C-Max VIGO User manual

Table of contents
1. Introduction
2. Summary of Warnings
3. Installation
3.1 Location
3.2 Extending and Retracting the Boom
3.3 Fitting the line to the level-wind
3.4 The Line-Limit Tube
Removing and replacing the line-limit tube
3.5 Power Supply
3.6 Network
3.7 Integration into the Survey Network
3.8 Interfacing with Valeport profilers
3.8.1 Configuring Valeport Connect
3.9 Interfacing with AML profilers
3.9.1 Configuring AML Sailfish
3.9.2 Configuring Vigo Depth Relay
4. Getting Started
4.1 Powering the Winch
4.2 Using the IN and OUT Controls
4.3 Accessing and Navigating the Control Software
4.4 Configuring and Attaching the Profiler
4.5 Setting the Data Transfer Position
5. Profiling
5.1 Selecting a different profiler
5.2 Changing the Profiling Mode
5.3 Changing the Recovery Speed
5.4 Setting the Power Budget
5.5 Acquiring a Profile
Using automatic coverage mode
5.6 Repeating a Profile
Repeat Cast on New SWiFT Message
Repeat Cast after ‘x’ minute(s)
Repeat Cast every ‘x’ meters
6. Action if Power Lost
7. Action if the Profiler becomes caught
8. Routine Maintenance
9. Storage and Transport
2

1. Introduction
The Vigo profiling winch (hereafter referred to as ‘the winch’) simplifies the task of repeatedly
deploying a sound velocity profiler or other instrument (hereafter referred to for simplicity as ‘the
profiler’), either from a moving or stationary vessel, eliminating the need for an operator to manually
collect profiles from the rear deck. It can also be configured for use from unmanned surface vessels
(USV’s).
The system is designed to operate primarily with a Valeport SWiFT SVP, with an option to use a Rapid
SV profiler for deeper water work. Both these profilers feature Bluetooth® data transmission, allowing
automatic retrieval of the recorded profile.
The winch control software allows profiles to be collected manually, when required, or automatically
based on distance or time interval. It is a self-contained system, requiring only single phase 230v
power, and a wired ethernet connection to operate.
The winch incorporates several features designed to make its installation easier and its operation
simpler and more reliable. These features include:-
a) Integrated control and operation software that runs on the winch and is accessed through a
web browser.
b) Built-in GPS receiver.
c) A boom carrying the line sheave that can be extended over the stern for deployment of the
profiler, or retracted for access to the sheave and profiler on completion of the series of casts;
no swiveling platform is needed.
d) A line-limit tube and switch mechanism to alert the operating software that the profiler is very
close to the line sheave.
e) Audible and visual warnings prior to any automatic movement of the winch.
2. Summary of Warnings
The warnings summarised below are intended to prevent injury to personnel and damage to
equipment in what can be a hazardous environment.
OPERATORS OF THIS EQUIPMENT ARE RESPONSIBLE FOR THEIR OWN SAFETY
THE SUPPLIER ACCEPTS NO LIABILITY FOR THE CONSEQUENCES OF EQUIPMENT USE
OVER WHICH IT HAS NO CONTROL
ALWAYS OPERATE THE WINCH WITH THE SPOOL GUARD IN PLACE
ALWAYS OPERATE THE WINCH WITH THE LINE-LIMIT TUBE IN PLACE
BE AWARE THAT THE LINE CAN ACT ABRASIVELY AT HIGH SPEED
AVOID PLACING EXCESSIVE SIDEWAYS FORCE ON THE BOOM
ASSUME THAT THE WINCH MAY OPERATE AT ANY TIME WHEN IT IS POWERED ON
DO NOT STAND ON THE LINE OR STAND INSIDE LOOPS OF LINE THAT MAY BE LYING ON
DECK. DO NOT WRAP THE LINE AROUND YOUR HANDS
ENSURE THE EMERGENCY CRANK HANDLE IS ALWAYS AVAILABLE ON BOARD THE VESSEL
4

3. Installation
3.1 Location
The winch should be mounted at a location which allows the boom to be extended over the stern, far
enough from the vessel outline that the profiler is unlikely to contact the hull.
Apart from its location the height of the mounting platform should be such that when the profiler has
been fully recovered it will be suspended clear, or partially clear, of the water and in a position where it
can reliably transmit data.
If a raised platform is needed this can be a simple wooden structure. The boom should be parallel to
the boat's centreline so that it will experience minimum sideways force when the profiler is deployed
and the boat is underway.
The winch is supplied with eight points at which attachment screws can be fitted. However it can be
secured with as few as six screws if necessary, leaving two of the holes empty.
3.2 Extending and Retracting the Boom
The winch is supplied originally with the boom in the retracted position; a configuration that it will
usually be returned to when not in use.
To extend the boom, release the red latch. This latch pivots on one of the top hinges of the boom, and
when closed, extends outwards to grip one of the other hinges. With the latch lifted pull the end of the
boom outwards until it locks in position. The mechanism that locks the boom reports the fact to the
winch computer which, if powered, switches on the two white LED’s that illuminate the boom area.
This extended position is necessary (in a normal installation) before the computer will allow casts to
be performed, and is confirmed to the operator via the control software.
To retract the boom from the fully extended position, lift the red knob on the levelwind unit. Whilst this
knob is held raised the boom lock is released and the boom can be retracted. Ensure that the rotating
red latch is above the path of the retracting boom then push the boom back fully towards the winch.
When the boom is fully retracted rotate the latch down to secure it.
5

The deployment boom
3.3 Fitting the line to the level-wind
As supplied from the factory, the line is installed into the level-wind wiper arm between the clevis pin
and the removable drop-nose pin, as shown in the illustration below. Should the line need to be
re-fitted it is a simple matter to remove the drop-nose pin, threading the line between the guides and
refitting the pin. Ensure that the toggle on the end of the drop-nose pin is closed fully.
Fitting the line to the level-wind
6

3.4 The Line-Limit Tube
The winch is supplied with a line-limit tube fitted to the line. This item is vital for the correct operation
of the winch.
The sheave assembly mounted at the end of the extending boom incorporates both the main pulley
and, above the line, a smaller wheel. This upper wheel detects when the line-limit tube enters the
sheave assembly and triggers a switch which has two functions, as follows:-
1. It tells the winch to stop pulling the line in, preventing the profiler from impacting the sheave
assembly
2. When performing the pre-launch configuration it enables the winch to position the profiler
automatically a certain distance from the sheave assembly (see section 4.5).
The line-limit tube consists primarily of a flexible tube, one that engages with the upper wheel to rotate
it but without applying excessive force to the sheave assembly. In normal operation, because the
recovered line cannot stop instantly, the tube is carried a little distance through the sheave assembly.
The tube is fitted to the line immediately above the line’s suspension loop, the loop that carries the
profiler’s attachment shackle. In this position it typically stops the line recovery with the shackle 65mm
above the plane of the winch’s mounting platform. If the boat’s freeboard is such that this does not
allow reliable communications then the platform may need to be raised, as already mentioned.
7

The line-limit tube
Removing and replacing the line-limit tube
It is strongly recommended that only genuine C-MAX line-limit tubes are used. Silicone tube is
available in various diameters, thicknesses and grades, and a repair or a substitute may not work as
intended. An unreliable limiting action could result in equipment damage.
To remove the tube, first slacken the gland nut and extract the tapered grommet which it has been
gripping. Pull the grommet off the end of the line past the suspension loop in the line where the
shackle is normally attached. Follow this by removing the gland and tube via the same route.
8

Fitting the replacement tube is the reverse of the removal process. With the new tube in place over
the line follow that with the tapered grommet, tapered end first. Getting the grommet over the
suspension loop can be made easier by passing a light line (eg. cotton thread) through the grommet,
through the line's loop then back through the grommet: this enables the bulky loop to be pulled
through the grommet.
With the grommet just clear of the line's loop advance the tube’s gland over it and tighten. Whilst
tightening the gland continue to press the grommet into it.
3.5 Power Supply
The winch is supplied with a 10m power cable. The power cable should be routed safely to a suitable
230v single phase source and terminated either directly into a switched disconnect or in a suitable
plug. The cable should be protected with a 6 amp fuse or circuit breaker. For operator safety ensure
that all applicable requirements for neutral-earth bonding have been followed when installing the
power cable.
The power connector on the winch has a bayonet locking ring which should be fully rotated to lock the
connector into place and to ensure a watertight seal. Avoid forceful insertion of the power connector
into the receptacle; this can easily damage the plastic bayonet latches on the locking ring.
Conductor colours used in the supplied power cable
The winch will monitor the voltage of the AC supply every second to ensure it is within the range
200-255v. If the supply exceeds these values, a warning will be displayed to the user. If this warning
appears, the user should power down the system and rectify the voltage supply issue before
restarting the system.
9

3.6 Network
The winch is controlled through a web application and to facilitate this a connection to the survey
network is required. A 10m ethernet cable is supplied with the winch as standard. The cable has a
waterproof RJ45 connector on one end that locks onto the corresponding LAN connection on the
left-hand cover of the winch.
Connecting the waterproof RJ45 connector
The ethernet cable should be routed safely to a suitable network switch in the survey room.
NOTE: If the cable needs to be passed through a gland or bulkhead penetration, the dry end RJ45
connector can be removed and subsequently replaced with a standard RJ45 crimp connector using
the EIA-568B wiring colours:
RJ45 wiring to the EIA-568B standard
Do not remove the waterproof RJ45 connector from the cable under any circumstances.
10

The winch is configured to use DHCP by default and will obtain an address automatically if a DHCP
server is present on the network. In the absence of a DHCP response, it will fall back to the static
address of 192.168.0.10
This static address is not easily adjusted by the user so if a DHCP server is not running on the
1
network, the address range of the survey network should be set to match the 192.168.0.X range.
If a DNS server is present on the network, a DNS entry will be registered, the hostname being ‘vigo’.
3.7 Integration into the Survey Network
A typical survey network that is present on a vessel will usually comprise the following components,
connected together by an ethernet switch :-
1. Multibeam sonar
2. Motion sensor
3. GPS receiver
4. Survey computer
To complete the integration into this existing setup, the winch requires a connection to the ethernet
switch and the survey computer requires the addition of a USB Bluetooth or WiFi receiver and, in the
case of certain profilers, the installation of C-MAX’s Vigo Depth Relay software.
This receiver provides the connection to the Sound Velocity Profiler and in conjunction with software
from the profiler manufacturer, enables automatic retrieval of the recorded profile.
1Please contact C-MAX for details if this address needs to be changed
11

The diagram below shows a typical configuration:
A typical equipment configuration
The winch operating software uses the UDP protocol to receive information/messages from third party
software and an echo sounder. To facilitate this, two ports are opened by the winch, bound to the
broadcast address (x.x.x.255) :-
Port 8090 - receives data from Valeport Connect/Valeport Ocean or C-MAX’s Vigo Depth Relay
software.
Port 8091 - receives depth messages from a network connected echo sounder or navigation
system.
Valid depth messages are: $DBT,$DBK,$DBS, & $DPT. There is no requirement to specify
which message to use; depth information will be extracted from any messages as they are received.
With these ports being bound to the broadcast address, there is no requirement to specify the IP
address of the winch either in Valeport Connect/Ocean, C-MAX’s Vigo Depth Relay or in the echo
sounder/navigation system configuration.
If the echo sounder/navigation system configuration requires a destination IP address to be specified,
then enter the broadcast address for your network, x.x.x.255.
12

3.8 Interfacing with Valeport profilers
When profiling with a SWiFT or Rapid profiler, data can be downloaded into Valeport’s Connect
software automatically when the profiler surfaces after each cast. The Connect software runs under
Windows and should be installed on a PC that is connected to the survey network.
It is recommended that this PC be equipped with an external Bluetooth receiver and magnetic mount
antenna, part number 0660EA3, supplied by Valeport Ltd. to improve the performance of the
Bluetooth link. This module and antenna replaces the receiver usually supplied with the SWiFT or
Rapid profilers.
The module is supplied with a 10m antenna that would typically be positioned near the stern of the
vessel. On smaller vessels or autonomous platforms, this antenna can be positioned on the main
antenna platform, typically in the centre of the vessel, and well above the waterline.
The profiler will need to be paired to the Bluetooth module before use, using the Valeport Bluetooth
Configurator utility available from http://www.valeport.download
Pairing the profiler to this module will remove the pairing to the original receiver. If the profiler is to be
used with either the original receiver, or on another vessel equipped with an external module, the
pairing procedure will need to be completed again.
3.8.1 Configuring Valeport Connect
Connect version 1.0.7.0 is required: this can be downloaded from http://www.valeport.download
It is advisable to set the profiler into automatic mode. This will cause Connect to broadcast a message
via the UDP broadcast address when the latest profile has downloaded. Please review the Connect
Software Operating Manual, document 8500800b, available from the Valeport Download site.
When configuring Connect to work in automatic mode, it should be set to enable the broadcast of the
‘Winch Go message’. The ‘Pause after download’ option should be changed from the default 60s to
2s, all other settings can be left as the default.
13

Configuring Valeport Connect to operate in automatic mode
It may be necessary to allow Connect to access the network through the Windows Firewall. In this
case, a popup message will appear when Connect tries to send the first message.
3.8.2 Valeport Ocean software
Since the initial release of this operation manual, Connect has been superseded by Ocean. This new
software package works in a similar way and all configuration options are in the same location. It is
available for download from www.valeport.download
C-MAX recommends the use of Ocean in all cases where a SWiFT profiler is used. Users of the
rapidPro profilers should continue to use Connect until advised otherwise by Valeport.
3.9 Interfacing with AML profilers
The Vigo can be used with either the AML3 or AML6 profilers, in the ‘-LGR’ variant. These profilers
connect to the survey computer using WiFi and download their data automatically on completion of a
profile.
AML Sailfish software does not have the functionality to send the depth of the profile to the Vigo, so
an additional software utility is used to enable this feedback loop.
14

C-MAX’s Vigo Depth Relay software is run on the same PC as Sailfish and performs the following
functions:
1. Watch a folder for new profile files downloaded by Sailfish from the profiler.
2. Parse the file and extract the maximum depth value from the data.
3. Send this information in the correct format over the network to the Vigo.
3.9.1 Configuring AML Sailfish
AML’s Sailfish software should be configured to automatically connect to a detected profiler and
automatically download log files. The operator should take a note of the ‘download folder’ location as
this will be required when configuring the Vigo Depth Relay software in the next step.
15

Configuring AML Sailfish software to operate in automatic mode
3.9.2 Configuring Vigo Depth Relay
Vigo Depth Relay is supplied as a self contained executable file requiring the Microsoft .NET runtime
2
version 5.0 to run. It monitors a specified folder for new files, extracts the depth and broadcasts this
over the survey network in the same manner as Valeport Connect.
Vigo Depth Relay can be used with either AML profilers or older Valeport profilers that do not work
with the latest version of Connect.
Three settings need to be configured before use:
1. The type of profiler being used
2. The folder to watch for new files
3. The network adapter to use to connect to the survey network
2Please contact C-MAX for download details
16

Vigo Depth Relay when first loaded
The settings are changed by accessing the ‘File’ menu as shown below.
Accessing the file menu to configure the settings
Begin by selecting the ‘Watch Folder’. This is the folder on the computer where new log files are
saved when downloaded automatically from the profiler.
17

Selecting a folder to watch for new files
With the watch folder selected, the display will now show the name of this folder in the lower part of
the window. Hovering the mouse over this will show a tooltip with the full path to the folder. Check that
this matches the download folder that was configured in Sailfish earlier.
Continue by selecting the type of profiler that is being used.
Selecting the profiler
With a profiler selected, Vigo Depth Relay will know which file types to process when they are added
automatically to the watch folder.
18

The final setting to configure is the network adapter used to connect this PC to the survey network.
This would typically be a wired ethernet connection and it should be on the same logical subnet as the
Vigo winch.
There is no need to specify the IP address of the Vigo, all data is sent to the broadcast address.
Selecting a network adapter
Vigo Depth Relay will force you to select an adapter that is connected. You should check the IP
address field to check that the selected adapter is correct.
Clicking the ‘Look for Vigo’ button will send a custom query message to the broadcast address. Any
Vigo that is powered on, with its web control panel open will respond to this query .
3
A dialog will alert the user if a Vigo is found on the network.
When the three settings have been configured, Vigo Depth Relay will appear as shown below.
3Vigo operating software version 2021.05.11b or later is required for this functionality to work
19

Vigo Depth Relay waiting for a new file
When a file is written into the watch folder, Vigo Depth Relay will process the file, extract the depth,
update the user interface and broadcast the depth to the Vigo over the network. New files are added
to the log, with the newest at the top.The log can be cleared through a right-click context menu.
Processing an AML record from the watch folder
20
Table of contents
Popular Winch manuals by other brands
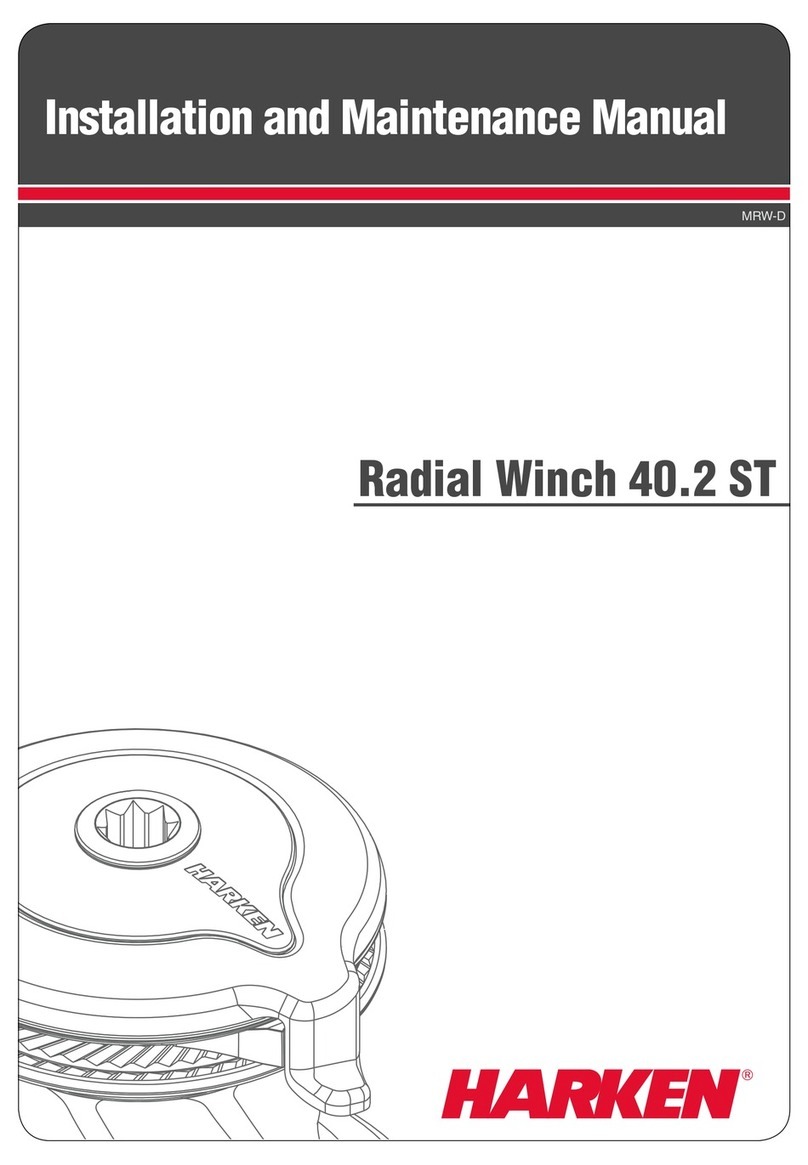
Harken
Harken Radiial 40.2 ST Installation and maintenance manual
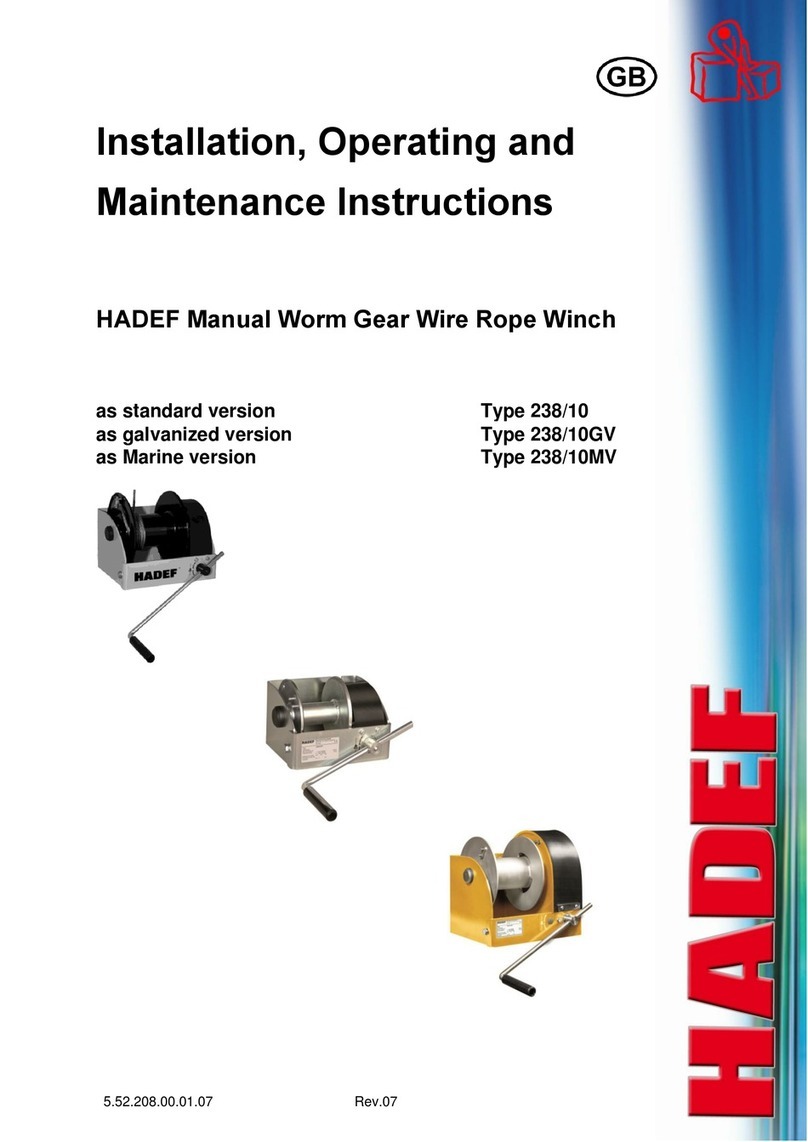
HADEF
HADEF 238/10MV Installation, Operating and Maintenance Instruction
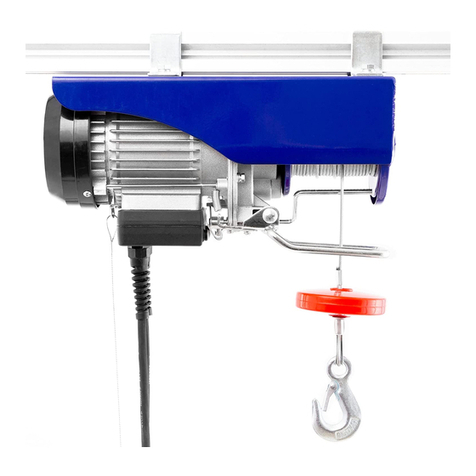
Einhell Global
Einhell Global SHZ 300-2 operating instructions
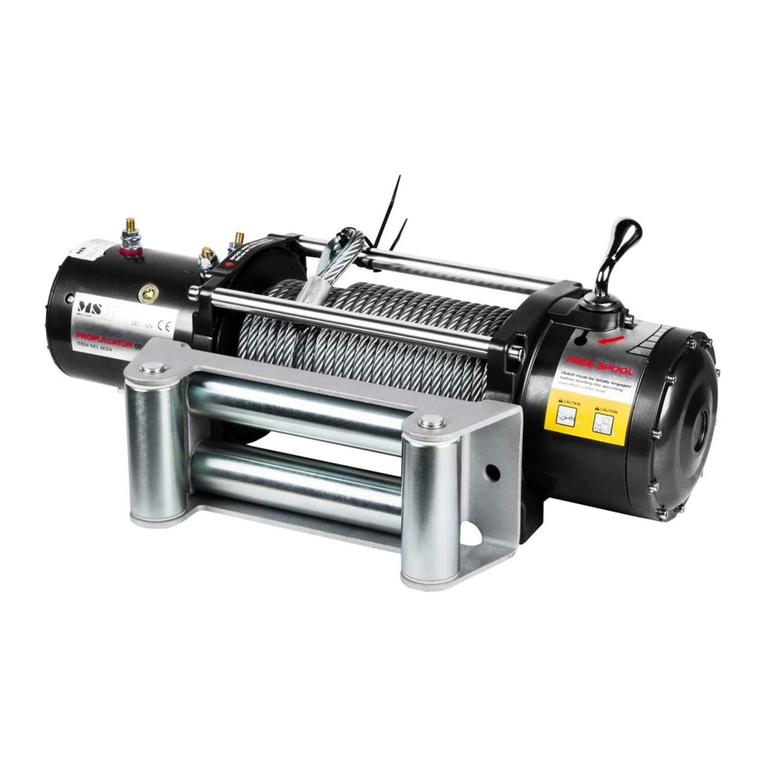
MSW
MSW Propullator 13500-PRO user manual
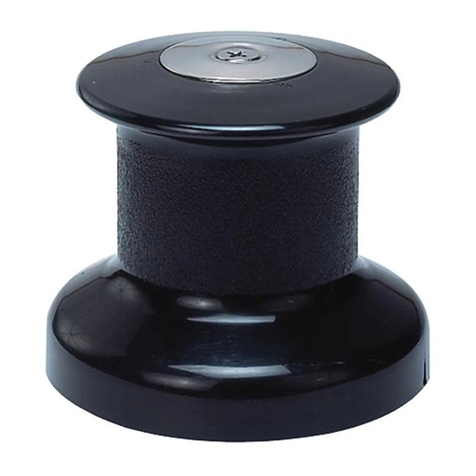
Antal
Antal W 6 Instructions For Fitting
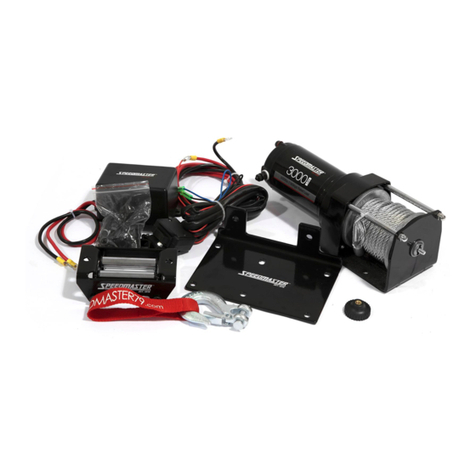
SPEEDMASTER
SPEEDMASTER PCE553.1002 Installation