Information 1-5
Figure 1-5. Relay Response Time for Typical Time Dial Settings
Table 1-2. Power Supply Options and Burdens
Type
Nominal Input
Voltage
Input Voltage
Range
Burden at
Nominal
O (Mid Range) 48 Vdc 24 to 150 Vdc 5.0 W
P (Mid Range) 125 Vdc
120 Vac
24 to 150 Vdc
90 to 132 Vac
5.2 W
15.1 VA
R (Low Range) 24 Vdc 12† to 32 Vdc 5.1 W
S(Mid Range) 48 Vdc
125 Vdc
24 to 150 Vdc
24 to 150 Vdc
5.0 W
5.2 W
T (High Range) 250 Vdc
240 Vac
62 to 280 Vdc
90 to 270 Vac
5.2 W
14.0 VA
NOTE:
†TypeRpowersupplyinitiallyrequires14Vdctobeginoperating.Onceoperating,the
voltage may be reduced to 12 Vdc and operation will continue.

1-6 BE1-40Q General Information
Target Indicators Function targets may be specified as either internally operated, or cur-
rent operated by a minimum of 0.2 ampere through the output trip
circuit. When current operated, the output circuit must be limited to 30
amperes for 0.2 seconds, 7 amperes for 2 minutes, and 3 amperes
continuously.
Radio Frequency Maintains proper operation when tested for interference in accordance
Interference (RFI) with IEEE C37.90.2-1987,
Trial-Use Standard Withstand Capability of
Relay Systems to Radiated Electromagnetic Interference from
Transceivers
.
Isolation In accordance with IEC 255-5 and ANSI/IEEE C37.90-1989 one minute
dielectric (high potential) tests as follows:,
All circuits to ground: 2121 Vdc.
Input to output circuits: 1500 Vac or 2121 Vdc.
Shock In standard tests, the relay has withstood 15 g in each of three mutually
perpendicular planes without structural damage or degradation of perfor-
mance.
Vibration In standard tests, the relay has withstood 2 g in each of three mutually
perpendicular planes, swept over the range of 10 to 500 Hz for a total of six
sweeps, 15 minutes each sweep, without structural damage or degradation
of performance.
Surge Withstand Capability Qualified to ANSI/IEEE C37.90.1-1989,
Standard Surge Withstand
Capability (SWC) Tests for Protective Relays and Relay Systems
.
UL Recognition UL Recognized per Standard 508, UL File No. E97033. Note: Output
contacts are not UL Recognized for voltages greater than 250 volts.
Fast Transient Qualified to ANSI/IEEE C37.90.1-1989.
Standard Surge Withstand
Capability (SWC) Tests for Protective Relays and Relay Systems.
Operating Temperature -40°C (-40°F) to +70°C (+158°F).
Storage Temperature -65°C (-85°F) to +100°C (+212°F).
Weight 13.5 pounds (6.12 kg) maximum.
Case Size S1. (Dimensions are provided in
Section 4, Installation
.)

BE1-40Q Human-Machine Interface 2-1
SECTION 2 • HUMAN-MACHINE INTERFACE
CONTROLS AND INDICATORS
Table 2-1 lists and briefly describes the operator controls and indicators of the BE1-40Q Overexcitation
Relay. Reference the call-out letters to Figure 2-1.
Table 2-1. Controls and Indicators
Letter Control or Indicator Function or Indicator
ATAP Switch A ten-position rotary switch sets the pickup point
when used in conjunction with the RANGE Switch
(see I). Pickup levels (in vars) are labeled on the
Tap Range Chart (see G).
BPICKUP Indicator LED illuminates to indicate that the pickup level
has been exceeded.
CPOWER Indicator LED illuminates to indicate that the relay power
supply is functioning properly.
DTargetResetLever Linkageextendsthroughbottomoffrontcoverto
reset the target indicator.
ETargetIndicator(Optional)Magneticallylatchingindicatoristrippedtoredto
indicate that the output relay either has been
energized (internally operated) or that a minimum
of 0.2 amperes has flowed through the contacts
(current operated).
FPUSH-TO-ENERGIZE
(Optional)
Momentary pushbutton is accessible through the
front panel and used to test the output relay and
verify system wiring.
GTapRangeChart Providesanindexofreactivepowerlevels(in
vars) that correspond to the TAP Switch positions.
HTIME DELAY Selectors Two thumbwheel switches select the trip time
delay. The left thumbwheel represents seconds;
the right thumbwheel represents tenths of a
second. A TIME DELAY setting of 00 indicates
instantaneous trip time.
IRANGE Switch Two-position switch selects the reactive power
range (HI or LOW) desired.

2-2 BE1-40Q Human-Machine Interface
Figure 2-1. Location of Controls and Indicators

BE1-40Q Functional Description 3-1
SECTION 3 • FUNCTIONAL DESCRIPTION
GENERAL
BE1-40Q Loss of Excitation Relays are static devices that respond to the relation of voltage to current
magnitudes of the monitored circuit. As such they are sensitive to phase rotation. All connections shown
in this manual assume ABC rotation.
FUNCTIONAL DESCRIPTION
Refer to Figure 3-1 to follow the functional description of the BE1-40Q Loss of Excitation Relay.
Figure 3-1. Functional Block Diagram
Volta
g
e Sensin
g
The monitored voltage input is derived from a system voltage transformer connected phase-to-phase. An
internal voltage transformer (PT) provides isolation and reduces the nominal value of the voltage sensing
input (i.e., 120, 208, or 240 Vac) to internal circuitry requirements.
Phase Shift
Since the voltage input, VAB, leads the sensed input current, IB, by an angle of 150!for a unity power factor
condition, the voltage phasor is internally shifted 68!in a lagging direction (delayed) to achieve the relay
response characteristics. The resultant ITRIP leads the polarizing voltage VPOL by 8!(when the system power
factor angle (!) is equal to —90!), as shown in Figure 3-2.

3-2 BE1-40Q Functional Description
Front Panel Pickup Setting!
VAB(IB)
3
sin(8!
"!)
cos8!(3.1)
IB
!Front Panel Pickup Setting
VAB
3cos8!
sin(8!
"!)(3.2)
Figure 3-2. Phase Shift Example
The response of the relay is:
or
Where:
VAB =phaseAtophaseBvoltagemagnitude
IB=phaseBcurrentmagnitude
!=systempowerfactorangle=(voltageangle)-(currentangle)
Current Sensin
g
The monitored current is derived from the secondary of a system current transformer rated nominal five
amperes. An internal current transformer (CT) provides isolation and scaling for proper relay operation. The
front panel HI/LOW RANGE Switch uses the tapped secondary of the internal CT for range selection to
increase pickup stability.
Note that when the connection plugs (paddles) are removed, the CT inputs are shorted.
HI/LOW RANGE Switch
The front panel HI/LOW RANGE switch selects which secondary winding of the internal CT is connected to
the TAP Switch and thus the measurement circuitry. The position of this switch may be changed while
sensing current is present. The effect of this switch, in conjunction with the TAP switch, is shown in the

BE1-40Q Functional Description 3-3
Specifications,
Table 1-1, and on the front panel tap range chart.
TAP Switch
The front panel TAP switch selects the pickup setting (in single-phase vars), depending on the position of
the HI/LOW RANGE switch, as shown in Table 1-1. The TAP switch selects the resistive burden value that
is placed across the output of the internal sensing input CT. The resistive burden establishes the scaling
of the internal signal that represents the input current value.
Transducer
The transducer consists of a multiplier and integrator. The multiplier and associated control circuits produce
an output that is representative of the product of the scaled current input and the scaled, phase-shifted
voltage input signal. The output waveform of the multiplier is an instantaneous value; therefore, the output
is integrated to develop a signal that represents the average var value. The integrator response time is a
function of the pickup multiple, as shown in Section 1,
Specifications
.
Com
p
arator
The signal representing the single-phase var value is compared with the pickup reference. When the
reference value is exceeded, the PICKUP LED indicator is illuminated and timing is initiated.
Timin
g
A definite time delay is initiated when the monitored var level exceeds the pickup reference. A calibrated
frequency generating circuit, in conjunction with counter circuits and the front panel TIME DELAY
thumbwheel switches, establishes the definite time delay interval.
Time delay is adjustable from 0.1 to 9.9 seconds in 0.1 second intervals. A setting of 00 enables
instantaneous (no intentional time delay) operation. Timing is instantaneously reset if the var level reduces
to less than the pickup setting.
For a complete description of timing accuracy, refer to
Specifications
in Section 1.
Out
p
uts
Defined by the style number, the output relay may have either a normally open (NO) or normally closed (NC)
configuration. The normally open output contact option is required when current operated targets are
desired.
In addition, an auxiliary output contact may be provided which is specified by style number as NO, NC, or
SPDT. If an auxiliary contact is provided, then the power supply status output is not available.
Tar
g
ets
A magnetically-latching target indicator may be provided for the output contact as an option. This target is
actuated upon relay trip and may be either internally operated or current operated. An internally operated
target may be specified with either a normally open or normally closed output contact. When a current
operated target is desired, the output contact must be specified with a normally open configuration. The
current operated target requires a minimum of 0.2 amps flowing through the output relay contacts. The
target indicator must be reset with the manual target reset lever.
PUSH-TO-ENERGIZE OUTPUT Pushbutton
A small pushbutton switch may be provided as an option to allow testing the primary output contact and (if
present) the auxiliary output contact. To prevent accidental operation, the pushbutton is recessed behind
the front panel and is depressed by inserting a thin, non-conducting rod through an access hole in the front
panel.

3-4 BE1-40Q Functional Description
Power Su
pp
l
y
Basler Electric enhanced the power supply design for unit case relays. This new design created three, wide
range power supplies that replace the five previous power supplies. Style number identifiers for these power
supplies have not been changed so that customers may order the same style numbers that they ordered
previously. The first newly designed power supplies were installed in unit case relays with EIA date codes
9638 (third week of September 1996). Relays with a serial number that consists of one alpha character
followed by eight numerical characters also have the new wide range power supplies. A benefit of this new
design increases the power supply operating ranges such that the 48/125 volt selector is no longer
necessary. Specific voltage ranges for the three new power supplies and a cross reference to the style
number identifiers are shown in the following table.
Table 3-1. Wide Range Power Supply Voltage Ranges
Power Supply Style Chart Identifiers Nominal Voltage Voltage Range
Low Range R 24 Vdc 12†to 32 Vdc
Mid Range O, P, S 48, 125 Vdc,
120 Vac
24 to 150 Vdc,
90 to 132 Vac
High Range T 125, 250 Vdc,
120, 240 Vac
62 to 280 Vdc,
90 to 270 Vac
†14 Vdc is required to start the power supply.
Relay operating power is developed by the wide range, isolated, low burden, flyback switching, solid state
power supply. Nominal ±12 Vdc is delivered to the relay internal circuitry. Input (source voltage) for the
power supply is not polarity sensitive. A red LED turns ON to indicate that the power supply is functioning
properly.
Power Su
pp
l
y
Status Out
p
ut
A normally closed output relay may be provided, whose contact remains open when energized by the
presence of nominal voltage at the output of the power supply. If the power supply voltage fails or falls
below requirements, the power supply status output relay will deenergize, closing its contact.
A shorting bar is included in the relay case so that the status output terminals can provide a remote
indication that the BE1-40Q Relay has been withdrawn from its case or taken out of service by removing the
connection plug.
If the power supply status output is provided, then auxiliary output contacts are not available.

BE1-40Q Installation 4-1
SECTION 4 • INSTALLATION
GENERAL
When not shipped as part of a control or switchgear panel, relays are shipped in sturdy cartons to prevent
damage during transit. Immediately upon receipt of a relay, check the model and style number against the
requisition and packing list to see that they agree. Visually inspect the relay for damage that may have
occurred during shipment. If there is evidence of damage, immediately file a claim with the carrier and notify
the Regional Sales Office, or contact the Sales Representative at Basler Electric, Highland, Illinois.
In the event the BE1-40Q Relay is not to be installed immediately, store it in the original shipping carton in
a moisture and dust free environment. See Section 5 for further information. When the relay is to be placed
in service, it is recommended that the Operational Test Procedure (Section 5) be performed prior to
installation.
RELAY OPERATING PRECAUTIONS
Before installation or operation of the relay, note the following precautions:
1. A minimum of 0.2 A in the output circuit is required to ensure operation of current operated
targets.
2. The relay is a solid-state device. If a wiring insulation test is required, remove the connection
plugs and withdraw the cradle from its case.
3. When the connection plugs are removed, the relay is disconnected from the operating circuit and
will not provide system protection. Always be sure that external operating (monitored) conditions
are stable before removing a relay for inspection, test, or service.
4. Be sure the relay case is hard wired to earth ground using the ground terminal on the rear of the
unit. It is recommended to use a separate ground lead to the ground bus for each relay.
DIELECTRIC TEST
In accordance with IEC 255-5 and ANSI/IEEE C37.90-1989, one-minute dielectric tests (high potential) may
be performed as follows:
All circuits to ground: 2121 Vdc.
Input to output circuts: 1500 Vac or 2121 Vdc.
MOUNTING
Because the relay is of solid-state design, it does not have to be mounted vertically. Any convenient
mounting angle may be chosen. Relay outline dimensions and panel drilling diagrams are supplied in
Figures 4-1 through 4-9.

4-2 BE1-40Q Installation
2-02-01
D1427-01
Figure 4-1. S1 Case, Outline Dimensions, Front View

BE1-40Q Installation 4-3
D1427-29
02/2001
D1427-03
02/2001
DETAIL A-A
SHOWING THE ADDITION OF WASHERS
OVER THE BOSS TO TIGHTEN THE
RELAY AGAINST THE PANEL.
CASE
Figure 4-2. S1 Case, Single-Ended, Semi-Flush Mounting, Outline Dimensions, Side View
Figure 4-3. S1 Case, Single-Ended, Projection Mounting, Outline Dimensions, Side View
Other manuals for BE1-40Q
1
Table of contents
Other Basler Relay manuals
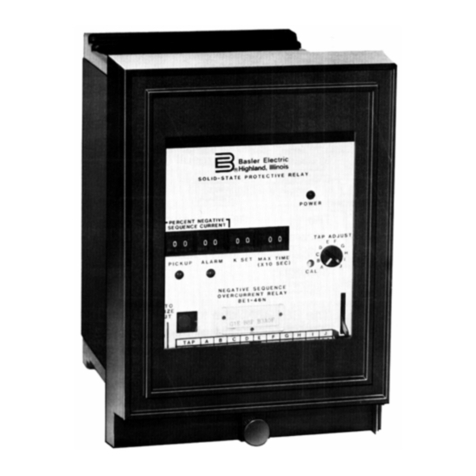
Basler
Basler BE1-46N User manual
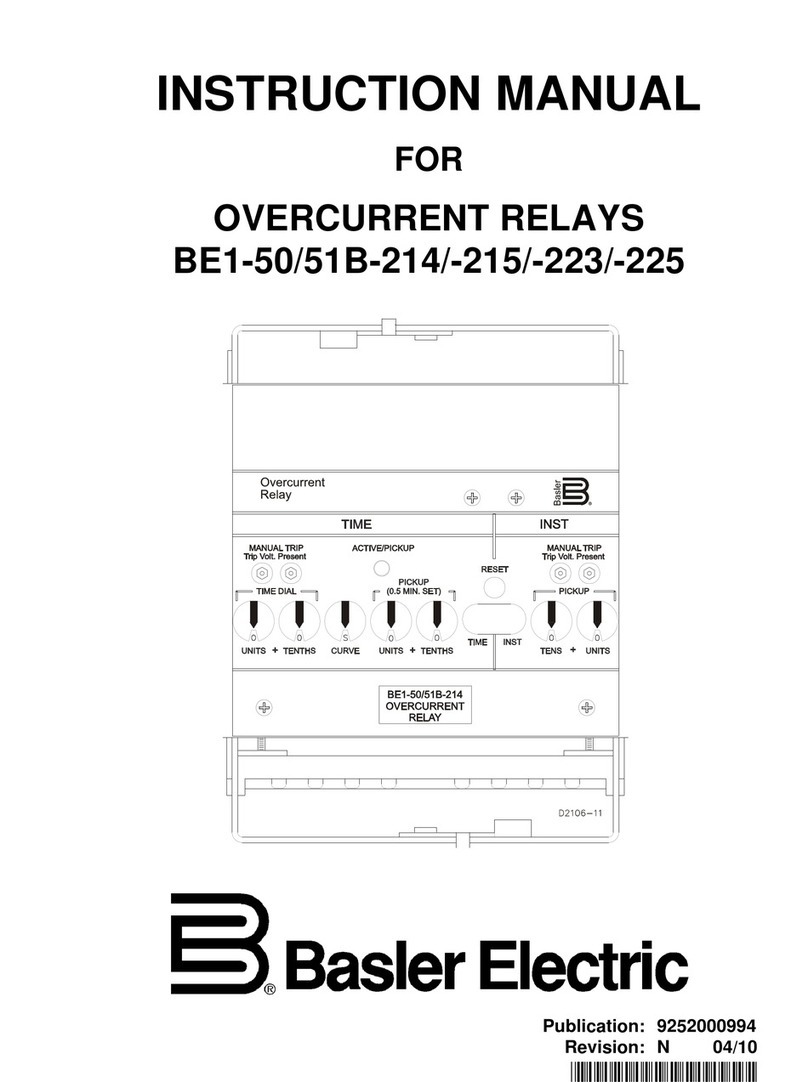
Basler
Basler BE1-50/51B-214 User manual
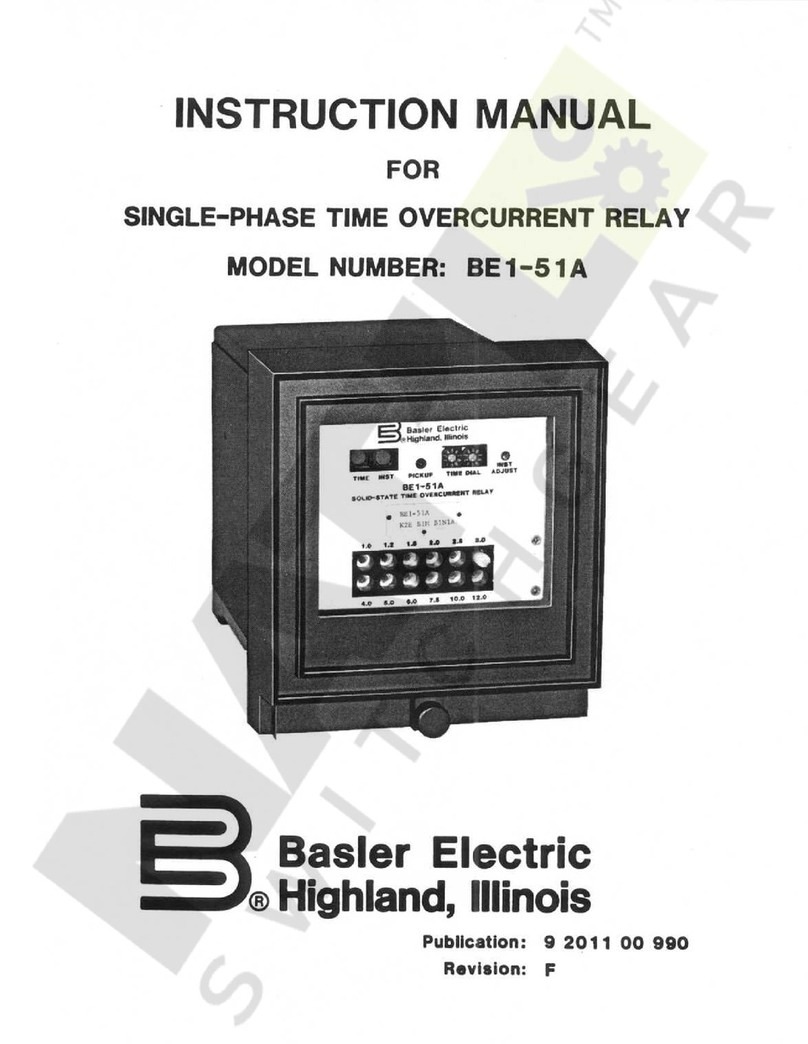
Basler
Basler BE1-51 User manual
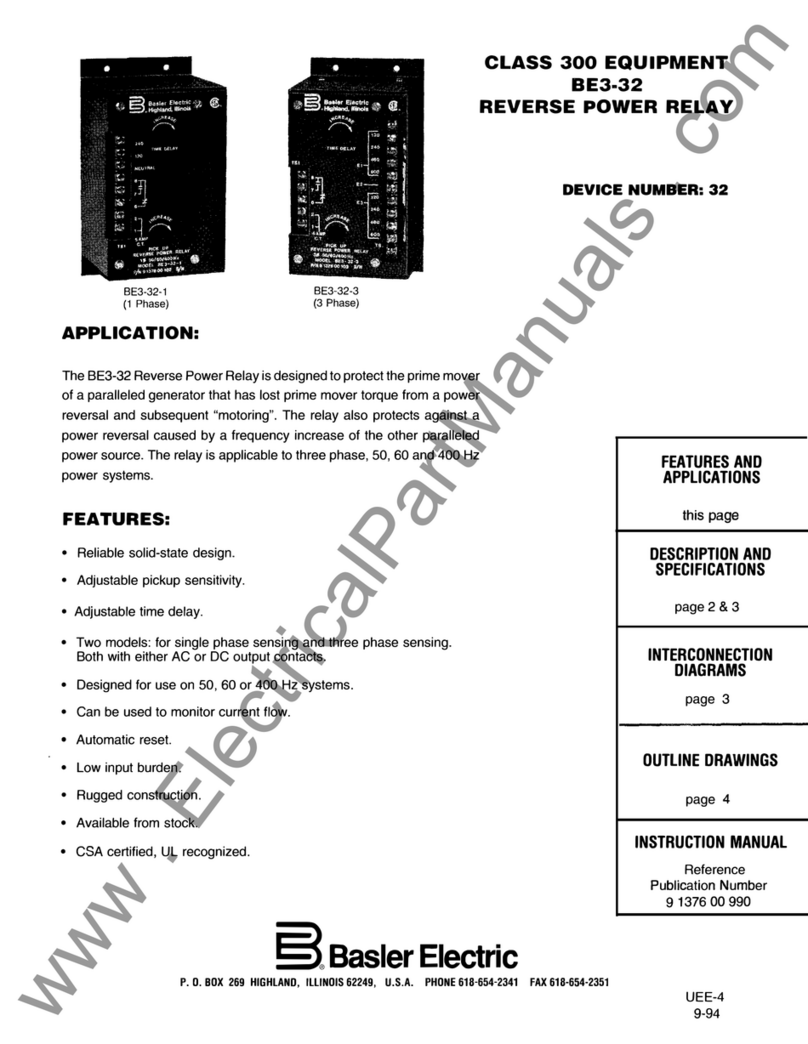
Basler
Basler Class 300 User manual

Basler
Basler BE1-87G User manual
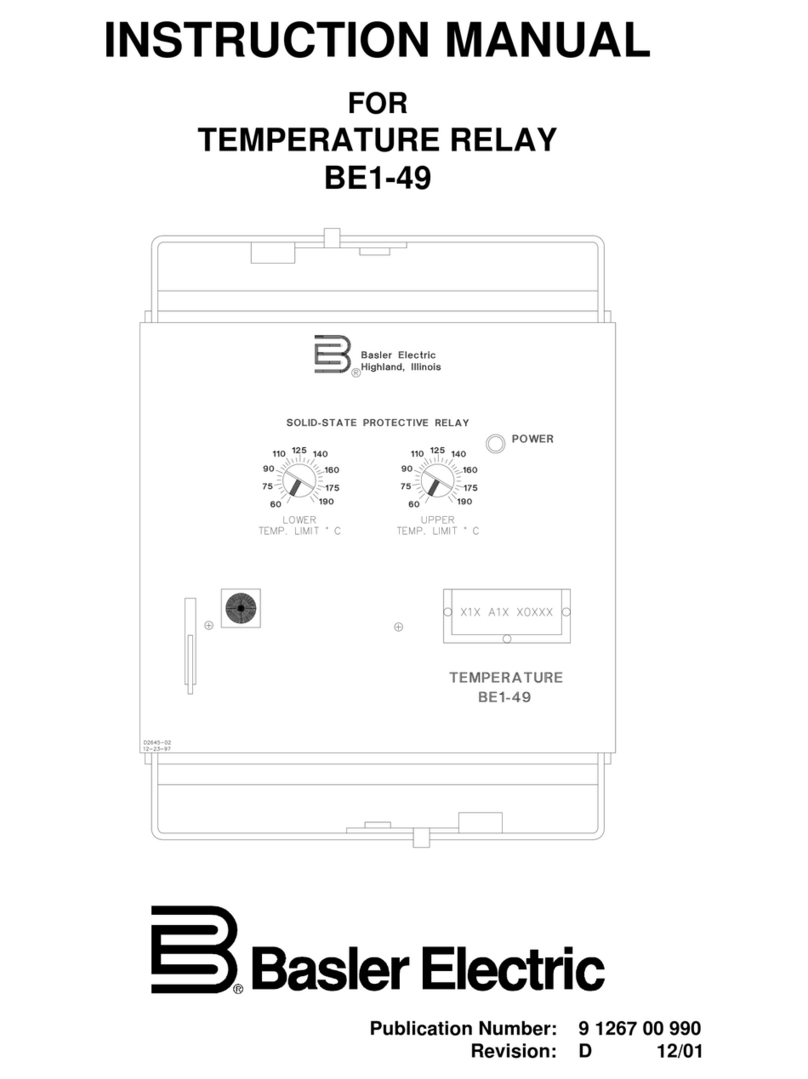
Basler
Basler BE1-49 User manual
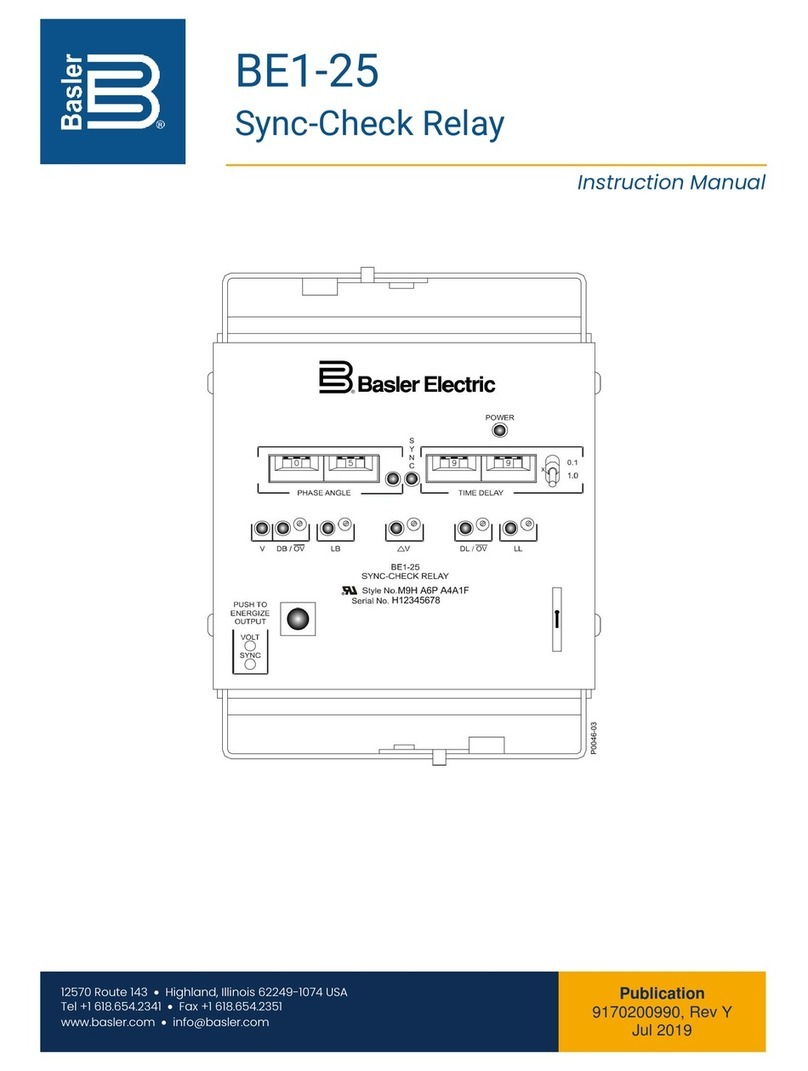
Basler
Basler BE1-25 User manual
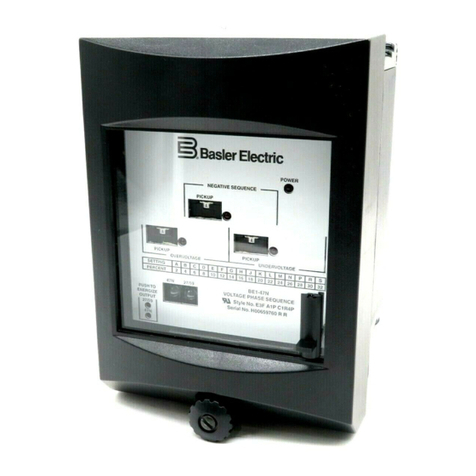
Basler
Basler BE1-47N User manual
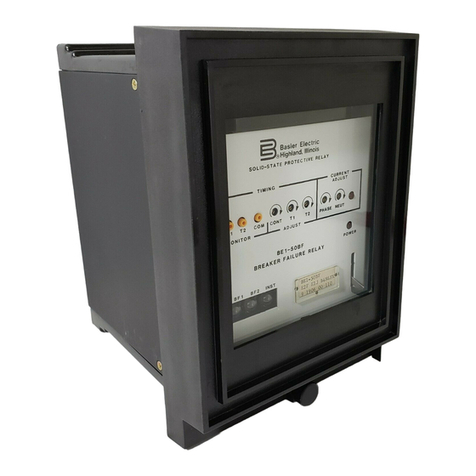
Basler
Basler BE1-50BF User manual
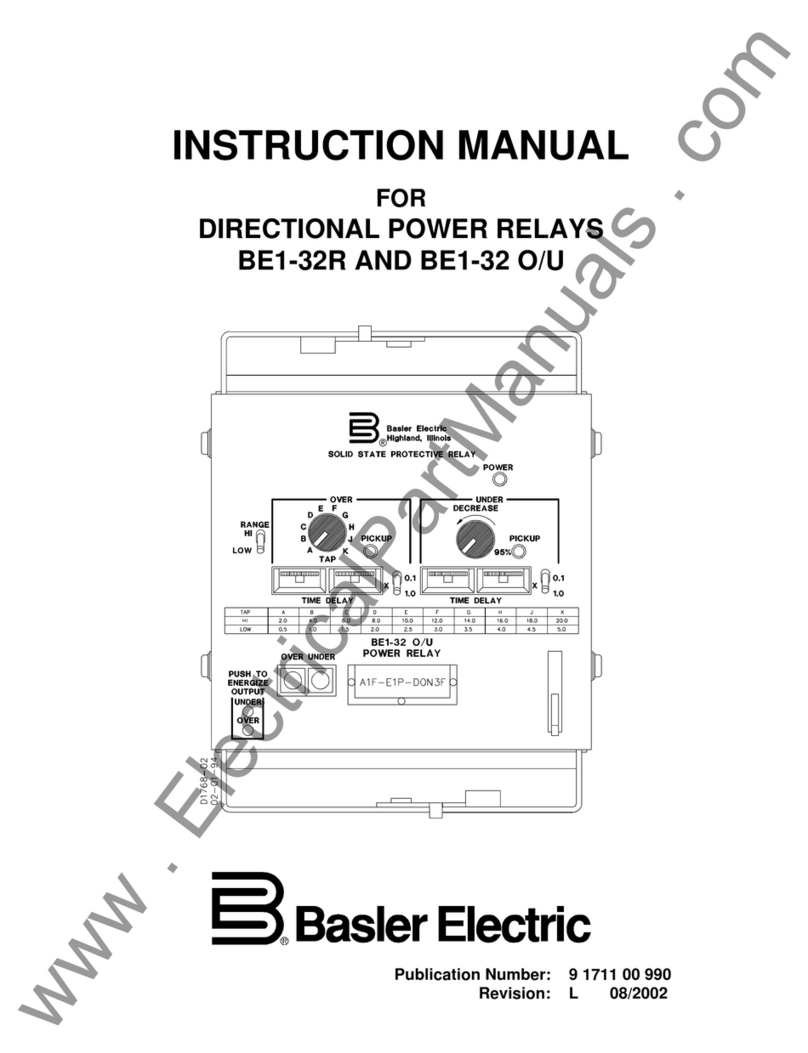
Basler
Basler BE1-32R User manual
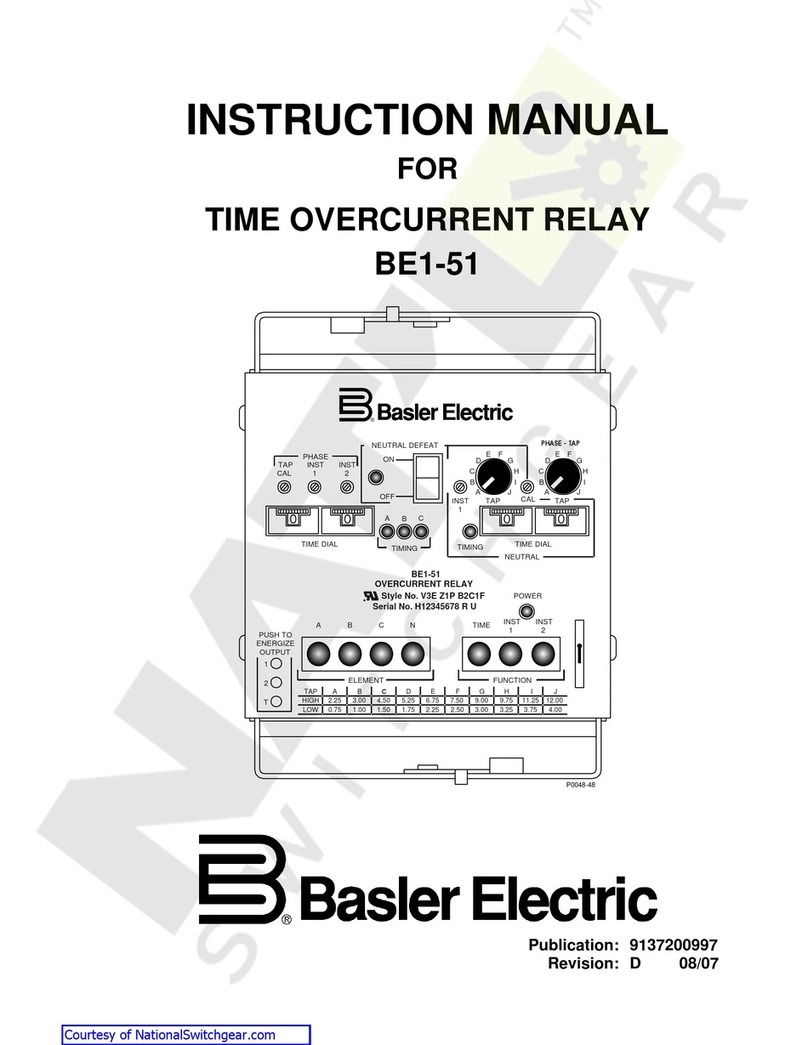
Basler
Basler V3E Z1P B2C1F User manual
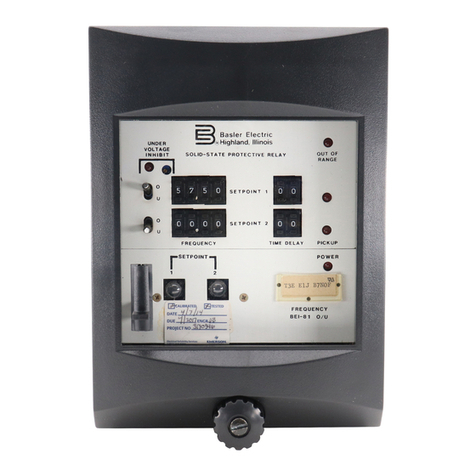
Basler
Basler BE1-81O/U User manual
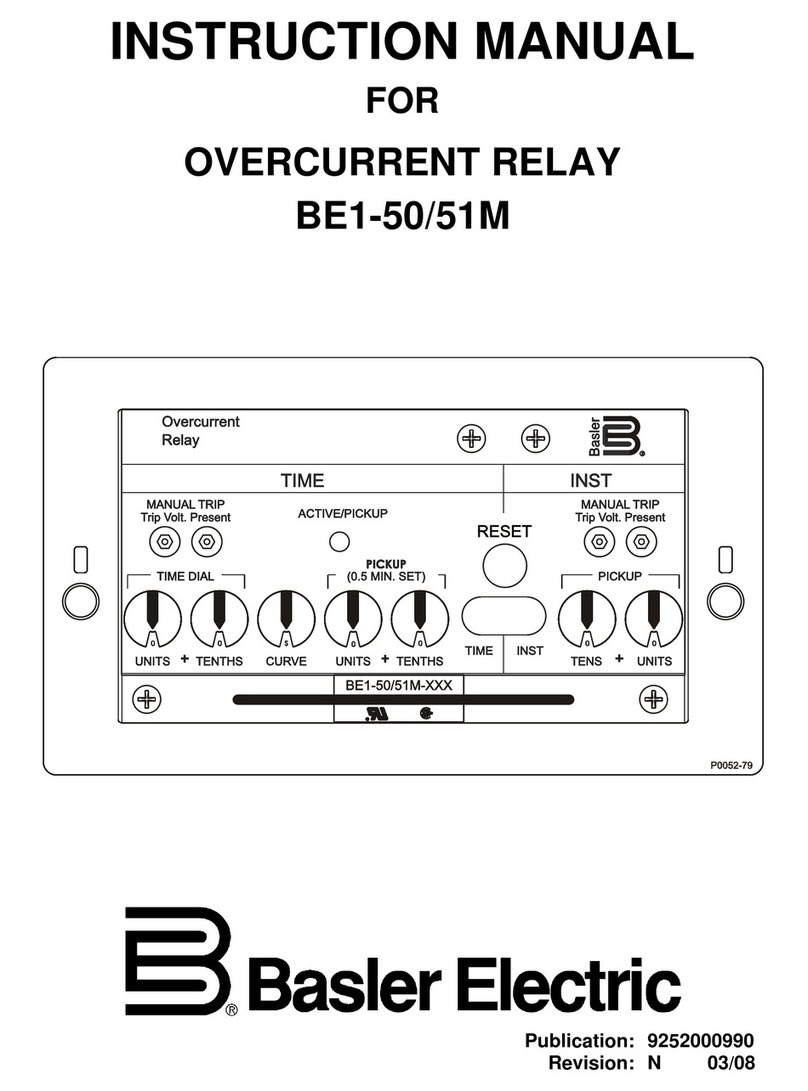
Basler
Basler BE1-51M User manual
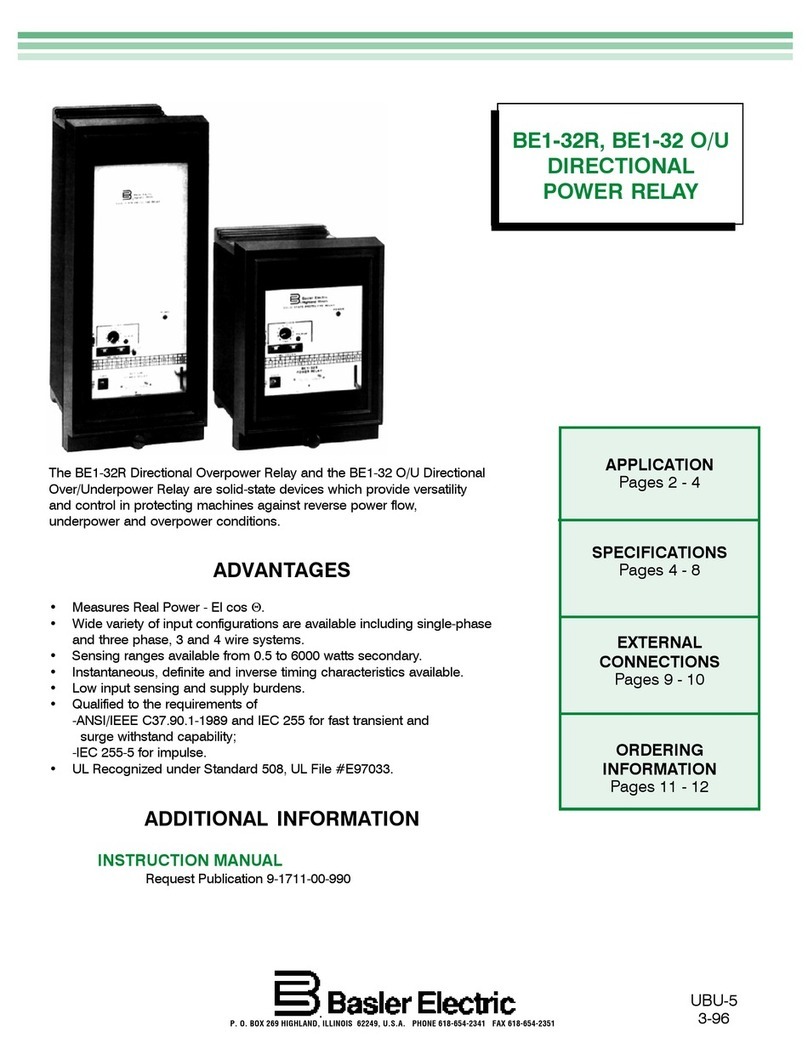
Basler
Basler BE1-32R User manual
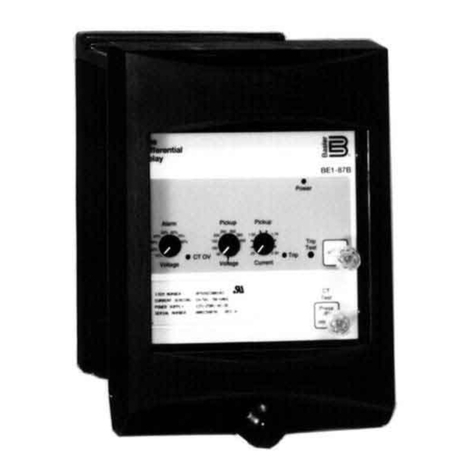
Basler
Basler BE1-87B User manual
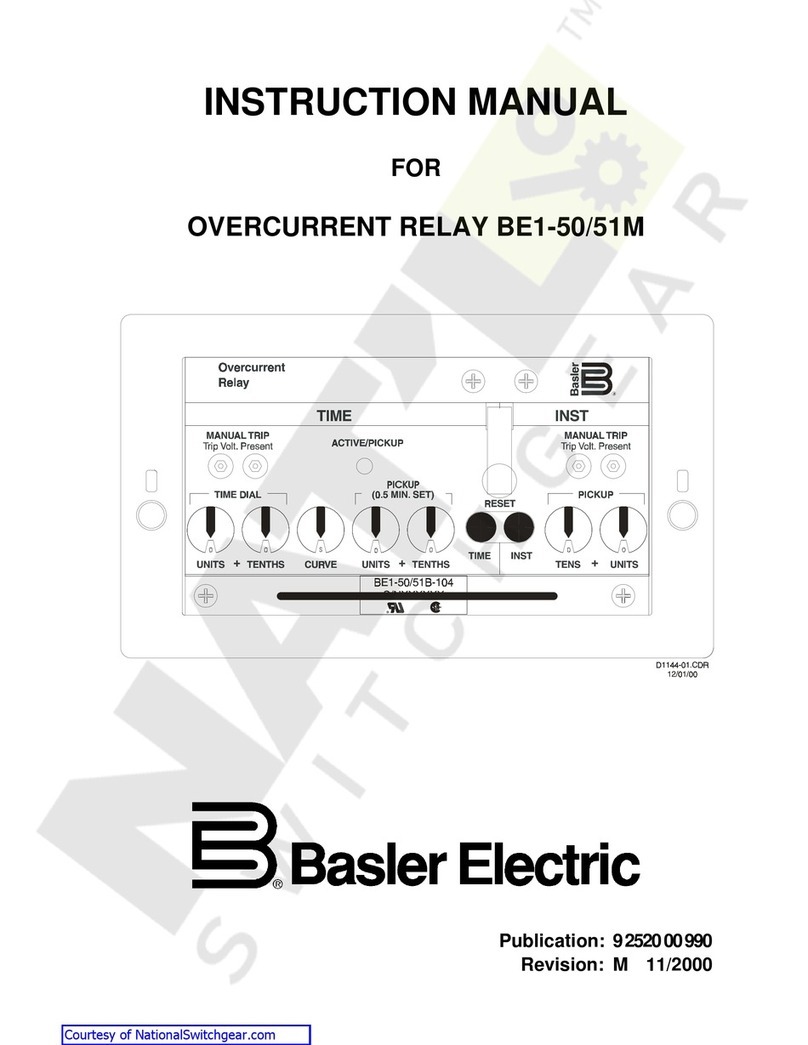
Basler
Basler BE1-50/51M-100 Series User manual
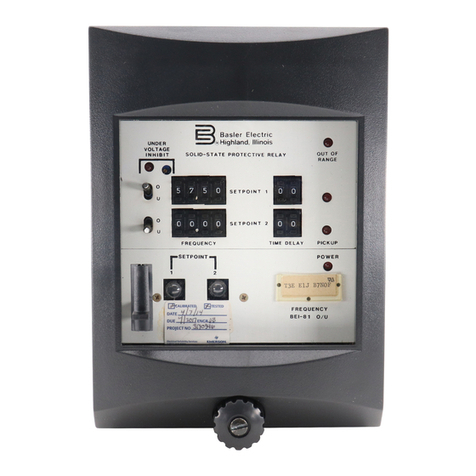
Basler
Basler BE1-81O/U User manual
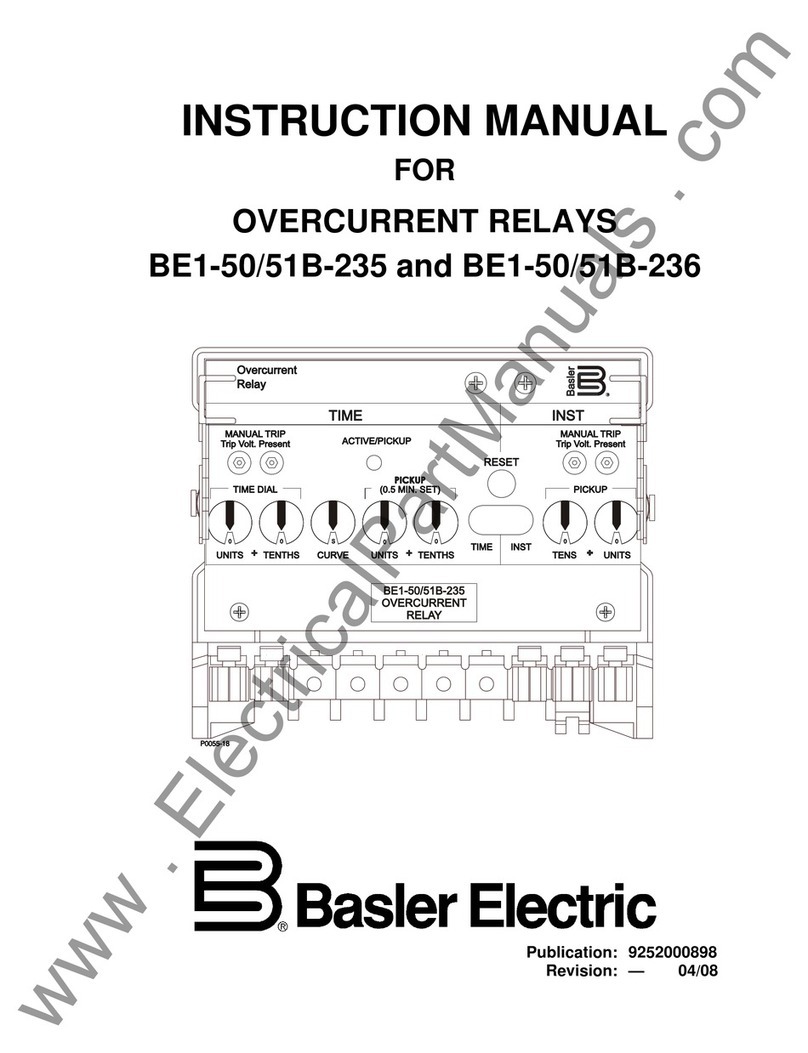
Basler
Basler BE1-50B-235 User manual
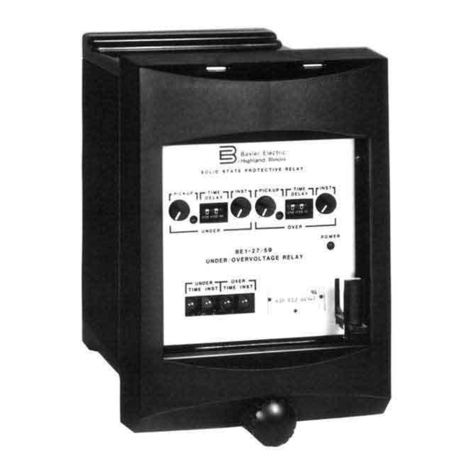
Basler
Basler BE1-27 User manual
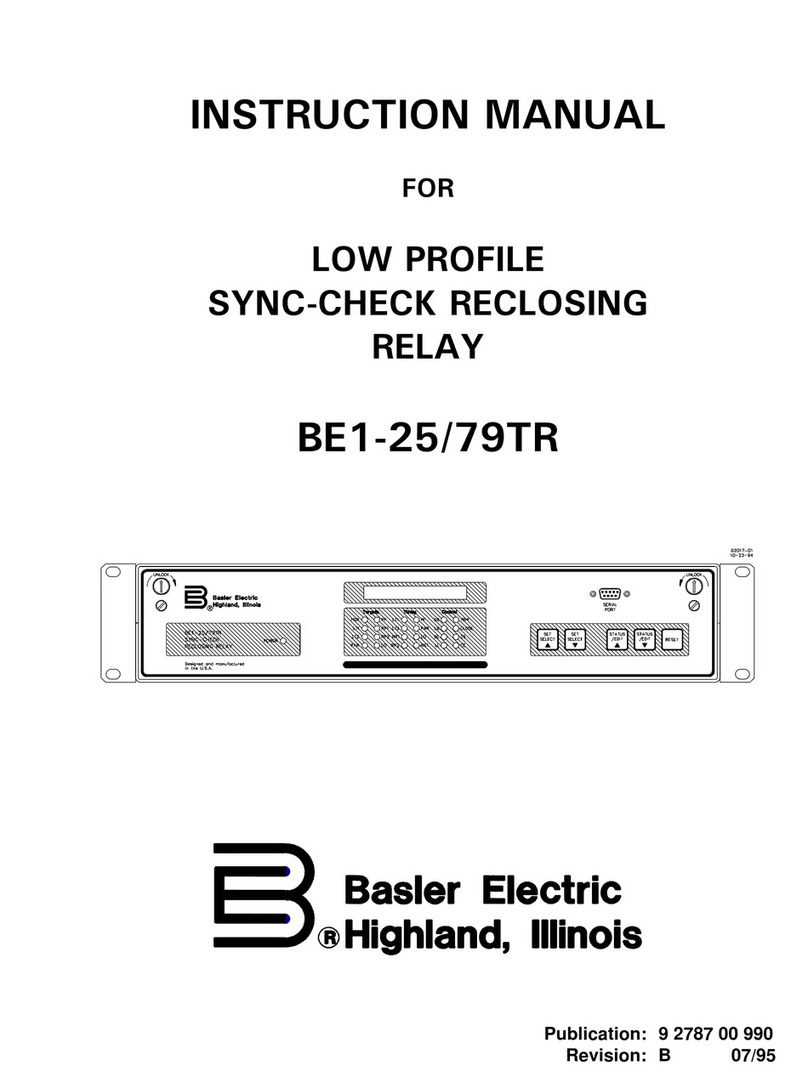
Basler
Basler BE1-25/79TR User manual