BeiJer iX T7AM User manual

iXT7AM
InstallationManual
English
MAEN118A,2013-06

Foreword
InstallationmanualforiXT7AM
Foreword
All are developed to satisfy the demands of human-machine communication.
Built-in functions such as displaying and controlling text, dynamic indication,
time channels, alarm and recipe handling are included.
The operator panel works primarily in an object-oriented way, making it easy to
understand and use. Configuration is carried out on a PC using the iX Developer
configuration tool. The project can then be transferred and stored in the operator
panel itself.
Various types of automation equipment such PLCs, servos or drives can be
connected to the . In this manual, the term “the controller” refers to the connected
equipment.
This manual explains how to install the operator panel. Please refer to the
iX Developer reference manual for further information.
Order no: MAEN118A
Copyright © 2013-06 Beijer Electronics AB. All rights reserved.
The information in this document is subject to changewithoutnoticeandisprovidedasavailableatthe
time of printing. Beijer Electronics AB, including all its group companies, reserves the right to change any
information without updating this publication. Beijer Electronics AB, including all its group companies,
assumesnoresponsibilityforanyerrorsthatmayappearinthisdocument. Readtheentireinstallation
manual prior to installing and using this equipment. Only qualified personnel may install, operate or repair
this equipment. Beijer Electronics AB, including all its group companies, are not responsible for modified,
altered or renovated equipment. Because the equipment has a wide range of applications, users must acquire
the appropriate knowledge to use the equipment properly in their specific applications. Persons responsible
for the application and the equipment must themselves ensure that each application is in compliance with
all relevant requirements, standards and legislationinrespecttoconfigurationandsafety. Onlypartsand
accessories manufactured according to specifications set by Beijer Electronics AB, including all its group
companies, may be used.
BEIJER ELECTRONICS AB, INCLUDING ALL ITS GROUP
COMPANIES, SHALL NOT BE LIABLE TO ANYONE FOR ANY
DIRECT, INDIRECT, SPECIAL, INCIDENTAL OR CONSEQUENTIAL
DAMAGES RESULTING FROM THE INSTALLATION, USE OR
REPAIR OF THIS EQUIPMENT, WHETHER ARISING IN TORT,
CONTRACT, OR OTHERWISE. BUYER'S SOLE REMEDY SHALL
BE THE REPAIR, REPLACEMENT, OR REFUND OF PURCHASE
PRICE, AND THE CHOICE OF THE APPLICABLE REMEDY SHALL
BE AT THE SOLE DISCRETION OF BEIJER ELECTRONICS AB,
INCLUDING ALL ITS GROUP COMPANIES.
BeijerElectronics, MAEN118A

Contents
Contents
1 SafetyPrecautions ....................................................... 4
1.1 UL and cUL Installation ......................................... 4
1.2 General ........................................................... 5
1.3 DuringInstallation .............................................. 5
1.4 DuringUse ....................................................... 6
1.5 Service and Maintenance ........................................ 6
1.6 Dismantling and Scrapping ..................................... 6
2 Installation ............................................................... 7
2.1 SpaceRequirements ............................................. 7
2.2 InstallationProcess .............................................. 8
2.2.1 ConnectionstotheController .................................. 9
2.2.2 OtherConnectionsandPeripherals .............................10
3 TechnicalData ........................................................... 11
4 ChemicalResistance .................................................... 13
4.1 MetalCasing ..................................................... 13
4.2 Touch Screen and Overlay ....................................... 14
4.2.1 AutoflexEBA180L ..............................................14
4.2.2 TouchScreenSurface ............................................15
4.2.3 Autotex ..........................................................15
5 OperatorPanelDrawings .............................................. 16
5.1 Connectors ....................................................... 16
5.2 CommunicationPorts ........................................... 16
5.3 iXT7AMOutline ............................................... 17
6 Additional Installation Tips ............................................ 18
6.1 Grounding the Operator Panel ................................. 18
6.2 Ethernet Connection in the Operator Panel ................... 19
6.3 To Achieve Better EMC Protection ............................. 21
6.4 AmbientTemperature ........................................... 22
6.5 Safety ............................................................. 23
6.6 GalvanicIsolation ................................................ 24
6.7 Cable and Bus Termination RS485 ............................. 25
BeijerElectronics, MAEN118A

Safety Precautions
1SafetyPrecautions
Both the installer and the owner and/or operator of the operator panel must read
and understand this installation manual.
1.1 ULandcULInstallation
•This equipment is suitable for use in Class 2 non-hazardous locations only.
[Combinations of equipment in your system are subject to investigation by
the local Authority Having Jurisdiction at the time of installation].
•All devices have to be supplied by a Class 2 power supply.
Warning:
Donotdisconnectequipmentunlesspowerhasbeenremovedortheareais
knowntobenon-hazardous
•For Canada also AVERTISSEMENT – AVANT DE DECONNECTER
L’EQUIPEMENT, COUPER LE COURANT OUS’ASSURER QUE
L‘EMPLACEMENT EST DESIGNE NON DANGEREUX.
Warning:
OnlyULandcULapprovedexpansionunitsareallowedtobeconnectedto
theportdesignated“EXPANSION”. Atthemomenttherearenosuchunits
evaluatedorallowed
Warning:
Donotreplaceexpansionunitunlesspowerhasbeenswitchedofforthearea
isknowntobenon-hazardous.
•This product contains a battery; this must only be changed in an area known
to be non-hazardous.
–Replace Battery with Seiko Instruments or similar, Part No. MS920SE.
Use of another battery may present a risk of fire or explosion. See owner's
manual for safety instructions.
Warning:
Batterymayexplodeifmistreated. Donotrecharge,disassembleordispose
ofinfire.
•For use on a flat surface of a type 4X enclosure indoor use only.
•Use 75 degree conductors only
•Use copper conductors only
BeijerElectronics, MAEN118A 4

Safety Precautions
•To make wiring connections to the power supply connector, follow the table
with cable and torque specifications below:
TerminalBlockNo. WireSizeAWG TQLb.In.
X1/X100Phoenixconnectors AWG30-12 5-7
X1/X100Anytekconnectors AWG24-12 3.5
•ThesedevicesareClass2suppliedprogrammablecontrollers(industrialPCs)
for the use in industrial control equipment and are intended to be (front)
panel mounted (Type 1 and 4x for indoor use only).
1.2 General
•Read the safety precautions carefully.
•Check the delivery for transportation damage. If damage is found, notify the
supplier as soon as possible.
•Do not use the operator panel in an environment with high explosive hazards.
•The supplier is not responsible for modified, altered or reconstructed
equipment.
•Use only parts and accessories manufactured according to specifications of
the supplier.
•Read the installation and operating instructions carefully before installing,
using or repairing the operator panel.
•Neverallowfluids,metalfilingsorwiringdebristoenteranyopeningsinthe
operator panel. This may cause fire or electrical shock.
•Only qualified personnel may operate the operator panel.
•Storing the operator panel where the temperature is lower/higher than
recommended in this manual can cause the LCD display liquid to
congeal/become isotopic.
•The LCD display liquid contains a powerful irritant. In case of skin contact,
wash immediately with plenty of water. In case of eye contact, hold the eye
open,flushwithplentyofwaterandgetmedicalattention.
•Thefiguresinthismanualservesanillustrativepurpose. Becauseofthemany
variables associated with any particular installation, the supplier cannot
assume responsibility for actual use based on the figures.
•The supplier neither guarantees that the operator panel is suitable for your
particular application, nor assumes responsibility for your product design,
installation or operation.
•It is recommended to turn on and shut down the operator panel at least once
before installing any components/cards or before connecting the operator
panel to external devices, like for example serial devices.
1.3 DuringInstallation
•The operator panel is designed for stationary installation on a plane surface,
where the following conditions are fulfilled:
–no high explosive risks
–no strong magnetic fields
–no direct sunlight
–no large, sudden temperature changes
•Install the product according to the accompanying installation instructions.
BeijerElectronics, MAEN118A 5

Safety Precautions
•Ground the product according to the accompanying installation instructions.
•Only qualified personnel may install the operator panel.
•Separate the high voltage, signal and supply cables.
•Make sure that the voltage and polarity of the power source is correct before
connecting the product to the power outlet.
•Peripheral equipment must be appropriate for the application and location.
1.4 DuringUse
•Keep the operator panel clean.
•Emergency stop and other safety functions may not be controlled from the
operator panel.
•Do not use too much force or sharp objects when touching the keys,
touchscreen etc.
1.5 ServiceandMaintenance
•Only qualified personnel should carry out repairs.
•The agreed warranty applies.
•Before carrying out any cleaning or maintenance operations, disconnect the
equipment from the electrical supply.
•Clean the display and surrounding front cover with a soft cloth and mild
detergent.
•Replacing the battery incorrectly may result in explosion. Only use batteries
recommended by the supplier. During the warranty period, the battery needs
to be replaced by an authorized Beijer Electronics service center.
1.6 DismantlingandScrapping
•The operator panel or parts thereof shall be recycled according to local
regulations.
•The following components contain substances that might be hazardous
to health and the environment: lithium battery, electrolytic capacitor and
display.
BeijerElectronics, MAEN118A 6

Installation
2Installation
2.1 SpaceRequirements
•Maximum installation plate thickness: 11 mm
•Space requirements in millimeters when installing the operator panel:
50 mm50 mm
100 mm
100 mm
100 mm
204 mm
143 mm
Note:
Thedimensionsonthedrawingarenotproportional.
BeijerElectronics, MAEN118A 7

Installation
2.2 InstallationProcess
The following is needed:
•A Phillips/slot screwdriver
1. Unpack and check the delivery. If damage is found, notify the supplier.
Note:
Placetheoperatorpanelonastablesurfaceduringinstallation.
Droppingthepanelorlettingitfallmaycausedamage.
2. Usethecutoutdimensionsthatareincludedontheoutlinedrawing,found
in section Operator Panel Drawings and in the Technical Data table, to cut
a correct opening in the cabinet. A separate cut out drawing is available for
download from the Beijer Electronics web site.
3. Secure the operator panel in position using all the fastening holes and the
provided brackets and screws:
x 4 0.5 - 1.0 Nm
BeijerElectronics, MAEN118A 8

Installation
4. Connect the cables in the specified order, according to the drawing and steps
below.
Caution:
•Ensurethattheoperatorpanelandthecontrollersystemhavethesameelectrical
grounding(referencevoltagelevel),otherwiseerrorsincommunicationmay
occur.
•Theoperatorpanelmustbebroughttoambienttemperaturebeforeitisstarted
up. Ifcondensationforms,ensurethattheoperatorpanelisdrybeforeconnecting
ittothepoweroutlet.
•Ensurethatthevoltageandpolarityofthepowersourceiscorrect.
•Useonlyshieldedcommunicationcables.
•Separatehighvoltagecablesfromsignalandsupplycables.
24V DC
RS232/
RS422/
RS485
24V DC
A
D
Controller
Power
B
Ethernet
C
–Connect cable A.
–Connect cable B, using an M5 screw and a grounding conductor (as short
as possible) with a cross-section of minimum 2.5 mm2.
–Connect cable C.
–Connect cable D.
5. Carefully remove the laminated film over the operator panel display, to avoid
static electricity that could damage the panel.
2.2.1 ConnectionstotheController
For information about the cables to be used when connecting the operator panel to
the controller, please refer to the help file for the driver in question.
BeijerElectronics, MAEN118A 9

Installation
2.2.2 OtherConnectionsandPeripherals
Cables, peripheral equipment and accessories must be suitable for the application
and its environment. For further details or recommendations, please refer to the
supplier.
BeijerElectronics, MAEN118A 10

Technical Data
3TechnicalData
Parameter iX T7AM
Frontpanel,W×H×D 204×143×7mm
Cutoutdimensions,
W×H 187×126mm
Mountingdepth 43mm(143mmincludingclearance)
Standalonemounting VESA75×75
Note: MaximumscrewlengthforVESAmountingis4mm.
Usageoflongerscrewsmayleadtodamage.
Frontpanelseal IP65
Rearpanelseal IP20
Touchscreen
material Polyesteronglass,resistive.
Overlay: AutoflexEBA180L(1).
Touchscreen
operations 1millionfingertouchoperations
Reverseside
material Powder-coatedaluminum
Framematerial Powder-coatedaluminum
Weight 0.8kg
Serialportfor
COM1RS232and
COM2RS422/RS485
9-pinD-subcontactwithRS232RTS/CTS,chassis-mounted
femalewithstandardlockingscrews4-40UNC
Serialportfor
COM3RS232and
COM4RS422/RS485
9-pinD-subcontactwithRS232RTS/CTS,chassis-mounted
femalewithstandardlockingscrews4-40UNC
Ethernet 1×10Base-T/100Base-T(shieldedRJ45)
USB 1×USBHost2.0,maxoutputcurrent200mA
Processor 400MHzARM9
Externalstorage
media 1×SDcard(optional). OnlycompatiblewiththestandardSD
formatwithupto2GBstoragecapacity.
Flashmemory 128MBSSD(NANDFlash)
MemoryRAM 128MB(DDR2)
LED 1×blue/redsoftwareprogrammable
Realtimeclock Yes
Battery BR2032Poly-carbonmonofluorideLithiumCoin
Powerconsumption
atratedvoltage 6.0W
Fuse InternalDCfuse,2.0AT,5×20mm
Powersupply +24VDC(18-32VDC)
CE:Thepowersupplymustconformwiththerequirements
accordingtoIEC60950andIEC61558-2-4.
ULandcUL:Thepowersupplymustconformwiththe
requirementsforclassIIpowersupplies.
Display TFT-LCDwithLEDbacklight.800×480pixels,64kcolors
Activeareaof
display,W×H 152.4×91.4mm
BeijerElectronics, MAEN118A 11

Chemical Resistance
4 ChemicalResistance
4.1 MetalCasing
The frame and casing material is powder-coated aluminum. This powder paint
withstands exposure to the following chemicals without visible change:
Aceticacid10% Phosphoricacid4%
Citricacid10% Phosphoricacid10%
Diesel Seawater
Distilledwater Sodiumchloride2%
Edibleoil Sodiumchloride20%
Fueloil Sulphuricacid20%
Hydrogenperoxide3% Tapwater
The powder paint shows limited resistance to the following chemicals at room
temperature:
Butanol Nitricacid3%
Hydrochloricacid5% Nitricacid10%
Isopropylalcohol Phosphoricacid43%
Na-hypochlorite10% Turpentine
Note:
Ifexposuretoanyoftheabovechemicalsisdemanded,itisrecommendedtofirsttest
thechemicalinahiddenspotofthemetalcasing.
Thepowderpaintshowslittleornoresistancetothefollowingchemicalsatroom
temperature:
Aceticacid,conc. Methyl-ethylketone Toluene
Acetone Nitricacid30% Trichlorethylene
Ammonia5% Phenol Xylene
Ammonia,conc. Sodiumhydroxide5% 97octaneunleadedpetrol
Ethylacetate Sodiumhydroxide30% 98octaneleadedpetrol
BeijerElectronics, MAEN118A 13

Chemical Resistance
4.2 TouchScreenandOverlay
4.2.1 AutoflexEBA180L
Autoflex EBA 180L covers the overlay surrounding the touch screen.
SolventResistance
Autoflex EBA 180L withstands exposure of more than 24 hours duration under
DIN42115Part2tothefollowingchemicalswithoutvisiblechange:
Acetonitrile DieselDowney/Lenor(1) Phosphoricacid(<30%)
Ajax/Viminsolution Ethanol Potassiumferricyanide
Alkalicarbonate
solution(1) Glycerine Potassiumhydroxide(<30%)
Ammonia(<40%)(1) Glycol PureTurpentine
Aceticacid(<50%) Gumption(1) SBP60/95(1)
Arielpowderin
solution(1) Hydrochloricacid(<36%) Sulfuricacid(<10%)
Bleach(1) Linseedoil Tomatoketchup
Castoroil Methanol Trichloroaceticacid(<50%)
Causticsoda(<40%)(1) Nitricacid(<10%) WhiteSpirit
Cuttingoil Paraffinoil Windex(1)
Cyclohexanol Persilpowderin
solution(1) Wisk
Diacetonealcohol Petroleumspirit(1) -
(1)Extremelyfaintglossingofthetexturewasnoted.
Autoflex EBA 180L withstands DIN 42 115 Part 2 exposure of up to 1 hour
duration to glacial acetic acid without visible change.
Autoflex EBA 180L is not resistant to high pressure steam at over 100 °C or the
following chemicals:
Concentratedmineralacids Benzylalcohol
Concentratedcausticsolution Methylenechloride
BeijerElectronics, MAEN118A 14

Chemical Resistance
4.2.2 TouchScreenSurface
The touch screen surface on the operator panel withstands exposure to the
following solvents without visible change:
Solvents Time
Acetone 10minutes
Isopropanol 10minutes
Toluene 5 hours
4.2.3 Autotex
It is recommended to use the Autoflex EB touch display protection film, that can
be ordered from Beijer Electronics.
OutdoorUse
In common with all polyester based films, Autoflex EB is not suitable for use in
conditions of long-term exposure to direct sunlight.
BeijerElectronics, MAEN118A 15

Operator Panel Drawings
5 OperatorPanelDrawings
5.1 Connectors
1234
COM 3/4LANCOM 1/2
Pos. Connector Description
1 Powersupply +24VDC(18-32VDC)
2 COM1/2 CommunicationPorts
3 LAN 1×10/100Base-T(shieldedRJ-45)
4 COM3/4 CommunicationPorts
5.2 CommunicationPorts
Serialport,9-pinfemale Serialport,9-pinfemale
Pin COM1 COM2 COM3 COM4
1- RS422Tx+
RS485Tx+/Rx+ -RS422Tx+
RS485Tx+/Rx+
2 RS232RxD - RS232RxD -
3 RS232TxD - RS232TxD -
4 - RS422Rx+ - RS422Rx+
5 GND GND GND GND
6- RS422Tx-
RS485Tx-/Rx- -RS422Tx-
RS485Tx-/Rx-
7 RS232RTS - - RS422RTS+
8 RS232CTS - - RS422RTS-
9 - RS422Rx- - RS422Rx-
Note:
Inordertoutilizetwocommunicationportsonthesamephysicalport,theY-splitcable
CAB109mustbeused.
DrawingforexternalcableCAB109(drawing#Z7100-029E)isavailableonthewebsite:
www.beijerelectronics.com
BeijerElectronics, MAEN118A 16

Additional Installation Tips
6 AdditionalInstallationTips
When experiencing communication problems in for example noisy environments
or when operating close to temperature limits, the following recommendations
are to be noticed.
6.1 GroundingtheOperatorPanel
1
2
3
4
5
6
5350
Door
Operator panel
Ferrite core
Mounting plate in the cabinet
Power supply
24 V DC
The operator panel’s mounting clamps do not provide a secure grounding
connection between the panel and the device cabinet, see 1 in drawing above.
1. Connect a 2.5 mm2wire between the operator panel’s quick-connect plinth
and the panel’s chassis, see 2 in drawing above.
2. Connect a 6 mm2or 4 mm2wire or grounding braid between the operator
panel’s chassis and the closest grounding point on the door, see 3 in drawing
above.
3. Connect a strong but short grounding braid between the door and the device
cabinet, see 4 in drawing above.
4. Twist the cables onto the 24 V DC feed, see 5 in drawing above. Minimum
cross-section of the cable is 2.5 mm2.
2 turns around the ferrite core provide 4 times the suppression of 1 turn.
3 turns around the ferrite core provide 9 times the suppression of 1 turn.
A ferrite core suppresses disturbances to the 24 V feed, see 6 in drawing above.
BeijerElectronics, MAEN118A 18

Additional Installation Tips
Note:
Thegroundingwiresshouldbeshortandtheconductorshouldhavealargearea.
Along,thingroundingwirehasaveryhighimpedance(resistance)athighfrequencies
andwillnotguidedisturbancestotheground.
Multi-wireconductorsarebetterthansinglewireconductorswiththesamearea.
Abraidedconductorwirewiththesameareaisevenbetter. Thebestisashort,thick
groundingbraid.
6.2 EthernetConnectioninthe
OperatorPanel
1
2
3
4
5
RJ45
RJ45
RJ45
RJ45
RJ45
RJ45
RJ45
RJ45
Industrial Ethernet
Operator panel
Operator panel
Operator panel
Operator panel
Shielded
Short and
unshielded
0.1 μF
250 V
1-1
3-3
8-8
2-2
In some industrial units for Ethernet, the RJ45 contact’s shield is connected to the
chassis via a capacitor, see 1 in drawing above.
The operator panel’s Ethernet shield is directly connected to the chassis, see 2 in
drawing above.
1. Check whether the other Ethernet unit has its shield directly grounded or
grounded via a capacitor.
Note:
Inmanycases,connectingtheshieldedEthernetcablingtothechassisatbothendsis
inappropriate. Humorgroundingloopscanoccur. Unshieldedcablingmayevenresult
infewercommunicationerrors.
BeijerElectronics, MAEN118A 19

Additional Installation Tips
A good solution may be to use a shielded Ethernet cable, but to connect the shield
at one end only.
One option is to break the shield, see 3 in drawing above.
A more elegant method is to expand the shielded Ethernet cabling with a piece of
unshielded Ethernet cable, see 4 in drawing above.
The shield can be grounded via an external 0.1 μF/250 V plastic capacitor, see 5 in
drawing above. This will connect the HF transients to ground.
BeijerElectronics, MAEN118A 20
Table of contents
Other BeiJer Control Panel manuals
Popular Control Panel manuals by other brands
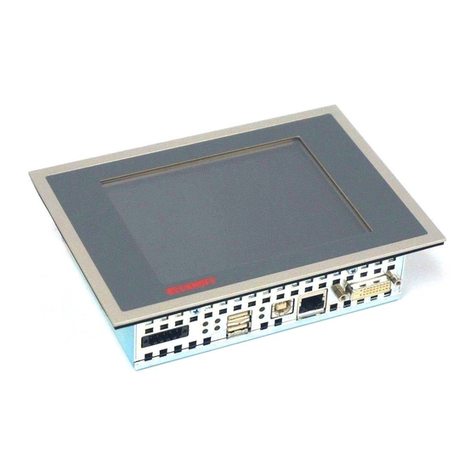
Beckhoff
Beckhoff CP69 Series Installation and operating instructions

Texecom
Texecom Premier 412 user guide

Vents
Vents VENTS RTS-1-400 instructions
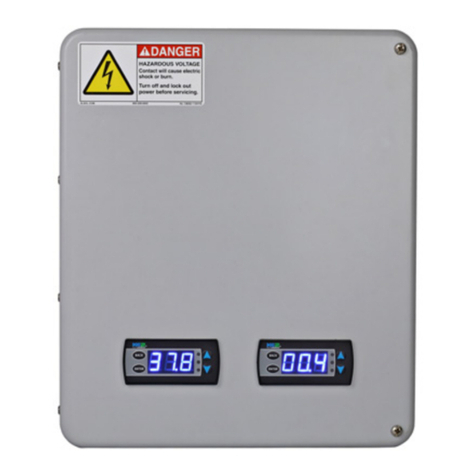
KE2 Therm Solutions
KE2 Therm Solutions EvapPanel quick start guide
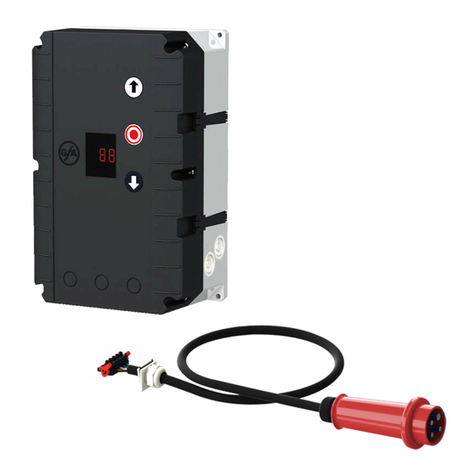
GFA
GFA Elektromaten TS 956 Electrical operating instructions
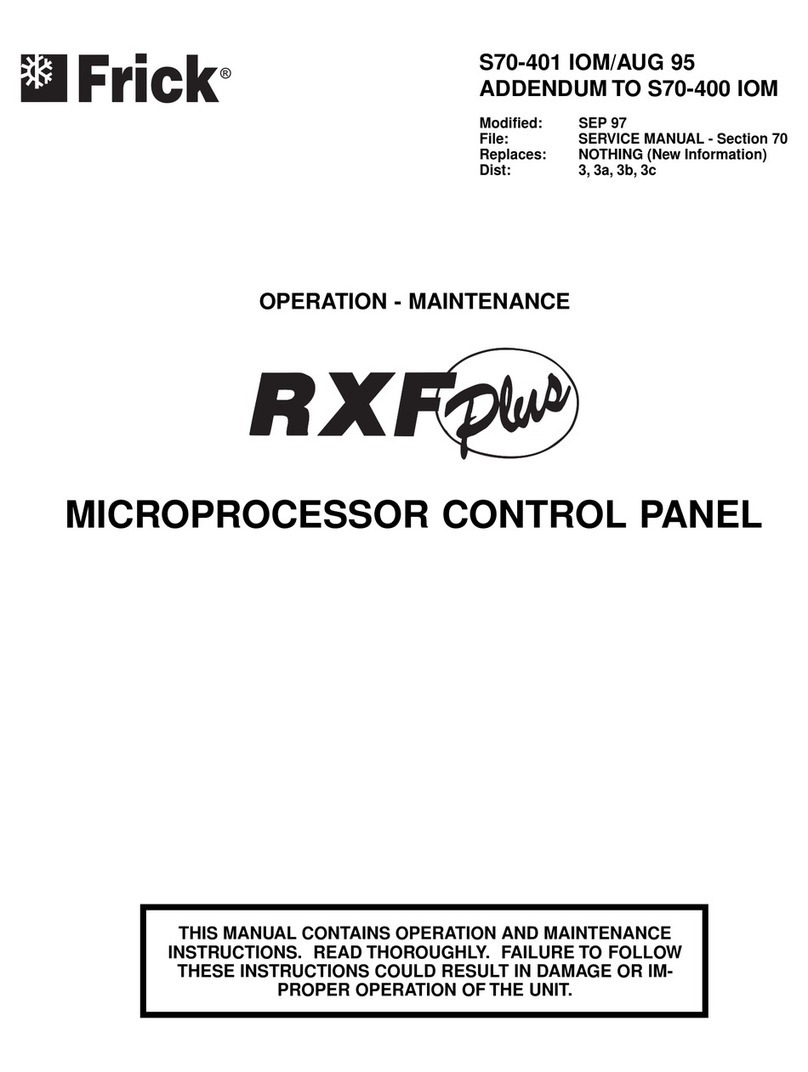
Frick
Frick RXF Plus operation & maintenance