BRONKHORST ES-FLOW Series User manual

Liquid Dosing Control Manual
Dosing functions and parameter overview
9.17.150 REV A
September 2020

Liquid Dosing Control Manual 9.17.150 rev A – September 2020
Page 2of 34
Introduction ................................................................................................................................................... 3
1. Reference documents ........................................................................................................................... 4
2. Connect and Configure ......................................................................................................................... 5
2.1 Connect with the device ............................................................................................................... 5
2.1.1 Via FlowDDE and FlowPlot ...................................................................................................... 5
2.1.2 Via FlowSuite............................................................................................................................ 5
2.1.3 Via user specific control platform.............................................................................................. 5
2.2 Modify controller configuration...................................................................................................... 5
2.2.1 Disable and Enable protected mode ........................................................................................ 5
2.2.2 Change configuration from Flow Meter to Flow Controller ....................................................... 5
2.2.3 Change Flow Settings – Mass or Volume ................................................................................ 6
2.2.4 Change Flow Settings – Capacity Unit ..................................................................................... 8
2.2.5 Change Flow Settings – Capacity Value .................................................................................. 9
2.2.6 Dosing specific settings – Response Alarm / Dry Running Protection Alarm ........................ 10
2.2.7 Dosing specific settings – OUT signal to external device....................................................... 11
2.2.8 Ratio dosing specific configuration settings ........................................................................... 12
2.2.9 Batch dosing specific configuration settings........................................................................... 13
3. Prepare for operation .......................................................................................................................... 17
3.1 Fill the system............................................................................................................................. 17
3.2 Flush the system ........................................................................................................................ 18
3.3 Verify system status ................................................................................................................... 21
3.4 Zero procedure ........................................................................................................................... 22
4. Operate the Liquid Dosing Set ............................................................................................................ 23
4.1 Start dosing................................................................................................................................. 23
4.1.1 Continuous Dosing ................................................................................................................. 23
4.1.2 Ratio Dosing ........................................................................................................................... 24
4.1.3 Batch Dosing .......................................................................................................................... 24
4.2 Pause dosing .............................................................................................................................. 25
4.3 Stop dosing................................................................................................................................. 25
4.4 Read parameters ........................................................................................................................ 26
5. Optimize control settings ..................................................................................................................... 28
5.1 Changing Filter Settings ............................................................................................................. 28
5.2 Actuator Control Speed .............................................................................................................. 29
5.3 Adjust Proportional and Integral value (Kp and Ti)..................................................................... 29
5.4 Correct for actuator delay ........................................................................................................... 30
5.5 Setpoint Slope ............................................................................................................................ 30
5.6 Batch Dosing specific control optimization ................................................................................. 31
5.6.1 Minimize ON/OFF Valve temperature .................................................................................... 31
5.6.2 Tune the Batch Counter Controller......................................................................................... 31
5.6.3 General guide for batch dosing optimization based on observation ...................................... 32
6. Parameters .......................................................................................................................................... 33

Liquid Dosing Control Manual 9.17.150 rev A – September 2020
Page 3of 34
Introduction
This document provides a description of functions required for a successful operation of the Liquid Dosing
Set (LDS). These functions are listed in detail, including applicable pre-conditions, manual actions and
involved instrument parameters.
The scope for this version of the document includes:
Bronkhorst controlling instrument
- ES-FLOW series
- mini CORI-FLOW M-series
- mini CORI-FLOW MI-series
- mini CORI-FLOW ML-series
- CORI-FLOW M-series
Actuator
- Pumps
- Valves
Functions for setup and operation
- Connect and configure settings
- Prepare for Operation
- Start, pause and stop dosing
For the ease of reading:
- Instructions are for all instruments and written for an RS232 interface using a Proces
Parameter (ProPar) protocol, and references are made to Dynamic Data Exchange (DDE)
parameter numbers, which are unique numbers for parameter identification.
- Chapter 1 contains a table with reference documentation, uncluding dedicated manuals for
fieldbus specific communication instructions.
- Where instructions deviate for specific instruments, this will be clearly noted
- Fieldbus specific parameters will be provided
- Instructions are for all types of actuators, unless specific deviations are noted
- Instructions for (manual) operator actions are shown in blue
- Programmable interactions or system control and parameter readout are shown in red
Note
this document does not include any instructions or recommendations on the installation and connection of
the Liquid Dosing Set.
Image 1 - Example of a Liquid Dosing Set

Liquid Dosing Control Manual 9.17.150 rev A – September 2020
Page 4of 34
1. Reference documents
The documentation listed can be downloaded from www.bronkhorst.com/downloads
Type
Document
Document number
Manual
Manual DeviceNet™ interface
9.17.026
EtherNet/IP interface
9.17.132
CANopen interface
9.17.131
EtherCAT® interface
9.17.063
FLOW-BUS interface
9.17.024
Modbus ASCII / RTU / TCP interface
9.17.035
PROFIBUS DP interface
9.17.025
PROFINET interface
9.17.095
RS232 interface
9.17.027
Manual
Instruction Manual mini CORI-FLOW ML120
9.17.097
Manual
Instruction Manual CORI-FILL
9.17.075
Manual
Installation Manual – Liquid Dosing Sets
9.17.146
E-book
How to handle low liquid flows
Release October 2020

Liquid Dosing Control Manual 9.17.150 rev A – September 2020
Page 5of 34
2. Connect and Configure
2.1 Connect with the device
Several methods to open connection with the Bronkhorst controlling instrument
2.1.1 Via FlowDDE and FlowPlot
Refer to the instrument manual for details
2.1.2 Via FlowSuite
Find out more about FlowSuite on our website.
2.1.3 Via user specific control platform
Refer to the manual of the used platform.
Bronkhorst offers Fieldbus specific configuration files.
2.2 Modify controller configuration
2.2.1 Disable and Enable protected mode
To prevent accidental changes to the instrument settings, a Protection mode has been
automatically enabled. Disabling this mode is required at several steps throughout this document.
After making the required changes, it is strongly recommended to enable the protection mode
again.
Parameters marked with a symbol can only be changed after disabling the protected mode
Disable protected mode
- Write value 64 to parameter 7 – Init Reset (unlock secured parameters)
Enable protected mode
- Write value 82 to parameter 7 – Init Reset (lock secured parameters)
2.2.2 Change configuration from Flow Meter to Flow Controller
When the Bronkhorst instrument has been purchased as a controller, then the controller functions
have been enabled. If an instrument was originally purchased as a flow meter and needs to be
configured as a controller, then please contact your local Bronkhorst representative for support.

Liquid Dosing Control Manual 9.17.150 rev A – September 2020
Page 6of 34
2.2.3 Change Flow Settings – Mass or Volume
(mini) CORI-FLOW
The Bronkhorst Coriolis based flow meters are mass flow meters.
Setpoint and measurement values can be displayed in volume flow units using an internal
conversion.
3 options are currently available (not for CORI-FLOW M54 / M55).
Disable protected mode
- Write value 64 to parameter 7 – Init Reset (unlock secured parameters)
Option A – Mass Flow (default)
- Write value 0 to parameter 243 – Capacity Unit Type Index (set to mass flow mode)
Option B – Volume Flow with fixed density (volume flow mode)
- Write value 1 to parameter 243 – Capacity Unit Type Index (set to volume flow mode)
Set fixed fluid density value
- Write value <density> to parameter 170 – Density (density value in [kg/m3])
Option C – Actual Volume Flow using measured density (actual converted volume flow)
- Write value 4 to parameter 243 – Capacity Unit Type Index (set to actual volume flow mode)
Read measured fluid density value (for reference)
- Read value [kg/m3] from parameter 270 – Actual Density (density measurement)
Note on Actual Volume Flow mode
Using the instrument for measuring volume flows (e.g. l/h, ml/min) will introduce an additional
inaccuracy, based on the actual density measured by the instrument.
Enable protected mode
- Write value 82 to parameter 7 – Init Reset (lock secured parameters)
Step DDE ProPar Name
Data
Type
Execute
Value Remark
Unlock Secured Parameters
1
7
0/10
Init Reset
Uint8
write
64
Unlock secured parameters
Mass Flow
2 243 1/29
Capacity Unit Type
Index
Uint8
write 0 Mass Flow
Volume Flow
2 243 1/29
Capacity Unit Type
Index
Uint8
write 1 Volume Flow (with fixed density)
3 170 33/21 Density
Float
write <density> Density for the fluid [kg/m3]
Actual Volume Flow
2 23 1/29
Capacity Unit Type
Index
Uint8
write 4
Actal Volume Flow (with measured
density)
3 270 116/15 Actual Density
Float
read <density>
Measured density for the fluid
[kg/m3]
Lock Secured Parameters
4
7
0/10
Init Reset
Uint8
write
82
Lock secured parameters

Liquid Dosing Control Manual 9.17.150 rev A – September 2020
Page 7of 34
ES-FLOW
The Bronkhorst Ultrasonic based flow meters are volume flow meters.
Setpoint and measurement values can be displayed in mass flow units using an internal
conversion.
2 options are currently available.
Disable protected mode
- Write value 64 to parameter 7 – Init Reset (unlock secured parameters)
Option A – Volume Flow (default)
- Write value 1 to parameter 243 – Capacity Unit Type Index (set to volume flow mode)
Option B – Mass Flow with fixed density (converted mass flow mode)
- Write value 0 to parameter 243 – Capacity Unit Type Index (set to mass flow mode)
Set fixed fluid density value
- Write value <density> to parameter 170 – Density (density value in [kg/m3])
Enable protected mode
- Write value 82 to parameter 7 – Init Reset (lock secured parameters)
Step DDE ProPar Name
Data
Type
E
xecute
Value Remark
Unlock Secured Parameters
1
7
0/10
Init Reset
Uint8
write
64
Unlock secured parameters
Volume Flow
2 23 1/29
Capacity Unit Type
Index
Uint8
write 1 Volume Flow
Mass Flow
2 23 1/29
Capacity Unit Type
Index
Uint8
write 0 Mass Flow (with fixed density)
3 170 33/21 Density
Float
write <density> Density for the fluid [kg/m3]
Lock Secured Parameters
4
7
0/10
Init Reset
Uint8
write
82
Lock secured parameters

Liquid Dosing Control Manual 9.17.150 rev A – September 2020
Page 8of 34
2.2.4 Change Flow Settings – Capacity Unit
The options for the capacity unit can be found in the table below.
Changing between mass flow or volume flow can affect the displayed capacity unit.
Capacity unit index
FLOW-DDE 23
Mass-flow
(Actual)
Volume Flow
0
kg
/
h
l
/
min
1
kg
/
min
ml
/
h
2
kg
/
s
ml
/
min
3
g
/
h
l
/
h
4
g
/
min
mm3
/
s
5
g
/
s
cm3
/
min
6
mg
/
h
m3
/
h
7
mg
/
min
ul
/
min
8
mg
/
s
Disable protected mode
- Write value 64 to parameter 7 – Init Reset (unlock secured parameters)
Change Capacity Unit Index
- Write value <index>to parameter 23 – Capacity Unit Index (capacity unit index)
Enable protected mode
- Write value 82 to parameter 7 – Init Reset (lock secured parameters)
Step DDE ProPar Name
Data
Type
Execute
Value Remark
Unlock Secured Parameters
1
7
0/10
Init Reset
Uint8
write
64
Unlock secured parameters
Volume Flow
2 23 1/15 Capacity Unit Index
Uint8
write <index> Unit index
Lock Secured Parameters
3
7
0/10
Init Reset
Uint8
write
82
Lock secured parameters
Alternative: Instruments in the ES-FLOW, ML- and MI-series automatically change to Mass or
Volume mode when only changing the Capacity Unit.
Step DDE ProPar Name
Data
Type
Execute
Value Remark
Unlock Secured Parameters
1
7
0/10
Init Reset
Uint8
write
64
Unlock secured parameters
Volume Flow
2 129 1/31 Capacity Unit
String
write <index> Unit
Lock Secured Parameters
3
7
0/10
Init Reset
Uint8
write
82
Lock secured parameters

Liquid Dosing Control Manual 9.17.150 rev A – September 2020
Page 9of 34
2.2.5 Change Flow Settings – Capacity Value
The instrument has a set minimum and maximum Full Scale capacity, which are the operating
limits of the instrument as set by Bronkhorst according to the specification sheet.
The Capacity Value can be changed between these minimum and maximum values.
Situations where changing the Capacity Value can benefit the dosing application:
- An oversized instrument is selected because of a larger sensor tube diameter (lower
pressure drop). The Capacity Value can be adjusted to match the application.
Example: An instrument with a maximum flowrate of 30 kg / h is used for an application
operating at a maximum of 10 kg / h, resulting in a flow measurement of 33.3%.
Lowering the Capacity Value to 10 kg / h to match the application will result in a
flow measurement of 100%, which can be beneficial for monitoring and logging
purposes.
- The setup is used for flows in both the lower range and higer range of the instrument.
Changing the capacity value to match the desired flow rate can increase the resolution of the
measurement data.
- The Bronkhorst instrument sends an Analog signal to another instrument. The resolution of
the analog signal improves when the Capacity Unit is in the same range as the process flow.
Please note that by changing the Capacity Unit, the analog out signal can change as well,
and the receiving instrument might need to be adjusted
- A Ratio control setup where the setpoint (Slave Factor) is calculated using the Capacity
Value (100% point) of the instrument. Adjusting this value can help to determine the ratio
control setpoint.
Disable protected mode
- Write value 64 to parameter 7 – Init Reset (unlock secured parameters)
Change Capacity Value
- Write value <flow> to parameter 21 – Capacity (Full Scale capacity value)
Use the same flow measurement unit as configured in the Capacity Unit section
Enable protected mode
- Write value 82 to parameter 7 – Init Reset (lock secured parameters)
Step DDE ProPar Name
Data
Type
Execute
Value Remark
Unlock Secured Parameters
1
7
0/10
Init Reset
Uint8
write
64
Unlock secured parameters
Volume Flow
2 21 1/13 Capacity
Float
write <capacity> Full Scale Capacity in Capacity Unit
Lock Secured Parameters
3
7
0/10
Init Reset
Uint8
write
82
Lock secured parameters

Liquid Dosing Control Manual 9.17.150 rev A – September 2020
Page 10 of 34
2.2.6 Dosing specific settings – Response Alarm / Dry Running Protection Alarm
Enable Response Alarm / Dry Running Protection Alarm
The response alarm is setup to trigger when the measured value does not reach the setpoint
within a certain time. A band around the setpoint must be configured in which the measure is
valid. The range in which the measure should be is setpoint + Maximum Limit and setpoint –
Minimum Limit.This alarm can be useful to indicate a potential problem in the liquid flow setup.
Examples
- Liquid supply vessel is empty
- Blocked fluid lines preventing liquid to be supplied or blocking the flow downstream
- Tubing is incorrectly dimensioned
For pump systems this alarm can be used to prevent Dry Running, which can damage the pump
head and reduce the lifetime.
Disable protected mode
- Write value 64 to parameter 7 – Init Reset (unlock secured parameters)
Enable and set the Response Alarm
- Write value 2 to parameter 118 - Alarm Mode (enable response alarm)
Value 0 = alarm disabled
Value 2 = alarm on limits related to setpoint (response alarm) 100%
- Write <delay time> to parameter 182 – Alarm Delay Time (delay before alarm)
Value defined in seconds between detection and triggering an actual alarm
- Write <maximum limit> to parameter 116 – Alarm Maximum Limit (0 – 32000)
- Write <minimum limit> to parameter 117 – Alarm Minimum Limit (0 – 32000)
0 – 32000 = 0 – 100%
A limit of 5% translates to a value of 1600
Define action when alarm triggers
- Write <setpoint mode> to parameter 120 – Alarm Setpoint Mode (enable alarm action)
Value 0 = no action
Value 1 = change setpoint to ‘Alarm new Setpoint’
- Write <alarm new setpoint> to parameter 121 – Alarm New Setpoint (new setpoint)
Define new setpoint after alarm trigger, value 0 – 32000
Value 0 = 0% setpoint
Value 3200 = 10% setpoint
Enable protected mode
- Write value 82 to parameter 7 – Init Reset (lock secured parameters)

Liquid Dosing Control Manual 9.17.150 rev A – September 2020
Page 11 of 34
Reset alarm status
There are several methods to reset the alarm status. The most commonly used are the Automatic
Reset – when the alarm conditions do not longer apply, and the Reset.
- Write value 2 to parameter 114 – Reset (reset alarm)
Step DDE ProPar Name
Data
Type
Execute
Value Remark
Unlock Secured Parameters
1
7
0/10
Init Reset
Uint8
write
64
Unlock secured parameters
Response Alarm
2 118 97/3 Alarm Mode
Uint8
write 2 Response Alarm
3 182 97/7 Alarm Delay
Uint8
write _ Delay in seconds.
4 116 97/1 Alarm Maximum Limit
Uint16
write _ Limit 0-32000 = 0-100%
5 117 97/2 Alarm Minimum Limit
Uint16
write _ Limit 0-32000 = 0-100%
6 120 97/5 Alarm Setpoint Mode
Uint8
write 1 Setpoint change on alarm.
7 121 97/6 Alarm New Setpoint
Uint16
write 0 Setpoint 0.
Lock Secured Parameters
8
7
0/10
Init Reset
Uint8
write
82
Lock secured parameters
Reset alarm
9
114
115/8
Reset
Uint8
Write
2
Alarm reset
Note
At startup, only air is present in the sytem which can trigger the alarm.
2.2.7 Dosing specific settings – OUT signal to external device
Configure OUT signal to external device
Instruments within the ES-, MI- and ML-series have the option to trigger an external device, such
as a indication light or sound.
To configure a physical output on the instrument, please contact your local Bronkhorst
representative for support.

Liquid Dosing Control Manual 9.17.150 rev A – September 2020
Page 12 of 34
2.2.8 Ratio dosing specific configuration settings
Ratio or Master/Slave control loop
In a Ratio or Master/Slave control loop, the Liquid Dosing Set operates in a Slave control mode
based on a measurement signal from an external flow meter, the Master signal.
The Master measurement signal is connected as an analog input signal.
Using the calculated Slave Factor, the Liquid Dosing Set doses the right amount of liquid as a
function of the Master measurement signal.
Electrical connection
Refer to the electrical hook-up diagram of the instrument for Analog Operation connection
instructions.
Depending on the type of actuator, the control signal is configured as 4 – 20 mA or 0 – 10 V.
The Master measurement analog signal needs to be configured in the same way.
Configure instrument for Ratio Control
Change control mode
Change Control Mode
- Write value 10 to parameter 12 – Control Mode (Analog Slave Operation)
Calculate Ratio Control setting
The ratio control setting is defined as a percentage, the Slave Factor.
To determine the settings:
Master Flow Analog signal 4 – 20 mA or 0 – 10 V = 0 – 32000 = 0 – 100% of range.
- Read parameter 11 – Measure (Measure of Master 0 – 32000)
Example A Master Flow meter with a maximum capacity of 10,000 kg / h provides
an input signal of 16000 = 50%, therefore a measurement of 5,000 kg / h.
Determine the Slave Factor
Example The ratio of liquid to be dosed is 1 : 1,000, for every 1,000 kg measured
in the main flow, the Liquid Dosing Set will need to add 1 kg of liquid.
The Bronkhorst controller is configured for 10 kg / h (Capacity Value)
Capacity Value Master 10,000 kg / h (100%)
Capacity Value Slave 10 kg / h (100%)
Ratio 1:1,000
At 100% Master flow, a dosage of 1:1,000 for 10,000 kg = 10 kg = 100%
of Slave capacity.
Slave Factor = 100
If Master meter measures 50% (5000 kg) and Slave factor is 100, then
the setpoint for the dosed amount of liquid will be 50% = 5 kg / hr.

Liquid Dosing Control Manual 9.17.150 rev A – September 2020
Page 13 of 34
Example The ratio of liquid to be dosed is 1:25.
Capacity Value Master 1,000 kg / hr (100%)
Capacity Value Slave 200 gr / hr (100%)
Ratio 1:10,000
At 100% Master flow, a dosage of 1:10,000 for 1,000 kg = 100 gr
100 gr = 50% of the Slave Capacity
Slave Factor = 50
Or, by adjusting the Capacity Value (100% - point) of the instrument to
100 gr / hr, the factor changes to:
Slave Factor = 100
To start dosing
Write determined factor
- Write value <_> to parameter 139 – Slave Factor (0 – 500%)
Read instrument internal calculated setpoint
Defined as Analog Input x Slave Factor
- Read parameter 9 – Setpoint (Measure 0 – 32000)
Step DDE ProPar Name
Data
Type
Execute
Value Remark
Control Mode
1 12 1/4 Control Mode
Uint8
write 10 Analog Slave Operation.
Factor
2 11 1/3 Analog Input
Sint16
read 0-32000 Measure of master
3 139 33/1 Slave Factor
Float
write xx 0 – 500%
4 9 1/1 Setpoint
Uint16
read Analog Input * Slave Factor
2.2.9 Batch dosing specific configuration settings
Generic dosing settings
Due to the potential complexity of batch dosing applications and the high amount of optimization
possibilities this section is limited to generic settings regarding batch dosing.
For more detailed information and background information, please refer to the Batch Dosing
information in the applicable Instruction Manuals:
- 9.17.097 – Instruction Manual mini CORI-FLOW ML120, chapter 5
- 9.17.075 – Instruction Manual CORI-FILL
Dosing Principles (explained in more detail in referenced documents)
At the start of each batch, the flow is initiated by opening a valve (or starting a pump). The
flow meter measures and totalizes the flow, continuously calculating the current batch size

Liquid Dosing Control Manual 9.17.150 rev A – September 2020
Page 14 of 34
(Batch size = Flow x Time. As soon as the delivered batch size reaches the configured batch
size, the flow is stopped.
Depending on the importance of accuracy as opposed to dosing speed, proportional control
or on/off control is advised. Proportional control using a control valve or (gear) pump is the
common method if batch size accuracy is of critical importance. On/off control using a shut-
off valve is typically used in situations where dosing speed is more important.
Example Proportional Control (left) and ON/OFF Control (right)
The overshoot can also occur in Proportional control mode, although it will be minimized. In
both control modes the automatic self-learning function will optimize the delivered batch size
until it matches the required batch size.
Estimated Dosing Time
With Proportional Control, the estimated dosing time per batch can be calculated:
()= 2 +
With ON/OFF Control, the estimated dosing time per batch can be calculated:
()= 1 +
Generic batch dosing requirements
- In order to achieve consisten batches within the specified timeframe, the liquid supply
pressure needs to be constant. When the required dose cannot be achieved, it might be
required to increase the supply pressure.
- Gas bubbles in the liquid can influence the batches. It is therefore strongly recommended to
ensure that the system is completely filled with liquid and (if needed) to periodically bleed out
any entrapped gas. Gas entering the system can be minized by following the
recommendations for a system setup in the E-book on Low Flow Handling
Configure instrument for Batch Control
Enable and configure the Counter functionality
- Write value 2 to parameter 130 – Counter Mode (mode Up to Limit – Batch)
- Write value <_> to parameter 124 – Counter Limit (Batch size)
Batch Size is defined in the Capacity Unit as configured in section 1.2.4
For optimization purposes, the measurement unit can be changed with Counter Unit using
the same index values as listed in section 1.2.4

Liquid Dosing Control Manual 9.17.150 rev A – September 2020
Page 15 of 34
- Write value <index> to parameter 128 – Counter Unit (Measurement unit per batch)
- Write value 1 to parameter 126 – Counter Setpoint Mode (Enable new setpoint on limit)
- Write value 0 to parameter 127 – Counter New Setpoint (Setpoint 0 on batch limit)
When configuring the instrument for batch dosing, always set New setpoint on limit to 0. With
any other value the media flow will not stop after reaching the configured batch size. In that
case, dosing can only be stopped by disabling the counter (Counter Mode = Off) and
changing the main setpoint to 0.”
- Write value <index> to parameter 157 – Reset Counter Enable (Reset counter)
The following reset methods are supported
Value 1 – Micro-Switch
Value 4 – Parameter 114 – Reset / External Input (pin 5)
Value 7 – Micro-switch / parameter 114 – Reset / External Input (pin 5)
Value 8 – Automatically
Value 16 – Analog Setpoint Input
Note on External Input (pin 5)
External input (pin5) is optional on instruments in the ES-FLOW, ML- and MI-series.
Note on Analog Setpoint Input
When the Analog Setpoint Input will be set to 0, the counter will be reset. When the
setpoint will be set to a value >0, the batch counter will restart the next batch.
For connecting an external device for a Batch Reset signal, refer to the Liquid Flow Controller
hook-up diagram.
Prepare a Batch counter [Batch mode]
Step
DDE
ProPar
Name
Data
type
Execute
Value
Remark
1
130
104/8
Counter Mode
Uint8
write
2
Counter Mode up to limit (batch
Mode)
2
124
104/3
Counter Limit
Float
write
x.xx
Batch size
3
128
104/2
Counter Unit
Uint8
write
xx
Counter Unit [for example g / kg]
4
126
104/5
Counter setpoint
mode
Uint8
write
1
Enable new setpoint on batch
limit
5
127
104/6
Counter New
setpoint
Uint16
write
0
New setpoint when batch limit is
reached
6
157
104/9
Reset Counter
Enable
Uint8
write
7
Enable reset source [default 7 =
all inputs]
Optimize Full Scale flow for Batch mode
The Liquid Flow Controller needs to be configured for the hourly total flow equivalent.
With a 1 gram dose in 1 second every 10 seconds, the hourly equivalent is 3600 gram.
The total amount of liquid dosed is 360 gram.
For the best performance it's advised to optimize the Full Scale Capacity according to the
maximum flow rate during a batch.This will result in a minimum loss of resolution and highest
possible accuracy.

Liquid Dosing Control Manual 9.17.150 rev A – September 2020
Page 16 of 34
For example, when execute a batch with a flow rate of 100 g/h at an Full scale capacity of 100 g/h
is more accurate then at an Full Scale capacity of 1000 g/h.
To calculate the optimal Full Scale value in kg / h = []
[]× 3.6
Changing the Full Scale value is explained in section 1.2.5 – Change the Capacity Value
When another Capacity Unit is used (section 1.2.4), then the Full Scale flow needs to be
calculated accordingly.
Tune the Batch Counter Controller
The Batch Counter value is used to control the actuator to achieve the desired Batch value.
By setting Counter Controller Overrun Correction to a value between 0 and 1, the system closes
the valve (or stops the pump) a fraction before reaching the batch size, minimizing overshoot.
- Write value <_> to parameter 274 – Counter Controller Overrun Correction
(Overrun Correction)
Value can be defined between 0 and 1. A typical value is 0.8.
A higher value corresponds with a faster correction and less learning cycles required, but
might also result in an unstable control behaviour.
A lower value corresponds with a slower correction and more learning cycles required.
The Counter Controller Gain will gradually close the valve or decrease the pump speed to ramp
down the flow speed until the batch size is reached. This will result in a more accurate batch.
The starting point of the ramp down is determined by the value of Counter control gain.
- Write value <_> to parameter 275 – Counter Controller Gain (Point to ramp down)
Value can be defined as listed in the below overview.
If set to 0, the Control Gain is disabled and the system operates in ON/OFF control.
Step
DDE
ProPar
Name
Data
type
Execute
Value
Remark
1
274
104/10
Counter Controller
Overrun Correction
Float
Write
0.0…1.0
Overrun correction
Default = 0.8
2
275
104/11
Counter Controller
Gain
Float
Write
1…100
% of Batch size [point to ramp down]

Liquid Dosing Control Manual 9.17.150 rev A – September 2020
Page 17 of 34
3. Prepare for operation
The main purpose of this section is to prepare the Bronkhorst Liquid Dosing Set for operation.
This includes filling the controlling instrument and actuator with liquid, flushing all the air from the
dosing set, and performing an instrument Auto-Zero function.
Tip !
The goal is to completely fill the instrument and actuator with liquid. This is required for a smooth
start of the control loop, and for this reason it is not necesseray to completely fill the downstream
process lines at this time.
By opening a drain point (if installed) directly downstream of the dosing set, the filling time can be
reduced and the presence of liquid can be directly observed.
Only if the fluid, method of collecting the drained liquid and process environment allows for this
tip.
3.1 Fill the system
Filling the system is the first step of removing all air to ensure a stable and smooth control loop.
1. Prepare the system to be filled
- Make sure all fluid connections have been leak tested
- Make sure the system outlet is connected to the process or a suitable waste
- Open (if applicable) process valves outside the Bronkhorst set
To ease the filling process by decreasing the system pressure drop and volume to be filled
- Open (if present) a drain point between the Bronkhorst set and the process
- Close (if present) the installed bypass downstream of the pump
Note, ensure that any liquid is safely collected at the opening.
Ensure Batch Mode is disabled
- Write value 0 to parameter 130 – Counter Mode (Batch Mode disabled)
2. Slowly operate the actuator to draw in liquid
- Write value <___> to parameter 206 – Flow setpoint (provide setpoint to draw liquid)
Choose 10% of the normal operation flow of the system as setpoint at this step. Increase
with steps of 10% to speed up the filling process.
Filling a system can take a long time depending on tube diameters and the configured
flow rate of the system. By taking larger setpoint steps, the filling time can be reduced,
but when the system is sensitive to pressure spikes, then take caution and use a slow but
steady flowrate.

Liquid Dosing Control Manual 9.17.150 rev A – September 2020
Page 18 of 34
3. Wait until liquid is present in the system
Visually check if liquid is present downstream of the Liquid Dosing Set
(observed in process, visibile in clear tubing if used, ……)
or
Wait 60 seconds
or
- Monitor the Actual Density reading (mini CORI – parameter 270) for readings as
expected what indicates liquid is detected
4. Stop filling
- Write value 0 to parameter 206 – Flow setpoint (setpoint 0)
5. Completion of Filling step
- Check (partially) filled system for leaks
- Close any used drain points of bypass lines
Step DDE ProPar Name
Data
Type
Execute
Value Remark
Preparation
1
130
104/8
Counter Mode
Uint8
write
0
Counter Mode disabled (batch
mode)
Start Filling
2
206
33/3
fSetpoint
Float
write
<value>
Flow rate in Capacity Unit.
CORI-FLOW
3 270 116/15 Actual Density
Float
read
Check if density is range of used
liquid
Stop Filling
4
206
33/3
fSetpoint
Float
write
0.0
In Capacity Unit.
3.2 Flush the system
After the system is partially filled with liquid, the system can now be flushed to remove all air out of the
liquid flow control loop.
1. Operate the actuator at 100% setpoint
When a pump is used, run at full application flow (actuator 100%)
- Write value <___> to parameter 206 – Flow setpoint (full application flow)
Choose 100% of the application flow as setpoint
When a valve is used, fully open the valve (actuator 100%)
- Write value 8 to parameter 12 – Control Mode (Actuator 100%)

Liquid Dosing Control Manual 9.17.150 rev A – September 2020
Page 19 of 34
2. Wait until all entrapped gas is flushed out of the system
- Visually check for bubbles downstream of the Liquid Dosing Set
(observed in process, visibile in clear tubing if used, ……)
or
- Monitor the Actual Density reading (mini CORI – parameter 270) until the value is in
range of used liquid and stable over a time of ~ 30 seconds
or
- Monitor the Flow Rate reading (parameter 205 – fMeasure) until the value is stable over a
time of ~ 30 seconds
3. Stop de pump or close the valve
When a pump is used
- Write value 0 to parameter 206 – Flow setpoint (stop flow)
When a valve is used
- Write value 3 to parameter 12 – Control Mode (Actuator 0%)
4. Optional steps for actuator – Valve with bleed connection
(i.e. Bronkhorst C2 valve)
- Ensure the bleed connection or bypass are connected to a suitable container or waste
line
- Ensure that liquid downstream of the dosing set is properly collected
Start bleeding the valve
- Write value 3 to parameter 12 – Control Mode (Actuator 0%)
- Open the bleed connection
- Allow the system pressure to flush out all air bubbles
(observed at bleed tube outlet or visibile in clear tubing if used)
Force remaining air out of the valve by opening and closing several times
- Write value 8 to parameter 12 – Control Mode (Actuator 100%)
- Write value 3 to parameter 12 – Control Mode (Actuator 0%)
- Write value 0 to parameter 12 – Control Mode (Restore to previous)
- Repeat 2 ~ 5 times
- Write value 0 to parameter 206 – Flow setpoint (end with setpoint 0)
- Allow the system pressure to flush out all air bubbles
(observed at bleed tube outlet or visibile in clear tubing if used)
Wrap-up
- Close the bleed connection

Liquid Dosing Control Manual 9.17.150 rev A – September 2020
Page 20 of 34
5. Optional step for actuator – Pump with bypass circuit
- Ensure the bleed connection or bypass are connected to a suitable container or waste
line
- Ensure that liquid downstream of the dosing set is properly collected
Start bleeding the bypass circuit
- Write value <___> to parameter 206 – Flow setpoint (provide setpoint to fill bypass)
Choose roughly 25% of the normal operation flow of the system as setpoint at this step.
- Slowly open the bypass valve to allow flow to pass through
- Wait 10 seconds
- Write value 0 to parameter 206 – Flow setpoint (setpoint 0)
Wrap-up
- Close the bypass valve (default state)
The system is now ready to perform the bypass adjustment
See Installation Manual – Liquid Dosing Sets (9.17.146) for instructions
6. Completion of Flush step
- Check for leakages with complete system being filled
- Close (if applicable) process valves outside the Bronkhorst set to avoid unexpected liquid
flows
Re-Enable Batch Mode if required for operation
- Write value 2 to parameter 130 – Counter Mode (Counter mode up to limit)
Step DDE ProPar Name
Data
Type
E
xecute
Value Remark
1 206 33/3 fSetpoint
Float
write <value> Flow Setpoint
1 12 1/4 Control Mode
Uint8
write 8 Actuator 100%
2 270 116/15 Actual Density
Float
read
Check for change, which
indicates fluid in instrument.
3 205 33/0 fMeasure
Float
read <measure> Flow Rate in Capacity Unit.
4 12 1/4 Control Mode
Uint8
write 8 Actuator 100%
5 12 1/4 Control Mode
Uint8
write 3 Actuator 0%
6 270 116/15 Actual Density
Float
read
Check for change, which
indicates fluid in instrument.
7 206 33/3 fSetpoint
Float
write <value> Flow Setpoint for bypass circuit
8
130
104/8
Counter Mode
Uint8
write
2
Counter Mode up to limit (batch
Mode)
This manual suits for next models
4
Table of contents
Other BRONKHORST Control Unit manuals
Popular Control Unit manuals by other brands
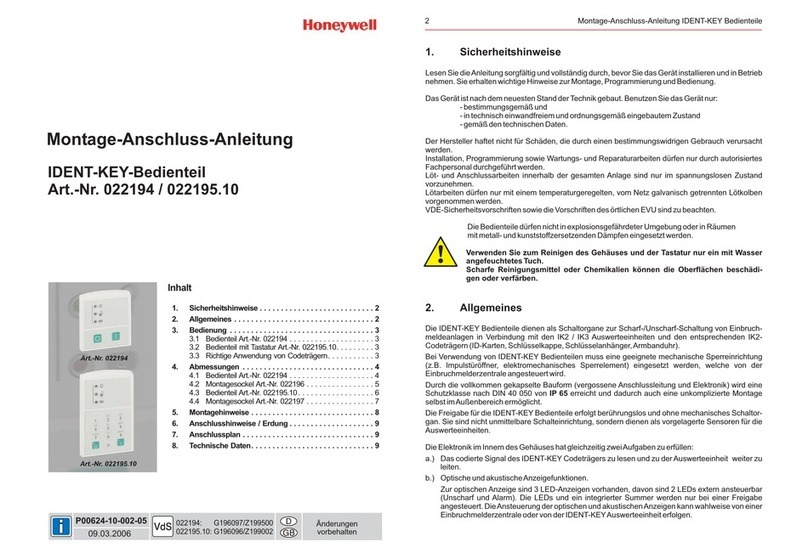
Honeywell
Honeywell IDENT-KEY Series Mounting and Connection Instructions
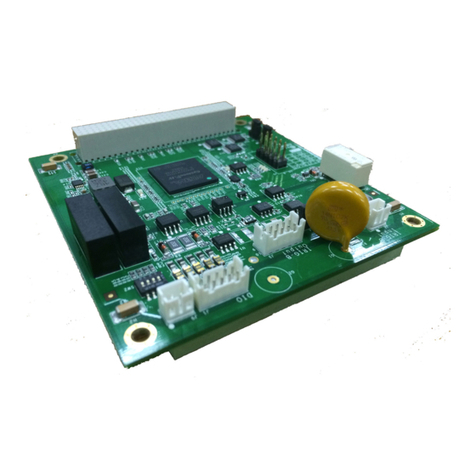
Moxa Technologies
Moxa Technologies DA-IRIGB-4DIO-PCI104-EMC4 user manual
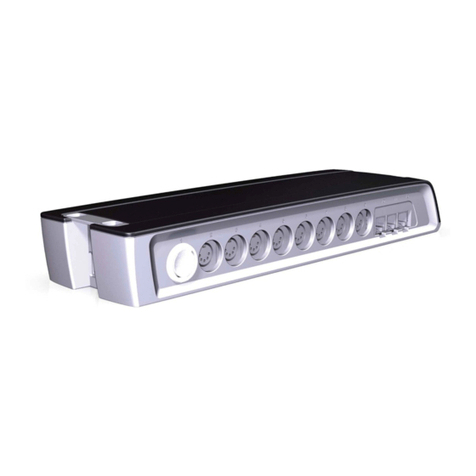
Phoenix Mecano
Phoenix Mecano Dewert Okin HE-300 SMPS installation instructions
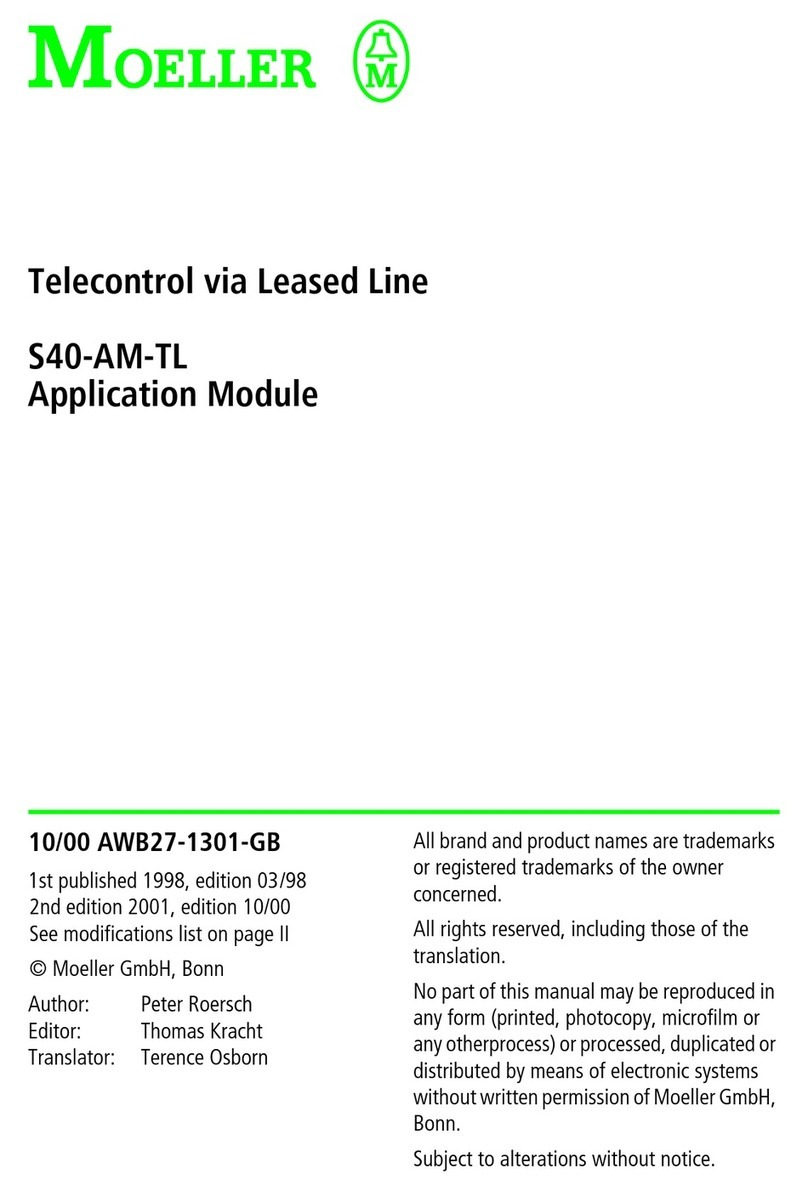
Moeller
Moeller S40-AM-TL manual
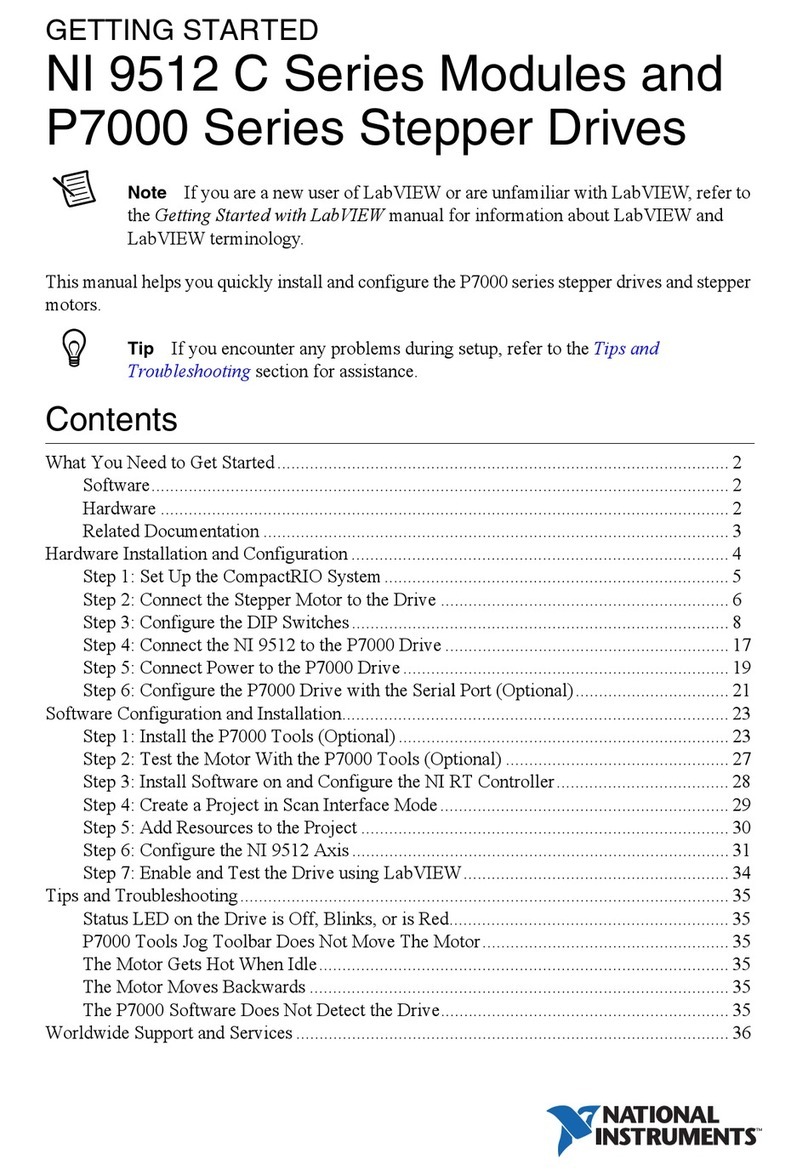
National Instruments
National Instruments 9512 C Series Getting started
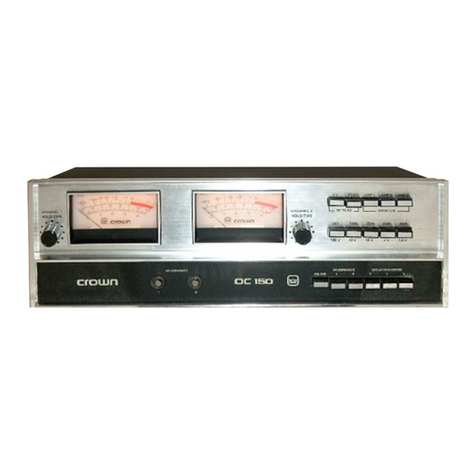
Crown
Crown OC-150 user guide