digigate slider ROBO 24 User manual

1
R
RO
OB
BO
O
2
24
4
SLIDING GATE OPERATOR
Introduction The Nice 24 Sliding Gate Controller was designed to take advantage of
the superior torque and power of the 24 Volt motor. Conceived as a Dual Supply”
system, the operator runs efficiently on the 220Volt Mains supply under normal
conditions, and, changing over seamlessly, continues to run from the on-board
batteries during a power failure. A switch mode power supply is used to convert the
mains to the 24 Volt power for the motor, the controller and accessories, and the
charging circuit, which ensures that the batteries are fully charged at the correct
voltage for long life.
Performance Using micro-processor control to provide ramp-up and ramp-down
speed control, the Nice 24 starts smoothly, accelerates quickly to full speed (16,7metres
per minute, one of the fastest operators available), slows down in the last half metre of
travel and stops firmly and gently under electronic braking.
Designed to operate without limit switches for ease of installation, the unit learns” the
full extent of the gates travel by physically sensing the rail-stops, and then automatically
leaves a small safety gap at each end during normal operation, eliminating noisy
knocking.
Features
Easy Programming An on-board display makes it easy to select and enter the required
features, which include Learning Limits, Auto-close (none, 5, 10 or 20 seconds), Safety
beam selection, Obstacle Sensing Level, Recording Remote controls (up to 16), and
Type of operation, which may be ‘Standard’ (Residential) or ‘Commercial’.
On-board Radio Receiver The controller has a Digitronic e-Key receiver on board that
provides state-of-the-art secure access control using Keeloq code-hopping technology.
The receiver stores up to 16 transmitters in non-volatile memory.
Optional external Lamp External 220V lamps may be connected to the controller,
which will come on with every gate operation, and time-out 3 minutes later. These
lamps may turned or off by means of a connection to the intercom. The combined
power of these lamps is restricted to 250W.
Easy Installation Connections to the controller are made by means of plug-able
terminal blocks, simplifying installation and maintenance. These connections include
the intercom connection, partial opening for pedestrians, lock, safety beam, etc.
The configuration of the machine and the transmitter are stored in a plug-able memory
chip, which can be easily transferred to a replacement controller, making re-
programming un-necessary.
Installation Install the operator according to the enclosed instructions.
Important! For safety reasons, the gate must have physical end-stops in both the closed
and open positions. A sturdy rail-stop must be securely fitted to the track of the sliding
gate in the fully open position. In the closed position, the gate normally stops against the
gatepost. If not, a sturdy rail-stop must be securely fitted in the closed position as well.

2
Height ad ustment For the height adjustment to be possible, the four adjusting screws
provided in the small accessory box must be fitted as in fig. 9 on page 7, before
mounting the machine to the steel base plate. Ideally, these screws should protrude 5 to
10 mm, creating a gap between the base plate and the under side of the machine. This
will allow for subsequent height adjustment.
Wiring For all connections refer to Fig. 1.
Mains. A suitable cable (armoured 3-core or Surfex) should be used from a 2-amp
circuit breaker on the distribution board to the site of the motor, where it is
brought up through the opening in the base plate. See page 5 Fig. 4. Connect
the earth wire and the armour to the spare lug provided on the chassis earthing
point. Connect the Line and Neutral wires to the terminals ‘L’ and ‘N’ on the
controller, shown as ‘230V MAINS’ in Fig. 1.
PROGRAM DISPLAY
PLUGGABLE MEMORY
ENTER BUTTON
SELECT BUTTON
TYPE
STANDARD
PARTIAL
CONTROL
LOCK
LIGHT
0V-COM
BEAM N.C.
BEAM 24V+ BEAM 24V+
COMMERCIAL
STOP
BEAM N.C.
0V-COM
CLOSE
OPEN
PARTIAL
ON/
OFF
GATE
STATUS LED+ STATUS LED+
GATE
MAINS LAMP BATTERY MOTOR
230V~ 24V DC
L N N L + - + -
MANUAL
ENCODER
F g. 1
0V-COM
ANTENNA
Accessories.
Before connecting any accessories, decide which ‘Type’ of operating mode will be
used, ‘Standard’ or ‘Commercial’. ‘Standard’ is suitable for residential purposes, giving
each user full control of the gate. ‘Commercial’ avoids conflicting inputs by providing a
dedicated ‘Open’ input for the users. Separate ‘Stop’ and ‘Close’ connections are also
provided.
Note: All the accessories are referenced to ‘0V-COM’.
N.C. and N.O. refer to switch contacts, and stand for ‘Normally Closed’ and
‘Normally Open’.
Partial. For pedestrian use, a key Switch may be connected to ‘Partial’.
This switch will cause the gate to open to a width of about 1,2m. Once partially opened,
the gate may be re-closed using the same switch, or it will auto-close in the time
selected (5, 10 or 20 seconds) or in 5 seconds if Auto-close is not selected.
If the gate is closing after being partially opened and the safety beam is blocked, the
gate will only re-open to the partially open point.

3
Control. The wire for control from the intercom (or other devices for opening, ground
loops, card readers, keypads, etc.) is connected to ‘Control’ or ‘Open’ depending on
the ‘type’ chosen.
Lock. An optional switch (e.g. fitted to the intercom) may be connected this input.
When active, the gate cannot be operated, even by a valid control.
Using this input once the gate is open will disable Auto-close until the Lock switch is
released. In Commercial mode this input serves as a ‘Stop’ command.
Light On/Off. If an optional external lamp or lamps have been connected to ‘LAMP, N, L’
as in Fig. 1, these may be controlled by a push-button connected to this input. If off, they
will be turned on or off if they were on. The combined power of these lamps is restricted
to 250W.
In Commercial mode this input serves as a ‘Close’ command.
Safety Beam. If a Safety Beam is fitted, it is connected to ‘0V-COM’, Beam N.C.’ and
‘Beam 24V+’. If the Safety Beam is blocked whilst the gate is closing, it will automatically
stop, pause and re-open. The Safety Beam has no effect during opening of the gate. An
active Safety Beam will prevent the gate from Auto-closing, or being deliberately
closed.
Position the Safety Beam low enough to protect toddlers and pets, yet high enough so
that the under-side of most cars will not clear the beam. Be aware that high-bed trailers
or trucks may not block the beam, and care must be taken while they are in the
gateway.
If, during the course of the day, direct sunlight at a low angle falls on one side of the
gateway, it is advisable to fit the transmitter of the Safety Beam units to that side.
The installation of Safety Beams is strongly recommended, especially if Auto-close is to
be used. If Auto-close is selected and Safety Beams are not fitted, the gate will not
operate, unless a wire link is fitted from ‘0V-COM’ to ‘Beam N.C.’. This is, however, not
advised.
Gate Status. An LED fitted to the intercom in the house and connected to ‘Gate Status
LED+’, will indicate the status of the gate by illuminating when the gate is not closed,
and flashing while the gate is running. This signal may also be used to drive an audible
device such as a buzzer, with interfacing suitable to the device.
On-board Radio Receiver. The Radio Receiver on-board will support up to 16 Digitronic
eKey Remote controls. The recording of these uniquely coded Remotes is simple, as is
the removal of the codes. These codes are stored in a plug-able memory chip, together
with the controller configuration, limit positions etc., and may be swapped onto a
replacement control board for maintenance purposes.
If an off-board Receiver is to be used, connect it to ‘BATTERY’ + and –, and the N.O.
output to ‘CONTROL/OPEN’. The On-board Radio Receiver should be disabled as
follows:
Isolate the power by switching off the mains 220 volt supply, and removing the
wire link between the batteries.
Remove the clear protective cover (held by a screw at the top) and the control
board (held by a screw at the bottom).
Locate the link on the left side on the back of the board.
Using a small drill-bit, remove the small circle pad between the two square pads.
Initial Power-up
Once the motor, the rack and the Rail-stops have been installed, proceed as follows:
1. Put the machine in ‘Manual’ by unlocking and pulling the Manual Over-ride
Lever, and position the gate mid-way.
2. Connect the batteries with the white jumper lead, and switch on the mains.

4
3. Engage the Manual Over-ride Lever. The display will flash ‘S C’ and the motor will
start running slowly.
4. Check that the gate is closing, in which case skip to 6. If not, go to step 5.
5. Pull the Manual Over-ride Lever. Referring to Fig.1, swap the Motor wires on the
second plug. Re-engage the Manual Over-ride Lever and the motor will close.
6. On reaching the closed position, the operator will detect the rail-stop and halt.
The display will show C” for closed.
If the gate has stopped short of the fully closed position, this is an indication of the
amount of power required by the gate, considering all the related factors.
The power setting and Obstacle Sensing are directly related, and should be increased
incrementally and re-tried until the gate reaches the closed position on the lowest
possible obstacle setting. If, on the highest setting of 3, the gate still fails to close fully,
then the gate is possibly too heavy (greater than 400 Kg), or there is too much rolling
resistance due to the condition of the track, the size of the wheels related to the weight
of the gate, or the state of the wheel bearings and guide rollers. Also check that the
rack is engaging smoothly with the gear, showing the correct clearance over the full
length of travel.
Programming Overview
Note: Programming mode may be entered only if ‘C’ (for closed), ‘S-n’ (Seek stopped)
or if a fault code ‘F’ is displayed.
Programming of features is achieved by pressing the Enter (ENT) and Select (SEL)
buttons together. The Program Display will show ‘P’. Thereafter every press of the SEL
button will cause a different letter to appear, each representing different features.
When the required letter appears, press ENT to program that feature, and the letter will
start flashing. Use SEL to step through the setting options and ENT to confirm the
selection. After the display returns to ‘P’, press ENT to exit.
Limits (L)
1. As above, press ENT and SEL together and ‘P’ will appear on the display.
2. Press the SEL button. The Display will change to ‘L’.
3. Press the ENT button and the ‘L’ will start flashing.
4. Press the ENT button again and the motor will open slowly to detect the rail-stop.
5. The operator will automatically close again at normal speed, leaving a small gap
before the stop, and the Display will show ‘C’. The Limits have now been
programmed.
Obstacle Sensing (o)
1. Press SEL until ‘o’ is displayed. Levels 1, 2 and 3 of sensitivity may be selected, 1
being the most sensitive and 3 the least.
2. Press ENT and the ‘o’ and a digit will flash.
3. Press SEL until the desired option is displayed.
4. Press ENT to confirm the selection.
Note: Start with this setting on 1, and increase it if, during normal running, the gate stops
or reverses.
Next, record the Digitronic e-Key Remote control(s) as follows:
Record Remote (r)
1. Press SEL until ‘r’ is displayed.
2. Press ENT and the display will flash ‘r n’ (for new” remote).
3. Press the desired button on the e-key Remote. The decimal point on the display will
flash.
4. Release the button and ‘r C’ will be flash. (‘C’ for ‘confirm’).
5. Press the same e-key Remote button to confirm the code.
6. Release the button and the display will flash ‘r n’, ready for the next remote, if any.
7. Repeat from step 3 for each required e-key Remote.

5
8. Press ENT to end the sequence.
Note: The controller can store sixteen separate e-key Remotes, using different buttons
on each. An attempt to record a seventeenth remote will be ignored.
To program the other features, refer to the Quick Guide section at the end.
Normal Operation
Standard (Residential) Type
Assuming the gate is closed, when the controller receives a command from a
remote control, the gate will start opening, ramp up to full speed, and ramp down to
stop in the fully open position.
The gate may now be closed using the remote control, or it may be left to Auto-
close, if selected. The gate will close, ramping up and ramping down to stop in the
closed position.
Whilst the gate is opening or closing, a further command will cause it to stop.
If the gate is obstructed while closing, the gate will stop, reopen at slow speed and
bump the open rail-stop to re-calibrate itself.
If the gate is obstructed while opening, the gate will simply stop. When the gate next
closes, it will do so at slow speed and bump the closed rail-stop to re-calibrate itself.
Commercial Type
If selected as a Commercial Type, the controller regards all signals from remote
controls as dedicated ‘Open’ commands, thus avoiding the conflict that arises in a
multi-user situation.
If required, separate buttons for Open, Stop and Close may be installed, for instance,
in a guard-room.
Manual Over-ride
If it should be necessary to use the gate manually, slide the key-cover open, unlock
and pull the Manual over-ride lever. The gate may now be operated manually.
When the Manual over-ride lever is re-engaged, the motor will immediately start
closing the gate at slow speed to re-establish the closed position. Normal operation
will then continue.

6
R
RO
OB
BO
O
2
24
4
SLIDING GATE OPERATOR
QUICK GUIDE INSTRUCTIONS
Installation
Install the 24V Robo sliding gate motor as per the enclosed instructions.
Important! For safety reasons, a sturdy rail-stop must be securely fitted to the track of the sliding gate in the
fully open position, and in the closed position if there is no other physical stop.
The installation of Safety Beams is strongly recommended, especially if Auto-close is to be used. If Auto-
close is selected and Safety Beams are not fitted, the gate will not operate, unless a wire link is fitted from
‘0V-COM’ to ‘Beam N.C.’. This is, however, not advised.
Wiring The 24V Robo is designed to operate on 220V mains supply and a built-in 24V battery. A
suitable mains supply must be provided to the site of the gate motor.
PROGRAM DISPLAY
PLUGGABLE MEMORY
ENTER BUTTON
SELECT BUTTON
TYPE
STANDARD
PARTIAL
CONTROL
LOCK
LIGHT
0V-COM
BEAM N.C.
BEAM 24V+ BEAM 24V+
COMMERCIAL
STOP
BEAM N.C.
0V-COM
CLOSE
OPEN
PARTIAL
ON/
OFF
GATE
STATUS LED+ STATUS LED+
GATE
MAINS LAMP BATTERY MOTOR
230V~ 24V DC
L N N L + - + -
MANUAL
ENCODER
F g. 1
0V-COM
ANTENNA
Refer to Fig. 1
With the mains supply isolated, connect
Earth, Line and Neutral.
An external lamp may be optionally
connected to the terminals marked N
and L, LAMP, 230V~. This lamp will
come on with every gate operation
and time-out after three minutes.
Accessories
Connect the accessories as indicated,
referenced to ‘0V-COM’.
All inputs, excepting the Beam, are
‘Normally Open’.
If an off-board Receiver is to be used,
connect it to ‘BATTERY + and -, and the
N.O. output to ‘CONTROL/OPEN’.
The common of the receiver must be
linked to negative.
Note 1: Do not use 12v devices by
connecting them to one of the
batteries, as this will cause improper
charging.
Note 2: The 24 volt supply from the
Robo24 controller (‘BATTERY +, -’) is
suitable for powering one or two safety
beams and an extra receiver. Traffic
Detector Loops, Intercoms, CCTV
Cameras etc., must use their own
power supplies.
Initial Power-up
1. Put the machine in ‘Manual’ by unlocking and pulling the Manual Over-ride Lever, and position the
gate mid-way.
2. Connect the two batteries with the white jumper lead provided, and switch on the mains.
3. Engage the Manual Over-ride Lever. The display will flash ‘S C’ and the motor will start running slowly.
4. Check that the gate is closing, in which case skip to 6. If not, go to step 5.
5. Pull the Manual Over-ride Lever. Referring to Fig. 1, swap the Motor wires on the second plug. Re-
engage the Manual Over-ride Lever and the motor will close slowly.
6. On reaching the closed position, the operator will detect the rail-stop and halt, and display C”.
Once the operator has found the closed position, it is then necessary to learn the open position, as
described in the next section. Important! For safety reasons, a sturdy rail-stop must be securely fitted to
the track of the sliding gate in the fully open position.

7
Programming Overview
Note: Programming may be entered only if ‘C’ (for closed), ‘S-n’ (Seek stopped) or if a fault code ‘F’ is displayed.
Programming of features is achieved by pressing the Enter (ENT) and Select (SEL) buttons together. The Program Display will
show ‘P’. Thereafter every press of the SEL button will cause a different letter to appear, representing different features. When
the required letter appears, press ENT to program that feature, and the letter will start flashing. Use SEL to step through the
setting options and ENT to confirm the selection. After the display returns to ‘P’, press ENT to exit.
Limits (L)
1. As above, press ENT and SEL together and ‘P’ will
appear on the display.
2. Press the SEL button. The Display will change to ‘L’.
3. Press the ENT button again and the ‘L’ will start
flashing.
4. Press the ENT button again and the motor will open
slowly until the open rail-stop is detected.
5. The operator will automatically close again at
normal speed, leaving a small gap before the stop,
and the Display will show ‘C’. The Limits have now
been programmed.
Auto close delay (d)
Note: Autoclose requires a functional Safety Beam to
be fitted and selected (see next section). If
Autoclose is required with no Safety Beam fitted,
then connect a link from ‘0V-COM’ to ‘Beam N.C.’
1. Press ENT and SEL to display ‘P’.
2. Press SEL until ‘d’ is displayed.
3. Pressing ENT will cause the ‘d’ and 0, 1, 2 or 3 to flash.
0 indicates auto close is not selected. 1 indicates a 5
second delay, 2 for 10 seconds and 3 for 20 seconds.
4. Press SEL until the desired option is displayed.
5. Press ENT to confirm the selection.
Safety Beam (b)
1. Press SEL until ‘b’ is displayed.
2. Press ENT and ‘b 0’ or ‘b 1’ will flash. ‘b 0’ means
beam disabled and ‘b 1’ means beam enabled.
3. Press SEL to select 0 or 1.
4. Press ENT to confirm the selection.
Obstacle Sensing (o)
1. Press SEL until ‘o’ is displayed. Level 1 is the most
sensitive and 3 the least.
2. Press ENT and the ‘o’ and a digit will flash.
3. Press SEL until the desired option is displayed.
4. Press ENT to confirm the selection.
Note: Start with this setting on 1, and increase it if,
during normal running, the gate stops and reverses
while closing.
Record Remote (r)
1. Press SEL until ‘r’ is displayed.
2. Press ENT and the display will flash ‘r n’ (for new”
remote).
3. Press the desired button on the e-key Remote. The
decimal point on the display will flash.
4. Release the button and ‘r C’ will flash. (‘C’ for
‘confirm’).
5. Press the same button to confirm the code.
6. Release the button and the display will flash ‘r n’,
ready for the next remote, if any.
7. Repeat from step 3 for each required e-key Remote.
8. Press ENT to end the sequence.
Note: The controller can store sixteen separate e-key
Remotes, using different buttons on each.
An attempt to record a seventeenth remote will be
ignored.
Erase Remotes (E)
Warning: This function removes all of the e-key
Remotes that have been recorded.
1. Press SEL until ‘E’ is displayed.
2. Press ENT and the ‘E’ will flash. To exit without erasing
at this point, press ENT.
3. Press SEL and ‘≡’ is displayed.
4. Press ENT and all codes will be erased.
Type (t)
(Type of operation: ‘Standard’ or ‘Commercial’)
1. Press SEL until ‘t’ is displayed.
2. Press ENT and ‘t S’ for Standard, or ‘t C’ for
Commercial will flash. Standard type gives the
normal operation with ‘Open, Stop and Close’ by
means of the Remote or ‘Control’ input.
Commercial type gives separate Open, Close and
Stop functions, connected as in Fig. 1.
3. Press SEL to select ‘S’ or ‘C’ is displayed.
4. Press ENT to confirm the selection.
Exit programming (P)
1. Press SEL until ‘P’ is displayed.
2. Press ENT to exit, or press SEL to go through the
options again.
After exiting, the machine will move to the stop
position again.
Other Display Features
While opening the display will flash ‘r -O’ for ‘run
open’.
While closing the display will flash ‘r -C’ run close.
When the Lock feature is active, ‘≡’ is displayed. The
operator will not respond to any OPEN/CLOSE inputs,
and Auto close (if selected) will be disabled.
Fault Codes
If the motor encoder is faulty, ‘F 1’ will flash on the
display.
If the obstacle setting is too low, ‘F 2’ will flash to
indicate a false obstacle during opening.
Head Office 011 474 9060
Johannesburg 011 792 7117
Pretoria 012 348 6829
Cape Town 021 933 5556
Durban 031 700 2110
Port Elizabeth coming soon
www.hydrodoors.co.za
Popular Gate Opener manuals by other brands
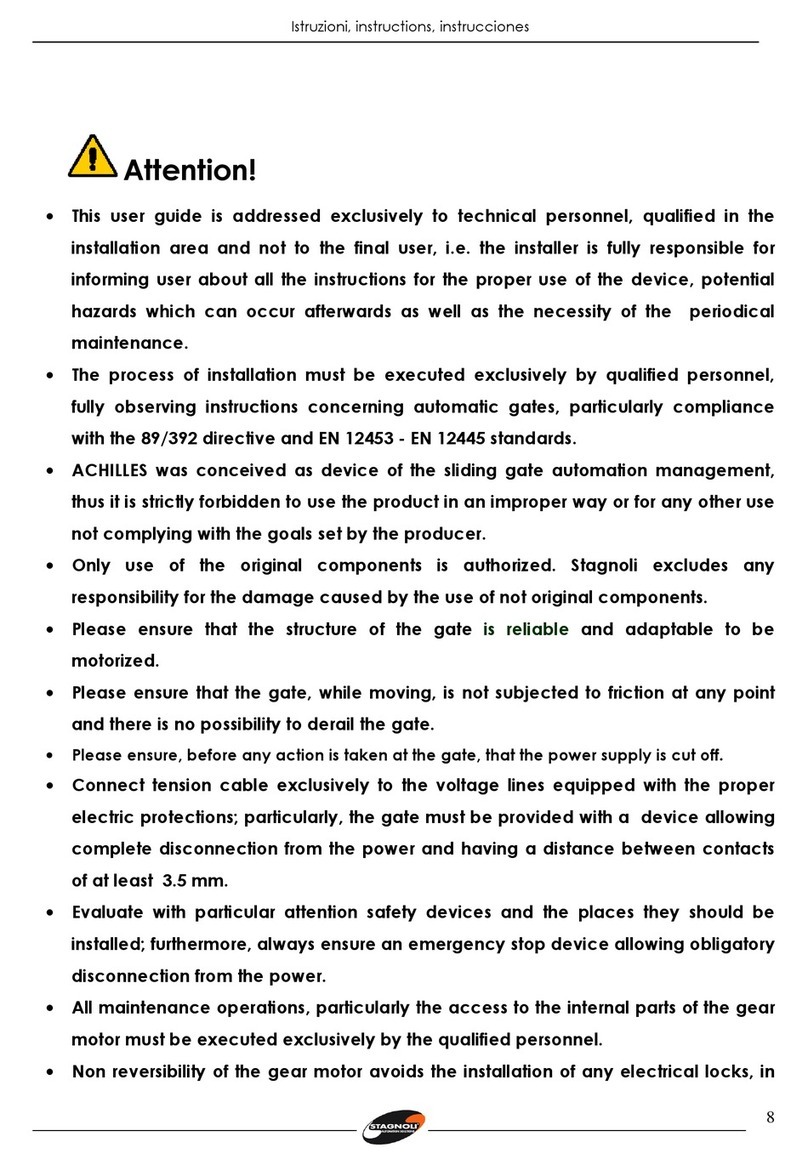
Stagnoli
Stagnoli ACHILLES-4000 instructions
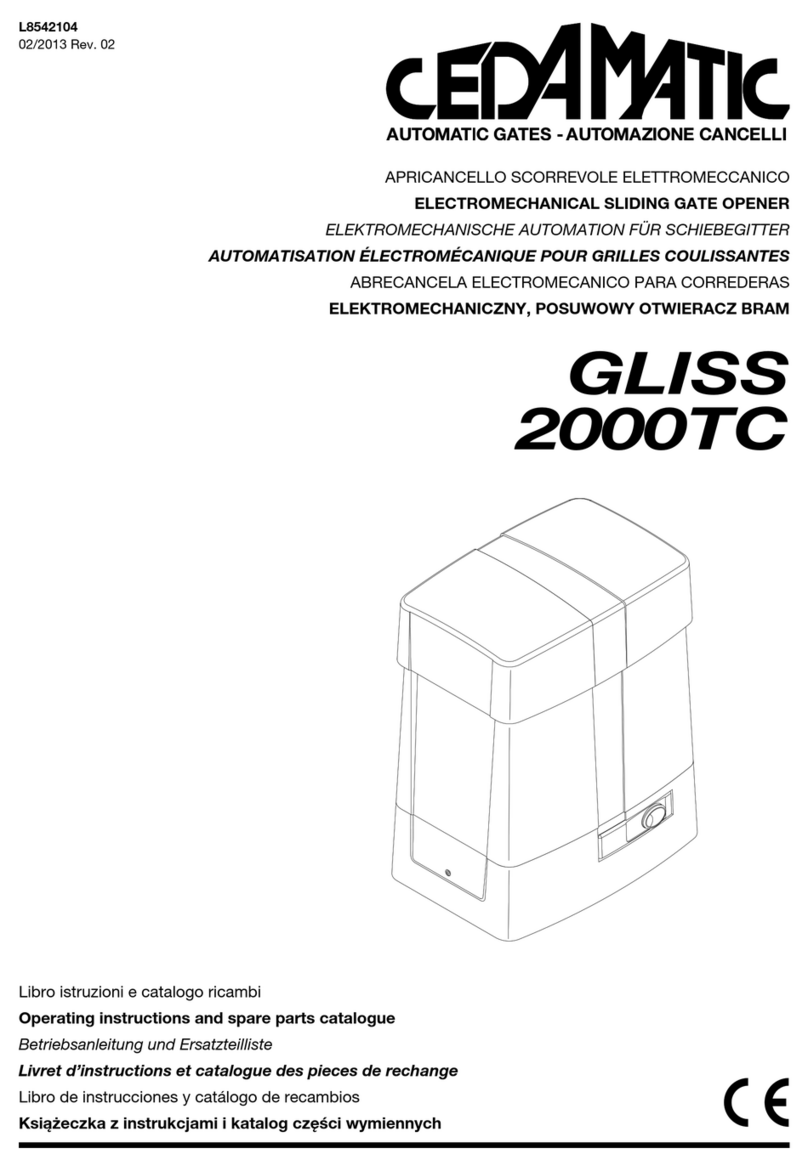
cedamatic
cedamatic GLISS 2000TC Operating instructions and spare parts catalogue
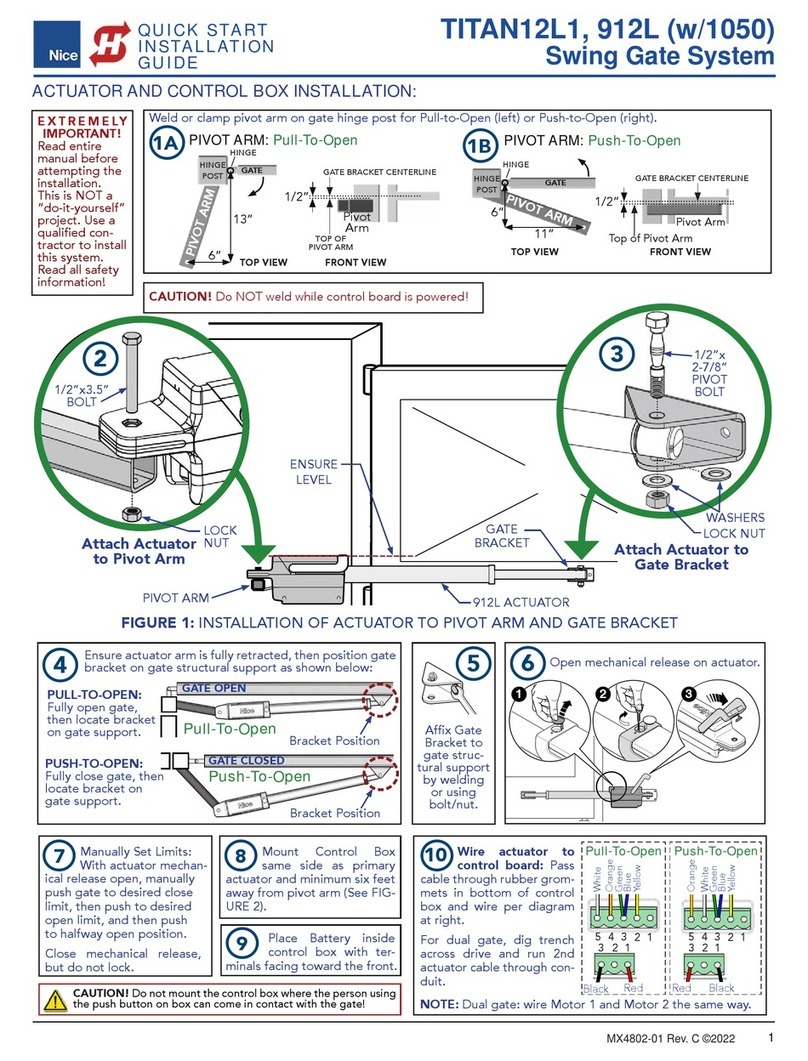
Nice
Nice Titan 912L Quick start installation guide

Solavis
Solavis DKC400Y installation manual

Chamberlain
Chamberlain LiftMaster LM3800A Additional Instructions for Installation and Operation

BFT
BFT ELI-250 manual

Erreka
Erreka LINCE Quick installation and programming guide
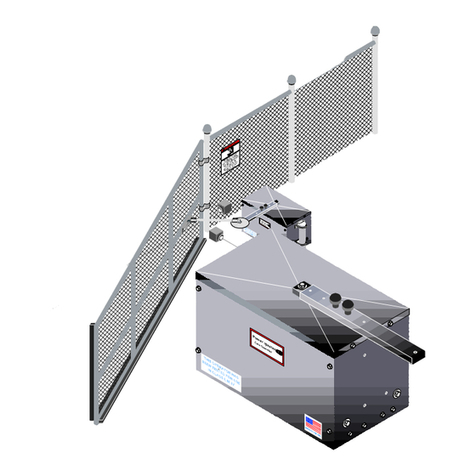
Power Master
Power Master rsw installation manual
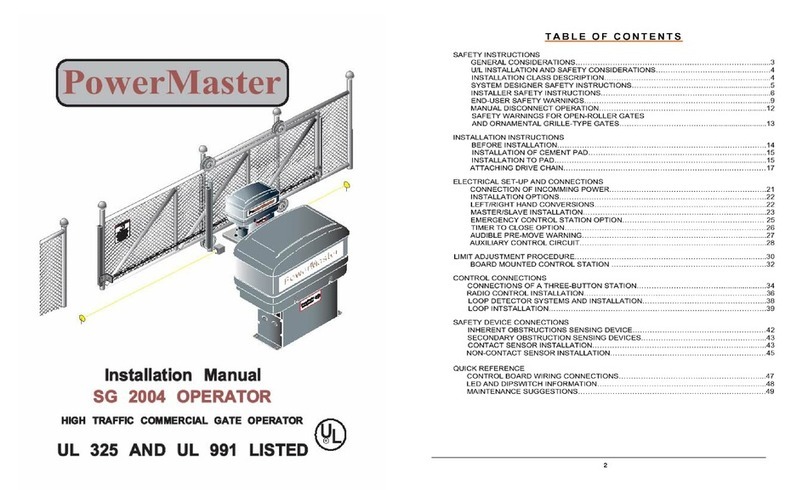
Power Master
Power Master SG 2004 installation manual
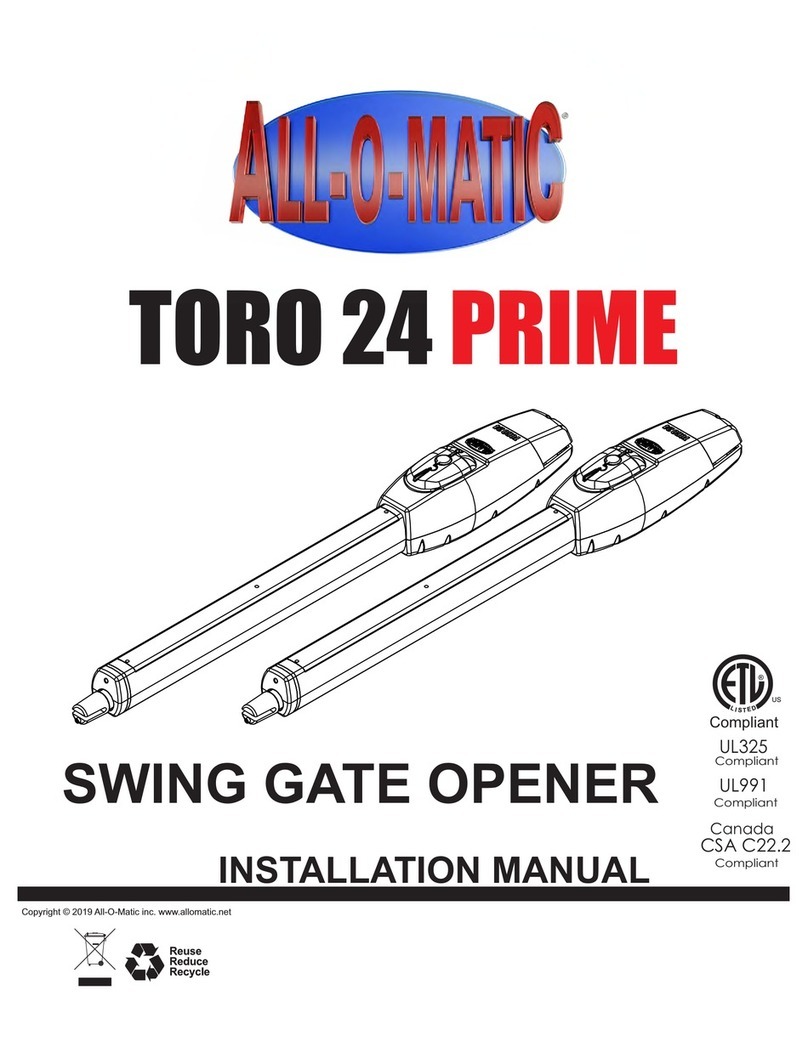
ALLOMATIC
ALLOMATIC TORO 24 PRIME installation manual

GiBiDi
GiBiDi MODO 220 Instructions for installation
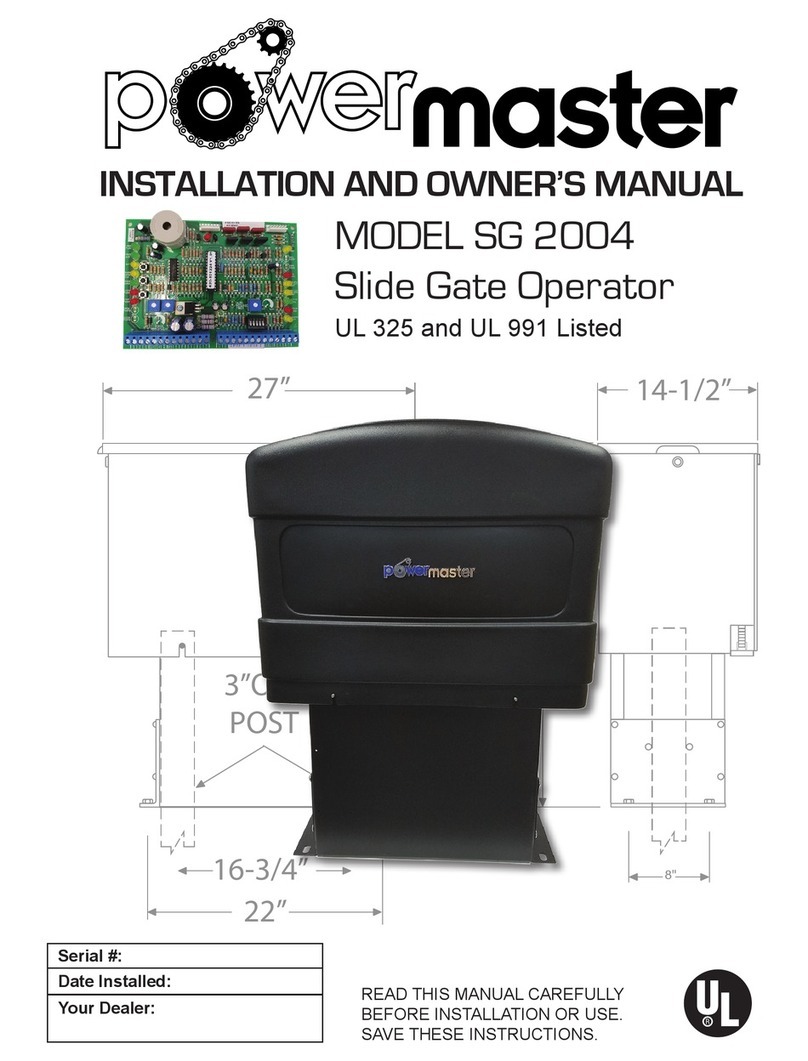
Power Master
Power Master SG 2004 Installation and owner's manual