DCS 090 Series User manual

090 Series
Microprocessor Based parametric Controller
Reference Manual
Digital Control Systems, Inc.
7401 SW Capitol Hwy
Portland, OR 97219 USA
www.dcs-inc.net
Phone: 503/246-8110
Fax: 503/246-6747
Copyright (c) 2004
SUNSTAR传感与控制 http://www.sensor-ic.com/ TEL:0755-83376549 FAX:0755-83376182E-MAIL: [email protected]
SUNSTAR自动化 http://www.sensor-ic.com/ TEL: 0755-83376489 FAX:0755-83376182 E-MAIL: [email protected]

090 Series Reference Manual
2/21/05 Digital Control Systems Page: ii
Rev Date Description
10/22/2004 Preliminary version release
2/21/2005 1ST UL draft
SUNSTAR传感与控制 http://www.sensor-ic.com/ TEL:0755-83376549 FAX:0755-83376182E-MAIL: [email protected]
SUNSTAR自动化 http://www.sensor-ic.com/ TEL: 0755-83376489 FAX:0755-83376182 E-MAIL: [email protected]

090 Series Reference Manual
2/21/05 Digital Control Systems Page: iii
Table of Contents
INTRODUCTION .......................................................................................................................... 1
SPECIFICATIONS........................................................................................................................ 2
FRONT PANEL OPERATION...................................................................................................... 3
Start up ..................................................................................................................................................................................... 3
Normal Operation.................................................................................................................................................................... 3
Viewing and Modifying the Setpoint...................................................................................................................................... 3
Calibrating Process Input ....................................................................................................................................................... 4
FUNCTIONAL DESCRIPTION..................................................................................................... 5
Block Diagram Hardware Description. ................................................................................................................................. 5
Overview............................................................................................................................................................................... 5
Main ECB ............................................................................................................................................................................. 6
Power ECB ........................................................................................................................................................................... 6
INSTALLATION ........................................................................................................................... 8
Main ECB Electrical Connections.......................................................................................................................................... 8
Sensor Connection ................................................................................................................................................................ 8
Power Line Connection ........................................................................................................................................................ 8
Control Output Connections ................................................................................................................................................. 9
Jumpers ................................................................................................................................................................................. 9
Option Port............................................................................................................................................................................ 9
Power ECB Electrical Connections...................................................................................................................................... 10
Load Connection................................................................................................................................................................. 10
Control Cable Connection .................................................................................................................................................. 10
Alarm Relay........................................................................................................................................................................ 11
Load Circuit Considerations ................................................................................................................................................ 12
Triac Power Dissipation...................................................................................................................................................... 12
Triac Fault Protection ......................................................................................................................................................... 12
Mechanical Mounting............................................................................................................................................................ 12
Main Board Mounting ........................................................................................................................................................ 13
Power Board Mounting....................................................................................................................................................... 14
SUNSTAR传感与控制 http://www.sensor-ic.com/ TEL:0755-83376549 FAX:0755-83376182E-MAIL: [email protected]
SUNSTAR自动化 http://www.sensor-ic.com/ TEL: 0755-83376489 FAX:0755-83376182 E-MAIL: [email protected]

090 Series Reference Manual
2/21/05 Digital Control Systems Page: 1
INTRODUCTION
The 090 series microprocessor based controllers are designed to be incorporated into end
products that must accurately maintain the value of an electrically controllable process parameter
such as temperature, relative humidity, gas concentration, etc. The 090 series is UL recognized
to UL 61010-1 (2nd edition) and CSA C22.2 No. 1010.1 (2nd edition) making it inexpensive to
incorporate into equipment that meets domestic and overseas safety certificating agency
requirements.
Members of the 090 family accept inputs from a wide variety of variable resistance or voltage
sensors and can directly control loads up to 15 Amps at up to 240 VAC. An available second
control channel, several alarm output options and the ability to directly operate on power mains
from 80 to 280 VAC make the 090 series an economical choice for a wide range of appliance
control applications for the worldwide market.
This manual is intended for the OEM purchaser of the control. It describes the controller's
operation and covers the installation as well as the front panel operation of the 090 series.
Purchasers of 090 series controllers are granted a license to make copies of the Front Panel
Operation section of this manual for the sole purpose of providing operating instructions to their
end users.
The Functional Description section provides a technical overview of the 090 series and their
operation. It contains information useful to technical and engineering personnel who will be
involved with integrating the controller into the end product.
The Installation section of this manual is a guide to integrating the 090 series into the end
product. It contains the mechanical mounting dimensions which are common to all 090 series
models. A typical installation is described in detail and the pros and cons of several variations
are discussed. This section also contains data on electrical connections for operating power,
sensor inputs and control outputs.
SUNSTAR传感与控制 http://www.sensor-ic.com/ TEL:0755-83376549 FAX:0755-83376182E-MAIL: [email protected]
SUNSTAR自动化 http://www.sensor-ic.com/ TEL: 0755-83376489 FAX:0755-83376182 E-MAIL: [email protected]

090 Series Reference Manual
2/21/05 Digital Control Systems Page: 2
SPECIFICATIONS
This section covers the basic specifications common to all M090 series controllers. Specific
features of different variants are covered in their detail documentation.
Parameter Value
Display
(display type must be specified when
ordering)
3 or 4 digit, 0.56" 7 segment LED
Optional ‘Output Active’ LED
(Green is standard, red & yellow available)
Operator Controls Front panel ‘UP’ and ‘DOWN’ buttons
On-board jumpers for option control
Resolution (Control and Display) ± 1 least significant display digit
Control Algorithm PID
Load Control PWM Triac contact rated 15 Amps RMS
Sensor inputs available
(sensor type must be specified when
ordering)
10 mV/ °C integrated sensor
Type ‘J’ or ‘K’ thermocouple
100 Ohm RTD
Analog voltage (5 volts max)
Alarm Contact (optional) 2 dry contacts field configurable as NO or NC.
Rated 110VAC, 1A.
Alarm Sounder (optional) 85dB, 2 KHz beeper
Operating Power Requirements 80 to 280 VAC, 45 - 65 Hz, 5W max
Ambient Operating Conditions 0 to 50 degrees Celsius
0 to 80 %RH non-condensing
Pollution Degree 2
Mechanical Dimensions Main ECB: 5.25” x 2.35” (13.5 x 6 cm)
Power ECB: 1.9” x 2.0” (5 x 5 cm)
Weight Main ECB: 2.3 Oz (65 g)
Power ECB: 1.5 Oz (42 g)
Ambient Storage Conditions -30 to 85 °C
0 to 90%RH (non-condensing)
SUNSTAR传感与控制 http://www.sensor-ic.com/ TEL:0755-83376549 FAX:0755-83376182E-MAIL: [email protected]
SUNSTAR自动化 http://www.sensor-ic.com/ TEL: 0755-83376489 FAX:0755-83376182 E-MAIL: [email protected]

090 Series Reference Manual
2/21/05 Digital Control Systems Page: 3
FRONT PANEL OPERATION
The front panel of the 090 series consists of a three or four digit numeric LED display, and two
momentary push button switches labeled 'UP' and 'DOWN'. In normal operation the current
process value is displayed.
Several other parameters can be displayed, depending on the operating modes as described
below. Whenever a parameter other than the current process value is first displayed, it is
annunciated by a two letter code displayed for several seconds before the parameter’s value is
displayed.
Start up
Whenever power is first applied to the controller, its firmware version data is displayed as three
separate numbers, each preceded by an identifying quasi-alpha string as shown in the table
below.
Identifier Meaning
SN1 Firmware type number
Sn2 Firmware major version number
Sn3 Firmware minor version number
Table 1: Version Number Display Annunciation.
After these values are displayed, the controller begins operation in normal operation mode as
described below.
Normal Operation
In this mode the display shows the current process value. The display intensity is steady and at
most a single decimal point is illuminated. The controller always returns to this mode from any
other mode after approximately five seconds of no front panel button activity.
If over/under alarms are enabled and the process value is in either over or under alarm the
display will alternate between showing either ‘HI’ or ‘LO’ (depending on process value) and the
actual process value. When in alarm, the audible beeper will also sound if installed.
Viewing and Modifying the Setpoint
The current setpoint can be displayed by momentarily pressing and releasing either the 'UP' or
'DOWN' button. The display briefly shows ‘SP’ to annunciate the value about to be displayed,
then shows the setpoint value.
Whenever the setpoint value is showing, the display blinks. While the setpoint value is blinking
its value can be adjusted with the ‘UP’ and ‘DOWN’ buttons.
The controller automatically stores the current display value as the new setpoint and reverts to
Normal Operation mode after approximately five seconds of no front panel button activity.
SUNSTAR传感与控制 http://www.sensor-ic.com/ TEL:0755-83376549 FAX:0755-83376182E-MAIL: [email protected]
SUNSTAR自动化 http://www.sensor-ic.com/ TEL: 0755-83376489 FAX:0755-83376182 E-MAIL: [email protected]

090 Series Reference Manual
2/21/05 Digital Control Systems Page: 4
Calibrating Process Input
The process input can be calibrated from the front panel by pressing and holding both ‘UP’ and
‘DOWN’ buttons for approximately three seconds until the display shows one of the calibration
indicators shown in the table below:
INDICATOR Cal Mode
CP IC temp probe calibration
CO Offset Calibration
CS Span Calibration
Table 2: Calibration Mode Annunciation
The type of calibration is determined by the sensor input configuration.
After displaying the calibration indicator for several seconds, the display blinks the current
process value to indicate that it can be changed with the ‘UP’ and ‘DOWN’ buttons.
After approximately five seconds elapse without either button being pressed, the controller will
exit calibration mode. If the displayed value is to be changed, the operator must begin making
the change within a few seconds after the display begins to blink. When the changes are
complete, the controller will return to normal operation approximately five seconds after the last
button press.
At this point the new calibration value is stored in non-volatile memory and takes effect
immediately.
SUNSTAR传感与控制 http://www.sensor-ic.com/ TEL:0755-83376549 FAX:0755-83376182E-MAIL: [email protected]
SUNSTAR自动化 http://www.sensor-ic.com/ TEL: 0755-83376489 FAX:0755-83376182 E-MAIL: [email protected]

090 Series Reference Manual
2/21/05 Digital Control Systems Page: 5
FUNCTIONAL DESCRIPTION
This section provides a technical overview of the M090 series.
Block Diagram Hardware Description.
The block diagram of the 090 series is shown as Figure 1.
3
Optically
Isolated
Triac
Drive
Optically
Isolated
Triac
Drive
3
Relay & Driver
2
OPTIONAL
M090 Main Power ECB
(With Optional Alarm Relay)
J4 J5
UP DOWN
LOAD
LOAD
M090 Auxilary
Power ECB
HOT
NEUT
SAFETY
GND
SENSOR
INPUT
M090 Main ECB
90 - 280VAC
50 - 60 Hz
+5V
RELAY
(optional)
*LOAD1
GND
*LOAD2
+5V
GND
260VAC
15A (MAX) 260VAC
15A (M
A
Figure 1: 090 Series Block Diagram
Overview
The 090 Series controller’s main ECB contains the power supply as well as controller logic and
implements the user interface consisting of two buttons (‘UP’ and ‘DOWN’) and a numeric LED
display. The process sensor (various temperature sensors and voltage inputs are supported
depending on the exact controller configuration) and line voltage operating power are the inputs
to the main ECB. The controller’s load and alarm outputs are generated as isolated, TTL level
signals on the main ECB and used to actuate the alarm relay and load contacts located on the
Power ECB.
A maximum of two power ECBs can be connected to each main ECB. The power ECB
implements an optically isolated, electrically floating triac. The two power terminals of the triac
(MT1 & MT2) are terminated with ¼” ‘quick connect’ tabs and intended to be connected in
series with the controlled load as shown in Figure 1. The 090 series triac power ECBs can
control only alternating current. Do not attempt to use them for controlling direct current loads.
SUNSTAR传感与控制 http://www.sensor-ic.com/ TEL:0755-83376549 FAX:0755-83376182E-MAIL: [email protected]
SUNSTAR自动化 http://www.sensor-ic.com/ TEL: 0755-83376489 FAX:0755-83376182 E-MAIL: [email protected]

090 Series Reference Manual
2/21/05 Digital Control Systems Page: 6
Main ECB
The 090 series main ECB is designed for mounting behind the front panel of the end-user’s
equipment. It implements all the front panel displays and controls, requiring only descriptive
annunciation on the equipment panel. An audible alarm beeper, intended to sound through the
front panel, is available.
The 090 is powered directly from the AC power line, draws under 5W and operates on voltages
from less than 80 to 280 VAC at 45 to 65 Hz making it directly connectable to virtually any
power grid worldwide. The circuitry on the primary side of the transformer T1 (shown cross-
hatched in Figure 2) has voltages significantly above the input line voltage and can provide
unpleasant and potentially lethal electrical shocks both to earth ground and other components on
the board.
The low voltage side of the power supply is electrically isolated so that all control connections to
the power ECBs present no shock hazard. The earth ground connection is tied to the ground side
of the low voltage supply and passes through to the power ECB(s).
There are three control outputs from the main ECB. Two load contact controls designated
*LOAD1 & *LOAD2 as well as one relay control designated RELAY. All these signals are
TTL level referenced to earth ground. *LOAD1 & *LOAD2 are active low (i.e. the load contact
is closed when the voltage is less than approximately 0.4V), RELAY is active high. (see Table 3
on page 9)
These outputs are intended to drive the corresponding features on power ECBs. *LOAD1 and
RELAY actuate the triac and alarm relay respectively on the primary power ECB. *LOAD2
actuates the triac on the auxiliary power ECB if present.
All three signals (along with power) appear on connector J4 so that a single control cable can be
used to remotely drive the full complement of outputs. In addition, *LOAD2 (along with power)
appears on J5 for applications where the main and auxiliary power ECBs are most efficiently
served with two separate cables.
There are 2 two-pin jumpers (designated JP1 & JP2) located in the lower right-hand corner of the
main ECB when viewed from the rear. These are to implement various user functions in
different configurations. Each jumper has two states: OPEN and CLOSED. A jumper is
considered OPEN when its two pins ARE NOT electrically connected. A jumper is considered
closed whenever its two pins ARE electrically connected. A jumper is typically closed
momentarily with a small bladed screwdriver and closed semi-permanently with a shorting block
that slides over the two pins of the jumper.
The sensor input connector is located on the back side near the bottom edge of the main ECB
just to right of center. Various sensor inputs are supported depending on the exact configuration.
Each 090 series has only a single sensor input. The value displayed on the front panel during
normal operation is the process value associated with this sensor.
Power ECB
The load contact is implemented with a 25 amp, 600 volt triac, triggered with an optically
isolated, zero crossing triac trigger. All control inputs are electrically isolated from the
controlled circuit so there is no shock hazard from the interconnect cabling.
SUNSTAR传感与控制 http://www.sensor-ic.com/ TEL:0755-83376549 FAX:0755-83376182E-MAIL: [email protected]
SUNSTAR自动化 http://www.sensor-ic.com/ TEL: 0755-83376489 FAX:0755-83376182 E-MAIL: [email protected]

090 Series Reference Manual
2/21/05 Digital Control Systems Page: 7
When controlling load currents above 1 amp the mounting tab of the triac MUST be firmly
screwed down to a suitable metal surface that can sink the heat generated by the triac while
passing the full-load current. The higher the load current, the more thermal energy must be
removed to keep the triac within safe operating limits. An approximately 6 x 6 inch square of 18
Ga cold rolled steel is usually adequate for most loads up to 10 Amps.
The load contacts are the two ¼” quick connect tabs marked ‘LOAD’ and ‘HOT’. A third 3/16”
quick connect tab, covered by a plastic cap, is located near the two load terminals. This tab is
electrically hot (under the cap) and must never be electrically connected-to.
The load contact is intended to be connected in series with the load as shown in Figure 1.
Because the triac floats electrically, it can operate in either polarity on either side of the load.
The triac always operates in quadrants I & III regardless of the connection topology.
The standard power ECB is intended for control of primarily resistive loads in the .25 to 15 amp
range. Specific options exist for driving small inductive loads (such as solenoids). Consult the
factory for applications driving inductive and higher power (above 15 amps) loads.
The load contact is NOT fused. IT IS THE RESPONSIBILITY OF THE END USE
EQUIPMENT TO PROVIDE THE OVER CURRENT PROTECTION APPROPRIATE TO
THE APPLICATION.
Power ECBs are connected to the main ECB through an isolated, low voltage (TTL) interface
connected at J1. At a minimum the power ECB requires +5, GND and the *LOADx control
signal, so at least a three conductor cable is required. A 4th conductor must be added to drive the
optional relay.
One power ECB can optionally be provisioned with a DPDT relay. In this configuration it is
referred-to as the main power ECB to distinguish it from the auxiliary power ECB which has
only a load contact. Two electrically separate dry contacts are provided at the two position
screw terminal blocks J2 & J3. Both contacts actuate simultaneously but can be separately
configured to operate as either normally open or normally closed using the jumpers JP1 and JP2.
The RELAY signal from the main ECB must be connected to the power ECB for the relay to
operate.
SUNSTAR传感与控制 http://www.sensor-ic.com/ TEL:0755-83376549 FAX:0755-83376182E-MAIL: [email protected]
SUNSTAR自动化 http://www.sensor-ic.com/ TEL: 0755-83376489 FAX:0755-83376182 E-MAIL: [email protected]

090 Series Reference Manual
2/21/05 Digital Control Systems Page: 8
INSTALLATION
This section covers the major points to consider when incorporating the 090 series into the end
product's design.
Main ECB Electrical Connections
J5
AUXILIARY POWER
ECB CONNECTOR
J4
PRIMARY POWER
ECB CONNECTOR
OPTION
JUMPERS
(JP1 & JP2)
J8
SENSOR INPUT J6
OPTION PORT
Components and traces in
crosshatched area have
potentially lethal voltages present
while unit is under power.
CONTROLLER
POWER INPUT
80 - 280 VAC
45 - 65 Hz
Figure 2: 090 Main ECB Part Locations (Viewed from rear)
Sensor Connection
The sensor is connected to the two pin header J8 located at the bottom of the power board as
shown in Figure 2. The exact sensor type is determined by the controller configuration. The
sensor cable should not be routed near power carrying wires to minimize noise pick-up.
Power Line Connection
The controller’s operating power is connected at the three ¼” quick connect tabs located on the
left hand edge of the main ECB as shown in Figure 2. Beware that traces and components in the
area shown crosshatched in Figure 2 can have potentially lethal voltages to ground and each
other while the unit is under power.
If one leg of the power supply is grounded (i.e. neutral for domestic applications) it should be
connected to the power tab marked ‘NEUT’, since the ‘HOT’ terminal is the fused input.
SUNSTAR传感与控制 http://www.sensor-ic.com/ TEL:0755-83376549 FAX:0755-83376182E-MAIL: [email protected]
SUNSTAR自动化 http://www.sensor-ic.com/ TEL: 0755-83376489 FAX:0755-83376182 E-MAIL: [email protected]

090 Series Reference Manual
2/21/05 Digital Control Systems Page: 9
The ‘GND’ terminal is the ground of the low voltage power supply and should be connected
directly to earth ground.
Fusing
The operating power input is fused for fire protection in the event of a component failure by a 1
Amp fuse F1 located near the power input tabs. This fuse is not intended for operator
replacement and should never open during normal operation. It is very unlikely that normal
operation can be restored by simply replacing F1 after it blows.
If replaced, it must be replaced with a fuse of like rating (1 Amp at 250V) for continued
protection against fire.
Control Output Connections
All control outputs of the M090 main ECB appear on the five pin header J4. The *LOAD2
output as well as +5 VDC and ground are duplicated on the three pin header JP5. This is done to
give the user the option of providing a unique cable to the auxiliary power ECB if one is present
in the system. If both power ECBs are located distant from the main ECB, it may be more
convenient to run a single cable that carries all the signals needed to run both power ECBs.
The signals on J4 and J5 are shown in the table below.
Signal Description J4 Pin # J5 Pin #
*LOAD1 Active Low TTL control signal for main triac.
Connects to *LOAD pin on power ECB. 1 N/C
+5 V 5 volt DC operating power 2 2
GND system ground 3 3
RLY Active high TTL relay control signal 4 N/C
*LOAD2 Active Low TTL control signal for auxiliary triac.
Connects to *LOAD pin on power ECB 5 1
Table 3: Main ECB Control Output Connector Pinout
Jumpers
There are two contact closure inputs called option jumpers as shown in Figure 2. When the two
pins (.025” square pins spaced 0.1” apart) associated with each jumper are electrically connected
the jumper is considered closed. The result of closing a jumper varies by firmware
configuration.
Option Port
A seven pin header called J6 is used for factory testing and connecting to various options such as
RS-232.
SUNSTAR传感与控制 http://www.sensor-ic.com/ TEL:0755-83376549 FAX:0755-83376182E-MAIL: [email protected]
SUNSTAR自动化 http://www.sensor-ic.com/ TEL: 0755-83376489 FAX:0755-83376182 E-MAIL: [email protected]

090 Series Reference Manual
2/21/05 Digital Control Systems Page: 10
Power ECB Electrical Connections
The layout of the M090 power ECB is shown in Figure 3.
Load Connection
The load(s) to be
controlled by the 090 must
be connected in series
with the power ECB triac
as shown schematically in
Figure 1. The two floating
triac contacts appear as ¼”
quick connect tabs labeled
‘HOT’ and ‘LOAD’ as
shown in Figure 3.
One side of the load must
be connected to either one
of these quick connects.
The power line leg not
connected to the load is
connected to the quick
connect. Power line
polarity and whether the
triac is switching the
load’s supply or return are
irrelevant despite the nomenclature of the contacts. The triac always operates in quadrants I and
III.
Figure 3: Power ECB Component Locations
There is a 3/16” quick connect tab marked ‘NO CONNECT’ and covered with a plastic cap
located as shown in Figure 3. This is the gate terminal of the triac. It is at power line potential
and must never be connected to.
The power ECB triac starts conducting at the next power line voltage zero crossing after the
*LOAD signal voltage falls below the logic low threshold. The triac stops conducting at the
next load current zero crossing after the *LOAD signal rises above the TTL high threshold.
Control Cable Connection
The cable from the M090 power ECB is connected at J1 located as shown in Figure 3. Power
ECBs that have the relay option installed have a four pin connector at J1. Those without the
relay option can operate with only a three pin connector at J1. The pinout of J1 is shown in the
table below:
SUNSTAR传感与控制 http://www.sensor-ic.com/ TEL:0755-83376549 FAX:0755-83376182E-MAIL: [email protected]
SUNSTAR自动化 http://www.sensor-ic.com/ TEL: 0755-83376489 FAX:0755-83376182 E-MAIL: [email protected]

090 Series Reference Manual
2/21/05 Digital Control Systems Page: 11
Pin # Name Description
1 *LOAD Active low TTL triac control signal (triac conducts when < 0.4 V)
2 +5 5 VDC power supply
3 GND Power supply ground
4 RELAY Active high TTL relay control signal (relay actuated when > 2.5 V)
Table 4: Power ECB Control Connector Pinout.
All signals in the control cable connecting the main ECB to the power ECB(s) are low voltage
(under 10 volts) and do not require line voltage capable cabling. Current requirements of all
conductors is below 0.2 amps. Conductor sizes of 24 – 26 AWG are recommended.
Control cable connectors at both ECBs are .025” square pin, 0.1” pitch headers with a locking
tab. Several manufacturers offer insulation displacement style connectors that mate directly with
headers on the ECBs, such as the AMP MTA-100 series and ITW Pancon Mas-Con series
CE/CT. Some typical part numbers are shown below. There are other manufacturers as well.
ITW Pancon PN AMP PN Description
CE100F26-04 640442-4 4 position IDC connector for 26 AWG wire
CE100F24-03 640441-3 3 position IDC connector for 24 AWG wire
Table 5: Control Cable Connector Vendor PNs.
Alarm Relay
Figure 4: Alarm Relay Contact
Circuit
An optional DPDT relay rated 120 VAC, 1A can be supplied on
only one power ECB per Model 090. When the relay option is
installed two independent dry contact closures appear on the
two 2 position screw terminals J2 & J3. The circuit for a typical
contact is shown in Figure 4.
The two 3 position headers at JP1 & JP2 program the sense of
the two relay contact outputs as shown in the table below. The
two jumper pins are connected with supplied shorting blocks.
Pin 1 on all connectors is denoted with a square pad.
JP1 pins connected J2 Sense JP2 pins connected J3 Sense
1 - 2 Normally closed (NC) 1 - 2 Normally Closed (NC)
2 - 3 Normally Open (NO) 2 - 3 Normally Open (NO)
Table 6: Relay Contact Sense Jumper Settings.
Normally Closed means the relay contact is closed when the RELAY signal is at logic low.
SUNSTAR传感与控制 http://www.sensor-ic.com/ TEL:0755-83376549 FAX:0755-83376182E-MAIL: [email protected]
SUNSTAR自动化 http://www.sensor-ic.com/ TEL: 0755-83376489 FAX:0755-83376182 E-MAIL: [email protected]

090 Series Reference Manual
2/21/05 Digital Control Systems Page: 12
Load Circuit Considerations
Triac Power Dissipation
The load is switched with a triac rated for 25 amps at 600 volts. When conducting, the triac
dissipates up to 1.4 Watts per Ampere of load current. At load currents above 1 amp the
mounting flange of the triac must be secured to a suitable heat sink. For moderate loads (less
than 8 to 10 amps) the triac can be screwed directly to painted metal. For higher loads direct
contact to bare metal is usually required and actual temperature at full load must be verified as
described below.
The power ECB is intended to be installed by screwing the triac’s mounting flange to a flat metal
surface with two # 6 screws. A 6” x 6” area of 18 Ga. cold rolled is usually adequate heat
sinking. Larger area will result in cooler operation for the same load current. Actual heat sink
temperature must be evaluated under full load conditions to ensure maximum operating
temperature of the triac is not exceeded.
Case temperature of the triac is measured at the exposed portion of the mounting flange
immediately adjacent to the mounting screw’s head. The maximum temperature at this point is
85 °C. If the temperature at this point exceeds 85 °C, more heat sink area must be provided or
the load current reduced.
Triac Fault Protection
The load circuit is not fused. The triac used on the power ECBs is extremely rugged and can
usually endure load short-circuit current for long enough to trip a 15 to 20A branch circuit
breaker in most applications. In low source impedance applications where triac protection
under short circuit conditions is required, a fuse with an i2t rating of 260 Amps2sec or less must
be installed in series with the load circuit.
Mechanical Mounting
The 090 series consists of a main ECB intended to mount behind a control panel, and one or two
smaller power ECBs.
The numeric LED digits and two buttons on the main ECB are the 090 series' user interface.
This board is intended to be mounted behind the end product's front panel with the LED display
showing through a cutout. Two additional cutouts below it allow actuation of the switches.
The power board contains the power and (optional) alarm relay connectors, and need not be
accessible to the user. It is intended to be mounted on an internal metal wall which also acts as
the triac’s heat sink.
SUNSTAR传感与控制 http://www.sensor-ic.com/ TEL:0755-83376549 FAX:0755-83376182E-MAIL: [email protected]
SUNSTAR自动化 http://www.sensor-ic.com/ TEL: 0755-83376489 FAX:0755-83376182 E-MAIL: [email protected]

090 Series Reference Manual
2/21/05 Digital Control Systems Page: 13
Figure 5: Main ECB Front Panel
Mounting
Main Board Mounting
The preferred mounting for the main board is shown in
Figure 5. The board is mounted on standard 3/8 inch self-
clinching studs (PEM SOS-12-440 or equivalent) pressed into
holes drilled through the end product's front panel. Using self-
clinching standoffs is preferred because the thickness of the
front panel does not affect the position of the switch shaft
relative to the front surface of the panel. The length tolerance of
the stand offs should be ± .006" or better.
Proper standoff installation is critical. Insufficient standoff
protrusion may cause the button shafts to interfere with the
overlay at worst case tolerance conditions. Excessive
protrusion makes the button difficult or impossible to actuate.
Embossing a .030" inch raised 'button' into the overlay will
minimize tolerancing problems.
Maximum required switch shaft travel is .015 inches. At the
worst case tolerance condition of maximum stroke, shortest
shaft length and longest standoff length, the front of the switch
shaft must be depressed .027" below the front surface of the
panel.
In applications where other mounting schemes will be used,
some important tolerances to keep in mind are shown the table
below.
Dimension Value in Inches
Switch shaft length (from front surface of ECB) .374 ± .006
Switch actuation travel .010 ± .005
Thickness of plating at display board mounting holes .004 ± .001
Table 7: Important Front Panel Mounting Dimensions
Clearance and Ventilation
All main board components except the display and buttons are on the side facing away from the
front panel. Clearance of at least 1 inch (2.54 cm) must be provided behind the main board to
ensure that there is no mechanical interference with components on the board. There must be
free air movement within the clearance volume; packing the volume immediately behind the
board with loose-fill insulation or the like may lead to localized over-heating on the main board
and is to be avoided.
Thermal Issues
The power supply on the main board dissipates so little heat that self-heating should not be an
issue if the 1 inch back side clearance is maintained. The main board should be located so that it
is not heated to over 50 degrees Celsius by energy dissipated by other heat sources.
SUNSTAR传感与控制 http://www.sensor-ic.com/ TEL:0755-83376549 FAX:0755-83376182E-MAIL: [email protected]
SUNSTAR自动化 http://www.sensor-ic.com/ TEL: 0755-83376489 FAX:0755-83376182 E-MAIL: [email protected]

090 Series Reference Manual
2/21/05 Digital Control Systems Page: 14
Front Panel Trim
The preferred method of trimming the front panel is a lexan overlay with a clear window through
which the LED display can be read. A frosted window will noticeably blur the display digits,
though not usually enough to make them unreadable.
The area on the overlay above the two switches can be marked with just a button shaped graphic
to indicate where to press, or a raised button can be embossed. In any case the front panel hole
through which the switch shafts protrude should be at least a half inch in diameter and burr free
to allow the overlay to travel the required (up to) .027 inch into the front panel to actuate the
switch without chafing the overlay material.
Be sure to specify no adhesive on the back of the overlay in the button area.
Mechanical dimensions of the main ECB are shown in Figure 6.
Figure 6: Main ECB Mechanical Dimensions (in inches)
Power Board Mounting
This section discusses various issues related to mechanically mounting the power board in the
equipment to be controlled.
Mechanical Attachment
The power ECBs are intended to be attached to their mounting surface with the metal flange that
forms the bottom of the triac assembly. The mounting flange is electrically isolated and can be
directly attached to any surface.
There are two mounting holes in the flange. One is on the portion of the mounting flange that
extends past the perimeter of the circuit board, the other is accessible through a large hole in the
circuit board near the power connection tabs. Use of #6 hardware (or equivalent) is
recommended for mounting the power ECB, though #4 can be used for low to moderate current
applications.
SUNSTAR传感与控制 http://www.sensor-ic.com/ TEL:0755-83376549 FAX:0755-83376182E-MAIL: [email protected]
SUNSTAR自动化 http://www.sensor-ic.com/ TEL: 0755-83376489 FAX:0755-83376182 E-MAIL: [email protected]

090 Series Reference Manual
2/21/05 Digital Control Systems Page: 15
Thermal Considerations
The surface to which the power ECB is attached acts as the heat sink for the triac which must
dissipate 1.4 Watts per Amp of load current. Depending on the load current profile, the local
heating that results can be significant and must be accounted-for. In any case the power board
should be mounted in a location where it is not being heated by outside sources.
Because the excess heat from the triac is conducted into the surface onto which the power board
is mounted, only minimal air circulation is required. At least one inch (2.54 cm) of clearance is
recommended above the power board.
The actual triac case temperature at full load and maximum rated ambient temperature must be
verified during the design-in engineering phase to ensure that it does not exceed 85 °C. Case
temperature of the triac is measured at the exposed portion of the mounting flange immediately
adjacent to the mounting screw’s head. See the section on load considerations starting on page
12 for other important thermal considerations.
The power ECB(s) must be positioned so that it is inaccessible to the end user and the
interconnect cable is not under mechanical tension.
Mounting dimensions are shown in Figure 7.
Figure 7: Power ECB Mechanical Dimensions (in
inches)
SUNSTAR传感与控制 http://www.sensor-ic.com/ TEL:0755-83376549 FAX:0755-83376182E-MAIL: [email protected]
SUNSTAR自动化 http://www.sensor-ic.com/ TEL: 0755-83376489 FAX:0755-83376182 E-MAIL: [email protected]
Table of contents
Popular Controllers manuals by other brands
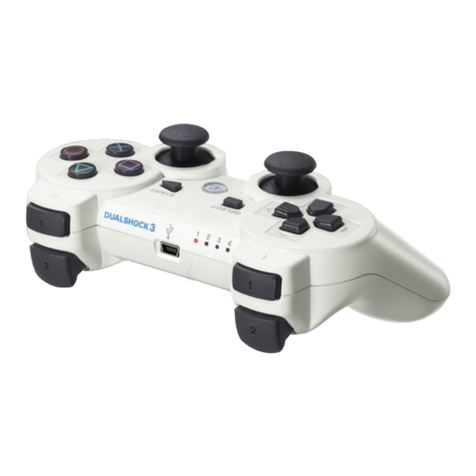
BGR Mods
BGR Mods INTENSAFIRE 2.0 quick start guide

Nexus
Nexus NEO manual

Sistemes Electrònics Progrés s.a.
Sistemes Electrònics Progrés s.a. AGRONIC 2500 instruction manual
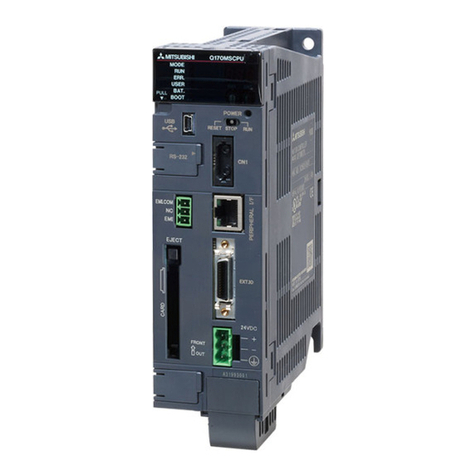
Mitsubishi Electric
Mitsubishi Electric Q170MSCPU user manual
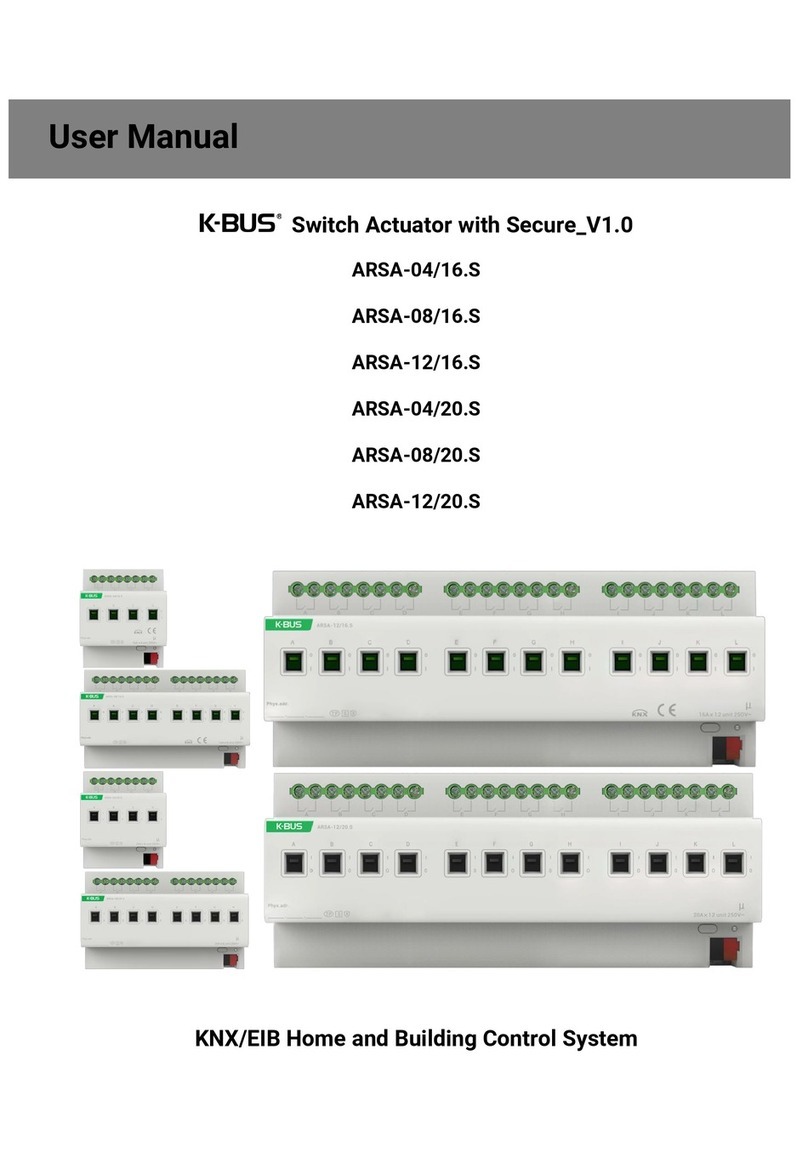
K-BUS
K-BUS ARSA-04/16.S user manual

RJX Hobby
RJX Hobby seriously pro user manual