Dalsa Piranha4 Series User manual

This document does not contain information whose export/transfer/disclosure
is restricted by the Canadian Export Control regulation.
Notice
© 2012-2021 Teledyne Digital Imaging, Inc.
All information provided in this manual is believed to be accurate and reliable. No responsibility is
assumed by Teledyne DALSA for its use. Teledyne DALSA reserves the right to make changes to this
information without notice. Reproduction of this manual in whole or in part, by any means, is prohibited
without prior permission having been obtained from Teledyne DALSA.
Microsoft and Windows are registered trademarks of Microsoft Corporation in the United States and
other countries. Windows, Windows 7, Windows 8 and Windows 10 are trademarks of Microsoft
Corporation.
All other trademarks or intellectual property mentioned herein belong to their respective owners.
Document date: September 30, 2021
Document number: 03-032-20133-05
About Teledyne DALSA
Teledyne DALSA, a business unit of Teledyne Digital Imaging Inc., is an international high-performance
semiconductor and electronics company that designs, develops, manufactures, and markets digital
imaging products and solutions, in addition to providing wafer foundry services.
Teledyne DALSA Digital Imaging offers the widest range of machine vision components in the world.
From industry-leading image sensors through powerful and sophisticated cameras, frame grabbers,
vision processors and software to easy-to-use vision appliances and custom vision modules.

Contents
Camera User’s Manual ______________________________________________________________________1
1. System Precautions and Cleaning__________________________________________________________5
2. The Piranha4 Camera _____________________________________________________________________8
Camera Highlights ............................................................................................. 8
Camera Performance Specifications............................................................... 9
Certifications and Compliance ........................................................................ 10
Supported Industry Standards........................................................................... 10
Responsivity........................................................................................................ 11
FPN Characteristics with Temperature ............................................................. 12
Mechanicals ...................................................................................................... 13
3. Software and Hardware Setup _____________________________________________________________15
Setup Steps: Overview....................................................................................... 15
Step 1. Install and configure the frame grabber, graphics card and GUI ..... 16
Step 2. Connect Data, Trigger, and Power Cables ......................................... 17
Step 3. Establish Communication with the Camera........................................ 23
Using Sapera CamExpert with Piranha4 Cameras .......................................... 26
4. Camera Operation________________________________________________________________________29
Factory Settings.................................................................................................. 29
Check Camera and Sensor Information.......................................................... 29
Verify Temperature and Voltage...................................................................... 30
Saving and Restoring Camera Settings............................................................ 30
Camera Link Configuration............................................................................... 32
Area Mode......................................................................................................... 33
TDI Stages ........................................................................................................... 35
Trigger Modes .................................................................................................... 37
Exposure Controls .............................................................................................. 37
Exposure Modes in Detail .................................................................................. 38
Set Line Rate ...................................................................................................... 40
Set Exposure Time .............................................................................................. 44
Control Gain and Black Level........................................................................... 44
Set Image Size.................................................................................................... 44
Set Baud Rate .................................................................................................... 45
Pixel Format........................................................................................................ 45
Camera Direction Control................................................................................. 46
Pixel Readout Direction (Mirroring Mode)........................................................ 48
Binning................................................................................................................ 48
Resetting the Camera....................................................................................... 49
Calibrating the Camera.................................................................................... 49
Appendix A: GenICam Commands __________________________________________________________52

Camera Information Category......................................................................... 52
Camera Control Category ............................................................................... 58
Flat Field Category ............................................................................................ 66
Image Format Control Category...................................................................... 68
Binning................................................................................................................ 71
Area of Interest (AOI) Setup.............................................................................. 71
Instructions on using the camera scan direction to control camera
parameters......................................................................................................... 74
Transport Layer Control Category .................................................................... 77
Acquisition and Transfer Control Category...................................................... 79
Serial Port Control Category ............................................................................. 80
File Access Control Category ........................................................................... 81
Appendix B: ASCII Commands _______________________________________________________________87
Appendix C: Error and Warning Messages ____________________________________________________102
Appendix D: Quick Setup and Image Acquisition______________________________________________104
Declarations of Conformity __________________________________________________________________107
Revision History ______________________________________________________________________________108
Contact Information_________________________________________________________________________109
Sales Information................................................................................................ 109
Technical Support.............................................................................................. 109

1. System Precautions and
Cleaning
Precautions
Read these precautions and this manual carefully before using the camera.
Confirm that the camera’s packaging is undamaged before opening it. If the packaging is damaged please
contact the related logistics personnel.
Do not open the housing of the camera. The warranty is voided if the housing is opened.
Keep the camera housing temperature in a range of 0 °C to 50 °C during operation.
Do not operate the camera in the vicinity of strong electromagnetic fields. In addition, avoid electrostatic
charging, violent vibration, and excess moisture.
To clean the device, avoid electrostatic charging by using a dry, clean absorbent cotton cloth dampened
with a small quantity of pure alcohol. Do not use methylated alcohol. To clean the surface of the camera
housing, use a soft, dry cloth. To remove severe stains use a soft cloth dampened with a small quantity of
neutral detergent and then wipe dry. Do not use volatile solvents such as benzene and thinners, as they
can damage the surface finish. Further cleaning instructions are below.
Though this camera supports hot plugging, it is recommended that you power down and disconnect
power to the camera before you add or replace system components.
Electrostatic Discharge and the CMOS Sensor
Image sensors and the camera bodies housing are susceptible to damage from electrostatic discharge
(ESD). Electrostatic charge introduced to the sensor window surface can induce charge buildup on the
underside of the window that cannot be readily dissipated by the dry nitrogen gas in the sensor package
cavity. The charge normally dissipates within 24 hours and the sensor returns to normal operation.
Protecting Against Dust, Oil, and Scratches
The sensor window is part of the optical path and should be handled like other optical components, with
extreme care. Dust can obscure pixels, producing dark patches on the sensor response. Dust is most
visible when the illumination is collimated. The dark patches shift position as the angle of illumination
changes. Dust is normally not visible when the sensor is positioned at the exit port of an integrating
sphere, where the illumination is diffuse. Dust can normally be removed by blowing the window surface
using an ionized air gun. Oil is usually introduced during handling. Touching the surface of the window
barehanded will leave oily residues. Using rubber fingercots and rubber gloves can prevent
contamination. However, the friction between rubber and the window may produce electrostatic charge

that may damage the sensor. To avoid ESD damage and to avoid introducing oily residues, avoid
touching the sensor. Scratches diffract incident illumination. When exposed to uniform illumination, a
sensor with a scratched window will normally have brighter pixels adjacent to darker pixels. The location
of these pixels will change with the angle of illumination.
An important note on window blemishes:
When flat field correction is performed, window cleanliness is paramount. The figure below shows an
example of what can happen if a blemish is present on the sensor window when flat field correction is
performed. The blemish will cast a shadow on the wafer. FFC will compensate for this shadow by
increasing the gain. Essentially FFC will create a white spot to compensate for the dark spot (shadow). As
long as the angle of the incident light remains unchanged then FFC works well. However when the angle
of incidence changes significantly (i.e. when a lens is added) then the shadow will shift and FFC will
makes things worse by not correcting the new shadow (dark spot) and overcorrecting where the shadow
used to be (white spot). While the dark spot can be potentially cleaned, the white spot is an FFC artifact
that can only be corrected by another FFC calibration.
Cleaning the Sensor Window
Recommended Equipment
•Glass cleaning station with microscope within clean room.
•3M ionized air gun 980
(http://solutions.3mcanada.ca/wps/portal/3M/en_CA/WW2/Country/)
•Ionized air flood system, foot operated.
•Swab (HUBY-340CA-003)
(http://www.cleancross.net/english/products/threeinch_standard.html)
•Single drop bottle (FD-2-ESD)
•E2 (Eclipse optic cleaning system (www.photosol.com)
Procedure
•Use localized ionized air flow on to the glass during sensor cleaning.
•Blow off mobile contamination using an ionized air gun.
•Place the sensor under the microscope at a magnification of 5x to determine the
location of any remaining contamination.
•Clean the contamination on the sensor using one drop of E2 on a swab.
•Wipe the swab from left to right (or right to left but only in one direction). Do
this in an overlapping pattern, turning the swab after the first wipe and with
each subsequent wipe. Avoid swiping back and forth with the same swab in
order to ensure that particles are removed and not simply transferred to a new

location on the sensor window. This procedure requires you to use multiple
swabs.
•Discard the swab after both sides of the swab have been used once.
•Repeat until there is no visible contamination present.

2. The Piranha4 Camera
Camera Highlights
Based on Teledyne DALSA's unique line scan CMOS sensor architecture, the new Piranha4 8k dual line
scan camera provides outstanding signal-to-noise for high speed imaging.
The P4-8k has 8k resolution with a 7.04 µm x 7.04 µm pixel size for optimized optical design. The camera
delivers a max line rate of 70 kHz.
Precise sensor alignment simplifies multiple camera calibration at the system level. The camera delivers a
throughput of 573 MPix/s using the Camera Link™ interface. An advanced GenICam™ compliant
interface makes the camera easier to setup, control, and integrate. Programmability includes exposure
control, flat field correction, and gain settings.
The Piranha4 8k camera is ideal for flat panel display, printed circuit board, solar cell, film, and large
format web inspection.
Key Features
•8192 x 2 pixels, 7.04 µm x 7.04 µm pixel pitch, 100% fill factor
•70 KHz line rates
•276 DN/(nJ/cm²) broadband @ 1x gain, 12 bit (dual line)
•62 dB dynamic range
Programmability
•Adjustable digital gain and offset
•8, 10 or 12 bit selectable output
•Adjustable integration time and line rate
•Test patterns and camera diagnostics
•Flat field calibration
Applications
•Flat-panel display inspection
•Printed circuit board inspection
•Parcel sorting
•High performance document scanning
•High throughput applications

Models
The camera is available in the following configurations:
Table 1: Camera Models Overview
Model Number
Description
P4-CM-8K070-00-R
8k resolution, 70 kHz line rate, 573 Mpix/s throughput, Camera Link interface.
Table 2: Software
Software
Product Number / Version Number
Camera firmware
Embedded within camera
GenICam™ support (XML camera description file)
Embedded within camera
Sapera LT, including CamExpert GUI application and
GenICam for Camera Link imaging driver
Version 7.20 or later
Camera Performance Specifications
Table 3: Camera Performance Specifications
Specifications
Performance
Imager Format
CMOS dual line scan
Resolution
8192 x 2 pixels
Pixel Size
7.04 µm x 7.04 µm
Pixel Fill Factor
100 %
Throughput
573 Mpix/s
Line Rate
0 kHz minimum to 70 kHz maximum (Full), 41 kHz maximum (Medium), 20
kHz maximum (Base), 100KHz (Deca in Area mode)
Exposure Time
7 µs minimum to 3,000 µs maximum
Bit Depth
8 bits, 10 bits, or 12 bits selectable
Connectors and
Mechanicals
Control & Data Interface
2 Camera Link MDR26 connectors, used to transmit Base, Medium, or Full
Camera Link configurations
Power Connector
Hirose 6-pin circular
Power Supply
+ 12 V to + 24 V DC (+11.4 V to +25.2 V maximum limits)
Power Dissipation
17 W
Size
80 mm (W) x 130 mm (H) x 57 mm (D)
Mass
< 700 g, including heat sinks (< 530 g without heat sinks)
Operating Temp
0 °C to 50 °C, front plate temperature
Optical Interface
Lens Mount
M72 x 0.75
Sensor to Camera Front Distance
12 mm
Sensor Alignment (aligned to sides of camera)

Flatness
y (parallelism)
x
y
z
z
50 µm
0.08° or 81 µm
± 80 µm
± 80 µm
± 250 µm
± 0.2°
Compliance
Regulatory Compliance
CE and RoHS; GenICam
Operating Ranges
Performance
Notes
Single Line
Dual Line
Dynamic Range
62 dB
63.3 dB
Random Noise
3.42 DN* rms
2.8 DN rms
FFC enabled
Broadband Responsivity
198 DN/(nJ/cm2)
276 DN/(nJ/cm2)
Gain
1x to 10x Nominal range
1x to 10x Nominal range
DC Offset
16 DN
16 DN
FFC enabled
PRNU
<1% @50% Sat
<1% @50% Sat
FPN
< 5 DN
< 5 DN
SEE
20.2 nJ / cm2
14.49 nJ / cm2
NEE
11.16 pJ / cm2
12.39 pJ /cm2
Antiblooming
> 100 x Saturation
Integral non-linearity
< 2% DN
*DN = digital number
Test Conditions:
•Values measured using 12-bit, 1x gain.
•10 kHz line rate
•Light source: broadband, quartz halogen, 3250 K with 700 nm IR cutoff filter.
•Front plate temperature: 45º C
Certifications and Compliance
Compliance
EN 55011, FCC Part 15, CISPR 11, and ICES-003 Class A Radiated Emissions Requirements
EN 55024 and EN 61326-1 Immunity to Disturbance
RoHS per EU Directive 2002/95/EC and WEEE per EU Directive 2002/96/EC and China Electronic Industry Standard
SJ/T11364-2006
GenICam XML Description File, Superset of the GenICam™ Standard Features Naming Convention specification
V1.5, Camera Link Serial Communication: GenICam™ Generic Control Protocol (GenCP V1.0)
Supported Industry Standards
GenICam™
Piranha4 cameras are GenICam compliant. They implement a superset of the GenICam™ Standard
Features Naming Convention specification V1.5.

This description takes the form of an XML device description file respecting the syntax defined by the
GenApi module of the GenICam™specification. The camera uses the GenICam™ Generic Control
Protocol (GenCP V1.0) to communicate over the Camera Link serial port.
For more information see www.genicam.org.
Responsivity
The responsivity graph describes the sensor response to different wavelengths of light (excluding lens
and light source characteristics).
0
50
100
150
200
250
300
350
350 450 550 650 750 850 950
Spectral Responsivity (DN/nJ/cm2)
Wavelength (nm)
P4 8K Spectral Responsivity vs Wavelength (12bit @ 1x Gain, Dual Line)
Figure 1: Spectral Responsivity vs. Wavelength (Dual Line)

Figure 2: Spectral Quantum Efficiency
FPN Characteristics with Temperature
Figure 3: FPN Derating Chart
0.0
10.0
20.0
30.0
40.0
50.0
60.0
70.0
400 450 500 550 600 650 700 750 800 850 900
Quantum Efficiency[ % ]
Wavelength [ nm ]
Spectral Quantum Efficiency

Mechanicals
Figure 4: Camera Mechanical

Figure 5: Camera Mechanical with External Heat Sink
Camera Mounting and Heat Sink Considerations
The Piranha4 cameras ships with two heat sinks installed and ideally positioned to allow close spacing of
the cameras. These heat sinks are designed to provide adequate convection cooling when not obstructed
by enclosures or mounting assemblies.
Teledyne DALSA recognises that each customer’s application can be unique. In consideration, the P4
camera heat sinks have been designed in such a way that they can be repositioned on the different faces
of the camera or removed entirely, depending on the mounting configuration and its heat sinking
potential.
Repositioning or removal of the heat sinks must be performed with care in order to avoid temperature
issues. The camera has the ability to measure its internal temperature. Use this feature to record the
internal temperature of the camera when it is mounted in your system and operating under the worst
case conditions. The camera will stop outputting data if its internal temperature reaches 75 °C.

3. Software and Hardware Setup
Recommended System Requirements
To achieve best system performance, the following minimum requirements are recommended:
•High bandwidth frame grabber recommended, e.g. Xcelera-CL PX4 Full Camera Link frame grabber
(Part # OR-X4CO-XPF00).
•Operating system: Windows XP 32-bit.
Setup Steps: Overview
Take the following steps in order to setup and run your camera system. They are described briefly below
and in more detail in the sections that follow.
1. Install and Configure Frame Grabber and GUI
If your host computer does not have a PX4 full Camera link frame grabber then you need to install one.
We recommend the Xcelera-CL PX8 Full or PX4 Full frame grabber or equivalent, described in detail on
the teledynedalsa.com site here. Follow the manufacturer’s installation instructions.
A GenICam™ compliant XML device description file is embedded within the camera firmware allowing
GenICam™ compliant application to know the camera’s capabilities immediately after connection.
Installing SaperaLT gives you access to the CamExpert GUI, a GenICam™ compliant application.
2. Connect Camera Link and Power Cables
•Connect the Camera Link cables from the camera to the computer.
•Connect a power cable from the camera to a +12 VDC to +24 VDC power supply.
3. Establish communicating with the camera
Start the GUI and establish communication with the camera. Refer to page 17 for a description on
communicating with the camera.
ASCII Commands
As an alternative to the CamExpert (or equivalent) GUI, you can communicate with this camera using
ASCII-based commands. A complete list of the commands and a description of how to access them can be
found in the appendix: Appendix B: ASCII Commands.
4. Operate the Camera
At this point you will be ready to start operating the camera in order to acquire images, set camera
functions, and save settings.

Step 1. Install and configure the frame grabber,
graphics card and GUI
Install Frame Grabber
Install a Full configuration Camera Link frame grabber according to the manufacturer’s description.
We recommend the Xcelera-CL PX8 or PX4 frame grabber or equivalent, described in detail on the
teledynedalsa.com site here.
Install Sapera LT and CamExpert
Communicate with the camera using a Camera Link-compliant interface. We recommend you use
CamExpert. CamExpert is the camera interfacing tool supported by the Sapera library and comes
bundled with Sapera LT. Using CamExpert is the simplest and quickest way to send commands to and
receive information from the camera.
Camera Link Control Communications
The P4 family of cameras are GenICam™ compliant. Sapera uses the GenICam™ Generic Control
Protocol (GenCP V1.0) to communicate with the camera over the Camera Link serial port. When
communications are first established Sapera will when connecting for the first time download the
GenICam™ XML Description file. This file details how to access and control the camera.

Step 2. Connect Data, Trigger, and Power Cables
Note: the use of cables types and lengths other than those specified may result in increased emission or
decreased immunity and performance of the camera.
Figure 6: Input and Output, Trigger, and Power Connectors
WARNING! Grounding Instructions
Static electricity can damage electronic components. It’s critical that you discharge any static
electrical charge by touching a grounded surface, such as the metal computer chassis, before
handling the camera hardware.
!
B
B
C
A
Power
+12V to +24V DC Hirose 6-pin
Control & Data
Camera Link 26-pin MDR26 connectors
Status
Diagnostic LED
A
B
B
C

Data Connector: Camera Link
The camera uses two Camera Link MDR26 cables transmitting the Camera Link Base, Medium, or Full
configuration. The figure below shows the MDR26 Camera Link Connector and the tables that follow list
the Camera Link Base, Medium, and Full configurations.
For detailed information on Camera Link please refer to the Camera Link Road Map available from the
Knowledge Center on the Teledyne DALSA Web site:
https://www.teledynedalsa.com/en/support/documentation/app-notes/
Figure 7. MDR26 Camera Link Connector
Data 2
Control / Data
1
Camera
Connector
Right Angle
Frame Grabber
Connector
Channel Link
Signal
Camera
Connector
Right Angle
Frame Grabber
Connector
Channel Link
Signal
1
1
inner shield
1
1
inner shield
14
14
inner shield
14
14
inner shield
2
25
Y0-
2
25
X0-
15
12
Y0+
15
12
X0+
3
24
Y1-
3
24
X1-
16
11
Y1+
16
11
X1+
4
23
Y2-
4
23
X2-
17
10
Y2+
17
10
X2+
5
22
Yclk-
5
22
Xclk-
18
9
Yclk+
18
9
Xclk+
6
21
Y3-
6
21
X3-
19
8
Y3+
19
8
X3+
7
20
100 ohm
7
20
SerTC+
20
7
terminated
20
7
SerTC-
8
19
Z0-
8
19
SerTFG-
21
6
Z0+
21
6
SerTFG+
9
18
Z1-
9
18
CC1-
22
5
Z1+
22
5
CC1+
10
17
Z2-
10
17
CC2+
23
4
Z2+
23
4
CC2-
11
16
Zclk-
11
16
CC3-
24
3
Zclk+
24
3
CC3+
12
15
Z3-
12
15
CC4+

25
2
Z3+
25
2
CC4-
13
13
inner shield
13
13
inner shield
26
26
inner shield
26
26
inner shield
*Exterior Overshield is connected to the shells of the connectors on both ends. Unused pairs should be terminated in 100 ohms at
both ends of the cable. Inner shield is connected to signal ground inside camera
Full Configuration
8 bits Camera Link Full Configuration
Connector 1: Channel link X
Connector 2: Channel link Y
Connector 3: Channel link Z
Camera/Frame
Grabber Pin
Bit Name
Camera/Frame
Grabber Pin
Bit Name
Camera/Frame
Grabber Pin
Bit Name
Tx0/Rx0
D0(0)
Tx0/Rx0
D3(0)
Tx0/Rx0
D6(0)
Tx1/Rx1
D0(1)
Tx1/Rx1
D3(1)
Tx1/Rx1
D6(1)
Tx2/Rx2
D0(2)
Tx2/Rx2
D3(2)
Tx2/Rx2
D6(2)
Tx3/Rx3
D0(3)
Tx3/Rx3
D3(3)
Tx3/Rx3
D6(3)
Tx4/Rx4
D0(4)
Tx4/Rx4
D3(4)
Tx4/Rx4
D6(4)
Tx5/Rx5
D0(7)
Tx5/Rx5
D3(7)
Tx5/Rx5
D6(7)
Tx6/Rx6
D0(5)
Tx6/Rx6
D3(5)
Tx6/Rx6
D6(5)
Tx7/Rx7
D1(0)
Tx7/Rx7
D4(0)
Tx7/Rx7
D7(0)
Tx8/Rx8
D1(1)
Tx8/Rx8
D4(1)
Tx8/Rx8
D7(1)
Tx9/Rx9
D1(2)
Tx9/Rx9
D4(2)
Tx9/Rx9
D7(2)
Tx10/Rx10
D1(6)
Tx10/Rx10
D4(6)
Tx10/Rx10
D7(6)
Tx11/Rx11
D1(7)
Tx11/Rx11
D4(7)
Tx11/Rx11
D7(7)
Tx12/Rx12
D1(3)
Tx12/Rx12
D4(3)
Tx12/Rx12
D7(3)
Tx13/Rx13
D1(4)
Tx13/Rx13
D4(4)
Tx13/Rx13
D7(4)
Tx14/Rx14
D1(5)
Tx14/Rx14
D4(5)
Tx14/Rx14
D7(5)
Tx15/Rx15
D2(0)
Tx15/Rx15
D5(0)
Tx15/Rx15
Not Used
Tx16/Rx16
D2(6)
Tx16/Rx16
D5(6)
Tx16/Rx16
Not Used
Tx17/Rx17
D2(7)
Tx17/Rx17
D5(7)
Tx17/Rx17
Not Used
Tx18/Rx18
D2(1)
Tx18/Rx18
D5(1)
Tx18/Rx18
Not Used
Tx19/Rx19
D2(2)
Tx19/Rx19
D5(2)
Tx19/Rx19
Not Used
Tx20/Rx20
D2(3)
Tx20/Rx20
D5(3)
Tx20/Rx20
Not Used
Tx21/Rx21
D2(4)
Tx21/Rx21
D5(4)
Tx21/Rx21
Not Used
Tx22/Rx22
D2(5)
Tx22/Rx22
D5(5)
Tx22/Rx22
Not Used
Tx23/Rx23
Not Used
Tx23/Rx23
Not Used
Tx23/Rx23
Not Used
Tx24/Rx24
LVAL
Tx24/Rx24
LVAL
Tx24/Rx24
LVAL
Tx25/Rx25
FVAL
Tx25/Rx25
FVAL
Tx25/Rx25
FVAL
Tx26/Rx26
Not Used
Tx26/Rx26
Not Used
Tx26/Rx26
Not Used
Tx27/Rx27
D0(6)
Tx27/Rx27
D3(6)
Tx27/Rx27
D6(6)
Tap 1 bits are D0(x)...Tap 8 bits are D7(x)

Camera Link Bit Definitions
BASE
Configuration
T0
Pixel Format
Port A
Bits 0 thru 7
Port B
Bits 0 thru 7
Port C
Bits 0 thru 7
Mono 8
Tap 1 LSB..Bit 7
Pixels (1, 3, 5, ... 8189,
8191)
Tap 2 LSB..Bit7
Pixels (2, 4, 6, ... 8190, 8192)
xxxxxxx
Mono 12
Tap 1 LSB.. Bit 7
Pixels (1, 3, 5, ... 8189,
8191)
Tap 1 Bits 8,9,10,11
Pixels (1, 3, 5, ... 8189,8191)
Tap 2 Bits 8,9,10,11
Pixels (2,4,6, ... 8190, 8192)
Tap 2 LSB..Bit 7
Pixels (2,4,6, ... 8190, 8192)
Medium
Configuration
T0
Pixel Format
Port A
Bits 0 thru 7
Port B
Bits 0 thru 7
Port C
Bits 0 thru
7
Port D
Bits 0
thru 7
Port E
Bits 0 thru 7
Port F
Bits 0 thru 7
Mono 8
Tap 1
LSB..Bit 7
Pixels (1, 5, 9, ...
8185, 8189)
Tap 2
LSB..Bit 7
Pixels (2, 6, 10,
... 8186, 8190)
Tap 3
LSB..Bit 7
Pixels (3, 7,
11, ... 8187,
8191)
Tap 4
LSB...Bit 7
Pixels (4,
8, 12, ...
8188,
8192)
xxxxxxxx
Xxxxxxxx
Mono 10 /
Mono 12
Tap 1
LSB.. Bit 7
Pixels (1, 5, 9, ...
8187, 8191)
Tap 1
Bits 8,9,10,11
Pixels (1, 5, 9, ...
8187, 8191)
Tap 2
Bits 8,9,10,11
Pixels (2, 6, 10,
... 8188, 8192)
Tap 2
LSB..Bit 7
Pixels (2, 6,
10, ... 8188,
8192)
Tap 4
LSB…Bit
7
Pixels (4,
8, 12, ...
8186,
8190)
Tap 3
LSB…Bit 7
Pixels (3, 7,
11, ... 8185,
8189)
Tap 3
Bit 8,9,10,11
Pixels (3, 7, 11,
... 8185, 8189)
Tap 4
Bits 8,9,10,11
Pixels (4, 8, 12,
... 8186, 8190)
Full
Configuration
T0
Pixel Format
Port A
LSB…Bit
7
Port B
LSB…Bit
8
Port C
LSB…Bit
8
Port D
LSB…Bit
8
Port E
LSB…Bit
8
Port F
LSB…Bit
8
Port G
LSB…Bit
8
Port H
LSB…Bit
8
Mono 8
Tap 1
LSB…
Bit 7
Pixels (1,
9, 17, ...
8177,
8185)
Tap 2
LSB…
Bit 7
Pixels (2,
10, 18, ...
8178,
8186)
Tap 3
LSB…
Bit 7
Pixels (3,
11, 19, ...
8179,
8187)
Tap 4
LSB…
Bit 7
Pixels (4,
12, 20, ...
8180,
8188)
Tap 5
LSB…
Bit 7
Pixels (5,
13, 21, ...
8181,
8189)
Tap 6
LSB…
Bit 7
Pixels (6,
14, 22, ...
8182,
8190)
Tap 7
LSB…Bit
7
Pixels (7,
15, 23, ...
8183,
8191)
Tap 8
LSB…
Bit 7
Pixels (8,
16, 24, ...
8184,
8192)
Table 4: Camera Link Bit Definitions
Other manuals for Piranha4 Series
5
This manual suits for next models
1
Table of contents
Other Dalsa Machine Vision System manuals
Popular Machine Vision System manuals by other brands
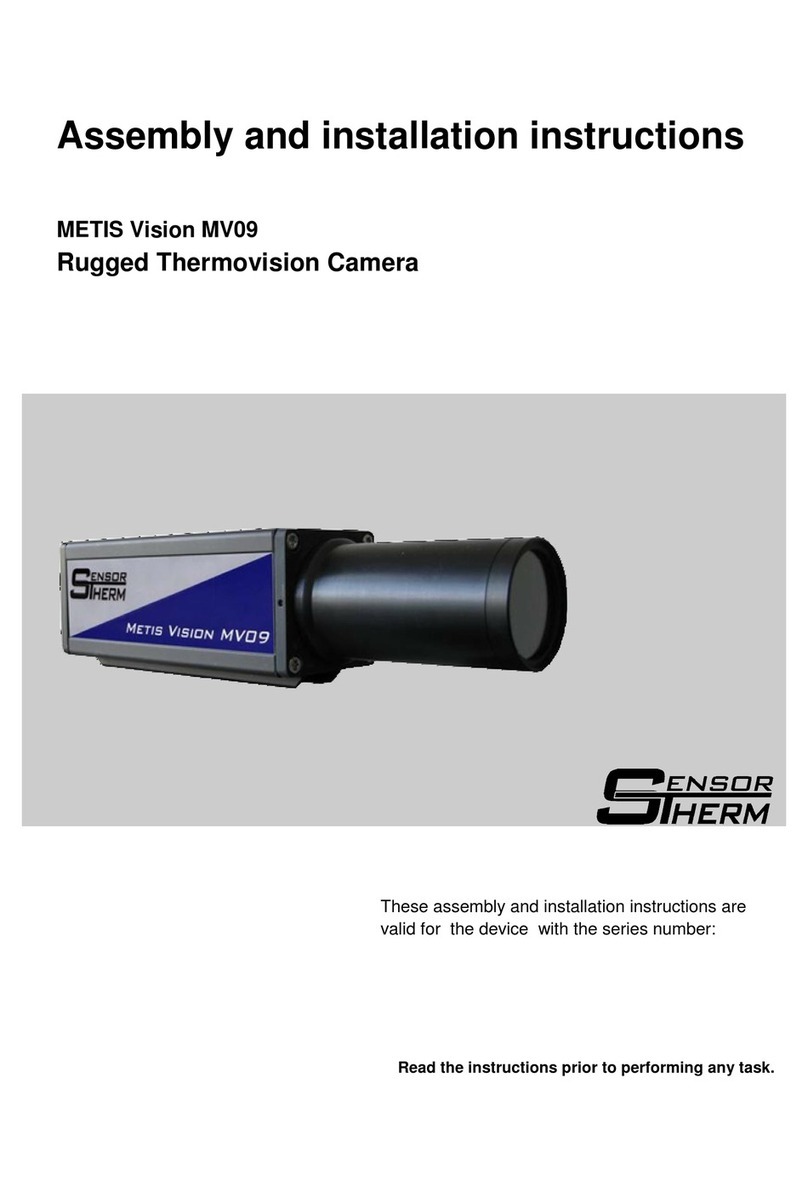
Sensor Therm
Sensor Therm METIS Vision MV09 Assembly and installation instructions
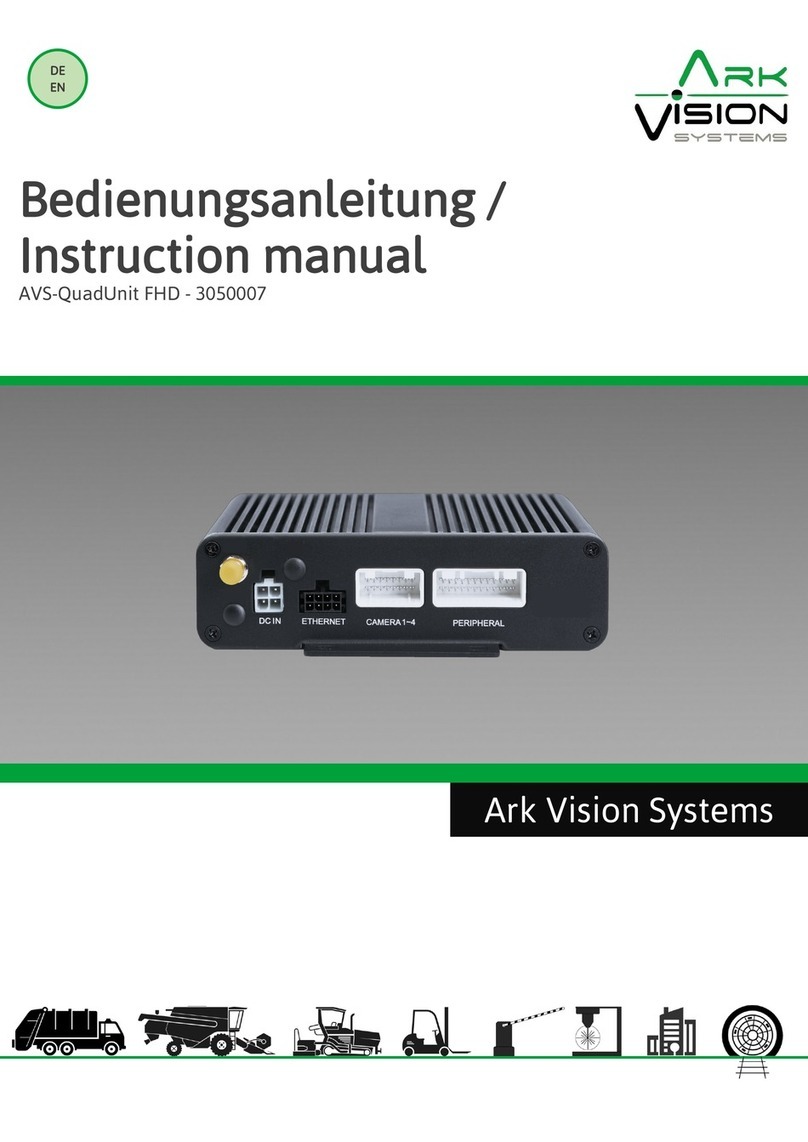
Ark Vision Systems
Ark Vision Systems AVS-QuadUnit FHD instruction manual

Festo
Festo SBO*-M-* Series Electronic manual
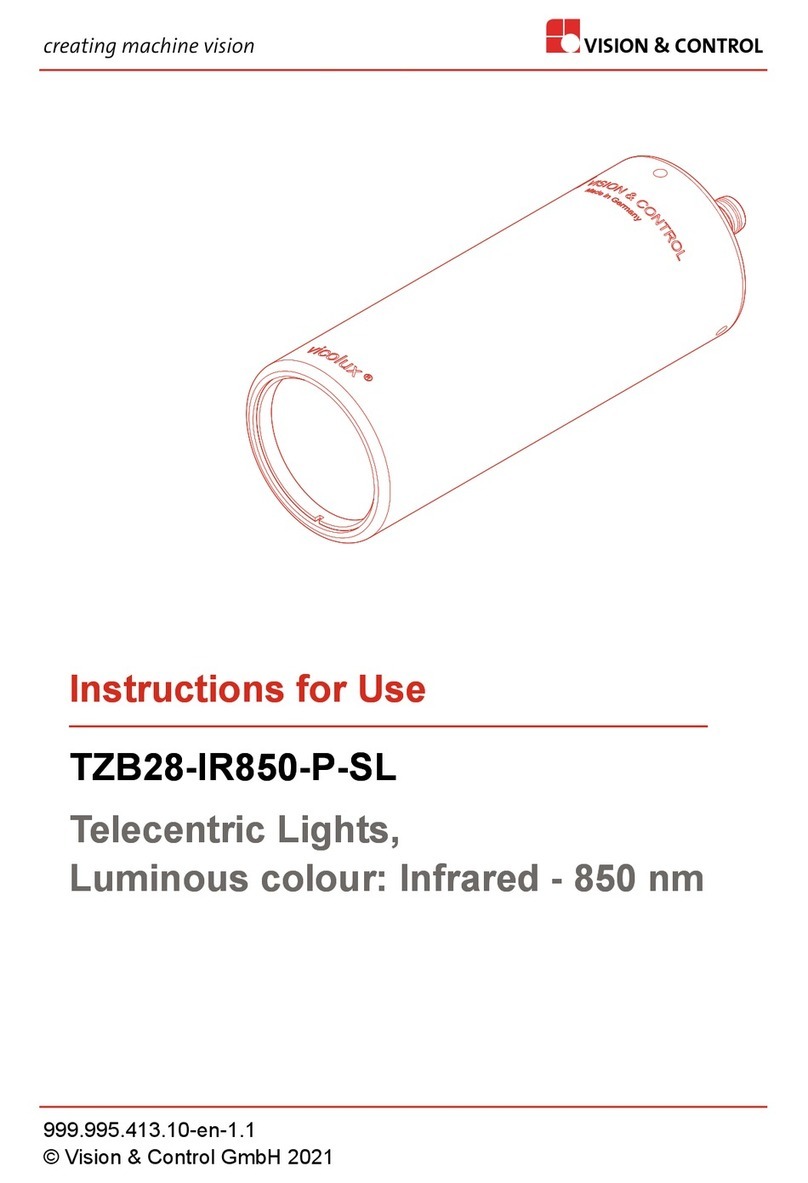
Vision & Control
Vision & Control TZB28-IR850-P-SL Instructions for use
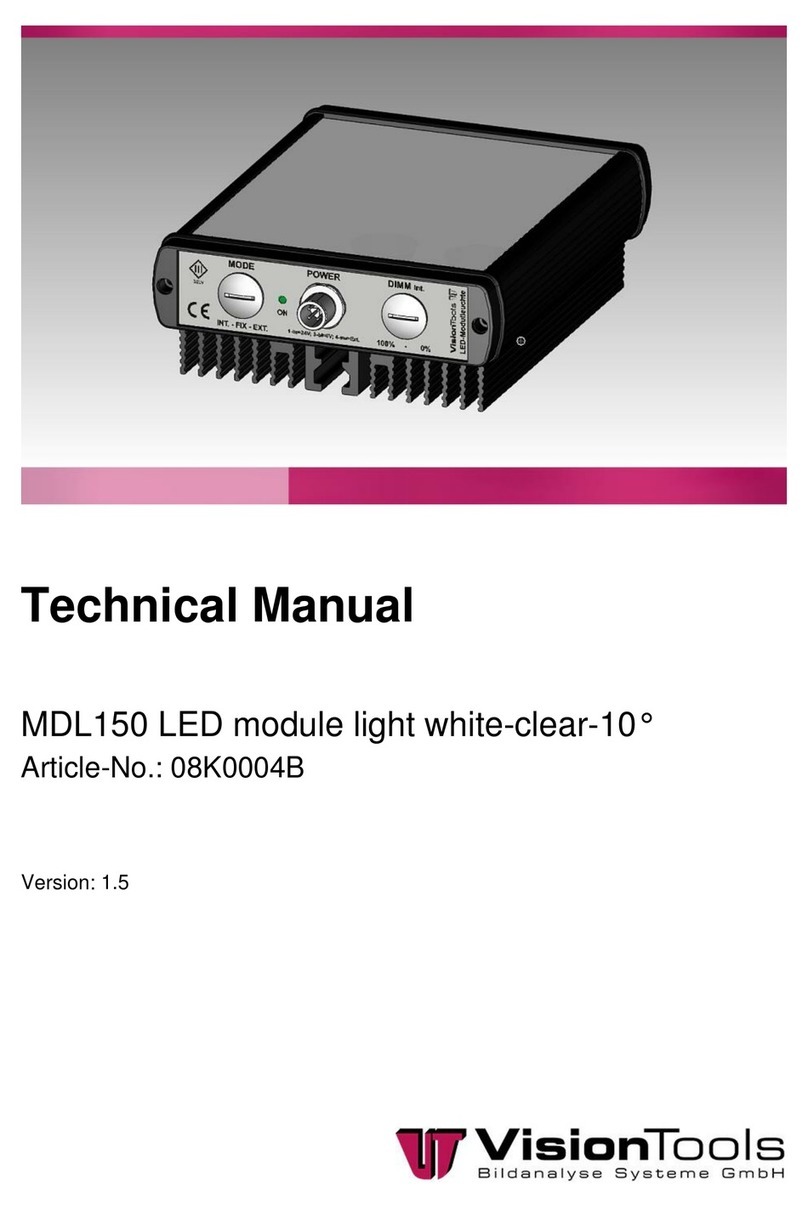
Vision tools
Vision tools MDL150 Technical manual
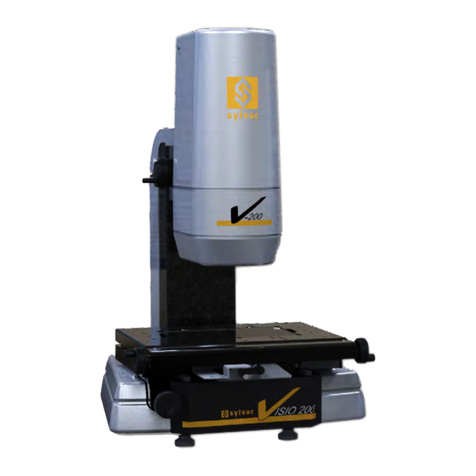
Sylvac
Sylvac VISIO 200 GL Instruction Manual Quick Start Version