BeiJer BFI-H3 Installation manual

Page 1 (29)
Beijer Electronics a company in the Beijer Electronics Group
Parent Company (Reg. office) Subsidiaries
Beijer Electronics AB Norway, Drammen: Beijer Electronics AS, +47 32 24 30 00
P.O. Box 426 Denmark, Copenhagen: Beijer Electronics A/S,
+45 75 76 66
SE-201 24 MALMÖ, SWEDEN Germany, Nürtingen: Beijer Electronics GmbH, +49 7022 9660 0
Telephone +46 40 35 86 00 UK, Castle Donington: Beijer Electronics Products, +44 (0)845519 5430
Fax +46 40 93 23 01 France, Champlan: Beijer Electronics +33 (0)1 69 10 22 42
Visiting address: Stora Varvsgatan 13a, Malmö Turkey Istanbul: Beijer Electronics ve Ticaret A.s 0090 216 366 32 0200
Beijer Electronics Frequency Inverter BFI-H3 KI00363B 2019-09
1 Start-up document
This document is a short start-up guide describing basic functionality of the drive BFI-H3,
firmware 2.50, manufactured from August 2019. Detailed explanations are to be read in
User Manual BFI-H3. This manual is attached with the drive itself but also possible to
download from www.beijerelectronics.se or .dk or .no or .de or .com or .tw or .co.uk/ or
beijerelektronik.com.tr
2 Important Safety Information
Please read the IMPORTANT SAFETY INFORMATION below, and all Warning and Caution
information elsewhere.
Danger : Indicates a risk of electric shock, which, if not
avoided, could result in damage to the equipment and
possible injury or death.
Danger : Indicates a potentially hazardous
situation other than electrical, which if not
avoided, could result in damage to property.
This variable speed drive product is intended for professional incorporation into complete equipment or systems as part of a fixed installation. If installed
incorrectly it may present a safety hazard. The BFI uses high voltages and currents, carries a high level of stored electrical energy, and is used to control
mechanical plant that may cause injury. Close attention is required to system design and electrical installation to avoid hazards in either normal operation
or in the event of equipment malfunction. Only qualified electricians are allowed to install and maintain this product.
System design, installation, commissioning and maintenance must be carried out only by personnel who have the necessary training and experience.
They must carefully read this safety information and the instructions in this Guide and follow all information regarding transport, storage, installation and
use of the
BFI
, including the specified environmental limitations.
Do not perform any flash test or voltage withstand test on the
BFI
. Any electrical measurements required should be carried out w
ith
BFI
disconnected.
Electric shock hazard! Disconnect and ISOLATE the BFI before attempting any work on it. High voltages are present at the terminals and within the
drive for up to 10 minutes after disconnection of the electrical supply. Always ensure by using a suitable multimeter that no voltage is present on any
drive power terminals prior to commencing any work.
Where supply to the drive is through a plug and socket connector, do not disconnect until 10 minutes have elapsed after turni
ng off the
supply.
Ensure correct earthing connections. The earth cable must be sufficient to carry the maximum supply fault current which normally will be limited by the
fuses or MCB. Suitably rated fuses or MCB should be fitted in the mains supply to the drive, according to any local legislation or codes.
Do not carry out any work on the drive control cables whilst power is applied to the drive or to the external control circuits.
Within the European Union, all machinery in which this product is used must comply with Directive 98/37/EC, Safety of Machinery. In particular, the
machine manufacturer is responsible for providing a main switch and ensuring the electrical equipment complies with EN60204
-
1.
The level of integrity offered by the BFI control input functions – for example stop/start, forward/reverse and maximum speed is not sufficient for use in
safety-critical applications without independent channels of protection. All applications where malfunction could cause injury or loss of life must be
subjec
t to a risk assessment and further protection provided
where needed.
The driven motor can start at power up if the enable input signal is present.
The STOP function does not remove potentially lethal high voltages. ISOLATE the drive and wait 10 minutes before starting any work on it. Never carry
out any w
ork on the Drive, Motor or Motor cable whilst the input power is still applied.
The BFI can be programmed to operate the driven motor at speeds above or below the speed achieved when connecting the motor directly to the mains
supply. Obtain confirmation from the manufacturers of the motor and the driven machine about suitability for operation over the intended speed range
prior to machine start up.
Do not activate the automatic fault reset function o
n any systems whereby this may cause a potentially dan
gerous situation.
The
BFI has
an Ingress Protection rating of IP20
, IP55
or IP66 depending on the model.
IP20 units must be installed in a suitable enclosure.
When mounting the drive, ensure that sufficient cooling is provided. Do not carry out drilling operations with the drive in place, dust and swarf from
drilling may lead to damage.
BFI
are intended for indoor use only.
The entry of conductive or flammable foreign bodies should be prevented. Flammable material should not be placed close to the drive
Relative humidity must be less than 95% (non
-
condensing).
Ensure that the supply voltage, frequency and no. of phases (1 or 3 phase) correspond to the rating of the
BFI
as delivered.
Never conn
ect the mains power supply to the Output terminals U,
V, W.
Do not install any type of automatic switchgear between the drive and the motor
Wherever control cabling is close to power cabling, maintain a minimum separation of 100 mm and arrange crossings at 90 degrees
Ensure that all terminals are tightene
d to the appropriate torque setting
Do not attempt to carry out any repair of the BFI. In the case of suspected fault or malfunction, contact Beijer Electronics office for further assistance.

Beijer Electronics Frequency Inverter BFI-H3 KI00363B 2019-09
www.beijer.se www.beijer.no www.beijer.dk www.beijerelectronics.de www.beijerelectronics.com www.beijerelektronik.com.tr 2 (29
)
3 Contents
1 START-UP DOCUMENT .................................................................................................................................................. 1
2 IMPORTANT SAFETY INFORMATION ......................................................................................................................... 1
3 CONTENTS ........................................................................................................................................................................ 2
4 INSTALLATION ................................................................................................................................................................. 3
4.1 PHYSICAL DIMENSIONS IP66 ........................................................................................................................................... 3
4.2 PHYSICAL DIMENSIONS IP20 ........................................................................................................................................... 4
4.3 PHYSICAL DIMENSIONS IP55 ........................................................................................................................................... 5
4.4 FUSES, CABLE DIMENSIONS AND POWER LOSES ............................................................................................................. 6
4.5 DERATING INFORMATION ................................................................................................................................................. 7
4.6 OVERVIEW OF POWER SUPPLY, GROUNDING AND MOTOR CABLE ................................................................................... 8
4.7 SAFE TORQUE OFF, STO ................................................................................................................................................ 9
4.8 OVERVIEW CONTROL INPUTS/OUTPUTS ........................................................................................................................... 9
5 BASIC PARAMETER SETTING ................................................................................................................................... 10
5.1 DIGITAL START IN ONE DIRECTION AND ONE PRESET OR ANALOG SETPOINT ............................................................... 10
5.2 DIGITAL START IN TWO DIRECTIONS AND ONE PRESET OR ANALOG SETPOINT ............................................................ 11
5.3 DIGITAL START SIGNAL IN TWO DIRECTIONS AND 8 FIXED PRESET SPEEDS ................................................................. 12
5.4 ALARM RESET ................................................................................................................................................................. 13
5.5 TRANSISTOR OUTPUTS 24 VDC OR ANALOG OUTPUT, 0-10 V/4-20 MA ...................................................................... 13
5.6 RELAY OUTPUTS............................................................................................................................................................. 13
5.7 FIELDBUS CONTROL SETTINGS ...................................................................................................................................... 14
5.8 FIELDBUS COMMUNICATION PROTOCOL ........................................................................................................................ 14
5.9 PTC-THERMISTOR ......................................................................................................................................................... 15
5.10 CONTROL FROM A MODBUS RTU MASTER .................................................................................................................... 16
5.11 VECTOR CONTROL ......................................................................................................................................................... 17
5.12 PID-CONTROL ................................................................................................................................................................ 18
5.13 BFI-SMARTSTICK ........................................................................................................................................................... 20
6 KEYPAD ............................................................................................................................................................................ 21
6.1 DRIVE OPERATING DISPLAY – OLED KEYPAD, IP55 AND IP66 .................................................................................. 21
6.2 ACCESSING AND CHANGING PARAMETER VALUES – OLED KEYPAD .......................................................................... 22
6.3 RESETTING PARAMETERS TO FACTORY DEFAULT SETTINGS – OLED KEYPAD ......................................................... 22
6.4 CHANGING THE LANGUAGE ON THE OLED DISPLAY – OLED KEYPAD ....................................................................... 23
6.5 SELECTING BETWEEN HAND AND AUTO CONTROL – OLED KEYPAD .......................................................................... 23
6.6 KEYPAD SHORT CUTS .................................................................................................................................................... 24
6.7 MONITORING FROM KEYPAD .......................................................................................................................................... 25
7 GENERAL SPECIFICATION ......................................................................................................................................... 26
8 WARNING AND ALARM CODES ................................................................................................................................ 27
Copyright © Beijer Electronics, 2019
This software/documentation/information (below referred to as ‘the material’) is the property of Beijer Electronics. The holder
or user has a non-exclusive right to use the material.
The holder is not allowed to distribute the material to anyone outside his/her organization except in cases where the material is
part of a system that is supplied by the holder to his/her customer.
The material may only be used with products or software supplied by Beijer Electronics.
Beijer Electronics assumes no responsibility for any defects in the material, or for any consequences that might arise from the
use of the material.
It is the responsibility of the holder to ensure that any systems, for whatever applications, which is based on or includes the
material (whether in its entirety or in parts), meets the expected properties or functional requirements.
Beijer Electronics has no obligation to supply the holder with updated versions.

Beijer Electronics Frequency Inverter BFI-H3 KI00363B 2019-09
www.beijer.se www.beijer.no www.beijer.dk www.beijerelectronics.de www.beijerelectronics.com www.beijerelektronik.com.tr 3 (29
)
4 Installation
The drive should be mounted in a vertical position only on a flat, flame resistant, vibration free
mounting using the integral holes. IP55/66 is allowed to be mounted outdoors but must be
protected from sunlight and it also recommended having a roof to avoid snow directly on the
drive. See User Manual BFI-H3 for more details.
4.1 Physical dimensions IP66
BFI-H3-IP66 Drive
size
A
Height
[mm]
B
[mm]
D
[mm]
E
[mm]
F
Depth
[mm]
G
Width
[mm]
H
[mm]
I
[mm]
J
[mm]
Weight
[kg]
1 x 230 V 3 x 230 V 3 x 400 V
0043 – 0105
[0,75–2,2 kW]
0043 – 0105
[0,75–2,2 kW]
0022 – 0095
[0,75- 4 kW] 2 257 220 200 29 239 188
178 4.2
8.5
4,8
None 0180 – 0240
[4,0 – 5,5 kW]
0140 – 0240
[5,5 – 11 kW] 3 310 277 252 33.4 266 211
198 4.2
8.5
8,5
NOTE
Mounting bolts for Size 2 and 3: 4 x M4.
Control Terminal, Required Torque all sizes 0,5 Nm.
Power Terminal, Required Torque all sizes 1 Nm.
Drive IP-class
and
Size
X [mm]
Above &
Below
Y [mm]
Either
Side
Z [mm]
Between
drives
Minimum
Airflow
[m3/min]
IP20, size 2 75 10 46 0,3
IP20, size 3 100 10 52 0,9
IP20, size 4 200 25 70 1,7
IP20, size 5/6 200 25 70 2,9
IP20, size 8 300 100 100 20
All IP55 and
IP66
200 10 0 No require-
ment
Note All BFI can be mounted close to each without
any space in between
A
F
G
H
D
B
E
Ø
I
Ø
J
Ø
I
Ø
J

Beijer Electronics Frequency Inverter BFI-H3 KI00363B 2019-09
www.beijer.se www.beijer.no www.beijer.dk www.beijerelectronics.de www.beijerelectronics.com www.beijerelektronik.com.tr 4 (29
)
IP66 drives are fitted with 3 knockout holes for cable inlet and outlet. If more than 3 cables are to
enter the drive it is possible to have two or more cables going through one gland. This is to ensure
IP66.
Holes and recommended glands are listed in table below. The motor cable does not have to be
attached to the drive with an EMC-gland.
4.2 Physical dimensions IP20
BFI-H3-IP20 Drive
size
A
Height
[mm]
B
[mm]
C
[mm]
D
[mm]
E
[mm]
F
Depth
[mm]
G
Width
[mm]
H
[mm]
Weight
[kg]
1 x 230 V 3 x 230 V 3 x 400 V
0043 -
0105
[0,75-2,2kW]
0043 -
0105
[0,75- 2,2kW]
0022 -
0095
[0,75 - 4,0 kW]
2 221 207
137 209 5.3 185 110 63 1,8
None 0180-
0240
[4,0- 5,5kW]
0140 –
0240
[5,5 - 11 kW] 3 261 246
- 247 6 205 131 80 3,5
None 0300 – 046
0
[7,5 - 11 kW]
0300 – 046
0
[15 - 22 kW] 4 418 - 400 240 160 125 9,2
None 0610 – 090
0
[15 - 22 kW]
0610 – 090
0
[30 - 45 kW] 5 486 - 460 260 222 175 18
None 1100 – 150
0
[30 - 37 kW]
1100 – 150
0
[55 - 75 kW] 6A 614 - 578 320 286 200 32
None 1800 – 202
0
[45 - 55 kW]
1800 – 202
0
[90 - 110 kW] 6B 726 - 680 320 330 225 43
None None 3700 – 450
0
[200 - 250 kW]
8 995 480 482 128
NOTE
Mounting bolts Frame size 2-3: M4 FrameSize 4-5 and 6A: M8
Frame Size 6B: M10 Frame Size 8: M12
Control Terminal, Required Torque All Frame sizes: 0.5 Nm.
Power Terminal, Required Torque
Frame size 2-3: 1 Nm FrameSize 4: 2 Nm
FrameSize 5: 4 Nm Frame Size 6A: 12 Nm Frame
Size 6B: 15 Nm
Cable Gland, IP66 Hole Size & recommended glands
Frame size Hole sizes Gland PG
Size 2 1x22mm & 2x28 mm 1xPG13,5 & 2xPG21
Size 3 1x22mm & 2x28 mm 1xPG13,5 & 2xPG21

Beijer Electronics Frequency Inverter BFI-H3 KI00363B 2019-09
www.beijer.se www.beijer.no www.beijer.dk www.beijerelectronics.de www.beijerelectronics.com www.beijerelektronik.com.tr 5 (29
)
4.3 Physical dimensions IP55
BFI-H3-IP55 Drive
size
A
Height
[mm]
B
[mm]
D [mm]
E
[mm]
F
Depth
[mm]
G
Width
[mm]
H
[mm]
I
[mm]
J
[mm]
Weight
[kg]
3 x 230 V 3 x 400 V
0300 – 0460
[ 7,5-11 kW]
0300 – 0460
[ 15-22 kW] 4 450 428 433 8 252 171 110 8,5 15 12
0610 - 0900
[ 15–22 kW]
0610 – 0900
[ 30–45 kW] 5 540 515 520 8 270 235 175 8,5 15 23
1100 – 1500
[ 30–37 kW]
1100 – 1800
[ 55–90 kW] 6 865 830 840 10 330 330 200 11 22 55
1800 – 2480
[ 45–75 kW]
2020 – 3020
[110–160 kW] 7 1280 1245 1255 10 360 330 200 11 22 89
NOTE
Mounting bolts: Size 4 and 5: M8 Size 6 and 7: M10 (5/16 UNF)
Control Terminal Torque Settings: 0.5 Nm.
Power Terminal Torque Settings: Size 4: 2 Nm Size 5: 4 Nm Size 6 and 7: 20 Nm.
IP55 Drives do not have any predrilled gland holes for cable inlet.
H
G
A
B
D
E
F
Ø
I
Ø
J

Beijer Electronics Frequency Inverter BFI-H3 KI00363B 2019-09
www.beijer.se www.beijer.no www.beijer.dk www.beijerelectronics.de www.beijerelectronics.com www.beijerelektronik.com.tr 6 (29
)
4.4 Fuses, cable dimensions and power loses
380-480V ±10% - 3 Phase Input – 3 Phase Output
Output
Power
[kW]
BFI-H3
model
Nominal Input
Current
Fuse or
MCB
(type B)
Supply
Cable
Size, A1
40°C
Supply
Cable
Size,
E 30°C
Nominal
Output
Current
Motor
Cable
Size,
E 30°C
Max
Motor
Cable
Length
Power
losses
Amps Amps mm2 mm2 Amps mm2 m W
0.75 0022 2,0 6 1.5 1.5 2.2 1.5 100 15
1.5 0041 3,7 6 1.5 1.5 4.1 1.5 100 30
2.2 0058 5,2 10 1.5 1.5 5.8 1.5 100 44
4 0095 8,6 10 1.5 1,5 9.5 1.5 100 80
5.5 0140 12,4 16 2,5 2,5 14 1.5 100 110
7.5 0180 14 25 4 2,5 18 2,5 100 150
11 0240 21,6 25 4 2,5 24 4 100 220
15 0300 27 32 6 4 30 6 100 300
18,5 0390 35,1 50 16 6 39 10 100 370
22 0460 41,4 50 16 6 46 16 100 440
30 0610 48,2 80 35 16 61 16 100 600
37 0720 58 80 35 16 72 16 100 720
45 0900 76 100 70 25 90 35 100 900
55 1100 113 125 70 35 110 35 100 1650
75 1500 153 160 120 50 150 50 100 2250
90 1800 184 200 150 95 180 95 100 2700
110 2020 206 250 185 150 202 150 100 3300
132 2400 245 315 2x150 2x70 240 2*70 100 3900
160 3020 308 400 2x185 2x95 302 2x95 100 4800
200 3700 393 (4% choke) 500 370 100 6000
250 4500 479 (4% choke) 500 450 100 7500
NOTE
Maximum motor cable length stated applies to using a screened motor cable. When using an unscreened cable, maximum
cable length is increased by 50%. Using an output choke, the maximum cable length limited can be increased by 100%
The PWM output switching from any inverter when used with a long motor cable length can cause an increase in the
voltage at the motor terminals, depending on the motor cable length and inductance. The rise time and peak voltage can
affect the service life of the motor. Beijer recommend using an output choke for motor cable lengths of 50m or more to
ensure good motor service life.
All recommended sizes of cable sizes and fuses are recommendations. National laws and
recommendations are to be considered.
Recommended choice of cable sizes and fuses follows DIN VDE 0100 paragraph 430
Appendix, motor cable is copper, way of wiring A1 and E is following SS 424 24 24 edition.
A1 means cable/conductors in some kind of duct in a maximum temperature of 40°C. E
means cable/conductors mounted on a ladder. Calculated at 30°C with 9 or several cables
(correction factor 0,78).

Beijer Electronics Frequency Inverter BFI-H3 KI00363B 2019-09
www.beijer.se www.beijer.no www.beijer.dk www.beijerelectronics.de www.beijerelectronics.com www.beijerelektronik.com.tr 7 (29
)
4.5 Derating Information
Derating of the drive maximum continuous output current capacity is require when:
Operating at ambient temperature in excess of 40°C/104°F (IP55 & IP66) or 50°C / 122°F (IP20).
Operating at Altitude in excess of 1000m/ 3281 ft.
Operation with Effective Switching Frequency higher than the minimum setting.
The following derating factors should be applied when operating drives outside of these conditions.
Derating for Ambient Temperature
Enclosure Type Maximum Temperature
Without Derating Derate by Maximum
Permissible
IP20 50°C / 122°F N/A 50°C / 122°F
IP20 Frame Size5 35°C / 95°F 1.1% per °C (1.8°F) 50°C / 122°F
IP55 40°C / 104°F 1.5% per °C (1.8°F) 50°C / 122°F
IP66 40°C / 104°F 2.5% per °C (1.8°F) 50°C / 122°F
Derating for Altitude
Enclosure Type Maximum Height Above Sea Level
Without Derating
Derate by Maximum
Permissible
IP20, IP55 and IP66 1000m / 3281ft 1% per 100m / 328 ft 4000m / 13123 ft
Derating for Switching frequency
Example of Applying Derating Factors
A 4kW, IP66 drive is to be used at an altitude of 2000 metres above sea level, with 16 kHz switching
frequency and 45°C ambient temperature.
From the table above, we can see that the rated current of the drive is 9.5 Amps at 40°C,
Firstly, apply the switching frequency derating (if any), 16 kHz, 0% derating.
Now, apply the derating for higher ambient temperature, 2.5% per °C above 40°C = 5 x 2.5% = 12.5%
9.5 Amps x 87.5% = 8.3 Amps.
Now apply the derating for altitude above 1000 metres, 1% per 100m above 1000m = 10 x 1% = 10%
8.3 Amps x 90% = 7.5 Amps continuous current available.
If the required motor current exceeds this level, it will be necessary to either:
Reduce the switching frequency selected or use a higher power rated drive and repeat the calculation to
ensure sufficient output current is available.
Enclosure
Type
Switching Frequency
Frame
Size
4
kHz
8
kHz
10
kHz
12
kHz
14
kHz
16
kHz
18
kHz
20
kHz
24
kHz
32
kHz
IP66 2 N/A N/A 0 % 0 % 0 % 0 % 0 % 0 % N/A N/A
3 N/A N/A 0 % 0 % 0 % 6 % N/A N/A N/A N/A
IP55 4 N/A N/A 0 % 0 % 12% 23 % 33% 41% N/A N/A
5 N/A N/A 0 % 0 % 11% 23% 36% 42% N/A N/A
6 0 % 16 % N/A 28% N/A 39 % N/A N/A N/A N/A
7 0 % 12 % N/A N/A N/A N/A N/A N/A N/A N/A
IP20 2 N/A N/A 0 % 14% 23% 32% 37 % 43% N/A N/A
3 N/A N/A 0 % 2% 13% 19% 25 % 35% N/A N/A
4 N/A N/A 0 % 15% 13% 39% 52% 62% N/A N/A
5 N/A N/A 0 % 3% 9% 14% 19 % 24% N/A N/A
6 0 % N/A N/A N/A N/A N/A N/A N/A N/A N/A
8 0 % N/A N/A N/A N/A N/A N/A N/A N/A N/A

Beijer Electronics Frequency Inverter BFI-H3 KI00363B 2019-09
www.beijer.se www.beijer.no www.beijer.dk www.beijerelectronics.de www.beijerelectronics.com www.beijerelektronik.com.tr 8 (29
)
4.6 Overview of power supply, grounding and motor cable
Drive is to be connected with ground/PE by separate grounding wire.
3-phase power supply should be connected to L1, L2 and L3.
Phase sequence of power supply is not important and cable doesn’t have to be a shielded.
400V
230V
690V
400V
S
TAR
DELTA
Motor cable must be a symmetrical shielded cable to fulfil EMC requirements. Example of
cables to be used are RKFK, Ölflex Classic 100 CY, FKKJ-EMC, or similar.
Shield of the motor cable should be connected to ground/earth in both ends. On motor side an
EMC-gland is to be used.
Shield of motor cable is to be connected to ground terminal in the drive itself. For IP20 drives
the shield can instead be clamped to the mounting plate with a clip.
Motor must also be well attached into the mechanical frame of the machinery and have the
same potential as the electrical cabinet. Separate earth connection might be necessary.
Motor cable should avoid to be installed close to telephone-, network- or signal wiring.
Minimum distance is 10 cm.
M ~
U
V
W
L1
L2
L3
Protective grounding of motor is connected to drive
Motor cable should be connected to U, V, W.
Inverter Power supply 3*400 VAC:
- Rated voltage of motor 230/400, Star connection
- Rated voltage of motor 400/660, Delta connection

Beijer Electronics Frequency Inverter BFI-H3 KI00363B 2019-09
www.beijer.se www.beijer.no www.beijer.dk www.beijerelectronics.de www.beijerelectronics.com www.beijerelektronik.com.tr 9 (29
)
4.7 Safe Torque Off, STO
BFI-H3 has two digital inputs for Safe Torque Off. These two inputs must be correct
connected otherwise the Drive will not run andInhibitwill be shown on the display.
If safety is not to be used terminal 12 must be connected to terminal 1 and terminal 13
connected to terminal 7. More about safety inputs can be read in User Manual BFI-H3.
4.8 Overview control inputs/outputs
Picture below shows an overview of control signals and factory set functionality.
Use internal or external 24 VDC.
The CPU board of BFI can be activated even though power supply, 380-480 VAC, is off. This is done by an external 24VDC
suppy to terminal 1 and 0 VDC to terminal 7. This must be a 24 VDC power supply only used for BFI:s and no other units.
2
3
5
6
7
1
DIN1: Startsignal and Reset
DIN2: Analog or Preset speed
DNI3: Analog1 or Analog2
+24 VDC
AIN1: Analog ref 1
+10 VDC
8
9
AOUT1: 0-10 V / 24 VDC
Output frequency 0-10 V
0 VDC
0 V reference
Relay Output 2
Drive Enabled
17
18
10
12
13
AIN2: Analog ref 2
STO+ Safety in +
STO- Safety in -
AOUT2: 0-10 V / 24 VDC
Output current 0-10 V
11
Relay Output 1
Drive Healthy
14
15
16
4
Wires should be
protected
against short
circuits as
shown above

Beijer Electronics Frequency Inverter BFI-H3 KI00363B 2019-09
www.beijer.se www.beijer.no www.beijer.dk www.beijerelectronics.de www.beijerelectronics.com www.beijerelektronik.com.tr 10 (29
)
5 Basic Parameter setting
The basic parameter setting that always is to be checked or modified is listed below:
Para-
meter
Name Default
settng
To be set
Function
P1-
01
Maximum Frequency 50 Hz Max freq.
If P1-10, Motor rated speed, ≠ 0 unit is rpm instead of Hz.
P1-
02
Minimum Frequency 0 Hz Min freq. Set to some few Hz to ensure torque in motor. If P1-10, Motor rated
speed, ≠ 0 unit is rpm instead of Hz.
P1-03
Acceleration Time 5/30,0 sec
Acceleration ramptime from 0 Hz to P1-09 (50 Hz)
P1-04
Deceleration Time 5/30,0 sec
Deceleration ramptime from P1-09 (50 Hz) to 0 Hz
P1-07
Motor Rated Voltage 230/400 V
Put rated voltage of motor from motor nameplate in unit V
P1-08
Motor Rated Current - Put rated current of motor from motor nameplate in unit A
P1-09
Motor Rated Frequency
50 Hz 50 Hz Put rated frequecy of motor from motor nameplate in unit Hz
P1-12
Command Source 0 0 0: Control by digital and/or analog signals
1: Control from Keypad
P1-14
Parameter Access 0 201 Normally only parameters P1-01 to P1-14 are accessable. All other
parameters are accessable with this parameter put to 201.
P2-24
Switching Frequency Drive
depending
Keep as low as possible. Higher value decreas audible noise in
motor but increase losses in drive.
P2-26
Spin Start Enable 1
0: Disabled
1: Enabled. The drive will attempt to determi
ne if the motor is already
rotating, at what speed and direction on start up. The control of the
motor will start from the measuring. A delay of a few seconds will be
observed when starting the drive.
P4-01
V/F Characteristic
Select 0
0: Induction motors that require variable torque, for example fans
1: Induction motors that require constant torque, for example pumps,
conveyors and all heavy loads.
5.1 Digital start in one direction and one Preset or Analog setpoint
Start of drive is done by digital Start signal and set frequency is either a fixed preset speed
or an analog input signal on terminal 6. Analog signal can be either 0-10 V, 10-0 V, 4-
20/20-4 mA. If 4-20 mA signal is used then current should flow into terminal 6 and out
from terminal 7.
Status Action
DIN1
DIN2
P1-13 = 1
0 0 No output from drive
0 1
1 0 Start Forward & Analog
setpoint speed on terminal 6
1 1 Start Forward & PreSpeed 1 in
P2-01
DIN2: Preset speed
2
3
5
6
7
1
DIN1: Startsignal
0 VDC
+24 VDC
AIN1:Analog ref
+10 VDC
4-20
mA
Use internal or external 24 VDC

Beijer Electronics Frequency Inverter BFI-H3 KI00363B 2019-09
www.beijer.se www.beijer.no www.beijer.dk www.beijerelectronics.de www.beijerelectronics.com www.beijerelektronik.com.tr 11 (29
)
Para-
meter
Name Default
settng
To be
set
Function
P1
-
13
Dig
ital I
nputs Function
1
1
Must be put to 1
P2-01
PresetSpeed1 5 Hz Can be set between P1-02(Minimum speed) to P1-01 setting (Maximum speed)
P2-30
Analog Input 1 Format 0
Type of
analog
input
0: 0 to 10 VDC; 3: 0 to 20mA
4: 4 to 20mA. Trip if signal level < 3mA
5: 4 to 20mA,
Ramp to Preset speed 4
if signal level < 3mA
P2-31
Analog Input 1 Scaling 100 %
Defines scaling of analog input 1 at maximum analog input value towards
maximum speed in P1-01.
Output frequency= (Analog input value)/100 x (P
2
-
31
)/100
* P1
-
01 [Hz]
P2-32
Analog Input 1 Offset 0 %
P2-32 defines an offset in % of full range for analog input 1.
A positive offset is deducted from the incoming analog signal and a negative
offset is added.
Example, if P2-30=0–10V and P2-32=10.0%, then 1 volt (10% of 10V) will be
deducted from incoming analog reference prior to it being applied.
5.2 Digital start in two directions and one Preset or Analog setpoint
Start in forward or reverse direction by digital signal and set frequency is either a fixed
preset speed or analog input signal on terminal 6. Analog input is either 0-10 V or 4-20
mA.
If 4-20 mA signal is used the current should go into terminal 6 and out from terminal 7.
For scaling see chapter 5.1.
Para-
meter
Name Default
settng
To be set
Function
P1
-
13
Digital Inputs Function
1
0
0:
Open up I/O cinfiguration in Parameter Group
9
P2
-
01
PresetSpeed1
5 Hz
Can be set between 0 to P
1
-
0
1
setting ( Maximum speed)
P9
-
0
1
En
able I
nput Source
1
0
0: Enable is activated by safety inputs
P9
-
03
Forward Run Input Source
1
1
1: Digital Input 1
P9
-
04
Reverse Run Input Source
0
2
2
: Dig
ital Input 2
P9-10
Speed Source 1 0 0 0: Analog input 1
P9-11
Speed Source 2 0 9 9: Preset speed 1
P9-18
Speed Select Input 1 0 3 3: Digital input 3 activates PresetSpeed1
Status inputs Action
DIN1
DIN2
DIN3
0 0 Any No output from drive
1 0 0 Forward & Analog speed on terminal 6
1 0 1 Forward & PreSpeed 1 in P2-01
0 1 0 Reverse & Analog speed on terminal 6
0 1 1 Reverse & PreSpeed 1 in P2-01
1 1 Any No output from drive
DIN2: Start Reverse
2
3
5
6
7
1
DIN1: Start Forward
0 VDC
+24 VDC
AIN1: Analog ref
+10 VDC
4-20
mA
Use internal or external 24 VDC
4
DIN3: Preset speed1

Beijer Electronics Frequency Inverter BFI-H3 KI00363B 2019-09
www.beijer.se www.beijer.no www.beijer.dk www.beijerelectronics.de www.beijerelectronics.com www.beijerelektronik.com.tr 12 (29
)
5.3 Digital start signal in two directions and 8 fixed Preset speeds
Start in two direction and up to 8 fixed speeds.
If only 4 fixed speeds are to be used, AIN2 terminal 10, can be excluded.
If only 2 fixed speeds are to be used, AIN1 terminal 6, can be excluded.
Table below shows what parameters needs to be set to get 2,4 or 8 fixed speeds.
Para-
meter
Name
Default
settng
To be set
if
2 fixed
speeds
To be set if
4 fixed
speeds
To be set if
8 fixed
speeds
Function
P1
-
12
Command
S
ource
0
0
0=
C
ontrol b
y
digital and
/or
analog signals
P1
-
13
Digital Inputs
F
unc
1
0
Open I/O
-
functionality
in Parameter group 9
P2-01
PresetSpeed 1 5 Hz Select Select Select
Can be set between P1-02 (Minimum speed) to
P1-01 setting (Maximum speed)
P2
-
02
PresetSpeed
2
10 Hz
Select
Select
Select
P2
-
03
Pre
setSpeed
3
25 Hz
Not used
Select
Select
P2
-
04
PresetSpeed
4
5
0
Hz
Select
Select
P2
-
05
Pre
setSpeed
5
0
Not used
Select
P2
-
06
PresetSpeed
6
0
Select
P2
-
07
PresetSpeed
7
0
Select
P2
-
08
PresetSpeed
8
0
Select
P
9
-
01
Enable Input Source
1
0
P
9
-
03
Forward Run Input
1
1
P
9
-
0
4
Reverse Run Input
0
2
P
9
-
10
Speed Source 1
0
9
P
9
-
11
Speed Source 2
1
10
P
9
-
12
Speed Source 3
2
2
11
P
9
-
13
Speed Source 4
2
2
12
P
9
-
14
Speed Source 5
0
0
0
13
P
9
-
15
Speed Source 6
0
0
0
14
P
9
-
16
Speed Sour
ce 7
0
0
0
15
P
9
-
17
Speed Source 8
0
0
0
16
P
9
-
18
Speed
S
elect
In
put0
3
3
P
9
-
19
Spe
ed
S
elect
I
nput 1
2
2
4
P
9
-
20
Speed
S
elect
I
nput 2
0
0
0
5
Status inputs Action
AIN2 AIN1 DIN3
0 0 0 Preset speed 1, P2-01
0 0 1 Preset speed 2, P2-02
0 1 0 Preset speed 3, P2-03
0 1 1 Preset speed 4, P2-04
1 0 0 Preset speed 5, P2-05
1 0 1 Preset speed 6, P2-06
1 1 0 Preset speed 7, P2-07
1 1 1 Preset speed 8, P2-08
DIN2: Start reverse
2
3
4
6
1
DIN1: Start forward
0 VDC
+24 VDC
AIN1: Preset speed
Use internal or external 24 VDC
7
DIN3: Preset speed
AIN2: Preset speed
10

Beijer Electronics Frequency Inverter BFI-H3 KI00363B 2019-09
www.beijer.se www.beijer.no www.beijer.dk www.beijerelectronics.de www.beijerelectronics.com www.beijerelektronik.com.tr 13 (29
)
5.4 Alarm reset
Alarm reset is factory set dedicated terminal 2, DIN1. Drive is reseted by positive edge on
terminal 2. Observe that terminal 2 also can be Start forward and drive might start if Alarm
reset is too long or not turned off. It is possible to dedicate a specific input to just Alarm reset.
5.5 Transistor outputs 24 VDC or analog output, 0-10 V/4-20 mA
Terminal 8 and 11 can be either analog output 0-10 VDC/4-20 mA or transistor output 24
VDC. Outputs do not need an external power supply. Maximum load is 20 mA.
5.6 Relay outputs
Para-
meter
Name Default
setting
Function
P2-11 Analog Output 1
F
unction
8
0: Drive Enabled or running
1: Drive Healthy. Power is applied to the drive and no fault exists
2: At Target Frequency. Output frequency matches the setfrequency
3: Output Frequency > 0 Hz
4: Output Frequency ≥ Limit. Output frequency > P2-16 (AOUT1) or P2-19(AOUT2)
5: Output Current ≥ Limit. Motor current > P2-16 (AOUT1) or P2-19(AOUT2)
6: Output Frequency < Limit. Output frequency > P2-17(AOUT1) or P2-20(AOUT2)
7: Output Current < Limit. Motor current < P2-17(AOUT1) or P2-20(AOUT2)
8: Output Frequency 0-10 V => 0 Hz to setting in P1-01
9: Output Motor Current 0-10 V: 0 to 200% of setting in P1-08
10: Output (Motor) Torque. 0 – 165% of motor rated torque
11: Output (Motor) Power. 0 to 150% of drive rated power
12:
PID Output
. 0
–
100% represents the output of the internal PID controller
P2-13 Analog Output 2
Function 9
P2
-
12
Analog Output 1
0
If outputs is to be transistor outputs these parameters do not need to be configured.
0: 0 to 10 VDC; 1: 10 to 0 VDC; 2: 0 to 20 mA;
3: 2
0 to 0
mA
;
4: 4 to 20mA; 5: 20 to 4 mA
P2-14 Analog Output 2
0
Parameter Default
setting
Function
P2-15: Relay
output 1
function
terminal
15 and
16
1
0: Drive Enabled or running
1 Drive Healthy. Power is applied and no fault exists
2: At Target Frequency. Output frequency= Set frequency
3: Output Frequency > 0.0 Hz
4: Output Frequency ≥ Limit. Output frequency > P2-16
(Relay1) or P2-19 (Relay2)
5: Output Current ≥ Limit. Motor current > P2-16 (Relay1) or
P2-19 (Relay2)
6: Output Torque ≥ Limit. Motor torque current > P2-16
(Relay1) or P2-19 (Relay2)
7: Analog input 2 > Limit. Analog input 2 > P2-16 (Relay1) or
P2-19(Relay2)
8: DOL1 Pump staging – DOL Cascade.
9: Fire Mode Active
10: Maintenance Due
11: Drive available- Ready to run
12: Drive Tripped and in a fault condition
13: Sate Torque off (STO) status
14: PID Error ≥ Limit. The PID Error ≥ Programmed limit
15:
Low and High Current Warning
P2-18: Relay
output 2
function
terminal 18
0
Relay Output 2
Default Drive
Enabled
17
18
Relay Output 1
Default Drive
Healthy
14
15
16
8
9
AOUT1: 0-10 V / 4-20 mA / 24 VDC Default Output Frequency 0-10 V
0 V reference
AOUT2: 0-10 V / 4-20 mA / 24 VDC Default Output Motor Current 0-10 V 11

Beijer Electronics Frequency Inverter BFI-H3 KI00363B 2019-09
www.beijer.se www.beijer.no www.beijer.dk www.beijerelectronics.de www.beijerelectronics.com www.beijerelektronik.com.tr 14 (29
)
5.7 Fieldbus control settings
The drive can be controlled by fieldbus or Ethernet. Following settings must be done:
P1-12=4, Start/stop/frequency setpoint command by bus
P1-14=201, make access to parameters in group 5 mentioned below
Terminal 2 must be connected to 24 V and safety inputs(STO+/STO-) correctly connected.
Specific details Station-
number
Fieldbus
ramp action
P5-07
Communication
Speed/Baud rate Timeout [sec] P5-
05
Loss action
P5-06
ProfiNet GSDML-V2.25-HMS-
ABCC-PRT2P-
201110111.xml
Set by master 0: Ramp time
by parameter
1: Ramp time
sent by serial,
fieldbus or
Ethernet
Set by master
Drive behaviour if a
communication
command is not
received within time
specified in this
parameter. Type of
reaction decided in
P5-06.
0: Trip
1: Ramp to
stop and
trip
2: Ramp to
stop and no
trip
3: Preset
speed 8
(P2-08)
Profibus DP HMSB1811.gsd P5-01
EtherNet/IP
Set manually by
PC-program
Modbus TCP
CC-Link Ver1, Remote device
station, Exclusive
station 2
P5-01 P5-03:
9,6= 156 kbs
19,2= 625 kbs
38,4= 2,5 Mbs
57,6= 5 Mbs
115= 10 Mbs
Ethercat Contact Beijer support
for latest version
Set by master Set by master
DeviceNet
005A000000620200.eds
P5
-
01
P5
-
03
5.8 Fieldbus communication protocol
Cyclic data for all bus types consist of four 16-bit word input and output. Word 1 and 2 has
the following meaning:
Word Data to drive Data from drive
1
Bit 0 0: Stop
1: Start
Bit 0 0: Stop
1: Startsignal on
Bit 1 0: Deceleration time in P1-04
1: Deceleration time in P2
-
25
Bit 1 0: Drive Healthy
1: Drive tripped
Bit 2 0: No function
1: Alarm reset
Bit 2 0: Auto Mode (IP 20 drives)
1: Hand mode (IP2
0 drives)
Bit 3 0: No function
1: Coasting stop
Bit 3 0: Safe Torque inputs activated
1: Safe Torque inputs deactivated
Bit 4-
15
Not used Bit 4 0: Maintenance not required
1: Maintenance required
Bit 5-7
Not used
Bit 8-15
Alarmcode
2
Set frequ
ency [0,1 Hz]
Actual output freq
uency [0,1 Hz]

Beijer Electronics Frequency Inverter BFI-H3 KI00363B 2019-09
www.beijer.se www.beijer.no www.beijer.dk www.beijerelectronics.de www.beijerelectronics.com www.beijerelektronik.com.tr 15 (29
)
Word 3 and 4 of output/input data can be individually configured as described in table below.
Para-
meter
Name Default
settng
Function Explanation
P5-12
Fieldbus
Module
PDO3
0 What to be
read in word
3
0 : Motor Current [0,1 A], 105 = 10,5 A
1 : Output Power [0,01 kW], 405 = 4.05kW
2 : Digital Input Status. Bit 0 =Digital input 1 status, Bit 1= Digital input 2 status etc
3 : Analog Input 2. Signal Level 0 to 1000 = 0 to 100.0%
4 : Drive Heat-sink Temperature in BFI [°C]
5 : User Register 1. Variable in PLC program or group 9 parameters
6 : User Register 2. Variable in PLC program or group 9 parameters
7 : P0
-
80 Value
P5-08
Fieldbus
Module
PDO4
1 What to be
read in word 4
P5-14
Fieldbus
Module
PDI3
0 What to be
written in word 3
0 : Not used - No function
1 : User PID Reference - 0 to 1000 = 0% to 100.0%
2 : User Register 3
–
Variable in
PLC program or group 9 parameters
P5-13
Fieldbus
Module
PDI4
0 What to be
written in word 4
0: User ramp time – In second with two decimal places.
1: User Register 4 – Variable in PLC program or group 9 parameters
Acyclic data is also available for all Ethernet and field buses except for CC-link.
5.9 PTC-thermistor
A motor thermistor or thermistor contact can be connected to analog input 2, terminal 10.
Set P1-13 to 5 or 10, make sure functionality for other inputs follows your specification. If not,
adjust functionality manually in parameter group 9. Contact Beijer Electronics for further
assistance.
Put P2-33=2, “Ptc-th".
Inverter will trip with open contact or a resistance above 2.5 kOhm. Input is not ATEX approved.
The cable for PTC-wires must be shielded and well separated from the motor cable. Otherwise an
external PTC-relay might be needed due to disturbances.

Beijer Electronics Frequency Inverter BFI-H3 KI00363B 2019-09
www.beijer.se www.beijer.no www.beijer.dk www.beijerelectronics.de www.beijerelectronics.com www.beijerelektronik.com.tr 16 (29
)
5.10 Control from a Modbus RTU master
A Modbus RTU network with BFI-E3, BFI-H3 or BFI-P2 is connected as below:
Settings in BFI-H3 are speed setting is 115 200 bit/sec, 8 data bits, 1 stop bit, No Parity.
Hardware Function Comment
CAB 114 Shielded cable with one RJ45 and 3 wires marked
SDA, SDB and SG for screwte
rminals.
Cable length 3 m. Modbus RTU- pin7 and Modbus
RTU
+
p
in8
i
n
BFI.
CAB 113 Shielded cable with one RJ45 for BFI and one 9-pole
D
-
sub
for X2 pan
els
.
Cable legth 3 m. Built-in 120 ohm resistor in D-sub
b
etween
pin
7 and
pin
8
.
OPT-2-J45SP-BFI T-Connection of 2 serial cables into one drive. RJ45 male to BFI and 2 female RJ45 for network
connection
OPT
-
2
-
RJTRM
-
BFI
RJ45
with a
110 ohm resistor
.
To be put in the last BFI
-
splitter
.
Para-
meter
Name Default
settng
To be set
Function
P1
-
12
Command Source
0
4
4
=
C
ontrol b
y
Modbus RTU
.
P1
-
14
Parameter Access
0
201
Get access
to
all
parameter
.
P5
-
01
Drive Fieldbus Adress
0
Stationnumber 0
-
63. First Drive should be stationnumber 1
P5
-
03
Baud Rate
115
9,6, 19,2, 38
,4,
57,6 or 115= kbs
P5-04
Data Format 0 0 0 or "n-1”= No Parity, 1 stop bit 1 or “n-2”= No parity, 2 stop bits
2
or
“0
-
1”
: Odd parity, 1 stop bit
3
or
“E
-
1”
=
Even parity, 1 stop bit
P5-05
Comm Loss Timeout 1,0 Drive behaviour if a communication command is not received within time
specified in this parameter.
Type of r
eaction decided in P5
-
06.
P5-06
Comm Loss Action 0 0: Trip and coast to stop 1: Ramp to stop and trip;
2: Ramp to stop and no trip
3: Preset speed 8 (P2
-
08)
P5-07
Fieldbus Ramp Ctrl 0 Decide which ramp for accelearation and deceleration to be used. 0: From
parameters
1:
From Modbus
RTU
2
1
DI1: Startsignal
+24 VDC
DI1 must always be closed to start
Modbus master RTU
SG
SDB
BFI
RDB
SDA
RDA
Put termination switch in 100 ohm
8
7
3
1 8
BFI
IP20
CAB 113
Patchcable
Cat 6
Modbus master
X2 panel
CAB 114
RS485 + Pin1
OPT-2-
RJTRM-
BFI
OPT-2-
J45SP
-
BFI
RS485 – Pin6
GND Pin5
Modbus master
Nexto Express
D+
D-
GND
BFI
IP
66

Beijer Electronics Frequency Inverter BFI-H3 KI00363B 2019-09
www.beijer.se www.beijer.no www.beijer.dk www.beijerelectronics.de www.beijerelectronics.com www.beijerelektronik.com.tr 17 (29
)
5.11 Vector control
BFI-H3 is delivered with vector control for a standard induction motor activated. Standard
values for a motor with same power rating as the drive is being used.
Following parameters must be set properly:
- P1-14: Parameter access code, set to 201
- P1-07: Motor Rated Voltage, 230 or 400 V
- P1-08: Motor Rated Current, motor rated current
- P1-09: Motor Rated Frequency, motor rated frequency
- P4-05: Motor Power Factor, normally called cos φ of the motor
- P4-01: 0: Standard induction motor with variable torque demand like fans
1: Standard induction motor with constant torque demand like pumps, conveyors and
so on.
If motor current is too high, motor is not running smooth or does not stop properly the standard
values are incorrect.
A new auto tuning must be performed. The auto tuning is done in following way:
- Set the parameters above correctly
- Make sure Enable and Safety inputs are activated, jumpers between terminal 1 to 2, 1 to 12 and 9
to 13.
- Set P4-02=1 => Auto tuning is started. Autotuning can only be started on the keypad.
- Wait until auto tuning is done => Indicated by “Autotuning Done” on the display.
Test run the motor again. Motor should now behaviour correctly and motor current level be on a
reasonable level.
The result of auto tuning can be read in parameter group 7.

Beijer Electronics Frequency Inverter BFI-H3 KI00363B 2019-09
www.beijer.se www.beijer.no www.beijer.dk www.beijerelectronics.de www.beijerelectronics.com www.beijerelektronik.com.tr 18 (29
)
5.12 PID-control
Related parameters to be set when using PID-control.
Para-
meter
Name Default
settng
To be
set
Function
P1
-
01
Maximum frequency
50 Hz
Maximum output frequency from PID-controller
P
1
-
12
Command source
0
3
3
: PI
D
-
contro
l
mode
by digital startsignal
P1
-
14
Parameter Access
0
201
Get access to parameter group 5
P1
-
13
Digital Inputs Function
1
0
Get access to parameter group 9
Do only change if
PID-control and
running with fixed
speed is to be
selectable on digital
input 1
P9
-
01
Enable Input source
1
1
Enable on Digital Input1, terminal 2
P9
-
03
Forward Run Input Source
1
1
Start signal on Digital Input1, terminal 2
P9
-
07
Reset Input Source
1
1
Alarm Reset on Digital
Inpu
t1, terminal 2
P9
-
10
Speed Source 1
0
4
Digi
tal Input 2 = 0 => PID
-
control
P9
-
11
Speed Source 2
1
9
Digital Input 2 = 1 => Preset speed 1 in P2
-
01
P9
-
18
Speed Select Input 1
3
2
Status on Digital Input 2 decides speed
P9
-
19
Speed Select Input 2
2
0
Turned off
P2
-
01
Preset Speed1
50 Hz
Outpu
t frequency if DI2=24V (PID
-
control disabled)
Status Action
DIN1
DIN2
P1-12=3
0 any No output from drive
1 0 Run with PID-control
1 1 Run with Preset speed
in P2-01
10
2
3
5
6
7
1
DIN1: Start signal
DIN2: PID/Preset Speed 1
AIN2: PID-feedback
+24 VDC
AIN1: PID-reference
+10 VDC
0 VDC
0
-
10V /
4
-
20mA
Sensor
Use internal or external 24 VDC

Beijer Electronics Frequency Inverter BFI-H3 KI00363B 2019-09
www.beijer.se www.beijer.no www.beijer.dk www.beijerelectronics.de www.beijerelectronics.com www.beijerelektronik.com.tr 19 (29
)
P2-30
Analog Input 1, AI1
0
0: 0-10 V 3: 0-20 mA
4: t 4-20 mA, trip if signal is below 3 mA
5: r 4-20 mA, ramp to Preset Speed 4, Pr2-04, if signal is below 3 mA.
P2-33
Analog Input 2, AI2
P3-01
PID Proportional Gain 1,0 (Setpoint value–Feedback value) of PID controller is multiplied by P3-01 to
produce
o
utput from
PID controller.
Too high value can cause instability
.
P3-02
PID Integral Time 1,0
Accumulated error in the PID control between (Setpoint value–Feedback value)
to
influence the output from PID controller. P3-02 is time constant. Larger values
provide a more damped response. Lower values result is a faster system response
but may result in instability. 0= Turned off
P3-03
PID Differential Time 0 0
The
Differential time constant references the rate of change of the feedback signal
over time and works to slow the rate of change of the PID controller, particularly
as it approached the set-point. Setting a shorter time will decrease overshoot but
slow
down
response and may lead to instability.
0= Turned off.
P3-04
PID Operating Mode 0 0 : Direct Operation. Increase in motor speed should increase feedback signal
1 : Inverse Operation.
I
ncrease in motor speed should decrease feedback signal
P3-05
PID Digital Reference
source
0 0 : PID-reference in P3-06
1 : Analog reference on terminal 6
P3-06
PID Digital Reference 0,0 % PID–reference: 0-100 % of PID-feedback signal if P3-06=0
P3
-
07
PID Output Up
p
er
Limit
100 %
Maximum output frequency in % of P1-01
P3
-
08
PID Output Low Limit
0 %
Minimum output frequency in % of P1-01
P
3
-
10
PID Feedback Source
0
0
0 : Analog Input 2 (Terminal 10)
P3-11
PID Error to Enable Ramp 0 %
0: Internal ramps are always used.
0,1-100: When PID-error is less than setting internal ramps are not used and PID–
control
l
er ramps output frequency.
D
rive
can
react quickly to small errors.
Extra special PID functions
P3-12
Feedback Display Scaling 0 Scaling factor of displayed PID feedback. If analog input is 0–10 V(=0-100%)
and is equal to 0
-
10 bar pressure setting is 0,1.
P3
-
14
Standby Activation Speed
0 Hz
PID Sleep mode parameters.
P3-14 defines output frequency at which the drive will enter
standby mode (stop).
Drive enters standby mode if motor speed remains below level in P3-14 for time
period in P2
-
27.
D
isplay will show
Standby
. Function
disabled if P2
-
27=0.
P2-27
Standby Mode Enable 20 sec
P3-13
Feedback Wake Up Level 0 % PID Wake up level. When PID error > P3-13 drive will return to normal
operat
ion.
P3
-
15
2nd PID Digital Reference
0 %
Second PID reference activated by a digital signal.
P3-16
Pump Prime Time 0 sec
≠ 0: Burst pipe protection function enabled.
If PID feedback, when starting motor, is not > P3-17 within time P3-16 the drive
will trip with "Pr
-
Lo" (pressure low trip
)
.
P3
-
17
Burst Pipe Threshold
0 %
% of PID feedback signal. See P3
-
16.
P3-19
Burst Pipe Detection Trip
Delay
0 sec Delay/filtering false trip due to overshoot or undershoot of sensor signal. For
instance pressure shocks due to valves going on and off.
P3-18
PID Reset Control 0
0: PID loop will continue running as long as P gain (P3-01) ≠ 0.
1: PID loop will only run when drive is enabled. If drive is not running, PID
output will reset to 0 (Including integral result)
.
P
2
-
07
Boost function at start
0 Hz
Drive can be started with speed in P2-07 without PID active. When time from
start in P6-11 has elapsed the drive enters automaticall PID-control.
P
6
-
1
1
0
sec
If PID-control is to be performed by serial, Fieldbus or Ethernet, contact Beijer Electronics.

Beijer Electronics Frequency Inverter BFI-H3 KI00363B 2019-09
www.beijer.se www.beijer.no www.beijer.dk www.beijerelectronics.de www.beijerelectronics.com www.beijerelektronik.com.tr 20 (29
)
5.13 BFI-Smartstick
Communication between BFI Drive and PC-software BFI-Tools or app BFI-Tools Mobile is done
by Bluetooth through BFI-Smartstick. Bluetooth is not built into BFI but in BFI-Smartstick, see
picture below. BFI-Smartstick is connected to BFI through it’s RJ45 connector. BFI-Smartstick also
has a memory for parameter settings that can be read or written by it’s buttons.
Chose BFI-Smartstick in Communication Settings. Scan Devices and when BFI-Smartstick is
found, connect.
P-14 must be set to 201 to access all parameters in the drive.
Cable CAB115 can also be used, USB connection to PC and RJ45 to BFI. Choose ”Wired Serial
Interface(RS485/RS232)” in picture above.
Table of contents
Other BeiJer DC Drive manuals
Popular DC Drive manuals by other brands
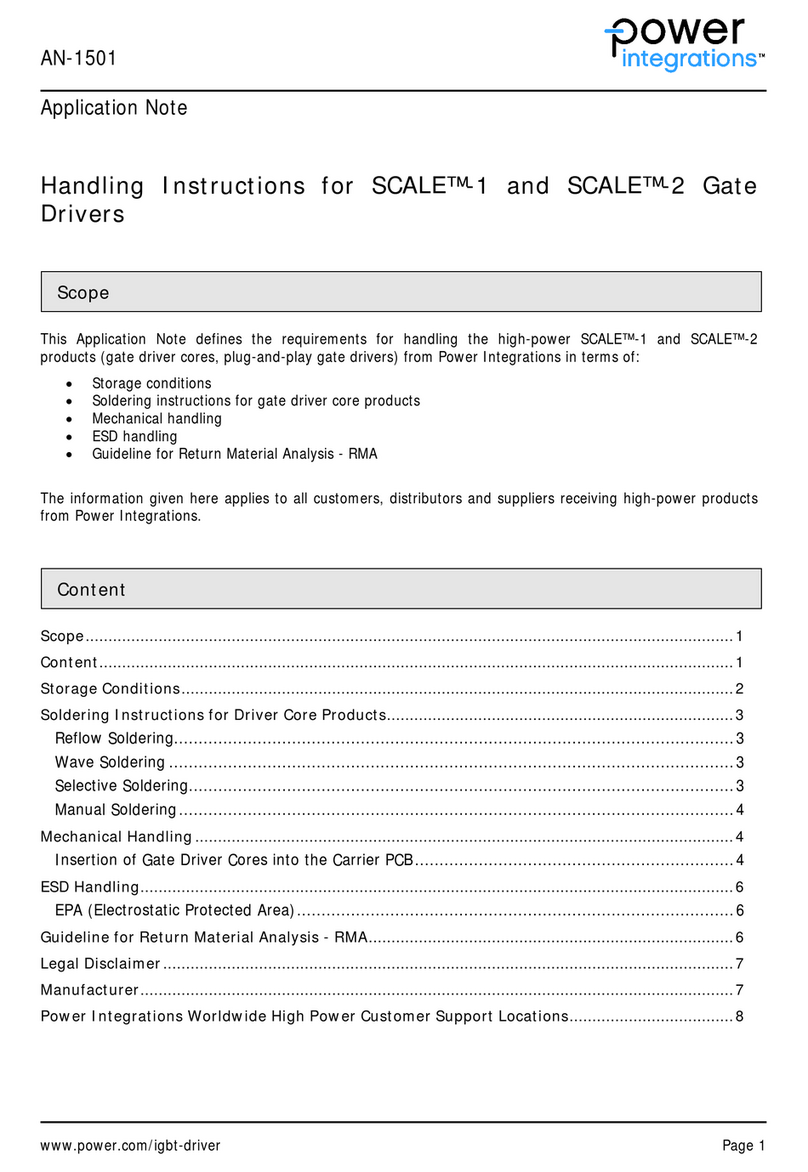
Power integrations
Power integrations SCALE-1 Handling instructions
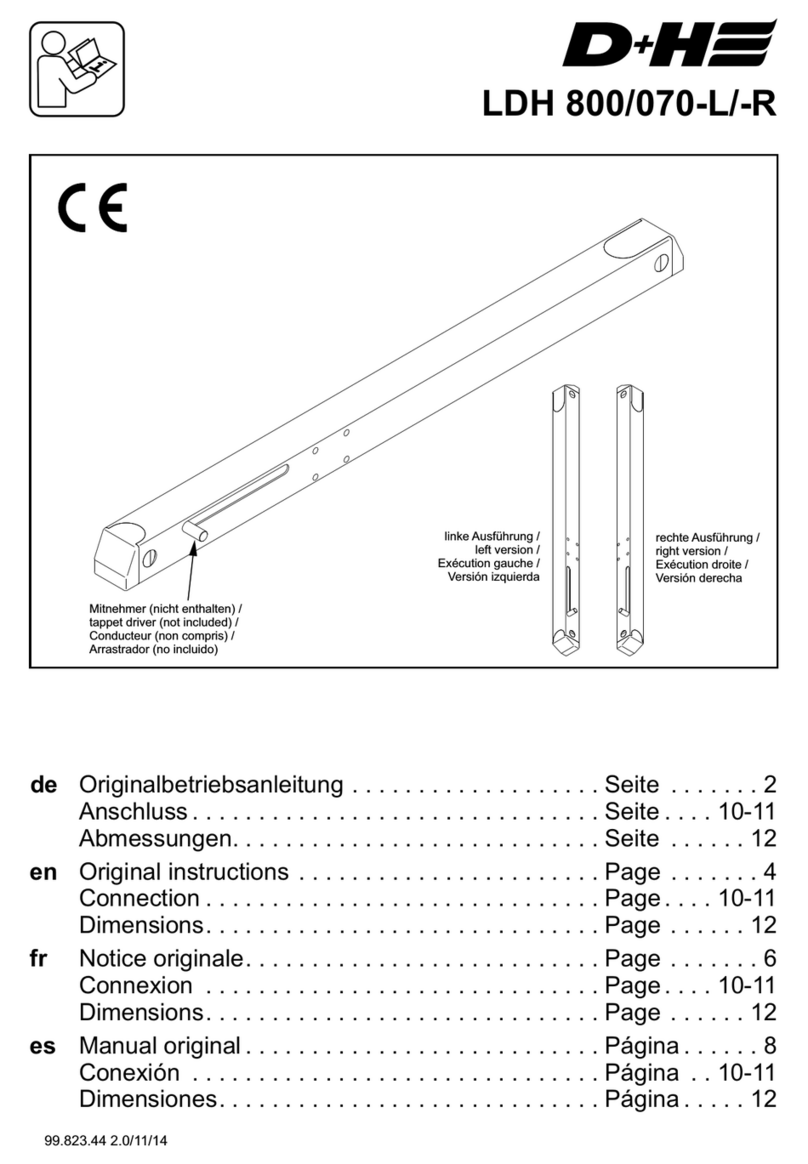
D+H
D+H LDH 800/070-L: LDH 800/070-R Original instructions
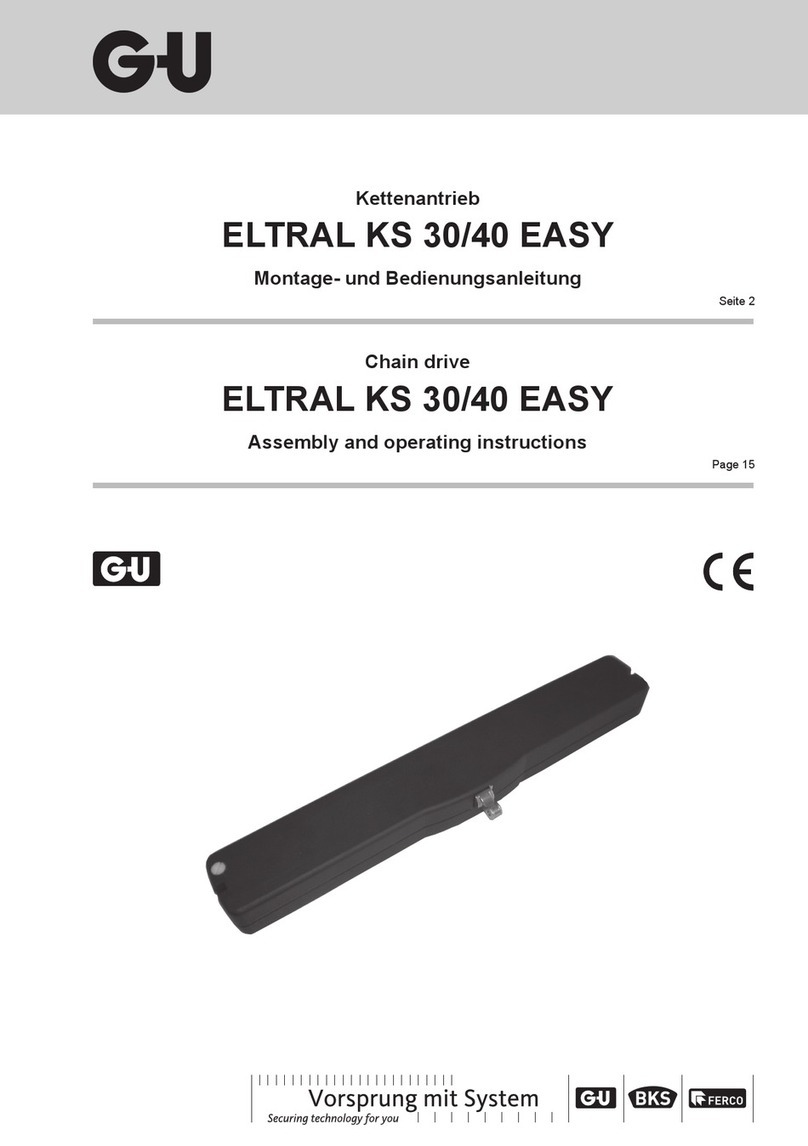
GU
GU ELTRAL KS 30 EASY Assembly and operating instructions
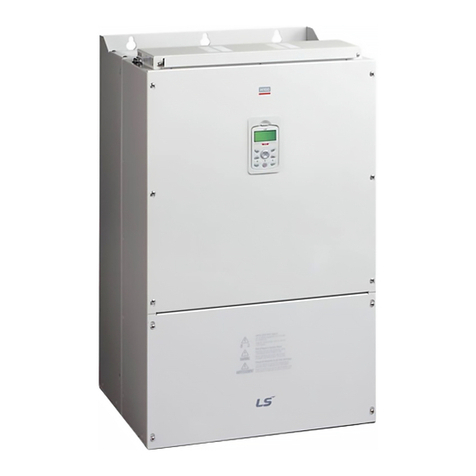
LSIS
LSIS LSLV-H100 user manual
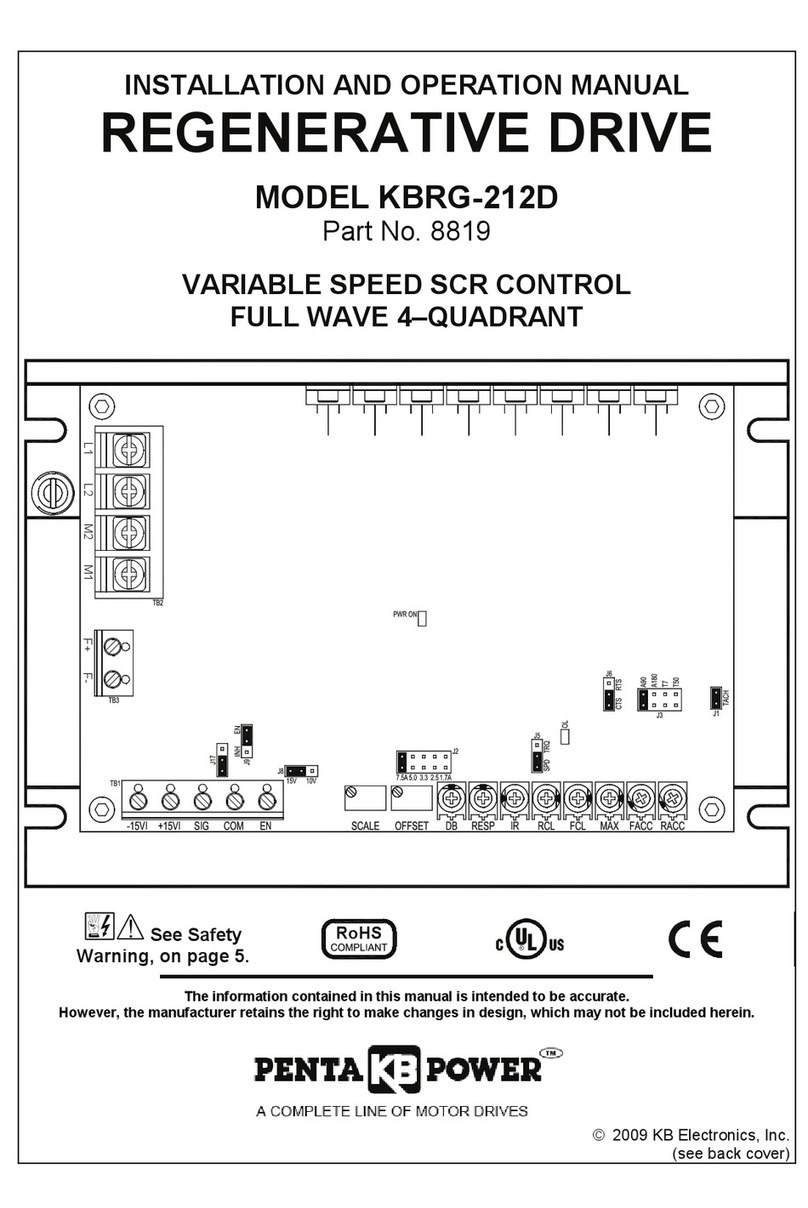
KB Electronics
KB Electronics Penta Power KBRG-212D Installation and operation manual

ABB
ABB ACS 800 Series Hardware manual