Coreline Fig.223 Wafer Instruction manual

Rubber seat butterfly valves
Fig.223 : Wafer
Fig.224 : Lug
English
Introduction
In order to benefit from the excellent properties of the Coreline butterfly valves, it is necessary to follow the instructions of
this user manual carefully. For errors resulting from improper installation, the manufacturer or Distributer can not be held
responsible. Consult the applicable standards for allowable flange dimensions. Dimensions, materials and applicability of
the valves should be derived from the technical datasheets and documentation, which can be found in our latest
catalogue from our website - www.coreline.dk .
Requirements for the maintenance staff
The staff assigned to assembly, operating and maintenance tasks, should be qualified to carry out such jobs and in any
circumstance, ensure personal safety.
www.coreline.dk
Installation-Operation-Maintenance Manual

www.coreline.dk
2/8
Installation-Operation-Maintenance Manual
page 3 ………………… Transportation and storage
Precautions before installation
Inspection of valve
Confirmation of valve working conditions
Operation of valve
page 4 ………………… Service and medium factor - Actuator Sizing
Installation direction of shaft
Pipe cleaning
Valve installation
page 6 ………………… After installation
Additional information
Use and maintenance
page 7 ………………… Material part list of valve
page 8 ………………… Troubleshooting
General warning
Chart for medium resistance

Installation-Operation-Maintenance Manual
Transportation and storage
Valves must be well protected and gently transported to avoid scratches, damage and enviroment damage. Stock the
valves indoors in dark and cool places to reduce rubber aging. Rubber is organic and lifetime will be reduced if
exposed to light and warm ambient temperatures.
During the storage, the valve disc must be in the slightly open position with an angle between 5~10° (See Fig.1).
Precautions before installation
Before installing the valve, please read the instruction manual carefully, pay attention to the safety matters and precautions
in the instruction manual before and during installation. Follow the instructions in the installation manual to help ensure that
the valve can be installed quickly and correctly.
Inspection of valve
Although valve manufacturers will take certain steps to prevent shipping damage, such damage can still occur and can be
discovered and notified before installation. Do not install valves that are known to be damaged during transportation and
storage. Before installation, check and remove all transport stops, protective plugs or protection covers, and check the
inside of the valve body to ensure that there are no foreign objects.
Confirmation of valve working conditions
Before installing the valve, check that the specification on the identification plate meets the requirements regarding
pressure, temperature and media. The valve shall not be installed, in environment that may cause corrosion or damage to
the valve.
Operation of valve
There is a small triangular shaped figure on the sealing surface of the seat from DN40 to DN300. This triangle indicates
which way the disc has to enter the seat. The operation of the valves, therefor, either free stem, handle or gear operated,
must follow the guidelines as shown below:
Turn the disc clockwise, towards the arrow (See Fig.2) to close the disc. Turn the disc anti-clockwise, towards the arrow to
open. This is to achieve the lowest possible torque - and thus the longest possible lifetime (See Fig.3).
The best angle for a closed valve is 2°. The patented design of the liner make the valve tight at this angle and reduce
torque and wear.
Though the valves are constructed to work as described above, Clockwise rotation can be applied without problems, if you
take in to consideration that the torque in this case will increase.
For butterfly valves ≥ DN350, the valve can be operated with both clockwise and counterclockwise direction, and the
recommended angle for a closed valve is 0°.
Fig.1
Fig.2
Fig.3 Turn clockwise 2° to close
www.coreline.dk
3/8

Installation-Operation-Maintenance Manual
Installation direction of shaft
Most butterfly valves can be installed in any position, but the most common method is to mount the shaft in vertical
direction with the activating upwards. However, if there is lot of dirt floating in bottom of pipeline, we recommend to
mount the valve with horizontal shaft. Then you avoid massive dirt at the turning points, which is sealing to ambient (See
Fig.4). Let the lower disc plate open in flow direction to avoid wear.
Pipe cleaning
Foreign matters in the pipeline may damage the sealing surface of the valve or prevent the movement of the butterfly
disc, resulting in the valve not closing properly. In order to reduce the possibility of dangerous situations, all pipes need
to be cleaned before installing the valve. Check that pipe dirt, metal chips, welding slag and other foreign objects have
been removed. In addition, check the flange surface of the pipe to ensure that there is a smooth surface (If any cleaning
proces after the valve is installed in pipeline, the disc has to be in open position and must not be activated before rinsing
completed, to avoid damage of seat).
Valve installation
Welding operation must not be done nearby the butterfly valve, as welding drops can damage the seat.
Check if the flange inner diameter is too small, it may cause valve disc damaged or the valve cannot be operated (See
Fig.6).
When installing a butterfly valve with rubber seat, there shall be no additional gasket on the flange surface. It is recom-
mended that the flange installed with the butterfly valve meet the relevant standards.
Check that the pipes are in a straight line and the flanges are clean and parallel. Do not install the valve between two
non-parallel flange faces(See Fig.7).
The distance between the flanges must correspond to the face to face dimension of the butterfly valve. If the flange gab
is too small, there is risk of damaging the seat or body surface of the butterfly valve. If the opening is too large, it can
cause leaking.
Fig.4
www.coreline.dk
4/8
Fig.6 Fig.7
Flow direction Flow direction
Service and medium factor - Actuator Sizing
OBS: Butterfly valve torque is 100% by 0° to 6° angle and 33% from 7° to 90° angle.
* Valve is completely closed and opened 2 times a day minimum.
** Valve is completely closed and opened only one time per week or longer.
Having a long period without maneuvering the valve, will increase the breakaway torque.
Service factor [SF] Multiply by Medium factor [MF] Multiply by Medium factor [MF] Multiply by
ON/OFF operation 1.15 Lubricating liquid/gas 0.9 For dry service (Dry gas/air) 1.25
Modulating operation 1.25 Viscous Liquids, Molasses 1.3 Dirty air slurry, natural gas, dirty slurry 1.5-1.8
*) 2 cycle/day “NC” 1.15 Degreasing liquid 1.25 Lime water, chlorin gas,oxygen, powder 1.5-1.8
**) 1 cycle/week “NC” 1.5 Saturated steam 1.2 Hydrodynamic torque NA

Installation-Operation-Maintenance Manual
When the valve is carefully installed, the angle of the valve disc shall be within the face to face dimension (See Fig.8).
Check that the flange covers the area of the seat and the valve is in line with the pipes. Then tighten the bolt on the
flange by hand (Fig.8). Carefully open and close the valve to check that the disc centralizes and the disc does not touch
the flange. With the disc in the open position, tighten crosswise with a wrench (See Fig.9 + Fig.10).
After the installation of the valve, enough space must be reserved around the valve, so that there is enough operation
space during the inspection and maintenance.
Important: Fig.224 Lug butterfly valve installation
The valve has vulcanized seat on back up-ring. This gives many advantages, but the seat is floating in the body. For
Fig.223 Wafer version, the valve will be automatically centered, but Fig.224 Lug butterfly valve must be mounted
according to below description.
Follow Fig.11 about procedures to fasten flange bolts for Fig.224 butterfly valve. The valve will be in right position and
be tight in general afterwards(See Fig.12). Due to a Coreline patent, our Fig.224 Lug butterfly valve can be used as end
of pipe valve. Ensure that the flow arrow direction on valve mounting flange is in accordance with the flow direction of
medium.
It is important to follow procedures showing in Fig.11, otherwise there might be problem as showed in Fig.13.
After the valve is aligned with the pipeline, then gently tighten the bolts, and finally tighten them in a staggered order as
showed in Fig.10, taken 8 bolts as an example. Correct tightening can avoid uneven valve pressing force, prevent
leakage, and also help to avoid flange damage.
Fasteners used during the installation should comply with the laws, regulations and standards of the relevant countries.
Those which do not meet the requirements of the relevant regulations are strictly prohibited to use for the installation.
When tightening the flange bolts and nuts, a reasonable torque should be used according to the relevant regulations.
The following table lists the torque values for reference.
Fig.8
Fig.12 Fig.13
Fig.9
www.coreline.dk
5/8
Fig.10
1
2
3 4
5
6
7
8
Fig.11
Arrow marking on
mounting flange
Firstly fasten flange
bolts on this side.
Secondly fasten flange
bolts on this side.
Flow direction Flow direction

Installation-Operation-Maintenance Manual
After installation
Ensure that the pipeline will not bent due to weight or other force. The pipeline shall not generate pipeline stress and
transmit pipeline stress to the valve.
The valve installation, including accessories (handle, gearbox, actuator etc.), cannot be used to withstand external
forces, for instance as support point or lifting devices.
After the valve is installed, it should be able to open and close smoothly. There should be no jamming during the valve
switching process.
The valve opens when the valve shaft rotates counterclockwise, and closes when it rotates clockwise.
Before commissioning the system, the pipeline and the valve should be subjected to a hydrostatic test to check whether
there is leakage. The system can be commissioned only after the test has passed.
Additional information
The valve has a patent, with two holes underneith the mounting flange (See Fig.14). Here you can hang user's manual or
project code.
www.coreline.dk
6/8
Use and maintenance
The use of the valve shall be carried out in accordance with the instruction manual, and shall not exceed the design
parameters. The operator must go through on-the-job training to understand the basic operationprinciple of the valve.
Prevent incorrect opening and closing of valves. The operator should clearly understand the role of each valve and its
position in the process pipeline to prevent misuse. It should be ensured that the valve can be opened and closed at least
twice within a week to prevent the valve from being stuck due to long-term inactivity. After the valve has been installed,
welding and other operations on the pipeline are not allowed (Fig.15).
Valves should be inspected regularly, at least every three months, or in accordance with the corresponding laws and
regulations, or on-site process conditions to set the frequency of maintenance. Regularly check the valve connections for
looseness and tighten in time. Check whether the valve leaks or malfunctions. If leaks or malfunctions occur, the valves
and pipelines should be repaired in time on the premise of ensuring safety.
If there is an actuator, attention should be paid to the actuator and its connecting mechanism during valve maintenance.
Maintenance should be carried out according to the instruction manual of the actuator.
4.6 5.6 6.8 8.8 10.9 12.9
240 300 480 640 900 1080
6 4-5 5-7 7-9 9-12 13-16 16-21
8 10-12 12-15 17-23 22-30 30-36 38-51
10 20-25 25-32 33-45 45-59 65-78 75-100
12 36-45 45-55 58-78 78-104 110-130 131-175
14 55-70 70-90 93-124 124-165 180-201 209-278
16 90-110 110-140 145-193 193-257 280-330 326-434
18 120-150 150-190 199-264 264-354 380-450 448-597
20 170-210 210-270 282-376 376-502 540-650 635-847
22 230-290 290-350 374-512 512-683 740-880 864-1152
24 300-377 370-450 488-650 651-868 940-1120 1098-1464
27 450-530 550-700 714-952 952-1269 1400-1650 1606-2142
30 540-680 680-850 969-1293 1293-1723 1700-2000 2181-2908
33 670-880 825-1100 1319-1759 1759-2345 2473-3298 2968-3958
36 900-1100 1120-1400 1694-2259 2259-3012 2800-3350 3812-5082
39 928-1237 1160-1546 1559-2079 2923-3898 4111-5481 4933-6577
Bolt strength grade
Yield Strength(N/mm2)
Tightening torque
(N·M)
Nominal Diameter
of bolt (mm)
Fig.14
Fix point -
for tag No. etc.
Fig.15

Installation-Operation-Maintenance Manual
Material part list of the valve
www.coreline.dk
7/8
DN40-DN300 DN350-DN2000
13 13
6
4
10
7
1
9
3
2
9
5
11
14
15
6
4
10
7
1
9
3
2
9
85
11
12
No. Part name Material Specification No. Part name Material
1 Body Ductile iron EN1563 JS1030 SS420
ASTM A351 CF8 SS431
ASTM A351 CF8M 17-4PH SS
ASTM A351 CF3M SS304
2507 SS316
1.4462 7 Body bearing RPTFE with graphite
1.4529 8 Disc bearing Rainforced nylon
1.4539 9 O ring Same as seat
Hastelloy 10 Weather seal NBR
Aluminium bronze C95800 11 Anti-dust seal NBR
Ductile iron Rilsan, Halar coated 12 Plug Steel galvanized
NBR (Eq. Nitrile) -15℃~+85℃SS304
X-NBR
1)
-15
℃
~+85
℃SS316
NBR-DVGW
2)
-15℃~+60℃14 Bottom cover Same as body
EPDM-H -20℃~+125℃SS304
EPDM-FDA (white)
-20
℃
~+85
℃SS316
EPDM-FDA (black)
-20
℃
~+125
℃
FPM (Eq. FKM, Viton) -15℃~+150℃
FPM-B (Eq. FEPM)
3)
-15℃~+150℃
PTFE
-15
℃
~+150
℃
4)
Seat3
Disc
Stem4/5
Alloy steel
Stainless steel
2
Preventing plate6
13 Screw
Bolt15
Notes:
1) Well -resistant NBR. 2) German gas certificate. 3) Steam resistant FPM. 4) Depending on the backup rubber material,
available with EPDM and FPM backup.
The above temperature range for the valve seats are provided as reference for general working conditions. Please note that the actual
applications may vary due to the different media, pressure etc. in the pipeline. Contact Coreline in advance for technique supports.

Installation-Operation-Maintenance Manual
Troubleshooting
The relevant safety regulations must be observed when troubleshooting.
General warning
The installation, use and maintenance of the valve must comply with relevant laws and regulations. The installation, use
and maintenance of the valve must be carried out under the environment of safety regulations, and the pipeline engineer
must meet the production process and use requirements on site when selecting the valve. Before purchasing the valve,
the purchaser is obliged to clearly inform the valve manufacturer of the working conditions of the valve. If the user fails to
install, maintain and use the valve according to the regulations and requirements, the user shall bear the consequences.
Problem Possible cause Corrective measures
No flow Flange dust caps were not removed Remove dust caps
Valve not completely open Open valve completely
Piping system clogged Check piping system
Replace valve
Consult supplier
Power failure Check power supply.
Wrong direction of rotation Turn in correct direction (anti-clockwise for opening)
Fouling of the disc and/or seat Remove fouling on the disc and/or seat
Valve not properly closed Close valve properly or readjust limit switch/stop screw
Seat damaged by foreign particles Replace valve or seat
Medium contaminated Clean valve and install dirt screen
Valve with locking device can not be opened Locking device tightened Slacken locking device
Little flow
Valve is impossible or difficult to open or close
Service conditions (e.g. medium, temperature) outside
permissible limits.
Valve leaking
Chart for medium resistance
Liner Suitable for Unsuitable for
EPDM
Water, steam, alcohol, glycol, caustic soda, ozone,food products, glycerine,
milk, oxygen, air, saturated salt, iron chloride, gelatine, dry hydrogen
sulphide, potassium chloride, sodium, magnesium chloride
Mineral oil, chlorine compounds, ketones, acetyl, chloride, asphalt,
bromine, butane, butyl, petrol, diesel oil, acid, fish oil, freon, chlorine,
natural gas, exhaust gas, nitric acid
NBR
Mineral oil, grease, air, seawater, gas, boric acid, aluminium chloride,
ammonia gas, citric acid, diesel oil, fish oil, petrol, gelatine, glycerine,
magnesium chloride, lactic acid, linseed oil, natural gas
Ozone, acetone, aniline, chlorine dioxide, chromic acid, phenol, ethyl
acetate, freon 21+22+23, hot nitric acid, styrene, hydrogen sulphide,
isopropyl acetate, oxygen, sulphuric acid
NATURAL
RUBBER
Abrasive medium, aluminium chloride, sugar beet fluid, boric acid, potassium
chloride, citric acid, magnesium chloride, ferritic nitrate, formic acid,
gelatine, sugar, glycerine, lactic acid, nitrogen
Steam, aniline, asphalt, butadiene, diesel oil, ethane, ethyl acetate,
hydraulic oil, hydrochloric acid, linseed oil, methane, mineral oil, oxygen,
styrene, soyabean oil, turpentine
HYPALON Mineral, organic and inorganic chemicals, air, oxygen, fish oil, glycerine,
citric acid, ozone, sodium solphate
Ammonia, diesel oil, grease, ketone, methyl, phenol, propyl, bromine,
nitric acid, tar, urea, varnish, lectine
SILICONE Food products, ammonia gas, barium, boric acid, potassium, bisulphite,
citric acid, copper cyanide, glycerine, nitrogen, lactic acid
Steam and hot water (max. 100º C), asphalt, diesel oil, ethane, freon,
ethyl chloride, methane, nitric acid, olive oil, propane, turpentine
FPM
FPM-B
Oil, mineral acid, grease, phosphorus, tannic acid,
gelatine, glycol, oxygen, slaked lime, carbon acid,
natural gas, pulp, salt, sugar, sulphur
Acid, alkali, amine hot water, steam Gasoline, naphtha, hydrocarbon solvent, chlorine solvent
PTFE Almost available for all medium applications None
Hot water, steam, ketone, ammonia gas, acetone,
formaldehyde, cellulose acetate, freon, urea,
ethanoic acid, methyl
www.coreline.dk
8/8
2020-08-28 Coreline Valve Co., Ltd.
CORELINE VALVE CO., LTD.
Add: No.210 Xinyuan Road, Ehu Industrial Park, 214116 Wuxi, China
Phone: +86 510 8852 5336
The contents of this catalogue are confidential
and proprietary to Coreline, we reserve the right
to change the specifications without any notice.
This manual suits for next models
1
Table of contents
Other Coreline Control Unit manuals
Popular Control Unit manuals by other brands
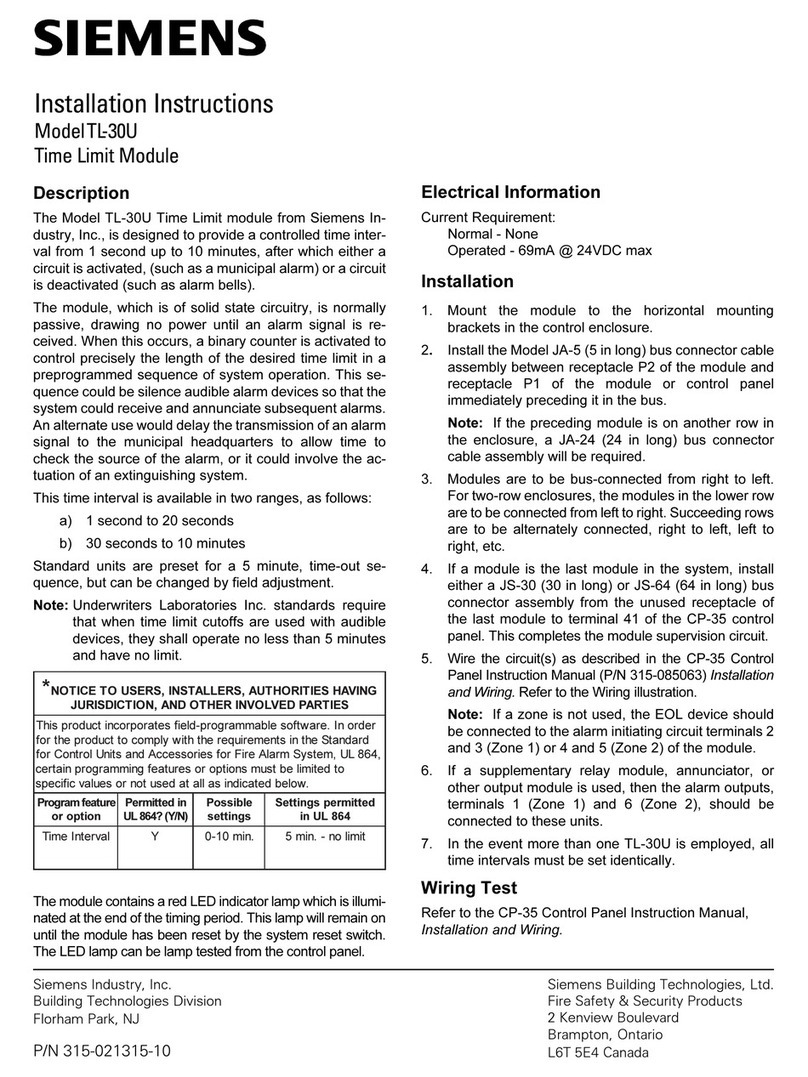
Siemens
Siemens TL-30U installation instructions
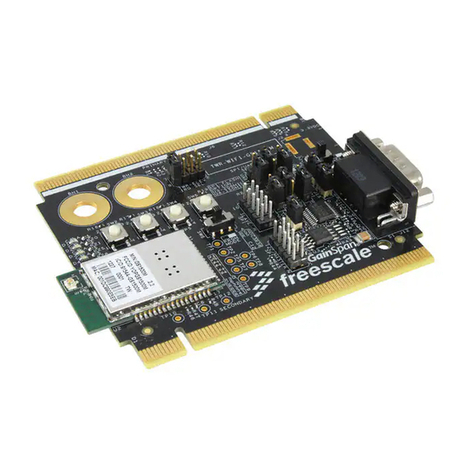
NXP Semiconductors
NXP Semiconductors Freescale TWR-WIFI-GS1500M Lab Guide
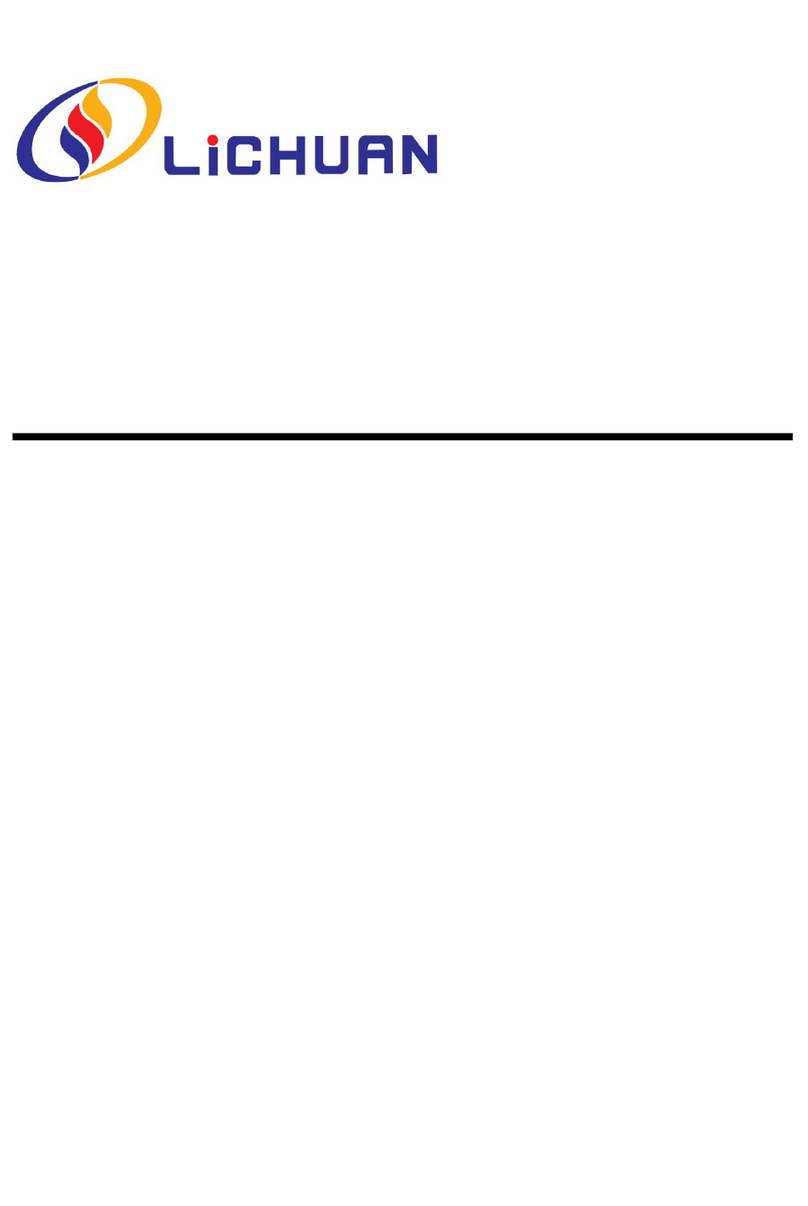
LICHUAN
LICHUAN LCDA2263C user manual
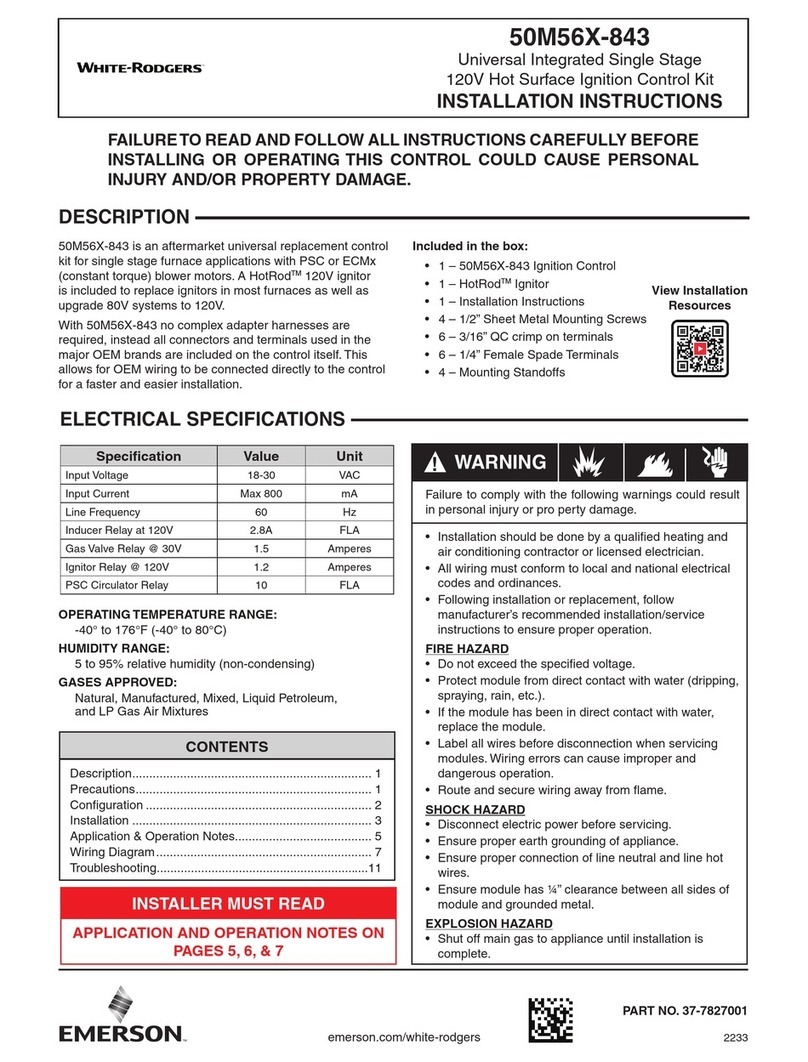
White Rodgers
White Rodgers 50M56X-843 installation instructions
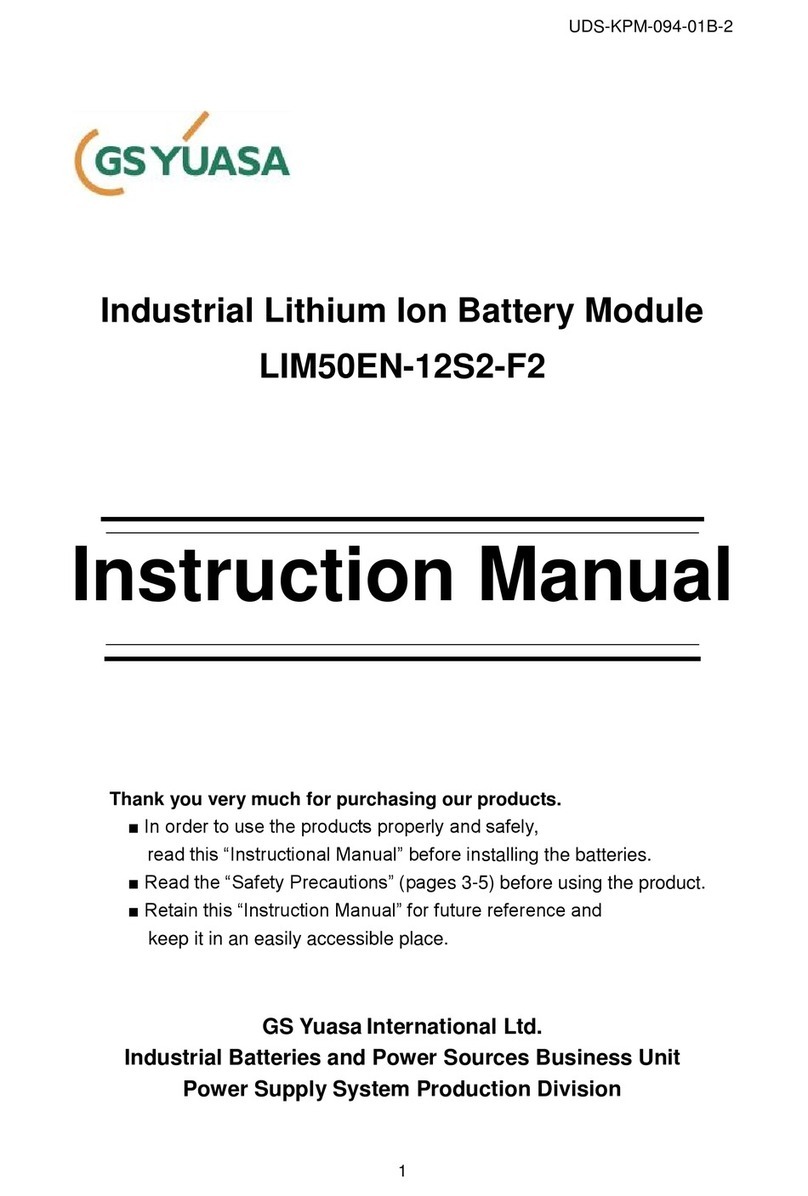
gs yuasa
gs yuasa LIM50EN-12S2-F2 instruction manual
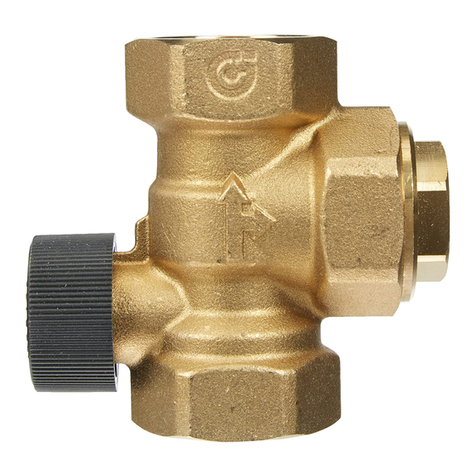
CALEFFI
CALEFFI 510 Series quick start guide

System Sensor
System Sensor M902M Installation and maintenance instructions
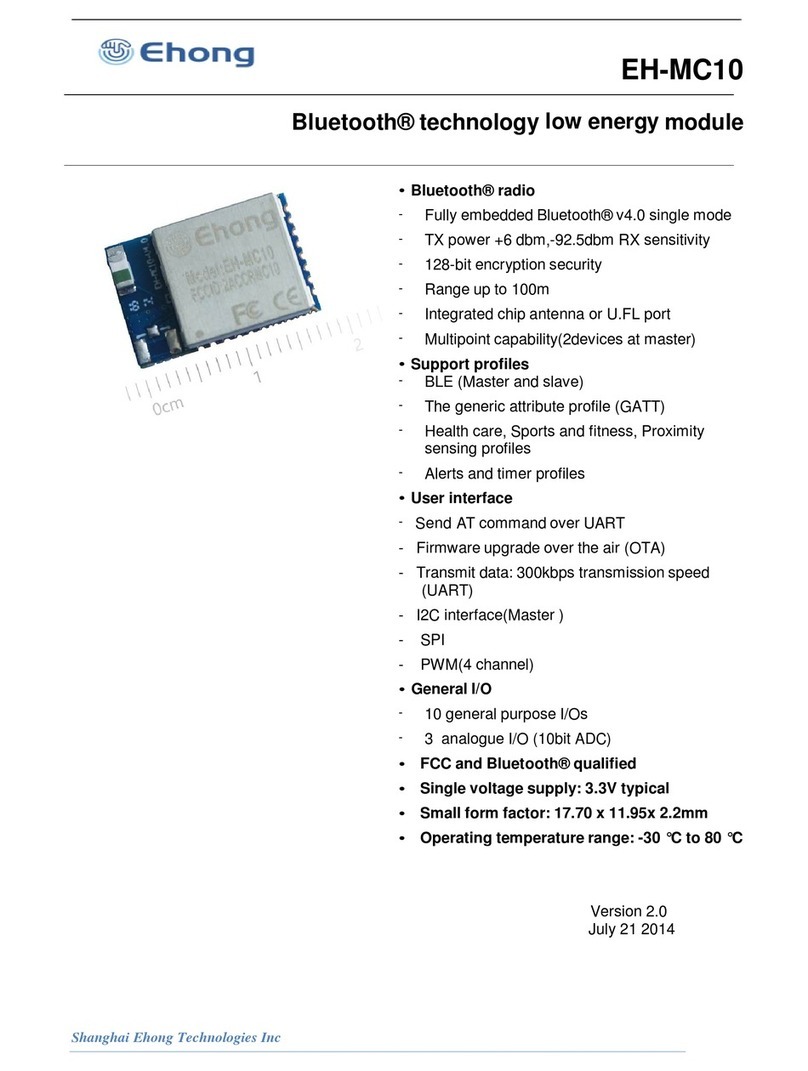
Ehong
Ehong EH-MC10 manual

Gemu
Gemu 650 manual
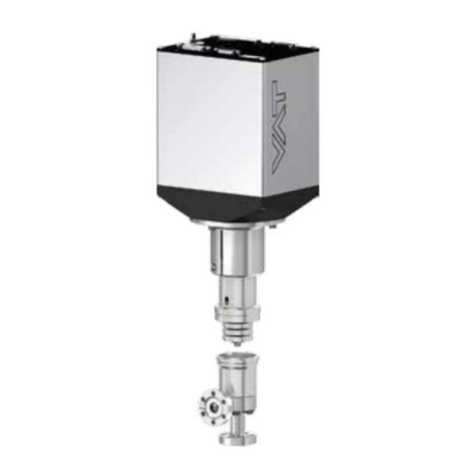
VAT
VAT 590 Series Installation, operating, & maintenance instructions

CIAT
CIAT XtraConnect 2 Installation, Operation, Commissioning, Maintenance
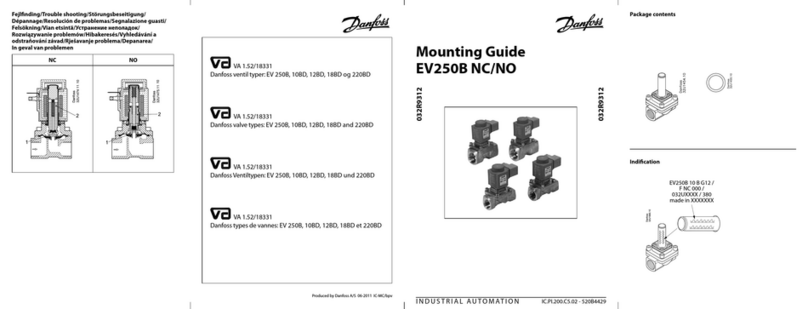
Danfoss
Danfoss EV250B NC Mounting guide