Baumuller DSD2 Series Guide

TAM 00699 1
DSD2 045 –132 04/2018
Three-phase synchronous motor English
TAM 00699
DSD2 045 - 132
Three-phase-synchronous motor
Version: 04/2018
English
Commissioning
and Maintenance Instructions

TAM 00699 2
DSD2 045 –132 04/2018
Three-phase synchronous motor English
LEGAL NOTES ON DOCUMENTATION
Copyright
This documentation may only be copied, as many times as required, by the owner for internal use.
For other purposes, this documentation may not be copied or duplicated either in whole or in part.
Utilization by and provision of the contents to third parties is not permitted. Names and company
logos used in this documentation may be trademarks, whose use by third parties for their own
purposes may infringe the rights of the owner.
Applicability
This documentation is part of the unit/the machine. These Commissioning and Maintenance
Instructions must be available to the operator at all times and be in a readable condition.
If the unit/machine is sold or put into storage, the owner must pass on this documentation together
with the unit/machine. Following the sale of the unit/machine, this original and all copies are to be
passed on to the purchaser. Following disposal or any other form of termination of utilization, this
original and all copies are to be destroyed.
With the introduction of this documentation, corresponding documentation with earlier issue dates
is superseded.
Please note that all data/figures/information represent current data at the time of going to press.
These details are not legally binding for the purposes of dimensioning, computation, or
calculation.
Baumüller Nürnberg GmbH reserves the right to change the technical data and the method of
operation of Baumüller products in the context of the further development of the products.
No liability can be accepted concerning the correctness of this documentation unless otherwise
specified in the General Conditions of Sale and Delivery.
BAUMÜLLER NÜRNBERG GmbH
Motors Division
90482 Nürnberg, Germany
www.baumueller.com

TAM 00699 3
DSD2 045 –132 04/2018
Three-phase synchronous motor English
Table of contents
1General safety instructions...........................................................................................4
1.1 Safety...........................................................................................................................................4
1.2 Designated purpose.....................................................................................................................5
1.3 Prohibition of unauthorized modifications and changes..............................................................6
2Operating conditions.....................................................................................................6
2.1 Product description......................................................................................................................6
2.2 Items supplied..............................................................................................................................6
2.3 Type plate....................................................................................................................................7
2.4 Technical Data.............................................................................................................................8
2.5 Transport, bearing lock, intermediate storage.............................................................................9
2.6 Installation conditions, cooling details .......................................................................................10
2.7 Balancing, output elements, vibrations......................................................................................11
3Mounting.......................................................................................................................13
3.1 Safety instructions .....................................................................................................................13
3.2 Installation, mounting.................................................................................................................13
4Electrical connections.................................................................................................14
5Commissioning, operation..........................................................................................15
5.1 Safety instructions .....................................................................................................................15
5.2 Checks prior to commissioning..................................................................................................16
5.3 Commissioning, operation.........................................................................................................16
5.4 Malfunctions in operation...........................................................................................................17
6Inspection and maintenance.......................................................................................18
6.1 Inspection ..................................................................................................................................19
6.2 Maintenance ..............................................................................................................................19
7Disposal........................................................................................................................19
8Appendix 1: pole assignment (main connection and Control terminal)...................20
8.1 Main connection via plug...........................................................................................................20
8.2 Main connection via the terminal box (Standard design acc. to catalogue)..............................20
8.3 Main connection via the terminal box (customer specific design acc. to EN 60034; non UL-approved).................22
8.4 Main and control connection via combination-mounting-box (customer specific design) .........23
8.5 Fan / cooling fan connections via connection socket or terminal box .......................................24
8.6 Control terminal: Resolver.........................................................................................................25
8.7 Control terminal: SRS / SRM 50................................................................................................25
8.8 Control terminal: SEK / SEL 52 .................................................................................................26
8.9 Control terminal: ECN 1313 / EQN 1325...................................................................................26
8.10Control terminal: ECN 1325 / EQN 1337 (encoder with EnDat 2.2-port of Heidenhain)...........27
8.11Brake connection at the size 132 ..............................................................................................27
9Appendix 2: water-cooled machines ..................................................................28
9.1 Definitions of power ratings for water-cooled machines............................................................28
9.2 Motor cooling .............................................................................................................................28
9.3 Instructions for installation.........................................................................................................29
9.4 Electrical connections................................................................................................................29
9.5 Specifications for required coolant volume flows ......................................................................30
9.6 Coolantconsistency....................................................................................................................31
9.7 Min. coolant temperature against ambient temperature and humidity ......................................31
9.8 Malfunctions in operation...........................................................................................................33
9.9 Inspection ..................................................................................................................................33

TAM 00699 4
DSD2 045 –132 04/2018
Three-phase synchronous motor English
1 General safety instructions
1.1 Safety
This electric motor has been constructed in accordance with the relevant safety standards and underwent
an operational safety check before leaving our factory.
To make sure that the machine is commissioned correctly and used safely, please read the following:
The Commissioning and Maintenance Instructions and their attached appendices
•The safety and commissioning notes
•The technical documentation that accompanies the product
•The commissioning and safety notes provided by the manufacturer of the converter
•The national, local, and system-specific regulations concerning your finished product
•The technical instruction of TAM 00697 for use in safety-oriented applications
We draw your attention to the following hazards when using the product:
Hazards resulting from • Lifting and transport
• Electrical power
• Moving parts
• Hot surfaces
• EMC interference
• Mechanical overload
• Thermal overload
Please, read all the safety instructions and in particular those which are marked with a symbol to avoid
injury to people and damage to property and to minimize residual risks,.
Risk of fatality due to electric shock
Failure to observe can lead to fatal or serious injuries.
General dangers warning
Failure to observe can lead to serious injury.
Dangerous situation warning
Failure to observe can lead to damage to the system or peripheral equipment.
Touching prohibited
Failure to observe can lead to serious injury.
Improper handling prohibited
Failure to observe can lead to serious injury
Hot surface warning.
Magetic field warning.
Failure to observe can lead to severe injuries or damage to property.
Electrostatically sensitive components
Failure to observe can lead to damage to the system or peripheral equipment.

TAM 00699 5
DSD2 045 –132 04/2018
Three-phase synchronous motor English
1.2 Designated purpose
The electric motor must only be used for its designated purpose. In this context, the electric motor must
only be used for the applications described in the technical documentation under strict observance of all
the notes in these Commissioning and Maintenance Instructions.
All assembly, commissioning, maintenance, and operating tasks must be carried out by qualified
personnel only.
Within the context of these safety instructions, qualified personnel refers to persons who are trained and
authorized in the specialized area, who are authorized to set up, assemble, commission, and operate
units, systems, and circuits under application of the applicable safety standards (EN 50110-1).
Inappropriate behavior can result in serious injury and damage to property.
The electric motor is designed to be used for industrial applications and is subject to a number of
standards and directives, including the following:
Standards
EN 60034-1, EN 60034-5, EN 60034-6, EN 60034-7, EN 60034-9, EN 60034-11,
EN 60034-14, EN 60204-1
EU Low Voltage Directive
The electric motors in this series fully comply with the requirements of the Low Voltage Directive EU
2014/35/EU (conformity).
EU Machinery Directive
Electric motors are components which are intended to be installed in machines as described in the
Machinery Directive. Commissioning is not permitted until such time as the conformity of the finished
product with this directive has been established (refer to EN 60204-1 "Electrical Equipment of
Machines").
EU EMC Directive
When the electric motor is used as intended, its operation must comply with the safety requirements
laid down in the EMC Directive 2014/30/EU. Proper installation (e. g. physical isolation of signal and
power cables, shielded wiring and cable etc.) is the responsibility of the system installer and system
vendor. With systems which have converters, the EMC notes from the manufacturers of the
converter-, encoder- and brake-manufacturer must be observed.
Furthermore, all the national, local, and system-specific regulations must be observed!
The electric motor is designed for the following ambient conditions:
• Ambient temperature: 0 °C to +40 °C
• Altitude: 1000 m above sea level
• Relative humidity: 5 % to 85 %
Please, take note of any deviating details specified on the type plate or in the technical
documentation. The conditions at the place of use must correspond to the details on the rating plate.
Use in areas with potentially explosive atmospheres is prohibited unless the unit is
expressly designed for this purpose (refer to additional notes).Furthermore, the area
surrounding the electric motor must be free of inflammable gas mixtures and
hazardous concentrations of dust.
Live and hot motor parts are inflammable and may cause serious injury and damage
to property.
If, in special cases (for utilization in non-industrial applications), more stringent
requirements are in place, such as protection against contact with a child's fingers,
these conditions must be met by the customer when installing the system.

TAM 00699 6
DSD2 045 –132 04/2018
Three-phase synchronous motor English
Motor design with rare earth magnets:
Please be aware of the following risks in the vicinity of a retracted or exposed rotor with
a strong magnetic field:
People with electronic or metallic implants (such as cardiac pacemakers, hearing
aids, plates or pins) are at risk, if the distance between the implant and the
magnetic pole is less than 0.5 m.
Due to the strong attraction forces exerted on ferromagnetic parts there is a risk of:
oBruises
oDamage to measuring and assembly tools, credit cards, watches etc.
oContamination of the rotor assembly due to attracting metal debris or powder.
Thermal hazard:
Beware of risk of burns!
The surface temperatures on the motors can exceed 70 °C. If necessary, provide
guards!
Temperature-sensitive parts, such as normal cables or electronic components, must
not be placed on or fixed to the hot surfaces.
Thermal overloading can destroy the winding and the bearing and can cause
demagnetization of the rare-earth magnets. A thermal sensor should be used to
monitor the temperature.
1.3 Prohibition of unauthorized modifications and changes
For safety reasons, unauthorized modifications and changes to the electric motor are
not permitted. If such modifications/changes are necessary, please contact the motor
manufacturer.
No safety devices may be dismantled or decommissioned when operating the electric
motor.
2 Operating conditions
2.1 Product description
The "DSD2" series electric motors are 8-pole three-phase synchronous motors with rare-earth magnets.
These motors are capable of excellent acceleration performance thanks to the low inertia of the rotor.
When operated in conjunction with a motor-controlled pulse converter, these motors respond extremely
well to speed and position control and are highly dynamic. Therefore, they are ideal for applications
associated with machine tools and production machines (e. g. printing, packaging, textile machinery), as
well as handling devices and robots.
2.2 Items supplied
The delivery is put together on an order-specific basis.
•The carrier must be immediately notified of any damage caused during transit.
•On receipt of delivery, please make sure that the ratings and motor type agree with the order data. In
the event of apparent defects or incomplete delivery, the appropriate Baumüller office or the
Baumüller head office in Nuremberg should be notified immediately.
In both of the above cases, commissioning may not be made until the error has been removed
professionally.

TAM 00699 7
DSD2 045 –132 04/2018
Three-phase synchronous motor English
2.3 Type plate
The type plate is used to identify each electric motor. The unique motor number is clearly shown on each
type plate and is essential for internal tracking procedures. It must be possible to read the type plate at all
times. Never remove the type plate from your motor.
Type plate data:
Figure 1: Type plate
1 →
Motor number
2 →
Standards and approbation
3 →
Motor type / designation
4 →
Motor protection class
5 →
Heat category (class of insulation VDE)
6 →
Motor is powered with converter
7 →
(optional) Supply voltage of the brakes DC
8 →
Motor type: 3-phase motor
9 →
Permitted ambient temperature
10 →
Rated frequency
11 →
Isolation system UL
12 →
Motor operating type
13 →
Rated voltage UN
14 →
Standstill torque Mo
15 →
Standstill current lo
16 →
Rated speed nN
17 →
Rated output PN
18 →
Article number
19 →
Kind of balancing

TAM 00699 8
DSD2 045 –132 04/2018
Three-phase synchronous motor English
2.4 Technical Data
Designs (EN 60034-7) IM B5 Horizontal installation position
IM V1 Vertical installation position, shaft end down
IM V3 Vertical installation position, shaft end up
Note: For installation according to IM V3 combined with IP 64 ensure protection against the
ingress of water and dirt.
IM B35 Horizontal mounting position of size 132
Note: The mounting positions IM V1 und IM V3 are not available for size 132.
Degree of protection (EN 60034-5) with consideration, of the shaft duct
IP 64 Standard: without shaft sealing ring
(size 45-100)
IP 65 Optional: with shaft sealing ring
(size 45-100)
IP 54 size 132
without consideration of the shaft duct
IP 67 for models with self-cooling (IC 410 and
IC 3W7); not for motors with terminal box
(size 45-100)
IP 65 for model with surface-cooling (IC 416)
(size 45-100)
IP 65 for model with terminal box
(size 45-100)
IP 54 size 132
Caution: All specified protection classes are only achieved in the event of completely
assembled plug connectors (mains and control connections) and fully closed terminal
box.
Cooling method (EN 60034-6) IC 410 Standard:
completely enclosed motor design,
surface-cooled, no fan, size 45-100
IC 416 Optional: from shaft height 56
completely enclosed motor design,
surface-cooled with fan,
IC 3W7 Optional available as of size 56
completely enclosed motor design,
water-cooled,
Electrical connections (see Appendix 1) via angled (3x90°) rotatable mounting boxes.
Caution: In the event of idling currents I0> 36 A the mains connection is via terminal boxes
Main connection 8-pin connector / Terminal box
Standard: U V W + thermal sensor
Optional: brake
Control connection 12-pin Standard: Resolver
12 / 17-pin Option: absolute encoder
Option: encoder + thermal sensor
12-pin Option: Hiperface-port
17-pin Option: Endat 2.1 port
9-pin Option: Endat 2.2 port
Fan (as an option) 6-pin plug or terminal box
Thermal motor protection (EN 60034-11) Temperature sensor PT1000, KTY84 in stator winding

TAM 00699 9
DSD2 045 –132 04/2018
Three-phase synchronous motor English
Winding insulation (EN 60034-1) Thermal class F(Δθ = 105 K)
Ambient temperature 0 °C to+40 °C (standard)
Altitude (EN 60034-1) ≤1.000 m above sea level (standard)
Rolling-contact bearings with long-term
grease lubrication: Standard: Ball bearing
Option (from shaft height 56): Roller bearing (DE-side)
Calculated bearing life LH10 20.000 h (approximate value)
Vibration severity (EN 60034-14) standard: level A
on request: level B (only for ball bearings)
True running (DIN 42955) standard: N
on request: R (reduced)
Vibration resistant (EN 60068-2-6) radial: 3 g (10 Hz to 100 Hz) size 45-100
axial: 0,5 g (10 Hz to 100 Hz) size 45-100
radial: 3 g (10 Hz to 55 Hz) size 132
axial: 1 g (10 Hz to 55 Hz) size 132
Holding brake Option
Actual speed value encoder Standard: 2-pole resolver (higher quality version on
request)
Option: absolute encoder with Hiperface-port
Option: absolute encoder with EnDat-port
For further technical data, refer to our technical product list online at: www.baumueller.com in the
download area under Technical documentation. If necessary, you can request the corresponding
documents.
Attention!
If the electric motor supplied is not a standard type as per the technical documentation or if special
contractual arrangements have been made, there may be technical differences to these Commissioning
and Maintenance Instructions. In this case request the related technical supplements.
2.5 Transport, bearing lock, intermediate storage
Water-cooled motors:
To avoid frost damages it must be ensured that there is no coolant in the motor during
the transport or intermediate storage at ambient temperatures < 3 °C. The blowing out
of the cooling water can be made by compressed air.
Transport:
The permitted environmental conditions which affect the motor during the transport
must be taken from DIN EN 60721-3-2 (class 2K2/2M1). Contrary to the DIN, a
reduced temperature range of –15 °C to + 60 °C is permitted.
Suitable lifting tackles must be used, e. g. belt webbing, loop belts etc. If provided, the
lifting lugs of the motor can be used for lifting.
The motor connectors are not supposed to be used to secure during transport or as
lifting lugs.
The regulations of the respective countries must be adhered to during transport. Lifting
devices and transport and load suspending devices must comply with the relevant
regulations.
For information on weight of the single motors, please refer to the technical documentation that
accompanies the product.

TAM 00699 10
DSD2 045 –132 04/2018
Three-phase synchronous motor English
The motor shaft and the connection surfaces must be protected against corrosion. The motor may only be
transported with a shaft protection cover; damage to the motor shaft must be avoided.
Bearing lock (for motors with cylinder roller bearings only):
On motors with cylinder roller bearings, the runner must be blocked at the end of the
shaft in order to prevent damage during transit.
The transport protector must be used every time the machine is moved.
If this lock no longer can be used due to mounting of a drive element, other suitable
means must be employed for axial fixing of the rotor for transport.
Intermediate storage:
If a motor is not to be commissioned immediately after delivery, it should be stored inside a building in a
dry, dust-free and low-vibration room (Veff ≤0.2mm/s).
The electric motors should not be stored longer than 2 years at a consistent temperature which is within
the temperature range of -15 to +60 °C. Elevated storage temperatures within the framework of the
working temperature accelerate the rate at which seals and bearing grease deteriorate and therefore
have a negative impact on the service life even before the unit has been commissioned. Direct exposure
to incident solar radiation, UV light and ozone also lead to an ageing of the gaskets and must be avoided!
Please note that the warranty periods commence from the date of delivery. For this reason, we
recommend that storage periods are kept to a minimum.
Should nevertheless a longer storage be necessary, the environmental conditions acc. to DIN EN 60721-
3-1 (class 1K2/1M1) have to be observed. Contrary to the DIN, an expanded temperature range of –
15 °C to + 60 °C is permitted.
2.6 Installation conditions, cooling details
For motors with water-cooling please take Section 9 into account in addition.
Surroundings:
The motor can be installed in roofed rooms complying with the degree of protection in dusty or damp
environment and under normal climatic conditions.
Unless alternative arrangements have been made, the motor is designed by default for the following
climatic conditions:
Ambient temperature 0 °C to 40 °C
Installation height ≤1000 m above sea level
The relative humidity reaches 5 % to 85 %
All other allowed application conditions have to correspond to DIN EN 60721-3-3 (class 3K3/3Z12).
It is absolutely imperative to comply with these climatic conditions when installing the unit.
Aggressive, corrosive, abrasive and plastic-dissolving solutions should be kept well away from the motor
and the air that is used to cool it.
Consultation with the motor manufacturer is essential in the case of installation outdoors.

TAM 00699 11
DSD2 045 –132 04/2018
Three-phase synchronous motor English
Air cooling:
For ambient conditions, see Section 2.4 and the technical documentation that accompanies the product.
Cooling method IC 410 –Self-cooling without a fan.
Cooling method IC 416 –Surface cooling with a fan.
The following must be observed:
The installation conditions must not impair thermal convection and radiation.
The cooling air used for forced ventilation must be able to flow in freely and the hot air must be able
to flow out freely. The hot exhaust air must not be sucked back in.
A clearance of at least 100 mm must be observed in relation to neighboring machine parts.
If installed in very dirty locations, the housing surface and airways must be cleaned regularly.
The motors with the size 132 require a minimum air volume during air cooling of ≥ 5,8 m³/min (
required minimum pressure height of ≥ 370 Pa)
flange connection:
By connecting the motor to the mounting surface, a part of the motor loss performance is lead away via
the flange. The dimensions of the mounting surface based on their axis height are listed in
table 1. This information provides minimum values for the safe heat dissipation via the motor flange
surfaces.
Axis height
Steel plate, width x height x thickness
in mm
Mounting surface
in m2
45
250 x 250 x 10
0.06
56 –100
450 x 400 x 30
0.18
Table 1: Mounting surfaces
The heat dissipation conditions approve on larger mounting surfaces. An insulated mounting of the
motors is not permitted.
2.7 Balancing, output elements, vibrations
Do not subject the shaft or bearings to impacts.
On mounting and dismounting output elements, it is not permitted for any axial forces
to be applied to the motor.
The generally applicable measures for the protection of output elements against
physical contact are to be followed.
If a motor is to be commissioned without output elements, measures must be taken to
ensure the key is not flung out.
Balancing
In the optional design, the rotors are dynamically balanced with a half key (in accordance with
DIN EN 60034-14 / DIN ISO 21940-32 / ISO 1940)).
NOTE: Observe the type of balancing as identified on the shaft end face and on the type plate:
H = Balancing with half key (standard design)
F = Balancing with full key (special design)
N = Balancing without key (special design)

TAM 00699 12
DSD2 045 –132 04/2018
Three-phase synchronous motor English
Output elements:
On mounting the output element, pay attention to the related type of balancing. The output elements must
themselves be balanced in accordance with ISO 1940.
Suitable jigs are always to be used for fitting or removing output elements (e.g. clutch disk, gear, pulley).
•Use the threaded hole in the end of the shaft.
•When pulling, use intermediate washers to provide the shaft with mechanical protection.
When hoisting heat up the drive elements if required (max. permissible temperature at shaft end
150°C).
Attention:
•On shaft versions without a key, the output elements are to be fastened to the output shaft by
means of suitable clamping sets.
•On shaft versions with a key, it must be ensured that the output elements rest on the shaft
shoulder. Note: The chamfer or radius on the output element and the shaft radius on the shoulder
must be matched.
•Is the tapped hole in the end of the shaft used for axial securing of output elements (e. g. belt pulley),
the maximum tightening torque acc. to following table 2 must not be exceeded.
Thread
Tightening torque
in Nm
M5
2,2
M8
10,0
M10
19,0
M12
33,0
M16
80,0
M20
160,0
Table 2: Tightening torque for safety screw S of a belt pulley
appropriate measures for securing screw must be applied
Vibration:
The site vibration response of the system, which is determined by the output elements, the
mounting conditions, the alignment, the installation, and the effects of external vibrations,
may cause the vibration values at the motor to increase.
In the interest of reliable motor operation and a long bearing service life, the permitted
vibration values in accordance with EN 60034-14 should not be exceeded. Under certain
circumstances, the rotor may need to be fully balanced with the output element (in
accordance with ISO 140).
The vibration value after mounting must not exceed the permitted rates of acceleration
(comp. Section 2.4 )
Where there are deviations from normal operation –e. g., rise in temperature, noises,
vibration –switch off the motor. Identify the cause and, if necessary, contact the
manufacturer.
S

TAM 00699 13
DSD2 045 –132 04/2018
Three-phase synchronous motor English
3 Mounting
3.1 Safety instructions
Before mounting:
Never mount or commission a damaged electric motor.
Never install the electric motor in a damaged machine.
Before mounting the electric motor, make sure it is suitable for your machine.
During mounting:
Only mount the motor using the fastening features provided.
The motor should not be exposed to knocks, e. g., with a hammer, or shocks when
mounting.
Make sure that all covers and safety devices are mounted. All safety devices must comply
with the latest regulations (e. g. EN 60204).
Air cooling:
Protective guards have to be fitted to the air inlets and outlets, if there is a risk of foreign
bodies falling into the fan during operation.
3.2 Installation, mounting
Prior to and during mounting, check that
the motor is not damaged (e. g. the shaft sealing ring must not have sustained any damage at all from
sharp or pointed objects).
the motor is not mounted in the danger zone of other equipment.
the motor is used for the designated purpose (comp. Section 1.2, Section 2.4).
Observe type plate details, warning labels, and signs.
anti-corrosion agents have been fully removed from the shaft ends.
If a common solvent such as acetone or a cleaning solvent is used, it must not be allowed to wet the
shaft sealing ring.
the motor is designed for the ambient conditions and environmental influences on site (comp.
Section 2.4).
the mounting space in the machine is suitable for the cooling method employed for the electric
motor. The motor has to mounted in such a way as to guarantee sufficient waste heat removal via
the housing and motor flange surfaces; during air cooling the incoming air and the outgoing air must
be able to flow freely so that the outgoing air is not drawn in again; at water cooling the connection of
cooling supplies is possible (compare chapter. 2.6 and 9).
That there is enough space in the machine to connect the motor and for inspection and maintenance
works. In order to obtain the installation dimensions of the motor including the tolerance
specifications refer to the technical documents or your dimension drawing
the motor can be mounted and operated with the connection data and fastening features provided.
The mounting dimensions of the motor and the tolerance details are provided in the technical
documentation.
When flanging to the motor, make sure that the flange surface is in good, even contact. The supports
and bearing surfaces must be clean and undamaged. They must be precisely aligned with the
connecting shafts to prevent exposure of the bearings, shafts and housing to damaging loads
through misalignment. When tightening the flange mounting screws (min. strength class 8.8), make
sure that the flange connection is not distorted.
no liquid can penetrate the upper bearing when installing vertically with the shaft end facing upwards.

TAM 00699 14
DSD2 045 –132 04/2018
Three-phase synchronous motor English
the permitted radial forces according to the operating characteristics in the technical documentation
that accompanies the product are not exceeded (if necessary, contact Baumüller for clarification).The
motor manufacturer must always be contacted if axial forces occur.
the brake (optional) can be released once the operating voltage has been applied (audible operating
noise).
the rotor rotates smoothly without a scraping sound.
On motors with a brake fitted, release the brake beforehand.
the design of the motor and encoder cables –and of the fan cable (if available), complies with the
details in the technical documentation that accompanies the product.
the output and input elements are secured.
the complete cooling circuit is leak proof and fully functional and protected against any foreign
objects falling into it.
4 Electrical connections
Important notes:
All work must be carried out by specially trained personnel.
Work must only be carried out when the system is electrically isolated and secured
against unintentional restarting (also auxiliary circuits).
Work must only be carried out once the motor has come to a standstill.
In the case of three-phase synchronous motors with permanent magnet excitation,
voltages of > 60 V can occur at the motor contacts with the rotor running.
Regulations for working in electrical plants must be observed!
Attention! The safety regulations for work on electrotechnical systems in accordance with
EN 50110-1 must be followed:
Isolate
Secure against unintentional restarting
Verify safe isolation from the supply
Earthing and short-circuiting
Safeguard or cover adjacent live parts
The electric motor must be operated by a correspondingly designed converter. A
direct connection to the three-phase mains can destroy the motor.
Ensure that the phase sequence and the pin assignment are correct!
Electrical connections, protective conductor connections, and screen connections
(when using screened cables) must be permanently secure!
Never touch the contacts of the encoder or thermal sensor with your hands or with
tools which are or may be electrostatically charged. The encoder and the thermal
sensors are electrostatically sensitive components.
Electrical installation:
•The person setting up the system is responsible for correct electrical installation.
•The motor data on the type plate must be observed.
•Connection cables and connectors must be correctly rated for the voltages and currents and must be
suitable for the method of installation employed.
•The motor and the modules (brake, encoder, fan etc.) must be connected in accordance with the
details on the wiring diagrams (see enclosed wiring diagrams and Section 8).
•Screened power and encoder cables must be used to protect against electromagnetic EMC
interference from motor cables and their effects on the encoder and control systems. Please refer to
the EMC notes provided by the supplier of the converter.

TAM 00699 15
DSD2 045 –132 04/2018
Three-phase synchronous motor English
•In the interest of ensuring operational safety, we recommend that you use connecting cables
assembled by Baumüller (see Technical Product List).
•Before connection, the plugs, sockets and the terminal boxes must be checked for damage,
corrosion, dirt and dampness.
•Ensure the connections are made correctly and are tight. Seals and sealing faces on the connectors
and the terminal boxes maintain the type of protection.
Note! Also in the interests of safeguarding the degree of protection, the rotatable junction boxes
should not be turned in their direction of connection more than 5 times altogether.
•Connectors and terminal box connections must not be exposed to mechanical stress. If necessary,
protect against strain, shearing, twisting and kinking.
In case of connection using a terminal box it is to be ensured
•the insulation is not over stripped, i. e. that the insulation extends right up to the cable lugs or
terminals. The ends of the cables must not protrude.
•the cable lugs that are used are suitable for the dimensions and cross-sections of the terminals and
cables.
•the screwed electrical connections are tightened in accordance with the specified tightening torque
(comp. Section 8.2 table 4 /8.3 table 5).
•the protection type is maintained.
Note: All lead-ins that are not used must be closed off with the sealing caps. The sealing elements
must be fully functional and undamaged when closing the terminal box.
5 Commissioning, operation
5.1 Safety instructions
Working on the electric motor:
Work must not be carried out on the electric motor until the motor has come to a
standstill and is electrically isolated. All connections, such as screw connections, that
were loosened when working on the motor must be tightened again prior to
commissioning.
When carrying out work on the motor, please observe the technical instructions and
notes in the respective sections in these Commissioning and Maintenance
Instructions.
Attention: If the optional holding brake is fitted, it must not be used to secure
anything while working on the motor (e. g. for retaining loads)!
Risk of fatality due to electric shock:
Make sure that the motor is disconnected and electrically isolated.
Never disconnect the motor connections during operation.
Only connect measuring instruments when the motor is disconnected from the power
supply and electrically isolated.
Only commence work on the motor connections when you are sure the motor is
electrically isolated and there is no potential.
When in operation, electric potential can be found at the motor terminals / contacts
and at the motor windings. Never touch these modules / elements while the motor is
in operation.

TAM 00699 16
DSD2 045 –132 04/2018
Three-phase synchronous motor English
Installing and uninstalling safety devices:
The electric motor may not be commissioned without first mounting the safety
devices.
The motor must be put out of operation when installing and dismantling components
and systems which are provided for monitoring the motor for safe operation.
Danger on physical contact:
Make sure that the electric motor has come to a standstill and is secured against
accidental restarting before you touch it.
Only touch the output shaft when it is electrically isolated and the motor has come to
a standstill. Otherwise there is a risk due to the rotating rotor.
Danger of burns! Never touch the motor housing when the motor is running at rated
load. The surface temperatures on the motors may exceed 70 °C.
5.2 Checks prior to commissioning
•The drive is undamaged and is not located within the danger zone of other equipment.
•The motor is correctly aligned and fastened. All screwed connections are correctly tightened.
•All the appropriate safety devices (mechanical, thermal, and electrical) are mounted.
•The motor connections have been made correctly.
•The protective conductor system is correct and its functionality has been checked.
•The cables are not in contact with the surface of the motor.
•The drive is not blocked (release brake, if present).
•Emergency stop functions have been checked
•Fan is connected properly and its function has been checked.
5.3 Commissioning, operation
Notes on the brake function (if present):
The brake is designed as a holding brake with an emergency stop function.
(power failure and emergency stop)
It must not be used as a working brake.
Commissioning must be carried out exclusively by qualified personnel.
Please refer to the commissioning instructions for the converter and the cooling system.
Checks during commissioning:
•Release the brake, if necessary.
•Have all the modules of the motor such as the brake, encoder, fan etc. been checked and are they in
compliance with the conditions of use?
•Were all electrical connections executed correctly and tightened properly? (observe wiring diagrams,
see Section 8 and respectively the enclosed wiring diagrams).
•Have all protection measures which eliminate the possibility of physical contact with live parts, hot
surfaces, rotating and moving parts been followed and are these measures fully functional?
•Have all output elements been mounted and adjusted in accordance with the manufacturer's
instructions?

TAM 00699 17
DSD2 045 –132 04/2018
Three-phase synchronous motor English
•Are measures in place to ensure that the maximum permitted speed nmax of the motor cannot be
exceeded? The maximum permitted speed nmax is the highest permitted operating speed for short-time
duty.
Checks during operation:
•Listen out for unusual noises.
•If scraping, scratching, grinding, or other similar noises occur, stop the drive immediately and locate
the cause.
•Check the motor surface and connection cables for dirt (such as layers of dust, oil deposits,
dampness and leakiness etc.
•Check the maintenance intervals.
Check air inlet and outlet ports for dirt.
5.4 Malfunctions in operation
Safety instructions:
Troubleshooting and rectification must only be performed by qualified personnel.
Do not disconnect any of the safety devices –even during test runs.
Only disconnect and connect electrical cables when electrically isolated and secured.
Observe the 5 safety rules for "Isolation" (see Section 4).
Beware of hot surfaces!
In case of malfunctions in operation always
Refer to the operating instructions for the machine/system.
Refer to the operating instructions for the converter.
If necessary, contact the manufacturer of the motor or converter.
Have the following information ready:
Type plate data
Type and scope of the malfunction situation on occurrence of the malfunction
Application data (torque cycle, speed and forces over time; ambient conditions)
The following selection of possible causes can be helpful in the troubleshooting process:
Malfunction
Cause
Remedy
Motor does not start
No controller enable
Controller fault, encoder fault
Brake does not release
Faulty brake
No power supply
Rotating field
Activate controller enable
Read out fault list on the
converter or controller; rectify
faults
Check control, connections, and
power supply
Repairs carried out by
manufacturer
Check connections and power
supply
Check phase sequence. If
necessary, switch over the
connecting cables

TAM 00699 18
DSD2 045 –132 04/2018
Three-phase synchronous motor English
Malfunction
Cause
Remedy
Uneven running
Insufficient screening on
connecting cables
Controller parameters too high
Check screening connection and
grounding
Optimise controller parameters
Vibrations
Coupling element or driven
machine poorly balanced
Inadequate alignment of the drive
train
Fixing screws loose
Rebalance
Realign machine set
Check and tighten screwed
connections
Running noises
Foreign bodies in the motor
Bearing damage
Repairs carried out by motor
manufacturer
Repairs carried out by motor
manufacturer
Temperature rise in the
motor
Motor temperature
monitoring unit trips
Drive overload
Motor surface/airways dirty
Filter is very dirty(at the motor
size 132)
Has been installed in an area that
does not allow enough space
Brake not releasing fully –brake
dragging
Check motor load and compare
with type plate
Clean motor surface/airways
Check and clean or replace if
required
Check motor has been installed
in acc. with Sections 2.6and 3
Have repaired by the motor
manufacturer
Current consumption too
high, motor torque too low
Indexing angle incorrect
Check indexing angle and adjust
if necessary
Table 3: Malfunctions
6 Inspection and maintenance
Working on the electric motor:
Work must not be carried out on the electric motor until the motor has come to a
standstill, is electrically isolated, de-pressurized and has cooled down. All
connections, such as screws on the motor that were loosened must be tightened
again after the inspection and maintenance work.
When carrying out work on the motor, please observe the technical instructions and
notes in the respective sections in these Commissioning and Maintenance
Instructions.
When carrying out maintenance work, observe all safety instructions which also apply
to the commissioning of the motor (see Section 5.1).
Attention!:
If the optional holding brake is fitted, this brake must not perform a safety function
during work on the motor (e. g., retaining loads)!

TAM 00699 19
DSD2 045 –132 04/2018
Three-phase synchronous motor English
6.1 Inspection
Depending on the severity of soiling on site, cleaning will have to be carried out regularly to guarantee
the continuous adequate dissipation of heat. The flow rate and the pressure ratio of the cooling system
must be checked.
If an optional brake is fitted, wear limits are specified (e. g., maximum permissible operating air gap,
maximum number of emergency braking operations). The actual degree of wear on the brake must be
checked at regular intervals. When the permissible wear limits have been reached, the brake must be
replaced (see Section 6.2).
If an optional shaft sealing ring is used, it must be checked at regular intervals to ensure it is functioning
correctly (leakage).
6.2 Maintenance
The service life of the bearings and sealing elements can differ greatly depending on the operating
conditions, (e. g. operating mode, temperature, speed and load).
In the case of trouble-free operation, we generally recommend the following maintenance procedures:
•Replacement of the bearings after 20.000 running hours (the bearings are designed for a calculated
service life of 20.000 running hours)
•Replacement of the shaft-sealing ring, if applicable, if a leakage occurs.
If an optional brake is fitted, it is essential that it is replaced when its wear limits are reached.
The maintenance work is to be undertaken by Baumüller or a specialist organization authorized by
Baumüller.
The independent maintenance works of an operator are the following:
The cleaning of the motor surfaces and of the air channels.
The replacement or cleaning of the filter mats when using dust filters (as at motor size 132):
Dust filters should generally be cleaned or replaced after 100 operating hours. If there is high
pollution the service intervals are to be reduced.
Filters polluted by dry dirt can be cleaned by vacuuming, blowing them out or beating them.
Filters polluted by wet dirt can be rinsed out in lukewarm water while adding a commercially
available washing agent and then drying them.
Note: If the filter mats must be replaced then use original replacement filters of the motor
manufacturer, only. These can be requested from Baumüller under specification of the motor
number as well as of the order number (see type plate).
Caution!
The specifications of the technical instructions TAM 00697 must be followed during maintenance
and servicing on motors which are used for safety-oriented applications.
7 Disposal
The motor must be disposed of in accordance with the relevant national and local regulations within the
framework of the normal recycling process.
Note: The motor rotors include rare earth magnets with a high magnetic energies. Refer to the note
in Chapter 1.2
The encoder electronics (if an absolute value encoder was integrated optionally) must be disposed of in
the proper manner as electronic scrap.

TAM 00699 20
DSD2 045 –132 04/2018
Three-phase synchronous motor English
8 Appendix 1: pole assignment (main connection and Control terminal)
Key:
- U; V; W Power connection
- K+ / K- Temperature sensor (KTY84-130)
- R1 / R2 Temperature sensor (PT 1000)
- BD+ / BD- Brake
- SL Earth conductor
8.1 Main connection via plug
The standstill current I0 of the motor determines the size of the built-in box.
Size 1: I0to 20 A Size 1.5 I0to 36 A
Figure 2: Main connection with thermal sensor and brake
Note: If the temperature sensor is wired ideally via the encoder cable, then the signals K+ and K-
are omitted in the above diagrams.
8.2 Main connection via the terminal box (Standard design acc. to catalogue)
Use during standstill current I0 > 36 A.
Figure 3A: pole assignment with thermal sensor and brake at motor sizes of 56 to 100
Table of contents
Other Baumuller Engine manuals
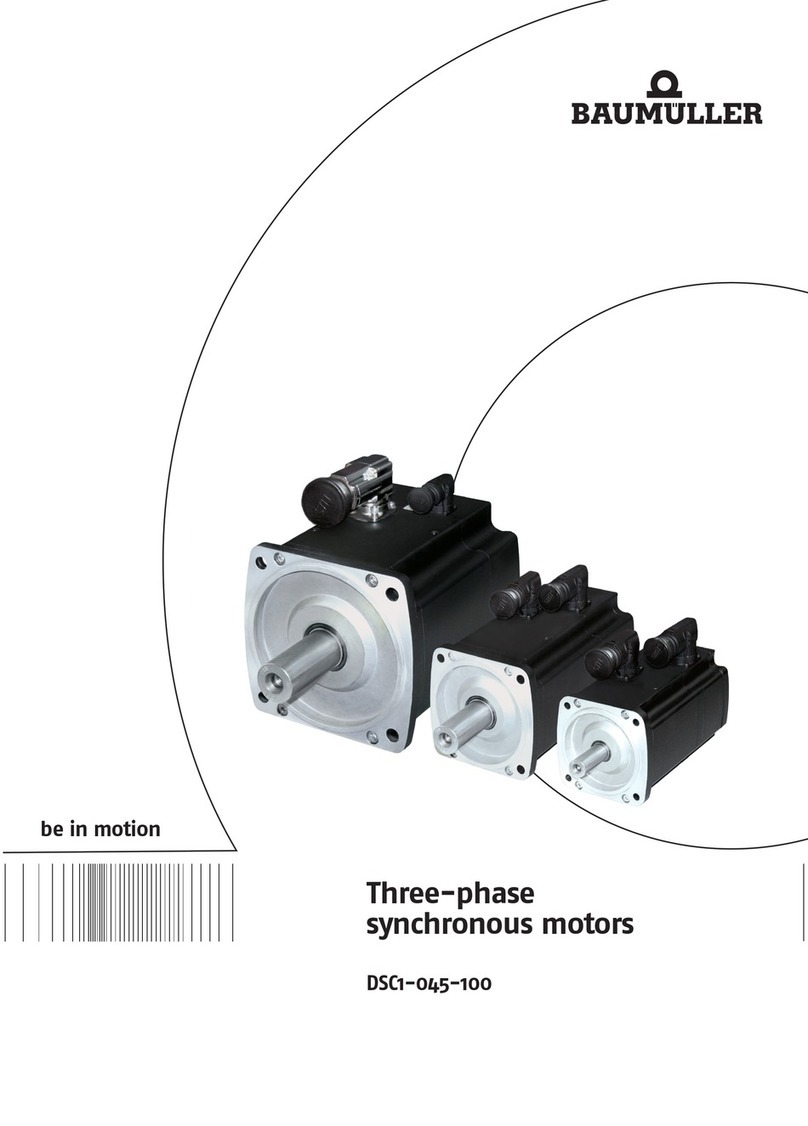
Baumuller
Baumuller DSC1-045-100 Series User manual
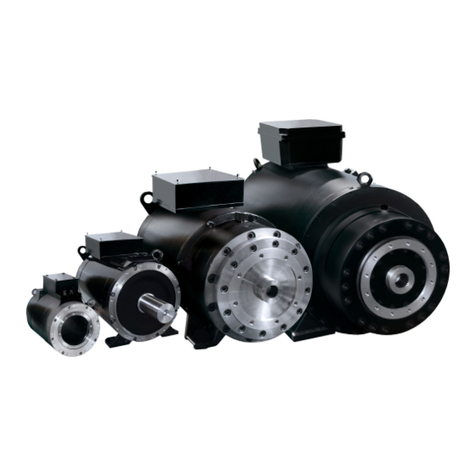
Baumuller
Baumuller DST2 Series Installation instructions

Baumuller
Baumuller DA 100 Guide
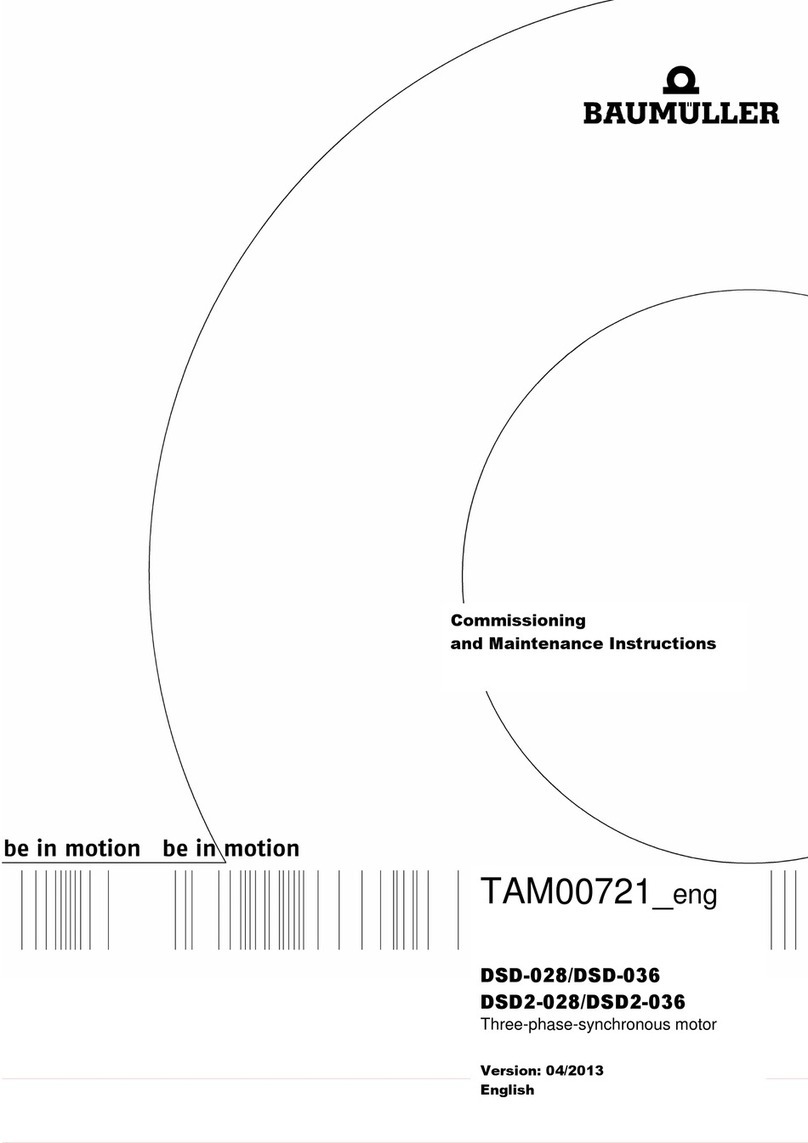
Baumuller
Baumuller DSD-028 Guide
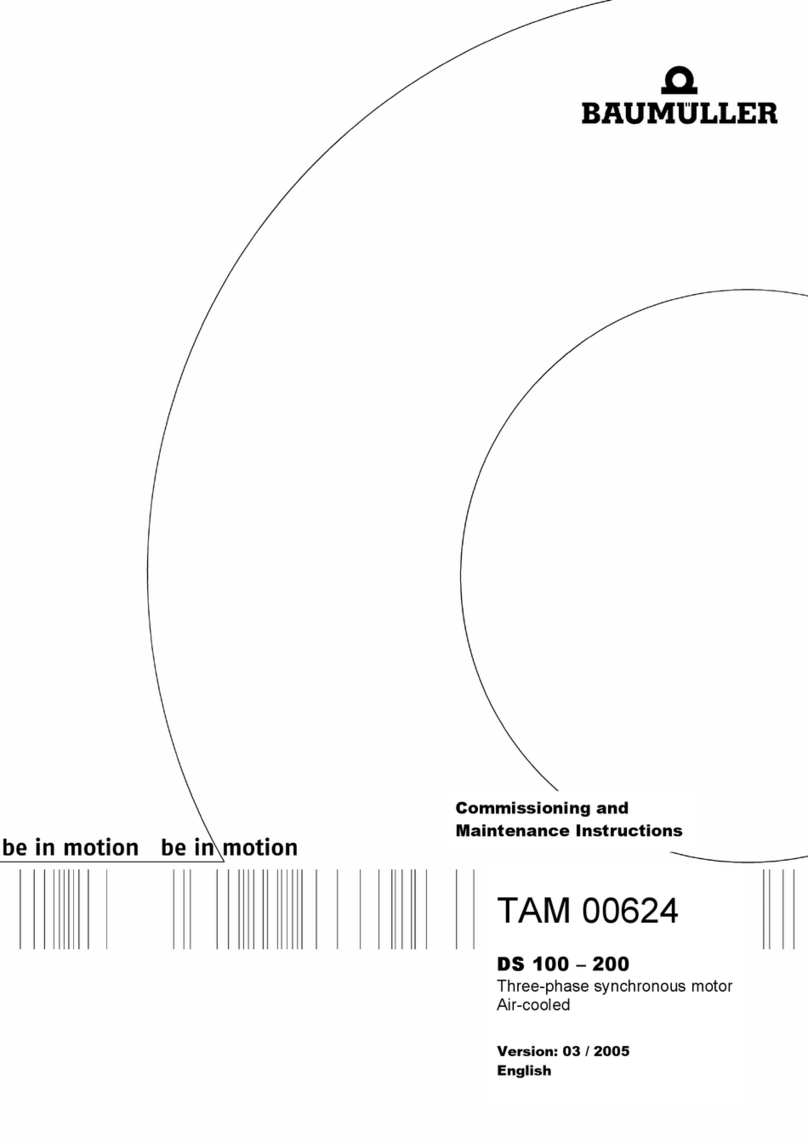
Baumuller
Baumuller DS 100 Guide

Baumuller
Baumuller DSM1 Guide
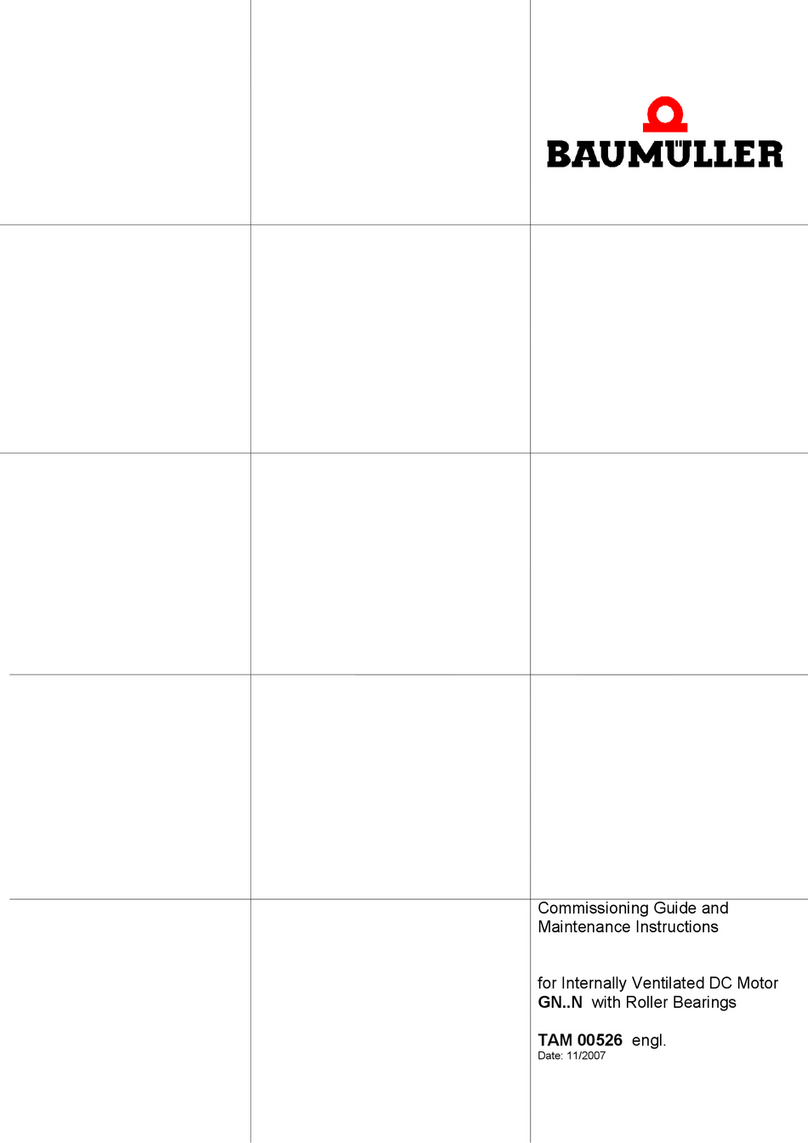
Baumuller
Baumuller GNA 100 User manual
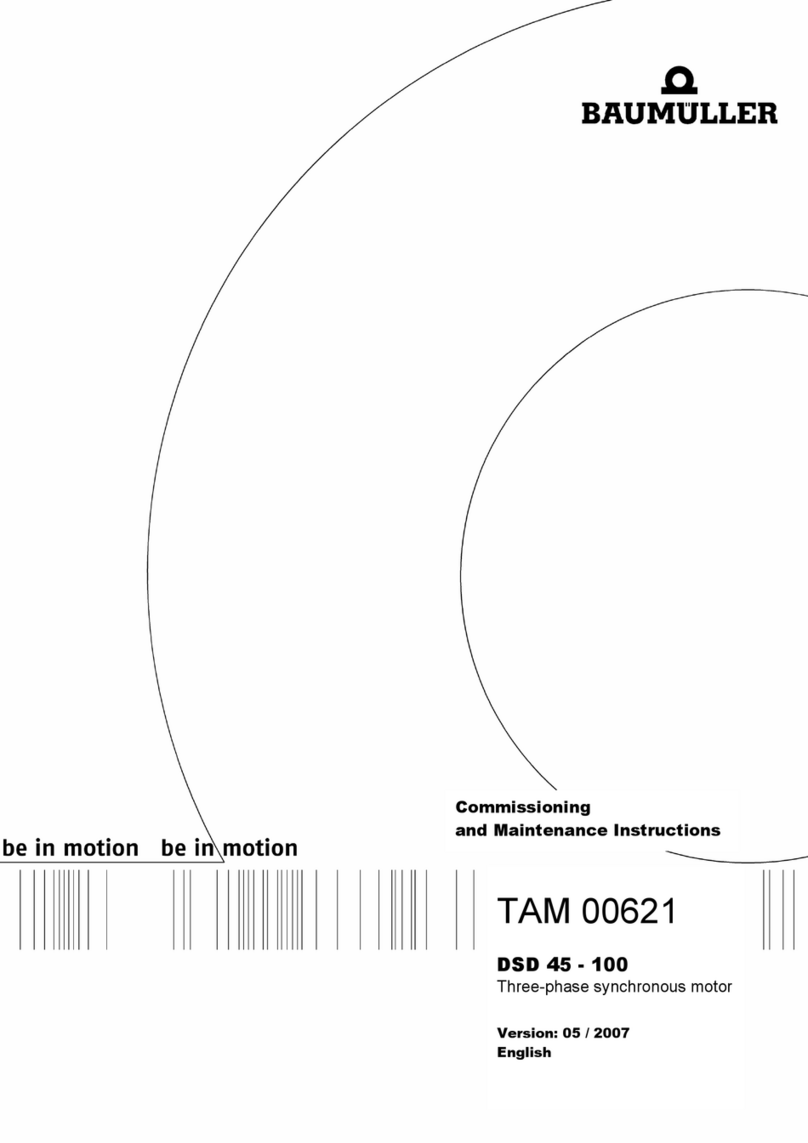
Baumuller
Baumuller DSD 45 Guide
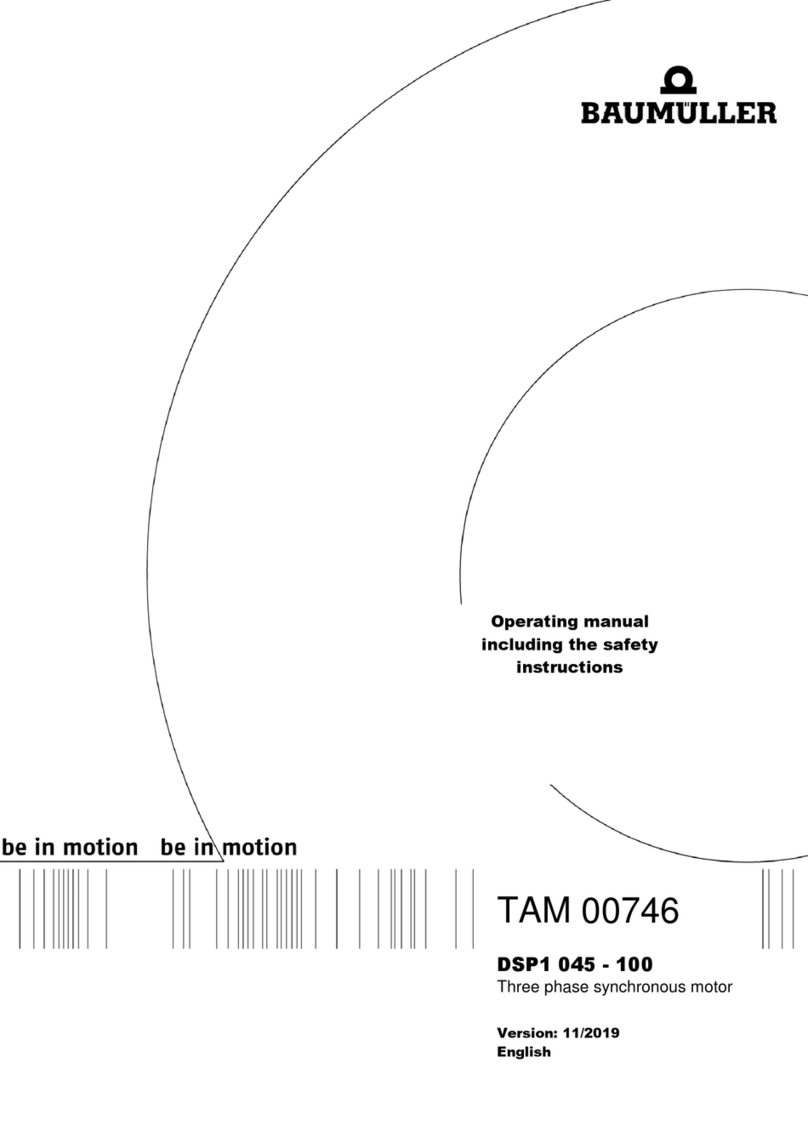
Baumuller
Baumuller DSP1 Series User manual
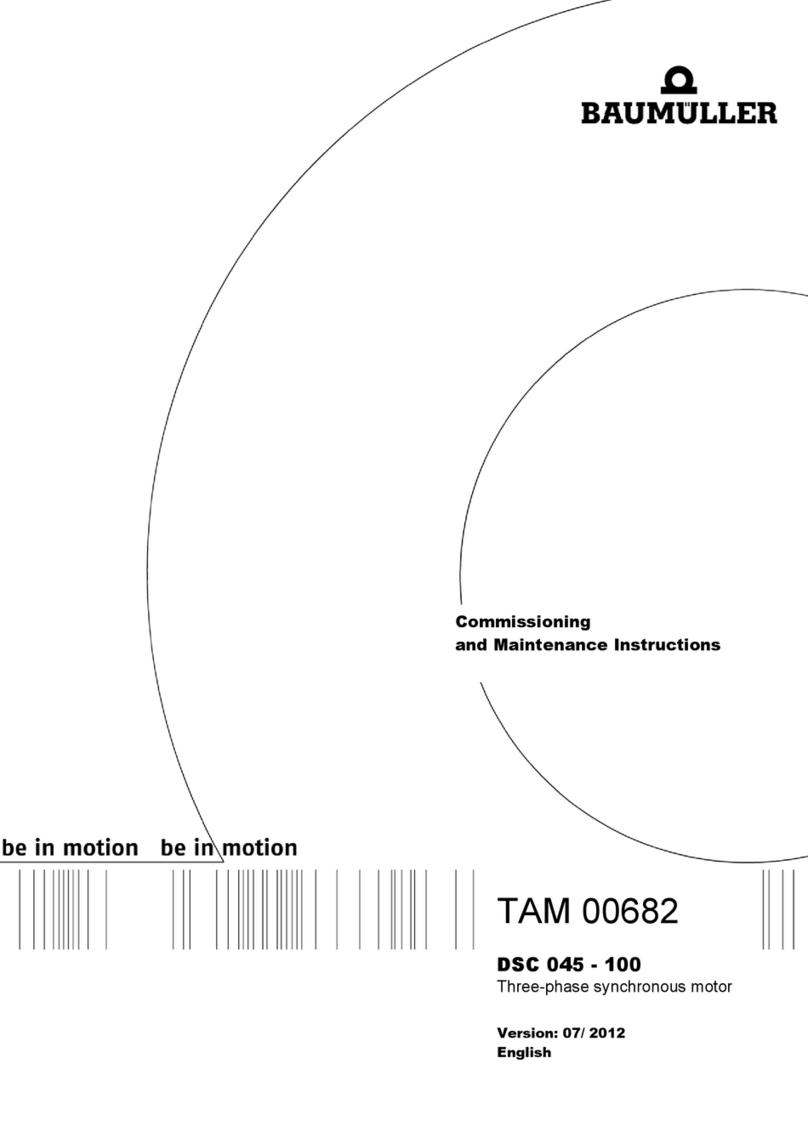
Baumuller
Baumuller DSC Series Guide
Popular Engine manuals by other brands
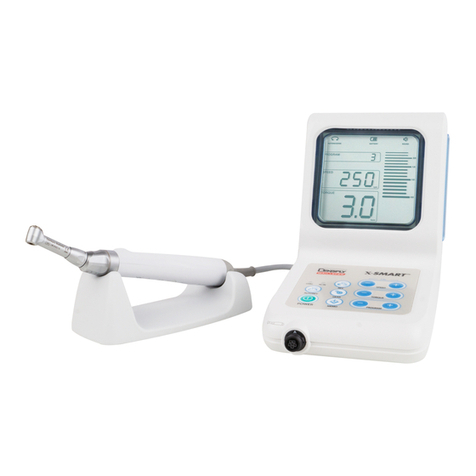
Dentsply Maillefer
Dentsply Maillefer X-SMART user manual
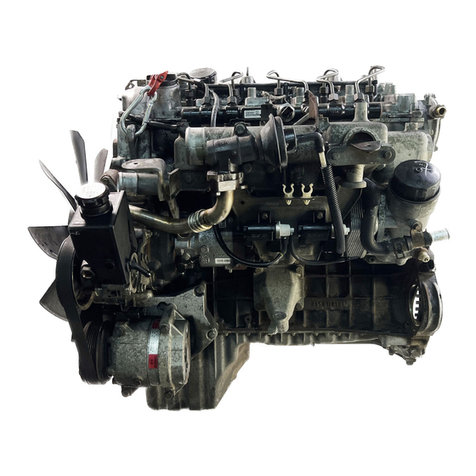
SSANGYONG
SSANGYONG REXTON Service manual

O.S. engine
O.S. engine FS-120S-E quick start guide

Briggs & Stratton
Briggs & Stratton Vanguard 80000 Operator's manual
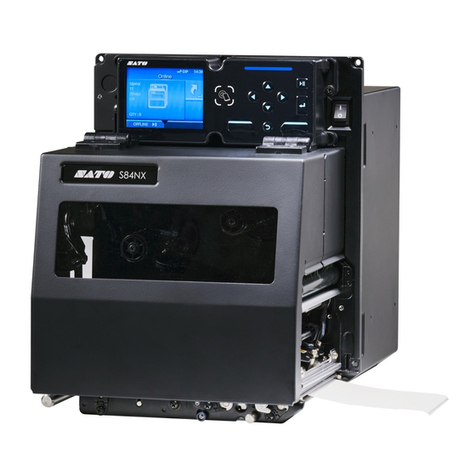
SATO
SATO S84NX Operator's manual

Briggs & Stratton
Briggs & Stratton 210000 Series Operator's manual