EASTMAN PACEMAKER Setup guide

EASTMAN
®
THE EASTMAN
779 Washington St., Buffalo, N.Y. 14203-1396 U.S.A. • (716)856-2200 • Fax (716)856-1140 or (716)856-2068
Manufacturers of Eastman Cloth Cutting and Cloth Spreading Machines
Instruction Manual &
Illustrated Parts List
Please read completely before attempting
to operate your new Eastman Pacemaker.
PACEMAKER
From the library of: Diamond Needle Corp

2
EASTMAN
TABLE OF CONTENTS
Pictorial Index ..................................................... 9
Front Frame Assembly ......................................... 10-13
Back Frame Assembly .......................................... 14-15
Cross Member & Component Kit .......................... 15-16
Front Upright Assembly ........................................ 18-19
Rear Upright Assembly ......................................... 20
Edge Control Box .................................................. 21
Auto Edge Control Assembly ................................ 22-23
Edge Control Probe .............................................. 24
Mast Assembly ...................................................... 25
Roll Aid Device ..................................................... 26
Flat Fold Platform ................................................. 27
Tricot Uprights ....................................................... 28-29
Rayon Bar ............................................................. 30
Expandabar ........................................................... 31
H/D Expandabar .................................................... 32-33
Movable Catcher ................................................... 34-36
Stationary Catcher ................................................ 37-39
Extension Plates ................................................... 40
Triangle Attachments ............................................ 41
T-Track .................................................................. 42
Service Record ..................................................... 43
Technical
Electrical Diagram #11-3306 ................................ 8
Service Records.................................................... 43
INSTALLATION
Table Preparation ................................................. 3
To Level Table ..................................................... 3
Track Installation................................................... 3
Premium Track Chairs .......................................... 3
Plastic Track Chairs .............................................. 3
Mounting Track ..................................................... 3
Machine Setup
Placement of Pacemaker ..................................... 4
Mounting Pickup Fingers ...................................... 4
Squaring Machine to Table ................................... 4
Safety Bracket ...................................................... 4
Mast Power Connection ........................................ 4
Setup for Spreading
Stationary Catcher ................................................ 4
Movable Catcher ................................................... 4
Setting Stops and Elevator ................................... 4
Loading and Threading ......................................... 5
Edge Control
MANUAL ............................................................... 5
Automatic Edge Control ........................................ 5
Edge Control Sensitivity Adjustment .................... 5
Setting Marker and Spreading .............................. 6
Drop Sizes............................................................. 6
Familiarization
Control Box and Machine ..................................... 6-7
IMPORTANT
The purchaser must instruct all operators on the proper use of this equipment. All standard industrial
safety measures and equipment should be provided to protect the operator. Operators must be
cautioned that improper or careless use of this equipment may cause personal injury. If you do not
have qualified operators to instruct new persons, contact your EASTMAN sales representative or
EASTMAN factory direct.
Electrical connections and servicing to this equipment should be made by a qualified electrician who
is familiar with applicable codes and regulations. Disconnect this equipment from electrical power
source before proceeding with any disassembly for adjustment or repair.
From the library of: Diamond Needle Corp

3
The Eastman PACEMAKER is shipped with all the neces-
sary parts for proper setup and operation. To get the best
performance, familiarize yourself with all functions and
adjustments of this equipment. Before any operation can
take place, it is important that you carefully read and follow
the instructions in this manual in the same sequence in
which they are presented.
The following items listed below may be included with your
installation kit or purchased at a later date:
MS- Machine size in Inches.
*: Optional Equipment.
F-218 C-Clamps (2)
F-261-T T-Track (50'-0")
PM-0213-MS *Flat Fold Platform
PM-0216 *Triangle Attach., Stationary
PM-0217 *Triangle Attach., Movable
PM-02238-MS *Frozen Bar
PM-02243-MS *Mast
PM-03078 *Roll Aid
PM-0401 *Tricot Uprights
PM-0404-MS Movable Catcher
PM-0405-MS Stationary Catcher
PM-04132-MS *Heavy Duty Expandabar
PM-158 *Stationary Catcher Extension
PM-159 *Movable Catcher Extension
PM-1004-MS Expandabar with Shifter
TA-3002, TA-3003 *Premium Track Chairs
TC-1, TC-2 *Plastic Track Chairs
11-2000-voltage *Trolley
205-34 Hex Nut (4)
301-14-20 Wood Screw (4)
331-34-32 Hex Bolt (4)
402-34 Lock Washer (4)
410-34 Flat Washer (4)
9136-001 Allen Wrench Set
INSTALLATION
Table Preparation
Spreading table must be at least six inches wider than
machine size.
The spreading table must be smooth and level, along its
entire length, for proper operation of your Pacemaker. A
level table with properly attached tracking is the single
most important factor affecting the performance of your
spreader.
To Level Table
Use a carpenter's level to check spreading table. Be
especially careful to make sure table joints mate closely.
Adjust levelling feet, on table legs, as necessary.
Track Installation
Note: The methods for mounting "T" track and gear track
are identical as follows:
Lay track sections along table top, end to end, in the
locations they will be mounted. Make sure that joints in
track DO NOT align with seams in table.
Note: If roll weight will exceed 200 lbs. (91kg), premium
track chairs should be used (TA-3002, TA-3003).
Premium Track Chairs
Starting at center section of tracking, drill 1/4" dia. holes
into skirt of table, 3/4" down from top surface of table. Use
included hardware to mount double track chairs (TA-3003)
at track joints and single track chairs (TA-3002) at interme-
diate mounting holes.
Plastic Track Chairs
Starting at center section of tracking, drill 1/4" dia. holes
into edge of table top. Use included hardware to mount
double chairs (TC-2) at track joints and single track chairs
(TC-3) at intermediate mounting holes.
Mounting Track
Loosely screw tracking onto track chairs. Align track edge
slightly below top surface of table, to avoid interference
with cutting machine base plate. Tighten track, making
sure all joints mate closely and tracking is level.
From the library of: Diamond Needle Corp

4
EASTMAN
MACHINE SETUP
Placement of Pacemaker
Lift the Pacemaker onto the spreading table so that
grooved wheels, on the front frame of the machine, fit over
the lip in the track.
Mounting Pickup Fingers
The tuck blade's pickup fingers are packed in the parts
carton with your spreader. Referring to the front and rear
frame exploded assemblies, fasten the four pickup finger
to the lifting blocks on the front and rear frames.
Note: All set up adjustments are preset at the factory.
However, if adjustment is necessary, follow proce-
dures below.
Squaring Machine to Table
Align tuck blades of the machine with a seam in spreading
table. If tuck blades do not match seam, along their entire
length, adjust turnbuckles on tie rods until tuck blades are
parallel to seam. Secure adjustment with locknuts on tie
rod.
To square Heavy Duty Pacemaker, shims must be added
between one track wheel and front frame. Add shims in
.010 increments until machine is square to table.
Safety Bracket
Refer to front frame exploded assembly for proper orien-
tation and mounting of safety bracket. Be sure that roller
bearing rides fully on bottom side of tracking.
Mast Power Connection
For machines with optional edge control or quick-cut only.
Mount the mast as shown in the mast exploded view.
Check voltage rating of power cord with electrical rating
stamped on the serial number plate. If compatible, con-
nect cord to mating connector on the mast.
Note: Voltage varying more than 10% (11v for 110 volt
machine, 22v for 220 volt machine) may damage
your system's electronics.
SET UP FOR SPREADING
Stationary Catcher
Place stationary catcher onto table, to left of the spreader,
and insert the catcher bearing studs (located at ends of
pinbar) into the slots on lifting blocks. Center the studs in
these slots and push the Pacemaker and catcher to the
proper location on your table. Mark the table around the
catcher frames, and drill holes needed to fasten stationary
catcher to table with hardware provided. Remove bearing
studs from lifting blocks and push the machine away from
the catcher.
Movable Catcher
Place movable catcher onto spreading table to the right of
Pacemaker and insert bearing studs into lifting blocks, in
the same manner as done for stationary catcher. Push the
machine to the desired location and mark location of
catcher frames. Clamp the movable catcher to spreading
table, at BOTH front and rear of catcher.
Note: All set up adjustments are preset at factory. How-
ever, if adjustments are necessary, follow proce-
dures below.
Setting Stops and Elevator
Carefully push your Pacemaker into the stationary catcher
until the catcher pinbar drops over the left hand tuck blade.
Check to be sure pinbar lies evenly across entire length of
tuck blade. Adjust the bumper/stops in front and rear
catcher frames to touch Pacemaker side frames. Secure
the bumpers with locknuts.
Test operation of catcher and placement of stops to
ensure full actuation of the stationary catcher. If pinbar
does not drop completely over teardrop blade, shorten the
adjustment of bumper/stops until operation is satisfactory.
Push the spreader to opposite end of spread and make
similar adjustments to the movable catcher. The elevator
can be adjusted so the tuck blades clear each new ply of
cloth being spread. Turn the elevator adjusting screw
(located on right end of elevator mechanism):
Clockwise to Reduce elevator step
Counterclockwise to Increase elevator step.
From the library of: Diamond Needle Corp

5
If elevator fails to engage fully, the elevator bumper
(located on front frame of movable catcher) may not be
fully actuating the elevator mechanism. Adjustment is
similar to setting the catcher bumpers.
LOADING AND THREADING
Place the piece goods bar through the roll core and secure
the bar to the roll.
For machines equipped with optional roll-aid device; raise
roll onto roll-aid and insert rear end of bar into rear upright,
then front of bar into R.B.A. (front upright). The shifter
groove on the bar must rest on the upright bearings for
proper operation.
Adjust thumbscrew on roll brake until tension on bar
prevents free spinning of piece goods roll. Secure the
tension setting locknut.
Follow threading diagram to thread fabric through Pace-
maker. If equipped with automatic edge control, make
certain cloth is properly fed through edge control eyes.
Turn edge control box power ON. Press the AUTO switch
on to center fabric. The Pacemaker is ready for operation.
Edge Control
MANUAL
Manual edge control is maintained by turning the hand
wheels at either side of the front frame, while machine is
in motion. Slide nylon collar to approx. 2 inches from
frame, and use it as a guide for edge control.
Automatic Edge Control
Before threading fabric, the edge control switch should be
in MANUAL mode. This allows the operator load material
without movement of the edge control unit. After roll is
loaded and the roll brake is set, turn the automatic edge
control to AUTO.
Edge Control Sensitivity Adjustment
Factory set to be suitable for most fabrics. NOT affected
by cutting room lighting. If adjustment is required the
sensor must be removed for sensitivity adjustment. Each
sensor has a countersunk adjusting screw on the bottom
surface. Turn screw CLOCKWISE to INCREASE sensitiv-
ity, COUNTERCLOCKWISE to DECREASE sensitivity.
Use care not to damage lens of scanner. When relocating
sensor on support, scanner lenses must be aimed perpen-
dicular to reflector for edge control to operate properly.
Switch edge control to automatic and test for proper
functioning.
Threading Diagram
From the library of: Diamond Needle Corp

6
EASTMAN
EDGECONTROL
POWER
ON
OFF
AUTO
MANUAL
OUT
IN
1
43
5
6
2
Setting Marker and Spreading
Place marker onto table, starting 1/2 inch from left edge of
blade on stationary catcher. This will allow 1/2 inch for
trimming of folds. Be sure marker lies straight and parallel
to edge of spreading table.
From right end of marker, measure to right 19 1/2 inches
and mark table. Place movable catcher into Pacemaker,
as explained in "Setup For Spreading". Move Catcher to
the right until right end of catcher base plate matches the
19 1/2 inch mark. This allow 1/2 inch for trimming of folds.
Clamp movable catcher in this position with C- clamps
provided. Disengage catcher from machine, mark section
in marker and remove marker from table.
Load and thread Pacemaker with piece goods as ex-
plained in "Setup For Spreading". Reset counter to zero.
Place end of piece goods under movable catcher pinbar.
Spread cloth by pushing machine down table while main-
taining edge control with hand wheels on front frame.
Drop Sizes
When spreading drop sizes, keep highest lay of goods at
stationary catcher end of marker and lowest lay of goods
at movable catcher end of marker.
If dropping sizes without using movable catcher; pass the
drop edge" by approx. one foot. Tip tuck blade up and
catch the slack cloth. Begin moving spreading back to-
ward stationary catcher allowing slack cloth to roll back
until it aligns with "drop edge". Hold or weight the fold of
cloth and continue spreading back to stationary catcher.
FAMILIARIZATION
Control Box
1. Power Light: Activates when Main Power (4) is on.
2. In/Out: Press to move Edge Control Platform in or out.
3. Auto/Manual: Sets Auto/Manual Edge Control Mode.
4. Main Power: Activates Power to all Circuits.
5. Circuit Breaker: (2 Amp): Edge Control Platform.
6. Circuit Breaker: (2 Amp): Edge Control Platform.
Machine
7. Transformer: For 220 volt Automatic Edge Control or
Quick-Cut only.
8. Edge Control Motor: Automatic Edge Control only.
9. Edge Control Roller Bearings: Shifter Groove in
Roll Bar fits over bearings for edge control.
10. Roll Brake: Adjust Knob for proper fabric tension.
11. Hand wheel
12. Edge Control Reflector and Sensor: Move Sensor
and Reflector to adjust edge of fabric lay. The
reflector must be square to sensing eyes for
proper operation.
13. Rear Upright: Roll bar rests in nylon roller.
14. Lifting Blocks: Lifts pinbar when in catcher.
15. Tuck Blades: Folds fabric at each end of spread.
16. Elevator Actuating Link: Lifts Tuck Blades when
actuated by catcher.
17. Safety Bracket: Rides under table edge.
18. Elevator Step Adjuster: Adjust in or out for elevator
step adjustment.
19. Elevator Release: Press to lower Elevator/Tuck
Blades.
20 Ply Counter: Counts number of plies spread.
21. Push Handle: Auto Edge Control only.
22. Control Box: Auto Edge Control only.
From the library of: Diamond Needle Corp

7
8
7
22 21 20
18 17 16
15
14
12
19
11
9
10
13
From the library of: Diamond Needle Corp

8
EASTMAN
Pacemaker Electrical Diagram
Blue Print No. (11-3306)
From the library of: Diamond Needle Corp

9
Pictorial Index
Item numbers are for reference only. Please
Specify PART NUMBER when ordering replace-
ment parts.
Please Specify machine voltage and
complete serial number when ordering
replacement parts.
Edge Control Box
Assembly
Page 21
Back Frame Assembly
Pages 14-15
Rear Upright Assembly
Page 20
Cross Member &
Component Kit
Pages 16-17
Front Upright Assembly,
Manual Edge Control
Pages 18-19
Automatic
Edge Control
Assembly
Pages 22-24
Front Frame &
Elevator Mechanism
Pages 10-13
ASSEMBLY PAGE
Mast Assembly 25
Roll Aid Device 26
Flat Fold Platform 27
Tricot Uprights 28-29
Rayon Bar 30
Expandabar 31
H/D Expandabar 32-33
Movable Catcher 34-36
Stationary Catcher 37-39
Extension Plates 40
Triangle Attachments 41
T-Track 42
Service Record 43
From the library of: Diamond Needle Corp

10
EASTMAN
Front Frame Assembly, 9"
Please Specify machine voltage and
complete serial number when ordering
replacement parts.
Item numbers are for reference only. Please
Specify PART NUMBER when ordering replace-
ment parts.
ITEM PART NO. DESCRIPTION QTY.
1 PC-1 Frame, Front, 9" 1
2 PM-02410 Shaft, Counter Arm 1
3 A-267 Counter 1
4 PC-9-1 Cover, Elevating Mech. 1
PM-40 Decal, Pacemaker 1
PM-42 Decal, Adjustment 1
5 PM-74 Nut, Lock, Counter 1
6 PM-70 Screw, Adj., Counter 1
7 PM-30 Stud, Elevating Mech.,
Ratchet 1
8 PS-21 Cam, Elevating Mech. 1
9 F-134 Pawl, Elevating 1
10 PS-17 Dog, Elevating Mech. 1
11 PM-36 Spring, Dog 1
12 PM-34 Stud, Dog Spring 1
13 F-57 Stud, Dog Pivot 1
14 F-131A Ratchet 1
15 F-131B Pinion 1
16 F-131-1 Ratchet & Pinion Ass'y 1
17 CH-1055 Link, Actuating Ass'y 1
18 F-119 Gear, Front Elevating 1
19 PM-31 Stud, Elevating Gear &
Sprocket 1
20 PM-136 Bushing, Counter Bar 1
21 PM-37 Spring, Return 1
22 PM-33 Stud, Return Spring 1
23 PM-21 Stud, Wheel Front 1
24 PS-32 Bracket, Safety Roller 1
25 PM-55 Bearing 1
26 PM-11389 Stud, Bearing,
Safety Bracket 1
ITEM PART NO. DESCRIPTION QTY.
27 PM-0218 Wheel, Track Ass'y 2
28 F-7A Wheel, Track, Regular 2
29 F-100 Bearing 4
30 F-275 Ring, For F-7 Wheel 2
31 E-225 Washer, Steel
1.00 x .69 6
32 TL-221 Bushing, Track Wheel 2
33 313-86-6 Scr. Mach. Slt. Rd. Hd.
6-32 x .375 4
34 314-99-28 Scr. Mach. Std. Ovl.
10-24 x 1-3/4 3
35 211-34 Nut, Elastic Hex 1/4-20 1
36 331-36-8 Scr. Cap hex Hd.
5/16-18 x 1/2 1
37 410-36 Washer, Flat 5/16 3
38 320-93-5 Scr. Mach. Sltd. Bind
8-32 x 5/16 1
39 335-99-16 Scr. Sokt. Cap Hd.
10-24 x 1 1
40 410-010 Washer, Flt., #10 9
41 203-99 Nut, Hex 10-24 4
42 335-99-12 Scr. Sokt. Cap Hd.
10-24 x 3/4 1
43 410-44 Washer, Flt., 1/2 4
44 331-99-6 Scr. Cap Hex Hd.
10-24 x 3/8 2
45 402-10 Washer, Lock #10 2
46 410-10 Washer, Flt., #10 2
From the library of: Diamond Needle Corp

11
From the library of: Diamond Needle Corp

12
EASTMAN
ITEM PART NO. DESCRIPTION QTY.
34 PS-IL LInk, Pivot, L.H. 1
35 PM-84-2-MS Tube, Teardrop 2
36 344-34-4 Scr. Set Nylok Sokt.
1/4-20 x 1/4 2
37 *9141-046-012 Chain Assembly 1
PM-82 Screw Block, Long 1
PM-83 Screw Block, Short 1
38 *331-44-28 Scr. Cap Hex Hd.
1/2-20 x 1-3/4 2
39 *402-44 Washer, Lock, 1/2 2
40 *410-44 Washer, Flat 1/2 4
41 *410-010 Washer, Flat .#10 9
42 *335-99-10 Scr. Sokt. Cap Hd.
10-24 x 5/8 4
43 *332-99-8 Scr. Cap. Hd. Sokt.
10-24 x 1/2 3
44 *203-102 Nut, Hex 10-32 2
45 *542-6-5 Rivet, Flt. Hd. Solid 1
46 *410-010 Washer, Flat, (Modified) 4
47 *335-99-12 Scr. Sokt. Cap Hd.
10-24 x 3/4 1
48 *410-34 Washer, Flat 1/4 2
49 *335-34-10 Scr. Sokt. Cap Hd.
1/4-20 x 5/8 1
50 342-34-6 Scr. Set Sokt. Hd.
1/4-20 x 3/8 2
51 342-34-12 Scr. Set Sokt. Hd.
1/4-20 x 3/4 4
52 203-34 Nut, Hex 1/4-20 4
53 546-6-8 Pin 2
54 9002-001 Wsher, Flat 2
55 332-36-16 Scr. Cap Flthd. Sokt.
5/16-18 x 1 4
56 DY-1012 Finger, Pick Up Ass'y, Rear 1
57 DY-403 Finger, Pick Up, Rear 1
58 PM-03067-MS Teardrop Blade Ass'y 2
59 PM-11977 Retaining Clip 1
60 211-34 Nut, Elastic 1/4-20 2
61 PM-82 Stud 1
62 PM-83 Stud 1
MS- Machine Size
* Part of PM-0402
Front Frame Assembly, 9"
Please Specify machine voltage and
complete serial number when ordering
replacement parts.
Item numbers are for reference only. Please
Specify PART NUMBER when ordering replace-
ment parts.
ITEM PART NO. DESCRIPTION QTY.
1 CHT-424-3 Wheel, Hand, 5/8 Bore 1
2 V-68 Washer, Turbine 2
3 PM-76 Sprocket 1
4 PM-79 Bearing, Sprocket tube 1
5 PM-4-MS Shaft, Sprocket 1
PM-4-2-MS Shaft, Sprocket, Edge
Control, ONLY 1
6 *PC-1 Frame, Front, 9" 1
7 PM-77 Collar, Guide 1
8 PM-5-MS Tube, Sprocket, Shaft 1
9 *PM-11-1 Rod, Sliding, Short,
9" Machine 1
10 *PM-10-1 Rod, Sliding, Long,
9" Machine 1
11 *PM-0218 Wheel, Track Assembly
Pacemaker 2
12 *F-100 Bearing 2
13 *F-275 Ring for F-7 Wheel 1
14 *E-225 Washer, Steel 3
15 *F-7A Wheel, Track 1
16 *TL-221 Bushing, Track Wheel 1
17 *PM-25 Shaft, Connecting Bar 1
18 *PM-26 Bushing, Connecting Bar
Shaft 1
19 *PS-2 Plate, Fulcrum Support 1
20 *PM-27 Link, Counter Activating 1
21 *F-121 Sprocket 1
22 *PS-4 Bar, Actuating Counter 1
23 *PM-11465 Washer, Spring 1
24 *PM-29 Stud, Fulcrum Actuating 1
25 *PM-28 Stud, Fulcrum Pivot 1
26 *PS-3 Fulcrum, Counter 1
27 *PC-3 Block, Front Lifting 1
28 DY-1011 Finger, Pick Up Ass'y,
Front 1
29 PM-72 Bearing, Brake 2
30 DY-402 Finger, Pick Up, Front 1
31 PM-0101 Finger, Stud Assembly 2
32 PS-1 Link, Pivot R.H. 1
33 PM-0102 Stud, Pivot Link 2
From the library of: Diamond Needle Corp

13
From the library of: Diamond Needle Corp

14
EASTMAN
Back Frame Assembly , 9"
Item numbers are for reference only. Please
Specify PART NUMBER when ordering replace-
ment parts.
Please Specify machine voltage and
complete serial number when ordering
replacement parts.
ITEM PART NO. DESCRIPTION QTY.
26 202-34 Nut, Hex 1/4-20 4
27 342-34-12 Scr. Set Sokt. Hd.
1/4-20 x 3/4
28 *411-48-2 Washer, Fiber .625 ID
x .0625 Thk. 1
29 *335-99-10 Scr. Sokt. Cap Hd.
10-24 x 5/8 4
30 *410-010 Washer, Flat #10 4
31 *410-44 Washer, Flat 1/2 6
32 *402-44 Washer, Lock 1/2 3
33 *205-44 Nut, Hvy Hex Jam 1/2-20 2
34 *9141-046-012 Chain Assembly, 9" 1
PM-82 Screw Block, Long 1
PM-83 Screw Block, Short 1
35 *206-44 Nut, Hex Fin. Jam 1/2-20 2
36 *411-44-2 Washer, Fiber
.500 ID x .062 Thk. 2
37 342-34-6 Scr. Set Sokt. Hd.
1/4-20 x 3/8 4
38 332-36-16 Scr. Cap Flthd. Sokt.
5/16-18 x 1 4
39 PM-03067-MS Teardrop Blade Assembly 2
MS-Machine Size
NOTE: All Pacemakers 84" and above require a
double track wheel configuration
(part number PM-02439).
ITEM PART NO. DESCRIPTION QTY.
1 *PC-2 Frame, Back 9" 1
2 *PM-76 Sprocket, Upper 1
3 *V-68 Washer, Turbine 2
4 *PM-12A Stud, Rubber Wheel 2
5 *PM-0205 Wheel, Rubber Ass'y 2
6 *PM-1000 Wheel, Rubber Modified 1
7 *TL-247 Bushing, Pillow Block Long 1
8 *PM-79 Bearing, Sprocket Tube 1
9 *PM-10-1 Rod, Sliding, Long 9"
Machine 1
10 *PM-11-1 Rod, Sliding, Short 9"
Machine 1
11 *PM-12 Stud, Sprocket Wheel 1
12 *F-121 Sprocket, Lower 1
13 *PC-4 Block, Back Lifting 1
14 DY-1012 Finger, Pick Up Ass'y, Rear 1
15 PM-72 Bearing, Brake 1
16 DY-403 Finger, Pick Up, Rear 1
17 PM-0101 Finger, Stud Assembly 2
18 PS-IL Link, Pivot, L.H. 1
19 PM-18 Stud, Pivot Link 2
20 PS-1 Link, Pivot, R.H. 1
21 PM-84-2-MS Tube, Teardrop 2
22 Dy-1011 Finger, Pick Up Ass'y
Front 1
23 DY-402 Finger, Pick Up Front 1
24 9002-001 Washer, Flat 2
25 546-6-8 Pin 2
From the library of: Diamond Needle Corp

15
From the library of: Diamond Needle Corp

16
EASTMAN
Cross member &
Component Kit
Item numbers are for reference only.
Please Specify PART NUMBER when
ordering replacement parts.
ITEM PART NO. DESCRIPTION QTY.
1 CHT-424-3 Wheel, Hand Bore 1
2 PM-77 Collar, Guide 1
3 PM-79 Bearing, Sprocket Tube 2
4 PM-5-MS Tube, Sprocket Shaft 1
5 PM-4-MS Shaft, Sprocket 1
6 PM-22-MS Platform 1
7 PM-0100-MS Staytube & Plug Ass'y 2
8 PM-11415 Plug, Nip Roller 2
9 F-122 Washer, Lower Rear
Elevating 2
10 PM-11394 Stud, Nip Roller 2
11 F-228 Bearing, Ball Flange 2
12 PM-8-MS Roller, Staytube 1
13 301-14-20 Scr. Wood Sltd. Flt. Hd.
14 x 1-1/4 4
14 342-102-3 Scr. Set Sokt. Hd.
10-32 x 3/16 1
15 331-44-32 Scr. Cap Hex Hd.
1/2-20 x 2 6
16 402-44 Washer, Lock 1/2 6
17 410-44 Washer, Flat 1/2 7
18 203-34 Nut, Hex 1/4-20 10
19 331-36-10 Scr. Cap Hex Hd.
5/16-18 x 5/8 4
20 402-36 Washer, Lock 5/16 10
21 331-36-16 Scr. Cap Hex Hd.
5/16-18 x 1 4
22 410-36 Washer, Flt. 5/16 10
23 F-185 Rod, Cross Short 2
24 F-183-A Turnbuckle 1/4-20 2
25 PM-2-MS Rod, Tie Long 2
26 9066-001 Tape, Poly A/R
MS-MachineSize
Heavy Duty KIT
ADD PM-6001-2-MS
PM-11445-MS Channel, Cross HD 2
PM-03065-MS Channel, Cross HD 2
PM-20743 Plate, End HD 4
SY-20295 Channel, Plate End 1
SY-20331-MS Channel, Cross Frame 2
SY-20330-MS Channel, Cross
Extrusion 2
PM-11401 Shim, Cross Channel 4
PM-0403-3 Frame, Back Ass'y HD 1
PM-0402-3 Frame, Front Ass'y HD 1
OMIT
PM-0402-1 Frame, 9" Front Ass'y 1
PM-0403 Frame, 9" Back Ass'y 1
PM-0402-2 Frame, 11" Front Ass'y 1
PM-0403-2 Frame, 11" Back Ass'y 1
F-183-A Turnbuckle 1/4-20 2
F-185 Rod, Tie Short 2
PM-2-MS Rod, Tie Long 2
PM-0100-MS Staytube & Plug Ass'y 2
From the library of: Diamond Needle Corp

17
From the library of: Diamond Needle Corp

18
EASTMAN
Front Upright Assembly
Manual Edge Control Item numbers are for reference only.
Please Specify PART NUMBER when
ordering replacement parts.
ITEM PART NO. DESCRIPTION QTY.
36 560-6-16 Pin, Roller 3
37 702-25 Chain, Link Connecting 4
38 203-34 Nut, Fin. Hex 1/4-20 2
39 331-36-12 Scr. Cap Hex Hd.
3/16-18 x 3/4 2
40 402-36 Washer Lock 5/16 2
41 335-34-40 Scr. Sokt. Cap Hd.
1/4-20 x 2-1/2 1
42 205-36 Nut Heavy Hex
5/16-18 2
43 335-99-12 Scr. Socket Cap Hd.
10-24 x 3/4 2
44 402-010 Washer Lock #10 2
45 410-010 Washer Flat #10 2
46 9120-604-1 Leather Brake Pad 2
47 531-2-8 Pin, Cotter 1
48 410-34 Washer, Flat 1/4 2
49 9004-0223 Spring Comp. Brake Adj. 1
50 632-18 Retaining Ring 1
51 A-253 Washer, Flat .502 ID
x .0299 Thk. 2
52 325-102-8 Scr. Mach. Phillips Jack
Hd. 10-32 x 1/2 2
53 9060-012 Collar, 1/2 ID 2
54 331-36-10 Scr. Cap Hex Hd.
5/16-18 x 5/8 2
* PS-29N Upright, Bottom Front, Lg. 1
(PM-0302-1 Upright #3 Only)
ITEM PART NO. DESCRIPTION QTY.
1 PS-11 Support, R.B.A. Roller R.H. 1
2 PM-54 Roller, R.B.A. Chain 3
3 PS-11L Support, R.B.A. Roller L.H. 1
4 PS-7 Bracket, R.B.A. Shaft 1
5 CEC-13 Roller, Guide 1
6 PS-9 Plate, R.B.A. Sliding 2
7 PM-50 Stud, R.B.A. Sliding Sleeve 2
8 PM-51 Stud, R.B.A. Sliding 2
9 PS-12 Plate, R.B.A. Chain
Mounting 2
10 PM-53 Spacer, R.B.A. 4
11 PM-55 Bearing 2
12 PM-52 Stud, R.B.A. Bearing 2
13 PS-6 Upright, Top Front 1
14 PS-8 Batwing, Front 1
15 PM-46 Stud, R.B.A. Stop 2
16 PM-56 Stud, R.B.A. Brake 2
17 *PS-30N Upright, Bottom Front
Med. Lg. 1
18 PS-10L Support, R.B.A. Double
Roller L.H. 1
19 PC-7 Bracket, Brake 2
20 PM-02200 Brake Adjustment Ass'y 1
21 PM-11390 Block, Brake Left 1
22 PM-11391 Block, Brake Right 1
23 PM-69 Nut, Brake Lock 1
24 PM-11392 Screw, Brake Adj. 1
25 PS-10 Support, R.B.A. Double
Roller R.H. 1
26 PM-58 Shaft, R.B.A. Actuating 1
27 M-52 Bearing, Flanged 2
28 CHT-424-2 Handwheel 2
29 PS-20 Support, R.B.A.
Actuating Shaft 2
30 PM-57 Actuating Sprocket 1
31 PM-63 Turnbuckle, R.B.A. Chain 1
32 PM-65 Screw, R.B.A. Chain L.H. 1
33 CH-58 Screw Chain 1
34 9140-020-002 Chain, Sprocket Ass'y 1
35 541-4-4 Rivet 6
From the library of: Diamond Needle Corp

19
From the library of: Diamond Needle Corp

20
EASTMAN
Rear Upright
Assembly
ITEM PART NO. DESCRIPTION QTY.
1 PM-47 Shaft, Nylon Roller 1
2 PM-45 Roller, Nylon 1
3 PS-15 Batwing 1
4 PS-14 Bracket, Upright R.B.A. Top 1
5 *PS-31 Upright, Bottom Back
32" High 1
6 410-38 Washer, Flat 3/8 2
7 313-34-8 Scr. Mach. Sltd. Rd. Hd.
1/4-20 x 1/2 3
8 203-34 Nut, Hex 1/4-20 3
9 205-36 Nut, Heavy Hex
5/16-18 2
10 402-36 Washer, Lock 5/16 4
11 331-36-10 Scr. Cap Hex Hd.
5/16-18 x 5/16 4
12 PS-29 Upright, Bottom Back 1
13 TL-217 Bracket, Wheel 1
14 PM-0212-1 Upright Assembly, 12" High 1
PM-0212-2 Upright Assembly, 18" High 1
PM-0212-3 Upright Assembly, 25" High 1
From the library of: Diamond Needle Corp
Table of contents
Other EASTMAN Spreader manuals
Popular Spreader manuals by other brands
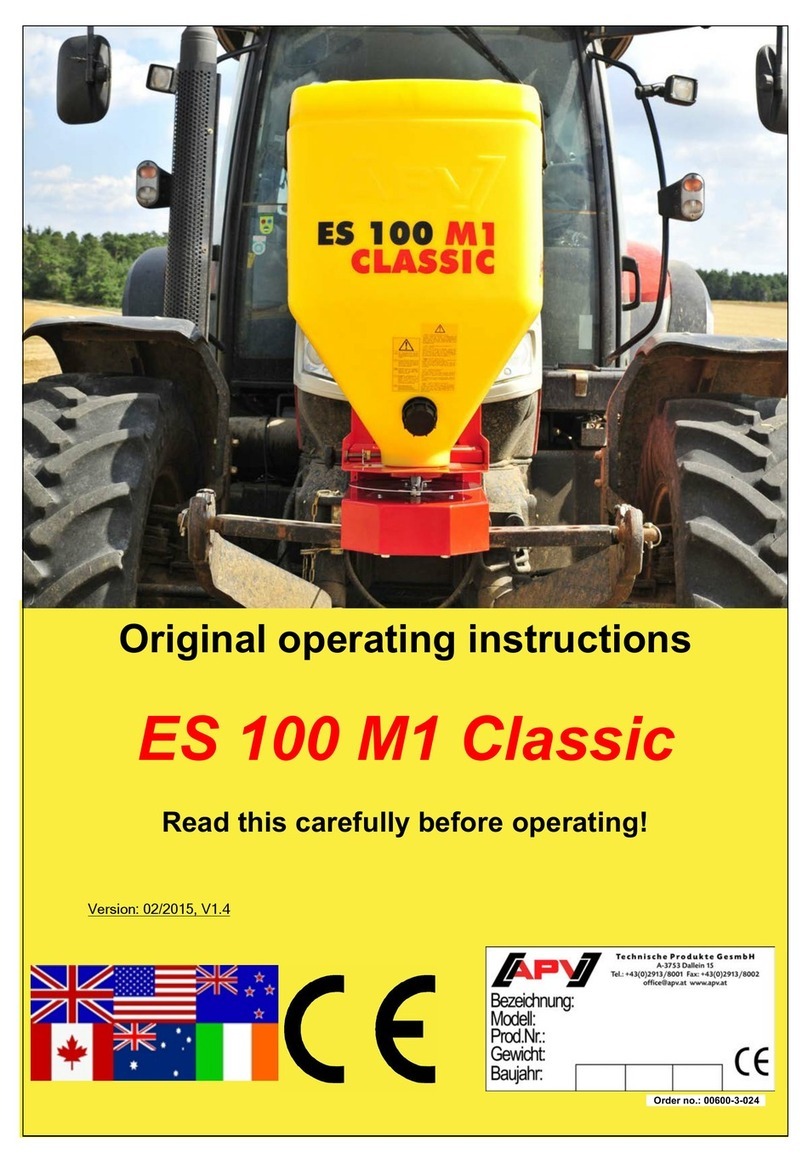
APV
APV ES 100 M1 Classic Original operating instructions

Gardena
Gardena Classic 300 Assembly instructions
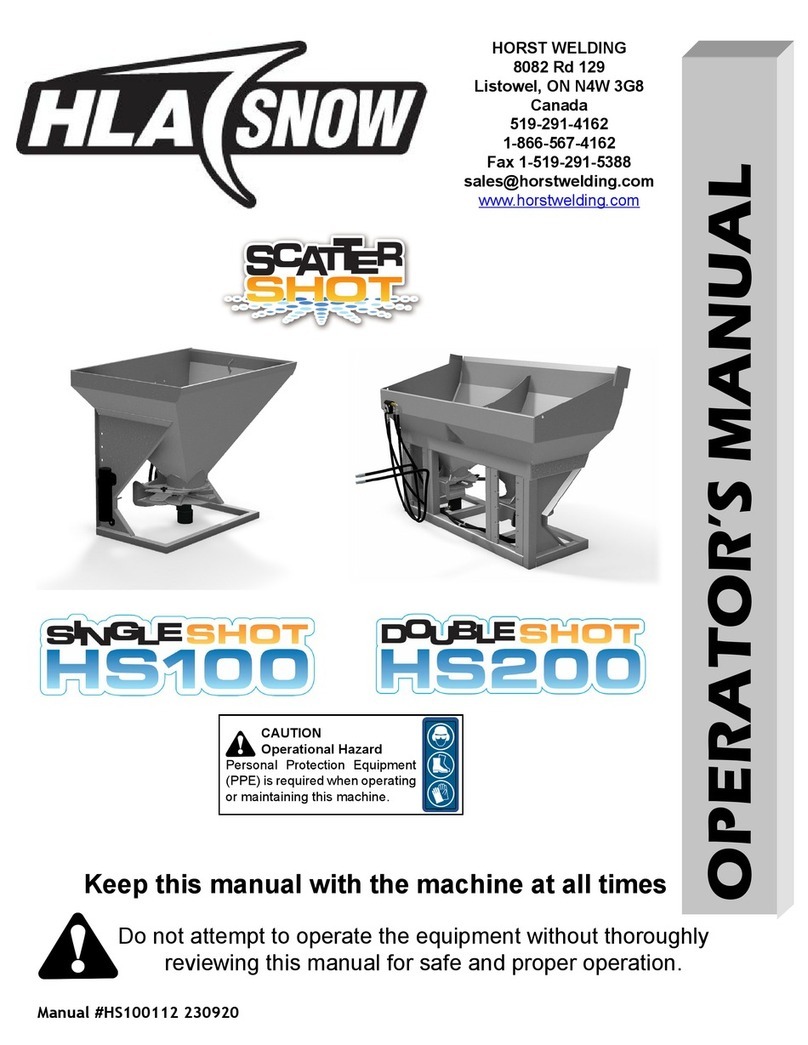
Horst Welding
Horst Welding HLA SNOW SINGLESHOT HS100 Operator's manual
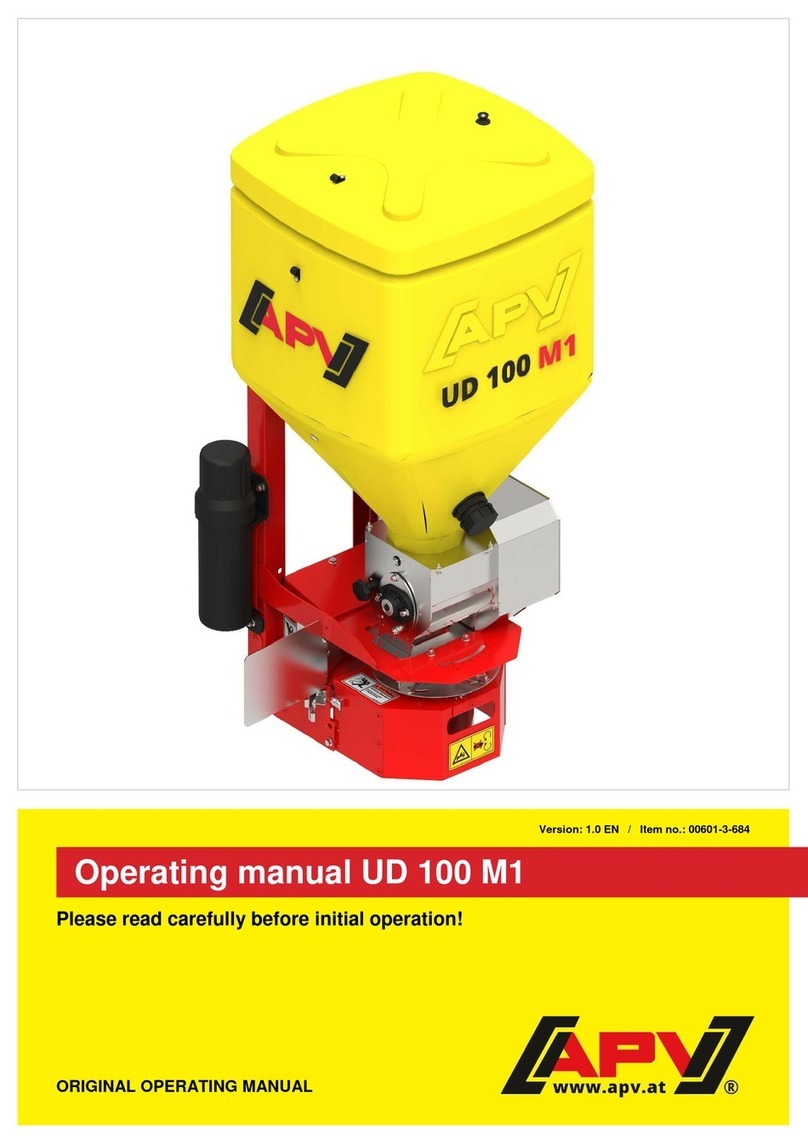
APV
APV UD 100 M1 operating manual

Western
Western Striker 98825 installation instructions
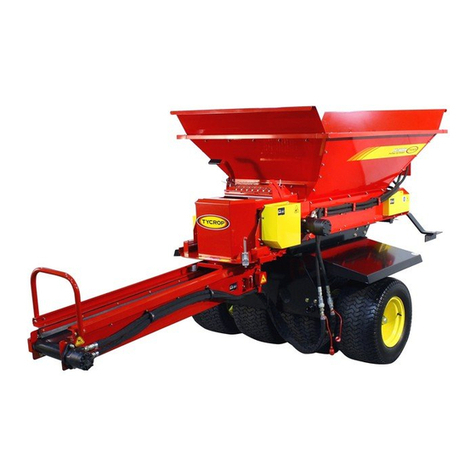
TYCROP
TYCROP ProPass 180 Operator's manual
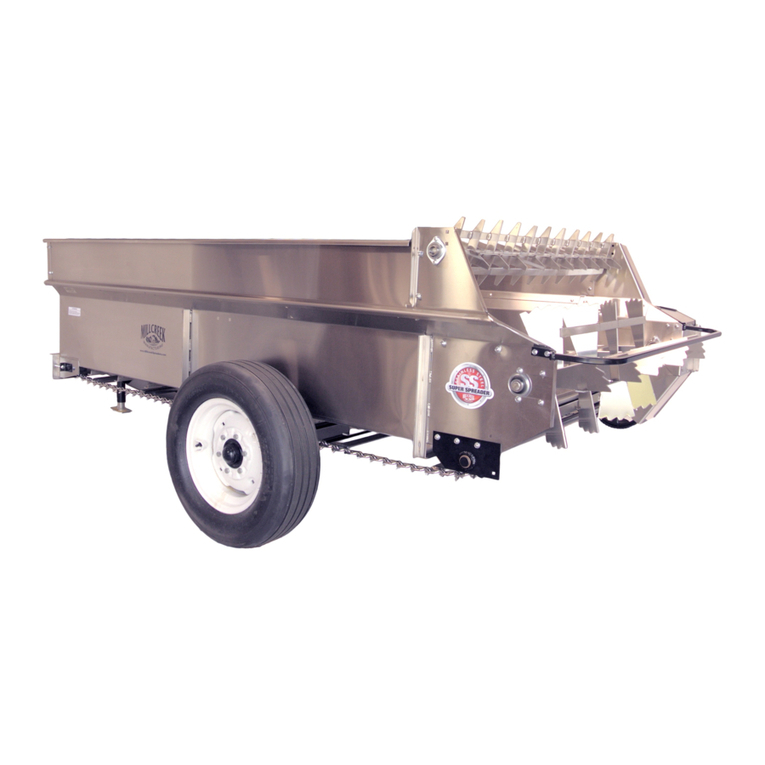
Millcreek
Millcreek 97 Operator's manual

Trynex International
Trynex International TurfEx TT5000 owner's manual

L.T. Rich Products
L.T. Rich Products 135LB owner's manual

Gardena
Gardena Classic 300 Assembly instructions
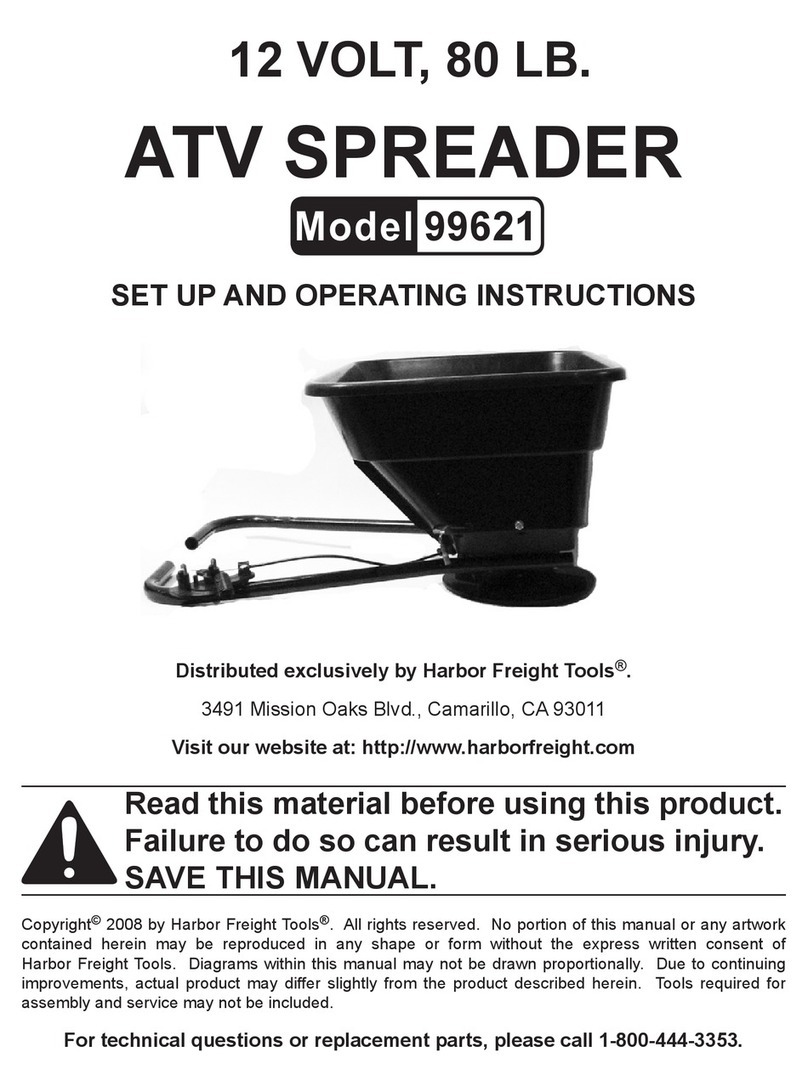
Harbor Freight Tools
Harbor Freight Tools 99621 Set up and operating instructions
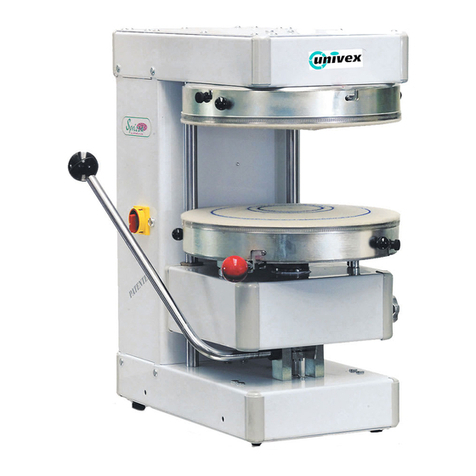
Univex
Univex SPZ40 Operator's manual