CTR Electronics PDP User manual

PDP User’s Guide
3/28/2018
Cross The Road Electronics Page 1 3/28/2018
Power Distribution Panel
User’s Guide
Revision 1.6
Cross The Road Electronics
www.crosstheroadelectronics.com

PDP User’s Guide
3/28/2018
Cross The Road Electronics Page 2 3/28/2018
Table of Contents
1. Power Distribution Panel at a Glance..................................................................................... 4
1.1. Connection Specifications ............................................................................................... 5
1.2. Electrical Specifications................................................................................................... 6
1.3. Mechanical Specifications ............................................................................................... 6
1.4. Communication Specifications......................................................................................... 6
2. Installing a PDP ..................................................................................................................... 7
2.1. Battery harness ............................................................................................................... 7
2.1.1. Split Washer.............................................................................................................. 8
2.2. Breakers.......................................................................................................................... 9
2.2.1. Snap Action 40 Amp Breaker.................................................................................... 9
2.2.2. Snap Action 20/30 Amp Breaker..............................................................................10
2.3. Weidmuller Connectors ..................................................................................................11
2.3.1. roboRIO, PCM, VRM................................................................................................12
2.3.2. CAN bus ..................................................................................................................13
2.4. Blade Fuse.....................................................................................................................14
2.4.1. Blade Fuse Replacements.......................................................................................15
2.5. WAGO OperatingTool.....................................................................................................15
3. LED States............................................................................................................................16
4. Functional Limitations (software)...........................................................................................17
4.1. Firmware <1.40: If Robot Is Enabled/Disabled/Enabled Quickly, FRC robot may
momentarily disable...............................................................................................................17
4.2. Firmware <1.40: Power and Energy ...............................................................................17
4.3. LabVIEW: Energy signal is not scaled to Joules.............................................................17
4.4. C++/Java: Energy signal is in Millijoules.........................................................................17
4.5. Firmware <1.37: Current may read ~2A when there is no current...................................17
4.6. FRC2016 roboRIO: CAN Device does not appear in web page diagnostics. ..................18
4.7. FRC 2018: CTRE CAN Receive Timeout........................................................................19
5. Troubleshooting Tips and Common Questions......................................................................20
5.1. What is the threshold for Vbat fault?...............................................................................20
5.2. Are sticky faults cleared during/after a firmware field-update?........................................20
5.3. Do I need to firmware-update? Where are the files?......................................................20

PDP User’s Guide
3/28/2018
Cross The Road Electronics Page 3 3/28/2018
TO OUR VALUED CUSTOMERS
It is our intention to provide our valued customers with the best documentation
possible to ensure successful use of your CTRE products. To this end, we will
continue to improve our publications, examples, and support to better suit your
needs.
If you have any questions or comments regarding this document, or any CTRE
product, please contact support@crosstheroadelectronics.com
To obtain the most recent version of this document, please visit
www.ctr-electronics.com.
6. Revision History....................................................................................................................21

PDP User’s Guide
3/28/2018
Cross The Road Electronics Page 4 3/28/2018
1. Power Distribution Panel at a Glance

PDP User’s Guide
3/28/2018
Cross The Road Electronics Page 5 3/28/2018
1.1. Connection Specifications
●Battery
○Bushings Lugs x 2
○Thread M6x1 (10mm Length)
●Power Channels (All Channels provide battery power)
○WAGO Connectors
■8 Red Channels 4-11
●30 Amp
■8 Red Channels 0-3, 12-15
●40 Amp
■Black terminals are common
○6 Position Weidmuller Connector
■PCM, VRM Supply
●20 Amp fused (ATM blade mini fuse)
■roboRIO Supply
●10 Amp fused (ATM blade mini fuse)
■Max: 16 AWG
■Min: 24 AWG
See Section 2.3. Weidmuller Connectors for wire insert instructions.
●CAN
○4 Position Weidmueller Connector
■Yellow CAN High x 2
■Green CAN Low x 2

PDP User’s Guide
3/28/2018
Cross The Road Electronics Page 6 3/28/2018
1.2. Electrical Specifications
Input Voltage (Vbat)
5.5-16 V
Absolute Max Input Voltage(1)
0 - 20 V
Output Voltage
●Channels 0-3, 12-15
Vbat - 40 A
●Channels 4-11
Vbat - 20 or 30 A
●VRM, PCM Weidmuller
Vbat - 20 A fused
●Controller Weidmuller
Vbat - 10 A fused
Note 1: Stresses above those listed under “Absolute Maximum Ratings” may cause permanent damage to the device. This is a
stress rating only and functional operation of the device at those or any other conditions above those indicated in the operation
listings of this specification is not implied. Exposure to maximum rating conditions for extended periods may affect device reliability.
1.3. Mechanical Specifications
Length
7.586 in.
Width
4.748 in.
Height
1.422 in.
Weight
1 lb. 5.3 oz.
1.4. Communication Specifications
Baud Rate
1 MB/s
CAN Termination
120 Ohm (jumper placed in the ON position).
None (jumper missing or placed in the OFF
position).
CAN High / Low
2 Ports

PDP User’s Guide
3/28/2018
Cross The Road Electronics Page 7 3/28/2018
2. Installing a PDP
2.1. Battery harness
●Components
○QTY 2 - M6x1 Bolts (10mm Length) Socket Head Cap Screws
○QTY 2 - 6mm Split (Lock) Washers
○Battery Cover
■QTY 2 - 6-32 (1/2” Length) Battery Cover Flat-Head Socket Cap Screw
○12 Volt Supply (Battery, Power Supply, etc...)
Warning:Do not reverse the battery voltage as this can cause permanent damage to
current sense circuitry. Additionally the FRC Control System Components that
draw power from PDP may not have reverse battery protection, and can also be
damaged in a reverse battery event.

PDP User’s Guide
3/28/2018
Cross The Road Electronics Page 8 3/28/2018
2.1.1. Split Washer
Warning:Care should be taken to ensure the split washers are installed under the
screw head. If this is not done, the robot could exhibit several forms of power/brownout
issues as the cable harness loosens over time.

PDP User’s Guide
3/28/2018
Cross The Road Electronics Page 9 3/28/2018
2.2. Breakers
2.2.1. Snap Action 40 Amp Breaker
●Channels 0-3, Channels 12-15
○40 Amp Breaker
○Limits Closest Red WAGO
○Supplies Battery Power
Warning: Inductive loads (motor, compressor) must have a power management device
(motor controller, PCM, spike) between itself and the PDP. No inductive loads (motor,
compressor) may be directly connected to the PDP channels as this can damage current
sense circuitry.

PDP User’s Guide
3/28/2018
Cross The Road Electronics Page 10 3/28/2018
2.2.2. Snap Action 20/30 Amp Breaker
●Channels 4-11
○30 or 20 Amp Breaker
○Limits Closest Red WAGO
○Supplies Battery Power
Warning: Inductive loads (motor, compressor) must have a power management device
(motor controller, PCM, spike) between itself and the PDP. No inductive loads (motor,
compressor) may be directly connected to the PDP channels as this can damage current
sense circuitry.

PDP User’s Guide
3/28/2018
Cross The Road Electronics Page 11 3/28/2018
2.3. Weidmuller Connectors
Wire Insertion
●Disconnect PDP from Battery before adding or modifying connections
●Strip wire back ~0.375” (3/8”)
●Press and hold down connector button. Though this isn’t necessary, it ensures the
stripped wire does not deform and split into “whiskers” after excessive use. A small
screwdriver can be used to easily hold down the connector button.
●Insert wire into connector opening
●Release connector button
●Pull wire to ensure wire is locked in connector
●Confirm wire strands are not extruded
Wire Inspection
●Verify that there are no “whiskers” outside of the connector that may cause a short.
●Verify that the stripped portion of the wire is not excessive enough to cause a short.
●Tug on the wire and verify wire does not pull out. If it does then recheck gauge and/or
strip the wire back further.
Wire Removal
●Press and hold down connector button immediately above connector opening
●Pull wire to remove from connector
Limitations
●Wire should not be frayed upon insertion. Extruded wire may short to adjacent
channels.
●Wire should be no larger than 16 AWG, larger gauges will not properly fit in connector
●Wire should be no smaller than 24 AWG, smaller gauges will not lock in connector
Warning: Tug-testing wires can make the difference between a seamless match and one
filled with radio disconnects, roboRIO reboots, bad sensor data, etc… Every inserted wire
should be immediately tug-tested to ensure proper operation of the robot.
Additional video and suggestions can be found at:
http://wpilib.screenstepslive.com/s/4485/m/24166/l/144971-wiring-the-2015-frc-control-system

PDP User’s Guide
3/28/2018
Cross The Road Electronics Page 12 3/28/2018
2.3.1. roboRIO, PCM, VRM
Weidmuller Connectors are used for connecting the roboRIO, PCM, and VRM modules to
power. See Section 2.3. Weidmuller Connectors for wire insertion and removal procedures.
See Section 2.4. Blade Fuse Replacements for fuse details.

PDP User’s Guide
3/28/2018
Cross The Road Electronics Page 13 3/28/2018
2.3.2. CAN bus
Weidmuller Connectors are also used for CAN Communication. See Section 2.3. Weidmuller
Connectors for wire insertion and removal procedures. Smart Module provides termination
and may be placed at the end of CAN bus chain.
Termination Resistor Jumper
- Only place the jumper to the ON position when PDP is at the end of the CAN bus.
- ON State - Positioning the jumper closest to the inside of the PDP (shown above).
- OFF State - Positioning the jumper closest to the edge of the PDP or removing the jumper.

PDP User’s Guide
3/28/2018
Cross The Road Electronics Page 14 3/28/2018
2.4. Blade Fuse
Be sure to place the 20A fuse (yellow) on the left and the 10A fuse (red) on the right.
Warning: Also take care to ensure fuses are fully seated into the fuse holders. The fuses
should descend at least as far as the figure below (different brand fuses have different lead
lengths). It should be nearly impossible to remove the fuse with bare hands (without the use
of pliers). If this is not properly done, the robot/radio may exhibit intermittent connectivity
issues.

PDP User’s Guide
3/28/2018
Cross The Road Electronics Page 15 3/28/2018
2.4.1. Blade Fuse Replacements
Both automotive fuses are type ATM automotive blade mini fuses. Spares can be purchased at
most hardware stores (Do not purchase ATC as they will not fit).
Example replacement purchase for 10A Controller fuse
2.5. WAGO OperatingTool
A small flathead screwdriver may be used to operate the WAGO connectors. More information
(and video) can be found online at http://wpilib.screenstepslive.com.
However there is an available tool designed specifically for WAGO connectors that teams may
choose to purchase.

PDP User’s Guide
3/28/2018
Cross The Road Electronics Page 16 3/28/2018
3. LED States
The STAT and COMM LEDs are multi-color LEDs that can blink green, orange, or red.
The two LEDs are always the same color/blink pattern. The only exception to this is when the
device is in boot-loader.

PDP User’s Guide
3/28/2018
Cross The Road Electronics Page 17 3/28/2018
4. Functional Limitations (software)
Functional Limitations describe behavior that deviates from what is documented. Feature
additions and improvements are always possible thanks to the field-upgrade features of the
PDP.
4.1. Firmware <1.40: If Robot Is Enabled/Disabled/Enabled Quickly, FRC
robot may momentarily disable.
When PDP is wired to roboRIO’s CAN bus and robot enters disabled state, roboRIO typically
begins extracting logged records from PDP. However if robot is immediately enabled after
initially entering disable, the roboRIO may very briefly disable as it finishes extracting PDP logs
despite being enabled in the Driver Station.
This occasionally causes motor-drive to briefly disable once after enabling robot. Additionally
the fault count will increment in the Driver Station (lightening tab).
Issue is fixed in PDP Firmware 1.40. When PDP detects roboRIO is enabled it will abort
extraction, therefore preventing the problem condition from occurring.
4.2. Firmware <1.40: Power and Energy
Power and energy signals were not computed correctly in firmware versions earlier than 1.40.
Updating to 1.40 will ensure Power and Energy signals are updated correctly.
4.3. LabVIEW: Energy signal is not scaled to Joules.
The Energy signal in LabVIEW is computed in engineering units where each unit is 0.020
Joules. Multiply the signal value by 0.020 to scale to Joules.
4.4. C++/Java: Energy signal is in Millijoules.
The Energy signal in C++/Java is computed in units where each unit is 0.001 Joules. Multiply
the signal value by 0.001 to scale to Joules. If using this signal for robot-processing, be sure to
check for the fix whenever updating C++/Java libraries.
4.5. Firmware <1.37: Current may read ~2A when there is no current.
The current sense circuitry has biasing (similar to a gyro). Firmware 1.37 and on will zero the
output so that 0A is read when there is no load.

PDP User’s Guide
3/28/2018
Cross The Road Electronics Page 18 3/28/2018
4.6. FRC2016 roboRIO: CAN Device does not appear in web page
diagnostics.
Under specific conditions, a CAN device may no longer appear in the left tree view in the
roboRIO web-based configuration page. For this to occur the following criteria must be met.
•FRC_roboRIO_2016_v19.zip is imaged in the roboRIO.
•The missing device ID must be greater than 20.
•All other device IDs must be either: greater than the missing ID, or less than missing ID
minus 50.
If there is a CAN device which has an ID that meets this criteria, and therefore is no longer
appearing in the web-page, the user can apply the following procedure. This procedure will
force the device to appear, and will allow the user to change the device ID so as to work around
this limitation. The user can either…
•Power cycle just the missing-ID-device and manually refresh the browser until device
appears…
•…or alternatively disconnect CAN bus between the robot controller and the missing-ID-
device. Then power-cycle or reboot the roboRIO. Navigate to the roboRIO’s webpage
and wait until page fully renders. Now reconnect CAN bus and manually-refresh the
browser until device appears.
After forcing the missing device to appear, modify its device ID so that this limitation doesn’t
occur again. To work around this limitation, either…
•use device IDs less than 20 or …
•…avoid gaps in IDs that exceed 50 and ensure there is (at least) one device ID less than
20.
This limitation will not prevent the robot API from controlling/monitoring CTRE CAN Devices.
Note that if this functional limitation is in effect, the PDP LEDs will still transition from slow-green
blink to fast-green blink when robot controller is enabled.

PDP User’s Guide
3/28/2018
Cross The Road Electronics Page 19 3/28/2018
4.7. FRC 2018: ERROR 1 CTRE CAN Receive Timeout
The CAN Receive Timeout occurs when the requested data has not been received within the
timeout. This is usually caused when the PDP is not connected to the CAN bus.
However, with the 2018 version of WPILib, having a PDP object in robot code can result in a
CTRE CAN Timeout error being reported in the console/DriverStation.
This seems to be a result of automatic LiveWindow behavior with the PDP and can be fixed by
disabling LiveWindow telemetry.
LiveWindow can either be disabled for the PDP object…
LiveWindow.disableTelemetry(_pdp);
… or by disabling all LiveWindow telemetry:
LiveWindow.disableAllTelemetry();
It is also possible to get CTRE CAN Timeout errors if PDP data is requested in multiple threads.
It is recommended to keep all PDP functions within a single thread to prevent these timeout
errors.

PDP User’s Guide
3/28/2018
Cross The Road Electronics Page 20 3/28/2018
5. Troubleshooting Tips and Common Questions
5.1. What is the threshold for Vbat fault?
PDP will assert the battery fault when battery voltage drops below 6.5V. This only causes the
status LED to slowly blink orange when robot-disabled. No robot functionality is affected.
Battery voltage is ignored the first 500ms since power-up to ensure erroneous trips are not
detected (battery connect, closing 200A breaker).
5.2. Are sticky faults cleared during/after a firmware field-update?
No. Sticky faults will persist during and after a field-update. They do not affect robot
functionality and only exist for diagnostic purposes. See FRC WPILib Screensteps
(http://wpilib.screenstepslive.com) for steps to detect and clear faults (“Updating and
Configuring Pneumatics Control Module and Power Distribution Panel“).
At the time of writing this link can be used:
http://wpilib.screenstepslive.com/s/4485/m/24166/l/216217-updating-and-configuring-
pneumatics-control-module-and-power-distribution-panel
5.3. Do I need to firmware-update? Where are the files?
The ship firmware of the PDP is not FRC legal. The latest CRF can be found at
http://www.crosstheroadelectronics.com/control_system.html. Consult FRC game rules for what
is required. Consult Section 4 for software details.
Additionally the firmware file can be found after updating/installing the driver station software on
your hard drive.
Instructions on how to field-upgrade the PDP are available at FRC WPILib Screensteps
(http://wpilib.screenstepslive.com).
At the time of writing this link can be used:
http://wpilib.screenstepslive.com/s/4485/m/24166/l/216217-updating-and-configuring-
pneumatics-control-module-and-power-distribution-panel
Table of contents
Other CTR Electronics Power Distribution Unit manuals
Popular Power Distribution Unit manuals by other brands
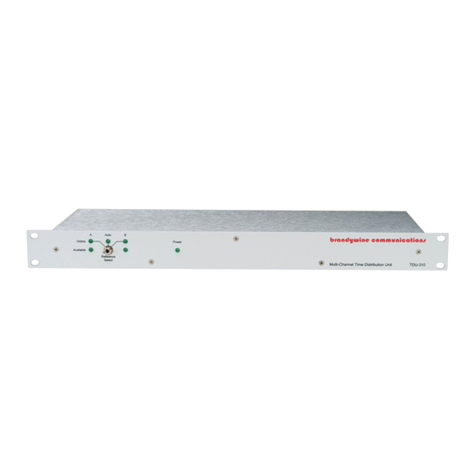
Brandywine
Brandywine TDU-310 user guide
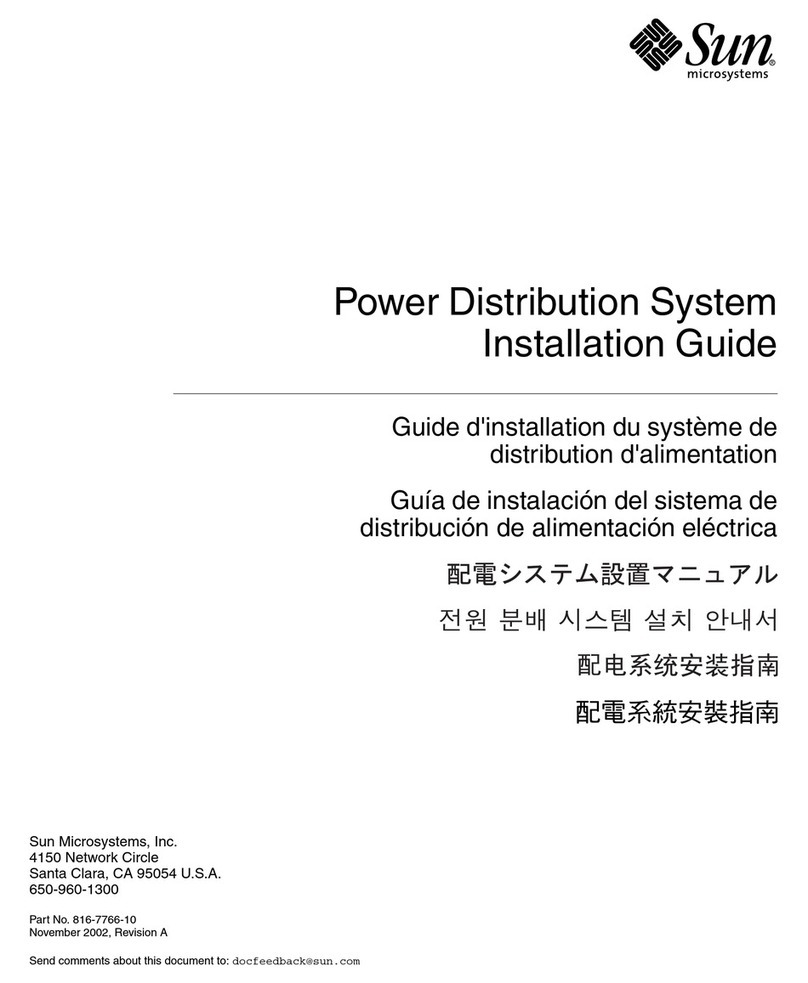
Sun Microsystems
Sun Microsystems 816-7766-10 installation guide

Eaton
Eaton Crouse-hinds series Installation & maintenance information
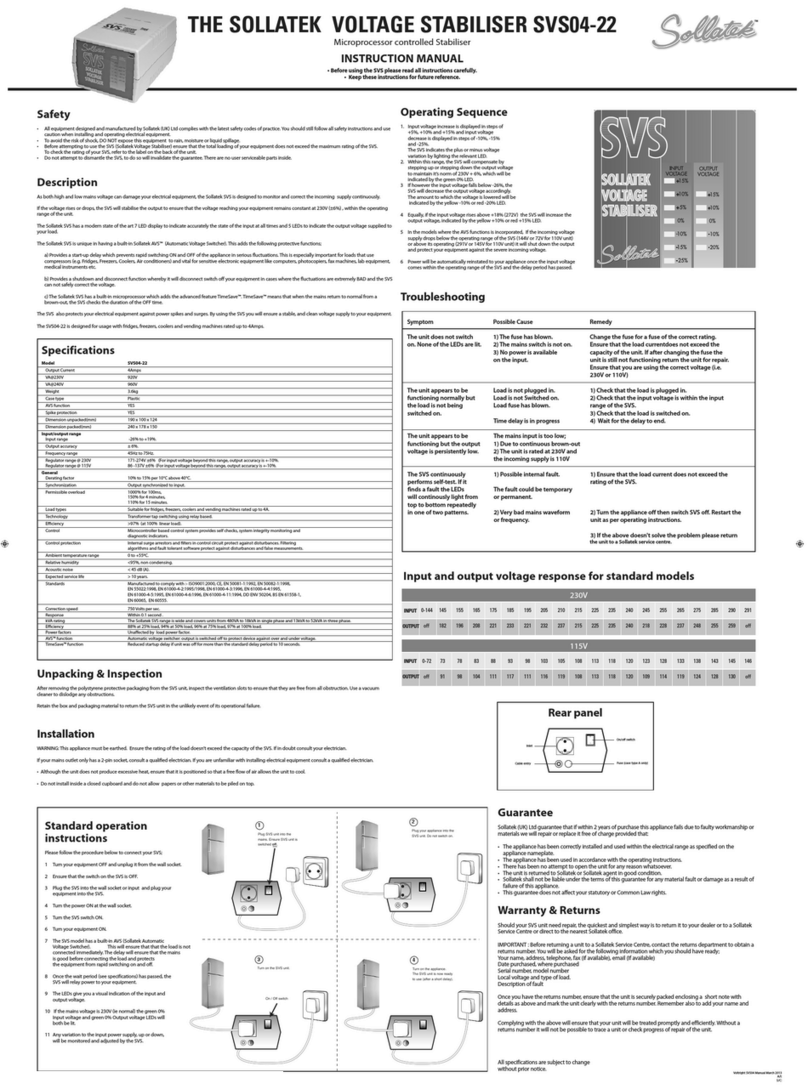
Sollatek
Sollatek SVS04-22 instruction manual
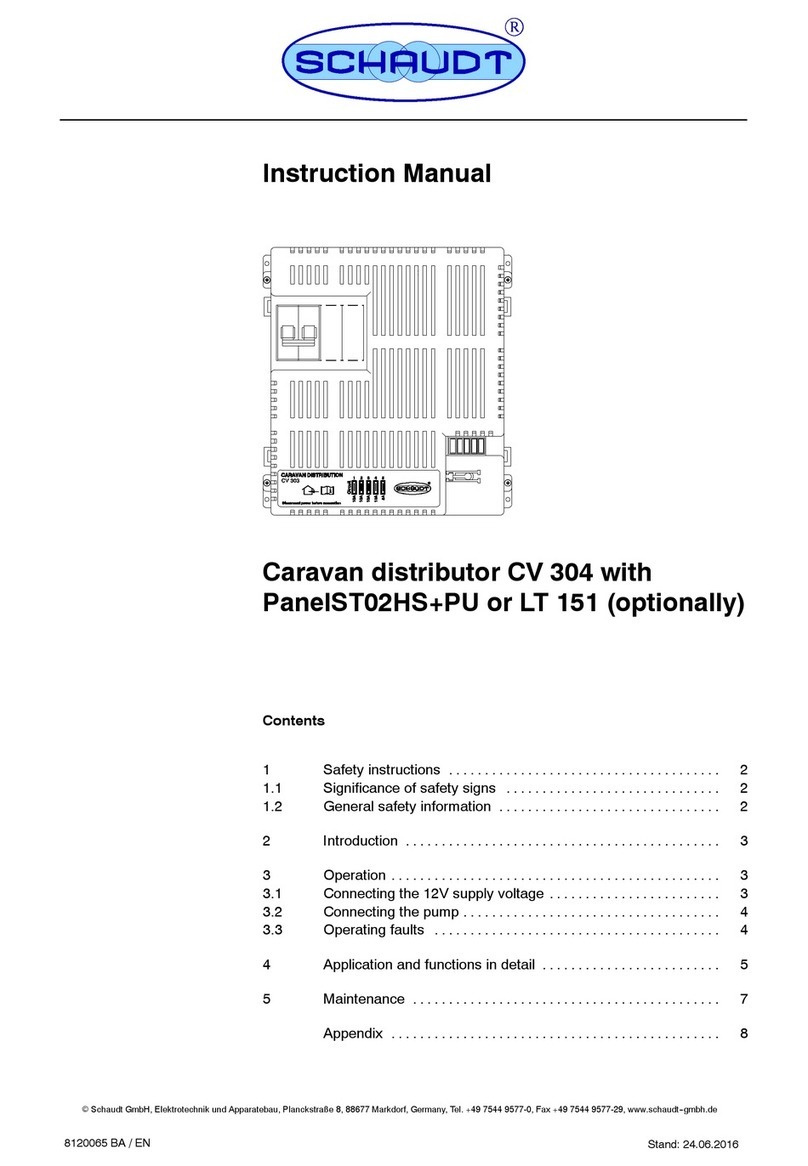
Schaudt
Schaudt CV 304 instruction manual

aldes
aldes InspirAIR Home Series Installation and maintenance guide