Echelon LONWORKS FT 5000 User manual

LONWORKS®Twisted Pair
Control Module User’s Guide
078-0015-01F

Echelon, LONWORKS,LONMARK,NodeBuilder, LonTalk,Neuron,
3120, 3150, ShortStack, LonMaker, and the Echelon logo are
trademarks of Echelon Corporation registered in the United
States and other countries.
Other brand and product names are trademarks or
registered trademarks of their respective holders.
Smart Transceivers, Neuron Chips, and other OEM Products
were not designed for use in equipment or systems, which
involve danger to human health or safety, or a risk of
property damage and Echelon assumes no responsibility or
liability for use of the Smart Transceivers or Neuron Chips in
such applications.
Parts manufactured by vendors other than Echelon and
referenced in this document have been described for
illustrative purposes only, and may not have been tested
by Echelon. It is the responsibility of the customer to
determine the suitability of these parts for each
application.
ECHELON MAKES AND YOU RECEIVE NO WARRANTIES OR
CONDITIONS, EXPRESS, IMPLIED, STATUTORY OR IN ANY
COMMUNICATION WITH YOU, AND ECHELON SPECIFICALLY
DISCLAIMS ANY IMPLIED WARRANTY OF MERCHANTABILITY
OR FITNESS FOR A PARTICULAR PURPOSE.
No part of this publication may be reproduced, stored in a
retrieval system, or transmitted, in any form or by any means,
electronic, mechanical, photocopying, recording, or
otherwise, without the prior written permission of Echelon
Corporation.
Printed in the United States of America.
Copyright © 1992, 2011 Echelon Corporation.
Echelon Corporation
www.echelon.com

LonWorks Twisted Pair Control Module User's Guide iii
Welcome
Echelon’s LONWORKS®Twisted Pair Control Modules contain the core elements
for device designs using LONWORKS technology. The core elements of a control
module are an FT 5000 Smart Transceiver or Neuron®3150®Chip, crystal clock
circuit, I2C EEPROM or JEDEC MO-052 AE PLCC memory socket (32-pin
rectangular), Communications Transformer or twisted pair transceiver, and
unbuffered access to the I/O, SERVICE~, and RESET~ signals.
All of the Neuron 3150 LONWORKS Twisted Pair Control Modules share a
common footprint and I/O interface to allow systems with different media
requirements to share common application electronics board designs. The FT
5000 Control Module has a similar I/O interface so that you can easily modify
designs that use a Neuron 3150 Control Module to use the FT 5000 Control
Module.
Table 1lists the available modules.
Table 1. LONWORKS Twisted Pair Control Modules
Module
Model
Number Features
FT 5000 Control Module 55040R-10 Transformer-isolated, free topology, 78
kbps communications, up to 80 MHz
system clock (the system clock rate is
application configurable; see
Configuration for FT 5000 Control
Modules on page 41).
TP/FT-10 Free Topology Control
Module
55020R-01 Transformer-isolated, free topology, 78
kbps communications, 5 MHz clock
TP/FT-10F Free Topology Flash
Control Module
55020R-10 Transformer-isolated, free topology, 78
kbps communications, flash memory
support, 10 MHz clock
TP/XF-78 Control Module 55010R-00 Transformer-isolated, bus operation, 78
kbps communications, 5 MHz clock
TP/XF-78F Flash Control Module 55010R-10 Transformer-isolated, bus operation, 78
kbps communications, flash memory
support, 10 MHz clock
TP/XF-1250 Control Module 55030R-10 Transformer-isolated, bus operation, 1.25
Mbps communications, 10 MHz clock
This manual provides technical specifications for the electrical and mechanical
interfaces and operating environment characteristics for the control modules.

iv
Audience
This document provides specifications and user instruction for customers who
have purchased any of Echelon’s Twisted Pair Control Modules.
Related Documentation
The following manuals are available from the Echelon Web site
(www.echelon.com) and provide additional information that can help you develop
applications for Neuron Chip or Smart Transceiver devices:
•FT 3120 / FT 3150 Smart Transceiver Data Book (005-0139-01D).This
manual provides detailed technical specifications on the electrical
interfaces, mechanical interfaces, and operating environment
characteristics for the FT 3120®and FT 3150 Smart Transceivers.
•I/O Model Reference for Smart Transceivers and Neuron Chips (078-
0392-01B). This manual provides information about the I/O models used
by Echelon’s Neuron Chips and Smart Transceivers. It includes
hardware and software considerations for each of the I/O models.
•Introduction to the LONWORKS Platform (078-0183-01B).This manual
provides an introduction to the ISO/IEC 14908-1 (ANSI/CEA-709.1 and
EN14908) Control Network Protocol, and provides a high-level
introduction to LONWORKS networks and the tools and components that
are used for developing, installing, operating, and maintaining them.
•LONMARK®Application Layer Interoperability Guidelines.This manual
describes design guidelines for developing applications for open
interoperable LONWORKS devices, and is available from the LONMARK
Web site, www.lonmark.org.
•LonMaker User's Guide (078-0333-01A). This manual describes how to
use the Turbo edition of the LonMaker®Integration Tool to design,
commission, monitor and control, maintain, and manage a network.
•Mini FX User’s Guide (078-0398-01A). This manual describes how to use
the Mini FX Evaluation Kit. You can use the Mini FX Evaluation Kit to
develop a prototype or production control system that requires
networking, or to evaluate the development of applications for control
networks using the LONWORKSplatform.
•NodeBuilder®FX User’s Guide (078-0405-01A). This manual describes
how to develop a LONWORKS device using the NodeBuilder tool.
•Neuron C Programmer’s Guide (078-0002-02H). This manual describes
how to write programs using the Neuron C Version 2.2 programming
language.
•Neuron C Reference Guide (078-0140-02F). This manual provides
reference information for writing programs using the Neuron C Version
2.2 programming language.
•Series 5000 Chip Data Book (005-0199-01B). This manual provides
detailed technical specifications on the electrical interfaces, mechanical

LonWorks Twisted Pair Control Module User's Guide v
interfaces, and operating environment characteristics for the Neuron
5000 Chips and FT 5000 Smart Transceivers.
•ShortStack FX User's Guide (078-0365-01B). This manual describes how
to develop an application for a LONWORKS device using Echelon’s
ShortStack®FX Micro Server. It describes the architecture of a
ShortStack device and how to develop a ShortStack device.
All of the Echelon documentation is available in AdobePDF format. To view the
PDF files, you must have a current version of the Adobe Reader, which you can
download from Adobe at: get.adobe.com/reader.
Reference Documentation
The following documents and books provide additional information that can help
you develop applications for Neuron Chip or Smart Transceiver devices:
•American Society for Testing and Materials (ASTM) B258 - 02(2008)
Standard Specification for Standard Nominal Diameters and Cross-
Sectional Areas of AWG Sizes of Solid Round Wires Used as Electrical
Conductors. www.astm.org/Standards/B258.htm
•Comité européen de normalisation electrotechnique1(CENELEC) EN
55022 – Information technology equipment – Radio disturbance
characteristics – Limits and methods of measurement.
•Comité international spécial des perturbations radioélectriques2(CISPR)
22 – Information Technology Equipment – Radio Disturbance
Characteristics – Limits and Methods of Measurement.
•Digital Communications: Fundamentals and Applications, 2nd Edition,
by Bernard Sklar, Prentice Hall, 2001.
•Electrostatic Discharge Association standard ESD STM5.1: Electrostatic
Discharge Sensitivity Testing – Human Body Model.
www.esda.org/freedowloads.html
•EMC for Product Designers, Fourth Edition, by Tim Williams, Newnes,
2007.
•EMI Troubleshooting Techniques, by Michel Mardiguian, McGraw-Hill
Professional, 1999.
•European Union Restriction of Hazardous Substances (RoHS) Directive
2002/95/EC. europa.eu.int/eur-lex/pri/en/oj/dat/2003/l_037/
l_03720030213en00190023.pdf
•Comité européen de normalisation3(CEN) Electromagnetic
Compatibility (EMC) standards (such as the IEC 61000-4 series of
standards).
•High Speed Digital Design: A Handbook of Black Magic, by Howard
Johnson and Martin Graham, Prentice Hall, 1993.
1European Committee for Electrotechnical Standardization
2International Special Committee on Radio Interference
3European Committee for Standardization

vi
•High-Speed Digital System Design: A Handbook of Interconnect Theory
and Design Practices, by Stephen H. Hall, Wiley-IEEE Press, 2000.
•International Organization for Standardization (ISO) and International
Electrotechnical Commission (IEC) standard ISO/IEC 14908 Control
Network Protocol
•Introduction to Electromagnetic Compatibility (Wiley Series in
Microwave and Optical Engineering), by Clayton R. Paul, Wiley-
Interscience, 2006.
•Institute for Printed Circuits (IPC) / Joint Electron Device Engineering
Council (JEDEC) Solid State Technology Association standard:
IPC/JEDEC J-STD-020D.1 – Moisture/Reflow Sensitivity Classification
for Nonhermetic Solid State Surface Mount Devices.
www.jedec.org/download/search/JSTD020D-01.pdf
•Neuron Chip data book:
oMotorola®LONWORKS Technology Device Data
oToshiba Neuron Chip TMPN3150/3120
oCypress™ Neuron Chip Technical Reference Manual
See the Echelon Series 5000 Chip Data Book (005-0199-01B) or FT 3120
/ FT 3150 Smart Transceiver Data Book (005-0139-01D) for information
about Echelon Smart Transceivers.
•Noise Reduction Techniques in Electronic Systems, 2nd ed., by Henry W.
Ott, John Wiley & Sons, 1988.
•Protection of Electronic Circuits from Overvoltages, by Ronald B.
Standler, John Wiley & Sons, 1989, 2002.
•Title 47 of the Code of Federal Regulations (CFR) Part 15, Radio
Frequency Devices. www.fcc.gov/oet/info/rules/
•US Military Standard MIL-STD-883 Test Method Standard,
Microcircuits: Method 3015.7, Electrostatic Discharge Sensitivity
Classification.
You can purchase copies of CENELEC documents, IEC EMC standards, ISO
standards, US Military Standards, and CISPR documents from the Information
Handling Services (IHS) Global page at: global.ihs.com.IEC EMC standards are
also available from the IEC at: www.iec.ch.

LonWorks Twisted Pair Control Module User's Guide vii
Table of Contents
Welcome.........................................................................................................iii
Audience ........................................................................................................ iv
Related Documentation ................................................................................ iv
Reference Documentation.............................................................................. v
Chapter 1. Electrical Interface ...................................................................... 1
FT 5000 Control Module ................................................................................ 2
JP1 Connector.......................................................................................... 2
Neuron 3150 Control Modules ...................................................................... 3
P1 and P2 Connector Terminals............................................................. 4
Reset Pin......................................................................................................... 5
Service Pin ...................................................................................................... 6
Chapter 2. Mechanical Considerations ....................................................... 7
FT 5000 Control Module ................................................................................ 8
Floorplan Layout ..................................................................................... 8
Mechanical Footprint .............................................................................. 8
Neuron 3150 Control Module ........................................................................ 8
Mechanical Footprint .............................................................................. 9
Chapter 3. Power Requirements .................................................................15
FT 5000 Control Module .............................................................................. 16
Control Module Power Requirements .................................................. 16
Neuron 3150 Control Modules .................................................................... 16
Control Module Power Requirements .................................................. 16
Chapter 4. Network Cabling and Connection..........................................19
Performance Characteristics and Cabling.................................................. 20
Free Topology TP/FT-10 and TP/FT-10F.................................................... 20
Wire Characteristics.............................................................................. 21
Cable Terminations – Free Topology ................................................... 21
Cable Terminations – Doubly Terminated Bus................................... 21
TP/XF-78, TP/XF-78F, and TP/XF-1250 ..................................................... 22
Wire Characteristics.............................................................................. 22
Device Distribution Rule for TP/XF-1250 Segments........................... 22
Cable Terminations – TP/XF-78, -1250 Segments .............................. 24
Chapter 5. Design Issues ...............................................................................27
EMI Design Issues ....................................................................................... 28
Designing Systems for EMC........................................................................ 28
EMC Design Tips................................................................................... 28
FT 5000 Control Module PC Board Layout Guidelines ...................... 29
Neuron 3150 Control Module Keepout Areas...................................... 31
ESD Design Issues ....................................................................................... 32
Designing Systems for ESD Immunity ................................................ 33
Designing for Interoperability..................................................................... 34
Chapter 6. Programming Considerations................................................. 35
External Memory Considerations ............................................................... 36
FT 5000 Control Module ....................................................................... 36
Using an Aardvark I2C/SPI Host Adapter.................................... 36
Clearing the Non-Volatile Memory................................................ 37
Neuron 3150 Control Modules .............................................................. 38

viii
Application Program Development and Export ......................................... 40
NodeBuilder FX Development Tool...................................................... 40
Configuration for FT 5000 Control Modules ................................. 41
Configuration for Neuron 3150 Control Modules ......................... 43
Programming................................................................................... 45
Mini FX Evaluation Kit......................................................................... 45
ShortStack FX Developer’s Kit............................................................. 45

LonWorks Twisted Pair Control Module User's Guide 1
1
Electrical Interface
FT 5000 Control Modules interface to the device application
electronics and to the network through the JP1 connector.
Neuron 3150 Control Modules interface to the device
application electronics and to the network through two
connectors, P1 and P2, respectively.

2 Electrical Interface
FT 5000 Control Module
The following sections describe the electrical interface for the FT 5000 Control
Module.
JP1 Connector
Figure 1and Table 2show the pinout of the JP1 header connector for the FT
5000 Control Module. The I/O pin function names defined in Table 2are the
same as those used in the Series 5000 Chip Data Book, which defines the
functions and electrical characteristics for the signals. The I/O signals are
connected directly to the FT 5000 Smart Transceiver without buffering.
MOV_GND
IO2
IO0
CP2_TXLED
SVC-
RST-
FT_NETA
IO10
IO8
IO6
IO4
SCL
SDA_CS1-
IO11
FT_NETB
IO3
IO1
IO5
IO9
IO7
VDD3V3
CP3_RXLED
JP1
HEADER 13X2
2
4
6
8
10
12
14
16
18
20
22
24
26
1
3
5
7
9
11
13
15
17
19
21
23
25
Figure 1. FT 5000 Control Module JP1 Connector
Table 2. FT 5000 Control Module JP1 Connector
Pin Number Signal Name Description
1 GND Ground
2 RST~ Reset (active low)
3 CP3_RXLED RxActive for network activity LED
4 CP2_TXLED TxActive for network activity LED
5 NC No Connect
6 VDD3V3 3.3 V Input Power
7 GND Ground

LonWorks Twisted Pair Control Module User's Guide 3
Pin Number Signal Name Description
8 SCL I2C serial clock for in-circuit programming
9 SDA_CS1~ I2C serial data for in-circuit programming
10 SVC~ Service (active low)
11 IO0 IO0 for I/O objects
12 IO1 IO1 for I/O objects
13 IO2 IO2 for I/O objects
14 IO3 IO3 for I/O objects
15 IO4 IO4 for I/O objects
16 IO5 IO5 for I/O objects
17 IO6 IO6 for I/O objects
18 IO7 IO7 for I/O objects
19 IO8 IO8 for I/O objects
20 IO9 IO9 for I/O objects
21 IO10 IO10 for I/O objects
22 IO11 IO11 for I/O objects
23 MOV_GND Return (ground) for MOV ESD clamp
24 GND Ground
25 FT_NETA FT network connection
26 FT_NETB FT network connection
Note: The FT 5000 Control Module incorporates DC blocking capacitors and
therefore can directly connect to either non-link power or link power channels.
Neuron 3150 Control Modules
The following sections describe the electrical interface for the Neuron 3150
Control Modules.

4 Electrical Interface
P1 and P2 Connector Terminals
Table 3, Table 4on page 5, and Table 5on page 5 show the pinout of the P1
and P2 connector terminals for the Neuron 3150 Control Modules. The I/O pin
function names defined in Table 3are the same as those used in the Neuron
Chip Data Book, which defines the functions and electrical characteristics for the
signal names. The I/O signals are connected directly to the Neuron 3150 Chip
without buffering.
Table 3. 18-pin I/O Connector (P1) for Neuron 3150 Control Modules
Pin Number Name Description
1 NC No Connect
2 IO0 IO0 for I/O objects
3 GND Ground
4 IO1 IO1 for I/O objects
5 GND Ground
6 IO2 IO2 for I/O objects
7 GND Ground
8 IO3 IO3 for I/O objects
9 RESET~ Reset (active low)
10 IO4 IO4 for I/O objects
11 IO5 IO5 for I/O objects
12 +5 V 5 V Input Power
13 IO6 IO6 for I/O objects
14 IO9 IO9 for I/O objects
15 IO7 IO7 for I/O objects
16 IO10 IO10 for I/O objects
17 IO8 IO8 for I/O objects
18 SERVICE~ Service (active low)

LonWorks Twisted Pair Control Module User's Guide 5
Table 4. 6-pin Network Connector (P2) for the TP/XF Control Modules
Pin Number Name Description
1 CTB Transformer center tap
2 CTA Transformer center tap
3 Data B Network data B signal
4 Data A Network data A signal
5 NC No connection
6 NC No connection
Note: CTA and CTB must be shorted together on the applications electronics
board.
Table 5. 6-pin Network Connector (P2) for the TP/FT-10 and TP/FT-10F
Control Modules
Pin Number Name Description
1 1 No connection
2 2 No connection
3 Data B Network data B signal
4 Data A Network data A signal
5 5 No connection
6 6 No connection
Note: The TP/FT-10 and TP/FT-10F Control Modules incorporate DC blocking
capacitors and therefore can directly connect to either non-link power or link
power channels.
Reset Pin
Pin 2 of the JP1 header on the FT 5000 Control Module is the Smart Transceiver
reset pin (RST~). Pin 9 of the P1 header on the Neuron 3150 Control Module is
the Neuron Chip reset pin (RESET~).
The reset pin on the Smart Transceiver or Neuron Chip can be driven low
externally or can be used as an open drain output to provide a reset signal for the
application circuit. The details of the recommended circuit and loading on the

6 Electrical Interface
reset pin are described in the Series 5000 Chip Data Book or the Neuron Chip
Data Book.
Service Pin
You can access the service pin (SVC~) of the FT 5000 Control Module at pin 10 of
the JP1 header. You can access the service pin (SERVICE~) of the Neuron 3150
Control Module at pin 18 of the P1 header.
This pin is used for various network installation and maintenance scenarios. The
function of this pin is described in the Series 5000 Chip Data Book or Neuron
Chip Data Book.
Figure 2shows a typical circuit for the device service pin. Typical applications
do not require debounce conditioning of momentary push buttons attached to the
service or reset pins. The software response time associated with these inputs is
long enough to effectively provide a software debounce for switches with a contact
bounce settling time as long as 20 msec.
SVC~
VCC VCC
Control Module
VCC
SERVICE~
Smart Transceiver
or Neuron Chip
P1.18
JP1.10
VCC = +3.3V for FT 5000 Control Module
VCC = +5V for Neuron 3150 Control Module
Figure 2. Typical Service Pin Circuit

LonWorks Twisted Pair Control Module User's Guide 7
2
Mechanical Considerations
This chapter discusses the mechanical footprint and connectors of the
Twisted Pair Control Modules. Details of mounting to an application
electronics board are provided.

8 Mechanical Considerations
FT 5000 Control Module
The following sections describe the mechanical interface for the FT 5000 Control
Module.
Floorplan Layout
Figure 3shows three views of the floorplan layout of the FT 5000 Control
Module with some of its prominent features labeled.
FT-X3
1
1
2
3
4
8
7
6
5
FT
5000
AT
24C
512
Y1
1
RV1
C7,17
43.18 mm
(1.7 in)
29.85 mm
(1.175 in)
Back View Front View
Side
View
16 mm
(0.63 in)
Figure 3. FT 5000 Control Module Floorplan Layout
Mechanical Footprint
Figure 4shows the mechanical footprint for an FT 5000 Control Module. You
can solder the module directly to your PCB as a through-hole part or mount it in
a connector. The module includes a male Samtec, Inc. TSW-113-08-T-D-RA
square post header, which fits into a 13x2 pin female connector, such as a
Samtec, Inc. SSM-113-L-DV surface mount socket strip.
Figure 4. FT 5000 Control Module Mechanical Footprint
The figure also shows positioning for Richco®Inc. VMCGE-30M-01 vertical
mount card guides for the Control Module. The card guides are optional,
depending on your application.
Neuron 3150 Control Module
The following sections describe the mechanical interface for the Neuron 3150
Control Modules.

LonWorks Twisted Pair Control Module User's Guide 9
Mechanical Footprint
The Neuron 3150 Twisted Pair Control Modules share a common footprint and
connectors as shown in Figure 5on page 10. The most common control module
mounting scenario uses socket strips on the application electronics board which
connect with P1 and P2 as shown in Figure 6and Figure 7on page 11.
Example vendor information for socket strips that mate with the 0.025 inch (0.64
mm) square header posts of P1 and P2 are listed in Table 6on page 11.
If necessary, taller socket strips can be used to gain more clearance between the
control module and the application board. Decisions about component placement
on the application electronics board must also consider the electromagnetic
interference (EMI) and electrostatic discharge (ESD) issues discussed in Chapter
5, Design Issues, on page 27.
Figure 6and Figure 7show the maximum height of parts on both sides of the
control modules. Application designs using the transformer-isolated twisted pair
transceivers should maintain a minimum of 0.15 inch (3.81 mm) clearance from
P2 pins and traces on the network side of the transformer to achieve the
minimum isolation specified for these modules. Refer to EMI Design Issues on
page 28 and Neuron 3150 Control Module Keepout Areas on page 31 for isolation
requirements.
Three plated mounting holes that accept No. 6 (3.5 mm) mounting screws are
electrically connected to the control module ground plane. When the 0.025 inch
(0.64 mm) square posts of P1 and P2 are inserted into the sockets they provide
enough holding strength (3 oz (85 g)/pin) to secure the control module against
shock and vibration to the operating limits of the components on the control
module. However, at least one metal standoff and fastening screw located at the
mounting hole near the P2 connector is recommended to meet EMI limits and for
ESD protection (see Chapter 5).
For the TP/FT-10 control modules, the recommended metal standoff height is
0.56 inch (14.3 mm) to provide adequate clearance. Note that the Methode
Socket (referenced in Table 6) in this case is not recommended, because its
minimum insertion depth requirement is not met. Use of metal 0.50 inch (12.7
mm) #6 standoffs together with metal spacers can achieve this. Alternately,
metal 0.56 inch (14.3 mm) #6 standoffs alone will be adequate. For the TP/XF
and TP/FT-10F control modules, 0.50 inch (12.7 mm) #6 metal standoffs alone are
recommended.
Figure 8on page 12 presents the height restrictions of the component side of the
control module. The board is divided into two height zones: the maximum height
of components in the first zone is 0.20 inch (5.1 mm). The second zone's
components are 0.47 inch (11.93 mm) for the TP/XF and TP/FT-10F control
modules and 0.555 inch (14.1 mm) for the TP/FT-10 control module. Care should
be taken to ensure that no components on the application electronics board
interfere with the height restricted areas of the control modules.
Figure 9on page 13 shows the recommended PCB pad layout for the application
electronics board to interconnect a control module with an application board that
has socket strips mounted on the component side.

10 Mechanical Considerations
Figure 5. Neuron 3150 Control Module Mechanical Footprint

LonWorks Twisted Pair Control Module User's Guide 11
Table 6. Socket Strips Suitable for Use with the Control Module Header Pins
Manufacturer P1: 18-pin (2 X 9) P2: 6-pin (1 X 6)
Samtec SSW-109-01-T-D SSW-106-01-T-S
Methode * 9000-209-303 9000-106-303
Advanced
Interconnections
BC-009-124TL BC006-123TL
* Not recommended for use with the TP/FT-10 or TP/FT-10F Control Modules.
Figure 6. Recommended Spacing between the TP/XF-78, TP/XF-78F, and TP/XF-1250
Control Modules and the Application Electronics Board
Figure 7. Recommended Spacing between the TP/FT-10 and TP/FT-10F Control Modules
and the Application Electronics Board

12 Mechanical Considerations
Figure 8. Vertical Component Profile for the Control Modules
This manual suits for next models
16
Table of contents
Popular Control Unit manuals by other brands

Weidmüller
Weidmüller DPA/RES operating instructions
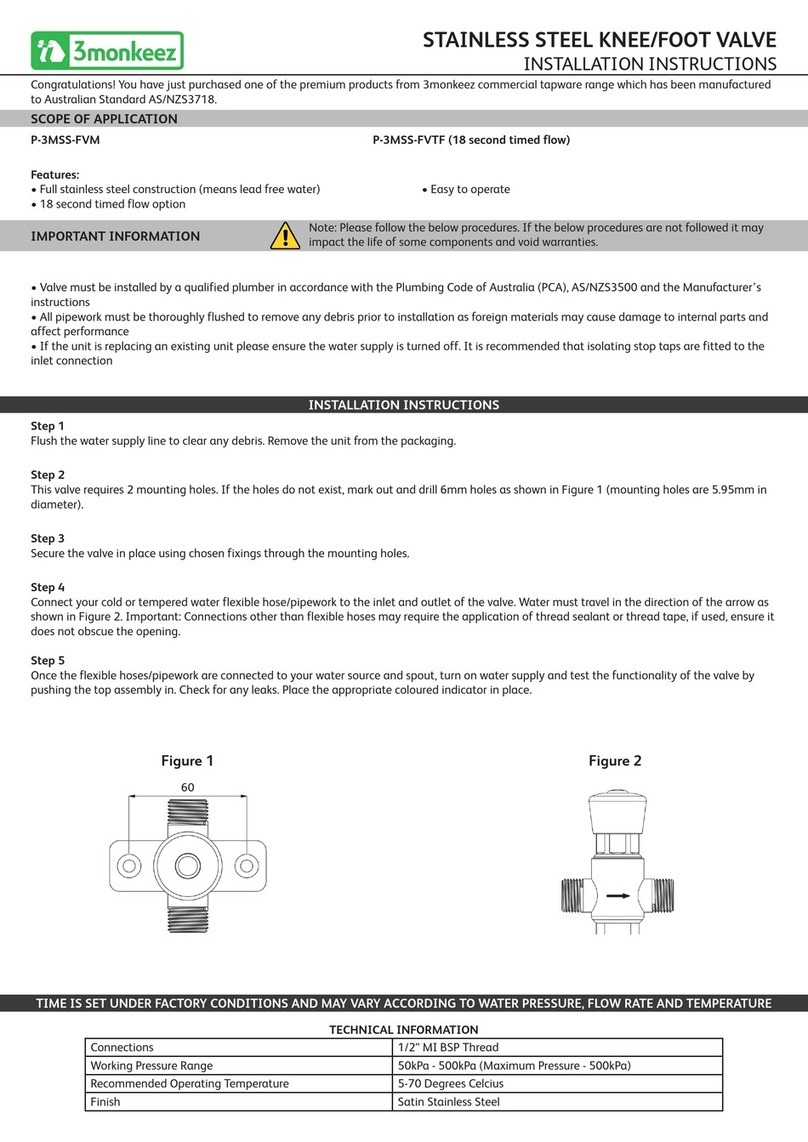
3monkeez
3monkeez P-3MSS-FVM installation instructions

Wahoo Fitness
Wahoo Fitness GymConnect Programming guide
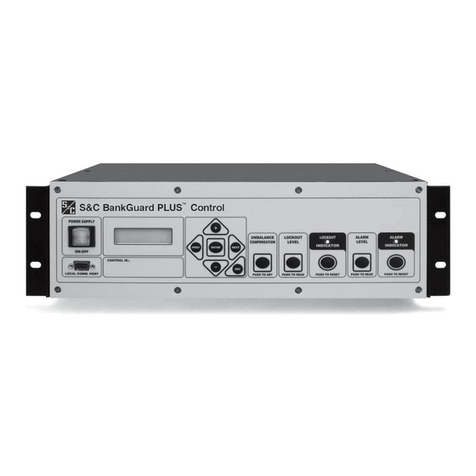
S&C
S&C BankGuard PLUS Operation instructions

Emerson
Emerson ENARDO 860 Series instruction manual

Motorola
Motorola Canopy Backhaul Module quick start guide