Dongcheng DZC05-26 User manual

Edition 3 Jan., 2017
Read through carefully and understand these
instructions before use.

GENERAL POWER TOOL SAFETY WARNINGS
(For All Power Tools)
WARNING! Read and understand all instructions.
Failure to follow all instructions listed below may result in electric
shock, fire and/or serious personal injury.
Save all warnings and instructions for future reference.
The term “power tool”in the warnings refers to your mains-operated (corded)
power tool or battery-operated (cordless) power tool.
Work Area Safety
1. Keep work area clean and well lit. Cluttered or dark areas invite accidents.
2. Do not operate power tools in explosive atmospheres, such as in the
presence of flammable liquids, gases, or dust. Power tools create sparks
which may ignite the dust or fumes.
3. Keep children and bystanders away while operating a power tool.
Distractions can cause you to lose control.
Electrical Safety
4. Power tool plugs must match the outlet. Never modify the plug in
anyway. Do not use any adapter plugs with earthed (grounded) power
tools. Unmodified plugs and matching outlets will reduce risk of electric
shock.
5. Avoid body contact with earthed or grounded surfaces, such as pipes,
radiators, ranges and refrigerators. There is an increased risk o electric
shock if your body is earthed or grounded.
6. Do not expose power tools to rain or wet conditions. Water entering a
power tool will increase the risk of electric shock.
7. Do not abuse the cord. Never use the cord for carrying, pulling or
unplugging the power tool. Keep cord away from heat, oil, sharp edges
or moving parts. Damaged or entangled cords increase the risk of electric
shock.
8. When operating a power tool outdoors, use an extension cord suitable for
outdoor use. Use of a cord suitable for outdoor use reduces the risk of electric
shock.
9. If operating a power in a damp location is unavoidable, use a residual current
device (RCD) protected supply. Use of an RCD reduces the risk of electric
shock.
NOTE: The term “residual current device (RCD)” may be replaced by the term
“ground fault circuit interrupter (GFCI)” or “earth leakage circuit breaker (ELCB)”.
Personal Safety
10.Stay alert, watch what you are doing and use common sense when operating
a power tool. Do not use a power tool while you are tired or under the
influence of drugs, alcohol, or medication. A moment of inattention while
operating power tools may result in serious personal injury.
11.Use personal protective equipment. Always wear eye protection. Protective
equipment such as dust mask, non-skid safety shoes, hard hat, or hearing
protection used for appropriate conditions will reduce personal injuries.
12.Prevent unintentional starting. Ensure the switch is in the off-position before
connecting to power source and /or battery pack, picking up or carrying the
tool. Carrying power tools with your finger on the switch or energising power tools
that have the switch on invites accidents.
13.Remove any adjusting key or wrench before turning the tool on. A wrench or a
key left attached to a rotating part of the power tool may result in personal injury.
14.Do not overreach. Keep proper footing and balance at all times. This enables
better control of the power tool in unexpected situations.
15.Dress properly. Do not wear loose clothing or jewellery. Keep your hair,
clothing, and gloves away from moving parts. Loose clothes, jewellery or long
hair can be caught in moving parts.
16.If devices are provided for the connection of dust extraction and collection
facilities, ensure these are connected and properly used. Use of dust
collection can reduce dust-related hazards.
Power Tool Use and Care
-1- -2-

17.Do not force the power tool. Use the correct power tool for your
application. The correct power tool will do the job better and safer at the rate
for which it was designed.
18. Do not use tool if switch does not turn it on or off. Any power tool that
cannot be controlled with the switch is dangerous and must be repaired.
19. Disconnect the plug from the power source and/or the battery pack
from the power tool before making any adjustments, changing
accessories, or storing power tools. Such preventive safety measures
reduce the risk of starting the power tool accidentally.
20. Store idle power tools out of the reach of children and do not allow
persons unfamiliar with the power tool or these instructions to operate
the power tool. Power tools are dangerous in the hands of untrained users.
21. Maintain power tools. Check for misalignment or binding of moving
parts, breakage of parts and any other condition that may affect the
power tool’s operation. If damaged, have the power tool repaired before
use. Many accidents are caused by poorly maintained power tools.
22. Keep cutting tools sharp and clean. Properly maintained cutting tools with
sharp cutting edges are less likely to bind and are easier to control.
23. Use the power tool, accessories and tool bits etc. in accordance with
these instructions, taking into account the working conditions and the
work to be performed. Use of the power tool for operations different from
those intended could result in a hazardous situation.
Service
24. Have your power tool serviced by a qualified repair person using only
identical replacement parts. This will ensure that the safety of the power
tool is maintained.
VOLTAGE WARNING:
Before connecting the machine to a power source (receptacle, outlet, etc.), be
sure the voltage supplied is the same as that specified on the nameplate of the
machine. A power source with voltage greater than that specified for the machine
can result in SERIOUS INJURY to the user, as well as damage to the machine. If
in doubt, DO NOT PLUG IN THE MACHINE. Using a power source with voltage
less than nameplate rating is harmful to the motor.
SPECIFICATIONS
Rated Power Input
720 W
Blows per Minute
0-4000 …/min
No-Load Speed
0-1200 r/min
Max. Drilling Capacity
Concrete
26 mm
Wood
30 mm
Steel
13 mm
Net Weight
2.93 kg
※Due to the continuing program of research and development, the specifications
herein are subject to change without prior notice.
ADDITIONAL SAFETY RULES
1. Wear a hard hat (safety helmet), and ear protectors. Exposure to the noise can
cause hearing damage.
2. Hold the tool firmly by both hands and always use the auxiliary handle. Failure to
operate can cause personal injury.
3. Hold tools by insulated gripping surfaces when performing an operation where the
cutting tool may contact hidden wiring or its own cord. Contact with a “live”wire will
make exposed metal parts of the tool “live”and shock the operator
4. Use appropriate detectors to determine or consult local power supply units for
relative data if utility lines, such as electric lines, gas lines and water lines are
hidden in the work area before screwing or drilling on the wall, floor or ceiling.
Once those utility lines are drilled, it will cause fire and electric shock accidents,
explosion or other damages to properties..
5. Check and ensure that the drill bit be correctly installed and secured before
operation.
-3- -4-

6. Under normal operation, the tool is designed to produce vibration. The screws
can come loose easily, causing a breakdown or accident. Check tightness of
screws carefully before operation.
7. Under normal operation, the tool is designed to produce vibration. The screws
can come loose easily, causing a breakdown or accident. Check tightness of
screws carefully before operation.
8. Always be sure to have a firm footing. Wear safety belt when using this tool in
high locations and ensue no one is below.
9. Keep hands away from the rotating parts.
10.Do not leave the tool running. Operate the tool only when hand-held.
11.Do not point the tool at any one in the area when operating. The bit could fly
out and injure someone seriously.
12.Do not touch the bit or parts close to the bit immediately after operation; they
may be extremely hot and could burn your skin
SAVE THESE INSTRUCTIONS.
WARNING! MISUSE or failure to follow the safety rules stated in this
instruction manual may cause serious personal injury.
INSTRUCTIONS FOR OPERATION
Setting Operating Mode
Caution:
Always be sure that the tool is switched OFF before changing the operating
mode, or the gears inside the tool maybe damaged.
If the drill bit gets stuck by the steel hidden in the wall during impact drilling, and
the tool rotates due to the kickback, hold the handle and auxiliary handle firmly
to avoid personal injuries.
The Operating mode can be changed by turning the
operating mode selector.
Drilling Operation
When impact drilling on the concrete or stone, turn the selector to the position as
shown in the figure.
When normally drilling on the wood, metal, ceramics or
plastic, turn the selector to the position as shown in the
figure.
Demolition Operation
When the position of chisel needs adjusting during
operation, turn the selector to the position as shown in the
figure to avoid gears from meshing and then adjust the
chisel.(Z1C-FF05-26/Z1C-FF05-26B)
After adjusting the chisel, turn the selector to the position
as shown in the figure to restart demolition operation.
Installing SDS-plus Hammer Drill Bit
SDS-plus hammer drill bit can be used
when drilling on the steel, wood or plastic.
Screw the drill chuck in the connecting rod
and tighten the lock screw. Then insert the
connecting rod into the collect in the same
way as installing SDS-plus hammer drill bit.
SDS-plus hammer drill bit and drill chuck
are optional accessories. (Fig. 1)
Installing /Removing Drill Bit
-5- -6-

CAUTION:
Always be sure that the tool is switched OFF and unplugged before installing or
removing the drill bit.
The SDS-plus drill bit will be
off-center when rotating with no-load,
but it will align with the center
automatically during operation and
its precision won’t be affected.
Clean the bit shank and smear it with
bit grease before installation.
To install the drill bit (SDS-plus shank),
fully pull back the slide grip and insert
the drill bit as far as it will go while
rotating. (Fig. 2)
By releasing the slide grip, the drill bit
will be secured automatically.
To remove the SDS-plus drill bit, fully
pull back and hold the slide grip and
the drill bit can be removed. (Fig. 3)
Auxiliary Handle
Always use the auxiliary handle
ensure operating safety. Loosen the
auxiliary handle by turning it
counterclockwise, swing it to the
desired position and then tighten it by
turning clockwise. (Fig. 4)
Switch Action
CAUTION:
Before plugging in the tool, always check to see that the trigger switch actuates
properly and returns to the “OFF”position when released.
To start the tool, simply pull the switch
trigger. Release the switch trigger to
stop.
For continuous operation, pull the switch
trigger and then push in the lock lever.
To stop the tool from the locked position,
pull the switch trigger fully, and then
release it. The rotating speed of the tool
becomes faster and faster until it
reaches the full speed during the
process of pressing the switch. (Fig. 5)
The switch of Z1C-FF05-26 is with
positive and negative going motion,
which can be used to change the tool’s
direction of rotation. You can only
change it when the tool completely stops
rotating, otherwise the tool will be
damaged. (Fig. 6)Set the direction of
rotation for hammer drilling, drilling and chiseling always to right rotation.
Depth Gauge
CAUTION:
The depth gauge cannot be used at the position where he depth gauge strikes
against the tool body.
-7- -8-

The depth gauge enables the drilling depth to be set for convenient drilling holes
of uniform depth.
Loosen the auxiliary handle, and insert
the linear part of the depth gauge into
the fitting hole of the clip board. (Fig. 7)
Move the depth gauge to the desired
depth and secure it by rotating the
auxiliary handle clockwise.
MAINTENANCE AND INSPECTION
CAUTION:
Always be sure that the tool is switched off and unplugged before attempting to
perform inspection or maintenance.
1. Inspecting Drill Bits
Blunt drill bit or chisel will decrease the work efficiency and causes the motor
be overloaded. Exchange or sharpen your drill bits when they become blunt.
2. Inspecting the Mounting Screws
Regularly inspect all mounting screws and ensure that they are properly
tightened.
Should any of the screws be loose, retighten them immediately. Failure to do
so could result in serious hazard.
3. Maintenance of the Motor
The motor unit winding is the very “heart”of the power tool. Exercise due care
to ensure the winding does not become damaged and /or wet with oil or water.
4. Inspecting and Replacing Carbon Brushes
Remove and check the carbon brushes regularly. Replace when they wear down
to the limit mark. Keep the carbon brushes clean and free to slip in the holders.
Both carbon brushes should be replaced at the same time. Use only identical
carbon brushes.
Use a screwdriver to remove the brush holder caps. Take out the worn carbon
brushes insert the new ones and secure the brush holder caps
5. Replacing Dust Cap
Replace the dust cap once it is damaged to avoid chippings from getting into the
collet. Clean the collet regularly.
.
※Damaged cord must be replaced by a special cord purchased from authorized
service center.
※To maintain product SAFETY and RELIABILITY, repairs, any other
maintenance or adjustment should be performed by authorized centers, always
using original replacement parts.
-9- -10-

Z1C-FF05-26
Z1C-FF05-26B
-11- -12-

Z1C-FF05-26C
EXPLANATION OF GENERAL VIEW
(Z1C-FF05-26)
1
Dust Cap
28
Clutch Spring
2
Roundwire Snap Ring for
Shaft
29
Roundwire Snap Ring for Shaft
3
Washer
30
Clutch Gear
4
Roundwire Snap Ring
31
Lock Pin
5
Locking Sleeve
32
Cylinder
6
Clamping Ring
33
Pin
7
Steel Ball
34
Clutch Plate
8
Clip Board
35
Retaining Ring for Hole
9
Compression Spring
36
Guide Sleeve
10
Retainer Sleeve
37
Damping Washer
11
O Ring
38
O Ring
12
Seal Ring
39
Adaptor Sleeve
13
Thrust Ring
40
Roundwire Snap Ring for Hole
14
Impact Bolt
41
Striker
15
Label
42
O Ring
16
Gear Housing
43
Piston
17
Seal Ring
44
Washer
18
Needle Bearing
45
Piston Pin
19
Needle Bearing Cover
46
Shaft Sleeve
20
Clamping Ring
47
Seal Ring
21
Operating Mode Selector
48
Metal Sheet for Support
22
O Ring
49
Gear Housing Cover
23
Selector Lever
50
O Ring
24
Spring
51
Needle Bearing
25
Slider
52
Metal Sheet for Fix
26
Pan Head Tapping Screw
53
Pan Head Tapping Screw
27
Washer
54
Gear Shaft
-13- -14-

EXPLANATION OF GENERAL VIEW
(Z1C-FF05-26)
55
Retainer
82
Pan Head Tapping Screw
56
Ball Bearing
83
Belleville Spring
57
Buckle
84
Handle Cover
58
Needle Bearing
85
Pan Head Tapping Screw
59
Pendulum Bearing
86
Trigger Switch
60
Needle Bearing
87
Cord Guard
61
Gear
88
Cord
62
Spring
89
Strain Relief
63
Pressing Block
90
Wire
64
Bush
91
Inductance
65
Rubber Pad
92
Depth Gauge
66
Deep Groove Ball Bearing
93
Steel Band
67
Bearing Retainer
94
Trapezoid Square-neck Bolt
68
Cross Recessed
Countersunk Head Screw
95
Lock Screw
69
Washer
96
Steel Band Base
70
Armature Assembly
97
Hex Nut
71
Insulation Washer
98
Clip Board
72
Ball Bearing
99
Auxiliary Handle
73
Rubber Sleeve
100
Nut
74
Baffle Plate
75
Pan Head Tapping Screw
76
Stator Assembly
77
Inductance
78
Nameplate
79
Motor Housing
80
Carbon Brush Holder
81
Carbon Brush
EXPLANATION OF GENERAL VIEW
(Z1C-FF05-26B)
1
Dust Cap
28
Clutch Spring
2
Roundwire Snap Ring for
Shaft
29
Roundwire Snap Ring for Shaft
3
Washer
30
Clutch Gear
4
Roundwire Snap Ring
31
Lock Pin
5
Locking Sleeve
32
Cylinder
6
Clamping Ring
33
Pin
7
Steel Ball
34
Clutch Plate
8
Clip Board
35
Retaining Ring for Hole
9
Compression Spring
36
Guide Sleeve
10
Retainer Sleeve
37
Damping Washer
11
O Ring
38
O Ring
12
Seal Ring
39
Adaptor Sleeve
13
Thrust Ring
40
Roundwire Snap Ring for Hole
14
Impact Bolt
41
Striker
15
Label
42
O Ring
16
Gear Housing
43
Piston
17
Seal Ring
44
Washer
18
Needle Bearing
45
Piston Pin
19
Needle Bearing Cover
46
Shaft Sleeve
20
Clamping Ring
47
Seal Ring
21
Operating Mode Selector
48
Metal Sheet for Support
22
O Ring
49
Gear Housing Cover
23
Selector Lever
50
O Ring
24
Spring
51
Needle Bearing
25
Slider
52
Metal Sheet for Fix
26
Pan Head Tapping Screw
53
Pan Head Tapping Screw
27
Washer
54
Gear Shaft
-15- -16-

EXPLANATION OF GENERAL VIEW
(Z1C-FF05-26B)
55
Retainer
82
Pan Head Tapping Screw
56
Ball Bearing
83
Belleville Spring
57
Buckle
84
Handle Cover
58
Needle Bearing
85
Pan Head Tapping Screw
59
Pendulum Bearing
86
Trigger Switch
60
Needle Bearing
87
Cord Guard
61
Gear
88
Cord
62
Spring
89
Strain Relief
63
Pressing Block
90
Wire
64
Bush
91
Wire
65
Rubber Pad
92
Wire
66
Deep Groove Ball Bearing
93
Depth Gauge
67
Bearing Retainer
94
Steel Band
68
Cross Recessed
Countersunk Head Screw
95
Trapezoid Square-neck Bolt
69
Washer
96
Lock Screw
70
Armature Assembly
97
Steel Band Base
71
Insulation Washer
98
Hex Nut
72
Ball Bearing
99
Clip Board
73
Rubber Sleeve
100
Auxiliary Handle
74
Baffle Plate
101
Nut
75
Pan Head Tapping Screw
76
Stator Assembly
77
Inductance
78
Nameplate
79
Motor Housing
80
Carbon Brush Holder
81
Carbon Brush
EXPLANATION OF GENERAL VIEW
(Z1C-FF05-26C)
1
Dust Cap
28
Clutch Spring
2
Roundwire Snap Ring for
Shaft
29
Roundwire Snap Ring for Shaft
3
Washer
30
Clutch Gear
4
Roundwire Snap Ring
31
Lock Pin
5
Locking Sleeve
32
Cylinder
6
Clamping Ring
33
Pin
7
Steel Ball
34
Clutch Plate
8
Clip Board
35
Retaining Ring for Hole
9
Compression Spring
36
Guide Sleeve
10
Retainer Sleeve
37
Damping Washer
11
O Ring
38
O Ring
12
Seal Ring
39
Adaptor Sleeve
13
Thrust Ring
40
Roundwire Snap Ring for Hole
14
Impact Bolt
41
Striker
15
Label
42
O Ring
16
Gear Housing
43
Piston
17
Seal Ring
44
Washer
18
Needle Bearing
45
Piston Pin
19
Needle Bearing Cover
46
Shaft Sleeve
20
Clamping Ring
47
Seal Ring
21
Operating Mode Selector
48
Metal Sheet for Support
22
O Ring
49
Gear Housing Cover
23
Selector Lever
50
O Ring
24
Spring
51
Needle Bearing
25
Slider
52
Gear Shaft
26
Pan Head Tapping Screw
53
Retainer
27
Washer
54
Ball Bearing
-17- -18-

EXPLANATION OF GENERAL VIEW
(Z1C-FF05-26C)
55
Buckle
82
Handle Cover
56
Needle Bearing
83
Pan Head Tapping Screw
57
Pendulum Bearing
84
Trigger Switch
58
Needle Bearing
85
Cord Guard
59
Gear
86
Cord
60
Spring
87
Strain Relief
61
Pressing Block
88
Wire
62
Bush
89
Inductance
63
Rubber Pad
90
Depth Gauge
64
Deep Groove Ball Bearing
91
Steel Band
65
Bearing Retainer
92
Trapezoid Square-neck Bolt
66
Cross Recessed
Countersunk Head Screw
93
Lock Screw
67
Washer
94
Steel Band Base
68
Armature Assembly
95
Hex Nut
69
Insulation Washer
96
Clip Board
70
Ball Bearing
97
Auxiliary Handle
71
Rubber Sleeve
98
Nut
72
Baffle Plate
73
Pan Head Tapping Screw
74
Stator Assembly
75
Inductance
76
Nameplate
77
Motor Housing
78
Carbon Brush Holder
79
Carbon Brush
80
Pan Head Tapping Screw
81
Belleville Spring
-19-
This manual suits for next models
5
Table of contents
Other Dongcheng Drill manuals
Popular Drill manuals by other brands
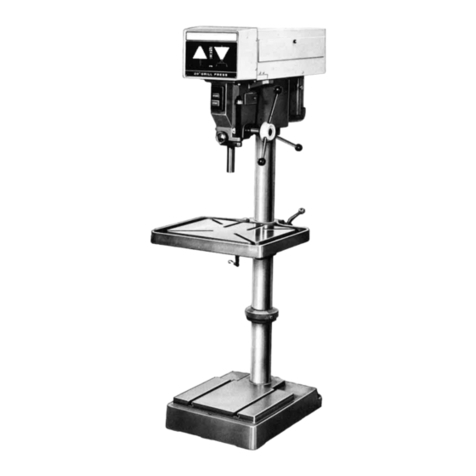
Delta
Delta 2000 instruction manual

BLACK DECKER
BLACK DECKER KR5010 Original instructions

MEISTER CRAFT
MEISTER CRAFT MSB 850 EB Operating instructions & safety hints

BLACK DECKER
BLACK DECKER ASD18 Original instructions

Bosch
Bosch GBH 2-23 REA Original instructions
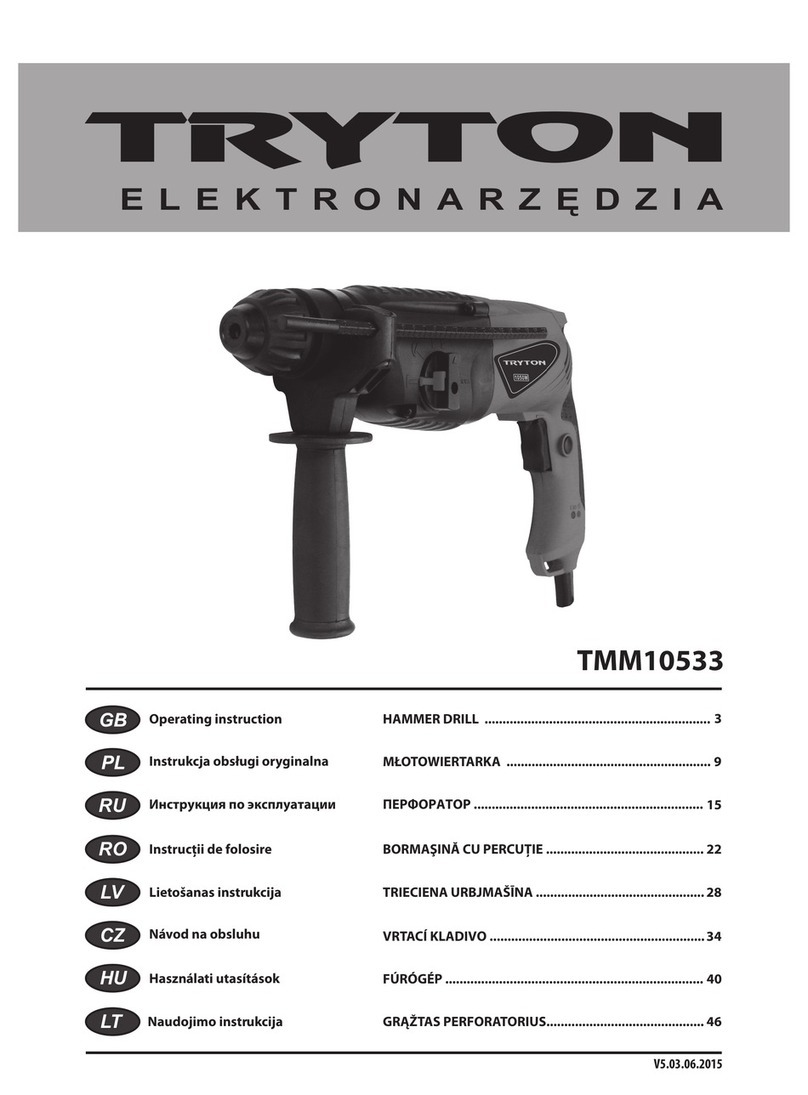
Tryton
Tryton TMM10533 Operating instruction