Condair Links Series Owner's manual

2584458-G EN 1902
Humidication and Evaporative Cooling
MODBUS
Addendum manual for installation and operation
for use with DL, ME, RS, EL and RO-A
devices as of software 5.8.x.x
Modbus

Thank you for choosing Condair
Installation date (MM/DD/YYYY):
Commissioning date (MM/DD/YYYY):
Site:
Model:
Serial number:
Proprietary Notice
This document and the information disclosed herein are proprietary data of Condair Group AG. Neither this document,
nor the information contained herein shall be reproduced, used, or disclosed to others without the written authori-
zation of Condair Group AG, except to the extent required for installation or maintenance of recipient's equipment.
Liability Notice
Condair Group AG does not accept any liability due to incorrect installation or operation of the equipment or due
to the use of parts/components/equipment that are not authorized by Condair Group AG.
Copyright Notice
© Condair Group AG, All rights reserved.
Technical modications reserved

3Contents
Contents
1 Introduction 5
1.1 Notes on this addendum manual 5
2 For your safety 6
3 Communication interface Integrated Controller 7
3.1 Technical data Modbus RTU 7
3.2 Technical data Modbus TCP 8
4 Modbus RTU 9
4.1 Before installation 9
4.2 Network structure Modbus RTU 9
4.3 Connection and conguration of the Integrated Controller for Modbus RTU 10
4.4 Determining the Modbus RTU interface parameters 11
5 Modbus TCP 13
5.1 Before installation 13
5.2 Network structure Modbus TCP 13
5.3 Determining the Modbus TCP interface parameters 14
5.3.1 Setting the network parameters (or IP parameters) 14
5.3.2 Setting the Modbus TCP interface parameters 15
6 Control signal settings 17
7 Notes on data register tables 18
7.1 Software version 1.1.x.x 18
7.2 Software version 4.x.x.x 18
7.3 Software version 5.x.x.x 18
7.4 Software version 5.3.x.x 18
7.5 Software version 5.7.x.x 19
7.6 Software version 5.8.x.x 19
8 Data register tables 20
8.1 Data register DL 20
8.2 Data register ME 22
8.3 Data register RS 25
8.4 Data register RO-A 29
8.5 Data register EL 30
9 Options 32
9.1 Galvanic Isolation Module 32
9.2 Mounting the "Isolation Module" option 32

5Introduction
1 Introduction
1.1 Notes on this addendum manual
This addendum manual is intended for use by engineers and properly trained technical personnel.
Please read this manual thoroughly before installing and conguring the Condair Integrated Controller
or a Modbus network.
If you have questions after reading this documentation, please contact your Condair representative.
They will be glad to assist you.
Symbols used in this manual
CAUTION!
The catchword "CAUTION" used in conjunction with the caution symbol in the circle designates notes
in this addendum manual that, if neglected, may cause damage and/or malfunction of the unit or
other material assets.
WARNING!
The catchword "WARNING" used in conjunction with the general caution symbol designates safety
and danger notes in this addendum manual that, if neglected, may cause to injury to persons.
DANGER!
The catchword "DANGER" used in conjunction with the general caution symbol designates safety and
danger notes in this addendum manual that, if neglected, may lead to severe injury or even death
of persons.
Safekeeping
Please safeguard this addendum manual in a safe place, where they can be immediately accessed. If the
equipment changes hands, the documentation must be passed on to the new operator.
If the documentation gets mislaid, please contact your Condair representative.
Language versions
This operation manual is available in various languages. Please contact your Condair representative
for information.

6For your safety
2 For your safety
General
Every person working with the Condair Integrated Controller must have read and understood this ad-
dendum manual, and the installation manual and operation manual of the Condair Integrated Controller,
before carrying out any work.
Knowing and understanding the contents of the manuals is a basic requirement for protecting the person-
nel against any kind of danger, to prevent faulty operation, and to operate the unit safely and correctly.
All icons, signs and markings applied to the unit must be observed and kept in readable state.
Qualication of personnel
All work described in this addendum manual may only be carried out by trained Condair service
technicians.
It is assumed that the service technicians working with the Condair Integrated Controller are familiar and
comply with the appropriate regulations on work safety and the prevention of accidents.
Danger that may arise from the Condair Integrated Controller
DANGER!
Danger of electric hazard!
The electrical compartment where the Integrated Controller is located may have live mains
voltage connected for other uses of the device. Live parts may be exposed when the control
unit is open. Touching live parts may cause severe injury or danger to life.
Prevention: Before commencing any work on the control unit disconnect the mains supply voltage
to the device via the electrical isolator in the mains supply line, and secure electrical isolator in "Off"
position against inadvertent switching on.
Safety reporting
All persons working with the Condair Integrated Controller are obliged to report any alterations to the
system that may affect safety to the owner without delay and to secure such systems against accidental
power-up.
Prohibited modications to the unit
No modications must be undertaken on the Condair Integrated Controller without the express written
consent of the manufacturer. For the replacement of defective components use exclusively original ac-
cessories and spare parts available from your Condair representative.

7Communication interface Integrated Controller
3 Communication interface Integrated Controller
3.1 Technical data Modbus RTU
Protocol Modbus RTU
Interface EIA-485 (RS485) (2-wire / GND)
Galvanic isolated No (Galvanic isolation optional possible, see chapter 9)
Connection Plug-in screw terminal 3-pole:
Data + / Data - / GND
Telegram format 1 Start / 8 Data / 1 Parity / 1 Stop
Data check CRC according to Modbus RTU specication
Modbus address 1 – 247 (10)
Parity None, even, odd
Baud rate 9600, 19200, 38400, 57600, 115200
Control signal timeout 0-300s (300s)
Max. number of devices 32 (according to RS485 specication)
Supporting Modbus functions 3 Read Holding Registers
4 Read Input Registers
6 Write Single Registers
Register format 16-Bit UInt Register
32-Bit Float Register (only from software version 5.x.x.x or higher)
Max. cable lengths/ type 600 m
Balanced twisted pair with shield, 100-120 Ohm impedance
Topology Line (Daisy Chain)
Software version device 5.x.x.x or higher
bold data = default settings

8Communication interface Integrated Controller
3.2 Technical data Modbus TCP
Protocol Modbus TCP
Interface RJ45 Ethernet port
Port 502 (options 1 - 65535)
Modbus address 255
Max. number of devices According Ethernet specication
Bitrate 10 / 100 Mbits/s (according to Ethernet specication)
Control signal timeout 0-300s (300s)
Supporting Modbus functions 3 Read Holding Registers
4 Read Input Registers
6 Write Single Registers
Register format 16-Bit UInt Register
32-Bit Float Register
Max. cable lengths/ type 100m, CAT5 / 6
Topology Bus (according to Ethernet specication)
Max. number of clients 3
Software version device Version 5.8 or higher
bold data = default settings

9Modbus RTU
4 Modbus RTU
4.1 Before installation
To do installation works on the respective device you have to switch off the device and secure it from
unintended switch-on according to the operation manual! Also follow any other safety instructions from
the user manual. If not mentioned otherwise, the specications of the Modbus RTU or RS485 standard
apply. The installation has to be carried out in accordance with local regulations.
It's recommended to update the device software to the newest version before start the implementation
of the device in a Modbus RTU network.
The respective device acts as a slave only. The Modbus RTU master - slave principle only allows the
master (e.g. a control computer) to initiate date transmission. The respective slave device then reacts and
exports the requested data to the master or carries out the action required by the master. In a Modbus
RTU network only one master may be present.
4.2 Network structure Modbus RTU
GND
+
–
GND
+
–
J6
GND
+
–
J6
Device 1
Master
RS485
Device 2
Shield
Fig. 1: Example Modbus RTU Network
– Connect the cable shield on one side with the functional earth
– Connect all GND together
– Install bus line separate from supply voltage
– Topology: Daisy chain
– All devices of the same network need the same settings concerning baud rate and parity
– Every Modbus device address can only be allocated once within the same network.

10 Modbus RTU
4.3 Connection and conguration of the Integrated Controller for Modbus RTU
3V
CR2032
GND + – GND + – GND + –24V GND
BMS
(USB)
RJ45
J7
J4J8J11
J6
J10
J12
J14
3J 2J
J7
J4
GND
+
–
Fig. 2: Integrated Controller (back view)
– Modbus RTU communication via port J6 "BMS"
– Jumper J7 has to be set for all devices.
– Jumper J4 only has to be set for the last devices in the net (end of line termination at the beginning
and end of the Modbus net). Jumper J4 set = end of line termination resistor activated.
– Jumper J4 has to be always removed by using the optional galvanic isolation (see chapter 9).
– All devices have to connected via GND.
– Software Version 1.1.0.23 or higher is needed (recommended software version 5.x.x.x or higher).
Important: When laying the network cabling,
make sure there is sufcient distance to other
cables, especially if they are connected to the
mains!

11Modbus RTU
4.4 Determining the Modbus RTU interface parameters
The following interface parameters are xed and can not be modied:
– 1 start bit
– 8 data bits
– 1 parity bit
– 1 stop bit
The following Modbus RTU settings must be specied. Changes to these settings only become
effective after a restart!
Select "Communication" (Path: Menu > Password entry 8808 > Conguration > Communication). In
the "Communication" submenu scroll to "Modbus-Parameter" tab. Touch the "Modbus" eld, set Mod-
bus function to "Modbus/RTU" and conrm with the check mark button. The setting parameters for the
Modbus RTU communication appear.
Modbus Address: With this setting you determine the Modbus address for
the device for the communication via a Modbus network.
Note: The same address may only be assigned once per Modbus network.
Factory setting: 10
Setting range: 1 ... 247
Parity: With this setting you set the parity bit for the data transfer.
Factory setting: Even
Options: None, Even or Odd

12 Modbus RTU
Baud Rate: With this setting you set the baud rate for the data transfer.
Note: In the same Modbus network the baud rate must be the same for all
participants. Only use for Modbus RTU the baud rates listed under Option.
Factory setting: 9600
Options: 9600, 19200, 38400, 57600 or 115200
Register Sequence: With this setting you determine the register sequence
for the transmission of oating-point numbers. .
Note: With Modbus communication 32 Bit oating-point numbers are transmitted
in two registers of 16 Bit each. In order that sender and receiver understand
each other (that means both use the identical partitioning of the 32 Bit to the
two 16 Bit registers) it must be determined whether the high-order register
(MSR = Most Signicant Register) or the low-order register (LSR = Least
Signicant Register) is transmitted rst.
Factory setting: MSR rst
Options: LSR rst (low-order register is transmitted rst)
Edianness: Little Edian Byte Swapped
(Format 32 Bit Float [CD] [AB])
MSR rst (high-order register is transmitted rst)
Edianness: Big Endian
(Format 32 Bit Float [AB] [CD])
In the "Communication" submenu scroll to "BMS-Timeout" tab. Touch the "BMS-Timeout" eld.
BMS-Timeout: With this setting you determine the timeout for the timeout for
the data transfer. If the communication with the Modbus master fails longer
than the set time, warning W35 "BMS Timeout" is triggered.
Note: The BMS timeout is only evaluated if the signal source (Path: Menu>
Conguration> Control Settings > Source) is not set to "Analog".
Factory setting: 300 s
Setting range: 1 ... 300 s
Note: As of software version 5.3.x.x, the device is stopped when warning
W35 occurs.

13Modbus TCP
5 Modbus TCP
5.1 Before installation
To do installation works on the respective device you have to switch off the device and secure it from
unintended switch-on according to the appropriate operation manual! Also follow any other safety in-
structions from the user manual. If not mentioned otherwise, the specications of the Modbus TCP or
Ethernet standard apply. The installation has to be carried out in accordance with local regulations.
It's recommended to update the device software to the newest version before start the implementation
of the device in a Modbus TCP network. Modbus TCP is only supported as of software version 5.8.
The device acts as a server only. The Modbus TCP client - server principle only allows the client (e.g.
a control computer) to initiate date transmission. The respective server (respective device) then reacts
and export the requested data to the client or carries out the action required by the client.
5.2 Network structure Modbus TCP
3V
CR2032
GND + – GND + – GND + –24V GND
BMS
(USB)
RJ45
J7
J4J8J11
J6
J10
J12
J14
J2J3
Ethernet (Modbus TCP)
CAT6A cable (or higher) with RJ45
connector
Integrated Controller
(back view)
RJ45
Fig. 3: Example Modbus TCP Network
Important: When laying the network cabling,
make sure there is sufcient distance to other
cables, especially if they are connected to the
mains!

14 Modbus TCP
5.3 Determining the Modbus TCP interface parameters
5.3.1 Setting the network parameters (or IP parameters)
The network settings (or IP settings) are used for the communication via the integrated Modbus TCP
interface.
Select "Communication" submenu (Path: Menu > Password entry 8808 > Conguration > Communica-
tion). In the "Communication" submenu select the "Network Parameters" tab.
– IP Type: With this setting you determine whether you want to assign the IP
Address, the Subnet Mask, the Standard Gateway as well as the Primary
and Secondary DNS address as xed values or whether these should be
dynamically assigned via a DHCP server.
Note: After 5 unsuccessful attempts at obtaining an address with DHCP
the system will revert to xed assignment
Factory setting: DHCP
Options: DHCP (dynamic assignment)
Fixed (xed assignment)
– IP Address: This eld shows the actual IP address of the device assigned
manually or assigned by a DHCP server.
If the parameter "IP Type" is set to "Fix", the IP address of the device can
be set via this eld. If the parameter "IP type" is set to "DHCP", the IP
address of the device is assigned by a DHCP server.
– Subnet Mask: This eld shows the actual subnet mask of the IP network
assigned manually or assigned by a DHCP server.
If the parameter "IP Type" is set to "Fix", the subnet mask can be set via
this eld. If the parameter "IP type" is set to "DHCP", the subnet mask is
assigned by a DHCP server.
– Default Gateway: This eld shows the actual IP address of the default
gateway assigned manually or assigned by a DHCP server.
If the parameter "IP Type" is set to "Fix", the IP address of the default gate-
way can be set via this eld. If the parameter "IP type" is set to "DHCP",
the IP address of the default gateway is assigned by a DHCP server.

15Modbus TCP
– Primary DNS: This eld shows the actual IP address of the primary domain
name server (DNS) assigned manually or assigned by a DHCP server.
If the parameter "IP Type" is set to "Fix", the IP address of the primary
domain name server can be set via this eld. If the parameter "IP type"
is set to "DHCP", the IP address of the primary domain name server is
assigned by a DHCP server.
– Secondary DNS: This eld shows the actual IP address of the secondary
domain name server (DNS) assigned manually or assigned by a DHCP
server.
If the parameter "IP Type" is set to "Fix", the IP address of the secondary
domain name server can be set via this eld. If the parameter "IP type"
is set to "DHCP", the IP address of the secondary domain name server
is assigned by a DHCP server.
– MAC Address: Factory set MAC Address (Media Access Control) of the
device. Not modiable.
– Host Name: Host Name of the device automatically generated by the
control. Format: "IC_"+"Serial number of the device". Not modiable.
5.3.2 Setting the Modbus TCP interface parameters
Select "Communication" submenu (Path: Menu > Password entry 8808 > Conguration > Communica-
tion). In the "Communication" submenu scroll to the "Modbus Parameters" tab. Touch the "Modbus" eld,
set Modbus function to "Modbus/TCP" and conrm with the check mark button. The setting parameters
for the Modbus TCP communication appear.
IP Port: With this setting you assign a IP port number for Modbus TCP. By
default, Modbus TCP uses port 502.
Factory setting: 502
Setting range: 1 ... 65535

16 Modbus TCP
Register Sequence: With this setting you determine the register sequence
for the transmission of oating-point numbers. .
Note: With Modbus communication 32 Bit oating-point numbers are transmitted
in two registers of 16 Bit each. In order that sender and receiver understand
each other (that means both use the identical partitioning of the 32 Bit to the
two 16 Bit registers) it must be determined whether the high-order register
(MSR = Most Signicant Register) or the low-order register (LSR = Least
Signicant Register) is transmitted rst.
Factory setting: MSR rst
Options: LSR rst (low-order register is transmitted rst)
Edianness: Little Edian Byte Swapped
(Format 32 Bit Float [CD] [AB])
MSR rst (high-order register is transmitted rst)
Edianness: Big Endian
(Format 32 Bit Float [AB] [CD])
In the "Communication" submenu scroll to "BMS-Timeout" tab. Touch the "BMS-Timeout" eld.
BMS-Timeout: With this setting you determine the timeout for the timeout for
the data transfer. If the communication with the Modbus master fails longer
than the set time, warning W35 "BMS Timeout" is triggered.
Note: The BMS timeout is only evaluated if the signal source (Path: Menu>
Conguration> Control Settings > Source) is not set to "Analog".
Factory setting: 300 s
Setting range: 1 ... 300 s
Note: As of software version 5.3.x.x, the device is stopped when warning
W35 occurs.

17Control signal settings
6 Control signal settings
If the demand or control signal is also to be transmitted via Modbus, the signal source must be set to
"Modbus" in "Menu> Password entry 8808> Conguration> Control Settings> Source" as shown below.
Important: If the demand or control signal via Modbus is used, no second, hard-wired demand or control
signal may be connected to the driver board!
Further information on the control settings can be found in the operating instructions for the correspond-
ing device.
Notes on monitoring of the bus communication
Monitoring of the bus communication as described below takes place only if the "Source" parameter in
the "Control Settings" submenu is not set to "Analog".
As soon as the control signal (demand or humidity signal) is transmitted via Modbus RTU or Modbus
TCP, the communication via the bus system is also monitored. The control signal must be periodically
updated within the time set in "BMS Timeout".
If the control signal is not updated within the set time, warning W35 "BMS Timeout" will be triggered
and the humidication will be stopped until the humidier receives a valid signal into one of the writable
holding registers.
This monitoring is intended to prevent the humidier from humidifying with the last transmitted value in
the event of a bus failure.

18 Notes on data register tables
7 Notes on data register tables
7.1 Software version 1.1.x.x
– UInt16 register only
– No decimals
e.g.:
>0,1 bar ... <1,0 bar = 0
>1,0 bar ... <2,0 bar = 1
>2,0 bar ... <3,0 bar = 2
etc.
– Only imperial display via Modbus
– Pressure values in bar
7.2 Software version 4.x.x.x
– UInt16 register only
– No decimals
– Values rounded
e.g.:
>0,1 bar ... <1,5 bar = 1
>1,5 bar ... <2,5 bar = 2
>2,5 bar ... <3,5 bar = 3
etc.
– Metric or imperial units according to the control unit settings of the corresponding device
7.3 Software version 5.x.x.x
– Use of UInt16 and 32-Bit Float register
– Decimals are shown by all 32-Bit Float registers
– New register addresses for 32-Bit Float
7.4 Software version 5.3.x.x
– When warning W35 "BMS Timeout" occurs, the device is stopped. The BMS timeout is only evaluated,
if the signal source under "Menu > Control Settings > Source" is not set to "Analog" (see chapter 6)
– EL new register for "Operating status A unit" and "Operating status B unit"
– EL new register for internal controller settings

19Notes on data register tables
7.5 Software version 5.7.x.x
– ME: New unit of measure "days" at next Ag+ service and next UV bulb replacement
– EL: Various new registers, weighted hours removed, Fault and Warning implemented in maintenance
and malfunction status
7.6 Software version 5.8.x.x
– Modbus TCP integrated for DL, ME, RS, EL and RO-A
– DL: New register 41707 "Remote ush"
– DL register 31010: New status "Temperature ush"
– DL register 31013: New status "Replace Ag+ cartridge" and status "Disinfection"

20 Data register tables
8 Data register tables
8.1 Data register DL
Description Range Input Register 1-based Format
Read with function 04
Max. capacity 1) 2 - 1000 kg/h
4 - 2573 lb/hr 31300
32-Bit Float 7)
Actual capacity 1) 0 - 1000 kg/h
0 - 2573 lb/hr 31302
Actual humidity or demand 0 - 100 % 31304
Operating hours 0 - 1'200'000 h 31308
Next service 0 - 10000 h 31310
Remaining Ag-ion
capacity 0 - 58.4 Ah 31312
Target Ag-ion current 0 - 29.2 mA 31314
Inlet pressure PS4 1) 0 - 12.0 bar
0 - 174.0 psi 3) 31316
Nozzle pressure PS5 1) 0 - 12.0 bar
0 - 174.0 psi 3) 31318
Water temperatur 1) °C or °F 31320
Conductivity 0 - x μS/cm 31322
Pump current 0 - 5.0 A 31324
Ag-ion current 0 - x mA 31326
Device type
0 = Hum
1 = Hum + FU
2 = Hum + RO-C
3 = RO
31000
UInt16
Operating status
0 = Initializing
1 = Diagnostic
2 = Stopped
3 = Flushing
4 = Standby
5 = Flushed
6 = Humidifying
7 = Ready
8 = Refreshing
9 = Air pressure cleaning
10 = Filling
11 = Conductivity ush
12 = Switched Off
13 = Remote Off
14 = Regenerating
15 = Temperature ushing
31010
Maintenance and
malfunctions status
0 = Service Info
1 = Warning
2 = Activation Code
3 = Out of Commissioning
4 = Rell Disinfection
5 = Service
6 = Fault
7 = Replace Ag Cartridge
8 = Disinfection
31013
Error code 2) 0 = No error 31014
Other manuals for Links Series
4
This manual suits for next models
1
Table of contents
Other Condair Controllers manuals
Popular Controllers manuals by other brands
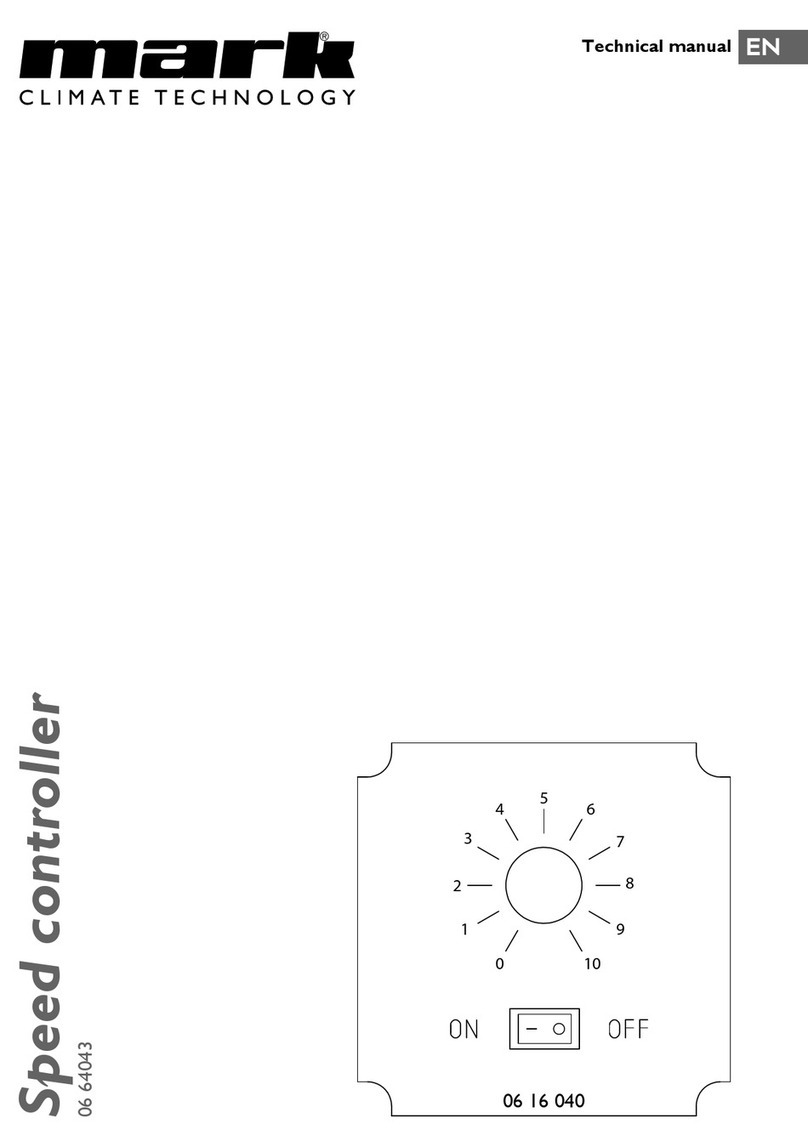
Mark
Mark 06 64043 Technical manual
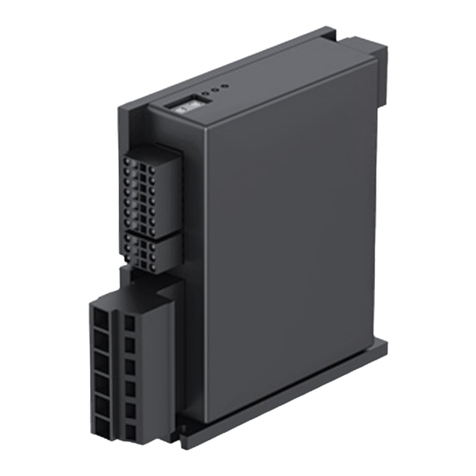
Ebmpapst
Ebmpapst VTD-60 K5SB Series Translation of the original operating instructions

EP Solar
EP Solar Tracer1215BN user manual

MB QUART
MB QUART Hifonics TPS-BT1 Quick start installation guide

WindowMaster
WindowMaster MotorController WCC 103 Installation instruction
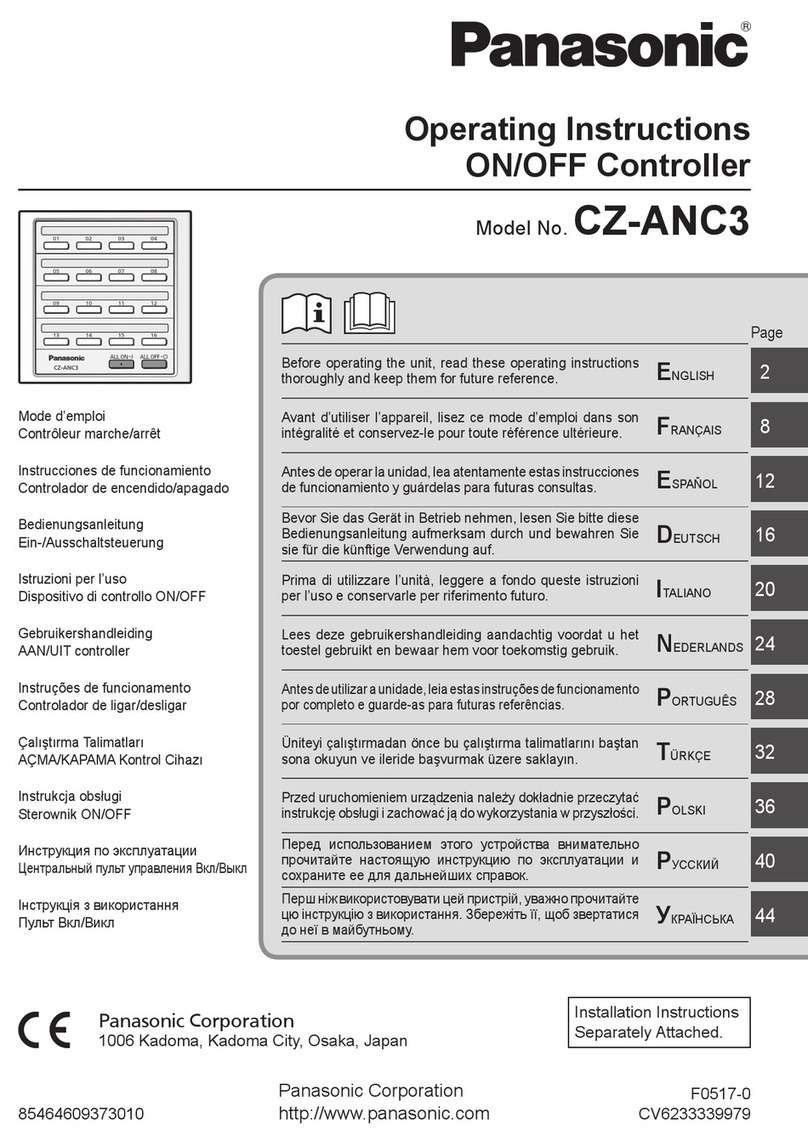
Sky Wing
Sky Wing CZ-ANC3 operating instructions