Datong Autosun Power Control YSD OT2106A Guide

Installation and Use Manual
Datong Autosun
Power Control Co.,LTD
OT2106A
Electronic Engine Governor
Speed Controller

OT2106A Electronic Engine Governor Speed Controller
1
目 录
SAFETY PRECAUTIONS....................................................................................................................2
一、OVERVIEW.........................................................................................................................................1
1.1 OUTLOOK............................................................................................................................................ 1
1.2 DESCRIPTION.......................................................................................................................................1
1.3 APPLICATIONS..................................................................................................................................... 2
1.4 FUNCTIONS.......................................................................................................................................... 3
1.5 SPEED AND SPEED FREQUENCY.......................................................................................................... 3
1.6 RELEVANT DEVICES............................................................................................................................ 4
二、SPECIFICATIONS......................................................................................................................... 4
三、INSTALLATION.............................................................................................................................. 4
3.1 DISMOUNTING..................................................................................................................................... 4
3.2 INSTALLATION REQUIREMENTS...........................................................................................................4
3.2.1 Installation order................................................................................................................. 5
3.2.2 Power requirements............................................................................................................. 5
3.2.3 Requirements for the installation location........................................................................ 5
3.3 INSTALLATION DRAWINGS AND ELECTRICAL CONNECTION DIAGRAM................................................ 6
3.3.1 Connecting Wires.............................................................................................................. 7
3.3.2 Electrical connection............................................................................................................8
3.4 INSTALLATION AND WIRING CHECK.................................................................................................... 8
3.4.1 Actuator installation check..................................................................................................8
3.4.2 Check electrical connections............................................................................................... 8
3.4.3 Speed sensor installation check.......................................................................................... 8
四、COMMISSIONING........................................................................................................................ 8
4.1 PRE-SET...............................................................................................................................................8
4.2 START ADJUSTMENT............................................................................................................................ 9
4.3 SPEED DROOP ADJUSTMENT.............................................................................................................. 11
4.4 GENERAL OPERATION....................................................................................................................... 12
五、PRINCIPLE....................................................................................................................................... 12
六、COMMON MALFUNCTION AND TROUBLESHOOTING.......................... 13
6.1 COMMON MALFUNCTION...................................................................................................................13
6.2 TYPICAL MALFUNCTION.....................................................................................................................14

OT2106A Electronic Engine Governor Speed Controller
2
Safety Precautions
Warning—Read the Instructions
Before installation, operation, commissioning or maintenance for this equipment, you should read the
full text of this manual, be familiar with all of the system components, operating procedures, safety
instructions, and related precautions. If you did not follow the requirements to perform operation and use,
may cause personal injury or property damage.
Warning—Overspeed Protection
The engine shall be equipped with a device being independent of the overspeed shutdown device to
protect against overspeed or damage to the engine resulting in personal injury or property damage.
Warning—Proper Use
Without the authorization of this product manufacturers and technical guidance, any unauthorized
modification of the system in machinery, electric or structure or use, may cause the damage to the product
itself, and even lead to personal injury or property damage.
Warning—Properly Shut Down
The electronic governor must be in the case of system power supply turned on to stop the engine
according the instructions; if illegal operation, directly turn off the power supply to carry out stop during
the engine operating, the engine is likely to arise uncontrolled serious accident, may cause property
damage or casualties. Solution to this problem is: linkage should contain a return spring, the spring force
size should be able to ensure that once the actuator power down, pulling the fuel delivery immediately to
the minimum position, making the engine shut down.
Warning—Battery Charge
Should ensure that the battery voltage of power supply of the product being within the specified
range. If the battery voltage does not meet requirements, this will result in the system not to work or run
unstable. Battery charging without delay should be given to ensure that the output voltage stability.
Warning—Prohibit directly using charger for power supply
When cutting off the connection of unit battery charger and the controller, the former output voltage
will exceed the latter power supply voltage range, so using the charger directly for the controller power
supply will cause permanent damage to the controller.
The Company reserves the right to modify any part of this manual. We guarantee that the information
provided in this manual is accurate and reliable, but unless otherwise expressly written commitment, the
Company assumes no responsibility.

OT2106A Electronic Engine Governor Speed Controller
3
Copyright © 2010 Autosun Company.

OT2106A Electronic Engine Governor Speed Controller
1
一、Overview
1.1 Outlook
The OT2106A electronic engine governor speed controller(controller for short) is made of metal and
consists of circuit boards inside. All the adjustable potentiometer of circuit boards are on the panel and marked
with printed label, the terminals are arranged at the front end of the controller. The real pictures were shown in
figure 1-1.
figure 1-1 real pictures of the controller
1.2 Description
Rated Speed Potentiometer: This is used for setting rated speed. At rated speed condition, it can make sure
that the engine speed is equal to the set value. When adjusting clockwise, speed increase; when
adjusting anti-clockwise, the speed reduced.
Start-up oil quantity potentiometer: for engine starting enrich. This feature is automatically enabled in the
engine startup process, when the startup is over, this function will be automatically replaced by
speed control function. Adjustment range: 25% to 100% of the controller output signal, turn
clockwise will increases the start-up oil quantity.
Stable potentiometer; Gain potentiometer; Compensation potentiometer: these three potentiometers are used
to adjust and correct the control characteristics of the amplifier circuit, so that the controller can adapt different
types of engine. Stable potentiometer is used to adjust the recovery time of dynamic process; Gain
potentiometer can adjust the biggest speed amplitude when the load has a sudden change; Compensation
potentiometer is used to adjust the response of actuators and the engine. All these three potentiometer increase
with clockwise adjustment, decrease with counter-clockwise adjust.
Rising time potentiometer: used to adjust the speed up time when the engine runs from the idle speed to the
rated speed. Adjusting range: 5 seconds ~ 35 seconds, it will increase with clockwise adjustment.
Idle Speed potentiometer: used to set the idle speed. In idle condition, it can make sure that the engine speed is

OT2106A Electronic Engine Governor Speed Controller
2
equal to the set value. Speed will increase when turning clockwise; Speed will decrease when turning
anti-clockwise.
Terminal 1, 2:18 VDC ~ 36 VDC 12W-- power supply, "-" is for negative, "+" is for positive.
Terminal 3: open: shutdown - shutdown switch. Open: actuator move to the minimum position, Closed: the
engine can normally operates.
Terminal 4: open: overspeed protection - overspeed protection switch. Open: activate the overspeed
protection function, when speed is over, the actuator move to the minimum position; Closed: overspeed
protection function is not available. When the drag speed is lower than the minimum control speed, the PID
controller circuit has not been working, It makes the controller output a start signal which is set by start-up oil
quantity .
Terminal 5: Closed: rated speed-- idle/rated switch. Closed: the rated speed; Open: idle speed.
Terminal 7, 8: Speed input--speed signal input. The input range: 1 ~ 30 VRMS (ac voltage RMS, RMS
means square), regardless of polarity.
Terminal 9,10: Position output - the position signal. Output to the driver, '-' is for negative, '+' is for
positive.
Terminal 11, 12: speed trim – speed trim potentiometer is more than 100 Ω.In differential mode, it can be
used to complete a manual synchronization or add and subtract load.
Terminal 13,14,15: differential rate - more than 2 k Ω circle rate potentiometer. They are used to adjust rate.
Terminal 6: spare - manufacturer reserves, no electrical connections.
Terminal 15,16: synchronizer signal input--provide for synchronizer, It is used in the speed and phase
matching.
Terminal 15, 17: load distributor signal input - load distribution wire and connected with other similar
controllers distribution line.
Note: differential rate and speed trim should be set within the reference speed of 10% / V.
1.3 Applications
Controller is mainly used for speed control of diesel engine, gasoline engine, gas machine (engine as
general designation). The engine controlled by the controller is only used for driving a generator and make up
generator sets (generators for short) with the controller. It could be used in three types application: single,
parallel with another machine and parallel in network.
The controller is a component of the system, the relationship with the application system is shown in
figure 1-2.

OT2106A Electronic Engine Governor Speed Controller
3
Motor
Actuator
Engine
Speed Sensor
Controller
Generator
figure 1-2 The relationship with the application system
1.4 Functions
The controller is the core component of the engine speed control function, controlling the whole process
of engine operation: start, idle, acceleration, rated, load/unload and so on. there are two control modes for
engine speed in response to load changes: no differential mode and differential mode. In addition, the
controller also has a normal shutdown, startup enriched fuel control, setting the speed protection value, output
overload protection.
1.5 Speed and Speed Frequency
The engine speed is described by gear teeth (tooth frequency) which is detected by the engine speed
sensor ;
Through speed sensor, Speed controller perceives the engine speed characteristics;
The control target is frequency (Hz) signal output by speed sensor, rather than the speed (r / min) of
engine crankshaft;
The engine speed (r/min) is proportional to the voltage signal frequency sensed by the sensor. The
frequency is called speed frequency (Hz). Each speed sensor output feature frequency (Hz) which was convert
proportionally from each feature speed (r/min), such as idle speed (r/min), rated speed (r/min) was
correspondingly called idle frequency (Hz), rated frequency (Hz), etc.
The relationship between speed and the speed frequency: f = n * z / 60. And n is the engine speed (r /
min), z is the flywheel teeth.

OT2106A Electronic Engine Governor Speed Controller
4
1.6 Relevant Devices
Drives, actuators, sensors are relevant devices, they are used together with the controller. For details, see the
drive, actuators, sensors manual.
二、Specifications
Power supply voltage: 20 ~ 32 VDC
Power: 12 W
Speed Frequency range: Select the following four speed frequency ranges through DIP switches on the
board
500 ~ 1500 Hz 2000 ~ 6000 Hz
1000 ~ 3000 Hz 4000 ~ 12000 Hz
Speed input signal: 1 ~ 30 Vrms, input AC impedance 1000 Ω / kHz, DC resistance of 300 Ω
External speed trim: 100Ω potentiometer, providing ± 5% of the speed of adjustment
Raising speed time: 5 ~ 35 s
Output position signal: 0 ~ 200 mA, load impedance 30 ~ 45 Ω
Actuator Compensation: time constant adjustment range is 0 ~ 500 ms
Differential rate: 0 ~ 8% 2000Ω potentiometer
Application temperature range: -40 ~ +85 ℃
Storage temperature range: -55 ~ +105 ℃
Relative Humidity: 38 ℃95% when
Vibration and shock: 4 Gs vibration frequency range 5 ~ 500 Hz; Shock 60 Gs
Weight: about 1.2 kg
三、Installation
3.1 Dismounting
Before unpacking, please check the label on the box, check whether the product is consistent with the
order and make a record, if there is any question, please contact the supplier immediately.
After opening the package, carefully inspect the controller housing for deformation, scratching, loosing or
any component damaged and so on. If there is any question, please contact the supplier immediately.
3.2 Installation Requirements

OT2106A Electronic Engine Governor Speed Controller
5
3.2.1 Installation order
• set the speed frequency range switch, see 3.3.1;
• Installing the controller, see 3.2.3 and figure 2-2;
• Electrical connection, see 3.3;
• Check the installation, see 3.4.
3.2.2 Power requirements
The controller requires a power supply of 18VDC ~ 36VDC, 12W DC. There is an internal DC / DC switching
power supply, which need surge to start. A low-output impedance power supply (for example, using storage
battery directly for power supply) is required and the controller power on and off by a power switch adopted at
the terminal 2 to meet the switching power timing requirements. The AC - DC converter power supply is not
recommended. For the correct power connection , see figure 3-1.
figure 3-1 correct power connect
WARNING: If you use the battery to power the controller, a charging device shall be equipped to maintain a
stable voltage supply and make sure that the controller is not connected solely with the charging device. Before
removing the battery cables, you should turn off the charging device first, avoiding controller damage from the
charging device.
3.2.3 Requirements for the installation location
When selecting the installation position of the controller, please consider the following conditions:
• conducive to air cooling;
• Having adequate space for easy operation and maintenance;
• Avoid installing near water or easy to form water vapor environment;
• away from high-voltage, high-current cables, or equipment which is easy to produce electromagnetic
interference;
• Installation position can not have violent vibration;
• surrounding temperature is within the specified range: -40 ° C ~ + 85 ° C.
Note: Do not install the controller on the engine

OT2106A Electronic Engine Governor Speed Controller
6
3.3 Installation drawings and electrical connection diagram
Controller installation outline is shown in figure 3-2. Electrical connection is shown in figure 3-3.
figure 3-2 Controller installation Outline Drawing

OT2106A Electronic Engine Governor Speed Controller
7
figure 3-3 Electrical connection
3.3.1 Connecting Wires
Cable W4 ~ W8 wire core area should not be less than 1.5 mm2, if the length of the line increases, the
cable area should also be increased in order to meet the requirements.
All signal lines should be shielded to prevent electromagnetic interference signals picked up from nearby
equipment. All shielded should use twisted pair wire.
The shielded cable is connected to ground terminal of the housing below the terminal 9, with length no
more than 5cm. Make sure there is a conductor connecting controller terminal and the earth terminal or

OT2106A Electronic Engine Governor Speed Controller
8
system designated joint, make sure electrical connection is reliable, so that the housing is grounded. The
stripped length of shielding wire should be as short as possible, preferably not more than 15cm. The
other end of the shielded wire left open and insulated from other conductors. Shielded cable should be
arranged to avoid the strong current and high voltage cables.
Generally, special cable provided by the manufacturer is suggested for use.
3.3.2 Electrical connection
Connect the relevant equipment as figure 3-3, including: power, overspeed protection switch, high / low
speed switch, speed sensors, actuators, speed trimmer potentiometers, speed droop potentiometer ect.
3.4 Installation and wiring check
3.4.1 Actuator installation check
Check whether or not the connection between the actuator and the engine is loose or catching, if so,
please exclude. For details about the connection, please refer to the "actuator using the installation
instructions."
WARNING: When the engine is idling, the position of actuator arm should be in the vicinity of the
minimum position (counterclockwise in the end) This is to prevent danger occurs when the engine can not
stop.
3.4.2 Check electrical connections
According to Figure 3-3 , check whether the electrical connector is correct ; and check the shield wire is
connected to the ground terminal below the 9th terminal.
3.4.3 Speed sensor installation check
Check whether the speed sensor is damaged, check whether the gap between sensor probe and the engine
gear top surface is within the normal range of 0.25mm ~ 1.0mm.
Note: roundness tolerance of the sensor detected engine gear surface can not be greater than 0.01mm. For
instructions, see "magnetic speed sensor using the installation instructions."
四、commissioning
The first time you use the controller, you need set and adjust each parameter to the best control effect
according to the engine feature. The following will teach you the steps and methods of how to match the
controller and the engine, the role of each adjustment potentiometer and calibration methods.
4.1 Pre-set
Warning: When setting up the control system, overspeed may result in equipment damage and personal injury.
Before starting the engine for the first time, please read the start-up procedures.
WARNING: On the control panel, only the rated speed potentiometer is the multi-turn potentiometer, others
are single-turn potentiometer. Do not set these potentiometers rotation range beyond their limits.

OT2106A Electronic Engine Governor Speed Controller
9
(1) The rated speed potentiometer: Set the rated speed potentiometer at minimum (ten turns
potentiometer, counterclockwise to the end).
(2) Stability potentiometer: Set the stability potentiometer in the middle position (one turn potentiometer).
(3) Gain potentiometer: Set it in the middle position (one turn potentiometer).
(4) Rising time potentiometer: Set at minimum (one turn potentiometer, counterclockwise to the end).
(5) Idle speed potentiometer: Set at minimum (one turn potentiometer, counterclockwise to the end).
(6) Start-up fuel quantity potentiometer: Set at maximum (one turn potentiometer, clockwise to the end).
(7) Compensating potentiometers (one turn potentiometer): Set in the scale 2 position;
(8) Speed trim potentiometer: If an external speed trim potentiometer is used, set it in the middle position.
(9) droop potentiometer: If an external speed droop potentiometer is used, set it to the minimum value
(one turn potentiometer, counterclockwise to the end).
Make sure that the actuator has been connected with the terminal 9 (+) and terminal 10 (-).
4.2 Start adjustment
Before starting the engine, make sure the installation, connection, and the pre-set are correct.
Note: Make sure the controller speed set range is within the actual needs of the engine work. Emergency
stop devices should be prepared to prevent overspeed or personal property damage when starting the engine.
(1) Stability adjustment:
If the engine is in a steady state, skip this step and directly adjust the rated speed.
If the engine is seriously unstable, then slowly lower the gain (gain potentiometer,
counter-clockwise) until the engine is stable. Adjusting the gain potentiometer will change the
speed immediately, so the adjusting process should be slow.
If the engine is slightly unstable, increase the value of stability setting (stability potentiometer,
clockwise) until the engine is stable. If increasing the value of stability potentiometer setting can
not make the engine stable, you need make the following adjustments at the same time:
Slowly lower the gain (gain potentiometer, counter-clockwise);
Slowly lower gain and increase compensating potentiometers (clockwise rotation compensation
potentiometer).
(2) Rated speed adjustment:
when the engine is running in a steady state, (if an external speed trim potentiometer is used, turn
it in the middle position), adjust the rated speed potentiometer slowly, the speed will increase

OT2106A Electronic Engine Governor Speed Controller
10
when adjusting clockwise, otherwise speed will be reduced when adjusting counterclockwise;
Make the engine speed reaches rated speed.
(3) Dynamic adjustment:
Adjust the gain and stability potentiometer is to obtain a stable or optimum engine speed
response.
Increase the gain potentiometer can achieve faster transient response, reducing the speed droop
rate (the ratio of speed variation and load variations which cause the speed change).
To get the best response, the pre-adjusted should be made first. Slowly increase the gain
potentiometer (turn the potentiometer clockwise) until execution begins a slight instability, then
slowly returned a little in the opposite direction, until the engine regain stability; and then increase,
reduce the load or touch actuators rod in a stepwise manner, the observed the amplitude of speed
change, overshoot and recovery. If there is significant overshoot, the value of stability should be
appropriate increased. If the stability potentiometer is in the low range region of 0 to 3 scale at
this time, gain potentiometer should be reduced at the same time;
If the engine response slowly in the process returns to the appropriate speed, then
counterclockwise rotate stability potentiometer to lower stabilizing value.
NOTE: Generally you do not have to turn the gain potentiometer to maximum to get the best
dynamic characteristics. Sometimes, the gain should be slightly reduced, in order to ensure the
stability under various conditions change.
(4) Compensation adjustment:
If the engine continues periodic slight unstable running, you should slowly increase actuator
compensation (compensating potentiometer, clockwise), and then re-adjust the gain and stability
potentiometer, repeat adjustments until the engine is stable.
If the engine continues serious unstable running, or actuator is very sensitive (there is obviously
instability), then slowly lower the actuator compensation (compensation potentiometer,
counterclockwise). If the actuator is still swing, turn it to the minimum.
(5) idle adjustment:
1. First set the idling potentiometer at the maximum position (clockwise to the maximum position,
note that the potentiometer is 1-turn potentiometer, do not over-rotation), disconnect the external
idle / rated speed switch, so that the engine runs near the rated speed.
2. Reduce the idle speed setting (turn the potentiometer counterclockwise) to the required idle
position.
If the rated speed potentiometer setting position is changed, the idle setting will change too. But
the idle setting change will not make an effect on the rated speed setting.
Note: When the engine is idling, make sure that the output of the actuator motor corner is in the

OT2106A Electronic Engine Governor Speed Controller
11
effective angle range.
(6) rising speed time adjustment:
Appropriately adjust the rising time potentiometer so the overshoot from idling state to rated state
will be minimal. If you start for the first time, you can turn it clockwise to the maximum position,
then return to the proper position. When the speed changes from idle to rated, the acceleration
time can be adjusted between 5-35 seconds. Adjusting potentiometer clockwise, acceleration time
become longer; otherwise, time is shorter.
(7) Start-up fuel quantity adjustment:
When the engine runs at rated speed with empty load, record the terminal pin 9 (+) and 10 (-)
voltage, and then shut down the engine, close the switch on the terminal 4, mask overspeed
protection function, adjust start oil potentiometer , measure the terminal pin 9 (+) and 10 (-)
voltage until the voltage is 30% higher than the rated no-load voltage (record value).
Restart the engine and observe the start time, speed overshoot and smoke intensity. If the
requirements are satisfied, the start-up fuel quantity potentiometer settings would be appropriate;
otherwise, it should be appropriately reduced. If the engine can not start up, then slowly turn
clockwise start-up fuel quantity potentiometer until the engine starts up.
In order to optimize engine starting characteristic, the start-up fuel quantity potentiometer can be
appropriately adjusted. When the speed controller is in the speed control state, the start-up fuel
quantity control will lose its function.
Note: For the engine which does not need start-up fuel quantity control, the potentiometer should
be turned clockwise to the maximum position to turn off this feature (be careful not to
over-rotation potentiometer).
4.3 Speed droop adjustment
Transfer rate is usually expressed as a percentage, it can be calculated by the following formula:
100%
emptyspeed
eedfullloadspemptyspeed
speeddroop
Speed droop adjustment depends on the applications: stand-alone, parallel with another or more, and
parallel with the network.
In most stand-alone applications, speed droop is not important. If the engine needs to run in the speed
droop mode, but the value of droop is not important, then, you should turn the speed droop potentiometer in
the middle position, then use the speed trim potentiometer to adjust the load.
When two or more generators parallel (make up a large generating units), and a local area power
generating unit network is built, the frequency of the local area generating network will change with the size of
the load. In this case, all the generators should have a same speed droop value.

OT2106A Electronic Engine Governor Speed Controller
12
When the generator parallel with unlimited network, the network frequency does not change. In order to
keep the operating stability, speed droop mode must be used. Turn the speed droop potentiometer in the middle
position, parallel generators with the network, and increase the speed trim potentiometer (or rated speed
potentiometer) until the engine meets the required load capacity.
If speed droop control is excessive, the engine will run overspeed when suddenly unloading, meanwhile,
it may also lead to engine response lag respect to the load; If speed droop control is too small, the engine may
be unstable, similar to improper adjustment of gain and stability potentiometers.
For an isolated power generators, usually setting the speed droop rate to a specific value is necessary, to
prevent excessive overspeed when the load changes.
4.4 General Operation
1. closed normal shutdown switch, disconnect the rated speed switch;
2. If the drag speed is less than the minimum control speed, close the overspeed protection switch,
otherwise cut off the switch;
3. Set the speed trim potentiometer in the middle position (when commissioning);
4. Close the power switch to power up the speed controller and actuator;
5. Drag the engine and start;
6. Run the engine into idle state, cut off the overspeed protection switch, wait for the cooling water,
lubricating oil reach the required temperature;
7. Close the rated speed switch, the engine accelerates to the rated speed;
8.If running stand-alone, close load switch in groups and load;
If paralleling with others, adjust the speed trim potentiometer, synchronize with other generators,
parallel and share the load;
If paralleling with network, adjust the speed trim potentiometer, s synchronize with network, parallel and
share the load;
9. Turn speed trim potentiometer counterclockwise or cut off load switch one by one until load is empty,
off network;
10. Disconnect the rated speed switch so that the engine runs to idle state;
11. Shutdown: stop oil supply or stop gas supply or cutoff shutdown switch;
12. Turn off the power switch, turn off the power.
五、Principle
The engine control system is made up of speed sensor which was connected to the engine flywheel
housing and the actuator which was used to control on oil supply, etc. All of device together complete the
precise control of the engine speed. Speed control system structure is shown in figure 5-1.

OT2106A Electronic Engine Governor Speed Controller
13
figure 5-1 Speed control system structure
The controller includes speed signal processing circuit, the reference setting circuit, PID error processing
circuit, the correction amplifier circuit, signal loss protection and output protection circuit. Its principle of
work is that: first it receives speed signal from magneto electric sensor. After processing and transform, it
compares with reference signal and then generate error signal. After PID operation on this error signal,
regulation voltage is formed. After being amplified, this regulation voltage is used to drive actuator for
achieving control.
Besides, inside the controller there is speed signal loss protection circuitry to monitor the speed signal
input. Once the signal is not detected, the controller immediately reduce outputs control signal to the minimum
fuel supply amount, then the actuator response the signal and turn the fuel supply flow rate to minimum
position, forcing the engine to stop.
To protect the controller from being shorted or overloaded, a automatic circuit breaker is set in the output
circuit. After the short circuit or overload is repaired, circuit breaker automatically recover. During the open
circuit protection, the overheating circuit will be cooled so that the output position signal is 0, forcing the
engine to stop.
六、Common malfunction and troubleshooting
6.1 Common malfunction
Improper operation is usually the main reason of various engine malfunction. When a malfunction occurs,
you should first check whether the engine itself is in a good state. Therefore, you should first separate control
system from the engine, and then determine the real cause of the malfunction.
Based on the using time, the cause of the controller malfunction can be divided into following two
situations:
1, use for the first time, following reasons are tipical:
(1) Power supply: The system is not receiving power or reverse polarity or the power does not meet the
requirements;
(2) Installation and connection: improper mechanical installation or incorrect electrical connections; bad

OT2106A Electronic Engine Governor Speed Controller
14
linkage between the actuator and the engine throttle;
(3) Signal: Speed sensor installation space does not meet the requirements; incorrect wiring or
shielding problems;
2, If the system has been running for quite long time, the reason of malfunction is usually:
(1) Connectors loosing;
(2) Speed sensor loosing; the gap does not meet the requirements or damaged; mechanical linkage serious
wear and tear;
(3) Wire aging;
Check and confirm item above one by one, if the malfunction still exists, Please do as the following
procedure.
6.2 Typical malfunction
Typical malfunction list is shown in table 6-1.
Table 6-1 Typical malfunction and solution
Phenomena
Probable cause
Processing method
The engine
cannot started up,
the actuator does
not move to the
start fuel supply
position
Governor power is
connected inversely or
too low.
Check whether governor power is connected inversely
or too low..
Actuators does not
respond on the input
signal from the
controller
If there is a voltage output between the terminal 9 and
terminal 10, but the actuator does not move, you should
check whether the actuator wiring is open or shorted.
Check whether the input resistance between terminal
9 and terminal 10 when the drive is not connected is about
35Ω.
Start-up fuel quantity
set value too low
Turn start-up fuel quantity potentiometer clockwise until
the engine starts
Check whether the actuator is installed correctly,
worn and well-connected.

OT2106A Electronic Engine Governor Speed Controller
15
The engine
cannot started up,
the actuator does
not move to the
start fuel supply
position
When crankshaft
rotates, there is no
position output
signal between
terminal 9 and
terminal 10
1When crankshaft rotates, detect whether the
voltage between the terminal 7 and 8 has reached
the minimum 1Vrms, whether the minimum
frequency range is within the range of 30Hz to
80Hz.
If the above condition cannot be reached, closed
terminal 4 switch, masked overspeed protection function.
2Stop the rotation of the crankshaft. Remove the
wiring on terminal 9 and 10, check whether the
actuator wire shorted or grounded. Closed
terminal 4 switch, so that the terminal 11 and 12 is
shorted. Check whether the voltage between
terminal 9 and 10 is between 18 to 22V.
3Check whether the speed sensor position is too
far away from the gear; whether the speed sensor
wiring and shielding is correct; whether the ends
of the sensor is attached to a metal or other matter.
4If the speed is lower than the set value during
the startup, you should turn the rated speed potentiometer
clockwise to increase the setting.
If clockwise adjustment does not produce the correct
output signal, you need to reset the rated speed
potentiometer to the maximum position counter-clockwise.
Idling potentiometer set
value is too low
Adjust the idle speed potentiometer clockwise.
shutdown switch is
turned off
Check switch of terminal 3. Normally, the shutdown
switch be closed.
There is problem in
shutdown switch or
wire
Check whether the voltage between the controller
terminal 2 (+) and terminal 3 (-) is between DC 0 to 3V.
Speed sensor does not
provide signal to the
controller
Check whether the speed sensor wiring is properly
connected; whether speed sensor is open or short; whether
the shielding wire is properly connected.
Disconnect the connection between the speed sensor
and the controller, check whether the speed sensor output
resistance is between 100 to 300Ω.
terminal 11 and 12 are
open
If an external speed trimming potentiometer is not
used, you should confirm that the terminal 11 and 12 are
short-circuited.

OT2106A Electronic Engine Governor Speed Controller
16
The engine
cannot started up,
the actuator does
not move to the
start fuel supply
position
Check the voltage between terminal 11 (+) and12
(-)(the voltage should be less than 2V).
Speed trimmer
potentiometer is broken
Cut off the power supply, use an ohmmeter to check
the speed trimmer potentiometer.
Overspeed only
happens when
engine the start up
The value of rising
time potentiometer is
set too small
Clockwise increases rising time potentiometer to
lower accelerating rate (from idle to rated speed).
The value of rated
speed potentiometer is
set too high
Re-set rated speed potentiometer.
Correction amplifier
adjustment
Running state of the controller is adjusted to a slow
run, this will lead to overspeed at startup. Slowly adjust the
gain to achieve the fastest steady-state response. Stable set
too low, increase stability settings.
Engine Trouble
Check whether the fuel supply gear lever is clamping
stagnation, whether adjustment of the fuel supply
connection is appropriate. Check whether the fuel supply
mechanism is moving fast with actuator input voltage.
When the overspeed protection device is operating
normally, check whether the shutdown action take place
while engine is not over-speeding.
Speed controller setup
issues
When the speed setting is counterclockwise set to
maximum, and the controller position output signal voltage
is not reduced, the controller may be bad, or the speed
range was set incorrectly. If the actuator voltage is
lowered, check whether the fuel supply connection or
actuator is in trouble.
engine occasionally
overspeed after
reaching the rated
speed
Engine fuel supply
system breakdown
Check whether that the engine fuel supply system is
operating normally. If the actuator is moved to the
minimum fuel supply position during the overspeeding
process, then the problem is in the fuel supply system.
Speed sensor and
controller breakdown
Check the speed sensor output voltage (at least
1.0Vrms) when speed exceeds an idle speed. If the voltage
is less than 1.0Vrms and terminal 4 is closed, the controller
will ask for maximum fuel supply.
Table of contents
Popular Controllers manuals by other brands
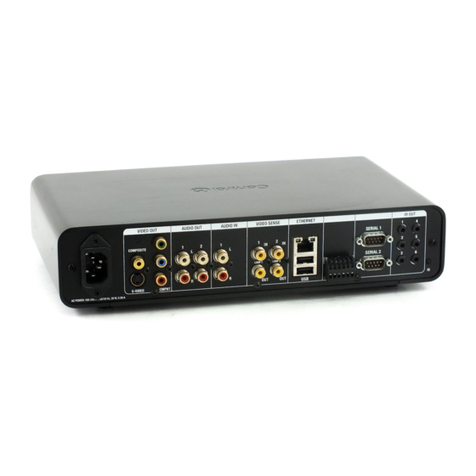
Contro l4
Contro l4 HC-300 installation guide

Oriental motor
Oriental motor DRLII Series operating manual
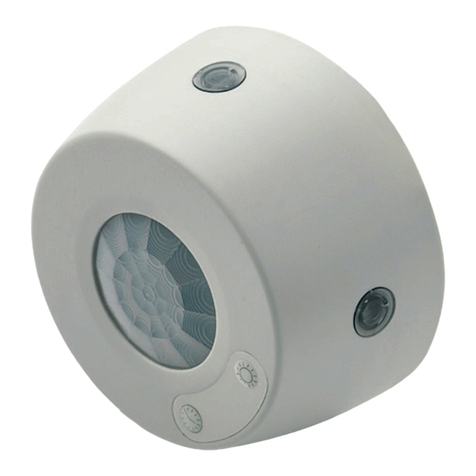
C.P. Electronics
C.P. Electronics GESM-AC installation guide
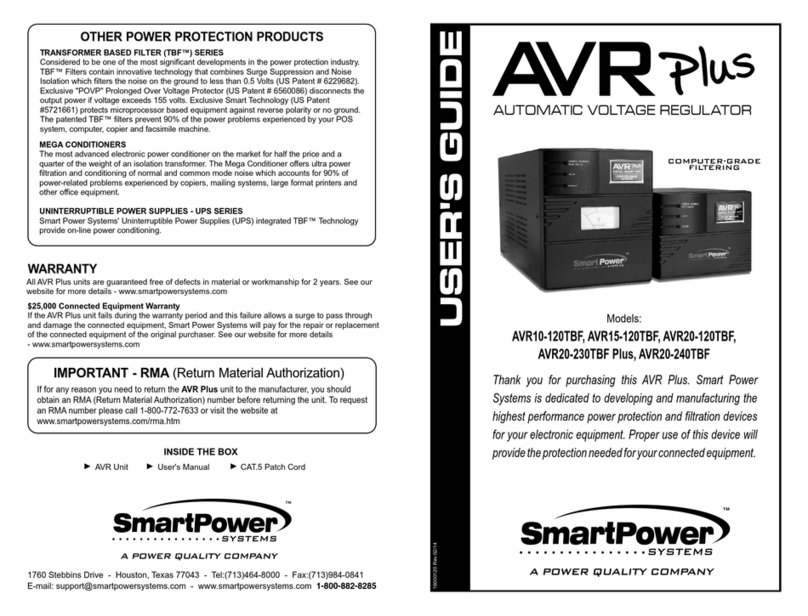
Smart power
Smart power AVR10-120TBF user guide
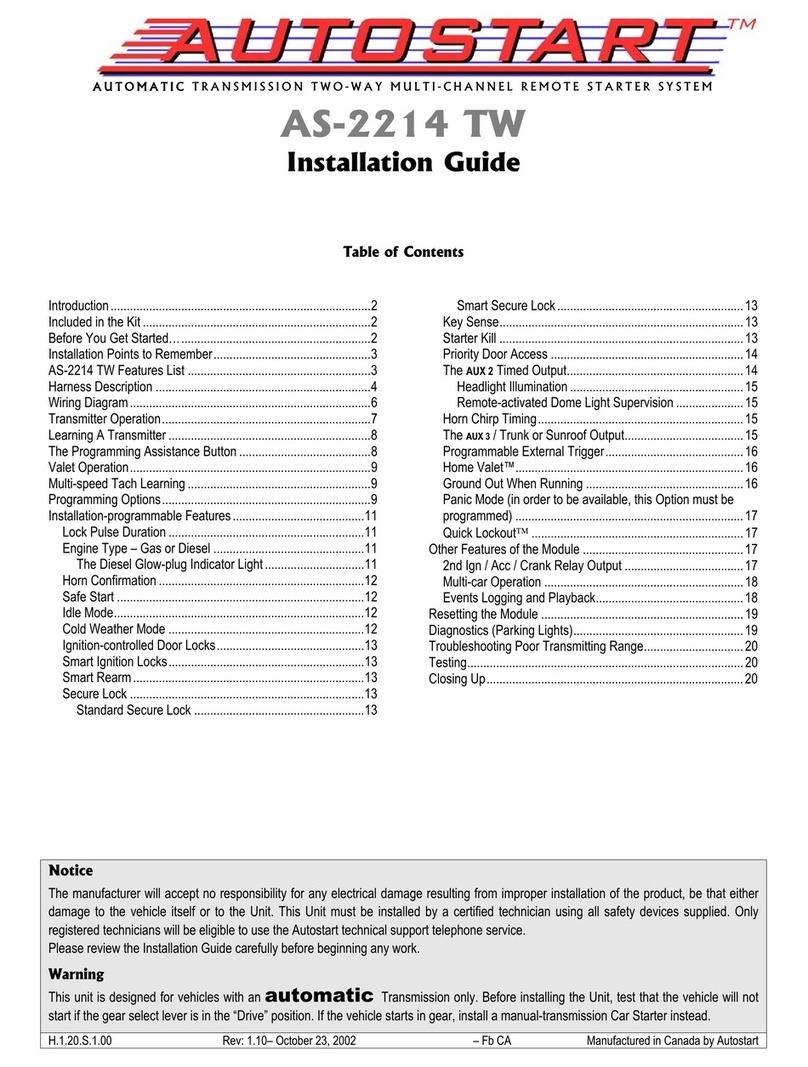
Autostart
Autostart AS-2214 TW installation guide
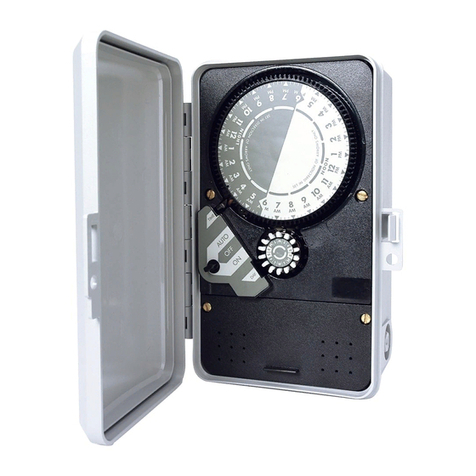
Hydro Tek
Hydro Tek 1000 Installation & troubleshooting guide
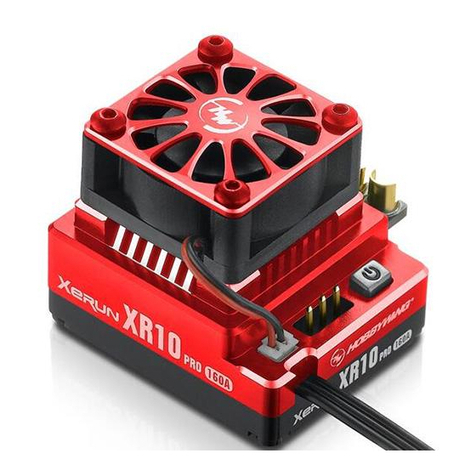
Hobby-Wing
Hobby-Wing Xerun XR10 Pro user manual
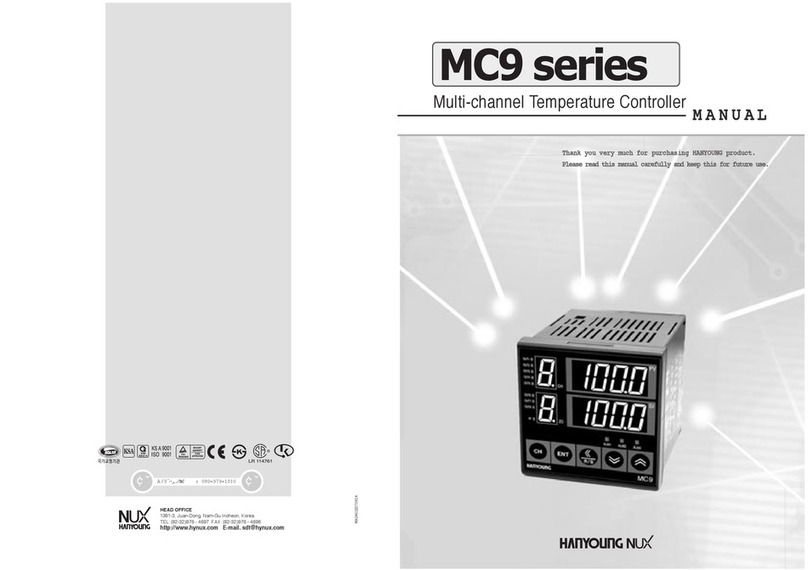
HANYOUNG NUX
HANYOUNG NUX MC9 Series manual
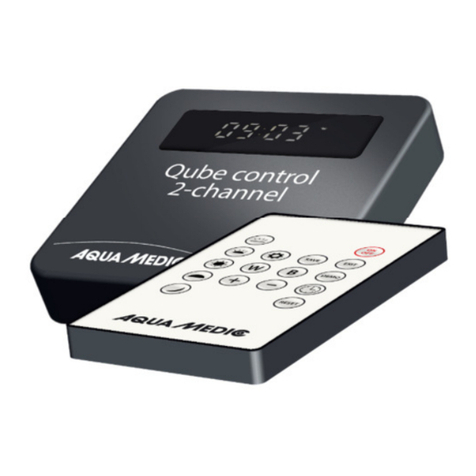
Aqua Medic
Aqua Medic Qube control Operation manual
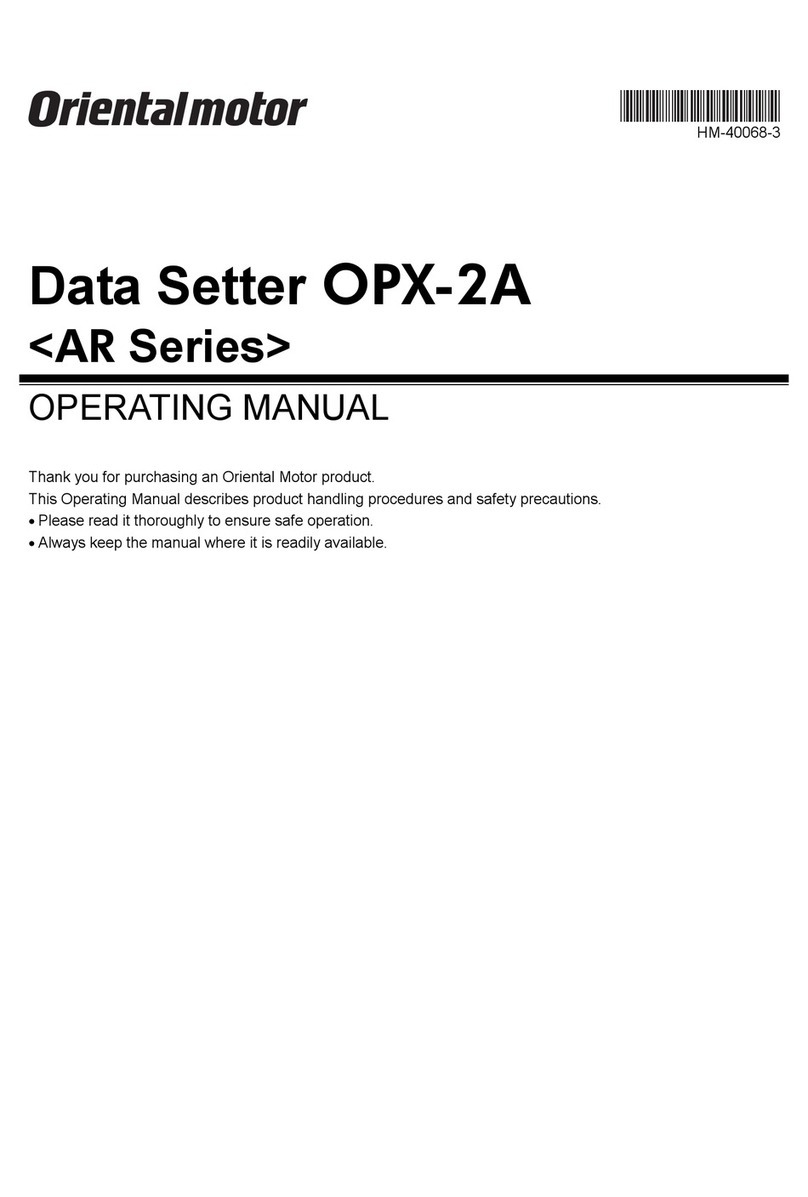
Oriental motor
Oriental motor AR Series operating manual
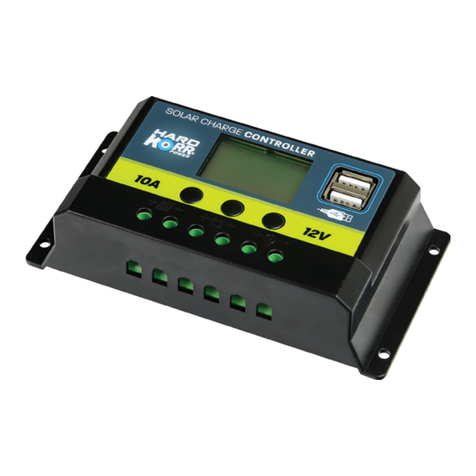
HARDKORR
HARDKORR 10A SOLAR CHARGE CONTROLLER user manual
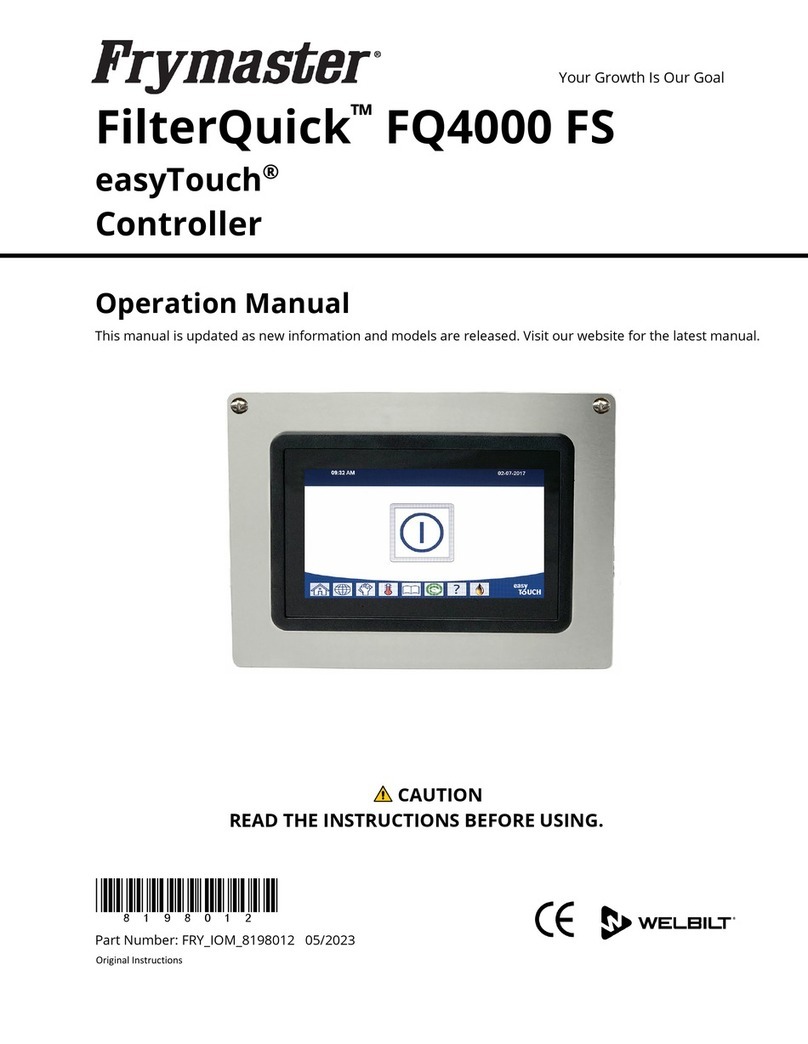
Welbilt
Welbilt Frymaster FilterQuick FQ4000 FS Operation manual