Bochi Machine Tool Group Co. CS6140 Series User manual

CS6140 (CS16″)Series Lathe
CS6140B(CS16″)Series Lathe
Operator’s Manual
Bochi Machine Tool Group Co.,Ltd.
Baoji Zhongcheng Machine Tool Co.,Ltd.
The People’s Republic of China

Notes
1. CS6140 (CS16”) series lathes include the following specifications:
CS6140 (CS16”) CS6240 (CS16”G)
CS6150 (CS20”) CS6250 (CS20”G)
CS6166 (CS26”) CS6266 (CS26”G)
2. CS6140B (CS16B”) series lathe include the following specifications:
CS6140B (CS16”B) CS6240B (CS16”GB)
CS6150B (CS20”B) CS6250B (CS20”GB)
CS6166B (CS26”B) CS6266 B (CS26”GB)
3. This manual is for reference only and its contents are subject to change
without notice.
4. Ticked specification is the machine user purchased.
Max. swing over bed mm
Max.workpiece length mm
Manufacturing No.

Table of contents
1Safety Instructions……………… ……………………………………………………………………1-1
2Application of machine………………………………………………………………………………..2-1
3Technical data………………………………………………………………………………………….3-1
4Machine drive system…………………………………………………………………………………4-1
5Machine operation……………………………………………………………………………………..5-1
6Electrical part of the machine….……………………………………………………………………..6-1
7Lubrication…………………………….……………………………………………………………….7-1
8Coolant unit……………………. …………………….…………………….………………………8-1
9Lifting, installation and test operation………………………………………………………………..9-1
10 Maintenance and care………………………………………………………………………………..10-1
11 Adjustment and structure…………………………………………………………………………….11-1
12 Wear parts of the machine and their machining diagrams……………………………………….12-1
13 Standard accessories, tools and optional accessories……………………………………………13-1
14 Foot brake………………………………………………………………………………………………14-1
15 Taper turning attachment……………………………………………………………………………...15-1
16 Mechanical Feed Stop…………………………………………………………………………………3

CS6140, CS6140B Series Turning Machine Instructions
1
-
1
1Safety Instructions
1.1 General Safety Rules
Operator must read the instructions carefully before operating the machine, and the manager of safety
department should assure the operator knows the requirements well.
1)The operation, maintenance and repair of the machine must be done by qualified persons who have been
trained the ability to forecast the potential risks. Only safety-conscious persons who are fully aware of the
risks can operate the machine.
2)To those people who assemble, operate, or maintain the machine must be confirmed to have read and
understood the operating instructions.
3)After stopping the machine, the chuck will still run for a period of time due to inertia, so you need to pay
extremely attention to the chuck when you remove the chuck guard and fetch the workpiece.
4)Do not detach or modify any safety guard. Be sure that the machine is disconnected from the power when
adjusting, maintenance and repair.
5)Do not dismantle any safety precaution sign attached to the machine. They should always be kept clean
and legible.
WARNING! Never touch the tool or any other driving parts with hands when they are still turning.
6)Assign only special persons to operate, maintain and adjust the machine.
7)Operate the machine in accordance with technological process. Only qualified persons can completely
repair the machine.
8)Use standard spanners and pliers for adjustment and repair.
9)Stop the machine immediately if an abnormality occurs. Ask for qualified persons to check and repair.
10)Dismantle and assembly the machine with the hoisting equipment which is of enough load capacity.
11)Observe all safety instructions and warnings attached to the machine; make sure they are always
complete and perfectly legible.
12)Do safety inspection before operating. Be sure that limit switches for each axis, stop dogs and emergency
stop button are all in good condition.
13)Reinstalled the removed guards and safety devices in place after maintaining.
14)Do maintenance or adjustment only after switch the machine off and remove the plug from the power
source outlet, until all moving parts absolutely stop.
15)Always keep children away from the machine. Operating personal must be at least 18 years of age.
16)Do not wear loose clothing, gloves, neckties or jewelry (rings, watches, etc). Keep the sleeves and the
edges of the work uniform tight. Always be sure to wear safety goggles and safety shoes during
operation.
17)Those with long hair, no matter whether it is a man or woman, should wear safety hat and wrap the hair in

CS6140, CS6140B Series Turning Machine Instructions
1
-
2
when operating.
18)The machine was inspected carefully before shipment from factory. Its noise emission is not higher than
81dB. Wear suitable personal protective equipment when necessary, for instance, wear hearing
protection to reduce the risk of induced hearing loss.
19)Provide adequate light around the machine, and keep the perimeter around the machine dry, clean and in
good order. In addition, do not place anything near the machine; otherwise it becomes an obstacle during
operation.
20)Do not move away any guard during all working.
21)Isolate the machine from the power sources when leaving the machine.
22)Restart the machine only after the guards and safety devices are replaced to their position.
23)Do not place tools, work-pieces or other items on the machine, especially on the moving parts.
24)Do not start the spindle unless the workpiece is clamped completely in the chuck, and the key is taken
away from the chuck and the chuck guard is closed.
25)When chucking an irregular-shaped workpiece, make some adjustments to center of its gravity so that the
workpiece can rotate steadily.
26)Stop the machine before adjusting the position of the coolant nozzles.
27)Avoid as much as possible, using compressed air to remove dust and chips etc. deposited on the
machine, switchboard, NC controller etc.
28)The fixtures to be set on the machine must have sufficient rigidity and proper steps should be taken so that
the surface of the fixtures will be slip-free.
29)Both operators and the maintenance men should read with care the description on the caution plate
attached to the machine. They should observe the precautions on this plate during their work. During
operation and maintenance, care should be used so that this caution plate is not dirtied or damaged..
30)Memorize where the emergency stop push button is so that it can be depressed without delay in case of
an emergency.
31)Follow the starting procedures given in this manual to start the machine.
32)Keep your hands away from the moving parts of the machine during operation.
33)Do not get direct access to the work light when it is on. That may cause being scalded.
34)Never remove chips from machine during operation. Especially do not handle chips with hands.
35)When removing chips caught around the turret or deposited on machine, take them out with a tool instead
of hand, because your hand may be injured. Be sure to stop the machine when removing chips from it.
36)Prior to starting test operation, carefully read this manual so as to be completely familiar withthis machine.
37)Contact this company if for some reason the manual should become unreadable.
38)When setting up a tool, stop the spindle and the feed in each axis.

CS6140, CS6140B Series Turning Machine Instructions
1
-
3
1.2 Additional Safety Rules for machine
WARNING! When using electric tools basic safety precautions should always be followed to reduce the
risk of fire, electrical shock and personal injury including the following:
Read all these instructions before attempting to operate this product and save these instructions.
1) Operating speed of spindle should not exceedpermissible speed of chuck (See Operator’s Manual of Chuck).
2) Do not use a turning tool that is damaged or deformed or unsharp.
3) Be sure that the machine is disconnected from the power when adjusting, maintenance and repair.
4) Besure to switch off the machine when performing periodicalmaintenanceor service.
5) Release the carriage by loosing the lock screws before moving itlongitudinally.
6) Add oil or grease to every oil site including guideways, oil cups and 3 cases for ensuring safe and normal
operation.
7) Use special tools to install turning tool.
8) Wear suitable personal protective equipment when necessary, this could include:
-Eye protection safety goggles
-.Safety hat or headgear for long hair
-Tight work uniform from head to foot
-Safety shoes
-Hearing protection
9) When turning a slender shaft work, recommend to fasten it with a follow rest, or steady rest or tailstock to prevent
it from getting off.
10) Put the machine on a solid foundation.
11) Never machine flammable materials (like magnesiumbar)
12) Always use in a well-ventilated area. Remove dust frequently. Clean out dust from the interior to prevent a
potential hazard.
13) Store idle tools. When not in use, tools should be stored in a dry locked-up place, out of reach of children.
14) Keep the cord away from heat, oil and sharp edges.
15) Stay alert. Watch what you are doing, use common sense and do not operate the tool when you are tired.
16) Inspect the cords and extension cords periodically and if damaged have them repaired or replaced.
17) Have the machine repaired by a qualified person. Using of electric toolsshould compliywith the relevant rules.
18) Repair of important parts should only be carried out by qualified persons using original spare parts, otherwise

CS6140, CS6140B Series Turning Machine Instructions
1
-
4
this may result in considerable danger to the user.
19) When the machine is used outdoor, use only extension cords intended for outdoor use.
20) Recommend to use rust preventive coolant. Important: Coolant must be used in correct ways. Care not to spill it
into eyes or onto skin. If do without intention, wash them with plenty of water and go to see a doctor at once.
21) Recommend to use refined petrolatum per ISO VG46 (GB/T3141 N46) lubricating the guideways, and to use
refined petrolatum per ISO VG32 (GB/T3141 N32) lubricating every cases.
22) Hand tools are not allowed to use on the machine.
23) When repairing the chuck, please follow the requirements of manufacturer. Make sure that the rated speed of
chuck should not be lower than the maximum speed of machine spindle.
24) The machine must be checked for balance and alignment after replacement of fixtures.
25) Be sure to clamp the workpiece completely and not to leave the wrench on the chuck before starting the
machine.
26) When turning a long bar,user must protect the part of bar that stretches out of spindle back end using a guard.
Remove the guard after completion of machining.
27) Irregular-shaped workpieces should be cut at a low speed and in balanced state.
28) The machine should be grounded to reduce risk of getting shocked.
29) Do not operate the machine in flammable, explosive and damp environment.
WARNING! FAILURE TO FOLLOW THESE RULES MAY RESULT IN SERIOUS PERSONAL INJURY.
WARNING! DO NOT EXPOSE THE MACHINE TO RAIN OR IN DAMP LOCATIONS.
Transport:
Move the machine to a location with lifting hooks or forklift truck. Observe the lifting marks painted on the case
when lifting. Lifting can only be started after the case is opened or the skids are removed.
In order to keep balance, move the carriage and tailstock to the extremely right side, and lock them there.
Lift the machine according to Fig. 9-1. Insert a steel bar of 35mm diameter and of 760mm long, and stretch out at
least 100mm away from every side of machine. When lifting, use wire ropes of 12mm (1/2”) diameter. Prevent direct
contact between ropes and machineby insertion of wood or used chipboards. Raise and lower the machine
carefully, and take special care to prevent impact with any object at the time of lowering. During transporting, the
machine should be fastened firmly. The parts easy to be collided should be packed with shock absorption material.
The uncovered parts of the machine such as table should be smeared with anti-rust oil.
Installation:
Prepare sufficient space to put the machine and allow safe operation and normal service.
Requirements: Leave at least 600mm between machine back, tailstock and wall. Mount the machine on flat
concrete ground and adjust the machine level with gradienter, then fasten it.
For training:

CS6140, CS6140B Series Turning Machine Instructions
1
-
5
(1). The operator must be trained for safety and operation before usingthe machine.
(2). Be sure to disconnect power supply before making some adjustment and performing service..
(3). Always wear gloves when handling tools or cutters.
For work-piece guiding the use of:
(1). The work-piece is possible to be made of the following materials:
-steel
-casting
-copper
(2). The work-piece is possible to take the following shapes:
-cylindrical
-disk
-pipe
-irregular shape
If the work-piece may affect the process due to unbalance itshould be treated additionally. For example, an
irregular shaped workpiececan be cut by adding a weight.
WARNING: FAILTURE TO FOLLOW THESE RULES MAY RESULT IN SERIOUS PERSONAL INJURY.
1.3Limitations on ambient conditions
The machine is designed for operating on the site:
-The height above sea level doesn’t exceed 1000m;
-The temperature range of air doesn’t exceed 5℃~40℃
-The relative humidity doesn’t exceed 50% or 90% at a maximum temperature of +40℃or +20℃.
-Transportation and storage temperature range is -25℃~+55℃.
1.4Notes on handling Electrical Unit
When operating the machine or performing check and maintenance, observe the following notes.
(1) Be careful not to touch and jolt the NC controller and the electric circuits.
(2) Be sure to use a wire or cable of proper length for connecting power supply to the machine. When the power
wire or cable inevitably runs across the floor, take adequate measures to protect it against damage from chips
etc.
(3) Do not change the value of current, which has been set with the thermal relay on the distribution board, or other
values set previously to various volumes. Use breakers specified in the operation manual for replacement.
(4) Before checking and maintaining the electrical apparatus, turn off the power switch of the control panel, and the

CS6140, CS6140B Series Turning Machine Instructions
1
-
6
main switch of the distribution board. In addition, turn off the power switch supplying power from the plant to the
machine. Proceed with checks and maintenance only upon confirmation that the power has indeed been cut off.
If possible, the power supply should be locked in the off-position during checks and maintenance, or else signs
should be posted warning that the maintenance is being performed and no operation is permitted.
(5) Handle the electrical apparatus of machine with cautions and pay attention to their water proofness.
(6) An external power supply cable should be prepared by user, which must be larger in diameter than that specified
by the manual. Use over voltage protects. Cable in bottom of cabinet should be fixed with cable connector.
(7) Rated input voltage with fluctuation: 220V/380V/400V/415V/420V/440V/500V/575V/600V/660V±10%
(8) Rated input frequency: 50Hz/60Hz±1 Hz
(9) Phase: 3-phase AC, grounding
(10) Ambient temperature and humidity should be controlled as steady as possible so that there is no violent
change.
(11) Do not expose the machine as well as the electric unit to environment where corrosive gas or liquid exist such
as acid, alkali and salt.
(12) Do not expose the machine as well as the electric unit to dusty environment. Avoid dust accumulating on any
parts of machine.
(13) Do not expose the machine as well as the electric unit to magnetic or electrostatic environment.
Table of electric data
Rated voltage
Frequency Phase Total Current IP grade
220V 50Hz/60Hz 363A IP54
380V/400V 50Hz/60Hz 350A IP54
415V~660V 50Hz/60Hz 340A IP54
1.5Safety precaution signs on machine
DANGER
Never touch the parts of machine attached with this sign.
WARNING AND CAUTION
Proper precautions should be taken.

CS6140, CS6140B Series Turning Machine Instructions
1
-
7
External power cable should be correctly connected to terminals
marked by this sign.
Do not operate during turning of spindle.

CS6140, CS6140B Series Turning Machine Instructions
2
-
1
2Applicationof machine
2.1 This lathe in series can perform many operations, such as internal and external turning, taper turning, facing,
threading of metric, module and DP threads, drilling, boring and groove broaching.
2.2 Gap-bed lathe, additionally, can machine all kinds of flat stocks and those in irregular shapes.
2.3 Machining accuracy: circularity deviation less than 0.01 mm, cylindricity deviation not more than 0.02 mm for a
measured length of 200 mm, surface finish is excellent.
2.4 B series lathe with ø 82(3 15/64") thru-bore spindle, can hold bar stocks in larger diameter.
2.5 There are inch measure feeding mechanism and metric measure feeding mechanism for users to choose. So it
is easy for people from different measure countries to operate.
2.6 There are hand brake and foot brake for users to choose.
2.7 The lathe operates on power supply of different voltages (220V, 380V, 420V) and different frequencies (50Hz,
60Hz).
2.8 The lathe has a wide range of optional accessories for users to select.

CS6140, CS6140B Series Turning machine Instructions
3
-
1
3Technical data
Table 3-1 Technical data
Model
Data
Item
CS6140 CS16"
CS6140B CS16"B
CS6240 CS16"G
CS6240B CS16"GB
CS6150 CS20"
CS6150B CS20"B
CS6250 CS20"G
CS6250B CS20"GB
CS6166 CS26"
CS6166B CS26"B
CS6266 CS26"G
CS6266B CS26"GB
Max. swing over bed ?400(16") ?500(20") ?660(26")
Max. swing over slide ?220(8") ?300(12") ?420(17")
Max. swing over gap ?630(25") ?710(28") ?870(34")
Effective length in gap 240(9")
Max. workpiece length 750/1000/1500/2000/2500/3000(30"/40"/60"/80"/100"/120")
Max. turning length 700/950/1450/1950/2450/2950(28"/38"/58"/75"/96"/116")
Spindle thru-hole ?52(2 3/64") B series ?82(3 15/64")
Dia. and taper of spindle bore MT.No.6 B series ?90 1:20(3 35/64" 1:20)
Spindle nose ISO 702/ⅢNo.6 bayonet type B series ISO 702/ⅡNo.8 short cam-lock type
Spindle speeds 24-step 9—1600r/min
Max. output torque of spindle 1400N.m(1013 lbf.ft) 1200N.m(885 lbf.ft)
Number and range of long. feeds
Standard 0.063-2.52mm/r 65 sorts,(0.0023-0.0937in/r,65)
Decreased 0.028-0.056mm/r 13 sorts, (0.0010-0.0021in/r,13)
Increased 2.86-6.43mm/r 15 sorts,(0.1064-0.2392in/r,15)
Number and range of cross feeds
Standard 0.027-1.07mm/r 65 sorts, (0.0011-0.0404in/r,65)
Decreased 0.012-0.026mm/r 13 sorts, (0.0004-0.0010in/r,13)
Increased 1.21-2.73mm/r 15 sorts, (0.0457-0.1032in/r,15)
Number and range of threading
Metric threads 0.5-224 48 sorts
Inch threads 72-1/8tpi 46 sorts
Module threads 0.5-112 42 sorts
D.P. threads 56-1/4DP 45 sorts
Longitudinal rapid traverse 4.5m/min(15ft/min)50Hz 5.4m/min(18ft/min)60Hz
Cross rapid traverse 1.9m/min(6.37ft/min)50Hz 2.3m/min(7.67ft/min)60Hz
Pitch of leadscrew 12(2tpi)
Height of spindle to bearing surface
of tool 28(1 3/32")
Tool section 25mm×25mm(1"×1")
Swivel angle of fourway tool post ±90°

CS6140, CS6140B Series Turning machine Instructions
3
-
2
Model
Data
Item
CS6140 CS16"
CS6140B CS16"B
CS6240 CS16"G
CS6240B CS16"GB
CS6150 CS20"
CS6150B CS20"B
CS6250 CS20"G
CS6250B CS20"GB
CS6166 CS26"
CS6166B CS26"B
CS6266 CS26"G
CS6266B CS26"GB
Max. travel of compound rest 145 (5 3/4")
Max. travel of cross slide 320 (12 5/8") 310 (12 1/8")
Max. permissible cutting force(Pz) 14000N(3086 lbf) 12000N(2643 lbf)
Max. permissible feeding force(Px) 3500N (772 lbf)
Tailstock quill diameter 75(2 61/64")
Taper of tailstock quill MT No.5
Max. travel of quill 150 (5 29/32")
Cross move of tailstock ±15 (±19/32")
Main motor type, power
and speed Y132M ,7.5kW(10HP) 1450r/min(50Hz),1750r/min(60Hz)
Rapid traverse motor type, power
and speed 2AOS,5632,250W(0.34HP),1360r/min(50Hz), 1750r/min(60Hz)
Coolant pump type, power and flow
50L/min(11gal/min)
V-belt B2108 4 pieces B2184 4 pieces B2337 4 pieces
Machine net weight
750(30") 1975kg(4354 lb) 2052kg(4520 lb) 2150kg(4735 lb)
1000(40") 2050kg(4520 lb) 2100kg(4630 lb) 2200kg(4845 lb)
1500(60") 2250kg(4960 lb) 2300kg(5070 lb) 2400kg(5286 lb)
2000(80") 2450kg(5400 lb) 2500kg(5510 lb) 2600kg(5727 lb)
2500(100") 2650kg(5840 lb) 2700kg(5950 lb) 2800kg(6168 lb)
3000(120") 2850kg(6280 lb) 2900kg(6390 lb) 3000kg(6610 lb)
Machine dimensions(L×W×H)
750(30") 2382×975×1230 2382×975×1270 2382×975×1350
94"×38 3/8"×48 7/16" 94"×38 3/8"×50" 94"×38 3/8"×53"
1000(40") 2632×975×1230 2632×975×1270 2632×975×1350
104"×38 3/8"×48 7/16" 104"×38 3/8"×50" 104"×38 3/8"×53"
1500(60") 3132×975×1230 3132×975×1270 3132×975×1350
123"×38 3/8"×48 7/16" 123"×38 3/8"×50" 123"×38 3/8"×53"
2000(80") 3632×975×1230 3632×975×1270 3632×975×1350
143"×38 3/8"×48 7/16" 143"×38 3/8"×50" 143"×38 3/8"×53"
2500(100") 4132×975×1230 4132×975×1270 4132×975×1350
163"×38 3/8"×48 7/16" 163"×38 3/8"×50" 163"×38 3/8"×53"
3000(120") 4632×975×1230 4632×975×1270 4632×975×1350
183"×38 3/8"×48 7/16" 183"×38 3/8"×50" 183"×38 3/8"×53"

CS6140, CS6140B Series Turning machine Instructions
4
-
1
4Machine drive system
4.1 Tables and diagrams
Fig.4-1 shows the machine’s drive system. Table 4-1 lists all the metric parts while Table 4-2 lists all the inch
parts. Every bearing in drive system is listed in Table 4-3 and their positions are illustrated in Fig. 4-2.

CS6140, CS6140B Series Turning machine Instructions
4
-
2
Right handwheel drive system diagram
Fig. 4-1 Drive system diagram

CS6140, CS6140B Series Turning machine Instructions
4
-
3
Fig. 4-2 Bearing location diagram

CS6140, CS6140B Series Turning machine Instructions
4
-
4
Table 4-1 List of metric drive parts
Name
No. Part
No. No.of teeth
or starts Module or
pitch Position
change ratio
or start dir. Helix / profile
angle Material
Heat
treat-ment
102081 45
202082 45 45 G48
302083 40
402084 36
502085 28
602086 32
40Cr G52
702106 48 45 G48
802087 32
902089 36
10 02091 44
11 02088 40
12 02092 36
13 02092 20
40Cr G52
14 02105 32 +0.525 45 G48
15 02093 45
16 02094 61
2.5
40Cr G52
17 02095 30
18 02095 17
19 02096 48
20°
20 02056 16 Left
21 02097 17
22 02098 60 Right
45 G48
23 02099 20
3
L+0.5868
20°/13º10"
40Cr G48
24 *B02104 48 20°
25 *B02102 40 Left
26 *B02101 80 3R-0.5868 20°/13º10" 45 G48
27 02114 32
28 02103 26 40Cr G48
29 02107 48
30 02108 31
2.5 20°
45 G48
31 02108 31 45 G48
32 02111 18 40Cr G48
Head-
stock
33 02109 31 45 G48

CS6140, CS6140B Series Turning machine Instructions
4
-
5
To continue from the above table 4-1
Name No.
Part No. No.of teeth
or starts Module
or pitch
Position
change ratio
or start dir. Helix / profile
angle Material Heat
treat-
ment
34
08042 60 45
35
08043 69 Nylon MC
36
08041 56
Change
gear
37
08044 57
?2
/2.25
/2.75
20°
45
38
07061 28 2.25 +0.6
39
07061 30 1.75
40
07062 27 2.25 -0.1323
41
07063 41 1.75 +0.5254
42
07064 30 2.25 -0.3323
43
07064 29 1.75 +0.5731
44
07066 21 3+0.50
45
07066 28 2+0.30
46
07073 20 +0.04256
47
07072 118 +01.352
48
07071 21
3
-0.50
49
07069 36 +0.7687
50
07068 32 +1.444
51
07067 33
2
+0.8117
52
07065 30 1.75
53
07066 21 3+0.50
54
07066 28 2+0.30
55
07032 14
56
07032 22 +0.40
57
07076 42 -0.40
58
07077 33 +0.1323
59
07078 15 +0.5324
60
07079 24
2.25
61
07074 22 +0.40
62
07074 40
63
07074 32
64
07075 21
65
07034 21 +0.25
Feeding
case
66
07038 42
2
-0.25
20° 45 G42

CS6140, CS6140B Series Turning machine Instructions
4
-
6
To continue from the above table 4-1
Name
No.
Part
No. No.of teeth
or starts Module or
pitch
Position
change ratio
or start dir.
Helix /
profile
angle Material Heat
treat-
ment
67
06061 36 40Cr
68
06062 32 45
69
06063 56 1.5 20° GCr15
70
06057 26º20'25" 45
71
06021 26 2.5 6º20'25" ZcuSn10Pb1
72
06064 32 45
73
06065 36 1.75 Left 20° 45 G48
74
06065 36 45
75
06066 45
76
06066 45 40Cr
77
06069 87
1.75 Left
78
06052 12 +0.249
79
01024 Rack 2.5036
80
06071 18 1.75
81
06072 28
82
06073 20
83
06074 89 1.5
45 G48
84
06066 G52
85
06066 45 40Cr G48
86
06067 35
87
06068 58
1.75 45 G48
88
06022 ZcuSn10Pb1
Apron
89
01021 112
20°
Y40Mn
79
01024A
2.5036 45
89
01021A
12 20° Y40Mn
70
06057A
22.5 Left 6º20'25"
RH
apron
78
06052A
12 2.5036 +0.049 45 G48
90
05031 18 1.75 Left 20° 40Cr D0.3-550
91
05021 Y40Mn
92
05011
93
04011 HT200
Tool
post
94
04031
95
03022 Y40Mn
Tail-
stock 96
03005
15
HT150
15002
?115
97
15002/
60Hz ? 93Pulley
98
02003 ? 175
B type HT150

CS6140, CS6140B Series Turning machine Instructions
4
-
7
Table 4-2 List of inch drive parts
Name No.
Part
No.
No.of
teeth or
starts
Module or
pitch
Position
change ratio
or start dir.
Helix / profile
angle Material Heat
treat-
ment
34
08042Y
82
35
08043Y
57
36
08041Y
81
Change
gear
37
08044Y
69
1.5/2.25 20° 45
81
06072Y
30
82
06073Y
28
83
06074Y
97
1.5 45
88
06022Y
ZcuSn10Pb1
Apron
89
01021Y
12.7
20°
Y40Mn
91
05021Y
Y40Mn
92
05011Y
ZcuSn10Pb1
93
04011Y
HT200
Tool post
94
04031Y
1
5.08
Y40Mn
Note: Part No. of CS6140B series are marked by asterisk *.
This manual suits for next models
1
Table of contents
Popular Lathe manuals by other brands
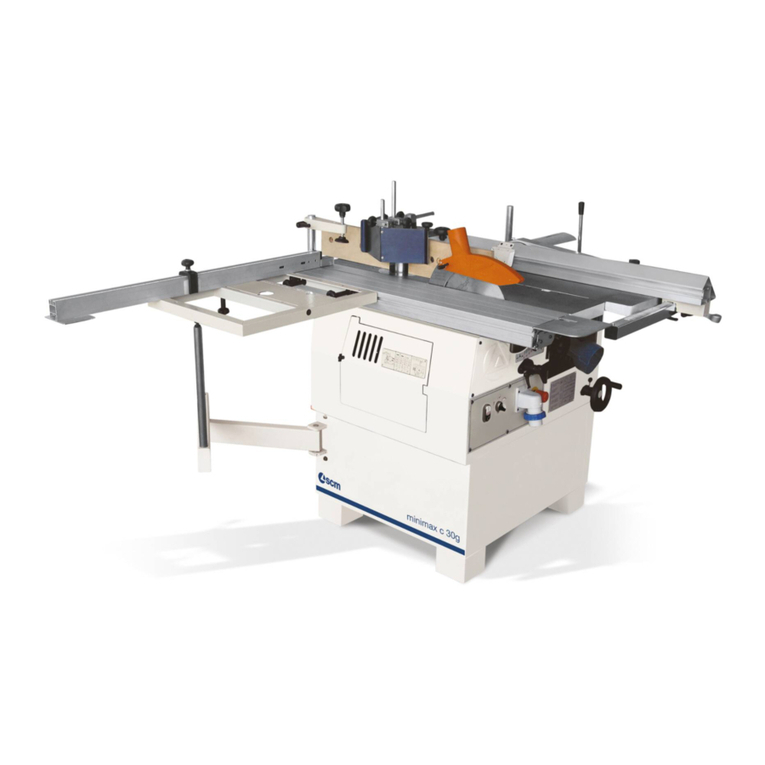
MiniMax
MiniMax C 26 GENIUS Operation and maintenance
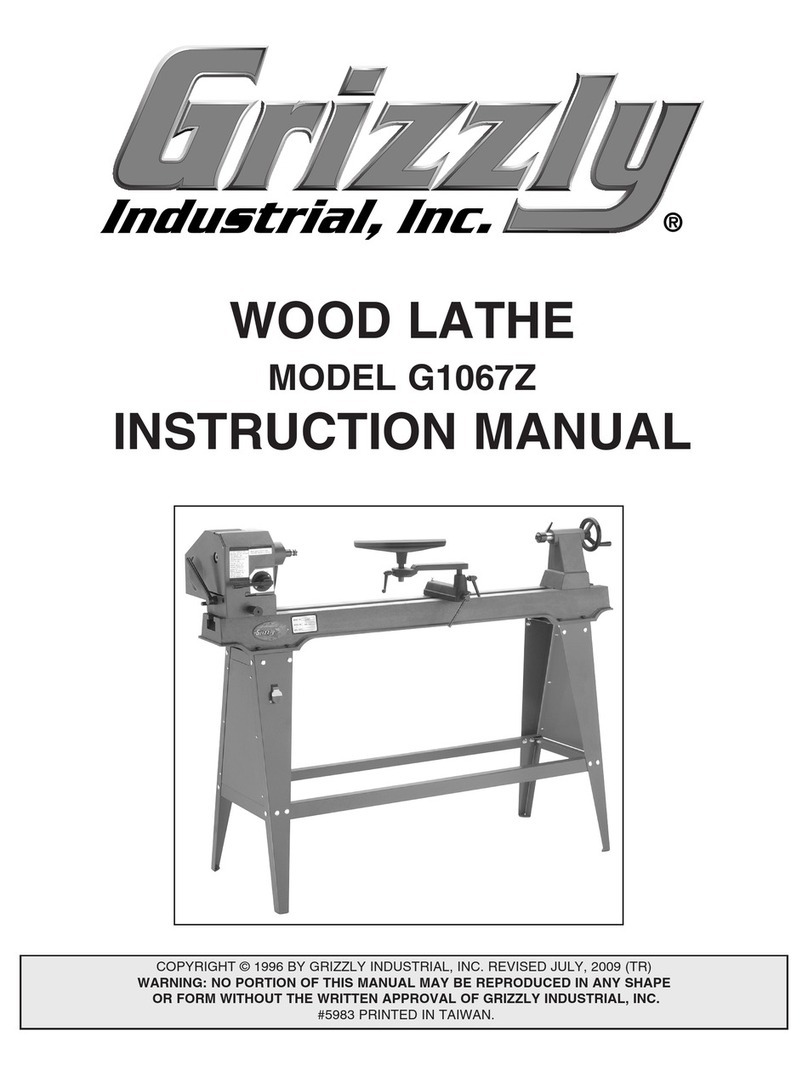
Grizzly
Grizzly G1067Z instruction manual

Denford
Denford TURN 270 PRO Installation & commissioning guide
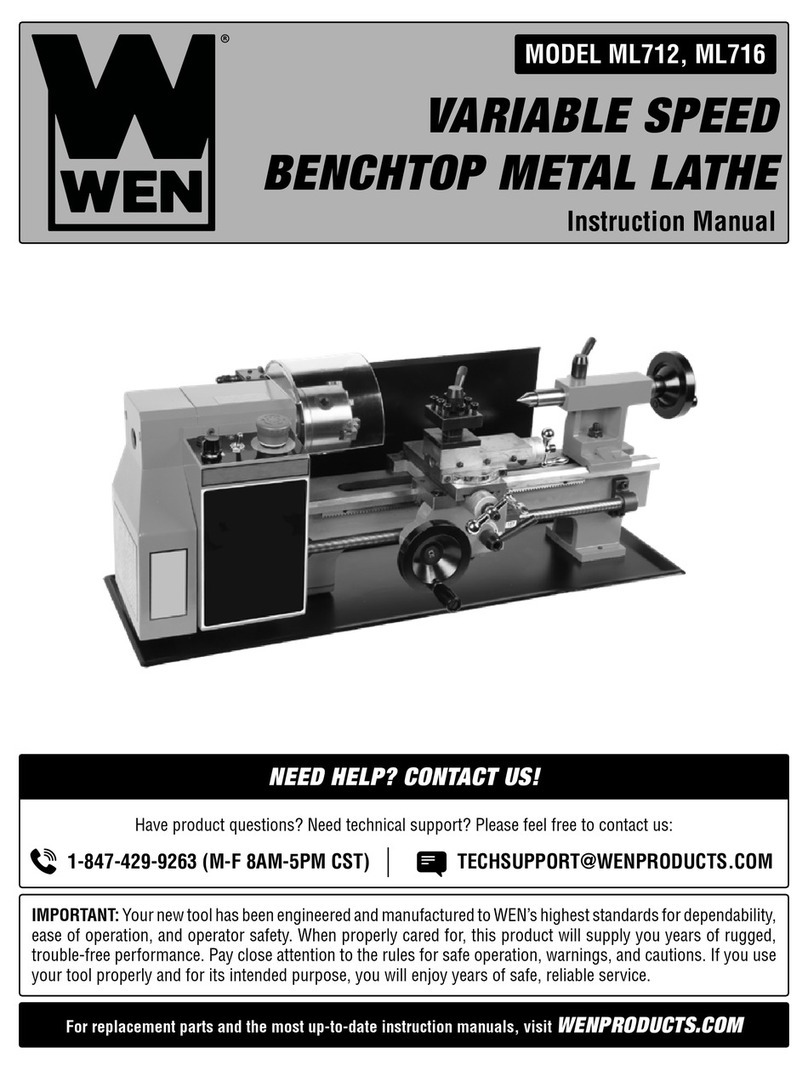
Wen
Wen ML712 instruction manual
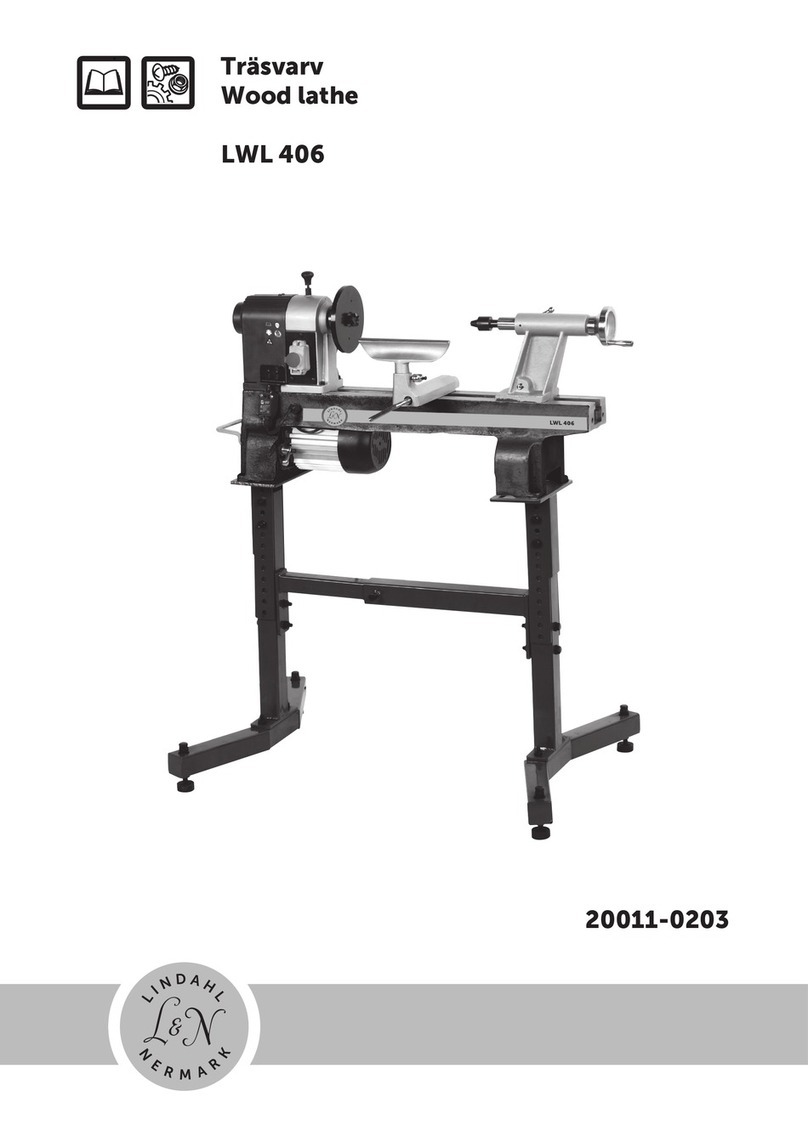
Lindahl & Nermark
Lindahl & Nermark LWL 406 Original instructions
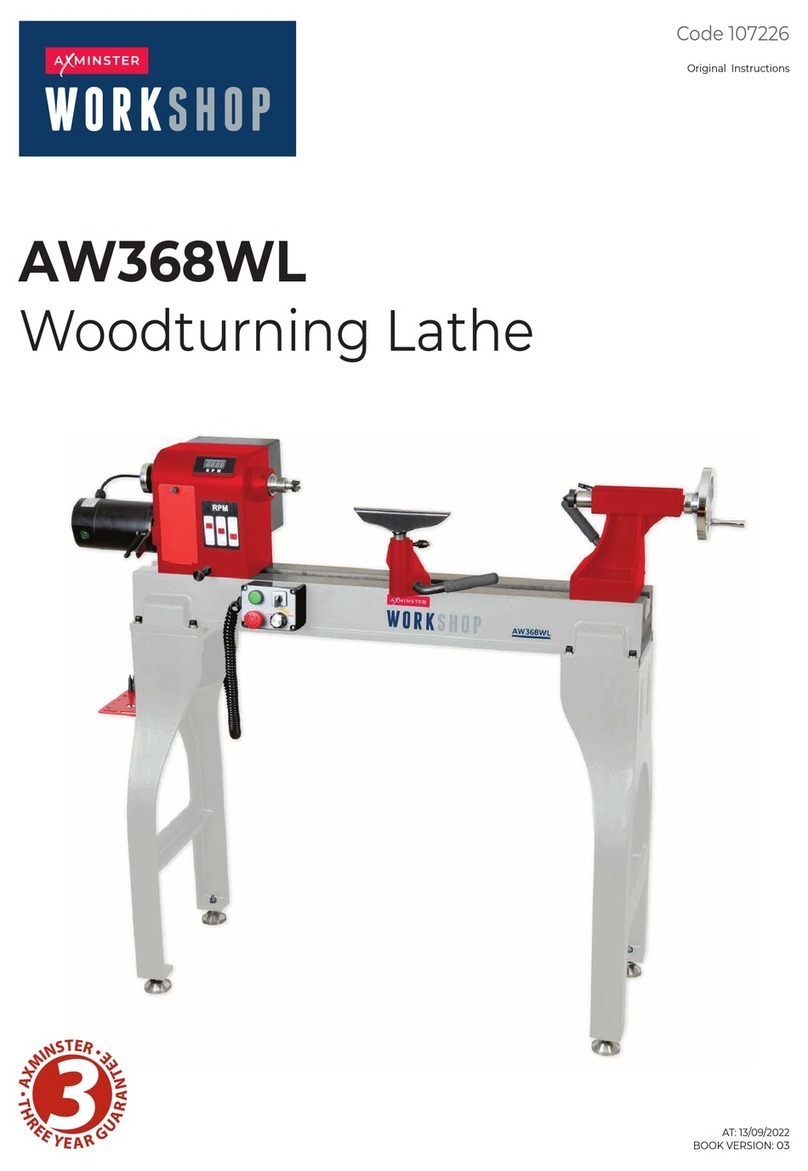
AXMINSTER WORKSHOP
AXMINSTER WORKSHOP AW368WL Original instructions