Compu-Flow EXM MAG User manual

Compu-Flow™ EXM MAG
™
Electromagnetic Insertion Flow Meter
Compu-Flow
www.advancedflow.com
1-800-649-5331

INTRODUCTION:
When you need a reliable flow meter the Compu-Flow™ is the right choice. We have been
manufacturing for the flow meter markets for the last 28 years.
Mag meters are the popular choice for closed pipe applications. he EXM model is the
most advanced design in the industry for Low Profile Single Point Insertion mag meters.
Compu-Flow™ EXM MAG
his style of flow meter is the practical choice for virtually all full pipe applications. he
EXM offers features often not found in even the most expensive spool piece models.
Rapid response time, simple installation and removal, rugged design, and unmatched
accuracy are just some of the advantages the EXM MAG offers. Combine this with our
user friendly display and competitive pricing and you have a winning combination.
2

INTRODUCTION:
Compu-Flow™ EXM MAG
The basic kit of the C6 Compu-Flow™
Electromagnetic flow meter consists of a low
profile insertion sensor and a display control
panel.
A modular system of electronics can be attached
directly to the flow sensor or remotely mounted.
The meter pro ides full indication of rate and
total, plus 4-20 mA, HiLo Alarms, RS232, and
Batch Control.
The adapter of the EXM models, mates with a
standard female NPT fitting, and can be directly
threaded into ordinary saddles or threaded weld
fittings. The EXM115 thru EXM136 offer an
isolation al e, allowing hot-tap installation, or
installation and remo al under pressure.
Compu
-
Flow
electromagnetic
flow
meters
work
under
the
Faraday
law
of
Compu
-
Flow
electromagnetic
flow
meters
work
under
the
Faraday
law
of
electromagnetic induction. They can be used to accurately measure the flow rate of
liquids which are electrical conducting, and mixed with liquids and solids. They are
widely used throughout industries of petroleum, pharmacology, papermaking,
electric power, en ironmental protection and so forth.
The main features of the control panel include:
• Smart LCD screen featuring high-resolution, 32 character, 2-line alphanumeric
pro iding rate and totalization simultaneously, in Metric or English units.
• Splash proof NEMA 4X case protects from moisture and caustics.
• Easy configuration for set up and operation with on-screen prompting, quick
scrolling menus, display panel keypad, and color coded LEDs.
• RS232 ia DB9 PORT 9600 Baud.
• Batch Control, Isolated Output for Dry Contact Relay.
• Separate High and Low Alarm outputs for Dry Contact Relay with LED status.
• Data Logger 1 – 32 GB memory USB Flash Dri e data transfer.
• Wireless Signal option from Sensors and/or Recei er (sensor singular).
• Optional signal cable lengths up to 5000 ft. No Tuning required.
3

INTRODUCTION:
Compu-Flow™ EXM MAG
• Great accuracy e en in turbulent flows.
• Wide pipe diameter range 2 – 72 inches.
• Maintenance-modular construction simplifying field ser ice.
• Non- olatile Flash Memory for installed parameters 99 yrs.
Operating Conditions:
• Ambient temperature: 0°-180° F (-17° - 82° C).
• Fluid temperature: 32°-200° F (0° - 93° C).
• Submersibility: Water proof up to 200 ft.
• Pressure: Brass/SS = 200 psi (13.8 bar)
• PVC = 150 psi (10 bar) @ 75° F.
• Applicable Fluid: Electrically conducting liquid.
• Electrical conducti ity: 20 Microsiemens / cm².
• Pipe Range: 2” –72” ID.
• Flow Range: 0.01 – 20.0 fps. (0.03 – 6.09 m/sec)
echnical Parameters:
• Housing: IP68 cast housing with modular electronics.
• Housing: IP68 cast housing with modular electronics.
• R/T Back Lit LCD UFMC6 Display Std.
• Power range 10-24 VDC, no fuses to change. Carbon Arc auto resettable
circuit brakers,1 million cycle a g. life. Fast acting break and quick reset.
• Digital signal: 12VDC proportional to flow @ 60 Hz/fps, nom. 50/50 duty
cycle.
• Signal LED output 12 VDC @ 10 mA with full pipe and flow.
• Update time: Selectable 1-30 sec. at recei er.
• Fitting size: 1½” Male NPT (EXM110/136); 2” Male NPT Ball Val e.
• Auto a eraging: 30 sec.
• Frequency Output: 60 Hz /fps.
• Bar Graph Flow/mA output LCD indicator.
• Pulse Output: Square wa e pulse, isolated, 1200 Hz @ 20 fps.
Forward flow standard, re erse flow optional.
• Flow signal: 10 mA @ 12 VDC Green Wire.
• K factor Default: 60 Hz/fps. Adjustable 1-256.
• Empty pipe detection: Software defaults to zero flow.
• Voltage output 1-5 VDC proportional to flow selectable.
• Hi&Lo Limit Alarms user select output to solid state relays.
4

Compu-Flow™ EXM MAG
echnical Parameters: (cont.)
• Communication: RS232 Recei er output DB9 / USB cable.
• Data Logger with USB memory and SD card platforms.
• Accuracy: 1% of full scale.
• Supply power: 12 VDC @ 300mA minimum.
• Housing material: Cast aluminum, powder-coated paint.
• Shaft/Fitting made of: 316 SS or Brass.
• Electrode Material: Hastelloy.
• Electrode cap material: Teflon, Mylar or Nylon.
• Val e assembly (EXM120-136): Bronze with SS ball al e.
• Nylon Tapered Ferrel Shaft Seal all models.
• Calibration accuracy: ± 1% of full scale.
• Re erse flow rate output with indicator signal. Optional.
• Noise immune circuitry, ery stable, not ground loop sensiti e.
• Nominal formula for insertion depth: 10% of pipe ID.
• Virtually unlimited cable length with no tuning required. Signal Cable 25ft std.
up to 1,000 ft w/o boost; 5,000 ft max.
• Simple 4 wire terminal connection with no tuning required.
• Digital signal output from the pipe. Unique stand alone sensor.
• Rugged construction. Quality components. SMT build format. Ultra reliable.
• Rugged construction. Quality components. SMT build format. Ultra reliable.
• Easily multiplexed to SCADA and PLC recei ers.
EXM110B
EXM124BBV
Custom Length
Special Model
EXM136BBV
5

Compu-Flow™ EXM MAG
INSTALLATION:
For best performance, the EXM sensor should be installed with at least ten
diameters of straight pipe upstream and fi e downstream. Certain extreme
situations such as partially-opened al es are particularly difficult and may
require more straight diameters upstream.
Chemical Injection or Fertigation. When any magmeter, by any
manufacturer,
is
used
in
a
chemical
injection
application
(including
Position of the meter:
Vertical flow in upward direction is the
preferred installation orientation, since it
impro es low-flow performance and a oids
problems with trapped air and sediment.
Bottom, top, and ertical pipe installations are
all acceptable if required by the piping layout.
manufacturer,
is
used
in
a
chemical
injection
application
(including
fertigation), the chemical line must be placed downstream of the
magmeter OR far enough upstream for complete mixing to occur before
the fluid reaches the meter. When unmixed chemical or fertilizer alternates
with water passing through the meter, the rapid changes in conducti ity
may cause sudden spikes and drops in the meter’s reading, resulting in
inaccurate measurement. The magmeter will restabilize, howe er, with a
steady flow of fluid of uniform conducti ity. Caution!: In chemical injection
or fertigation applications, install chemical line downstream of magmeter,
or far enough upstream to allow complete mixing of fluids before the
meter.
6
Yes
No
No

Compu-Flow™ EXM MAG
Caution!: These flow sensors are not recommended for installation
downstream of a boiler feedwater pump where installation fault may
expose the flow sensor to boiler pressure and temperature. Maximum
recommended temperature is 200°F.
Fitting Installation. EXM adapters mate with a 1-
1/2” female NPT pipe thread adapter fitting. Any
fitting that pro ides the matching NPT female
thread may be used. Installation procedure
compensates for fitting height differences. Cut a
minimum 1-3/4” hole in the pipe. If possible,
measure the wall thickness and write it down for
use in depth setting. Then install the threaded
fitting (saddle, weldolet, etc.) on the pipe.
INSTALLATION:
Installation of EXM 110-136:
Meter
Installation
.
Loosen
the
compression
nut
so
that
the
adapter
slides
Compression
Nut
Meter
Installation
.
Loosen
the
compression
nut
so
that
the
adapter
slides
freely. Pull the meter fully upward and finger-tighten the compression nut.
Using a thread sealant, install the adapter in the pipe fitting. Do not
o ertighten. Now loosen the compression nut, lower the meter to the
appropriate depth setting (see diagram and instructions that follow). Be
sure flow is in the direction of the arrow on the housing. Tighten
compression nut fully.
Installation of Hot Tap’ EXM 115-136:
‘Hot tap’ EXM meters are designed so they can be
installed and ser iced without depressurizing the
pipe.
Fitting Installation. The EXM 115 thru 136
adapters mate with a 2” FNPT threaded fitting for
compatibility with the 2” isolation al e. Any
fitting that pro ides matching NPT female thread
may be used. The installation procedure
compensates for differences in fitting height.
If initial installation is performed on an
unpressurized pipe, cut a minimum 1-3/4” hole in
the pipe.
7

Compu-Flow™ EXM MAG
INSTALLATION:
Installation of (Hot Tap) EXM 110 thru 136: (cont.)
If possible, measure the wall thickness and write it down for use in depth
setting. Then install the threaded fitting (saddle, weldolet, etc.) on the pipe.
If it is necessary to do the initial installation under pressure, any standard
hot tap drilling machine with 2” NPT adapter, such as a Transmate or a
Mueller, can be used. Ordinarily, it is not necessary to use an installation
tool, due to the small diameter tube the meter can be installed by hand at
all but the highest pressures.
Meter Installation. Remo e the sensor unit from the
al e assembly. Using a thread sealant, install the al e
assembly on the pipe fitting. If the initial installation is a
pressure (“hot”) tap, remo e the 1-1/2” x 2” adapter
bushing at the back of the al e. Thread the tapping
machine on, open the al e, and tap using a minimum of
1-3/4” or maximum 1-7/8” cutter. After retracting the
machine and closing the al e, reinstall the flow sensor.
When the sensor is secure, open the al e and adjust
depth
setting
(see
diagram
and
instructions
that
follow)
.
depth
setting
(see
diagram
and
instructions
that
follow)
.
Be sure flow is in the direction of the arrow on the
housing. Tighten fitting and compression nut fully.
Depth Setting. It is important for accuracy
that the sensor be inserted to the correct
depth into the pipe.
1. Take dimension from reference point (joint
in the housing) up to the tip of sensor.
2. From this whole dimension, subtract
10% of pipe I.D., and pipe thickness, to
obtain dimension “D”.
3. Measuring from the outside of the pipe to
the joint in the housing, as shown in the
diagram, adjust the sensor to Dimension D
and hand-tighten compression nut.
3. Align the conduit housing with the
centerline of the pipe. Be sure the arrow
on the housing points in the direction
of flow.
8
Flow
Flow

Compu-Flow™ EXM MAG
INSTALLATION:
Depth setting: (cont.)
4. Check Dimension D one more time.
5. Tighten the compression nut fully.
Caution!. Ne er attempt to remo e a flow sensor when there is pressure in
the pipe unless it is specifically designed for hot tap installation and remo al.
Loosen the compression nut slowly to release any trapped pressure. If fluid
sprays out when remo ing the sensor, stop turning and depressurize the
pipe. Failure to do so could result in the sensor being thrown from the pipe,
resulting in damage or serious injury.
NOMINAL PIPE SIZE
3" 4" 6" 8" 10" 12" 14" 16" 18" 20" 24" 30" 36"
PVC/Steel
Sch.40 0.216 0.237 0.280 0.322 0.365 0.406 0.438 0.500 0.562 0.593 0.687
PVC/Steel
Sch.80
0.300 0.337 0.432 0.500 0.593 0.687 0.750 0.843 0.937 1.031 1.218
Table 1: Pipe Wall Thickness
Sch.80
St inless
Steel(10S) 0.120 0.120 0.134 0.148 0.165 0.180 0.188 0.188 0.188 0.218 0.250 0.312 0.312
St inless
Steel(40S) 0.216 0.237 0.280 0.322 0.365 0.375 0.375 0.375 0.375 0.375 0.375 0.375 0.375
Copper
Tubing
(Type L)
0.090 0.110 0.140 0.200 0.250 0.280
Copper
Tubing
(Type k)
0.109 0.134 0.192 0.271 0.338 0.405
Br ss Pipe 0.219 0.250 0.250 0.312 0.365 0.375
Duct. Iron
(Cl ss 52) 0.280 0.290 0.310 0.330 0.350 0.370 0.390 0.400 0.410 0.420 0.440 0.470 0.530
9

Compu-Flow™ EXM MAG
INSTALLATION:
Minimum Straight Pipe Length Requirements
The meter´s accuracy is affected by disturbances such as pumps, elbows,
tees, al es, etc., in the flow stream. Install the meter in a straight run of
pipe as far as possible from any disturbances. The distance required for
accuracy depend on the type of disturbance.
Type of disturbance Straight Lengths of Pipe Required
Upstre m from tr nsducers Downstre m from tr nsducers
Fl nge 5 X Nomin l Pipe Size 5 X Nomin l Pipe Size
Reducer 7 X Nomin l Pipe Size 5 X Nomin l Pipe Size
90° Elbow 10 X Nomin l Pipe Size 5 X Nomin l Pipe Size
Two 90° Elbows - 1 Direction 15 X Nomin l Pipe Size 5 X Nomin l Pipe Size
Two 90° Elbows - 2 Directions 20 X Nomin l Pipe Size 5 X Nomin l Pipe Size
G te v lve or Pump 25 X Nomin l Pipe Size 5 X Nomin l Pipe Size
•The meter can be mounted on horizontal or ertical runs of pipe.
•A oid mounting on ertical down flows when possible.
•Mounting on the sides (3 o´clock and 9 o´clock) position on
horizontal pipe is recommended.
•Mounting anywhere around the diameter of ertical pipe is
acceptable,
howe er,
the
pipe
must
be
completely
full
of
fluid
NO
NO
Air could be trapped
Pipe must be full
Down flows
must ha e
back pressure
>= 10Ø >= 5Ø
acceptable,
howe er,
the
pipe
must
be
completely
full
of
fluid
at all times.
•Back pressure is required on downward flows to ensure a full pipe.
•See the minimum straight length of pipe requirement chart abo e.
•The meter can accurately measure flow from either direction.
Best recommended () spots to install flow meters:
10

Compu-Flow™ EXM MAG
ELECTRICAL CONNNECTIONS:
Transducer wiring:
If your electromagnetic sensor is not yet connected to the electronics
control panel, open the panel, and use the next figure as a guide to make
the proper wiring for the 4 transducer cables: Black (-12VDC), Red (+12VDC),
Green (Echo), White (Signal).
VDC BRG W
-+
General Electrical Guidelines:
• Whene er possible a oid running control cables in the same
conduit with or bundled with AC power.
• Using shielded cable, be sure to connect shield to ground at
power supply end of the cable.
• A oid routing flow sensor cables in close proximity to a
ariable frequency dri e when possible.
• Recommended power and output wiring is shielded twisted pair
18-22 AWG control cable.
• Recommended oltage is 12-24 Vdc. Note that unregulated
power supplies can ary from nameplate oltage by a
considerable amount, especially with AC line oltage fluctuation.
Therefore 24V power supplies must be regulated.
Output: The EXM sensor output is a 0-5V square wa e digital pulse train
proportional to flow @ 60Hz/fps .
Note: The EXM power requirement is 190mA@12VDC .
11

Compu-Flow™ EXM MAG
ELECTRICAL CONNNECTIONS:
Grounding Guidelines:
For best results, use a good quality earth ground, such as metallic water
piping or a dri en ground, to ensure a good connection to earth ground and
good noise suppression.
If the flow sensor is installed in metallic piping, for optimum connection
clamp wire to the piping a short distance to one side of the flow sensor
using an electrical grounding clamp. Connect the wire to the earth ground
and to one of the housing screws. For Non-Metallic Pipe: Connect one to the
housing screws by wire to a good earth ground, such as metallic water
piping or a rod dri en into the ground.
EXM meters are usually unaffected by moderate le els of electrical noise. In
some applications performance may be impro ed by taking the following
steps:
• Use shielded twisted pair cable (Belden 8723 or equi alent abo e
ground or Alpha 35482 or equi alent burial).
• Clamp a ferrite bead (Steward 28A2029-OAO or equi alent) on meter
signal/power
wire
within
3
/
4
”
of
the
meter
strain
relief
(tape
or
tie
wrap
signal/power
wire
within
3
/
4
”
of
the
meter
strain
relief
(tape
or
tie
wrap
in place if necessary). See diagram below.
• IMPORTANT - Connect the cable shield ground wire to ground, ONLY at
power supply end of cable.
Earth Ground
Metallic Pipe
Grounding Clamp
Place Ferrite
Bead Here
Housing Screw
Grounding diagram:
Earth Ground
12

Compu-Flow™ EXM MAG
TROUBLESHOOTING
Problem: No pulse output
Probable cause:
•Unit not grounded
•Below minimum flow cutoff
•Flow reversed
•Output connections reversed
•Pipe not full
•Excessive electric l noise
•No power
•Power reversed
•Fluid conductivity <20 microSiemens/cm
Try:
•Connect to e rth ground
•Check the Presence of Flow
•Note flow direction rrow, reverse direction to meter
•Ch nge output connections
•Check plumbing
•Check for proper electric l wiring
•Check for power cross power input termin ls
•Reverse connections
•Select nother flow meter
Problem: Output pulses incorrect
Probable cause:
•Missing or incorrect ground wire
•
Incorrect depth setting
Try:
•Check for proper ground
•
Check depth setting
p ge
•
Incorrect depth setting
•Fluid conductivity <20 microSiemens/cm
•Empty pipe
•Not enough str ight pipe
•Excessive electric l noise
•
Check depth setting
p ge
•Select nother flow meter
•Check for full pipe or inst ll meter in the vertic l position
•Check for ir pockets or turbulence. Refer to
inst ll tion p ge
•Check for proper electric l wiring
Problem: Jump reading
Probable cause:
•R pidly ch nging conductivity (in chemic l
injection or fertig tion pplic tions)
Try:
•Inst ll chemic l injection line downstre m of m gmeter
(or f r enough upstre m to llow complete mixing of
fluids before meter)
13

Compu-Flow™ EXM MAG
PROGRAMMING
To Operate Your Flow Meter for the First Time:
1. Complete all the steps in “Installation” pages.
2. Turn on power and obser e the display panel LCD. The display will show the
model name and number of the unit.
3. Following the prompts presented by the display panel LCD, and making your
entries using the keypad, configure your unit for operation for English or
Metric
.
Metric
.
□The LCD screen displays SELECT RATE. Select the unit of measure for
rate display: All rate selections may be displayed in seconds, minutes,
hours, days. Time elements: (1=Sec 2=Min 3=Hr 4=Day)
Table 2. Rate selection - English
Key Selection Definition
1FPS Feet per second
2GAL Gallon
3CF Cubic feet
4MG Million Gallons
5AF Acre Feet
6BL Barrel 42 gal
7MPS Meters per second
8LT Liter
9CM Cubic meter
14

Compu-Flow™ EXM MAG
PROGRAMMING
If you select FPS, the flow meter will automatically begin measuring flow in
feet per second. If you select keys 1 through 6, the LCD screen will ask that
you enter your pipe ID in inches. If you select keys 7 through 9, the LCD
screen will ask that you enter your pipe ID in millimeters.
After you enter your rate time element, the LCD screen will then display
SELECT TOTALIZER. Select the unit of measure for totalizer display:
Table 3. Totalizer selection
Key Selection Definition
1GAL Gallons
2CF Cubic feet
3MG Millions of gallons
4AF Acre feet
5BL Barrels 42 gal
6LT Liters
7CM Cubic meters
Your EXM flow meter is now configured to measure the flow parameters you
ha e set. After you set the flow reading parameters you need for your
system, you can secure these settings so they are sa ed in the e ent of
power loss to the electronics enclosure.
Note: To clear the rate and totalizer parameters you ha e set, select “0”
reset or switch the power off using the on/ off switch on the display panel.
Until settings are sa ed using Key # 8, “Secure On”, the security switch,
turning off power clears all pre iously set parameters. When you turn on
power again, the LCD screen will prompt you to restart programming.
After you enter your totalizer selection, the LCD screen will then display
Enter Pipe ID. If you select keys 1 through 5, the LCD screen will ask that you
enter your pipe ID in inches. If you select keys 6 through 7, the LCD screen
will ask that you enter your pipe ID in millimeters.
15

Compu-Flow™ EXM MAG
PROGRAMMING
To Sa e Your Programmed Flow Reading Settings Using the Secure Function:
1. Complete setting the flow reading parameters.
2. Press and hold key # 8 for 5 seconds until “Secure On” appears on the
LCD display.
Note: If you need to change your programming, press and hold key # 8
“Secure” until “Secure Off” appears on the LCD display.
If you wish to further customize your flow meter system for operation in
your process, continue on to “Ad anced Configuration Options”.
Advanced Configu ation Options
The display panel keypad has a secondary menu for ad anced configuration
options (the keypad toggle menu). You may want to use this menu to set 4-
20mA analog output, set up bar graph, select HI/LO alarm set points, and
configure batch control. To access the secondary menu, press appropriate
key until the display changes. To exit, press the key again.
•Figure 1 pro ides a isual representation of the toggle menu.
•Table 4 lists the ad anced configuration options accessible from the
display panel keypad.
Figure 1. Display unit keypad
B r gr ph
K f ctor reset (1 to 256)FPS/PWR cle r
4-20 mA
MPS/PWR cle r
High / Low l rm
Low flow cutoff
(M ximum = 2.5 fps)
Set upd te time
(1sec,10sec, uto v.)
Tot lizer reset
16

Compu-Flow™ EXM MAG
PROGRAMMING
Key Selection Functional Specifications
1FPS Feet per second/ clear pwr
2Bar Graph Analog 16 pt bar graph (n/a with batch)
3K Factor Select K factor while running
44-20 mA Set up 4-20 mA analog output
5Vel Sim Velocity Simulator for systems test
6Low Flow Cut Off Set low flow cut off (maximum = 2.5 fps)
7MPS Meters per second/ clear pwr
8Secure Secure parameters On / Off
9Update Time Select update time: 1, 2, or 3
0Reset / Recall Pipe ID Recall pipe ID/ configure batch/ system reset
HI / LO ALARM Set up HI/LO limit alarms/ reset cursor
TOT RESET Reset totalizer while running/ reset cursor
Table 4. Keyboard Toggle Menu
The default setting for secondary keyboard functions is feet per second (fps),
or meters per second (mps) if the flow meter is configured for metric units.
Once the flow meter is operational and you wish to acti ate the analog bar
graph, 4-20 mA output, batch control, high or low alarm, or low flow cut-off
options, consult ad anced parameter setting.
Before Setting Advanced Parameters
Sample parameter setting:
You ha e a elocity of 5 fps and you would like the 4-20 mA output to be 12
mA or 50% of scale. Push and hold the MA/4 key until the screen changes
and then release the key. Enter a scale alue of 10 fps ia the keypad. The
screen will automatically return the display to olumetric indication. The 4-
20 mA output will read 12 mA at the terminal strip located on the right side
of the main electronics circuit board. You may check your 4-20mA output
setting ia the bar graph.
17

Compu-Flow™ EXM MAG
PROGRAMMING
Note: Ne er adjust any of the potentiometers on the main processor board.
These settings are to be performed by authorized personnel only.
SETTING ADVANCED PARAMETERS
Bar Graph
To Set the Analog Bar Graph of Flow Rate: (n/a with batch)
1. Press the Bar Graph/2 key. Enter the desired full-scale flow rate
in the indicated engineering unit.
2. To return to the rate and totalizer flow reading, press the
Graph/2 key again.
3. To return to the graph, press the Graph/2 key again and select OK.
This section explains how to set ad anced parameters using the keyboard on
the front panel of the unit.
Batch Control
K Factor (Correction Factor)
The default K Factor on the flow meter is set at 60 hZ/ fps for EXM Sensors.
For nearly all applications, this default K Factor setting should be adequate.
There are only a few circumstances that might merit adjusting the default K
Factor setting on your Electromagnetic flow meter.
1. To configure batch control press “0” key and select Batch.
2. Select Enable and choose 1=Pulse, 2=Batch.
3. Select Batch olume in preselected engineering units.
Analog Output:
To Set the Analog Output:
1. Press the MA/4 key Enter the full scale preselected
engineering unit.
2. After the output le el has been set, the LCD screen will
return to the rate and totalizer flow reading.
18

Compu-Flow™ EXM MAG
PROGRAMMING
Low Flow Cutoff
To Set the Low Flow Cutoff:
1. Press the FPS/1 or MPS/7 key to obtain the current reading in feet
per second or meters per second. Press the key again to return to
the flow reading parameters pre iously shown.
2. Press the LFC/6 key. Enter the cutoff in feet per second or meters
per second. If you enter a parameter that is too high, the LCD
screen will display the maximum allowable cutoff setting and then
will return to the prompt for cutoff in feet per second.
Meters per Second/ Power Clear
3. After the low flow cutoff is set, the LCD screen will return to the rate
and totalizer flow reading.
To Read Meters Per Second:
1. Press the MPS/7 key. The LCD will show the flow reading in meters
per second on the upper line of the LCD screen, replacing the rate
parameter pre iously on the screen. The totalizer reading remains
the same parameter.
2. To return to the pre ious flow rate, press the MPS/7 key again.
Update Time
To Set Update Time:
1. Press the UT/9 key. To enter the selection screen.
1 = 1 sec 2 = 10 sec 3 = auto; “Auto” mode will update e ery
second when the elocity change is >5%. When the flow stabilizes
to < 5% change, the update time resets to a 10 second running a erage.
2. Enter the update time in 1 second, 10 seconds , or Auto.
3. After the update time is set, the LCD screen will return to the rate
and totalizer flow reading.
19

Compu-Flow™ EXM MAG
PROGRAMMING
Hi/Low Alarms
Totalizer Reset
To Set the High/ Low Alarms:
1. Press the HI/LO ALARM key. Select Hi, Lo, or Both.
You may change the alarms one at a time without
affecting anything else.
2. Next enter the high limit alarm in your preselected
engineering unit.
3. Now enter the low limit alarm in your preselected
engineering unit.
4. After the high and low alarm parameters are set, the LCD
screen will return to the rate and totalizer flow reading.
To Reset the Totalizer While the Unit is Running:
1. Press the TOT RESET key. The totalizer reading will return to zero.
2. The meter will begin taking totalizer readings from zero.
The rate reading remains unchanged.
20
This manual suits for next models
5
Table of contents
Other Compu-Flow Measuring Instrument manuals
Popular Measuring Instrument manuals by other brands
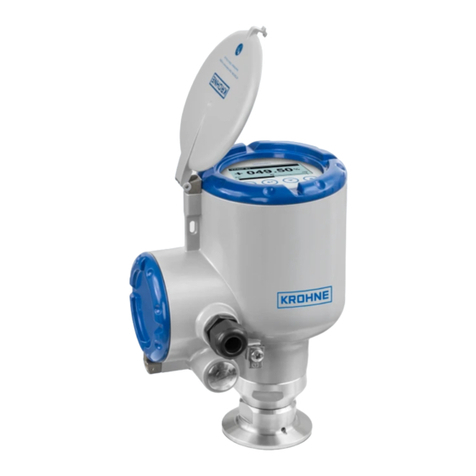
KROHNE
KROHNE OPTIWAVE 3500 C Handbook

Anaheim Scientific
Anaheim Scientific M130 user manual
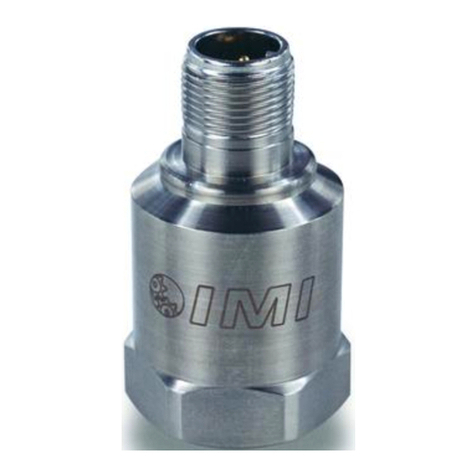
PCB Piezotronics
PCB Piezotronics IMI SENSORS M626B02 Installation and operating manual
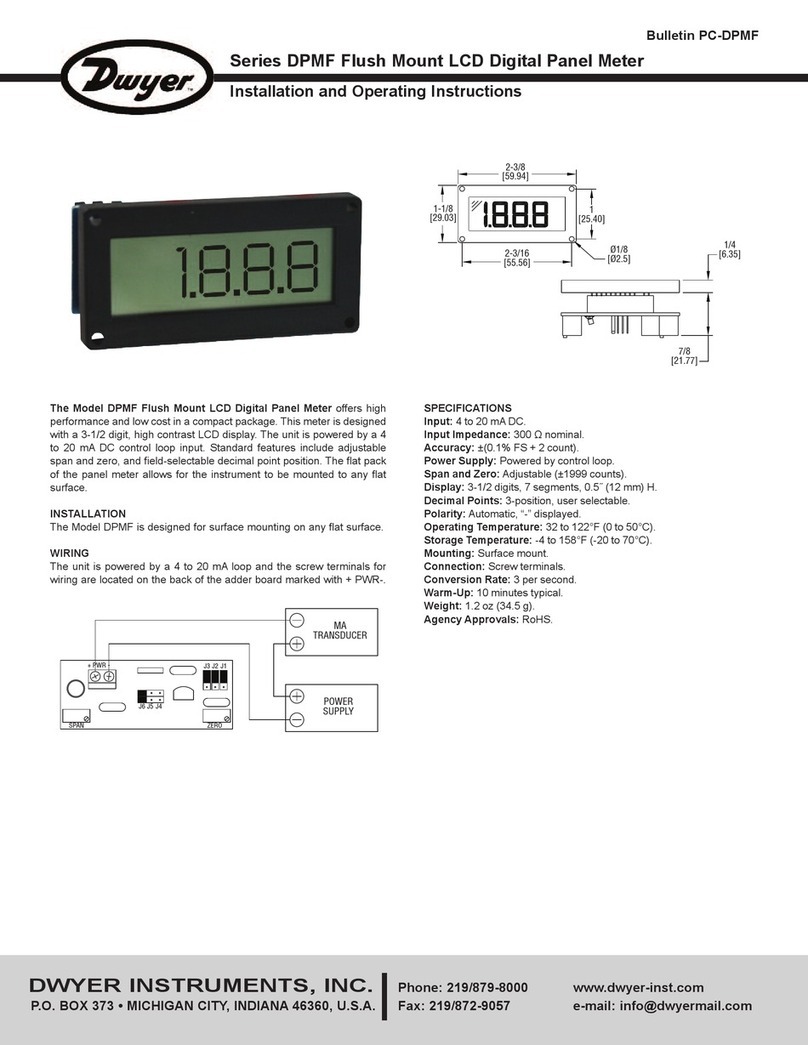
Dwyer Instruments
Dwyer Instruments DPMF Series Installation and operating instructions

Bender
Bender MRCDB423 Series quick start guide
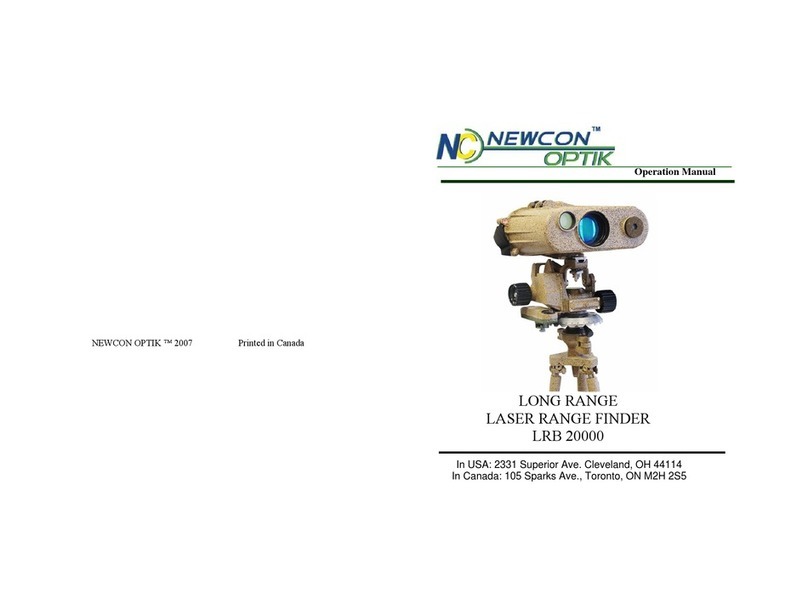
Newcon Optik
Newcon Optik LRB 20000 Operation manual