DSEGenset DSEP100 User manual

DSEP100 Operator Manual ISSUE 4
DEEP SEA ELECTRONICS PLC
DSEP100 Mains Decoupling Relay
Operator Manual
Document Number: 057-184
Author: Anthony Manton

DSEP100 Operator Manual
2
Deep Sea Electronics Plc
Highfield House
Hunmanby
North Yorkshire
YO14 0PH
ENGLAND
Sales Tel: +44 (0) 1723 890099
Sales Fax: +44 (0) 1723 893303
E-mail : sales@deepseaplc.com.
Website : www.deepseaplc.com
DSEP100 Operator Manual
© Deep Sea Electronics Plc
All rights reserved. No part of this publication may be reproduced in any material form (including
photocopying or storing in any medium by electronic means or other) without the written permission of
the copyright holder except in accordance with the provisions of the Copyright, Designs and Patents
Act 1988.
Applications for the copyright holder’s written permission to reproduce any part of this publication
should be addressed to Deep Sea Electronics Plc at the address above.
Any reference to trademarked product names used within this publication is owned by their respective
companies.
Deep Sea Electronics Plc reserves the right to change the contents of this document without prior
notice.
Amendments Since Last Publication
Amd. No.
Comments
1 First release
1.1 Added accuracy of phase measurement
2 Added updates to include changes for module version 1.5
3 Update Configuration Table (additional ROCOF alarms). Correction to relay output
designations (NO/NC).
4 Update wiring diagrams section and added UL information.
Typeface : The typeface used in this document is Arial. Care should be taken not to mistake the upper
case letter I with the numeral 1. The numeral 1 has a top serif to avoid this confusion.
Clarification of notation used within this publication.
NOTE:
Highlights an essential element of a procedure to ensure correctness.
CAUTION!
Indicates a procedure or practice, which, if not strictly observed, could result in
damage or destruction of equipment.
WARNING!
Indicates a procedure or practice, which could result in injury to personnel or loss
of life if not followed correctly.

DSEP100 Operator Manual
3
Table of Contents
1
INTRODUCTION..................................................................................................5
1.1
BIBLIOGRAPHY ......................................................................................................................5
2
SPECIFICATIONS...............................................................................................6
2.1
REQUIREMENTS FOR UL ......................................................................................................6
2.2
TERMINAL SPECIFICATION ..................................................................................................6
2.3
DC POWER SUPPLY...............................................................................................................6
2.4
AC POWER SUPPLY...............................................................................................................6
2.4.1
MODULE SUPPLY INSTRUMENTATION DISPLAY........................................................6
2.5
DIGITAL INPUTS.....................................................................................................................7
2.6
MAINS VOLTAGE / FREQUENCY SENSING.........................................................................7
2.7
RELAY OUTPUTS ...................................................................................................................7
2.8
USB CONNECTION.................................................................................................................8
2.9
DISPLAY ..................................................................................................................................9
2.10
DIMENSIONS .......................................................................................................................9
2.11
MAINS DECOUPLING STANDARDS..................................................................................9
2.12
OTHER APPLICABLE STANDARDS................................................................................10
3
INSTALLATION.................................................................................................11
3.1
USER CONNECTIONS..........................................................................................................11
3.1.1
CONNECTOR A – DC SUPPLY AND CONFIGURABLE INPUTS.................................11
3.1.2
CONNECTOR B – AC POWER SUPPLY.......................................................................11
3.1.3
CONNECTOR C – RELAY OUTPUT D ..........................................................................11
3.1.4
CONNECTOR D – RELAY OUTPUT E ..........................................................................12
3.1.5
CONNECTOR E – MAINS L1 MONITORING.................................................................12
3.1.6
CONNECTOR F – MAINS L2 MONITORING.................................................................12
3.1.7
CONNECTOR G – MAINS L3 MONITORING ................................................................12
3.1.8
CONNECTOR H – RELAY OUTPUT A ..........................................................................12
3.1.9
CONNECTOR I – RELAY OUTPUT B............................................................................12
3.1.10
CONNECTOR J – RELAY OUTPUT C...........................................................................12
3.2
TYPICAL WIRING DIAGRAM................................................................................................13
3.2.1
MAINS BREAKER...........................................................................................................13
3.2.2
MAINS BREAKER AND GENERATOR / COMMON BUS BREAKER............................14
3.2.3
ALTERNATE TOPOLOGY WIRING DIAGRAMS...........................................................15
3.3
INTERCONNECTION WITH THE GENERATOR CONTROLLER........................................16
3.3.1
OPEN THE MAINS BREAKER .......................................................................................16
3.3.2
OPEN THE GENERATOR OR COMMON BUS BREAKER...........................................16
3.3.3
OPEN BOTH BREAKERS...............................................................................................17
4
CONTROLS AND INDICATIONS......................................................................18
4.1
OPERATOR BUTTONS.........................................................................................................18
4.2
LED INDICATIONS................................................................................................................19
4.3
INSTRUMENTATION PAGES ...............................................................................................20
4.3.1
STATUS PAGE ...............................................................................................................20
4.3.2
MAINS PAGE..................................................................................................................21
4.3.3
ALARMS PAGE...............................................................................................................23
4.3.4
EVENT LOG PAGE.........................................................................................................23
4.3.5
ABOUT PAGE.................................................................................................................24
5
ALARMS............................................................................................................25
5.1
RESET....................................................................................................................................25
5.2
UNDER FREQUENCY / OVER FREQUENCY ......................................................................25
5.3
UNDER VOLTAGE / OVER VOLTAGE.................................................................................25
5.4
OVER AVERAGE VOLTAGE ................................................................................................26
5.5
LOSS OF MAINS (R.O.C.O.F. & VECTOR SHIFT)...............................................................26
5.5.1
WHAT IS LOSS OF MAINS DETECTION (LOM)?.........................................................26
5.5.2
WHY DO WE NEED LOSS OF MAINS DETECTION (LOM)? .......................................26
5.5.3
WHY DO G59 AND G83 REQUIRE LOM DETECTION?...............................................26
5.5.4
WHAT METHODS ARE USED FOR LOSS OF MAINS (LOM) DETECTION? ..............27

DSEP100 Operator Manual
4
5.5.5
WHY HAVE MUTLIPLE VOLTAGE AND FREQUENCY ALARM STAGES?.................27
5.5.6
RELATIVE MERITS OF R.O.C.O.F AND VECTOR SHIFT............................................27
5.5.6.1
R.O.C.O.F. SUMMARY............................................................................................27
5.5.6.2
VECTOR SHIFT SUMMARY ...................................................................................27
5.5.6.3
EXAMPLE OF POTENTIAL TO NOT DETECT A MAINS FAILURE.......................28
5.5.7
R.O.C.O.F........................................................................................................................29
5.5.7.1
EXAMPLE OF ROCOF (FREQUENCY DIP UPON MAINS FAILURE)...................29
5.5.7.2
EXAMPLE OF ROCOF (FREQUENCY RISE UPON A MAINS FAILURE).............30
5.5.8
VECTOR SHIFT..............................................................................................................31
5.5.9
EXAMPLE OF A VECTOR SHIFT (INCREASE IN LOAD UPON MAINS FAILURE).....31
5.5.10
EXAMPLE OF A VECTOR SHIFT (DECREASE IN LOAD UPON MAINS FAILURE) ...32
5.6
ZERO SEQUENCE VOLTAGE..............................................................................................33
5.7
POSITIVE SEQUENCE VOLTAGE .......................................................................................33
5.8
NEGATIVE SEQUENCE VOLTAGE......................................................................................33
5.9
ASYMMETRY.........................................................................................................................33
5.10
PHASE ROTATION............................................................................................................33
6
FRONT PANEL CONFIGURATION...................................................................34
6.1
DISPLAY EDITOR..................................................................................................................34
6.1.1
ACCESSING THE DISPLAY EDITOR............................................................................34
6.1.2
EDITING A PARAMETER...............................................................................................34
6.2
MAIN CONFIGURATION EDITOR ........................................................................................35
6.2.1
SETTING LOCK..............................................................................................................35
6.2.2
ACCESSING THE MAIN CONFIGURATION EDITOR...................................................35
6.2.3
EDITING A PARAMETER...............................................................................................36
6.2.4
DISPLAY EDITOR CONFIGURATION TABLES ............................................................36
6.2.5
MAIN EDITOR CONFIGURATION TABLES...................................................................37
7
FAULT DIAGNOSIS ..........................................................................................39
8
MAINTENANCE, SPARES, REPAIR AND SERVICING...................................40
8.1
WARRANTY...........................................................................................................................40
8.2
DISPOSAL .............................................................................................................................40

Introduction
5
1 INTRODUCTION
This document details the installation requirements of the DSEP100 Mains Decoupling Relay. The
manual forms part of the product and should be kept for the entire life of the product. If the product is
passed or supplied to another party, ensure that this document is passed to them for reference
purposes.
This is not a controlled document. You will not be automatically informed of updates. Any future
updates of this document will be included on the DSE website at www.deepseaplc.com
DSEP100 is used to detect mains failure when in parallel and disconnect the mains supply from the
local supply in line with common international requirements.
Typical applications able to benefit from DSEP100 are:
•Peak Lopping
•Fixed Export
•Short Term Operating Reserve (STOR)
•No Break, Seamless Or Closed Transition
•Commercial And Domestic Local Power Generation.
The powerful ARM microprocessor contained within the module allows for incorporation of a range of
complex features:
•Text Based LCD Display With Additional LED Indications
•True RMS Voltage.
•Instrumentation Of All Measured Parameters.
•Enables Applications To Meet The Standards Of Many European And Other Countries.
•ROCOF / Vector Shift Detection.
•Positive, Negative And Zero Sequence Detection.
•Under / Over Voltage Detection.
•Under / Over Frequency Detection.
•Manual And Auto Reset Functionality.
•USB Communications.
•Configuration Lock Facility To Prevent Parameter Changes Being Made.
For details on configuring the DSEP100 using a PC, you are referred to the relevant configuration
software manual.
1.1 BIBLIOGRAPHY
This document refers to and is referred to by the following DSE publications which can be obtained
from the DSE website www.deepseaplc.com
DSE
Part
Description
053-149 DSEP100 Installation Instructions
057-186 DSEP100 Configuration Suite PC Software Manual

Specifications
6
2 SPECIFICATIONS
2.1 REQUIREMENTS FOR UL
Surrounding Air Temperature -22 ºF to +122 ºF (-30 ºC to +50 ºC)
Operating Temperature -22 ºF to +122 ºF (-30 ºC to +50 ºC)
Storage Temperature -40 ºF to +176 ºF (-40 ºC to +80 ºC)
2.2 TERMINAL SPECIFICATION
NOTE: For purchasing additional connector plugs from DSE, please see the section
entitled Maintenance, Spares, Repair and Servicing elsewhere in this document.
Connection Type
Two part connector.
•Male part fitted to
module
•Female part supplied in
module packing case -
Screw terminal, rising
clamp, no internal
spring.
Example showing cable entry and screw
terminals of a 10 way connector
Minimum Cable Size 0.5 mm² (AWG 22)
Maximum Cable Size 2.5 mm² (AWG 14)
2.3 DC POWER SUPPLY
Minimum Supply Voltage 8 V continuous, 5 V for up to 1 minute.
Cranking Dropouts Able to survive 0 V for 50 mS providing the supply was at least 10 V
before the dropout and recovers to 5 V afterwards.
Maximum Supply Voltage 35 V continuous (transient protection to 60 V)
Maximum Operating Current 360 mA at 12 V DC, 170 mA at 24 V DC
2.4 AC POWER SUPPLY
Input Current at 85 V
rms
71 mA
rms
Input Current at 110 V
rms
58 mA
rms
Input Current at 230 V
rms
28 mA
rms
2.4.1 MODULE SUPPLY INSTRUMENTATION DISPLAY
Range 0 V-70 V DC (note Maximum continuous operating voltage of 35 V DC)
Resolution 0.1 V
Accuracy 1% full scale (±0.7 V)

Specifications
7
2.5 DIGITAL INPUTS
Number 5 inputs each with fixed function
Polarity Configurable
Arrangement Contact between terminal and battery negative
Low Level Threshold 2.1 V minimum
High Level Threshold 6.6 V minimum
Maximum Input Voltage +50 V DC with respect to battery negative
Minimum Input Voltage -24 V DC with respect to battery positive
Contact Wetting Current 7 mA
Open Circuit Voltage 12 V DC typical
2.6 MAINS VOLTAGE / FREQUENCY SENSING
Measurement Type True RMS conversion
Supported Topologies 2 phase 3 wire L1-L2.
2 phase, 3 wire L2-L3.
3 phase, 3 wire.
3 phase, 4 wire.
3 phase, 4 wire Delta.
Single phase, 2 wire.
3 phase, 3 wire NVD.
Sample Rate 5 kHz
Harmonics Up to 25th
Input Impedance 600 kΩbetween terminals.
Hardware Ranges 576 V ac / 288 V ac between terminals depending on range
selected.
Resolution 1V AC
Voltage Accuracy ±1% of full scale
Phase Measurement Accuracy ±0.5°
Minimum Frequency 3.5 Hz
Maximum Frequency 75.0 Hz
Frequency Resolution 0.01 Hz
Frequency Accuracy ±0.05 Hz
2.7 RELAY OUTPUTS
Number 5 configurable outputs
Polarity Configurable
Arrangement Volt-Free single pole changeover contacts
Rated Load 8 A at 250 VAC, 5 A at 30 VDC
Maximum Switching Voltage 250 VAC, 30 VDC
Maximum Switching Current 8 A

Specifications
8
2.8 USB CONNECTION
The USB port is provided to give a simple means of connection between a PC and the controller.
Using the DSE Configuration Suite Software, the operator is then able to monitor the device and
perform reset operations.
Additionally, the various operating parameters are available to be viewed or changed.
To connect a module to a PC by USB, the following items are required:
•DSEP100
•DSE Configuration Suite PC Software
(Supplied on configuration suite software CD or available from
www.deepseaplc.com).
•USB cable Type A to Type B.
(This is the same cable as often used between a PC and a USB
printer)
DSE can supply this cable if required :
PC Configuration interface lead (USB type A – type B) DSE Part
No 016-125
NOTE: The DC supply must be connected to the module for configuration by PC.
NOTE: For further details of module configuration, refer to DSE Publication: 057-186
DSEP100 Configuration Suite PC Software Manual.
NOTE: DSE stock a USB suitable cable for this purpose. Part number 016-125.

Specifications
9
2.9 DISPLAY
Type LCD graphics display.
Size 132 x 64 pixels.
Backlight LED
Contrast Control Software controlled.
Type Of Display Text
2.10 DIMENSIONS
Overall size 157 mm x 95 mm x 67 mm
(6.18” x 3.74” x 2.64”)
Weight 380 g
(13.4 oz.)
Mounting type DIN rail
DIN rail type EN 50022 35 mm type only
2.11 MAINS DECOUPLING STANDARDS
DSEP100 Mains Decoupling Relay has been designed to assist system designers to meet the
following standards. However as the DSEP100 is only one component in the complete system,
external circuits, must also be designed to meet the required standard.
Standard Name Notes
G59/2 and G59/3
(United Kingdom)
“Recommendation for the
connection of generation plant to
the distribution systems of licensed
distribution network operators”.
DTIS-250701-BDW
(Republic of Ireland)
“Conditions Governing Connection
to the Distribution System:
Connections at MV and 38 kV,
Embedded Generators at LV, MV
and
38 kV”
In some applications this standard
requires a directional over current
alarm (not included in the
DSEP100).
A relay from an external protection
device(s) can be fed into the ‘Aux
mains failure’ digital input to provide
this function.
DTIS-230206-BRL
(Republic of Ireland)
“Conditions Governing the
Connection and Operation of Micro-
generation”
C10/11
(Belgium)
“SPECIFICATION FOR MAINS
DECOUPLING RELAYS (according
to the document C10/11- version
06.2012)”
DIN V VDE V 0126-1-1
(Germany)
“Automatic disconnection device
between a generator and the public
low voltage Grid”
This requires a DC current injection
alarm and residual current alarm
(not included in the DSEP100).
A relay from an external protection
device(s) can be fed into the ‘Aux
mains failure’ digital input to provide
these functions.
CEI 0-21
(Italy)
“Reference technical rules for the
connection of active and passive
users to
the LV electrical Utilities”

Specifications
10
2.12 OTHER APPLICABLE STANDARDS
BS EN 60068-2-1
(Minimum temperature) -30 °C (-22 °F)
BS EN 60068-2-2
(Maximum temperature)
+70 °C (158 °F)
Degrees of protection
provided by enclosures IP31
UL508
NEMA rating Enclosure type 1 (indoor use only)
Operating Temperature -30 ºC to +70 ºC
(-22 ºF to +158 ºF)
Storage Temperature -40 ºC to +80 ºC
(-40 ºF to + 176 ºF)
IEEE C37.2
ANSI Device Numbers Under the scope of IEEE 37.2, function numbers can also be used to
represent functions in microprocessor devices and software programs.
As the module is configurable by the generator OEM, the functions
covered by the module will vary. However the device includes the
following configurable protections :
•27 Under Voltage
•59 Over Voltage, Above Average Voltage, Voltage Symmetry
•81H Over Frequency
•81L Under Frequency
•81R R.O.C.O.F.
•78 Vector Shift
•47H Negative Sequence Voltage, Zero Sequence Voltage
•
47L Positive Sequence Voltage
•
Phase rotation
In line with our policy of continual development, Deep Sea Electronics Plc, reserve the right to change
specification without notice.

Installation
11
3 INSTALLATION
The DSEP100 is designed to be mounted within a control panel, either on the panel DIN rail utilising
the integral mounts, or chassis mounted, utilising the mounting holes. For dimension and mounting
details, see the section entitled Specifications, Dimensions elsewhere in this document.
3.1 USER CONNECTIONS
3.1.1 CONNECTOR A – DC SUPPLY AND CONFIGURABLE INPUTS
The DC Supply on terminals 1 & 2 is optional if an AC Supply is connected to terminals 8 and 9.
Connecting a DC supply to terminals 1 & 2 at the same time as connecting an AC supply to terminals
8 & 9 is perfectly acceptable and has no detrimental affect on the operation of the device.
Terminal
Function
Recommended
Size
1 Plant –ve 1.0mm² (AWG18)
2 Plant +ve 1.0mm² (AWG18)
3 Digital Input A (Generator Closed Auxiliary) 0.5mm² (AWG20)
4 Digital Input B (Mains Closed Auxiliary) 0.5mm² (AWG20)
5 Digital Input C (Alarm Reset) 0.5mm² (AWG20)
6 Digital Input D (Alternative Config’ Select) 0.5mm² (AWG20)
7 Digital Input E (Auxiliary Mains Failure) 0.5mm² (AWG20)
3.1.2 CONNECTOR B – AC POWER SUPPLY
Used to power the DSEP100. This is optional if connected to a DC Supply on terminals 1 and 2.
Connecting a DC supply to terminals 1 & 2 at the same time as connecting an AC supply to terminals
8 & 9 is perfectly acceptable and has no detrimental affect on the operation of the device.
Terminal
Function
Recommended
Size
8 AC PSU Neutral 1.0mm² (AWG18)
9 AC PSU Live 1.0mm² (AWG18)
3.1.3 CONNECTOR C – RELAY OUTPUT D
Terminal
Function
Recommended
Size
D
10 Relay Output D (NO) 1.0mm² (AWG18)
11 Relay Output D (C) 1.0mm² (AWG18)
12 Relay Output D (NC) 1.0mm² (AWG18)

Installation
12
3.1.4 CONNECTOR D – RELAY OUTPUT E
Terminal
Function
Recommended
Size
E
13 Relay Output E (NO) 1.0mm² (AWG18)
14 Relay Output E (C) 1.0mm² (AWG18)
15 Relay Output E (NC) 1.0mm² (AWG18)
3.1.5 CONNECTOR E – MAINS L1 MONITORING
Terminal
Function
Recommended
Size
Ua3 Ua2 Ua1
16 Ua1 (Mains L1) 1.0mm² (AWG18)
17 Ua2 (Mains N, internally connected to Ua3) 1.0mm² (AWG18)
18 Ua3 (Mains N, internally connected to Ua2) 1.0mm² (AWG18)
3.1.6 CONNECTOR F – MAINS L2 MONITORING
Terminal
Function
Recommended
Size
Ub3 Ub2 Ub1
19 Ub1 (Mains L2) 1.0mm² (AWG18)
20 Ub2 (Mains N, internally connected to Ub3) 1.0mm² (AWG18)
21 Ub3 (Mains N, internally connected to Ub2) 1.0mm² (AWG18)
3.1.7 CONNECTOR G – MAINS L3 MONITORING
Terminal
Function
Recommended
Size
Uc3 Uc2 Uc1
22 Uc1 (Mains L3) 1.0mm² (AWG18)
23 Uc2 (Mains N, internally connected to Uc3) 1.0mm² (AWG18)
24 Uc3 (Mains N, internally connected to Uc2) 1.0mm² (AWG18)
3.1.8 CONNECTOR H – RELAY OUTPUT A
Terminal
Function
Recommended
Size
A
25 Relay Output E (NC) 1.0mm² (AWG18)
26 Relay Output E (C) 1.0mm² (AWG18)
27 Relay Output E (NO) 1.0mm² (AWG18)
3.1.9 CONNECTOR I – RELAY OUTPUT B
Terminal
Function
Recommended
Size
B
28 Relay Output E (NC) 1.0mm² (AWG18)
29 Relay Output E (C) 1.0mm² (AWG18)
30 Relay Output E (NO) 1.0mm² (AWG18)
3.1.10 CONNECTOR J – RELAY OUTPUT C
Terminal
Function
Recommended
Size
C
31 Relay Output E (NC) 1.0mm² (AWG18)
32 Relay Output E (C) 1.0mm² (AWG18)
33 Relay Output E (NO) 1.0mm² (AWG18)

Installation
13
3.2 TYPICAL WIRING DIAGRAM
NOTE: The DSEP100 may be powered using AC and DC at the same time. When powering
the DSEP100 from AC only, terminal 1 must be grounded to enable the digital input functions.
3.2.1 MAINS BREAKER

Installation
14
3.2.2 MAINS BREAKER AND GENERATOR / COMMON BUS BREAKER

Installation
15
3.2.3 ALTERNATE TOPOLOGY WIRING DIAGRAMS

Installation
16
3.3 INTERCONNECTION WITH THE GENERATOR CONTROLLER
The DSEP100 is intended to be placed into the application wiring in such a way as to decouple the
mains and generator supplies in case of a mains failure when in parallel.
Depending upon the requirements of the system, the relay is used to open the mains breaker,
generator breaker or both as described below.
Additionally, any other control logic placed between the DSEP100 and the breakers being controlled
must also be designed with fast operation in mind. The combined time between the DSEP100
detecting the fault, and the time of the breaker opening must be within the specification of the
legislation in place at the site. This legislation differs between countries.
3.3.1 OPEN THE MAINS BREAKER
NOTE: You must ensure that the generator(s) are capable of supplying the remaining load
after the mains breaker has been opened.
It is recommended that the DSEP100 is used to open the mains breaker directly, giving signal to the
opening or tripping coil. This ensures that the decoupling operation occurs as quickly as possible after
the signal to open is given by the DSEP100.
In addition to this, it is recommended that the DSEP100 signal is also given to any other device that
has control over the mains breaker. For example this could be a DSE8620 type controller.
Where connected to a DSE module with control over the mains breaker, this signal is fed into a digital
input configured to “Auxiliary Mains Failure”. This ensures that this controller is informed about the
mains decoupling operation and can take action itself to open the mains breaker.
Additionally, the DSE module must have “Immediate Mains Dropout” enabled. This configures the
controller to open the mains breaker as soon as the input is received from the DSEP100 device.
Failure to do this may result in “Fail To Close” alarms caused by the mains breaker opening under
control of a device other than the DSEP100.
3.3.2 OPEN THE GENERATOR OR COMMON BUS BREAKER
NOTE: You must ensure that the mains supply is capable of supplying the remaining load
after the generator or common bus breaker has been opened.
It is recommended that the DSEP100 is used to open the generator or common bus breaker directly,
giving signal to the opening or tripping coil. This ensures that the decoupling operation occurs as
quickly as possible after the signal to open is given by the DSEP100.
In addition to this, it is recommended that the DSEP100 signal is also given to any other device that
has control over the generator or common bus breaker. For example this could be a DSE8660 type
controller.
Where connected to a DSE module with control over the generator or common bus breaker, this
signal is fed into a digital input configured to “Electrical Trip”. This ensures that this controller is
informed about the mains decoupling operation and can take action itself to open the generator or
common bus breaker.
Failure to do this may result in “Fail To Close” alarms caused by the mains breaker opening under
control of a device other than the DSEP100.

Installation
17
3.3.3 OPEN BOTH BREAKERS
This application may be required if the size of the load requires both the generator and mains supplies
to be in parallel.
In this application, if the mains supply fails, the generator supply is incapable of supplying the load so
both breakers must be opened.
It is recommended that the DSEP100 is used to open the mains breaker AND generator or common
bus breaker directly, giving signal to the opening or tripping coil. This ensures that the decoupling
operation occurs as quickly as possible after the signal to open is given by the DSEP100.
In addition to this, it is recommended that the DSEP100 signal is also given to any other device that
has control over the generator or common bus breaker. For example this could be a DSE8660 type
controller.
Where connected to a DSE module with control over the generator or common bus breaker, this
signal is fed into a digital input configured to “Electrical Trip” and to another digital input configured to
“Auxiliary Mains Failure”. This ensures that this controller is informed about the mains decoupling
operation and can take action itself to open the mains breaker AND generator or common bus
breaker.
Additionally, the DSE module must have “Immediate Mains Dropout” enabled. This configures the
controller to open the mains breaker as soon as the input is received from the DSEP100 device.
Failure to do this may result in “Fail To Close” alarms caused by the breakers opening not under
control of the DSEP100.

Controls and Indications
18
4 CONTROLS AND INDICATIONS
4.1 OPERATOR BUTTONS
Button Function Description
Up Cycle round the instruments in the current page / adjust parameter when in
configuration mode.
Down Cycle round the instruments in the current page / adjust parameter when in
configuration mode.
Left Move between the different instrumentation / configuration pages.
Right Move between the different instrumentation / configuration pages.
Tick Used in conjunction with the Front Panel Editor (FPE)
Reset Reset alarms (when present) if the cause of the alarm is no longer present.
Lamp
Test Press and hold the Reset button for five seconds to perform a Lamp Test of all
LEDs.
During Lamp Test, the following LED colours show normal operation :
Trip
:
Red
U
:
Amber
F
:
Amber
df/dt
:
Red
Vec
:
Red
Alt
:
Amber
Sup
:
Green

Controls and Indications
19
4.2 LED INDICATIONS
LED
Colour Function
Trip Red Common Alarm LED to show Trip status.
Flashing: Indicates that a mains decoupling event has been detected. Further
LED indication shows the type of trip.
Unlit : No alarms active.
U Mutlicolour
(see below) Indicates activation of one or more of the following Voltage Alarm conditions.
•Under Voltage Stage 1
•Under Voltage Stage 2
•Under Voltage Stage 3
•Under Voltage Stage 4
•Under Voltage Stage 5
•Over Voltage Stage 1
•Over Voltage Stage 2
•Over Voltage Stage 3
•Over Voltage Stage 4
•Over Voltage Stage 5
•Over Average Voltage
•Zero Sequence Voltage
•Negative Sequence Voltage
•Positive Sequence Voltage
•Asymmetry
•Phase Rotation Alarm
f Mutlicolour
(see below) Indicates activation of one or more of the following Frequency Alarm conditions.
•Low Frequency Stage 1
•Low Frequency Stage 2
•High Frequency Stage 1
•High Frequency Stage 2
df/dt
Red
Lit :
Indicates activation of one or more of the following R.O.C.O.F. Alarm
conditions
•R.O.C.O.F Stage 1
•R.O.C.O.F Stage 2
•R.O.C.O.F Stage 3
Unlit : R.O.C.O.F. has not been activated.
Vec Red
Lit :
Indicates that the Vector Shift trip has been activated.
Unlit : Vector Shift has not been activated.
Alt Amber
Lit :
The device’s ‘alternative configuration is active.
Unlit : The device’s ‘main configuration’.
Sup Green Shows the operating state of the device.
Flashing : The Supervision Timer is in progress, after which the device
supervision becomes active.
Lit Steady : The DSEP100 is active, checking for a mains decoupling event.
Unlit : The device is disabled.
U and f LEDs are multicolour LEDs. The colour of the LED indicates the exact status of the LED as
below:
Colour Function
Unlit Alarm disabled.
Green Alarm active and measured values are within configured normal operating parameters.
Amber Alarm active and measured values are outside configured normal operating parameters
during the trip delay timer.
Red Alarm tripped.

Controls and Indications
20
4.3 INSTRUMENTATION PAGES
Press and to move between the available instrumentation pages.
When viewing an instrumentation page, press and to cycle between the instruments in each
page.
While viewing the ROCOF/Vector Shift instruments in the Mains page, Press and hold for 5
seconds to reset their ‘peak hold’ values.
4.3.1 STATUS PAGE
Contains a status summary of the operation of the DSEP100.
Press down
to cycle through the available instruments.
•Clock.
•Supervision Disabled / Enabled.
•Rate of Change of Frequency (ROCOF), actual and ‘peak hold’. The peak hold value is reset
on the Mains page.
•Vector Shift, actual and ‘peak hold’. The peak hold value is reset on the Mains page.
•Average L-N Voltage.
•Average L-L Voltage.
•Frequency
•Negative Sequence Voltage.
•User selectable items using DSE Configuration Suite PC Software.
Example showing the Status pages.
Status
9:22
Electrical Trip
ROCOF
0.4Hz
0.6Hz
Vector
0.2º
3.2º
Status
L
-
N
230V
50.0Hz
L
-
L
400V
ROCOF
0.6Hz
Neg
0.
7V
3.2º
Current ROCOF and Vector Shift values.
Peak Hold ROCOF and Vector Shift values.
These are reset on the Mains page for ROCOF
Current time.
Operating Status or Common Alarm indication
L-N Average Voltage
L-L Average Voltage
Negative Sequence Voltage
Supply Frequency
Current ROCOF value
Current Vector Shift value
Table of contents
Other DSEGenset Remote Control manuals
Popular Remote Control manuals by other brands
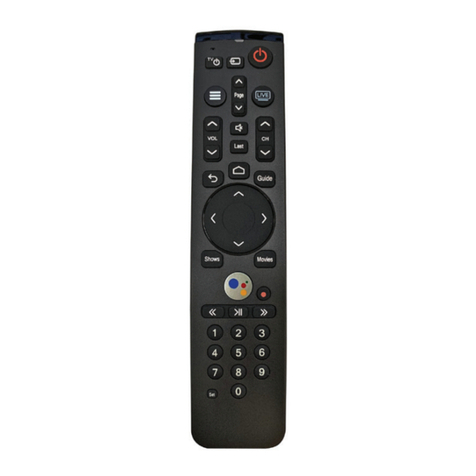
Quadro
Quadro Q tv Remote KURV 2.0 Voice Remote Control Quick reference guide

Mitsubishi Electric
Mitsubishi Electric PAR-32MAA installation manual
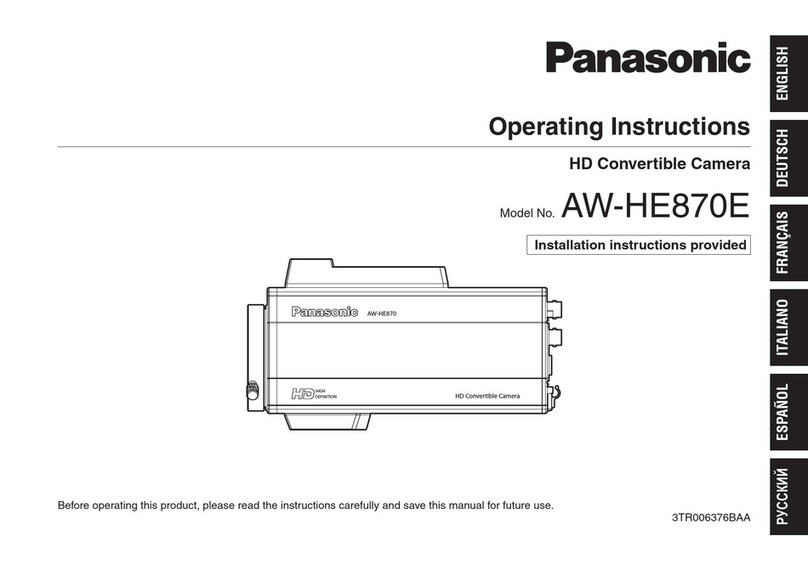
Panasonic
Panasonic AW-HE870E Operation instructions
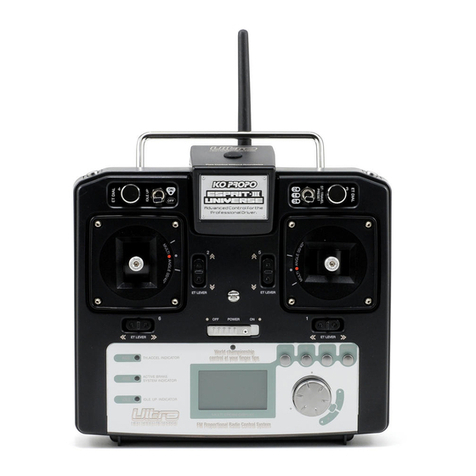
Ko Propo
Ko Propo Esprit-3 Universe instruction manual
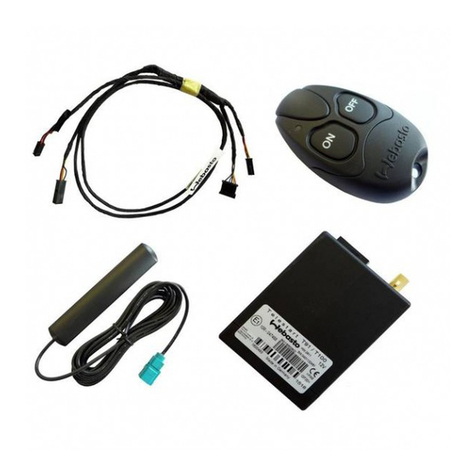
Webasto
Webasto Telestart T91 operating instructions
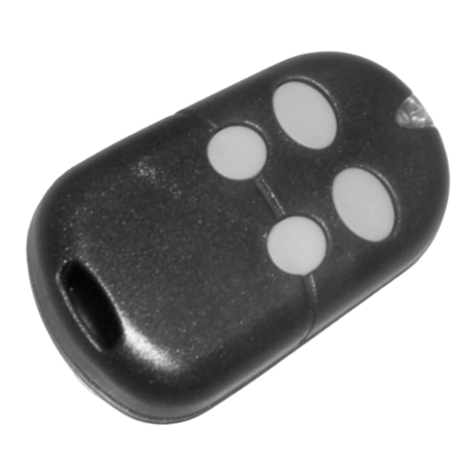
Leb Electronics
Leb Electronics TSAW4 instructions