DMN AL Series User guide

Declaration of conformity_2177176_1_Sn_153680 Page 1
Declaration of Conformity
(according to EU Directive 2014/34/EU, Annex X)
Order number: 2177176
Client : Unitec UK Ltd
Order number : 19838 - 26177
Description :Drop through valve Type : AL150 2
Serial number : RVNL153680
The manufacturer and technical authorised representative DMN Machinefabriek Noordwykerhout B.V.
herewith declares that the product described above is in compliance with the basic requirements of
Machine Directive 2006/42/EC with reference to the technical related documents corresponding Appendix
VII, Part B of the Directive and conforms to the following fundamental stipulations of this directive (Addendum
1): Nbr. 1.1.2; 1.1.3; 1.1.5; 1.1.6; 1.2.2; 1.2.6; 1.3.1 - 1.3.4; 1.3.6-1.3.8.2; 1.3.9; 1.4.1; 1.4.2. 1; 1.4.2.2; 1.5.1-
1.5.4; 1.5.6-1.5.9; 1.5.13; 1.6.1-1.6.5; 1.7.1; 1.7.1.1; 1.7.1.2; 1.7.2; 1.7.3; 1.7.4.1- 1.7.4.3; 2.1.1; 2.1.2.
Pressure Equipment Directive 2014/68/EU. The DMN-WESTINGHOUSE rotary valves and/or diverter
valves do not fall under the scope of this directive (see Article 1 –2f) as they are classified no higher than
category I under article 13 of this directive.
ATEX Directive 2014/34/EU.
1. The DMN-WESTINGHOUSE Drop through valve is certified according to
Type Examination CertificateBVS03 ATEX H051 X.
D St1.
II1D (Internal)
II3D (External)
Applicable standards:
EN 1127-1:2011, EN 13463-1:2009, EN 13463-5:2011, EN 14460:2006
2. DMN Machinefabriek Noordwykerhout B.V. has a quality notification according to Annex IV
through LCIE 03 ATEX Q 8082
The notified bodyin charge of quality surveillance is
LCIE (0081)
33, Avenue du Général Leclerc
92260 Fontenay aux Roses
France
Check the data on the type plate and read the manual before installing the valve.
The above mentioned machine in the supplied version is designed to be incorporated into an installation or
mounted on one or more other machines. Operation is prohibited until it has been confirmed that the complete
installation or composition of machines of which the component is part of has been installed in accordance with
the Directive 2006/42/EC or any other applicable directives or national regulations. The operation and safety
instructions in the operating and maintenance manual must be complied with.
In response to a reasoned request bythe national authorities relevant information on the partlycompleted
machinery will be submitted for inspection. Inspection of the information shall be without prejudice to the
intellectual propertyrights of the manufacturer of the partly completed machinery.
DMN Machinefabriek
Noordwykerhout B.V.
3, Gieterij
2211 WC Noordwijkerhout
The Netherlands
www.dmnwestinghouse.com
Print date : 15-12-2017
H.E.J.H. Meima
Quality Assurance Manager

DOC Packing cord Teadit 2006_2177176_1_Sn_153680 Page 1
Declaration of Compliance
for materials and articles intended to come into contact with food
Order number: 2177176
Client : Unitec UK Ltd
Order number : 19838 - 26177
Description : Drop through valve Type : AL150 2
Serial number : RVNL153680
The manufacturer and technical authorised representative DMN Machinefabriek Noordwykerhout
B.V. herewith declares that
Packing cord Teadit 2006 FDA
is in compliance with the basic requirements of
FDA 21 CFR 177.1550 materials are conform to the Code of Federal Regulations of the
Food and Drug Administration (FDA).
The part is made identifiable by this certification: the relevant documentation is archived on file and
in response to a reasoned request by the customer and national authorities relevant information on
the partly completed machinery will be submitted for inspection. Inspection of the information shall
be without prejudice to the intellectual property rights of the manufacturer of the partly completed
machinery.
The end user has to verify that the end product does not change the organoleptic properties of the
foodstuff.
Article number Description
20803064 Packing set AL 100 TEADIT 2006 FDA
20803066 Packing set AL-BL 150/175 TEADIT 2006 FDA
20803070 Packing set AL-BL 200/250 TEADIT 2006 FDA
20803074 Packing set AL-BL 300/350 TEADIT 2006 FDA
20803076 Packing set AL-BL 400/450 TEADIT 2006 FDA
20803078 Packing set AL 500 TEADIT 2006 FDA
DMN Machinefabriek
Noordwykerhout B.V.
3, Gieterij
2211 WC Noordwijkerhout
The Netherlands
www.dmnwestinghouse.com
Print date : 3-1-2018
H.E.J.H. Meima
Quality Assurance Manager

Explosion-Proof Rotary valves
DMN-WESTINGHOUSE
Operation instructions + Maintenance
Safety instructions
AL
AML
BL
ML(D)
ATEX –Approval autonomous Protective System and Equipment
D
II 1D / 2GD c
or
D
II 1D / 3GD c
or
D
II 1D / - c
IMPORTANT: Read before commissioning :
Operation instructions Explosion-Proof Rotary valves.
Operation instructions Standard Rotary valves. (Appendix)
and then store carefully for future use !
Type : AL150 2
Serial no. : RVNL153680 to RVNL 153680
DMN-WESTINGHOUSE order no. :2177176
Year of construction : 2017

DMN-WESTINGHOUSE Explosion-Proof Rotary Valves
Code: RV-Ex.pro-E.B.01.D 05-2016
2
Directive 2014/34/EU
Notified body EC-Type examination.
EXAM
BBG Prüf- und Zertifizier GmbH
Dinnendahlstr. 9
44809 Bochum
Germany
Certificate number BVS 03 ATEX H 051 X.
Notified body in charge of quality surveillance.
LCIE
33, Avenue du Général Leclerc
92260 Fontenay aux Roses
France
Identification number 0081
D
II 1D/ 2 GD c
1D Internal Rotary valve
Zone 20-21-22
2 GD External Rotary valve
Zone 1-21
D
II 1D/ 3 GD c
1D Internal Rotary valve
Zone 20-21-22
3 GD External Rotary valve
Zone 2-22
D
II 1D/ - c
1D Internal Rotary valve
Zone 20-21-22
- External Rotary valve
No Zone
DMN Machinefabriek Noordwykerhout B.V.
3, Gieterij
2211 WC Noordwijkerhout
The Netherlands
www.dmnwestinghouse.com

DMN-WESTINGHOUSE Explosion-Proof Rotary Valves
Code: RV-Ex.pro-E.B.01.D 05-2016
3
General
- For the promotion of the life span and correct functioning of DMN-
WESTINGHOUSE rotary valves we advise you to respect these operation
instructions and to carry out maintenance work accordingly.
- Should there be any problems, please contact our technical sales depart-
ment.
-No liability is accepted for damage and malfunction caused by non-observation
of these operation instructions, modification of the rotary valve without written
approval of DMN Machinefabriek Noordwykerhout B.V. (hereinafter called
DMN). DMN does not accept any liability for damage or accidents resulting from
improper use.
Copyright
Copyright © DMN Machinefabriek Noordwijkerhout B.V. All rights reserved. All
information including drawings shown in this manual are covered by copyright. No part
of this manual may be reproduced or published in any form or in any way,
electronically, by print, photo print, microfilm or any other means without prior written
permission from DMN.

DMN-WESTINGHOUSE Explosion-Proof Rotary Valves
Code: RV-Ex.pro-E.B.01.D 05-2016
4
Contents Page
1. Safety instructions Rotary valves 5
1.1 General safety instructions 5
1.2 Symbols 5
1.3 Responsibilities of management and maintenance personnel 6
1.4 Applying the safety instructions when installing a valve 6
1.5 Applying the safety instructions when the valve is in operation 6
1.6 Applying the safety instructions during maintenance and repair 6
1.7 Safety instructions for use in potentially explosive atmosphere 7
2. Explosion-Proof Rotary valves 8
2.1 ATEX approved autonomous protective system 8
2.2 Type designation 11
2.3 Intended use 11
3. Installing the Rotary valve in a potentially explosive atmosphere 12
3.1 Power and rotor speed of rotary valves 14
3.2 Drive 15
3.3 If delivery excludes drive 15
3.4 Accessories 17
4. Dismantling, re-assembling and adjusting instructions 19
4.1 Clearances settings 19
5. Inspection and maintenance 20
5.1 Checking rotor clearances 20
5.2 After an explosion 21
5.3 Maintenance every 3 months or after 2,500 operating hours 21
5.4 Maintenance of motor / gearbox 21
30

DMN-WESTINGHOUSE Explosion-Proof Rotary Valves
Code: RV-Ex.pro-E.B.01.D 05-2016
5
1. Safety instructions Rotary valves
1.1. General safety instructions
The safety instructions as described below should be followed by the user when:
- installing the valve;
- maintaining and repairing the valve.
The safety instructions should be read carefully both by management and maintenance
personnel before carrying out the above operations.
Failure to follow these safety instructions, may result in one or more of the following:
- the safety of the maintenance personnel could be endangered;
- the valve may not function correctly;
- the system which contains the valve may be damaged.
Modifications and alterations to the product are not permitted other than by
DMN trained personnel, to ensure safe operation.
1.2. Symbols
Hazard.
Possible consequences: Severe or fatal injuries.
Hazardous situation.
Possible consequences: Slight or minor injuries.
STOP
Harmful situation.
Possible consequences: Damage to the Rotary valve and the
environment.
Important Notes on Explosion Protection.
Remark.

DMN-WESTINGHOUSE Explosion-Proof Rotary Valves
Code: RV-Ex.pro-E.B.01.D 05-2016
6
1.3. Responsibilities of the management and maintenance personnel
The management must ensure that:
- the maintenance personnel observe the safety instructions, as described in this
document;
- any equipment necessary for working according to the safety instructions is made
available;
- the maintenance personnel possess the necessary skills.
Maintenance personnel should follow these safety instructions when carrying out
installation, repair and maintenance.
1.4. Applying the safety instructions when installing a valve
After removing the packaging material it is possible to reach the inlet and outlet of the
valve. During this operation do not turn the rotor by hand.
Do not alter, remove or paint the type specification plates of the valve, drive unit or
fitted switches.
1.5. Applying the safety instructions when the valve is in operation
Only operate the valve when it is fitted with the protective safety parts supplied by
DMN. These are:
- mechanical protection e.g. chain guard and end cover plates;
- electro-mechanical protection e.g. safety switches (if fitted).
While the valve is in operation no maintenance or repair work must
be carried out.
1.6. Applying the safety instructions during maintenance and repair work
When product qualities necessitate supplementary safety instructions and wearing of
protective equipment, it is obligatory to follow the local safety instructions.
Before maintenance and repair work is carried out:
- electrical supply to the valve motor must be isolated.
- air pressure to shaft seals must be isolated (if fitted).
After the maintenance and repair work has been carried out, all safety parts removed
during the work should be re-assembled and their operation should be checked.

DMN-WESTINGHOUSE Explosion-Proof Rotary Valves
Code: RV-Ex.pro-E.B.01.D 05-2016
7
1.7. Safety instructions for use in potentially explosive atmosphere
Explosive concentrations of dust can lead to severe or fatal injuries
in connection with hot surfaces, parts under power and moving
parts of the Rotary valve.
Installation, connection, start-up, maintenance and repair work on
the rotary valve may only be performed by a qualified specialist
while taking the following into account:
these instructions
the warning and information signs on the Rotary valve
currently valid national / regional regulations
(Explosion protection, Safety, accident prevention)
Check if there are any potentially explosive atmosphere, oils,
acids, gases, vapours, radiation etc. present during installation,
connection, start-up, maintenance and repair work.
The Rotary valves are intended for industrial systems and may only be used in
accordance with the information provided in DMN technical documentation and the
information listed on the nameplate.
They comply with the applicable standards and regulations and meet the
requirements of directive 2014/34/EU.

DMN-WESTINGHOUSE Explosion-Proof Rotary Valves
Code: RV-Ex.pro-E.B.01.D 05-2016
8
2. Explosion-Proof Rotary valves
2.1. ATEX approved Autonomous protective system.
The following table shows the valve types that can be used as autonomous protective
system:
Executions
Type
Size
Dust-
class
Max.
Clearance
Standard
Easy
detachable
MZC
Dairy
Dairy MZC
AL
150-175-200
250-300-350
St.1
0.2mm
1
1D
1MZC
AML
150-200-250
300-350
2
2D
2MZC
BL
150-175-200
250-300-350
3N
3ND
3NMZC
AL
400-450-500
0.3mm
3C
3CD
3CMZC
AL
150
St. 2
< 0.15mm
4C
4CD
4CMZC
4TCO
4TCOD
4TCOMZC
4TS
4TSD
4TSMZC
AL
150-175-200
250-300
St1.
0.2mm
DAI
DMZC
BL
150-175-200
250-300
AML
150-200-250
300-350
ML
150
St1.
0.2mm
1
MLD
150
2
3N
3C
4C
These valves correspond to the design requirements of device group II
D
II 1D/ 2 GD c
1D Internal Rotary valve
Zone 20-21-22
2 GD External Rotary valve
Zone 1-21
2GD for the external of the valve if mounted with direct drive or with a brass
chain guard with chain tensioner.
D
II 1D/ 3 GD c
1D Internal Rotary valve
Zone 20-21-22
3 GD External Rotary valve
Zone 2-22
3GD for the external of the valve if mounted with direct drive or standard mild
steel chain guard.
D
II 1D/ - c
1D Internal Rotary valve
Zone 20-21-22
- External Rotary valve
No Zone

DMN-WESTINGHOUSE Explosion-Proof Rotary Valves
Code: RV-Ex.pro-E.B.01.D 05-2016
9
The Rotary valves are explosion proof tested according to VDI 2263 Part 3.
Certified to have a pressure shock resistance of 10 bar and flame proof ness.
Excluded are:
-Type BL enlarged inlet
-Aluminium castings
-Rotor executions with Plastic (Teflon, Polyurethane, etc), or scraper
blades
Ambient temperature
Operate rotary valves at an ambient temperature of –20°C to +40°C.
Conveying air temperature
The conveying air must not exceed a temperature of +70°C.
Surface temperature
The surface temperature of the rotary valve depends on the temperature of the
product to be handled.
The recommended maximum product temperature for the rotary valve is +150°C
depending on the type of rotary valve.
The temperature increase of the valve by failure is T=50°C.
Marked temperature if equipment is subject to type testing (EN-13463-1)
T=50°C = measured maximum surface temperature + 5 K
If rotary valve is supplied bare shaft.
Maximum surface temperature of the bare shaft Rotary valve is 120°C/T4.
(calculation: conveying air 70°C +(T=50°C) =120°C)
If the temperature of the product to be handled can is higher then 70°C than this will
influence the surface temperature of the rotary valve. (see table)
Product temperature
Max.surface temperature
70°C
120°C
T4
80°C
130°C
85°C
135°C
90°C
140°C
T3
100°C
150°C
110°C
160°C
120°C
170°C
130°C
180°C
140°C
190°C
150°C
200°C

DMN-WESTINGHOUSE Explosion-Proof Rotary Valves
Code: RV-Ex.pro-E.B.01.D 05-2016
10
Relationship of the maximum surface temperature of the equipment and the
minimum ignition temperature of dust cloud and dust layer.
Dust cloud.
Maximum surface temperature = 2/3 x Minimum Ignition Temperature
Dust layer up to 5mm.
Maximum surface temperature = Smouldering Temperature –75 K
Depending on the properties of the product to be handled, it can be necessary to
reduce the frictional area of the blades that maintain the air pressure in the valve.
This can be done in the first instance by using blades that are chamfered on 3 sides.
Examples: PVC powder tends to smear, Sugar glazes etc.
If in doubt please contact DMN.
If the properties of the product to be handled are not known then the surface
temperature must be checked several times after starting the valve to see if there is
a temperature increase.
If the surface temperature is higher then listed on the nameplate,
the rotary valve must be stopped immediately.
It is not allowed to exceed above the maximum surface temperature
listed on the nameplate.
If in doubt please contact DMN.
The plant operator must ensure that any possible dust accumulation does not
exceed a maximum thickness of 5 mm in accordance with EN50281-1-2.
There must be no flammable solvents within the dust.

DMN-WESTINGHOUSE Explosion-Proof Rotary Valves
Code: RV-Ex.pro-E.B.01.D 05-2016
11
2.2. Type designation
Example Rotary valve
Type
Size
Material of
construction
Execution
AL
150
2
MZC
Type
AL
Size
150
AML
175
BL
200
ML
250
MLD
300
350
400
450
500
Material of
construction
1
Cast Iron
2
Stainless steel
3N
Cast Iron-Complete Nickel plated
3C
Cast Iron- Internals Chrome plated
4C
Cast Iron-Bore Chrome plated
4TCO
Cast Iron-Tungsten coated
4TS
Cast Iron-Tungsten coated
Execution
-
Standard
D
Easy detachable
MZC
Easy detachable with extraction mechanism
DAI
Dairy
DMZC
Dairy with extraction mechanism
2.3. Intended use
The Rotary valves are designed for the metering and pneumatic transport of products in
powder or granular form in a potentially explosive atmosphere.
The rotary valve can be mounted under/above a silo, mill, sifter, etc.
The rotary valve is flameproof in conveying direction.
Depending on Type and execution the Rotary valve can be used for pressure
differentials up to 2 Bar and product temperture up to 150°C.
The technical specifications, General assembly and parts list of the Rotary valve are
in a separate Operation and maintenance instructions. (see appendix)

DMN-WESTINGHOUSE Explosion-Proof Rotary Valves
Code: RV-Ex.pro-E.B.01.D 05-2016
12
3. Installing the Rotary valve in a potentially explosive atmosphere
Remove all packing material and preservatives.
Check for any transport damage.
Check valve interior is free from foreign material.
Check if there are any potentially explosive atmosphere, oils,
acids, gases, vapours, radiation etc. present during installation.
Please follow safety instructions of chapter 1 when installing the
Rotary valve in a potentially explosive atmosphere.
Does the following information on the nameplate of the Rotary
valve corresponds to the potentially explosive on-site atmosphere.
Pay specific attention to:
Unit group
Explosion-proof category
Dust- or Gas area
Temperature class
Maximum surface temperature
If an explosion takes place the rotary valve must stop immediately,
a sensor suited for the purpose must do this automatically.
This to prevent transport of burning or smoldering product over
the rotary valve further into the system.
The sensor and control unit are not part of the standard supply of
DMN.
Ensure that a sensor and control unit are installed in the system.
The DMN-WESTINGHOUSE rotary valves are pressure shock
resistant up to 10 bar.
If an explosion could occur above 10 bar, then the user of this
equipment must ensure adequate safety measures are installed.
Turning the rotor is prohibited.
Danger to fingers and hands.
Always ground the rotary valve, use the flange connection bolts,
or the optional earth-stud on end cover or motor base plate.
Check that the electrical leakage resistance is less than 106.

DMN-WESTINGHOUSE Explosion-Proof Rotary Valves
Code: RV-Ex.pro-E.B.01.D 05-2016
13
Before installing the rotary valve in the system check the
clearances between rotor and Body/Cover. (See 5.1)
STOP
When installing the valve make sure it is not unevenly loaded by
external forces or subject to vibrations.
D
II 1D/ - c
1D Internal Rotary valve
Zone 20-21-22
- External Rotary valve
No Zone
Rotary valve external no zone.
It is not allowed to have explosive atmosphere out side.
No dust layers are allowed.
Pay specific attention to the shaft seal and the shaft seal area
- Gland seals
In case of gland seals by means of gland packing it is necessary before starting the
system to fasten the gland in order to set the gland packing in such a way that it seals
and the rotor will be able to run.
After running in tighten gland follower to ensure sealing.
- Shaft sealing with air purge.
When using an air purge gland oil-free dry air must be used. The diameter of the air
pipe supply should be equal to or larger than the connection on the valve. The pressure
of this purging air should be 0.5 bar higher than the pressure in the valve. The air
pressure must be applied before product enters the valve and before conveying
pressures are applied.
The air supply must always be present when there is product in the valve, and
especially after conveying ceases.
After running in tighten gland follower to ensure sealing.
Check adjustment and functioning purge air, if necessary re-adjust.
For more information about adjustment and replacement instructions
for shaft sealing see Standard operation instructions. (Appendix)

DMN-WESTINGHOUSE Explosion-Proof Rotary Valves
Code: RV-Ex.pro-E.B.01.D 05-2016
14
3.1. Power and rotor speed rotary valves
The following tables show the power and rotor speed for each type and size of DMN-
WESTINGHOUSE valve.
For good functioning of the valve the rotor tip speed must not exceed 0.66m/sec.The
standard rotor speeds are usually between 15-25 RPM depending on size of valve.
The Power depends on the minimum required torque and rotor speed.
According to the ATEX directive the maximum velocity must not be
higher then 1 m/s and the maximum power of the motor gear unit is
not higher then 4 kW.
If higher velocity or power are required then please contact
DMN.
The ATEX approval ceases without prior consultation.
Type
Size
Minimum
torque
Max.
Power
Max. advised
Rotor speed
Max. allowed
Rotor speed
Rotor diameter
AL-BL
150
145 Nm
0,75 kW
30 RPM
30 RPM
170mm
AL-BL
175
145 Nm
0,75 kW
30 RPM
30 RPM
210mm
AL-BL
200
215 Nm
1,1 kW
30 RPM
30 RPM
260mm
AL-BL
250
290 Nm
1,5 kW
30 RPM
30 RPM
310mm
AL-BL
300
360 Nm
1,5 kW
30 RPM
30 RPM
380mm
AL-BL
350
510 Nm
1,5 kW
28 RPM
30 RPM
450mm
AL
400
1200 Nm
3 kW
23 RPM
30 RPM
555mm
AL
450
1875 Nm
4 kW
20 RPM
30 RPM
620mm
AL
500
2500 Nm
4 kW
18 RPM
26 RPM
720mm
Type
Size
Minimum
torque
Max. Power
Max. allowed
Rotor speed
Rotor diameter
AML
150
145 Nm
0,75 kW
30 RPM
170mm
AML
200
145 Nm
0,75 kW
30 RPM
210mm
AML
250
215 Nm
1,1 kW
30 RPM
260mm
AML
300
290 Nm
1,5 kW
30 RPM
310mm
AML
350
360 Nm
1,5 kW
30 RPM
380mm
Type
Size
Minimum
torque
Max. Power
Max. allowed
Rotor speed
Rotor diameter
ML(D)
150
145 Nm
0,75 kW
30 RPM
170mm

DMN-WESTINGHOUSE Explosion-Proof Rotary Valves
Code: RV-Ex.pro-E.B.01.D 05-2016
15
3.2. Drive
D
II 1D/ 2 GD c
1D Internal Rotary valve
Zone 20-21-22
2 GD External Rotary valve
Zone 1-21
D
II 1D/ 3 GD c
1D Internal Rotary valve
Zone 20-21-22
3 GD External Rotary valve
Zone 2-22
Explosive gas mixtures or concentrations of dust can lead to
servere or fatal injuries in connection with hot surfaces, parts
under power and moving parts on the gear unit / geared motor.
Installation, connection, start-up, maintenance and repair work on
the gear unit / geared motor may only be performed by a qualified
specialist while taking the following into account:
these instructions
the warning and information signs on the gear unit / geared
motor
currently valid national / regional regulations
(Explosion protection, Safety, accident prevention)
- Before starting the valve, check the oil level in the gear box. It should be filled
with the correct amount and type of oil according to the instructions.
Fit the breather cap on the gear box and check that the venting nipple is clean.
- Check the rotating direction of the valve rotor. It should rotate clockwise seen
from the drive end (see direction of the arrow).
Always ground the rotary valve, use the flange connection bolts,
or the optional earth-stud on end cover or motor base plate.
Check that the electrical leakage resistance is less than 106.
After assembly test run the valve.
3.3. If delivery excludes drive
Use drive and drive components that are CE marked and with a
ATEX-approval equal to or better than that of the rotary valve.
Please study the operation instructions supplied by the drive
manufacturer.

DMN-WESTINGHOUSE Explosion-Proof Rotary Valves
Code: RV-Ex.pro-E.B.01.D 05-2016
16
Does the following information on the nameplate of the gear unit
corresponds to the potentially explosive on-site atmosphere.
Pay specific attention to:
Unit group
Explosion-proof category
Dust- Gas area
Temperature class
Maximum surface temperature
Chain drive
- On one side of the valve holes have been tapped for fitting the motor base plate
(see drawing for dimensions).
- To fasten the chain guard, three holes have been tapped in the bearing housing
of the valve (see drawing for dimensions).
The chain drive must be protected by a guard.
When assembling the chain guard make sure that no ignition
sources (e.g. sparks through contact) can be created.
Check if there are any potentially explosive atmosphere, oils,
acids, gases, vapours, radiation etc. present during installation.
Please follow safety instructions of chapter 1 when installing the
Rotary valve in a potentially explosive atmosphere.
Chain guard
Zone
Marking
Chain guard
1-21
II 2GD
Brass chain guard
with chain tensioner.
2-22
II 3GD
Standard mild steel Chain guard
STOP
The sprockets should be fitted on the rotor shaft as close as possible
to the bearing housing.
The sprockets should not be hammered on to the shafts.
The sprockets on the shafts of the valve and the gear unit should
always be perfectly aligned.

DMN-WESTINGHOUSE Explosion-Proof Rotary Valves
Code: RV-Ex.pro-E.B.01.D 05-2016
17
3.4. Accessories ( If fitted )
D
II 1D/ 2 GD c
1D Internal Rotary valve
Zone 20-21-22
2 GD External Rotary valve
Zone 1-21
D
II 1D/ 3 GD c
1D Internal Rotary valve
Zone 20-21-22
3 GD External Rotary valve
Zone 2-22
Only use
Safety switch
Solenoid valve
Proximity switch
that are CE marked an with a ATEX-approval equal to or better
than that of the rotary valve.
Please study the operation instructions supplied by the
manufacturer.
Does the following information on the nameplate of the
Safety switch
Solenoid valve
Proximity switch
corresponds to the potentially explosive on-site atmosphere.
Pay specific attention to:
Unit group
Explosion-proof category
Dust- Gas area
Temperature class
Maximum surface temperature
-Safety switch

DMN-WESTINGHOUSE Explosion-Proof Rotary Valves
Code: RV-Ex.pro-E.B.01.D 05-2016
18
- Pressure regulator
-Zero speed indication
Drive side option 1. Drive side option 2.
Non drive side.
This manual suits for next models
27
Table of contents
Popular Control Unit manuals by other brands

Coster
Coster GCR 120 MANUAL RESET NORMALLY CLOSED SOLENOID VALVE FOR GAS
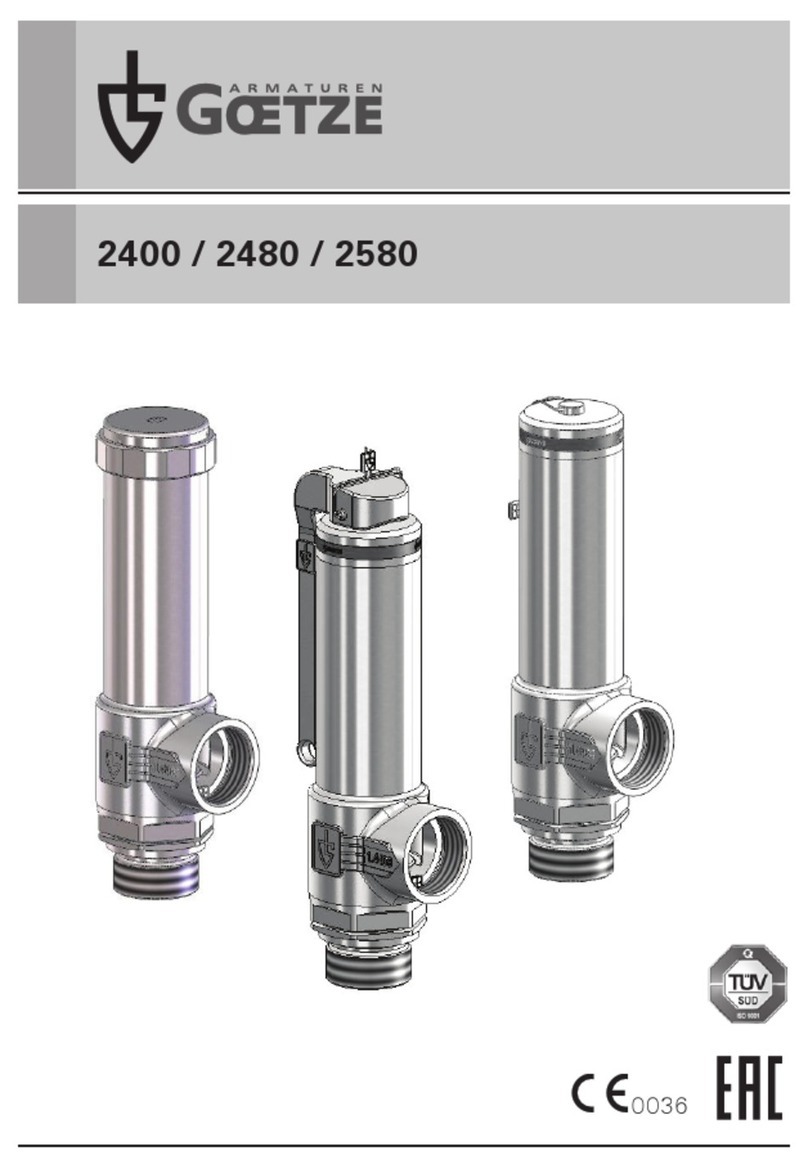
Goetze
Goetze 2400 Assembly instructions
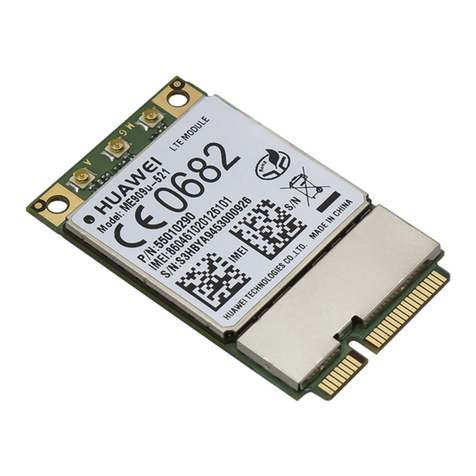
Huawei
Huawei ME909 Series Hardware guide
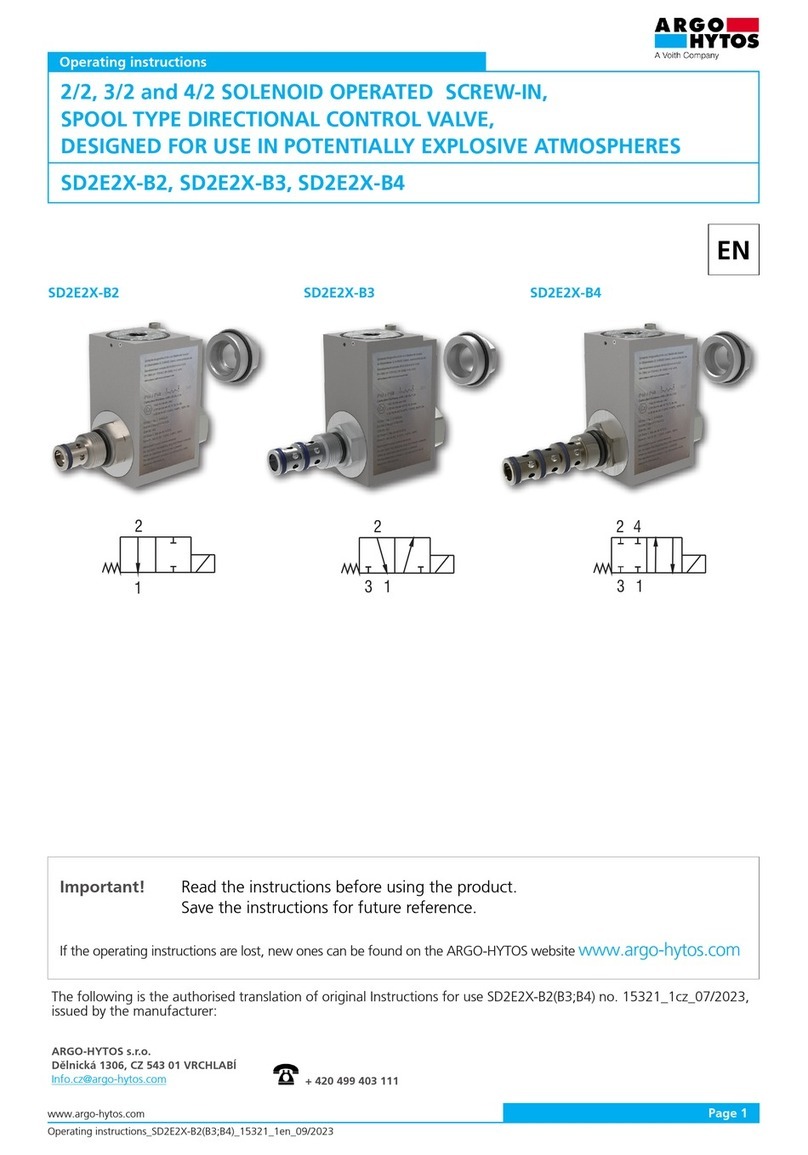
Volth
Volth ARGO HYTOS SD2E2X-B2 operating instructions
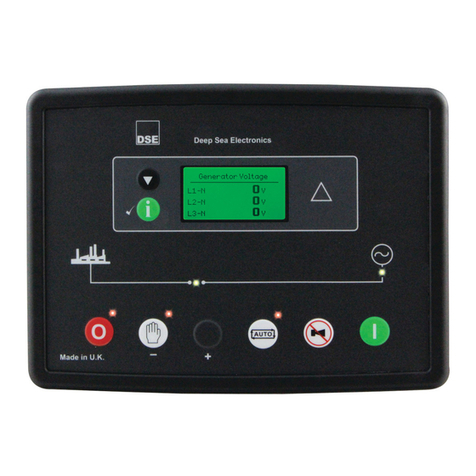
DEEP SEA ELECTRONICS
DEEP SEA ELECTRONICS DSEGenset DSE6110 MKIII Operator's manual

KSB
KSB BOAX- B operating instructions
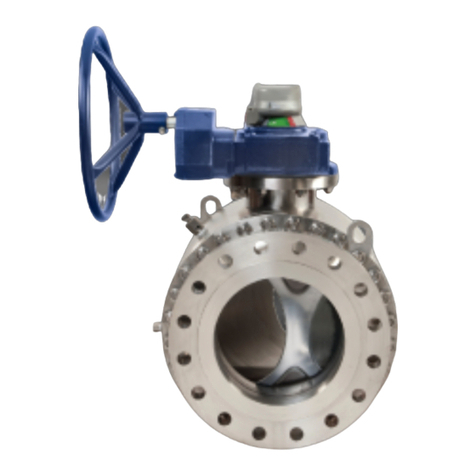
Val-Matic
Val-Matic QuadroSphere 4700 Series Operation, maintenance and installation manual

MKS
MKS HPS 145 Vacuum Sentry Series Operation and maintenance manual
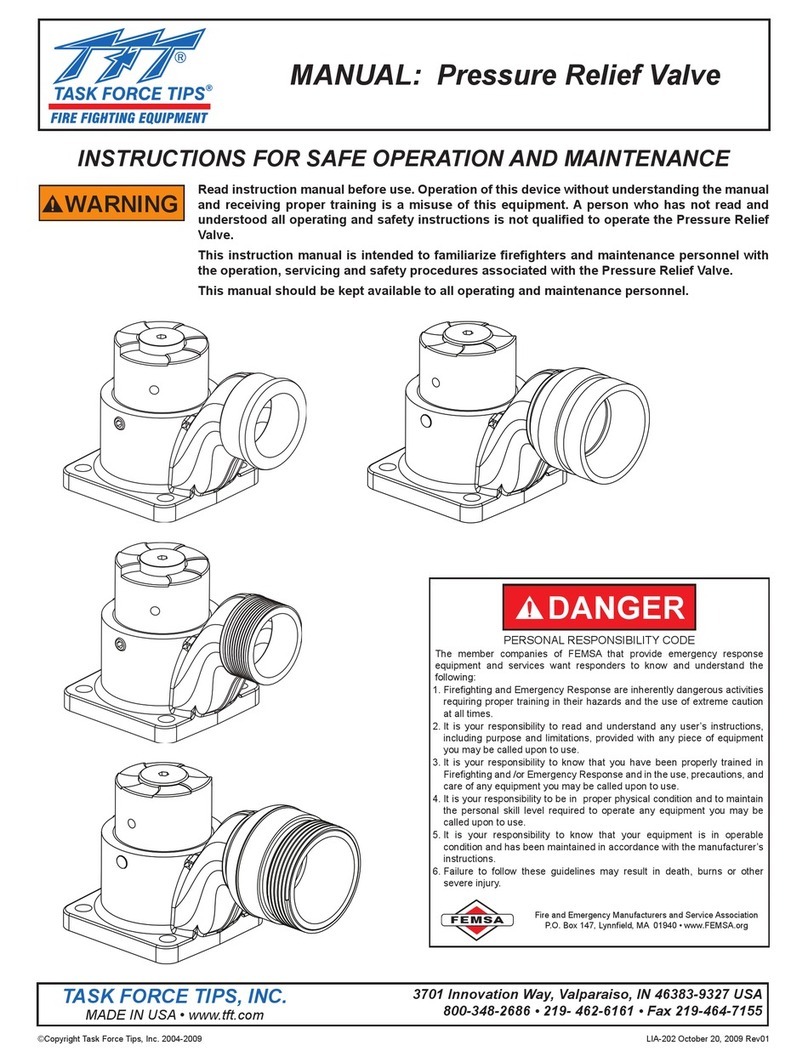
Task Force Tips
Task Force Tips A1150 INSTRUCTIONS FOR SAFE OPERATION AND MAINTENANCE
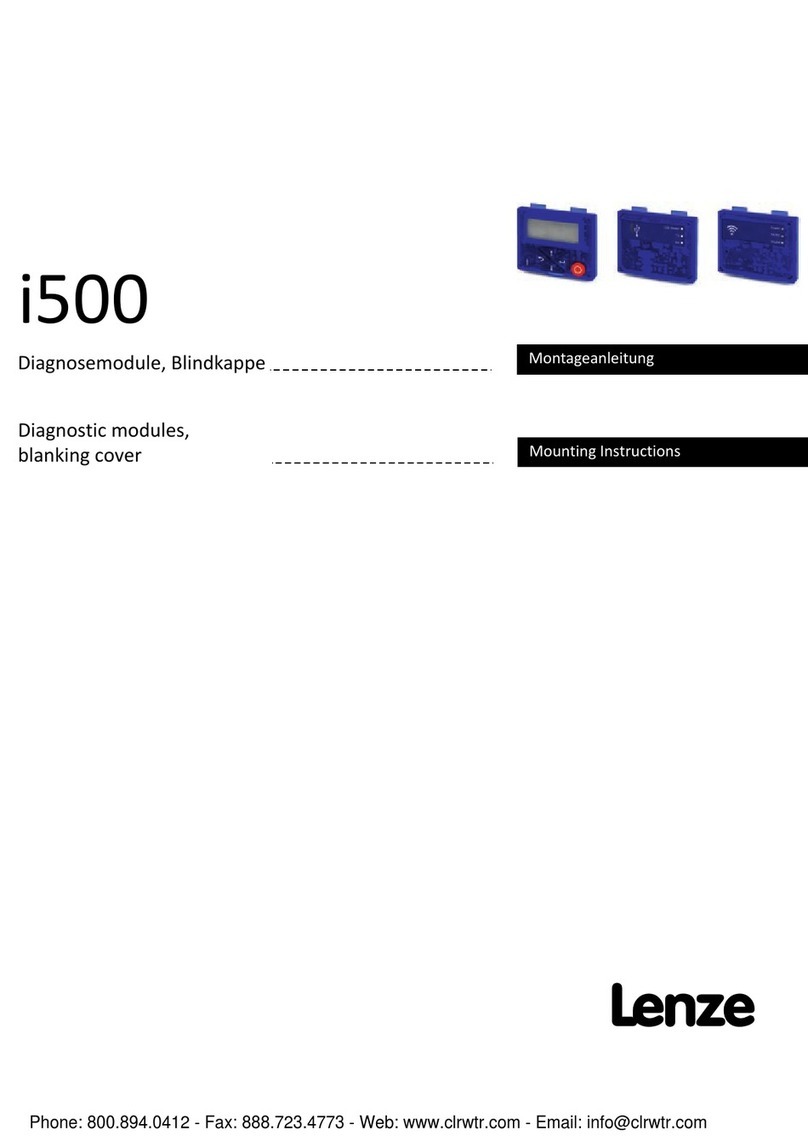
Lenze
Lenze i500 Series Mounting instructions

evertz
evertz 7700ACO-HD user manual
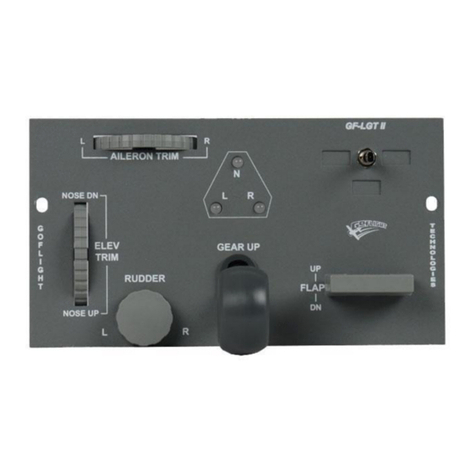
GoFlight
GoFlight GF-LGT manual