Danfoss ET5020 User manual


Imprint
Manufacturer:
UNIFLEX-Hydraulik GmbH
Robert-Bosch-Strasse 50-52
D-61184 Karben
Germany
Phone: +49 (0) 60 39 / 91 71 - 0
Fax: +49 (0) 60 39 / 91 71 - 181
This Operating Manual of the machine is a translation; the origi-
nal is in German.
Date of revision:2022-10-05
Version: 1.0
© Copyright by UNIFLEX-Hydraulik GmbH
Technical modifications reserved.
The reproduction, distribution and utilization of this document as well
as the communication of its contents to others without explicit authori-
zation are prohibited. Offenders will be held liable for the payment of
damages. All rights reserved in the event of the grant of a patent, util-
ity model or design.


EC / UK - Declaration of Conformity
In accordance with EC Machinery Directive 2006/42/EC and UK-Sup-
ply of Machinery (Safety) Regulations 2008.
The following machine
Danfoss ET5020
was developed, designed and manufactured in compliance with EC
Directive 2006/42/EC and UK-Supply of Machinery
(Safety) Regulations 2008, in the sole responsibility of
UNIFLEX-Hydraulik GmbH
Robert-Bosch-Strasse 50 - 52
D-61184 Karben
The following standards, codes and specifications have been applied:
•EC Directive 2006/42/EC
•EMC Directive 2014/30/EC
•EN ISO 12100: 2010
•EN 60204-1: 2018
•UK-Supply of Machinery (Safety) Regulations 2008
•UK-Electromagnetic Compatibility Regulations 2016
This declaration are invalid when the machine is modified or if unau-
thorized and unapproved third-party components are used without
our prior approval.
Entity authorised for documentation: Uniflex-Hydraulik GmbH, Tech-
nical Documentation Dept.
Karben, 29.09.2022
Managing Director Harald von Waitz

Contents
1About this document .......................................................................................... 8
1.1 Target groups ............................................................................................... 8
1.2 Storage....................................................................................................... 10
1.3 Name plate ................................................................................................. 10
1.4 Abbreviations.............................................................................................. 10
2Safety instructions............................................................................................ 11
2.1 Presentation of warnings ............................................................................ 11
2.2 Intended use............................................................................................... 11
2.3 Product-specific risks.................................................................................. 13
2.3.1 Risks imposed by mechanical equipment........................................ 13
2.3.2 Risks imposed by electricity............................................................. 13
2.3.3 Risks imposed by hydraulic equipment............................................ 13
2.3.4 Risks imposed by noise................................................................... 14
2.3.5 Risks imposed by substances ......................................................... 14
2.3.6 Risk by hot surfaces ........................................................................ 14
2.3.7 Risks in case of fire.......................................................................... 15
2.4 Safety.......................................................................................................... 16
2.4.1 Working area................................................................................... 16
2.4.2 Emergency-stop button.................................................................... 17
2.4.3 Protection equipment....................................................................... 17
2.4.4 Warning signs on the machine ........................................................ 18
3Machine description.......................................................................................... 20
3.1 Design and function.................................................................................... 20
3.2 Accessories ................................................................................................ 21
3.3 Forming process......................................................................................... 22
3.4 Operation and display elements C.2........................................................... 24
3.5 Electric sockets........................................................................................... 25
3.6 Foot pedal (accessory) ............................................................................... 26
3.7 Depth stop (accessory)............................................................................... 27
3.8 Operation modes ........................................................................................ 27
3.9 Technical data ............................................................................................ 30
4Transport and commissioning......................................................................... 33
4.1 Transport .................................................................................................... 33

4.2 Intermediate storage of machine/unit ..........................................................34
4.3 Commissioning............................................................................................34
4.3.1 Filling hydraulic oil............................................................................35
4.3.2 Electrical connection ........................................................................37
4.3.3 Bleeding the hydraulic system..........................................................39
5Operation............................................................................................................40
5.1 What you have to observe...........................................................................40
5.2 Activation.....................................................................................................40
5.3 Forming the workpiece................................................................................41
5.3.1 Prerequisites ....................................................................................41
5.3.2 Operation mode buttons control panel .............................................41
5.3.3 Remote automatic mode, via dual foot switch..................................43
5.3.4 Remote automatic mode, via depth stop..........................................44
5.3.5 Changing the crimping dies with the quick die change system (only
profile 239)...................................................................................................45
5.4 Adjusting the depth stop..............................................................................47
5.5 Setting the forming dimension.....................................................................49
5.6 Stop.............................................................................................................50
5.7 Emergency stop...........................................................................................50
5.8 Cleaning ......................................................................................................51
6Maintenance .......................................................................................................52
6.1 What you have to observe...........................................................................52
6.2 Maintenance schedule.................................................................................52
6.3 Hydraulic oil change....................................................................................54
6.4 Checking and replacing slide bearing plates ...............................................56
6.5 Replacement of relay/opto-coupler..............................................................58
7Troubleshooting.................................................................................................60
8Decommissioning, disposal..............................................................................61
8.1 Dismantling..................................................................................................62
8.2 Recycling.....................................................................................................62
8.3 Consumables and waste .............................................................................62
9Annex..................................................................................................................64
9.1 Accessories (retrofittable)............................................................................64
9.2 Spare parts list.............................................................................................65
9.2.1 Mechanical equipment .....................................................................65
9.2.2 Hydraulic system..............................................................................69

9.2.3 Electric equipment........................................................................... 71
9.3 Depth stop, manual..................................................................................... 72
9.4 Depth stop, automatic................................................................................. 73
9.5 Spare parts kit............................................................................................. 74
9.6 Retaining bolt for standard crimping dies (depending on crimping die)....... 75
9.7 Hydraulic diagram....................................................................................... 77
9.8 Electric diagram.......................................................................................... 78
9.9 Maintenance log.......................................................................................... 87
9.10 Declaration of qualified staff........................................................................ 88

1 About this document
In this Operation Manual, the “forming machine Danfoss ET5020” is
consistently referred to as machine.
This Operation Manual includes important notes on how you operate
your machine/unit safely, properly and economically.
Use not in compliance with the intended purpose may result in hazard
to the operator's health and life and/or in the risk of damage to/the
machine/unit. Consequently, please only use the machine/unit
•in good order and condition,
•in accordance with its intended purpose,
•in a safety-conscious manner, with awareness of risks and haz-
ards,
•in compliance with all notes included in this Operation Manual.
The machine/unit may only be operated by staff who
•has read the Operation Manual,
•has understood it,
•has been instructed in the operation of the machine/unit, and
•has signed in the Annex.
Figures may include accessories/options. Customer-specific
equipment may vary.
The product images shown are for reference only and may differ
from the product delivered.
1.1 Target groups
The target groups of this Operation Manual are:
Owner
An owner is a natural person or entity using the device himself/her-
self/itself, or on whose behalf the device is used. An owner may ap-
point a representative to exercise the owner's rights and obligations.
The owner has to make sure that

•national provisions, occupational safety regulations and applica-
ble environmental protection regulations are fully complied with;
•persons working on the machine/unit are adequately qualified;
•persons working on the machine/unit are suitable for operating
the machine/unit;
•the Operation Manual has been read and understood. One hard-
copy of the Operation Manual must always be kept at a desig-
nated place where the machine/unit is used.
•persons working on the machine/unit are aware of potential
risks;
•the operating staff is familiar with the location as well as with op-
erating the fire alarm and fighting means. Free access to this
equipment must be ensured.
•personal protection equipment is worn (safety footwear, protec-
tion gloves and safety glasses).
Machine/unit fitters
Machine/unit fitters must be at least 18 years old and have completed
training for the task, i.e. they must have attended a specialist voca-
tional training.
A fitter
•must observe the instructions in the Operation Manual;
•must inform the owner on failures and damage.
Operator
An operator is a person charged with and instructed in the proper op-
eration of the machine/unit by the owner or the otherwise contractu-
ally obliged person.
The operator
•must observe the instructions in the Operation Manual;
•must inform the owner on failures and damage.
•must not perform and maintenance or repair work on the ma-
chine/unit.

1.2 Storage
The Operation Manual is part of the machine/unit and must be kept
near the machine/unit at all times. Upon disposal of the machine/unit,
the Operation Manual must also be handed over.
1.3 Name plate
The name plate is fixed near the power cable.
1.4 Abbreviations
CFM Crimp Force Monitoring
FD Manual Flow Divider
PB Crimping dies
PBK Calibration crimping dies
PFC Pressure Force Control
PFM Pressure Force Monitoring
QDC Quick crimping die change system
ZWB Intermediate dies

2 Safety instructions
2.1 Presentation of warnings
Warning notes in the Operation Manual warn against risks involved
with the handling of the machine/unit. Risk levels are identified as fol-
lows:
The signal word HAZARD identifies an imminent hazard resulting in
serious injuries or death. This warning is supplemented by a triangu-
lar hazard symbol.
The signal word WARNING identifies a potentially hazardous situa-
tion, which might result in serious injuries or death. This warning is
supplemented by a triangular hazard symbol.
The signal word CAUTION identifies a potentially hazardous situa-
tion, which might result in light injuries. This warning is supplemented
by a triangular hazard symbol.
The signal word ATTENTION identifies a potentially hazardous situa-
tion, in which the product or property in the environment may be dam-
ages. This warning is supplemented by a hazard symbol or a excla-
mation mark.
2.2 Intended use
This machine is a forming machine for industrial use, only suitable for
the manufacture of hose connections with a permissible diameter de-
pending on the fitting and the hose thickness, see “Technical Data” in
Section 3.
Intended purposes include:
•single workplace for one person only,
•single stroke with manual feed and withdrawal,
•for maximum hydraulic operating pressure, see “Technical Data”
in Section 3.
•operating temperature between 10 °C and 35 °C,
•operation in a closed room,
HAZARD!
WARNING!
CAUTION!
ATTENTION!

•use of eight identical original UNIFLEX dies with the same label
or seven dies and one associated marking crimping die.
•The machine must not be operated by persons not capable of
operating the machine without any risk. These may include:
➢persons with physical or mental disabilities;
➢children and persons under age;
➢persons with a restricted capability for the operation of ma-
chines (e.g. under the influence of drugs, alcohol or narcot-
ics)
Use of the control in compliance with the intended purpose also inclu-
des compliance with the instructions in this Operation Manual.
Use for other than the intended purpose
Any other use is considered as being not in compliance with the in-
tended purpose, in particular:
•design modification of the machine;
•use in explosive environments;
•forming of non-metal workpieces without specific safeguards ap-
proved by UNIFLEX;
•misuse of consumables and waste materials.
In particular non-metal workpieces may by overstressed by the for-
ming process so that this may result in a sudden failure. Chips or se-
riously accelerated workpiece parts impose a high risk potential for
operators, individuals and objects, even outside the working area.
WARNING!
Risk for life and health!
Use not in compliance with the intended purpose imposes risks
for life and health. Consequences resulting from use for other
than the intended purpose shall be under the sole responsibility
of the owner.
•Always use the machine in compliance with its intended pur-
pose.

2.3 Product-specific risks
The machine/unit is designed in accordance with the latest state of
technology. Nevertheless, the machine/unit may impose risks:
2.3.1 Risks imposed by mechanical equipment
Risk of squeezing
When the die system closes, there is a risk of getting squeezed
between the die and the workpiece.
•Keep the feed opening for the workpiece as small as possible.
•Keep sufficient distance to the die system.
Tilting hazard
The risk of tilting mainly exists while the machine is being trans-
ported.
•Observe the machine's centre of gravity during transport.
2.3.2 Risks imposed by electricity
There is a risk of electrocution near the live parts!
•Work on electric systems may only be performed by qualified
electricians or instructed and trained persons under the supervi-
sion of a qualified electrician.
•Deactivate the machine/unit and secure it against unintentional
restart before maintenance.
2.3.3 Risks imposed by hydraulic equipment
Risks are imposed by all hydraulic lines and connections. Hydraulic
systems are subject to special safety provisions. Work on hydraulic
equipment may only be performed by persons with expert knowledge
of and experience with hydraulic equipment.
•After the machine/unit is deactivated, the given and potentially
hazardous residual energy has to be considered.
•Relieve the residual pressure in the system before performing
repair or maintenance work on hydraulic systems.

•Regularly check lines and bolted connections for leaks and visi-
ble damage. Immediately remedy any damage detected.
Repair work on the hydraulic system of the machine/unit or on its
components may only be performed by UNIFLEX specialist staff.
2.3.4 Risks imposed by noise
The noise level meter acc. to IEC 804, Class 2, was calibrated before
measuring.
The operation of the machine/unit causes noise emissions of < 70
dB(A) at the workplace. Noise protection is not required.
Higher noise emissions may occur when other machine/unitry is sim-
ultaneously used at the workplace. The machine/unit owner must pro-
vide for appropriate protection, e.g.
•instruct staff to wear ear protection,
•provide information/instructions on risks,
•identify hazardous areas,
•provide health monitoring.
2.3.5 Risks imposed by substances
Oils, greases and emulsions may penetrate the skin. When handling
hazardous substances, oils and greases, the manufacturers' safety
instructions have to be observed. Apply skin protection appropriate
for the hazardous substances used.
2.3.6 Risk by hot surfaces
There is a risk of burning when the electric motor and/or the work-
piece are touched after forming.
•Keep sufficient distance to the electric motor.
•Wear protection gloves.

2.3.7 Risks in case of fire
The operating staff has to be familiar with the location as well as with
operating the fire alarm and fighting means. Free access to this
equipment must be ensured.
Never use water to extinguish a fire. For appropriate fire extinguishing
action, please read the safety data sheet of the hydraulic oil supplier.

2.4 Safety
2.4.1 Working area
The working area is designed as the area 1 metre all around the ma-
chine (shaded).
•Keep the working area free from trip hazards
•Use ducts for lines and cables
•Provide good illumination
•Keep access to hydraulic supply free

2.4.2 Emergency-stop button
The machine is fitted with an emergency-stop button on the control
panel.
Immediately activate the emergency-stop button (1) in cases of emer-
gency.
Remedy the cause of the emergency stop first before unlocking the
emergency-stop button.
Do not pull the emergency-stop button for unlocking it, but release it
by rotating it.
2.4.3 Protection equipment
Due to the variety of customer-specific workpieces, UNIFLEX is not
capable of supplying additional standard protection equipment to-
gether with the machine for the prevention of potential residual risks
imposed by the machine.
The necessity of additional, workpiece-specific protection equipment
may for instance arise for angled workpiece geometries needing a
large opening for being inserted into the forming machine. The pres-
sure joining of insulators, structural steel and steel ropes, too, may re-
quire special safeguards.
The owner has to consider the need for adapted protection equip-
ment before commissioning. If such need exists, the relevant protec-
tion equipment has to be mounted before commissioning of the ma-
chine.

UNIFLEX will provide you with customized solutions for protection
equipment upon request. Please do not hesitate to address your per-
sonal contact for consultation.
Mounted safety equipment must not be removed, bypassed or
avoided.
2.4.4 Warning signs on the machine
Hand injury
on the die system
Risk of squeezing
on the die system
Hot surface
on the electric motor

Oiling / greasing prohibited
on the die system
Illegible or missing warning signs must immediately be replaced by
the owner.

3 Machine description
3.1 Design and function
Basic machine
(1) Crimping tool
(2) Control cabinet
(3) Unit (comprising electric motor, pump, control block)
(4) Position encoder system
(5) Control panel with buttons and control system CONTROL C.2
The crimping tool (1) is closed hydraulically, whereby the workpiece
is formed. The pressure needed for this purpose is built up by the
electrically driven pump (3) in the cylinders.
The position encoder system (4) records the current position of the
die system and transfers the value to the control system.
Table of contents
Other Danfoss Crimping Tools manuals
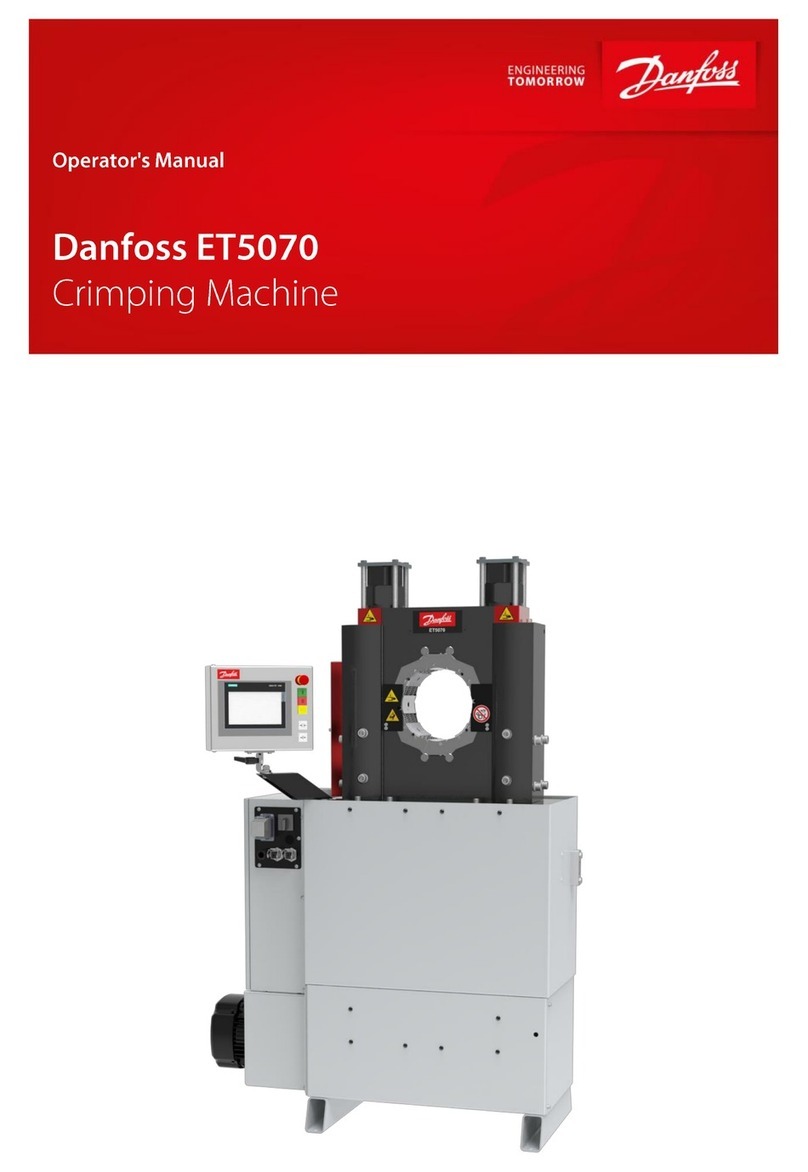
Danfoss
Danfoss ET5070 User manual
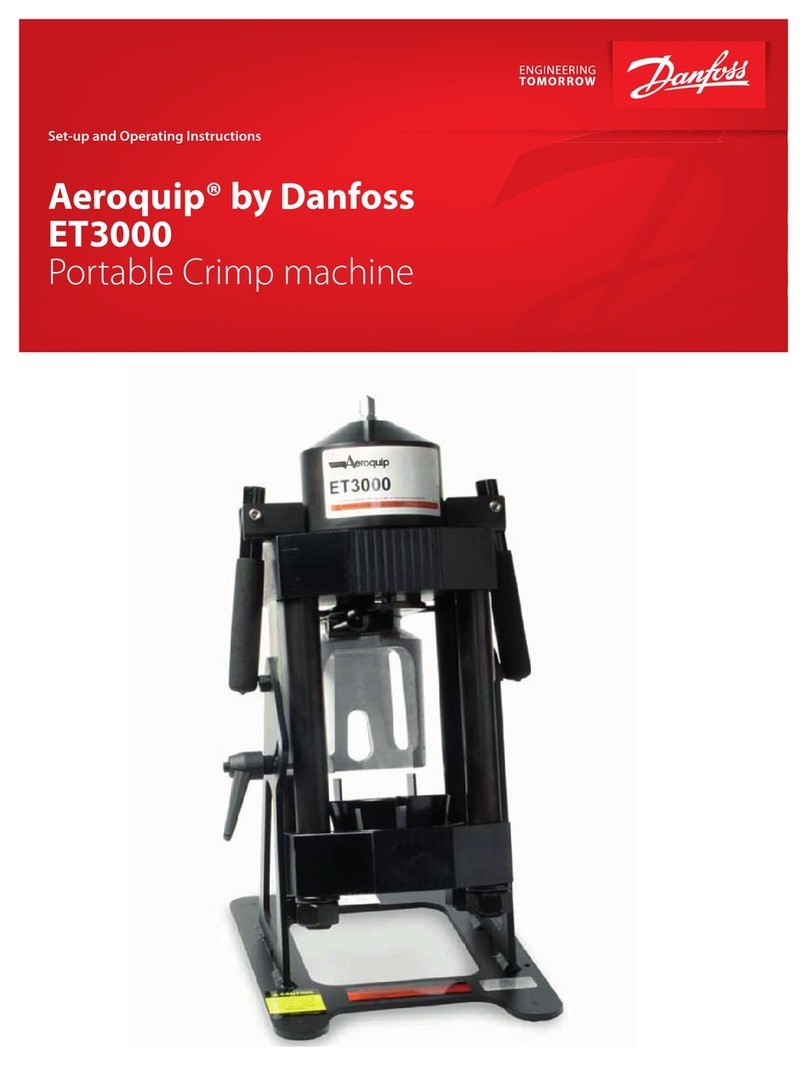
Danfoss
Danfoss Aeroquip ET3000 Installation manual

Danfoss
Danfoss ET1280 User manual
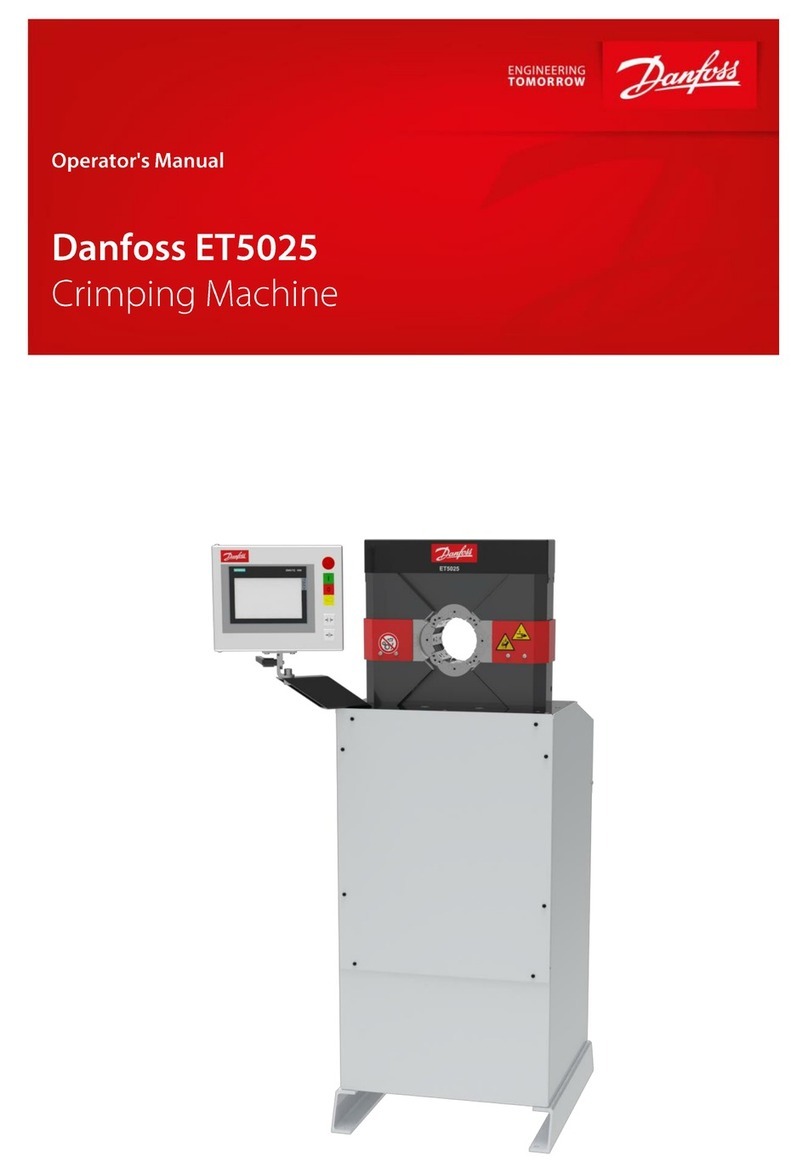
Danfoss
Danfoss ET5025 User manual
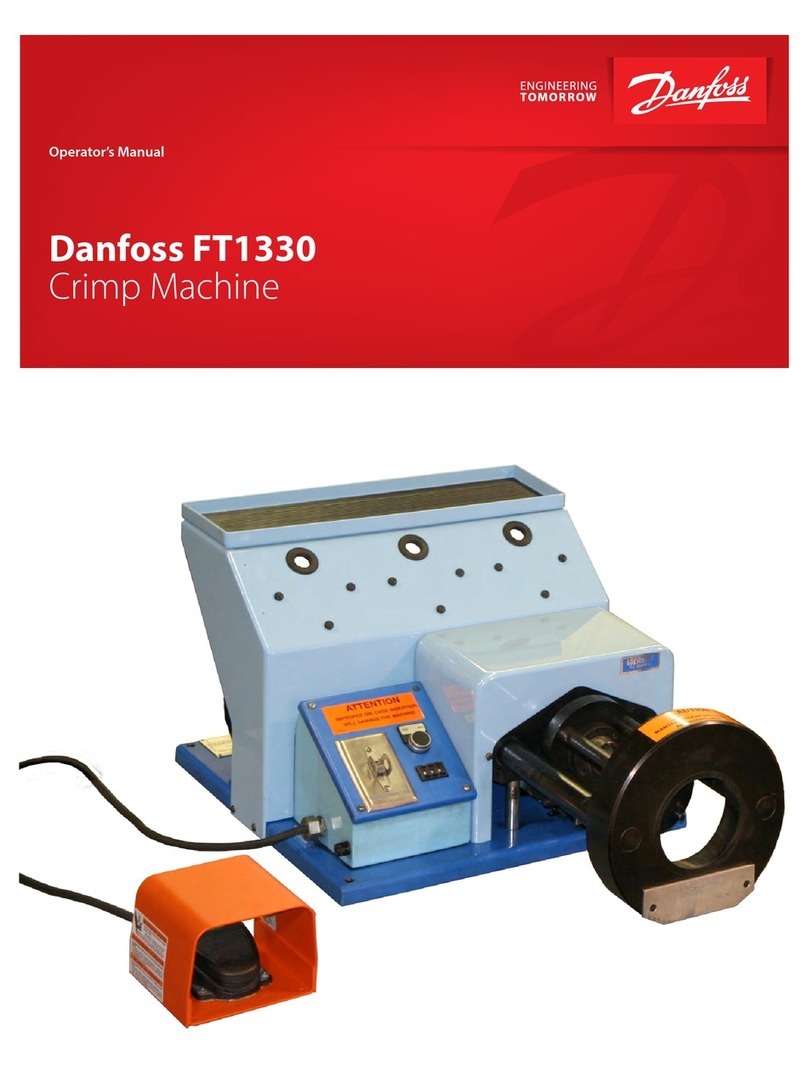
Danfoss
Danfoss FT1330 User manual
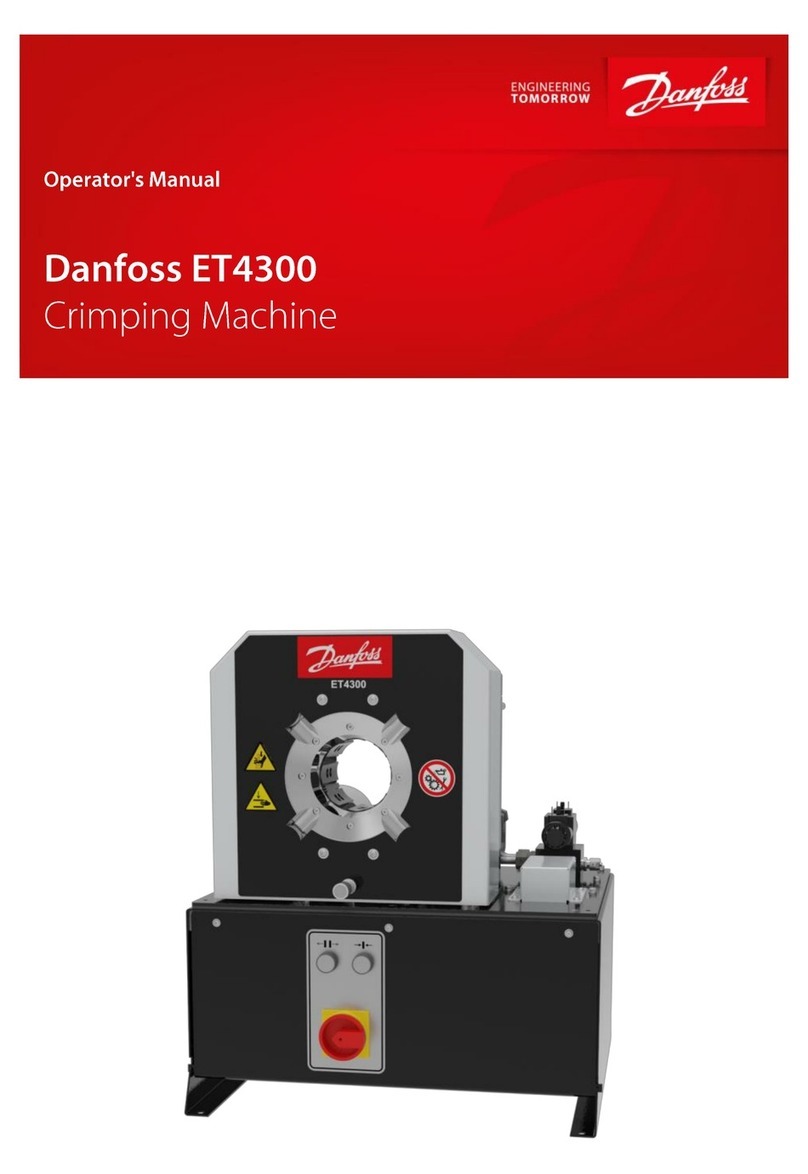
Danfoss
Danfoss ET4300 User manual
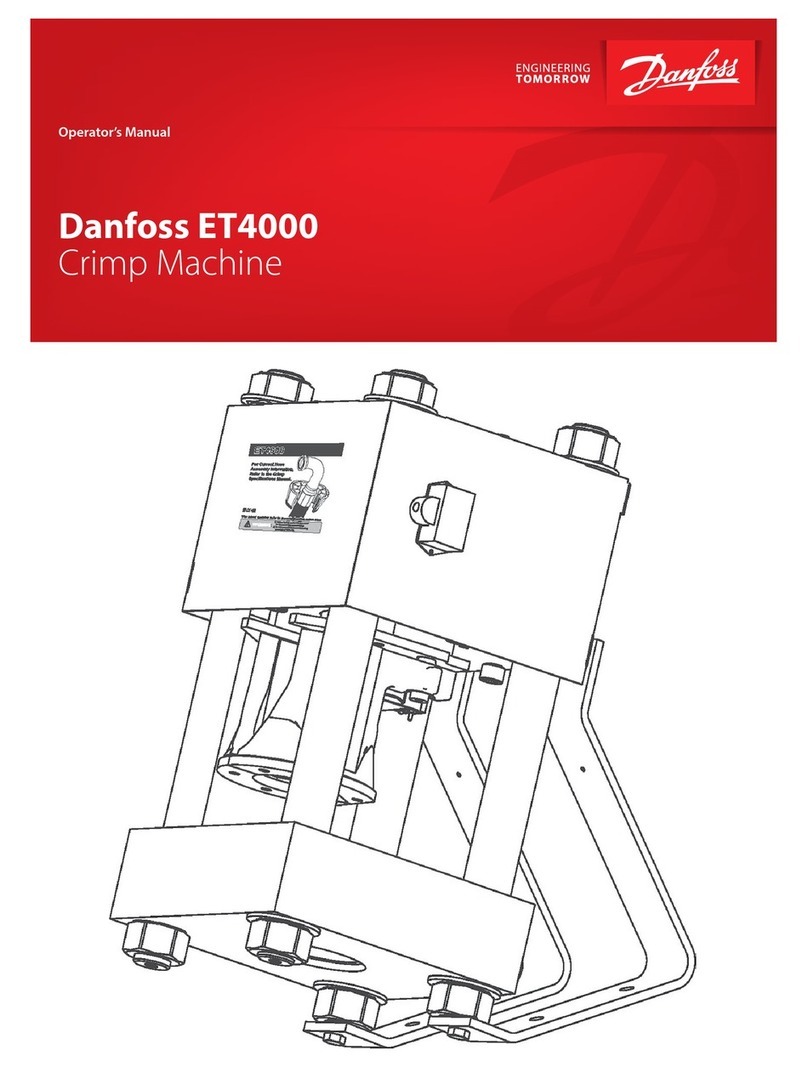
Danfoss
Danfoss ET4000 User manual
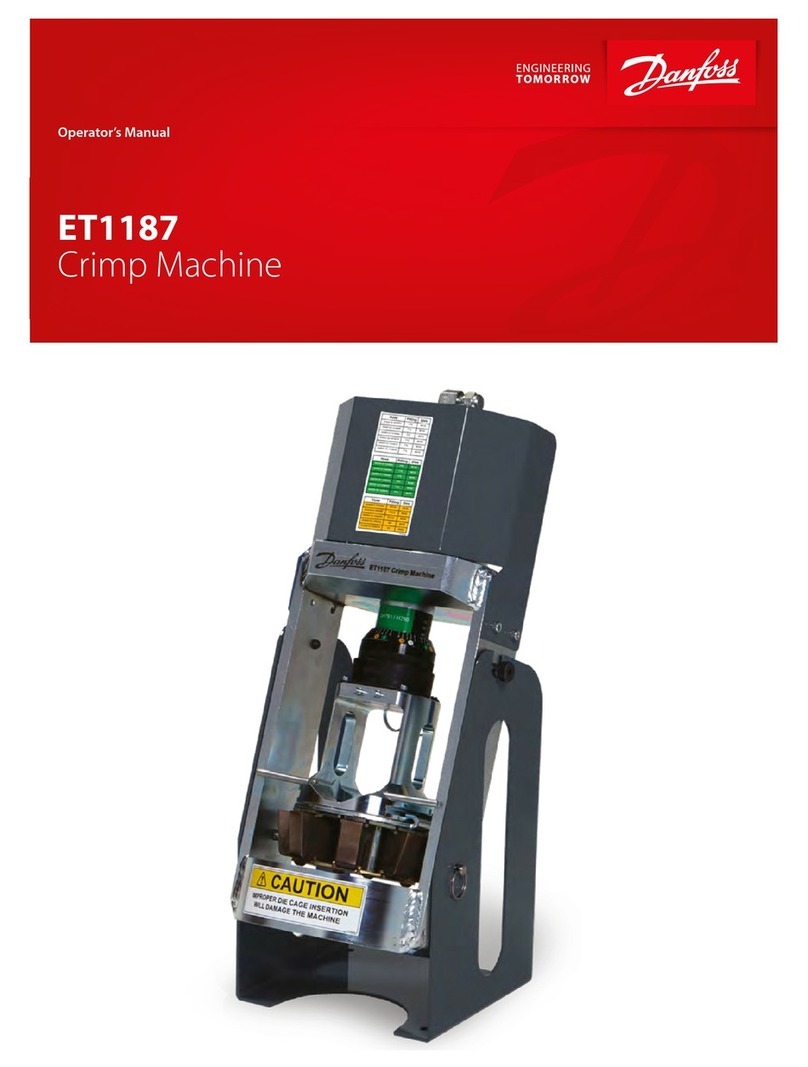
Danfoss
Danfoss ET1187 User manual
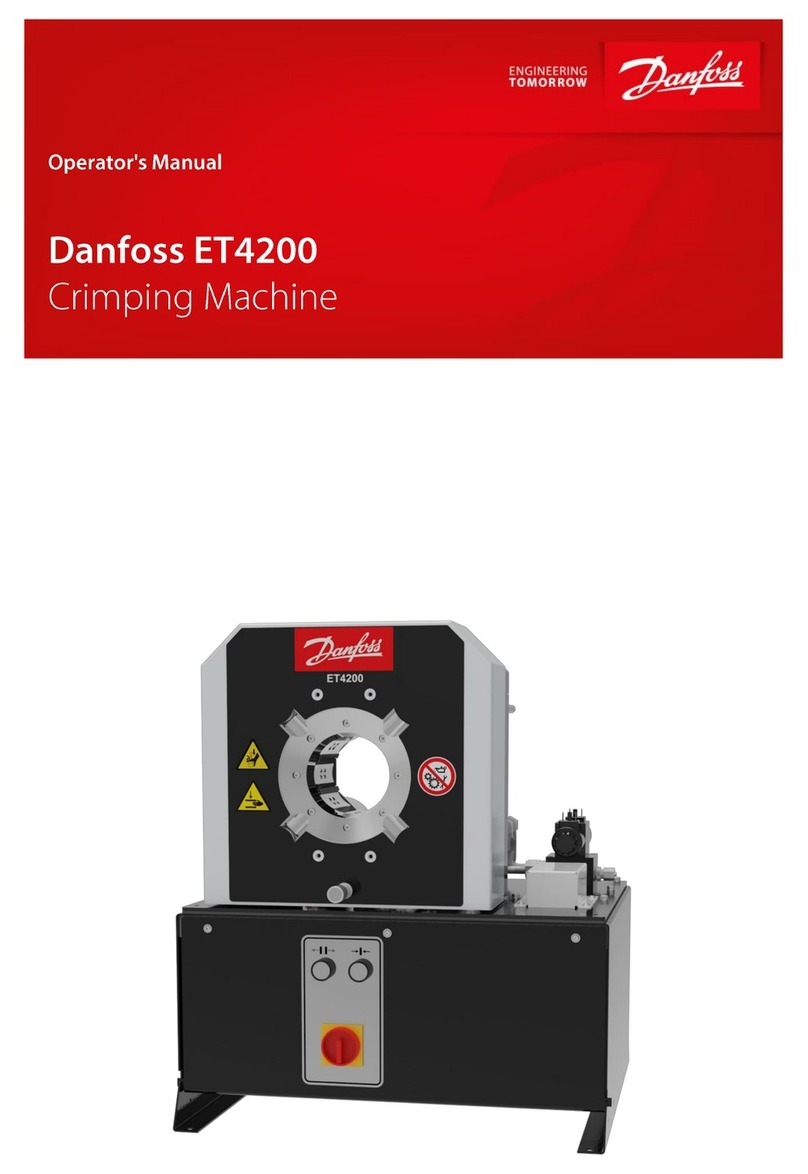
Danfoss
Danfoss ET4200 User manual
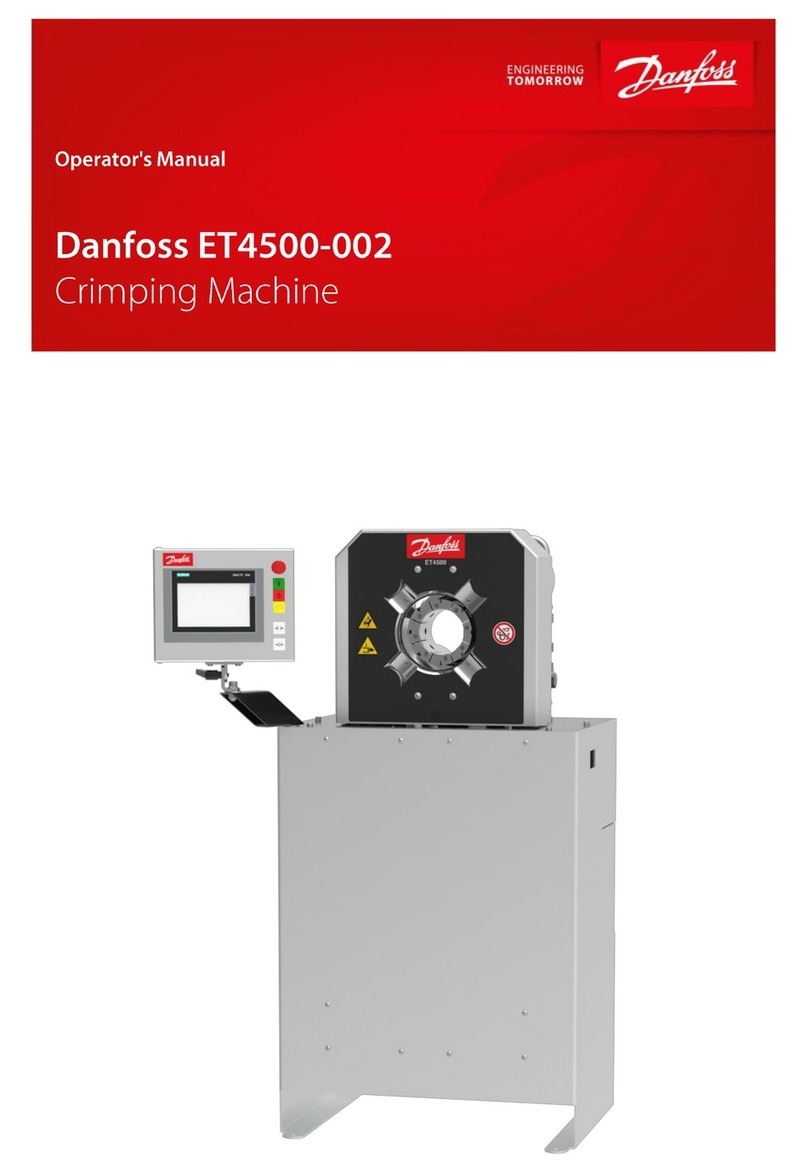
Danfoss
Danfoss ET4500-002 User manual
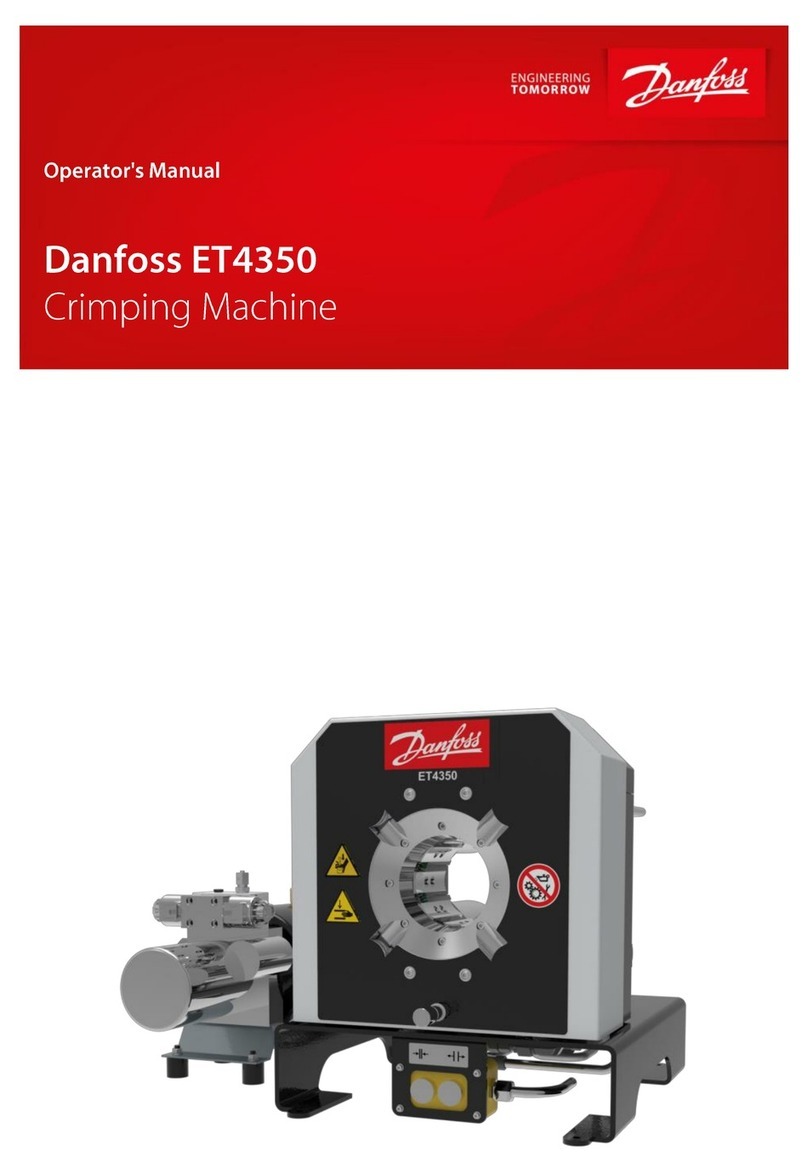
Danfoss
Danfoss ET4350 User manual
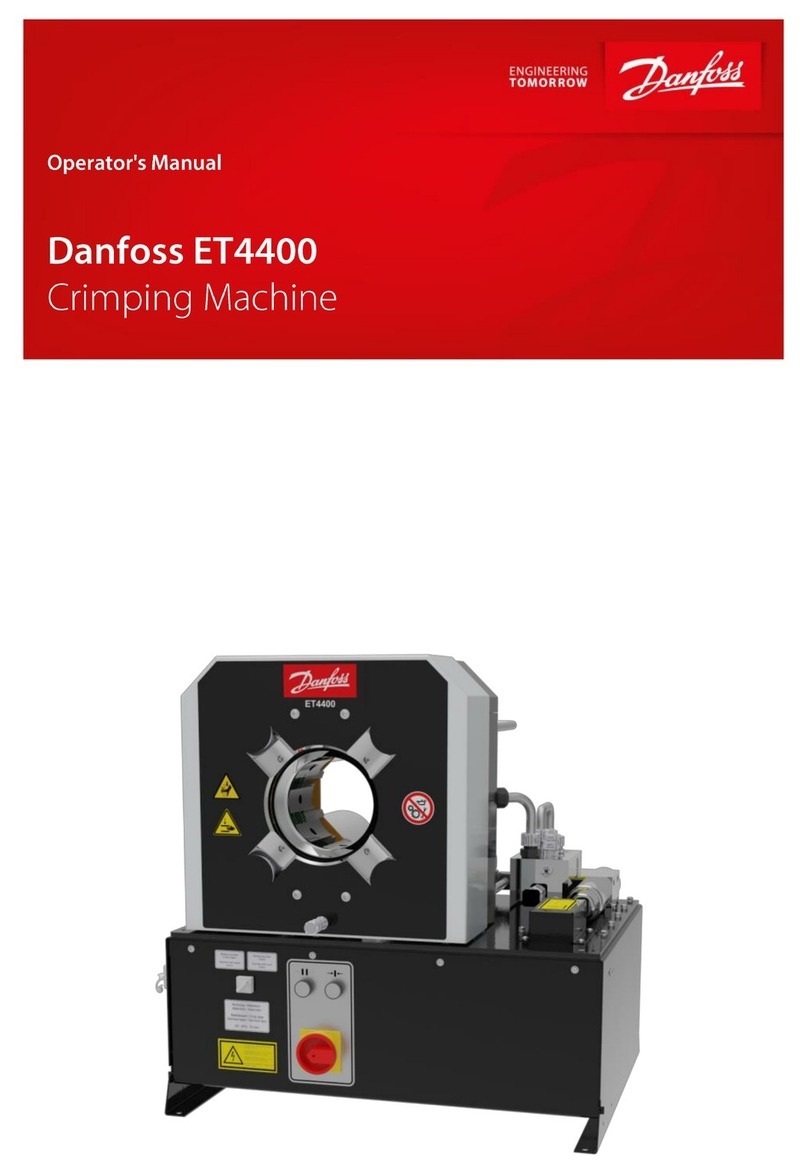
Danfoss
Danfoss ET4400 User manual
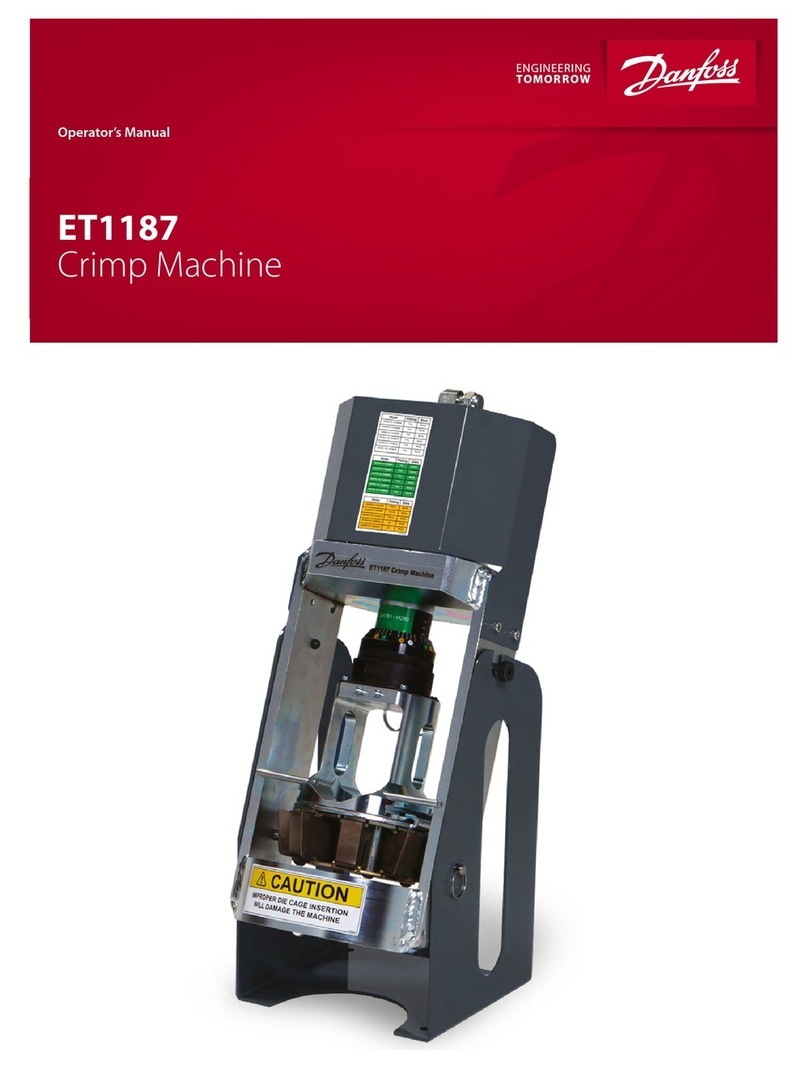
Danfoss
Danfoss ET1187 User manual
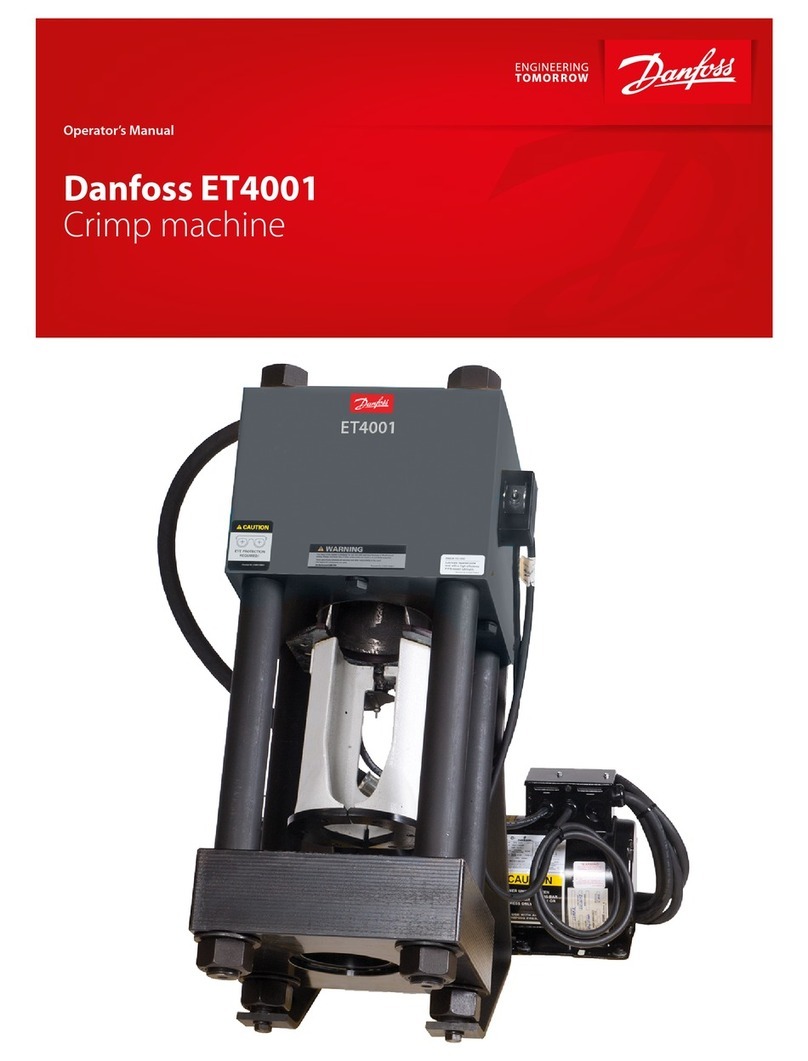
Danfoss
Danfoss ET4001 User manual
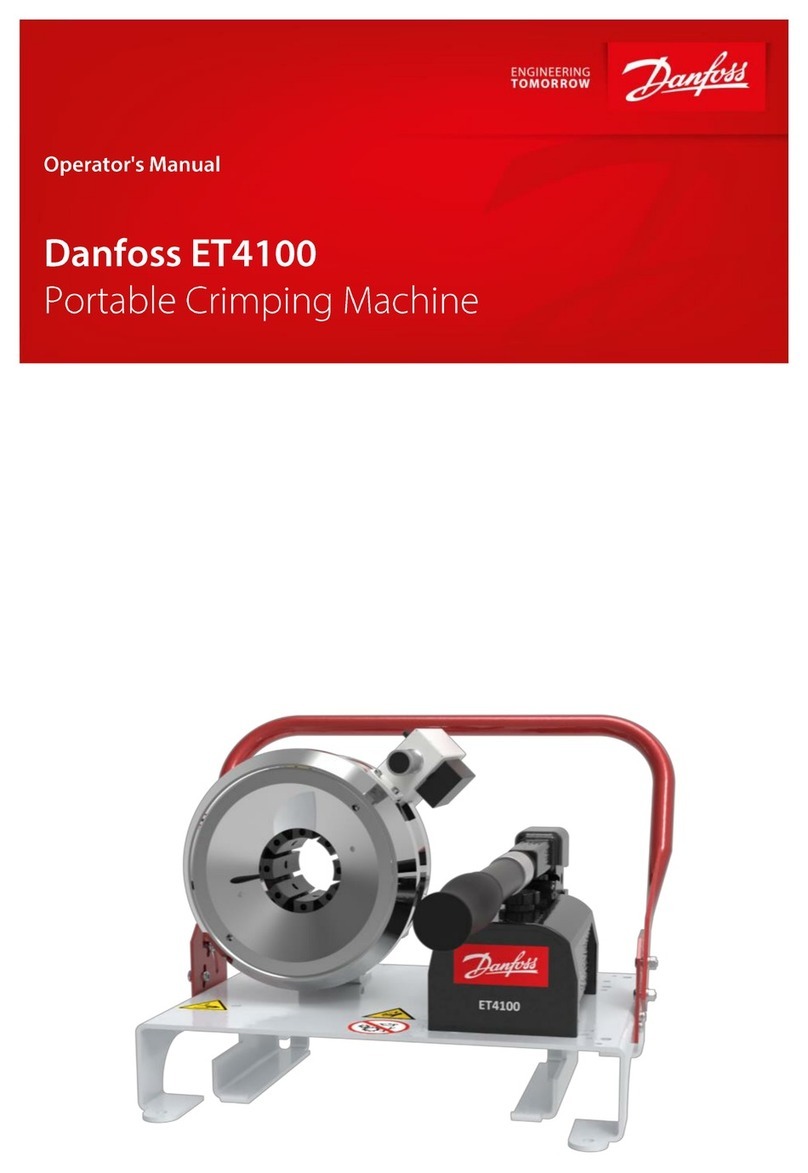
Danfoss
Danfoss ET4100 User manual
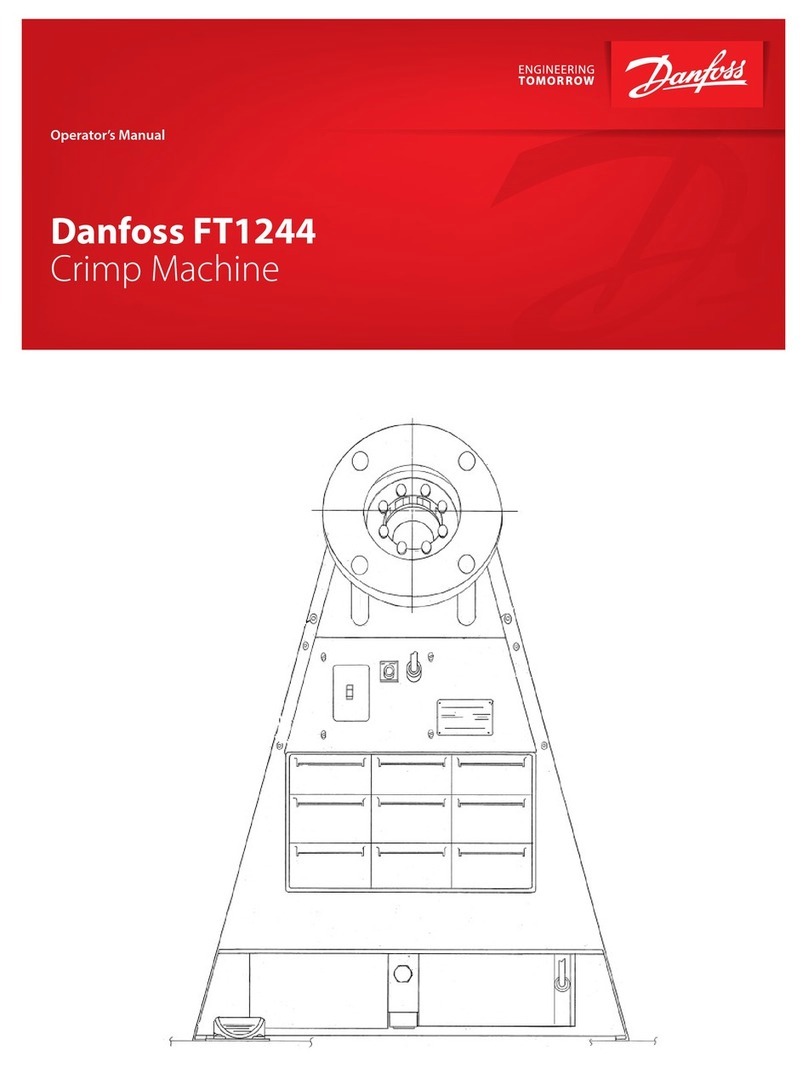
Danfoss
Danfoss FT1244 User manual
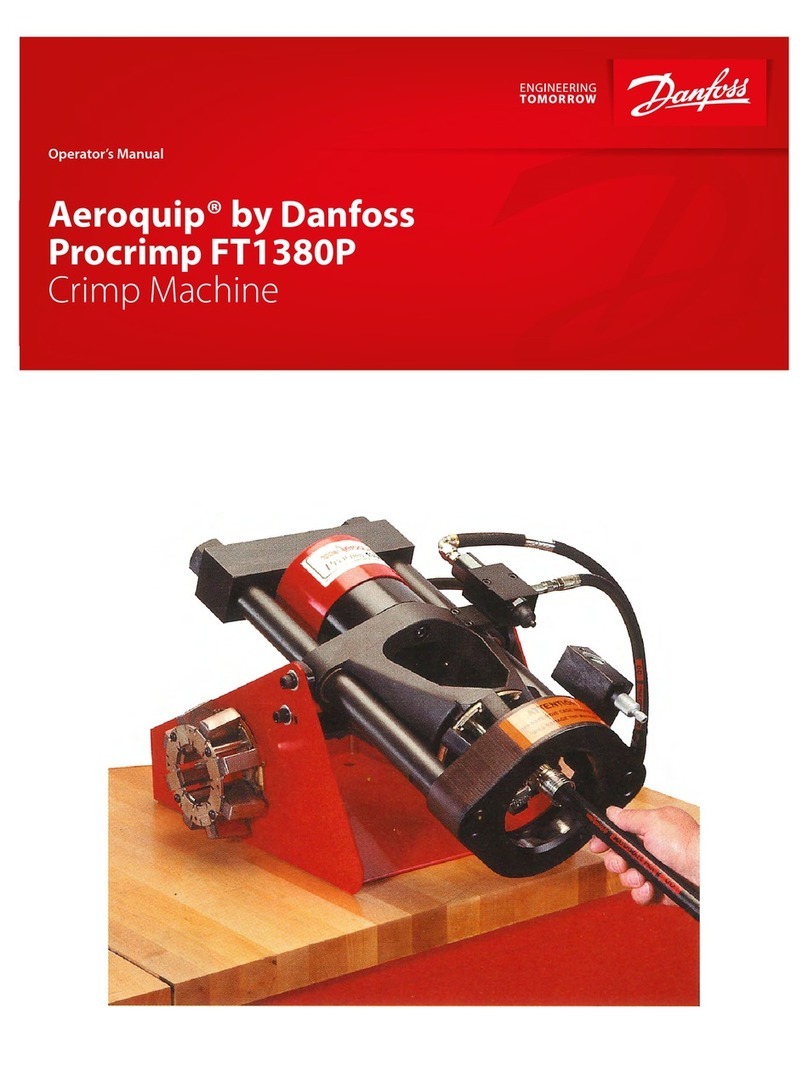
Danfoss
Danfoss Aeroquip FT1380P User manual
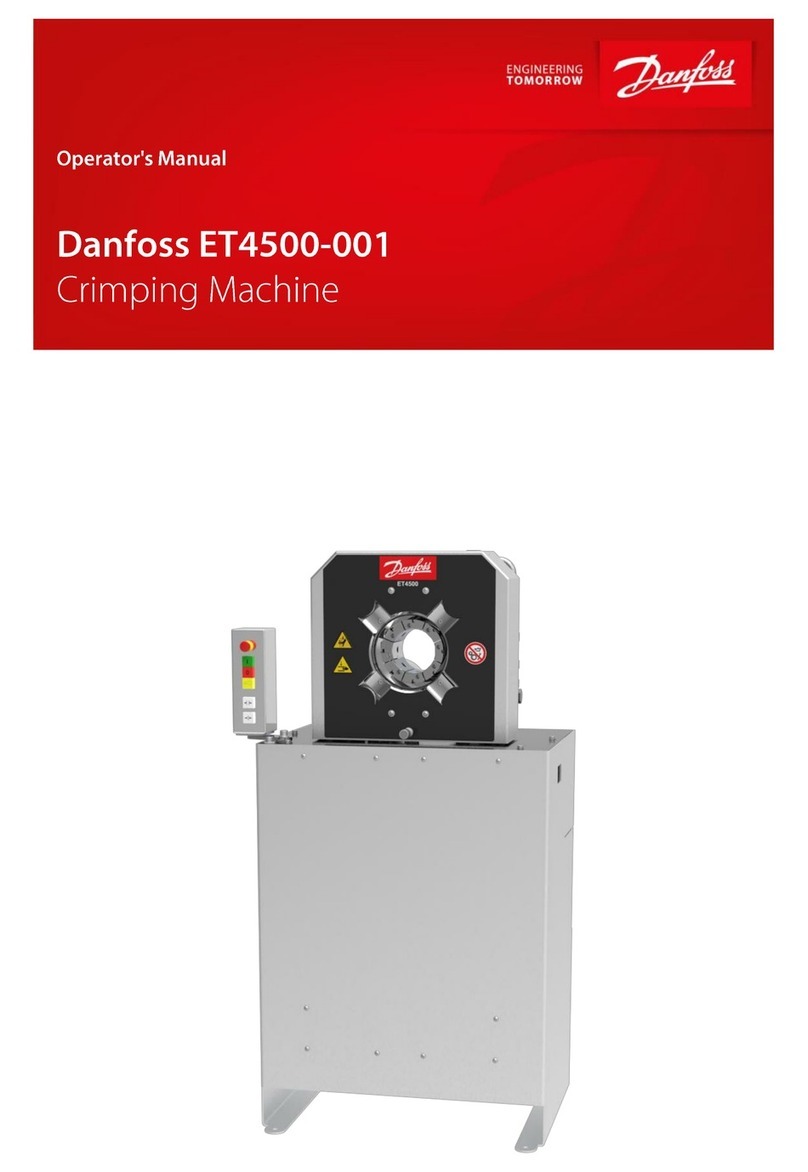
Danfoss
Danfoss ET4500-001 User manual
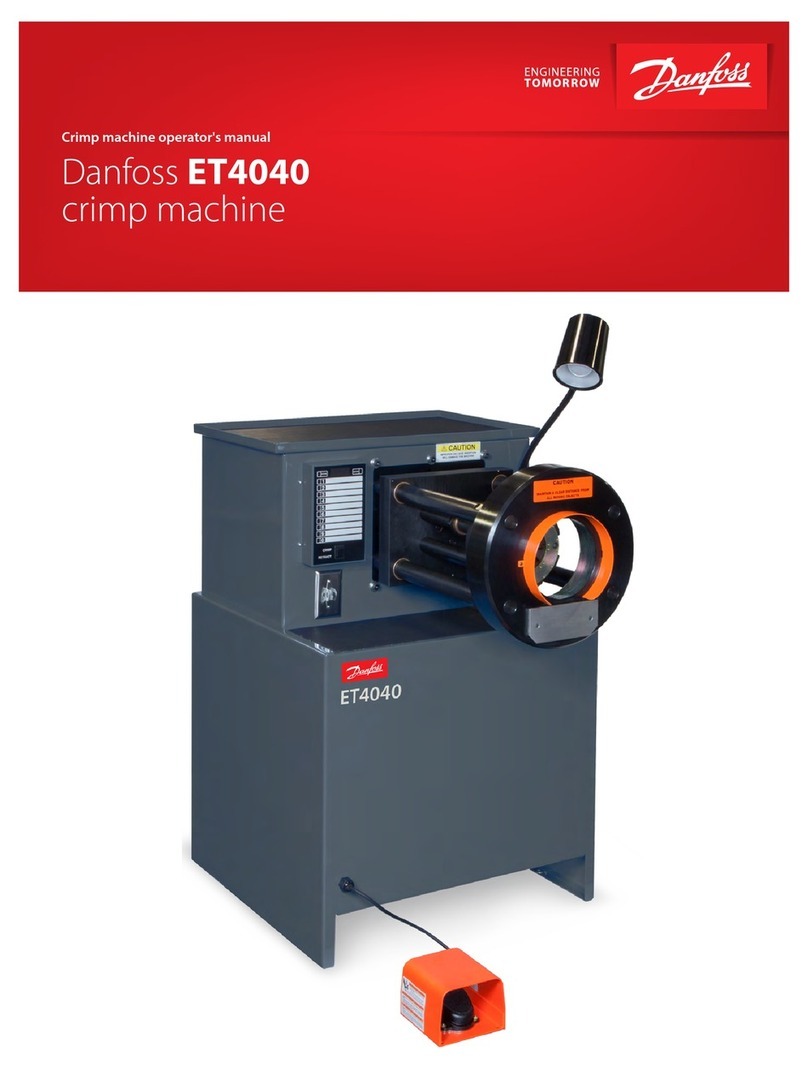
Danfoss
Danfoss ET4040 User manual
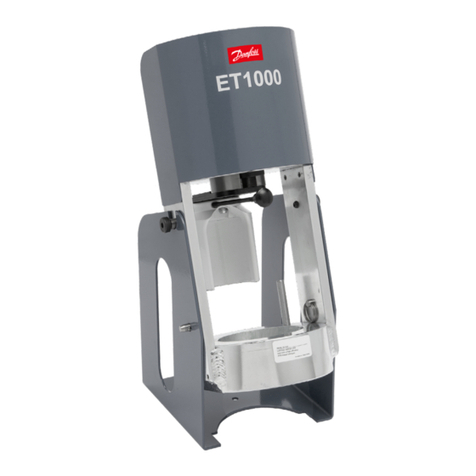
Danfoss
Danfoss ET1000 User manual