BERGHOF EC1000 User manual

USER MANUAL 1.7
EC1000
Ethernet-Controller

Copyright © Berghof Automation GmbH
Reproduction and duplication of this document and
2
ft he
2
tion and communication of its content is
prohibited, unless with our express permission. All rights reserved. Damages will be payable in case of in-
fringement.
Disclaimer
The content of this publication was checked for compliance with the hardware and software described. How-
ever, discrepancies may arise, therefore no liability is assumed regarding complete compliance. The infor-
mation in this document will be checked regularly and all necessary corrections will be included in subse-
quent editions. Suggestions for improvements are always welcome.
Subject to technical changes.
Trademarks
CANtrol®and CANtrol®- dialog are registered trademarks of Berghof Automation GmbH
Microsoft®, Windows®and the Windows®Logo are registered trademarks of Microsoft Corporation in
the USA and other countries.
EtherCAT®is a registered trademark and patented technology, licensed from Beckhoff Automation
GmbH, Germany.
CiA®and CANopen®are registered community trademarks of CAN in Automation e.V.
All rights reserved by the individual copyright holders.
General Information on this Manual
This equipment manual contains product-specific information valid at the time of publication.
This equipment manual is only complete in conjunction with the product-related hardware and software user
manuals required for the individual application.
You can reach us at:
Berghof Automation GmbH
Harretstr. 1
72800 Eningen
Germany
T +49.7121.894-0
F +49.7121.894-100
e-mail: [email protected]
www.berghof.com
Berghof Automation GmbH works in accordance with DIN EN ISO 9001:2000.
Content
Completeness

USER MANUAL 1.7 | EC1000
Berghof Automation GmbH | Harretstrasse 1 | 72800 Eningen | www.berghof.com
EC1000_HB_en_2D1652008ZD00.docx
3
Update
Version
Date
Subject
1.01
25.09.2012
First Version
1.1
31.10.2012
Update of chapter ‘Product description, Block diagram’
1.2
09.11.2012
Update 3ft he trademarks
1.3
06.02.2013
Update of chapter ‘Annex, Nameplate’ and ‘Annex, Addresses’
Transition into new CD
Update of the title page
Update of chapter ‘Product description, Module view and pin assignment’
Update of chapter ‘Product description, Technical data’ and ‘Product
description, Identification’
1.4
20.05.2014
New corporate name ‘Berghof Automation GmbH’
UL certification
1.5
19.10.2015
Update of chapter ‘General Information, Working on the controller module’
Update of chapter ‘Annex, Nameplate’
1.6
01.02.2017
Update of chapter ‘General Information, Conformity Declaration’
Update of chapter ‘Product description, Technical data’
Update of chapter ‘Product description, Module view and pin assignment’
Update of chapter ‘Function Selection, Indicators, Diagnostics, Status
Indicators’
Update of chapter ‘Annex, Nameplate’
1.7
25.05.2018
New device 204900002
New device 204900102
Update of chapter ‘General Information, Conformity Declaration’
Update of chapter ‘Product description, Overview, Accessoires’
Update of chapter ‘Product description, Technical data’
Update of chapter ‘Product description, ’Mounting and connecting, Mounting’
Update of chapter ‘Controller operation, ’Real-Time Clock with Backup Bat-
tery’
Update of chapter ‘Annex, Bibliography / Standards’

USER MANUAL 1.7 | EC1000
Berghof Automation GmbH | Harretstrasse 1 | 72800 Eningen | www.berghof.com
EC1000_HB_en_2D1652008ZD00.docx
4
Blank page

USER MANUAL 1.7 | EC1000
Berghof Automation GmbH | Harretstrasse 1 | 72800 Eningen | www.berghof.com
EC1000_HB_en_2D1652008ZD00.docx
5
Contents
1. GENERAL INFORMATION .................................................................................................................7
1.1. About This Manual.............................................................................................................................7
1.2. Hazard Categories and Terminology ................................................................................................8
1.3. Conformity Declaration......................................................................................................................8
1.4. Qualified Personnel............................................................................................................................9
1.5. Due Diligence......................................................................................................................................9
1.5.1. Working on the controller module.........................................................................................................9
1.6. Use as Prescribed............................................................................................................................10
2. PRODUCT DESCRIPTION EC1000..................................................................................................11
2.1. Overview ...........................................................................................................................................11
2.2. Technical data...................................................................................................................................13
2.3. Block diagram...................................................................................................................................15
2.4. Identification.....................................................................................................................................16
2.5. Module view and pin assignment ...................................................................................................16
2.6. Mounting and connecting................................................................................................................17
2.6.1. Mounting ............................................................................................................................................17
2.6.2. Connecting.........................................................................................................................................18
2.6.3. Earth...................................................................................................................................................19
2.7. Pin assignment.................................................................................................................................20
2.7.1. 10/100 Base-T network connection (Ethernet)...................................................................................20
2.7.2. USB....................................................................................................................................................20
2.7.3. CAN bus and serial interface..............................................................................................................22
2.7.4. EtherCAT............................................................................................................................................23
2.7.5. SD Card .............................................................................................................................................24
3. CONTROLLER OPERATION............................................................................................................25
3.1. Commissioning ................................................................................................................................25
3.2. Function Selection, Indicators, Diagnostics..................................................................................25
3.2.1. Status Indicators.................................................................................................................................25
3.3. Real-Time Clock with Backup Battery............................................................................................27
4. ANNEX...............................................................................................................................................29
4.1. Environmental Protection................................................................................................................29
4.1.1. Emission.............................................................................................................................................29
4.1.2. Disposal .............................................................................................................................................29
4.2. Maintenance/Upkeep........................................................................................................................29
4.3. Repairs/Service ................................................................................................................................29
4.3.1. Warranty.............................................................................................................................................29
4.4. Nameplate.........................................................................................................................................30
Nameplate descriptions (example).....................................................................................................30

USER MANUAL 1.7 | EC1000
Berghof Automation GmbH | Harretstrasse 1 | 72800 Eningen | www.berghof.com
EC1000_HB_en_2D1652008ZD00.docx
6
4.5. Addresses and Bibliography / Standards ......................................................................................31
4.5.1. Addresses ..........................................................................................................................................31
4.5.2. Bibliography / Standards....................................................................................................................32

USER MANUAL 1.7 | EC1000
Berghof Automation GmbH | Harretstrasse 1 | 72800 Eningen | www.berghof.com
2VF100185FE05.docx | EC1000_HB_en_2D1652008ZD00.docx
7
1. General Information
Documentation
This equipment manual is intended for qualified personnel and contains information regarding mounting,
installation, commissioning and maintenance. The information contained in this manual is subject to change
without prior notice.
1.1. About This Manual
This equipment manual is an integral part of the product. Make sure the equipment manual is always availa-
ble near the product’s point-of-employment. The manual contains information about the following topics:
Areas of application;
Safety;
Mechanical construction;
Electrical construction;
Connections;
Commissioning;
Care and maintenance;
Decommissioning;
Disposal.

USER MANUAL 1.7 | EC1000
Berghof Automation GmbH | Harretstrasse 1 | 72800 Eningen | www.berghof.com
EC1000_HB_en_2D1652008ZD00.docx | 2VF100185FE05.docx
8
1.2. Hazard Categories and Terminology
The indications described below are used in connection with safety instructions you will need to observe for
your own personal safety and the avoidance of damage to property.
The indications have the following meaning:
DANGER
Immediate danger
Failure to observe the information indicated by this warning will result in death,
serious injury or extensive property damage.
WARNING
Potential danger
Failure to observe the information indicated by this warning may result in
death, serious injury or extensive property damage.
CAUTION
Danger
Failure to observe the information indicated by this warning may result in injury
or property damage.
NOTICE
No hazard
Information indicated in this manner provides additional notes concerning the
product.
1.3. Conformity Declaration
Both the standard version of the controller module and the extension modules mentioned below comply with
and make allowance for the following directives and standards:
EMC Directive 2014/30/EU
RoHS Directive 2011/65/EU
DIN EN 61131-2: Programmable controllers
Part 2: Equipment requirements and tests
EN 50581: Technical documentation for the assessment of electrical and electronic products with
respect to the restriction of hazardous substances
UL 508: Industrial Control Equipment
17 th edition / 1999-01-28

USER MANUAL 1.7 | EC1000
Berghof Automation GmbH | Harretstrasse 1 | 72800 Eningen | www.berghof.com
2VF100185FE05.docx | EC1000_HB_en_2D1652008ZD00.docx
9
1.4. Qualified Personnel
Only qualified personnel may install, operate and maintain the controller module.
Within the context of this documentation and the safety information it contains, qualified personnel consti-
tutes trained specialists who have the authority to mount, install, commission, ground and identify equip-
ment, systems and power circuits in accordance with the standards of safety technology, and who are familiar
with the safety concepts of automation technology.
1.5. Due Diligence
The operator, or the processor (OEM) must ensure that …
the controller module is only used for the purpose for which it was intended;
the controller module is only operated in impeccable full working order;
the user manual is always available in full and in a legible condition;
only specialists with sufficient qualification and authorisation mount, install, commission and main-
tain the controller module;
these specialists are regularly instructed in all relevant questions of occupational health and safety and
environmental protection and that they also know the contents of the user manual and especially of
the safety notes therein;
the device markings, identifications, safety and warning notes attached to the controller module are
not removed and are always kept in a legible state;
the national and international regulations for controlling machines and systems which apply at the rel-
evant usage site are observed;
the relevant information about the controller module and its application and operation is always avail-
able to the users
1.5.1. Working on the controller module
Before carrying out work on the controller module you must always:
first ensure that the controller and the system are in a secure state;
only then switch off the controller and the system and
only now disconnect the controller module from the system.
CAUTION
Live parts!
Before starting any work on the device, disconnect all inputs, including any
connected peripherals.
Inappropriate handling (installation and movement), while the device is pow-
ered on, may result in damage and / or data loss.

USER MANUAL 1.7 | EC1000
Berghof Automation GmbH | Harretstrasse 1 | 72800 Eningen | www.berghof.com
EC1000_HB_en_2D1652008ZD00.docx | 2VF100185FE05.docx
10
1.6. Use as Prescribed
This is a modular automation system based on the CANbus, intended for industrial control applications with-
in the medium to high performance range.
The automation system is designed for use within Overvoltage Category I (IEC 364-4-443) for the controlling
and regulating of machinery and industrial processes in low-voltage installations in which the rated supply
voltage does not exceed 1,000 VAC (50/60 Hz) or 1,500 VDC.
The automation system is further usable in a pollution degree 2 environment or similar.
The modules shall be supplied by a power source with safe separation protected by an UL 248 fuse, rated
max. 100/V where V is the DC supply voltage with maximum value of 28.8 VDC, such that the limited voltage
/ limited current requirements of UL 508 are met.
Wire connection specifications: Use AWG wire size 16-22 or equivalent.
Qualified project planning and design, proper transport, storage, installation, use and careful maintenance
are essential to the flawless and safe operation of the automation system.
The automation system may only be used within the scope of the data and applications specified in the pre-
sent documentation and associated user manuals.
The automation system is to be used only as follows:
as prescribed
in technically flawless condition
without arbitrary or unauthorized changes and
exclusively by qualified users
The regulations of the German professional and trade associations, the German technical supervisory board
(TÜV), the VDE (Association of German electricians) or other corresponding national bodies are to be ob-
served.
Safety-oriented (fail-safe) systems
Particular measures are required in connection with the use of SPC in safety-oriented systems.
If an SPC is to be used in a safety-oriented system, the user ought to seek the full advice of the SPC manufac-
turer in addition to observing any standards or guidelines on safety installations which may be available.
WARNING
As with any electronic control system, the failure of particular compo-
nents may result in uncontrolled and/or unpredictable operation.
All types of failure and the associated fuse systems are to be taken into ac-
count at system level. The advice of the SPC manufacturer should be sought if
necessary.

USER MANUAL 1.7 | EC1000
Berghof Automation GmbH | Harretstrasse 1 | 72800 Eningen | www.berghof.com
2VF100179FE06.docx | EC1000_HB_en_2D1652008ZD00.docx
11
2. Product description EC1000
2.1. Overview
The EC1000 is a CODESYS PLC controller with a broad range of data interfaces.
In compliance with IEC 61131-3 the module can be programmed either with version 2.3 or 3.x.
Installation
The EC1000 is designed for installation in switching cabinets on a DIN mounting rail in a rough industrial
environment. The fanless design and the flash memory make the cost and effort for maintenance minimal.
Ethernet
A 10/100 Mbit/s Ethernet interface is available. Thanks to the TCP/IP and UDP/IP protocols it is possible to
link it very variably to visualisation software, to higher order control units or to the IT infrastructure.
EtherCAT interface
An EtherCAT E-bus interface with a lateral 10-pin connection is available.
USB
The USB host interface provides a widely-used peripheral interface. For example, it can be used to carry out
an application update or data migration simply via a USB stick. Please contact our Technical Support if no
driver support is available for a specific USB device.
CAN Interfaces
The EC1000 possesses 1 standard CAN interface which can be used up to 1 Mbit/s.
Serial Interfaces
The RS232 can also be used as a programming interface.
Realtime clock
An accumulator battery-buffered, maintenance-free realtime clock can be set at the current time via a soft-
ware interface.
SD card
The EC1000 possesses 1 SD card slot, e.g. for data copies.
Slot extension
Optionally, for communication purposes a slot is available for an extension module on the left-hand side.
Applicable interfaces are LAN, CAN RS485 or RS232.
Visualisation
CODESYS Target and Web Visualisation are included in the scope of supply. An easy-to-use display is availa-
ble with the Berghof ET1000 Ethernet Terminal.
Networking
PROFINET device and BACnet controller function as a software option.
Brief description

USER MANUAL 1.7 | EC1000
Berghof Automation GmbH | Harretstrasse 1 | 72800 Eningen | www.berghof.com
EC1000_HB_en_2D1652008ZD00.docx | 2VF100179FE06.docx
12
Performance features –an overview
400 MHz CPU
User program and data memory (RAM): 128 MB on board, max. 96 MB for application
User program memory (Flash): 64 MB on board / 56 MB for CODESYS V2.3 resp. 40 MB for
CODESYS V3 application
Retain memory, 24 kB
1 Ethernet 10/100 base T interface
1 USB Host interface V1.1
1 CAN interface at the front
1 RS232 serial interface for programming tools and application
1 EtherCAT interface with up to 10 users (or max. 2 A)
Realtime clock
1 SD card slot
Slot for left-hand extension module for communication (optional)
Scope of Supply
The scope of supply of the controller module consists of:
Ethernet Controller EC1000
Accessories
PLUG-IN CONNECTOR SET for EC1000; order no.: 201605600 (only 204900001 and 204900101)
PLUG-IN CONNECTOR SET for EC1000; order no.: 201608400 (all)
Shield connection terminals:
2 x 8 mm; order no.: 204802400
1 x 14 mm; order no.: 204802500
Scope of Supply
and Accessories

USER MANUAL 1.7 | EC1000
Berghof Automation GmbH | Harretstrasse 1 | 72800 Eningen | www.berghof.com
2VF100179FE06.docx | EC1000_HB_en_2D1652008ZD00.docx
13
2.2. Technical data
Ethernet Controller EC1000
Module data
Designation
EC1000 MP400 00 1131
EC1000 MP400 00 1131 V3
Item no.
204900001
204900002
204900101
204900102
Programming tool
CODESYS V2.3
At least CODESYS V3.5
Installation
Bearing rail NS 35/7.5 EN 60715
I/O Extension
Via EtherCAT
CPU, user memory
CPU
Freescale PowerPC, CPU 400 MHz
Program memory (Flash)
64 MB on board / 56 MB for CODESYS V2.3 / 40 MB CODESYS V3
Program memory and data
memory (RAM)
128 MB on board / max. 96 MB for application
Retain memory
24 kB
Sizes and weights
Dimensions (WxHxD [mm])
25 x 120 x 90
Weight
Approx. 150 g
Operating conditions
Ambient temperature
0 °C to 50 °C; 55 °C as standalone specification (if installation instruc-
tions are observed)
Relative air humidity
Max. 85 %, non-condensating
Transportation, storage
Ambient temperature
-20 °C to +70 °C
Relative air humidity
Max. 85 %, non-condensating
Resistance to vibrations
Vibration
Sinus-shaped (EN 60068-2-6) test: Fc 10 ... 150 Hz, 10 m/s²
Shock resistance
15 G (approximately 150 m/s²), 11 ms duration, semi-sinus (EN
60068-2-27) test: Ea
EMC, protection class
Emitted interference
EN 61000-6-4, industrial sector
Immunity to interference
EN 61000-6-2, industrial sector
Protection class
III
Insulation strength
SELV (Ue< 30 V) in compliance with EN 61131-2
Protection type
IP20

USER MANUAL 1.7 | EC1000
Berghof Automation GmbH | Harretstrasse 1 | 72800 Eningen | www.berghof.com
EC1000_HB_en_2D1652008ZD00.docx | 2VF100179FE06.docx
14
Ethernet Controller EC1000
Energy supply (24 V power supply unit)
Supply voltage
+24 VDC (-20 % / +25 %) SELV max. proportion of a.c. voltage 5 %
Power consumption
typ. 0.3 A, max. 0.3 A with +24 VDC, fuses depending on number of
connected extension modules, max. 2.5 A
Reverse voltage protection
Yes
Potential isolation
No
Bridging in case of power failure
10 ms at < 20.4 VDC (at max. external bus load of 5 V / 2 A) Power
Fail < 19.2 VDC
Ethernet interface
Number / type of interface
1x 10/100 Base T
Connection technology
1x RJ45
EtherCAT interface
Number / type of interface
1x EtherCAT E-bus, lateral 10-pin connection
Connection technology
Series connectors on right-hand side
USB interfaces
Number / type of interface
1 x Host USB Rev. 1.1
Number of mating cycles
max. 1.000
CAN-Bus interfaces
Number / type of interfaces
1x CAN in front (on 2x 5-pin multipoint connector COM / CAN)
Potential isolation
Yes (galvanic isolation)
Transmission rate
ISO 11898 max. 1 Mbit/s
Terminating resistor
external via plug-in connector
Serial interfaces
Number / type of interfaces
1x RS232 3 wire connection to 2x 5-pin multi-point connector in front
panel (RS232+CAN) (RX,TX,GND)
Potential isolation
Yes (galvanic isolation)
Transmission rate
max. Baud rate 115 kBaud
Other functions
Realtime clock
Yes, accumulator battery-buffered (maintenance-free)
SD card
1 SD card slot
Digital input
24 V (-20 % / +25 %)
Slot for left-hand extension module for communication (optional)
Number / type of interfaces
prepared for 1x LAN, 1x CAN, 1x RS485 / 1x RS232

USER MANUAL 1.7 | EC1000
Berghof Automation GmbH | Harretstrasse 1 | 72800 Eningen | www.berghof.com
2VF100179FE06.docx | EC1000_HB_en_2D1652008ZD00.docx
15
2.3. Block diagram
2VF100514DG01.vsd
Flash
RAM
Ethernet-
Controller
DC
DC
L +
L -
USB
Transceiver
Ethernet-
Transceiver
CAN
Transceiver
SIO
Transceiver
S0+
Status-LED EtherCAT-
Transceiver
USB
LAN
COM /
CAN
+5 V
+3,3 V
GND
Ether
CAT
CAN
SIO
CPU
EtherCAT
Ethernet /
COM / CAN
Accu
RTC
Serial
EEPROM
Retain memory
Voltage control
Energy reserve

USER MANUAL 1.7 | EC1000
Berghof Automation GmbH | Harretstrasse 1 | 72800 Eningen | www.berghof.com
EC1000_HB_en_2D1652008ZD00.docx | 2VF100179FE06.docx
16
2.4. Identification
Product: Ethernet-Controller, Type EC1000
Identification code
The features of the Ethernet-Controller (see ‘Annex, Nameplate’) can be itemised according to the
identification code.
2VF100582DG00.cdr
2.5. Module view and pin assignment
2VF100515DG02.vsd
EC 1 0 0 0 MP00
1 2 3 4 5 6 7 8 9 10 11 12 13 14 15
1 1 1
3
0 0 3V
16 17 18 19 20 21 23
00 = part
equipping
variant
MP400 = Power PC 400 MHz
V3 = CODESYS
Version 3.x
1131 = CODESYS
controller
EC = Ethernet-
Controller
Product
Programming tool
Processor type
Variant
EtherCAT
USB
LAN
EtherCAT
green/red
Run/Stop
red/green/yellow
Error red
LAN acitvity
Stop/Reset
Button
DI yellow
Power green
SD Card Slot
COM /
CAN
DI /
Supply
204900001

USER MANUAL 1.7 | EC1000
Berghof Automation GmbH | Harretstrasse 1 | 72800 Eningen | www.berghof.com
2VF100179FE06.docx | EC1000_HB_en_2D1652008ZD00.docx
17
2
1
2.6. Mounting and connecting
2.6.1. Mounting
The CANtrol E-I/O modules are intended for mounting rail installation (DIN EN 60715, 35 x 7.5 mm).
Push up the module against the mounting rail from below,
allowing the metal spring to snap in between mounting
rail and mounting area as illustrated.
Push the module above against the mounting wall until it
snaps in.
Rail mounting of module
CAUTION
There must be at least 100 mm clearance above and below the EC1000.
This guarantees the necessary convection cooling for the EC1000.
The mounting plate must be metal in order to ensure heat conduction.
To interconnect two modules
After snapping on the first module to the rail, snap on the second module about 1cm away towards the right
of the first module. Push the second module along the rail towards the first module until you hear the locking
device snap in.
To disconnect two modules
Push down the unlock button (see figure below) of the module that you wish to disconnect from the module
to the left of it. Push both modules away from one another until they are about 1 cm apart.
To snap on a
single module
To take down a
single module
Push the module up and against the metal spring lo-
cated on the underside of the rail guide.
Tip the module away from the rail as shown in the il-
lustration.
Pull the module down and out of the mounting rail.
Uninstalling a module
Unlock botton
1
2
3

USER MANUAL 1.7 | EC1000
Berghof Automation GmbH | Harretstrasse 1 | 72800 Eningen | www.berghof.com
EC1000_HB_en_2D1652008ZD00.docx | 2VF100179FE06.docx
18
2.6.2. Connecting
Power supply
The controller is energised from an external 24 VDC external power supply. Before connecting up, check that
the specifications required for the external power supply are observed.
External power supply (24 VDC)
Output voltage
+24 VDC SELV (-15 % / +20 %)
Ripple
Max. 5 %; the DC voltage must not fall short of 20.4 V.
Internal power supply unit
A power supply unit for the system electronics is installed to provide 24-VDC input voltage (-15 % / +20 %).
The power supply unit possesses integrated polarity-reversal protection and inrush-current limitation.
Both supply lines and the power supplies must be protected by an external short circuit and overload protec-
tion with a maximal tripping current of 5 A in each case (depending on the number of I/O).
Installation
All connections and lines must be executed so that no faults are caused by inductive and capacitive interfer-
ence in the controller. The supply lines must be sufficiently resilient to current and voltage. Shielded lines
must be used for communication. The shield must be fitted onto the module.
Plug DI/Supply assignment
DI/Supply
DI
Digital input 24 VDC (-20 % / +25 %)
L+
External power supply 24 VDC (-15 % / +20 %)
L-
External power supply GND
Energy buffering
Power Fail 10 ms depending on compliance with the max. number/load by I/O modules.

USER MANUAL 1.7 | EC1000
Berghof Automation GmbH | Harretstrasse 1 | 72800 Eningen | www.berghof.com
2VF100179FE06.docx | EC1000_HB_en_2D1652008ZD00.docx
19
2.6.3. Earth
Connect the EC1000 to earth by attaching the metal housing to operative earth.
Since the operative earth connectors dissipate HF currents, it is of utmost importance for the module's noise
immunity. HF interference is dissipated from the electronics board to the metal housing. The metal housing
therefore needs to be suitably connected to an operative earth connector.
You will normally have to ensure that
the connection between module housing and DIN rail conducts well,
the connection between DIN rail and switching cabinet conducts well,
the switching cabinet is safely connected to earth.
In special cases you may attach the earth wire straight to the module.
NOTICE
Earth wires should be short and have a large surface (copper mesh).
Further details has site http://en.wikipedia.org/wiki/Ground (electricity).
Aluminium profile
Attach cable shield here
Connect DIN rail with operative
earth
M3x5 Bolt connec-
tion

USER MANUAL 1.7 | EC1000
Berghof Automation GmbH | Harretstrasse 1 | 72800 Eningen | www.berghof.com
EC1000_HB_en_2D1652008ZD00.docx | 2VF100179FE06.docx
20
2.7. Pin assignment
2.7.1. 10/100 Base-T network connection (Ethernet)
The 10/100 Base-T on board Ethernet adapter with RJ-45 connection enables connection to the network.
The “LNK” and “RCV” status LED give information about successful connection to the network in compliance
with IEEE 802.3, clause 25.
LAN plug-in connector assignment
LAN
RJ45
1
TX+
2
TX-
3
RX+
4
75 Ohm
5
75 Ohm
6
RX-
7
75 Ohm
8
75 Ohm
“LNK” LED
green
ON: ready to operate
“RCV” LED
yellow
FLASHING: Data Receive
2.7.2. USB
Devices with USB interfaces can be connected on the USB master port (rev. 1.1). The only classes of USB de-
vices which can be used by CODESYS users are USB sticks. A mouse can only be used at the level of Linux.
The following issues must be taken into account when using USB sticks:
CAUTION
A USB stick may only be unplugged during operation if all file operations
have been completed, otherwise the USB may become unserviceable!
If programs still have files open, the directory cannot be deleted when the USB
stick is removed. In this situation file or directory operations cause blockages
because a reading must be taken from a device which is no longer available in
the system. Therefore, when removing the USB stick, always make sure that
no program has any files still open on the USB stick.
Connection to the
network
Table of contents
Other BERGHOF Controllers manuals
Popular Controllers manuals by other brands
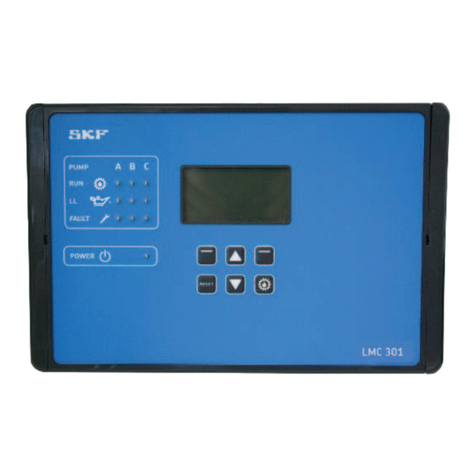
SKF
SKF LMC 301 Series installation guide
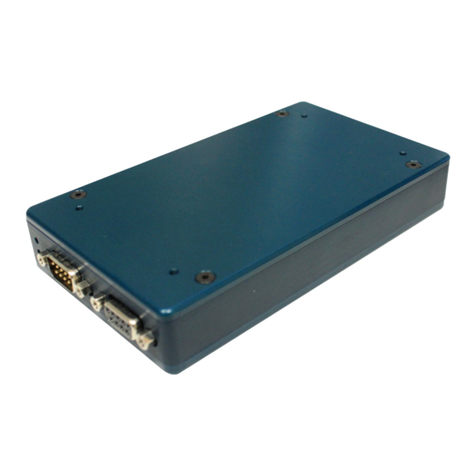
Micronix
Micronix MMC-110 Series Reference manual
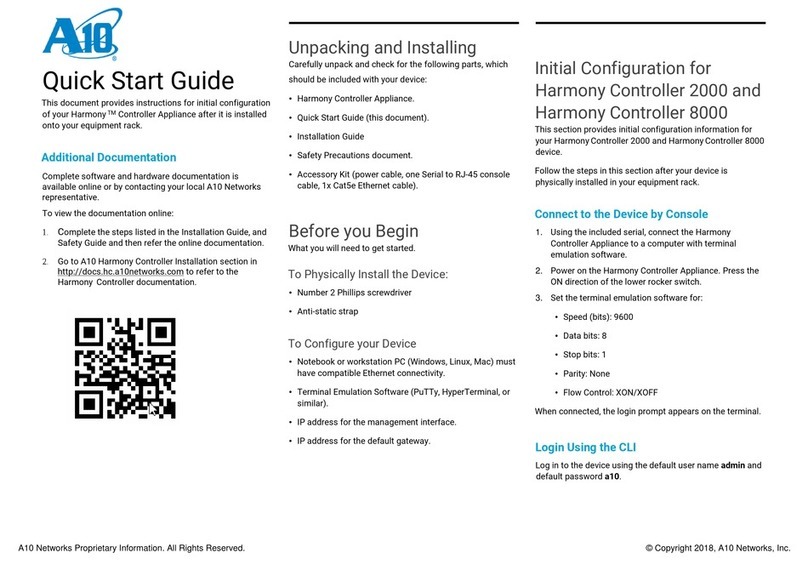
A10
A10 Harmony Controller 2000 quick start guide
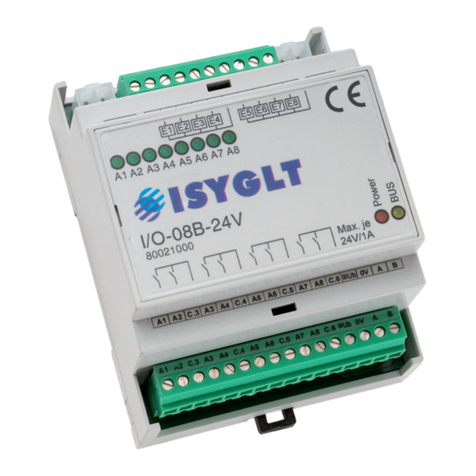
Seebacher
Seebacher ISYGLT I/O-08B-24V-1A Technical Data/Instruction Manual
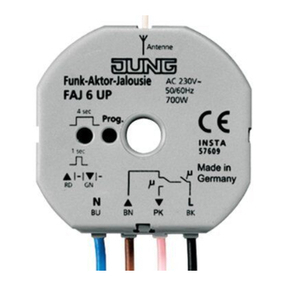
Jung
Jung FAJ 6 UP operating instructions
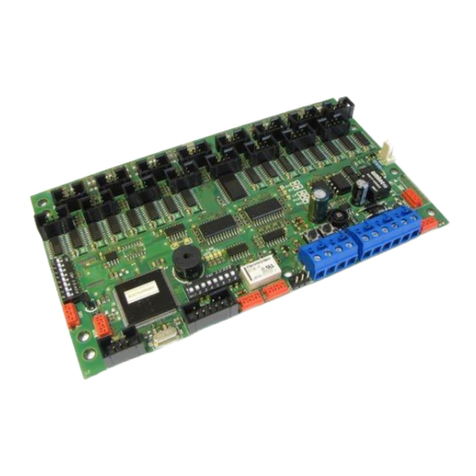
Metra Electronics
Metra Electronics ELS NET LC16ANT Technical manual

Kampmann
Kampmann KaController 3210001 quick guide
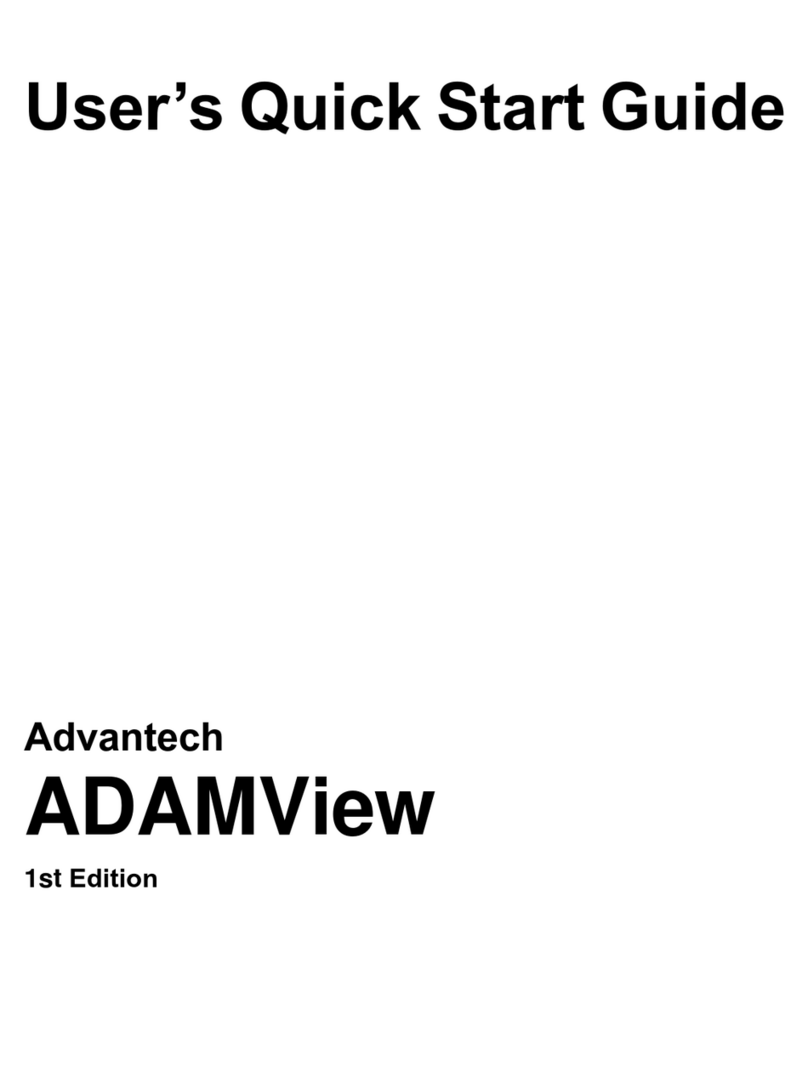
Advantech
Advantech ADAMView quick start guide
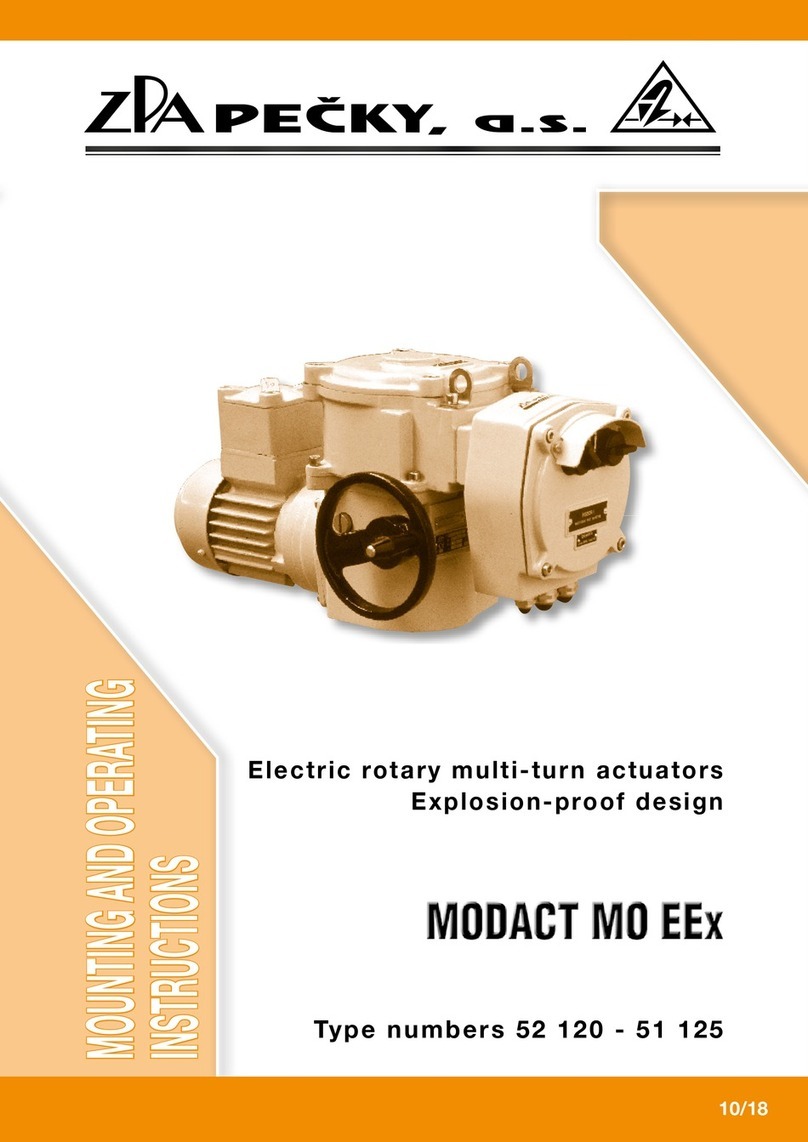
ZPA Pecky, a.s.
ZPA Pecky, a.s. MODACT MO EE Series Mounting and operating instructions
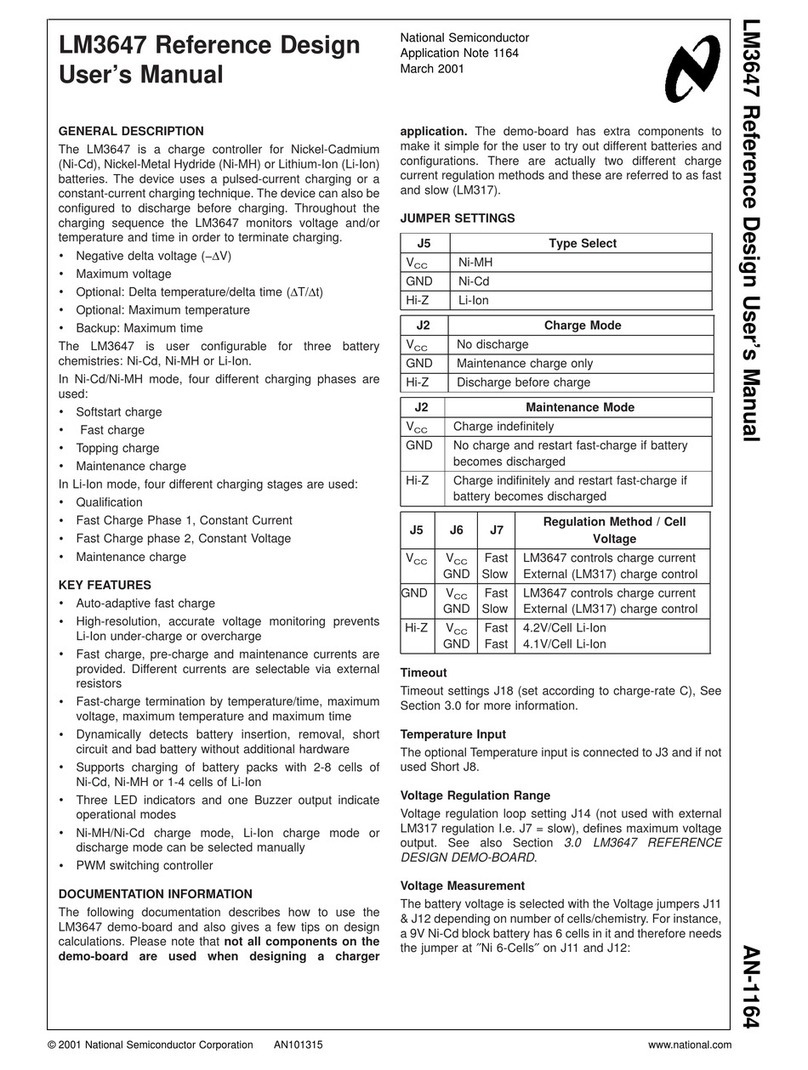
National Semiconductor
National Semiconductor LM3647 user manual
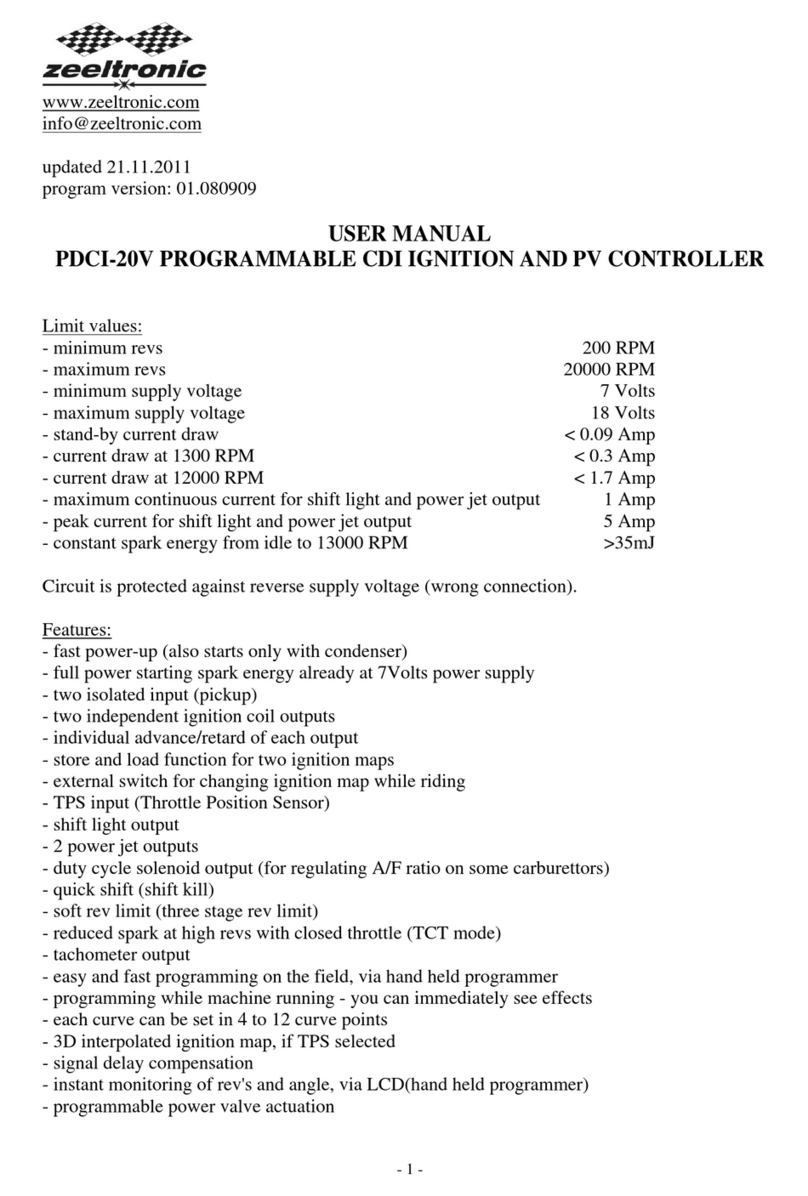
zeeltronic
zeeltronic PDCI-20V user manual
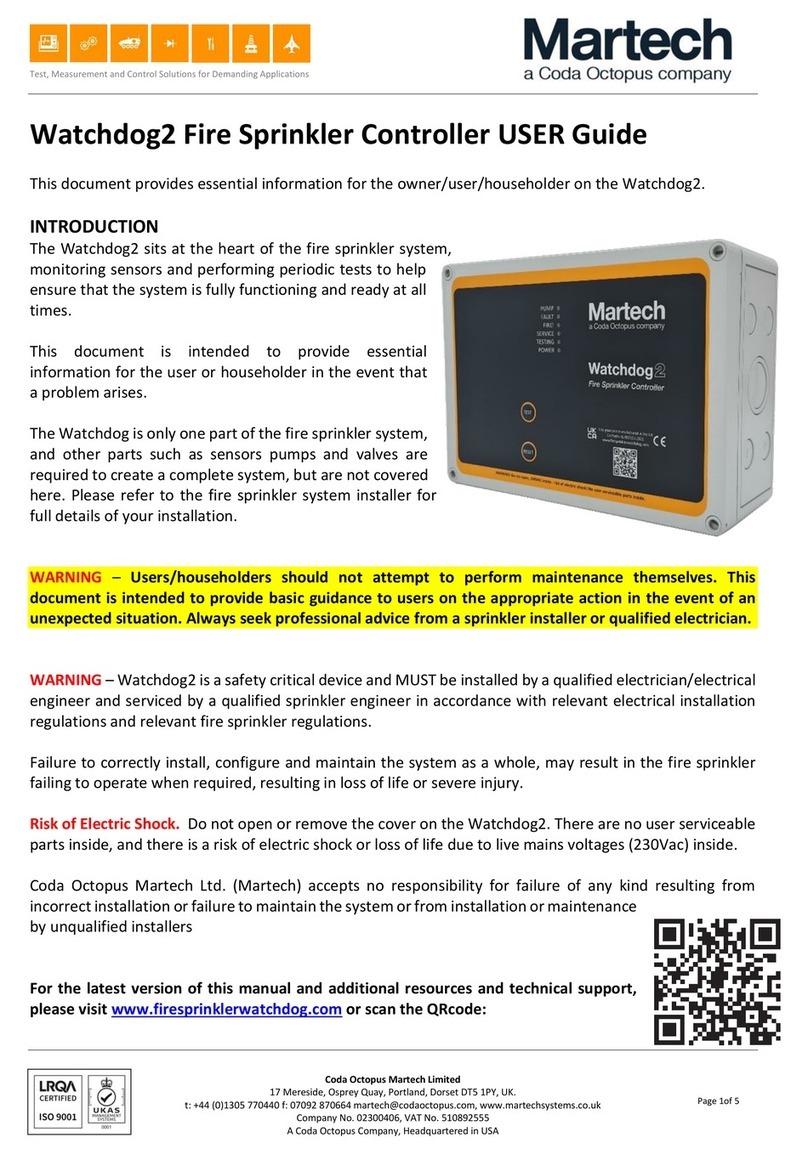
CodaOctopus
CodaOctopus Martech Watchdog2 user guide