CODEL GCEM4000 User manual

OPS.080 Issue : C Rev. : Date : 16/7/08 Doc. i/d : 0080/6 Ref. : 080040
TECHNICAL MANUAL
GCEM4000 MCERTS
Multi-Gas Analyser
1m & 2m Probe Versions
CODEL International Ltd.
Station Building, Station Road, Bakewell, Derbyshire DE45 1GE United Kingdom

CODEL
OPS.080 Issue : C Rev. : Date : 16/7/08 Doc. i/d : 0080/6 Ref. : 080040

CODEL
OPS.080 Issue : C Rev. : Date : 16/7/08 Doc. i/d : 0080/6 Ref. : 080040
CODEL International Ltd is a UK company based
in the heart of the Peak District National Park at
Bakewell, Derbyshire. The company specialises
in the design and manufacture of high-technology
instrumentation for the monitoring of combustion
processes and atmospheric pollutant emissions.
The constant search for new products and
existing product improvement keeps CODEL one
step ahead. With a simple strategy, to design
well-engineered, rugged, reliable equipment,
capable of continuous operation over long
periods with minimal maintenance, CODEL has
set standards both for itself and for the rest of the
industry.
All development and design work is carried out
‘in-house’ by experienced engineers using proven
state-of-the-art CAD and software development
techniques, while stringent assembly and test
procedures ensure that the highest standards of
product quality, synonymous with the CODEL
name, are maintained.
High priority is placed upon customer support.
CODEL’s dedicated team of field and service
engineers will assist with any application problem
to ensure that the best possible use is derived
from investment in CODEL quality products.
If you require any further information about
CODEL or its products, please contact us using
one of the numbers below or alternatively visit our
web site.
t : +44 (0) 1629 814 351
f : +44 (0) 8700 566 307
web : www.codel.co.uk
CODEL offices, Bakewell, Derbyshire

CODEL
OPS.080 Issue : C Rev. : Date : 16/7/08 Doc. i/d : 0080/6 Ref. : 080040

Technical Manual CODEL
OPS.080 Issue : C Rev. : Date : 16/7/08 Doc. i/d : 0080/6 Ref. : 080040
Contents
1. CODEL GCEM4000 Analyser – Introduction 1
1.1. Foreword 1
1.2. GCEM4000 Basic Principles 2
1.3. Emission Monitoring and the GCEM4000 3
1.3.1. Normalisation 3
1.3.2. Verification 3
1.4. User Interface 3
1.5. Analogue and Logic Inputs and Outputs 3
1.6. CDC Serial Port - for use with the CODEL SmartCEM system 4
1.7. Analyser Protection 4
2. Summary Specification 5
3. Preparing for Installation 7
3.1. Unpacking. 7
3.1.1. The Basic Analyser 7
3.1.2. Transceiver Weather Cover 8
3.2. Additional Materials 8
3.3. Ancillary/Additional Equipment 10
3.4. Services 10
4. Installation 11
4.1. Selection of Measurement Position 11
4.2. Analyser Positioning 12
4.3. Fitting of Stub-Pipes and Mounting Flanges 13
4.3.1. Metal Ducts/Stacks 14
4.3.2. Concrete and Brick Stacks 14
4.3.3. Double Skin Stacks 15
4.4. Installation of Purge Air Supply 15
4.5. Installation of Measurement Tube 15
4.6. Fitting the Active Weather Cover and Sensor Head 17
4.7. Installation of the GCU 22
4.8. Wiring Connections 22
4.8.1. Installation and Connection of Cables 22
4.9. Installation of Normalising Measurements (Oxygen, Temperature and Pressure) 22
4.10. System Connections 23
5. Commissioning 25
5.1. Pre-Commissioning Checks 25
5.2. Power On 25
5.3. Initial Set-Up Using SmartCOM Software 25
5.3.1. Adjust Alignment 27
5.3.2. Thermistor Control 28
5.3.3. Source Temperature Control 30
5.3.4. Cell Oven Control 31
5.3.5. Rx Temperature Check 31

Technical Manual CODEL
OPS.080 Issue : C Rev. : Date : 16/7/08 Doc. i/d : 0080/6 Ref. : 080040
5.3.6. Cell Oven Control 32
5.3.7. Detector levels 36
5.3.8. Zero Calibration 36
5.3.9. Current Data 38
5.3.10. 'Y' Values 39
5.3.11. Plant Status Set-Up 40
5.3.12. Span Verification 41
5.3.13. Water Vapour Checks 44
5.3.14. General Overview 44
5.3.15. Setting the Output Configuration 45
5.3.16. Read/Set RTC 47
5.3.17. Memory Back-Up 49
6. Analyser Records 51
6.1. Serial Numbers (Complete on First Inspection) 51
6.2. Installation Records 51
6.3. Commissioning Records 51
6.3.1. Table 1 : Analyser Configuration Record - Parameters 51
7. Calibration and Measurement Verification 52
7.1. Introduction 52
7.2. Factory Calibration 52
7.3. Verification 52
7.3.1. Automatic Zero Calibration 52
7.3.2. Manual Zero Verification 52
7.3.3. Comparative Testing 53
7.4. Re-calibration 53
8. Maintenance 54
9. Fault Finding 55
Appendix 1 – Setting Analyser Gains 58
List of Figures 59

Technical Manual Page 1 CODEL
OPS.080 Issue : C Rev. : Date : 16/7/08 Doc. i/d : 0080/6 Ref. : 080040
1. CODEL GCEM4000 Analyser – Introduction
Please take a few minutes to read this section before proceeding with installation. It is designed to
provide an overview of the analyser and its capabilities so that the information given later will be more
easily understood.
1.1. Foreword
SmartCEM is the ultimate solution for continuous monitoring of flue gas emissions. It is a fully integrated
monitoring concept from the basic analysers and their calibration verification packages through to digital
communications, data logging and automatic reporting.
At the heart of this concept is the SmartCEM station containing all the analysers and monitors to provide
comprehensive stack emission monitoring. The SmartCEM Station Control Unit (SCU) provides power to and
communicates with the analysers and monitors within that station.
Data from up to 32 SmartCEM stations is transmitted via a serial digital link (CODEL SmartBUS) to the Central
Datapoint where it is logged on a dedicated pc or assembled for onward transmission to a plant computer or
DCS. The arrangement of a typical SmartCEM system is illustrated in Figure 1.
Figure 1 : Typical SmartCEM System Arrangement

Technical Manual Page 2 CODEL
OPS.080 Issue : C Rev. : Date : 16/7/08 Doc. i/d : 0080/6 Ref. : 080040
1.2. GCEM4000 Basic Principles
The GCEM4000 analyser uses an in-situ probe set into a duct to measure the concentration of gases of interest.
Figure 2 illustrates the arrangement. The in-situ tube includes a section that allows the diffusion of flue gases
into the measurement zone or the dispersion of purge or calibration gas out of the tube and into the duct. This
section of the tube is the analysers’ measurement cell. The analyser is capable of simultaneous measurement
of up to six different gases (plus water vapour as a seventh measurement if required).
As with conventional cross-duct analysers, this probe configuration does not require the extraction of a sample
from the gas stream and makes its measurement by analysing the way in which infrared radiation, transmitted
through the measurement section of the probe, is modified by the gases present.
Figure 2 :GCEM4000 Analyser with 'in-situ' Probe
The transceiver unit containing the infrared source and detector system, required to measure the received light
energy after its passage through the gas, is totally isolated from the flue gas. There is, therefore, no contact
between the analyser electronics and the flue gas. Correctly installed and commissioned, this provides the
opportunity to achieve very low maintenance factors and totally eliminates any possibility of altering the
composition of the flue gases to be measured.
The remaining components of a GCEM4000 analyser are:
•The Gas Control Unit (GCU) that controls the input of zero and span calibration gases into the
analyser. It contains the necessary compressed air filtration and drying equipment to ensure high
quality air supply for the zero calibration and probe purge functions. The analyser power supply and
Station Control Unit (SCU) are also housed within the GCU. The function of the SCU is as an
emissions data processing unit, communications centre for the monitor and controller of the zero and
span calibration functions.
•The Central Data Controller (CDC) that accepts data from 1 to 16 SCUs and processes the data for
onward transmission to a remote pc or SCADA system.
•The Active Weather Cover utilises a Peltier heat pump to provide heating or cooling to maintain a
constant air temperature around the sensor head in a wide range of ambient temperatures.

Technical Manual Page 3 CODEL
OPS.080 Issue : C Rev. : Date : 16/7/08 Doc. i/d : 0080/6 Ref. : 080040
1.3. Emission Monitoring and the GCEM4000
Although GCEM4000 analysers can be used for process gas analysis, they have been primarily designed to
monitor pollutant emissions from industrial stacks. Legislation governing such emissions usually requires data to
be reported in very specific formats. GCEM4000 analysers are therefore designed to fulfil this requirement
without the need for external data manipulation. Although differing in detail from country to country, the essential
demands of legislation are common world-wide.
1.3.1. Normalisation
Emission limits are always defined under standard conditions of temperature, pressure and air dilution (air
dilution is defined using the waste gas CO2or O2concentration). Most legislation also requires concentrations to
be reported on a dry basis; i.e. water vapour in the flue gas is not permitted to dilute the measurement. The
correction of the measurement from ‘as measured conditions’ to ‘standard’ conditions is known as
‘normalisation’. Like all in-situ analysers, GCEM4000 analysers measure concentrations of pollutant ppm
(parts per million by volume) or %, under the conditions at the measurement position.
This basic ppm measurement is always corrected for the duct pressure and presented as vpm by the analyser.
GCEM4000 analysers have the capability for the outputs and display to be configured in vpm (or %) or mg/m3
(which is a mathematical conversion depending on the molecular weight of the gas being measured and the flue
gas temperature), or in mg/Nm3(i.e. ’normalised’ to the required standard conditions).
When the outputs are required to be normalised to a pre-defined O2concentration as opposed to a CO2level,
then an external O24-20mA signal representing Oxygen levels can be input into the GCEM4000. All other
normalising parameters i.e. pressure, temperature, and CO2are measured as standard by the GCEM4000
1.3.2. Verification
It is important that the accuracy of measurement can be verified. Often, legislation requires the regular testing,
reporting and correction of measurement zero and span. GCEM4000 analysers are equipped with automatic
zero verification and correction procedures that allows the measurement cell to be flooded with dry air (or
Nitrogen) to provide a zero check or a certified calibration gas as a span verification.
1.4. User Interface
The analyser is supplied with SmartCOM pc software that enables a pc connected to the SCU to display of all
real-time measurements as well as the setting up and display of all the analysers’ configurable operating
parameters. This interface includes a diagnostic mode that allows interrogation of the condition of the analysers’
critical functions for service and trouble-shooting purposes. A full description is provided in Section 5.
1.5. Analogue and Logic Inputs and Outputs
The GCEM4000 SCU is equipped with an analogue output (0/4-20mA) for each measurement channel (up to
seven). Each output is freely configurable for any span (within the limits for that measurement, as given in
Section 2. Summary Specification and measurement units (vpm or %, mg/m3, mg/Nm3).
Volt-free contact outputs (250V/10A) are provided for data valid and measurement alarm level (common output
for all measurement channel alarms).
Three 4-20mA inputs are provided for normalisation measurements (273Ωinput impedance, ±200V DC
common mode voltage range). These inputs are also able to provide isolated 24V DC supplies to drive
either 2 or 3-wire external normalisation measurement transducers.

Technical Manual Page 4 CODEL
OPS.080 Issue : C Rev. : Date : 16/7/08 Doc. i/d : 0080/6 Ref. : 080040
1.6. CDC Serial Port - for use with the CODEL SmartCEM system
The CDC is equipped with a 2-way serial communications port for use with the CODEL SmartCEM system. On
a plant where more than one CODEL analyser is installed, this is the preferred method and, even for a single
analyser installation, can provide significant benefits. The main ones are:
•Up to 32 SCUs can be connected to a CDC via a single data bus.
•No corruption of digital data, even over long distances.
•Common data (e.g., normalisation measurements and plant status) can be transmitted to all
relevant measurement channels and analysers from a single input.
•Real time display can show all measurements simultaneously.
•Multi-level and period alarms can be freely configured for any measurement data set.
•Up to 5 years data can be logged and instantly recalled in graphical or tabular format.
•All processor user interface functions can be carried out from a central control point, i.e. once
physical installation is complete, all commissioning operations can be carried out from the central
control. Thereafter, real time analyser operating parameters, including diagnostic data, can be
accessed at any time.
•All real time and historical data and diagnostics can be accessed remotely via a MODEM.
•Reports can be formatted to suit local legislation and printed automatically.
•Digital data can be transferred directly to the plant DCS or computer.
1.7. Analyser Protection
GCEM4000 analysers are designed for outdoor installation and all units are constructed to IP65 (NEMA 4)
standards and are designed for ambient temperatures from -20oto +50oC.

Technical Manual Page 5 CODEL
OPS.080 Issue : C Rev. : Date : 16/7/08 Doc. i/d : 0080/6 Ref. : 080040
2. Summary Specification
Measurements
•Main measurement channels (1-7)
•any combination of up to seven gases from CO/CO2/NO/NO2/SO2/HCl/UHC/H2O
Measurement Limits (maximum)
•CO/NO/NO2/HCl/UHC 6000 vppm.metres
•SO250000 vppm.metres
•CO2/H2O 40%.metres
Note that although very low spans can be configured, this should not be done without
consideration of the measurement uncertainty.
Measurement Uncertainty
•CO2±0.2%
•H
2O ±0.2%
•Other gases ±2vpm or ±2% of measurement (whichever is the greater).
Measurement Temperature (Flue gas)
•0-300°C
Measurement Units
•vpm (% for CO2and H2O)
•mg/m3
•mg/Nm3
Display
•via pc running SmartCOM software
•real-time measurements
•operating parameters
•diagnostic information
•set-up menus
Outputs
•Analogue One for each main measurement channel (channels 1 to 7) 0/4-20mA isolated
(located in SCU) 500Ωmax. load, fully configurable in measurement units (vpm or %, mg/m3,
mg/Nm3), and span.
•Logic Volt-free contact outputs (110V DC/125V AC @ 1A max. for data valid and
(located in SCU) measurement alarm level.
Serial Port For connection to bi-directional 4-wire data bus terminating at the CDC when
(located in SCU) installed as part of an integrated emission monitoring (SmartCEM) system.
Ambient Temperature All units are designed to operate in ambient temperatures of -20°C to +50°C.
Extreme climatic conditions may require further protection.

Technical Manual Page 6 CODEL
OPS.080 Issue : C Rev. : Date : 16/7/08 Doc. i/d : 0080/6 Ref. : 080040
Enclosures All units are sealed to IP65 (NEMA 4) standards and are suitable for outdoor
installation.
Power Requirements Power Supply Unit - 85-264V AC
-47-62Hz
-200VA
Purge Gas Requirements
•Compressed air/N2Clean and dry to -20oC.
Normal operation 5 l/min
Calibration (≈10 minutes) 20 l/min
Nominal Dimensions
•Transceiver and 1m Probe (2m Probe)
Overall length 1670mm (2450mm)
Largest diameter 340mm
Probe length 1315mm (2105mm)
Measurement path 1450mm (2000mm)
Transceiver Length 425mm
Transceiver diameter 300mm
Probe weight 50kg (65kg)
Transceiver weight 30kg
•Gas Control Unit
W800mm x H1000mm x D200mm
Weight 100kg
•CDC
W200mm x H230mm x D110mm
Weight 5kg

Technical Manual Page 7 CODEL
OPS.080 Issue : C Rev. : Date : 16/7/08 Doc. i/d : 0080/6 Ref. : 080040
3. Preparing for Installation
3.1. Unpacking
The analyser and any other items are normally protected for transportation by an expanded foam packing
material. When unpacking, please ensure that smaller items are not discarded with the packing material.
If any items are missing please inform CODEL or your local CODEL agent immediately.
3.1.1. The Basic Analyser
- standard supplied items
Figure 3 : Standard Supplied Items and Dimensions

Technical Manual Page 8 CODEL
OPS.080 Issue : C Rev. : Date : 16/7/08 Doc. i/d : 0080/6 Ref. : 080040
The transceiver, GCU and SCU, are supplied with blanking plugs fitted in the cable gland entry holes. Cable
Glands are packed separately.
Some contracts require the mounting of all power supply, processing and control units in
instrumentation panels. In such cases please refer to the additional system schematics
supplied. These are always contract-specific.
Although transceivers and GCUs are essentially interchangeable, analysers are configured and tested as
complete systems in the factory. If more than one analyser is received, ensure that all units are matched.
3.1.2. Transceiver Weather Cover
Model 4000 analysers are suitable for outdoor installation in ambient temperatures ranging from -20°C to +50°C.
However, it is good practice to install units in positions where they have maximum protection. Whilst this is
usually possible for the GCU and CDC, options may be limited for the transceiver. To protect generally against
exceptional weather conditions, even in temperate climates, and particularly to facilitate servicing under these
conditions, a weather cover is fitted to maintain a stable air temperature around the sensor head.
Figure 4 : Active Weather Cover
3.2. Additional Materials
The installation of a 4000 Series analyser will require a number of materials in addition to those supplied with
the analyser. The following are intended to cover most possibilities, but not all listed materials will be required
for all installations. See also Figure 5.
•Cables
Unit Function No. of
Cores Core Specification/Cross Sectional Area O/D
min/max Screened
YES/NO
CDC (if
required) Serial
Comms. 4 Multi-strand 16/0.2mm, 0.5mm2min. 5mm/12.8mm YES
Normalising
inputs 2 Multi-strand 16/0.2mm, 0.5mm2min. 5mm/12.8mm YES
Analogue
outputs 2 Multi-strand 16/0.2mm, 0.5mm2min. 5mm/12.8mm YES
Gas
Control
Unit
Fault alarm 2 Multi-strand 16/0.2mm, 0.5mm2min. 5mm/12.8mm YES
Note that screened cables should have the screen terminated as described in Section 4.
Installation. If steel wire armoured cable is used the steel wire sheath should be earthed at the
analyser end only.

Technical Manual Page 9 CODEL
OPS.080 Issue : C Rev. : Date : 16/7/08 Doc. i/d : 0080/6 Ref. : 080040
•Other Materials
-Stub pipe. 1 x 8’’ nominal bore (o/d219mm, i/d206mm), steel tube (see Section 4.3. Fitting of
Stub-Pipes and Mounting Flanges for details).
-1 x BS4504, PN16, DN200 steel flange (supplied).
-Mounting brackets/panels, screws, bolts, etc. for gas control unit and SCU/CDC.
-Cable trays/conduits/ties and associated fixing materials.
-Compressed air supply (20 l/min clean and dry to -20°C) for (a) measurement cell purge (2 l/sec
on demand) and (b) purging of the neutral zone (0.5 l/min/sec continuous). 30m of 10mm o/d.
PTFE tube is supplied.
-Consideration should also be given to the possible need for temporary/permanent access
platforms and lifting equipment.
Figure 5 : CODEL Supplied Connections
When calculating cable requirements remember to take into account cable routing relative to
equipment location and also the need for conduit, cable trays, supports etc.
Thermocouple
8-Core CODEL local bus
(+48V, MOSI, MISO & 0V,
O2 Input & Weather Cover
Temperature)
Weather Cover
Power Supply
Zero Span Gas Supply
(20 litre/min during Cals)
Dead Zone Supply
(constant purge 5 litre/min)
Pressure
Span Gas INCompressed Air IN
Customer supply:
- Mains power cable
- Alarm output cable
- Analogue output cable
- Interconnecting cable
SCU to CDC

Technical Manual Page 10 CODEL
OPS.080 Issue : C Rev. : Date : 16/7/08 Doc. i/d : 0080/6 Ref. : 080040
3.3. Ancillary/Additional Equipment
The 4000 analyser is rarely supplied alone. It is usually associated with other equipment that makes up an
emission monitoring system. In planning installation, consideration should be given to the requirements of other
equipment by consulting the specific manuals so that the whole system may be installed in the most cost
effective and efficient way. If the complete system has been engineered by CODEL, detailed contract specific
information and schematics will have been provided.
Other equipment commonly provided may be:
- CODEL SmartCEM system (system management, data display, logging and reporting)
- Other CODEL monitors/analysers
- Non-CODEL monitors/analysers
- Normalising measurement - oxygen
3.4. Services
Electrical Power - Power Supply Unit - 110 or 240V AC (switchable)
-47-62Hz
-200VA
Compressed Air - @ 5bar
- Dry (to -20°C)
-Clean (better than 10μm)
-Consumption 20 l/min during calibration, 5 l/min continuous

Technical Manual Page 11 CODEL
OPS.080 Issue : C Rev. : Date : 16/7/08 Doc. i/d : 0080/6 Ref. : 080040
4. Installation
PLEASE BE SURE TO READ SECTION 3. Preparing for Installation BEFORE PROCEEDING
Installation of the several units that make up a 4000 Series analyser may be carried out in any order. However,
the recommended order, reflected in this manual, is:
-Selection of measurement position
-Installation of the stub-pipe and mounting flange
-Installation of purge air supply
-Fitting of transceiver
-Installation of GCU and CDC
-Installation and connection of cables
-Installation of normalising measurements and input connections to the GCEM4000
-Installation of span verification gases
4.1. Selection of Measurement Position
This analyser measures the average concentration of gas across a significant proportion of the width of the
stack or duct. Measurement position is therefore not as critical as with single point measuring systems, where
consideration must be given to ensuring representative results. Nevertheless, positions where significant
stratification might occur are best avoided. On most combustion plant, flue gas homogeneity can be guaranteed
after the ID fan, so from this point of view, the selected position could be anywhere in the ductwork after the ID
fan or in the stack.
The next factor to consider is that of flue gas pressure. Choosing a position where the flue gas is at negative
pressure, compared with ambient pressure, is not as important as it is for conventional open path cross-duct
analysers. However, it is advantageous in reducing pressure and flow requirements, to ensure complete
flooding of the measurement cell, of both zero and calibration gases. Under normal operating conditions
negative flue gas pressure exists from 10-15m after the ID fan outlet to stack exit. If possible, open any existing
port near the selected measurement position to confirm.
Take care in doing this. Use suitable protective clothing, including eye protection. Positive
pressure in the duct will cause hot flue gases to be vented from the open port.
Take care also to ensure that duct vibration at the selected mounting point is kept to a minimum. Severe
vibration may cause malfunctioning of the instrument or at worst a catastrophic failure of the duct. Take in to
consideration the total weight of the instrument when selecting the mounting position and the effect that this may
have on duct vibration.
The final factors to be considered in selection of measurement position are those of convenience and cost of
installation. Access from existing platforms or walkways and proximity of existing services are obvious
advantages, both for installation and subsequent commissioning and servicing. Drilling holes in metal ductwork
or flues is easier than drilling concrete stacks. Also ensure that there is enough space between the duct or stack
and any other obstruction to allow installation of the transceiver and probe. A minimum clearance of 2.25m is
required from the mounting flange. Ensure that there is space to manoeuvre the tube in to position ready for
insertion (see Figure 9).

Technical Manual Page 12 CODEL
OPS.080 Issue : C Rev. : Date : 16/7/08 Doc. i/d : 0080/6 Ref. : 080040
Conditions vary from plant to plant but, in general, the following guidelines should be followed:
•Firstly, look for a suitable location on ductwork between the ID fan and the stack.
•Large power plant with multiple flues having concrete wind-shields can provide good alternative
mounting locations within the stack. Access stairs, lifts and working platforms at various levels
usually exist.
•On smaller plant, mounting on metal stacks is acceptable, provided suitable access platforms exist.
•Only locate analysers on single flue concrete stacks if no other position is possible.
•Do not locate analysers any higher than necessary on stacks. There is no benefit to measurement
quality and significant disadvantages for service personnel.
4.2. Analyser Positioning
The preferred analyser position is shown below in Figure 6.
Figure 6 : Preferred Transceiver Position
The transceiver should be angled at 50downward to encourage condensation to flow into the measurement tube
and then dissipate.
Figure 7 : Angled Probe Installation
5odownward slope

Technical Manual Page 13 CODEL
OPS.080 Issue : C Rev. : Date : 16/7/08 Doc. i/d : 0080/6 Ref. : 080040
The measurement tube should always be on the centre line of circular ducts. On square or rectangular ducts,
the axis may be displaced from the centre line. Figure 8 shows the recommended displacement limit.
Figure 8 : Rectangular Ducts - Acceptable Position
In many applications, the GCEM4000 analyser will be installed in close proximity to other analysers. Figure 9
shows the minimum separation required.
Figure 9 : Spacing From Other Analysers
4.3. Fitting of Stub-Pipes and Mounting Flanges
Before proceeding further note that under no circumstances should holes be cut in the stack
with the plant operational if flue gases are under positive pressure with respect to atmosphere.
Even if pressure is believed to be negative great care should be exercised and all appropriate
protective clothing, including eye protection, should be worn.
Construct a mounting assembly (Figure 10) by welding a stainless steel mounting-flange (BS 4504 PN16
DN200) to a suitable diameter stub-pipe. This should be 8" nominal bore stainless steel tube and long enough to
extend about 200mm outside the outer surface (including lagging) of the duct or stack, where possible.
Cut 'slip-fit' holes in the duct at the chosen position; note that the assembly should be installed at a 50downward
angle to the horizontal to allow condensate to flow into the stack.

Technical Manual Page 14 CODEL
OPS.080 Issue : C Rev. : Date : 16/7/08 Doc. i/d : 0080/6 Ref. : 080040
4.3.1. Metal Ducts/Stacks
Before proceeding, note that the total weight of the measurement probe and transceiver assembly is
approximately 95kg. The duct or stack should be appropriately strengthened if necessary (see Figure 10).
Figure 10 : Standard Site Mounting Flange
Tack-weld the inner end of the stub-pipe to the duct/stack. Ensure that it is aligned at least 50downward from
the horizontal.
If the analyser is not being fitted immediately it is advisable to close the stub-pipe with a blanking plate (not
supplied) cut and drilled to suit the fitted flange.
The mounting flange should be mounted 'four-square' on the stub-pipe as shown in the drawing above.
4.3.2. Concrete and Brick Stacks
A suggested stub-pipe mounting arrangement is shown below. The many variations in stack dimensions, wall
thickness and material that may be encountered do not permit the recommendation of exact details. However,
the general guidelines already given in Sections 4.3. Fitting of Stub-Pipes and Mounting Flanges and 4.3.1.
Metal Ducts/Stacks may be followed. Such installations require particular care to be taken in establishing
alignment of the two stub-pipes as once fixed they may be impossible to adjust. If in doubt, consult CODEL
before commencing installation.
Table of contents
Other CODEL Measuring Instrument manuals
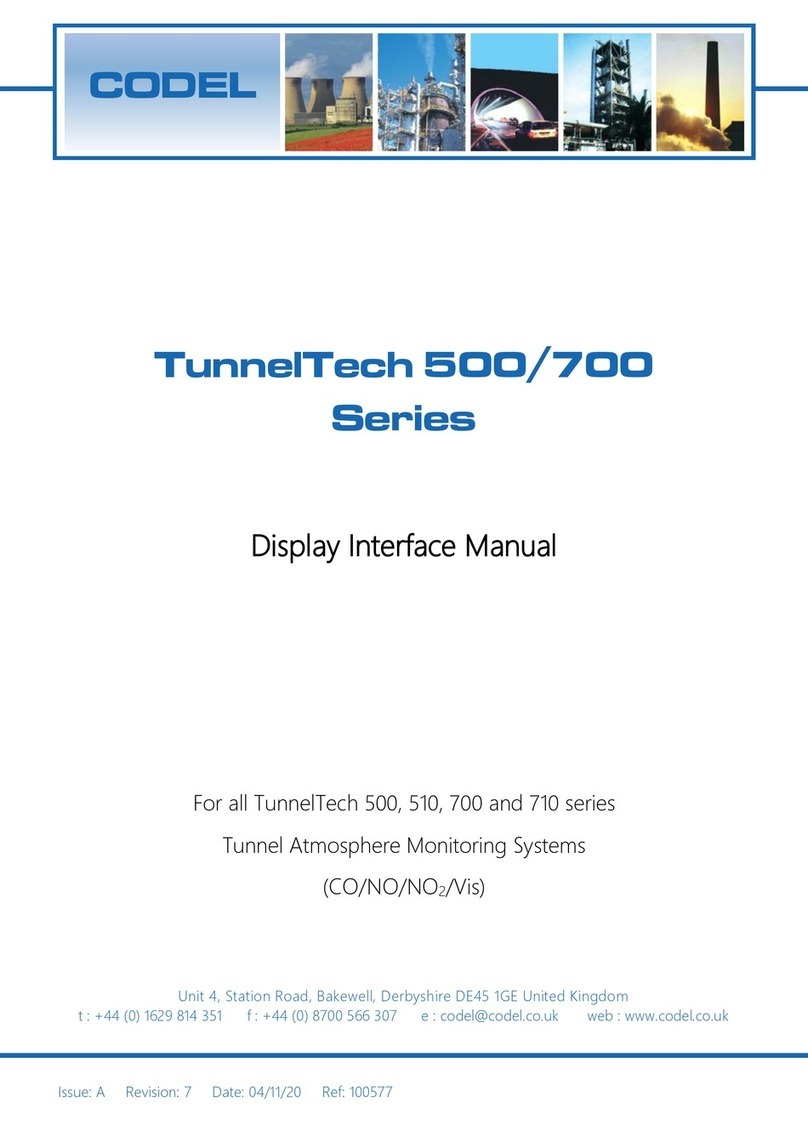
CODEL
CODEL TunnelTech 500 Series User manual
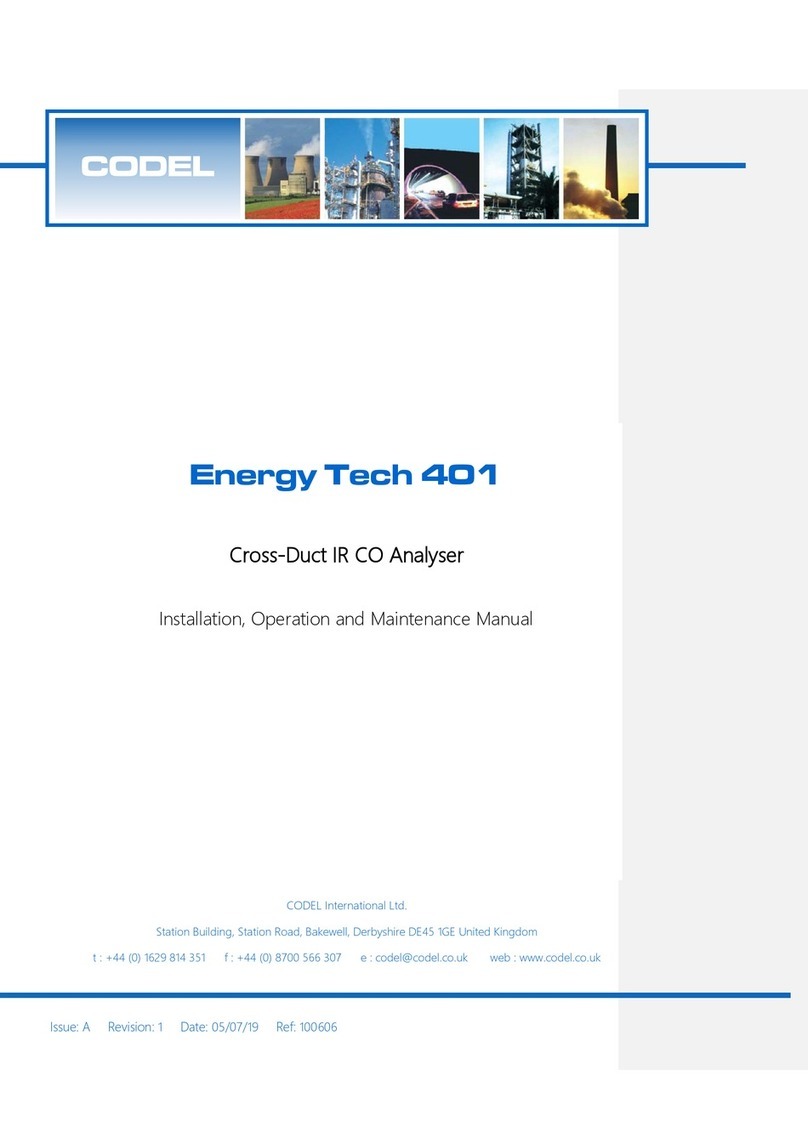
CODEL
CODEL Energy Tech 401 User manual
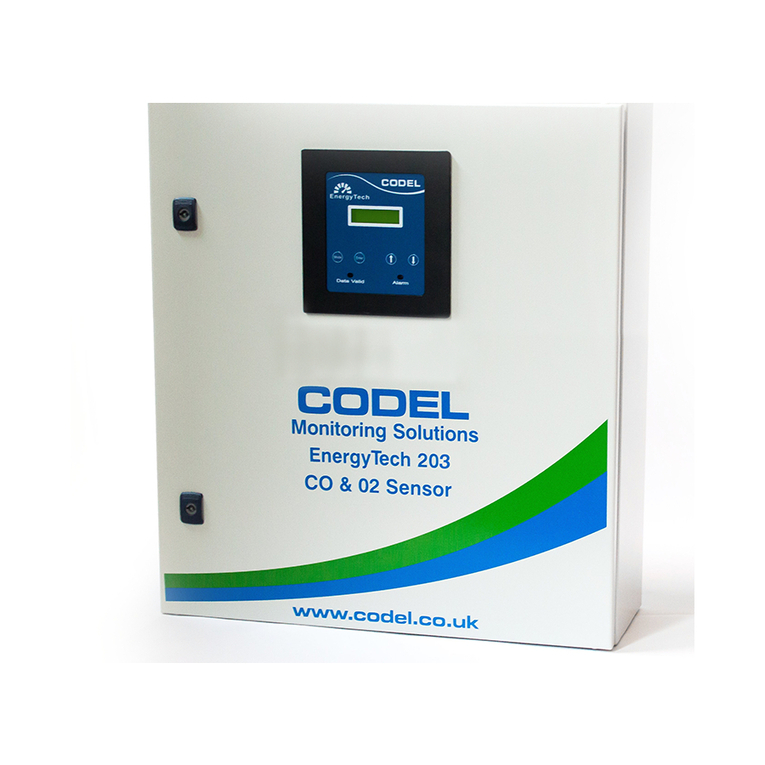
CODEL
CODEL EnergyTech 203 User manual
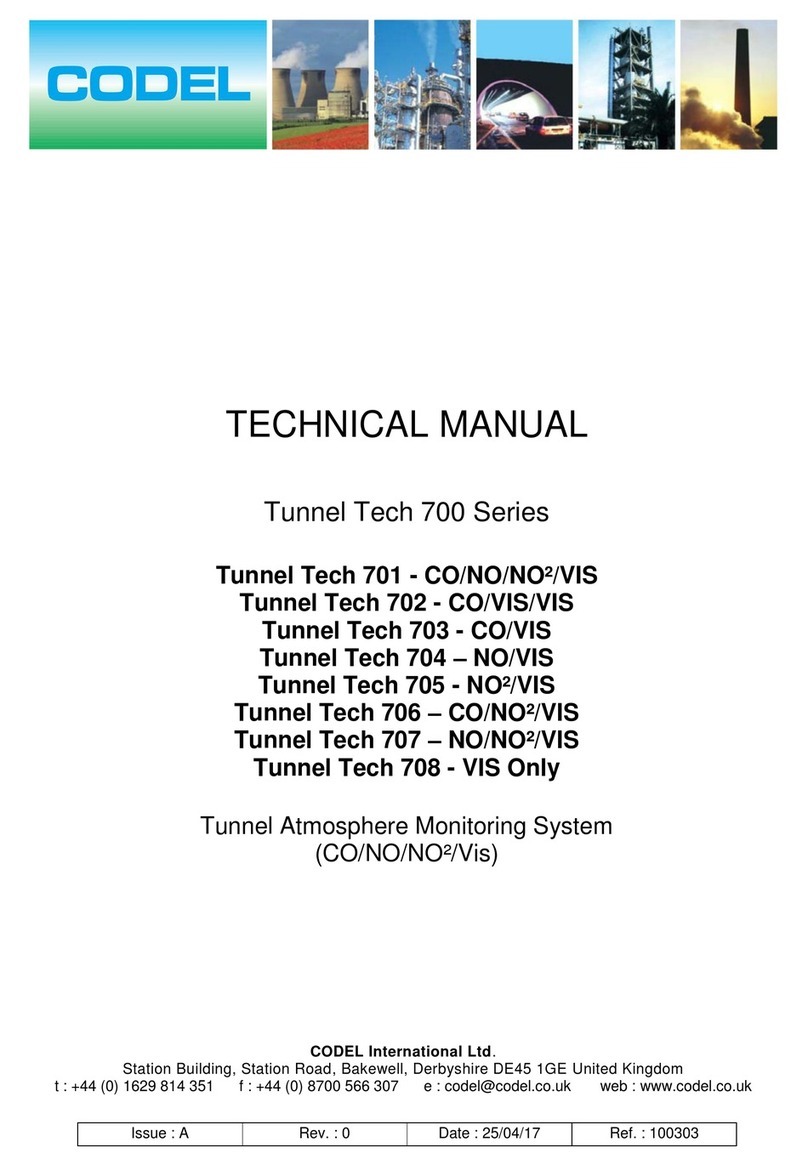
CODEL
CODEL Tunnel Tech 700 Series User manual
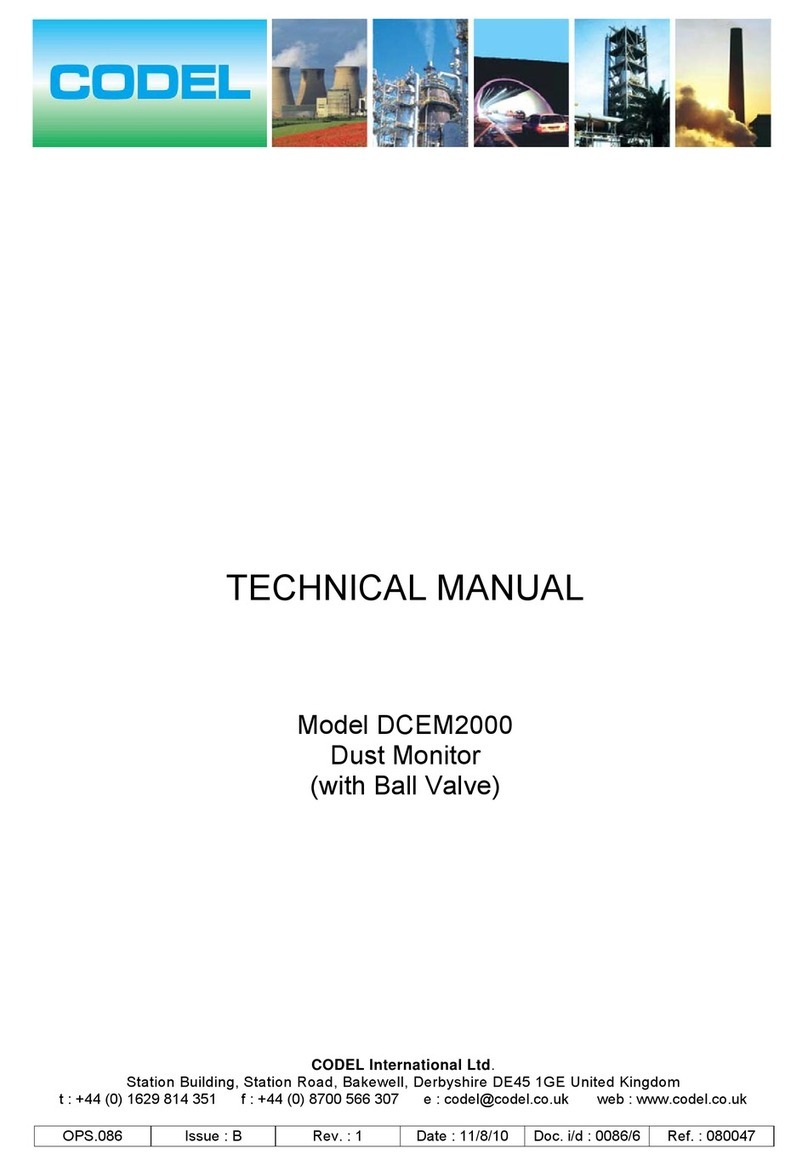
CODEL
CODEL DCEM2000 User manual
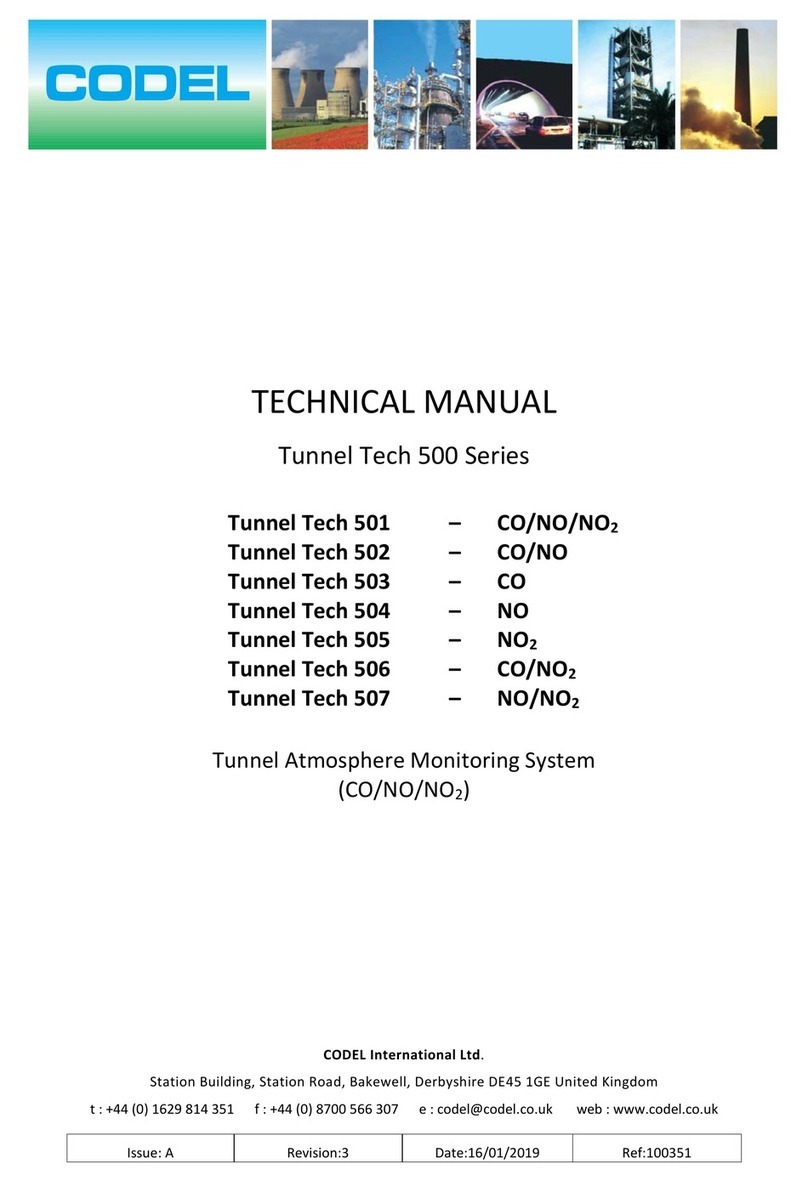
CODEL
CODEL Tunnel Tech 500 Series User manual
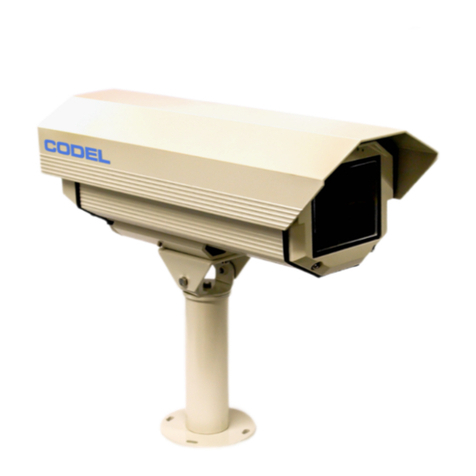
CODEL
CODEL TunnelTech 601 User manual
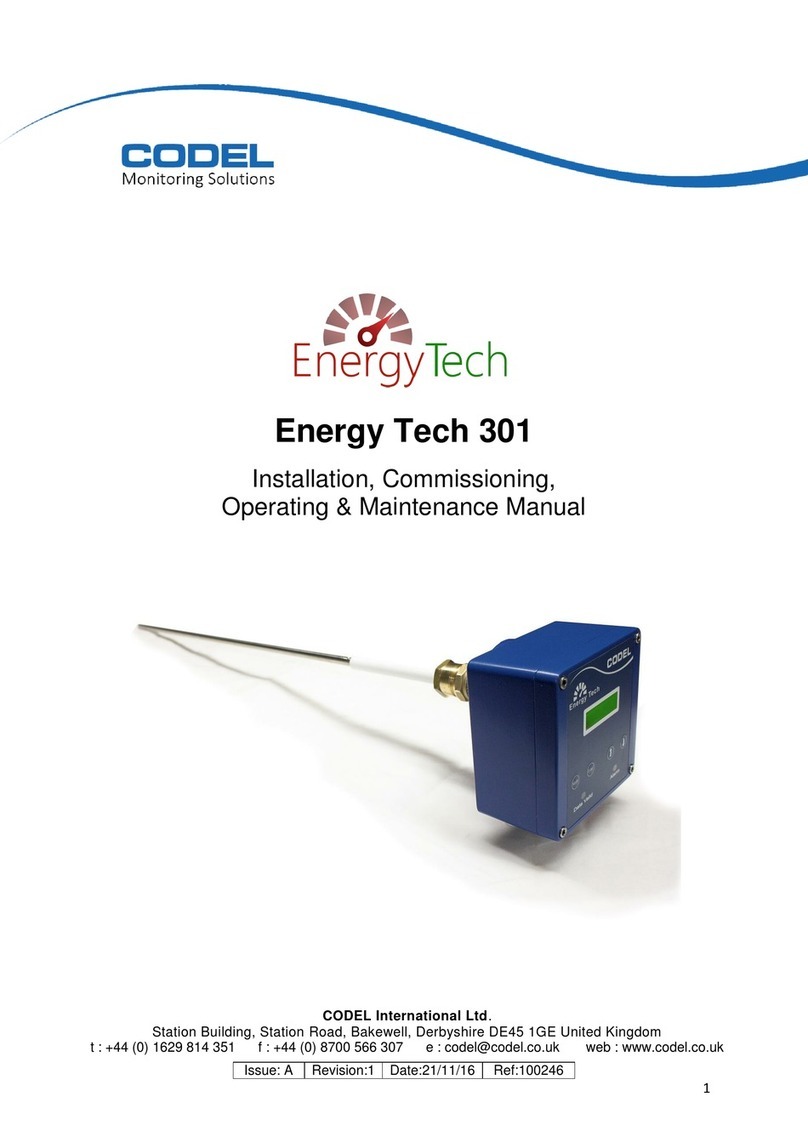
CODEL
CODEL Energy Tech 301 Guide

CODEL
CODEL EnergyTech 100 Series Guide
Popular Measuring Instrument manuals by other brands
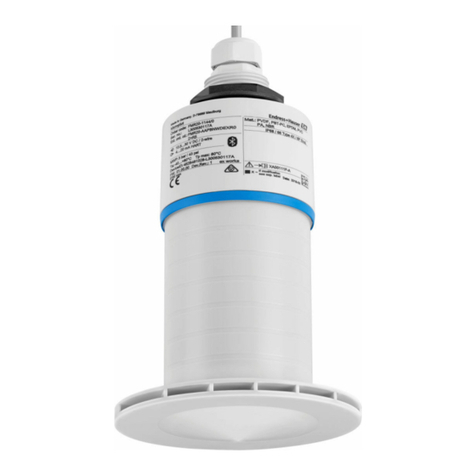
Endress+Hauser
Endress+Hauser Micropilot FMR20 Brief operating instructions

Anemoment
Anemoment TriSonica Mini user manual
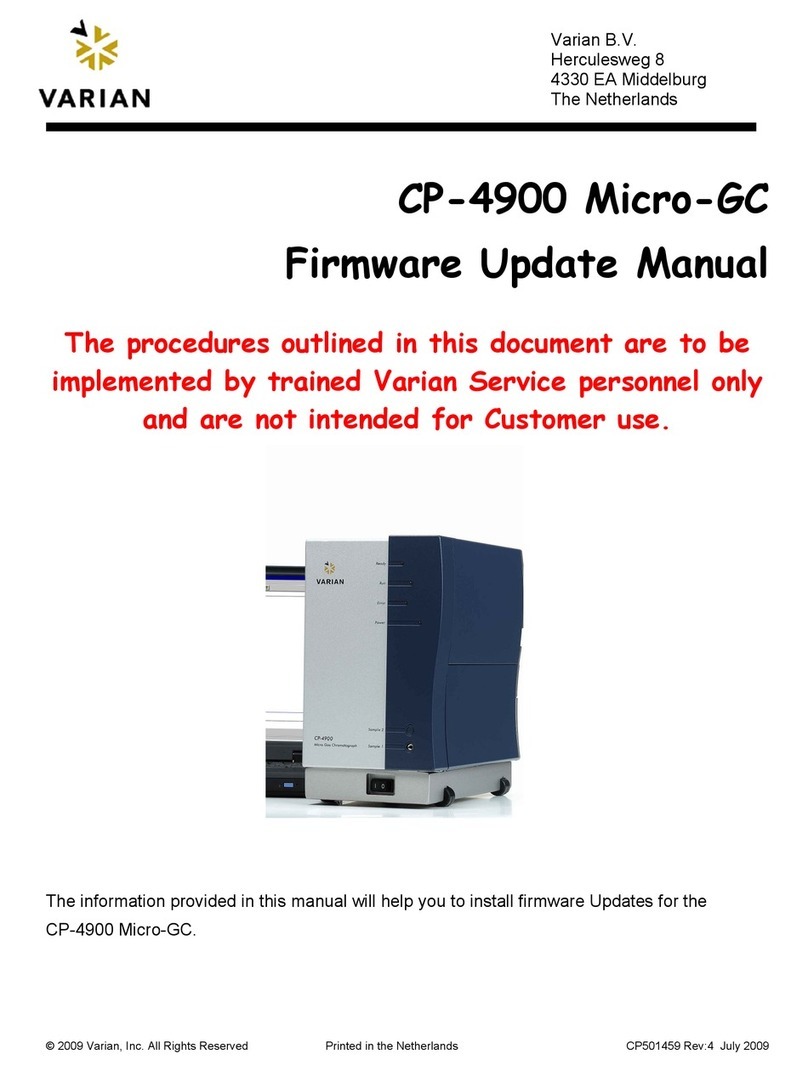
Varian
Varian CP-4900 Micro-GC Firmware update manual
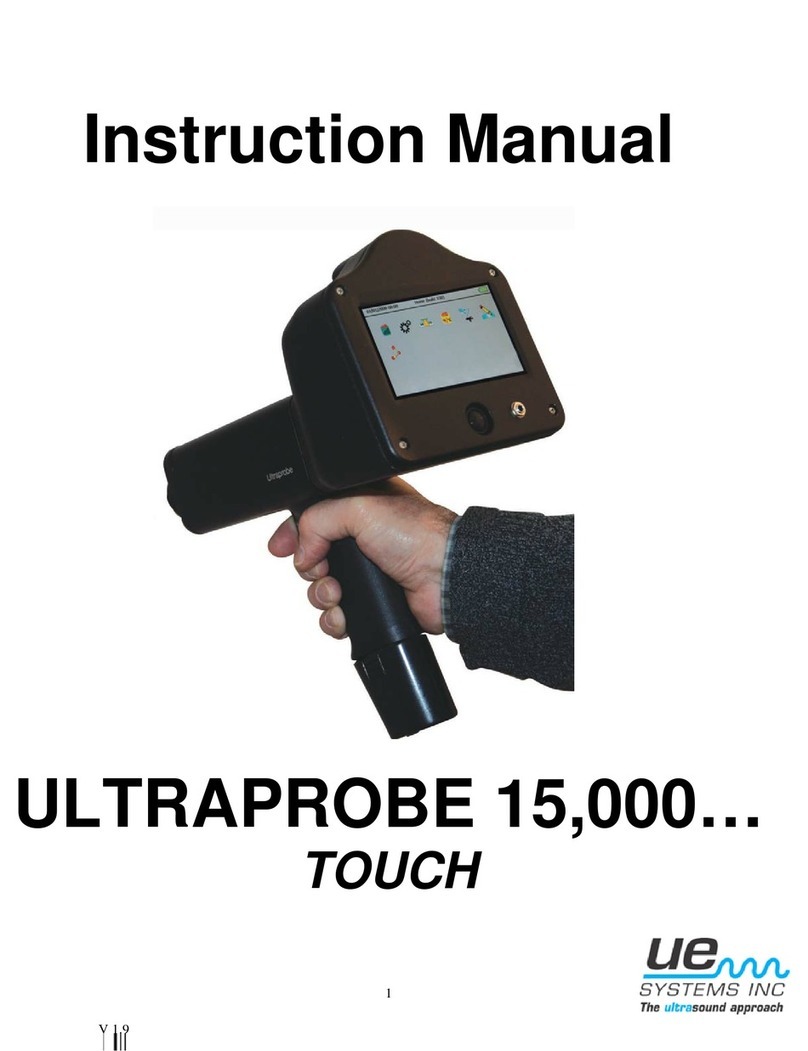
UE Systems
UE Systems Ultraprobe 15000 Touch instruction manual
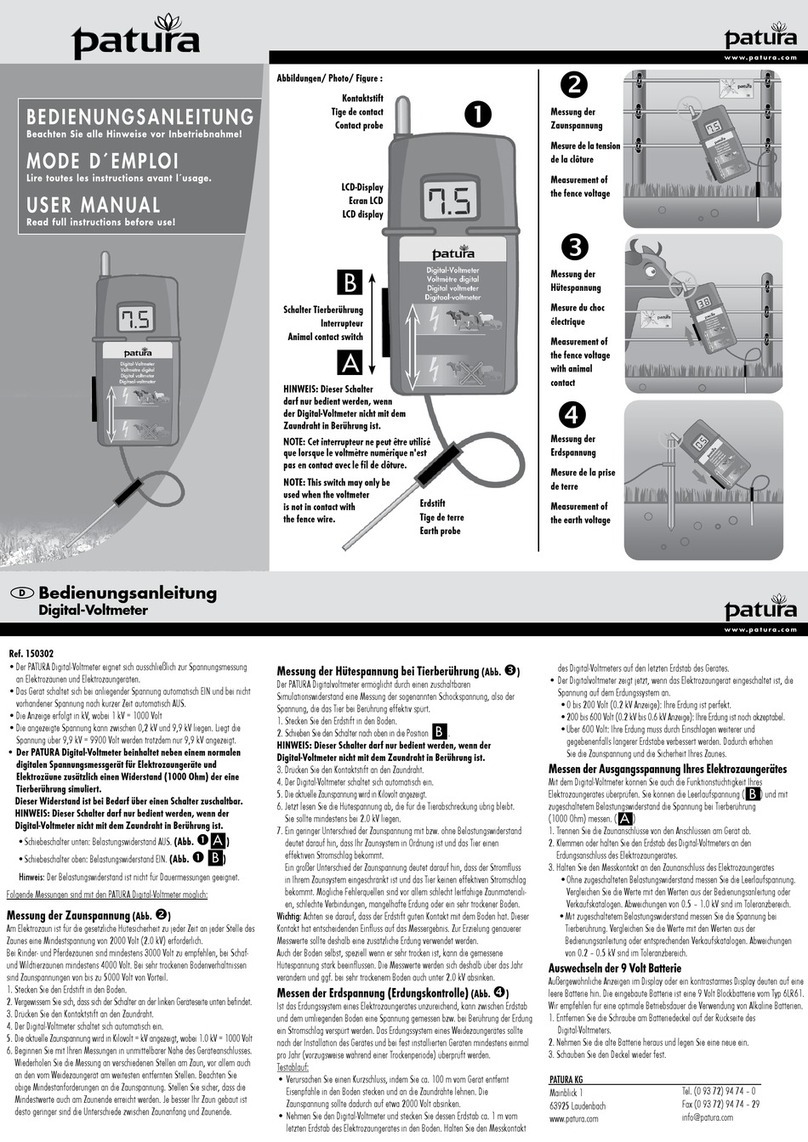
patura
patura 150302 user manual

ViroGates
ViroGates suPARnostic GENSPEED R2 manual