Chino IRGMEG2 Series User manual

INST.No.INE-479-P0 Software Version 1.0
IRMA·IRGMEG2 series
For Infrared multiple-constituents
analyzer Operatorinterface/displayunit
Model: IRGMEG2S
(MODBUS Protocol Communications)
Store this manual in a readily accessible
location for future reference.
This manual should be provided to the end user.

INST.No.INE-479-P0 Software version 1.0
-Contents-
1. Introduction···················································1
1.1 Models of infrared multiple-constituents
analyzer detector···································1
1.2 Models of infrared multiple-constituents
analyzer operator interface/display unit·2
2. Specifications of communications················2
3. Connections ···················································3
3.1 Connections of IRMA series infrared
multiple-constituents analyzer detector
IRMA········································3
3.2 Connection between IRMA series
and personal computer:
In case of using communication
interface converter K3SC-10···············4
3.2.1 In case of using IRMA series
exclusive use cable······························4
3.2.2 In case of using a cable that
customer made with a self ·····················4
3.3 Connections of IRGMEG2 series
infrared multiple-constituents analyzer
operator interface/display unit···············5
3.3.1 Rear terminal board figure of
IRGMEG2 ······································5
3.3.2 Example of IRGMEG2 connections··5
4. MODBUS protocol-Message ··················6
4.1 Message frame configuration····················6
4.2 Slave address: Detector No. ······················6
4.3 Function code············································6
4.4 Data department········································7
4.4.1 Data configuration··································7
4.4.2 Reference No. ········································7
4.5 Error check················································7
4.5.1 Calculation of CRC-16···························7
5. MODBUS protocol-Function code·············· 8
5.1 Function code············································8
5.2 Function code of an analogue input data···8
5.2.1 Reading of an analogue input data ·········8
5.2.2 Reference table of an analogue
input data·············································9
5.3 Function code of an analogue
setting value······································12
5.3.1 Reading of an analogue setting value···12
5.3.2 Writing of an analogue setting value····12
5.3.3 Writing of a plural analogue
setting value··································13
5.3.4 Reference table of an analogue
setting value······································13
5.4 Function code of a digital setting value···16
5.4.1 Reading of a digital setting value·········16
5.4.2 Writing of a digital setting value··········17
5.4.3 Writing of a plural digital setting value···17
5.4.4 Reference table of a digital
setting value··································18
5.5 Communication check between
the master and slave(Loop back test) ·18
6. MODBUS protocol- Data interval
/Answer at the time of abnormality······ 19
6.1 Time interval of data·······························19
6.2 Answer at the time of abnormality ··········19
6.2.1 In case of no answer·····························19
6.2.2 Answer of an error message ·················20
6.2.2-1) Format of an error message ·············20
6.2.2-2) Error code table·······························20
■Symbols in this instruction manual
The symbols shown below are used depending on important degrees for using the thermometer
safely and avoiding unexpected situations.
Important
degree Symbols Contents
1This symbol is attached to a title for the sentence with .
2For avoiding dangerous accidents (may cause death or serious injury)
like as electrical shock, fires, or troubles/damages of the thermometer.
3For avoiding injury or in physical damage to the thermometer.
4Information that we suggest to read carefully.
5Information that you can use as a reference.
!
Contents
!
!
Warning
Warning
Remarks
Reference
Caution
!

INST No. INE-479-P0Software version 1.0
-1-
This instruction manual is explaining about the communication betweenthe personal computer
such as upper class devices and “IRMA series Infrared multiple-constituents analyzer detector
IRMAS” or “IRGMEG2 series infrared multiple-constituents analyzer operator interface/
display unit IRGMEG2R (A,S)”.
The communication protocol is able to select it from 2 modes of [MDBUS RTU mode] or [Chino
exclusive use protocol PRIV modes] by selection/setting of the communication protocol.
This instruction manual is explaining about the [MODBUS RTU mode] only.
1.1 Models of infrared multiple-constituents analyzer detector
IRMA
Model type classification
▪1000 series ·····Moisture meter (Mirror type)
11: General-purpose type
12: High moisture type
13: Very-low moisture type
▪2000 series ·····Moisture meter (Fiber type)
21: General-purpose type
22: High moisture type
▪5000 series ·····Multiple-constituents meter (Mirror type)
51: Multi-constituents (NIR)
52: Multi-constituents (Thin-film, Infrared)
▪6000 series ·····Multiple-constituents meter (Fiber type)
61: Multi-constituents
▪7000 series ·····Thickness/coating-thickness meter (Mirror type)
71: Thickness/coating-thickness
72: Thin-film/coating-thickness
▪8000 series ·····Thickness/coating-thickness meter (Fiber type)
81: Thickness/coating-thickness
Number of wavelength and Number of constituent
00 : Except for the 00:5000, 6000 series
: Only 5000, 6000 series
Wavelength: 2 to 0 (Designate 2 to 10)
Constituent : 1 to 4 (Designate 1 to 4)
Communication interface (*1)
S: RS-485 (standard)
L: LAN (option)
(*1) To be specified. In case of connecting to IRGMEG2(IM series
infrared multiple-constituent analyzer operator interface/display unit)
it is RS-485 communications.
Special specifications
Blank: Standard
1 : For small diameter
2 : Dust laying
3 : Special gain
4 : P polarized light
1. Introduction
In case of using [Chino exclusive use protocol PRIV], read the separate manual
“IRGMEG2 series infrared multiple-constituents analyzer operator interface
/
display unit Model for IRGMEG2R (A,S)(Chino exclusive use protocol PRIV)”.
Reference

INST No. INE-479-P0Software version 1.0
-2-
1.2 Models of infrared multiple-constituents analyzer
operator interface/display unit
IRGMEG2Communication interface
R: RS-232C (standard)
A: RS-422A
S: RS-485
*In case of connecting with IM-VXA, it is RS-232C.
Special specifications
Blank: Standard
V : Complying with CE
Item Specifications
Communication method Half-duplex communication system
Communication protocol MODBUS protocol RTU mode
Communication speed 19200, 9600 bps (switching)
Start bit length 1 bit
Data bit length 8 bits
Parity bit Even/odd/none (switching)
Stop bit length 1 bit/2 bits (switching)
Transmission code Binary
Error check CRC-16
Data transmission procedure Non-procedure
1. Introduction
2. Specifications of communications

INST No. INE-479-P0Software version 1.0
-3-
3.1 Connections of IRMA series
infrared multiple-constituents analyzer detector IRMA
The internal terminal board is accessible by removing the terminal board cover of the detector unit.
Lead in cables through the upper cable glands, and connect them to respective terminals.
Lead in the exclusive cable IR-WERP (Ø10mm outer diameter) through the cable gland 1.
Lead in a signal cable through the cable grand 2.
Read the separate manual “IRMA series infrared multiple-constituents analyze
r
detector unit Model for IRMA” without fail.
Make sure that all mains power is turned off to prevent an electric shock whe
n
connecting power to the power terminals.
!
Warning
M
ake sure to use the signal cable with the outer diameter of Ø7.0 to 12.5mm.
Use cables suiting to the applicable outer diameter of the cable glan
d
, otherwise
waterproofing of the detector unit may deteriorate. Tighten the cable glands wit
h
the nuts and fix the terminal board cover securely after wiring.
!
3. Connections
Remarks
Reference
Caution
P+ P-
OUT+ OUT-
SA SB SG DI
COM
DO
COM
IN+ IN-
24VDC 4-20mADC RS-485 DIGITAL IN DIGITAL OUT 4- 20mADC
P+ P-
OUT+ OUT-
SA SB SG DI
COM
DO
COM
IN+ IN-
24VDC 4- 20m AD C RS-485 DIGITAL IN DIGITAL OUT 4-20mADC
-V +V
OUTPUT
DC 24V 2.1A
DC ON
DC LOW
V.ADJ
INPUT 50/60Hz
AC100-240V 1.3A
Setting display unit of
Personal computer
sequencer communication
out
p
ut Recorder etc
Analog output :4-20mA DC
Connection cable lead-in part
• Outer diameter of applicable
connection cable
(ø7.0 to ø12.5)
Connection cable
(IR-WERP) Communication output :RS-485
Power unit
(IR-WEP)
P-
(Blue)
Power suppl
y
100-120V AC
200-240V AC
Protective grounding
Contact inpu
t
Contact output
Correction input
P+
(Red) G
(Green)
G (Green)
P+
(
Red
)
P-(Blue)
SA(Black)
SB(White)
SG(Brown)

INST No. INE-479-P0Software version 1.0
-4-
3.2 Connection between IRMA series and personal computer
: In case of using communication interface converter K3SC-10
This chapter is explaining the connection method between IRMA and personal computer.
A communication interface converter (for RS-485 ↔RS-232C) is required for connecting IRMA
series and personal computer, because the communication interface of IRMA is RS-485.
This chapter is explaining the case to use K3SC-10 made of the Omron Corporation.
3.2.1 In case of using IRMA series exclusive use cable
Detector IRMA series
side
Communication
interface converter
K3SC-10 side
Personal computer
side
Terminal
NameTerminal
NoTerminal
NameTerminal
NoTerminal
NameTerminal
No
SA 6 SD 5 SD 2
SB 7 RD 6 RD 3
SG 8
SG 3 SG 5
SDB(+) 12
SDA(+) 9
SG 7
3.2.2 In case of using a cable that customer made with a self
Detector IRMA series
side
Communication
interface converter
K3SC-10 side
Personal computer
side
Terminal
NameTerminal
NoTerminal
NameTerminal
NoTerminal
NameTerminal
No
SA 6 SD 5 SD 3
SB 7 RD 6 RD 2
SG 8
SG 3 SG 5
SDB(+) 12 RS 7
SDA(+) 9 CS 8
SG 7 DR 6
ER 4
!
3. Connections
Read the separate manual “IRMA series infrared multiple-constituents analyze
r
detector unit Model for IRMA” without fail.
Remarks

INST No. INE-479-P0Software version 1.0
-5-
3.3 Connections of IRGMEG2 series infrared multiple-constituents
analyze operator interface/display unit
3.3.1 Rear terminal board figure of IRGMEG2
3.3.2 Example of IRGMEG2 connections
Example of attaching places of ferrite cores
(3 pieces attached as standard)
: To be attached absolutely
: At any place (Note)
Read the separate manual “IRMA series infrared multiple-constituents analyze
r
operator interface/display unit Model for IRGMEG2” without fail.
Make sure that all mains power is turned off to prevent an electric shock whe
n
connecting power to the power terminals.
!
Warning
!
3. Connections
Remarks
Terminal board on the
rear panel of this unit
[RS-232C]
Terminal board on the
rear
p
anel of this unit
[RS-422A]
Terminal board on the
r
ea
r
pa
n
e
l
o
f
t
hi
s
u
ni
t
[RS-485]
High-order side terminals High-order side terminals High-order side terminals
20 2219 21 23
SD RD SG
RD SD SG
19 20 21 22 23
SDA RDA SG
SG
SDB RDB
RDA RDB SDA SDB
20 21 2219 23
SA SB SG
RA RB SG
IRGMEG2
IRGMEG2
V (complying with CE)
Comm output Comm output
A
L2 low alarm output
A
L1 high alarm output
Self-diagnosed
abnormal
A
larm output Contact
OFF when an
abnormal condition
occurs
Output 2
4 to 20mA DC
SA (black)
SB (white
)
SG (brown
)
To the
detector unit Contact input
Output 1
4 to 20mA DC
Power
100 to 240V AC
A
L2 low alarm output
A
L1 high alarm output Protective
ground
Power
24V DC
Protective
ground Self-diagnosed
abnormal
A
larm output Contact
OFF when an
abnormal condition
occursOutput 1
4 to 20mA DC
To the
detector unit Contact input
(Note) If 4 pieces or more are required, order them separately.
Comm output
Refer to [3.1.1 Rea terminal
board figure of IRGMEG2]

INST No. INE-479-P0Software version 1.0
-6-
4.1 Message frame configuration
The MODBUS message is the configuration like a list shown below.
Due to the MODBUS RTU mode, the message is configured of all the binary data.
Slave address →Refer to [4.2 Slave address: Detector No.]
Function code →Refer to [4.3 Function code]
Data →Refer to [4.4 Data department]
Error check →Refer to [4.5 Error check]
4.2 Slave address: Detector No.
Program the slave address (the detection number) in 1 to 9 ranges previously by using front key.
The master usually communicates it to 1 slave.
All the connected devices are received the message from the master in common.
However, the only slave in accord with the slave address answers the message.
4.3 Function code
The function code is the implementation command code to a slave (detector).
Each data is the next classification approximately.
(1) Analog input data Measured data, Status etc.
(2) Analog setting value Various kinds setting information such as the detector, calibration curve.
(3) Digital setting value Smoothing/Real switching, Preset output ON/OFF etc.
[List of function code]
Code Function Unit Reference chapter
04 Reading of an analogue input data 16 bits 5.2.1
03 Reading of an analogue setting value 16 bits 5.3.1
06 Writing of an analogue setting value 16 bits 5.3.2
16 Writing of a plural analogue setting value 5.3.3
01 Reading of a digital setting value 1 bit 5.4.1
05 Writing of a digital setting value 1 bit 5.4.2
15 Writing of a plural digital setting value 5.4.3
08 Communication check between the master and slave 5.5
4. MODBUS protocol-Message
Programming to the slave address (the detector number) of IRMA series.
·PressSEL key and ENT key for more than 2 seconds simultaneously and move to
[Setting operation conditions] mode screen.
·By pressing the SEL key several times, program it at the item of [Detecto
r
number (Hn)].
(Refer to [6.4 Setting operation conditions] in the separate manual “IRMA series
infrared multiple-constituents analyzer detector unit Model for IRMA”.
Details, refer to [5.3.4 Reference table of an analogue setting value] and [5.4.4
Reference table of a digital setting value].
Remarks
Reference

INST No. INE-479-P0Software version 1.0
-7-
4.4 Data department
4.4.1 Data configuration
The configuration of the data differs by the function code.
The demanded data from the master is configured of the code number (Relative number that
calculates it from [4.4.2 Reference No.]) and data number etc. to the reading and writing of the
object data. The answer from the slave is configured of the demanded data etc.
The basis data of MODBUS is all the integers of 16 bits and the existence or nonexistence of the
mark is prescribed at each data.
4.4.2 Reference No.
"The reference number" of the list shown below is assigned to the data inside IRMA series infrared
multiple-constituents analyzer detector unit Model for IRMA.
This number is required to the reading and writing of data.
It is classified like the list shown below by the kind of data.
The number appointment in the message is "Relative number" that corresponds to each reference
number.
Kind of data Reference number Relative number
Digital setting value 1 to 10000 Reference number: 1
Digital input data 10001 to 20000 Reference number: 10001
Analog input data 30001 to 40000 Reference number: 30001
Analog setting value 40001 to 50000 Reference number: 40001
4.5 Error check
The error check of the communication frame uses CRC-16.
4.5.1 Calculation of CRC-16
The communication method of the CRC system divides the information that should be sent with the
generation polynomial expression and add the remainder behind information.
The generation polynomial expression is as follows.
Calculate the data from the slave address to last data with the following procedure.
1) Initialize the data of CRC-16 (It makes X): (=FFFFH)
2) Exclusive OR of data 1 and X: (EX-OR) →X
3) Shift X to the right 1 bit →X
4) If a carry comes out, take A001H and Ex-OR. Move to 5) if a carry does not come out.
5) Repeat the above 3) to 4) until it shifts 8 times.
6) Next data and X of Ex-OR →X
7) With from 3) to 5) same.
8) Repeats it to the last data.
9) The message is made in order to the upper class from the subordinate class of calculated 16 bits
data (X).
The relative number of the measured value (temperature data) of "reference numbe
r
30011" becomes "10".
4. MODBUS protocol-Message
The data of an error check becomes , because CRC-16 becomes
1241H in the case that data is .
02H 07H
41H 12H
Remarks
1+X
2
+X
15
+X
1
6
Remarks

INST No. INE-479-P0Software version 1.0
-8-
5.1 Function code
Following columns from [5.2 Function code of an analogue input data] to [5.4 Function code of a
digital setting value] is explaining the answer at each function code.
5.2 Function code of an analogue input data
5.2.1 Reading of an analogue input data
[Function code: 04 (04H)]
Continuously analogue input data (2 bytes: 16 bits) is read out only the designated number from
the designated No.
The data of the answer message is configured with arranged at the order of the number that was
divided to an upper class 8 bits and subordinate class 8 bits.
Refer to [6.2 Answer at the time of abnormality] about the answer at the time o
f
abnormality.
The example of an answer is simila
r
to [Function code 03].
*: The start No (relative number) is [Reference number-30001].
5. MODBUS protocol-Function code
Remarks
Remarks

INST No. INE-479-P0Software version 1.0
-9-
5.2.2 Reference table of an analogue input data
Application function Write (Writing): None
Read (Reading): 04
No Data name Detailed contents Data format Reference
30001 Model code 1,2 column ASCII data
30002 Model code 3,4 column ASCII data
30003 Model code 5,6 column ASCII data
30004 Model code 7,8 column ASCII data
30005 Model code 9,10 column
Reference to following
model code
ASCII data
Model code 1, 2 column
Model code 3, 4 column
Model code 5, 6 column
Model code 7, 8 column
Model code 9, 10 column
IRMA
Model type classification
▪1000 series ·····Moisture meter (Mirror type)
11: General-purpose type
12: High moisture type
13: Very-low moisture type
▪2000 series ·····Moisture meter (Fiber type)
21: General-purpose type
22: High moisture type
▪5000 series ·····Multiple-constituents meter (Mirror type)
51: Multi-constituents (NIR)
52: Multi-constituents (Thin-film, Infrared)
▪6000 series ·····Multiple-constituents meter (Fiber type)
61: Multi-constituents
▪7000 series ·····Thickness/coating-thickness meter (Mirror type)
71: Thickness/coating-thickness
72: Thin-film/coating-thickness
▪8000 series ·····Thickness/coating-thickness meter (Fiber type)
81: Thickness/coating-thickness
Number of wavelength and Number of constituent
00 : Except for the 00:5000, 6000 series
: Only 5000, 6000 series
Wavelength: 2 to 0 (Designate 2 to 10)
Constituent : 1 to 4 (Designate 1 to 4)
Communication interface
S: RS-485 (standard)
L: LAN (option)
Special specifications
Blank: Standard
1 : For small diameter
2 : Dust laying
3 : Special gain
4 : P polarized light
5. MODBUS protocol-Function code

INST No. INE-479-P0Software version 1.0
-10-
Data format I: 16bits integer
F: 32bits actual number (IEEE754 form)
No Data name Detailed contents Data format Reference
30011 Upper class 16 bits
30012
Measured value
(Constituent 1: Constituent value)
Measured value of
Constituent 1FSubordinate class 16 bits
30013 Upper class 16 bits
30014
Measured value
(Calculation mode 1: X)
Absorbance of
Calculation mode 1 FSubordinate class 16 bits
30015 Upper class 16 bits
30016
Measured value
(Constituent 2: Constituent value)
Measured value of
Constituent 2FSubordinate class 16 bits
30017 Upper class 16 bits
30018
Measured value
(Calculation mode 2: X)
Absorbance of
Calculation mode 2 FSubordinate class 16 bits
30019 Upper class 16 bits
30020
Measured value
(Constituent 3: Constituent value)
Measured value of
Constituent 3FSubordinate class 16 bits
30021 Upper class 16 bits
30022
Measured value
(Calculation mode 3: X)
Absorbance of
Calculation mode 3 FSubordinate class 16 bits
30023 Upper class 16 bits
30024
Measured value
(Constituent 4: Constituent value)
Measured value of
Constituent 4FSubordinate class 16 bits
30025 Upper class 16 bits
30026
Measured value
(Calculation mode4: X)
Absorbance of
Calculation mode 4 FSubordinate class 16 bits
30027 Measurement status Bit0: Smoothing
/Real
Bit1: Preset
Bit2: Hold
Bit3: Remote/Local
Bit4: Absorbance
display
Bit5: Surface wate
r
ratio computation
Bit6:Sample
temperature
correction
Bit7 to 15: Open
I
30028 Alarm status Bit0: Self-diagnosis
abnormal
Bit1: Low limit
constituent 1 alarm
Bit2: High limit
constituent 2 alarm
Bit3: Low limit
constituent 1 alarm
Bit4: High limit
constituent 2 alarm
Bit5: Low limit
constituent 3 alarm
Bit6: High limit
constituent 3 alarm
Bit7: Low limit
constituent 4 alarm
Bit8: High limit
constituent 4 alarm
Bit9 to 15: Open
I
5. MODBUS protocol-Function code

INST No. INE-479-P0Software version 1.0
-11-
Data format I: 16bits integer
F: 32bits actual number (IEEE754 form)
No Data name Detailed contents Data format Reference
30029 Device statusBit0: EEPROM abnormal
Bit1: Motor rotation
abnormal
Bit2: Open
Bit3: Calculation error
Bit4: Element temp
abnormal
Bit5: Ambient temp. too hig
h
Bit6: Ambient temp. too low
Bit7: Sample temp. too high
Bit8: Sample temp. too low
Bit9: Sample low reflection
Bit10: Sample high
reflection
Bit11: Number of calibration
curves insufficient for
sample temperature
correction
Bit12 to 15: Open
I
30051 Upper class 16 bits
30052
Wavelength 1
data FSubordinate class 16 bits
30053 Upper class 16 bits
30054
Wavelength 2
data FSubordinate class 16 bits
30055 Upper class 16 bits
30056
Wavelength 3
data FSubordinate class 16 bits
30057 Upper class 16 bits
30058
Wavelength 4
data FSubordinate class 16 bits
30059 Upper class 16 bits
30060
Wavelength 5
data FSubordinate class 16 bits
30061 Upper class 16 bits
30062
Wavelength 6
data FSubordinate class 16 bits
30063 Upper class 16 bits
30064
Wavelength 7
data FSubordinate class 16 bits
30065 Upper class 16 bits
30066
Wavelength 8
data FSubordinate class 16 bits
30067 Upper class 16 bits
30068
Wavelength 9
data FSubordinate class 16 bits
30069 Upper class 16 bits
30070
Wavelength 10
data
The data prescribed as 1, in
case of calibrating with the
output checker plate.
FSubordinate class 16 bits
The wave
-length data is
logged in case
of demanding
the wavelength
data logging to
detector.
30071 Gain value 0 to 3 I
5. MODBUS protocol-Function code

INST No. INE-479-P0Software version 1.0
-12-
5.3 Function code of an analogue setting value
5.3.1 Reading of an analogue setting value
[Function code: 03 (03H)]
Continuously analogue setting value (2 bytes: 16 bits) is read out only the designated number
from the designated No. The reading order is an upper class (H) 8 bits, the subordinate class (L) 8
bits.
5.3.2 Writing of an analogue setting value
[Function code: 06 (06H)]
Program the analogue setting value of the designated No to the designated value.
[Example] Reading of upper class “H” data and subordinate class “L” data of
calibration curve coefficient a0 of slave 1.
(Reading out 2 data of reference No 40022 to 40023)
Reference No 40022 40023
Data 42F6H E666H
<RTU mode>
Master →Device Device →Master
Upper class as personalIRMA series
Slave address 01H Slave address 01H
Function code 03H Function code 03H
Start No (H) *1 00H Number of data *2 04H
Start No (L) *1 15H a0 data H (H)*3 42H
The number (H) *3 00H a0 data H (L)*3 F6H
The number (L) *3 02H a0 data L (H)*3 E6H
CRC (L) *4 D5H a0 data L (L)*3 66H
CRC (H) *4 CFH CRC (L) *4 C4H
CRC (H) *4 33H
*1: Start No (Relative No) is "Reference No-40001".
*2: The data number is the byte number of data. (It is not the demand number).
*3: The reading order is an upper class (H) 8 bits, the subordinate class (L) 8 bits.
*4: The reading order is the subordinate class (L) 8 bits, an upper class (H) 8 bits.
←a0 = 123.45
Example of (Floating point: 42F6E666)
Same answer as a command message at the time of a normal answer.
[Example] Progra
m
the [Constituent 1: Calibration curve No] to “1”.
Program the [Analog setting value reference No 40001] to “1”.
<RTU mode>
Master →Device Device →Master
Upper class as personal IRMA series
Slave address 01H Slave address 01H
Function code 06H Function code 06H
Setting value No (H) *1 00H Setting value No (H) *2 00H
Setting value No (L) *1 00H Setting value No (L) *2 00H
Setting condition (H) 00H Setting condition (H) *2 00H
Setting condition (L) 01H Setting condition (L) *2 01H
CRC (L) 48H CRC (L) *3 48H
CRC (H) 0AH CRC (H) *3 0AH
*1: Setting value No (Relative No) is "Reference No-40001".
*2: The writing order is an upper class (H) 8 bits, the subordinate class (L) 8 bits.
*3: The writin
g
order is the subordinate class
(
L
)
8 bits, an u
pp
er class
(
H
)
8 bits.
5. MODBUS protocol-Function code
Remarks
Remarks
Reference

INST No. INE-479-P0Software version 1.0
-13-
5.3.3 Writing of a plural analogue setting value
[Function code: 16 (16H)]
Program the plural designated analogue setting value of the designated No to the designated value.
The data is communicated with arranged at the order of the number that was divided to an upper
class 8 bits and subordinate class 8 bits.
5.3.4 Reference table of an analogue setting value
Application function Write (Writing): 06/16 Data format I: 16bits integer
Read (Reading): 03 F: 32bits actual number (IEEE754 form)
No Data name Setting
range Default Data
format Reference
40001 Calibration curve No 1 to99 1.000 I
40002 Decimal place displaying0 to 4 1 I
40003
Constituent 1
Time constant0.0 to 99.9
(0 to 999) 0.2 (2) I 10 times value
sending/receiving
40004 Calibration curve No 1 to99 1.000 I
40005 Decimal place displaying0 to 4 1 I
40006
Constituent 2
Time constant0.0 to 99.9
(0 to 999) 0.2(2) I
10 times value
sending/receiving
40007 Calibration curve No 1 to99 1.000 I
40008 Decimal place displaying0 to 4 1 I
40009
Constituent 3
Time constant0.0 to 99.9
(0 to 999) 0.2(2) I
10 times value
sending/receiving
40010 Calibration curve No 1 to99 1.000 I
40011 Decimal place displaying0 to 4 1 I
40012
Constituent 4
Time constant0.0 to 99.9
(0 to 999) 0.2(2) I
10 times value
sending/receiving
40014 Constituent No displaying 0 to 4 1 I
40015 Analog output · Contact output
(High/Low alarm) Constituent No1 to 4 1 I
[Example] Progra
m
the [Calibration curve coefficient a0] of slave 1 to “0.123
(Floating point: 3DFBE76D)”.
Program the [Analog setting value reference No] to 40022 up 40023
<RTU mode>
Master →Device Device →Master
Upper class as personal IRMA series
Slave address 01H Slave address 01H
Function code 16H Function code 16H
Start No (H) *1 00H Start No (H) *2 00H
Start No (L) *1 15H Start No (L) *2 15H
The number (H) *2 00H The number (H) *2 00H
The number (L) *2 02H The number (L) *2 02H
Data number 04H CRC (L) *3 50H
First data (H) *2 3DH CRC (H) *3 0CH
First data (L) *2 FBH
Second data (H) *2 E7H
Second data (L) *2 6DH
CRC (L) *3 C4H
CRC (H) *3 DCH
*1: Start No (Relative No) is "Reference No-40001".
*2: The writing order is an upper class (H) 8 bits, the subordinate class (L) 8 bits.
*3: The writing order is the subordinate class (L) 8 bits, an upper class (H) 8 bits.
5. MODBUS protocol-Function code
Remarks

INST No. INE-479-P0Software version 1.0
-14-
Data format I: 16bits integer
F: 32bits actual number (IEEE754 form)
No Data name Setting
range
D
efault Data format Reference
40016 Contact input usage0 to 3
0: NONE
1: HOLD
2: PRESET
3: SMT.RL
0 I NONE: None
HOLD: Hold
PRESET: Preset
SMT.RL:
Smoothing/Real
40017 Contact input usage0 to 2
0: NONE
1: ALARM
2: ERROR
0 I NONE: None
ALARM: High/Low
alarm
ERROR: Self-
diagnostic abnormal
40021 Calibration curve
calculation mode
1 to 4 1 I
40022 Upper class 16 bits
40023
Calibration curve
coefficient a00 to ±99999 0.0000 F Subordinate class 16 bits
40024 Upper class 16 bits
40025
Calibration curve
coefficient a10 to ±99999 0.0000 F Subordinate class 16 bits
40026 Upper class 16 bits
40027
Calibration curve
coefficient a20 to ±99999 0.0000 F Subordinate class 16 bits
40028 Upper class 16 bits
40029
Calibration curve
coefficient a30 to ±99999 0.0000 F Subordinate class 16 bits
40030 Upper class 16 bits
40031
Calibration curve
coefficient a40 to ±99999 0.0000 F Subordinate class 16 bits
40032 Upper class 16 bits
40033
Calibration curve
coefficient a50 to ±99999 0.0000 F Subordinate class 16 bits
40034 Upper class 16 bits
40035
Calibration curve
coefficient a60 to ±99999 0.0000 F Subordinate class 16 bits
40036 Upper class 16 bits
40037
Calibration curve
coefficient a70 to ±99999 0.0000 F Subordinate class 16 bits
40038 Upper class 16 bits
40039
Calibration curve
coefficient a80 to ±99999 0.0000 F Subordinate class 16 bits
40040 Upper class 16 bits
40041
Calibration curve
coefficient a90 to ±99999 0.0000 F Subordinate class 16 bits
40042 Upper class 16 bits
40043
Calibration curve
coefficient a100 to ±99999 0.0000 F Subordinate class 16 bits
40044 Upper class 16 bits
40045
Calibration curve
coefficient b00 to ±9999.9 0.0000 F Subordinate class 16 bits
40046 Upper class 16 bits
40047
Calibration curve
coefficient b10 to ±9999.9 1.0000 F Subordinate class 16 bits
40048 Upper class 16 bits
40049
Calibration curve
coefficient b20 to ±9999.9 0.0000 F Subordinate class 16 bits
40050 Upper class 16 bits
40051 Low limit output 0 to ±9999.9 0.0000 F Subordinate class 16 bits
40052 Upper class 16 bits
40053 High limit output 0 to ±9999.9 100.00 F Subordinate class 16 bits
40054 Upper class 16 bits
40055 Low limit alarm 0 to ±9999.9 0.0000 F Subordinate class 16 bits
40056 Upper class 16 bits
40057 High limit alarm 0 to ±9999.9 100.00 F Subordinate class 16 bits
40058 Upper class 16 bits
40059
Ch1
Preset value 0 to ±9999.9 0.0000 F Subordinate class 16 bits
5. MODBUS protocol-Function code

INST No. INE-479-P0Software version 1.0
-15-
Data format I: 16bits integer
F: 32bits actual number (IEEE754 form)
No Data name Setting
range
D
efault Data format Reference
40060 Upper class 16 bits
40061 Absorbance Ab 0 to ±9999.9 0.0000 F Subordinate class 16 bits
40062 Upper class 16 bits
40063
C
h1
Sample
temperature 0 to ±9999.9 0.0000 F Subordinate class 16 bits
40064
to
40106
Calibration curve data of Ch 2.
· · · ·
to
· · · ·
Calibration curve data of Ch n.
Head number: (n-1) × 43 + 40021
44235
to
44277
Calibration curve data of Ch 99.
4
4281 0, 1 0 I 0: OFF 1: ON
44282
U
pper class 16 bits
44283
Calibration curre
output limit values
Enable/Disable
0 to ±9999.9 0.0000 F Subordinate class 16 bits (Low limit)
44284
U
pper class 16 bits
44285
Absorbance
output limit YL0 to ±9999.9 0.0000 F Subordinate class 16 bits (Low limit)
44286
U
pper class 16 bits
44287
Absorbance
output limit XH0 to ±9999.9 9.9999 F Subordinate class 16 bits (High limit)
44288
U
pper class 16 bits
44289
C
h1
Absorbance
output limit XH0 to ±9999.9 9.9999 F Subordinate class 16 bits (High limit)
44290
to
44298
Setting data for the calibration curve output limit values of Ch 2.
· · · ·
to
· · · ·
Setting data for the calibration curve output limit values of Ch n.
Head number: (n-1) × 9 + 44281
45163
to
45171
Setting data for the calibration curve output limit values of Ch 99.
45181 Sample temperature
correction
Enable/Disable
0, 1 0 I 0: OFF 1: ON
45182 Upper class 16 bits
45183
Sample temperature
correction scaling L
-999.9
to 999.9 0.0 F Subordinate class 16 bits
45184 Upper class 16 bits
45185
Sample temperature
correction scaling H
-999.9
to 999.9100.0 F Subordinate class 16 bits
49899 Upper class 16 bits
49900 Weight α1 0 to 1.0000.5000 F Subordinate class 16 bits
49901 Upper class 16 bits
49902 Weight α2 0 to 1.0000.5000 F Subordinate class 16 bits
49903 Upper class 16 bits
49904 Weight α3 0 to 1.0000.5000 F Subordinate class 16 bits
49905 Upper class 16 bits
49906
Calibration constant
K 11 0 to ±9999.9 1.0000 F Subordinate class 16 bits
49907 Upper class 16 bits
49908
Calibration constant
K 21 0 to ±9999.9 1.0000 F Subordinate class 16 bits
49909 Upper class 16 bits
49910
Calibration constant
K 31 0 to ±9999.9 1.0000 F Subordinate class 16 bits
5. MODBUS protocol-Function code

INST No. INE-479-P0Software version 1.0
-16-
5.4 Function code of a digital setting value
5.4.1 Reading of a digital setting value
[Function code: 01 (01H)]
Continuously digital setting value (ON/OFF) is read out only the designated number from the
designated No.
ON/OFF data is configured of the data of the answer message that was arranged to 1 data (1 byte)
in the order of 8 each numbers.
LSB (D0 side) of each data becomes the youngest number of the digital data.
In the case that the reading number is not 8 multiples, an unnecessary bit becomes 0.
[Example]: Program the digital setting value reference number 1 of slave 1 to
“ON”.
<RTU mode>
Master →Device Device →Master
Upper class as personal IRMA series
Slave address 01H Slave address 01H
Function code 01H Function code 01H
Start No (H) *1 00H Data number 01H
Start No (L) *1 00H First 8 data 01H
The number (H) 00H CRC (L) 90H
The number (L) 01H CRC (H) 48H
CRC (L) FDH
CRC (H) CAH
First8data 00000001 (01H)
↑↑
ReferenceNo 87654321
Next 8 data 1
↑
Reference No 16 15 14 13 12 11 10 9
*1: Start No (Relative No) is "Reference No-1".
5. MODBUS protocol-Function code
Absorbance displaying mode
Surface water ratio computation
Measured value hol
d
Preset output
Smoothing/Real
Remarks

INST No. INE-479-P0Software version 1.0
-17-
5.4.2 Writing of an digital setting value
[Function code: 05 (05H)]
Program the digital setting value of the designated No to the designated condition (ON/OFF).
5.4.3 Writing of a plural digital setting value
[Function code: 15 (0FH)]
Program the plural designated digital setting value of the designated No to the designated
condition (ON/OFF). The designation of “ON/OFF” becomes 1 data with the unit 8 pieces in the
order of the number. LSB (D0 side) of each data becomes the youngest number of the digital
data. The case that the reading number is not 8 multiples, an unnecessary bit becomes 0.
Same answer as a command message at the time of a normal answer.
Program “0000H” when turn OFF, or “FF00H” when turn ON
[Example]: Progra
m
the digital setting value reference number 1 of slave 1 to
“ON”.
<RTU mode>
Master →Device Device →Master
Upper class as personal IRMA series
Slave address 01H Slave address 01H
Function code 05H Function code 05H
Setting value No (H) *1 00H Setting value No (H) *1 00H
Setting value No (L) *1 00H Setting value No (L) *2 00H
Setting condition (H) FFH Setting condition (H)
*2 FFH
Setting condition (L) 00H Setting condition (L) *2 00H
CRC (L) 8CH CRC (L) *3 8CH
CRC (H) 3AH CRC (H) *3 3AH
*1: Setting value No (Relative No) is "Reference No-1".
*2: The writing order is an upper class (H) 8 bits, the subordinate class (L) 8 bits.
*3: The writin
g
order is the subordinate class
(
L
)
8 bits
,
an u
pp
er class
(
H
)
8 bits.
5. MODBUS protocol-Function code
[Example] Progra
m
the [Preset of slave 1] to “ON”.
Program the digital setting value reference number 2 to “ON”.
<RTU mode>
Master →Device Device →Master
Upper class as personal IRMA series
Slave address 01H Slave address 01H
Function code 0FH Function code 0FH
Start No (H) *1 00H Start No (H) *200H
Start No (L) *1 02H Start No (L) *202H
The number (H) *1 00H The number (H) *200H
The number (L) *1 01H The number (L) *201H
Data number 01H CRC (L) *335H
First 8 data 40H CRC (H) *3CBH
CRC (L) *3 56H
CRC (H) *3 A7H
*1: Start No (Relative No) is "Reference No-1".
*2: The writing order is an upper class (H) 8 bits, the subordinate class (L) 8 bits.
*3: The writing order is the subordinate class (L) 8 bits, an upper class (H) 8 bits.
Remarks
Remarks
Reference

INST No. INE-479-P0Software version 1.0
-18-
5.4.4 Reference table of a digital setting value
Application function Write (Writing): 05/15
Read(Reading):01 (*)Writing:05only
N
o Data name Setting range Default Reference
1 Smoothing/Real 0,1 0 0: Smoothing 1: Real
2 Preset output 0,1 0 0: OFF 1: ON
3 Measured value hold 0,1 0 0: OFF 1: ON
5 Absorbance displaying mode 0,1 0 0: OFF 1: ON
6 Surface water ratio computation 0,1 0 0: OFF 1: ON
9 Wavelength data logging demand 0,1 0 0: OFF 1: ON (*)
17 Calibration designation 0,1 0 0: OFF 1: ON (*)
25 Ch display part switching demand 0,1 0 0: Constituent No display
1: Calibration curve No display
5.5 Communication check between the master and slave (Loop back test)
[Function code: 08 (08H)]
Check the communication between the master and slave.
Answer for according to the diagnosis code that was designated.
This device does [the return check that transmits reception data as it is] and the diagnosis code is
"0000H" fixation.
5. MODBUS protocol-Function code
[Example] Carrying out the loop back test to slave 1.
<RTU mode>
Master →Device Device →Master
Upper class as personal IRMA series
Slave address 01H Slave address 01H
Function code 08H Function code 08H
Diagnosis code (H) *1 00H Diagnosis(H) *100H
Diagnosis code (L) *1 00H Diagnosis(L) *100H
Any data * Any data *
Any data * Any data *
CRC (L) *2 * CRC(L) *2*
CRC (H) *2 * CRC(H) *2*
*1: The writing order is an upper class (H) 8 bits, the subordinate class (L) 8 bits.
*2: The writing order is the subordinate class (L) 8 bits, an upper class (H) 8 bits.
Remarks
This manual suits for next models
1
Table of contents
Other Chino Measuring Instrument manuals

Chino
Chino AH4000 User manual
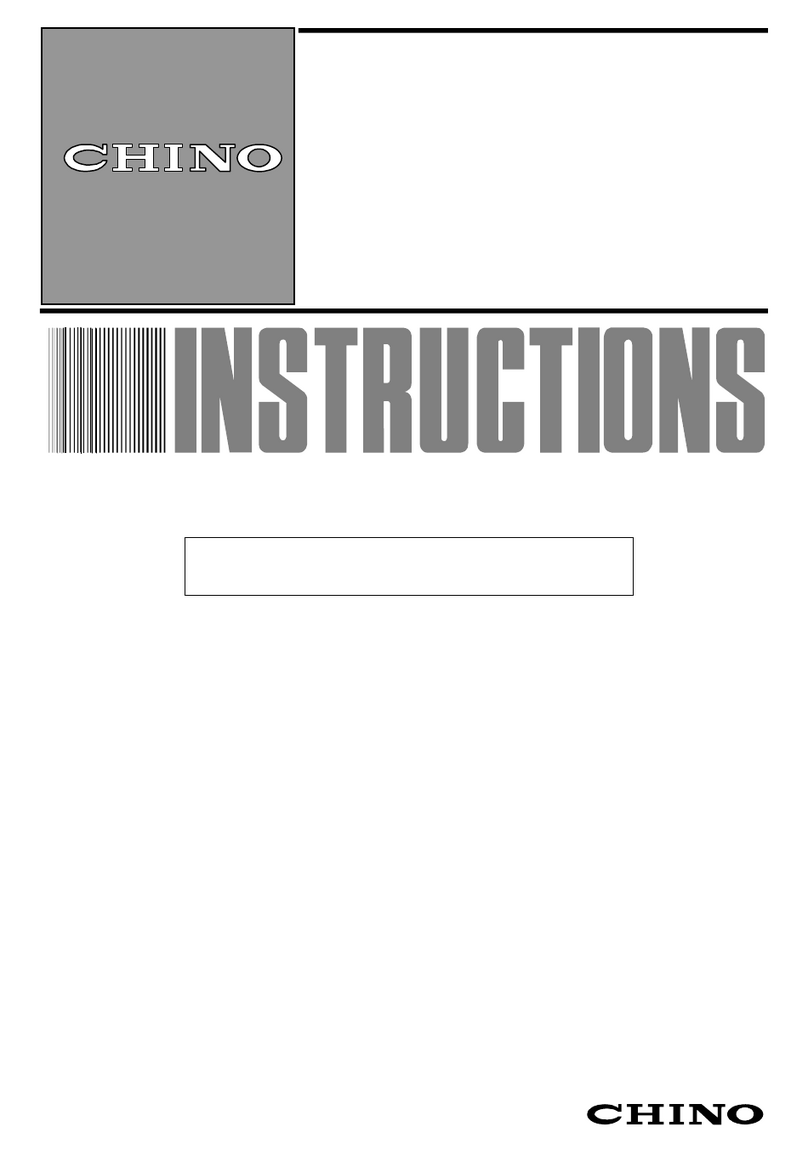
Chino
Chino IM Series User manual
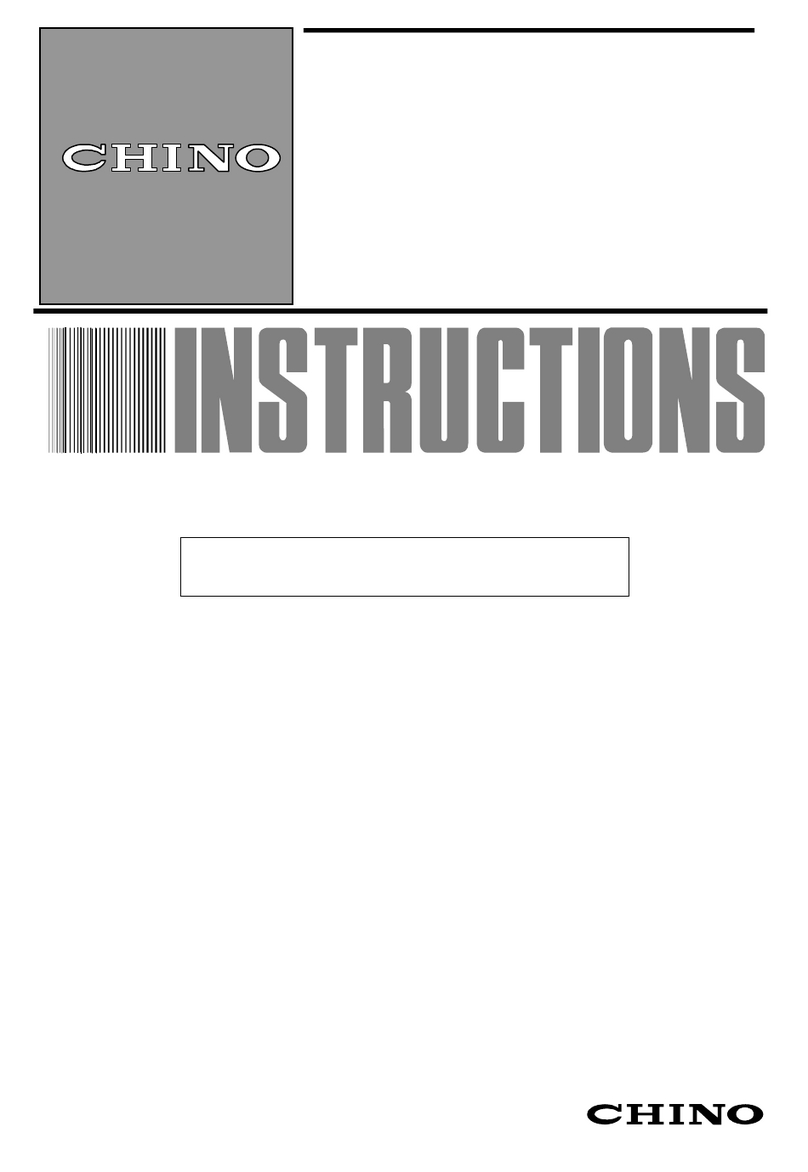
Chino
Chino IM Series User manual

Chino
Chino AL3000 SERIES User manual
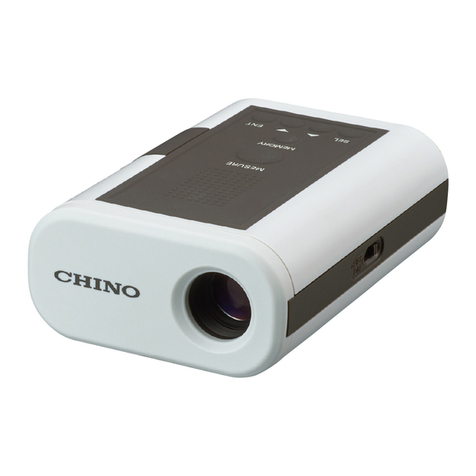
Chino
Chino IR-HA Series User manual

Chino
Chino LE5100 User manual

Chino
Chino IR-M22 SERIES User manual

Chino
Chino AH4000 User manual

Chino
Chino IRMA IRGMEG3 Series User manual
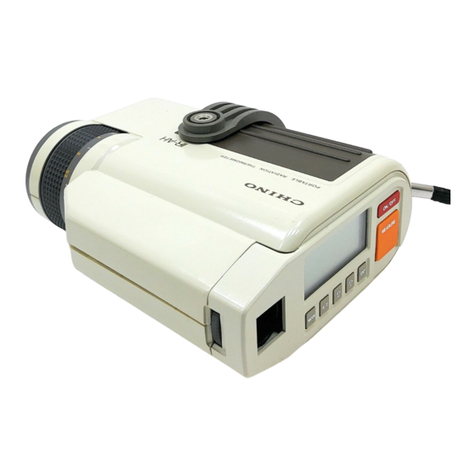
Chino
Chino IR-AH Series User manual
Popular Measuring Instrument manuals by other brands
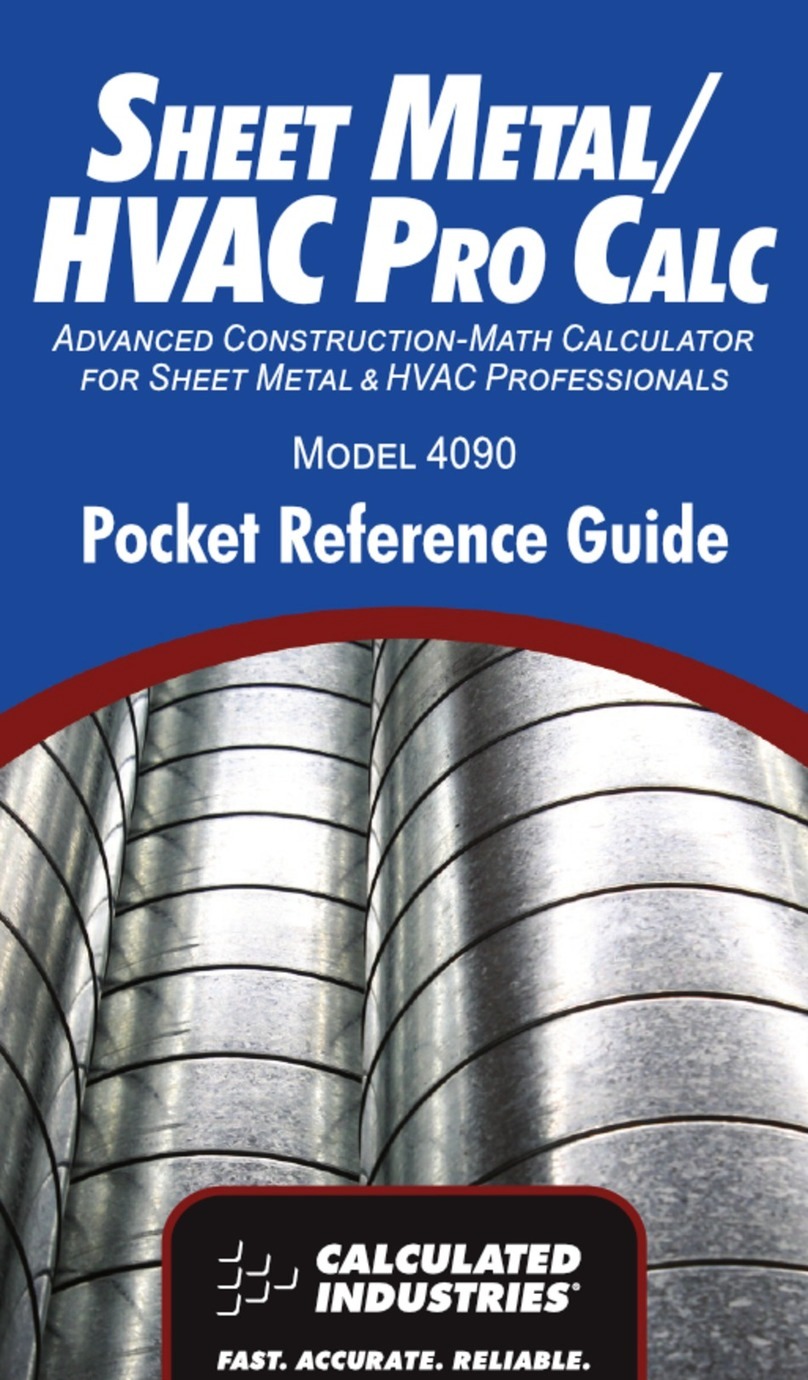
Calculated Industries
Calculated Industries 4090 Pocket reference guide
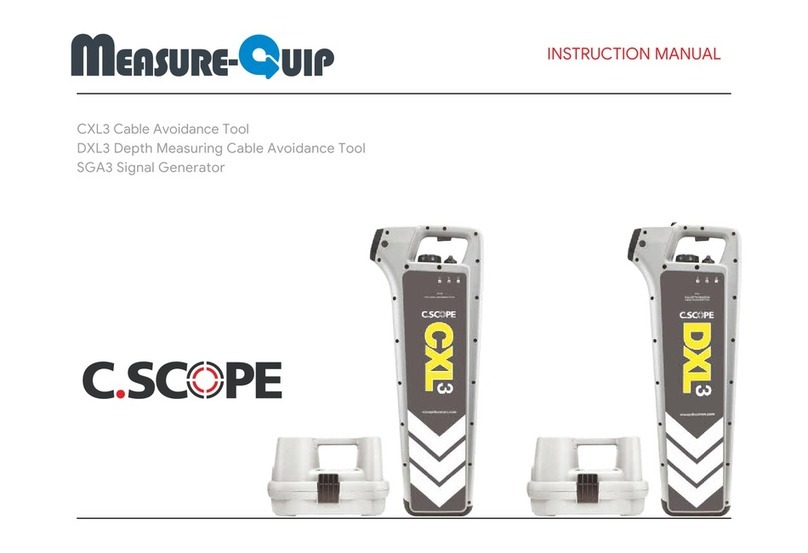
Measure-Quip
Measure-Quip C.Scope CXL3 instruction manual
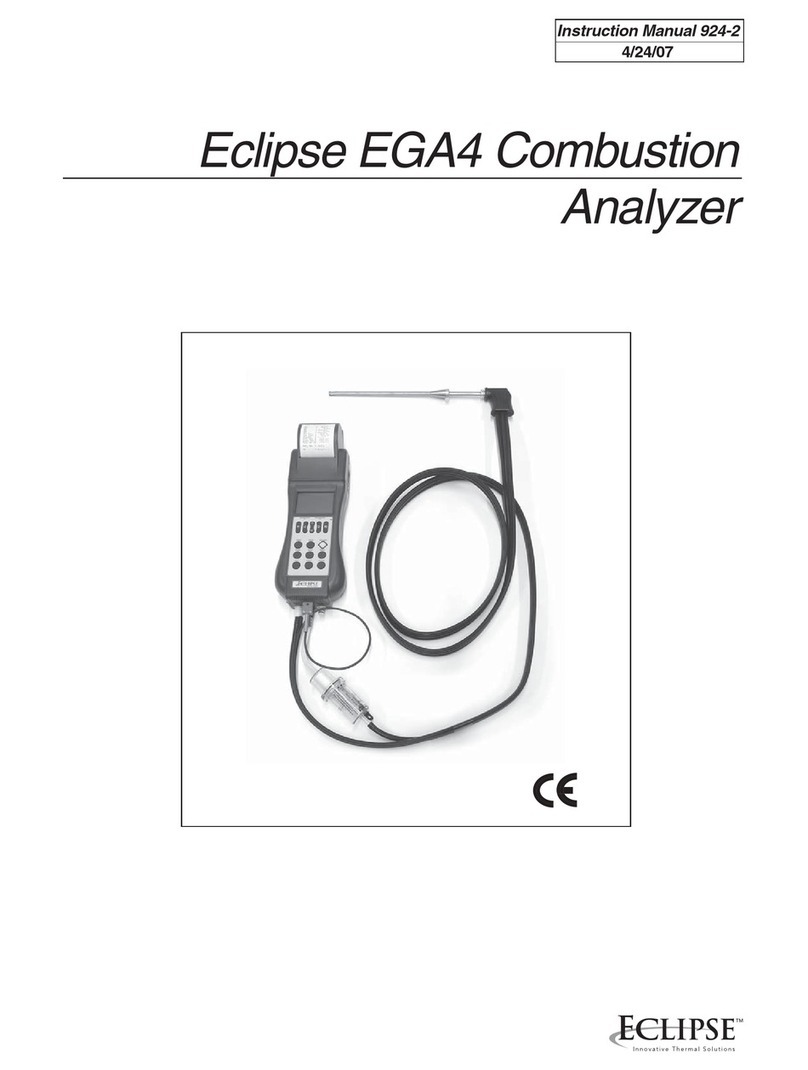
Eclipse
Eclipse EGA4 user manual

Greenlee
Greenlee 93-20 instruction manual
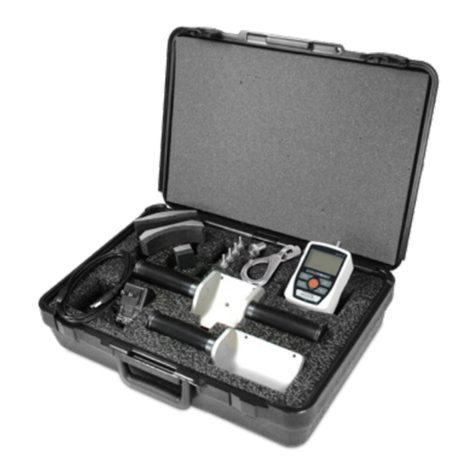
Mark-10
Mark-10 EK3 Series quick start guide
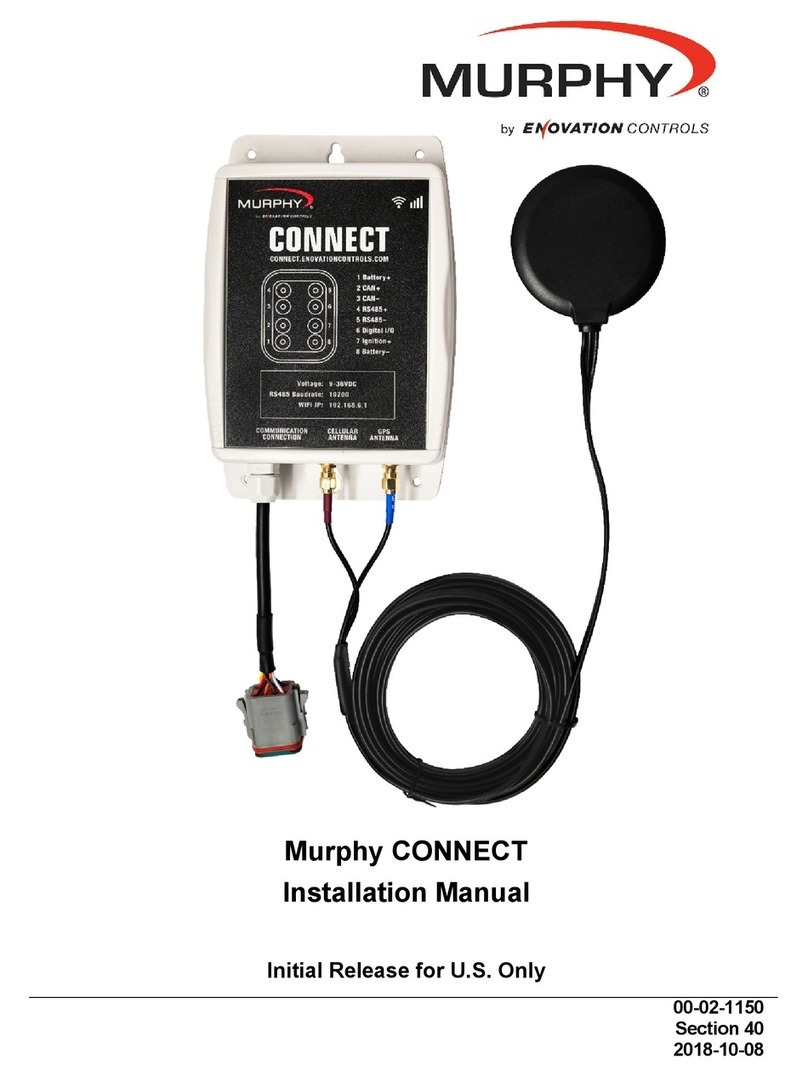
Enovation Controls
Enovation Controls Murphy CONNECT installation manual