BST ekrPro Com60 User manual

Quick Reference Guide EDV no.: MD.337.01.04
ekrPro Com60 with CLS Pro 600 Issue Date: 30.06.2011
Web Guiding Systems
ekrPro Com60
with CLS Pro 600
Translation of the
Original Quick Reference Guide

Quick Reference Guide QRG
Qick Reference Guide EDV no.: MD.337.01.04
ekrPro Com60 with CLS Pro 600 Issue date: 30.06.2011
General information
This Quick Reference Guide describes the assemblyand the
commissioning of the web guiding system ekrPro Com60 with
CLS Pro 600.
The web guiding system ekrPro Com60 with CLS Pro 600 should
only be commissioned after you have acquainted yourself with the
corresponding more detailed operating manual of the controller
ekrPro Com60 and the line and contrast sensor CLS Pro 600. This
will help to avoid hazards and prevent damage to the system due
to improper commissioning or operation.
Prior to commissioning and before performing any maintenance
work, you must read, without fail, the safety instructions in the
corresponding operating manual!
The detailed operating manual for the devices specified above are
a part of the delivery. They can also be found in internet under the
following address:
http://www.bst-international.com
BST eltromat International Bielefeld GmbH
Heidsieker Heide 53
33739 Bielefeld, Germany
Telefon: +49 5206 999-0
Telefax: +49 5206 999-999
info@bst-international.com
Our service department is available for special queries
under the telephone number 0049 (0) 5206 999760 or under
service@bst-international.com.

Quick Reference Guide QRG
Qick Reference Guide EDV no.: MD.337.01.04
ekrPro Com60 with CLS Pro 600 Issue date: 30.06.2011
Contents Contents.......................................................................................... 2
1System overview....................................................................... 1
2Commissioning ekrPro Com60 .................................................. 1
2.1 Actuator EMS 17 –EMS 22................................................... 4
2.1.1 Select actuator.................................................................... 4
2.1.2 Setting the actuator guiding direction ................................. 5
2.1.3 Select servo-center component.......................................... 5
2.1.4 Setting the actuator path limits ........................................... 6
2.2 Actuators EMS 3 / 4............................................................... 7
2.2.1 Select actuator.................................................................... 7
2.2.2 Setting the actuator guiding direction ................................. 8
2.2.3 Check the limit switch allocation......................................... 8
2.2.4 Select the servo-center component.................................... 9
2.3 Hydraulic actuator.................................................................. 9
2.3.1 Select hydraulic actuator .................................................... 9
2.3.2 Setting the actuator guiding direction ............................... 10
2.3.3 Select the servo-center component.................................. 12
3Setting up the CLS Pro 600.................................................... 13
3.1 General ................................................................................ 13
3.2 Requirements....................................................................... 13
3.3 Adjust password level.......................................................... 14
3.4 Configuration........................................................................ 15
4Material Setup......................................................................... 17
4.1 at the controller .................................................................... 17
4.2 at the sensor ........................................................................ 17
4.3 Edge set-up mode................................................................ 18
4.4 Line setup mode .................................................................. 19
5Job administration................................................................... 20
5.1 Selecting a job ..................................................................... 21
5.2 Creating and saving a job.................................................... 21
5.3 Deleting a job....................................................................... 21
5.4 To show the current job ....................................................... 22

Quick Reference Guide QRG
Quick Reference Guide EDV no.: MD.337.01.04
ekrPro Com60 with CLS Pro 600 Issue Date: 30.06.2011 Seite: 1/22
1 System overviewUse this Quick Reference Guide if the system you use has the
following configuration:
2 Commissioning ekrPro Com60
ekrPro Com60 firmware > 1.7.6 is needed to run the system!
You will find the information:
on the nameplate
in the start screen
of the ekrPro Com60.
Attention: You must connect the sensor up to the controller and
turn the sensor’s S1 rotary switch to Position 1 (default)
and then switch the sensor on before you select the
standard system with CLS Pro 600.
controller
ekrPro Com60
electromotor powered actuator
Line and contrast sensor
CLS Pro 600
hydraulic powered actuator
or
connector X71
connector X101

Quick Reference Guide QRG
Quick Reference Guide EDV no.: MD.337.01.04
ekrPro Com60 with CLS Pro 600 Issue Date: 30.06.2011 Seite: 2/22
Afterwards proceed as follows:
1. Wire in and switch on the ekrPro Com60 controller as stipulated
in the operating manual of the controller.
2. Configure the ekrPro Com60 controller.
For it select the standard system for use with the CLS Pro 600
as follows.
a) Press the MENU key on the controller. The set-up menu will
be displayed on the screen.
b) Select Sel.Std. System and then press ENTER.
c) The selection window for standard system appears.
Press the ENTER key.
d) The option list opens with the most common standard
systems.
e) Now select the CLS :EMS 17/18 [+efePlus] entry and
confirm the selection by pressing ENTER.
Use this entry with all applications that
use the CLS Pro 600.
f) Press the function key F2 (Set).
Now the system will request a restart. For this purpose, turn off the
supply voltage for the controller and shortly afterwards, turn it back
on.
Further procedures depend on which actuator is connected to the
system that you use.
In the following, you will find an overview of the actuators that can
be connected and the further procedures.
F2

Quick Reference Guide QRG
Quick Reference Guide EDV no.: MD.337.01.04
ekrPro Com60 with CLS Pro 600 Issue Date: 30.06.2011 Seite: 3/22
Type
see
EMS 17
section 2.1
EMS18
section 2.1
EMS 21
section 2.1
EMS 22
section 2.1
EMS 3
section 2.2
EMS 4
section 2.2
SV 1-6; SV 1-10/xx
section 2.3

Quick Reference Guide QRG
Quick Reference Guide EDV no.: MD.337.01.04
ekrPro Com60 with CLS Pro 600 Issue Date: 30.06.2011 Seite: 4/22
2.1 Actuator EMS 17 –EMS 22
These actuators all have something in common; they are fitted with
an integrated position feedback.
2.1.1 Select actuator Pre-adjustments are already carried out with the selection of the
standard system when using the EMS 17/18 actuator. In this case
you can continue with point 2.1.2.
You have to enter the EMS 21 or EMS 22 if there is one of these
actuators connected.
1. Call up the General Setup menu.
2. Select the Actuator sub-menu and then the select the
Type (EMS&Hydr.) sub-directory afterwards.
Confirm the respective selection by pressing ENTER.
3. The default actuator will be dispalyed on the screen.
4. Press the ENTER button. The actuator option list will then be
opened.
Use the vertical arrow keys to select the actual actuator that
is connected to the system (EMS 21 / EMS 22).
Confirm the selection by pressing ENTER.
5. Press the ESC button to exit the window.
123 45 6 789 0
Material Setup
Sel. Std. System
Save/Load Settings
opt. Logic
General Setup
Actuator
Sensors/EFE
Control Loop
FVG
Type (EMS&Hydr.)
Hydraulics Add-on
Direction
SC-Transducer

Quick Reference Guide QRG
Quick Reference Guide EDV no.: MD.337.01.04
ekrPro Com60 with CLS Pro 600 Issue Date: 30.06.2011 Seite: 5/22
2.1.2 Setting the actuator guiding direction
1. Select the sub-directory Direction from the sub-menu
Actuator. Confirm the selection by pressing ENTER.
The actuator guiding direction for manual mode can be
reversed by activating the checkbox Mot. Dir. Inverted.
The direction can be checked on the spot.
Move the actuator using the F2 or F3 key.
If key F2 is pressed, the actuator must move the material
web to the left hand side in material running direction, if F3 is
pressed it must move it to the right hand side in material
running direction!
Pressing F2 or F3 automatically changes the controller to
the manual operating mode.
2.1.3 Select servo-center component
1. Select the sub-directory SC-Transducer from the Actuator
sub-menu and select then Type & Dir. .
Confirm the respective selection by pressing ENTER.
2. Use the horizontal left or right arrow keys in the newly
opened window to select the servo-center selection window
and confirm it by pressing ENTER.
3. Select and mark the relevant servo-center component from
the option list. For actuators with integrated position
feedback (EMS 17, EMS 21 and EMS 22) there is a
common servo-center component
In this case EMS_Pot. Has to be selected.
4. Confirm the selection by pressing ENTER.
The screen will return to the previous window.
5. Move the actuator using the F2 key, while monitoring the bar
indicator int he display. The black bar on the left side gets
smaller.
If the length of the black bar increases when the F2 key is
pressed, inverting is to be switch on by selecting the
checkbox Inv..
Pressing the F3 key must cause the black bar to increase
towards the right side.
Toggle Man Dir. until
F2 moves to sensor 1
Mot. Dir. Inverted
F2
F3
not connected
F2
F3

Quick Reference Guide QRG
Quick Reference Guide EDV no.: MD.337.01.04
ekrPro Com60 with CLS Pro 600 Issue Date: 30.06.2011 Seite: 6/22
6. Press the ESC button to exit the window.
2.1.4 Setting the actuator path limits
1. Switch to the sub-directory SC-Transducer and select the
position Pos. Limit.
Confirm the respective selectuion by pressing ENTER.
2. Use the vertical arrow keys to deactivate the checkbox
active. This deactivates the function of both limit switches.
The settings can only be entered in deactivated state.
3. Use the F2 key to move the actuator until it reaches the
required left limt switch position (lim. l). The actual position
of the actuator supplied by the position feedback is shown in
the middle above the F2 and F3 keys.
4. Confirm this position by pressing the F1 key.
The acceptance of the limit switch position is displayed by
the empty graphic bar in the middle.
The corresponding position value is shown below the
checkbox.
5. Use the F3 key to move the actuator until it reaches the
required right limit switch position (lim. r).
6. Confirm this position by pressing the F4 key.
The acceptance of the limit switch position is displayed by
the filled (black) graphic bar in the middle.
7. Reactivate both limit switches.
Select (x) checkbox active to do this.
Triggering of the respective limit switch is indicated by a
black circle in the read-only checkbox above the F1
and/or F4 key.
Acknowledge a possibly indicated error message by
pressing ENTER.
8. Press the ESC button to exit the inputting menu.
Press the MENU button to exit the set-up menu.
Setting up the ekrPro Com60 is finished with it.
Continue with point 3.
left
right
Deactivate to set limits
Activate to test limits
lim.l lim.r
<<<<
<<<<
-264 1258
active
47%
456
Deactivate to set limits
Activate to test limits
lim.l lim.r
<<<<
<<<<
-264 1258
active
47%
456
F2
F3
F1
F4
F2
F3
F1
F4
F2
F3
F1
F4

Quick Reference Guide QRG
Quick Reference Guide EDV no.: MD.337.01.04
ekrPro Com60 with CLS Pro 600 Issue Date: 30.06.2011 Seite: 7/22
2.2 Actuators EMS 3 / 4 The EMS 17/18 has been entered as an actuator when selecting
the standard system. As this is not connected in your system, the
actual actuator fitted must be entered and the necessary settings
must be carried out.
2.2.1 Select actuator The relevant servo-center component must be entered before
starting the commissioning (see section 2.2.4).
Any remote control which may possibly be running, must be
deactivated.
1. Call up the General Setup menu.
2. Select the sub-directory Type (EMS&Hydr.) from the sub-
menu Actuator.
Confirm the relevant selection by pressing ENTER.
3. The default actuator will be displayed on the screen.
4. Press the ENTER key. The actuator option list will be
opened.
Now use the vertical arrow keys to select the actual actuator
(EMS3 / EMS4) that is connected to the system.
Confirm the selection by pressing ENTER.
5. Press the ESC button to exit the window.
123 45 6 789 0
Material Setup
Sel. Std. System
Save/Load Settings
opt. Logic
General Setup
Actuator
Sensors/EFE
Control Loop
FVG
Type (EMS&Hydr.)
Hydraulics Add-on
Direction
SC-Transducer

Quick Reference Guide QRG
Quick Reference Guide EDV no.: MD.337.01.04
ekrPro Com60 with CLS Pro 600 Issue Date: 30.06.2011 Seite: 8/22
2.2.2 Setting the actuator guiding direction
1. Switch to the sub-directory Direction.
The actuator guiding direction for manual mode can be
reversed by activating the checkbox Mot. Dir. Inverted.
The direction can be checked on the spot.
Move the actuator using the F2 or F3 key.
If key F2 is pressed, the actuator must move the material
web to the left hand side in material running direction, if F3 is
pressed it must move it to the right hand side in material
running direction!
Pressing F2 or F3 automatically changes the controller to
the manual operating mode.
2. Press the ESC to exit the window.
2.2.3 Check the limit switch allocation
Move the actuator in direction to one limit switch in MAN mode until
the limit switch is actuated.
The message „Limit switch set“ appears in the display of the
ekrPro Com60 and the error LED lightens simultaneously.
Check the allocation. The actuator must not move into this
direction.
EMS 3
EMS 4
left
right
limit switch
tripping device
limit switch
tripping device
F2
F3
Toggle Man Dir. until
F2 moves to sensor 1
Mot. Dir. Inverted

Quick Reference Guide QRG
Quick Reference Guide EDV no.: MD.337.01.04
ekrPro Com60 with CLS Pro 600 Issue Date: 30.06.2011 Seite: 9/22
2.2.4 Select the servo-center component
1. Select the sub-directory SC-Transducer from the sub-
menu Actuator and then the position Type & Dir..
Confirm the respective selection by pressing ENTER.
2. Use the horizontal arrow keys left and/or right in the
newly opened window to select the servo-center
component selection window and confirm it by pressing
ENTER.
3. Select not connected from the option list for these
actuators.
4. Confirm the selection by pressing ENTER.
The screen will return to the previous window.
5. Press the ESC button to exit the window.
Press the MENU button to exit the set-up menu.
Setting up the ekrPro Com60 is finished with it.
Continue with point 3.
2.3 Hydraulic actuator
2.3.1 Select hydraulic actuator 1. Call up the General Setup menu.
2. Select the menu sub-directory Type (EMS&Hydr.)
from the sub-menu Actuator.
Confirm the respective selection by pressing ENTER.
not connected
123 45 6 789 0
Material Setup
Sel. Std. System
Save/Load Settings
opt. Logic
General Setup
Actuator
Sensors/EFE
Control Loop
FVG
Type (EMS&Hydr.)
Hydraulics Add-on
Direction
SC-Transducer

Quick Reference Guide QRG
Quick Reference Guide EDV no.: MD.337.01.04
ekrPro Com60 with CLS Pro 600 Issue Date: 30.06.2011 Seite: 10/22
3. The default actuator will be displayed on the screen.
4. Press the ENTER button. The actuator option list will then be
opened.
Now use the vertical arrow keys to select the actual actuator
that is connected to the system.
Confirm the selection by pressing ENTER.
The allocation of the hydraulic powered actuators to the
options is as follows:
300 mA: SV 1-6, SV 1-10/4, SV 1-10/8
SV 1-10/16, SV 1-10/32, EH-St 9/3
1000 mA: SV 1-10/48
(You will find the specifications of the type used on the
nameplate of the unit)
5. Press the ESC button to exit the window.
2.3.2 Setting the actuator guiding direction
1. Switch to the sub-directory Direction.
The actuator guiding direction for manual mode can be
reversed by activating the checkbox Mot. Dir. Inverted.
The direction can be checked on the spot.
Move the actuator using the F2 or F3 key.
If key F2 is pressed, the actuator must move the material
web to the left hand side in material running direction, if F3 is
pressed it must move it to the right hand side in material
running direction!
Pressing F2 or F3 automatically changes the controller to
the manual operating mode.
2. Press the ESC button to exit the window.
left
right
Select an actuator type
EMS 17
Toggle Man Dir. until
F2 moves to sensor 1
Mot. Dir. Inverted
F2
F3

Quick Reference Guide QRG
Quick Reference Guide EDV no.: MD.337.01.04
ekrPro Com60 with CLS Pro 600 Issue Date: 30.06.2011 Seite: 11/22
If a hydraulic actuator is used, then additional hydraulic settings
must be made in the menu Hydraulics Add On.
1. Switch to the sub-directory Hydraulics Add-on.
Confirm the respective selection by pressing ENTER.
2. This will open an inputting window, in which the settings for
the connected hydraulic actuator have to be made.
We recommend not to change the default settings for Zero
elevation and Dither amplitude.
The system must be optimized to the actual settings after
the parameters have been entered. This is realized by an
integrated self-teach function.
Press the F3 key to start this function. This will take the flow
curve for the hydraulic actuator. The measured values are
saved in table as non-volatile settings.
Attention: The hydraulic actuator moves in one direction
getting faster up to the stop and afterwards into
the opposite direction as well.
3. Activate the function Use teach table following the
determination of the flow curve.
4. Press the ESC button to exit the inputing window.

Quick Reference Guide QRG
Quick Reference Guide EDV no.: MD.337.01.04
ekrPro Com60 with CLS Pro 600 Issue Date: 30.06.2011 Seite: 12/22
2.3.3 Select the servo-center component
1. Select the sub-directory SC-Transducer from the sub-
menu Actuator and then the position Type & Dir..
Confirm the respective selection by pressing ENTER.
2. Use the horizontal arrow keys left and/or right in the
newly opened window to select the servo-center
component selection window and confirm it by pressing
ENTER.
3. Select not connected from the option list for these
actuators.
4. Confirm the selection by pressing ENTER.
The screen will return to the previous window.
5. Press the ESC button to exit the window.
Press the MENU button to exit the set-up menu.
Setting up the ekrPro Com60 is finished with it.
Continue with point 3.
not connected

Quick Reference Guide QRG
Quick Reference Guide EDV no.: MD.337.01.04
ekrPro Com60 with CLS Pro 600 Issue Date: 30.06.2011 Seite: 13/22
3 Setting up the CLS Pro 600
3.1 General The display area in the graphic display of the keypad has
differently coloured borders. The different colours show which
mode you are in at present.
There are the following possibilities:
Operating mode AUTOMATIC Operating mode MANUAL
(green) (grey)
SETUP mode Error (flashes red)
(blue) (line/edge not recognized)
3.2 Requirements 1. The controller ekrPro Com60 must be in the MAN operating
mode.
2. The distance between sensor and material of web / scanning
roller has to be set correctly.
(See also manual CLS Pro 600, section 2.2.4)
20
Sensing
roller
Sensor enclosure
Protective
packaging

Quick Reference Guide QRG
Quick Reference Guide EDV no.: MD.337.01.04
ekrPro Com60 with CLS Pro 600 Issue Date: 30.06.2011 Seite: 14/22
3.3 Adjust password level The password level Operator is set after switching on the sensor.
You have to be logged in as Administrator to carry out sensor set-
up and the sensor must be in set-up mode (blue border strip).
The procedure for selecting the password levels is described in the
following, e.g. for commissioning or operating.
1. Press the button MENU on the commander of the sensor for at
least 3 seconds.
2. Afterwards the menu will be displayed. Mark the change user
entry and press ENTER for confirmation.
3. Use the up or down arrow keys to select the password level
Administrator and press ENTER for confirmation.
4. You will be asked to enter the password afterwards.
Enter the valid password 00002.
Use the arrow key right to select the last place of the
password. Now press the arrow keys up or down as often as
the 2appears at this place.
5. Confirm the entry by pressing ENTER.
You are now logged into the selected user level. You can now
adapt the parameters that can be accessed from this level.

Quick Reference Guide QRG
Quick Reference Guide EDV no.: MD.337.01.04
ekrPro Com60 with CLS Pro 600 Issue Date: 30.06.2011 Seite: 15/22
3.4 Configuration Open the Mounting-Position in the Configuration sub-menu and
teach-in the sensor’s mounting position.
The system must be in operating mode MAN.
This procedure consists of 4 sub-steps.
Use the teach-in model shown in the operating manual (annex 5)
to carry out the teach-in process.
Mounting position A is shown as the example in this procedure.
Note that mounting positions B, C and D must first be activated
before you can use them.
1. Call up and open the sub-memnu configuration.
2. Select config positon A.
3. Start the teach-in process for this mounting position.
Select the teach in parameter and confirm your selection by
pressing ENTER. The teach-in process has now started.
3a) The first step is to set up the manual adjustment.
Use the left / right arrow keys to move the guiding
device.
The actuator has to be moved in the respective
direction.
The settings can be inverted from here if the arrow
key assignments are incorrect. This is realized by
using the up / down arrow keys.
Press ENTER to confirm your settings.
arrow key left
moving direction of
the actuator
arrow key right
moving direction of
the actuator
\\configuration\mounting position\
!

Quick Reference Guide QRG
Quick Reference Guide EDV no.: MD.337.01.04
ekrPro Com60 with CLS Pro 600 Issue Date: 30.06.2011 Seite: 16/22
3b) The window for the second step is now open.
Position the teach-in model line in the green field and
then press ENTER to confirm the process:
The line identification process will now be run.
3c) Move the line some millimetres to the left by hand in
step 3 afterwards.
Now press the arrow key left once.
The system will now calculate all of
the parameters automatically.
3d) Press key ENTER. Set-up is now complete.
The settings are displayed summarised again in the
window Step 4.
If necessary, you can make changes to the parameters
displayed here.
However, we recommend that you do not change the
factory default settings.
4. Press key Menu to leave the set-up menu.
5. Switch off the sensor now (pull the connector X101) and
switch it on shortly after. The sensor is reset to the password
level Operator now.
6. This completes the commissioning of the sensor connected
to the ekrPro Com60 controller.
Now you can carry out the material set-up.
The last activated mounting position is loaded with every further
system restart.
teach-in model
Material to be
scanned
Laser line

Quick Reference Guide QRG
Quick Reference Guide EDV no.: MD.337.01.04
ekrPro Com60 with CLS Pro 600 Issue Date: 30.06.2011 Seite: 17/22
4 Material Setup
The set-up of the CLS Pro 600 sensor is only possible in the
operating mode MAN.
Switching the controller to the operating mode MAN
You can switch on the MAN mode at the controller keyboard or via
the sensor keyboard.
4.1 at the controller
Press key MAN. The LED of the key lightens.
4.2 at the sensor
Use the arrow keys up / down to select the operating
mode MAN.
The selected mode with a green border stripe
will be displayed in the bottom left corner.
Confirm the selection by pressing ENTER.
Then the current operating mode will be
displayed in the right upper corner.
1
2
1
2
Other manuals for ekrPro Com60
1
Table of contents
Other BST Control System manuals
Popular Control System manuals by other brands
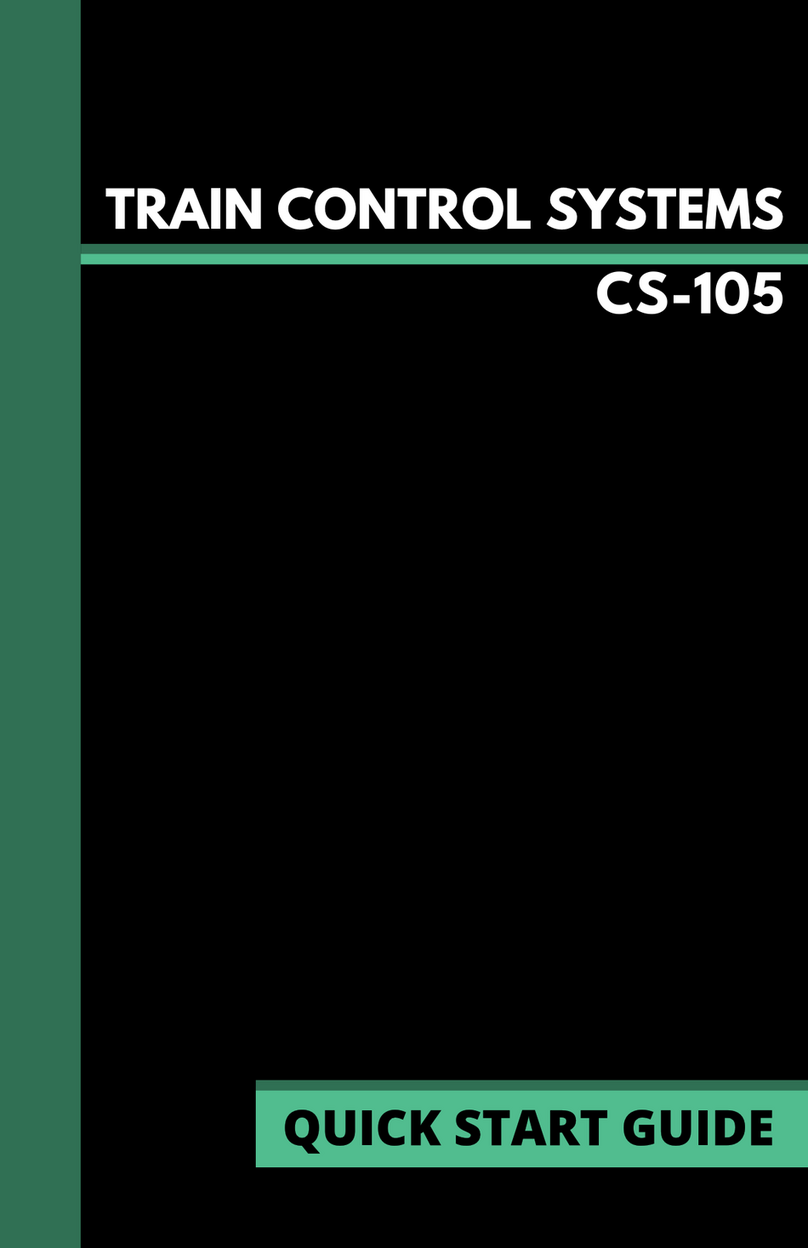
TCS
TCS CS-105 quick start guide
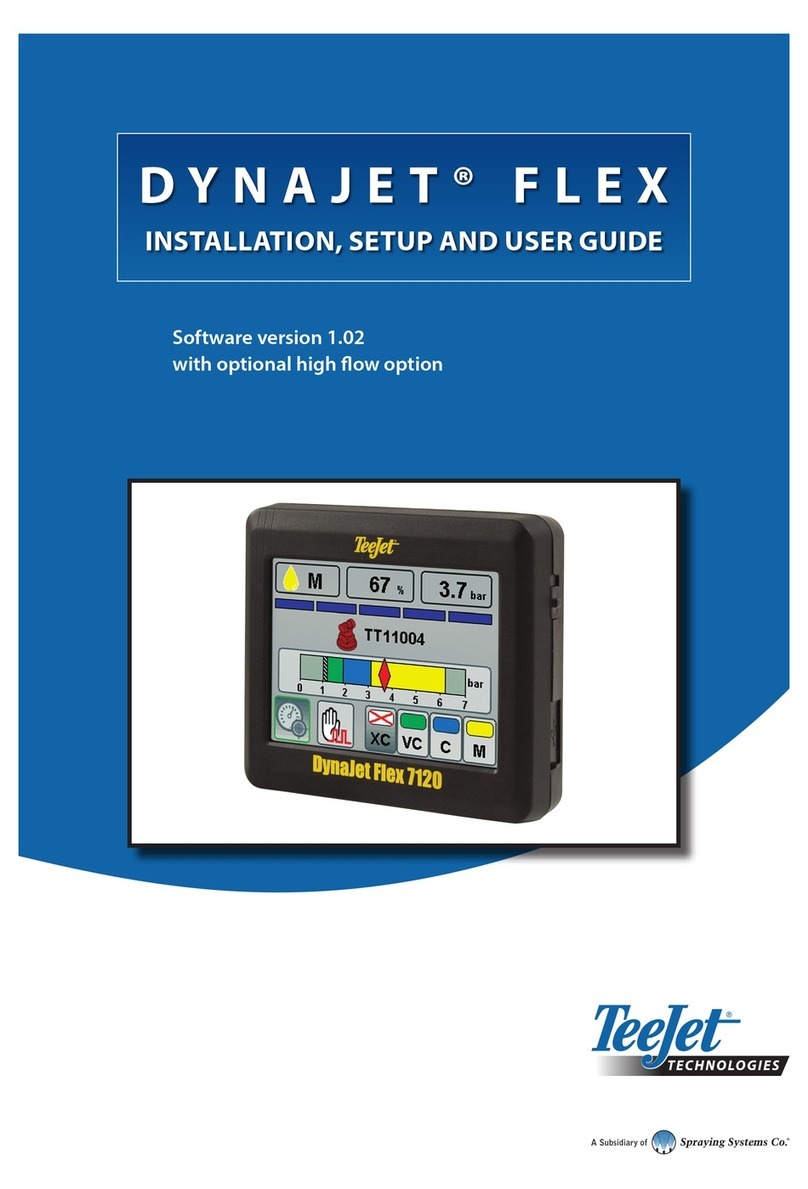
TeeJet Technologies
TeeJet Technologies DynaJet Flex Series INSTALLATION, SETUP AND USER GUIDE
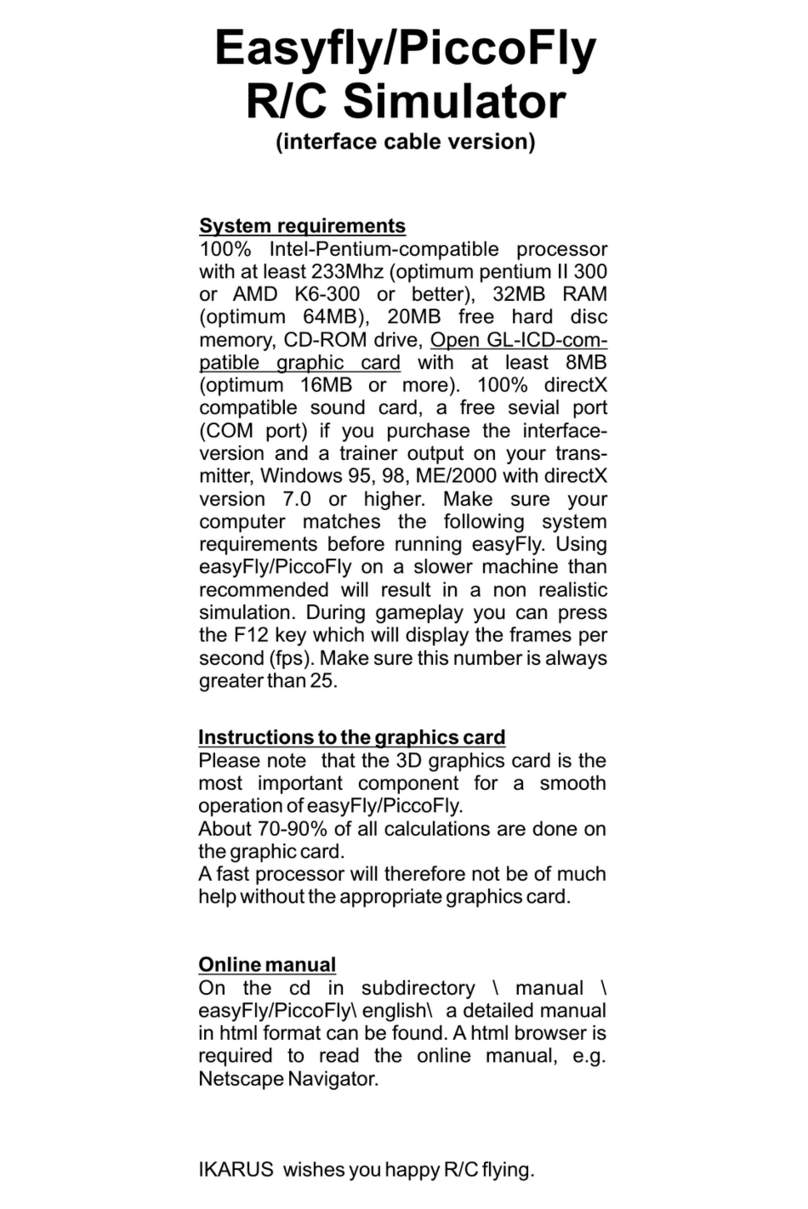
iKarus
iKarus Easyfly Quick installation guide

Intelligent Motion Systems
Intelligent Motion Systems MicroLYNX-4 Quick manual
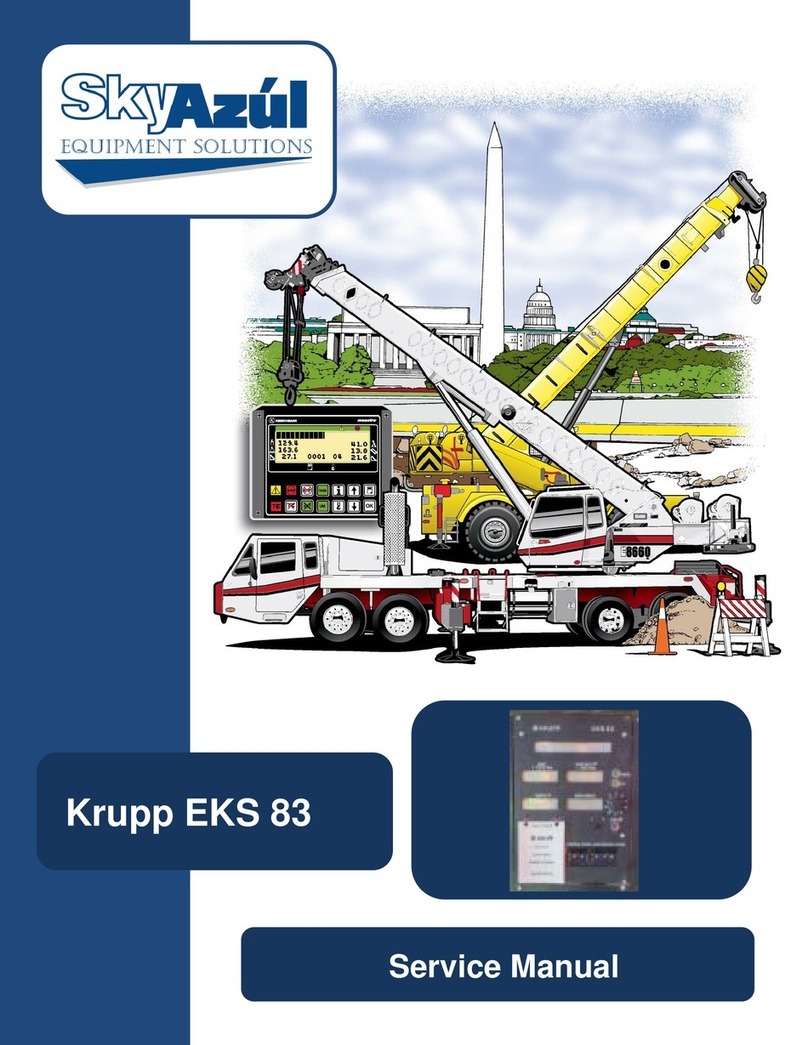
SkyAzúl
SkyAzúl Krupp EKS 83 Service manual
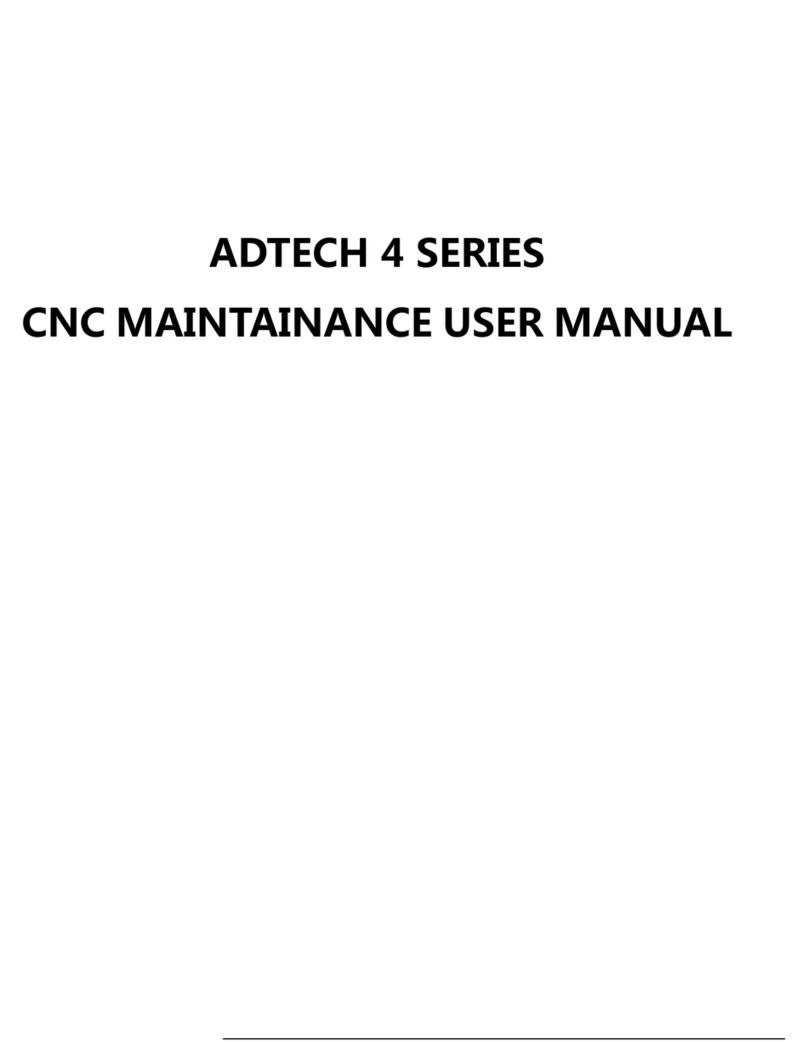
Adtech
Adtech 4 Series Installation and Maintenance user Manual