Bernhard Express Dual 3000 User manual

EXPRESS DUAL 3000 MANUAL
EXPRESS DUAL 3000
Please read this manual carefully before using the Express Dual.
This manual should be kept in a safe place so that it can be used for future reference.
ED3000 Automatic Spin Grinder
User’s Guide &
Instruction Manual

2
EXPRESS DUAL • ED3000
© Bernhard and Company Limited
EXPRESS DUAL
Contents
BERNHARD AND COMPANY LTD
Bilton Road • Rugby • England • CV22 7DT
Tel +44 1788 811600 • Fax +44 1788 812640
Email: info@bernhard.co.uk
USA Toll Free 1-888 GRIND IT (
1-888 474 6348)
ED3000 Precision Reel/Cylinder Grinder
You are now the owner/operator of a Bernhard’s Express Dual 3000 which, if cared
for and operated correctly, will give you years of good service.
This manual will enable you to obtain the best results from your Express Dual so
please read it thoroughly before using your machine.
If you have any service or operational problems contact your distributor,
or phone our
Technical Helpline (USA only) – 1-888 474 6348
or
Bernhard and Company Ltd, England –
(+44) 1788 811600
or email
use the technical support feedback form on our web site
www.expressdual.com or www.bernhard.co.uk
Identication of Pictograms 3
Safety 6
Installation 7
Identication of Tools and Equipment 9
Understanding the Machine 10
In Frame Grinding 12
Electrical Fault Finding 20
Maintenance 21
Part Lists and Exploded Diagrams 25
Wiring Diagrams 44
© Bernhard and Company Limited • ED3000_2004/04

3
EXPRESS DUAL • ED3000
© Bernhard and Company Limited
BEWARE! HIGH VOLTAGE
1. Identication of Pictograms
MAXIMUM LIFT PLATFORM
LOAD - 250 KG (550 LBS)
BEWARE!
TRAPPING FEET OR OTHER OBJECTS
WHEN LOWERING LIFT PLATFORM
MAXIMUM GRINDSTONE
DIAMETER 150mm
MAXIMUM SPEED 2200 Rev/Min
BEWARE!
MOVING GRINDSTONE AND SHAFT
REEL ROTATING AT BETWEEN
147 AND 255 Rev/Min
TOTAL WEIGHT OF MACHINE (KG)

4
EXPRESS DUAL • ED3000
© Bernhard and Company Limited
WEAR EYE, EAR AND BREATHING
PROTECTION
1. Identication of Pictograms
(Continued)
POINTS FOR ATTACHING
LIFTING EYES
BEWARE!
MOVING COMPONENTS KEEP HANDS
AND OTHER OBJECTS CLEAR
GRINDSTONE START CONTROL
REEL START CONTROL
STOP CONTROL
TRAVERSE START CONTROL
ENGAGE / DISENGAGE (INCREASE /
REDUCE) GRINDSTONE FEED

5
EXPRESS DUAL • ED3000
© Bernhard and Company Limited
Emergency Stop
(Twist to release)
Unclamp
Clamp
Reset
Display
Traverse On Reel (Spin)
Drive On
Grindstone
On
Position
Value
Display
Balance
Indicator

6
EXPRESS DUAL • ED3000
© Bernhard and Company Limited
2.1 This machine is designed and manufactured ONLY for grinding lawn mower reels, rollers,
groomers and verticut units, and MUST NOT be used for any other purpose.
2.2 This machine should be installed, operated and maintained by competent personnel who
have received adequate training.
2.3 Before carrying out any work on the machine, other than grinding, ALWAYS SWITCH OFF
the main electrical supply, or remove the power lead from its socket.
2.4 ALWAYS operate the machine with the guards in position.
2.5 NOISE - Owing to the widely varying conditions of use, noise emissions may vary
considerably. There may be occasions when the safe noise level may be exceeded (see
note on noise emission). In this case adequate ear protection MUST be worn.
2.6 NEVER t or use a grinding wheel (or other spares) other than those supplied specically
for use on the EXPRESS DUAL (Warranty will be invalidated).
2.7 NEVER t or use a grinding wheel which has been dropped or subjected to any other form
of abuse.
NOTE: Grinding wheels should be tted ONLY by competent, trained personnel.
2.8 NEVER leave rags or tools on the machine or wear any loose clothing or other articles
which could be caught in moving components.
2.9 NEVER allow any combustible materials to be placed on or around the machine.
2.10 ALWAYS ensure that all parts of the cutting unit being ground are securely xed.
2.11 ALWAYS ensure that all electrical connections are sound and all cables are safely routed.
2.12 ALWAYS carry out cleaning and maintenance of the machine as instructed in this manual
(Refer to safety note 1.3).
2.13 STAY ALERT. Watch what you are doing. NEVER operate the machine when tired, or
under the inuence of drugs or alcohol.
If a lift table is fitted NEVER attempt to lift in excess of the rated capacity, and always
ensure that the area is clear before lowering the load.
2. Safety

7
EXPRESS DUAL • ED3000
© Bernhard and Company Limited
3. Set Up and Installation
Fig: 3.2
3.1
Handling
If the machine is crated, it can be moved by a suitable fork lift truck or pallet truck under
the pallet (skid). Once the lid and sides of the crate are removed, a fork lift truck may be
used under the lifting members of the machine chassis.
The machine can be lifted off the pallet using suitable lifting tackle through 4 lifting eyes
(provided) tted at the points indicated on the top corners of the machine.
The total weight of the machine is indicated on the machine plate and also at the front of
this manual.
3.2 Location
The machine should be located in a well lit environment with adequate headroom. For
ideal operation, the machine should be accessible from the front, rear and at least one
side, with clearance around it as indicated in the sketch (Fig. 3.2).
3.3 Leveling
The machines should,ideally, be placed on a solid level oor, and this should be checked
by placing a spirit level on the table. Check the level in both directions. Steel shims should
be placed under the feet as necessary to ensure that the machine is rm and level. Bolt
holes are provided in the feet which can be used for xing down if required.
NOTE Ensure that the packing under the feet is correct before tightening the bolts, otherwise
twisting of the frame may occur.

8
EXPRESS DUAL • ED3000
© Bernhard and Company Limited
3.4 Electrical Supply
USE A QUALIFIED ELECTRICIAN
The EXPRESS DUAL is supplied with a .55 kW ( HP) single phase main (grind) motor
plus 2 fractional HP motors, for spin and traverse.
Power connection to the machine is via plug and socket termination of the lead supplied.
Connection is at the rear of the main electrical control box on the right hand end of the
machine.
Ensure that any cable or conduit run to the machine does not constitute a hazard to the
operator or other personnel.
Machine should be connected to the supply via a 20A breaker.
The top of the reel and the top of the grinding wheel should both move away from the
front of the machine (i.e. both rotate clockwise when viewed from right hand end of the
machine). In this way, the reel and grinding wheel are moving in OPPOSITE DIRECTIONS
at the point of contact.
[For full electrical spec’s, see bid spec at rear of manual.]
3.5 Preparation
If the machine has been
received in a crate, the handles
on the control wheels should be
removed from the underneath of
the control wheels and retted to
the top (see Fig. 3.5).
It is important that the protective
film on the main shaft is
removed prior to using the
machine. This can be done
using a WD40 or similar product
(not gas/petrol) and then drying
the shaft with a clean, dry cloth
so that the grinding wheel
assembly moves freely along
the whole length of the shaft.
A spray lubricant, such as WD40, should be applied to all bare metal surfaces and moving
parts; this includes the reversing bar and the shafts (along which the fork assembly
traverse, but NOT THE MAINSHAFT).
The mainshaft should be washed down as instructed in the maintenance section of this
manual. The feed control screws are normally coated with molycote, and may be washed
down with WD40 if required and recoated with molycote (or similar anti friction coating)
when dry.
Fig: 3.5
3. Installation
(Continued)

9
EXPRESS DUAL • ED3000
© Bernhard and Company Limited
4. Identication of Tools and Equipment
The items below may not necessarily be included since the tools and equipment
supplied will vary according to the machine specication.
4.1
Express Dual 3000 and 3000DX (see illustrated parts list).
A4066 Long 1/2” AF Ball handled Allen Key
A2706 3/16” AF Tee handled Allen Key
A2719 Grinding Wheel Nut Wrench
A2720 1/2” AF Allen Key
A2714 Adjustable Sprocket Driver
A9182 Drive Rod Plain (short)
A4134 Drive Rod Square (short)
A4063 2 Pin Drive (large)
A4276 2 Pin Drive (small)
A9181 3 Pin Drive (small)
A4097 Adjustable Plain Shaft Driver
A2712 8mm Long Series Allen Key
A6161 1/8” Allen Key
A4087 Channels for Multix Brackets
A6342 Backing up/Pressure Plate (not shown)
A4106 Ransomes 5/7 Driver (Standard only on European units)
A6737 Diamond Dresser
A9500 Adustable Front Roller / Multix Brackets

10
EXPRESS DUAL • ED3000
© Bernhard and Company Limited
5. Understanding the Machine
5.1
General Principles
The EXPRESS DUAL is designed to grind reels completely assembled, or as a separate
“loose” reel. A Loose Reel Kit (Available as an optional extra, at additional cost) is required
for this operation.
The basic principle of the EXPRESS DUAL is to grind mowers in exactly the same
conditions that they mow in. The grinding wheel takes the place of the grass, striking the
reel in relatively close proximity to that found in the mowing position.
5.2 Basic Requirements
It is important that grinding the cutting unit, when it remains completely assembled, takes
place under the following conditions:
5.2.1 The reel bearings MUST be in good condition, adjusted correctly and if the roller is to be
located on the roller mounting brackets or the multix brackets, the roller bearings MUST
also be in good condition.
5.2.2 The bedknife must be ground separately on a machine, such as the ANGLEMASTER
bedknife grinder which can guarantee that the blade will be perfectly STRAIGHT and at
whilst mounted on the bedbar.
During the reel grinding process, it is advisable that the bedknife/bedbar assembly is
replaced in the unit after having been ground. On many units the bedknife/bedbar is an
integral part of the frame and contributes to its strength and rigidity.
5.2.3 The reel or bedknife must be adjusted away from one another to allow free rotation (There
should be no reel to bedknife contact!).
5.2.4 It is essential that all work to be carried out on the mowing unit (all mower repairs
– bearings, seals, roller work, etc.) has been completed prior to grinding the reel. The last
operation of all, apart from nal setting reel to bedknife, is the actual grinding of the reel
in-frame.
It is essential that the unit is held totally rm during the grinding process. When in frame
grinding, the front of the unit must be held rmly in the multix brackets or on the front
roller brackets.
5.2.5 It is essential that the unit is held totally rm during the grinding process. When in frame
grinding, the front of the unit must be held rmly in the multix brackets or on the front
roller brackets.
The rear of the unit will be held by the radiused pressure bar at the rear of the grinder.

11
EXPRESS DUAL • ED3000
© Bernhard and Company Limited
5. Understanding the Machine
(Continued)
5.3 Machine Functions
The EXPRESS DUAL has 3 separate motors driving the different functions of the machine,
all are controlled from the control panel . These functions are as follows:
5.3.1 Traverse
This motor and the accompanying drive mechanism controls the automatic movement of
the grinding wheel along the mainshaft.
5.3.2 Reel/Spin drive
This motor drives the reel through a exible shaft driving from a drive mechanism under
the table. It is a three phase motor controlled by an inverter for varying output speed.
5.3.3 Grinding Wheel
A motor situated under the table, drives the mainshaft and grinding wheel at 2200 rpm.
5.3.4 Stop
Pressing the stop button shuts off all 3 motors and locks into the “off” position. None of
the start buttons will operate until the stop button has been unlocked by twisting the knob
counter-clockwise to release it.
NOTE The machine must NOT be stopped when there is contact between the reel and grinding
wheel, except in cases of emergency.
5.3.5 Reset Button (see also Electrical Fault Finding section)
If the main motor is subject to a voltage drop or overloading, the current being drawn will
rise and a safety device will automatically shut the grinder off. The overload trip switch is
situated behind the blue reset button on the cover of the main electrical control box which
is located on the right hand end of the machine.(looking from the front).
The trip setting will vary with the electrical specication of each machine and is normally
set to the full load current of the motor. If the overload trip has shut off the grinder it can be
reset by pushing the reset button after a few minutes delay. This will allow the grinder to be
re started.
NOTE The reset button and overload are both variable and should be adjusted, if required, as
indicated in the appropriate service bulletins.
The reel drive motor, traverse motor, and VSD inverter (reel spin speed control) are
protected by individual fuses located in the electrical control box and accessible without
the necessity of opening the box.

12
EXPRESS DUAL • ED3000
© Bernhard and Company Limited
6.1 Mower Preparation
Units of up to 36” long can be ground
in frame, this includes most machines
including Greens mowers and Fairway
units. In order to spin / drive the reel,
one end of the reel shaft drive must be
exposed. This will require the removal
of the hydraulic motor, the chain / belt
or cover depending on which type
of unit is being ground. This should
be done before the mower is on the
grinder (see example Fig. 6.1).
Ensure that the mower is clean and
that both reel and roller bearings are
in good condition. Also ensure that
the bedknife has been sharpened, if
necessary, and replaced with a small
amount of clearance between it and the reel.
6.2. Mounting Mower
The mainshaft / Grinding stone should
be wound down to its lowest position
and the unit placed on the table. The
unit should then be carefully moved
towards the multix brackets or front
roller brackets, which can be adjusted
in any direction to allow the unit to be
xed in such a position that the grinding
wheel can be raised towards the reel
without coming into contact with either the
bedknife or the front roller/groomer.
With the mower correctly positioned the radiused
pressure bar) is moved forward to rest on the rear of the
mower and locked in position by operating the toggle switch on
the operator control panel downwards. The operator should release
the toggle switch as the pressure bar engages the cutting unit thus retaining pressure
on the mower until the grinding operation is completed. A backing up plate is supplied to
protect the rear of the units and to evenly disperse the force of the pressure bar across the
width of the mower (see Fig. 6.2).
6. In-frame Grinding
Fig: 6.1
Fig: 6.2

13
EXPRESS DUAL • ED3000
© Bernhard and Company Limited
6.3 To ensure that the correct position for the mower unit has been achieved, both control
wheels (right hand and left hand) should be wound in a clockwise direction so that the
grinding wheel may be placed to contact each end of the reel evenly. If the grinding wheel
touches the bedknife or any part other than the reel, the whole unit must be moved by
adjusting the position of the multix brackets or roller brackets. The exact position required
will be easily seen by looking along the mainshaft from one end of the machine as the
stone is raised to check that the point of contact is in a suitable position (see Figure 6.3).
NOTE If the cutting unit has no front roller tted so that the multix brackets are used then, once
the correct position for any particular unit has been nalised a “set up guide” should be
completed and led for future reference so that the identical multix brackets positions can
be used for all subsequent applications on the same type of unit.
6. In-frame Grinding
(Continued)
Fig: 6.3
Reel
blades
Front Roller position
is adjustable
Grind stone has to contact
reel blades for sharpening
without touching anything else
Adjustable Front
Roller support
Position of
bedknife is
adjustable

14
EXPRESS DUAL • ED3000
© Bernhard and Company Limited
6.4 Set up of Traverse
The reversing bar is located in the aperture to the front panel of the machine. Rotate
hand wheels anti-clockwise to move grinding wheel away from reel, unscrew the traverse
engagement screw until it is released from the traverse chain, traverse the grinding wheel
by hand, using the Traverse Engagement Screw until it is at the extreme point of desired
travel. Ensure that the traverse reversing bar is also moved in that direction and slide the
reversing stop up to the grinding wheel traverse assembly and tighten. Move the grinding
wheel to the opposite end of the desired travel and repeat the operation ensuring that the
reversing bar has also been moved in the opposite direction. This is critical where the
grinding wheel cannot pass beyond the end plates if they protrude below the maximum
diameter of the reel.
NOTE On the EXPRESS DUAL it is not necessary for the whole width of the grinding wheel to
pass the end of the reel and it SHOULD NOT DO SO EVEN IF SPACE PERMITS (see
Fig. 6.4).
Ensure that the leading edge
of grinding stone passes the
end of the reel - but clearance
must be maintained between
stone and end frame of unit.
NOTE: The reversing bar will move approximately 1/2” (13mm) before the direction of travel is
reversed and will allow the grinding wheel to move with it. It is therefore ESSENTIAL that
this is taken into account when setting the maximum point of travel.
Should the reversing bar be dragged by the traverse assembly in the direction of travel
during the grinding processes, causing the stone traverse to reverse prematurely, it will be
necessary to adjust the reversing bar damper as indicated in the service bulletin (No.003).
6. In-frame Grinding
(Continued)
Fig: 6.4

15
EXPRESS DUAL • ED3000
© Bernhard and Company Limited
6.5 Linking Up The Reel Drive Unit to the Reel
Machines are supplied with the reel drive motor under the table and a exible drive which
can be attached to either end of the machine do not have to be prepared before the mower
unit is placed on the table, as the complete drive unit can be moved to either side of the
table with a mower unit in place.
6.5.1 Select the attachment with which to drive the reel. If the reel sprocket, gear or pulley
is secured with a nut it may be easier to use a standard socket together with a 1/2”
square end driver. Ensure the nut is tight as the direction of rotation may tend to unscrew
it. Ensure that the drive shaft is through the exible coupling/driver before setting the
machine on the table and that the whole unit is at the correct end of the table.
Alternatively it may be easier to drive directly onto the sprocket using one of the pin or
adjustable type sprocket drivers tted to the plain drive rod.
6.5.2 When the cutting unit is in place and rmly xed into the multix brackets, or front roller
brackets, and the rear clamped with the radiused pressure bar, adjust the drive unit left or
right so that the appropriate drive rod will reach the end of the reel shaft. Tighten unit in
place
Adjust the height and position, forwards and backwards and up and down, of the cable
drive drive support so that the shaft is square with the driven end of the reel, and tighten
clamps to hold it in place.
The black lobed hand screw allows the drive head to be moved along the square support
shaft to adjust the height of the drive, while the 5/8” hex headed socket screw allows the
support shaft to be clamped at any desired angle, and also allows the whole assembly to
be moved left or right along the machine bed to engage in the drive mechanism on the
reel.
The drive head of the shaft can also be slid through it’s support for further adjustment or
nal connection/ disconnection of drive.
6.5.3 Tighten the drive rod via the allen screw in the exible coupling onto the at of the drive
shaft.
6. In-frame Grinding
(Continued)

16
EXPRESS DUAL • ED3000
© Bernhard and Company Limited
6.5.4 Moving the exible Shaft
There is a layshaft socket at both ends of the
machine into which the exible drive can be
engaged as required. The other end of the
exible shaft can be disconnected if required
but this would not generally be necessary as the
bracket and shaft would normally be moved as
an assembly.
The exible drive shaft can be detached
from its socket on the end of the machine by
pulling sharply on the shaft, to release it from
a spring loaded ball detent. (Earlier units by
rst removing the spring retainer (R-pin)), and
withdrawing the complete shaft. When replacing
the shaft, ensure that it is properly engaged
in the layshaft socket (and if appropriate, the
spring retainer securely replaced).
By loosening the socket screw and allowing
the clamp nut, under the table, to twist through
approximately 90 degrees, the whole assembly
can be lifted clear of the table, and moved to the
other side of the mower unit if required.
6.6 Applying the Cut
Before starting any of the motors it is necessary to bring the grinding wheel into its
approximate cutting position.
6.6.1 With the stone positioned at the left hand end of the reel, place the left hand on the left
hand control wheel and the right hand on the reel, wind the control wheel clockwise while
slowly rotating the reel until the reel gently rides across the grinding wheel.
6.6.2 Unwind a complete turn to move the stone away from the reel.
6.6.3 Move the grinding wheel to the right hand end of the reel and, using the right hand on the
right control wheel and the left hand on the reel, raise the shaft until the reel again can be
gently rotated against the top of the grinding wheel.
6.6.4 Unwind half a turn.
6.6.5 Go back to the left hand end and repeat the process but this time, after contact has been
made, unwind only sufciently to release the contact.
6.6.6 Go back to the right hand end and repeat the process and again release the contact only
slightly.
NOTE It is important that the grinding wheel should clear the highest blade along the full length of
the reel before grinding commences.
6. In-frame Grinding
(Continued)

17
EXPRESS DUAL • ED3000
© Bernhard and Company Limited
6.7 To Commence Actual Grinding
NOTE With experience and familiarity setting / applying the cut can start here, speeding up the
set up procedure
6.7.1 If the machine has them tted, CLOSE THE GUARDS.
6.7.2 Start the reel drive motor and check for smooth, easy running.
6.7.3 Start the grinding wheel motor.
6.7.4 Start the traverse motor, rst ensuring that the traverse engagement screw is unwound
and not connected to the traverse chain.
6.7.5 Now repeat the adjustment process with the left hand on the control wheel and the right
hand on the traverse knob, moving the grinding wheel along the reel by hand using the
traverse engagement screw, winding up the left hand control wheel until the grinding wheel
strikes and sparks gently against the reel.
Repeat this process on the right hand side of the reel, raising the shaft with your right hand
and moving the grinding wheel along with your left hand. Repeat this process until the
contact along the reel is even and parallel.
6.7.6 Screw in traverse knob to engage power traverse.
NOTE Check auto traverse is changing direction at correct point at each end of its movement.
6. In-frame Grinding
(Continued)

18
EXPRESS DUAL • ED3000
© Bernhard and Company Limited
6.7.7 Place hands on the left and right control wheels and move both hand wheels clockwise the
same amount to apply an even cut.
The Light Emitting Diode (LED) feed balance system tted to the Express Dual 3000 spin
grinding machine is designed to ensure that the operator has a simple visual indication that
ensures that feed of cut is applied parallel across the length on any reel.
• Set the grind stone to the reel as with any other Express Dual, adjusting the independent
handwheels until there is a light and steady contact between reel and grind stone across
the entire length of the reel.
• Press the green “reset” button to “zero” the display (zero the grinder to the reel) the central
green LED illuminates and both counters zero.
• Winding the right hand handwheel will make the amber LED to the right of display centre
illuminate (further winding would then illuminate the red led to the right of the display)
counter readout increases in value.
• Winding the left hand handwheel will extinguish red and/or amber LED’s and return to
the green LED illuminated. Both counters now read the same. Equal feed has now been
applied to both sides and the feed is balanced (PARALLEL) – no taper has been applied.
NOTE It is important that the control wheels are moved equally.
6.7.8 Apply a good hard cut. Do not be afraid of the aggressive nature of the grinding process.
6. In-frame Grinding
(Continued)

19
EXPRESS DUAL • ED3000
© Bernhard and Company Limited
6. In-frame Grinding
(Continued)
6.8 When Is The Job Done ?
6.8.1 You will hear the cut begin to run out - a rough guide of cutting times will be:
Fairway Units 12–20 minutes
Medium Triple Units 10–15 minutes
Greens & Hand Mowers 8–10 minutes
6.8.2 Now take off the cut by simultaneously moving both hand wheels anti-clockwise, when the
stone is at one end of its traverse, until the grinding wheel is clear of the reel.
6.8.3 Push the total / “E”- stop button.
NOTE NEVER stop the machine while the grinding wheel and reel are in contact except in an
emergency. Never allow the grinding wheel and reel to spark out. If this does happen put
another cut on for a few more passes.

20
EXPRESS DUAL • ED3000
© Bernhard and Company Limited
USE A QUALIFIED ELECTRICIAN
In the event of any motor not starting, the following procedure should be adopted:
7.1. Check that STOP BUTTON in control panel on top of machine is not permanently in STOP
position.
7.2 Check fuses - main fuses feeding machine and small fuses in junction box for traverse and
reel motors.
7.3. Check that reset button on junction box is not making contact with red button on the
overload. If it is adjust RESET so that it CLEARS THE BUTTON, this must be tested with
lid held in position on box (see service Bulletin no.001).
7.4. Check voltage in electrical box, right hand side of machine – terminal block, terminals 1 and 4.
7.5. Check for open circuit on overload, terminals 95 and 96, to determine whether or not main
motor is faulty. If open press red resetting button on overload.
7.6. To determine that all three contactors are OK test each one by pushing start button on
the individual contactors, they should noticeably pull in. This can be checked by someone
looking in the junction box while the start buttons are pressed.
7.7. Traverse
If the contactor is functioning properly check the microswitch. If this is found to be OK
check capacitor if possible. If neither of these is faulty, then the motor is probably at fault.
7.8. Reel Drive
If the contactor is functioning properly, check the Inverter:
There is a small LED lamp on the front of the unit. This should be green. If it is red, or
changes to red when pressing the start button, there is an inverter fault.
Disconnect the power to the machine, wait 2 minutes, then re-connect and try again (to
re-set the inverter). If the LED is still red the inverter may have failed.
If neither are faulty then the motor is probably at fault.
7.9. Main Motor
If the contactor is functioning correctly, check the load current with an ammeter across
terminals 2 and 3 on 12 way terminal block. If this exceeds full load current indicated on
the motor identication plate then a new motor is needed. If the reading is below full load
current then possibly the overload is set too low.
NOTE Before assuming that there is an electrical fault in any of the systems ensure that the
mechanical drive assemblies attached to a particular motor are moving freely, and have
not got increased resistance due to damage, or the build up of dirt. This can best be done
by detaching the motor drive and ensuring that the mechanism is moving freely.
7. Electrical Fault Finding
This manual suits for next models
1
Table of contents
Other Bernhard Grinder manuals
Popular Grinder manuals by other brands
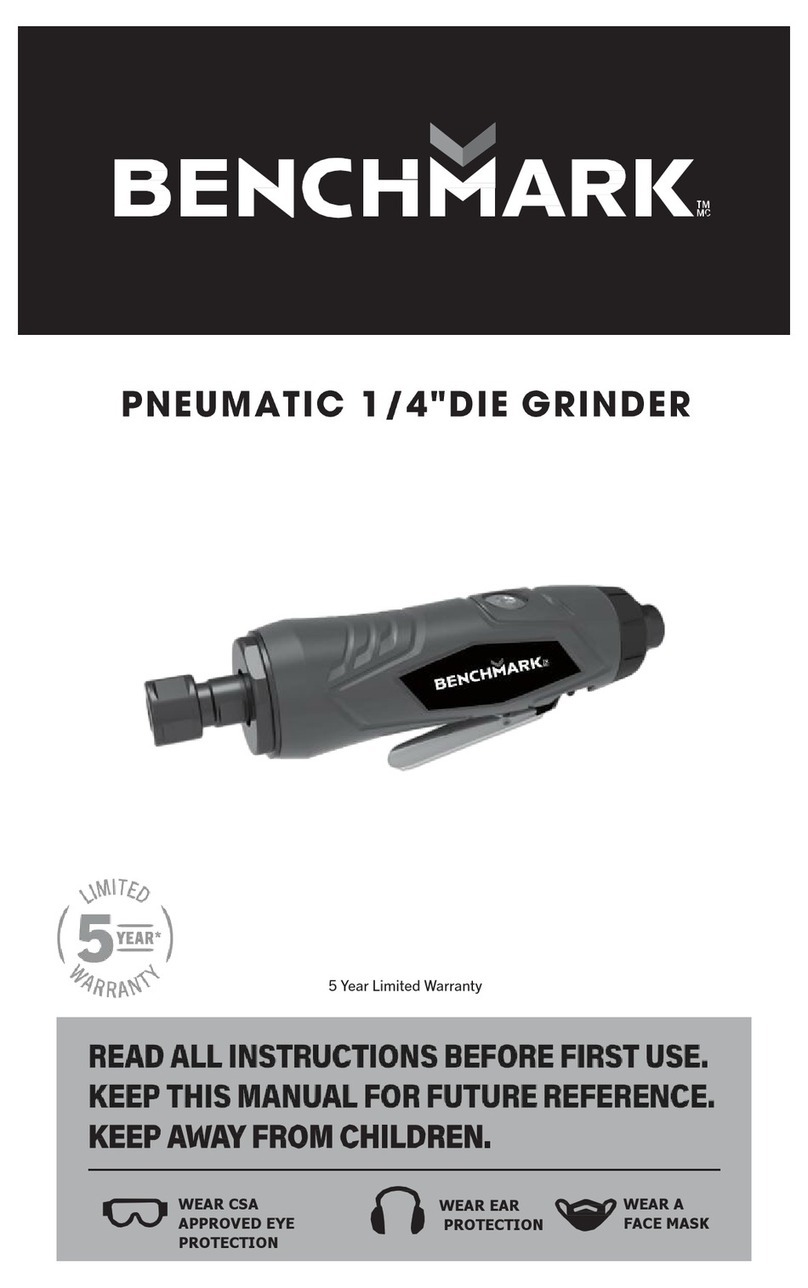
Benchmark
Benchmark 1282-943 instructions
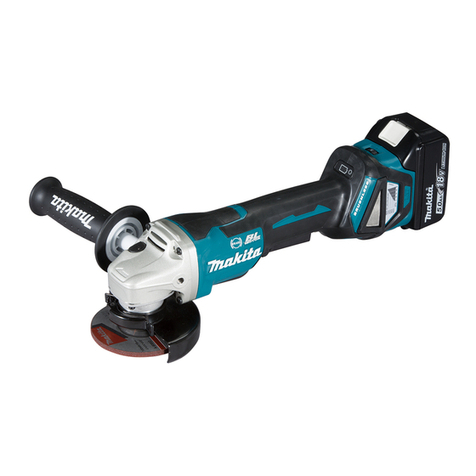
Makita
Makita DGA517RTJ instruction manual
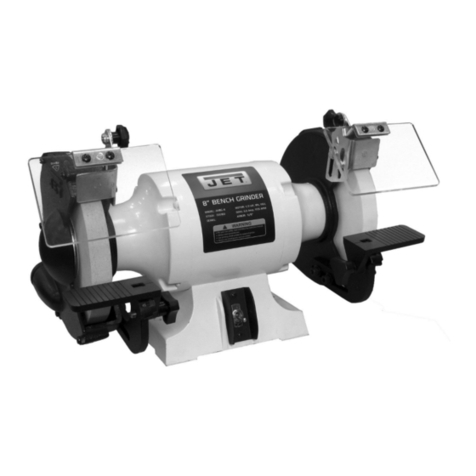
Jet
Jet 726101 Operating instructions and parts manual

Bort
Bort BWS-950 manual
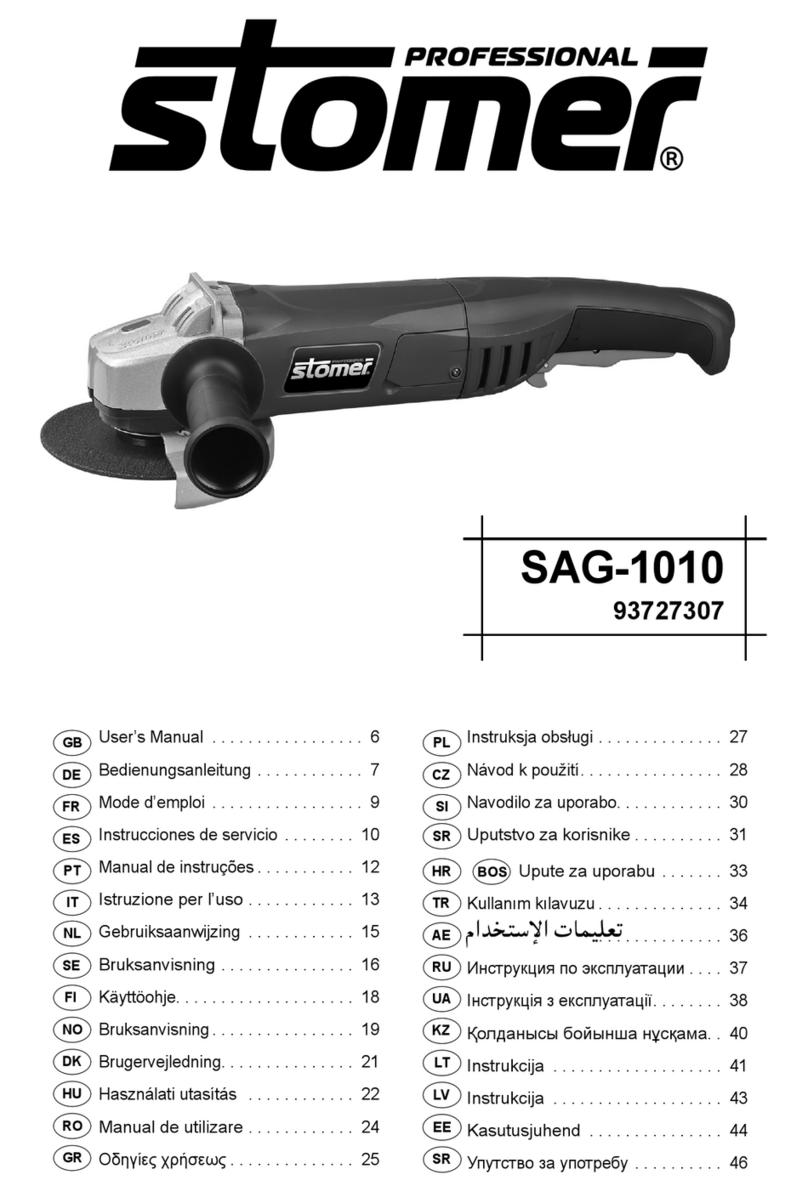
Stomer Professional
Stomer Professional SAG-1010 user manual

Cornwell Tools
Cornwell Tools CAT-530RXL Operating instructions, warning information, parts breakdown